Bühler technologies TC-MIDI Plus Reference guide

TC-MIDI (+)
Dok-No.: BX440016 ◦ Version: 09/2021 ◦ Ref.: 998BX440016
Analysentechnik
Kurzanleitung Peltier-Messgaskühler deutsch................................................................................................................................................. 2
Brief Instructions Peltier Sample Gas Cooler english ...................................................................................................................................... 11
Notice de montage Refroidisseur de gaz de mesure Peltier français ......................................................................................................... 20
Guía rápida Refrigerador termoeléctrico de gases de muestreo español................................................................................................. 29
快速使用指南 帕尔帖样气冷凝器 chinese (simplified)......................................................... 38
Краткое руководство Охладитель Пельтие для анализируемого газа русский.............................................................................. 45

TC-MIDI (+)
1 Einleitung
Diese Kurzanleitung unterstützt Sie bei der Inbetriebnahme
des Gerätes. Beachten Sie die Sicherheitshinweise, andernfalls
können Gesundheits- oder Sachschäden auftreten. Lesen Sie
vor der Inbetriebnahme die Originalbetriebsanleitung mit
Hinweisen zur Wartung und Fehlersuche sorgfältig durch.
Diese finden Sie auf der beigefügten CD und im Internet unter
www.buehler-technologies.com
Bei Fragen wenden Sie sich an:
Bühler Technologies GmbH
Harkortstraße 29
40880 Ratingen
Deutschland
Tel.: +49 (0) 21 02 / 49 89-0
Fax: +49 (0) 21 02 / 49 89-20
Diese Betriebsanleitung ist Teil des Betriebsmittels. Der Her-
steller behält sich das Recht vor, die Leistungs-, die Spezifikati-
ons- oder die Auslegungsdaten ohne Vorankündigung zu än-
dern. Bewahren Sie die Anleitung für den späteren Gebrauch
auf.
1.1 Bestimmungsgemäße Verwendung
Das Gerät ist zum industriellen Einsatz in Gasanalysensyste-
men bestimmt. Es stellt eine wesentliche Komponente zur
Aufbereitung des Messgases dar, um das Analysengerät vor
Restfeuchtigkeit im Messgas zu schützen.
Beachten Sie die Angaben hinsichtlich des spezifischen Ver-
wendungszwecks, vorhandener Werkstoffkombinationen so-
wie Druck- und Temperaturgrenzen.
1.2 Lieferumfang
• Kühler
• Produktdokumentation
• Anschluss- bzw. Anbauzubehör (optional)
2 Sicherheitshinweise
Das Gerät darf nur von Fachpersonal installiert werden, das
mit den Sicherheitsanforderungen und den Risiken vertraut
ist.
Beachten Sie unbedingt die für den Einbauort relevanten Si-
cherheitsvorschriften und allgemein gültigen Regeln der
Technik. Beugen Sie Störungen vor und vermeiden Sie da-
durch Personen- und Sachschäden.
Der Betreiber der Anlage muss sicherstellen, dass:
• Sicherheitshinweise und Betriebsanleitungen verfügbar
sind und eingehalten werden,
• die jeweiligen nationalen Unfallverhütungsvorschriften
beachtet werden,
• die zulässigen Daten und Einsatzbedingungen eingehal-
ten werden,
• Schutzeinrichtungen verwendet werden und vorgeschrie-
bene Wartungsarbeiten durchgeführt werden,
• bei der Entsorgung die gesetzlichen Regelungen beachtet
werden,
• gültige nationale Installationsvorschriften eingehalten
werden.
GEFAHR
Elektrische Spannung
Gefahr eines elektrischen Schlages
a) Trennen Sie das Gerät bei allen Arbeiten vom Netz.
b) Sichern Sie das Gerät gegen unbeabsichtigtes Wiederein-
schalten.
c) Das Gerät darf nur von instruiertem, fachkundigem Per-
sonal geöffnet werden.
d) Achten Sie auf die korrekte Spannungsversorgung.
GEFAHR
Giftige, ätzende Gase
Das durch das Gerät geleitete Messgas kann beim Einatmen
oder Berühren gesundheitsgefährdend sein.
a) Überprüfen Sie vor Inbetriebnahme des Geräts die Dich-
tigkeit ihres Messsystems.
b) Sorgen Sie für eine sichere Ableitung von gesundheitsge-
fährdenden Gasen.
c) Stellen Sie vor Beginn von Wartungs- und Reparaturar-
beiten die Gaszufuhr ab und spülen Sie die Gaswege mit
Inertgas oder Luft. Sichern Sie die Gaszufuhr gegen unbe-
absichtigtes Aufdrehen.
d) Schützen Sie sich bei der Wartung vor giftigen / ätzenden
Gasen. Tragen Sie die entsprechende Schutzausrüstung.
GEFAHR
Potentiell explosive Atmosphäre
Explosionsgefahr bei Verwendung in explosionsgefährdeten
Bereichen
Das Betriebsmittel ist nicht für den Einsatz in explosionsge-
fährdeten Bereichen geeignet.
Durch das Gerät dürfen keine zündfähigen oder explosiven
Gasgemische geleitet werden.
3 Transport und Lagerung
Die Produkte sollten nur in der Originalverpackung oder ei-
nem geeigneten Ersatz transportiert werden.
Bei Nichtbenutzung sind die Betriebsmittel gegen Feuchtig-
keit und Wärme zu schützen. Sie müssen in einem überdach-
ten, trockenen und staubfreien Raum bei einer Temperatur
von -20°C bis 60°C (-4 °F bis 140 °F) aufbewahrt werden.
4 Aufbauen und Anschließen
4.1 Anforderungen an den Aufstellort
Das Gerät ist für den Einsatz in geschlossenen Räumen zur
Wandmontage vorgesehen. Beim Einsatz im Freien ist ein
ausreichender Wetterschutz vorzusehen.
Montieren Sie das Gerät so, dass unterhalb des Kühlers genü-
gend Raum zur Ableitung des Kondensates vorhanden ist.
Oberhalb ist etwas Platz für die Gaszuführung vorzusehen.
Es ist darauf zu achten, dass die zulässige Umgebungstempe-
ratur eingehalten wird. Die Konvektion des Kühlers darf nicht
behindert werden. An den Lüftungsöffnungen muss ausrei-
2 Bühler Technologies GmbH BX440016 ◦ 09/2021

TC-MIDI (+)
chend Platz zum nächsten Hindernis sein. Insbesondere auf
der Luftauslassseite muss die Entfernung mindestens 10 cm
betragen.
Bei Montage in geschlossenen Gehäusen, z.B. Analysenschrän-
ken, ist für eine ausreichende Entlüftung zu sorgen. Reicht die
Konvektion nicht aus, empfehlen wir, den Schrank mit Luft zu
spülen oder einen Ventilator vorzusehen, um die Innentempe-
ratur zu senken.
4.2 Montage
Verlegen Sie die Gaszuführung zum Kühler mit Gefälle. Die
Gaseingänge sind rot markiert und zusätzlich mit „IN“ ge-
kennzeichnet.
Bei großem Kondensatanfall empfehlen wir, einen Flüssig-
keitsabscheider mit automatischer Kondensatentleerung ein-
zusetzen. Hierzu eignen sich unsere Kondensatabscheider
11LDV38, AK20, AK5.5 oder AK5.2.
Für die Kondensatableitung stehen Glasgefäße und automati-
sche Kondensatableiter zur Verfügung, die extern unterhalb
des Gerätes zu montieren sind. Bei Verwendung von automa-
tischen Kondensatableitern muss die Messgaspumpe vor dem
Kühler montiert werden (Druckbetrieb), da sonst die Funktion
der Kondensatableiter nicht mehr gewährleistet ist.
Befindet sich die Messgaspumpe am Ausgang des Kühlers
(Saugbetrieb), ist der Einsatz von Kondensatsammelgefäßen
aus Glas oder der Einsatz von peristaltischen Pumpen zu emp-
fehlen.
Anschluss der Kondensatableiter
Je nach Werkstoff ist eine Verbindungsleitung aus Verschrau-
bung und Rohr oder Schlauch zwischen Wärmetauscher und
Kondensatableiter herzustellen. Bei Edelstahl kann der Kon-
densatableiter direkt am Verbindungsrohr aufgehängt wer-
den, bei Schlauchleitungen ist der Kondensatableiter mittels
einer Schelle separat zu befestigen.
Der Kondensatableiter kann direkt am Wärmetauscher befes-
tigt werden.
Kondensatleitungen sind grundsätzlich mit Gefälle und Min-
destnennweite DN 8/10 (5/16“) zu verlegen.
Der Wärmetauscher DTV kann nicht in Verbindung mit einem
automatischen Kondensatableiter betrieben werden.
4.2.1 Anschluss Gasanschlüsse Filter (optional)
Die Verbindung zwischen Ausgang Wärmetauscher und Ein-
gang Filter ist bereits verschlaucht. Der Anschluss G1/4 oder
NPT 1/4“ (Filterkopf mit NPT gekennzeichnet) für den Gasaus-
gang ist mittels geeigneter Verschraubung sorgfältig und
fachgerecht anzuschließen.
Wird der Kühler mit der Option Filter ohne Feuchtefühler be-
stellt, kann am Filterkopf ein Bypass angeschlossen werden.
Auf dem Filterkopf ist ein G1/4 Innengewinde vorgesehen,
welches ab Werk mit einem Stopfen verschlossen ist. Um die-
ses zu nutzen, drehen Sie den Stopfen heraus und schrauben
eine geeignete Verschraubung hinein. Achten Sie auf Dicht-
heit.
HINWEIS
Durch den Einbau von Filtern wird der maximal zulässige Be-
triebsdruck im System eingeschränkt!
Betriebsdruck ≤ 2 bar
4.2.2 Anschluss Durchflussadapter (optional)
Wird der Kühler mit der Option Feuchtefühler ohne Filter be-
stellt, ist dieser werksseitig in einem Durchflussadapter mon-
tiert.
Die Verbindung zwischen Ausgang Wärmetauscher und Ein-
gang Durchflussadapter ist bereits verschlaucht. Der An-
schluss G1/4 oder NPT 1/4“ (Durchflussadapter mit NPT ge-
kennzeichnet) für den Gasausgang ist mittels geeigneter Ver-
schraubung sorgfältig und fachgerecht anzuschließen.
4.2.3 Anschluss Feuchtefühler (optional)
Wird der Kühler mit Option Feuchtefühler bestellt, ist dieser
bereits werksseitig in einem Durchflussadapter oder bei der
Option Filter im Filterkopf montiert und angeschlossen.
4.2.4 Anschluss Gasleitungen Messgaspumpe (optional)
Wird der Kühler mit einer angebauten Messgaspumpe be-
stellt, so ist diese bereits installiert, verschlaucht und verdrah-
tet. Mitbestellte Anbauteile sind eingebaut und an die Mess-
gaspumpe angeschlossen.
Die Messgaspumpe kann sowohl unterhalb des Kühlers wie
auch seitlich befestigt werden.
Vermeiden Sie Mischinstallationen, d.h. Rohrleitungen aus
Metall an Kunststoffkörpern. Sollte dies für vereinzelte An-
wendungen unvermeidlich sein, schrauben Sie die Metallver-
schraubungen vorsichtig und keinesfalls unter Gewaltanwen-
dung in den Pumpenkörper ein.
Verlegen Sie die Rohrleitungen so, dass die Leitung am Ein-
und Ausgang über eine genügende Strecke elastisch bleibt.
Die Pumpen sind am Befestigungsring mit IN für Inlet (Ein-
gang) und OUT für Outlet (Ausgang) gekennzeichnet. Achten
Sie darauf, dass die Anschlüsse an den Gasleitungen dicht
sind.
4.2.5 Anschluss peristaltische Pumpe (optional)
Wird der Kühler mit einer angebauten peristaltischen Pumpe
bestellt, so ist diese bereits installiert und verdrahtet. Mitbe-
stellte Wärmetauscher sind eingebaut und an die peristalti-
sche Pumpe angeschlossen.
Der Anschluss ø6 für den Kondensatausgang der Pumpe ist
mittels geeignetem Schlauch und Schlauchschelle sorgfältig
und fachgerecht anzuschließen.
Versionen mit Verschraubungen DN 4/6 oder 1/6“-1/4“ wer-
den mit Klemmring und Überwurfmutter geliefert und sind
sorgfältig mit passendem Schlauch zu verbinden.
HINWEIS
Durch den Einbau von peristaltischen Pumpen CPsingle / CP-
double wird der maximal zulässige Betriebsdruck im System
eingeschränkt!
Betriebsdruck ≤ 1 bar
3Bühler Technologies GmbHBX440016 ◦ 09/2021

TC-MIDI (+)
4.2.6 Anschluss Wärmetauscher
Der Anschluss zwei einzelner Wärmetauscher ist im linken
Bild schematisch dargestellt.
Zur Minimierung des Gas-Auswascheffektes im Kühler müs-
sen die beiden (baugleichen) Wärmetauscher in Reihe hinter-
einander betrieben werden (rechtes Bild). Hierbei sollte wie
folgt vorgegangen werden:
1. Gaseingangsleitung an rot markiertem Gaseintritt des
Wärmetauschers2 (Vorkühlung).
2. Verbindungsleitung zwischen Gasausaustritt des Wärme-
tauschers2 und dem rot markierten Gaseintritt von Wär-
metauscher1 (Nachkühlung).
3. Montage der finalen Gasausgangsleitung am Gasaustritt
des Wärmetauscher1.
Gas AUS Gas EIN Gas AUS Gas EIN
Kondensat AUS Kondensat AUS
Wärmetauscher 1 Wärmetauscher 2
Gaskühler
(zwei einzelne Wärmetauscher)
Gas AUS
Gas EIN
Gas AUS
Gas EIN
Kondensat AUS Kondensat AUS
Wärmetauscher 1 Wärmetauscher 2
Gaskühler +
(zwei Wärmetauscher in Reihe)
Die Gaseingänge sind rot markiert.
Bei Wärmetauschern aus Glas ist bei dem Anschluss der Gas-
leitungen auf die richtige Lage der Dichtung zu achten (siehe
Abbildung). Die Dichtung besteht aus einem Silikonring mit
einer Stulpe aus PTFE. Die PTFE Seite muss zum Glasgewinde
zeigen.
Glas PTFE
4.3 Elektrische Anschlüsse
Der Betreiber muss für das Gerät eine externe Trenneinrich-
tung installieren, die diesem Gerät erkennbar zugeordnet ist.
Diese Trenneinrichtung
• muss sich in der Nähe des Gerätes befinden,
• muss vom Benutzer leicht erreichbar sein,
• muss IEC 60947-1 und IEC 60947-3 entsprechen,
• muss alle stromführenden Leiter des Versorgungsan-
schlusses und des Statusausgangs trennen und
• darf nicht in die Netzzuleitung eingebaut sein.
WARNUNG
Gefährliche Spannung
Der Anschluss darf nur von geschultem Fachpersonal vorge-
nommen werden.
VORSICHT
Falsche Netzspannung
Falsche Netzspannung kann das Gerät zerstören.
Bei Anschluss auf die richtige Netzspannung gemäß Typen-
schild achten.
WARNUNG
Hohe Spannung
Beschädigung des Gerätes bei Durchführung der Isolations-
prüfung
Führen Sie keine Prüfung der Spannungsfestigkeit mit Hoch-
spannung am Gesamtgerät durch!
Spannungsfestigkeitsprüfung
Das Gerät ist mit umfangreichen EMV-Schutzmaßnahmen
ausgerüstet. Die notwendigen Prüfungen wurden werkseitig
durchgeführt (Prüfspannung je nach Zulassung 2,1kV bzw.
2,55kVDC).
Sofern Sie die Spannungsfestigkeit selbst nochmals prüfen
wollen, können sie diese am Gesamtgerät durchführen. Prü-
fen sie das Gerät nur mit den vorgegebenen Werten und mit
Gleichspannung. Bei einer Prüfung der Spannungsfestigkeit
mit Wechselspannung werden elektronische Bauteile beschä-
digt. Die empfohlene Spannung beträgt hierbei 2,1kV DC, 2s.
Ziehen sie vor der Prüfung alle Versorgungsleitungen vom Ge-
rät ab. Die Spannung kann direkt über den Netzanschluss er-
folgen.
Anschluss über Stecker
Das Gerät ist mit je einem Stecker nach EN 175301-803 für die
Spannungsversorgung und den Signalausgang ausgerüstet.
Diese sind bei korrektem Anschluss der Leitung verwechs-
lungssicher angebracht. Bitte achten Sie deshalb darauf, dass
die Stecker nach dem Anschluss der Leitungen wieder ent-
sprechend zusammengebaut werden. Nachfolgend sind die
Anschlussbelegungen angegeben, wobei die Nummern denen
auf den Steckern entsprechen.
Die Zuleitungsquerschnitte sind der Bemessungsstromstärke
anzupassen. Verwenden Sie maximal einen Leitungsquer-
schnitt von 1,5 mm2 (AWG16) und einen Kabeldurchmesser
von 8-10mm (0,31–0,39 inch).
Für den Anschluss des Analogausganges oder der digitalen
Schnittstelle sind geschirmte Signalleitungen vorzusehen.
4 Bühler Technologies GmbH BX440016 ◦ 09/2021

TC-MIDI (+)
Steckernummerierung Netzanschluss S1
Alarmkontakt S2 Analogausgang S3
1 - nicht belegt
2 - nicht belegt
3 - GND
4 - 4-20 mA out
5 - Schirmung
Digitalausgang S4
1 - nicht belegt
2 - RS485 A
3 - GND/Common
4 - RS485 B
5 - Schirmung
Die Klemmbereiche von S1 und S2 haben einen Durchmesser
von 8-10mm (0,31–0,39 inch).
4.4 Signalausgänge
Das Gerät verfügt über verschiedene Statussignale. Die maxi-
male Schaltleistung der Alarmausgänge beträgt jeweils
250VAC/150VDC, 2A, 50 VA.
Ein Alarm wird über den Alarmkontakt/Statusausgang (S2)
dann ausgegeben, wenn die Temperatur des Kühlers außer-
halb der festgelegten Grenzwerte liegt. Dabei wird nicht si-
gnalisiert, ob der Alarm wegen Übertemperatur oder Unter-
temperatur ausgelöst wurde.
Die Frontfolie enthält drei LEDs:
Farbe Beschriftung Funktion
Rot S2 Temperatur über-/unterschritten,
Gerätefehler
Gelb S1 ---
Grün OP Normalbetrieb
Die LEDs OP und S2 signalisieren den Gerätezustand analog
zum Alarmkontakt S2.
Ist die Option „Temperatursignal“ integriert, steht das Signal
für die Isttemperatur am Analogausgang des Kühlers zur Ver-
fügung.
Ist der Feuchtefühler (Option) installiert, wird zusätzlich ein
Alarm über den Alarmkontakt/Statusausgang (S2) ausgelöst,
wenn im aufbereiteten Messgas noch Feuchtigkeit enthalten
ist oder ein Kabelbruch erkannt wird. Dabei wird nicht unter-
schieden, ob der Alarm / Kabelbruch durch den Feuchtefühler
1 oder 2 ausgelöst wurde. Diese Information erscheint in der
Anzeige.
Das Temperatursignal kann über den Einbaustecker (S3) mit
dem Anschluss M12x1 abgenommen werden. Dieser Stecker
befindet sich neben den Anschlüssen für die Feuchtefühler
auf der Oberseite des Kühlers.
Beschreibung der Signalausgänge
Funktion /
Kontaktart
Beschreibung
Zu
S2)
interner
Wechsler-
kontakt:
max.
250VAC /
150VDC,
2A, 50VA
über zwei
Schaltausgän-
ge können fol-
gende Geräte-
zustände si-
gnalisiert
werden:
Kontakt zwischen 3 und 2 ge-
schlossen (Alarm)
• Keine Netzspannung
und/oder Temperatur
Istwert außerhalb der
gesetzten Alarmschwel-
len
Kontakt zwischen 3 und 1 ge-
schlossen (ok)
• Netzspannung angelegt
+ Temperatur Istwert in-
nerhalb der gesetzten
Alarmschwellen
Mit Option Feuchtefühler
Kontakt zwischen 3 und 2 ge-
schlossen (Alarm)
• Feuchtefühler registriert
Restfeuchte im Messgas
oder Kabelbruch: Fehler-
meldung
Kontakt zwischen 1 und 3 ge-
schlossen (ok)
• keine Restfeuchte im
Messgas/kein Kabel-
bruch
Mit Option Temperatursi-
gnal
Zu
S3)
4-20mA
Analogaus-
gang
(RLast<500Ω)
Signalisie-
rung der Ist-
temperatur
TKühler = -20°C ≙ (-4°F) ->
4mA/ 2 V
TKühler = 5°C ≙ (41°F) -> 9mA/
4,5 V
TKühler = 60°C ≙ (140°F) ->
20mA/ 10 V
Zu
S4)
Digitalaus-
gang
Modbus RTU
(RS-485)
Defaultwerte Schnittstelle
Baudrate – Parität – Stopp-
bit:
19200 – Even – 1
Default-ID: 10
Die Busleitungen sind intern
nicht terminiert.
5 Betrieb und Bedienung
HINWEIS
Das Gerät darf nicht außerhalb seiner Spezifikation betrieben
werden!
Nach dem Einschalten des Kühlers sehen Sie die Anzeige der
Blocktemperatur. Die Anzeige blinkt, bis die Blocktemperatur
den eingestellten Sollwert (± einstellbaren Alarmbereich) er-
reicht hat. Der Statuskontakt ist in der Stellung Alarm.
Wird der Soll-Temperaturbereich erreicht, wird die Tempera-
tur dauerhaft angezeigt und der Statuskontakt schaltet um.
5Bühler Technologies GmbHBX440016 ◦ 09/2021

TC-MIDI (+)
Sofern im laufenden Betrieb die Anzeige blinken sollte oder ei-
ne Fehlermeldung erscheint, betrachten Sie bitte Gliederungs-
punkt „Fehlersuche und Beseitigung“.
Die Leistungs- und Grenzdaten sind dem Datenblatt zu ent-
nehmen.
5.1 Beschreibung der Funktionen
Die Steuerung des Kühlers erfolgt durch einen Mikroprozes-
sor. Durch die Werksvoreinstellung sind die unterschiedlichen
Charakteristika der eingebauten Wärmetauscher bereits von
der Steuerung berücksichtigt.
Das programmierbare Display stellt die Blocktemperatur ent-
sprechend der gewählten Anzeigeeinheit (°C/°F) dar (werk-
seitig°C). Es können mittels der 5 Tasten menügeführt appli-
kations-individuelle Einstellungen einfach getätigt werden.
Dies betrifft zum einen den Soll-Ausgangstaupunkt, der von 2
bis 20°C (36 to 68°F) eingestellt werden kann (werksseitig
5°C/41°F).
Zum anderen können die Warnschwellen für die Unter- bzw.
Übertemperatur eingestellt werden. Diese werden relativ zum
eingestellten Ausgangstaupunkt τa gesetzt.
Für die Untertemperatur steht hier ein Bereich von τa -1 bis zu
- 3K (mindestens jedoch 1°C/ 34°F Kühlblock-Temperatur) zur
Verfügung, für die Übertemperatur ein Bereich von τa +1 bis zu
+7K. Die Werkseinstellungen für beide Werte sind 3K.
Ein Unter- bzw. Überschreiten des eingestellten Warnberei-
ches (z. B. nach dem Einschalten) wird sowohl durch Blinken
der Anzeige als auch durch das Statusrelais signalisiert.
Der Statusausgang kann z.B. zum Steuern der Messgaspumpe
verwendet werden, um ein Zuschalten des Gasstroms erst bei
Erreichen des zulässigen Kühlbereiches zu ermöglichen bzw.
die Pumpe im Falle eines Feuchtefühleralarms abzuschalten.
Das abgeschiedene Kondensat kann über angeschlossene pe-
ristaltische Pumpen oder angebaute automatische Kondensa-
tableiter abgeführt werden.
Weiterhin können Feinfilter verwendet werden, in die wieder-
um optional Feuchtefühler integrierbar sind.
Die Verschmutzung des Filterelementes ist durch die Glasglo-
cke einfach zu sehen.
Der Feuchtefühler ist einfach herauszunehmen. Dies kann
notwendig sein, wenn durch einen Fehlerfall ein Kondensat-
durchbruch in den Kühler gelangen sollte, den die peristalti-
sche Pumpe oder der automatische Kondensatableiter nicht
mehr abtransportieren kann.
An den Gaskühler kann eine Gaspumpe P1 angebaut werden,
wahlweise auch mit Bypassventil zur Regulierung des Durch-
flusses. Hierdurch ist die Erweiterung um die Förderpumpe
bei einem einsträngigen System möglich, also bei einer Aus-
rüstung mit einem Einfachen Wärmetauscher oder wenn bei
einer entsprechenden Applikation die beiden Gaswege des
Doppelwärmetauschers in Reihe geschaltet werden, wie zum
Beispiel Kühlung 1 – Pumpe – Kühlung 2.
5.2 Bedienung der Menüfunktionen
Kurzerklärung des Bedienungsprinzips:
Die Bedienung erfolgt über 5 Tasten. Sie haben folgende Funk-
tionen:
Taste Bereich Funktionen
bzw.
OK
Anzeige • Wechsel von der Messwertanzeige ins
Hauptmenü
Menü • Auswahl des angezeigten Menüpunktes
Eingabe • Übernahme eines editierten Wertes
oder einer Auswahl
Anzeige • temporärer Wechsel zur alternativen
Messwertanzeige (wenn Option vorhan-
den)
Menü • Rückwärts blättern
Eingabe • Wert erhöhen oder in der Auswahl blät-
tern
• hier gilt:
▪ Taste 1 x drücken = Parameter /
Wert um einen Schritt verändern;
▪ Taste gedrückt halten = Schnelllauf
(nur bei Zahlenwerten)
▪ Anzeige blinkt: geänderter Parame-
ter / Wert
▪ Anzeige blinkt nicht: ursprünglicher
Parameter / Wert
Anzeige • temporärer Wechsel zur alternativen
Messwertanzeige (wenn Option vorhan-
den)
Menü • Vorwärts blättern
Eingabe • Wert vermindern oder in der Auswahl
blättern
ESC
Menü • Zurück zur übergeordneten Ebene
Eingabe • Zurück zum Menü
Änderungen werden nicht gespeichert!
F
bzw.
Func
• Festlegung eines favorisierten Menüs.
(Hinweis: Das favorisierte Menü wird
auch bei aktiver Menü-Sperre aufgeru-
fen!)
5.2.1 Menü-Sperre
Um eine unbeabsichtigte Änderung der Einstellungen des Ge-
rätes zu verhindern, können einige Menüs gesperrt werden.
Dazu ist die Festlegung eines Codes erforderlich. Wie Sie die
Menü-Sperre einrichten bzw. aufheben, ist im Menü „Globale
Einstellungen“ (toP) unter dem Menü-Punkt toP>Loc be-
schrieben.
Im Auslieferungszustand ist die Menü-Sperre nicht aktiv und
alle Menü-Punkte sind zugänglich.
Bei aktiver Menü-Sperre sind ohne Eingabe des richtigen Co-
des nur die folgenden Menüpunkte sichtbar:
6 Bühler Technologies GmbH BX440016 ◦ 09/2021

TC-MIDI (+)
Menü-Punkt Erläuterung
toP > unit Auswahl der angezeigten Temperatureinheit
(°C oder °F).
F bzw. Func. Aufruf des favorisierten Menüs
HINWEIS!Dieses Menü kann aus dem nor-
malerweise gesperrten Bereich stammen.
5.2.2 Übersicht Menüführung
Wenn Sie während des Normalbetriebs die Taste OK drücken,
erscheint im Display bei aktiver Menü-Sperre die Eingabeauf-
forderung code. Geben Sie mit den Tasten ▲ und ▼ den rich-
tigen Code ein und drücken Sie OK.
Bei falscher oder keiner Eingabe wird die Menü-Sperre nicht
aufgehoben und Sie erreichen nicht alle Menüpunkte.
Falls Sie das Passwort vergessen haben, gelangen Sie jederzeit
mit dem Mastercode 287 ins Menü und die Menü-Sperre wird
deaktiviert.
Die Übersicht über die Menüstruktur finden Sie in der folgen-
den Abbildung.
Gestrichelt umrahmte Punkte werden nur angezeigt, wenn
die entsprechenden Einstellungen vorgenommen wurden
bzw. Status-Meldungen vorliegen.
Die Standard-Werkseinstellungen und Einstellbereiche sind in
der Übersicht sowie in dem jeweiligen Menüpunkt angege-
ben. Die Standard-Werkseinstellungen gelten, solange nichts
anderes vereinbart wurde.
Eingaben und Menüauswahl können Sie, ohne zu speichern,
mit der Taste ESC abbrechen.
Menü:
Top Settings top
Globale Einstellungen
3
21
1.
2.
3.
Menü-Bezeichnung
Anzeige
Kurze Erklärung
Parameter:
Eingabe 5'C
-20 . . . 60 'C
6
54
4.
5.
6.
Eingabe eines Wertes
Werkseinstellung
Parameterbereich
Auswahl oP
op haLf Lo hi
9
87
7.
8.
9.
Auswahl aus der Werteliste
Werkseinstellung
Parameterbereich /Auswahl
Optionale
Menüfüh-
rung:
10
10. gestrichelter Kasten = Opti-
on
7Bühler Technologies GmbHBX440016 ◦ 09/2021

TC-MIDI (+)
Auswahl
noP
nop- haLf - Lo - hi
OK
OK
OK
OK
OK
OK
OK
OK
Auswahl unit
'C - 'F
TC MIDI tc.Md
Gerätebezeichnung
Anzeige ch1
Temperatur CH1
Top Settings top
Globale Einstellungen
Analog Out1 An1
Einstellmenü Analog 1
Einstellmenü unit
Einheit Temperatur
Temperatur tEmP
Soll-Temp. Kühlblock
Exit E
Untermenü verlassen
Auswahlmenü
cout
Funktionstest
Exit E
Untermenü verlassen
OK
Anzeige Hauptmenü Untermenü 1 Untermenü 2 Parameter
Eingabe 5'C
2 . . . 20 °'C
OK
OK Eingabe 3'C
1 . . . 7 °'C
Einstellmenü A hi
Alarmhysterese
Einstellmenü A Lo
Alarmhysterese
Auswahlmenü dt
DeltaT Temp. Modus
OK
OK
Auswahlmenü h2o
Auswahlmenü sen
Feuchtefühler 1 Sensibilität
Auswahlmenü h2o.2
Auswahlmenü sen.2
OK Eingabe -3'C
-1 . . . -3 'C
OK Eingabe -15'C
-30'C .. . . 0'C K
Feuchtefühler 1 kalibrieren
Feuchtefühler 2 kalibrieren
Feuchtefühler 2 Sensibilität
Auswahlmenü Modu
DeltaT Modus deaktivieren
OK Auswahl Abso
Abso - dt
Auswahlmenü
out
Ausgangssignal
Auswahl
i
i- u
Feuchtefühler 1 rst
OK
Eingabe non
non - hi - Lo
OK
rst
OK
Eingabe non
non - hi - Lo
OK
Bestätigen
Feuchtefühler 2
Bestätigen
Anzeige ch2
Umgebungstemperatur CH2
Error Err
Statusmeldung
Login Loc
Menü-Sperre aktivieren
Eingabe 0
0. . . . 9999
OK
Reset rSt
Werkseinstellungen
Exit E
Untermenü verlassen
Bestätigung rst
yes - no
OK
Exit E
Untermenü verlassen
Auswahlmenü PuMP
Pumpen anhalten
Auswahlmenü noP
NoP - off
OK
Auswahlmenü hLtc
Feuchte autom. Rückstellung
Eingabe no
yes - no
OK
Auswahlmenü bLtc
Kabelbruch autom. Rückstellung
Eingabe YES
yes - no
OK
Neustart rESt
Geräteneustart
Bestätigung no
yes - no
OK
Auswahlmenü h.chn
Auswahl Wärmetauschermaterial
Auswahlmenü tS
tS
OK
t6 tU
(Stahl) (Glas) (PVDF)
oper
Betriebsstundenzähler
Anzeige
Auswahlmenü baud
Baudrate Modbus RTU
Eingabe 1920
480 - . - 1152
OK
Auswahlmenü pari
Parität Modbus RTU
Eingabe EUen
none - odd - eUen
OK
Auswahlmenü addr
Geräte-ID Modbus RTU
Eingabe 10
1 . 247
OK
Abb.1: Menü Übersicht TC MIDI
8 Bühler Technologies GmbH BX440016 ◦ 09/2021

TC-MIDI (+)
5.3 Verwendung der digitalen Schnittstelle
Bei der digitalen Schnittstelle des Gerätes handelt es sich um
ein Modbus RTU Protokoll, welches physikalisch über RS485 (2-
Draht) kommuniziert. Der Kühler nimmt innerhalb der Kom-
munikation die Rolle des Slaves ein.
Die Modbus-Schnittstelle ermöglicht den direkten Zugriff auf
Prozess- und Diagnosedaten und die Parametrierung im lau-
fenden Betrieb.
5.4 Modbus Konfiguration
Die unten genannten Einstellungen entsprechen der Standar-
deinstellung, bei aktiver Schnittstelle können die Parameter
angepasst werden.
1 Startbit
8 Datenbits
1 Paritätsbit (konfigurierbar)
1 Stoppbit (*)
Baudrate: 19200 bps (konfigurierbar)
Geräte-ID: 10 (konfigurierbar)
(*) Die Länge eines Modbus-Frames umfasst immer 11bit, wird
die Schnittstelle mit 0 Datenbits konfiguriert, ändert sich die
Anzahl der Stoppbits automatisch auf 2.
5.5 Modbuskommunikation
Eine Kommunikation über Modbus RTU wird immer durch
den Master initiiert (Request). Auf die Request antwortet der
Slave (i.d.R.) mit einer Response. Ein Modbus RTU Frame für ei-
ne Request/Response hat immer folgenden Aufbau:
Adressfeld (A) Functioncode (FC) Daten (Data) CRC
1 Byte 1 Byte 1 … 252 Bytes 2 Bytes
Registeradressen und Daten werden im Big Endian Format
übertragen.
Jedes Register steht für einen 16bit-Wert, wobei die Informa-
tion in verschiedenen Datentypen repräsentiert wird. Daten-
typ und erforderlicher Functioncode werden in den folgenden
Tabellen den jeweiligen Registern zugeordnet.
Für das Lesen/Schreiben von Datentypen, deren Größe die ei-
nes einzelnen Registers übersteigt, sind mehrere Register an-
zusprechen.
Unterstützte Functioncodes:
Functioncode (FC) FC-Werte
Read Holding Registers 3
Write Multiple Registers 16
Datentypen:
Bezeichnung Anzahl Bytes Anzahl Register
Float 4 2
Int16 2 1
Uint16 2 1
Int32 4 2
Uint32 4 2
6 Transport und Lagerung
Die Produkte sollten nur in der Originalverpackung oder ei-
nem geeigneten Ersatz transportiert werden.
Bei Nichtbenutzung sind die Betriebsmittel gegen Feuchtig-
keit und Wärme zu schützen. Sie müssen in einem überdach-
ten, trockenen und staubfreien Raum bei einer Temperatur
von -20°C bis 60°C (-4 °F bis 140 °F) aufbewahrt werden.
7 Wartung
Bei Durchführung von Wartungsarbeiten jeglicher Art müs-
sen die relevanten Sicherheits- und Betriebsbestimmungen
beachtet werden. Hinweise zur Wartung finden Sie in der Ori-
ginalbetriebsanleitung auf der beigefügten CD oder im Inter-
net unter www.buehler-technologies.com.
8 Service und Reparatur
Eine ausführliche Beschreibung des Gerätes mit Hinweisen
zur Fehlersuche und Reparatur finden Sie in der Originalbe-
triebsanleitung auf der beigefügten CD oder im Internet un-
ter www.buehler-technologies.com.
8.1 Fehlermeldungen im Display
Tritt ein Fehler auf, wird im Display „Err“ angezeigt. Durch
drücken der Taste „ “ wird/werden die Fehlernummer(n) an-
gezeigt.
Fehlermeldungen werden nach Auftreten des Fehlers so lange
angezeigt, bis das Gerät neu gestartet wird, oder der Fehler
durch drücken der „Func“ –Taste quittiert wird. Die Quittie-
rung funktioniert nur, wenn der die Fehlerbedingung nicht
mehr gegeben ist.
Ursachen / Abhilfe: In der folgenden Liste sind die wahr-
scheinlichsten Ursachen und Maßnahmen für den jeweiligen
Fehler angegeben. Sollten die angeführten Maßnahmen nicht
weiterhelfen, wenden Sie sich bitt an unseren Service.
Problem /
Störung
Mögliche Ursache Abhilfe
Keine
Anzeige
• Keine Netz-
spannung
• Verbindungs-
leitung gelöst
• Display defekt
• Zuleitung prüfen
• Sicherung prüfen
• Anschlüsse prü-
fen
(dauer-
haft)
D1.02 (Es wird die Softwa-
reversion des Dis-
plays angezeigt).
• Keine Kommu-
nikation zum
Regler
• Anschlüsse prü-
fen
Error • Es liegt ein Feh-
ler vor
• Auslesen der Feh-
lernummer wie
oben beschrieben
Error 01 • Störung Regler • Fehler quittieren
(vorübergehende
Störung)
• Spannungsver-
sorgung für ca. 5 s
trennen
• Service kontaktie-
ren
9Bühler Technologies GmbHBX440016 ◦ 09/2021

TC-MIDI (+)
Error 03 • Mikrocontrol-
ler-Störung /
MCP2
• Service kontaktie-
ren
Error 04 • EEPROM Fehler • Service kontaktie-
ren
Error 22 • Kabelbruch
Feuchtefühler 1
• Feuchtefühler-
Leitung kontrol-
lieren
• Feuchtefühler
kontrollieren
Error 32 • Kabelbruch
Feuchtefühler 2
• Feuchtefühler-
Leitung kontrol-
lieren
• Feuchtefühler
kontrollieren
Error 40 • Allgemeiner
Fehler Tempe-
raturfühler 1
(Blocktempera-
tur)
• Sensor möglicher-
weise defekt
Error 41 • Untertempera-
tur / Kurz-
schluss Tempe-
raturfühler 1
• Anschluss Tempe-
raturfühler prü-
fen
Error 42 • Übertempera-
tur / Kurz-
schluss Tempe-
raturfühler 1
• Anschluss Tempe-
raturfühler prü-
fen
Error 43 • Messwert-
schwankung
Temperatur-
fühler 1
• Anschluss Tempe-
raturfühler prü-
fen
Error 50 • Allgemeiner
Fehler Tempe-
raturfühler 2
(Referenztem-
peratur Delta-
T)
• Sensor möglicher-
weise defekt
Error 51 • Untertempera-
tur / Kurz-
schluss Tempe-
raturfühler 2
• Anschluss Tempe-
raturfühler prü-
fen
Error 52 • Übertempera-
tur / Kurz-
schluss Tempe-
raturfühler 2
• Anschluss Tempe-
raturfühler prü-
fen
Error 53 • Messwert-
schwankung
Temperatur-
fühler 2
• Anschluss Tempe-
raturfühler prü-
fen
Statustext Mögliche Ursache Abhilfe
H2o.1 • Feuchtealarm
Feuchtefühler 1
• Trocknen
• Kondensatsam-
melgefäß prüfen
H2o.2 • Feuchtealarm
Feuchtefühler 2
• Trocknen
• Kondensatsam-
melgefäß prüfen
init • Initialisie-
rungsphase
• Warten
PuMP • Pumpen deak-
tiviert
• Pumpen im Menü
wieder aktivieren
dt Nur bei aktiver Del-
ta T-Regelung: Die
Blocktemperatur
befindet sich nicht
im definierten
Temperaturbereich.
• Kühler befindet
sich noch in der
„Einlaufphase“
• Schwankende
Umgebung-
stemperatur
• Kühlleistung
nicht ausrei-
chend
• Warten, ob die
Zieltemperatur
noch erreicht
wird
• Umgebungstem-
peratur / einge-
brachte Leistung
kontrollieren
• Prozessbedingt:
Anpassen der
Alarmgrenzen
(Blinken)
• Über-/Unter-
temperatur
• siehe Kapitel
„Fehlersuche und
Beseitigung“
10 Bühler Technologies GmbH BX440016 ◦ 09/2021

TC-MIDI (+)
1 Introduction
This quick guide will assist you in starting up the unit. Follow
the safety notices or injury to health or property damage may
occur. Carefully read the original operating instructions in-
cluding information on maintenance and troubleshooting
prior to startup. These are located on the included CD and on-
line at
www.buehler-technologies.com
Please direct any questions to:
Bühler Technologies GmbH
Harkortstraße 29
40880 Ratingen
Germany
Tel.: +49 (0) 21 02 / 49 89-0
Fax: +49 (0) 21 02 / 49 89-20
These operating instructions are a part of the equipment. The
manufacturer reserves the right to change performance-, spe-
cification- or technical data without prior notice. Please keep
these instructions for future reference.
1.1 Intended use
This unit is intended for industrial use in gas analysis systems.
It's an essential component for conditioning the sample gas to
protect the analysis instrument from residual moisture in the
sample gas.
Please note the specifications in the data sheet on the specific
intended use, existing material combinations, as well as pres-
sure and temperature limits.
1.2 Scope of delivery
• Cooler
• Product documentation
• Connection-/mounting accessories (optional)
2 Safety instructions
The equipment must be installed by a professional familiar
with the safety requirements and risks.
Be sure to observe the safety regulations and generally applic-
able rules of technology relevant for the installation site. Pre-
vent malfunctions and avoid personal injuries and property
damage.
The operator of the system must ensure:
• Safety notices and operating instructions are available
and observed,
• The respective national accident prevention regulations
are observed,
• The permissible data and operational conditions are
maintained,
• Safety guards are used and mandatory maintenance is
performed,
• Legal regulations are observed during disposal,
• compliance with national installation regulations.
DANGER
Electrical voltage
Electrocution hazard.
a) Disconnect the device from power supply.
b) Make sure that the equipment cannot be reconnected to
mains unintentionally.
c) The device must be opened by trained staff only.
d) Regard correct mains voltage.
DANGER
Toxic, corrosive gases
The measuring gas led through the equipment can be hazard-
ous when breathing or touching it.
a) Check tightness of the measuring system before putting
it into operation.
b) Take care that harmful gases are exhausted to a save
place.
c) Before maintenance turn off the gas supply and make
sure that it cannot be turned on unintentionally.
d) Protect yourself during maintenance against toxic / cor-
rosive gases. Use suitable protective equipment.
DANGER
Potentially explosive atmosphere
Explosion hazard if used in hazardous areas.
The device is not suitable for operation in hazardous areas
with potentially explosive atmospheres.
Do not expose the device to combustible or explosive gas mix-
tures.
3 Transport and storage
Only transport the product inside the original packaging or a
suitable alternative.
The equipment must be protected from moisture and heat
when not in use. It must be stored in a covered, dry and dust-
free room at a temperature of -20 °C to 60 °C (-4 °F to 140 °F).
4 Installation and connection
4.1 Installation site requirements
The unit is only intended for wall-mounted use in enclosed
areas. Adequate protection from the weather must be
provided when used outdoors.
Install the unit leaving enough room below the cooler to dis-
charge the condensate. Leave room above for the gas supply.
Be sure to maintain the approved ambient temperature. Do
not obstruct the convection of the cooler. The vents must have
enough room to the next obstacle. The distance must espe-
cially be a minimum of 10 cm on the air outlet side.
Ensure adequate ventilation when installing in enclosed
housings, e.g. analyser cabinets. If the convection is inad-
equate, we recommend aerating the cabinet or installing a
fan to lower the inside temperature.
11Bühler Technologies GmbHBX440016 ◦ 09/2021

TC-MIDI (+)
4.2 Installation
Run the gas supply to the cooler with a downward slope. The
gas inputs are marked in red and additionally labelled "IN".
If a large amount of condensate accumulates, we recommend
using a condensate trap with automatic condensate drain.
Our condensate drains, 11LDV38, AK20, AK5.5 OR AK5.2, are
suitable.
Glass vessels and automatic condensate drains are available
for draining condensate for external mounting below the
unit. When using automatic condensate drains, the sample
gas pump must be installed upstream of the cooler (pressure
operation) to ensure proper function of the condensate drain.
If the sample gas pump is located at the cooler outlet (suction
operation), we recommend using glass condensate traps or
peristaltic pumps.
Connecting the condensate drains
Depending on the material, build a connecting line with fit-
tings and tubing or hose between the heat exchanger and
condensate drain. For stainless steel the condensate drain can
be suspended directly to the connecting tube, for hoses the
condensate drain must be secured separately using a clamp.
The condensate drain can be mounted directly to the heat ex-
changer.
Condensate lines must always be installed with a slope and a
minimum inside diameter of DN 8/10 (5/16”).
The DTV heat exchanger cannot be operated in conjunction
with an automatic condensate drain.
4.2.1 Connecting the filter gas connections (optional)
The connection between the heat exchanger outlet and the fil-
ter inlet already has tubing. The connection G1/4 or NPT
1/4" (filter head marked NPT) for the gas outlet must be care-
fully and properly connected using a suitable screw connec-
tion.
When ordering the cooler with the option filter without Mois-
ture detector, a bypass may be connected to the filter head.
The filter head is intended for a G1/4 internal screw thread
which is plugged at the factory. To use it, unscrew the plug
and screw in a suitable screw connection. Pay attention to
leaks.
NOTICE
Installing filters limits the maximum approved operating
pressure in the system!
Operating pressure ≤ 2 bar
4.2.2 Flow adapter connection (optional)
When ordering the cooler with the option moisture detector
without filter, it will be factory installed inside a flow adapter.
The connection between the heat exchanger outlet and the
flow adapter inlet already has tubing. The connection G 1/4 or
NPT 1/4” (flow adapter marked NPT) for the gas outlet must be
carefully and properly connected using a suitable screw con-
nection.
4.2.3 Connecting the moisture detector (option)
When ordering the cooler with moisture detector option, it
will be factory installed inside a flow adapter, or for the filter
option installed and connected in the filter head.
4.2.4 Sample gas pump connection gas lines (optional)
On coolers ordered with attached sample gas pump these are
already installed and wired. Add-on parts ordered at the same
time are already installed and connected to the sample gas
pump.
The sample gas pump may be installed both below and next
to the cooler.
Avoid mixed-material installation, i.e. metal piping to plastic
bodies. If this cannot be avoided in isolated applications,
screw the metal connections into the pump body with care,
never use force.
Lay the lines so the line at the inlet and outlet remains flexible
for an adequate distance.
The pumps are marked IN for inlet and OUT for outlet at the
mounting ring. Be sure the gas line connections are tight.
4.2.5 Peristaltic pump connector (optional)
Coolers ordered with attached peristaltic pump already have
it installed and wired. Heat exchangers ordered at the same
time are already installed and connected to the peristaltic
pump.
The ø6mm (0.24inch) hose nipple for the pump’s condensate
outlet must be carefully and properly connected with a suit-
able hose and hose clamp.
Versions with screw connections DN4/6 or 1/6”-1/4” are sup-
plied with ferrule and knurled nut and must be carefully
sealed with appropriate hose.
NOTICE
Installing peristaltic pumps CPsingle / CPdouble limits the
maximum permissible operating pressure in the system!
Operating pressure ≤ 1 bar
4.2.6 Connecting the heat exchanger
The picture on the left shows the schematics for connecting
two separate heat exchangers.
To minimise gas wash out in the cooler, the two (identical)
heat exchangers must be operated in series (right picture).
This should be done as follows:
1. Gas inlet line to red gas inlet on heat exchanger 2 (pre-
cooling).
2. Connection between gas outlet on heat exchanger 2 and
the red gas inlet on heat exchanger 1 (after-cooling).
3. Attaching the final gas output line to the gas outlet on
heat exchanger 1.
12 Bühler Technologies GmbH BX440016 ◦ 09/2021

TC-MIDI (+)
gas out gas in gas out gas in
condensate out condensate out
Heat exchanger 1 Heat exchanger 2
Gas cooler
(two single heat exchangers)
gas out
gas in
gas out
gas in
condensate out condensate out
Heat exchanger 1 Heat exchanger 2
Gas cooler +
(two heat exchangers in series)
The gas inputs are marked in red.
On glass heat exchangers the correct position of the seal is im-
portant when connecting the gas lines (see image). The seal
consists of a silicone ring with a PTFE sleeve. The PTFE side
must face the glass thread.
Glass PTFE
4.3 Electrical connections
The operator must install an external separator for the device
which is clearly assigned to this device.
This separator
• must be located near the device,
• must be easy for the operator to reach,
• must comply with IEC 60947-1 and IEC 60947-3,
• must separate all live conductors and the status output,
and
• must not be attached to the power feed.
WARNING
Hazardous electrical voltage
The device must be installed by trained staff only.
CAUTION
Wrong mains voltage
Wrong mains voltage may damage the device.
Regard the correct mains voltage as given on the type plate.
WARNING
High voltage
Damage to the device in case of insulation testing
Do not proceed insulation tests with high voltage to the
device as a whole!
Electric strength test
This device is equipped with extensive EMC protection. The
necessary tests were carried out at the factory (test voltage
2.1kV or 2.55kVDC depending on approval).
If you wish to check the electric strength again yourself, you
can do so on the entire unit. Only test the device with the spe-
cified values using direct current voltage. Testing the electric
strength with alternating current voltage will damage elec-
tronic components. The recommended voltage in this case is
2.1kV DC, 2s. Disconnect all supply lines from the device be-
fore testing. Power can be supplied via the mains connection.
Plug connection
This device has one EN 175301-803 plug each for the power
supply and the signal output. If the lead is connected cor-
rectly, these cannot be confused. Therefore please be sure to
correctly reassemble the plugs after connecting the wires. Be-
low you will find the pin assignments, with the numbers cor-
responding to those on the plugs:
The supply line cross-sections must be suitable for the rated
current. Use a maximum line cross-section of 1.5mm²
(AWG16) and a cable diameter of 8-10mm (0.31-0.39 inch).
Shielded signal lines are required to connect the analog out-
put or the digital interface.
Plug numbering Electric supply S1
Alarm contact S2 Analog output S3
1 - not assigned
2 - not assigned
3 - GND
4 - 4-20 mA out
5 - shield
Digital output S4
1 - not used
2 - RS485 A
3 - GND/Common
4 - RS485 B
5 - Shielding
The clamping areas for S1 and S2 are 8-10mm (0.31–0.39
inches) in diameter.
13Bühler Technologies GmbHBX440016 ◦ 09/2021

TC-MIDI (+)
4.4 Signal outputs
The device provides different status signals. The maximum
switching load of the alarm outputs is limited to
250VAC/150VDC, 2A, 50VA each.
An alarm is triggered by the alarm contact/status output (S2)
if the temperature of the cooler is outside the specified limits.
It does not indicate if the alarm was triggered due to excess
temperature or insufficient temperature.
The front film has three LEDs:
Colour Marking Function
Red S2 High/low temperature, device error
Yellow S1 ---
Green OP Normal operation
The LEDs OP and S2 indicate the device status similar to S2.
If the option “temperature signal” is built in, the unit has a
signal output via the analogue output to indicate the actual
cooler temperature.
When the moisture detector (optional) is installed, an alarm is
activated by the alarm contact/status output (S2) if the mois-
ture is still present in the prepared sample gas. Thereby, no
distinction is made between the alarm/cable break triggered
by moisture detector 1 or 2. This information is displayed by
an error message instead.
The temperature signal can be read via the panel plug (S3) us-
ing the M12x1 connector. This plug is located next to the mois-
ture detector connectors at the top of the cooler.
Description of signal outputs
Function/
contact type
Description
Re-
gar
d-
ing
S2)
internal
changeover
contact:
max.
250VAC/150
VDC, 2A,
50VA
the following
device
statuses can
be indicated
via two
switching
outputs:
Contact between 3 and 2
closed (alarm)
• No mains voltage and/or
actual temperature out-
side the alarm
thresholds
Contact between 3 and 1
closed (OK)
• Mains voltage attached
+ actual temperature
within the alarm
thresholds
With moisture detector op-
tion
Contact between 3 and 2
closed (alarm)
• The moisture detector
registers residual hu-
midity in the sample gas
or cable break: Error
message
Contact between 1 and 3
closed (OK)
• no residual moisture in
measuring gas/no cable
break
With temperature signal op-
tion
Re-
gar
d-
ing
S3)
4-20mA
analogue
output
(RLoad<500Ω
)
Signalling of
actual tem-
perature
Tcooler = -20°C ≙ (-4°F) ->
4mA/ 2 V
Tcooler = 5°C ≙ (41°F) -> 9mA/
4.5 V
Tcooler = 60°C ≙ (140°F) ->
20mA/ 10 V
Re-
gar
d-
ing
S4)
Digital out-
put
Modbus RTU
(RS-485)
Interface default values
Baudrate – parity – stop bit:
19200 – Even – 1
Default ID: 10
The bus lines are not intern-
ally terminated.
5 Operation and control
NOTICE
The device must not be operated beyond its specifications.
After switching on the cooler the block temperature will be
displayed. The display will flash until the block temperature
has reached the preset target value (± adjustable alarm
range). The status contact is in the Alarm position.
Once the target temperature range has been reached, the
temperature will continuously be displayed and the status
contact switches over.
14 Bühler Technologies GmbH BX440016 ◦ 09/2021

TC-MIDI (+)
If the display flashes during operation or an error message ap-
pears, please refer to bullet “Troubleshooting”.
Please refer to the data sheet for performance data and max-
imum ratings.
5.1 Description of functions
The cooler is controlled by a microprocessor. With the factory
preset the control already incorporates the various character-
istics of the built-in heat exchangers.
The programmable display shows the block temperature in
the selected display unit (°C/°F) (factory preset °C). Applica-
tion-specific settings can easily be configured guided by the
menu, using the 5 buttons. For one, this applies to the target
outlet dew point, which can be set from 2 to 20°C (36°F to
68°F) (factory preset 5°C/41°F).
And then the warning thresholds can be adjusted for low and
excess temperature. These are set relative to the outlet dew
point τa setting.
For the low temperature the range is τa -1 to - 3K (at a min-
imum 1°C/ 34°F cooling block temperature), for the excess
temperature the range is τa +1 to +7K. The factory presets for
both values are 3K.
The flashing display and the status relays indicate the condi-
tions are below or above the configured warning range (e.g.
after switching on).
The status output can e.g. be used to control the sample gas
pump to allow for the gas flow to only be switched on once
the permissible cooling range has been reached or shut off the
pump in the event of a moisture detector alarm.
The separated condensate can be drained via connected peri-
staltic pumps or add-on automatic condensate drains.
Fine mesh filters can also be used, which in turn can be in-
stalled in optional moisture detectors.
The glass dome allows the dirt level of the filter element to
easily be determined.
The moisture detector is easy to remove. This may be required
if a condensate enters the cooler due to a malfunction and the
peristaltic pump or the automatic condensate drain is unable
to remove it.
A P1 gas pump can be attached to the gas cooler, optionally
also with bypass valve for regulating the flow. This allows the
sample gas pump to be expanded by a single-leg system, so
when equipped with a single heat exchanger or for the re-
spective application the two gas paths of the dual heat ex-
changers are switched in series, for example Cooling 1 – Pump
– Cooling 2.
5.2 Use of menu functions
Brief description of the operating principle:
The unit is operated using 5 keys. Their functions are:
Button Section Functions
or
OK
Display • Switches from the measurement dis-
play to the main menu
Menu • Selects the menu item displayed
Enter • Applies an edited value or a selection
Display • temporarily switches to the alternat-
ive measurement display (if option
installed)
Menu • Back
Enter • Increase value or browse selection
• Note:
▪ Press button 1 x = changes para-
meter / value by one;
▪ Hold button = fast mode (numer-
ical values only)
▪ Display flashes: modified para-
meter/value
▪ Steady display: original display/
value
Display • temporarily switches to the alternat-
ive measurement display (if option
installed)
Menu • Next
Enter • Reduce value or browse selection
ESC
Menu • Move one level up
Enter • Return to menu
Changes will not be saved!
F
or
Func
• Sets a menu to favourite.
(Note: The favourite menu will also
be activated with the menu locked!)
5.2.1 Lock Menu
Some menus can be locked to prevent inadvertently changing
the settings of the unit. This requires setting a code. For in-
formation on setting up or disabling the menu lock please
refer to "Global Settings" (toP) under menu item toP>Loc.
The menu lock is not enabled at the time of delivery, all menu
items can be accessed.
With the menu locked, only the following menu items will be
visible without entering the correct code:
Menu item Explanation
toP > unit Temperature unit selection (°C or °F).
F or Func. Accessing the Favourites menu
NOTICE!This menu may be one that is nor-
mally locked.
15Bühler Technologies GmbHBX440016 ◦ 09/2021

TC-MIDI (+)
5.2.2 Overview of the menu items
When pressing the OK button in normal mode, the display will
show the prompt code if the menu is locked. Use the ▲ and ▼
buttons to enter the correct code and press OK.
If an incorrect code or no code is entered, the menu will not be
unlocked and you will not be able to access all menu items.
If you forgot the password you can always enter master code
287 to access the menu; the menu will be unlocked.
The following image shows an overview of the menu struc-
ture.
Items with a dashed frame will only appear with the respect-
ive settings or with the respective status messages.
The factory defaults and settings ranges are specified in the
overview as well as under the respective menu item. The fact-
ory defaults apply unless otherwise agreed.
You can cancel entries and menu selections without saving by
pressing the ESC key.
Menu:
Top Settings top
Globale Einstellungen
3
21
1.
2.
3.
Menu designation
Display
Brief description
Parameter:
Eingabe 5'C
-20 . . . 60 'C
6
54
4.
5.
6.
Value input
Factory preset
Parameter range
Auswahl oP
op haLf Lo hi
9
87
7.
8.
9.
Selecting from the list of val-
ues
Factory preset
Parameter range/selection
Optional
menu nav-
igation:
10
10. dashed box = Optional
16 Bühler Technologies GmbH BX440016 ◦ 09/2021

TC-MIDI (+)
Selection
noP
nop- haLf - Lo - hi
OK
OK
OK
OK
OK
OK
OK
OK
Selection unit
°C - °F
TC MIDI tc.Md
Device designation
Display ch1
Temperature CH1
Top Settings top
Global settings
Analogue Out1 An1
Settings menu Analog 1
Settings menu unit
Temperature unit
Temperature tEmP
Target temp. Cooling block
Exit E
Close submenu
Drop-down menu
cout
Functional test
Exit E
Close submenu
OK
Display Main menu Submenu 1 Submenu 2 Parameter
Input 5°C
2 . . . 20 °C
OK
OK Input 3°C
1 . . . 7 °C
Settings menu A hi
Alarm hysteresis
Settings menu A Lo
Alarm hysteresis
Drop-down menu dt
DeltaT Temp. Mode
OK
OK
Drop-down menu h2o
Drop-down menu sen
Moisture detector 1 sensitivity
Drop-down menu h2o.2
Drop-down menu sen.2
OK Input -3°C
-1 . . . -3 °C
OK Input -15°C
-30°C .. . . 0°C K
Calibrate moisture detector 1
Calibrate moisture detector 2
Moisture detector 2 sensitivity
Drop-down menu Modes
Deactivate DeltaT mode
OK Selection Abso
Abso - dt
Drop-down menu
out
Output signal
Selection
i
i- u
Moisture detector 1 rst
OK
Input non
non - hi - Lo
OK
rst
OK
Input non
non - hi - Lo
OK
Confirm
Moisture detector 2
Confirm
Display ch2
Ambient temperature CH2
Error Err
Status message
Login Loc
Enable menu lock
Input 0
0. . . . 9999
OK
Reset rSt
Factory settings
Exit E
Close submenu
Confirm rst
yes - no
OK
Exit E
Close submenu
Drop-down menu PuMP
Stop pumps
Drop-down menu noP
NoP - off
OK
Drop-down menu hLtc
Humidity auto reset
Input no
yes - no
OK
Drop-down menu bLtc
Cable break auto reset
Input YES
yes - no
OK
Restart rESt
Restart device
Confirm no
yes - no
OK
Drop-down menu h.chn
Heat exchanger material selection
Drop-down menu tS
tS
OK
t6 tU
(Steel) (Glass) (PVDF)
oper
Hour meter
Display
Drop-down menu baud
Modbus RTU baudrate
Input 1920
480 - . - 1152
OK
Drop-down menu pari
Modbus RTU parity
Input EUen
none - odd - eUen
OK
Drop-down menu addr
Modbus RTU device ID
Input 10
1 . 247
OK
Fig.1: Menu overview TC MIDI
17Bühler Technologies GmbHBX440016 ◦ 09/2021

TC-MIDI (+)
5.3 Using the Digital Interface
The digital interface on this device is a Modbus RTU protocol,
which physically communicates via RS485 (2-wire). The cooler
therefore takes on the role of the slave in communication.
The Modbus interface enables direct access to process and
diagnostic data and parameters during operation.
5.4 Modbus Configuration
The settings below are the defaults; the parameters can be ad-
justed if the interface is enabled.
1 start bit
8 data bits
1 parity bits (configurable)
1 stop bit (*)
Baudrate: 19200 bps (configurable)
Device ID: 10 (configurable)
(*) The length of a Modbus frame is always 11bit, configuring
the interface at 0 data bits automatically changes the number
of stop bits to 2.
5.5 Modbus Communication
Communication via Modbus RTU is always imitated by the
master (request). The slave (typically) responds to the request
with a response. A Modbus RTU frame for a request/response
always has the following structure:
Address field (A) Function code (FC) Data CRC
1 byte 1 byte 1 … 252 bytes 2 bytes
Register addresses and data are transferred in Big Endian
format.
Every register stands for a 16bit value, with the information
represented in various data types. The data type and required
function code are assigned to the respective registers in the
following tables.
To read/write data types with sizes larger than an individual
register, multiple registers must be addressed.
Supported function codes:
Function code (FC) FC values
Read Holding Registers 3
Write Multiple Registers 16
Data types:
Description Number of bytes Number of registers
Float 4 2
Int16 2 1
Uint16 2 1
Int32 4 2
Uint32 4 2
6 Transport and storage
Only transport the product inside the original packaging or a
suitable alternative.
The equipment must be protected from moisture and heat
when not in use. It must be stored in a covered, dry and dust-
free room at a temperature of -20 °C to 60 °C (-4 °F to 140 °F).
7 Maintenance
Always observe the applicable safety- and operating regula-
tions when performing any type of maintenance. Please refer
to the original operator’s manual on the included CD or online
at www.buehler-technologies.com for maintenance informa-
tion.
8 Service and Repair
Please refer to the original operator’s manual on the included
CD or online at www.buehler-technologies.com for a detailed
description of the unit including information on
troubleshooting and repair.
8.1 Error messages on the display
If an error occurs, the display will read "Err". Press the " "
button to show the error number(s).
Error messages will appear until the unit has been restarted
or the error is cleared using the "Func" button. It can only be
cleared if the cause for the error has been corrected.
Causes / Action: The following is a list of the most common
causes and actions for the respective error. If the actions listed
do not resolve the problem, please contact Service.
18 Bühler Technologies GmbH BX440016 ◦ 09/2021

TC-MIDI (+)
Problem/mal-
function
Possible cause Action
No dis-
play
• No voltage
• Loose connect-
ing cable
• Display failure
• Check the supply
cable
• Check fuse
• Check connec-
tions
(perman-
ent)
D1.02 (The software ver-
sion for the display
will appear).
• Not communic-
ating with the
controller
• Check connec-
tions
Error • An error has oc-
curred
• Read the error
number as de-
scribed above
Error 01 • Controller mal-
function
• Clear error (tem-
porary fault)
• Disconnect from
power for approx.
5 s
• Contact service
Error 03 • Microcontroller
fault / MCP2
• Contact service
Error 04 • EEPROM error • Contact service
Error 22 • Moisture de-
tector 1 cable
break
• Check moisture
detector line
• Check moisture
detector
Error 32 • Moisture de-
tector 2 cable
break
• Check moisture
detector line
• Check moisture
detector
Error 40 • General error
temperature
sensor 1 (block
temperature)
• Possible sensor
failure
Error 41 • Low temperat-
ure / short-cir-
cuit temperat-
ure sensor 1
• Check temperat-
ure sensor con-
nection
Error 42 • Excess temper-
ature / short-
circuit temper-
ature sensor 1
• Check temperat-
ure sensor con-
nection
Error 43 • Measurement
fluctuation
temperature
sensor 1
• Check temperat-
ure sensor con-
nection
Error 50 • General error
temperature
sensor 2 (refer-
ence temperat-
ure Delta-T)
• Possible sensor
failure
Error 51 • Low temperat-
ure / short-cir-
cuit temperat-
ure sensor 2
• Check temperat-
ure sensor con-
nection
Error 52 • Excess temper-
ature / short-
circuit temper-
ature sensor 2
• Check temperat-
ure sensor con-
nection
Error 53 • Measurement
fluctuation
temperature
sensor 2
• Check temperat-
ure sensor con-
nection
Status text Possible cause Action
H2o.1 • Moisture alarm
moisture de-
tector 1
• Dry
• Check condensate
trap
H2o.2 • Moisture alarm
moisture de-
tector 2
• Dry
• Check condensate
trap
init • Initialisation
phase
• Wait
PuMP • Pumps deactiv-
ated
• Reactive pumps
via menu
dt Active Delta T con-
trol only: The block
temperature is out-
side the defined
temperature range.
• Cooler is still in
the "break-in
phase"
• Fluctuating
ambient tem-
perature
• Insufficient
cooling capa-
city
• Wait to see if the
target temperat-
ure will be
reached
• Check the ambi-
ent temperat-
ure / power sup-
plied
• Process-related:
Adjust alarm lim-
its
(Flash-
ing)
• Excess/low
temperature
• see chapter
“Troubleshoot-
ing”
19Bühler Technologies GmbHBX440016 ◦ 09/2021

TC-MIDI (+)
1 Introduction
Ce court mode d'emploi vous assiste lors de la mise en service
de l'appareil. Veuillez respecter les instructions de sécurité
afin d'éviter les risques sanitaires ou matériels. Avant la mise
en service, lisez attentivement le mode d'emploi original ainsi
que les indications concernant la maintenance et le dépistage
des pannes. Vous le trouverez sur le CD fourni et sur Internet
en allant sur
www.buehler-technologies.com
Vous pouvez nous contacter pour toute demande :
Bühler Technologies GmbH
Harkortstraße 29
40880 Ratingen
Allemagne
Tél. : +49 (0) 21 02 / 49 89-0
Fax : +49 (0) 21 02 / 49 89-20
Cette instruction d'utilisation fait partie du moyen de produc-
tion. Le fabricant se réserve le droit de modifier sans préavis
toute donnée relative aux performances, aux spécifications
ou à l'interprétation. Conservez ce mode d'emploi pour une
utilisation ultérieure.
1.1 Utilisation conforme à la destination d'usage
Cet appareil est conçu pour un usage dans des systèmes
d'analyse de gaz. Il constitue une composante essentielle à la
préparation du gaz de mesure pour protéger l'appareil de
l'humidité résiduelle dans le gaz de mesure.
Veuillez respecter les indications de la fiche technique concer-
nant la finalité spécifique, les combinaisons de matériaux
présentes ainsi que les limites de pression et de température.
1.2 Contenu de la livraison
• Refroidisseur
• Documentation produit
• Accessoires de raccordement ou de montage (en option)
2 Indications de sécurité
L'appareil ne doit être installé que par du personnel spécialisé
et familiarisé avec les exigences de sécurité et les risques.
Respectez impérativement les indications de sécurité perti-
nentes relatives au lieu d'installation ainsi que les règles tech-
niques en vigueur. Évitez les défaillances et les dommages
corporels et matériels.
L'exploitant de l'installation doit s'assurer que :
• les indications de sécurité et les instructions d'utilisation
sont disponibles et respectées,
• les directives nationales respectives de prévention des ac-
cidents sont respectées,
• les données et conditions d'utilisation licites sont respec-
tés,
• les dispositifs de protection sont utilisés et les travaux
d'entretien prescrits effectués,
• les réglementations légales pour la mise au rebut sont
respectées,
• les prescriptions d'installation nationales en vigueur sont
respectées.
DANGER
Tension électrique
Danger d'électrocution
a) Pour tous travaux, débranchez l'appareil du réseau.
b) Assurez-vous que l'appareil ne puisse pas redémarrer in-
volontairement.
c) L'appareil ne peut être ouvert que par des personnels
spécialisés qualifiés et instruits.
d) Veillez à ce que l'alimentation électrique soit correcte.
DANGER
Gaz toxiques ou irritants
Le gaz de mesure transporté par l'appareil peut être nocif
pour la santé s'il est inspiré ou s''il entre en contact avec la
peau.
a) Avant la mise en service de l'appareil, vérifiez l'étanchéité
de votre système de mesure.
b) Assurez une évacuation sûre des gaz dangereux pour la
santé.
c) Avant de démarrer des travaux de maintenance ou de ré-
paration, coupez l'alimentation en gaz et rincez les
conduites de gaz avec du gaz inerte ou de l'air. Sécurisez
l'alimentation en gaz pour prévenir toute réouverture in-
volontaire.
d) Lors des travaux d'entretien, protégez-vous des gaz
toxiques/irritants. Portez l'équipement de protection ap-
proprié.
DANGER
Atmosphère potentiellement explosive
Risque d'explosion lors d'une utilisation dans des zones sou-
mises à des risques d'explosion
Ce moyen de production n'est pas adapté à un usage dans
des zones à risque d'explosion.
Aucun mélange gazeux inflammable ou explosif ne doit tra-
verser l'appareil.
3 Transport et stockage
Les produits doivent toujours être transportés dans leur em-
ballage d'origine ou dans un emballage de remplacement ap-
proprié.
En cas de non utilisation, les matériels d'exploitation doivent
être protégés de l'humidité et de la chaleur. Ils doivent être
stockés dans une pièce couverte, sèche et sans poussière à une
température comprise entre - 20°C et 60°C (- 4°F à 140°F).
4 Assemblage et raccordement
4.1 Exigences quant au lieu d'installation
L'appareil est destiné à un montage mural dans des lieux fer-
més. En cas d'utilisation en plein air, une protection contre les
intempéries suffisante doit être prévue.
Montez l'appareil de sorte à laisser assez d'espace sous le re-
froidisseur pour dériver le condensat. Un peu d'espace doit
également être prévu au-dessus pour l'alimentation en gaz.
20 Bühler Technologies GmbH BX440016 ◦ 09/2021
Table of contents
Languages:
Other Bühler technologies Freezer manuals

Bühler technologies
Bühler technologies EGK 10 Reference guide

Bühler technologies
Bühler technologies EGK 1/2 Reference guide

Bühler technologies
Bühler technologies EGK 2A Ex User manual

Bühler technologies
Bühler technologies Precooler TS 10 Owner's manual
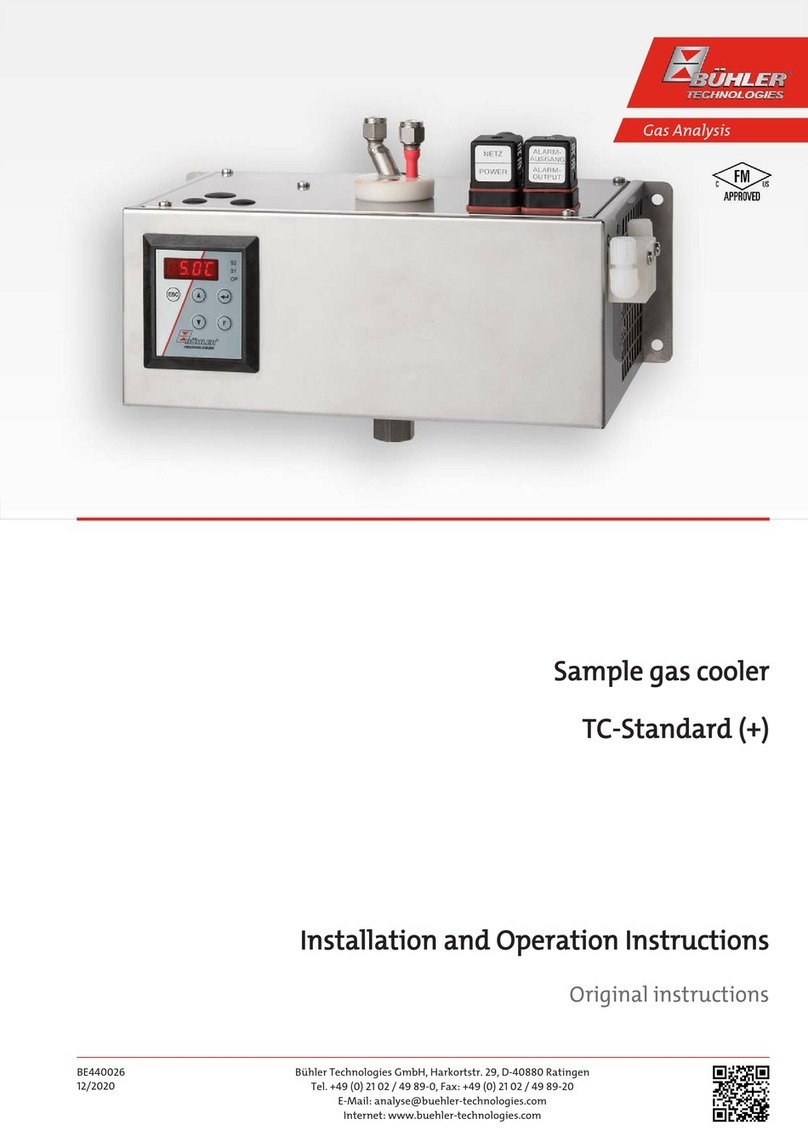
Bühler technologies
Bühler technologies 4496 Series User manual
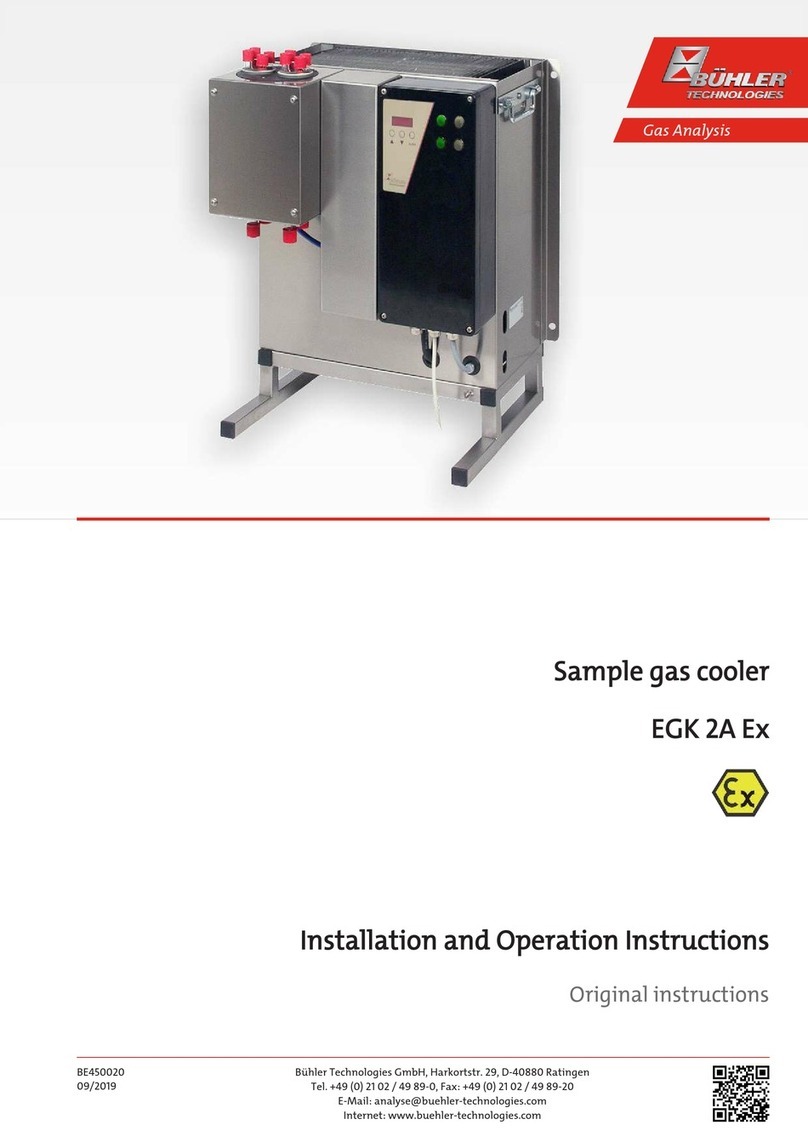
Bühler technologies
Bühler technologies EGK 2A Ex User manual

Bühler technologies
Bühler technologies TC-Double Plus User manual
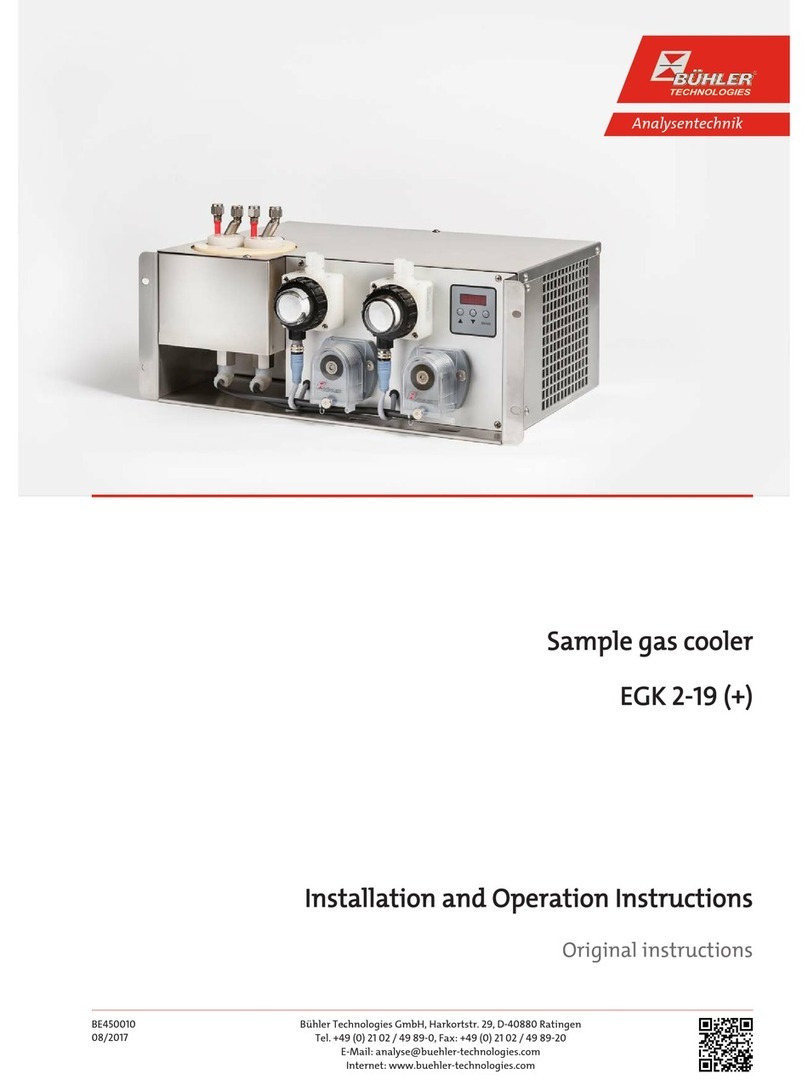
Bühler technologies
Bühler technologies EGK 2-19 User manual