Automatic Systems BL40 User manual

Technical Manual NAM-BL4x-MT-EN-C
The information in this document is the property of Automatic Systems and is confidential. The consignee withholds from using it for anything other than the use of the products or the execution of the
project to which they belong and withholds from communicating it to third parties without prior written agreement from Automatic Systems. Document subject to change without prior notice.
BL 4x
Technical manual
BL40 BL41
BL4
3
BL46

p 2/58
Technical Manual NAM-BL4x-MT-EN-C
The information in this document is the property of Automatic Systems and is confidential. The consignee withholds from using it for anything other than the use of the products or the execution of the
project to which they belong and withholds from communicating it to third parties without prior written agreement from Automatic Systems. Document subject to change without prior notice.
Document revisions
Revision
no.
Date Written
by
Checked by Subject
A 2011-09-22 SSA First edition
B 2012-05-09 SSA - SR barrier type added (all through manual)
- Speed controller adjustment procedure updated (CH 5.1)
- Spring adjustment table updated (CH 5.2)
- Wiring diagram updated (CH 9)
C 2013-02-08 JPS SSA - Component list (CH 2.1)
- Operating Principle (CH 2.2)
- Mechanical locking of the arm (CH 2.3)
- Positionning of the equipment (CH 4.2)
- Wiring diagram updated (CH 9)

p 3/58
Technical Manual NAM-BL4x-MT-EN-C
The information in this document is the property of Automatic Systems and is confidential. The consignee withholds from using it for anything other than the use of the products or the execution of the
project to which they belong and withholds from communicating it to third parties without prior written agreement from Automatic Systems. Document subject to change without prior notice.
TABLE OF CONTENTS
1. SAFETY WARNINGS 4
2. DESCRIPTION 6
2.1. Location of the components 6
2.2. Operating principle 7
2.3. Mechanical locking of the arm 8
3. AS1320 CONTROL BOARD 10
3.1. PRDSTD – BL_xxx menu: Troubleshooting and monitoring 12
3.2. QUICK START menu: Quick configuration 19
4. INSTALLATION 27
4.1. Storing the equipment before installation 27
4.2. Positioning the equipment 27
4.3. Assembly of the round arm for BL40 28
4.4. Assembly of the central round arm for BL41 30
4.5. Assembly of the oval arm for BL43 & BL44 32
4.6. Assembly of the arm with folding fence for BL46 34
4.7. Electrical connections 40
5. ADJUSTMENTS 41
5.1. Setting the parameters for the variable speed controller 41
5.2. Adjusting the balancing springs 42
5.3. Adjusting the position sensors 45
6. USE 46
6.1. First startup 46
6.2. Daily startup 46
6.3. Turning off the power 46
6.4. Manual opening of the arm 47
6.5. Maintenance 48
6.6. Troubleshooting 49
7. TECHNICAL SPECIFICATIONS 51
8. DIMENSIONS 52
9. WIRING DIAGRAMS 54
9.1. Control blocks assignment 55

p 4/58
Technical Manual NAM-BL4x-MT-EN-C
The information in this document is the property of Automatic Systems and is confidential. The consignee withholds from using it for anything other than the use of the products or the execution of the
project to which they belong and withholds from communicating it to third parties without prior written agreement from Automatic Systems. Document subject to change without prior notice.
1. SAFETY WARNINGS
IMPORTANT: SAFETY INSTRUCTIONS
WARNING – TO REDUCE THE RISK OF INJURY OR DEATH, READ AND FOLLOW
ALL SAFETY INSTRUCTIONS BEFORE INSTALLING, OPERATING, OR SERVICING
THE BARRIER. SAVE THESE INSTRUCTIONS!
ALL OPERATIONS OF THE GATE MUST BE DONE BY QUALIFIED PERSONNEL. ALL
NON-AUTHORIZED REPAIRS OR REPAIRS DONE BY A NON-QUALIFIED
TECHNICIAN VOID THE WARRANTY OF THE MANUFACTURER.
ALWAYS INSTALL THE ARM BEFORE OPERATING OR LOWERING THE GATE.
UNPIN THE SPRINGS BEFORE PROCEEDING TO ANY ARM INSTALLATION.
Installing a barrier exposes the user to responsibilities with regards to
the safety of people:
Circulation of pedestrians, cyclist and motorcyclist in the area
where the barrier is moving must be banned (risk of being hit
and pinching).
Two pictograms for the prohibition of pedestrian,cyclist and
motorcyclist access are provided with the equipment;
To allow the passage of motorcycles, a special loop
configuration along with photo cells must be used as specified
in the drawing BL229-IN-07-EN. The systems must be tested prior to use.
All operations performed on the equipment must be undertaken by qualified personnel. All operations
that are not authorised or that are carried out on this product by an unqualified technician shall
automatically and ipso jure lead to the denial of the manufacturer’s warrantee.
The access keys to the mechanism must only be used by personnel informed about the electrical and
mechanical risks incurred by negligent handling. This person is required to lock the mechanism’s
access door after completing the work.
As soon as the access door to the mechanism is opened, cut the power supply on the circuit
breaker (20, Ch. 2.1. ).
Raise the arm before any work inside the housing, in order to release the tension in the balancing
springs and avoid the untimely movement of the driving mechanism (Ch. 0).
All internal elements that could receive power or move must be handled with care.
KEEP GATES PROPERLY MAINTAINED. When servicing, keep the place around the gate secured to
avoid risk of injuries if the gate were to move without warning.
Test the gate operator monthly. It is important to test the gate to ensure that the force of the arm is not
excessive. If the gate is equipped with the safety contact sensor, the gate MUST reverse on contact
with a rigid object or stop dependent on the programming of the sensor. After adjusting the force or the

p 5/58
Technical Manual NAM-BL4x-MT-EN-C
The information in this document is the property of Automatic Systems and is confidential. The consignee withholds from using it for anything other than the use of the products or the execution of the
project to which they belong and withholds from communicating it to third parties without prior written agreement from Automatic Systems. Document subject to change without prior notice.
limit of travel, retest the gate operator. Failure to adjust and retest the gate operator properly can
increase the risk of injury or death.
The equipment is configured in a minimal risk mode for its users. All modifications to the parameters
must be undertaken by experienced and qualified personnel and in no way entails the responsibility of
Automatic Systems.
The end of the arm must always be kept at a distance of at least 0.5 m from any object.
Never let children operate or play with gate controllers or remote control devices.
The barrier must be fully visible by the user before being actuated.
After a collision, even without apparent damages, the equipment must be carefully checked by an
approved technician.
Install the arm and any accessories before any electrical tests (Ch.4. ).
Never operate the barrier without the bumpers (10, Ch. 2.1. ).
The installation of detection loops must be validated by qualified personnel who will determine their
optimal configuration (adapted to vehicle type and passageway).
WARNING: The risk of injury exists for people when using standard detection loops: they can
incorrectly detect trucks and (motorcycles) bikes and close the gate on them!

p 6/58
Technical Manual NAM-BL4x-MT-EN-C
The information in this document is the property of Automatic Systems and is confidential. The consignee withholds from using it for anything other than the use of the products or the execution of the
project to which they belong and withholds from communicating it to third parties without prior written agreement from Automatic Systems. Document subject to change without prior notice.
2. DESCRIPTION
2.1. Location of the components
1 Cover, locked with two locks and keys
2 Housing
3 Front door, locked by lock and key
4 Bearing for main shaft (x2 per barrier)
5 Detection cam (x2 per barrier)
6 Bracket for inductive sensors
7 Inductive position sensor (x2 per barrier)
8 Protective cover
9 Gear motor
10 Bumper (x2 per barrier)
11 Sector gear
12 Spring assembly (x1 or x2 per barrier) (see Ch. 0)
13 Hub
14 Plummer block
15 Pinion
16 Control board
17 Variable speed controller
18 Arm
19 Reinforcing V-block, optional arm locking support
20 Circuit breaker
19

p 7/58
Technical Manual NAM-BL4x-MT-EN-C
The information in this document is the property of Automatic Systems and is confidential. The consignee withholds from using it for anything other than the use of the products or the execution of the
project to which they belong and withholds from communicating it to third parties without prior written agreement from Automatic Systems. Document subject to change without prior notice.
2.2. Operating principle
The indicators in this chapter refer to the illustrations in Ch. 2.1.
The opening of the arm (18) is controlled by the user (through a lockable switch, a push-button, a radio
transmitter), presence detector loops buried under the road, or through an outside unit.
Closing is controlled in the same way, or automatically after a time delay.
The motion generated by the gear motor (9) is transmitted to the arm by means of pinion and sector gears
(15 + 11).
The speed of the arm movement, controlled by the variable speed controller (17), can be adjusted for both
opening and closing. The movement parameters are adjusted in the factory in order to offer brisk acceleration
and gentle deceleration at the end of the movement.
The 2 inductive position sensors (7) indicate the extreme arm positions (open and closed) to the control
board (16). The latter coordinates the barrier’s activity: Management of movements, options, processing of
incoming and outgoing information, etc (see Ch. 3. ). This information can, however, be transferred and
processed by an external terminal (not supplied by Automatic Systems).
There are one to six preloaded balancing springs (12) to help the motor open and close the barrier.
For barrier models with the automatic lifting option during power cuts, the preloading of springs is
increased in order for the latter to ensure the lifting of the arm in the event of power outages.
In normal operation condition a mechanical locking system holds the arm in its closed positions. Also, the
variable speed controller compensate for any effort made to move the barrier manually when the arm is in the
open, closed or stopped position.
In order to increase protection against vandalism (forcing the arm), the mechanical locking system can be
modified to act in power outage situation and also to lock the open position (see Ch 2.3. ).
The following table summarises the various possible combinations:
Locking situation
Locking of the arm (optional)
Locked position Type of lock
(see note Ch. 2.3. )
Locking in power outage and
operation.
(For barrier without automatic lifting
of the arm)
Locking of arm in open position
(option) Lock NC,
- Receives power during the movement of the arm in
order to release it.
- Lock released only during motion
Locking of arm in the closed position
(option)
Locking in operation only
(For barrier with automatic lifting of
the arm)
Locking of arm in open position
(option) Lock NO
- Receives power when the arm is closed or open in
order to lock it.
- Lock released in power outage and during motion.
Locking of arm in the closed position
(standard)
NC: Normally Closed = Closed in standby status (not turned on).
NO: Normally Open = Open in standby status (not turned on).
Note: The open and close position lock can only work in matching locking situation.

p 8/58
Technical Manual NAM-BL4x-MT-EN-C
The information in this document is the property of Automatic Systems and is confidential. The consignee withholds from using it for anything other than the use of the products or the execution of the
project to which they belong and withholds from communicating it to third parties without prior written agreement from Automatic Systems. Document subject to change without prior notice.
2.3. Mechanical locking of the arm
The lock type NO in closed position is standard on the equipment. However locks are available as an option
for the open position or in the NC type (locking in power outage).
These locks are placed on the reinforcing V-blocks (19), under the cover.
Note: Depending on the desired operating mode (specified when the order is placed), the installed locks will
be of NO (standard) or NC (option) type (see table in Ch. 2.2). However, for locking in both positions, the 2
locks will be systematically of the same type (NO or NC), as they are controlled by the same electromagnet.
The above illustration represents the locking of the arm in the open position by means of an NC lock. The
operation described below corresponds to this configuration, but can be applied in principle to other
configurations.
The lock is of the Normally Closed type: In standby mode (turned off), the spring (81) pushes the shank (82)
out of the electromagnet (80), which closes the clips (83) around the locking pin (84). The locking pin being
fastened to the hub (13), which in turn is attached to the arm’s driving shaft, which is therefore locked.
When a close command is sent to the barrier, the electromagnet is turned on. The shank (82) is pulled
towards the electromagnet, which results in the clips (83) opening.
At the same time, a pulse is given to the arm in the other direction (opening), to unlock the mechanism (the
clips could be stuck by the locking pin if the arm has been subjected to major stress in a locked position).
The closing of the arm is only started when the inductive sensor (86) detects the shank’s end washer, which
corresponds to the opening of the clips and the unlocking of the arm.
If the arm is not unlocked within 3 seconds, the barrier is put out of service.
Once the arm is closed (detection by the limit switch sensor (7, Ch. 2.1. ), the electromagnet is switched off.
LOCK NC DURING STANDBY (POWER OFF)
80
LOCK NC WHEN POWERED (POWER ON)
OPTION
LOCKING OF
THE ARM IN
OPEN
POSITION
8182
83
84
84
21
86
19. Reinforcing V-block (see Ch. 2.1. )
80. Electromagnet
81. Call back spring
82. Clip driving rod
83. Locking clips
84. Locking pin
86. Inductive sensor
19

p 9/58
Technical Manual NAM-BL4x-MT-EN-C
The information in this document is the property of Automatic Systems and is confidential. The consignee withholds from using it for anything other than the use of the products or the execution of the
project to which they belong and withholds from communicating it to third parties without prior written agreement from Automatic Systems. Document subject to change without prior notice.

p 10/58
Technical Manual NAM-BL4x-MT-EN-C
The information in this document is the property of Automatic Systems and is confidential. The consignee withholds from using it for anything other than the use of the products or the execution of the
project to which they belong and withholds from communicating it to third parties without prior written agreement from Automatic Systems. Document subject to change without prior notice.
3. AS1320 CONTROL BOARD
(Excract from AS1320 techniciean manual)
Legend
6:1. Fuses
6:2. Light indicating that the stabilised power supply is switched on
6:3. Menu display screen
6:4. Keys for navigating through the menu
6:5. Connector for the RJ45 communication cable
6:6. Terminal blocks for external communication (Input/Output connections)
6:7. Green LEDs (lights indicating that the control board has been turned on)
6:8. Connectors for presence detectors (for inductive loops)
6:1
6:2
6:3
6:7
6:4 6:5 6:8
6:6

p 11/58
Technical Manual NAM-BL4x-MT-EN-C
The information in this document is the property of Automatic Systems and is confidential. The consignee withholds from using it for anything other than the use of the products or the execution of the
project to which they belong and withholds from communicating it to third parties without prior written agreement from Automatic Systems. Document subject to change without prior notice.
The control board is the interface between the user and the barrier. It manages all of the latter’s actions,
including any potential options. The navigation of the display menus is based on an architecture using drop-
down menus with three levels: MENUS PARAMETERS VALUES.
Use the ◄►keys to move from one level to another (hold down for a few seconds to move from the standby
screen to another menu). Use the ▲▼ keys to navigate within the levels themselves. Press the OK key to
validate a value modification.
Note: The second column in the tables below provides the factory settings of the parameter values as they
are entered during manufacturing of the control board.
Nevertheless, as each piece of equipment has been specifically adjusted in our workshops, the values
actually present on the board may differ slightly.
Note: Below only the simplified menus are presented, which are sufficient for everyday use of the barrier.
Please refer to the control board manual (available upon request) for a detailed description of all of the
functions, adjusting their parameters, etc.
The menus are displayed on the
first line, in capital letters and
from the first character of the
LCD.
Press ▲or ▼for a few seconds
to leave the PRDSTD screen
and access other menus.
Only the first letter of each word in
the parameters is a capital.
Parameters are displayed on the
top line starting with the second
character of the LCD (i.e., there is
a space in front). At the end of the
first line the parameter unit
appears, if there is one.
The question mark (?) preceding the
parameter indicates that the latter is
ready to be modified.
The current value of the parameter
appears on the second line.
The asterisk (*) under a parameter
indicates that it is the factory setting.
The modification is validated by
pressing the OK key.
Save the modifications in
order to avoid losing them
during power outages (QUICK
START ►Memory
►Save.
Menus Parameters
A
rm Length
Barrier Type
A
rm Type
? Arm Length
* 3m00
? Arm Length
2m50
? Arm Length
2m00
? Arm Length
6m00
? Arm Length
3m50
? Arm Length
4m00
? Arm Length
4m50
? Arm Length
5m50
? Arm Length
5m00
CANCEL
VALIDATE OK
or
Values
QUICK START
PRDSTD - BL_xxx
DATE & TIME
CL REGULATION
TIMING
OUTPUT FUNCTION
SENSOR FUNCTION

p 12/58
Technical Manual NAM-BL4x-MT-EN-C
The information in this document is the property of Automatic Systems and is confidential. The consignee withholds from using it for anything other than the use of the products or the execution of the
project to which they belong and withholds from communicating it to third parties without prior written agreement from Automatic Systems. Document subject to change without prior notice.
3.1. PRDSTD – BL_xxx menu: Troubleshooting and monitoring
This screen appears when the unit is turned on and after there has not been any navigation through the
menus in simplified mode for 100 seconds.
Parameter Values Description
OK key: (only within this menu (*) and when no other
parameter is selected): command for opening and closing
the obstacle.
OK during opening: without effect.
OK during closing: inversion (= opening).
OK maintained: oscillating movement around the opening
limit switch: the obstacle opens, starts closing, opens
again, etc.
(*) Warning: in QUICKSTART menu, validating passage
from Extended to Simplified menus through the OK key
causes also an opening or closing movement of the arm,
even if a presence is detected by the Presence sensors.
Note: When the operating mode is configured as 1
contact (see the Exploitation parameter in the QUICK
START menu), the obstacle closes automatically when
the opening limit switch is detected.
Left key (◄): Change the menu display language with
each touch.
EN = English
FR = Français
NL = Nederlands
DE = Deutsch
ES = Español
IT = Italiano
SV = Svenska
Select the language using the OK key or allow it to
change automatically after a few seconds, following which
all of the preceding parameter modifications (including
the language) will be saved in MEM1.
Name of the program
Date (DD/MM)
Time (hh:mm)
Choice of language
by means of the ◄
button

p 13/58
Technical Manual NAM-BL4x-MT-EN-C
The information in this document is the property of Automatic Systems and is confidential. The consignee withholds from using it for anything other than the use of the products or the execution of the
project to which they belong and withholds from communicating it to third parties without prior written agreement from Automatic Systems. Document subject to change without prior notice.
Soft. Version Display the software version used by the control unit,
following format type – evolution – version – revision –
minor index of the application.
The descriptions included in this chapter correspond to
versions 00-00-06-rr-00.
Log Display of the last 100 events (use ►the ▲and keys to
view preceding events).
For the first two seconds, the event number (00 for the
last event recorded (= most recent), 01 for the preceding
event, and so on), as well as the date (year-month-day)
and time (hours-minutes-seconds) of creation are
displayed.
In the next two seconds, the event description is
displayed.
For example:
2 s Log
00 060324 235034 On 24 March 2006 at 23
hours (11 p.m.) 50 minutes
and 34 seconds…
2 s Log
Out Of Service …the apparatus was put out
of service.
2 s Log
01 060324 235034 View the preceding message
(01) using the ►▲ keys…
2 s Log
Open Time Out …we observe that it was put
out of service due to a time
out while opening.
Note: If no error message is displayed when the machine
fails, refer to the Troubleshooting chapter.
Power Up
Power was turned on.
Power Down
Power was turned off.
Short Circuit
Short circuit of the control board outputs (connector
blocks). The short circuit is declared and the equipment
put Out of Service only after 3 unsuccessful reactivation
tries within the 2.5 seconds following a voltage drop in the
24V power supply (this is to avoid putting it out of service
at inopportune moments, as for example during a network
changeover to an emergency generator).
If one of the outputs short circuits, all of them become
inactive and the control board must be powered up again
for the outputs to be reactivated.
Open Time Out Time out during opening: the time allocated for opening
was exceeded (TIMING menu, OpenTimeOut parameter).
Close Time Out Time out during closing: the time allocated for closing was
exceeded (TIMING menu, CloseTimeOut parameter).
Close Retries
Allotted number of trials to close have been executed (as
defined in the TIMING menu).

p 14/58
Technical Manual NAM-BL4x-MT-EN-C
The information in this document is the property of Automatic Systems and is confidential. The consignee withholds from using it for anything other than the use of the products or the execution of the
project to which they belong and withholds from communicating it to third parties without prior written agreement from Automatic Systems. Document subject to change without prior notice.
Arm Swing Off Arm detected out of its support jaw (see the Arm Swing Off
parameter in the OPTIONS menu).
If the message continues to be displayed after the arm is
rehinged, check the status of the SW arm presence
sensor and its fastening
Out Of Service Apparatus out of service. This may be caused by the following
events:
1) Time out during opening (see Open Time Out
message).
2) Time out during closing (see Close Time Out error) +
allotted number of tries to close have been executed
(see Close Retries message).
3) Arm is unhinged (see Arm Swing Off message).
4) Locking or unlocking failure of the BL4x (see Unlock
BL4x Er message).
5) Defect of the frequency inverter.
Time Adjust
Modification of the date and time.
Access Level Chg Change to the access level.
OOS Restore
Apparatus put back in service (after it has been out of
service) => see the RestartMode parameter under the
OPTIONS menu.
Test Intensive
Activation of the intensive test.
Lock Open
The Lock Open command of the test mode has been
activated.
Lock Close
The Lock Close command of the test mode has been
activated.
Safety Arm
Safety arm (only with the rubber protection profile option:
Rubber strip that detects when the arm makes contact
with a vehicle).
Sw Manual
Frequency converter power cut-off in order to prevent any
movement of the obstacle in case of:
Crank presence sensor activation (available on some
equipment for manual handling of the obstacle),
Door/hood opening sensors activation (option on
some equipment).
Reset Sensor Init Change of the positioning sensor type (cf. Positioning
parameter of QUICKSTART menu).
LS Fault
Both opening and closing limit switches are activated
simultaneously or badly connected during 100 ms, while
Positioning parameter of the QUICKSTART menu is set to
Limit Switches.
Reset LS Fault Limit switch problem resolved (see LS Fault error).

p 15/58
Technical Manual NAM-BL4x-MT-EN-C
The information in this document is the property of Automatic Systems and is confidential. The consignee withholds from using it for anything other than the use of the products or the execution of the
project to which they belong and withholds from communicating it to third parties without prior written agreement from Automatic Systems. Document subject to change without prior notice.
Analog. Fault
The analogue sensor gives 0 or 1023 during minimum
100 ms. This may result from a defective wiring, a wrong
positioning of the sensor in front of its cam, a defective
sensor, etc.
OP Power Cut Unlocking of the obstacle following an outage of the
supply voltage (if QUICK START ►Power Fail OP
►ON).
OP Power Blip Unlocking of the obstacle following a micro-outage of the
supply voltage (the voltage drops to 0 V during a few
milliseconds) (if QUICK START ►Power Fail OP ►ON).
In this state, the obstacle is STOPPED but still
operational, because the supply voltage has returned. The
apparatus waits for the next command to execute a
movement.
CoolingMotor ON
Start-up of the motor cooling fan.
Note: This message is only displayed if the Cooling – Log
(below) is ON.
CoolingMotor OFF Stopping of the fan that cools the motor.
Note: This message is only displayed if the Cooling – Log
(below) is ON.
Stop Time Out Elapse of the delay defined under the Max Stop
parameter of the TIMING menu for the regulation of the
obstacle position with regard to the Stop.
Download Chg Lv1 Downloading a version of the control board program that
differs from the one previously installed.
As the difference is of level 1 (minor index modification or
revision), the parameters continue operate with their value
saved in MEM1.
Download Chg Lv2 Downloading a version of the control board program that
differs from the one previously installed.
As the difference is of level 2 (modification of the version
or the evolution), all of the parameters are returned to
their default values.
WARNING: it is then necessary to set the parameters to
the actual configuration of the equipment and to save
them in MEM1.
Note: it would be wise to keep the parameters values
before changing the program version: Communication
parameter Extract Param (Technician level access).
Download Chg Lv3 Downloading a version of the control board program that
differs from the one previously installed.
As the difference is of level 3 (modification of the type), all
of the parameters are returned to their default values and
the counters are reset to 0.
WARNING: it is then necessary to set the parameters to
the actual configuration of the equipment and to save
them in MEM1.
Note: it would be wise to keep the parameters values
before changing the program version: Communication
parameter Extract Param (Technician level access).

p 16/58
Technical Manual NAM-BL4x-MT-EN-C
The information in this document is the property of Automatic Systems and is confidential. The consignee withholds from using it for anything other than the use of the products or the execution of the
project to which they belong and withholds from communicating it to third parties without prior written agreement from Automatic Systems. Document subject to change without prior notice.
Reset Counters
Counters reset to zero following the download of a
different program version of level 3 (see Download Chg
Lv3).
Curve 229Std
Change in the type of barrier: selection of curve 229
standard (Barrier Type parameter under the QUICK
START menu).
Curve 229Highway
Change in the type of barrier: selection of curve 229
highway (Barrier Type parameter under the QUICK
START menu).
Curve 1x-2x-3x-5x
Change in the type of barrier: selection of curve for BL16,
BL32, BL33, BL52, BL53 (Barrier Type parameter under
the QUICK START menu).
Curve BLG77
Change in the type of barrier: Selection of curve BLG77
(Barrier Type parameter under the QUICK START menu).
Curve Special
Change in the type of barrier: selection of the Special
curve (OPTIONS menu) for operation according to the OP
REGULATION and CL REGULATION menus.
Curve BL223
Change in the type of barrier: Selection of curve BL223
(Barrier Type parameter under the QUICK START menu).
Curve BL40 AVR
Change in the type of barrier: Selection of curve BL40
AVR (Barrier Type parameter under the QUICK START
menu).
Curve BL40 SR
Change in the type of barrier: Selection of curve BL40SR
(Barrier Type parameter under the QUICK START menu).
Curve BL41 AVR
Change in the type of barrier: Selection of curve BL41AVR
(Barrier Type parameter under the QUICK START menu).
Curve BL41 SR
Change in the type of barrier: Selection of curve BL41SR
(Barrier Type parameter under the QUICK START menu).
Curve BL43 AVR
Change in the type of barrier: Selection of curve BL43AVR
(Barrier Type parameter under the QUICK START menu).
Curve BL43 SR
Change in the type of barrier: Selection of curve BL43SR
(Barrier Type parameter under the QUICK START menu).
Curve BL44 AVR
Change in the type of barrier: Selection of curve BL44AVR
(Barrier Type parameter under the QUICK START menu).
Curve BL44 SR
Change in the type of barrier: Selection of curve BL44SR
(Barrier Type parameter under the QUICK START menu).
Curve BL46 AVR
Change in the type of barrier: Selection of curve BL46AVR
(Barrier Type parameter under the QUICK START menu).
Curve BL46 SR
Change in the type of barrier: Selection of curve BL46SR
(Barrier Type parameter under the QUICK START menu).
Curve RSB 70&71
Change in the type of equipment: Selection of curve RSB
70&71 (Barrier Type parameter under the QUICK START
menu).

p 17/58
Technical Manual NAM-BL4x-MT-EN-C
The information in this document is the property of Automatic Systems and is confidential. The consignee withholds from using it for anything other than the use of the products or the execution of the
project to which they belong and withholds from communicating it to third parties without prior written agreement from Automatic Systems. Document subject to change without prior notice.
Unlock BL4x Er
Only with locking of the arm option for BL4x. The inductive
sensor has not detected the release of the lock within the
3 seconds following the open or close request: check
whether the locking pin is pressing on the locking clips,
preventing them form opening, or whether the sensor is
defective.
Close Status Cases when the obstacle is prevented from closing during
a close request:
OK
Normal closure.
PS1 Activated A sensor (loop/cell) detects a presence or a fault in the
circuit. In the latter case:
Check whether the sensor is plugged into the
corresponding connector and whether it is functioning
properly.
Check whether the sensor is properly connected.
Check whether the sensors are programmed correctly
(SENSOR FUNCTION menu).
PS2 Activated
PS3 Activated
PS4 Activated
Lock OP Hold Check why the Lock Open command is being maintained
on the control board connector block.
Safe Arm Activ Activation of the Safety Arm sensor (only with the rubber
protection profile option: rubber strip that detects when the
arm makes contact with a vehicle):
Check whether the arm safety sensor is functioning
properly.
Check whether the Safety Arm parameter is
programmed correctly (Options menu).
PWF Open Activ Setting of the PWF Open Activ parameter of the
OPTIONS menu to ON, that is to say that during
activation the obstacle opens and waits for the activation
of a close or lock-close command.
Note: the closure loops are not taken into account for
closing in this case.
Lock Open LCD The Test Mode parameter of the TEST menu is not set to
Deactivated.
Delay Befor CL Wait for the delay programmed under the Delay Befor. CL
parameter under the TIMING menu to elapse.
Open Cmd Hold Check why the open command is being maintained on the
control board connector block.
Stop Cmd Hold Check why the stop command is being maintained on
the control board connector block.
Check whether the Stop Cmd parameter is
programmed correctly (Options menu).
Reader A Hold Check why the Reader A command is being maintained
on the control board connector block.
Reader B Hold Check why the Reader B command is being maintained
on the control board connector block

p 18/58
Technical Manual NAM-BL4x-MT-EN-C
The information in this document is the property of Automatic Systems and is confidential. The consignee withholds from using it for anything other than the use of the products or the execution of the
project to which they belong and withholds from communicating it to third parties without prior written agreement from Automatic Systems. Document subject to change without prior notice.
Position Fail The type of sensor selected is Analogue Sensor (QUICK
START ►menu Positioning); nevertheless, the obstacle
still has to be activated (►Activate Motor? ►OK).
Counter CR The reader counter (see the OPTIONS menu
Counter CR) is greater than zero.
Or the timing for no passage is other than zero (see
the TIMING menu No Passage).
Open Status Cases when the obstacle is prevented from opening
during a request to open.
OK Normal opening.
Lock CL Hold Check why the Lock CL command is being maintained on
the control board connector block.
Lock Close LCD The Test Mode parameter of the TEST menu is not set to
Deactivated.
Delay Befor OP Wait for the time programmed under the Delay Bef. OP
under the TIMING menu to elapse.
Stop Cmd Hold Check why the close order is being maintained on the
control board connector block.
Check whether the Stop CMD parameter is
programmed correctly (Options menu).
Arm ELV Locked Check whether the detector of the unlocking of the
electrically locking (ELV) tip is functioning properly.
Check whether the Arm parameter in the OPTIONS
menu is programmed correctly.
Arm ELV Detect Check whether the detector sensing the presence of the
arm is functioning properly on the control board connector
block.
Position Fail The type of sensor selected is Analog. Sensor (QUICK
START menu ►Positioning); nevertheless, the obstacle
still has to be activated (►Activate Motor? ►OK).
Counter 1 0 to 99,000,000
(0 by default)
Total number of manoeuvres executed by the obstacle
since it was first put into service.
Counter 2 0 to 99,000,000
(0 by default)
Representation of counter 1, with the possibility of
resetting it to zero.
Reset counter 2 Counter 2 reset to zero.
OFF (by default) No resetting.
ON Request to reset to zero.
Done Message is displayed for 1 second when the counter has
been reset to zero.

p 19/58
Technical Manual NAM-BL4x-MT-EN-C
The information in this document is the property of Automatic Systems and is confidential. The consignee withholds from using it for anything other than the use of the products or the execution of the
project to which they belong and withholds from communicating it to third parties without prior written agreement from Automatic Systems. Document subject to change without prior notice.
3.2. QUICK START menu: Quick configuration
This menu reviews the parameters that have to be configured before the equipment may be used.
Parameter Values Description
PS1 Function 0 (by default) to 7 Definition of the mode of operation of Presence
Sensor 1: see table below.
PS 2 Function: 0 (by default) to 7 Definition of the mode of operation of Presence
Sensor 2: see table below.
By default, the presence sensors are deactivated.
Therefore, in order to ensure that their safety functions are operational, it is
indispensable that the parameters for each of the presence sensors used be set.
closed obstacle open obstacle Closing obstacle
Sensor function Action upon
arrival in the
sensor’s field
Action upon
leaving the
sensor’s field
Action upon
arrival in the
sensor’s field
+
Action upon
leaving the
sensor’s field
0Deactivated ** --
1Opening Opening** Closing* Opening +Closing*
2CL_Stop+CL ** Closing*** Stop +Closing
3CL_OP+CL ** Closing*** Opening +Closing
4Nothin_Stop+CL ** -Stop +Closing
5Nothing_OP+CL ** -Opening +Closing
6Nothing_Stop ** -Stop
7Nothing_OP ** -Opening
Incompatible This message is displayed for 1 second if the selected operating mode for the sensor
is not compatible with the exploitation mode (parameter below). See the table of
incompatible modes here under.
*: Automatic closure only if the preceding opening was initiated by detection and not if presence is detected by another sensor.
Notably, if there is a power outage when the obstacle is open, the obstacle will not close automatically when the power is
brought back (a close command must be executed).
Warning: The presence sensor operating in Open mode may not be placed under the arm, because it is it is not secured, in
contrast to the other modes: a Lock Close command has priority for it (see the Exploitation parameter below) and could cause
the arm to close on a vehicle.
**: Opening is possible using the commands present on the control board's connector blocks: open command, reader command,
and Lock Open command.
***: If passage is detected while the obstacle is Locked Open, closure will take place when the Lock Open command is
deactivated.
: With regard to the underlined values, a close command must be executed to close the obstacle when it is open. The safety
function is only activated during the closing movement of the obstacle.
Note: the installation of 2 loops on PS1 and PS2 requires the use of a double detector since PS1 and PS2 are on the same
connector.
Note: 2 supplementary Presence Sensor functions (PS3 and PS4) are available through extended menu SENSOR FUNCTION.
Note: the sensor status (1/0) is always available (for each function mode) through extended menu OUTPUT FUNCTION.
Warning: When the power is turned on, the detectors (DP) measure the state of the loops and initialize the reference level with
regard to their environment. Hence, if a vehicle is present on the loop during activation, it will not be detected and the loop will give
the order to close (in modes 1, 2 and 3 only)!

p 20/58
Technical Manual NAM-BL4x-MT-EN-C
The information in this document is the property of Automatic Systems and is confidential. The consignee withholds from using it for anything other than the use of the products or the execution of the
project to which they belong and withholds from communicating it to third parties without prior written agreement from Automatic Systems. Document subject to change without prior notice.
Positioning Definition of the type of sensor used to position the
obstacle.
Limit Switches
(by default) To be selected if the open/close position is determined
by limit switches (standard for BL4x).
Analog. Sensor
To be selected if the position of the obstacle is
determined by an analogue sensor.
The analogue position sensor measures the distance
separating it from a spiral cam located on the shaft that
transmits the movement of the obstacle’s motor, which
means that the angular position of the obstacle is known
at all times. Also, see the Min Sensor Max parameter
below.
Manual Switch
This message is displayed if it is not possible to activate
the analogue sensor, as per one of these cases:
The crank presence detector (only present on some
equipments) is engaged.
=> Remove the crank so that the motor may be
engaged.
If the equipment does not have a crank presence
detector, the circuit may have been cut.
=> link the corresponding connections.
Activate Motor?
Pushing the OK key within 5 seconds launches the
analogue sensor activation procedure (see below) and
the movement of the obstacle!
The Barrier Type and Arm
characteristics must be selected
BEFORE initializing the analogue
sensor. Otherwise, rough movements of
the arm can occur with risk of injury for the
personnel and the equipment.
=> Navigate through the menus by means of the
upper key ().
Search LSO… The obstacle opens to look
for its open limit position.
The obstacle is moving
during this phase!
Search LSC… The obstacle closes to
look for its closed limit
position.
Init. Passed This is displayed if the open and closed limit values have
been recorded.
The analogue sensor is then operational.
The message disappears after 5 seconds or if the OK
key is pushed.
IMPORTANT: Save the values in MEM1 or MEM2
(MEMORY menu).
This manual suits for next models
3
Table of contents
Popular Automobile Electronic manuals by other brands

BASETech
BASETech 2162728 operating instructions
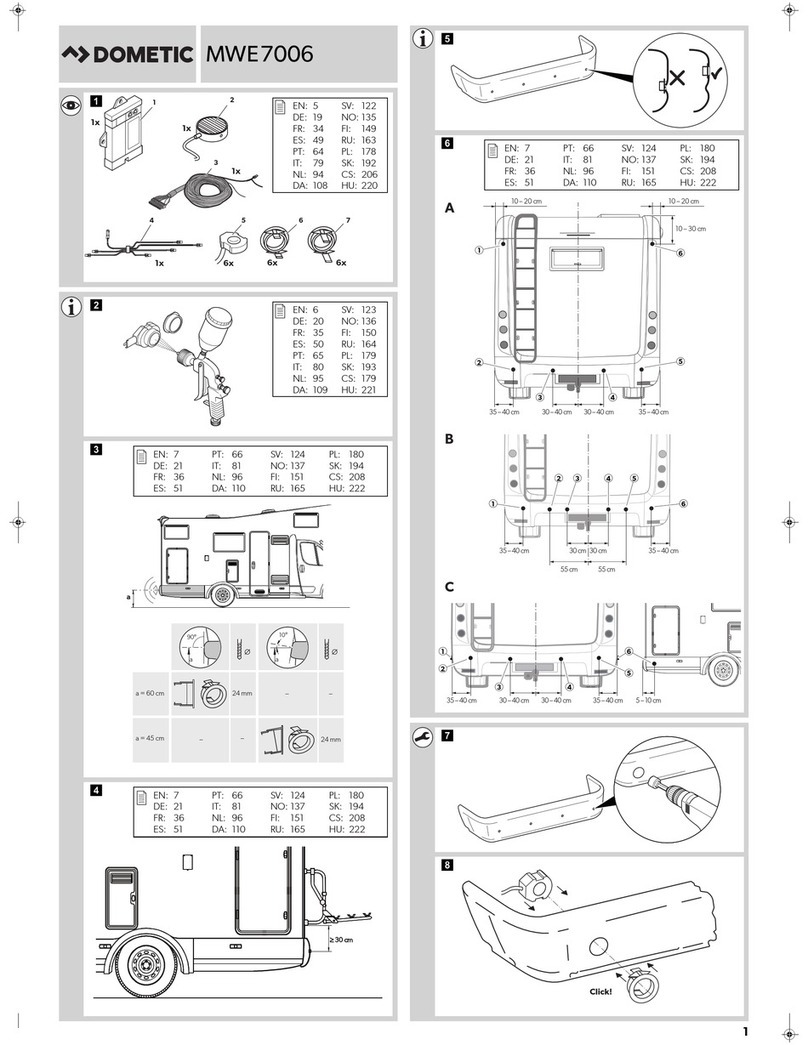
Dometic
Dometic MagicWatch MWE7006 Installation and operating manual
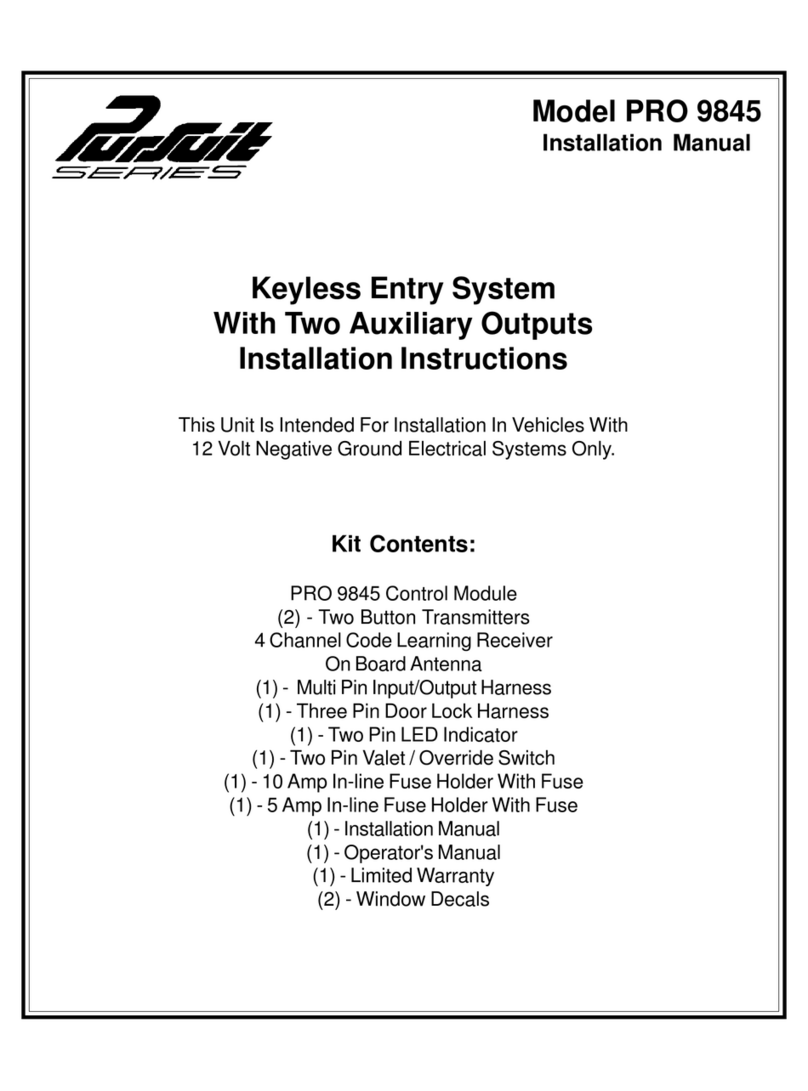
Audiovox
Audiovox Pursuit PRO 9845 installation manual
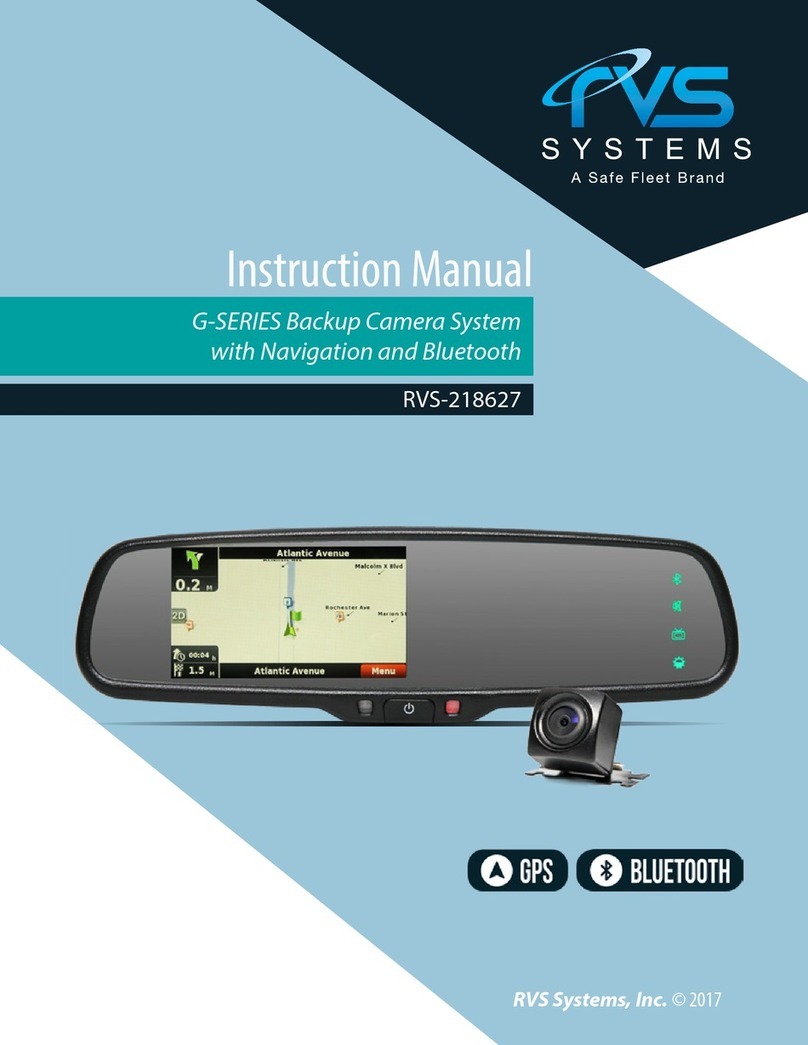
Safe Fleet
Safe Fleet RVS-218627 instruction manual
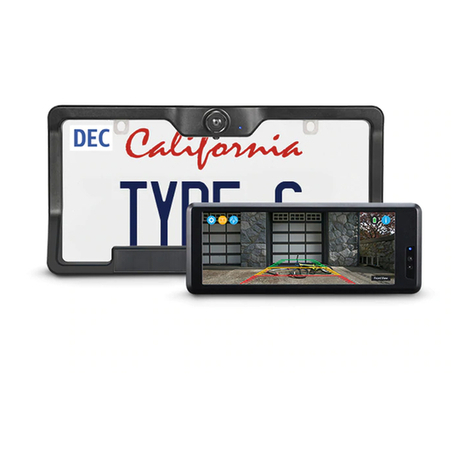
TypeS
TypeS BT57132 user manual
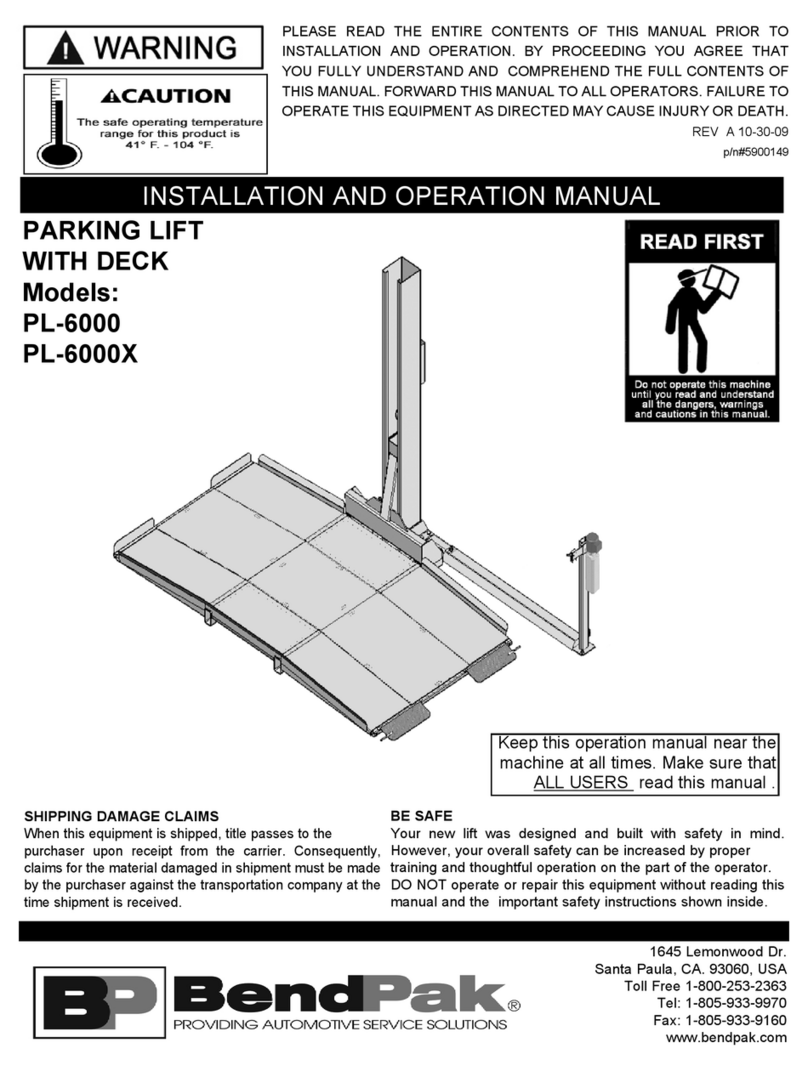
Bend-Pak
Bend-Pak PL-6000 Installation and operation manual