AMCI SMD23 Series User manual

SMD23
Integrated Stepper
Drive & Motor
A
M
C
I
M
o
t
i
o
n
C
o
n
t
r
o
l
P
r
o
d
u
c
t
s
ADV ANC ED
MIC RO CON T RO L S INC.
U
s
e
r
M
a
n
u
a
l
Manual #: 940-0S050

Important User Information
The products and application data described in this manual are useful in a wide variety of different
applications. Therefore, the user and others responsible for applying these products described
herein are responsible for determining the acceptability for each application. While efforts have
been made to provide accurate information within this manual, AMCI assumes no responsibility for
the application or the completeness of the information contained herein. Throughout this manual the
following two notices are used to highlight important points.
WARNINGS tell you when people may be hurt or equipment may be damaged if the procedure is
not followed properly.
CAUTIONS tell you when equipment may be damaged if the procedure is not followed properly. No
patent liability is assumed by AMCI, with respect to use of information, circuits, equipment, or
software described in this manual. The information contained within this manual is subject to
change without notice. UNDER NO CIRCUMSTANCES WILL ADVANCED MICRO CONTROLS,
INC. BE RESPONSIBLE OR LIABLE FOR ANY DAMAGES OR LOSSES, INCLUDING INDIRECT
OR CONSEQUENTIAL DAMAGES OR LOSSES, ARISING FROM THE USE OF ANY
INFORMATION CONTAINED WITHIN THIS MANUAL, OR THE USE OF ANY PRODUCTS OR
SERVICES REFERENCED HEREIN.
Standard Warranty
ADVANCED MICRO CONTROLS, INC. warrants that all equipment manufactured by it will be free
from defects, under normal use, in materials and workmanship for a period of [18] months. Within
this warranty period, AMCI shall, at its option, repair or replace, free of charge, any equipment
covered by this warranty which is returned, shipping charges prepaid, within one year from date of
invoice, and which upon examination proves to be defective in material or workmanship and not
caused by accident, misuse, neglect, alteration, improper installation or improper testing. The
provisions of the “STANDARD WARRANTY” are the sole obligations of AMCI and excludes all
other warranties expressed or implied. In no event shall AMCI be liable for incidental or
consequential damages or for delay in performance of this warranty.
Returns Policy
All equipment being returned to AMCI for repair or replacement, regardless of warranty status, must
have a Return Merchandise Authorization number issued by AMCI. Call (860) 585-1254 with the
model and serial numbers along with a description of the problem. A “RMA” number will be issued.
Equipment must be shipped to AMCI with transportation charges prepaid. Title and risk of loss or
damage remains with the customer until shipment is received by AMCI.
24 Hour Technical Support Number
Technical Support, in the form of documents, FAQs, and sample programs, is available from our
website, www.amci.com. 24 Hour technical support is also available on this product. For technical
support, call (860) 585-1254. Your call will be answered at the factory during regular business
hours, Monday through Friday, 8AM - 5PM EST. During non-business hours, an automated system
will ask you to leave a detailed message and the telephone number that you can be reached at.
The system will page an engineer on call. Please have your product model number and a
description of the problem ready before you call.
Revision History
This manual, AMCI number 940-0S050, supercedes revision 1.3 of the SMD Series Integrated
Stepper Driver and Motor manual. First released, April 17, 2007 it removes the SMD34’s and
slightly modifies the format

SMD-23 Integrated Stepper Drive & Motor
20 Gear Drive, Plymouth Industrial Park, Terryville, CT 06786 page: 3
Tel: (860) 585-1254 Fax: (860) 584-1973 Web: www.amci.com
ADV ANC ED
MIC RO CON T RO L S INC.
The AMCI Integrated Stepper Motor and Microstepping Drive Combination
represents the future of Stepper Motor Control applications.
The SMD is a self-contained stepper motor and
drive package, capable of optimizing a wide
variety of industrial stepper motor control
applications. It is no longer necessary to run a
cable from the indexer to the drive and then a
cable from the drive to the motor. Now you
simply have to connect the step and direction
signals, along with supply voltage, directly to the
SMD and your installation is complete.
Features
Optimized motor and drive combination
Industry standard Step/Direction control signals
More torque than competitive designs
Eliminates the need for a separate stepper drive
Wide range of operating voltages, 24-75Vdc
Speeds to 2000 RPM
Anti-resonance circuitry
Easy to use configuration software
Uses standard RS232 interface for programming
Programmable motor current
Programmable Idle Current Reduction
400, 1000, 2000, or 5000 selectable step resolution
AMCI quality and reliability
Single power supply
The SMD23’s use step and direction control signals generated from an external source such as
AMCI’s 3202 or 3601 stepper control modules. A logical diagram of the inputs is shown below.
CW Rotation CCW Rotation
STEP
DIR
The SMD23’s are powered by an external DC supply with an operating range of 24 to 75Vdc. There
is an additional control input that can be used to disable the motor. This input can be left floating if
you are not using the disable motor feature.

SMD-23 Integrated Stepper Drive & Motor
20 Gear Drive, Plymouth Industrial Park, Terryville, CT 06786 page: 4
Tel: (860) 585-1254 Fax: (860) 584-1973 Web: www.amci.com
ADV ANC ED
MIC RO CON T RO L S INC.
SMD23 Motor and Drive Specifications
Environmental Specifications
Supply Voltage
24Vdc to 75Vdc max, 4 Amps max per axis, user supplied.
The maximum supply input voltage includes power supply ripple and
motor back EMF.
Operating Temperature
32°to 122°F (0°to 50°C) Also, see Operating Note s on the following page.
Storage Temperature
–40°to 185°F (–40°to 85°C)
Relative Humidity
0 to 95%, non-condensing
Motor Specifications
SMD23-130
Holding Torque – 130 oz-in (0.91 Nm)
Maximum Starting Torque – 120 oz-in (0.85 Nm)
Rotor Inertia – 1.42 oz-in
2
(0.26 kg-cm
2
)
Weight – 1.56 lbs (0.71 kg)
SMD23-240
Holding Torque – 240 oz-in (1.69 Nm)
Maximum Starting Torque – 220 oz-in (1.55 Nm)
Rotor Inertia – 2.51 oz-in
2
(0.46 kg-cm
2
)
Weight – 2.48 lbs (1.13 kg)
Electrical Specifications
Motor Current
User Selectable – 3.4 Arms max 0.3 –3.4Arms in 0.3 increments (10%-100%)
Default value – 2.70 Arms (80%)
Steps per Revolution
400, 1000, 2000, and 5000 – user selectable
Default value – 2000 steps/rev
Frequency on the Step input (max) - 100KHz
Idle current reduction time
1 sec
Idle current selection
0% to 70% of the maximum operating current
Default Value – 20%

SMD-23 Integrated Stepper Drive & Motor
20 Gear Drive, Plymouth Industrial Park, Terryville, CT 06786 page: 5
Tel: (860) 585-1254 Fax: (860) 584-1973 Web: www.amci.com
ADV ANC ED
MIC RO CON T RO L S INC.
SMD23 Motor and Drive Specifications (continued)
Digital Inputs
Three opto-isolated differential inputs:
Step – Velocity/position command
Direction – Direction Control
Disable – Disables motion and disables current to motor
Type of input
5V TTL logic
Input Current
15mA max
Input Connector
AMCI Part # MS-8P, provided (Phoenix part # MC 1.5/8-ST3.81)
8 screw terminal type – 16 AWG max.
Programming Communications
Interface – RS232
Programming Interface – AMCI SPI Interface software, Windows 2000/XP supported
Interface Cable – AMCI CSMD-5 5 ft serial cable (optional)
Notes on Temperature Specifications
The maximum temperature of the SMD motor must not exceed 100
o
C(212
o
F) and maximum
temperature of the SMD drive heat sink must not exceed 85
o
C(185
o
F). If these temperatures
are exceeded the SMD thermal protection circuit will shut down the drive.
To prevent overheating a few factors must be considered:
• Operating motor current - configure just as much current as needed to provide the
torque for the specific application.
• Idle current: This is the amount of current that the drive provides to the motor when
motion is not occurring. To maximize motor efficiency and motor cooling, set the idle
current to the minimum value necessary to provide the required holding torque.
• Supply voltage: In general the higher supply voltage leads to higher switching losses
and higher heat generation in the motor-drive system.
• Motor mounting: If possible, mount the motor in such a manner that the mounting
hardware acts as a heat sink.
• Heat Sink position: Mount the motor so that the heat sink fins are vertical. This will allow
for free air flow between the fins. Maintain spacing around the SMD of one inch.

SMD-23 Integrated Stepper Drive & Motor
20 Gear Drive, Plymouth Industrial Park, Terryville, CT 06786 page: 6
Tel: (860) 585-1254 Fax: (860) 584-1973 Web: www.amci.com
ADV ANC ED
MIC RO CON T RO L S INC.
SMD23 Torque Curves

SMD-23 Integrated Stepper Drive & Motor
20 Gear Drive, Plymouth Industrial Park, Terryville, CT 06786 page: 7
Tel: (860) 585-1254 Fax: (860) 584-1973 Web: www.amci.com
ADV ANC ED
MIC RO CON T RO L S INC.
INSTALLATION
The mounting flange functions as both a mounting mechanism and also a heatsink. Mount the SMD
to a thermally conductive surface that is as large as possible. Heat is conducted from the SMD to
the mounting fixture resulting in motor/drive cooling. For proper cooling, the SMD must be mounted
with the heatsink fins vertical. In extreme cases a cooling fan may be required.
SMD23 Outline Drawings
4: ∅
∅∅
∅0.18"
+ 0.02"
– 0.00"
0.228"
±0.004"
(5.79 ±0.10)
Section S – S (3X Scale)
∅
∅∅
∅0.2500"
+ 0.0000"
– 0.0005"
∅
∅∅
∅6.350 + 0.000
– 0.013
)(
2.20"
±0.02"
(55.9 ±0.5)
1.858"
±0.005"
(47.19 ±0.13)
1.72"
(43.7)
Max.
1.520"
±0.005"
(38.61 ± 0.13)
0.59"
±0.02"
(15.0 ± 0.5)
0.81"
±0.02"
(20.6 ±0.3)
0.20"
±0.01"
(5.1 ±0.3)
0.06"
±0.01"
(1.5 ±0.3)
A
∅
∅∅
∅0.2500"
+ 0.0000"
– 0.0005"
S
Length
±0.03"
(Length ±0.8)
1.30"
±0.02"
(33.0 ±0.5)
∅
∅∅
∅
1.5000"
± 0.0010"
Length
2.12" (53.8)
2.98" (75.7)
AMCI Motor
SMD23-130
SMD23-240
Indexer Input Connector (8 Pins)
Mates with AMCI #: MS-8P
Phoenix Contact #: MC1,5/8-ST-3,81 Pin 1 +Vdc
Pin 2 Vdc Common
Pin 3 – Disable
Pin 4 + Disable
Pin 5 – Step
Pin 6 + Step
Pin 7 – Direction
Pin 8 + Direction
1 2 3 4 5 6 7 8
+
V
IN
–
V
IN
–
D
IS
+
D
IS
–
S
TP
+
S
TP
–
D
IR
+
D
IR
0.43" Nominal
(10.9 Nominal)
REAR VIEW
2.20"
±0.02"
(55.9 ±0.5)
1.858"
±0.005"
(47.19 ±0.13)
4: ∅
∅∅
∅
4.6 + 0.5
– 0.0
)(
0.001"
(0.03)
∅ 0.003"
(∅0.08)
A
(∅
∅∅
∅
38.100" ± 0.025)
∅
∅∅
∅6.350 + 0.000
– 0.013
)(
S

SMD-23 Integrated Stepper Drive & Motor
20 Gear Drive, Plymouth Industrial Park, Terryville, CT 06786 page: 8
Tel: (860) 585-1254 Fax: (860) 584-1973 Web: www.amci.com
ADV ANC ED
MIC RO CON T RO L S INC.
SMD23 Electrical Installation
Power supply inputs are NOT reverse connection protected. Applying
reverse voltage will damage unit.
Logic inputs are rated for 5Vdc max. Exceeding 5vdc will damage the
unit unless the recommended limiting resistors are used.
Control Signal Wiring
Programmer Wiring – CSMD-5 cable
SMD Connector – AMCI part # MS-8P Serial Port Connector – DB-9
To SMD To PC Serial Port
1. DC Supply 24-75Vdc 1. N/C
2. DC Common Vdc com 2. RXD
3. DTR 3. TXD
4. RXD 4. DTR
5. RTS 5. GND
6. N/C 6. N/C
7. TXD 7. RTS
8. GND 8. N/C
9. N/C
Use a general purpose diode with a breakdown voltage greater than 30Vdc such as 1N4005
or 1N4148 to protect the SMD RTS input.
The eight pin connector of the SMD is used for programming and control. The SMD drive monitors
the TXD signal coming from the computer’s serial port for a specific sequence of data. When the
SMD receives this data, it enters programming mode. To exit programming mode you must cycle
power on the SMD and reconnect the motion control signals. The SMD automatically enters motion
mode when power is re-applied.
Pin 1 +Vdc
Pin 2 Vdc Common
Pin 3 – Disable
Pin 4 + Disable
Pin 5 – Step
Pin 6 + Step
Pin 7 – Direction
Pin 8 + Direction
1 2 3 4 5 6 7 8
+
V
IN
–
V
IN
–
D
IS
+
D
IS
–
S
TP
+
S
TP
–
D
IR
+
D
IR
0.43" Nominal
(10.9 Nominal)

SMD-23 Integrated Stepper Drive & Motor
20 Gear Drive, Plymouth Industrial Park, Terryville, CT 06786 page: 9
Tel: (860) 585-1254 Fax: (860) 584-1973 Web: www.amci.com
ADV ANC ED
MIC RO CON T RO L S INC.
Wiring the SMD Control Signals to a Single-Ended Input
The SMD is built with differential inputs for optimal noise immunity. However many stepper
control circuits use single-ended (sinking or sourcing) control signals. The following schematics
show the correct wiring when using the SMD with single-ended control signals.
V
D C
R
L I M I T
5 V o l t s
1 2 V o l t s
1 5 V o l t s
2 4 V o l t s
N o n e
2 . 0 K
W
2 . 0 K
W
3 . 9 K
W
S M D
Input
+ S T E P
O R
+ D I R E C T I O N
S T E P
O R
D I R E C T I O N
R
L I M
Indexer
O u t p u t
V
D C
+ 5 t o + 2 4 V
S M D
Input
+ S T E P
O R
+ D I R E C T I O N
S T E P
O R
D I R E C T I O N
R
L I M
V
D C
+ 5 t o + 2 4 V
O p e n C o l l e c t o r S o u r c i n g O u t p u t
O p e n C o l l e c t o r S i n k i n g O u t p u t
Indexer
O u t p u t
S h i e l d e d , T w i s t e d
P a i r C a b l e
S h i e l d e d , T w i s t e d
P a i r C a b l e
Note: SMDinput resistorvalue –316 ohm
Disable Input Wiring
The Disable input circuit is the same as step and direction inputs. Electrical connections,
instructions, and commentsarethe same, except that the input resistor value is 1K.
The Disable Input on the SMD will shut off motor current when active. The circuitry of the
Disable Input is identical to the Step and Direction Inputs.
The SMD does not accept directional pulses while the Disable Input is active.

SMD-23 Integrated Stepper Drive & Motor
20 Gear Drive, Plymouth Industrial Park, Terryville, CT 06786 page: 10
Tel: (860) 585-1254 Fax: (860) 584-1973 Web: www.amci.com
ADV ANC ED
MIC RO CON T RO L S INC.
Changing the SMD23 Configuration Settings
Equipment required for changing the drive settings:
• Power supply – 24 to 75VDC, 4Amps;
• Programming cable - AMCI CSMD-5, 5 ft serial cable(optional). It connects the drive to a
PC. The connections are described in this document. The drive circuit provides optical
isolation from the PC;
• PC running Windows 98/2000/XP;
• AMCI SPI Programming software, downloadable from the AMCI website (www.amci.com);
Procedure:
1. Install the AMCI SPI Programming software on the PC.
2. Connect the programming cable(AMCI part# CSMD-5, optional) to the SMD.
3. Connect the power supply to the same connector (follow the specified polarity).
4. Connect the D-Sub connector of the programming cable to the serial port of the PC.
5. Run the AMCI SPI programming software. The following window will appear on the
screen:

SMD-23 Integrated Stepper Drive & Motor
20 Gear Drive, Plymouth Industrial Park, Terryville, CT 06786 page: 11
Tel: (860) 585-1254 Fax: (860) 584-1973 Web: www.amci.com
ADV ANC ED
MIC RO CON T RO L S INC.
Changing the SMD23 Configuration Settings (continued)
Procedure: (continued)
6. Select the Port menu and choose the COM port that the cable is connected to:
7. Turn on the power supply to the drive.
8. Press the Connect button. For a few seconds the TX and the RX lights can change
their color to green to inform that the program is establishing the communication.
Once they settle to red, the communication is established. The current settings of the
drive will be displayed (RESOLUTION, IDLE and CURRENT), together with the
identification of the Drive. The motor will be disabled until the next power up.
For example:
9. If a change to a setting is required, the new setting is selected from the appropriate
field.
By pressing the Defaults button, the default settings will appear:
• RESOLUTION: 2000 steps/revolution
• IDLE: 20% (Motor Current when motor is idle)
• CURRENT: 80% (Operating Current)
The firmware
version
Status
display

SMD-23 Integrated Stepper Drive & Motor
20 Gear Drive, Plymouth Industrial Park, Terryville, CT 06786 page: 12
Tel: (860) 585-1254 Fax: (860) 584-1973 Web: www.amci.com
ADV ANC ED
MIC RO CON T RO L S INC.
Changing the SMD23 Configuration Settings (continued)
Procedure: (continued)
10. By pressing the Apply button, the new settings will be saved in the drive’s
nonvolatile memory. The process of saving and verifying the new settings will take
about 8 seconds. During this time a warning to wait is displayed in the status display
of the window. When the process ends, a message that the command is accepted is
displayed.
11. Pressing the Test On button starts the self test. The motor will move back and forth
quarter of a revolution with slow speed until the Test button is pressed again.
Pressing the Recall button (in the menu above) will display the SMD’s current settings in
the data windows.
ERROR MESSAGES:
•
Check if power is applied to the motor;
• Check the wire connection;
• Check if the correct COM port is
selected;

SMD-23 Integrated Stepper Drive & Motor
20 Gear Drive, Plymouth Industrial Park, Terryville, CT 06786 page: 13
Tel: (860) 585-1254 Fax: (860) 584-1973 Web: www.amci.com
ADV ANC ED
MIC RO CON T RO L S INC.
NOTES:

ADV ANC ED MIC RO CONTROLS INC.
ADV ANC ED MIC RO CONTROLS INC.ADV ANC ED MIC RO CONTROLS INC.
ADV ANC ED MIC RO CONTROLS INC.
20GEARDRIVE,
TERRYVILLE,CT06786 T:(860)585-1254 F:(860)584-1973
www.amci.com
This manual suits for next models
2
Table of contents
Other AMCI Control Unit manuals
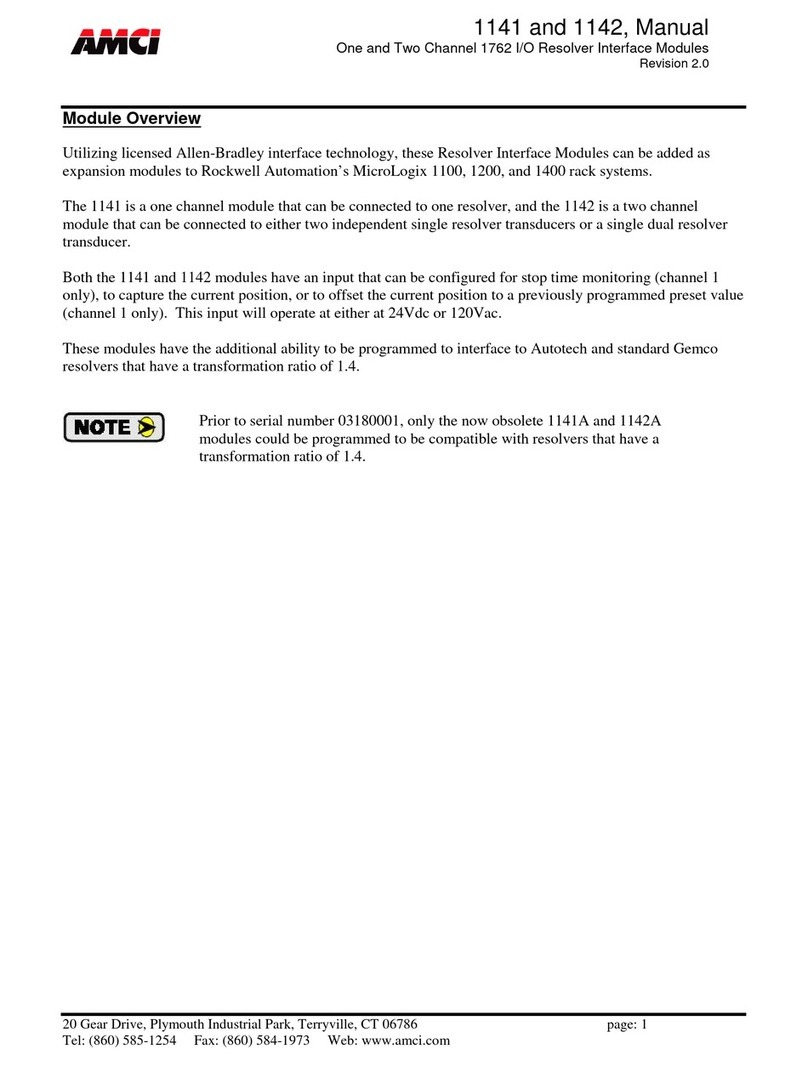
AMCI
AMCI 1141 User manual

AMCI
AMCI 7500 Series User manual
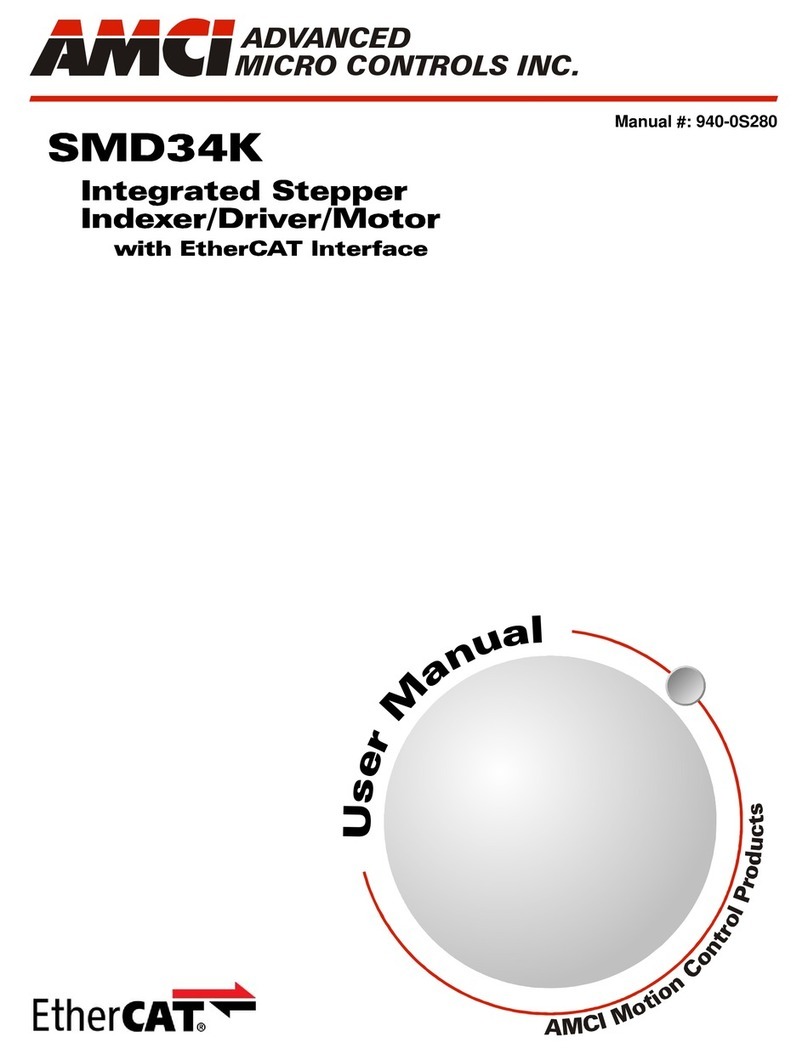
AMCI
AMCI SMD34K User manual
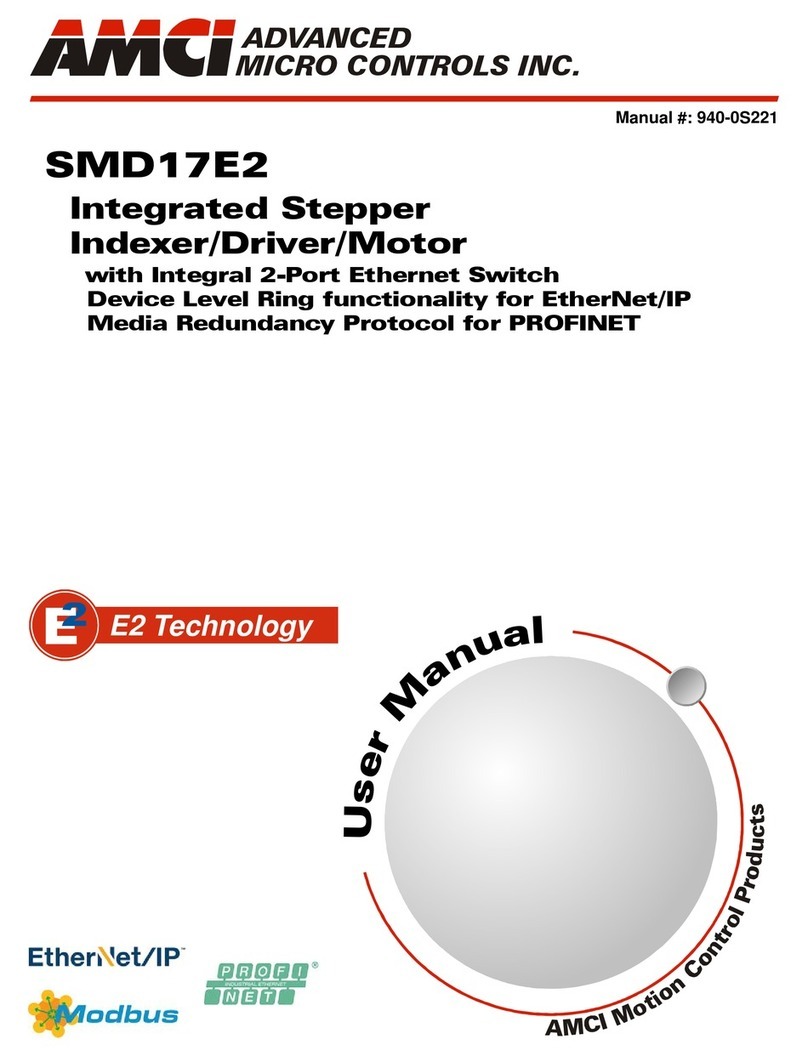
AMCI
AMCI SMD17E2 User manual
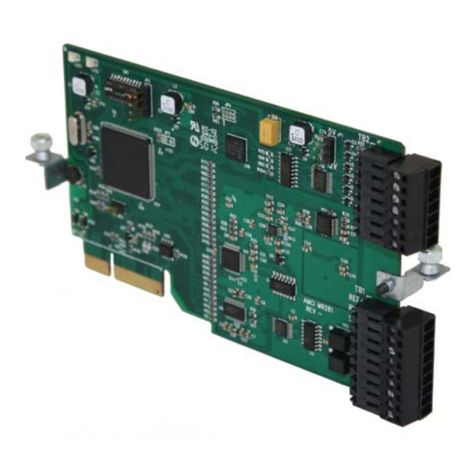
AMCI
AMCI PowerFlex 750 Series User manual
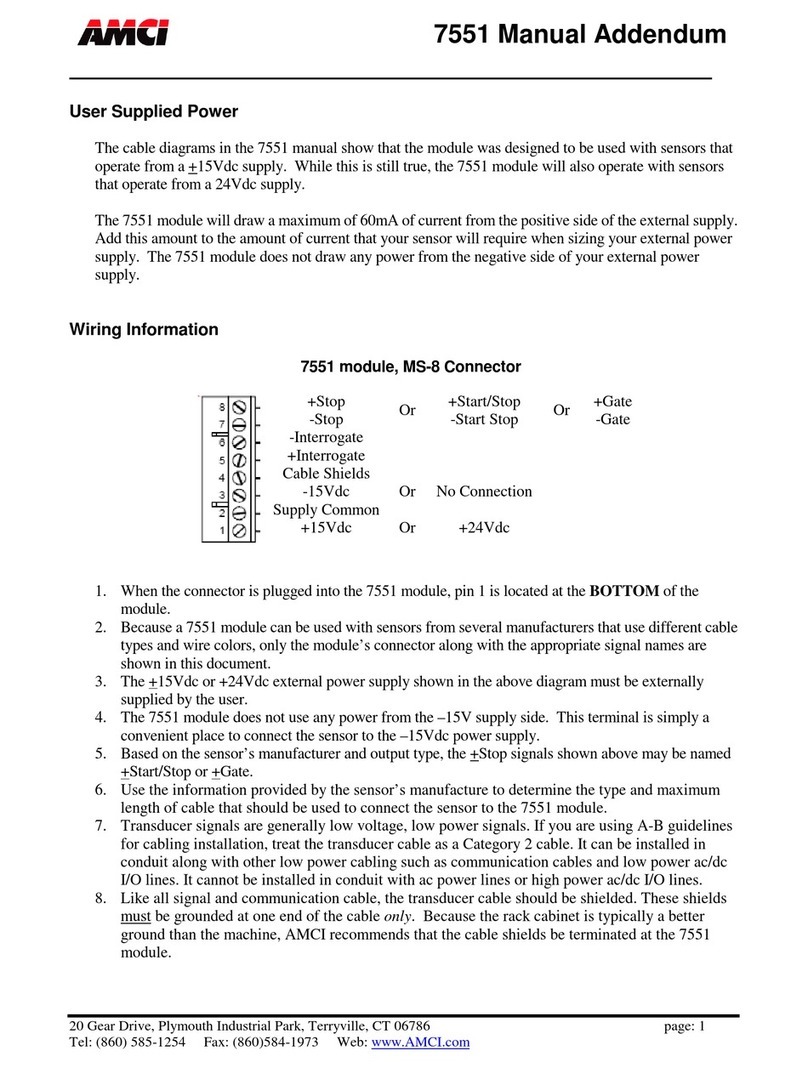
AMCI
AMCI 7551 Installation and operating instructions
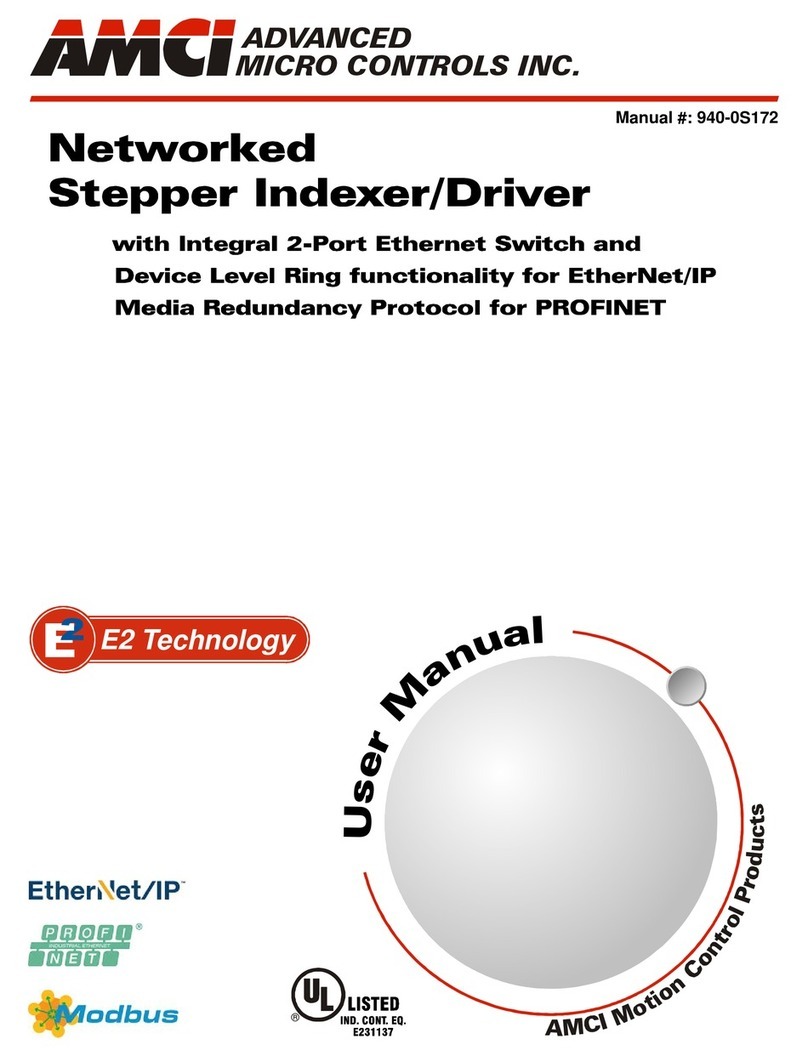
AMCI
AMCI SD17060E2 User manual
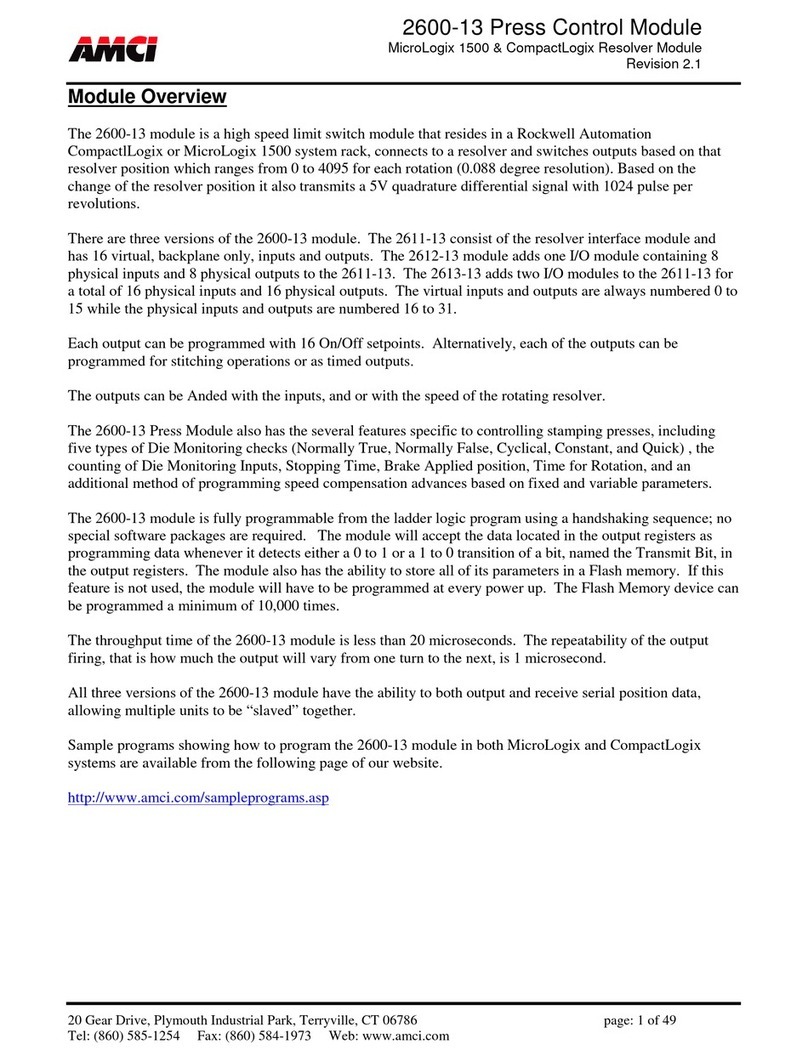
AMCI
AMCI 2600-13 User manual
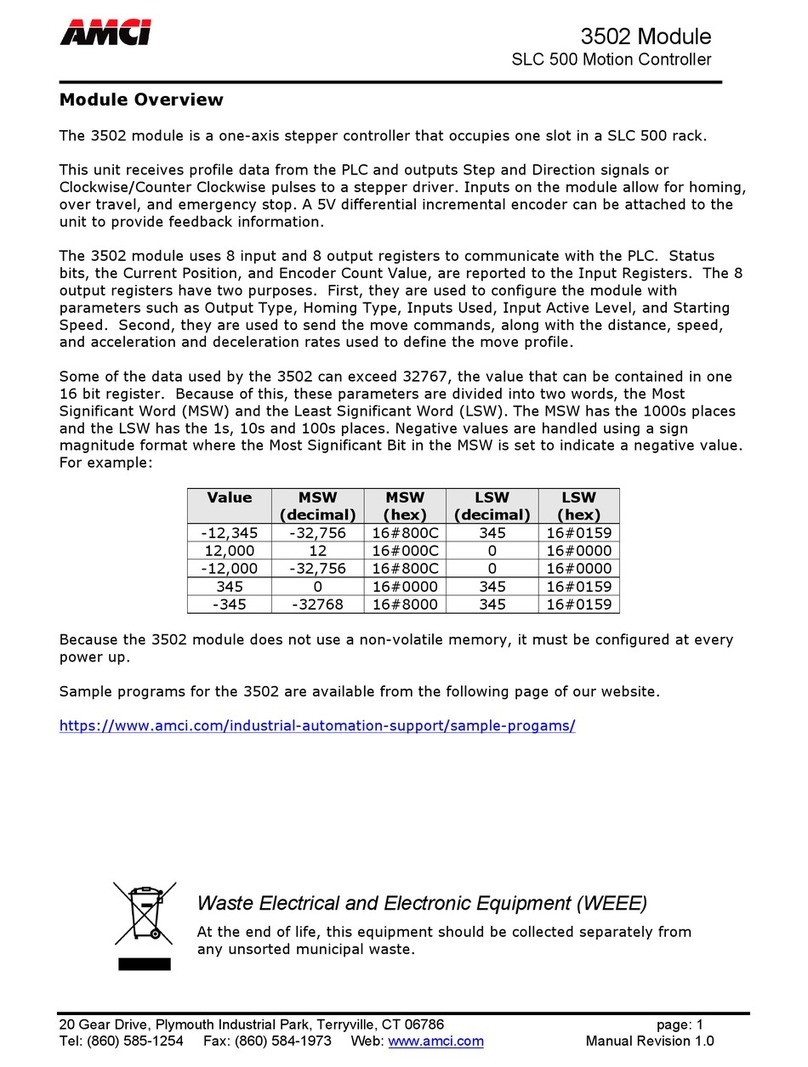
AMCI
AMCI 3502 User manual
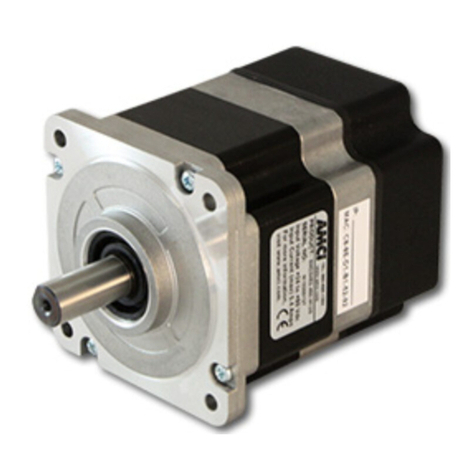
AMCI
AMCI SMD34E2 Instruction Manual
Popular Control Unit manuals by other brands
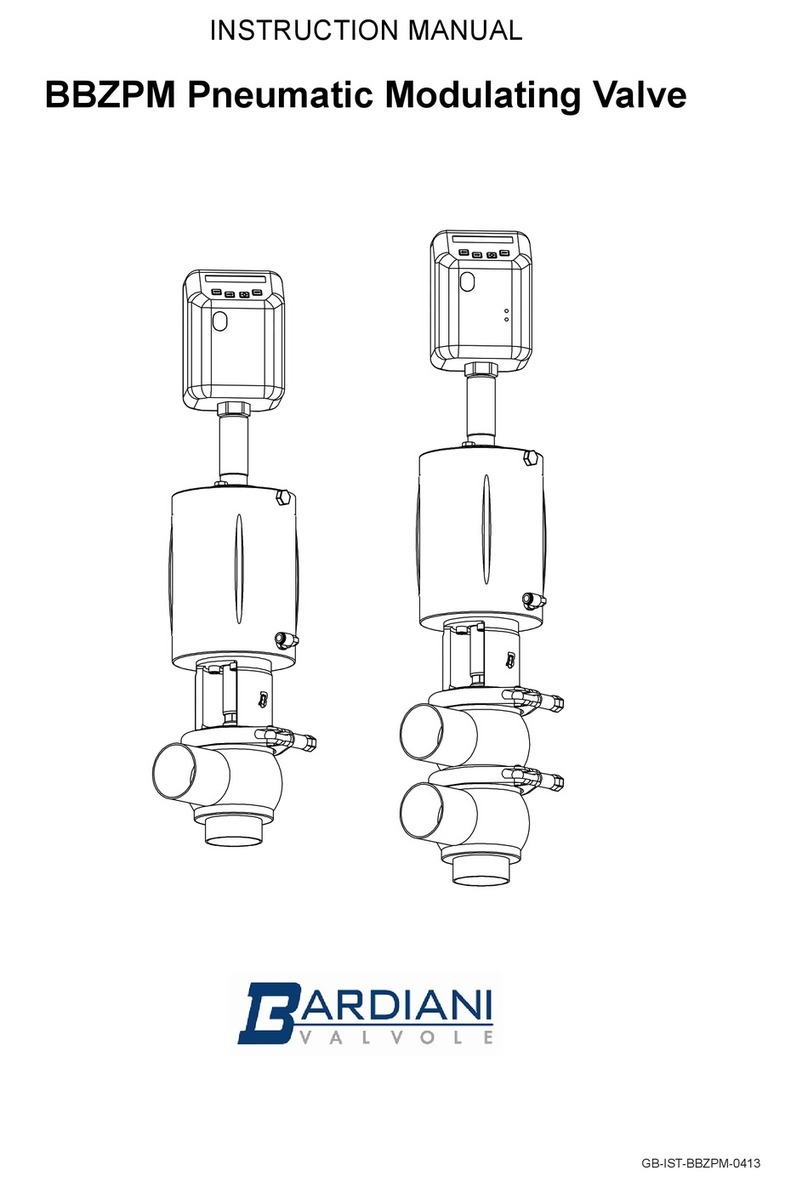
Bardiani Valvole
Bardiani Valvole BBZPM instruction manual
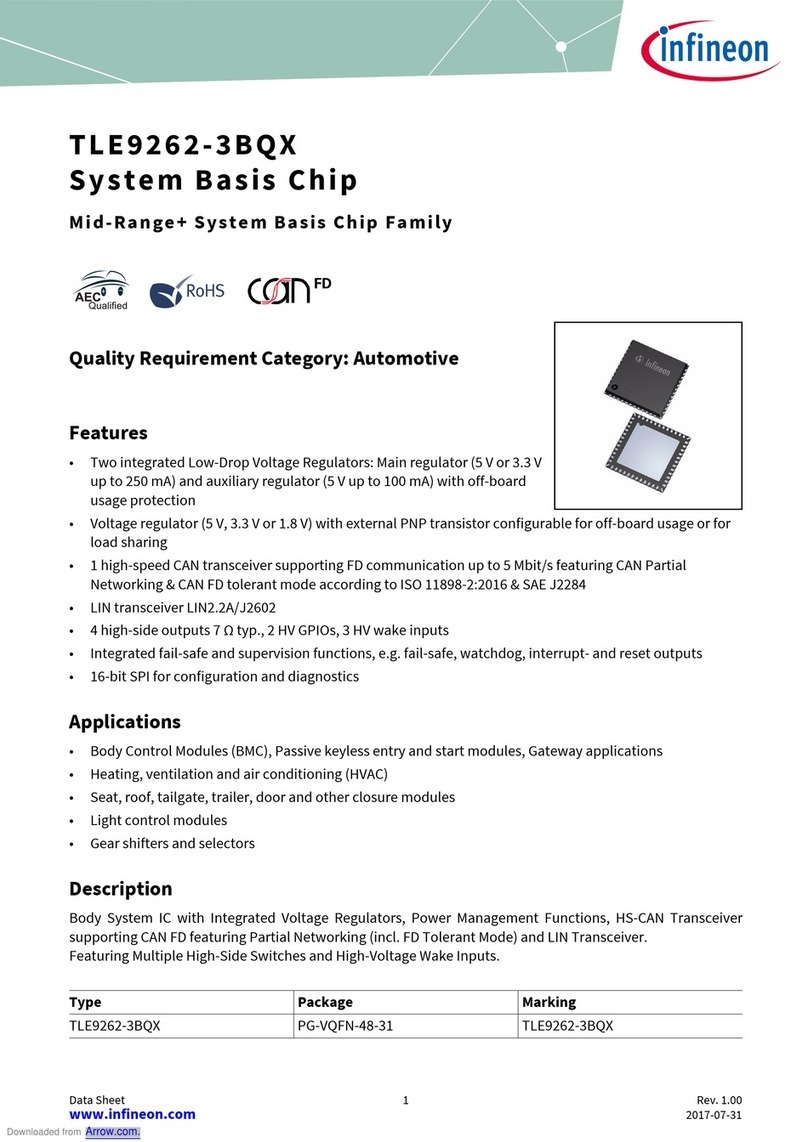
Infineon
Infineon TLE9262-3BQX manual
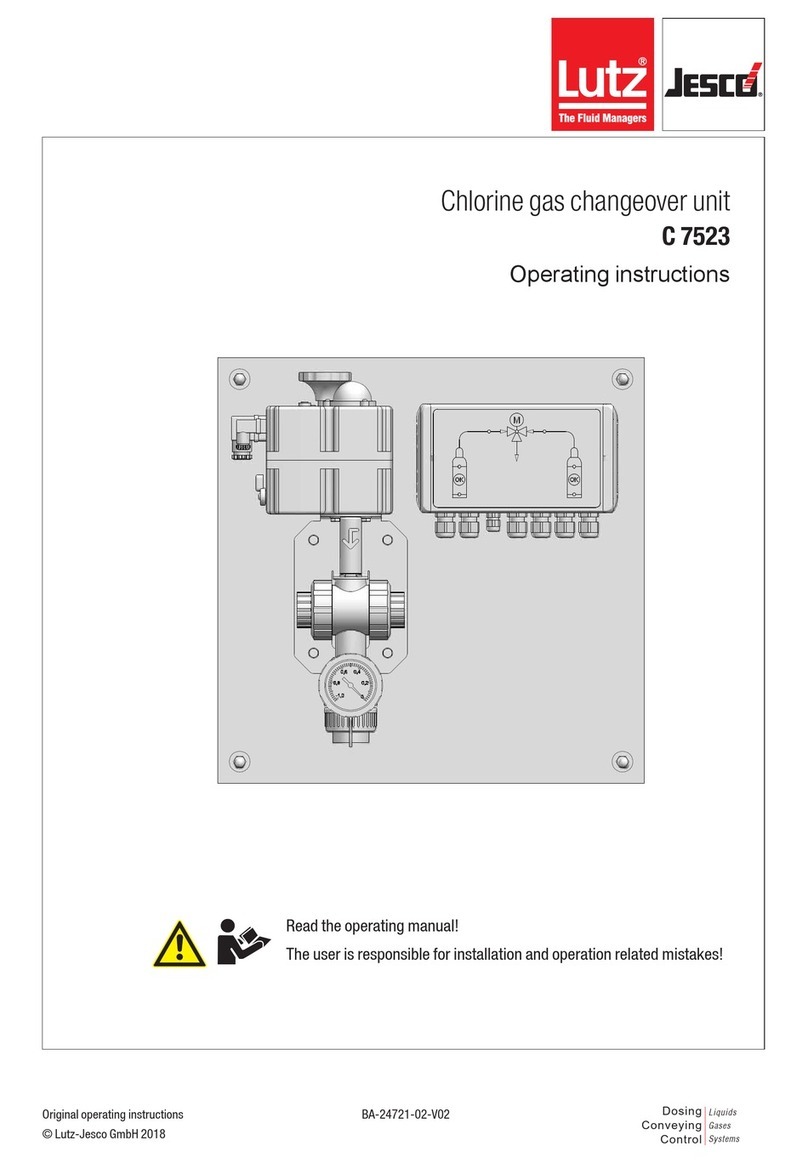
Lutz-Jesco
Lutz-Jesco C 7523 operating instructions

Ahlborn
Ahlborn ALMEMO 809 operating instructions
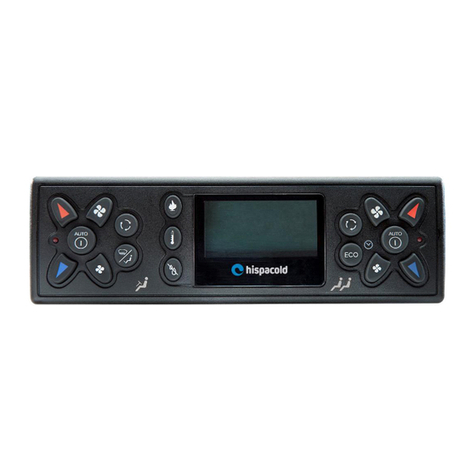
Hispacold
Hispacold Ecomaster Comfort MH-083 manual
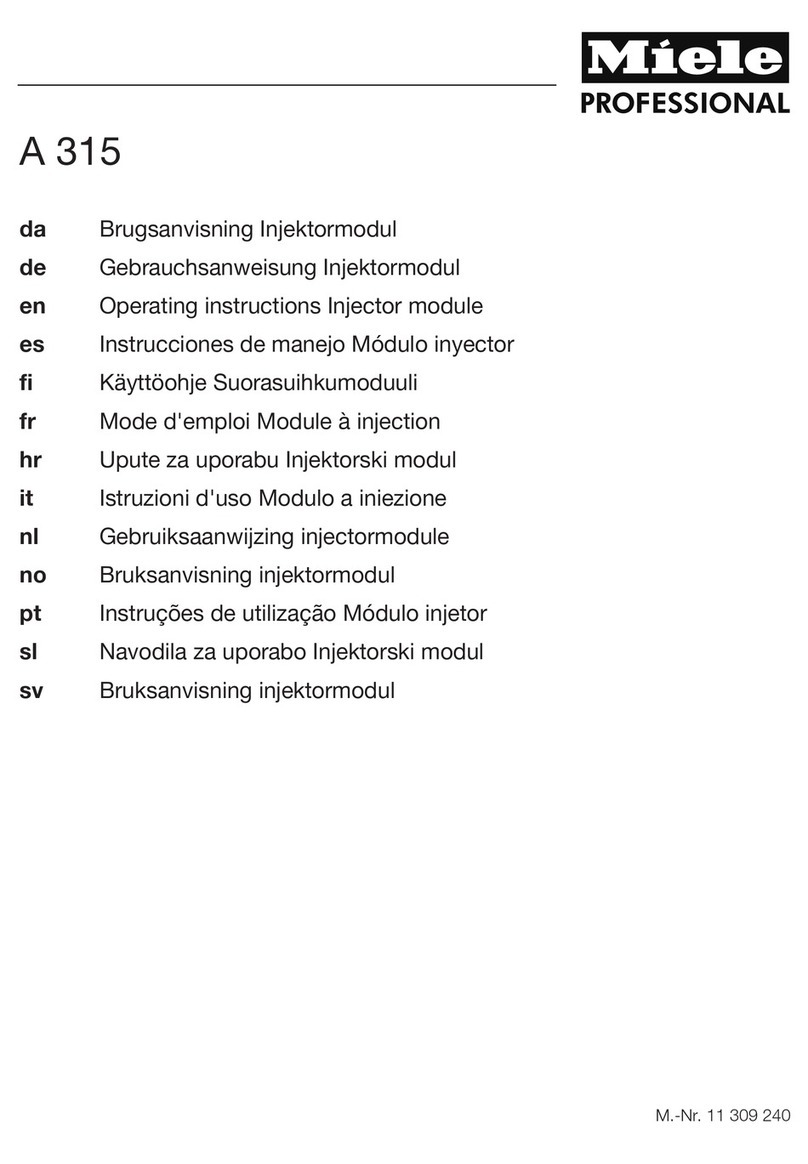
Miele professional
Miele professional A 315 operating instructions