AMSTRAD TS80 User manual

Stas
vo
canst
nan
BIBL
SSSR
oe
5
i
‘
TS80
/
TS88
REMOTE
CONTROL
TOWER
SYSTEM
SERVICE
MANUAL
fee
Price:
£3.50

CONTENTS
|
General
Routine
Maintenance
Trouble
Shooting
Guide
Safety
Test
Procedure
Alignment
Instructions
Cabinet
Drawing
and
Parts
List
Dial
Cord
Stringing
Cassette
Mechanism
and
Parts
List
Cassette
Deck
Alignment
and
Maintenance
Record
Deck
Drawing
Record
Deck
Parts
List
Chassis
Drawing
Chassis
Parts
List
Main
PCB
~TS80
PCB’s
2-5
TS88
PCB’s
2-5
TS88
Tape
11
PCB
10
TS80
VU
Meter
PCB
Electrical
Parts
List
IC
Pin
Voltages
TS80
Circuit
Diagram
TS88
Circuit
Diagram
.
OONN
DAA
—_
©
11
Middle
Spread
21
22
&
23
24
Inside
Back
Cover
Back
Cover
GENERAL
ROUTINE
MAINTENANCE
-
-AMPLIFIER
SECTION
Power
Output
Frequency
Response
Distortion
Graphic
Equaliser
Filters
Signal
to
noise
ratio
TUNER
SECTION
FM
Section
MW
Section
LW
Section
FM
Sensitivity
FM
Aerial
Input
CASSETTE
SECTION
Tape
Tape
Speed
Tracks
Wow
and
Flutter
Distortion
Frequency
Response
Noise
Reduction
Microphone
Sensitivity
TURNTABLE
Cartridge
Transmission
Speed
Control
REMOTE
CONTROL
UNIT
Method
of
Transmission
Volume
up/down
Balance
left/right
Bass
up/down
Treble
up/down
Batteries
DIMENSIONS
AND
WEIGHTS
Main
Unit
Weight
Speakers
Weight
Mains
Voltage
The
following
cleaning
and
maintenance
should
be
carried
out
on
a
regular
basis:
1)
Always
ensure
that
the
stylus
is
clean
and
properly
located
in
the
cartridge.
8
Watts
RMS
per
channel
into
4
ohms
32
watis
Total
Peak
Music
Power
30Hz
—
20KH2
1%
@
1KHz
Full
Power
0.2%
@
1KHz
half
Power
50Hz2
+12dB
150Hz
+.12dB
400Hz
+
12dB
KHz
+
12cB
2.5KHz
+12dB
5KHz
+
12dB
15KHz
+.12dB
Scratch
—10dB
@
12KHz
Rumble
—10d8
@
40Hz
Loudness
+10dB
@
100Hz
at
max.
vol.
+6dB
@
10KHz
—30dB
Better
than
55dB
86.5-—
109MHz
525
~—
1650KHz
140
—
280KHz
5uV
75ohms
Cassette
Type
4.75cm
per
second
2
Track
Stereo
0.15%
WRMS
1%
@
1KHz
80Hz
—6KHz
Standard
Tape
60Hz
—
8KHz
Chrome
Tape
60H2—
10KHz
Metal
Tape
—10dB
@
10KHz
0.5mV
—
6000nm
BSR
P267
SC12M
Bett
Drive
Electronic
infra
Red-Pulse
Position
Modulation
(PPM)
OdB
max
—80dB
min
—25dB
attenuation
per
channel
+.10dB
@
100Hz
+10dB
@
10KHz
2x
1.5V
Leak
Proof
Type:
Hitachi
Maxell
200.
Ever
Ready
R6PP
or
equivalent
86cm
(h)
x
42cm
(w)
x
37cm
(a)
29.0Kg
49cm
(h)
x
27cm
{w)
x
13cm
(d)
4kg
each
220—
240V
AC
50Hz
2)
Werétommend
regular
cleaning
of
the
heads
and
the
pinch
roller
of
the
cassette
deck
and
there
are
two
ways
of
cleaning
these
parts:
tl.
using
a
cotton
bud
and
methylated
spirits.
To
clean
the
relevant
paris,
you
should
press
the
‘eject’
button
so
that
the
door
is
open.
Ensure
that
the
power
is
switched
off,
then
press
the
‘play’
key,
which
will
raise
both
heads
and
the
pinch
roller
which
can
then
be
cleaned
with
the
cotten
bud
and
methylated
spirits.
ie
using
a
commercial
‘head
cleaning’
cassette
as
per
the
manufacturers
instructions.
When
carrying
out
this
operation,
please
be
careful
not
to
exert
tco
much
force
on
the
cassette
door
as
this
may
cause
damage.
Whilst
it
is
appreciated
that
using
a
head
cleaning
cassette
is
a
more
convenient
methad,
this
does
tend
to
have
a
some-
what
abrasive
action
and
may
increase
the
wear
of
the
heads.
The
cassette
parts
should
be
cleaned
after
approximately
25
hours
use.
However,
it
may
be
necessary
to
clean
the
cassette
mechanism
at
specific
instances
as
some
cassettes
themselves
have
a
deposit
of
oxide
dust
which
may
be
deposited
on
the
relevant
parts.
SAFETY
TEST
continued
electrical
safety.
APT
ARRANGE
PLEASE
NOTE:
When
any
work
is
compieted
on
this
unit,
correct
safety
tests
must
be
carried
out
to
ensure
PLEASE
NOTE:
All
parts
shown
with
the
part
number
prefix
‘S’
are
Safety
Items
and
must
be
replaced
with
similar
items
having
an
identical
safety
specification.
All
of
these
items
may
be
purchased
direct
from
AMSTRAD
COMSUMER
ELECTRONICS
PLC
A
A
RSA
SN
OA:
RM
EE
RET
SARTRE
TE,
PER
IPE
MR
Ee
Rte
TY
AU
AY
FER
aS
SE
ARTO
COR
TEERES
-

GENERAL
TROUBLE
SHOOTING
GUIDE
All
functions
on
unit
fail
to
operate.
Lack
of
power
supply.
Check
mains
plug/mains
fuse.
All
functions
fail
to
operate
except
Fuse
F501
blown.
Replace.
|
record
deck
mechanism.
{f
fuse
continues
to
blow,
check
for
Check
and
replace
as
necessary.
faulty
mains
transformer
or
meter
bulbs.
If
fuse
still
continues
to
blow.
Circuit
fault
somewhere
in
area
of
power
supply.
Check
and
replace
as
necessary.
Replace
as
necessary.
Check
Bridge
Rectifier
or
Power
IC.
General
circuit
fault.
Check
and
repair
as
necessary.
Re-locate.
Fuses
502
or
503
blown.
If
either
fuse
continues
to
blow.
If
fuse
stili
continues
to
blow.
All
functions
fail
to
operate
except
record
deck
mechanism
Connecting
plug
between
cassette
section
and
main
amplifier
not
locating
properly.
Aerial
not
connected
or
aerial
faulty.
VU
LEDs
not
working.
Check
aerial
and
replace
or
repair
as
necessary.
General
circuit
fault
in
FM
stage.
Check
and
repair
as
necessary.
Repair/replace
as
necessary.
General
FM
circuit
fault.
Check
and
repair
as
necessary.
Re-align
decoder
(see
alignment
instructions).
Replace.
FM
Tuner
section
selects
no
station
but
gives
loud
hiss.
If
there
is
no
fault
in
the
aerial.
Poor
aerial:
750hm
downlead
broken.
lf
aerial
and
leads
are
ok.
FM
Tuner
gives
some
sound
but
poor
quality.
FM
works,
but
stereo
light
in-
Decoder
incorrectly
aligned.
operative.
LED
faulty.
Check
decoder
IC
UPC1197C.
lf
UPC1197C
ok,
fault
is
probably
C203
(470pf
Poly).
incorrect
alignment.
If
alignment
correct.
Check
and
replace
as
necessary.
Check
and
replace
as
necessary.
Check
and
re-align
as
necessary.
Circuit
fault.
Repair
as
necessary.
N.B.
If
replacing
any
components
on
the
AM
section,
the
set
must
be
re-aligned.
Repair
as
necessary.
AM
radio
section
(MW/LW)
inoperative
or
very
weak.
Wire
disconnected
from
power
supply.
Motor
fault.
Belt
disconnected.
Stylus
damaged.
Stylus
not
located
correctly
in
cartridge.
Cartridge
faulty.
Replace.
Cartridge
faulty.
Replace.
Wiring
between
cartridge
and
amplifier
section
disconnected.
Belt
slipping
or
stretched.
Record
deck
fails
to
operate
mechanically.
Repair/replace
as
necessary.
Replace.
Re-locate.
Record
deck
operates
mechanically
but
gives
weak
or
distorted
sound
on
both
channels.
Record
Deck
operates
mechanically
but
gives
no
sound
on
either
or
one
channel.
Clean,
relocate
or
replace
as
necessary.
Record
deck
wow
or
flutter.
Check
and
replace
as
necessary.
Record
deck
speed
control
Speed
control
IC
faulty.
inoperative.

|
Symptoms
|
Fault
|
Cure
Connecting
plug
between
cassette
section
and
main
amplifier
not
locating.
Motor
faulty.
Drive
belt
not
tn
position.
Cassette
deck
mechanism
not
turning.
Cassette
jammed.
General
mechanical
fault
in
cassette
mechanism.
Cassette
speed
varies
(wow
and
flutter)
Drive
belt
in
incorrect
position.
Motor
faulty.
General:
mechanical
fault
in
cassette
mechanism.
Dirty
or
worn
pinch
roller
assembly.
Dirty
R/P
Head.
R/P
Head
picks
up
dust
deposit
almost
constantly.
R/P
Head
worn.
Poor
quality
of
recording
or
playback.
Pinon
connecting
plug
between
cassette
circuit
and
amplifier
circuit
not
locating
properly.
Generali
electronic
fault
on
Cassette
Faulty
erase
head.
Wire
disconnected
from
erase
head.
Faulty
oscillator
coil
(L303).
When
making
new
recordings,
old
recordings
not
erasing
properly.
Re-locate.
Check
and
replace
as
necessary.
Re-position
drive
belt.
Check
for
stretching
of
the
belt
and
replace
if
necessary.
Replace
cassette.
Check
and
repair
as
necessary
.
Clean
or
replace
as
necessary.
Re-position
drive
belt
or
replace
if
worn
or
stretched.
Check
and
replace
as
necessary.
Check
and
repair
as
necessary.
Clean
as
necessary.
Head
requires
demagnetisation.
Replace.
N.B.
Please
refer
to
cassette
re-alignment
instructions.
Re-locate
plug
correctly.
Check
and
repair
as
necessary.
Replace.
Repair
as
necessary.
Check
and
replace
as
necessary.
Faulty
leads
from
main
amplifier
and
cassette.
LEDs
faulty.
VU
LEDs
not
working
correctly.-
Check
and
repair
as
necessary.
Replace
and
re-adjust.
Severe
hum
on
one
or
both
channels
with
volume
at
minimum.
Output
IC
faulty.
Check
and
replace.
Hum
on
one
or
both
channels
at
General
circuit
fault.
high
volume
only.
Check
and
repair
as
necessary.
Check
speaker
and
speaker
leads
by
reversal.
Output
IC
faulty.
One
channel
not
working.
One
channel
not
working
and
blows
fuse(s)
502
or
503.
Volume
or
tone
controls
crackling
when
operated.
Output
LEDs
not
working
correctly.
Faulty
LEDs.
Fault
on
LED
PCB.
Headphone
socket
faulty.
Lead
disconnected
between
‘phone
socket
and
speaker
socket.
Speaker
socket
faulty.
Faulty
speaker.
Check
by
reversal
of
speakers.
If
reversal
of
speakers
demonstrates
fault
in
amplifier
section,
faulty
power
IC.
If
fault
condition
persists,
general
amplifier
fault.
Sound
through
headphones
but
not
speakers,
one
or
both
channels.
One
speaker
gives
distorted
sound.
Repair
or
replace
as
necessary.
|
Check
and
replace
as
necessary.
ee
Dirty
or
worn
potentiometers.
Spray
with
switchclean
or
replace
|
if
necessary.
Replace
as
necessary.
Check
and
repair
as
necessary.
Check
and
replace.
Check
and
repair
as
necessary.
Check
and
replace
as
necessary.
Repair
and
replace
as
necessary.
Check
and
replace.
Check
and
repair
as
necessary.

SAFETY
TEST
PROCEDURE
These
tests
should
be
applied
to
the
set
after
any
work
is
carried
out.
These
tests
must
be
done
to
the
set
before
the
six
screw
blanking
plates
are
fitted
to
the
cabinet.
REQUIRED
TEST
EQUIPMENT
1.
Flash
Test
Generator
capable
of
testing
at
2.2kV
AC.
2.
Megger
tester
rated
at
500V
DC.
3.
Instrument
capable
of
testing
resistance
down
to
0.10hm
at
10amps.
TEST
PROCEDURE
1,
Stand
on
bench
clear
of
all
metal
objects.
No
leads
should
be
connected
to
the
unit.
Ensure
that
the
on/off
switch
is
in
the
ON
position.
2.
Set
Flash
test
generator
to
2.2kV
AC.
Connect
1
pole
to
the
live
and
neutral
mains
lead
connected
together
and
flash
test
the
following
points:
a)
The
headphone
socket
ring.
b)
The
rings
of
both
microphone
sockets.
C)
The
record
deck
transit
screw.
d)
All
control
Knobs
and
buttons.
e)
The
underneath
of
the
front
panel,
below
the
RECORD
LEVEL
knob.
f)
The
back
panel.
a:
Connect
the
megger
tester
to
the
live
and
neutral
mains
lead
connected
together
and
megger
test
the
following
points:
a)
The
headphone
socket
ring.
b)
The
rings
of
both
microphone
sockets.
Cc)
The
record
deck
transit
screw.
d)
All
control
Knobs
and
buttons.
e)
The
underneath
of
the
front
panel,
below
the
RECORD
LEVEL
knob.
f)
The
back
panel.
4.
Check
that
the
earth
lead
continuity
is
below
0.5
ohms
at
10amps
between
the
mains
earth
lead
core
and
the
record
deck
transit
screw.
CAUTION:
High
voltages
may
be
present
on
a
faulty
set
and
care
should
be
taken
to
avoid
electric
shocks.
Certain
components
within
this
set
are
specific
safety
items
and
must
be
replaced
with
similar
items
which
comply
to
the
same
safety
specification.
All
such
parts
may
be
obtained
direct
from
AMSTRAD
CONSUMER
ELECRONICS
PLC

ALIGNMENT
INSTRUCTIONS
Equipment
required:
VTVM;
AM/FM
Band
SSG;
Loop
Antenna;
AM/FM
IF
Genoscope;
Non
Metalic
Trimming
Tool;
Dummy
Load
—
470K;
Oscilloscope.
AM
Alignment
Step
FUNCTION
SIGNAL
IN
SIGNAL
OUT
METHOD
REMARKS
1.
AM
IF
Alignment
at
Inject
signal
at
TP1
from
AM
IF
Connect
G’scope
at
TP4.
Adjust
IFT
103
and
IFT
104
to
get
1.
Ensure
set
switched
to
MW
band.
-
468KHz.
SG.
Select
468KHz
AS
IF.
max
signal
output
on
‘scope.
2.
Vol
control
max.
Tone
controlat
centre.
3.
Sig.
input
optimumto
avoid
AGC
action.
REPEAT
STEP
1
UNTIL
NO
FURTHER
IMPROVEMENT
IS
OBSERVED.
Connect
loop
antenna
to
the
Connect
VTVM
and
O’scope
|
Adjust
T101
to
obtain
max
sig.
output
ferrite
rod.
Inject
signal
from
across
speaker
output
via
on
the
meter
and
‘scope.
AM
SSG
at
525KHz.
470K
dummy
load.
Connect
loop
ant.
to
the
ferrite
Connect
VTVM
and
O’scope
rod.
[nject
sig
from
AM
SSG
at
across
speaker
output
via
1650KHz.
470K
dummy
load.
REPEAT
STEPS
3
&
4
UNTIL
NO
FURTHER
IMPROVEMENT
OBTAINED
Connect
loop
ant.
to
the
ferrite
Connect
VTVM
and
O'scope___—i[
Adjust
L104
to
obtain
max
sig.
output
rod
to
inject
sig
from
AM
SSG
at
|
across
speaker
output
via
on
the
meter
and
scope.
470K
dummy
load.
Connect
VTVM
and
O'’scope__|
Adjust
TC
103
to
obtain
max
sig
output
on
the
meter
&
scope.
600KHz.
Connect
loop
ant.
on
the
ferrite
rod
to
inject
sig
from
AM
SSG
at
|
across
speaker
output
via
1400KHz.
470K
dummy
load.
REPEAT
STEPS
6
&
7
UNTIL
NO
FURTHER
IMPROVEMENT
Connect
VTVM
and
O’scope__'|
Adjust
T102
and
L104
to
obtain
max
across
speaker
output
via
sig
output
on
the
meter
and
scope.
470K
dummy
load.
MW
Osc.
Alignment
at
1650KHz.
MW
aerial
alignment
at
600KHz.
7.
MW
aerial
alignment
at
1400KHz.
1.
Ensure
set
tuned
to
525KHz.
2.
Vol
control
max.
Tone
control
at
centfe.
3.
Sig.
input
optimumto
avoid
AGC
action.
1.
Ensure
set
tuned
to
1650KHz.
2.
Vol
control
max.
Tone
control
at
centre.
3.
Sig.
input
optimumto
avoid
AGC
action.
MW
Osc.
Alignment
at
525KHz.
Adjust
TC
105
to
obtain
max
sig
output
on
the
metez.
1.
Ensure
set
tuned
to
6O0KHz.
2.
Vol
control
max.
Tone
control
at
centre.
3.
Sig.
input
optimumto
avoid
AGC
action.
1.
Ensure
set
tuned
to
1400KHz.
2.
Vol
control
max.
Tone
control
at
centre.
3.
Sig.
input
optimumto
avoid
AGC
action.
1.
Ensure
set
switched
to
LW.
2.
Set
tuned
to
14QKHz
3.
Vol
contro!
max.
Tone
control
at
centre.
4.
Sig.
input
optimumto
avoid
AGC
action.
1.
Ensure
set
switched
to
LW.
2.
Vol
control
max.
Tone
control
at
centre.
3.
Sig.
input
optimumto
avoid
AGC
action.
MW
&
LW
alignment
now
complete.
Ensure
all
the
coils
and
transformers
are
sealed.
1.
Ensure
set
switched
to
FM.
2.
Ensure
stereo/mono
sw
switched
to
mono.
3.
Sig.
input
optimumto
avoid
AGC
action.
1.
Ensure
set
switched
to
FM.
2.
Ensure
stereo/mono
sw
switched
to
mono.
3.
Sig.
input
optimumto
avoid
AGC
action.
Connect
loop
ant
to
ferrite
rod.
Inject
140KHz
from
AM
SSG.
LW
Osc
and
aerial
alignment
at
140KHz.
Connect
loop
anit
to
ferrite
rod.
Connect
VIVM
and
O'scope
{Adjust
TC
106
and
TC
104
to
obtain
Inject
280KHz
from
AM
SSG.
across
speaker
output
via
max
sig
output
on
the
meter
and
470K
dummy
load.
scope.
REPEAT
STEPS
9
&
10
UNTIL
NO
FURTHER
IMPROVEMENT
LW
Osc
alignment
at
280KHz.
FM
ALIGNMENT
FM
IF
alignment
at
10.7
MHz.
Adjust
T101
to
obtain
max
output
on
the
scope
with
a
symmetrical
‘S’
curve
centered
at
10.7MHz.
Connect
O’scope
to
TP5.
Inject
10.7MHz
signal
from
FM
IF
SSG
at
TP2.
Adjust
T102
to
obtain
symmetrical
‘S’
curve.
Inject
10.7MHz
signa!
from
Connect
O’scope
to
TPS.
FM
IF
SSG
at
TP2.
FM
IF
alignment
at
10.7MHz.
REPEAT
STEPS
1
&
2
UNTIL
NO
FURTHER
IMPROVEMENT
Inject
86.5MHz
signal
from
Connect
scope
&
VTVM
Adjust
L103
to
obtain
max
output
on
FM
IF
SSG
at
J101.
across
dummy
load.
the
meter.
1.
Ensure
set
tuned
to
86.5MHz.
2.
Ensure
stereo/mono
sw
switched
to
mono.
3.
Sig.
input
optimum
to
avoid
AGC
action.
1.
Ensure
set
tuned
to
109.5MHz.
2.
Ensure
stereo/mono
sw
switched
to
mono.
3.
Sig.
input
optimum
to
avoid
AGC
action.
FM
Osc
alignment
at
86.5MHz.
Adjust
TC2
to
obtain
max
output
on
the
meter.
Connect
scope
&
VTVM
across
dummy
load.
FM
Osc
alignment
at
109.5MHz.
FM
Osc
tracking
at
90MHz.
FM
Osc
tracking
at
‘Inject
106MHz
signal
from
Connect
scope
&
VIVM
106MHz.
FM
IF
SSG
at
J101.
across
dummy
load.
Inject
109.5MHz
signal
from
FM
IF
SSG
at
J101.
REPEAT
STEPS
4
&
5
UNTIL
NO
FURTHER
IMPROVEMENT
Inject
SOMHz
signal
from
Connect
scope
&
VTVM
Adjust
L102
to
obtain
max
output
on
FM
IF
SSG
at
J101.
across
dummy
load.
the
meter.
Ensure
set
tuned
to
930MHz,
vol
max,
tone
control
to
centre
sig
input
optimum
to
avoid
AGC
action.
Ensure
set
tuned
to
106MHz,
vol
max,
tone
control
to
centre
sig
input
optimum
to
avoid
AGC
action.
REPEAT
STEPS
7
&
8
UNTIL
NO
FURTHER
IMPROVEMENT
We
aD
Set
tuned
to
a
strong
stereo
Monitor
stereo
beacon.
Adjust
VR201
to
get
the
st.
1.
Ensure
set
switched
to
FM.
station.
beacon
on.
2.
Ensure
stereo/mono
sw
to
stereo.
©
Adjust
TC1
to
obtain
max
output
on
the
meter.
FM
MXP
adjustment.
FM
alignment
now
complete.

2]
<
3
ONODARWODN
—
Description
Dust
Cover
B8308
BSR
P267
Turntable
|
S/83007
Hinge
Cover
Cabinet
Castor
Receptacle
Castor
Screw
Cover
Magnet
Glass
Door
Handle
Pack
Handle
Hinge
Grommet
Hinge
Screw
Hinge
Top
Hinge
Pack
Hinge
Bottom
Cartridge
BSR
or
Cartridge
TETRAD
Stylus
BSR
Stylus
TETRAD
B9109
B3041
B9003A
B9003B
B1043
B9005
B8310
BS006A
B9006B
B9110A
B9110B
B9110
B9110C
B9111
83002A
83007A
83002B
83007B
CABINET
DRAWING
&
PARTS
LIST
|
Le
A)
INIMUM
_
v
FREQUENCY
DIAL
CORD
STRINGING
ARGE
16/2
TURNS
MALL:
RN
cé
Kos
°Y
START:
Y4
TURNS

|
No.
OONOOaRND
—
Description
Motor
Assy
R.W.
Idler
Arm
Assy
Idier
Arm
Assy
Belt
Main
Flywheel
Leaf
Switch
Record
Safety
Lever
Take
Up
Spool
Assy
Rewind
Spool
Assy
Pinch
Roller
Spring
Pinch
Roller
Head
Erase
Head
R.P.B.
CASSETTE
MECHANISM
Part
No.
Description
809151
809152
809154
Idier
Spring
809155
Idler
F.F./R.W.
809156
Flywheel
Holder
809157
Pause
Lock
Lever
80S158
Spring
Locking
Plate
809159
Head
Base
809160
Auto
Stop
Arm
Assy
809161
Stopper,
Locking
Plate
809162
F.F.
Gear
700017
Locking
Plate
Poly
Washer
700016
809165
809166
809167
809168
809169
809170
809171
809172
809173
809174
809175

CASSETTE
ALIGNMENT
INSTRUCTIONS
Equipment
required:
Double
Beam
Oscilloscope;
Frequency
Counter;
RMS
Meter;
Non-Metallic
Trimming
Tool;
6.8KHz
Test
Tape;
1kHz
Test
Tape.
FUNCTION
SIGNAL
IN
SIGNAL
OUT
METHOD
REMARKS
1
Bias
frequency
Switch
SW
301
to
record.
Monitor
‘scope
or
freq.
Adjust
L303
to
give
625KHz.
Ensure
the
AFC
switch
is
off.
adjustment.
counter
from
junction
C328,
C331.
2
Bias
trap
adjustment.
Switch
SW
301
to
record.
RMS
Meter
across
Adjust
L301/302
to
get
the
same
Voltage
should
not
change
if
the
R301/302
in
turn.
voltage
at
R301
&
R302.
AFC
sw
is
on
or
off.
3
Bias
level
adjustment.
Switch
SW
301
to
record.
RMS
Meter
across
Adjust
VR
301/VR
302
to
Ensure
AFC
switchis
off.
R301/302
in
turn.
show
4.5mvV.
4
Head
azimuth
6.8KHz
Test
tape.
Double
beam
’scope
at
Ensure
set
switched
to
tape.
adjustment.
speaker
sockets.
5
Tape
speed
adjustment.
1KHz
Test
tape.
Frequency
counter
at
Ensure
set
switched
to
tape.
speaker
socket.
Adjust
azimuth
screw
for
max
amplitude
on
both
channels
ensuring
both
signals
in
phase.
Adjust
motor
with
non-metallic
trimming
tool
for
correct
frequency.
CASSETTE
DECK
MECHANISM
-
GENERAL
MAINTENANCE
Before
attempting
any
specific
fault-finding
on
the
cassette
mechanisms,
it
is
recommended
that
the
following
checks
and
maintenance
procedures
be
carried
out.
1.
R/P
HEAD
(Symbol
14)
Thoroughly
clean
the
head
and
examine
for
signs
of
wear;
replace
if
worn;
de-magnetise.
2.
PINCH-ROLLER
ASSEMBLY
(Symbol!
12)
Thoroughly
clean,
check
general
condition.
if
rubber
roller
is
in
any
way
distorted,
replace
the
assembly.
Check
the
tension
of
the
Pinch-Roller
Spring,
the
tension
should
be
40
to
60gm.
3.
MAIN
BELT
(Symbol
5)
Ensure
the
belt
is
correctly
located.
Check
that
it
is
not
stretched
or
worn
and
replace
if
necessary.
In
any
event,
remove
the
belt
and
clean
with
methylated
spirits.
4.
TAKE-UP
SPOOL
ASSEMBLY
(Symbol
9)
Check
the
tension
of
this
using
a
cassette
torque
meter.
The
correct
reading
should
be
40gm
per
cm.
A
reading
of
between
30
and
50gm
per
cm
may
be
regarded
as
within
tolerance.
Should
the
reading
fall
below
30gm
per
cm,
it
must
be
adjusted
to
give
the
correct
torque.
lf
it
cannot
be
adjusted
it
should
then
be
replaced.
5.
REWIND
IDLER
ASSEMBLY
(Symbol!
2)
Check
the
tension
with
the
cassette
torque
meter
using
the
rewind
function.
The
torque
should
be
100gm
per
cm
but
a
reading
of
between
80
and
110gm
per
cm
may
be
considered
within
tolerance.
If
the
torque
falls
below
80gm
per
cm,
it
should
be
adjusted
to
give
the
correct
reading.
If
it
will
not
adjust
sufficiently,
it
should
be
replaced.
6.
MOTOR
(Symbol!
1)
Ensure
that
the
motor
is
securely
mounted
and
that
the
motor
rubbers
are
in
good
condition.
7.
FLY-WHEEL
(Symbol
6)
Check
that
the
Fly-wheel
spindle
is
not
worn
or
bent
and
that
it
is
securely
seated
in
its
bearing.
8.
INTERNAL
MECHANISM
After
prolonged
use,
the
internal
mechanism
will
normally
contain
substantial
deposits
of
oxide
dust.
Ensure
that
these
are
thoroughly
cleaned.
There
are
no
places
on
either
mechanism
which
require
any
oil
or
grease
and
the
application
of
any
such
lubrication
is
likely
to
seriously
harm
the
internal
workings
of
the
mechanism.

10
Item
A102110
A117441
A117382
A106210
A114446
A114621
A104189
B117437
A114759
A102166
A106089
A106510
A102126
A102616
A116570
B116574
A106513
A102718
A114784
A114759
A106089
A106206
A106510
A117393
A106749
A111516
A104865
A105267
BSR
P267
RECORD
DECK
AND
PARTS
LIST
|
PartNo.
|
Description
Circlip
Turntable
Assembly
Motor
Mounting
Screw
(3
off)
Grommet
(3
off}
Drive
Belt
Thrust
Washer
Transit
Screw
Mainplate
Welding
&
Riveting
Assembly
Unit
Mounting
Spring
Retaining
Ctip
Spring
Cup
Screw
type
B
No.6
x
6.5
Rec.
Pan
Hd.
(2
off)
Solder
Tag
(2
off)
Phono
Socket
Drive
Sleeve
D.C.
Motor
Requirements
76mm
of
05
P.V.C.
Sleeving
Cable
Clamp
Screw
type
B.T.6-20
x
8
Rec.
Pan
Hd.
Unit
Mounting
Spring
(2
off)
Spring
Cup
(2
off)
Tag
Mounting
Strip
Screw
type
B
No.6
x
6.5
Rec.
Pan
Hd.
P.U.
Hinge
Retainer
4B.A.
Tag
Lockwasher
Molex
Plug
Insulating
Strip
Screw
type
B.T.4-24
x
8
Rec.
Pan
Hd.
(2
off}
A300126
A106512
A102166
A116564
A106089
A114759
A106512
B117369
A325010
A117464
A104189
A116565
A117461
A117376
A114155
A117378
B117375
B116562
A117439
A103373
117420
A105237
A105142
A103373
D117379
A117483
A117368
Description
On/Off
Speed
Control
Board
(B40)
Screw
type
B.T.4-24
x
16
Rec.
Pan
Hd.
Retaining
Clip
Detent
Spring
Spring
Cup
Spring
(Unit
Mounting)
Screw
type
B.T.4-24
x
16
Rec.
Pan
Hd.
L.E.D.
Mounting
Clip
L.E.D.
Requirements
Escutcheon
Printing
Transit
Screw
Knob
Spindle
Controt
Escutcheon
Printing
Pick-Up
Rest
Cue
Knob
Raising
Arm
Raising
Pad
Knob
P.U.
Lead
Assembly
Securing
Rubber
(2
off)
Pick-Up
Hinge
P.U.
Balance
Spring
Spring
Anchor
Securing
Rubber
Pick-Up
Arm
Screw
type
‘Plastite’
4-20
x
6.5
Rec.
Pan
Hd.
(Black)
Pivot
Pin

CARTRIDGE
OUTPUTS
R
BSR
-P267
RECORD
DECK
CIRCUIT
DIAGRAM
1V
—
ELECTRICAL
PARTS
LIST
BSR
267
Resistors
(¥4aW/+5%)
R1,5
4700hm
R2
1K20hm
R3
2700hm
R4
6800hm
|
R6
-
2K2ohm
R8
47Kohm
Resistors
(%2W/+5%)
R7
|
22ohm
Capacitors
C1
22mt/10V
Electrolytic
G2
2.2mfd/16V
Electrolytic
C3
100prf
Ceramic
Transistors
TR
BC212
BC337/25
806204
IC1
TDA1151
Information
on
Record
Deck
published
by
permission
of
BSR.
1

CHASSIS
DRAWING
=
y
|
filing
rr
A)
Y,
Y
ay
LYNG
ff
I=
INAS
YN
er
=
Ke
y/
m/e
/;
:
I
JS
@
VY
|
/
é
4
Lf
bs
3
as:
O\
ay
x
|
\
ve
ry
N
:
dS)
S
Y
13
Me
5

ING
CHASSIS
PARTS
LIST
TS80/88
po
8-80
Part
No.
1
Front
Panel
800001
800801
2
Graphic
Equaliser
Lens
800002
800002
3
Dial
Lens
800003
800003
4
Record
Level
Lens
800004
~
800004
5
Volume
Knob
800005 800005
6
Tun.
Record
Level
Knob
800006
800006
7
Select
Knob
800007 800007
|
8
Graphic
Tone
Knob
800008
800008
9
Record
Level
Knob
800809
10
Push
Button
Knob
(A)
800010
800010
11
Push
Button
Knob
(B)
800011
800011
12
Graphic
Inlay
800012
800812
13
Dial
Scale
800013
.
800013
14
VU
Meter
Inlay
800014
800014
15
Pointer
800015
800015
16
Carriage
Pointer
800016 800016
17
Slide
Controls
800017
800017
18
Record
Level
Pot
300133 300133
19
Volume
Switch
800019 800019
20
Push
Switch
800020
800020
21
Selector
Shaft
:
800021
800021
|
-
22
Selector
Switch
800022.
|
-.800022.
|.
23
Tuning
Shaft
800023
800023
24
Tuning
Flywheel
800024
800024
25
Tuning
Drum
800025
800025
26
Tuning
Spring
800026
800026
27
Tuning
Coupling
800027 800027
28
PVC
800028
800028
29
Ferrite
Rod
Bracket
800029 800029
30
~='|:-
Ferrite
Rod
800030
80003
31
Fuse
Holder
$/88020
$/88020
32
T315mA
F501
Fuse
$/88150
$/88150
33
T
2.5mA
F502
Fuse
$/800033
$/800033
34
T500mA
F503
Fuse
$/88005 $/88005
35
Tape
Select
Switch
800035
800835
36
PPM
Sensor
800036
|
800036
37
Cassette
Door
800037 800837
38
Cassette
Door
Lens
800038
800038
39
Eject
Spring
800039
800039
40
Cassette
Spring
809039
809039
41
Masking
Plate
809040
809040
42
Gear
809042
809042
43
Shaft
(Eject)
809043
809043
44
E
Ring
.
809044
809044
45
Bearing
Shaft
809045
809045
46
Spring
Eject
Shaft
809046
809046
47
Cassette
Keys
800047
800047
48
Play
Cassette
Key
800848
49
Counter
809049
809049
50
Counter
Belt
809050 809050
51
Complete
Cassette
Mechanism
(A)
809051
—
809051
52
Complete
Cassette
Mechanism
(B)
800052
53
Record
Play
Switch
800053
800053
54
ON/OFF
Switch
$/35028
$/35028
55
.
|
Headphone
Socket
800055
800055
56
Microphone
Socket
809056
809056
57
Cabinet
Securing
Bracket
|
800057
800057
58
Red
LED
400822
400822
59
Green
LED
400823
400823
60
Transformer
S/800060
$/800060
61
Mains
Lead
Restraint
$/250011
$/25001
1
62
Aerial
Socket
90042
90042
63
Speaker
Socket
250012
250012
64
Red
LED
800064 800064
65
Green
LED
800065
800065
Remote
Control
Module
800061
800061
Note:
All
parts
shown
with
either
the
symbol
AN
or
with
an
‘S’
prefix
on
the
part
numbers;
are
safety
critical
items
and
must
be
replaced
with
items
having
an
identical
safety
specification.
All
these
items
may
be
purchased
direct
from
AMSTRAD
CONSUMER
ELECTRONICS
PLC
13

¥
a
m
15
SAR
ANTENNA
L104
9824
EMM
MAIN
PCB
Bottom
View
HPP-153
oe
ame
ze
co
IN£Z0C02
ESO)
SES
2247
sR
LO
MBERIT
RI
BB
x20
BELEAAY
ep
160
eA
\-i0!
nS
a
ZENTENNA
Jack
.
—
-
~
mpm
a
ewe
-
‘
Sot
ue
StSmMA
PCE!
PyA318
|
EOTTOM
viEw
:
:
t
i
'
!
epemiianaiaas
'
+
90000660006
Pouver
Frans
TSO!
AC-3G0

MAIN
PCB
Top
View
PCBE
PCB?
i
153
of
©
is
fo.)
to
<>
+
\
\
F502
\
Ll!
Cee
Toler
PS
ve\
@S
9)
@js
Ta)
og
\
4
C154
|
RIT
e
E
14d
|
cs
|
“n
v
fe
t
a
_e.
©!
1
£124
mie
ens
Ss
0106
|
:
&
\;
Ritg
C126
CHE
Ci22
RIZE.
=r)
25
y
=O)
—
|
Ri?
f
:
t
'
TIQ?
°
QOS
ale
é
-OEX)-
RHE
PC!
708
Cod
tier
Los
tit
=]
~
Ne
2
i
§@)
S
A)
35
=<
ad
SU
“O88
Ono:
SY
a
5
2
Po
N
AY
mo
&
¥
ms
g
=
——?z
9
g
—CmmnD-™
2
s
&
io
~
Chior
meen
ne!
E
et
:
R105
Ono
Riis
xm
!
1
i
4
0
08
—
Som
C128
PT
mr
a4;
{
ait
S
OO
4;
3
.
——
ORI
Fave
a
8,
q
1
\
R48E
ASG
\
om
age
S
ae
5_Fa
oF
R497
&
|
ou
%
REA
8
rates:
pate
£
REG
fi
s
PTAC
See
fe
C865
>
cm!
R483
W515
sew)
8503
C47?
il
PCB
TUP-3188
TOP
vitW
17

TS80
PCB’s
2
-
5
Top
View
PCB
OP-1334
TOP
VIEW
|
R322
C316
ect
|
SWw30!
Sw302
se
ane
A506
i
é.
C318
RB
OO
Q302
f3i8
«(¢
)s
n338
G0
7
C322
e2
3
R312
=
L302
-
R310
R308
%
R34
C50!
=
«cD
ce
is
BLACK
rari
R302
poo
ae
i
i
324
6323
C335
R331
R305
;
R30!
xg
$
|
pile
C305
PCBS
«
§£
a
a
fils
OP-1335
TOP
VIEW
I
oe
CUT
RIF
=<
RINT
309
J}
(
ee
ne
C307
C)
130!
R340
C319
SW301
BLACK
—Omnoh-
A336
a
<—_—>
R325
C321
ELE
C330
“ae
[©
J302
MIC(R)
VRI01
|
ase!
VRI02
|
PCB4
OP-#332
TOP
VIEW
Bottom
View
ne
fr}
nei
HEAD
fo
i
\
oe
s.
v
vos"
Rall
de
:
rf,
£otfe
Ny
Pe
ee
co
ace
ea
id
OW.
Pedi
ggs
AL
AGOLIUM
Vt
ey
hes
Syi}
7
MP
ES
«
I)
ay)
Mi
MULUR
18
PCB2
OP-/333
TOP
VIEW
ie
a
AUITUM
VIF
W
A434
is
me.
Ay
pial
Ce
oP
ate
SelpoAt
ViEW

TS88
PC28’s
2-5
Top
View
AL
eee
'
32,
RIT
I
bel
eo
f-e
/00P
A315
2.9K
nd
63K
Sb
Si
%
sorrosd
view
eis.
Se
ei
sw30z
}
|
Suse
|
(Sw30l
|
4.7
C325
'
'
:7
'
ig
Qi
2.2K
‘aes
0382
0.0%
!
' '
oe
=
«R328
12K
4
KIC732
! !
Sw
if
7
Md
I
!
1
|
P
’
R338
ane
:
'
22K
ex
!
:
0;
10
Pe
otaea7
C34
ewe
35}
ea
aed
Gee
cosets
Iso
|
R312
100K
47
OP
eat
a
oe
a
(ts
eat
et
roe
ey
6
30°!
»
£308
100K
a
a
.
ISEIE
|
Ts
‘e
|
eee
=
i}
(7
[2i3}
Leap
=
I
§
Y
'
+
R324
2
ta8
2%
Rip
wEAD
AL
--—*4
Ga0P
|B
|
|
308.027}
78
Soe
”
z
‘e'
|
coq
ise
4
19-1
§
gages
|
a
170°!
T
ris
68
9c327
|
6335
t
optecagii
em
#70
|
ats
t
1136
R05
+,
1
207}
are
1S
68
er;
s
IE
\2a0i8
191
6305
47
37
ZAK,
o-
’
t
4
{
1
]
4
J
i
(
i]
<7
6307
0.027
9313.
oP
x
a
-———
|
+
r
+
{
rev
|
|
{90
rid
C313
4.7
C326
5
|
yaad
mcm)
|
15
2
'
+
{
t
iar
|
iG
|
fait,
8595
3
(Fuse).
c315
ott
Razy
21
@:
«'~!
R336.
180
(12W)
10
eens
sre
oe
eee:
OB
1
@
©
|
C32
5
‘es
!
R32.
¢
5
680P
12K
au
pa
ae
aces
E.HEAD
1
5301
MICIL)
|
|
I
i
|
@):
1
I
¥R301
@
©
1
100K
(
i
Leaf
L----------—
W.
Sw
Pcae
PCE2
H
if
Aer
OP-1332
villa
8.
BOTTOM
Vit
BOTTOM
VIEW
pce!
TUP
-3/8
@®
MI
MOTOR
PCB3
Bottom
View
OP-1334
PCBS
OP-1335
TOP
VIEW
a
PCS&2
OP-133.
TOP
#1
PC84
OP-1332
19
TOP
VIEW

TS88
TAPE
II
PCB
Top
View
a
FUE
INOS
Q306
se?
B
E
°
C348
3
e
C342
R356
C347
R359
ee
C)
Q30q
B
~E
g
SE
83%
C344
(|
j
C349
i
7
i
:
35/
is
R36)
C345
1®
RI6S
VR306
M2
Bottom
View
MOTOR
mE
AE
MC
NOR
A
NREIG
Ua
ya
RRC
ee
Ew
dvede
tae
Dimi
ebb
ne
EMAAR
Ghat
HOHE
HV
:
Se
Re
pote
wean
ar
engines
Metaranhetge
ty
H3
i
'
:
é
3
:
e
5
‘
{
iH
:
y
+3
‘
i
E
z
:
a
:
i
4
é
3
:
¢
2
:
$
:
wade
pee
20
NN
EVN
ANTENNAE
*
a
2
{fave
verrnrtiea
pans
ren
anrAaMiara
RMN
Ay
beRNONe!
he
Neila
he
eM
*
ty
ae
wy
Re
%
:
:
Hee
e%
%
g
%
:
rae)
wee
ra
aan
a
men
Cov
Oba
LESNAR
REC
2
a
tl
NES
ma
eH
so
Seat
mast
a!
Fase
one
wae
separ
HtENtO
a
wan
eieeRenen
MERE
RELAIS
ERMA
G
MMC
ENR
«yor
ge
ta
aK
COMES
yt
e
eat
:
2.
%

TS8O
VU
METER
PCB
Top
View
—OMmIQ—
4349
—OnmD—
#348
98765432
10303
D308
——
CIZP
©
0307
cast
;
e68—OMD-
it‘
ae
q
;
R347
—OOID—
<a
R346
—COOID—
b
>
<ecE
C338
C336
R350
—OnnD———
Bottom
View
iat
sis
ee
—
28
.
7
ee
S
ee
Sh
PRE
|
ee
CACRMISOOLVEM
ce
em
ahs
Mo
ow
6
|
(Fuse)
ek
ot
lyre
s{al
Ad
iat
PCBIO
21

22
ELECTRICAL
PARTS
LIST
Circuit
Reference
Electrolytic
Capacitors
0.1
uF/50V
C113
0.22uF/50V
C472,
473
1uF/50V
C140,
205,
210,
211,
301,
302,
403, 404,
408,
409,
467,
708,
712,713
800210
80021
1
20062
2.2UF/50V
C207,
336,
338,
484,
485,
709
|
809246
3.3uF/50V
C419,
420,
459,
460,
468
20146
4.7uF/50V
C132,
309,
310,
313,
314,
317,
20101
318,
454,
470,
471
C135,
201,
315,
316,
337,
353,
449,
486,
487,
488,
489
C465,
466
C147,
305,
306,
456,
457,
463,
476,
477,
701,
706
C141,
144,
148,
452,
453
C202,
326, 334,
339,
414,
478,
479,
511,
702
C409
C327,
407,
458
1000uF/25V
C482,
483,
510
2200uF/35V
C509
Mylar
Capacitors
0.0015uF
C151
0.0018uF
C303,
304, 433,
434
0.0022uF
C319,
320,
474,
475
0.0047uF
C333,
464,
461
0.0056uF
C331
0.0068uF
C212,
213,
323
-
325,
335,
431,
432, 445,
446
C417,
418
C120,
122,
138,
153,
332.
412,413
C443,
444
C145
C139,
146
C307,
308,
425,
426
C450,
451
C437,
438
C204
C423,
424
0.1uF
C480,
481,
707,
710,
711,
714
0.12uUF
C455,
462
Polystyrene
Capacitors
150pF
350pF
470pF
820pF
(125V)
Alumi
Solid
Capacitors
0.1uF/25V
C435,
436
0.15uF/25V
C429,
430
0.33uF/25V
C206,
427,
428
0.68uF/25V
C421,
422
10uUF/16V
20024
22uF/10V
47uF/10V
20025
20053
100uUF/16V
220uF/16V
20028
20029
220uUF/35V
470uF/16V
20055
20044
20118
20119
809231
809232
21002
21004
21015
21024
0.0082uF
0.01UF
21025
21006
|
0.01
5uF
0.01
8uF
0.022uF
0.02
7uF
0.033uF
0.039uUF
0.047uF
0.068uF
809234
809235
21007
21028
21012
21013
21008
809236
21029
21019
800235
800236
800212
22017
800213
809242
809243
800214
Value
|
Circuit
Reference
Extra
Capacitors
on
1S-88
Ceramic
Capacitors
Electrolytic
Capacitors
1uF/50V
C340,
341
10uF/16V
C345,
348
470uF/16V
C344
Mylar
Capacitors
21001
0.001uF
C351,
352
0.001
5uF
C342,
343
809231
0.01uF
C349,
350
21006
0.01
5uF
C323
—
325,
335, 443,
444
809234
iCs
IC101
AN7213
809201
iIC102
HA12413
809202
IC201
UPC1197C
800214
IC301
LA3160
901400
LB1403
UPC3246
TA7630P
STK4332
UPC1510C
IC302,
303, 407,
408
IC401
-
404,
702
IC405
iC406
IC701
Diodes
809207
800215
800216
800217
800218
D101
1TT410
Varicap
Diode
920117
D102,
103,
401
BA243A
800219
D104
OA9O
800220
D105
6ZA
6.8Y
Zener
809219
D501
—
508
IN4002
P.
Rectifier
15008
D509
G.
13Y
Zener
15005
D701
CZ.
049
Zener
800221
D702
KDS1555
800222
Transistors
Q101
KTC1923
BF595
Q102
-
104,
404
-
406,
701-703
Q105,
106
KTC380
BF595
Q301,
302,
401,
402)
KTC732
BC237
Q303
KTC2236
BD370
Q403
KTC
1627
BC237
KTG1173/25D313/
2N5496
Q704
-
707
KTC1015
BF594
Coils
Ant
Tranformers
L101,
102
0031SU
FM
Ant
Coil
0031SU
FM
RF
Coil
Q501
300616
L103
0035SU
FM
Osc
Coil
300617
L301,
302
RB-20299
Trap
Coil
300619
L303
RB20866
Bias
Osc
Coil
300620
|
|
T101
02192SU
MW
Osc
Coil
300621
T7102
02193SU
LW
Osc
Coil
800223
IFT
101
O565MM
FM
IFT
300623
IFT102
O566MM
FM
IFT
300624
IFT103
0461MM
AM
IFT
300625
lFT104
0462MM
AM
IFT
300626
Miscellaneous
PVC
1
CH
42
R311
PVC
800224
CF101,
102
10.7
MHz
Ceramic
Filter
993034
CF103
468KHz
Ceramic
Filter
800225
TC103,
105
8pF
Trimmer
800226
TC104,
106
16pF
Trimmer
800227
LPF201,
202
B3BN4103-32
Low
Pass
|
800228
Filter
CSA3.58MT
Ceramic
Osc
X701
800229
This manual suits for next models
1
Table of contents
Other AMSTRAD Desktop manuals
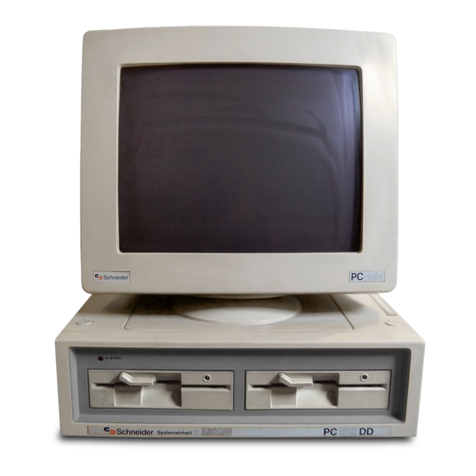
AMSTRAD
AMSTRAD PC1512 User manual
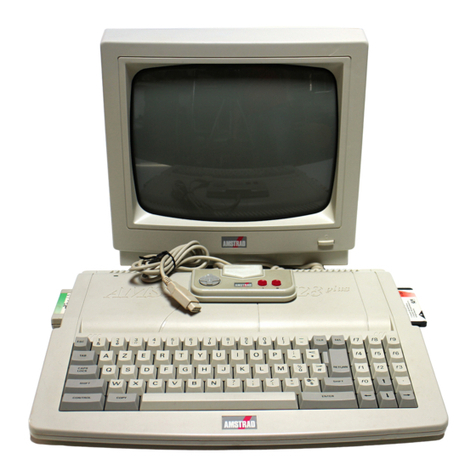
AMSTRAD
AMSTRAD 464 Plus User manual
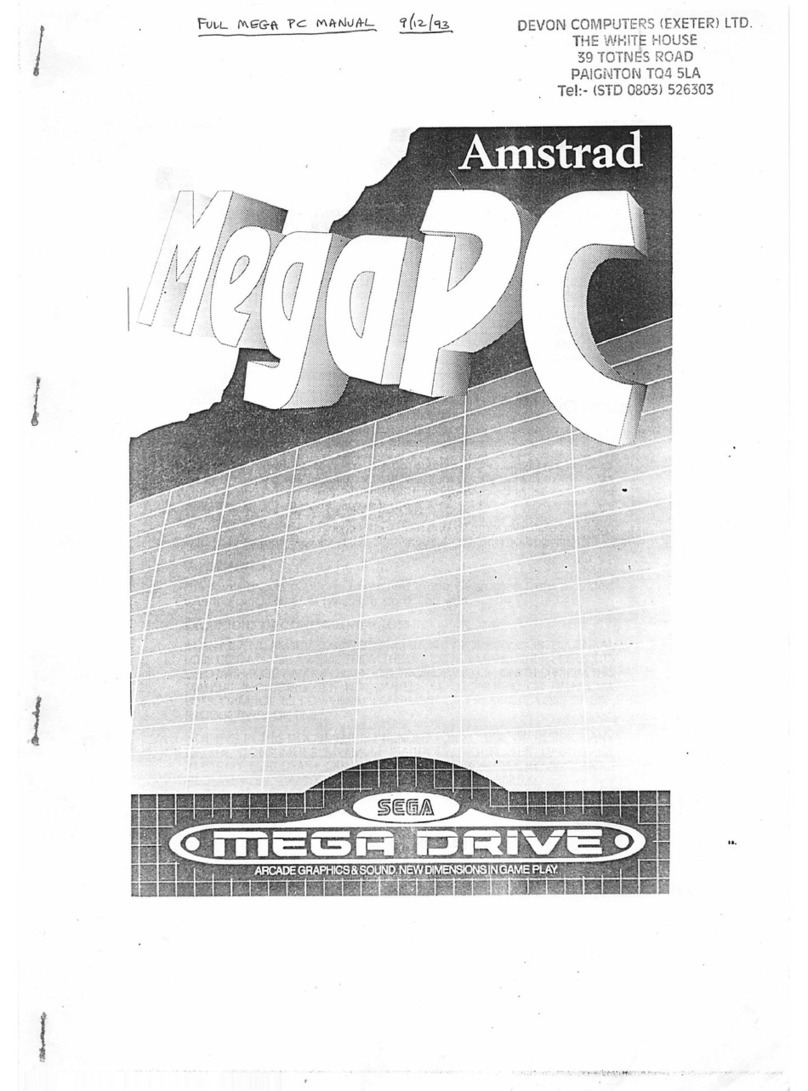
AMSTRAD
AMSTRAD MegaPC User manual

AMSTRAD
AMSTRAD PCW8256 User manual
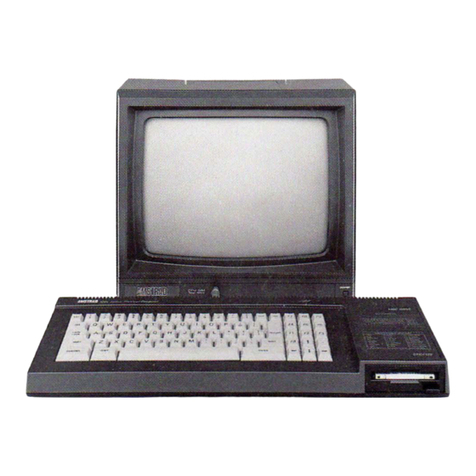
AMSTRAD
AMSTRAD CPC6128 User manual
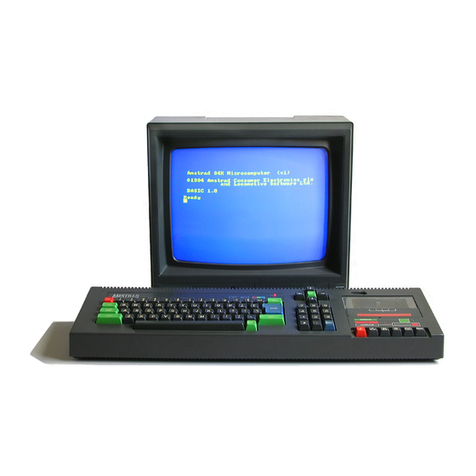
AMSTRAD
AMSTRAD CPC464 User manual
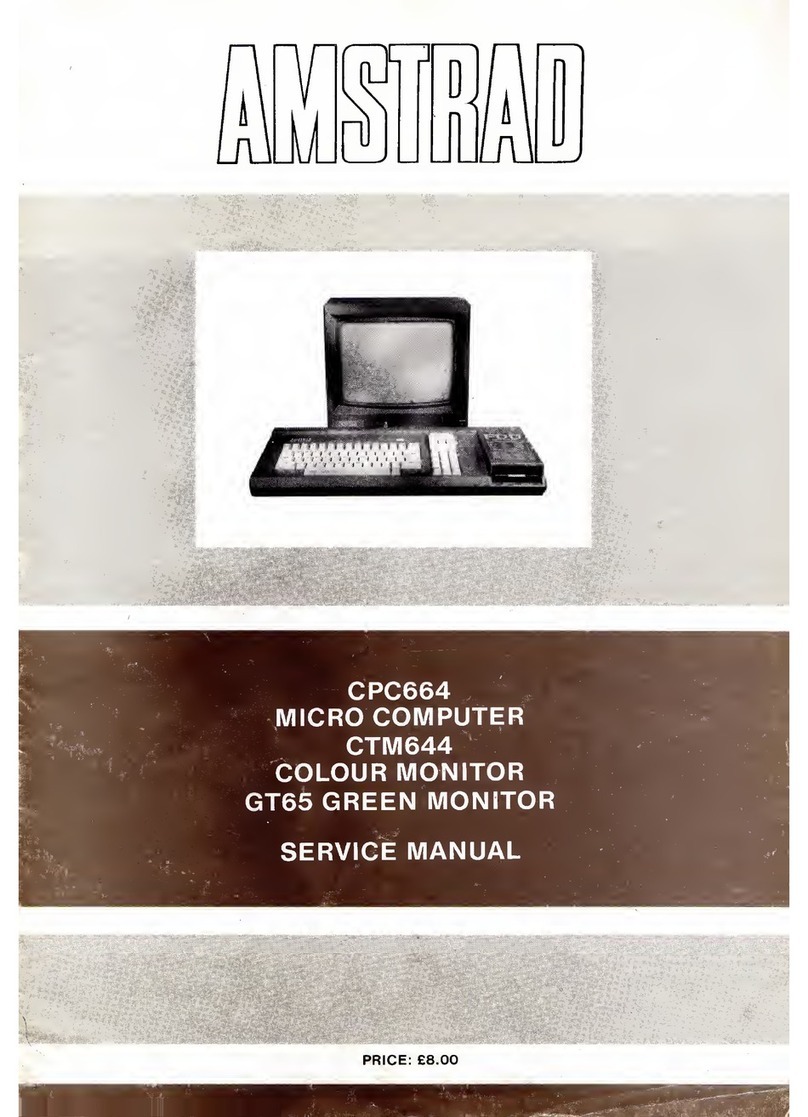
AMSTRAD
AMSTRAD CPC664 User manual
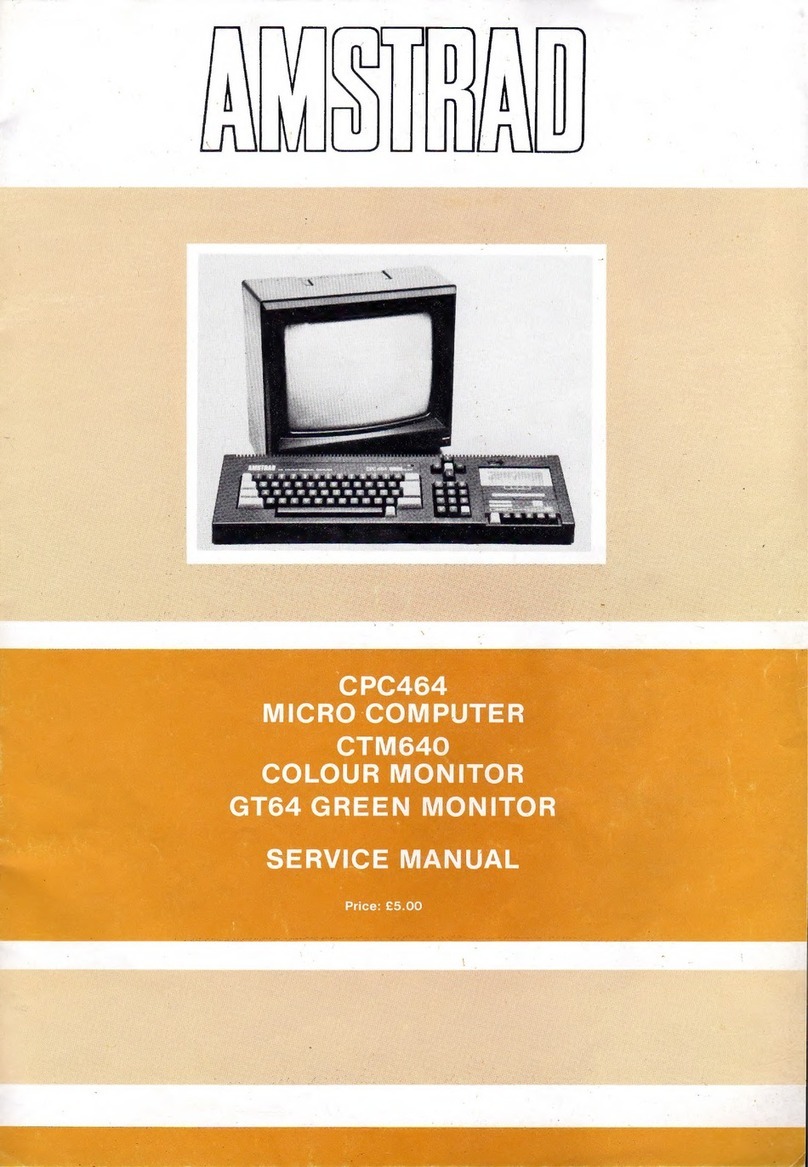
AMSTRAD
AMSTRAD CPC464 User manual

AMSTRAD
AMSTRAD CPC6128 User manual

AMSTRAD
AMSTRAD PC1640 User manual