ARMANO RCh series User manual

www.armano-messtechnik.com
Operating Instructions Pressure Gauges
Selection Criteria, Measuring Arrangements, Installation and Operation Manual
B00-100
09/22
1. Information on This Operating Instruction
• The manual is aimed at specialists and semi-skilled
personnel.
• Please read the instructions carefully before carry-
ing out any operation and keep the specied order.
• Thoroughly read and understand the information in
chapter 2 “Safety Instructions”.
If you have any problems or questions, please contact
your supplier or contact us directly at:
ARMANO Messtechnik GmbH
Location Beierfeld
Am Gewerbepark 9 •08344 Grünhain-Beierfeld
Tel.: +49 3774 58 – 0 •Fax: +49 3774 58 – 545
mail@armano-beierfeld.com
Location Wesel
Manometerstraße5 •46487 Wesel-Ginderich
Tel.: +49 2803 9130 – 0 •Fax: +49 2803 1035
Contents
1. Information on This Operating Instruction 1
1.1 Pictographs Used 2
1.2 Exclusion of Liability 2
1.3 General Information 2
2. Safety Instructions 2
3. Device Description 3
3.1 Resilient Elements, Construction Types of
Pressure Gauges and Chemical Seals 3
3.1.1 Resilient Elements 3
3.1.2 Construction Types Pressure Gauges 4
3.1.3 Construction Types Chemical Seals 5
4. Selection Criteria 5
4.1 Measuring Principles 5
4.2 Pressure Ranges 6
4.3 Error Limits 6
4.4 Operating Conditions 6
4.4.1 Medium Properties, Pressure Prole 6
4.4.2 Ambient Conditions 7
5. Additional Accessory 8
6. Measuring Arrangements 9
7. Installation 10
8. Intended Use 11
9. Electrical Accessories 12
10. Installation in Potentially Explosive Areas 13
10.1 General Information 13
10.2 Marking for the Explosion Hazardous Area 13
11. Maintenance/Cleaning, Handling and
Transport, Storage 14
12. Dismounting and Disposal 14
13. CE Conformity 15
14. Declarations of Conformity 16

B00-100•B1•09/22•GB •p. 2 of 20•www.armano-messtechnik.com
Operating Instructions Pressure Gauges
Selection Criteria, Measuring Arrangements, Installation and Operation Manual
1.1 Pictographs Used
In this manual, pictographs are used as hazard warnings.
Particular information, instructions and restrictions
designed for the prevention of personal or substantial
property damage:
WARNING! Is used to warn you against an
imminent danger that may result in personal
injury or death.
IMPORTANT! Is used to warn you against a
possibly hazardous situation that may result in
personal, property or environmental damage.
CAUTION! Is used to draw your attention
to important recommendations to be ob-
served. Disregarding them may result in
property damage.
Passages in the text containing explana-
tions, information or advice are highlight-
ed with this pictograph.
The following symbol highlights
actions you have to conduct
or
instructions that have to be strictly observed.
1.2 Exclusion of Liability
We accept no liability for any damage or malfunction
resulting from incorrect installation, inappropriate use
of the device or failure to follow the instructions in this
manual.
1.3 General Information
Please inspect the transport packaging and the deliv-
ered items immediately upon their receipt to deter-
mine their integrity and completeness.
You have purchased an instrument that was manufac-
tured according to high quality standards in our com-
pany, which is certied according to DIN ISO 9001.
The following manual was composed with due care. It
is not possible, however, to take into account all ver-
sions and possible cases of application in this operat-
ing instruction. If you have any questions regarding a
special application, instruments, storage, mounting,
operation or diculties, please contact us as manufac-
turer or the distributor.
Please support us in improving this operating instruc-
tion. We will gladly accept your advice.
2. Safety Instructions
IMPORTANT! Disregarding the respective
regulations may result in severe personal
injuries and / or property damage.
Please read this operating instruction thoroughly be-
fore installing the device.
Disregarding the containing warnings, especially the
safety instructions, may result in danger for people,
the environment, and the device and the system it is
connected to.
The device corresponds with the state of engineering
at the time of printing. This concerns the accuracy, the
operating mode and the safe operation of the device.
In order to guarantee that the device operates safely,
the operator must act competently and be conscious
of safety issues.
The ARMANO Messtechnik GmbH provides support
for the use of its products either personally or via rele-
vant literature. The customer veries that our product
is t for purpose based on our technical information.
The customer performs customer and application
specic tests to ensure that the product is suitable for
the intended use. With this verication, all hazards and
risks are transferred to our customers. Our warranty
expires in case of inappropriate use.

www.armano-messtechnik.com•p. 3 of 20•GB •09/22•B1•B00-100
Operating Instructions Pressure Gauges
Selection Criteria, Measuring Arrangements, Installation and Operation Manual
Qualied personnel:
• The personnel that is charged for the installation, op-
eration and maintenance of the instrument must hold
a relevant qualication. This can be based on training
or relevant tuition. The personnel must be aware of
this manual and have access to it at all times.
• The electrical connection shall be carried out by a
fully qualied electrician only.
General safety instructions:
• In all work, the existing national regulations for ac-
cident prevention and safety at the workplace must
be complied with. Any internal regulations of the op-
erator must also be complied with, even if these are
not mentioned in this manual.
• Use the instrument in its perfect technical condition
only. Damaged or defective instruments need to be
checked immediately and replaced if necessary.
• Only use appropriate tools for mounting, connect-
ing and dismounting the device.
• Nameplates or other information on the device shall
neither be removed nor obliterated, since otherwise
any warranty and manufacturer responsibility expires.
• In order to ensure measurement accuracy and du-
rability of the instrument and to avoid damage, the
limit values indicated in the technical data have to
be observed.
• In case of visible damage or malfunctions, the in-
strument must be put out of operation immediately.
• Excessive heat (e.g. during or after external re),
especially on soldered joints, may cause leakage of
the medium, which in turn can cause serious haz-
ards. After an external re, all instruments have to
be checked before recommissioning the system
and have to be replaced if necessary.
Special safety instructions:
Warnings, which are specically relevant to individual
operating procedures or activities, are to be found at
the beginning of the relevant sections of this operating
instruction.
3. Device Description
The information provided in this operating instruction,
concerning selection, application, measuring arrange-
ments, installation and operation, applies to pressure
measuring instruments with an elastic measuring
element.
3.1 Resilient Elements, Construction Types of
Pressure Gauges and Chemical Seals
3.1.1 Resilient Elements
Resilient elements with Bourdon tube:
resilient element with resilient element with
Bourdon tube in c-form Bourdon tube in helical form
Resilient elements with diaphragm:
horizontal vertical
Resilient elements with diaphragm capsule:

B00-100•B1•09/22•GB •p. 4 of 20•www.armano-messtechnik.com
Operating Instructions Pressure Gauges
Selection Criteria, Measuring Arrangements, Installation and Operation Manual
3.1.2 Construction Types Pressure Gauges
Pressure gauge with c-form Bourdon tube:
pointer
dial
pointer shaft
stem
(socket)
spring
of the movement
toothed segment
tip of the
Bourdon tube
zero stop pin
link
movement plate
overload
protection
process connection
(here) radial bottom
connection
Bourdon tube
link screw
Pressure gauge with diaphragm capsule:
process
connection
(here) centre back connection
diaphragm capsule
pointer
movement
dial
Pressure gauge with horizontal diaphragm:
horizontal
diaphragm
connecting
rod
lower ange
dial
pointer
toothed
segment
pointer shaft
upper
ange
process connection
radial bottom connection
Pressure gauge with vertical diaphragm:
vertical
diaphragm
process connection
(here) bottom
connection
pointer
dial
transfer lever
movement
Pressure gauges for safety requirements according to DIN EN 837-1, S3 (former DIN 16006 part 1 and 2):
bayonet ring
blow-out back case with break-
proof solid front window made of
laminated safety
glass

www.armano-messtechnik.com•p. 5 of 20•GB •09/22•B1•B00-100
Operating Instructions Pressure Gauges
Selection Criteria, Measuring Arrangements, Installation and Operation Manual
3.1.3 Construction Types Chemical Seals
diaphragm seal capsule seal in-line seal
4. Selection Criteria
The user has to ensure that the proper pressure meas-
uring instrument is selected regarding indication range
and version (e.g. resistance of the materials against
medium, atmosphere and temperature, overrange pro-
tection). The regulations applying to the particular ap-
plication as well as DIN EN 837-2 have to be regarded.
4.1 Measuring Principles
The pressure measuring instruments, described in this
operating instruction, contain measuring elements,
which deform elastically when subjected to pressure.
This motion is transferred to a movement. Due to their
robustness and easy handling, these instruments
(pressure gauges) are widely used in technical pressure
measurement. The measuring elements are generally
made of copper alloys or alloyed steels.
Bourdon tube pressure measuring instruments:
Bourdon tubes are circular bent tubes with an oval
cross-section. The pressure to be measured acts on the
inside of the tube, which results in the oval cross-section
becoming almost circular. Due to the curvature of the
tube, hoop stresses occur, which bend the Bourdon
tube. The end of the Bourdon tube, which is not xed,
performs a motion, which is a measure for the pressure.
For pressure ranges up to 40 bar, generally circular bent
Bourdon tubes with a torsion angle of 270° are used.
For higher pressure ranges, helical Bourdon tubes with
several torsions are applied.
Bourdon tubes have a relatively low restoring force.
When using additional accessories, such as drag indica-
tors, limit switch contact assemblies or potentiometric
transducers, therefore their inuence on the indication
has to be taken into account.
Bourdon tube resilient elements can only be protected
against overload to a limited extent by supporting the
measuring element at a specic pressure limit value.
Bourdon tube pressure gauges are applied for pressure
ranges from 0.6 bar to 4000 bar, mostly with accuracy
classes 0.6 to 2.5.

B00-100•B1•09/22•GB •p. 6 of 20•www.armano-messtechnik.com
Operating Instructions Pressure Gauges
Selection Criteria, Measuring Arrangements, Installation and Operation Manual
The inuence of temperature changes on the indication
mainly depends on the temperature coecient of the
modulus of elasticity of the Bourdon tube.
Depending on the material used, the temperature-related
error is between 0.3 % and 0.4 % per 10 K.
Diaphragm pressure gauges:
Diaphragms are circularly shaped corrugated mem-
branes. The pressure to be measured acts on one side
of the diaphragm. The deection of the diaphragm is a
measure for the pressure. Diaphragms have a relatively
high restoring force. Therefore, the inuence of addi-
tional accessories is lower compared to Bourdon tube
pressure gauges. Due to the annular xing arrangement
of the diaphragm, they are less sensitive to vibrations.
Diaphragms can be protected against high overload
by supporting the measuring element. They can be
protected against corrosive media by applying coatings
or foils. Diaphragm pressure gauges are also favourable
for highly viscous or crystallising media, since wide
connection bores, open connection anges or ushing
orices allow for cleaning options.
There are pressure gauges with horizontal diaphragm
and pressure gauges with vertical diaphragm, i.e. the
diaphragm is placed parallel to the dial. For pressure
ranges <0.6 bar, generally diaphragms with a diameter
of 160 mm are used, whereas for higher pressure ranges
diaphragms with a diameter of 100 mm are used. Due
to the annular xing arrangement of the diaphragm, the
indication deviation caused by temperature changes is
signicantly higher compared to Bourdon tube pressure
gauges. Diaphragm pressure gauges are applied for
pressure ranges from 10 mbar to 25 bar with accuracy
classes of 1.6 and 2.5, rarely also of 4.0.
Capsule gauges for low pressure:
A diaphragm capsule consists of two circularly shaped
corrugated membranes or a membrane and a base
plate, which are assembled pressure-tight at the edge.
The measurement pressure is passed into the centre of
one of the membranes and acts onto the inside of the
diaphragm capsule. The lifting movement generated
hereby is a measure for the pressure.
Capsule gauges for low pressure are not suitable for
liquid media.
They can be applied for pressure ranges from 2.5 mbar
to 600 mbar with accuracy classes from 0.6 to 1.6.
The indication deviation caused by temperature chang-
es can be between 0.3 % and 0.4 % per 10 K, depending
on the material.
4.2 Pressure Ranges
The operating pressure should be within the middle
third of the pressure range specied for the pressure
gauge. The maximum pressure load should not exceed
75 % of the full scale value at steady load or 65 % of the
full scale value at dynamic load (DIN EN 837-2).
4.3 Error Limits
The error limits for pressure measuring instruments are
dened in DIN EN 837-1 (Bourdon tube pressure gaug-
es) and DIN EN 837-3 (capsule gauges and diaphragm
pressure gauges).
• Pressure measuring instruments with classes 0.1
to 0.6 and higher are preferably used in laboratories
and workshops for precise measurements.
• Pressure measuring instruments with classes 1.0
and 1.6 are used for measurements on machines
and in production facilities.
• Pressure measuring instruments with classes 2.5
and 4.0 are used for monitoring tasks without spe-
cial accuracy requirements.
4.4 Operating Conditions
When selecting pressure measuring instru-
ments, attention should be paid on the se-
lection criteria and installation recommen-
dations according to DIN EN 837-2 as well
as the information provided in this manual
(chapters 4.4.1, 4.4.2 and 6.). The appli-
cation of pressure measuring instruments
that are not suited for the actual operating
conditions may cause considerable conse-
quential damage.
4.4.1 Medium Properties, Pressure Prole
CAUTION! Material damage!
Rapid pressure changes or pressure strokes
must not act abruptly on the measuring ele-
ment. Pressure strokes must not exceed the
pressure limits of the pressure measuring
instruments.
If required, upstream overload protection devices
(chapter 5 “Additional Accessory”) shall be provid-
ed. Pressure changes of >10 % of the full scale values
per second impair the reading of the measured values.
Moreover, this severely reduces the service life of the
devices. In such cases, attenuators must be provided.

www.armano-messtechnik.com•p. 7 of 20•GB •09/22•B1•B00-100
Operating Instructions Pressure Gauges
Selection Criteria, Measuring Arrangements, Installation and Operation Manual
With snubber devices (restrictor screw or adjustable
snubber), the inlet cross-section is signicantly re-
duced. This results in a delay of the pressure change
in the measuring element. The installation of a throttle
section (reduction of the measuring line cross-sec-
tion) is also possible. In both cases, the susceptibility
to contamination is disadvantageous. Attenuators on
the movement only decelerate the pointer motion. Liq-
uid lled cases dampen the motion of the measuring
element and reduce the wear of moving components.
Temperature:
If the medium temperature at the measuring
point deviates from the permissible operat-
ing temperature of the pressure measuring
instrument (chapter 8 “Intended Use” as
well as DIN EN 837-1, -2, -3), a measuring line
with sucient length, a siphon or a chemical
seal with capillary line must be connected
upstream to the pressure gauge. The inu-
ence on the indication due to instrument
temperatures deviating from +20 °C (+68 °F)
has to be regarded.
Highly viscous, crystallising or solid-containing
media:
For the pressure measurement of highly vis-
cous, crystallising or solid-containing media,
diaphragm pressure gauges or Bourdon tube
pressure gauges with attached chemical
seal (chapter 5 “Additional Accessory”)
are recommended.
Corrosive media:
If corrosive media can be kept away from the meas-
uring element by separating agents, standard devices
may be used.
Otherwise, the selection of the suitable mate-
rial is mandatory, whereas the operator has to
provide the manufacturer with any informa-
tion concerning the materials that are com-
patible with the medium under the specic
measuring conditions (DIN EN 837-2, 4.3).
Due to the limited choice of materials for the
elastic elements, diaphragm pressure gaug-
es with a protective lining might to be used,
or chemical seals made of media resistant
materials need to be connected upstream to
a Bourdon tube pressure gauge.
Safety:
A higher risk exists, for example, with gases or liquids
under high pressure. In case of leakage or bursting of
pressure-retaining components, employees standing in
front of the window of the device, must not be endan-
gered by medium emerging to the front. Safety pressure
gauges with a blow-out device at the rear side, e.g. a
blow-out back, provide for protection (chapter 3.1.2).
For hazardous media, such as
• oxygen
• acetylene
• combustible substances
• toxic substances
as well as for refrigerating units, compressors etc., the
applicable regulations have to be regarded.
CAUTION!
In accordance with DIN EN 837-1, 9.7, liquid
lled pressure gauges must be equipped
with blow-out devices (version S1, S2 or S3
according to DIN EN 837-1).
4.4.2 Ambient Conditions
Vibrations:
If vibrations of the pressure gauge cannot
be eliminated by appropriate installation,
devices with movement attenuation or liquid
lling should be used.
Ambient temperature:
The error limit given on the dial applies at a
reference temperature of +20 °C (+68 °F). De-
viating temperatures have an inuence on
the indication.
The extent of the inuence depends on the measuring
principle (chapter 4.1).
At outdoor installations, the prevailing ambient condi-
tions must be taken into account by selection or pro-
tection, e.g. to prevent the pressure gauge from freez-
ing over at temperatures below 0 °C (+32 °F). In liquid
lled instruments, the viscosity of the uid increases
as the ambient temperature drops – causing a consid-
erable indication delay.
The ambient temperature must also be taken into ac-
count regarding the maximum permissible operating
temperature specied for the device.

B00-100•B1•09/22•GB •p. 8 of 20•www.armano-messtechnik.com
Operating Instructions Pressure Gauges
Selection Criteria, Measuring Arrangements, Installation and Operation Manual
Corrosive atmosphere:
In corrosive atmospheres, suitable casings
and components made of resistant materi-
als must be provided.
Special surface treatments serve as exterior
protection.
5. Additional Accessory
Shut-o valves for pressure gauges:
It is recommended to install a shut-o de-
vice between measuring point and pressure
gauge, which allows for an exchange of
the pressure gauge and a zero point check
while the system is running. Depending on
the intended application, either cocks or
valves are used.
Cocks have three positions:
• Ventilation:
The feed line is closed, the measuring element
is open to the atmosphere. The zero point can be
checked.
• Operation:
The feed line is open, the measuring element is
pressurised.
• Blow-out:
The feed line is open, the medium is vented to the
atmosphere. The measuring element is not in use.
For valves (e.g. according to DIN 16270 and DIN 16271),
a vent screw is usually provided between valve seating
and pressure gauge.
IMPORTANT! Ventilation to the atmos-
phere shall be arranged in a way that em-
ployees are not endangered by escaping
medium.
Potential environmental damage is to be
avoided. In certain applications (e.g. steam
boilers), the shut-o valves require a test
connection, so that the pressure measuring
instrument can be checked without being
disassembled.
Gauge holder bracket:
A suitable gauge holder is to be provided if
the measuring line is not rigid enough for
a vibration-free installation of the pressure
measuring instrument.
Siphons:
Use measuring lines with an adequate
length or siphons to protect the shut-o
valves and the pressure gauges against
heating due to hot media (e.g. steam).
Chemical seals:
For aggressive, hot, highly viscous or crys-
tallising media, which must not enter the
pressure element, chemical seals can be
mounted to Bourdon tube pressure gauges
to provide separation.
For transmission of the pressure to the pressure el-
ement, a neutral liquid is used, which is chosen to
match the measuring range, temperature, viscosity
and other inuences by taking into account the com-
patibility of this liquid with the medium.
Chemical seals are available in various construction
types (chapter 3.1.3 “Construction Types Chemical
Seals”), whereas the diaphragm seal is the most com-
monly used model.
For in-line seals and ange type chemicals seals, the
pressure gauge has to be mounted to the chemical
seal by the manufacturer in accordance with the given
installation position.
The connection between pressure gauge and chemi-
cal seal must not be separated.
Potential errors, inuenced by mounting a chemical
seal to a pressure gauge have to be regarded.
Overrange protection devices:
CAUTION! If the indication range has to
be lower than the maximum operating
pressure due to operational reasons, the
pressure gauge can be protected against
damage by tting an overrange protection
device.
In the event of a pressure stroke, the protection device
closes instantly. If the pressure rises slowly, it closes
gradually. The closing pressure to be set thus depends
on the temporal pressure prole.
However, highly viscous and contaminated media might
impair or disable the function of the protection device.
Capsule gauges and diaphragm pressure gauges can
also be produced overrange protected (3-fold, 5-fold
or 10-fold).

www.armano-messtechnik.com•p. 9 of 20•GB •09/22•B1•B00-100
Operating Instructions Pressure Gauges
Selection Criteria, Measuring Arrangements, Installation and Operation Manual
6. Measuring Arrangements
General remarks:
Proven arrangements for pressure measurement and suggestions for component parts are specied in
VDE/VDI 3512 sheet 3. The following table gives an overview on the possible measuring arrangements:
State of the medium liquid gaseous
State of the lling
in the measuring line liquid partly
gas emitting
completely
gas emitting gaseous
partly
condensed
(moist)
completely
condensed
Examples condensate boiling
liquids
“liquid
gases” dry air moist air
ue gases steam
a) Pressure gauge higher
than measuring port
123456
b) Pressure gauge lower
than measuring port
7 8 9 10 11
The arrangements 3, 4, 5, 7, 8 and 11 are to be preferred.
Measuring line:
The measuring line is the connection be-
tween measuring port and pressure gauge.
The inner diameter of the line should be
large enough to avoid plugging.
The measuring line should be installed with a steady
incline (1:15 is recommended). If the medium is gas-
eous, a drain should be provided at the lowest point.
If the medium is a highly viscous liquid, a vent should
be provided at the highest point. If the gases or liquids
contain solids, separators should be provided, which
can be disconnected from the assembly by shut-o
valves and emptied during operation. The measuring
line should be arranged and tted in a way that it can
withstand stresses caused by expansion, vibration or
the inuence of heat.
Pressure measuring port:
The pressure measuring port should be ar-
ranged at a position with unimpaired ow
and consistent measuring conditions. It
is recommended to choose a suciently
large orice for the pressure measurement
and to close the measuring port with a
shut-o device.

B00-100•B1•09/22•GB •p. 10 of 20•www.armano-messtechnik.com
Operating Instructions Pressure Gauges
Selection Criteria, Measuring Arrangements, Installation and Operation Manual
Shut-o valves at the pressure gauge:
Shut-o valves at the pressure measuring instrument
serve to check the zero point or to exchange the meas-
uring instrument during operation (chapter 5 “Addi-
tional Accessory”).
Pressure measuring instrument:
The pressure measuring instrument needs
to be mounted vibration-free and positioned
for easy readability.
Parallax errors are to be avoided when reading the
dial. It has to be ensured that any blow-out devices
on the pressure gauge are protected against blocking
(DIN EN 837-1, 9.7). The pressure gauge shall be ar-
ranged in a way that the temperature does not fall be-
low or exceed the permissible operating temperature
(chapter 4.4 “Operating Conditions” and chapter 8
“Intended Use”). Here, the inuence of convection
and thermal radiation has to be regarded. If the meas-
uring element of a pressure gauge is lled with water
or a water mixture, the instrument has to be protected
against freeze. The pressure gauge is generally mount-
ed with vertical dial. In all other cases, the position
symbol on the dial according to DIN EN 837 applies.
A height dierence between measuring port and
pressure gauge causes a shift of the measuring
start value if the medium in the measuring line does
not have the same density as the ambient air. This
shift of the measuring start ∆p results from the den-
sity dierence (ρM−ρL) and the height dierence
Δh: 10-5 ·(ρM − ρL) g · Δh
∆ = shift of measuring start [bar]
ρM = density of the medium [kg / m³]
ρL = density of the air (1.205 at 20 °C) [kg / m³]
∆h = dierence in height [m]
g = gravitational acceleration [m/s²]
(medium gravitational acceleration 9.81 m/s²)
The indication is decreased by ∆p if the pressure
gauge is positioned higher than the pressure measur-
ing port, and increased by ∆p if it is positioned lower.
7. Installation
The mounting of pressure measuring instruments
shall be carried out by qualied personnel only.
For the measuring arrangements, please refer to chap-
ter 6.
During installation or removal, the pressure gauge
should never be held at the case, but at the wrench
at of the socket.
It must be ensured that the matching pro-
cess connection has been selected (nominal
width, if required, suitable sealing face etc.).
For instruments with thread connection, an installation
with clamping sleeve or union nut is recommended, in
order to position it for proper readability. Instruments
with ange connections are tted to the counter ange
and secured with suitable screws. It must be ensured
that the screws are rmly tightened.
The connections need to be leaktight. Therefore,
sealings made of suitable medium-resistant material
should be used for the connection. For the sealing
of pressure measurement connections with cylindri-
cal thread spigots, e.g. at sealing rings according to
DIN EN 837-1, prole packings or lens-type sealing
rings for corresponding high pressure connections
have to be applied at the sealing face. Conical threads
(e.g. NPT threads) are sealed with additional sealing
materials such as PTFE tape (DIN EN 837-2).
sealing face
wrench at
sealing in
the thread
cylindrical threads conical threads

www.armano-messtechnik.com•p. 11 of 20•GB •09/22•B1•B00-100
Operating Instructions Pressure Gauges
Selection Criteria, Measuring Arrangements, Installation and Operation Manual
For pressure gauges with pressure ranges of ≤6 bar
and pressure relief vent Ø 13 mm (0.51") at the top of
the case, it is recommended to cut o the nipple on
the lling plug in order to allow for internal pressure
compensation by venting the pressure gauge.
If the pressure gauge is positioned lower than the
pressure measuring port, the measuring line should
be rinsed thoroughly before putting into operation to
remove any foreign objects.
During pressure tests on pipes and vessels, no pres-
sure higher than indicated on the dial by the maximum
value mark must be applied to the pressure gauge
and the specied application limit at steady load must
not be exceeded (chapter 8 “Intended Use”).
For diaphragm pressure gauges, the clamping bolts
for the upper and lower ange must not be loosened.
For instruments with attached chemical seal, the con-
nections between pressure gauge and chemical seal
and, if applicable, between chemical seal and capillary
line must not be loosened.
IMPORTANT! Before dismounting the
pressure gauge, the measuring unit has to
be depressurised.
If necessary, the measuring line needs to be
relieved. Medium residues in dismounted
pressure gauges might endanger person-
nel, facilities and the environment. Adequate
precautionary measures shall be taken.
8. Intended Use
CAUTION! Shut-o devices shall only be
opened slowly in order to avoid sudden
pressure strokes during commissioning.
Application range:
On many pressure measuring instruments, the ap-
plication range for steady loads is indicated on the
dial by the maximum value mark (DIN EN 837-1,
DIN EN 837-3).
At steady load, the Bourdon tube pressure gauges with
nominal case size 100, 160 and 250 are loadable up
to the full scale value. At dynamic load, only 0.9 times
of this pressure is permissible as peak load, for the
pressure ranges 0/2500 bar and 0/4000 bar max. ⁄ of
the full scale value. Bourdon tube pressure gauges are
overrange protected up to 1.3 times the full scale value
(0/2500 bar and 0/4000 bar instruments can only be
loaded up to their full scale value!).
At steady load, the Bourdon tube pressure gauges
with nominal case size 40, 50, 60, 63, 80 and 72x72 are
loadable up to ⁄ of the full scale value, at dynamic load
up to max. ⁄ of the full scale value and only temporar-
ily to the full scale value.
At steady load, diaphragm pressure gauges with verti-
cal diaphragm are loadable up to the full scale value, at
dynamic load up to 0.9 times the full scale value.
Diaphragm pressure gauges with horizontal dia-
phragm are overrange protected up to 5 times the full
scale value (custom-made instruments also higher),
but never higher than 40 bar.
At steady load, capsule gauges for low pressure are
loadable up to the full scale value, at dynamic load max-
imum up to 0.9 times the full scale value. Just as Bour-
don tube pressure gauges, they are 1.3-times overrange
protected (custom-made instruments also higher).
Zero point check:
In order to check the zero point of the pressure gauge
during operation, the shut-o device, required for this
purpose (chapter 5 “Additional Accessory”), will
be shut and the pressure gauge will be relieved. The
pointer must be positioned within the zero range in-
dicated by .
If the pointer remains outside of this range, this gen-
erally results from a lasting deformation of the meas-
uring element, which needs to be submitted for a
closer examination in order to avoid accidents due to
measuring errors. In such a case, the device should be
replaced and, if required, returned to the manufacturer
for checking and repair.

B00-100•B1•09/22•GB •p. 12 of 20•www.armano-messtechnik.com
Operating Instructions Pressure Gauges
Selection Criteria, Measuring Arrangements, Installation and Operation Manual
Indication check:
If a check of the indication during operation is neces-
sary, the pressure gauge is separated from the process
via the required shut-o device with test connection
(chapter 5 “Additional Accessory”) and pressurised
with test pressure. The error limits according to DIN
EN 837-1 and DIN EN 837-3 apply.
Temperature resistance:
The permissible operating temperatures of
the pressure gauge must not be exceeded.
The temperature resistance or the permissible oper-
ating temperature generally is between max. −40 °C to
+60 °C (DIN EN 837-1 and DIN EN 837-3), whereas
unlled gauges with brazed Bourdon tube can with-
stand medium temperatures up to +100 °C and stainless
steel cases with shielded arc welding Bourdon tube can
withstand medium temperatures up to +200 °C.
Special versions with corresponding dial inscription
(tA/tR) might be suitable for higher temperatures.
Please note: these are only specications
concerning the temperature resistance of
the materials as well as the soldered joints
or weld seams. The specications concern-
ing indication errors due to deviations from
the reference temperature are to be regard-
ed! Detailed information can be found in
our model overview 1000 for Bourdon tube
pressure gauges.
Cleaning temperature:
During rinsing of the measuring line, the
permissible operating temperature of the
pressure gauge (see above) must not be
exceeded.
If necessary, the device needs to be shut-o or re-
moved. For pressure gauges with attached chemical
seals, the maximum cleaning temperature tRmust not
be exceeded.
9. Electrical Accessories
The mounting and the electrical connection shall be
carried out by qualied personnel only.
Instruments with electrical accessories are marked
with a nameplate, which indicates how the electric
connection has to be carried out.
It is necessary to regard the load limits. Exceeding the
load limits might cause damage.
The national and international safety regulations (e.g.
VDE 0100) have to be regarded during installation,
commissioning and operation of the instruments.
It must be ensured that the cable diameters match the
nominal widths of the sealing inserts. Screw ttings
must be tightened rmly. Only then compliance with
certied degrees of protection can be ensured. In
versions with angular plug, plug connector or termi-
nal box, the centrally arranged xing screws must be
tightened hand-tight.
For the connection of pressure transmitters DMU,
only shielded cable has to be used to ensure electro-
magnetic compatibility (EMC). The shield has to be
connected to the case or the ground terminal of the
angular plug.
Please regard that the CE mark according to the EMC
directive for instruments with magnetic contact only
applies, when the frequency of operation does not ex-
ceed 5 switching cycles per minute.
If specied, suitable switch ampliers or multifunc-
tional relays have to be used (e.g. for instruments with
inductive contact). The valid operating requirements
have to be regarded.

www.armano-messtechnik.com•p. 13 of 20•GB •09/22•B1•B00-100
Operating Instructions Pressure Gauges
Selection Criteria, Measuring Arrangements, Installation and Operation Manual
10. Installation in Potentially Explosive Areas
10.1 General Information
Pressure gauges are mechanical pressure measuring
instruments that do not have any potential ignition
sources during its intended operation. Versions made
of stainless steel with laminated glass are suitable for
the application in areas of category 2 and 3 according
to ATEX directive 2014/34/EU.
For the application in category 1 (e.g. installation to
zone 0), only pressure measuring instruments with
integrated, type-approved ame arrester, our model
Adapt FS, are suitable. This protection system avoids
ame penetration in case of deagrations of potential-
ly explosive vapour-air and gas-air mixtures of explo-
sion groups IIA, IIB and IIC in an upstreamed volume
of max. 0.2 l. The ame arrester “Adapt FS” is certied
with
II G IIC PTB 12 ATEX 4001 X
on condition that the operating pressure does not ex-
ceed 1.1 bar abs. and the operating temperature does
not exceed 60 °C (140 °F).
To avoid heating of the measuring elements of Bour-
don tube pressure gauges, dynamic load is not permis-
sible with gaseous media!
10.2 Marking for the Explosion Hazardous Area
Pressure gauges without limit switch contact assembly
are marked as follows for the application in explosion
hazardous areas.
Example:
Bourdon tube pressure gauge model RCh100 – 3,
manufacturer ARMANO Messtechnik GmbH
ARMANO Messtechnik GmbH
Manometerstraße 5 •46487 Wesel
Bourdon tube pressure gauge model RCh 100 – 3
II 2G Ex h IIC Gb
II 2D Ex h IIIC Db
Temperature range −25/+75 °C
(content obligatory, free layout)
The maximum temperature of +75 °C (+167 °F) was de-
termined as part of a “self-certification” with an addi-
tional safety of 10 K for the use in explosion hazardous
areas, which require temperature class T6.
Please observe the temperature specifications on the
nameplate to avoid hot surfaces due to increased am-
bient or medium temperatures.
Notwithstanding the above, for medium tempera-
tures TM≥75 °C, pressure gauge versions for combus-
tible substances, which may come into contact with
TM≥75 °C, are available. They can be marked accord-
ingly, the technical design remains unchanged.
If gas/air (dust/air) mixtures have a considerably
higher ignition point than TM, these would be such
substances. (Written conrmation of the operator with
description of the measuring point!)
Marking example for medium TM= 150 °C (302 °F)
II 2G Ex h IIC Gb
II 2D Ex h IIIC Db
Temperature range −25 / +150 °C (−13 / +302 °F)
Only for measuring point ###!
In that example, this allows for use in potentially ex-
plosive atmospheres, which require temperature class
T3 (maximum permissible surface temperature of the
equipment <200 °C (<392 °F)).
(The prerequisite is that the pressure gauge is general-
ly resistant to this temperature.)
Please contact the manufacturer in case of uncertainties.

B00-100•B1•09/22•GB •p. 14 of 20•www.armano-messtechnik.com
Operating Instructions Pressure Gauges
Selection Criteria, Measuring Arrangements, Installation and Operation Manual
11. Maintenance/ Cleaning, Handling and
Transport, Storage
CAUTION! Material damage and loss of
warranty!
Any modications or interventions in the
device, made by the customer, might dam-
age important parts or components. Such
intervention leads to the loss of any warran-
ty and manufacturer’s responsibility!
ÆNever modify the device or perform any
repairs yourself.
Maintenance:
Pressure measuring instruments are generally main-
tenance-free.
Repairs may only be executed by the manufacturer.
Cleaning:
Before returning an instrument for repair, the wetted
parts must be cleaned thoroughly, especially when
using hazardous media. The repair order should in-
clude a description of the medium or a declaration of
contamination.
Handling and transport:
Sensitive components!
The device contains sensitive components
and has to be handled with due care.
To prevent any impairment of the metrological proper-
ties, it is essential to protect the devices from mechan-
ical shocks or impacts during transport, installation
and operation. Special attention must be paid to the
following aspects:
• Do not throw or drop the device!
• Remove the devices carefully from their packaging.
• Avoid shocks caused by strong impacts on surfaces
or with objects.
• Please use a suitable packaging for the transport
(if possible, the original packaging) that adequately
protects the devices from shocks.
• Provide relevant transportation instructions on the
packaging.
Storage:
Please keep the pressure measuring instruments in
their original packaging until mounting and store them
protected against damage due to external inuences.
If a measuring instrument was removed (e.g. for test-
ing), it should be carefully placed back in its original
packaging for further storage.
In general, the storage temperature should not fall be-
low or exceed the temperature limitations of −40 °C
and +60 °C (DIN EN 837-1 and DIN EN 837-3).
12. Dismounting and Disposal
Before dismounting:
The instrument must be unpressurised before dis-
mounting! Please remove the instrument completely
from its application area.
Disposal:
NO DOMESTIC WASTE!
The instrument comprises various materi-
als. It shall not be disposed of together with
domestic waste.
ÆBring the device to your local recycling plant
or
Æsend the device back to your supplier or to the
ARMANO Messtechnik GmbH.

www.armano-messtechnik.com•p. 15 of 20•GB •09/22•B1•B00-100
Operating Instructions Pressure Gauges
Selection Criteria, Measuring Arrangements, Installation and Operation Manual
13. CE Conformity
The CE marking of the instruments certi-
es the conformity with prevailing EU di-
rectives for placing products on the market
within the European Union. The following
directive applies:
2014/68/EU (PED)
Pressure measuring instruments by ARMANO Mess-
technik GmbH with a pressure >0.5 bar are, dened
as pressure equipment parts, subject to the Pressure
Equipment Directive 2014/68/EU.
Our pressure measuring instruments according to
DIN EN 837-1 “Bourdon tube pressure gauges” re-
ceive the CE-marking in accordance to the conform-
ity assessment procedure if the upper range value is
200 bar and above.
Pressure gauges with ange connections > DN 25 or
1" or thread connection >1" receive the CE-marking if
the upper range value is 0.5 bar and above.
The CE-marking is placed on the outside of the case:
Pressure gauges with nominal case sizes 40, 50:
ASB 2020
NB 0045
Production Location Production Location
Grünhain-Beierfeld Wesel-Ginderich
Measuring instruments with a pressure range >0.5 bar
and <200 bar, which are subject to article 4 paragraph 3,
do not receive a CE-marking.
ASW 2020
NB 0045
Pressure gauges with nominal case sizes
63, 80, 100, 160, 250, 4⁄", 96x96, 144x144:
Measuring instruments with a pressure range >0.5 bar
and <200 bar, which are subject to article 4 paragraph 3,
do not receive a CE-marking.

B00-100•B1•09/22•GB •p. 16 of 20•www.armano-messtechnik.com
Operating Instructions Pressure Gauges
Selection Criteria, Measuring Arrangements, Installation and Operation Manual
14. Declarations of Conformity
EU Declaration of Conformity
EU-Konformitätserklärung
www.armano-messtechnik.de
abgegeben durch/by
Grünhain-Beierfeld, 2021-04-13
Bernd Vetter
Geschäftsführender Gesellschafter/Managing Director
Diese Erklärung wird verantwortlich für den Hersteller:
This declaration is issued under the sole responsibility of the manufacturer:
ARMANO Messtechnik GmbH
ARMANO Messtechnik GmbH
Standort Beierfeld
Am Gewerbepark 9
08344 Grünhain-Beierfeld
Tel.: +49 3774 58 – 0
Fax: +49 3774 58 – 545
Standort Wesel
Manometerstraße 5
46487 Wesel-Ginderich
Tel.: +49 2803 9130 – 0
Fax: +49 2803 1035
100 EU-Konformitätserklärung DGRL RM PM Di K Ausg. 04/21
Für die nachfolgend bezeichneten Erzeugnisse
ROHRFEDER-MANOMETER
Typ R…
PLATTENFEDER-MANOMETER
Ty p ( A) P…
DIFFERENZDRUCK- ODER DOPPEL-MANOMETER
Typ D(i)R…, DiK...
KAPSELFEDER-MANOMETER
Typ K…
wird hiermit bestätigt, dass sie den folgenden Normen entsprechen:
Sie werden gemäß den Bestimmungen folgender Richtlinie gefertigt:
RICHTLINIE 2014/68/EU DES EUROPÄISCHEN PARLAMENTS
UND DES RATES VOM 15. Mai 2014
zur Angleichung der Rechtsvorschriften der Mitgliedstaaten über
Druckgeräte – kurz: Druckgeräterichtlinie
Mit Messbereichen ab 200 bar oder Flanschanschlüssen ab
DN 25 und Messbereichen ab 0,5 bar fallen sie ihrer Art nach
unter „Druckhaltende Ausrüstungsteile“ und werden folgendem
Konformitätsbewertungsverfahren unterzogen:
Modul A2 „Interne Fertigungskontrolle mit
Überwachung der Abnahme”
Name & Anschrift der verantwortlichen Stelle, die unser Qualitäts-
sicherungssystem überwacht:
TÜV NORD Systems GmbH & Co. KG
Meidericher Straße 16
D-47058 Duisburg
Kennnummer: 0045
Die CE-Kennzeichnung erfolgt mittels Aufkleber auf dem Gehäuse.
We hereby declare for the following named goods
BOURDON TUBE PRESSURE GAUGES
Model R…
DIAPHRAGM PRESSURE GAUGES
Model (A)P…
DIFFERENTIAL OR DUPLEX PRESSURE GAUGES
Model D(i)R…, DiK...
CAPSULE PRESSURE GAUGES
Model K…
that they comply with the following standards:
They are manufactured according to the requirements of directive:
DIRECTIVE 2014 / 68 /EU OF THE EUROPEAN PARLIAMENT AND
THE COUNCIL from May 15, 2014
on the approximation of the laws of the Member States relating to
pressure equipment – short: Pressure Equipment Directive
With pressure ranges from 200 bar or flange connections from DN 25
and pressure ranges from 0.5 bar, they are, as pressure equipment
parts, subjected to the following conformity assessment procedure:
Module A2 “Internal Production Control with
Surveillance of Final Assessment”
Name & address of the responsible body controlling our quality
assurance system:
TÜV NORD Systems GmbH & Co. KG
Meidericher Straße 16
D-47058 Duisburg
Identification number: 0045
The CE-marking is made via sticker on the case.
DIN EN 837-1:1997-02
DIN EN 837-3:1997-02

www.armano-messtechnik.com•p. 17 of 20•GB •09/22•B1•B00-100
Operating Instructions Pressure Gauges
Selection Criteria, Measuring Arrangements, Installation and Operation Manual
www.armano-messtechnik.de
abgegeben durch/by
Grünhain-Beierfeld, 2021-04-13
Bernd Vetter
Geschäftsführender Gesellschafter/Managing Director
Diese Erklärung wird verantwortlich für den Hersteller:
This declaration is issued under the sole responsibility of the manufacturer:
ARMANO Messtechnik GmbH
ARMANO Messtechnik GmbH
Standort Beierfeld
Am Gewerbepark 9
08344 Grünhain-Beierfeld
Tel.: +49 3774 58 – 0
Fax: +49 3774 58 – 545
Standort Wesel
Manometerstraße 5
46487 Wesel-Ginderich
Tel.: +49 2803 9130 – 0
Fax: +49 2803 1035
EU Declaration of Conformity
EU-Konformitätserklärung
104 EU-Konformitätserklärung ATEX RM PM Di K T ohne GSG Ausg. 04/21
Für die nachfolgend bezeichneten Erzeugnisse
MANOMETER
Typen RCh…, RSCh…, RChg…, RQ…, RF…,
Pm…, PCh…, PSCh…, PsP…, D(i)RCh…, DiRZCh…, DiKPCh…,
KPB…, KPCh…
THERMOMETER
Typen TBi…, TSChg…, TGelChg…, TFChg…, TA…, TSCh…,
TGelCh…, TF…, TRCh…
ohne Grenzsignalgebern
wird hiermit erklärt, dass sie den wesentlichen Schutzanforderungen
entsprechen, die in der nachfolgend bezeichneten Richtlinie
festgelegt sind:
RICHTLINIE 2014/34/EU DES EUROPÄISCHEN PARLAMENTS
UND DES RATES vom 26. Februar 2014
für Geräte und Schutzsysteme zur bestimmungsgemäßen
Verwendung in explosionsgefährdeten Bereichen – kurz:
ATEX-Richtlinie
Zur Beurteilung der Erzeugnisse hinsichtlich der Richtlinie wurden
folgende Normen herangezogen:
Kennzeichnung:
II 2G Ex h IIC Gb
II 2D Ex h IIIC Db
Temperaturbereich: −25 °C* / +75 °C
* optional bis −60 °C, je nach Gerätetyp und Anforderung
We hereby declare for the following named goods
PRESSURE GAUGES
Models RCh…, RSCh…, RChg…, RQ…, RF…,
Pm…, PCh…, PSCh…, PsP…, D(i)RCh…, DiRZCh…, DiKPCh…,
KPB…, KPCh…
THERMOMETERS
Models TBi…, TSChg…, TGelChg…, TFChg…, TA…, TSCh…,
TGelCh…, TF…, TRCh…
without Limit Switch Contact Assemblies
that they meet the essential protective requirements, which have
been fixed in the following directives:
DIRECTIVE 2014/34/EU OF THE EUROPEAN PARLIAMENT AND
THE COUNCIL from February 26, 2014
relating to equipment and protective systems intended for use in
potentially explosive atmospheres – short:
ATEX Directive
The following standards have been used to assess the goods
regarding the directive:
Marking:
II 2G Ex h IIC Gb
II 2D Ex h IIIC Db
Temperature range: −25 °C* / +75 °C
* optionally up to −60 °C, depending on model and requirement
DIN EN 80079-36:2016-12
DIN EN 1127-1:2019-10
DIN EN 80079-37:2016-12

B00-100•B1•09/22•GB •p. 18 of 20•www.armano-messtechnik.com
Operating Instructions Pressure Gauges
Selection Criteria, Measuring Arrangements, Installation and Operation Manual
EU Declaration of Conformity
EU-Konformitätserklärung
www.armano-messtechnik.de
abgegeben durch/by
Grünhain-Beierfeld, 2021-04-13
Bernd Vetter
Geschäftsführender Gesellschafter/Managing Director
Diese Erklärung wird verantwortlich für den Hersteller:
This declaration is issued under the sole responsibility of the manufacturer:
ARMANO Messtechnik GmbH
ARMANO Messtechnik GmbH
Standort Beierfeld
Am Gewerbepark 9
08344 Grünhain-Beierfeld
Tel.: +49 3774 58 – 0
Fax: +49 3774 58 – 545
Standort Wesel
Manometerstraße 5
46487 Wesel-Ginderich
Tel.: +49 2803 9130 – 0
Fax: +49 2803 1035
Für die nachfolgend bezeichneten Erzeugnisse
ROHRFEDER-MANOMETER
Typ R…
DIFFERENZDRUCK- ODER DOPPEL-MANOMETER
Typ D (i)R…
in Kombination mit
DRUCKMITTLER
Typ MDM 7190 gemäß Datenblatt 7190
Typ MDM 72.. gemäß Datenblatt 7210, 7211, 7280
Typ MDM 73.. gemäß Datenblatt 7300, 7301, 7302, 7303, 7390
Typ MDM 74.. gemäß Datenblatt 7400
Typ MDM 75.. gemäß Datenblatt 7500, 7501, 7502, 7505, 7590
Typ MDM 76.. gemäß Datenblatt 7600, 7630, 7680
Typ MDM 79.. gemäß Datenblatt 7935, 7952
wird hiermit bestätigt, dass sie den jeweils gültigen Normen entsprechen
und gemäß den Bestimmungen folgender Richtlinie gefertigt werden:
2014/68/EU (Druckgeräte-Richtlinie)
Druckmittler mit Anschlussnennweiten > DN 25/1"bzw. Gewindean-
schlüssen >1"werden in Verbindung mit einem angebauten Druck-
messgerät mit Messbereichen >0,5 bar folgendem Konformitätsbe-
wertungsverfahren unterzogen:
Modul A2
„Interne Fertigungskontrolle mit
Überwachung der Abnahme“
Benannte Stelle:
TÜV NORD Systems GmbH & Co. KG
Meidericher Straße 16
D-47058 Duisburg
Kennnummer: 0045
Die CE-Kennzeichnung erfolgt mittels Aufkleber auf dem Gehäuse.
We hereby declare for the following named goods
BOURDON TUBE PRESSURE GAUGES
Type R …
DIFFERENTIAL OR DUPLEX PRESSURE GAUGES
Type D(i)R…
in combination with
CHEMICAL SEALS
Model MDM 7190 acc. to data sheet 7190
Model MDM 72.. acc. to data sheet 7210, 7211, 7280
Model MDM 73.. acc. to data sheet 7300, 7301, 7302, 7303, 7390
Model MDM 74.. acc. to data sheet 7400
Model MDM 75.. acc. to data sheet 7500, 7501, 7502, 7505, 7590
Model MDM 76.. acc. to data sheet 7600, 7630, 7680
Model MDM 79.. acc. to data sheet 7935, 7952
that they comply with the valid standards and are manufactured ac-
cording to the requirements of directive:
2014/68/EU (Pressure Equipment Directive)
Chemical seals attached to a pressure measuring instrument with
pressure ranges >0.5 bar, with process connections >DN 25/1" or
thread connections >1" are subjected to the following conformity as-
sessment procedure:
Module A2
“Internal Production Control with
Surveillance of Final Assessment”
Notified body:
TÜV NORD Systems GmbH & Co. KG
Meidericher Straße 16
D-47058 Duisburg
Identification number: 0045
The CE-marking is made via sticker on the case.
134 EU-Konformitätserklärung RM_Di_mit_DM Ausg. 04/21

www.armano-messtechnik.com•p. 19 of 20•GB •09/22•B1•B00-100
Operating Instructions Pressure Gauges
Selection Criteria, Measuring Arrangements, Installation and Operation Manual

www.armano-messtechnik.com
Operating Instructions Pressure Gauges
Selection Criteria, Measuring Arrangements, Installation and Operation Manual
© 2022 ARMANO Messtechnik GmbH · Technical changes, replacement of materials and printing errors excepted!
ARMANO Messtechnik GmbH
Location Beierfeld
Am Gewerbepark 9
08344 Grünhain-Beierfeld
Tel.: +49 3774 58 – 0
Fax: +49 3774 58 – 545
mail@armano-beierfeld.com
Location Wesel
Manometerstraße5
46487 Wesel-Ginderich
Tel.: +49 2803 9130 – 0
Fax: +49 2803 1035
Other manuals for RCh series
1
This manual suits for next models
23
Table of contents
Other ARMANO Measuring Instrument manuals
Popular Measuring Instrument manuals by other brands
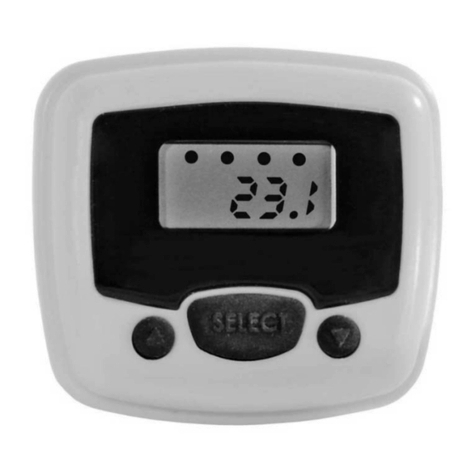
Omega
Omega LVCN-40 Series user guide

MAGEE Scientific
MAGEE Scientific Aethalometer AE33 user manual
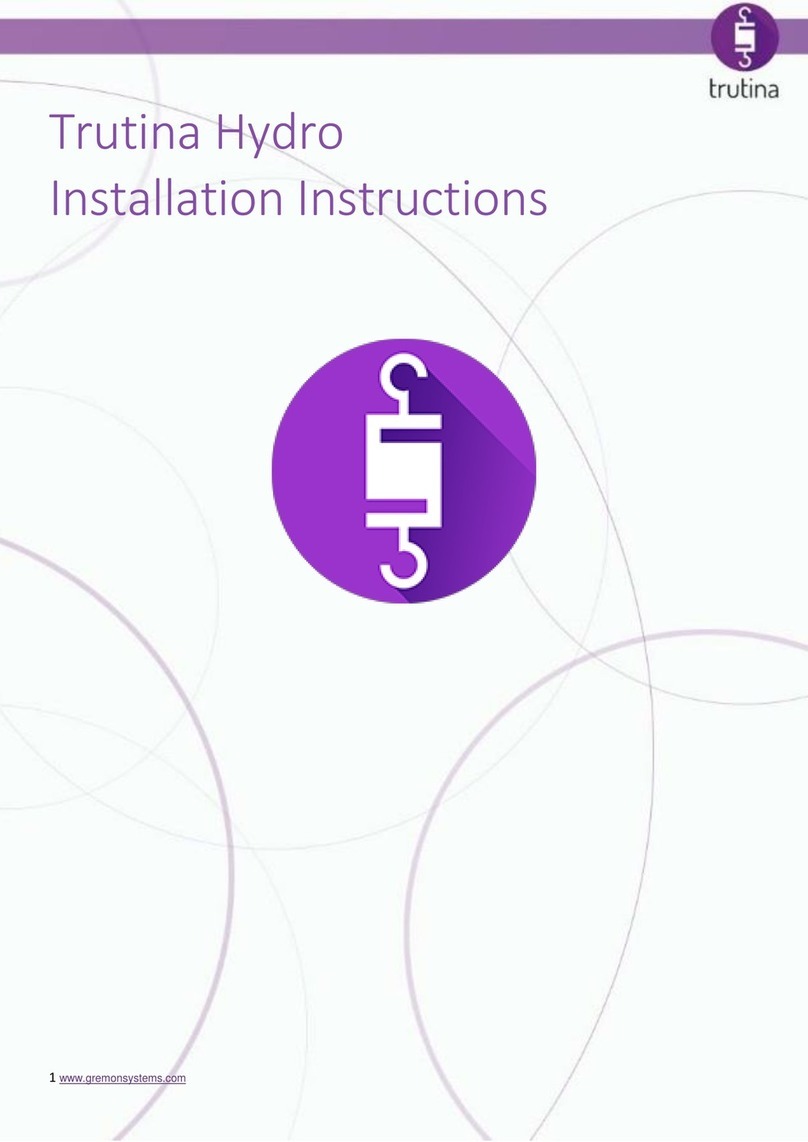
Gremon
Gremon Trutina Hydro installation instructions
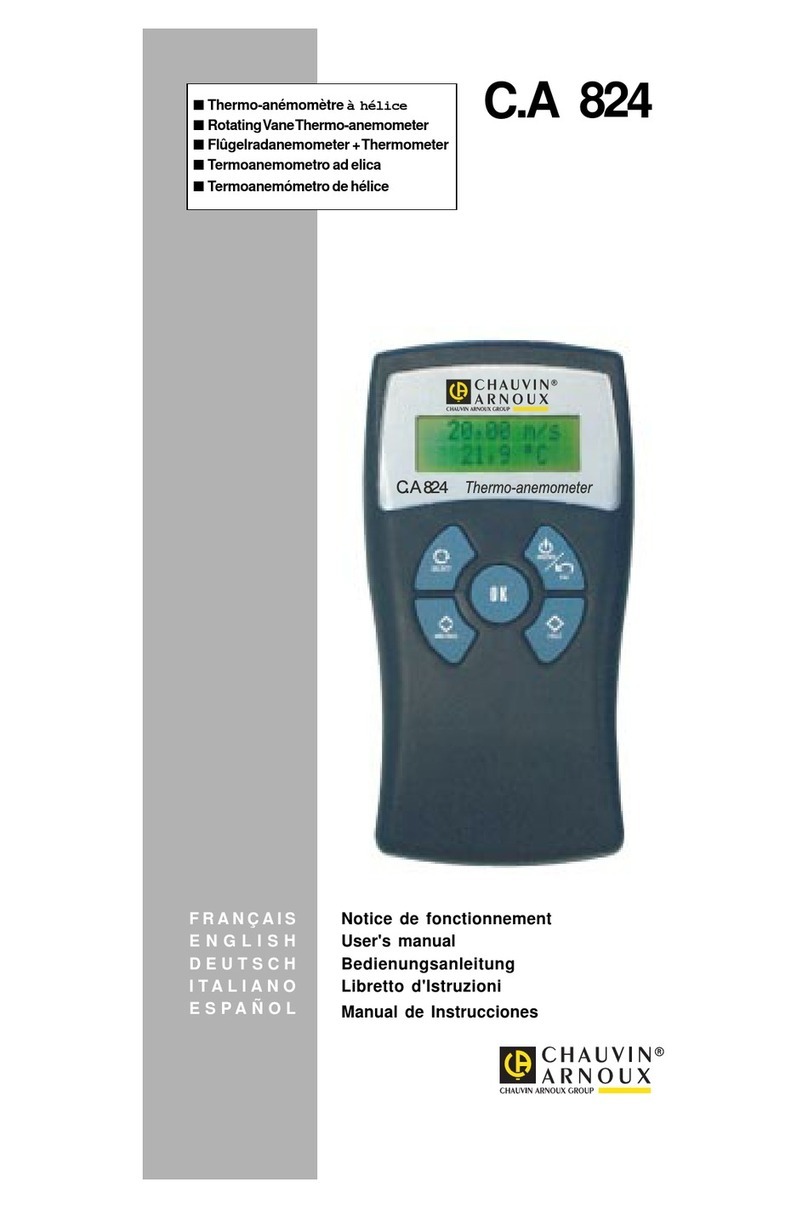
Chauvin Arnoux
Chauvin Arnoux C.A 824 user manual
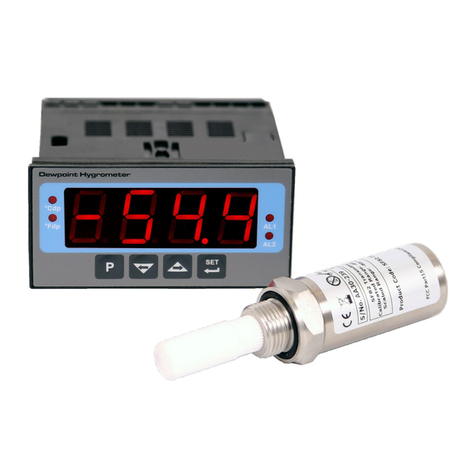
Michell Instruments
Michell Instruments SF82 Series user manual
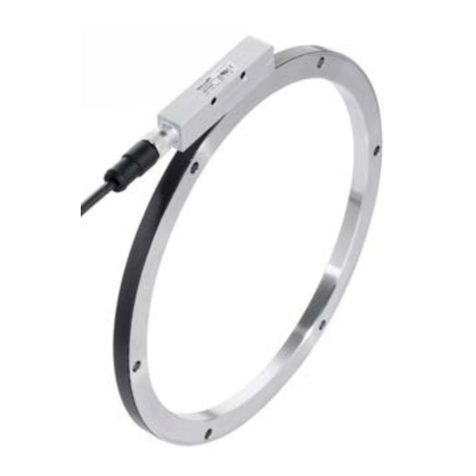
Balluff
Balluff BML-S1G0-Q71 Series Condensed guide