Ametek EN633 Building instructions

Your Choice. Our Commitment.
SERVICE AND PARTS MANUAL
FOR
BLOWER MODEL
EN633 and EN833
DIRECT DRIVE REGENERATIVE
BLOWER
AMETEK Dynamic Fluid Solutions
100 East Erie St., Kent, Ohio 44240
Telephone: 330-673-3452 Fax: 330-677-3306
internet: www.ametekdfs.com

1 Revised – June 2016
W A R R A N T Y , I N S T A L L A T I O N , M A I N T E N A N C E A N D
T R O U B L E S H O O T I N G I N S T R U C T I O N S
AMETEK Dynamic Fluid Solutions
100 East Erie St., Kent, Ohio 44240
Telephone: 330-673-3452 Fax: 330-677-3306
email: dfs.information@ametek.com
internet: www.ametekdfs.com
1. AMETEK Rotron DR, EN and HiE regenerative direct drive blowers are guaranteed for one full
year from the date of installation (limited to 18 months from the date of shipment) to the original
purchaser only. Should the blower fail we will evaluate the failure If failure is determined to be
workmanship or material defect related, we will at our option repair or replace the blower.
2. AMETEK Rotron Minispiral, Revaflow, Multiflow, Nautilair, remote drive blowers, moisture
separators, packaged units, CP blowers, Nasty Gas™ models and special built (EO) products are
guaranteed for one full year from date of shipment for workmanship and material defect to the
original purchaser only. Should the blower fail, If failure is determined to be workmanship or
material defect related, we will at our option repair or replace the blower.
3. Parts Policy - AMETEK Rotron spare parts and accessories are guaranteed for three months from
date of shipment for workmanship and material defect to the original purchaser only. If failure is
determined to be workmanship or material defect related we will at our option repair or replace the
part.
Corrective Action - A written report will be provided indicating reason(s) for failure, with suggestions
for corrective action. Subsequent customer failures due to abuse, misuse, misapplication or repeat
offense will not be covered. AMETEK Rotron will then notify you of your options. Any failed unit that is
tampered with by attempting repair or diagnosis will void the warranty, unless authorized by the
factory.
Terms and Conditions - Our warranty covers repairs or replacement of regenerative blowers only,
and will not cover labor for installation, outbound and inbound shipping costs, accessories or other
items not considered integral blower parts. Charges may be incurred on products returned for reasons
other than failures covered by their appropriate warranty. Out-of-warranty product and in warranty
product returned for failures determined to be caused by abuse, misuse, or repeat offense will be
subject to an evaluation charge. Maximum liability will in no case exceed the value of the product
purchased. Damage resulting from mishandling during shipment is not covered by this warranty. It is
the responsibility of the purchaser to file claims with the carrier. Other terms and conditions of sale are
stated on the back of the order acknowledgement.
Installation Instructions for SL, DR, EN, CP, and HiE Series Blowers
1. Bolt It Down - Any blower must be secured against movement prior to starting or testing to
prevent injury or damage. The blower does not vibrate much more than a standard electric motor.
2. Filtration - All blowers should be filtered prior to starting. Care must be taken so that no foreign
material enters the blower. If foreign material does enter the blower, it could cause internal
damage or may exit at extremely high velocity.
Should excessive amounts of material pass through the blower, it is suggested that the cover(s)
and impeller(s) be removed periodically and cleaned to avoid impeller imbalance. Impeller

2 Revised – June 2016
imbalance greatly speeds bearing wear, thus reducing blower life. Disassembling the blower will
void warranty, so contact the factory for cleaning authorization.
3. Support the Piping - The blower flanges and nozzles are designed as connection points only and
are not designed to be support members.
Caution: Plastic piping should not be used on blowers larger than 1 HP that are operating near
their maximum pressure or suction point. Blower housing and nearby piping
temperatures can exceed 200ºF. Access by personnel to the blower or nearby piping
should be limited, guarded, or marked, to prevent danger of burns.
4. Wiring - Blowers must be wired and protected/fused in accordance with local and national
electrical codes. All blowers must be grounded to prevent electrical shock. Slo-Blo or time delay
fuses should be used to bypass the first second of start-up amperage.
5. Pressure/Suction Maximums - The maximum pressure and/or suction listed on the model label
should not be exceeded. This can be monitored by means of a pressure or suction gage (available
from Rotron), installed in the piping at the blower outlet or inlet. Also, if problems do arise, the
Rotron Field representative will need to know the operating pressure/suction to properly diagnose
the problem.
6. Excess Air - Bleed excess air off. DO NOT throttle to reduce flow. When bleeding off excess air,
the blower draws less power and runs cooler.
Note: Remote Drive (Motorless) Blowers - Properly designed and installed guards should be used
on all belts, pulleys, couplings, etc. Observe maximum remote drive speed allowable. Due to the
range of uses, drive guards are the responsibility of the customer or user. Belts should be
tensioned using belt gauge.
Maintenance Procedure
When properly piped, filtered, and applied, little or no routine maintenance is required. Keep
the filter clean. Also, all standard models in the DR, EN, CP, and HiE series have sealed
bearings that require no maintenance. Bearing should be changed after 15,000 to 20,000
hours, on average. Replacement bearing information is specified on the chart below.
Bearing
Part Number Size Seal Material Grease Heat Stabilized
510217
510218
510219
205
206
207 Polyacrylic
Nye Rheotemp 500
30% +/- 5% Fill Yes – 325 F
510449
516440
516648
203
202
307
Buna N Exxon Polyrex Grease NO
516840
516841
516842
516843
516844
516845
516846
516847
206
207
208
210
309
310
311
313
Buna N Exxon Polyrex Grease NO

3 Revised – June 2016
Troubleshooting
POSSIBLE CAUSE OUT OF WARRANTY REMEDY ***
IMPELLER DOES NOT
TURN
Humming Sound
1. * One phase of power line not connected
2. * One phase of stator winding open
3. Bearings defective
4. Impeller jammed by foreign material
5. Impeller jammed against housing or cover
6. ** Capacitor open
1. Connect
2. Rewind or buy new motor
3. Change bearings
4. Clean and add filter
5. Adjust
6. Change capacitor
No
Soun
d
1. * Two phases of power line not connected
2. * Two phases of stator winding open 1. Connect
2. Rewind or buy new motor
IMPELLER TURNS
Blown
Fuse
1. Insufficient fuse capacity
2. Short circuit 1. Use time delay fuse of proper
rating
2. Repair
Motor Overheated Or
Protector Trips
1. High or low voltage
2. * Operating in single phase condition
3. Bearings defective
4. Impeller rubbing against housing or cover
5. Impeller or air passage clogged by foreign material
6. Unit operating beyond performance range
7. Capacitor shorted
8. * One phase of stator winding short circuited
1. Check input voltage
2. Check connections
3. Check bearings
4. Adjust
5. Clean and add filter
6. Reduce system pressure/vacuum
7. Change capacitor
8. Rewind or buy new motor
Abnormal
Sound
1. Impeller rubbing against housing or cover
2. Impeller or air passages clogged by foreign
material
3. Bearings defective
1. Adjust
2. Clean and add filter
3. Change bearings
Performance
Below Standard
1. Leak in piping
2. Piping and air passages clogged
3. Impeller rotation reversed
4. Leak in blower
5. Low voltage
1. Tighten
2. Clean
3. Check wiring
4. Tighten cover, flange
5. Check input voltage
* 3 phase units
** 1 phase units
*** Disassembly and repair of new blowers or motors will void the Rotron warranty. Factory should be contacted
prior to any attempt to field repair an in-warranty unit.
Blower Disassembly:
WARNING: Attempting to repair or diagnose a blower may void Rotron’s warranty. It may also
be difficult to successfully disassemble and reassemble the unit.
1) Disconnect the power leads. CAUTION: Be sure the power is disconnected before doing any work
whatsoever on the unit.
2) Remove or separate piping and/or mufflers and filters from the unit.
3) Remove the cover bolts and then the cover. NOTE: Some units are equipped with seals. It is
mandatory that these seals be replaced once the unit has been opened.
4) Remove the impeller bolt and washers and then remove the impeller. NOTE: Never pry on the
edges of the impeller. Use a puller as necessary.
5) Carefully note the number and location of the shims. Remove and set them aside. NOTE: If the
disassembly was for inspection and cleaning the unit may now be reassembled by reversing the
above steps. If motor servicing or replacement and/or impeller replacement is required the same
shims may not be used. It will be necessary to re-shim the impeller according to the procedure
explained under assembly.

4 Revised – June 2016
6) Remove the housing bolts and remove the motor assembly (arbor/.housing on remote drive
models).
7) Arbor disassembly (Applicable on remote drive models only):
a) Slide the bearing retraining sleeve off the shaft at the blower end.
b) Remove the four (4) screws and the bearing retaining plate from the blower end.
c) Lift the shaft assembly far enough out of the arbor to allow removal of the blower end snap
ring.
d) Remove the shaft assembly from the arbor.
e) If necessary, remove the shaft dust seal from the pulley end of the arbor.
Muffler Material Replacement:
1) Remove the manifold cover bolts and them manifold cover.
2) The muffler material can now be removed and replaced if necessary. On blowers with fiberglass
acoustical wrap the tubular retaining screens with the fiberglass matting before sliding the muffler
pads over the screens.
3) Reassemble by reversing the procedure.
NOTE: On DR068 models with tubular mufflers it is necessary to remove the cover and
impeller accessing the muffler material from the housing cavity.
Blower Reassembly:
1) Place the assembled motor (assembled arbor assembly for remote drive models) against the rear
of the housing and fasten with the bolts and washer.
2) To ensure the impeller is centered within the housing cavity re-shim the impeller according to the
procedure outlined below.
3) If blower had a seal replace the seal with a new one.
4) Place the impeller onto the shaft making sure the shaft key is in place and fasten with the bolt,
washer and spacer as applicable. Torque the impeller bolt per the table below. Once fastened
carefully rotate the impeller to be sure it turns freely.
5) Replace the cover and fasten with bolts.
6) Reconnect the power leads to the motor per the motor nameplate.
Bolt Size Torque
Pound-Force-Foot
1/4-20 6.25 +/- 0.25
5/16-18 11.5 +/- 0.25
3/8-16 20.0 +/- 0.5
½-13 49.0 +/- 1
5/8 –11 90.0 +/- 2

5 Revised – June 2016
Impeller Shimming Procedure:
WARNING: This unit may be difficult to shim. Extreme care may be exercised.
Tools Needed:Machinist’s Parallel Bar
Vernier Caliper with depth measuring capability
Feeler gauges or depth gauge
Measure the Following:
Distance from the flange face to the housing (A)
Distance from the flange face to the motor shaft shoulder (B)
Impeller Thickness (C)
Measurements (A) and (B) are made by laying the parallel bar across the housing flange face and
measuring to the proper points. Each measurement should be made at three points, and the average
of the readings should be used.
Shim Thickness = B – (A+C)/2
After the impeller installation (step #4 above) the impeller/cover clearance can be checked with feeler
gauges, laying the parallel bar across the housing flange face. This clearance should nominally be
(A-C)/2.
C
B
A

6/1/16 Rev. F
AMETEK Dynamic Fluid Solutions
.
100 East Erie St., Kent, Ohio 44240
Telephone: 330-673-3452 Fax: 330-677-3306
email: dfs.information@ametek.com
internet: www.ametekdfs.com
IMPORTANT: Read before wiring this Explosion-proof Blower
This AMETEK Rotron Explosion-proof Regenerative Blower may be equipped with Pilot Duty
Thermal Overload (PDTO) or Automatic Thermal Overload (ATO) protection. When properly
wired to a motor starter, this protection limits the motor winding temperature rise per the
National Electric Code (NEC) article 500. Failure to properly wire this blower is an NEC
violation and could cause an explosion. AMETEK Rotron assumes no responsibilities for
damages incurred by negligent use of this product, and will not warranty a blower on which the
PDTO is not properly connected. Some blowers 1 HP and under do not require PDTO and
have built in ATO. Consult the factory if verification of wiring connections is required.
In all cases, follow the motor controller manufacturer’s instructions. The following schematic is
for conceptual understanding only, and may not apply to all motor/controller combinations.
The manufacturer’s wiring diagram found on the motor takes precedent over reference
diagrams supplied by AMETEK Rotron Technical Motor Division.
The schematic is shown for a
three phase motor. For a
single phase motor disregard
L3 and M3. Pushing the
START button completes the
auxiliary control circuit,
allowing current to flow
through the magnetic coil.
The contacts are
magnetically closed, starting
the motor and latching the
auxiliary circuit. The motor
will continue to run until the
STOP push button is
depressed, the motor
reaches the overload
temperature, or the current
sensing overloads trip out.
If you have any questions, contact AMETEK Rotron at 914-246-3401 for the location of your
area representative.
EXPLOSION
-
PROOF BLOWERS
A1
A2
L1
L2
L3
Push Start
Push Stop
Magnetic Coil
Current
Overloads
Contacts
Auxiliary
Power
J
M1
M2
M3
J
J – Pilot Duty Thermal Overload Protection wires
L – Power leads from circuit breaker box
M – Motor leads (refer to wiring diagram inside T’box or on motor nameplate)
Motor
Schematic

6/1/16 Rev. F
P
OLICY
R
EGARDING
I
NSTALLATION OF
AMETEK
R
OTRON
R
EGENERATIVE
B
LOWERS IN
H
AZARDOUS
L
OCATIONS
AMETEK Rotron will not knowingly specify, design or build any regenerative blower for
installation in a hazardous, explosive location without the proper NEMA motor enclosure.
AMETEK Rotron does not recognize sealed blowers as a substitute for explosion-proof
motors. Sealed units with standard TEFC motors should never be utilized where local, state,
and/or federal codes specify the use of explosion-proof equipment.
AMETEK Rotron has a complete line of regenerative blowers with explosion-proof motors.
Division 1 & 2, Class I, Group D; Class II, Groups F & G requirements are met with these
standard explosion-proof blowers.
AMETEK Rotron will not knowingly specify, design or build any regenerative blower for
installation in a hazardous, corrosive environment without the proper surface treatment and
sealing options.
AMETEK Rotron has a complete line of Chemical Processing and Nasty Gas™ regenerative
blowers with Chem-Tough™, stainless steel parts, and seals.
AMETEK Rotron offers general application guidance; however, suitability of the particular
blower selection is ultimately the responsibility of the purchaser, not the manufacturer of the
blower.
FS2 Rev. B 3/10/98

7
H. 1
∅
∅∅
∅
, 6 WIRE
115 VAC 230 VAC
1
1
LINE
3
LINE
2
5
3
2
5
4
LINE
4
LINE
8
8
INTERCHANGE LEADWIRES 5 & 8 to REVERSE ROTATION
I. 1
∅
∅∅
∅
, 7 WIRE
115 VAC 230 VAC
1
LINE 1 LINE
3
2
2 3
4 LINE
4
8 LINE
8
5
5
9
9
INTERCHANGE LEADWIRES 5 & 8 to REVERSE ROTATION
K. 3
∅
∅∅
∅
, 9 WIRE
230 VAC 460 VAC
LINE
1 LINE 1
LINE
7 2
LINE
3
2 LINE
8 4
7
3 LINE
9 5
8
4
5 6
6 9
INTERCHANGE ANY TWO LEAD LINES TO REVERSE ROTATION
M. 1
∅
∅∅
∅
230 VAC
SINGLE VOLTAGE
1
LINE
5
4
LINE
8
INTERCHANGE LEADWIRES 5 & 8 TO REVERSE ROTATION
WIRING DIAGRAMS, XP MOTORS
L. PILOT DUTY THERMAL OVERLOADS
J
J
HOOK J LEADS TO CONTROL CIRCUITRY
N. 3
∅
∅∅
∅
575 VAC
1
LINE
2
LINE
3
LINE
INTERCHAGE ANY TWO LEAD LINES TO REVERSE ROTATION

22
23
35
36
37
25
2
3
29
30
2526
24
1
34
27
31
37
5309
15
16
17
18
11
89
10
IN
2223
5
4
6
7
41
39
40
20
21
12
13
14
12
4.
14
3.
13
LIPSEAL
DETAIL
SCALE2/1
D
33
32
EN633ANDEN833ASSEMBLYDRAWING

en 633/833
Service and Parts Manual
Model:
EN633
EN633
EN833
EN833
Part No.:
081275
081698
081291
081712
Item
No.
Qty.
Req'd Description
1 1 Housing 552132 552132 552133 552133
2 1 Cover 552135 552135 552136 552136
3 1 Impeller 552126 552126 552127 552127
4 1 Key 552138 552138 552138 552138
5 1 Washer- Imp 155367 155367 155367 155367
6 1 Lockwasher - Imp 155384 155384 155384 155384
7 1 Screw - Imp 155359 155359 155359 155359
8 A/R Shim 155571 155571 155571 155571
9 A/R Shim 155572 155572 155572 155572
10 A/R Shim 155573 155573 155573 155573
11 A/R Shim 155574 155574 155574 155574
12 1 Sleeve - Imp Not used Not used Not used Not used
13 1 Felt washer -Imp 155575 155575 155575 155575
14 1 Lipseal 552140 552140 552140 552140
15 2 O-ring 552141 552141 552141 552141
16 9 Screw housing to cover 155356 155356 155356 155356
17 2 Blind flange 552143 552143 552143 552143
18 8 Screw Blind flange 155356 (12 pcs) 155356 155356 (12 pcs) 155356
19 Not used Not used Not used Not used Not used
20 4
Lockwasher housing to motor
155537 155537 155537 155537
21 4 Screw housing to motor 155576 155576 155576 155576
22 4 Bolt -foot 155577 155577 155577 155577
23 4Bolt - foot 155362 155362 155362 155362
24 1 Manifold 552145 552457 552145 552457
2 Not used 552461 Not used 552461
25 1 Foot (left) 552147 552147 552147 552147
26 1 Foot (right) 552148 552148 552148 552148
27 1 Motor SEE BELOW SEE BELOW SEE BELOW SEE BELOW
Parts Breakdown
Manifold/muf tower gasket
*As needed **Viewed looking at inlet/outlet ports 5/31/16 REV C

en 633/833
Service and Parts Manual
Model:
EN633
EN633
EN833
EN833
Part No.:
081275
081698
081291
081712
Item
No.
Qty.
Req'd Description
Parts Breakdown
28 Not used Not used Not used Not used Not used
29 2 Retainer (muffler) 552149 552459 552149 552459
2 Muffler foam Not used 552482 Not used 552482
30 2 Muffler foam 552150 (6 pcs) 552478 552150 (6 pcs) 552478
31 2 Muffler tower 552152 552458 552152 552458
32 2 Closing plate 552154 not used 552154 Not used
10 closing plate washers Not used 155537 Not used 155537
33 2 Flange 529834 511480 529834 511480
4 Flange washers Not used 155629 Not used 155629
34 2 O-ring 155376 not used 155376 not used
35 7 Screw muffler long 155579 (6 pcs) 155576 155579 (6 pcs) 155576
36 1 Screw Muffler - Short 155581 (4 pcs) 155419 155581 (4 pcs) 155419
37 8 Screw- Flange 155419 Not used 155419 Not used
38 Not used Not used Not used Not used Not used
39 3 Bolt - Cover hole 155354 155646 155354 155646
40 3 Nut - Cover hole 155380 155380 155380 155380
41 6 Washer - Cover hole 155537 155537 155537 155537
42 0 Rails Not used Not used Not used Not used
43 0 Screw -rails Not used Not used Not used Not used
44 0 washer - rails Not used Not used Not used Not used
45 0 Lockwasher rails Not used Not used Not used Not used
46 0 Nut- rail Not used Not used Not used Not used
47 0 Lockwasher - Cover hole Not used Not used Not used Not used
*As needed **Viewed looking at inlet/outlet ports 5/31/16 REV C

en 633/833
Service and Parts Manual
Model:
EN633
EN633
EN833
EN833
Part No.:
081275
081698
081291
081712
Item
No.
Qty.
Req'd Description
Parts Breakdown
Part # Motor Wiring Diagram Inline Filter
(included)
081275 552205 K + L 515255
081291 552205 K + L 515255
081698 552205 K + L 515255
081712 552205 K + L 515255
EN633BA72L
Model
EN833BA72L
EN633BA72ML
EN833BA72ML
*As needed **Viewed looking at inlet/outlet ports 5/31/16 REV C
This manual suits for next models
5
Table of contents
Other Ametek Blower manuals
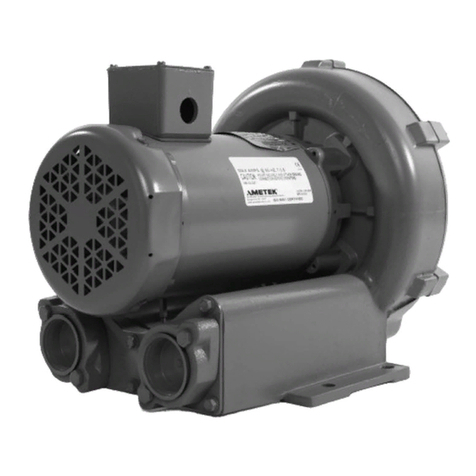
Ametek
Ametek CP101 Building instructions
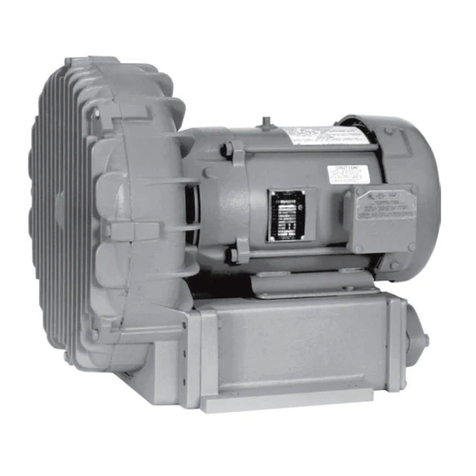
Ametek
Ametek EN707 Building instructions
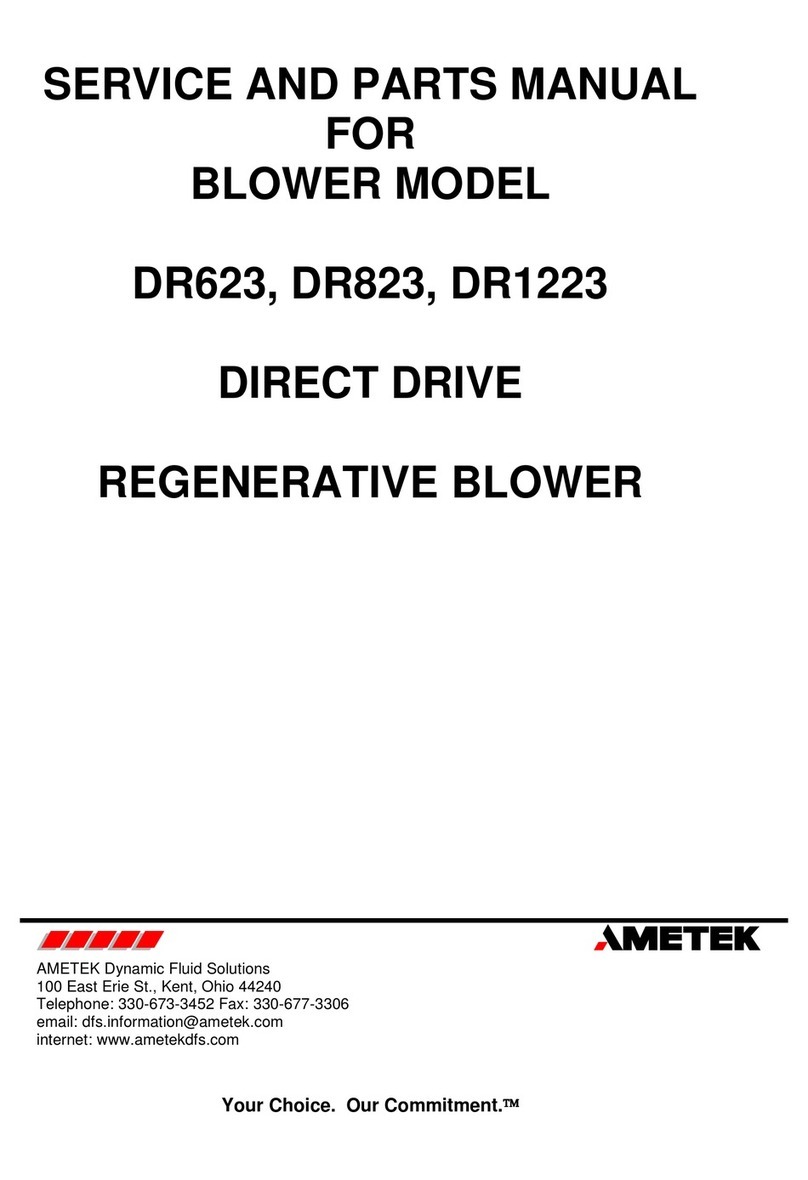
Ametek
Ametek DR623 User manual
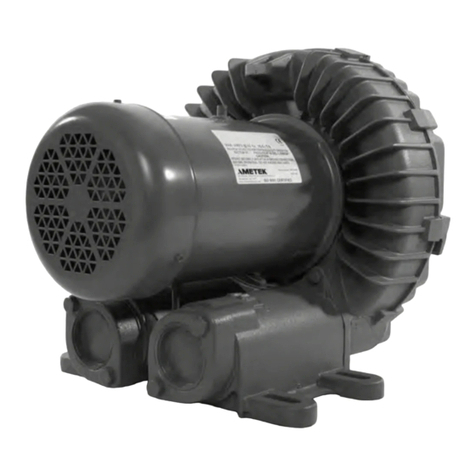
Ametek
Ametek DR707 Building instructions
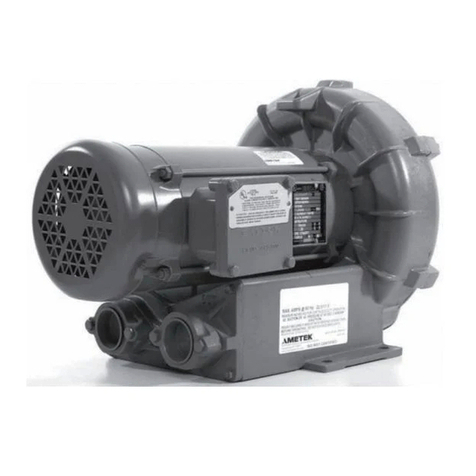
Ametek
Ametek EN101 Building instructions
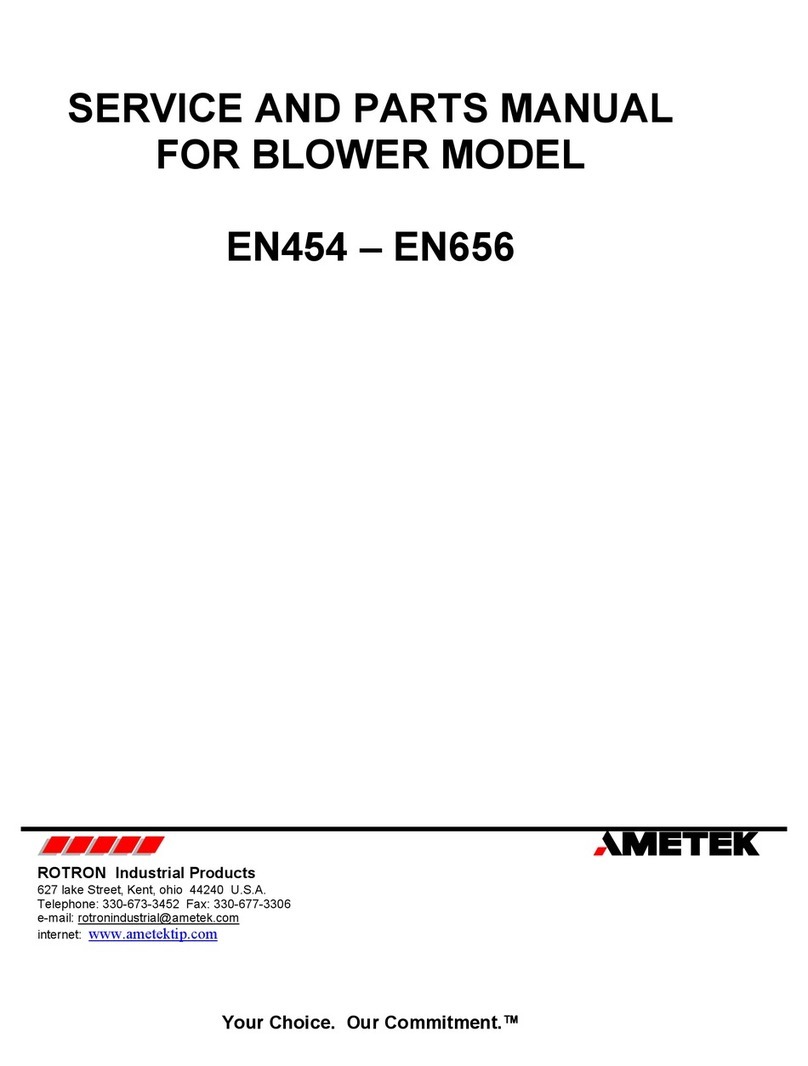
Ametek
Ametek EN454 User manual
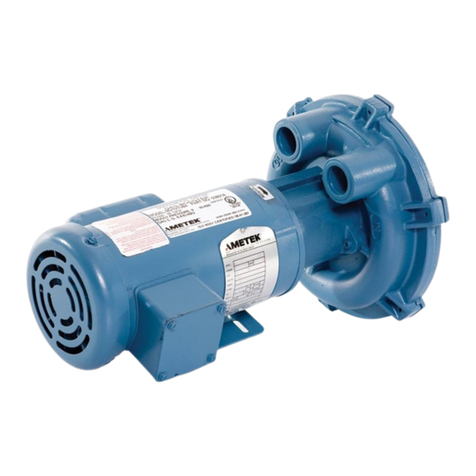
Ametek
Ametek MD101 Building instructions
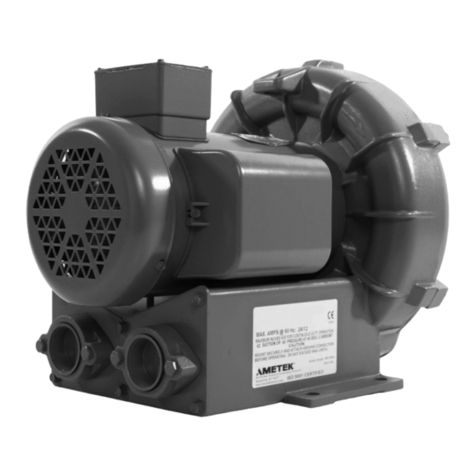
Ametek
Ametek CP454 Building instructions
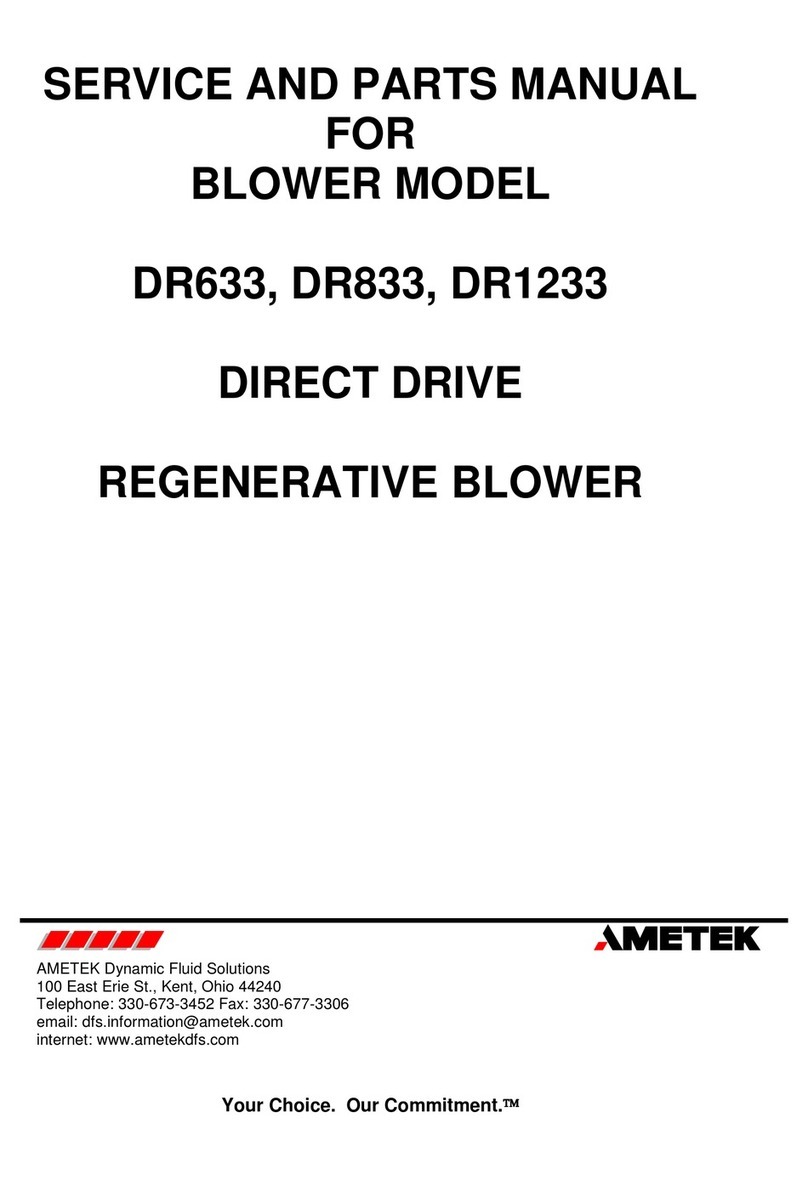
Ametek
Ametek DR633 Building instructions
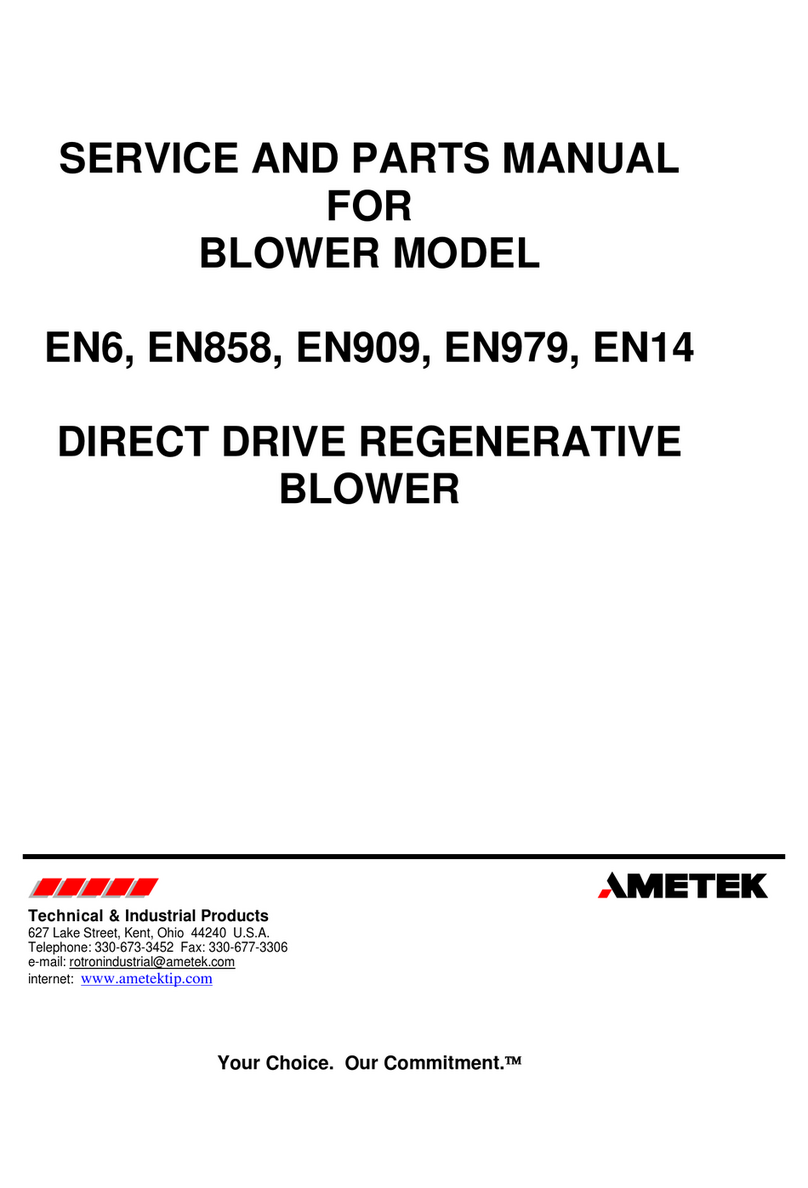
Ametek
Ametek EN858 Building instructions