Böcker LMX 500 Manual

Original Manufacturer Operating
and Maintenance Instructions
GB
Material Lifts
LMX / LHX
LMX 500
LHX 330
LHX 500
105000017

Material Lift LMX / LHX
2
105000017
Product identification
Type: LMX 500
LHX 330
LHX 500
Document identification
- Translation of the German original operating instructions -
Document No.: 105000017
Version: 06.04.2022
Manufacturer
© Böcker Maschinenwerke GmbH
Lippestr. 69-73
DE-59368 Werne
Tel. +49 2389 7989-0
Fax +49 2389 7989-9000
info@boecker.de
www.boecker.de
Before commencing any works, these operating and maintenance
instructions must be carefully read!

Material Lift LMX / LHX
105000017
3
1Description ......................................................................................................... 4
2Transport ............................................................................................................ 5
2.1 Conditions of transport....................................................................................................5
2.2 Transportation risks..........................................................................................................5
2.3 Transport of material and installation lift......................................................................6
3Installation .......................................................................................................... 8
3.1 Notes....................................................................................................................................8
3.2 Setting-up of the material-installation lift .....................................................................8
4Commissioning.................................................................................................10
5Operation of LMX / LHX ...................................................................................12
6Safety..................................................................................................................14
6.1 Safety instructions for assembly, commissioning, operation and maintenance14
6.2 Monitoring of the safety devices..................................................................................14
6.3 General safety instructions...........................................................................................16
7Maintenance and inspection ...........................................................................17
8Conduct in case of malfunction......................................................................19
9Replacement parts............................................................................................20
10 Safety regulations.............................................................................................21
10.1 UVV Regulations VBG 14 Lifting platforms................................................................21
11 Technical data LMX 500...................................................................................24
12 Technical data LHX 330 / 500..........................................................................25
Appendix.......................................................................................................................26

Material Lift LMX / LHX
4
105000017
1 Description
Item 1.5 /Koth es ! Network/Boeker/All ge me in es /Inform at ion en zurBe triebsanleitun g Böcker @7\mo d_ 1140875004052 _1 .do c@71 243
The material and installation lift is a mobile lifting device, which can be used in closed spaces.
Under the conditions listed in point 6 “Monitoring of safety equipment” in these operating
instructions, the material lifts listed below can also be used outside closed spaces.
(see page 14 ).
The listed material lifts must only be used on level surfaces and load-bearing substrate,
irrespective of whether they are used within or outside of closed spaces.
Prior to using the unit, please ensure that there are no steep slopes, holes, rubble or slippery
ground or other safety hazards.
This must be checked each time prior tocommissioning.
The max. load is ...
Type
Max. load [kg]
LMX 500
500
LHX 330
500
LMX 500
500
Item 1.8 /FI/ ----------Endofp aragraph----------- @3\mod_1120132332937 _1.doc @17416
Item 1.31 /FI/ ----------End of paragraph----------- @3\mod_1120132332937_ 1.doc @1 74 16
The installation lifts of the LHX series consist of a standard material and installation lift
LMX with an “electro-hydraulic drive”.
The standard power supply is 230V 50Hz.

Material Lift LMX / LHX
105000017
5
2 Transport
2.1 Conditions of transport
In order to prevent damage or life-threatening injuries during the transport of the material and
installation lifts, it is imperative that the following points are observed:
•Transport works must only be carried out by qualified personnel in accordance with the
safety instructions and in compliance with the unladen weight of thematerial-installation
lift, using a sufficient number of people.
•For the transportation of the material-installation lifts and associated component parts
only appropriate means of transport and suitable load handling attachments and lifting
tackle must be used.
•Prior to moving, check if any potential parking brakes must be released. After relocating,
the parking brakes must be applied.
•During transport, the permitted floor load must be observed!
•It is generally prohibited to be positioned below suspended loads!
•Ensure that your vehicle is suitable for the transportation of these material-installation
lifts. Check if your load securing equipment (e.g. lashing straps) is sufficient to
appropriately secure the load. The loading process must only be carried out on level
surfaces.
•The material-installation lifts must be sufficiently secured on the loading area of your
vehicle.
•The integrated wheels in the front parts are not designed for bearing permanent loads!
2.2 Transportation risks
During the transport of the material-installation lifts, the following specific hazards must be
expected:
•Improper moving of thematerial lifts may result in injury to persons or damage to objects.
•To prevent accidents, always ensure that you have a clear view in the driving direction
and that there are no people in the transport area. Depending on the circumstances, at
least one further person is required for safety purposes.
•If the proper load handling equipment is not used, the material-installation lift may be
severely damaged.
•Should a component of the material lift be damaged or disabled during transport,
commissioning of the material-installation lift is not permitted, as the consequences are
not calculable. The lift may only be commissioned when the damage has been properly
repaired.
•Make sure that all parking brakes have been engaged after transportation, as the
material lift could otherwise begin to move automatically.

Material Lift LMX / LHX
6
105000017
2.3 Transport of material and installation lift
Item 2.3 /Ko th es ! Net work /Bo ek er/Sicherheit/Allgemeiner Text Siche rhe it Boecker @8 \m od_1141813939045_1.doc @7 47 31
The installation lift can betransported in vehicles or on trailers either upright or lying flat. If it is
lying on its side during transport, the rail safety mechanism must be locked (Fig. 1) and the
cable must be tight, as otherwise the rails slide apart and the cable could become slack.
The installation lift is dispatched with the front parts of the chassis folded up and reverse
mounted crane fork (example LMX Fig. 2).
Fig. 1 - Rail safety mechanism
Fig. 2 - Transport position
Ensure that your vehicle is suitable for the transportation of these material lifts. Check if your
load securing equipment (e.g. lashing straps) is sufficient to appropriately secure the load. The
loading process must only be carried out on level surfaces.
For the loading of the material lifts, put the unit into the transport position (Fig. 2). Tilt the
material lift on the loading area with the loading wheels (near the hoist). Now raise thematerial
lift at the chassis and push the same horizontally via the loading wheels on the loading area
into the transport position. Whenthe transport position has been reached, secure the material
lift with suitable load securing equipment.
The material lifts must be sufficiently secured on the loading area of your vehicle.
We recommend that the material lifts of type LHX 300 and LHX 500 are loaded by 2 persons!

Material Lift LMX / LHX
105000017
7
LHX:
During each transport where the material and
installation lift LHX is lying on its side, the
hydraulic tank must also be closed by means of
the block tap (Fig. 2.1).
CAUTION!
If the tank is not closed, oil will leak out!
After unloadingfrom the transport vehicle or during the removal of the material lift from the
storage site, move it with the black wheels (ø250mm ).
For this purpose, carefully tilt the material lift backwards (hoist side) and let it onto the wheels
(ø250mm ). Keep the material lift balanced in this transport position.
CAUTION!
Caution at sharp gradients. The operator must always stand on the slopingside. Potentially
wheel the unit around using 2 persons.
Fig. 2.1 - block tap

Material Lift LMX / LHX
8
105000017
3 Installation
3.1 Notes
The material-installation lift has undergone a function test prior to professional packing! The
packaging material must be disposed of or reused in accordance with the applicable rules of
each country of installation.
During the installation of the equipment/system, the following safety instructions must always
be observed, in order to avoid life-threatening injuries, damage to machinery/systems and
other material damage.
•Upon delivery, check the material lift for damage. Only a faultless material lift may be set
up. Any potential transport damage must be immediately reported by the transport
company or the responsible body. If appropriate, the lift must not be commissioned.
•Setting up, assembly and installation of the material lifts may only be carried out by
qualified persons in compliance with the safety instructions.
•The transport locks may only be removed when thecomponents have beentaken to their
ultimate position and when they have been properly mounted there.
•Prior to the start of the setting-up work, all components must be checked for transport
damage. Pay particular attention to the cable guide (Danger: slack cable!)
•It must be ensured that only authorised persons are present in the work area and that
other persons are not exposed to hazards by the setting-up work.
•The material lift may only be set up on level andsuitable (bearingcapacity, oil tightness)
areas.
•All connections in the material lift - e.g. cables or similar - must be laid in such a way that
they do not cause any risk of stumbling.
•The rules for the operating materials, lubricants and auxiliary supplies must be observed.
•Welding operations cause a fire hazard, therefore it is imperative to be familiar with the
fire-extinguishing appliances on site.
3.2 Setting-up of the material-installation lift
First install the chassis with both front parts, by loosening and removing the horizontally
integrated hexagonscrew M16 x 170 with the hexagon nut.
Fold down the front parts in order:
First, fold down one front part, push the hexagon screw M16 x 170 into the existing hole from
above and firmly screw in with the hexagon nut. Repeat this process for the remainingside.

Material Lift LMX / LHX
105000017
9
CAUTION!
For this purpose, use a suitable tool to ensure that the link is strong.
CAUTION!
When folding the front parts, watch the boom (rail package) and if necessary, keep the
same back to prevent tipping of the material lift.
If you wish to set the unit to the transport position, follow the steps for thesetting-up in
reverse order.
For storing the material lift, select a safe storage place where the unit is protected from dirt,
weather and unauthorised use. Leave the unit only on level surfaces and fix the castors with
locks.

Material Lift LMX / LHX
10
105000017
4 Commissioning
CAUTION!
Directly after setting up or prior to commissioning LHX lifts, the block tap at the
hydraulic tank must always be opened (Fig. 2.2.)!
NOTE!
Prior to connecting the installation lift LHX with the local supply network, check with a
connector plug if the electric equipment of the lift is compatible with the local supply
network. If this is not the case, you must not operate the material and installation lift
LHX with this supply network!
Before putting the device into operation, check the wire rope for damage, correct wire
guidance and correct winding of the wire rope. In case of defective components (wire
cable, pulleys, mountings, cable crimping etc.) and/or incorrect cable guidance (wire
cable is not running in the pulley), the commissioning or operating of the equipment is
prohibited or must be stopped immediately!
Unbolt the carriage by pulling out the rail safety mechanism, turning it backwards andto lower
it again in the last rail (Example: Fig. 3 LMX).
Release the hexagon nut of the fork safety bolt and then remove the latter. Now pull the crane
fork fromthe carriage by carefully lifting the carriage.
Fit the crane fork either to the underside or the upper side of the carriage (Example: Fig. 4
LMX). The fork arms are now pointing away fromthe rail package. Push through the fork safety
bolt andscrew on with the hexagon nut.
The two lateral outriggers (Fig. 6) must be attached for additional stability and aligned
accordingly.The outriggers mayonly be loweredtothe extent that the fourcastors do not loose
contact with the ground. Ensure that the locking bolts lock the outriggers.
Fig. 2.2 - block tap

Material Lift LMX / LHX
105000017
11
With the spirit level (Example: fig. 5 LMX) the lift can be levelled off. The unit must be level on
all sides.
Fig. 3 - Rail safety mechanism
Fig. 4 - Crane fork
Fig. 5 - Spirit level above winch
Fig. 6 - Lateral outriggers with spindle
Follow the steps for commissioning in reverse order to stop the unit.

Material Lift LMX / LHX
12
105000017
5 Operation of LMX / LHX
The installation lift must only be used on even surfaces, all locks at the castors must be
engaged and never overloaded.
Installation lifts must not be wheeled around when loaded.The material lifts can be used within
enclosed spaces. Under the conditions listed in point 6 “Monitoring of safety equipment” in
these operating instructions, the material lifts listed can also be used outside closed spaces
(see page 14).
LMX:
The load is lifted by turning the crank handle clockwise. The load is automatically held if the
crank handle is released. To lower the load, the crank handle must be turned anti-clockwise.
The crank handle is prevented from winding back by means of an integrated automatic brake.
Approx. 20 m of unloaded cable can bespooled on the winch drum. Only a length of cablestill
enabling the winch drum flangeto project at least 1.5 times the cable diameter can bespooled.
This avoids overloading the winch and the cable running off at the side of the drum. It is
important to ensure that the wire rope is correctly wound onto the winding drum. When driving
down while loaded, at least 2 winds of the cable must remain on the drum.
Cable recommendation
Cable Ø 7 mm
Single wire strength
1770 N/qmm
DIN
Zinc coated according to DIN 3060, Section 20 + 22
VBG 14 UVV (Accident Prevention Regulations)
LHX:
After the power supply required for the unit has been established, switch the unit on via the
motor protection circuit breaker. The circuit breaker serves at the same time as emergency
shut-off for the unit. The hydraulic winch is operated via a manual control valve.
•Manual lever up = load upwards
•Manual lever down = load downwards
After releasingthe manuallever, it automatically goes intothemiddleposition and the hydraulic
winch is shut down. The raised load is thenkept in the respective position by means of a non-
return valve and hydraulically operated brakes.
An overloading of the hydraulic winch due to overload is prevented by a pressure relief valve.

Material Lift LMX / LHX
105000017
13
CAUTION!
It must be ensured that the hydraulic shutoff valve shuts off the winch in the lowest position of
the crane fork. Otherwise, damage is caused to the wire cable and the hydraulic winch.
After the work with this unit has been completed, or if the work with thematerial andinstallation
lift LHX is stopped for a longer period of time, the unit must be switched off using the circuit
breaker, in order to avoid unnecessary warming up of the hydraulic oil and unnecessary wear
and tear.
After the work is completed and the unit is left, it must be secured against unintended use (lock
on circuit breaker)!
WARNING!
The load must be secured on the crane fork with appropriate load securing
equipment (e.g. lashing straps) when moving up and down! The load must be placed
centrally in accordance with the crane fork diagram.
WARNING!
Prior to commencing work with the installation lift, the operator must be familiarised
with the unit and accurately instructed (Section 43 VBG 14 UVV).
Read, understand and follow the safety regulations and instructions by the
manufacturer as well as the operating manual.
Also read, understand and follow the safety regulations of the employer and the
workplace regulations.

Material Lift LMX / LHX
14
105000017
6 Safety
6.1 Safety instructions for assembly, commissioning, operation and
maintenance
•The material lift may only be operated, maintained and repaired by authorised, qualified
and instructed technical personnel!
•For safety reasons, the responsibilities of the personnel for assembly, commissioning,
operation and maintenance must be precisely defined!
•Refrain from any operation that adversely affects the safety of the material lift!
•The material lift may only be operated in a technically good order, while keeping safety
and potential dangers in mind. In case of any malfunctions, the material lift must be shut
down immediately!
•If the operator identifies any safety-relevant changes in the material-installation lift, he
has a duty to shut down the material-installation lift immediately and report this to the
competent person!
•For the security of the operator, all arising maintenance, cleaning and repair work may
only be carried out without the lift being loaded and appropriately secured!
•Prior to the commencement of all cleaning, servicing and repair works, the material lift
must be secured against rolling away unexpectedly or the rails extending. For this
purpose, the following procedure must be followed:
•Push down the locking brake at the castors, let the rail safety mechanism snap in
•Set up and place appropriate warning signs, cordon off or secure the area
•The operator must ensure that the safe condition of protection systems and locks at the
material lift are checked by qualified person at regular intervals, at least, however, once
a year.
•Work at the material-installation lift may only be carried out by specialist personnel.
6.2 Monitoring of the safety devices
•Never overload the installation lift.
•Do notcarry any persons - only use for loads. Only usethe unit forthe intended purpose.
•The load must be secured on the crane fork with appropriate load securing equipment
(e.g. lashing straps) when moving up and down! The load must be placed centrally in
accordance with thecrane fork diagram.
•Persons must not stand below the load. Persons are not permitted to be present in the
working and hazardous area of the material lift, except the operator.
•Do not stand below the load.
•Do not use a ladder at or on the lift.
•Never drive the extended lift with a load.
•Never leave the material lift unattended in operational condition or with a load that is
being lifted.
•Caution with tight wires, projected ceilings and overhead lines abovethelift.Always keep
a sufficient safety distance to electric lines and devices.
•Distance to live overhead lines of at least 5 m (up to 200kV), at higher voltage, the
distance must be correspondingly larger. While doing so, follow the respective official
regulations.
•The load centre must never be a distance of more than 330 mm from the back of the
fork.

Material Lift LMX / LHX
105000017
15
•When using crane fork extensions or bulky loads, the maximum load must be reduced
in proportion to the load centre.
•The material lifts can be used outside enclosed spaces in the following conditions:
- Load : 0 kg up to a maximum of 500 kg
- Wind force : Use up to a maximum of wind force 3 (Beaufort scale)
- Surface of load : lengthways (of the chassis) : 1.25 m²
: crossways (of the chassis) : 1.00 m²
When lifting loads with large wind-exposed areas (i.e. air ducts, metal containers),
operations must be discontinued correspondingly earlier.
•Daily:
- the wire cable and the cable guidance (pulleys, pulley displacements)
- correct winding of the wire rope on the rope drum
- the crane fork
- the rail profiles
- the rail guide (plastic rolls)
- the chassis with the front components
- the manual winch or the hydraulic winch
- Hydr. functional components (e.g. hoses, screw fittings, motor, brakes, and
similar)
- the castors and wheels
- the fixing elements (e.g. screws, nuts and bolts)
- the outriggers with the supporting spindles
need to be checked.
In case of damage or signs of damage immediately discontinue operation. Check the entire
unit for deformation or damage, corrosion or oxidation and tears in welding seams or
components.
•Always carry out an inspection prior to commissioning.
•Always carry out a functional test prior to commissioning.
•It is strictly prohibited to modify the unit in such a way that the safety may be adversely
affected or that the official safety regulations are breached.
•These operating instructions are expressly a part of the material lifts and must always be
kept with the units.
•The stickers on the material lift must be clearly visible and recognisable in terms of
content (text and pictures).

Material Lift LMX / LHX
16
105000017
6.3 General safety instructions
Apart from the notes in these operating instructions the general safety and accident prevention
regulations must be observed:
•The material-installation lift may only be operated if all protection systems are fully
functional and there is no apparent damage to the lift. Prior to each commissioning, the
material-installation lift must be checked for external visible damage and functionality of
existing safety devices
•The operator is responsible to ensure that all persons using the material-installation lift
have read and understoodthe entire operating instructions, paying particularattentionto
the chapter “Safety”!
•Böcker Maschinenwerke GmbH does not accept any liability for damage resulting from
failure to comply with the operating instructions!
•Unauthorised modifications and alterations of the material-installation lift relating to
safety are expressly prohibited!
•This include for example:
1. - Removal of safety devices
2. - Installation of non-original components etc...
Böcker Maschinenwerke GmbH does not accept any liability for damage attributable to such
actions! These are carried out solely at the risk of the user! Operating and maintenance tasks
must only be carried out by qualified personnel who are familiar with these operating and
maintenance instructions.
The operational safety of the material-installation lift is only ensured if the lift is used as
intended. In case of doubt, themanufacturer should be consulted. The manufacturer does not
accept any liability for damage caused as a result of improper use of the unit!
During all works, the existing respective domestic regulations regarding accident prevention
and occupational safety, as well as, if applicable, the internal regulations of the respective
operator, must be complied with, even if these are not comprehensively described in these
instructions.
The respective local applicable legal safety regulations must be complied with.
When any work is carried out on the unit, the surrounding area must be free from obstructions.
The work area should, if possible, be identified or marked in colour and if necessary, cordoned
off.
Always ensure that you are wearing protective clothing (protective helmet, glasses,
gloves) when using the material lift!

Material Lift LMX / LHX
105000017
17
7 Maintenance and inspection
•Daily:
- the wire cable and the cable guidance (pulleys, pulley displacements)
- correct winding of the wire rope on the rope drum
- the crane fork
- the rail profiles
- the rail guide (plastic rolls)
- the chassis with the front components
- the manual winch or the hydraulic winch
- Hydr. functional components (e.g. hoses, screw fittings, motor, brakes, and
similar)
- the castors and wheels
- the fixing elements (e.g. screws, nuts and bolts)
- the outriggers with the supporting spindles
need to be checked.
•In case of damage or signs of damage immediately discontinue operation. Prior to
commissioning the material lift, defective or damaged components must be replaced.
(see also point 9 “Replacement parts”).
•Check the entire unit for deformation or damage, corrosion or oxidation and tears in
welding seams or components.
•Protect the lift from contamination, rain and other weather effects. The mast elements
made of aluminium should be protected from dirt and rubbish.
•Treat the interior side of the mast with silicone spray.
•Check plastic rolls and pulleys for wear and tear or damage.
•The crank handle winch has already been greased at thefactory. Thethread at thecrank
handle must, however, be greased at all times. It is recommended to regularly oil the
bearing bushes of the drive shafts and the drum hubs. For this purpose, observe the
enclosed original operating instructions of the manufacturer of the manual winch.
CAUTION!
Do not oil or grease the brake mechanism!
•Ensure that the lift is inspected annually by a qualified person Parts that are subject to
wear and tear and safety components must be replaced as required. Only original parts
must be used (Section 39-40-50 VBG 14 UVV)

Material Lift LMX / LHX
18
105000017
•The installation lift must be inspected by a qualified person depending on operating
conditions andthe operationalcircumstances, however, at least once every year (annual
occupationalsafety inspection in accordance with UVV).
•These operating instructions are expressly a part of the material lifts and must always be
kept with the units.
•The stickers on the material lift must be clearly visible and recognisable in terms of
content (text and pictures).

Material Lift LMX / LHX
105000017
19
8 Conduct in case of malfunction
Before commencing work, check if the mast components are running upwards in the correct
sequence. First, the carriage must lift up, then the front mast, then the 2. mast etc. The
sequence during lowering is reversed. If the sequence changes, this should be checked
immediately.
Potential causes:
•The wire cable has jumped from the pulley.
•The wire rope is not correctly wound on the rope drum
•Pulleys or pulley bearings are defective.
•The pulley does not turn properly or not at all.
•Plastic pulleys or plastic pulley bearings are defective.
•The plastic pulley bearings do not turn properly or not at all.
•There is dirt and rubbish between the mast components or on the pulleys.
•Damaged mast cable or carriage.
•Overloading or one-sided load.
It is imperative to remove the cause and restore the correct sequence. In case of queries
regarding the unit you can call us at any time.
Böcker Maschinenwerke GmbH
Lippestraße 69-73
59368 Werne
Federal Republic of Germany
Tel. +49 ( 0 ) 2389 7989-0
Fax +49 ( 0 ) 2389 7989-9000
e-mail info@boecker.de

Material Lift LMX / LHX
20
105000017
9 Replacement parts
Only original replacement parts may be used, as otherwise warranty claims will not be valid
and the safety of the lift may potentially no longer be ensured. Modifications and alterations
not carried out by us release us from any responsibility in the event of any damage. In the
event of repair or procurement of replacement parts, please contact us.
Böcker Maschinenwerke GmbH
Lippestraße 69-73
59368 Werne
Federal Republic of Germany
Tel. +49 ( 0 ) 2389 7989-0
Fax +49 ( 0 ) 2389 7989-9000
e-mail info@boecker.de
This manual suits for next models
2
Table of contents
Other Böcker Lifting System manuals
Popular Lifting System manuals by other brands
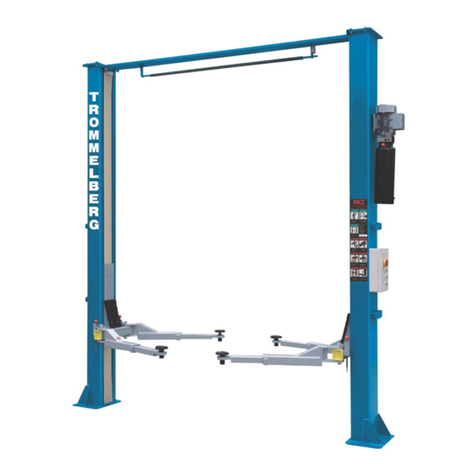
TROMMELBERG
TROMMELBERG TST40G user manual
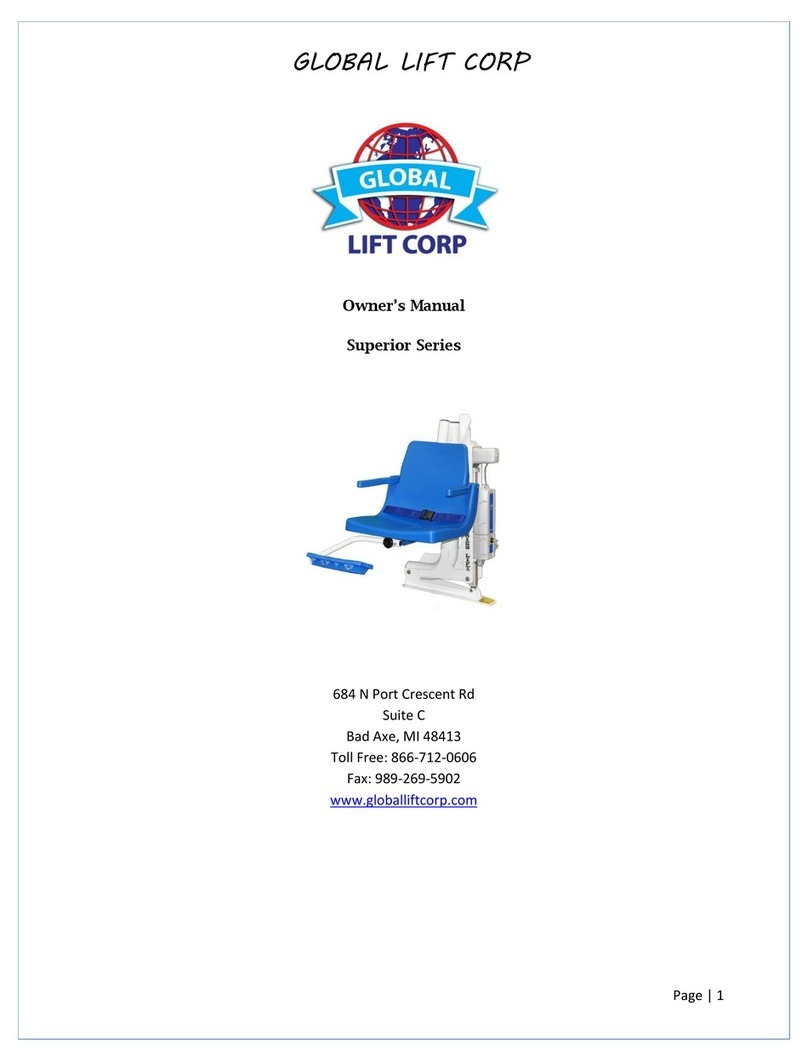
Global Lift
Global Lift Superior Series owner's manual
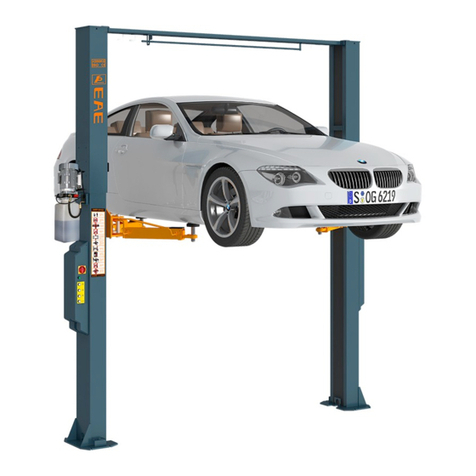
EAE
EAE EE62C-35T-E Installation, operation, and parts manual
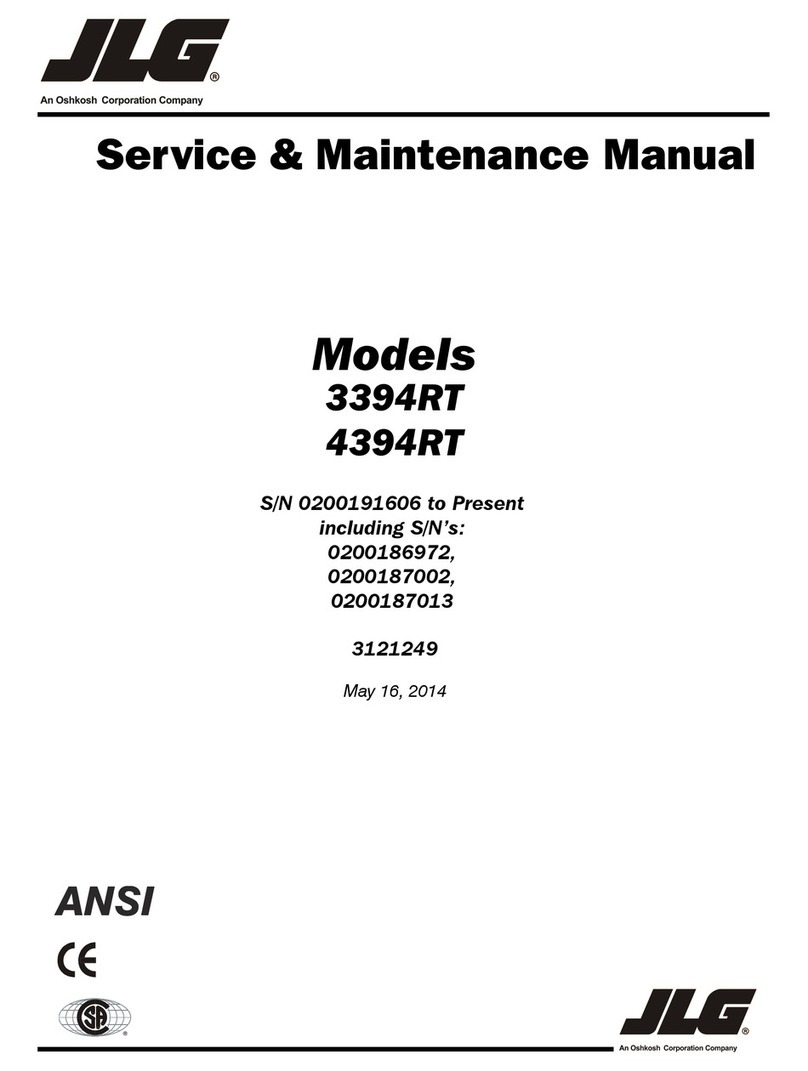
Oshkosh Corporation
Oshkosh Corporation JLG 3394RT Service maintenance manual
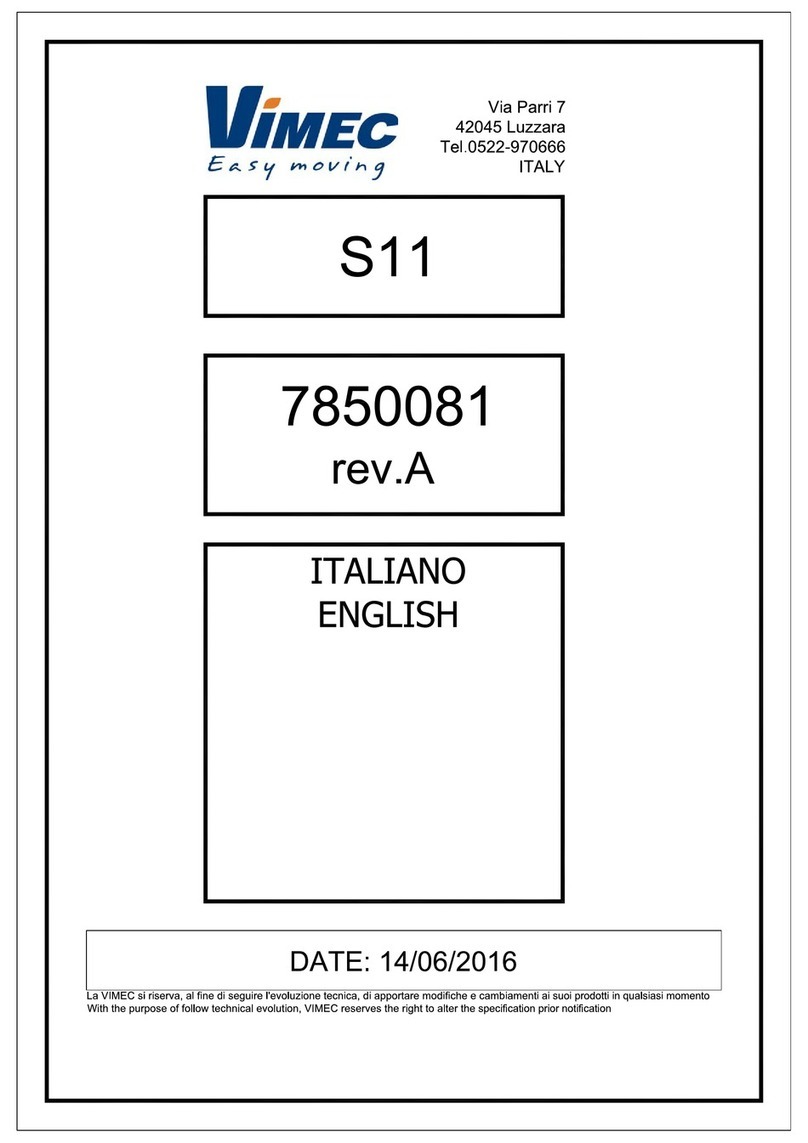
vimec
vimec S11 manual
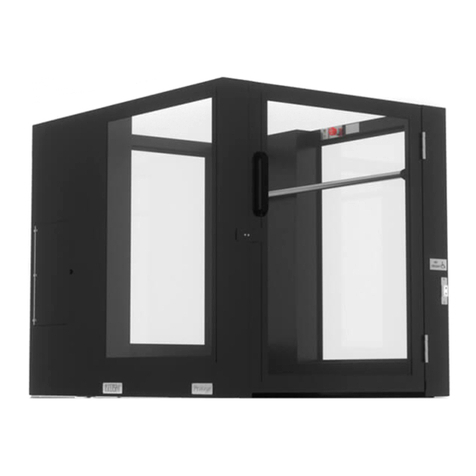
Ascension
Ascension 5442P Maintenance & Repair Manual