Bürkert 2380 User manual

Operating Instructions
Type 2380
Bellow Control Valve
Bellow Valve with Digital Electropneumatic Controller

We reserve the right to make technical changes without notice.
Technische Änderungen vorbehalten.
Sous réserve de modifications techniques.
© Bürkert Werke GmbH, 2016
Operating Instructions 1604/02_EU-en_00810512 / Original DE

3
1. OPERATING INSTRUCTIONS ..................................................................4
1.1. Symbols .............................................................................................. 4
1.2. Definition of term „device“ ............................................................ 4
2. AUTHORIZED USE .........................................................................................5
3. BASIC SAFETY INSTRUCTIONS .............................................................5
4. GENERAL INFORMATION ...........................................................................7
4.1. Contact addresses ..........................................................................7
4.2. Information on the internet ............................................................7
4.3. Warranty ............................................................................................. 7
5. DEVICE DESCRIPTION ................................................................................7
5.1. General description ......................................................................... 7
5.2. Versions .............................................................................................. 7
6. STRUCTURE AND FUNCTION..................................................................8
6.1. Structure ............................................................................................8
6.2. Control functions .............................................................................. 8
7. TECHNICAL DATA ...........................................................................................9
7.1. Conformity and standards .............................................................. 9
7.2. Type label ........................................................................................... 9
7.3. Operating conditions .......................................................................9
7.4. Technical data .................................................................................10
7.5. Pneumatical Data ...........................................................................10
7.6. Electrical Data .................................................................................10
8. INSTALLATION ............................................................................................... 11
8.1. Safety instructions .........................................................................11
8.2. Installation position ........................................................................11
8.3. Installation / connections ..............................................................12
8.4. Pneumatic installation ...................................................................13
8.5. Electrical installation ......................................................................14
8.6. Communication software..............................................................14
9. START-UP .........................................................................................................15
9.1. Safety instructions .........................................................................15
9.2. Start-up process ............................................................................15
10. CIP / SIP .........................................................................................................16
11. MAINTENANCE AND TROUBLESHOOTING ................................ 16
11.1. Safety instructions .......................................................................16
11.2. Maintenance ..................................................................................17
11.3. Malfunctions/troubleshooting ....................................................17
12. SPARE PARTS ............................................................................................. 18
12.1. Safety instructions .......................................................................18
12.2. Spare part sets .............................................................................18
12.3. Replacement of the bellow ........................................................20
13. DISASSEMBLY ............................................................................................ 22
13.1. Safety instructions .......................................................................22
13.2. Disassembly of Type 2380 ........................................................22
14. TRANSPORT, STORAGE, PACKAGING, DISPOSAL ................22
Table Of Contents
Type 2380
Table of Contents
english

4
Operating instructions
Type 2380
1. OPERATING INSTRUCTIONS
The operating instructions describe the entire life cycle of the device.
Keep these instructions in a location which is easily accessible to
every user and make these instructions available to every new owner
of the device.
The operating instructions contain important safety information!
Failure to observe these instructions may result in hazardous
situations.
▶The operating instructions must be read and understood.
1.1. Symbols
DANGER!
Warns of an immediate danger!
▶Failure to observe the warning will result in a fatal or serious
injury.
WARNING!
Warns of a potentially dangerous situation!
▶Failure to observe the warning may result in serious injuries or
death.
CAUTION!
Warns of a possible danger!
▶Failure to observe this warning may result in a moderately
severe or minor injury.
NOTE!
Warns of damage to property!
▶Failure to observe the warning may result in damage to the
device or the equipment.
Indicates important additional information, tips and
recommendations.
Refers to information in these operating instructions or in
other documentation
▶ Designates an instruction to prevent risks
→Designates a procedure which must be carried out
1.2. Definition of term „device“
The term “device” used in these instructions always stands for the
Bellow Control Valve Type 2380.
english

5
Authorized use
Type 2380
2. AUTHORIZED USE
Non-authorized use of the Bellow Control Valve Type 2380
may be a hazard to people, nearby equipment and the
environment.
▶The device is designed to control the flow of gases and liquids.
▶Do not expose the device to direct sunlight.
▶Only devices with a separate Ex type label may be used in a
potentially explosive area.
▶In potentially explosive areas the device may be used only accor-
ding to the specification on the separate Ex type label. At the same
time the additional instructions for activation with ATEX approval,
which contain safety instructions for potentially explosive areas
must be adhered to.
▶The admissible data, the operating conditions and conditions of use
specified in the contract documents and operating instructions are
to be observed during use. The designated application cases are
specified in the chapter „7. Technical Data“.
▶The device may be used only in conjunction with third-party pro-
ducts and components recommended and authorized by Bürkert.
▶Correct transportation, correct storage and installation and care-
ful use and maintenance are essential for reliable and faultless
operation.
▶Use the device only as intended.
3. BASIC SAFETY
INSTRUCTIONS
These safety instructions do not make allowance for any
• contingencies and events which may arise during the installation,
operation and maintenance of the devices.
• local safety regulations - the operator is responsible for observing
these regulations, also with reference to the installation personnel.
DANGER!
Risk of explosion in explosive atmosphere!
Improper application in potentially explosive areas may cause
explosions.
▶The additional instructions for activation with ATEX approval, which
contain safety instructions for potentially explosive areas must be
adhered to.
WARNING!
Danger – high pressure!
▶Before dismounting the lines and valves, turn off the pressure
and vent the lines.
Danger through electric voltage!
▶Before reaching into the device or the system, switch off the
power supply and secure to prevent reactivation!
▶Observe applicable accident prevention and safety regulations
for electrical equipment!
english

6
BASIC SAFETY INSTRUCTIONs
Type 2380
WARNING!
Risk of burns / fire hazard due to hot device surface after
continuous operation!
▶Keep the device away from easily flammable matter and media.
▶Do not touch the device with bare hands.
WARNING!
General hazardous situations.
To prevent injury, ensure that:
▶the system cannot be activated unintentionally.
▶installation and maintenance work may be carried out by autho-
rized technicians only and with appropriate tools.
▶after an interruption in the power supply or pneumatic supply,
the process is restarted in a defined or controlled manner.
▶the device may be operated only when in perfect condition and
in consideration of the operating instructions.
▶the general rules of technology apply to application planning
and operation of the device.
▶no unauthorized internal or external modifications are made to
the device.
NOTE!
Electrostatic sensitive components / modules!
The device contains electronic components, which react sensitively to
electrostatic discharge (ESD). Contact with electrostatically charged
persons or objects may be hazardous to these components. In the
worst case scenario, they will be destroyed immediately or will fail
after start-up.
▶Observe the requirements in accordance with DIN EN 61340-5-1
to minimize or avoid the possibility of damage caused by sudden
electrostatic discharge!
▶Do not touch electronic components while the operating voltage
is connected!
english

7
General information
Type 2380
4. GENERAL INFORMATION
4.1. Contact addresses
Germany
Bürkert Fluid Control Systems
Sales Center
Christian-Bürkert-Str. 13-17
D-74653 Ingelfingen
Tel. + 49 (0) 7940 - 10 91 111
Fax + 49 (0) 7940 - 10 91 448
E-mail: [email protected]
International
Contact addresses can be found on the final pages of the printed
operating instructions. And also on the Internet:
www.burkert.com.
4.2. Information on the internet
The operating instructions and the data sheets for Type 2380 can be
found on the Internet:
www.burkert.com.
4.3. Warranty
The warranty is only valid if the device is used as authorized in
accordance with the specified application conditions.
5. DEVICE DESCRIPTION
5.1. General description
The Bellow Control Valve Type 2380 controls the flow of gases or
liquids. It is designed for ultrapure, sterile, dirty, aggressive, abrasive
or even highly viscous media.
The device can be sterilized with steam.
The device may only have media flow through it which neither corrode
the body nor damage the sealing materials (see chapter „7. Technical
Data“).
The application in a potentially explosive area is only allowed for devices
with an appropriate Ex type label (ATEX II 3 GD).
5.2. Versions
There are 2 versions of the device:
• Standard version – without separate Ex type label.
The standard version must not be used in a potentially explosive
area.
• Ex version – with separate Ex type label.
The Ex version may be used in a potentially explosive area. The
specifications on the separate Ex type label and additionally
included instructions for activation with ATEX approval, which
contain safety instructions for potentially explosive areas must be
adhered to.
Other characteristics can be chosen - see data sheet Type 2380
on our website www.burkert.com.
english

8
Structure and function
Type 2380
6. STRUCTURE AND FUNCTION
6.1. Structure
The bellow control valve consists of a controller Type 869x with an
appropriate actuator and a valve body.
Controller, e.g. Type 8696
(type label at rear side)
Actuator
Valve body
Cap (transparent)
(access for adjustments)
Electrical and
control air connections
Port connection,
e.g. weld ends
Type label (Type 2380)
Fig. 1: General structure of Type 2380
See also chapter „8. Installation“ at page 11, where all
connections are described.
For more details of Type 869x see also documentations on
our website www.burkert.com.
6.2. Control functions
Type 2380 is available with the control functions A (NC) or B (NO):
A: Normally closed
B: Normally open
Pneumatically controlled,
closed in resting position
by spring force
Pneumatically controlled,
opened in resting position
by spring force
english

9
Technical Data
Type 2380
7. TECHNICAL DATA
7.1. Conformity and standards
In accordance with the EC Declaration of conformity, the device is
compliant with the EC Directives.
Several approvals such as FDA, EC Regulation No 1935/2004, USP,
ATEX and others can be provided, depending on the characteristics
of the ordered device.
7.2. Type label
Type label for Type 2380 (by the cap of the device, see „Fig. 1“)
Several features of type code
Pressure of medium in bar *)
Control air pressure in bar *)
Operating voltage, if applicable communication
Serial no. S/N CE (or other) marks
ID-No.
Date of manufacture (encoded)
Bar code
Control function
Orifice
Sealing material
Controller type
Type Body material
Fig. 2: Type label 2380 - example
*) all pressure values are listed as overpressure
relating to atmospheric pressure in bar
7.3. Operating conditions
WARNING!
Risk of injury by ignoring the permitted operating conditions!
Important device-specific technical specifications are indicated on
the type label.
▶Observe permitted operating conditions printed on the device
type label.
Ambient temperatures: -10 ... +55 °C *)
Media:
liquids and gases (ultrapure, sterile, dirty,
aggressive, abrasive or even highly viscous),
steam for sterilization only *)
Media temperatures: 0 ... +80 °C
(-10 °C ... +150 °C at limited operating
conditions *) )
Media pressure: vacuum ... 6 bar **)
*) media pressure max. 4 bar,
up to +134 °C: max. 60 min, ambient temperature max. +40 °C,
up to +150 °C: max. 30 min, ambient temperature max. +35 °C
**) all pressure values are listed as overpressure
relating to atmospheric pressure in bar
english

10
Technical Data
Type 2380
7.4. Technical data
Dimensions: see data sheet of Type 2380
Weight: 1.8 ... 2.5 kg
Materials: media contacting
valve body: stainless steel 316L ASME BPE
(1.4435 BN2)
bellow: advanced PTFE
not media contacting
actuator: 304 (1.4301) or CF-8 (1.4308)
controller: PPS, stainless steel
sealing: EPDM, FKM
Control function: A (NC - normally closed),
B (NO - normally open)
Protection class: IP65 / IP67 acc. to EN 60529
Connections: threaded ports,
weld ends,
clamp connections
7.5. Pneumatical Data
Control media: air, neutral gas -
quality classes as per ISO 8573-1
dust content: quality class 7,
water content: quality class 3,
oil content: quality class X
Control air pressure:
5.5 ... 7 bar
Connection: threaded port G1/8
7.6. Electrical Data
Operating voltage: 24 V DC (or via AS-i bus)
Electrical data /
settings: defined by the Type 869x used
Electrical connections: defined by the Type 869x used:
multipole circular plug-in connector,
cable gland,
flat cable terminal
Electrical signals /
communication: defined by the Type 869x used:
analogue standard signals,
bus communication
(AS-i, DeviceNet, Profibus DP)
english

11
Installation
Type 2380
8. INSTALLATION
8.1. Safety instructions
DANGER!
Risk of explosion in explosive atmosphere!
▶Should the device be used in potentially explosive areas, chapter
„3“ and the additional instructions for activation with ATEX appro-
val must be adhered to.
WARNING!
Danger – high pressure in the system!
▶Before dismounting the lines and valves, turn off the pressure
and vent the lines.
Risk of electric shock!
▶Before reaching into the device or the system, switch off the
power supply and secure to prevent reactivation!
▶Observe applicable accident prevention and safety regulations
for electrical equipment!
Risk of injury from improper installation!
▶Installation may be carried out by authorized technicians only
and with appropriate tools!
Risk of injury from unintentional activation of the system and
an uncontrolled restart!
▶Secure system from unintentional activation.
▶Following installation, ensure a controlled restart.
8.2. Installation position
The device can be installed in any installation position. Consider the
recommended flow direction.
Leakage detection bores
One of the two bores for leakage detection (see „Fig. 3“)
should be at the lowest point. The other bore should be
closed to protect the device from outside liquid entry.
The orientation of the actuator on the valve body can be varied in
steps of 90°. For that purpose disassemble/assemble the actuator
as described in chapter „8.3.2“.
recommended flow direction
2 x leakage detection bore M5
engraved seat and port size
Fig. 3: Leakage detection bores and recommended flow direction
english

12
Installation
Type 2380
For self-drainage, install the valve body as shown in „Fig. 4“.
arrow upward
Fig. 4: Installation position for self-draining
Installation position for self-draining
It is the responsibility of the plant manufacturer and operator
to ensure self-drainage of the device or system.
8.3. Installation / connections
8.3.1. Installation in the pipe system
→Clean pipelines (sealing material, swarf etc.)
→Before connecting the valve, ensure that the pipelines are flush:
support and align the pipelines.
→Connect the valve body to the pipe system; for welded connec-
tions see next chapter „8.3.2“.
Robust installation
It is the responsibility of the plant manufacturer and operator
to ensure a robust installation. The relation of size and length
of the pipe to weight of the device must be considered.
8.3.2. Devices with welded connection
NOTE!
Risk of damage to the bellow because of heat!
▶Before welding in the body, remove the actuator with controller
from the valve body.
Risk of mechanical damage to the bellow!
▶During disassembly of the actuator with controller from the valve
body, ensure that the valve is in open position.
→Valves with control function A (NC) should be opened before
removal: how to open the valve - see description in chapter
„12.3. Replacement of the bellow“ at page 20.
→Remove actuator with bellow by loosening the 4 valve body
screws - see „Fig. 6“. Keep the controller assembled to the
actuator.
→Remove O-ring 1 from the valve body - see „Fig. 5“
→Weld valve body in pipe system.
O-ring 2
O-ring 1
Bellow
Fig. 5: Detail (valve body - O-rings)
english

13
Installation
Type 2380
→Assemble O-ring 1 again.
→Before assembling actuator with controller to the valve body
again, the valve must be open!
→Check correct position of bellow and O-rings.
→Fix the actuator again by tightening the 4 valve body screws with
a tightening torque of 3.5 Nm.
Valve body screws (4x)
Actuator with bellow
Ports for control air
(port 3 and port 1)
Controller (e.g. Type 8696)
Leakage detection bore (2x)
Fig. 6: Installation of welded connections
8.4. Pneumatic installation
WARNING!
Danger – high pressure in the system!
▶Before dismounting the lines and valves, turn off the pressure
and vent the lines.
WARNING!
Risk of injury from unsuitable connections!
Hoses or pipes which cannot withstand the pressure and tempe-
rature range may result in hazardous situations.
▶Only use connections which are authorized for the indicated
pressure and temperature range.
▶Observe the data sheet specifications from the manufacturers.
Observe for a proper functioning of the device:
▶The installation must not cause back pressure to build up.
▶Connection tubes with a sufficient cross section must be
selected.
▶The exhaust air line must be designed in such a way that
no water or other liquid can get into the device through the
exhaust air port (3).
▶During operation, keep the fluctuations of the control
pressure as low as possible (max. ±10 %). If fluctuations are
greater, the control parameters measured with the X.TUNE
function are not optimal.
Connection of the control air (see „Fig. 7“)
→Connect the control air to the control air port (1) of the controller
Type 869x.
→Mount an exhaust air line or a silencer to the exhaust air port (3).
If used in an aggressive environment, we recommend con-
veying all free pneumatic connections into a neutral atmos-
phere with the aid of a pneumatic hose.
english

14
Installation
Type 2380
control air
(port 1)
and
exhaust air
(port 3)
Fig. 7: Pneumatic connections (for Types 8696, 8694, 8692/3)
8.5. Electrical installation
WARNING!
Risk of electric shock!
▶Before reaching into the device or the system, switch off the
power supply and secure to prevent reactivation!
▶Observe applicable accident prevention and safety regulations
for electrical equipment!
The electrical connection depends on the controller Type 869x used.
The electrical connection of Type 2380 is described in the
respective operating instructions of Type 869x controllers on
our website www.burkert.com.
8.6. Communication software
The Bürkert PC operating program “Communicator” is designed for
communication with the devices from the Bürkert positioner family (valid
since serial number 20000).
A detailed description for the installation and operation of the
software can be found in the respective operating instructions
- search for Type 8920 („Communicator“).
Download the software and respective operating instructions for
Type 8920 from:
www.burkert.com.
Follow the descriptions in the respective operating instructions for
Type 869x and 8920:
→First install the „Communicator“ software on the PC
→Connect the Type 869x to a PC - for that purpose you need a
special USB adapter set mentioned in chapter „Accessories“ in
the respective operating instructions for Type 869x.
To avoid errors during data transfer:
▶Use the same settings for the serial interface for the
device and in the „Communicator“ software.
For best compatibility and device support:
▶Use the current version of the software „Communicator“
(download from the Bürkert website)
english

15
Start-up
Type 2380
9. START-UP
9.1. Safety instructions
WARNING!
Risk of injury from improper operation!
Improper operation may result in injuries as well as damage to the
device and the surrounding area.
▶Before start-up, ensure that the operating personnel are familiar
with and have completely understood the contents of the opera-
ting instructions.
▶Observe the safety instructions and intended use.
▶Only adequately trained personnel may start up the device/the
system.
9.2. Start-up process
Before start-up, pneumatic, fluidic and electrical connections must
be established.
→Switch on pilot pressure and supply voltage, keep the process
media switched off!
→Remove the transparent cap of the controller to gain access to
the DIP switches or operating keys. Observe the special instruc-
tions for potentially explosive areas.
→Run the function X.TUNE for an automatic adjustment of
the positioner - see respective operating instructions for the
Type 869x used.
→For Type 8692/93: select the input signal (INPUT).
→If necessary, specify additional controller settings (via DIP
switches/menu/USB adapter) - see respective operating instruc-
tions.
NOTE!
Caution with using the function SET.FACTORY
(reset to factory settings)!
This function does not only reset the settings implemented by
the user, but also all possibly preconfigured customer-specific
settings (referring to devices with additional label „Customized
Settings“)
→Switch on process media and activate set point.
→If necessary, adjust the controller settings.
→Tighten transparent cap of the controller again.
The device is now ready for operation.
english

16
CIP / SIP
Type 2380
10. CIP / SIP
The device can be cleaned / sterilized in place.
The only media-contacting parts are the valve body and the bellow.
NOTE!
Danger of damage to sealings and electronics by overheating!
The permitted media temperature of 0 ... +80 °C can be exceeded
only due to specific operating conditions (see chapter “7.3”):
• media pressure max. 4 bar
• up to +134 °C: max. 60 min, ambient temperature max. +40 °C
• up to +150 °C: max. 30 min, ambient temperature max. +35 °C
(all pressure values are listed as overpressure relating to atmospheric pressure in bar)
Good results in rinsing the valve body can be reached with a flow
velocity of 2 m/s over 15 min.
Due to limited space between the ribs of the bellow in opened
position, the valve should be opened and closed repeatedly while
rinsing to reach best cleaning results.
For best cleaning / sterilization results:
The results of CIP/SIP can vary depending on installation,
media and application conditions.
It is the responsibility of the plant manufacturer and operator
to monitor and optimize the cleaning procedure.
11. MAINTENANCE AND
TROUBLESHOOTING
11.1. Safety instructions
WARNING!
Danger – high pressure in the system!
▶Before dismounting the lines and valves, turn off the pressure
and vent the lines.
Risk of electric shock!
▶Before reaching into the device or the system, switch off the
power supply and secure to prevent reactivation!
▶Observe applicable accident prevention and safety regulations
for electrical equipment!
Risk of injury from improper maintenance!
▶Maintenance may be carried out by authorized technicians only
and with appropriate tools!
▶Observe the permissible tightening torques.
Risk of injury from unintentional activation of the system and
an uncontrolled restart!
▶Secure system from unintentional activation.
▶Following maintenance, ensure a controlled restart.
english

17
Maintenance and troubleshooting
Type 2380
11.2. Maintenance
The device is maintenance-free provided it is used according to these
operating instructions.
However, the bellow is subject to natural wear.
Check the bellow for wear after a maximum of 106 switching cycles
or 1 year of operation.
Muddy and abrasive media or operation under inapprop-
riate conditions (e.g. high temperatures / pressures) require
correspondingly shorter inspection intervals!
The service interval can be extended at constant operating conditions
if the bellows show only minor signs of wear and tear.
If leaks occur or the bellow shows signs of wear replace the respective
parts (spare part set - see chapter „12“).
For all maintenance activities, ensure that dirt cannot penetrate the
system.
11.3. Malfunctions/troubleshooting
If errors occur, first check the electrical connections, fluidic connec-
tions and inlet pressure. Furthermore check that the assembly/instal-
lation was implemented according to operating instructions.
If the system is still not functioning correctly, please contact the relevant
Bürkert Service (chapter „4.1. Contact addresses“ at page 7).
Malfunction Cause / remedial action
Valve does not
open/close
(or rather not
completely)
Control air port is not connected correctly:
→Connect control air to port 1.
Control pressure too low:
→See pressure specifications on the type label.
Valve is not
sealed.
Control pressure too low (NO valves):
→See pressure specifications on the type label.
Media pressure too high:
→See pressure specifications on the type label.
Sealing closure function (CUTOFF) not activated:
→Activation according to the operating instruc-
tions for the Type 869x used
Bellow worn out:
→Replace the bellow as described in chapter „12“
Cleaning
of media
chamber (valve
body + bellow)
dissatisfying
Too little space between the ribs of the bellow
with valve in opened position
→Open and close the valve while rinsing
X.TUNE is not
successful
→Check the control air supply:
if this is in the required range, see also the
„error and warning messages“ in the ope-
rating instructions for type 869x
english

18
Spare parts
Type 2380
Malfunction Cause / remedial action
Control quality
dissatisfying
E.g. caused by changed pressure conditions, etc.
→Adjust the controller via function X.TUNE
→Check an adjust the dead band (see also
operating instructions for Type 869x)
→When control air leakage occurs: see
respec tive operating instructions
Bus communi-
cation doesn't
work correctly
Missing or incorrect data transfer
→Check (and correct if necessary) the settings
for bus interface at the device and check also
the right version of the EDS file (DeviceNet)
or GSD file (Profibus).
→See also the respective operating in struc-
tions of the controller Type 869x used for
correct installation, configuration and start-up
Serial commu-
nica tion with
software
"Com muni-
cator" doesn't
work correctly
Missing or incorrect data transfer
→Use the same settings of serial interface
at the device and in the „Communicator“
software
For best compatibility and device support
→Use the current version of the software
„Communicator“ (Type 8920 - download
from the Bürkert website)
Tab. 1: Malfunction / troubleshooting
12. SPARE PARTS
12.1. Safety instructions
WARNING!
Risk of injury when opening the actuator!
The actuator contains a tensioned spring. If the actuator is
opened, there is a risk of injury from the spring jumping out!
▶The actuator must not be opened.
CAUTION!
Risk of injury and/or damage by the use of incorrect parts!
Incorrect accessories and unsuitable spare parts may cause
injuries and damage the device and the surrounding area.
▶Use only original accessories and original spare parts from
Bürkert.
12.2. Spare part sets
The bellow and 2 O-rings are available as a spare part set.
Consider the right size of the bellow according to the type label -
see the order table below.
english

19
Spare parts
Type 2380
1x O-ring 20 x 2.5
1x O-ring 52 x 2
1x Bellow
Each set contains:
Fig. 8: Spare part set
Orifice
(bellow size)
Spare part set:
order no.
Corresponding valve body
(seat size engraved in body )
DN3 00796530 DN4
DN4 00796531
DN6 00796532 DN6
DN8 00796533 DN10
DN10 00796534
Tab. 2: Order table
Bellows DN3 and DN4 are both combined with a valve
body DN4. So a change of the valve orifice between DN3
and DN4 can simply be executed by changing the bellow.
However, the device then is no longer consistent with the
type label.
This applies accordingly for bellows DN8/DN10 and the
valve body DN10.
NOTE!
Risk of damage to the bellow / malfunction of the device!
▶Do not combine bellow and valve body sizes other than shown
in „Tab. 2“.
If a controller needs to be exchanged, the order no. can be found on
the type label of the controller Type 869x.
Devices with additional label “Customized Settings” on
the controller are delivered with preconfigured customer-
specific settings.
▶Order these spare controllers (Type 869x) with reference
to the device ID number (Type 2380)!
▶In case an adjustment of preconfigured customer-specific
settings is required for future deliveries, please contact
your Bürkert sales office.
If you have any queries, please contact your Bürkert sales
office - see chapter „4.1. Contact addresses“.
english

20
Spare parts
Type 2380
12.3. Replacement of the bellow
12.3.1. Preparations
Step Task description Illustration
1 Ensure that there is no potential explosive atmosphere.
2 Ensure that process media pressure is switched off
3 Remove the transparent cap
(where applicable, loosen
locking wire and earthing
cable before)
(example: Type 8696)
Transparent
cap
Option:
locking wire
Option:
earthing
cable
4
Switch from AUTO to MANUAL operation mode.
8696 / 8694: DIP4 to ON-position
8692 / 8693: press key „MANU“ to change operation mode
12.3.2.
Opening NC-valve (control function A)
Step Task description Illustration
1Open the valve:
8696: press key „1“ key 1
DIP4 (ON)
key 2
8694: press
key „S1/X.TUNE“
8692 and
8693: press key
Alternatively the valve can be opened in AUTO operation
mode by setting the appropriate set point value.
english
Table of contents
Other Bürkert Control Unit manuals

Bürkert
Bürkert 6014 User manual
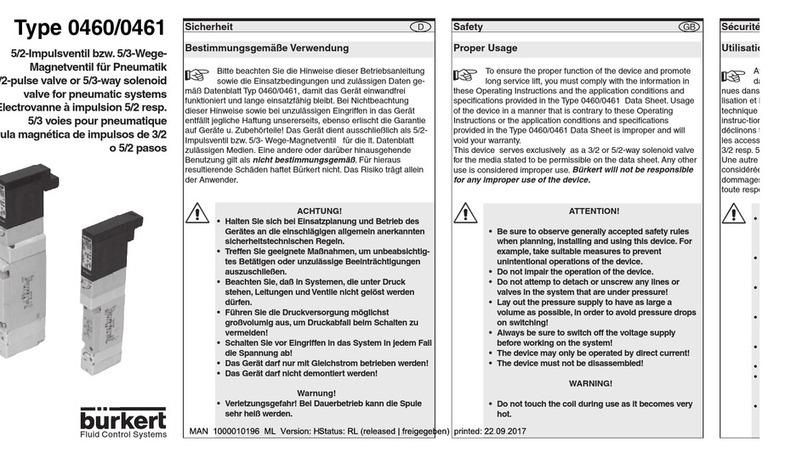
Bürkert
Bürkert 0460 User manual
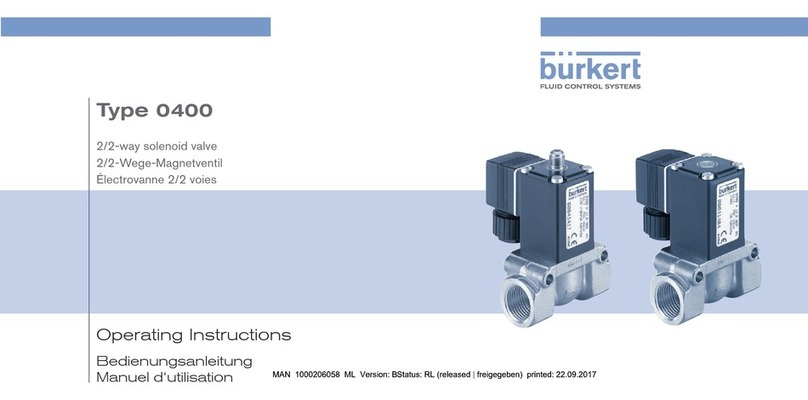
Bürkert
Bürkert 0400 User manual
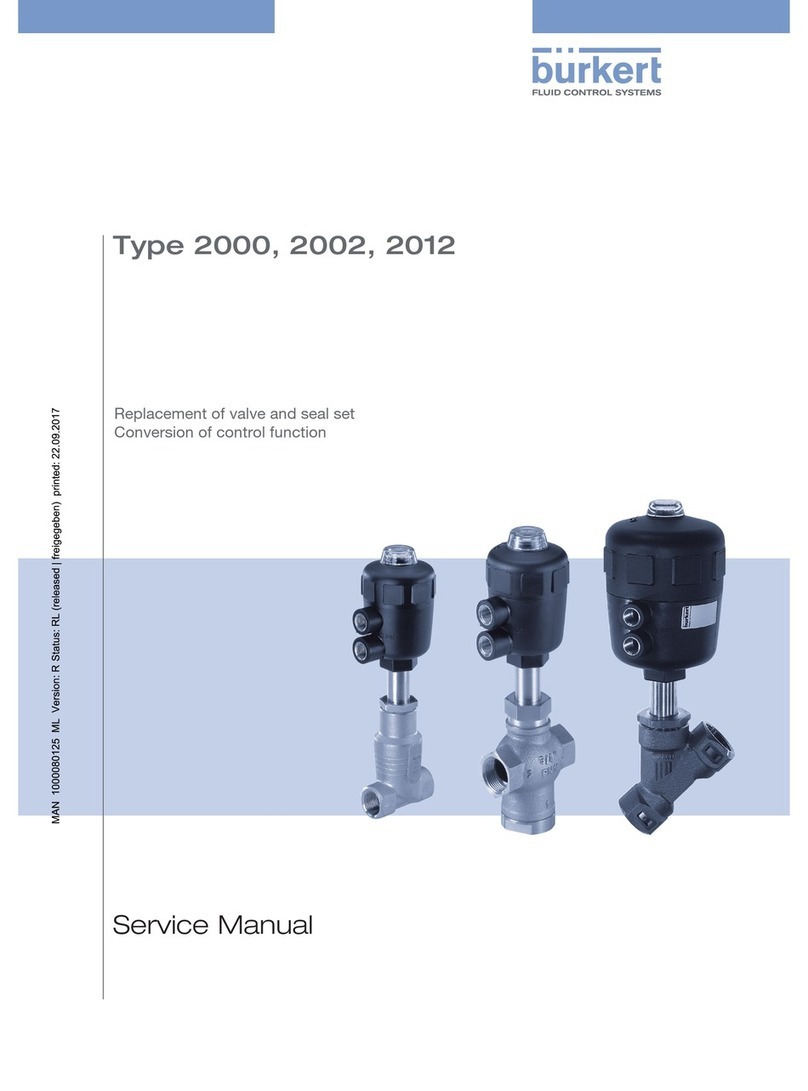
Bürkert
Bürkert Type 2000 User manual

Bürkert
Bürkert TwinPower 6624 User manual

Bürkert
Bürkert 2861 User manual

Bürkert
Bürkert 0255 User manual
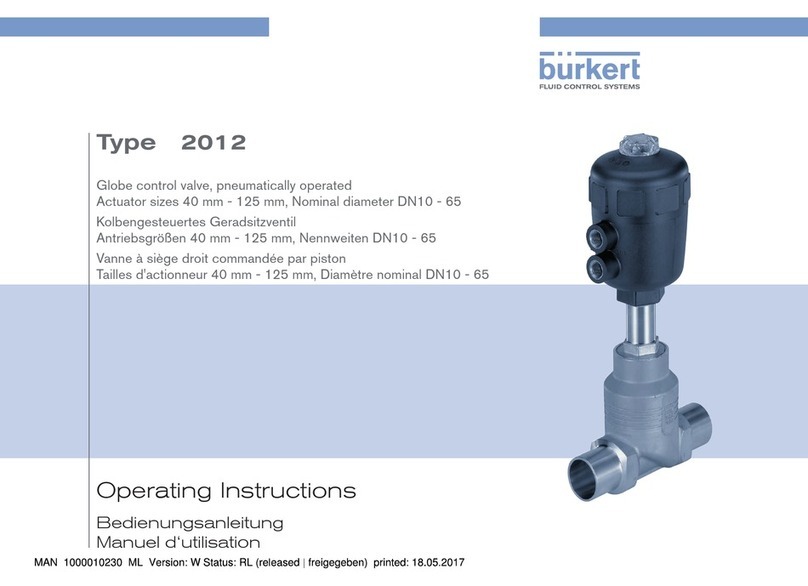
Bürkert
Bürkert Type2012 User manual

Bürkert
Bürkert 8695 User manual

Bürkert
Bürkert Type 2000 User manual
Popular Control Unit manuals by other brands
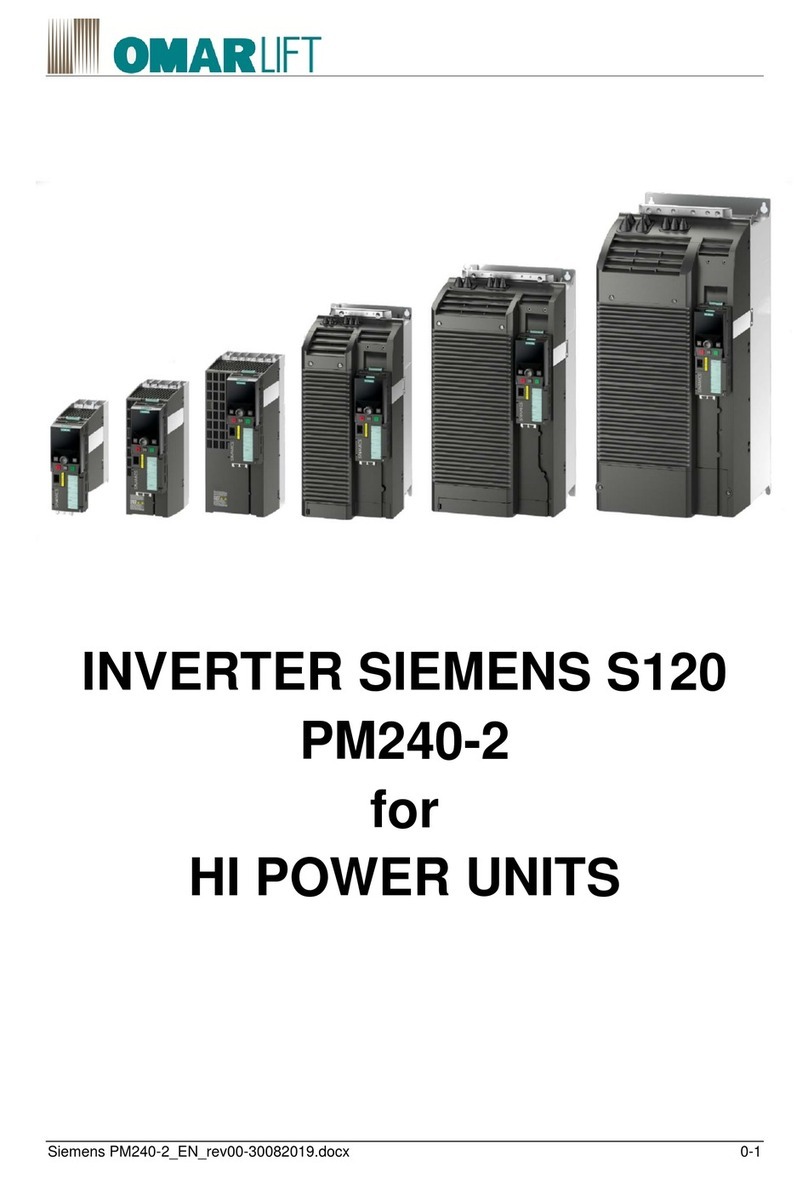
Siemens
Siemens S120 PM240-2 manual
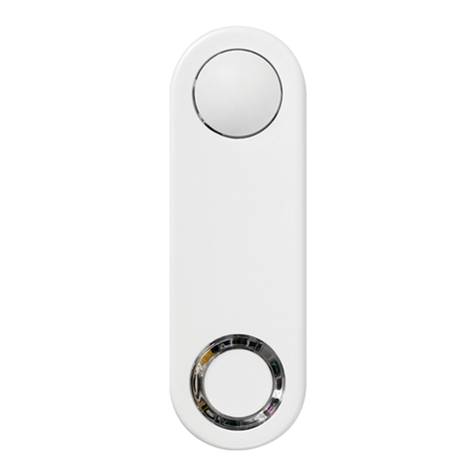
Lutron Electronics
Lutron Electronics Vive DFCSJ-OEM-OCC quick start guide
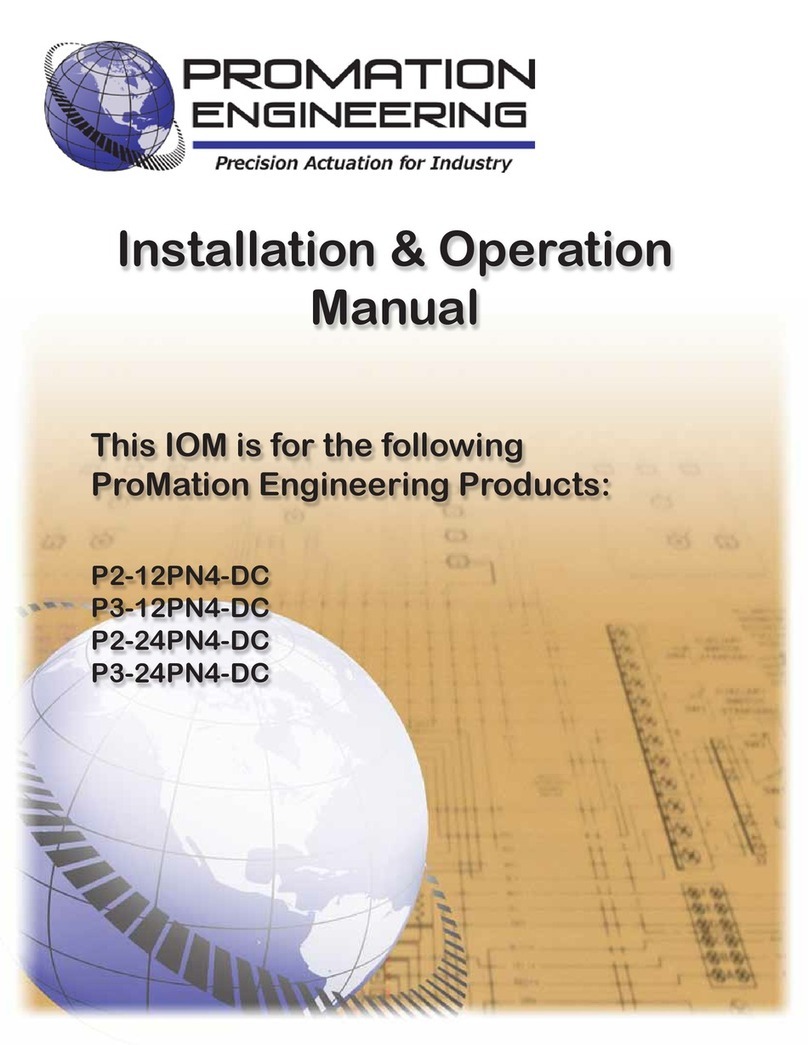
Promation Engineering
Promation Engineering P2 DC Series Installation & operation manual
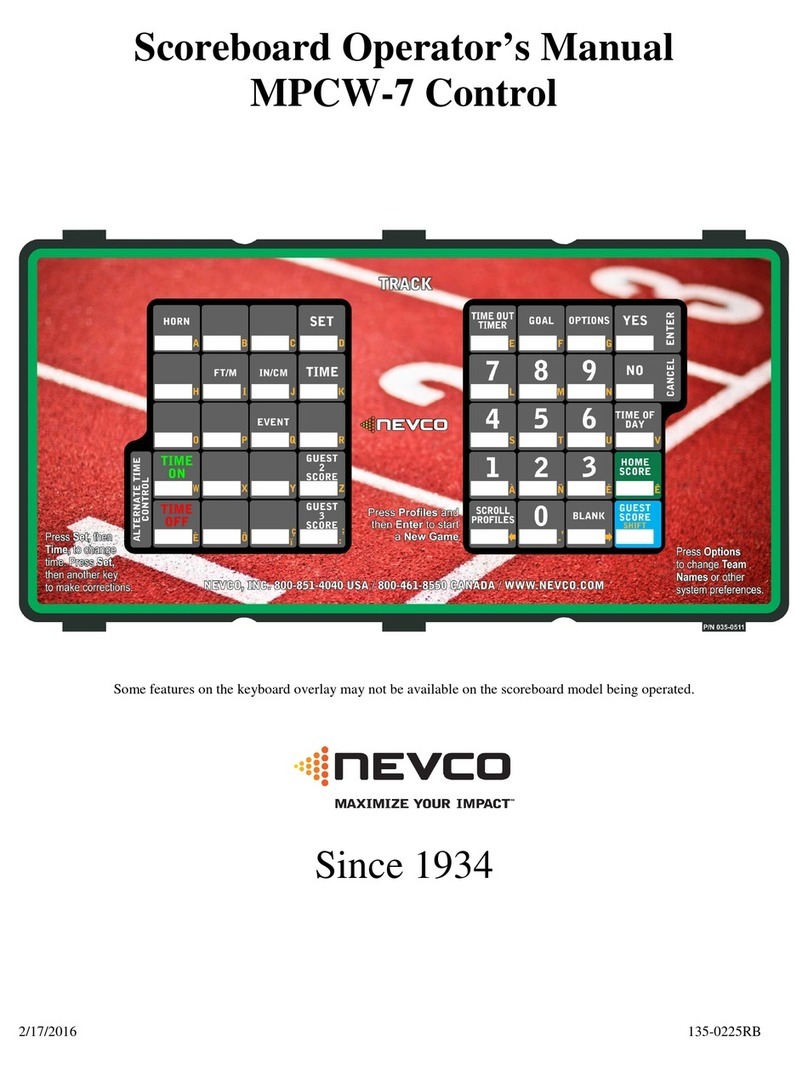
Nevco
Nevco MPCW-7 Control Operator's manual
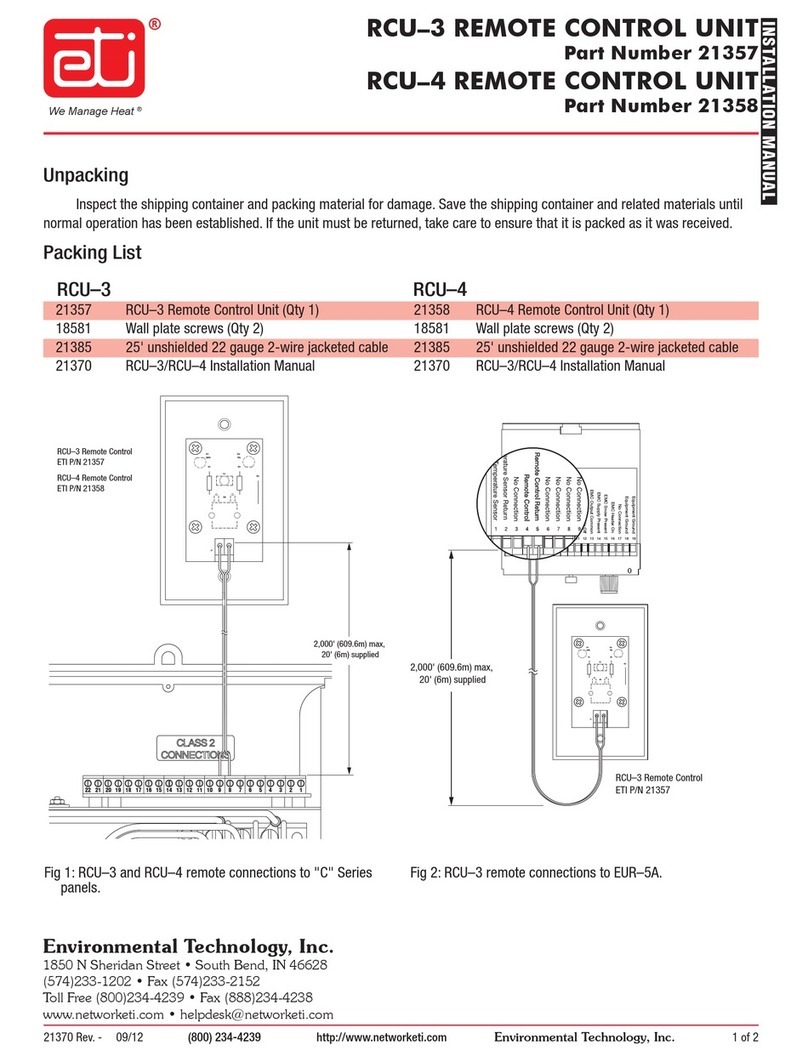
ETI
ETI RCU-3 installation manual
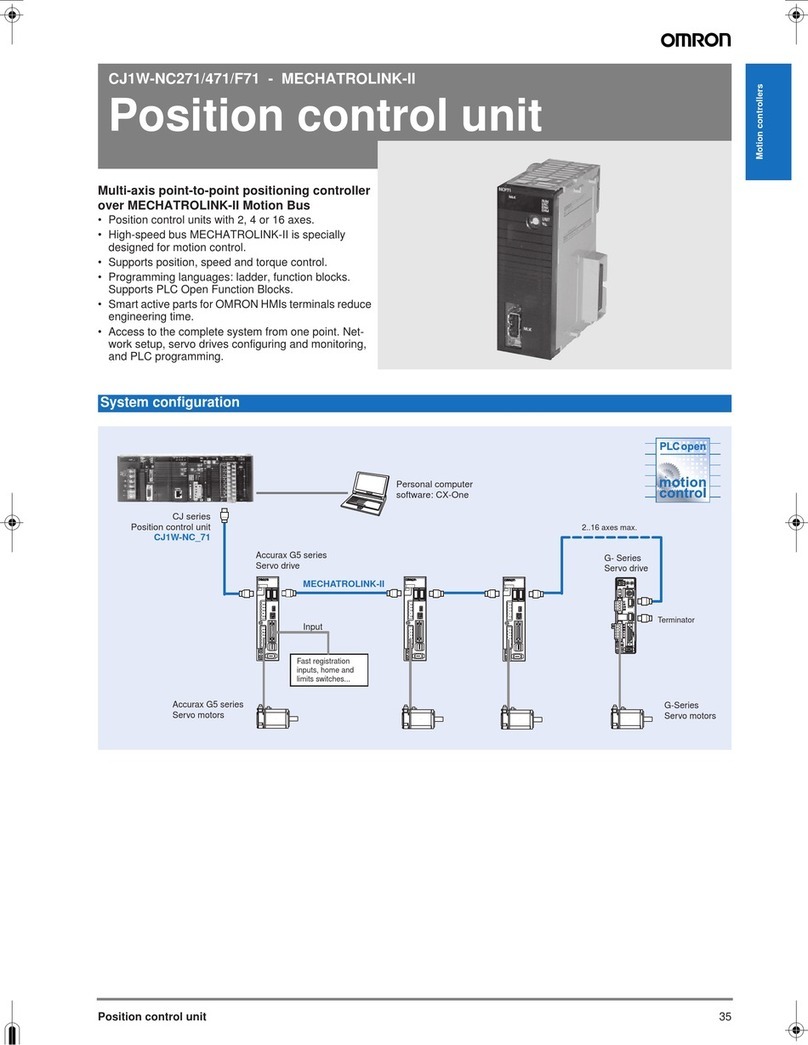
Omron
Omron CJ1W-NC271 System configuration