APV FS660 Series Instruction manual

www.australianpipelinevalve.com.au
INSTALLATION, OPERATION & MAINTENANCE MANUAL
2 PIECE BODY BALL VALVES
FS660 SERIES
API6FA, API607 5th Edition
API6FA, API607 5th Edition
ISO 10497 Firesafe Certied

AUSTRALIAN PIPELINE VALVE BRAND RANGE -CATALOGUES
APV FAMILY OF BRANDS RANGE - CATALOGUES
COMPLETE
PRODUCT LINE
“Australian Pipeline Valve
produces isolation,
control and flow reversal
protection products for
severe and critical service
media in utility, steam,
pipelines, oil & gas
and process industries.
APV valves and pipeline
products form the most
competitive portfolio
in the market.”
Oilfield Products
Valves & Wellheads
Gate, Globe & Check
Valves - Forged Steel
Plug Valves Lubricated,
Sleeved & Lined
Gate, Globe & Check
Valves - Cast Steel
Diamond Gear
Gearboxes
Flowturn Gate, Globe
& Check Valves
Flowturn
Instrument Valves
Flowturn Ball Valves
Multiway & Deadman
Flowturn Strainers
& Sight Glasses
Supercheck
Wafer Check Valves
Superseal
Butterfly Valves
Steamco
Steam Valves
Superseal
Industrial Ball Valves
TwinLok Tube Fittings Uniflo Check ValvesTorqturn Actuators
Ball Valves Floating
& Trunnion Mounted
Ball Valves
Floating Small Bore
Ball Valves
Special Service
Product Brochure
Contact us for your local stockist/distributor
View our catalogues at www.australianpipelinevalve.com.au

2 PIECE BODY BALL VALVES - FS660 SERIES
Australian Pipeline Valve - Installation, Operation and Maintenance Manual 1
Introduction 3
Safety Information 4-5
1.0 Scope 5-6
1.1 Environmental considerations 5
1.2 Storage 6
1.3 Preparation 6
2.0 Installation 6-10
2.1 Installation positions 7
2.2 Preparation for installation 7
2.3 End connections 7-8
2.4 Valve installation by welding 8-9
3.0 Operation 9-10
3.1 Manual operation 9
3.2 Lock device 10
4.0 Maintenance 10-13
4.1 Gland packing 10-12
4.2 Body seal 12
4.3 Troubleshooting 13
5.0 Construction 14-15
5.1 Bill of materials - non direct mount 14
5.2 Bill of materials - direct mount 15
Appendix - Exploded B.O.M. 16-19
Warranty 20
INDEX

2 PIECE BODY BALL VALVES - FS660 SERIES
Australian Pipeline Valve - Installation, Operation and Maintenance Manual
2
INTRODUCTION
The majority of this information is common knowledge to experienced valve users. When properly
installed in applications for which they were designed, Australian Pipeline Valve (APV) valves will give
long reliable service. This instruction is only a guide for installation and operation on standard service and
covers general maintenance and minor repairs. A professional APV approved valve engineering facility
should be utilised for reconditioning or major repairs. Check the part number on the label to ensure the
valve is configured to firesafe specifications if firesafe is required.
Note
We recommend that this entire document be read prior to proceeding with any
installation or repair. Australian Pipeline Valve and it’s parent company take no
responsibility for damage or injury to people, property or equipment. It is the sole
responsibility of the user to ensure only specially trained valve repair experts
perform repairs under the supervision of a qualified supervisor.
RESPONSIBILITY FOR VALVE APPLICATION
The User is responsible for ordering the correct valves. The user is responsible for ensuring APV Valves are
selected and installed in conformance with the current pressure rating and design temperature
requirements. Prior to installation, the valves and nameplates should be checked for proper identification
to ensure the valve is of the proper type, material and is of a suitable pressure class and temperature
rating to satisfy the requirements of the service application.
Do not use valves in applications where either the pressure or temperature is higher
than the allowable working values. Also valves should not be used in service media
if not compatible with the valve material of construction, as this will cause
chemical attacks, leakage, valve failure.
RECEIVING INSPECTION AND HANDLING
Valves should be inspected upon receipt to ensure:
- Conformance with all purchase order requirements.
- Correct type, pressure class, size, body and trim materials and end connections.
- Any damage caused during shipping and handling to end connections, hand wheel or stem.
The User is advised that specifying an incorrect valve for the application may result
in injuries or property damage. Selecting the correct valve type, rating, material
and connections, in conformance with the required performance requirements is
important for proper application and is the sole responsibility of the user.

2 PIECE BODY BALL VALVES - FS660 SERIES
Australian Pipeline Valve - Installation, Operation and Maintenance Manual 3
CONSIDERATIONS OF TECHNICAL RISK/ LIMIT
OF LIABILITY TO CLIENT FOR BALL VALVES
Australian Pipeline Valve don’t consider in our design the following factors of risk:
1. Australian Pipeline Valve ‘Standard’ ball valves can be used in a temperature range between -28.8 to +200°C. (Note,
pressure limitations apply above 38°C refer to Pressure/Temperature charts.) For service temperatures below -28.8°C
ball valve construction materials shall be submitted to an impact test at the minimum service temperature. For
temperatures outside of the range of -28.8°C to +200°C ball valves have to be provided with seats, seals and body
material able to withstand the temperature degree required.
2. The onus is on the customer to specify all materials of construction and service conditions. Australian Pipeline Valve shall
assume standard materials and conditions if not otherwise specified.
3. Australian Pipeline Valve ‘Standard’ ball valves are not equipped with devices suitable to avoid internal over-pressures
caused by incorrect operations of process or by-fluids & liquids subjected to an increase of volume and/or pressure
(these devices, such as the over-pressure hole in the ball or safety seats are available upon request).
4. Australian Pipeline Valve ‘Standard’ ball valves are not designed with special devices to withstand a sudden thermal
jump (thermal shock).
5. In general Australian Pipeline Valve ‘Standard’ ball valves are not mechanically designed to bear overloads due to
exceptional atmospheric or natural phenomenon’s (such as earthquakes).
6. In general Australian Pipeline Valve ‘Standard’ ball valves are not designed to bear loads on flanges, on pipe connections
or pipeline.
7. In general Australian Pipeline Valve ‘Standard’ ball valves can’t withstand ice inside their bodies (in this case user must
specify the optional stem extension for insulating, avoiding the presence of residual product inside the valve).
8. Australian Pipeline Valve ‘Standard’ ball valves are not suitable for low temperature service below -29°C (-20°F) unless
provided with cryogenic stem extension and other modifications (available on request).
9. Australian Pipeline Valve ‘Standard’ ball valves are suitable for ‘industrial’ oxygen (not medical) service when supplied
degreased and packed in polyethylene bags only.
10. The compatibility between ball valves construction materials and medium is selected by the user. The user is ultimately
responsible for verifying the compatibility between medium and materials.
11. Abrasive or dirty service, high temperature service, low temperature service, vacuum service, near zero pressure service
and other special applications should be clearly stated when requesting quotation.
BALL VALVE START-UP
Before installing the ball valve onto the pipe-line it is mandatory for the user to verify the compatibility of the ball valve with
service conditions (medium, temperature and pressure). With reference to standard ball valves held in stock the reseller and
end user will have to assure themselves of the compatibility with the use of conditions required by the customer. Australian
Pipeline Valve ball valves must be only used for on-off (fully open/fully closed) service.
Before using the ball valve in a potential explosive atmosphere it’s necessary: -
• To verify the compatibility between the ball valve and the zone in which the ball valve should be installed.
• To foresee the pipe-line ground condition on which the ball valve should be installed.
• To check that the temperature of the ball valve surface is not higher than the flammable point of the atmosphere in which
the ball valve is installed (in this case specify an insulating cover device for the valve and an extension for the wrench)
• Before installing ball valves with welding ends to make sure that the process of welding is carried out in accordance with
all the safety requirements of the classified zone.
• To avoid mechanical knocks during the installation that may cause sparks.
Australian Pipeline Valve cannot be held responsible for damage caused by use of the product especially if it is improper use or
modified.

2 PIECE BODY BALL VALVES - FS660 SERIES
Australian Pipeline Valve - Installation, Operation and Maintenance Manual
4
SAFETY INFORMATION
The following general safety information should be taken in account in addition to the specific warnings
and cautions specified in this manual. They are recommended precautions that must be understood and
applied during operation and maintenance of the equipment covered in this I.O.M.
Never attempt to disassemble a valve while there is pressure in the line. Ensure both
upstream and downstream pressures are removed. Disassemble with caution in case
all pressures are not relieved. Even when replacing stem packing, caution is
necessary to avoid possible injury.
To prevent valve bending, damage, inefficient operation, or early maintenance
problems, support piping on each side of the valve. When handling gases/fluids that
could cause damage to human health, the environment or property, the necessary
precautions to prevent risk must be taken.
• A valve is a pressurised mechanism containing energised fluids under pressure and
consequently should be handled with appropriate care.
• Valve surface temperature may be dangerously too hot or too cold for skin contact.
• Upon disassembly, attention should be paid to the possibility of releasing
dangerous and or ignitable accumulated fluids.
• Ensure adequate ventilation is available for service.
This manual provides instructions for storing, general servicing, installation and removal of ball valves.
APV and it’s resellers refuse any liability for damage to people, property or plant as well as loss of
production and loss of income under any circumstances but especially if caused by: Incorrect installation
or utilisation of the valve or if the valve installed is not fit for the intended purpose. It is the sole
responsibility of the user to ensure the valve type and materials are correctly specified.
SCOPE OF INSTALLATION ACCORDING TO THE TYPE OF FLUID
(DANGEROUS FOR THE ENVIRONMENT OR HUMAN HEALTH)
Group 1 Classification
- The incorporation of additional safety elements “Double Packing” (utilising a stem extension) is
recommended for the range of products included in Group 1.
- The use of valves without additional safety devices in Group 1 will be the responsibility of the user or
the purchaser, as well as the advisability of installing leakage detection systems.
Group 2 Classification
- Carbon steel valves will not be used in corrosive fluid lines.

2 PIECE BODY BALL VALVES - FS660 SERIES
Australian Pipeline Valve - Installation, Operation and Maintenance Manual 5
DURING OPERATION TAKE INTO ACCOUNT THE FOLLOWING WARNINGS:
• Graphite/Graphoil packing and body gasket is very brittle, any impacting, twisting or bending should
be avoided.
• The valve’s internal parts such as ball, stem, seats, seals, gaskets shall be handled with care avoiding
scratches or surface damage.
• All tools and equipment for handling internal critical sealing parts shall be soft coated.
• Valves can be fitted with gaskets or seals in PTFE, Buna, Viton, etc., hence high temperatures will
damage sealing components.
• Never part open valve. Valve must be full open of full closed to avoid seal damage.
• APV firesafe ball valves are provided with anti-static devices for ball-stem-body. When service
conditions require electrical continuity to prevent static discharge, the user is responsible for
specifying static grounding.
• When ball valves are to be utilised on liquids with very high velocity, check with the valve distributor
or manufacturer for appropriate advice to minimise the possibility of seat deformation, especially when
they are highly pressurised on a high-temperature line.
• Ball valves are generally not recommended for throttling service, where both the fluid flow and the
leading edge of the ball can damage or deform the resilient ball seats causing leakage. High fluid
velocity or the presence of solid particles in suspension will further reduce seat life in throttling
applications.
• Do not open the bonnet or cap when bearing pressure. Valve is not equipped with pressure access
device. User should check it by other method through its piping system.
• Do not touch the surface of a valve at high temperature.
• Not allowed for unstable fluid unless otherwise specified.
• Lock design on the handle is to avoid the valve being operated by non-related people and is an option
upon request.
For all operations make reference to position number on part list of the applicable drawing listed.
1.0 SCOPE
This manual describes the methods of installation and maintenance for floating ball valves, which are
designed to fit between ANSI Class 150, Class 300 and Class 600 flanges or with buttweld ends.
1.1 ENVIRONMENTAL CONSIDERATIONS
According to ISO 14000 regulations and the environmental policy of APV the recyclability of the
components that form part of APV valves is as follows:
Recyclable components - Metal parts, PTFE (hard), plastic plug (low-density polyethylene).
Non-recyclable components - PTFE mixed with other compounds (glass-fibre, graphite, etc.), nylon,
graphite and graphite mixed with metal.

2 PIECE BODY BALL VALVES - FS660 SERIES
Australian Pipeline Valve - Installation, Operation and Maintenance Manual
6
1.2 STORAGE
1.2.1 Temporary Storage
If valves are to be stored before installation, the following should be observed:
a) Keep the valves wrapped and protected as shipped from the manufacturer.
b) Do not remove the protective end covering until the valve is ready for installation. This will reduce the
possibility of foreign material damaging the internal valve components.
c) Valves stored outdoors should be positioned such that water does not accumulate in the valve body.
1.2.2 Long Term Storage
If valves are to be stored more than one year, they should be prepared in the following manner:
a) Remove the packing and apply a preservative to the packing chamber.
b) Do not remove the protective end covering.
c) Do not store the valves outdoors.
1.3 PREPARATION
a) Remove the valve end protection.
b) Prior to shipment, a preservative/corrosion inhibitor may have been applied to the inner body of the
valve. This preservative/corrosion inhibitor can be removed with a solvent provided the solvent used
does not affect the seats/seals used in the valve.
c) The inside of the valve should be inspected and blown out with compressed air. Adjacent piping must
be clean and free from debris to prevent damage to the valve.
d) To prevent valve distortion, inefficient operation or early maintenance problems, support piping on
each side of the valve.
e) Make sure the valve is positioned such that there is sufficient space so that the hand wheel is easily
and safely reached and there is enough clearance for the stem when the valve is open.
f) Install the valve according to the flow indicator on the valve body where applicable.
2.0 INSTALLATION
Piping should be properly aligned and supported to reduce mechanical loading on
end connections. Never use the lever (wrench) to hold the valve during transport,
handling or assembly.
The following procedure is required to be followed for correct installation.
a) Before installation confirm the marking (rating, size and material) on the valve body and name plate.
Ensure the valve is suitable for the service which it is being used.

2 PIECE BODY BALL VALVES - FS660 SERIES
Australian Pipeline Valve - Installation, Operation and Maintenance Manual 7
b) Body bolts and nuts on valve shall be checked and re tightened if necessary in case loosened during
installation.
c) Remove valve end protectors and ensure gasket faces are free from damage. Tighten all bolts between
mating flanges and valve equally paying careful attention to properly tighten bolts. Ensure you rotate
tightening procedure (opposing bolts sequentially) gradually increasing torque. Refer to Appendix Table
2 for bolt tightening sequence.
d) Prior to installation of valve, ensure the line is completely flushed to remove any debris as soft seated
ball valves are easily damaged. Filters or strainers should be installed upstream to protect soft seated
valves.
e) Valves will operate at any angle horizontally or vertically, although it is recommended you install
valves in a vertical position with stem pointing upwards for ease of operation, inspection and
accessibility.
2.1 INSTALLATION POSITIONS
Ball valves are usually bi directional, and therefore may be installed in either direction. In some cases,
ball valves such as ‘metal to metal’ seated and low temperature valves may be uni directional, in which
case the direction of flow will be indicated on the valve body.
2.2 PREPARATION FOR INSTALLATION
• Remove protective end caps or plugs and inspect valve ends for damage to threads, weld ends or
flange faces.
• Thoroughly clean adjacent piping system to remove any foreign material that could cause damage to
seating surfaces during valve operation.
• Verify that the space available for installation is adequate to allow the valve to be installed and to be
operated.
Ensure sufficient clearance for the stem in the full open position. Inadequate
clearance for valves may add mechanical loading to the valve ends. Sufficient
clearance should be allowed for threaded end valves to be ‘swung’ during
installation.
2.3 END CONNECTIONS
2.3.1 Threaded Ends
Check condition of threads on mating pipe. Apply joint compound to the male end of joint only. This will
prevent compound from entering the valve flow path.
2.3.2 Socket weld Ends
Remove all debris, grease, oil, paint, etc., from the pipe that is to be welded into the valve and from the
valve end connections.

2 PIECE BODY BALL VALVES - FS660 SERIES
Australian Pipeline Valve - Installation, Operation and Maintenance Manual
8
Insert the pipe into the valve end connection until it bottoms out in the socket weld bore. Withdraw the
pipe 1/16” so that a gap remains between the pipe and the bottom of the socket weld bore to prevent
cracks (ASME B16.11). Tack the pipe into the valve and complete the fillet weld.
WELDING INSTRUCTIONS
• Local welding regulations and specification must be complied with when carrying
out welding work.
• Remove any paint and rust around the weld area on the pipe and welded end of the
ball valve.
• Check that the ball valve is correctly positioned and aligned with the pipeline.
• Where weld connection is close to seat area, due to short length of the welded ends
there is a risk that the soft inserts may be destroyed during the welding work.
Hence the following procedure is advised: -
Use temperature measuring strips to check that the temperature does not rise beyond
the permissible limits (160°C). The strips must be fitted to the connection near the soft
inserts. These temperature measurements strips are designed so that, when a type-
dependent temperature is reached, the colour irreversibly changes from white to
black. The temperature measurement strip must be monitored constantly throughout
the welding work. If any change of colour is noticed, the welding work must be
interrupted immediately and the weld allowed to cool. For ‘swing out centre’ design,
the centre section containing soft parts can be removed during welding if preferred,
see 2.4.1.
2.3.3 Buttweld End Valves
Clean the weld ends as necessary and weld into the line using an approved weld procedure. Make sure
the pipe and valve body material given on the valve body or nameplate is compatible with the welding
procedure. (Refer our compatibility cross reference chart for equivalent pipe, valve & fittings grades at
the Technical section of our website). Soft seats can be damaged during welding, take steps to ensure
valve is not over heated, especially smaller size valves (see above caution note).
2.4 VALVE INSTALLATION BY WELDING
For all sizes of valves, leave valves in the full open position during installation, welding and post-weld
heat treatment. This will reduce temperature transmission to soft seats. After welding completion, open
the valve and flush line to clean out any foreign matter. Valves over 65 NB ( 2 1/2”) have minimal risk of
temperature damage to seats.
2.4.1 Method
For valves up to 80 NB (3”) the welding temperature can adversely affect the PTFE and elastomer
components. Follow the welding instructions above but also use temperature measuring strips to monitor
temperature. It will be the responsibility of the operator to ensure valves are kept cool during welding

2 PIECE BODY BALL VALVES - FS660 SERIES
Australian Pipeline Valve - Installation, Operation and Maintenance Manual 9
and then post-weld testing of the valve should be performed. Larger size valves over 80 NB (3”) are less
likely to transmit heat to seat and stem packing during welding but still care should be taken. Valves
80NB (3”) & under must have PUP ends to avoid seat damage.
The below procedures should also be followed:
a) Always ensure there is no pressure or product in the line. Ball valves will be supplied with socket weld
ends to ANSI B16.11 or butt weld ends to ANSI B16.25. Welding should be done using procedures and
welders qualified under section IX of the ASME boiler and pressure vessel code.
b) Always do as a low temperature weld as necessary to obtain a reliable connection. Use whatever
measure necessary to localise heat at the joint, dissipating it before damage can occur to adaptor
gaskets and/or seats (the main risk is seats). Use a tempil stick or other temperature indicator on the
outside of the valve body (centre section) directly adjacent to adapter end piece) being welded to
assure the body temperature does not increase 160°C. Always leave valve in open position during
welding but also at least 60 minutes after welding unit valve cools.
c) Where required APV will supply spare body gaskets. Graphite body gaskets are brittle so great care
should be taken not to damage.
The responsibility for welding of the valves into piping systems is that of those performing the welding.
Refer to ASME B31.1, B31.3 etc. Written welding procedures covering all attributes of the process and
materials to be welded shall be in accordance with Section IX of the ASME Boiler and Pressure Vessel Code
and any additional requirements from the applicable piping code including any possible necessary
localised post weld heat treatment depending on material specifications.
3.0 OPERATION
3.1 MANUAL OPERATION
Valve adjustment is by clockwise turning of stem. Lever operated and gear operated valves have a
position indicator to indicate open or closed (see figure 1). Ball Valves must not be used for throttling. Do
not leave part open, or seats will be damaged. Valve must be full open or full closed or damage to seats
or body will occur.
FIG 1.

2 PIECE BODY BALL VALVES - FS660 SERIES
Australian Pipeline Valve - Installation, Operation and Maintenance Manual
10
3.2 LOCK DEVICE
Where provided (optional) the valve has a locking lug that allows valve to be locked in full open or full
closed position.
4.0 MAINTENANCE
Valves should be periodically checked at least once every 3 months, but depending on service, criticality
and frequency of use, more regular checking may be required.
Packing leakage could result in personal injury. Valve packing is tightened prior to
shipping but may require adjustment to meet specific service conditions.
If a valve does not fully close, damage to the seat and body will result due to the
venturi effect resulting in high pressure erosion. Flush or remove the valve at next
opportunity.
A good program of inspection and maintenance cannot be overstressed. It is recommended that the valve
be periodically and at least partially stroked/function tested to ensure the valve functions and prevent
seizure/sticking of any mating surfaces. Duration depends on service, criticality etc. However it also must
be factored in that if there are impurities or particulates in the line each operation could reduce seat life
proportionately. Periodic inspection of critical leak-path areas such as body/bonnet joint, end
connections, seating surfaces, and around the stem packing should be a requirement.
The most common area for leakage is around the stem packing, this is usually due to wear and can
normally be stopped by adjusting the packing. This procedure is performed by turning gland bolts or nut
(9) 1/2 turn at a time until leakage stops. Once leakage stops, continue tightening gland plate nuts an
additional 1/2 turn. If leakage cannot be halted by adjusting packing, repacking of the valve is indicated.
(Refer to field repair).
Do not attempt to replacing packing or replace stem while the valve is in service!
(The stem is blowout proof and can only be removed by disassembling the valve).
Only graphite packing is to be used for firesafe service, PTFE is not firesafe. A FS660
valve is firesafe only when fitted with graphite packing and graphite or spiral
wound graphite filled body gasket. Check the full part number on the label to
ensure the valve is specified as firesafe. If there is no firesafe logo on the label the
valve is not firesafe. If the part number indicates PTFE packing or body gasket the
valve is not firesafe.
4.1 GLAND PACKING
In case of slight leakage from the gland, gland packing nut(s) can be lightly tightened up without
effecting torque.

2 PIECE BODY BALL VALVES - FS660 SERIES
Australian Pipeline Valve - Installation, Operation and Maintenance Manual 11
4.1.1 Stem Leakage – Stem Packing Replacement
The most common point for leakage is around the stem and packing this leakage can normally be stopped
by adjustment of the packing gland. If this does not stop the valve leakage, the valve will have to be
repacked.
The system and valve MUST be depressurised and removed from the line before attempting any repair
work. After removing all pressure from the valve and draining the system the following procedure should
be used to repack the valve.
1. Remove nuts or screw from the lever. Remove the lever and lock plate. Remove the gland nuts.
2. Remove old packing, taking care not to scratch or damage the stem of stuffing box. Note, the stem
design is anti-blow out so the stem cannot be removed up through the top of the valve.
3. Clean and inspect stem, stuffing box, and gland. If any scratches, nicks, or corrosion is found, the parts
should be replaced.
4. Slide each packing ring over the stem and into packing chamber. Carefully tap each ring into place and
continue installing rings until the recommended number of rings have been installed. A thin smear of
molybdenum sulfide anti-seize grease may be used on the stem and packing chamber wall for packing
lubrication.
5. Replace and tighten gland nut(s) alternately in 1/4 turn increments until a reasonable torque is applied
to lightly compress packing. Lubricate stem and cycle valve through a couple of complete cycles.
6. If slight stem leakage occurs after system is pressurised, continue tightening gland nut in alternating
1/4 turn increments until leakage stops. Once leakage stops, continue tightening gland plate nuts and
additional 1/4 turn. There is also a PTFE seal ring/bearing and some models also have an elastomer
o-ring. However, these parts can only be replaced during complete disassembly of the valve. If a stem
o-ring is fitted it can be replaced with an elastomer o-ring suitable for the service medium and
temperature. Should replacement of packing fail to prevent the leakage, complete reconditioning of
the valve may be required.
Personal injury may result from sudden release of any process pressure. APV
recommends the use of protective clothing, gloves and eye wear when performing
any installation or maintenance. Isolate the valve from the system and relieve
pressure prior to performing maintenance. Disconnect any operating lines providing
air pressure, control signals or electrical power to actuators.

2 PIECE BODY BALL VALVES - FS660 SERIES
Australian Pipeline Valve - Installation, Operation and Maintenance Manual
12
11
109
7
6
5
8
15
12
NO DESCRIPTION
5Gasket
6Thrust Seal
7Gland Packing
8Stem
9Gland Nut
10 Washer
11 Stem Nut
12 Lever
15 Anti-static Device
16 Stem O-ring*
*1 Depends on size & class
Sample only, design depends on size,
model & class. Refer to as-built drawing
FIG 2. CONSTRUCTION FOR GLAND PARTS
(non direct mount)
NO DESCRIPTION
5Stem
6Anti-static Device
8Stem Seal
9O-Ring
10 Stem Packing Set
11 Bushing
12 Gland
13 Belleville Washers
14 Stem Nut
15 Stop-Lock Cap
16 Handle Gland
17 Handle Nut
18 Lock Device
19 Handle
20 Handle Sleeve
21 Stop Bolt
Sample only, design depends on size,
model & class. Refer to as-built drawing
21
5
8
6
9
20
19
17
18
13
11
12
14
15
16
10
FIG 2a. CONSTRUCTION FOR GLAND PARTS
(direct mount)
4.2 BODY SEAL
Sealing between the threaded body is provided by a gasket (Teflon or graphite) and both valve segment
surfaces also provide metal to metal friction fit sealing. In larger sizes or higher pressures an elastomer
o-ring may also be used. In case of slight leakage check the threaded body joint is properly tightened up.
If a gasket seal is disturbed while removing or adjusting gasketed parts, APV
recommends installing a new gasket while reassembling. A proper seal is required
to ensure optimum operation.

2 PIECE BODY BALL VALVES - FS660 SERIES
Australian Pipeline Valve - Installation, Operation and Maintenance Manual 13
4.3 TROUBLESHOOTING
MALFUNCTION POSSIBLE CAUSE REDIAL ACTION
Valve does not rotate or operate 1. Packing is dropped too tightly.
2. The stem is damaged or there is dirt.
3. The times or on-off operation are too many or debris
exists on the surface of the ball.
1. Loosen packing and adjust again.
2. Pull apart the valve and clean the dirt.
Ball/Seat Leaking 1. Valve not fully closed.
2. Seat or ball damaged.
3. Debris trapped in valve.
1. Close the valve tightly.
2. Replace seat or ball.
3. Clean the debris.
Stem Packing Leaking 1. Packing gland nut loose.
2. Packing damaged or missing.
3. Seal misaligned.
1. Tighten gland nut.
2. Replace packing (shut down rst).
3. Replace and align it correctly.
Body Gasket Leaking 1. Body joint.
2. Body gasket damaged.
1. Tighten body nut.
2. Replace the gasket.
Note
Nylon and Devlon are hard and more scratch resistant compared to Teflon®, and
PEEK is harder still. However, Teflon® is more resilient and has better ‘memory’ in
terms of resistance to permanent indentations. All soft seated valves are only suited
to clean service applications.

2 PIECE BODY BALL VALVES - FS660 SERIES
Australian Pipeline Valve - Installation, Operation and Maintenance Manual
14
5.0 CONSTRUCTION
5.1 BILL OF MATERIALS - NON DIRECT MOUNT (EXAMPLE)
Optional Mount Pad
W
M
14
MATERIALS LIST
NO. PARTS STAINLESS CARBON STEEL
1Body ASTM A351 CF8M ASTM A216-WCB
2End Cap ASTM A351 CF8M ASTM A216-WCB
3Seat PTFE/RPTFE PTFE/RPTFE
4Ball ASTM A351 CF8M/316 ASTM A351 CF8M/316
5Gasket Graphite*/PTFE Graphite*/PTFE
6Thrust Washer PTFE PTFE
7Stem Packing Graphite*/PTFE Graphite*/PTFE
8Stem ASTM A276-316 ASTM A276-304
9Gland AISI 304 AISI 304
10 Spring Washer AISI 304 AISI 304
11 Handle Nut AISI 304 AISI 304
12 Handle AISI 304 Zinc Plated Steel
13 Handle Cover PVC PVC
14 Stop Screw AISI 304 AISI 304
15 Anti-Static Device AISI 304 AISI 304
* Firesafe
ØA
11
109
7
6
5
8
15
4
3
2
1
L
H
B
13
12
Pressure
Equalisation Hole Post-re metal
to metal seat
ØD
The above is indicative only. Design varies according to size, class, trim, etc. Refer as-built drawing.

2 PIECE BODY BALL VALVES - FS660 SERIES
Australian Pipeline Valve - Installation, Operation and Maintenance Manual 15
5.2 BILL OF MATERIALS - DIRECT MOUNT (EXAMPLE)
A
X
L
L1
h
H
Y
Direct Mount Pad
Post- re metal
to metal seal
Seat
J
MATERIALS LIST
NO. PARTS STAINLESS CARBON STEEL
1Body ASTM A351 CF8M ASTM A216 WCB
2End Cap ASTM A351 CF8M ASTM A216 WCB
3Ball ASTM A351 CF8M/316 ASTM A351 CF8M/316
4Ball Seat PTFE/TFM1600/TFM4215 PTFE/TFM1600/TFM4215
5Stem SUS316 SUS316
6Antistatic Device SUS316 SUS316
7Body Gasket PTFE/TFM1600 PTFE/TFM1600
8Tapered Stem Seal PTFE/TFM1600/RTFE PTFE/TFM1600/RTFE
9O-Ring FKM FKM
10 Stem Packing Set PTFE V-Rings PTFE V-Rings
11 Bushing 50% SS+50% PTFE 50% SS+50% PTFE
12 Gland SUS316 SUS316
13 Belleville Washers SUS301 SUS301
14 Stem Nut A194-8 A194-8
15 Stop-Lock Cap SUS304 SUS304
16 Handle Gland SUS304 SUS304
17 Handle Nut A194-8 A194-8
18 Lock Device SUS304 SUS304
19 Handle SUS304 SUS304
20 Handle Sleeve Vinyl Plastic Vinyl Plastic
21 Stop Bolt A2-70/SUS304 A2-70/SUS304
22 Stop Nut A2-70/SUS304 A2-70/SUS304
* Firesafe
3
1
4
6
5
472
8
22
9
21
19
20
18
17
16
15
14
13
12
11
10
The above is indicative only. Design varies according to size, class, trim, etc. Refer as-built drawing.

2 PIECE BODY BALL VALVES - FS660 SERIES
Australian Pipeline Valve - Installation, Operation and Maintenance Manual
16
APPENDIX
Sample Drawing 6000psi
Example only, refer to as-built drawing
www.australianpipelinevalve.com.au
API 6FA 3rd Edition
API 607 5th
ISO 10497
APV DWG FRM 533
BILL OF MATERIALS
Dimensions in millimeters
Firesafe Ball Valve, 2PC Mono Block,
Model FS660-AK1HUGABBN,
NPS 2” (DN50) 6000 PSI,
NPT, Lever Operated, FB, CF8M
ORDER No/ DWG No
REV.
APPROVED
CHECKED
DRAWN
533
00
NO. PART NAME MATERIAL NOTES
1
2
3
4
5
6-1
6-2
7
8
9
10
11
12
13
13A
14
BODY
BODY CAP
SEAT
BALL SOLID
BODY GASKET
THRUST WASHER SEALS
THRUST WASHER SEALS
STEM
STEM PACKING
GLAND
GLAND SEALS
SPRING WASHER
HANDLE NUT
HANDLE
LOCKING DEVICE
SLEEVE
ASTM A351 CF8M
ASTM A351 CF8M
DELRIN
ASTM A351 CF8M/316
GRAPHITE
PTFE
GRAPHITE
ASTM A276 316
GRAPHITE
AISI 304
PTFE
AISI 304
AISI 304
AISI 304
AISI 304
VINYL PLASTISOL
-
-
-
-
-
(2)
-
-
SOLID
(1)
(4)
-
-
(4)
(3)
-
Australian Pipeline Valve
B.T.
S.Q.
C.C.
15
16
17
ANTISTATIC DEVICE
BODY O-RING
STEM O-RING
AISI 316
VITON
VITON
-
(4)
-
DIMENSIONS (MM) & WEIGHT (KG) & TORQUE (NM)
DN ØD HW
50 50.0 133 255
M
3XM8
Inch
2”
L
159
ISO 5211
F07
Weight
8.0
RATING
DESIGN & MFG.
PRESS-TEMP RATING
FACE TO FACE DIM.
END CONNECTION
END DIMENSION
TEST & INSPECTION
MARKING & PAINT
OTHER REQ.
PORT SIZE
TRIM
NOTES
OTHER
CL 2500 6000 PSI
ASME B16.34 &API 608 & EN 12516-1
ASME B16.34
MFG
NPT
ANSI B1.20.1
API 598/ ISO 5208-A
MSS SP-55, PICKLED &PASSIVATED
NACE MR-01-75 &MR-01-03 (ISO 15156)
FULL PORT
316SS
FIRESAFE: API 607 5TH ED., API 6FA 3RD ED.
ANTI STATIC BS5351 &ISO 17292-2015
TEST PRESSURE
SHELL HYDRO SEAT HYDRO
SEAT AIR BACKSEAT
TEMPERATURE
MEDIUM Water, Oil, Gas
ºC
-29 TO 220
ºF
-20 TO 428
Mpa Psi
0.55 80
Mpa Psi
Mpa Psi Mpa Psi
62.0 9000 45.4 6600
SPECIAL OPTIONAL HP SEAT TEST PERFORMED ISO 5208-A
(1) STEM SMOOTHNESS Ra 0.7 ~0.9 µm
(2) STUFFING BOX SMOOTHNESS Ra 0.8 ~1.1 µm
(3) SEMI-FLEXIBLE ENERGISED SEAT FOR REDUCED TORQUE AND TIGHT SHUT-OFF AT VERY LOW AND HIGH PRESSURES
(4) FRICTION FIT THREADED BODY JOINT IN ADDITION TO ENCAPSULATED GRAPHITE AND VITON BODY SEALS,
PLUS 1 SAFETY TACK WELD TO BODY JOIN
P
70
13 14
17
8 10 9 7 11 12 13A
3
4
15
16
5
6
1
2
L
ØD
H
Pressure equalisation hole
P
Low and high pressure zero leakage capability.
Energised flexible seat face design and radial
grooves on sides of seats ensure upstream
pressure balances cavity pressure.
1 tack body weld
W
M
ISO 5211
DELRIND
500°F
(260°C)
400
(204)
300
(149)
-38
(-34)
0
(-18)
100
(38)
200
(93)
SERVICE TEMPERATURE
WORK PRESSURE IN PSIG
WORK PRESSURE IN BAR
0.0
103.4
310.3
413.7
482.7
0
1500
3000
4500
6000
7000
206.8
D
P-T RATING

2 PIECE BODY BALL VALVES - FS660 SERIES
Australian Pipeline Valve - Installation, Operation and Maintenance Manual 17
APPENDIX - CONT’D
Sample Drawing 3705psi
Example only, refer to as-built drawing
www.australianpipelinevalve.com.au
API 6FA 3rd Edition
API 607 5th
ISO 10497
APV DWG FRM 485
BILL OF MATERIALS
Dimensions in millimeters
Firesafe Ball Valve, 2PC Mono Block,
Model FS660-AK1GUAACCN,
NPS 2” (DN50) 3705 PSI,
NPT, Lever Operated, WCB
ORDER No/ DWG No
REV.
APPROVED
CHECKED
DRAWN
485
00
NO. PART NAME MATERIAL NOTES
1
2
3
4
5
6-1
6-2
7
8
9
10
11
12
13
13A
14
BODY
BODY CAP
SEAT
BALL SOLID
BODY GASKET
THRUST WASHER SEALS
THRUST WASHER SEALS
STEM
STEM PACKING
GLAND
GLAND SEALS
SPRING WASHER
HANDLE NUT
HANDLE
LOCKING DEVICE
SLEEVE
ASTM A216 WCB
ASTM A216 WCB
DELRIN
ASTM A276 316
GRAPHITE
PTFE
GRAPHITE
ASTM A276 316
GRAPHITE
AISI 304
PTFE
AISI 304
AISI 304
ZINC PLATED STEEL
AISI 304
VINYL PLASTISOL
-
-
-
-
-
(3)
-
-
SOLID
(2)
(5)
INNER
(1)
(1) (5)
(4)
OUTER
Australian Pipeline Valve
B.T.
S.Q.
C.C.
15
16
17
ANTISTATIC DEVICE
BODY O-RING
STEM O-RING
AISI 316
VITON
VITON
-
(5)
-
DIMENSIONS (MM) & WEIGHT (KG)
DN ØD HW
50 45.0 125 260
Inch
2”
L
149.0
Weight
5.9
RATING
DESIGN & MFG.
PRESS-TEMP RATING
END CONNECTION
END DIMENSION
TEST & INSPECTION
MARKING & PAINT
OTHER REQ.
PORT SIZE
TRIM
NOTES
OTHER
SPECIAL
CL 1500 3705 PSI
ASME B16.34 &API 608 & EN 12516-1
ASME B16.34
NPT
ANSI B1.20.1
API 598/ ISO 5208-A
MSS SP-55, PHOSPHATED
NACE MR-01-75 &MR-01-03 (ISO 15156), ISO 5211 MOUNT
FULL PORT
316SS
FIRESAFE: API 607 5TH ED., API 6FA 3RD ED.
ANTI STATIC BS5351 &ISO 17292-2015
OPTIONAL HP SEAT TEST PERFORMED ISO 5208-A
TEST PRESSURE
SHELL HYDRO SEAT HYDRO
SEAT AIR BACKSEAT
TEMPERATURE
MEDIUM Water, Oil, Gas
ºC
-29 TO 120
ºF
-20 TO 248
Mpa Psi
0.55 80
Mpa Psi
Mpa Psi Mpa Psi
37.2 5400 27.3 3975
ISO 5211
FØ7 3xM8
(1) FULLY PHOSPHATISED 18 µm MAGNESIUM PHOSPHATE
(2) STEM SMOOTHNESS Ra 0.8 ~1.0 µm
(3) STUFFING BOX SMOOTHNESS Ra 0.8 ~1.1 µm
(4) SEMI-FLEXIBLE ENERGISED SEAT FOR REDUCED TORQUE AND TIGHT SHUT-OFF AT VERY LOW AND HIGH PRESSURES
(5) FRICTION FIT THREADED BODY JOINT IN ADDITION TO ENCAPSULATED GRAPHITE AND VITON BODY SEALS,
PLUS 1 SAFETY TACK WELD TO BODY JOIN
13 14
17
8 10 9 7 11 12 13A
3
4
15
16
5
6
1
2
L
ØD
H
Pressure equalisation hole
Low and high pressure zero leakage capability.
Energised flexible seat face design and radial
grooves on sides of seats ensure upstream
pressure balances cavity pressure.
1 spot weld to body join
W
M
ISO 5211
P-T RATINGS

2 PIECE BODY BALL VALVES - FS660 SERIES
Australian Pipeline Valve - Installation, Operation and Maintenance Manual
18
APPENDIX - CONT’D
Sample Drawing 2000psi Direct Mount
Example only, refer to as-built drawing
www.australianpipelinevalve.com.au
API 6FA 3rd Edition
API 607 5th
ISO 10497
APV DWG FRM 635
BILL OF MATERIALS
Dimensions in millimeters
Firesafe Ball Valve, 2pc, High Cycle Design,
Direct Mount Pad, Model FS660-AK1EGGACBNM,
NPS 1/4”~1” (DN8~DN25) ANSI 2000 PSI WOG,
NPT, Lever Operated, FB, CF8M
ORDER No/ DWG No
REV.
APPROVED
CHECKED
DRAWN
635
00
NO. PART NAME MATERIAL NOTES
1
2
3
4
5
6
7
8
9
10
11
12
13
14
15
16
BODY
END CAP
BALL
SEATS
STEM
ANTISTATIC SPRING/BALL
BODY GASKET
PRIMARY STEM THRUST SEAL
PACKING
BUSHING
GLAND
BELLEVILLE SPRING WASHERS
STEM NUT
HANDLE NUT
STOP-LOCK-CAP
HANDLE GLAND
ASTM A351 CF8M
ASTM A351 CF8M
ASTM A351 CF8M/316
TFM4215 (CARBON GRAPHITE FILLED PTFE)
ASTM A276 316
AISI 316
GRAPHITE
PTFE (ENERGISED)
GRAPHITE
AISI 304
AISI 316
ASTM 301
ASTM A194-8
ASTM A194-8
AISI 304
AISI 304
(5) SET
-
-
-
-
(2)
-
-
(4) (7) LIVE ENERGISED
(5) TAPERED
(1) BLOW OUT PROOF
-
(3) (8)
(3) (6) (8)
-
(6)
Australian Pipeline Valve
B.T.
S.Q.
C.C.
17
18
LOCK DEVICE
HANDLE
AISI 304
AISI 304
-
-
DIMENSIONS (MM) & WEIGHT (KG)
Inch
RATING
DESIGN & MFG.
PRESS-TEMP RATING
FACE TO FACE DIM.
END CONNECTION
END DIMENSION
TEST & INSPECTION
MARKING & PAINT
OTHER REQ.
PORT SIZE
TRIM
NOTES
OTHER
ANSI 2000 PSI WOG
ASME B16.34/API 608
ASME B16.34
APV
NPT
ANSI B1.20.1
API598/ ISO 5208-A
MSS SP-55, PICKLED &PASSIVATED
NACE MR-01-75 &MR-01-03 ISO 5211 DIRECT MOUNT
FULL PORT
316SS, HIGH CYCLE TRIPLE BARRIER STEM SEAL SYSTEM
FIRESAFE : API 607 5TH ED., API 6FA 3RD ED.
ANTI STATIC BODY-STEM-BALL BS5351 &ISO 17292-2015
TEST PRESSURE
SHELL HYDRO SEAT HYDRO
SEAT AIR BACKSEAT
TEMPERATURE
MEDIUM Water, Oil, Gas
ºC
-29 TO 200
ºF
-20 TO 392
Mpa Psi
0.55 80
Mpa Psi
Mpa Psi Mpa Psi
20.7 3000 15.1 2200
SPECIAL OPTIONAL HP SEAT TEST PERFORMED ISO 5208-A
(1) STEM SMOOTHNESS Ra 0.80 ~1.4 µm
(2) STUFFING BOX SMOOTHNESS Ra ≤1.6 µm
(3) INVESTMENT CAST, CASTING APPROVED BY TUV AD 2000-MERKBLATT WU
(4) DYNEON (3M USA) TFM4215 SEATS
(5) TRIPLE BARRIER STEM SEAL SYSTEM ENERGISED WITH BELLEVILLE PACKING SPRING SET. LOW EMISSION TA LUFT COMPLIANT DESIGN
(6) FRICTION FIT THREADED BODY JOINT IN ADDITION TO ENCAPSULATED BODY GASKET
(7) ENERGISED SEAT INHERENTLY SELF RELIEVING CAPABLE. ALSO WITH RADIAL GROOVES ON SIDE OF SEAT ENSURE UPSTREAM PRESSURE BALANCES
CAVITY PRESSURE
(8) LOST WAX SILICA SOLUTION INVESTMENT CAST
19
20
HANDLE SLEEVE
O-RING
VINYL PLASTIC
FKM -
-
21
22
STOP BOLT
STOP NUT
A2-70
A2-70
(304SS)
(304SS)
DN L d W H H1 T P M E1 E2 U1 U2 Hex.B ISO 5211 Weight
1/4” 8 62 10.6 147 43.1 74 29 9 9 36 42 6 6 23.5 F03~F04 0.54
3/8” 10 62 12.7 147 43.1 74 29 9 9 36 42 6 6 23.5 F03~F04 0.55
1/2” 15 75 15 147 43.1 74 34.5 9 9 36 42 6 6 28 F03~F04 0.61
3/4” 20 80 20 147 50.7 82 37 9 9 36 50 6 7 33 F03~F05 0.82
1” 25 90 25 177 58.5 90 45 11 11 42 50 6 7 45 F04~F05 1.20
Threaded
T
L
12
3
4
5
6
7
8
9
11
10
1615141312
191817
W
20
H1
M
H
Ød
21
22 HEX.B
Lock Device
Direct Mount Pad
(ISO 5211)
ØE2
4-ØU2
4-ØU1
ØE1
P
Pressure balance hole
DETAIL B
SEAT
LIVE FLEXIBLE LIP SEAT DESIGN
BALL
SEAT
BODY
Table of contents
Other APV Control Unit manuals
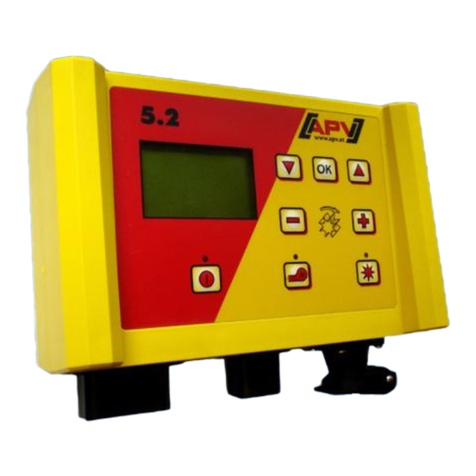
APV
APV 5.2 User manual
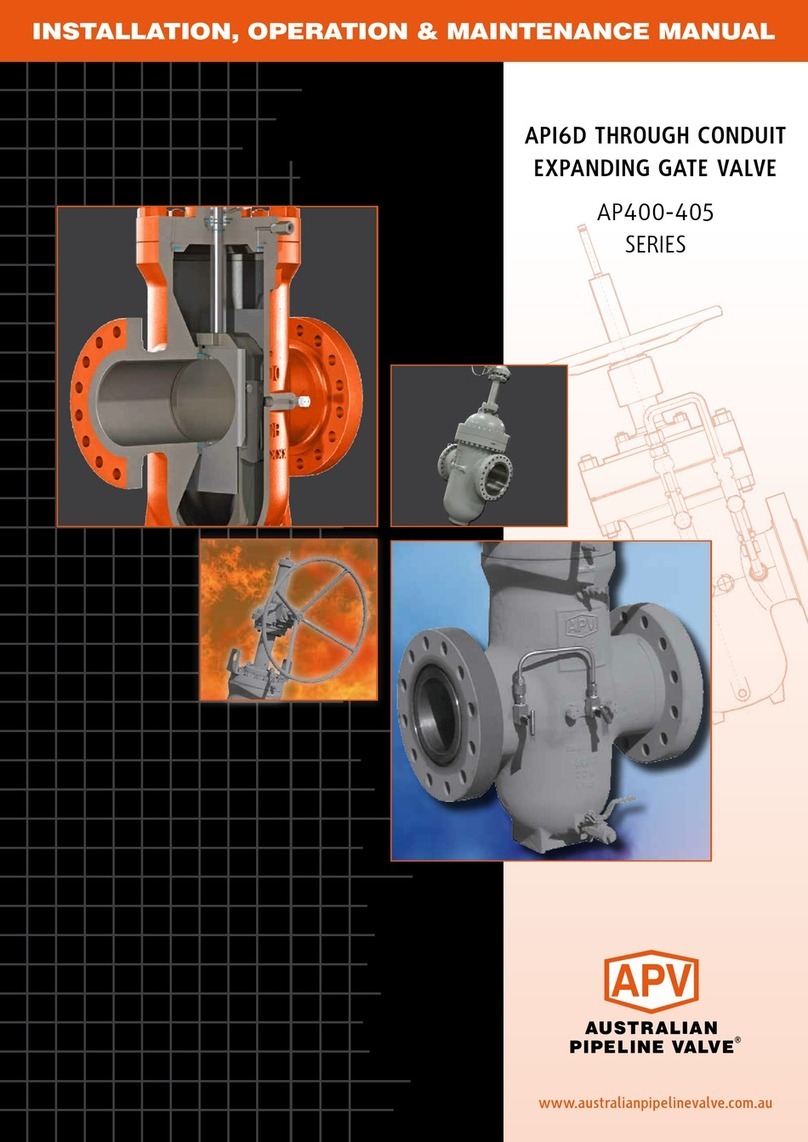
APV
APV AP 400 Series Instruction manual
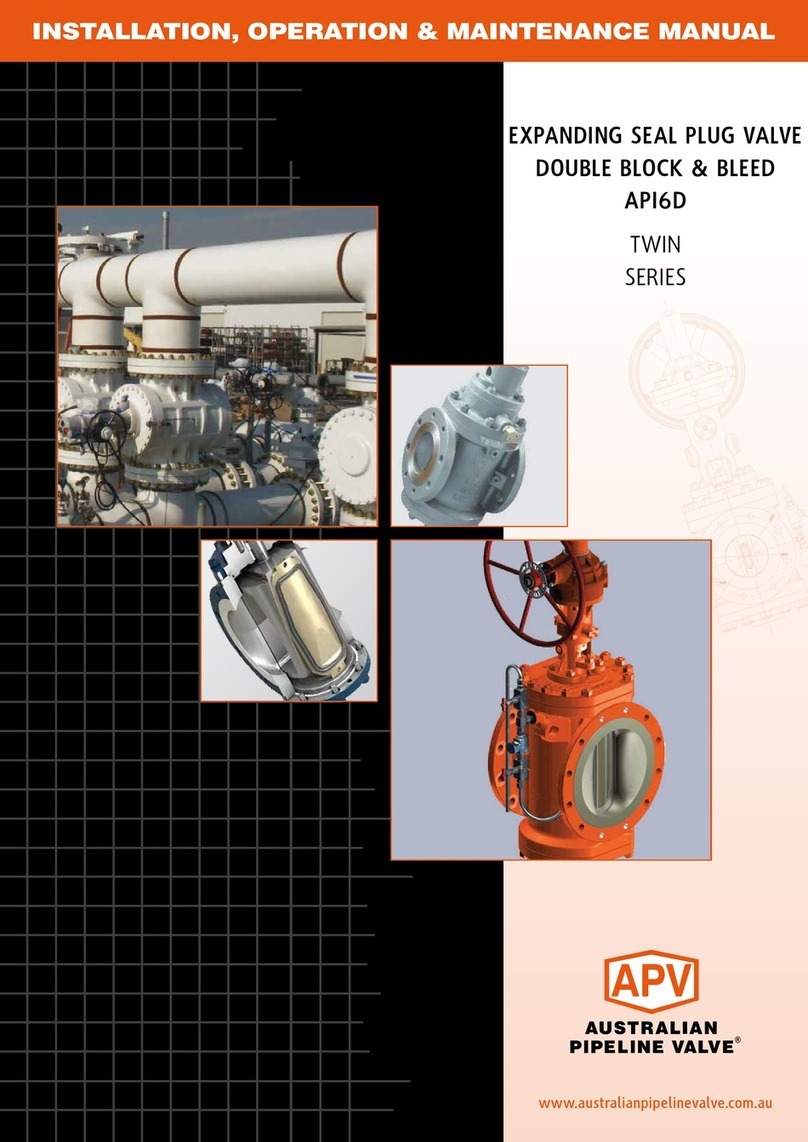
APV
APV TWIN Series Instruction manual
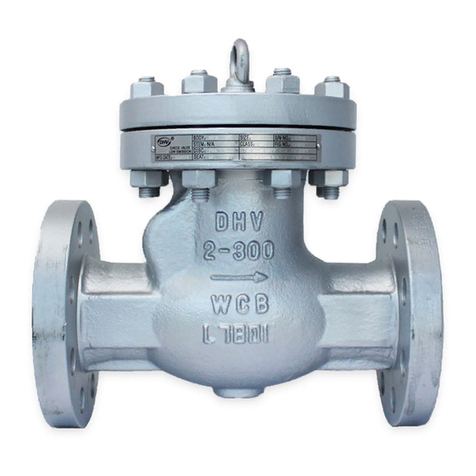
APV
APV API594 User manual
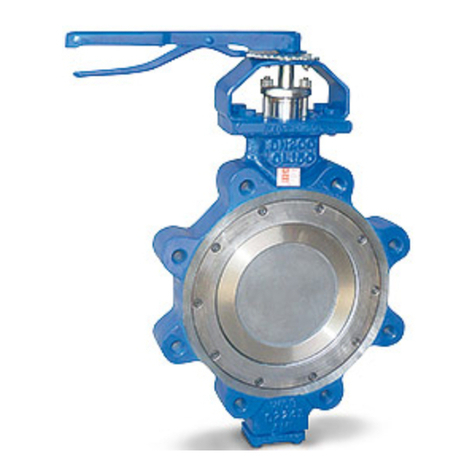
APV
APV SUPERSEAL 2014 Series Instruction manual
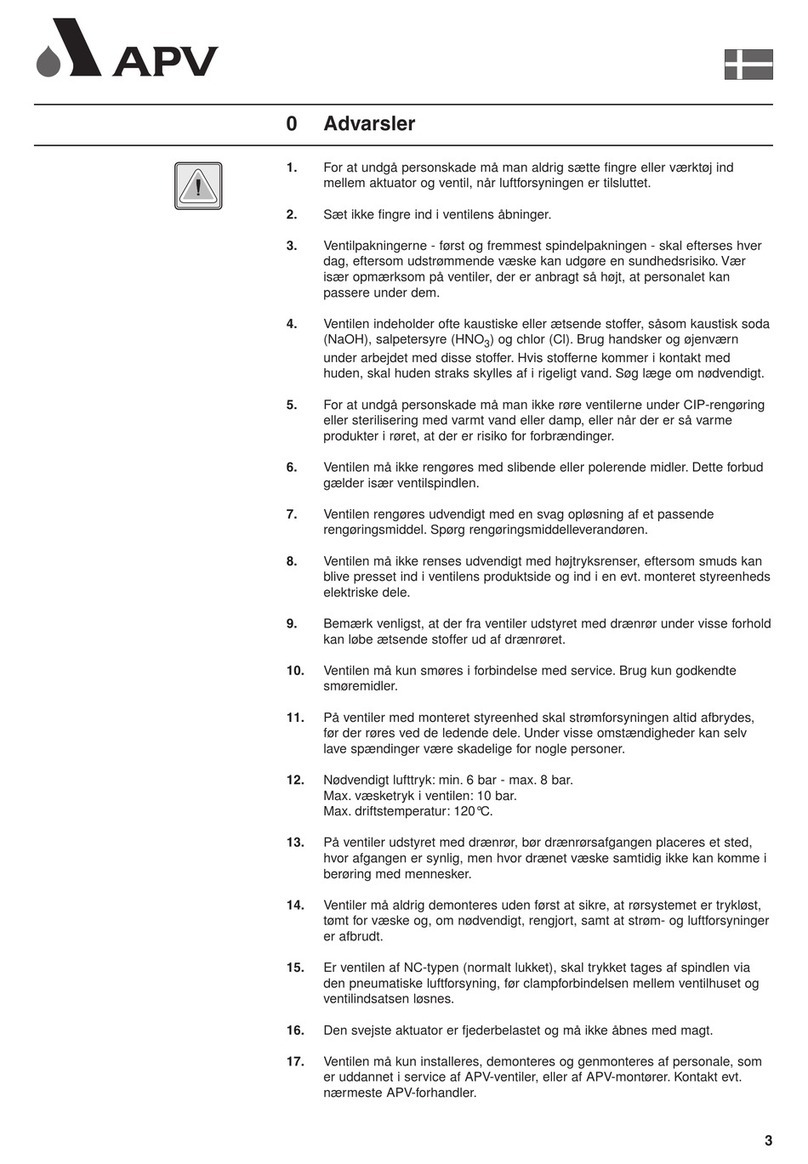
APV
APV DELTA SW4 User manual
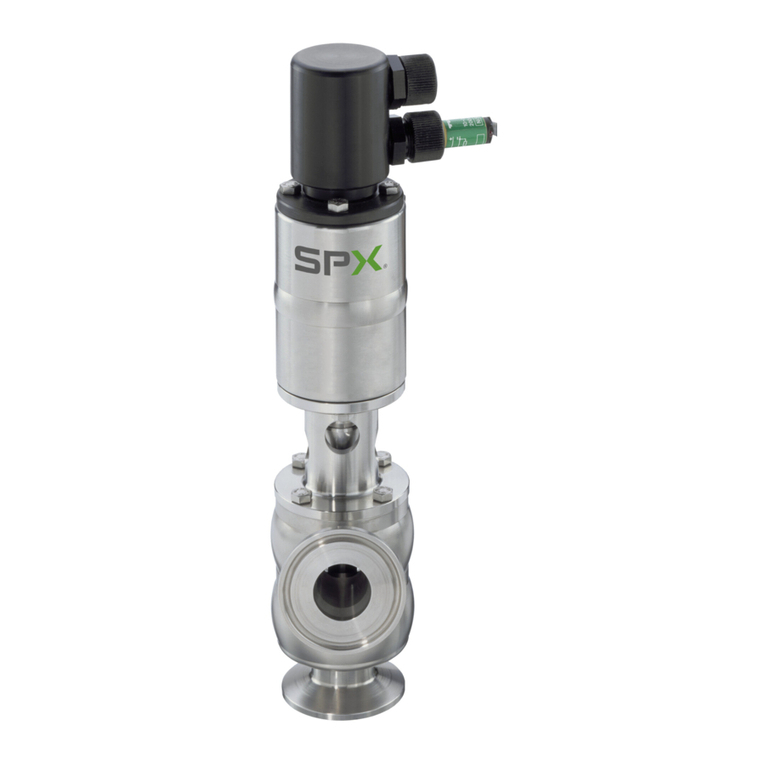
APV
APV SPX Flow APV DELTA SWmini4 User manual

APV
APV BVF100 Series Instruction manual
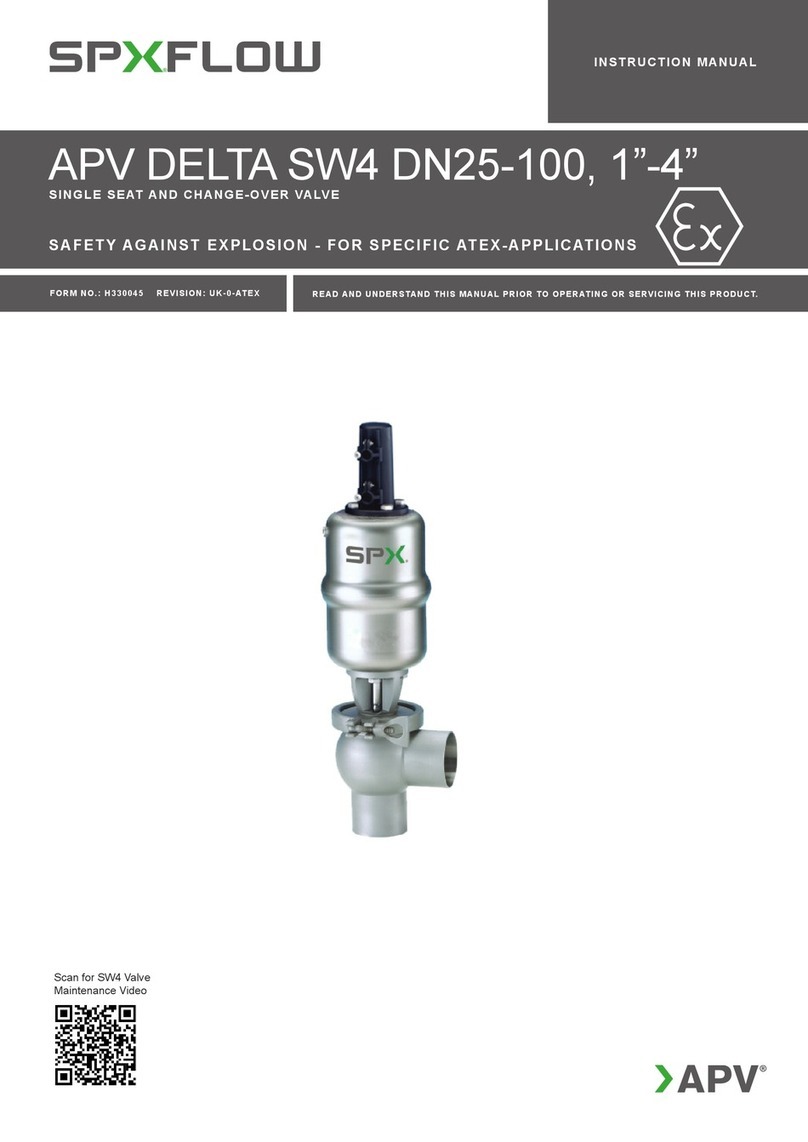
APV
APV DELTA SW4 User manual
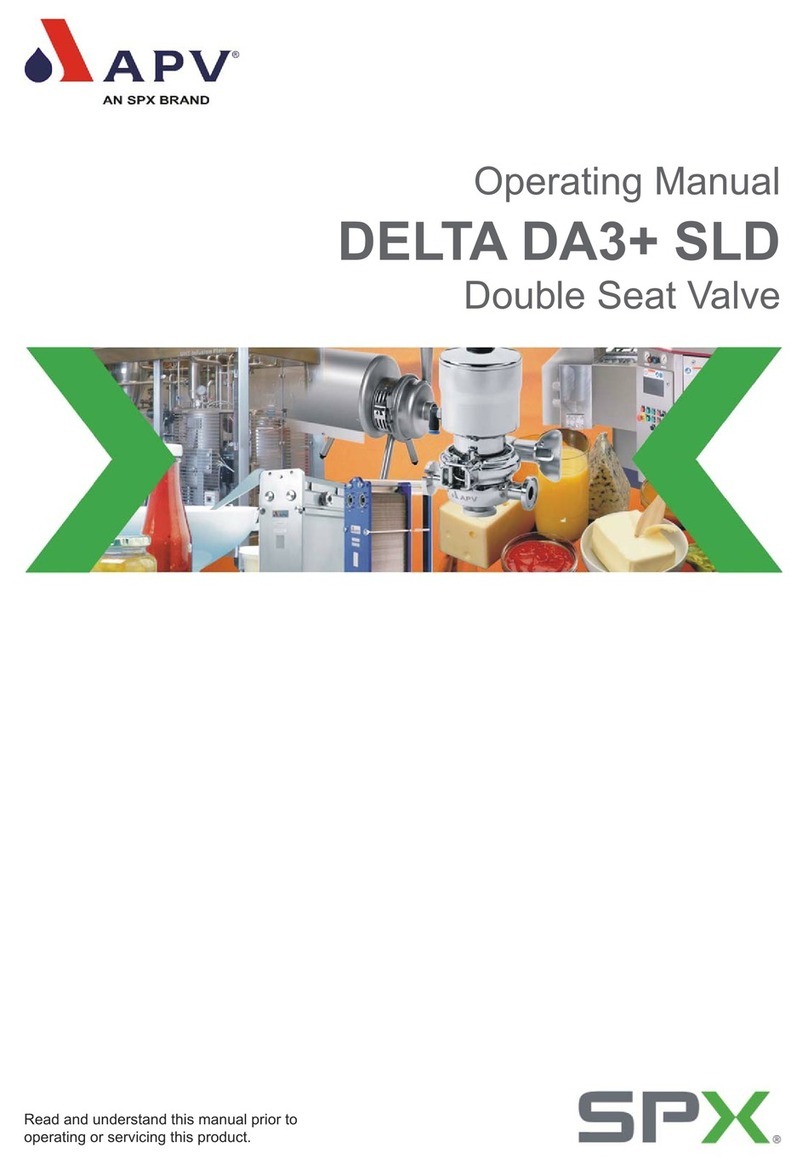
APV
APV DELTA DA3+ SLD User manual

APV
APV SPX DELTA DKR2 User manual
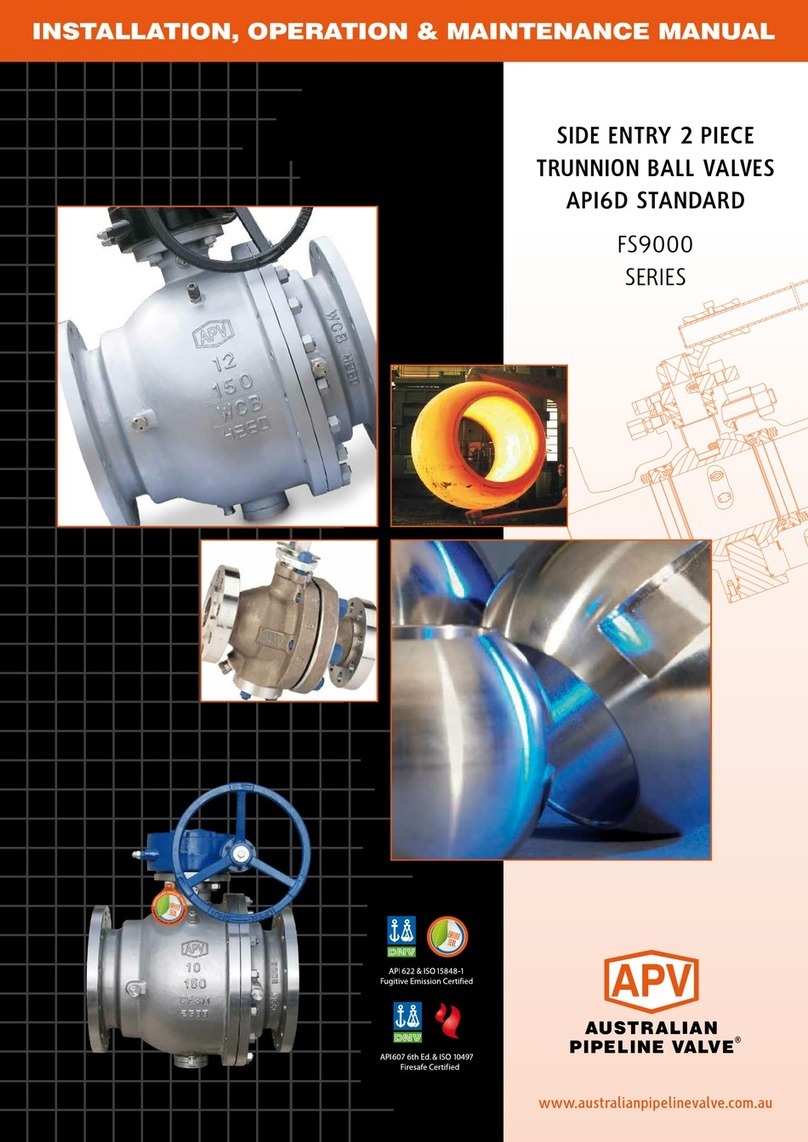
APV
APV FS9000 Series Instruction manual
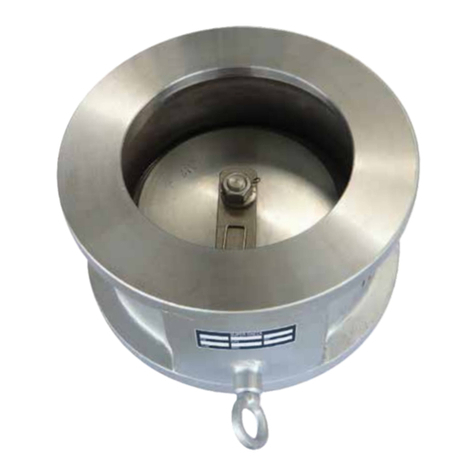
APV
APV SLP Instruction manual
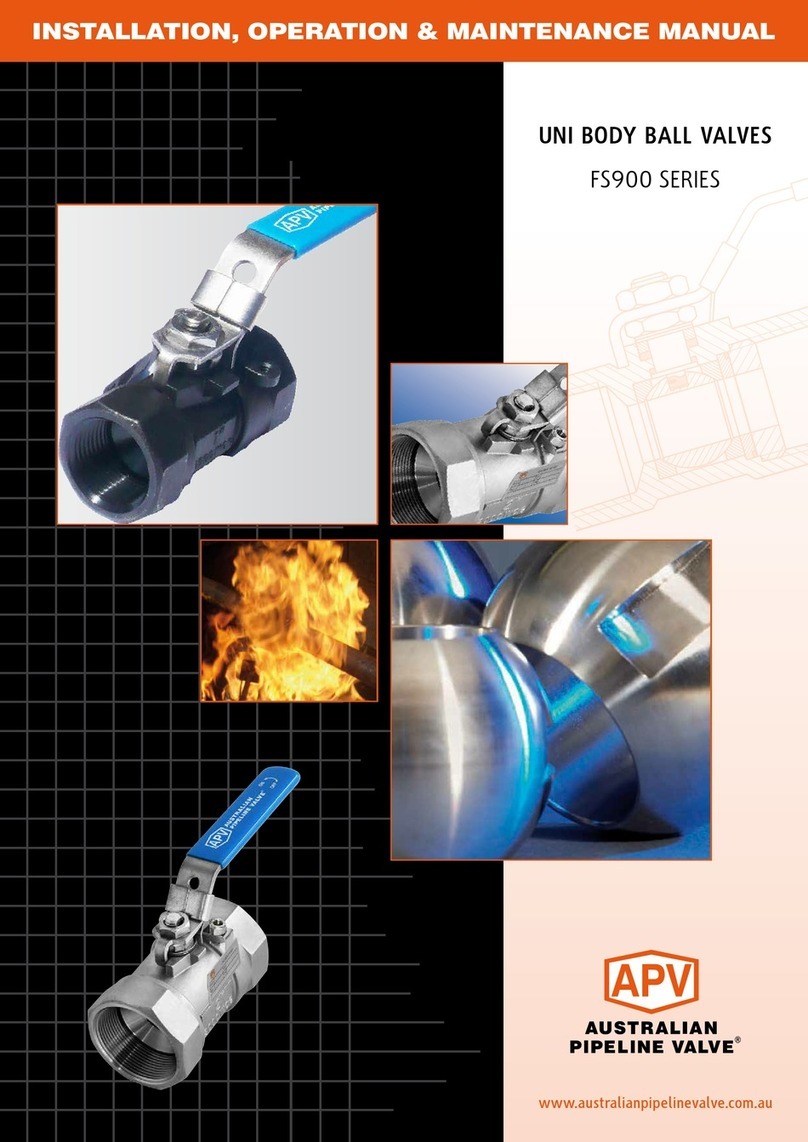
APV
APV FS900 Series Instruction manual
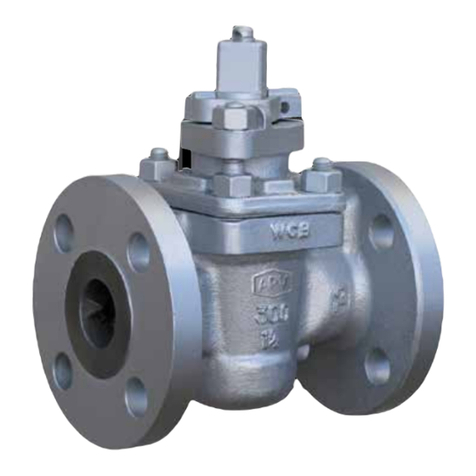
APV
APV SAPM User manual
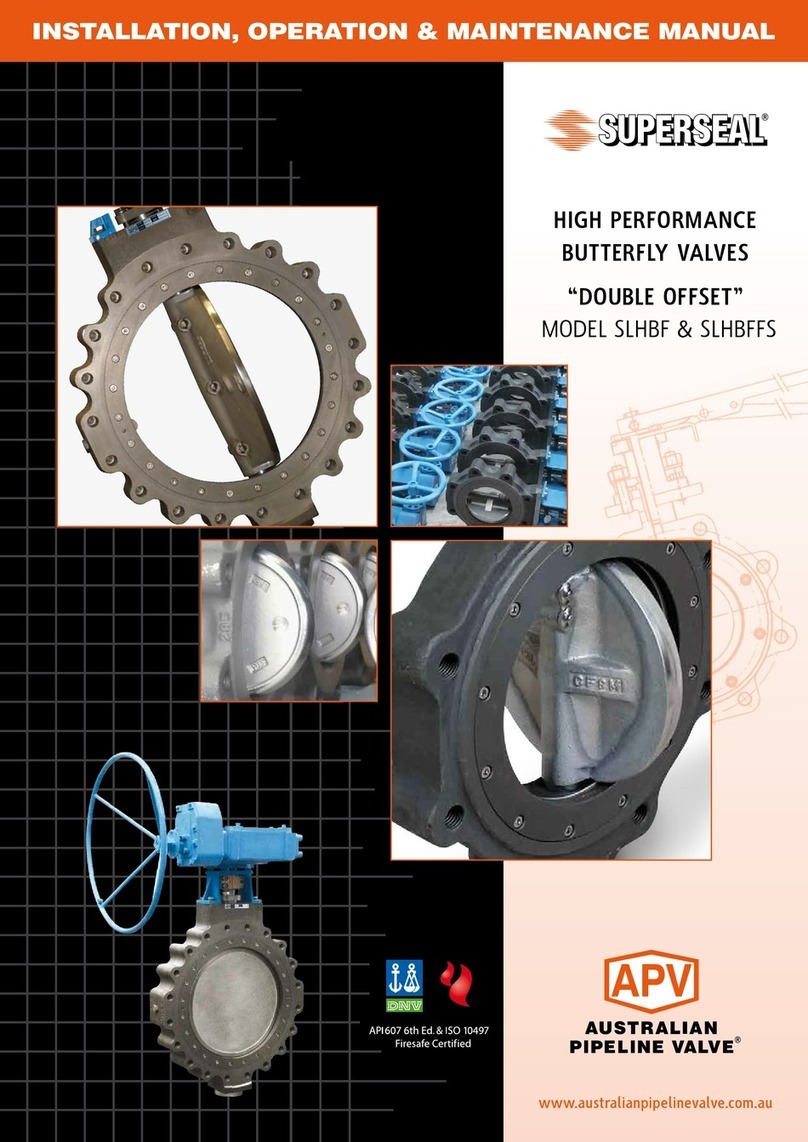
APV
APV Superseal SLHBF Instruction manual
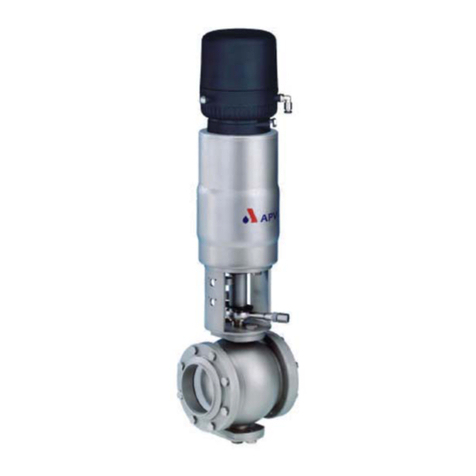
APV
APV SPX DELTA DKR2 User manual
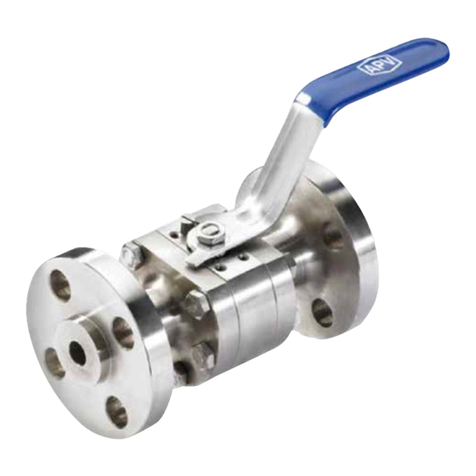
APV
APV BV100 Series Instruction manual
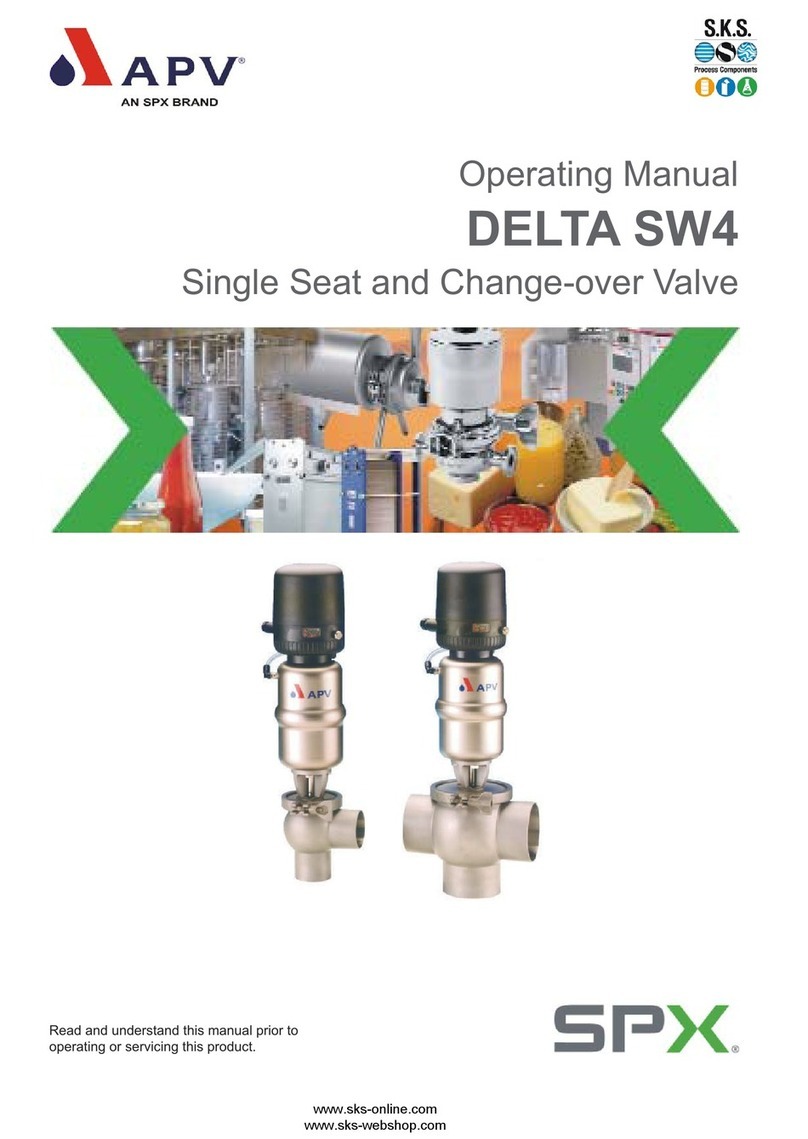
APV
APV DELTA SW4 User manual
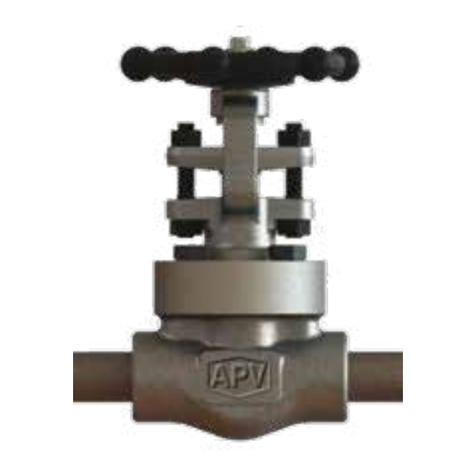
APV
APV GLPSNP250AUNF-F Instruction manual