ATWELL UMD-SRB01 User manual

Serving the lift industry since 1996
Operation and Installation Manual
Serving the lift industry since 1996
To find out more, visit our website
www.atwellinternational.com
or call us on
+44 (0) 1905 641 881
Other Products available at Atwell International
VG Products • ELSCO Roller Shoes • Henning Load
Weighing Equipment • SASSI Machines • Bedplates • Machine Guarding
• Divertors • Overspeed Governors • Tension Weights
Sliding Guide Shoes • Guide Rails • Buffers • Compensation Chains
Atwell International Ltd
Ball Mill Top Business Park
Hallow Worcester WR2 6PD
United Kingdom
Telephone +44 (0)1905 641881
Copyright© Atwell International Limited. All rights reserved.
Uncontrolled Movement Detector
for Bi Directional Rope Brakes
Installation Manual
Version 4.0 Includes New Wiring
Uncontrolled Movement Detector
for Bi Directional Rope Brakes
Installation Manual
Version 4.0 Includes New Wiring

1UMD-SRB01 Version 4
Contents Overview....................................................................................................................2
Safety Notes...............................................................................................................3
Owners Obligations ...................................................................................................4
Specification ..............................................................................................................5
Operation .............................................................................................................5
The System ..........................................................................................................6
The Movement Detector (UMD-SP01) ................................................................6
The Controller (UMD-SRB01)...............................................................................6
Signals..................................................................................................................7
Operational Flow Chart .......................................................................................8
Handling, transport and storage.............................................................................10
Components supplied.............................................................................................10
Installation................................................................................................................11
General Advice ..................................................................................................11
The Control Box (UMD-SRB01)..........................................................................11
Wiring .......................................................................................................................12
Mechanical Installation ...........................................................................................18
Normal Operation....................................................................................................19
Resetting the System ........................................................................................19
Bypassing the System .......................................................................................20
Test Deployment of brakes ...............................................................................21
Uncontrolled Movement Settings...........................................................................22
Site Testing of Uncontrolled Movement .................................................................22
Instructions for Rescue Operations........................................................................23
Regular Maintenance ..............................................................................................24
Maintenance Instructions………………………………………………… ..............25
Controller ...........................................................................................................25
Movement Detector Assembly .........................................................................25
Operational Checks ...........................................................................................25
Spare Parts...............................................................................................................26
Definitions................................................................................................................27
Very important.........................................................................................................28
Pulse count table.....................................................................................................29

2Atwell International Limited
The movement detection controls are designed to be installed with new lifts and
retro fitted to existing passenger and goods lifts and used in conjunction with the
bi-directional VG rope brake (VGRB2).
The movement detection controls connect to the main lift control panel. From
here it can receive power and signals to tell if the lift doors are open, or that the
lift over speed governor is OK. It also sends signals to the lift to say stop on next
floor if there is a problem, or emergency stop.
The system will always deploy the brakes immediately and interrupt the main
lift stop circuit, if over speed is signalled or if the emergency stop button on the
front of the panel is pressed.
The movement detector detects movement by looking at an idler wheel resting
on one of the main ropes. As the rope moves so does the idler wheel, and as the
idler wheel rotates movement and direction is detected.
When the doors are open the system is checking for excessive movement.
If excessive movement is detected then the brakes under its control will be
deployed and in addition to this an emergency stop signal will be sent to the
main lift control panel, by means of interrupting the main safety circuit.
There are other functions included with the system such as indication of status
to assist fault finding, resetting of the brakes, manual override to test the
deployment of the brakes, ability to bypass the system (allowing car top control,
without deploying the rope brakes) and pit safety to monitor lift motion when
engineers are in the lift shaft or pit.
Power loss is catered for by the incorporation of an internal battery back-up
system to seamlessly switch from mains power to battery and back again
without the need for manual intervention to reset the brakes. But if during the
power loss excessive movement occurs, or that the over speed governor trips,
the brakes will be deployed and a full reset will be required.
If during its normal operation the system develops a fault then an error or alert
signal will be sent requesting the lift stops at the next floor, doors opened and
stays there until the fault is corrected. During this time whilst the doors are open
the system will continue to detect excessive movement.
Overview

3UMD-SRB01 Version 4
Both employers and employees have a duty of care in relation to the health and
safety of people or property which may be affected by their actions, or failure to
act. Therefore, building owners, or those who have responsibility for controlling
buildings are required under the Management of Health and Safety at Work
Regulations to ensure that their premises are safe and free from risk to health so
far as is practicable. This includes access to the plant equipment and articles or
substances used and in this particular respect will be relevant to the Workplace
(Health, Safety and Welfare) Regulations.
Installation, commissioning and maintenance of this system should only be
carried out by authorised persons who have received the necessary instruction,
because it is dangerous for any other persons to attempt to do so.
Any failure to take adequate precautions may render the authorised person guilty
of negligence should an accident occur.
It is essential that a “Competent Person” has installed and commissioned this
system. It is also essential that a “Competent Person” maintain this system in a
safe manner and at regular intervals.
The “Competent Person” must have had adequate training in theory and
practice together with experience of the equipment in question; to enable a true
assessment of its condition for continued safe operation.
No alterations, modifications or repairs to this system or its components should
be undertaken without the written consent and advice or instruction of the
supplier Atwell International. Any advice or instructions from the supplier must
be followed; any deviation may risk the safe operation of the lift. Even if consent
is given then all the risks associated with the work will have to be suitably and
sufficiently assessed by the owner before these alterations are implemented.
No replacement parts other than those specified or supplied by the supplier
Atwell International should be used as incompatible parts may risk the safe
operation of the lift. Genuine spares are available within 24 hours at a reasonable
cost. But if spares are needed quicker then exact same or equivalent parts may
be sourced locally once the exact specification of those parts has been obtained
and you have suitably assessed the implications of using non standard parts.
If there is any doubt then you should render the lift out of service and contact
Atwell International or one of its appointed agents for assistance.
Safety Notes

4Atwell International Limited
The Owner of the Lift or any delegated party shall inform the Maintenance
Company immediately:
a) about any detected abnormal functioning of the installation;
b) before any modification work on the installation;
c) about any modification of any equipment or condition related to the
installation which existed at the time of the original installation;
In the case of suspected or actual dangerous situations, the installation
shall be put out of service immediately.
We strongly advise that you should carry out a Risk Assessment to determine, as
completely as possible, the different intervention procedures of the maintenance
operations and to associate appropriate safety measures with each of these
procedures.
This Warning Label is incorporated into the control box lid graphic to warn you
of Live Electrical Parts, DO NOT REMOVE the lid if you are not a competent
electrician capable of safely assessing the potentially dangerous internal
connections.
Owners Obligations
Danger
Isolate main
supply
before opening

5UMD-SRB01 Version 4
Operation
A sensor is fitted to an idler wheel or tension weight pulley acting from a wire
rope attached to the lift car. The sensor will detect movement in either direction.
A controller box will be fitted nearby and connected to the sensor, main lift
control panel, over speed governor & Rope brakes.
Once the system has been installed and set up and the rope brakes have been
reset.
The controller will receive an external signal to say that the lift doors are open,
which will activate the system to “Monitor for movement”.
If movement is detected above the predetermined limit of 100mm to
900 mm, (actual pre set limit is 150 mm but can be modified to suit customer
requirements) the controller will actuate a safety relay causing all safety systems
to be deployed. Once deployed, the controller will deliberately not allow the lift to
run or revert to a normal state until the brakes have been manually reset.
If no movement was detected and the controller receives a signal to say doors
are closed it will deactivate and allow normal operation of the lift and primary
safety circuit.
During its operation the control box will also continue to check the integrity
of the connection to the sensor assembly. It will also monitor the status of
the brakes.
It will perform a simple self diagnostic test to ensure all sensors are working, if a
fault develops a fault signal will be sent to the main lift control panel to request
it to bring the lift to halt at the next floor and open the doors (Please note the
controller can only send the signal and not control stopping of the lift). When the
doors open the brakes will be deployed.
If during the Monitoring phase the connection to the sensor is lost, the brakes
will be deployed.
Due to the battery backup, if mains power fails with the doors open, the system
will continue to operate and safely monitor for movement. If mains power fails
when the doors are closed the system will automatically monitor for movement
but will allow greater movement before applying the brakes.
The system is directly connected to the lift over speed governor. So if over speed
is signalled the rope brakes will be deployed immediately.
The control panel is fitted with an emergency stop button; this will allow
immediate deployment of the rope brakes with manual control.
Maintenance, other than checking cleanliness of idler pulley assembly, is
not required for the actual components of the system, but it will be strongly
recommended that the operation is regularly checked and tested by competent
persons (lift engineer) to comply with the regulations.
Specification

6Atwell International Limited
The System
Robust metal enclosure, Fail Safe Design, easy site wiring especially with plug and
socket option, where the sensors, brakes and controller will be connected via a
plug and socket arrangement to assist on site wiring.
Power feed and lift panel connections will be the responsibility of the end
customer.
Set of parts to be supplied in the full system include;
Control Box (UMD-SRB01)
Sensor Box (UMD-SP01)
Sensor Mounting Bracket and fixings
Set of 3 interconnecting cables,
32 Way interconnecting Hood,
Set of documentation (in English)
The Movement Detector (UMD-SP01)
The movement detector will be a fixed non-contact non-adjustable type.
The actual motion sensors are enclosed in a sealed enclosure to protect from
moisture, vibration and tampering. This is a non-serviceable component, any
doubt then it should be replaced.
The movement detector is sprung mounted to a bracket. The bracket is directly
mounted to the rope brake assembly. Alignment and tension to the rope can be
adjusted.
The Detector is constantly monitored, so if there is a fault with it or the
connection to it then an ALERT signal will be sent to the main lift panel. This is
to request the lift to be stopped at the next level, open doors then render itself
out of action. If the fault is detected whilst the doors are open then the brakes
will be deployed, because this is the worst case scenario and the system must
be fail safe.
The Controller (UMD-SRB01)
The controller will be enclosed in a painted steel enclosure suitably rated for the
lift control room. It is approximately 450mm long x 300mm tall x 150mm deep.
With the exception of replacing the battery and the relays every 3 years it does
not require any maintenance, other than periodical testing and inspection in
accordance with your site risk assessment and the lift regulations.
It contains a programmable safety device, display, visual and audible indicators,
key switch, battery, power supply and fuses.
The UMD-SRB01 controller has been designed and constructed to comply with all
current CE requirements, i.e. EMC, Low Voltage, RoHS, WEEE and more specifically
to meet the requirements of EN 81-80: 2003 5.9.4 Uncontrolled Movement with
doors Open.
With simple modification to the door wiring connections now also complies with
latest EN81-20/50:2014.

7UMD-SRB01 Version 4
Indication of the system status will be provided by LEDs i.e. power on, monitoring,
brakes set OK and emergency stop.
In addition to this there is a small visual display showing a text interface
explaining the status and warnings.
The UMD-SRB01 has two switches, one is an emergency stop button which when
pressed will immediately deploy the brakes. The other switch requires a key to
operate it, this is because regulations require a competent person to reset the
brakes in the event of them being deployed. So to prevent any unauthorised
tampering or resetting or bypassing of the system a key is used. We supply 2
keys per system; these should only be made available to competent persons. The
key switch will allow the brakes to be reset and the system to bypass the motion
detection, during maintenance, etc.
An audible alarm is included within the UMD-SRB01 controller; this will beep
at different rates, one slow pulse for bypass mode and a quicker pulse for
reset mode.
Signals
Controller input power supply will be 230V or 110V AC 50/60Hz, it has an internal
12v DC control voltage, power supply and battery backup.
The system requires the following signals and connection to the external
contacts to enable it to operate.
1. A car Door Open / Closed Input signal.
2. A landing Door Open / Closed Input signal.
These inputs should be a connected to a Dry / volt free, normally open, pair of
relay contacts wired parrallel. It only requires a maximum switching current of
0.25A 12V DC.
3. An over speed OK signal, normally closed when no over speed,
opens when lift is over speeding.
Please note if the lift loses mains power the above door signals will open,
therefore the third signal we need must be connected directly to the over speed
governor switch, as if this signal opens the brakes will be immediately deployed.
Output signals from the controller will be volt free relay contacts. The contacts
are rated for up to 6Amp Max at 250VAC. These are:-
4. Main Lift Safety Circuit Output Signal.
5. Main Lift Alert Output Signal

8Atwell International Limited
Status
Changed State
to:
deepsrevOssapyBniyeKteseRniyeKteStoN)s(ekarB
signalled
UMD Sensor
pack not OK
UMD Emergency
stop pressed
UMD Control
Power Lost
Mains power lost
Action for brakes
Deploy Brakes None unless
excessive
movement
detected
Movement
in excess of
150 mm (can be
increased or
decreased)
detected.
None None Unless
Overspeed.
Deploy Brakes None Unless
Doors open. Or
safety circuit cut
or overspeed.
Deploy Brakes Deploy Brakes None Unless
movement
500 mm to
1500 mm
detected. Or
overspeed.
Action signals to
lift
Signal Stop Lift None Deploy Brakes None None Signal Stop Lift Signal Alert Signal Stop Lift Signal Stop Lift
open
None
Signal Stop Lift
Action Display
Display "Brakes
Dragging"
Display "door open
Monitoring for
movement"
Excessive
Movement
Detected
Display "Key in
Reset position"
Display Bypass
Mode
Display "Over
Speed signal"
Display Warning
Connection to
sensor Lost
Display "Safety
circuit cut"
No display Display
Action LED
indicators
Illuminate Brakes
Deployed LED
Flash Monitoring
LED
Illuminate
Brakes Deployed
LED
None Flash Bypass
LED and sound
Buzzer
Illuminate Brakes
Deployed LED
None Illuminate Brakes
Deployed LED
No LEDs Extinguish control
voltage LED
Action Manual
Intervention
Wait for engineer
to reset system
and check wiring
and brakes. If all
OK return to run
mode
None required Investigate
reason. Wait for
engineer to reset
system and
check wiring and
brakes. If all OK
return to run
mode
be returned to
run.
returned to run.
Carry out
maintenance on
lift.
Wait for engineer
to reset system
and check why
lift was
overspeeding. If
all OK return to
run mode
Wait for engineer
to check
connection to
sensor and rectify
problem. If all OK
return to run
mode
Wait for engineer
to reset system
after resetting the
e.stop button. If
all OK return to
run mode
Wait for engineer
to reset system
why power was
lost. If all OK
return to run
mode
None - unless
power is not
resumed after 2-3
hours, then full
reset will be
required as
brakes will have
been deployed.
Action required
by lift
Lift should stop
and not move
until reset.
None required,
other than signal
doors closed or
open
Lift should stop
and not move
until reset.
None required
Run in engineer
test mode when
requested by
engineer.
Otherwise our
alert signal will
request lift is
stopped
Lift should stop
and not move
until reset.
Lift should move
to the nextfloor
and open doors.
Lift should stop
and not move
until reset.
Lift should stop
and not move until
reset. if doors were open
when the power
went off then
level of movement
will deploy brakes
notes
Ignore door open
signals. Will
deploy brakes on
Over speed
As soon as the
doors open the
brakes will be
deployed
Door(s) Opens
(only operates when both
door circuits are open)
System Status = OK
(Fully Rest, brakes set, doors closed, key in RUN position, safety circuits OK, overspeed governor OK, sensor pack OK, emergency stop OK)
CHANGE IN STATUS OF SYSTEM
Mar 08
Wait for key to be
Wait for key to
after inspecting
in excess of
50 mm to 150 mm
Atwell Uncontrolled Movement Detector and Rope Brake controller – Normal/Run Mode
System Status = OK
(Fully Reset, brakes set, doors closed, key in RUN position, safety circuits OK, overspeed governor OK, sensor pack OK, emergency stop OK)
Status

9UMD-SRB01 Version 4
Status
Changed State
to:
deepsrevOssapyBniyeKteseRniyeKteStoN)s(ekarB
signalled
UMD Sensor
pack not OK
UMD Emergency
stop pressed
UMD Control
Power Lost
Mains power lost
Action for brakes
Deploy Brakes None unless
excessive
movement
detected
Movement
in excess of
150 mm (can be
increased or
decreased)
detected.
None None Unless
Overspeed.
Deploy Brakes None Unless
Doors open. Or
safety circuit cut
or overspeed.
Deploy Brakes Deploy Brakes None Unless
movement
500 mm to
1500 mm
detected. Or
overspeed.
Action signals to
lift
Signal Stop Lift None Deploy Brakes None None Signal Stop Lift Signal Alert Signal Stop Lift Signal Stop Lift
open
None
Signal Stop Lift
Action Display
Display "Brakes
Dragging"
Display "door open
Monitoring for
movement"
Excessive
Movement
Detected
Display "Key in
Reset position"
Display Bypass
Mode
Display "Over
Speed signal"
Display Warning
Connection to
sensor Lost
Display "Safety
circuit cut"
No display Display
Action LED
indicators
Illuminate Brakes
Deployed LED
Flash Monitoring
LED
Illuminate
Brakes Deployed
LED
None Flash Bypass
LED and sound
Buzzer
Illuminate Brakes
Deployed LED
None Illuminate Brakes
Deployed LED
No LEDs Extinguish control
voltage LED
Action Manual
Intervention
Wait for engineer
to reset system
and check wiring
and brakes. If all
OK return to run
mode
None required Investigate
reason. Wait for
engineer to reset
system and
check wiring and
brakes. If all OK
return to run
mode
be returned to
run.
returned to run.
Carry out
maintenance on
lift.
Wait for engineer
to reset system
and check why
lift was
overspeeding. If
all OK return to
run mode
Wait for engineer
to check
connection to
sensor and rectify
problem. If all OK
return to run
mode
Wait for engineer
to reset system
after resetting the
e.stop button. If
all OK return to
run mode
Wait for engineer
to reset system
why power was
lost. If all OK
return to run
mode
None - unless
power is not
resumed after 2-3
hours, then full
reset will be
required as
brakes will have
been deployed.
Action required
by lift
Lift should stop
and not move
until reset.
None required,
other than signal
doors closed or
open
Lift should stop
and not move
until reset.
None required
Run in engineer
test mode when
requested by
engineer.
Otherwise our
alert signal will
request lift is
stopped
Lift should stop
and not move
until reset.
Lift should move
to the nextfloor
and open doors.
Lift should stop
and not move
until reset.
Lift should stop
and not move until
reset. if doors were open
when the power
went off then
level of movement
will deploy brakes
notes
Ignore door open
signals. Will
deploy brakes on
Over speed
As soon as the
doors open the
brakes will be
deployed
Door(s) Opens
(only operates when both
door circuits are open)
System Status = OK
(Fully Rest, brakes set, doors closed, key in RUN position, safety circuits OK, overspeed governor OK, sensor pack OK, emergency stop OK)
CHANGE IN STATUS OF SYSTEM
Mar 08
Wait for key to be
Wait for key to
after inspecting
in excess of
50 mm to 150 mm
Atwell Uncontrolled Movement Detector and Rope Brake controller – Normal/Run Mode
System Status = OK
(Fully Reset, brakes set, doors closed, key in RUN position, safety circuits OK, overspeed governor OK, sensor pack OK, emergency stop OK)

10 Atwell International Limited
The components of this system have been carefully packaged for shipping,
including strapping and strong tape. If you use a knife to cut open the boxes,
please be very careful to ensure that you only cut through the tape and straps
and not through the cardboard potentially damaging the components inside.
Please inspect the components of this system thoroughly prior to attempting
to install it. If the Brakes, Cables, Controller or Sensor has been or suspected to
have been damaged or exposed to moisture, they should not be used. Please
return them to Atwell International for examination and re-test.
The brakes, control boxes or sensors should never be lifted or carried by their
cables. They should never be allowed to get wet or exposed to moisture.
Please check that the following parts have been supplied and received in good
order prior to attempting to install the system.
nMovement Detector (UMD-SP01).
nMovement Detector Bracket and fasteners.
nControl box (UMD-SRB01).
nSpare fuses. (2 types 2 of each)
nMating 32 way multipole plug.
nManual & Documentation pack.
n2 keys.
n3 Prewired cables for simplified installation.
Handling, Transport
and Storage
Components Supplied

11UMD-SRB01 Version 4
General Advice
The area for which this unit is intended should comply with the lift room
regulations so that its installation, operation and maintenance is carried out in a
risk free environment.
Specific hazards arise for inadequate lighting, untidy work area, trip hazards and
poor access.
The Control Box (UMD-SRB01)
It is recommended that the Control box is ideally mounted at approx 1.5 metres
high on to a solid wall adjacent to the main lift control panel and close to the
rope brake and monitoring pulley position. Consideration should be given to
access for operation and maintenance of the control box as well as ease of cable
runs.
The enclosure weighs approx 8 kg, it is supplied with 4 brackets, one on each
corner. Use suitable screws and rawl plugs to secure this control box to the wall.
Installation
Mounting Brackets with keyholes
Fixing in place

12 Atwell International Limited
Once the control box is in place, cable runs can commence. See Drg. page 16
CONNECTION OVERVIEW DIAGRAM for help to plan the cable runs.
There is a 32 way connector supplied, which has an
industry standard PG thread. It is intended that flexible
armoured conduit is used to prevent strain and damage
to the individual cores.
We would strongly suggest that the power is fed from
the main lift panel protected by a circuit breaker Type
D rated at 3 Amps. The cable run should be as short as
possible. If the length does not exceed 2 metres the
size should be at least 1.5 mm2. Stranded tri-rated PVC
insulated. It should also comply with local regulations.
The 32-way connector is fitted so as to prevent the need for access inside
of the control box. If you should need access to the inside of the control box
please contact Atwell International for written consent as your warranty may be
invalidated if the internal seals are broken.
During wiring great care must be taken to ensure that there is no risk of short
circuits from stray strands, cross connection, loose terminals or strain on cable
joins. All terminations should be made using boot lace ferrules or similar and
each wire appropriately identified with its corresponding wire number at each
end of the cable. Wiring of power and internal main lift connections must be
carried out by a competent electrician, and checked prior to applying power.
Wiring
230V
Danger
Isolate main
supply
before opening

13UMD-SRB01 Version 4
SAFETY NOTE: Once connected to the main lift control panel there will be
potentially live connections within the UMD-SRB01 enclosure and the terminal
housing even when the fuses for the enclosure have been withdrawn. Within the
UMD-SRB01 enclosure the internal connecting cables are coloured orange, this is
so that you can easily identify them as potentially live, check them and beware
of them.
2 Fuses
Note: The 2 Fuses are not fitted
during shipping. The competent
electrician must only fit them after
testing the wiring of the 32 way
terminations and immediately prior
to switching on the power for the
first time.
Fitting of fuses

14 Atwell International Limited
Make Sure Power is disconnected prior to attempting to check or replace fuses.
As there are live terminals connected through to the end of the fuse so if you
touch the fuse it could be Live!
Please check rating against labels of each fuse.
F1 = Internal Power Supply 1.25Amps (230V AC)
F2 = Control voltage 2.5Amps (12V DC)
The Fuses we use are Manufactured by SIBA and they are:
5mm diameter x 20mm long glass fuses
Rated at 250V, with SEMKO – DEMKO – BSI – UL – CE approvals
To IEC 60127 – 2 / 3 and DIN VDE 0820
Breaking Capacity L 35Amps AC (min. 10 x ln)
T (Time lag)
TYPE 179 120 Part Numbers 70 001 35 97160/1 2.5A
TYPE 179 120 Part Numbers 70 001 35 17743 1.25A
Connections to the Main Lift Control Panel must be carried out carefully to
ensure that the correct function of the signals is produced.
The control box input signals are 12V DC 100mA they require a dry / volt free
relay contact normally open and energised when the Car and Landing doors are
closed.
In addition, a connection directly to the normally closed (when not in over speed
condition) over speed governor switch is required.
The operation of these switches is essential to enable the UMD-SRB01 to operate
safely, i.e. If a cable is broken or the lift over speeds the UMD-SB01 will be FAIL
SAFE. i.e. any problems, the brakes will be deployed.
The connection from the Main Lift Panel such as Alert signal and emergency
stop must be 230Volts maximum and must not exceed 5amps. The control box
provides dry / volt free relay contacts for your signals. This is done by connecting
via the 32 way Multipole Plug & Socket.
On the next page there is a list of all the connections to the multipole plug and
their functions.
Please also see electrical drawings supplied with this manual for further
information.
Connector 1 to 16
Connector 17 to 32
Wiring (continued)

15UMD-SRB01 Version 4
DO NOT TAMPER WITH THE CONTROL BOX
If it does not allow the brakes to reset then
there is still a problem with the lift!
Rectify the problem and the controller will allow a reset.
Correct Wiring of the Sockets
Spare Core (violet)
wrapped around 8 core
cable (in case of future
mods)
8 core cable
Cable screen
sheathed and
terminated to earth
Black wire removed
to show correct use
of boot lace crimps
Screened cable
connected with main
earth cable
SAFETY NOTE:
Do not leave the lift to run in engineer “bypass mode”, this is purely a function
to allow you to carry out maintenance on the lift without triggering uncontrolled
movement. You will have circumvented the part of the safety circuit.

16 Atwell International Limited
Wiring (continued)

17UMD-SRB01 Version 4
32
SPARE
28
25
24
23
22
21
20
19
18
* connect to the Hood, and both
terminal block grounding points. *
17
Earth Bond / Ground
30
32
30
28
25
Violet Not used.
Please Isolate.
SENSOR PACK
Fitted to ROPE BRAKE
or IDLER PULLEY
or OVER SPEED GOV.
PSC INPUT
PSC INPUT
PSC INPUT
PSC INPUT
PSC INPUT
+ 12V DC
- 0V DC
+12V
PSC INPUT
ROPE BRAKE A "Set" INPUT
21
19
18
24
23
22
20
+ 12V DC
- 0V DC
ROPE BRAKE B "Set" INPUT
- 0V DC
31
31
+ 12V DC
29
PSC INPUT
27
29
27
+12V
26
26
Violet, Brown, White Not used.
Please Isolate.
Rope Brake A
Rope Brake B
8 Core screened cable & Plug Supplied By ATWELL
8 Core screened cable & Plug Supplied By ATWELL
8 Core screened cable & Plug Supplied By ATWELL
Please Note: It is recommended that boot lace ferrules are used when connecting the 8-core cables to the 32 way
terminal blocks.
Please ensure all spare cores are insulated and secured.
The Screens of these cables must be connected
to the Ground / Earth points inside the hood.
CAUTION !
Make sure the socket with pins 17 to 32 mates with the correct plug on the UMD. It is interchangeable with Pins 1 to 16!
red
blue
yellow
green
Violet, Brown, White Not used.
Please Isolate.
green
yellow
blue
red
red
blue
yellow
green
white
brown
black
Connect Screen to ground
Connect Screen to ground
PLUG 17 TO 32 FITTED TO UMD & PRE- WIRED
SO CK ET 17 TO 32 TO BE W IR ED O N SI TE

18 Atwell International Limited
Mechanical Installation For information on mechanically installing the ROPE BRAKES please see the
specific documentation for the individual items as supplied.
Please note this device is a precision encoder device and is not capable of
withstanding a drop or severe mechanical shock, so never use a hammer to
adjust it.
It is also sealed, there are no user adjustable or repairable parts inside it, all
warranties will be void and the product will be destroyed if you open it. If you
suspect it is faulty then replace it, return to Atwell International who will inspect it
and will supply a replacement unit if it was found to have failed under warranty.
Securely bolt the brackets supplied to the tapped holes provided in the rope
brake side bars, adjust backward or forward for slight tension against the rope.
It may be necessary to adjust the alignment of the wheel to the rope. This is done
by carefully unscrewing the M4 cap head retaining screw on the wheel, and then
sliding the wheel so the rope is centred on the wheel. Re-tighten the M4 cap
headscrew onto the shaft.
Check for smooth operation and no excessive play or run out.
Connect the other end of this sensor cable to the UMD-SRB01 panel via the 32
way connector, if you have not done so yet.
Slight pressure only.
Allow further movement
on springs. Do not adjust
it so that the springs are
coil bound.
Connect sensor cable
to the sensor box.
M4 Screw

19UMD-SRB01 Version 4
Resetting the System
To “SET” the system for the very first time is the same procedure as each time
you need to “RESET” the system, and that is as follows.
nCheck that all faults are cleared and that there is no reason why the lift
cannot be put back into service. i.e. reason for brakes to be deployed has
been rectified.
(If there are faults rectify them first.)
nCheck that there is power at the controller i.e. “Control Voltage” LED
is illuminated.
(If there is no power test fuses etc, find out why)
nCheck that there are no brakes displaying that they are already “SET”.
(If they are already displaying “set” then check internal switches of the
rope brake)
nInsert the key into the reset/run/bypass switch.
nTurn the key to the reset position and leave it there whilst the brakes are reset.
(A sounder will beep to remind you that the system is in reset mode, also the
lift will be prevented to run until the brakes are reset and the key is returned
to run position.)
Warning the safety devices controlled by this controller are bypassed
while the key is in this position.
nThe rope brakes will require lifting into position, and then they will hold there.
nSystem is now SET.
nReturn key to central RUN position.
Normal Operation
Table of contents
Popular Security Sensor manuals by other brands
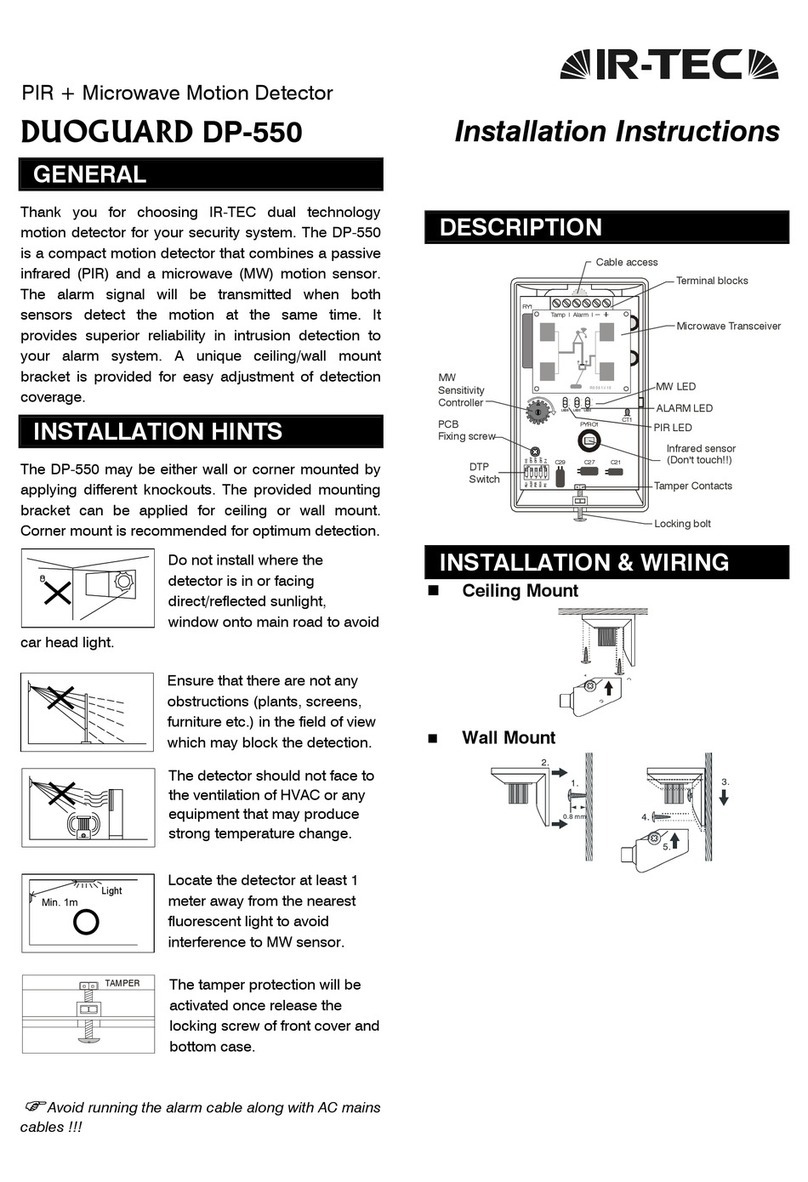
IR-Tec
IR-Tec DUOGUARD DP-550 installation instructions

Abus
Abus PLBW10100 quick guide
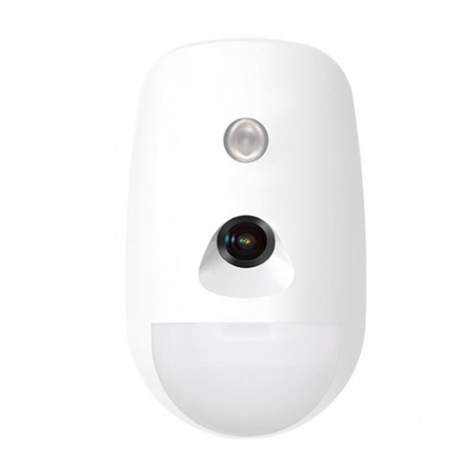
HIK VISION
HIK VISION DS-PDPC12PF-EG2-WB quick start guide

L3 Communications
L3 Communications Narda 8950/10 Operation and installation guide
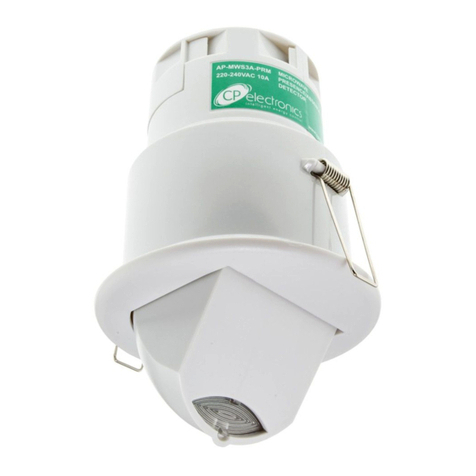
C.P. Electronics
C.P. Electronics MWS3A-PRM-2CH installation guide
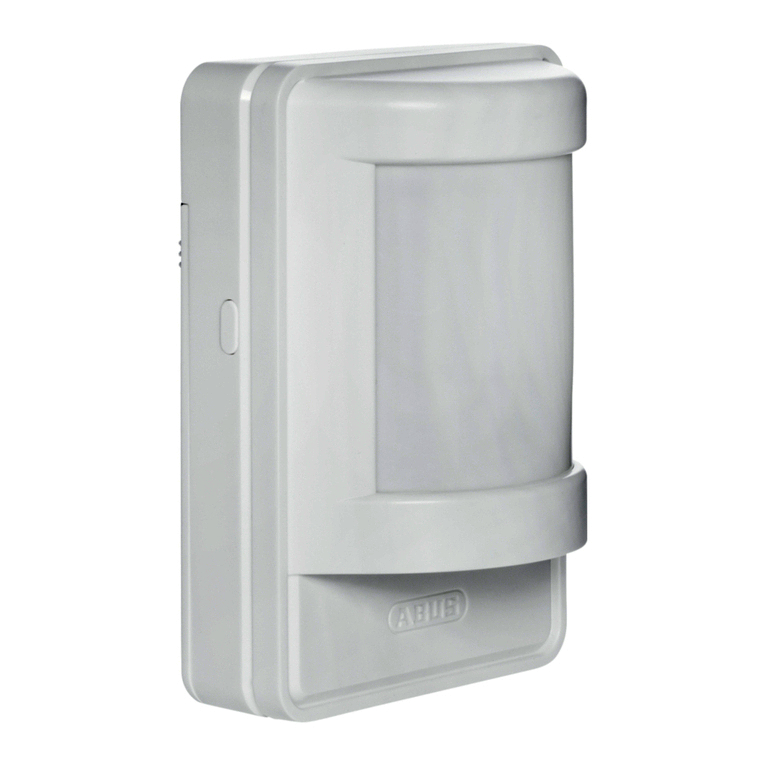
Abus
Abus PLBW10100 manual