Autonics ARIO-C-MT User manual

Coupler manual
Field Network Devices
ARIO-C-MT
(ModbusTCP compatible)
Thank you for purchasing an Autonics product.
This user manual contains information about the product and its proper use, and
should be kept in a place where it will be easy to access.
www.autonics.com

ii © Copyright Reserved Autonics Co., Ltd.

Preface
© Copyright Reserved Autonics Co., Ltd. iii
Preface
Thank you for purchasing Autonics product.
Please familiarize yourself with the information contained in the Safety Considerations section
before using this product.
This user manual contains information about the porduct and its proper use, and should be kept
in a place where it will be easy to access.

Coupler Manual Guide
iv © Copyright Reserved Autonics Co., Ltd.
Coupler Manual Guide
Please familiarize yourself with the information in this manual before using the product.
This manual provides detailed information on the product's features. It does not offer any
guarantee concerning matters beyond the scope of this manual.
This manual may not be edited or reproduced in either part or whole without permission.
This manual is not provided as part of the product package.
Please visit our website (www.autonics.com) to download a copy.
The manual's content may vary depending on changes to the product's software and other
unforeseen developments within Autonics, and is subject to change without prior notice.
Upgrade notice is provided through our homepage.
We contrived to describe this manual more easily and correctly. However, if there are any
corrections or questions, please notify us these on our website.

Coupler Manual Symbols
© Copyright Reserved Autonics Co., Ltd. v
Coupler Manual Symbols
Symbol
Description
Supplementary information for a particular feature.
Failure to follow instructions can result in serious injury or death.
Failure to follow instructions can lead to a minor injury or product damage.
An example of the concerned feature’s use.
※1
Annotation mark.

Safety Considerations
vi © Copyright Reserved Autonics Co., Ltd.
Safety Considerations
Please observe all safety considerations for safe and proper product operation to avoid
hazards.
Safety considerations consist of ‘warning’ and ‘caution. The following symbols represent
caution due to particular circumstances in which hazards may occur.
Warning
Failure to follow instructions can result in serious injury
or death.
Caution
Failure to follow instructions can lead to a minor injury
or product damage.
Fail-safe device must be installed when using the unit with machinery that may cause
serious injury or substantial economic loss. (e.g. nuclear power control, medical equipment,
ships, vehicles, railways, aircraft, combustion apparatus, safety equipment, crime/disaster
prevention devices, etc.)
Failure to follow this instruction may result in personal injury, economic loss or fire.
Do not use the unit in the place where flammable/explosive/corrosive gas, high humidity,
direct sunlight, radiant heat, vibration, impact, or salinity may be present.
Failure to follow this instruction may result in explosion or fire.
Do not disassemble or modify the unit.
Failure to follow this instruction may result in fire.
Do not connect, repair, or inspect the unit while connected to a power source.
Failure to follow this instruction may result in fire.
Check ‘Connections’ before wiring.
Failure to follow this instruction may result in fire.
Use the unit within the rated specifications.
Failure to follow this instruction may result in fire or shortening the life cycle of the product.
Use a dry cloth to clean the unit, and do not use water or organic solvent.
Failure to follow this instruction may result in fire or electric shock.
When connecting the power input and I/O wiring, use AWG 22~16 cable.
After checking the connecting and removing the wire, use the crimp terminal.
Failure to follow this instruction may result in fire or malfunction due to contact failure.
Keep the product away from metal chip, dust, and wire residue which flow into the unit.
Failure to follow this instruction may result in fire or product damage.
Do not cut off power or disconnect connectors (or terminals) while operating the unit.
Failure to follow this instruction may result in fire or product damage.
※The specifications and dimensions of this manual are subject to change without any
notice

Caution during Use
© Copyright Reserved Autonics Co., Ltd. vii
Caution during Use
Follow instructions in ‘Caution during Use’. Otherwise, it may cause unexpected accidents.
ABUS power and I/O power should be insulated by the individually insulated power device.
Power supply should be insulated and limited voltage/current or Class 2, SELV power
supply device.
Use the rated standard cables and connectors. Do not apply excessive power when
connecting or disconnecting the connectors of the product.
Keep away from high voltage lines or power lines to prevent inductive noise.
In case installing power line and input signal line closely, use line filter or varistor at power
line and shielded wire at input signal line.
For the stable operation, use shield wire and ferrite core, when wiring communication wire,
power wire, or signal wire.
Do not use near the equipment which generates strong magnetic force or high frequency
noise.
Do not touch the module communication connecter part of the base.
Do not connect or remove the base while connected to a power source.
For removing the terminal, body or base, do not operate units for a long time without it.
This unit may be used in the following environments.
①Indoors
②Altitude max. 2,000m
③Pollution degree 2
④Installation category II

Table of Contents
viii © Copyright Reserved Autonics Co., Ltd.
Table of Contents
Preface.............................................................................................................................iii
Coupler Manual Guide.................................................................................................... iv
Coupler Manual Symbols.................................................................................................v
Safety Considerations..................................................................................................... vi
Caution during Use .........................................................................................................vii
Table of Contents...........................................................................................................viii
1Reference manuals ...................................................................................10
1.1 Instruction manual .............................................................................................10
1.2 Coupler manual .................................................................................................10
1.3 Module manual..................................................................................................10
1.4 DAQMaster user manual...................................................................................10
2Protocol overview .....................................................................................11
2.1 Modbus TCP......................................................................................................11
2.2 Basic memory map of field network ..................................................................11
2.2.1 Data Register Summary.............................................................................11
2.2.2 Data Register .............................................................................................11
2.2.3 Input Register.............................................................................................12
2.2.4 Holding Register.........................................................................................14
3Specifications............................................................................................15
4Hardware....................................................................................................17
4.1 Dimensions........................................................................................................17
4.2 Unit descriptions................................................................................................18
4.3 Rotary switch for communication setting...........................................................19
4.3.1 Transfer rate...............................................................................................19
4.3.2 Switch for station no...................................................................................19
4.4 Status indicator..................................................................................................20
5Memory map..............................................................................................22
5.1 Memory system .................................................................................................22
5.1.1 Data handling .............................................................................................22
5.1.2 Data type....................................................................................................22
5.2 Memory structure...............................................................................................23
5.3 Memory area......................................................................................................24
5.4 Gather diagnostic information of modules.........................................................24
5.5 Process image...................................................................................................25
5.6 Example of memory map...................................................................................25
5.6.1 Device.........................................................................................................25
5.6.2 Input process image...................................................................................25
5.6.3 Output process image................................................................................26

Table of Contents
© Copyright Reserved Autonics Co., Ltd. ix
5.6.4 Memory map based on field network.........................................................26
6Diagnosis function....................................................................................27
6.1 Overview............................................................................................................27
6.2 Diagnostic type..................................................................................................27
6.3 Definition............................................................................................................28

1 Reference manuals
10 © Copyright Reserved Autonics Co., Ltd.
1Reference manuals
1.1 Instruction manual
It describes an overview of Remote I/O, definitions of terms, installation environment,
mounting/removing method, wiring and troubleshooting.
1.2 Coupler manual
It describes the overview, specification, demensions, memory map and troubleshooting of each
communication.
1.3 Module manual
It describes the demensions, specification, connections and diagnosis function of each module
1.4 DAQMaster user manual
DAQMaster, a device integration management program, provides the expanded user
convenience. You can use the module setting, real-time control, and monitoring/diagnosis
function of input/output signal (except ARIO-C-PN and ARIO-C-PB). Also, you can arrange
products through virtual mode and recommended sorting.

2 Protocol overview
© Copyright Reserved Autonics Co., Ltd. 11
2Protocol overview
2.1 Modbus TCP
The Modbus protocol is the typical means of transfer with TCP / IP and commonly used to
connect industrial electronics. Simple and robust, it has become the de facto standard
communication protocol and is currently used to connect industrial electronics.
ARIO-C-MT, Modbus TCP-Based Coupler, synchronizes the data of all connected I / O modules
with Modbus TCP. The coupler determines the physical structure of the node and automatically
creates a local process image of all the I / O. It also includes a mixed arrangement of analog
(word) and digital (byte) modules.
The process image consists of the input and output data area.
2.2 Basic memory map of field network
The memory map is based on the addressing system of Autonics.
2.2.1 Data Register Summary
Address
Type
Description
Initial
Value
Function
Register
04
0101~0114
R
Read the product data
04
1024~0126
R
Read the product state data
04
1034~1087
R
Read the product settings
04
2001~2256
R
Read the input data
04
2513~xxxx
R
Read the diagnostic data
03/06/16
1034~1087
R/W
Read and write the product settings
03
2001~2256
R
Read the output data
06/16
2001~2256
W
Write the output data
2.2.2 Data Register
Accessible data register area via the input register and holding register
Address
Type
Description
Initial
Value
Function
Register
04
2001~2256
R
Input Data
03/06/16
2001~2256
R/W
Output Data
04
2513~xxxx
R
Diagnostic Data
The minimum data size is treated as 1 byte unit based on the module information.

2 Protocol overview
12 © Copyright Reserved Autonics Co., Ltd.
2.2.3 Input Register
Access to the coupler information via the input register.
Address
Type
Description
Initial
Value
Function
Register
04
0101
R
Product no.H
04
0102
R
Product no.L
04
0103
R
Hardware version. (0.1 units : 10 -> 1.0)
10
04
0104
R
Software version. (0.1 units : 10 -> 1.0)
10
04
0105
R
Model name 1
"AR"
04
0106
R
Model name 2
"IO"
04
0107
R
Model name 3
"-C"
04
0108
R
Model name 4
"-M"
04
0109
R
Model name 5
"T "
04
0110
R
Model name 6
" "
04
0111
R
Model name 7
" "
04
0112
R
Model name 8
" "
04
0113
R
Model name 9
""
04
0114
R
Model name 10
" "
Address
Type
Description
Initial
Value
Function
Register
04
1024
R
ABUS Error state
- 0: No Error
- 1: No Extension Module
- 2: Error Initialize
- 3: Error of Extension Module
04
0126
R
The number of connected modules
Address
Type
Description
Initial
Value
Function
Register
04
1034~1037
R
Modbus Master IP (Client)
Control Station
192.168.1.
250
04
1038~1041
R
Modbus Slave IP (Server)
Controlled Station (Coupler)
192.168.1.X

2 Protocol overview
© Copyright Reserved Autonics Co., Ltd. 13
Address
Type
Description
Initial
Value
Function
Register
04
1042~1045
R
Gateway
192.168.1.1
04
1046
R
PORT
502
04
1047
R
TCP Timeout (msec 단위, Keep Alive)
120
Address
Type
Description
Initial
Value
Function
Register
04
1048~1051
R
Accessible Modbus Master IP 1
04
1052~1055
R
Accessible Modbus Master IP 2
04
1056~1059
R
Accessible Modbus Master IP 3
04
1060~1063
R
Accessible Modbus Master IP 4
04
1064~1067
R
Accessible Modbus Master IP 5
04
1068~1071
R
Accessible Modbus Master IP 6
04
1072~1075
R
Accessible Modbus Master IP 7
04
1076~1079
R
Accessible Modbus Master IP 8
04
1080~1083
R
Accessible Modbus Master IP 9
04
1084~1087
R
Accessible Modbus Master IP 10

2 Protocol overview
14 © Copyright Reserved Autonics Co., Ltd.
2.2.4 Holding Register
Access to the coupler information via the holding register.
Address
Type
Description
Initial
Value
Function
Register
03/06/16
1034~1037
R/W
Modbus Master IP (Client)
Control Station
192.168.1.
250
03/06/16
1038~1041
R/W
Modbus Slave IP (Server)
Controlled Station (Coupler)
192.168.1.X
03/06/16
1042~1045
R/W
Gateway
192.168.1.1
03/06/16
1046
R/W
PORT
502
03/06/16
1047
R/W
TCP Timeout (msec 단위, Keep Alive)
120
Address
Type
Description
Initial
Value
Function
Register
03/06/16
1048~1051
R/W
Accessible Modbus Master IP 1
03/06/16
1052~1055
R/W
Accessible Modbus Master IP 2
03/06/16
1056~1059
R/W
Accessible Modbus Master IP 3
03/06/16
1060~1063
R/W
Accessible Modbus Master IP 4
03/06/16
1064~1067
R/W
Accessible Modbus Master IP 5
03/06/16
1068~1071
R/W
Accessible Modbus Master IP 6
03/06/16
1072~1075
R/W
Accessible Modbus Master IP 7
03/06/16
1076~1079
R/W
Accessible Modbus Master IP 8
03/06/16
1080~1083
R/W
Accessible Modbus Master IP 9
03/06/16
1084~1087
R/W
Accessible Modbus Master IP 10

3 Specifications
© Copyright Reserved Autonics Co., Ltd. 15
3Specifications
Model
ARIO-C-MT
Coupler type
Modbus TCP
Power
supply※1
ABUS(external
consump.)
24VDCᜡ, max. 400mA
(Max. 9.6W, Coupler+Module, max. 200mA/CH, 2CH/COM)
ABUS(internal
supply)
5VDCᜡ, max. 960mA
(max. 4.8W, module)
I/O
24VDCᜡ, max. 4,000mA
(max. 96W, max. 2,000mA/CH, 2CH/COM)
Power
consumption
Coupler
24VDCᜡstandby/run: 200mA,
Max. load: 400mA (coupler max. load)
Internal
communication
Protocol
ABUS protocol
Transmission
speed
4Mbps only
Memory※2
Input
512 byte
Output
512 byte
Max. connections for modules
※2
64 units (max. length is up to 768mm)
Higher-level
protocols
Transfer rate
10/100Mbps
Distance
between Nodes
Max. 100m
Communication
connector
RJ45 connectors (min.CAT5e)
Concurrent
connection of
Node
Depending on the network settings
Node setting
Rotary switch for communication setting in ARIO (Station no.)
Topology
Bus, Tree, Star
Installation method
DIN rail mounting
Setting and monitoring
PC connection with USB 2.0 Micro type connector
(comprehensive device management program, DAQMaster)

3 Specifications
16 © Copyright Reserved Autonics Co., Ltd.
Model
ARIO-C-MT
Insulation resistance
Over 100MΩ(at 500VDCᜡmegger)
Dielectric strength
1000VAC 50/60Hz for 1 min
Noise immunity
±500V the square wave noise (pulse width: 1 ㎲) by the noise
simulator
Vibration
Mechanical
0.7mm amplified at frequency of 10 to 55Hz (for 1 min) in each
X, Y, Z direction for 1 hour
Malfunction
0.5mm amplified at frequency of 10 to 55Hz (for 1 min) in each
X, Y, Z direction for 10 min.
Shock
Mechanical
300m/s²(approx. 30G) in each X, Y, Z direction for 3 times.
Malfunction
100m/s²(approx. 10G) in each X, Y, Z direction for 3 times.
Environment
Ambient temp.
-10 to 55℃, storage: -25 to 70℃
Ambient humi.
35 to 85%RH, storage: 35~85%RH
Protection structure※3
IP20 (IEC standards)
Material
Terminal: polyamide6, Body: modified polyphenylene oxide,
Base: polyamide6, poly oxy methylene
Approval
Weight※4
Approx. 265g (approx. 165g)
※1. It is including power/special modules and excluding coupler/end modules. In case of one
coupler module connecting, the ARIO digital module is available to connect up to 8 units, and the
ARIO analog and special modules are available to connect up to 4 units. For connecting the
modules, consider power concumption of the sensors and drivers connected the ARIO coupler.
※2. If it over the limit size or connected units, system may be error.
※3. Autonics test standard
※4. The weight includes packaging. The weight in parenthesis is for unit only.
※Environment resistance is rated at no freezing or condensation.

4 Hardware
© Copyright Reserved Autonics Co., Ltd. 17
4Hardware
4.1 Dimensions
(1) Coupler
(2) End module

4 Hardware
18 © Copyright Reserved Autonics Co., Ltd.
4.2 Unit descriptions
1. Communication connector: RJ45 connector
: You can use a universal Ethernet connector / cable (Category 5E), but we recommend
using connectors and cables that are certified by the MODBUS(Modbus TCPAssociation).
2. Communication setting switch (station no: X16, X1)
3. Setting connector (USB 2.0 type Micro B)
: You can connect DAQMaster to configure and monitor.
4. Indicators for power and comm. status
4-1 Internal / external state of coupler: Displays the input power / operation state of the
coupler.
4-2 State of Field network: Displays the operation of the field network.
5. Power terminal block
6. ABUS comm. connector: Input terminal that supplies circuit driving power of the coupler,
ABUS, and modul by receiving 24VDC.
I/O power supply : Supplies power for input / output signal of module by receiving DC, AC,
etc.

4 Hardware
© Copyright Reserved Autonics Co., Ltd. 19
4.3 Rotary switch for communication setting
4.3.1 Transfer rate
Based on the network quality, Auto-Negotiation is performed to determine 10 / 100Mbps.
4.3.2 Switch for station no.
Switch
Description
Station no.: X16
Use to distinguish the order (name) of couplers.
Range: 01 to 255
Station no.: X1
The rotary switch cannot be changed while the power is operating. To apply the changed rotary
switch, the coupler must be turned on again.
The switch for station number can change the last 3 of the IP address '192.168.2.3' that the
coupler saves. You can also change the IP address arbitrarily via DAQMaster.
[Example] ‘12h' of the switch means '192.168.2.18'.
However, if settings of switches are all '00', the station number (IP address) is set based on the
information that the coupler saves.

4 Hardware
20 © Copyright Reserved Autonics Co., Ltd.
4.4 Status indicator
(1) Definition
Indicator
Color
ON
OFF
POWER
Green
The power voltage of coupler is connected.
(supply 24VDC)
No power supply
SYSTEM
Green
Normal operation
(device on online state, communicating with
master)
Stop operation
Red
Failure to initialize coupler (recovery failed)
Recovery error during the coupler operation
(recovery failed)
Difference between field network type and
firmware version (recovery failed)
Normal operation
DIAG
Green
Normal operation (Multi Packet and Single
Packet are operating)
Stop operation of
coupler or in error
condition.
Red
Internal network (ABUS) inoperable state
Normal operation
IO
POWER
Green
The I/O power voltage of coupler is connected.
No power supply
(2) Status
Indicator
Color
Flashing
Flashing 1
Flashing 2
Flashing 3
Flashing 4
POWER
Green
ㅡ
ㅡ
ㅡ
ㅡ
ㅡ
SYSTEM
Green
Wait for
connecting the
master after
coupler
initialization
completes
ㅡ
ㅡ
ㅡ
ㅡ
Red
Change during
Initializing coupler
or rotary switch
operation
Field network
initialization failed
(recovery failed)
ㅡ
ㅡ
ㅡ
ㅡ
DIAG
Green
Hot-swap state
(normal state)
ㅡ
ㅡ
ㅡ
ㅡ
Red
Module, which
different from the
removed module,
is inserted.
(normal operation)
ㅡ
Initialization
failure:
There is no
connected
module.(re
covery
failed)
Initialization
failure:
abnormal
module is
operating
(recovery
failed)
Initialization
failure:
maximum
module /
data size
exceeded
IO
POWER
Green
ㅡ
ㅡ
ㅡ
ㅡ
ㅡ
Table of contents
Other Autonics Switch manuals
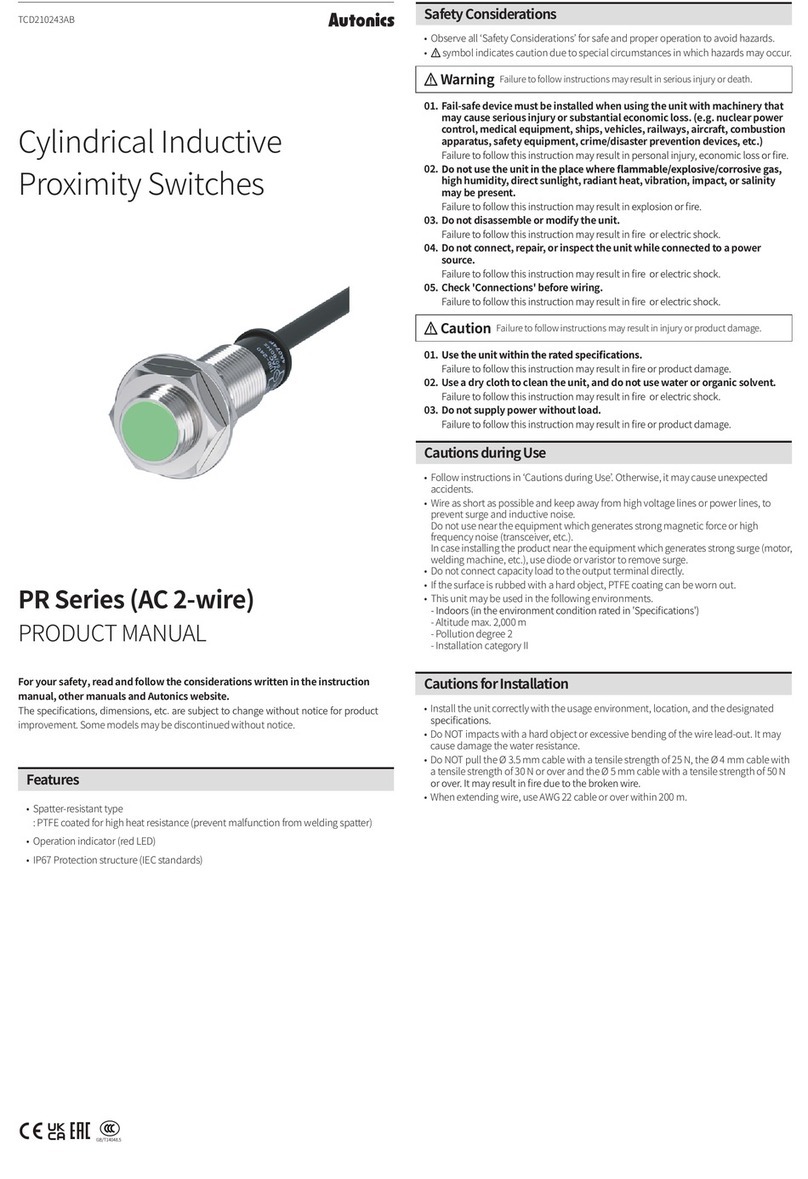
Autonics
Autonics PR Series User manual
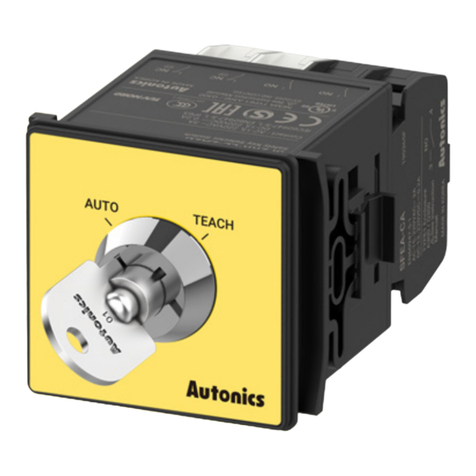
Autonics
Autonics SF2KR Series User manual
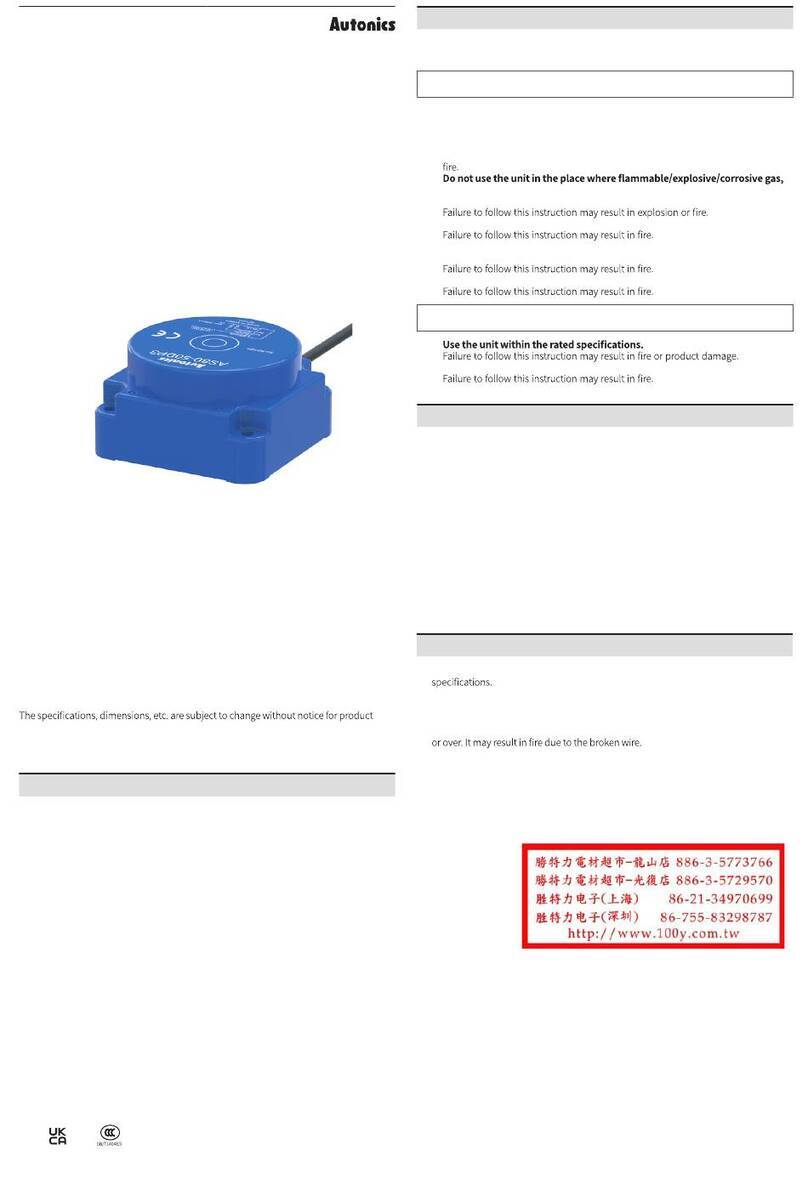
Autonics
Autonics AS Series User manual
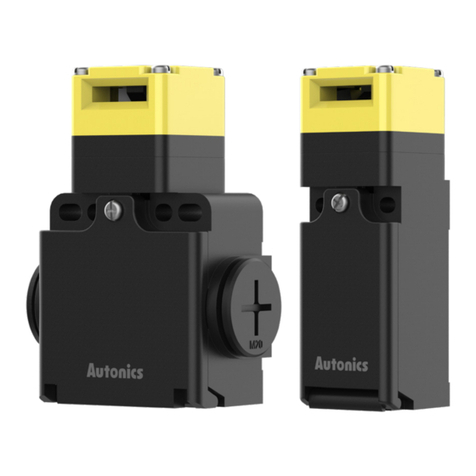
Autonics
Autonics SFD Series User manual

Autonics
Autonics SFDL2 Series User manual
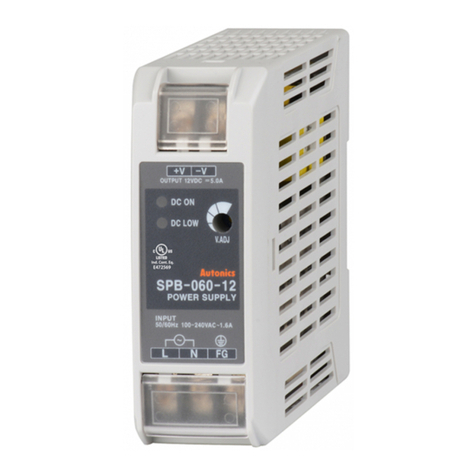
Autonics
Autonics SPB Series User manual
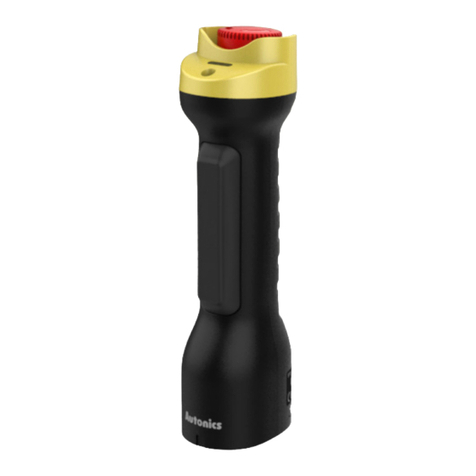
Autonics
Autonics SFEN Series User manual
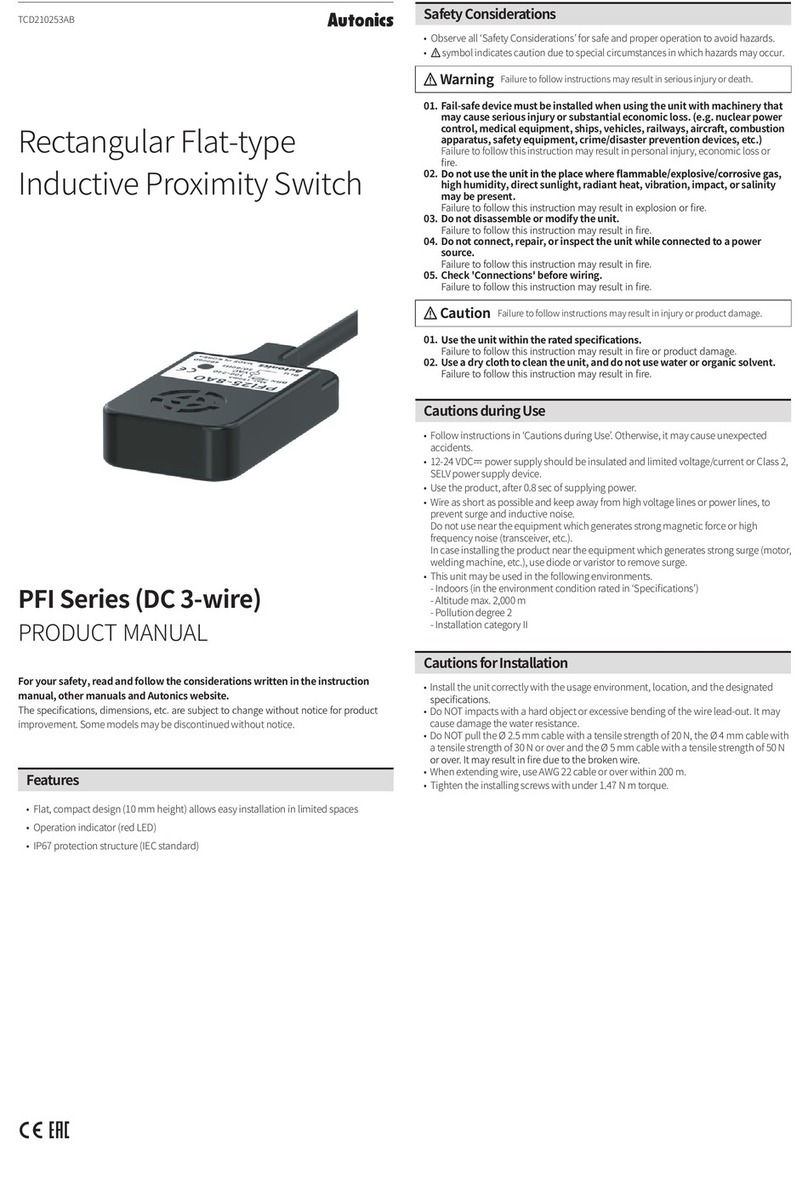
Autonics
Autonics PFI Series User manual
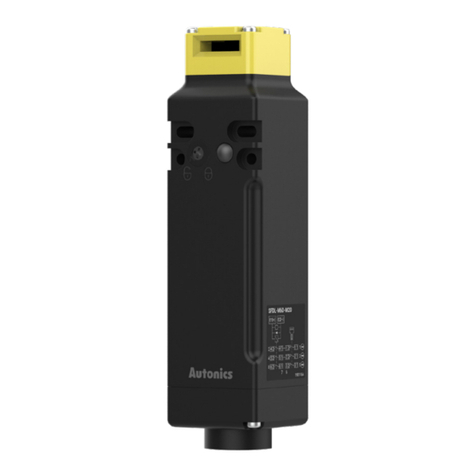
Autonics
Autonics SFDL Series User manual
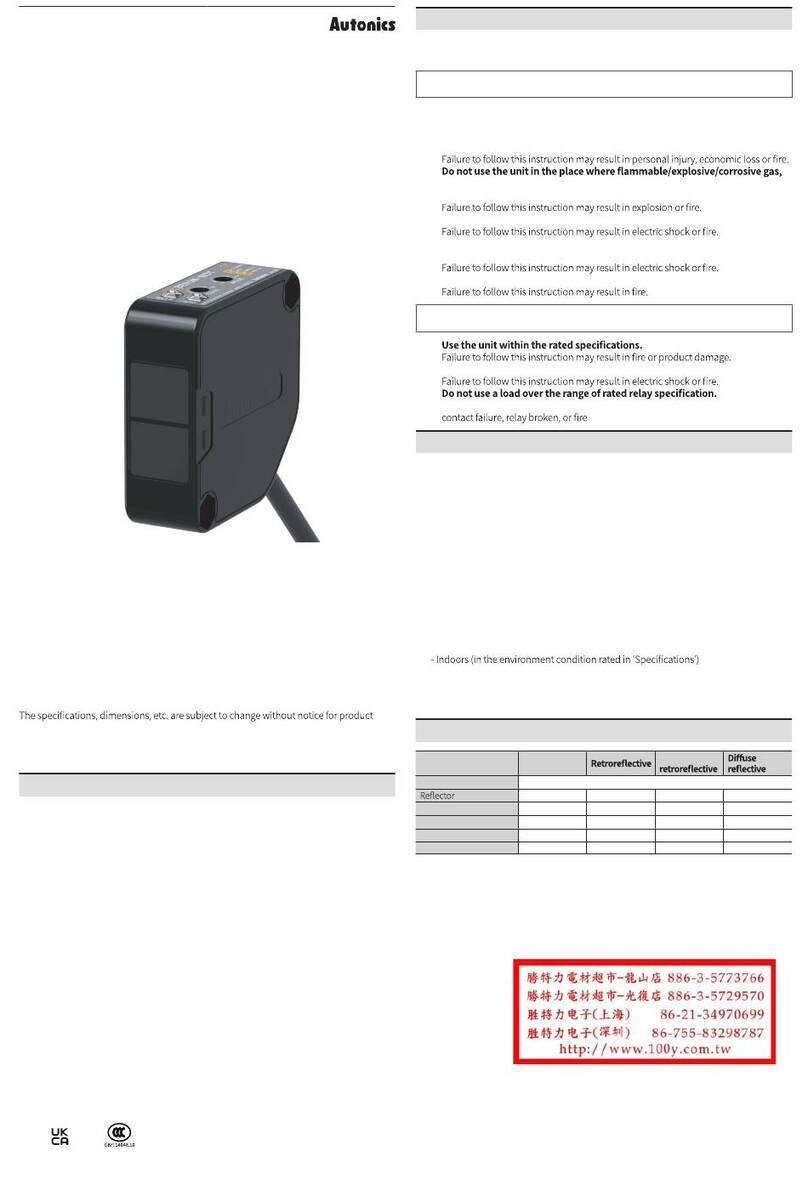
Autonics
Autonics BEN Series User manual