Becker C01 User manual

P5-16...R40-17
Model: C01
en Assembly and Operating Instructions
Roller shutter drive with integrated radio receiver
Important information for:
• Fitters / • Electricians / • Users
Please forward accordingly!
These instructions must be kept safe for future reference.
Becker-Antriebe GmbH
Friedrich-Ebert-Straße 2-4
35764 Sinn/Germany
www.becker-antriebe.com
2010 301 106 005/12/2018

Table of contents
General ............................................................................................................................................................................... 3
Warranty ............................................................................................................................................................................. 4
Safety instructions ............................................................................................................................................................... 4
Instructions for the user................................................................................................................................................... 4
Instructions for installation and commissioning.................................................................................................................. 4
Intended use ....................................................................................................................................................................... 6
Assembling and disassembling the plug-in connecting cable................................................................................................... 6
Assembling the plug-in connecting cable .......................................................................................................................... 6
Disassembling the plug-in connecting cable for tubular drives dia. 35. ................................................................................ 7
Disassembling the plug-in connecting cable for tubular drives dia. 45 and dia. 58 ................................................................ 8
Installation........................................................................................................................................................................... 9
Assembling the drive ....................................................................................................................................................... 9
Undoing the mounting pin................................................................................................................................................ 9
Drive adapter for obstacle detection ................................................................................................................................. 9
Drive adapter safety catch ............................................................................................................................................. 10
Assembling the drive adapter with safety catch on the drive shaft................................................................................. 10
Disassembling the drive adapter with safety catch on the drive shaft ............................................................................ 10
Assembling and disassembling the drive adapter with separate drive adapter safety catch............................................. 10
Assembling and disassembling the drive adapter with screw connection ...................................................................... 10
Mounting the drive in the tube ........................................................................................................................................ 11
Confirming the drive ...................................................................................................................................................... 12
First operation ................................................................................................................................................................... 12
Programming the master transmitter .............................................................................................................................. 13
Checking that the running direction is correct.................................................................................................................. 13
Intelligent installation management ................................................................................................................................ 14
Setting the limit positions............................................................................................................................................... 14
Upper stop to lower stop........................................................................................................................................... 14
Upper point to lower point......................................................................................................................................... 15
Upper stop to lower point.......................................................................................................................................... 15
Upper point to lower stop.......................................................................................................................................... 15
Changing the set limit positions ...................................................................................................................................... 16
Deleting the limit positions ............................................................................................................................................. 17
Intermediate positions I + II ............................................................................................................................................ 17
Programming additional transmitters.............................................................................................................................. 18
Deleting transmitters..................................................................................................................................................... 18
Overwriting the master .................................................................................................................................................. 19
Local operation with a single button..................................................................................................................................... 21
Upper anti-freeze mechanism ............................................................................................................................................. 22
Activating/Deactivating upper anti-freeze mechanism...................................................................................................... 22
Obstacle detection............................................................................................................................................................. 22
Fly screen protection function ............................................................................................................................................. 23
Programming the run times................................................................................................................................................. 23
Deleting the run times ........................................................................................................................................................ 23
Disposal ............................................................................................................................................................................ 23
Maintenance ..................................................................................................................................................................... 23
Technical data dia. 35 ........................................................................................................................................................ 24
Technical data dia. 45 ........................................................................................................................................................ 24
What to do if...?.................................................................................................................................................................. 25
Sample wiring diagram ....................................................................................................................................................... 26
Declaration of conformity ................................................................................................................................................... 27
2

General
These tubular drives are high-quality products with the following features:
•Optimised for roller shutter operation
•Individual, group and central radio control
•No need to run wires to a switch or relay control device
•Any combination of drive and transmitter possible
•Simple to set the limit positions with the transmitter
•Installation without stops possible (from upper point to lower point)
•Two freely selectable intermediate positions can be set
•Flexible radio grouping; can be altered at any time with no need to install/uninstall
•Integrated memo function facilitates easy programming of one or two switching times on daily repeat.
•Automatic detection of the lower limit position when using springs in conjunction with the "drive adapter for obstacle detec-
tion"
•Automatic detection of limit positions thanks to intelligent electronic system with stop systems
•Obstacle detection, even when using anti-lifting devices (axle shaft devices)
∙Secure anti-lifting device
∙Slight pressure applied to the roller shutter curtain makes it difficult to raise or reach under it
∙Suitable for rigid aluminium, steel and wooden profiles
•The final positions do not have to be reset: Changes in the shading solution are accommodated automatically when using stop
systems.
•Torque control in the up direction prevents damage to the roller shutter in the event of a frozen or blocked shutter
•Anti-freeze mechanism in the upper limit position can be enabled
•Considerably lower stop load, and thus considerably lower shading solution load.
•Smooth operation of the system and the drive increases the service life
•For plug-in connecting cable
•Fly screen protection function
Please observe these Assembly and Operating Instructions when installing and setting the equipment.
The date of manufacture comes from the first four digits of the serial number.
The numbers 1 and 2 indicate the year and the numbers 3 and 4 indicate the calendar week.
Example: 24th calendar week in 2012
Ser. No.: 1224XXXXX
Explanation of pictograms
CAUTION CAUTION indicates a hazardous situation which, if not avoided, could
result in injury.
ATTENTION ATTENTION indicates measures that must be taken to avoid damage to
property.
Denotes user tips and other useful information.
3

Warranty
Structural modifications and incorrect installation which are not in accordance with these and our other instructions can result in
serious injuries, e.g., crushing of limbs. Therefore, structural modifications may only be carried out with our prior approval and
strictly in accordance with our instructions, particularly the information contained in these Assembly and Operating Instructions.
Any further processing of the products which does not comply with their intended use is not permitted.
The end product manufacturer and fitter have to ensure that all the relevant current statutory, official and, in particular, EMC regu-
lations are adhered to during utilisation of our products, especially with regard to end product manufacture, installation and cus-
tomer advice.
Safety instructions
The following safety instructions and warnings are intended to avert hazards and to prevent property damage and personal injury.
Instructions for the user
General information
•The drive must be disconnected from its power source during cleaning and maintenance and when re-
placing parts.
•All work, including maintenance and cleaning, on electrical installations as well as other system parts
must always be performed by trained technicians, in particular qualified electricians.
•Children from the age of 8 years and persons with reduced physical, sensory or mental capabilities or
lack of experience and/or knowledge may use these devices, provided they are supervised or have
been instructed in the safe use of the device, and have understood the hazards involved. Children must
not play with the device.
•Systems have to be checked regularly by authorised specialists for wear and damage.
•Always put damaged systems out of operation immediately until they are repaired by an authorised
specialist.
•Do not operate equipment if people or objects are within the danger zone.
•Observe the danger zone of the equipment during operation.
•Ensure that there is adequate clearance (at least 40 cm) between moving parts and adjacent objects.
Caution
Safety instructions for avoiding serious injuries.
•Crushing or shearing points must be avoided or protected.
Instructions for installation and commissioning
General information
•Observe the safety instructions in EN 60335-2-97. Please note that this list of safety instructions is not
exhaustive, since it would be impossible for the standard to include all sources of danger. For example,
the design of the operated product, the way the drive works in the situation it is installed in or even the
way the end product is mounted in the end user’s place of use cannot be taken into consideration by
the drive manufacturer.
If any questions or uncertainties regarding the safety instructions contained in the standard arise,
please contact the manufacturer of the part or end product in question.
•All applicable standards and regulations for electrical installation must be complied with.
•All work, including maintenance and cleaning, on electrical installations as well as other system parts
must always be performed by trained technicians, in particular qualified electricians.
•Only use spare parts, tools and accessory devices which have been approved by the drive manufac-
turer.
Unapproved third-party products or modifications to the system and its accessories represent a risk to
4

your safety and the safety of others. This means that the use of unapproved third-party products, or
modifications which have not been agreed with or approved by us, are prohibited. We do not accept li-
ability for damage or injury arising from such actions.
•Position switch with OFF presetting within sight of the driven product, but away from moving parts, at a
height of over 1.5 m. This must not be publicly accessible.
•Permanently mounted control devices must be positioned where they can be seen.
•Rated torque and duty cycle must be suitable for the requirements of the driven product.
Technical data - rated torque and service life can be found on the type plate of the tubular drive.
•Hazardous moving parts of the drive must be installed at a height of over 2.5 m above floor level or any
other surface from which the drive can be accessed.
•To ensure safe operation of the system after commissioning, the limit positions must be correctly set/
programmed in.
•Drives with a H05VV-F connecting cable may only be used indoors.
•Drives with a H05RR-F, S05RN-F or 05RN-F connecting cable may be used both indoors and outdoors.
•To connect the drive to the driven part, solely mechanical accessory components made by the drive
manufacturer from the current product catalogue may be used. The components must be installed in
accordance with the manufacturer's instructions.
•If the drive is used for shading solutions in a specially marked area (e.g., escape routes, hazard zones,
safety areas), compliance with all applicable regulations and standards must be ensured.
Caution
Safety instructions for avoiding serious injuries.
•When electrical or electronic equipment and units are operated, certain components,
e.g., the power supply unit, are live. Physical injuries or damage to property can result in
the event of unauthorised interventions or failure to heed warnings.
•Be careful when touching the tubular drive, as it heats up during operation for technical
reasons.
•Before installation, shut down all lines and control devices that are not essential for op-
eration.
•Crushing or shearing points must be avoided or protected.
•When installing the drive, all-pole disconnection from the mains with a contact gap of at
least 3mm per pole must be provided (EN60335).
•If the mains connecting cable is damaged, it may only be replaced by the manufacturer.
If the drive has a plug-in connecting cable, it must be replaced with the same type of
mains connecting cable, which is available from the drive manufacturer.
Attention
Safety instructions for avoiding property damage.
•Ensure that there is adequate clearance between moving parts and adjacent objects.
•The drive must not be carried by the mains connecting cable.
•All latching connections and fastening screws on the brackets must be checked to en-
sure that they are secure.
•Ensure that nothing rubs against the tubular drive, such as shading solution attach-
ments, screws, etc.
5

Intended use
The type of tubular drive described in these instructions is intended solely for the operation of roller shutters.
This type of tubular drive supports not only curtain attachment by means of springs but also rigid shaft connectors, such as mech-
anical anti-lifting devices manufactured by Zurfluh-Feller, Simu, GAH Alberts and Deprat. These are detected automatically.
If the springs or the top lath are screwed or riveted to the barrel, a point must be set in the lower limit position.
When mounting connection parts on the drive dia. 35 mm PXX/XX, only use screws EJOT Delta PT 40x12 WN 5454 Torx (9900 000
545 4).
For sun protection applications, please use only the types of tubular drive designed for this purpose.
This type of tubular drive is designed for use in single systems (one drive per barrel).
The tubular drive must not be used in potentially explosive areas.
The connecting cable is not suitable for transporting the drive. Always carry the drive by the housing tube.
Other applications, uses and modifications are not permitted in order to protect the safety of the users and others, since these ac-
tions can impair the system’s safety and carry the risk of personal injury and property damage. The drive manufacturer does not
accept liability for damages or injury arising from such actions.
Always observe the information in these instructions when operating or repairing the system. The drive manufacturer does not ac-
cept liability for damage or injury resulting from improper usage.
Attention
Only use rigid shaft connectors if the roller shutter laths are sufficiently strong. The closed
curtain must not project beyond the guide tracks or else there is a risk of the joint between
the top two laths being subjected to excessive strain and getting damaged.
Assembling and disassembling the plug-in connecting cable
Assembling the plug-in connecting cable
Insert the dead connecting cable into the drive head until the locating lug clicks into place in the drive. If necessary, use a suitable
flathead screwdriver to assist with insertion. Set the screwdriver into one of the two plug grooves provided for this purpose.
Check that the cable is properly engaged.
1 = locating lug
6

Disassembling the plug-in connecting cable for tubular drives dia. 35.
Caution
Prior to disassembly, the power supply to the connecting cable must be disconnected.
Insert a suitable flathead screwdriver between the locating lug and the snap-in pin, so that the snap-in pin releases the locating lug
from the plug.
Now you can pull out the connecting cable along with the flathead screwdriver.
dia. 35
A
A = snap-in pin
7

Disassembling the plug-in connecting cable for tubular drives dia. 45 and dia. 58
Caution
Prior to disassembly, the power supply to the connecting cable must be disconnected.
Insert a suitable flathead screwdriver right into the recess of the locating latch, so that the latch releases the locating lug from the
plug.
Now you can pull out the connecting cable along with the flathead screwdriver.
dia. 45 and dia. 58
1.
2.
A
A = locating latch
8

Installation
Assembling the drive
Attention
To connect the drive to the driven part, solely mechanical accessory components made by
the drive manufacturer from the current product catalogue may be used.
Prior to mounting, the fitter must ensure that the masonry and the system being motorised are sufficiently robust (drive torque plus
weight of the shading solution).
Caution
Electrical connections may only be carried out by a qualified electrician. Prior to assembly,
the power supply must be disconnected and secured. Please give the enclosed connection
information to the responsible electrical contractor.
These drives cannot be operated with conventional switching elements (switches, timers
and the like).
If you want the roller shutter curtain to open to the upper stop, proceed as follows: The
roller shutter curtain must be prevented from being drawn into the shutter box with a
mechanical stop or an angled end strip. With face-fixed elements, we recommend con-
cealed stops in the guide tracks.
Calculate the space required at the side (M) by measuring the drive head (1) and wall
bracket (2). The clear dimension of the box (X) minus the space required at the side
(M) and idler (G) gives the length (L) of the barrel: L=X-M-G.
The space required at the side (M) varies depending on the combination of drive and
wall bracket.
Then mount the wall bracket and idler. Ensure that the barrel is aligned at right angles to the wall and that sufficient axial play is al-
lowed for the mounted system.
Attention
When using rigid shaft connectors, closed brackets must be fitted. The tubular drive
presses the closed curtain down to make it difficult for people to reach under it or raise it.
Only use curtains made of sufficiently strong material, such as aluminium, steel or wood.
To prevent damage to the curtain it must run in guide tracks from top to bottom.
Undoing the mounting pin
When pushed in, the mounting pin (2) locks automatically. To undo the mounting pin
(2), push the tab washer (1) upwards and pull out the mounting pin (2).
Drive adapter for obstacle detection
If you wish to use the "obstacle detection" function, you must use the "drive adapter for
obstacle detection".
9

Drive adapter safety catch
Assembling the drive adapter with safety catch on the drive shaft
Disassembling the drive adapter with safety catch on the drive shaft
Disassembly with disassembly tool, Item no. 4930 300 606 0
Disassembly with long nose pliers
2.
1.
Assembling and disassembling the drive adapter with separate drive adapter safety catch
Assembling and disassembling the drive adapter with screw connection
10

Mounting the drive in the tube
For profile tubes:
In the case of some drive adapters, tolerances of the groove widths in different bar-
rels can be offset by rotating the drive adapter into a different groove recess. These
groove recesses have different sizes and allow the drive to fit exactly.
Y
X
For round shafts:
Measure the lug of the thrust ring (X, Y). Then notch the tube on the motor side, so
the lug of the thrust ring can also be pushed into the shaft. There must be no play
between the lug of the thrust ring and the shaft.
-10 mm
To ensure secure torque transmission for round shafts, we recommend screwing the
drive adapter to the shaft (see the table below).
Attention!When drilling into the barrel, never drill near the tubular drive!
Size of drive
[mm]
Drive adapter Torque
max. [Nm]
Fastening screws
(4 units)
dia. 35-dia. 45 All Up to 50 Self-tapping screw
dia. 4.8 x 9.5 mm
dia. 58 Aluminium drive adapter Up to 120 Countersunk screw
M8 x 16 mm
dia. 58 diecast drive adapter Up to 120 Self-tapping screw
dia. 6.3 x 13 mm
We also recommend screwing the idler to the barrel.
Attention
Do not hammer the tubular drive into the tube or drop it into the barrel! The curtain can only
be secured using springs or rigid shaft connectors. We recommend at least three pieces
per metre of barrel.
Assemble the tubular drive with the relevant ring (1) and drive adapter (2). If the ring
has several grooves, select the groove which is a perfect fit and push the ring (1) onto
the thrust ring.
Insert the tubular drive with the pre-assembled ring (1) and drive adapter (2) into the
tube to achieve a form fit. Ensure that the ring and drive adapter are secure in the
tube.
Mount the assembled unit comprising barrel, tubular drive and idler on the box and secure the drive with a split or spring pin ac-
cording to the type of wall bracket fixing.
Position the barrel so that the roller shutter curtain can be attached with springs or fit the rigid shaft connectors in accordance with
the manufacturer's instructions.
Lay the connecting cable
Lay the connecting cable up to the tubular drive, and fix The connecting cable and
any antennae must not project into the winding chamber. Cover any sharp edges.
11

Confirming the drive
The drive confirms each programming and deletion action. The tubular drive does this through a small movement that can be per-
ceived (audibly) as "clicking" or (visually) as "shifting".
First operation
Explanation of symbols
UP button
STOP button
DOWN button
Programming button
The tubular drive clicks to confirm
(One or more times)
The tubular drive shifts to confirm
(One or more times)
1 = direction switch
2 = radio switch
Attention
The tubular drives are designed for short-time operation. An inbuilt thermal protection
switch prevents overheating of the tubular drive. During commissioning (long drop dis-
tance or long running time), the thermoswitch may trigger. The drive will switch off. After a
short cooling-down period, the system is ready for operation again.
The drive does not achieve its full duty cycle until it has cooled to ambient temperature.
Avoid a situation where the thermal protection switch cuts in repeatedly.
N1
2
1
2
4
3
4
230V AC / 50 Hz
L1
PE
Connecting the tubular drive
Connect the tubular drive to the power supply.
1 = blue 3 = black
2 = brown 4 = green-yellow
Readying the tubular drive for programming
Readying the tubular drive for programming by switching on the power
▻Switch on the power.
►The tubular drive is ready to programme for 3 minutes
If several tubular drives are to be connected in parallel, you can deactivate the program-
ming mode on one tubular drive by switching the radio switch to the outside position after
turning the power on.
12

Readying the tubular drive for programming with the radio switch
Switch the radio switch to the inside position. If the radio switch is already in this posi-
tion, switch it to the outside and back to the inside position.
►The tubular drive is ready to programme for 3 minutes
Programming the master transmitter
Press the programming button for 3 seconds when it is ready to programme.
▻The tubular drive acknowledges.
►The programming process is now complete.
If a transmitter is already programmed on the receiver, press the programming button for
10 seconds.
Checking that the running direction is correct
There are 2 ways to change the direction of rotation:
•Changing direction of rotation via rotation direction switch
•Changing direction of rotation via master transmitter
Changing direction of rotation via rotation direction switch
Press the UP or DOWN button
▻The shading solution runs in the desired direction
►The running direction is OK.
If the shading solution runs in the wrong direction, the running direction must be changed. Proceed as follows:
Switch the direction switch (1) to the opposite position.
▻The running direction will now have changed.
►Check the running direction again.
13

Changing direction of rotation via master transmitter
It is only possible to change the direction of rotation if no limit position has been set.
Press the UP or DOWN button
▻The shading solution runs in the desired direction.
►The running direction is OK.
If the shading solution runs in the wrong direction, the running direction must be changed. Proceed as follows:
First press the programming button and, within the next 3seconds, press both the UP
and DOWN buttons for 3seconds.
►The tubular drive acknowledges.
Check the running direction again.
Intelligent installation management
Limit position status indicator
A brief stopping and restarting indicates that no limit position has been set in that direction of movement.
Completion of installation following automatic setting of limit positions
The drive saves the limit position permanently once the upper limit position is reached 3 times in succession. Installation is then
complete. If the limit position is set above a point, this is stored permanently.
Setting the limit positions
The limit positions can only be set with the master transmitter. The shutter direction must
be correct. When setting the limit positions, the tubular drive runs in dead-man mode with
the limit position status indicator. The upper limit position must always be set first. When
setting the upper limit position, ensure that the roller shutter curtain is not pulled out of the
guide tracks.
When first installing using springs and adjusting the limit position "...to lower stop", the
barrel in the lower limit position turns approx. 1/4 of a turn further than usual. In doing so,
the tubular drive is able to automatically detect the use of anti-lifting devices or springs.
The tubular drive switches off automatically.
Attention
When operating the tubular drive without the drive adapter for obstacle detection, if using
springs a point must be set in the lower limit position.
There are 4 ways to set the limit positions:
•Upper stop to lower stop
•Upper point to lower point
•Upper stop to lower point
•Upper point to lower stop
The limit position becomes fixed after the tubular drive has turned off automatically in the desired position three times.
Upper stop to lower stop
Open to the permanent upper stop.
▻The tubular drive switches off automatically.
Then close to the permanent lower stop.
▻The tubular drive switches off automatically.
►The limit positions are now set.
14

Upper point to lower point
There is no shading solution length adjustment with this limit position setting.
Open to the desired upper limit position.
Press the programming button and, within 3 seconds, also press the UP button and
hold the two buttons down.
▻The tubular drive acknowledges.
Then close to the desired lower limit position.
Press the programming button and, within 3 seconds, also press the DOWN button
and hold the two buttons down.
▻The tubular drive acknowledges.
►The limit positions are now set.
Upper stop to lower point
Open to the permanent upper stop.
▻The tubular drive switches off automatically.
Then close to the desired lower limit position.
Press the programming button and, within 3 seconds, also press the DOWN button
and hold the two buttons down.
▻The tubular drive acknowledges.
►The limit positions are now set.
Upper point to lower stop
Open to the desired upper limit position.
Press the programming button and, within 3 seconds, also press the UP button and
hold the two buttons down.
▻The tubular drive acknowledges.
Then close to the permanent lower stop.
▻The tubular drive switches off automatically.
►The limit positions are now set.
15

Changing the set limit positions
Once set, the limit positions can only be changed with the master transmitter.
1) Shortening the range of travel (the desired limit position is located inside the current range of
travel)
Open/close to the desired new limit position.
Press the programming button and, within 3 seconds, also press the DOWN button
for the lower limit position or the UP button for the upper limit position and hold the
two buttons down.
▻The tubular drive acknowledges.
►The new limit position is now saved.
2) Extending the range of travel (the desired limit position is located outside the current range of
travel)
Attention
When both or individual limit positions are deleted, all the other set functions (intermediate
position I, intermediate position II, upper anti-freeze mechanism, obstacle detection, run
times, fly screen protection function) are deleted as well.
Open/close to the limit position in the direction in which you wish to extend the range
of travel.
Press the programming button and, within 3 seconds, also press the STOP button
and hold the two buttons down for 10 seconds.
▻The tubular drive acknowledges.
►The limit position is now deleted.
Open/close to the desired new limit position.
Press the programming button and, within 3 seconds, also press the DOWN button
for the lower limit position or the UP button for the upper limit position and hold the
two buttons down.
▻The tubular drive acknowledges.
►The new limit position is now saved.
16

Deleting the limit positions
Attention
When both or individual limit positions are deleted, all the other set functions (intermediate
position I, intermediate position II, upper anti-freeze mechanism, obstacle detection, run
times, fly screen protection function) are deleted as well.
Once set, the limit positions can only be deleted with the master transmitter. Deleted limit
positions are displayed on the limit position status indicator.
Deleting individual limit positions
Open/close to the limit position to be deleted.
Press the programming button and, within 3 seconds, also press the STOP button
and hold the two buttons down for 10 seconds.
▻The tubular drive acknowledges.
►The limit position is now deleted.
Deleting both limit positions
Open/close the shading solution to a point between the limit positions.
Press the programming button and, within 3 seconds, also press the STOP button
and hold the two buttons down for 10 seconds.
▻The tubular drive acknowledges.
►The limit positions are now deleted.
Intermediate positions I + II
The intermediate positions I + II are freely selectable positions for the shading solution
between the two limit positions. Each travel button can be assigned one intermediate posi-
tion. Both limit positions must be set before an intermediate position is set.
Setting the desired intermediate position
Open/close the shading solution to the desired intermediate position.
Press the STOP button and, within 3 seconds, also press the desired travel button
and hold the two buttons down.
▻The tubular drive acknowledges.
►The intermediate position is now saved.
Travelling to the desired intermediate position
Press the travel button for the desired intermediate position twice within one second.
►The curtain runs to the intermediate position assigned to the travel button.
17

Deleting the desired intermediate position
Move the shading solution to the intermediate position that is to be deleted.
Now press the STOP button and, within 3 seconds, also press the travel button as-
signed to the intermediate position and hold the two buttons down.
▻The tubular drive acknowledges.
►The intermediate position is now deleted.
Programming additional transmitters
In addition to the master transmitter, up to 15 further transmitters can be programmed in
the tubular drive.
Press the programming button of the master transmitter for 3 seconds.
▻The tubular drive acknowledges.
Now press the programming button of a new transmitter which has not yet been pro-
grammed in the tubular drive for 3 seconds. Doing so activates the programming
mode of the tubular drive for a new transmitter for 3 minutes.
▻The tubular drive acknowledges.
Now press the programming button of the new transmitter you wish to program again
for 3 seconds.
▻The tubular drive acknowledges.
►The new transmitter has now been programmed.
Deleting transmitters
Deleting individual transmitters
The programmed master transmitter cannot be deleted. It can only be overwritten (see
Programming the master transmitter [}13]).
Press the programming button on the master transmitter for 3 seconds.
▻The tubular drive acknowledges.
Now press the programming button of the transmitter to be deleted for 3 seconds.
▻The tubular drive acknowledges.
Then press the programming button of the transmitter to be deleted again for 10
seconds.
▻The tubular drive acknowledges.
►The transmitter is now deleted from the tubular drive.
18

Deleting all transmitters (except the master transmitter)
Press the programming button on the master transmitter for 3 seconds.
▻The tubular drive acknowledges.
Re-press the programming button on the master transmitter for 3 seconds.
▻The tubular drive acknowledges.
Re-press the programming button on the master transmitter for 10 seconds.
▻The tubular drive acknowledges.
►All transmitters (except the master transmitter) are now deleted from the re-
ceiver.
Overwriting the master
There are two ways to overwrite the master:
•Readying the tubular drive for programming by switching on the power
•Readying the tubular drive for programming with the radio switch
Readying the tubular drive for programming by switching on the power
To ensure that the new master transmitter is programmed in the desired tubular drive only,
all other tubular drives which are connected to the same power supply must be deactivated
from the programming mode. To do so, after switching back on the power, execute a drive
or stop command using the transmitter for the given tubular drives or switch the radio
switch from inside to outside. If the radio switch is already in this position, switch it to the
inside and back to the outside position.
N1
2
1
2
4
3
4
230V AC / 50 Hz
L1
PE
Switch off the tubular drive power for 5 seconds, then switch it back on.
▻The tubular drive is ready to program for 3 minutes.
1 = blue 3 = black
2 = brown 4 = green/yellow
Now press the programming button of the new master transmitter for 10 seconds.
▻The tubular drive acknowledges.
►The new master transmitter has now been programmed and the old master trans-
mitter overwritten.
19

Readying the tubular drive for programming with the radio switch
Switch the radio switch to the inside position. If the radio switch is already in this posi-
tion, switch it to the outside and back to the inside position.
▻The tubular drive is ready to program for 3 minutes.
Now press the programming button of the new master transmitter for 10 seconds.
▻The tubular drive acknowledges.
►The new master transmitter has now been programmed and the old master
transmitter overwritten.
20
Table of contents
Other Becker DC Drive manuals
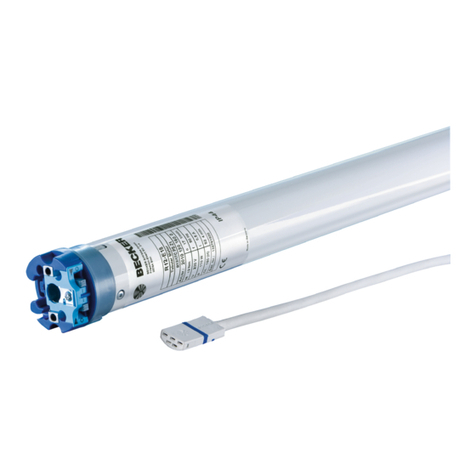
Becker
Becker R8/17R User manual
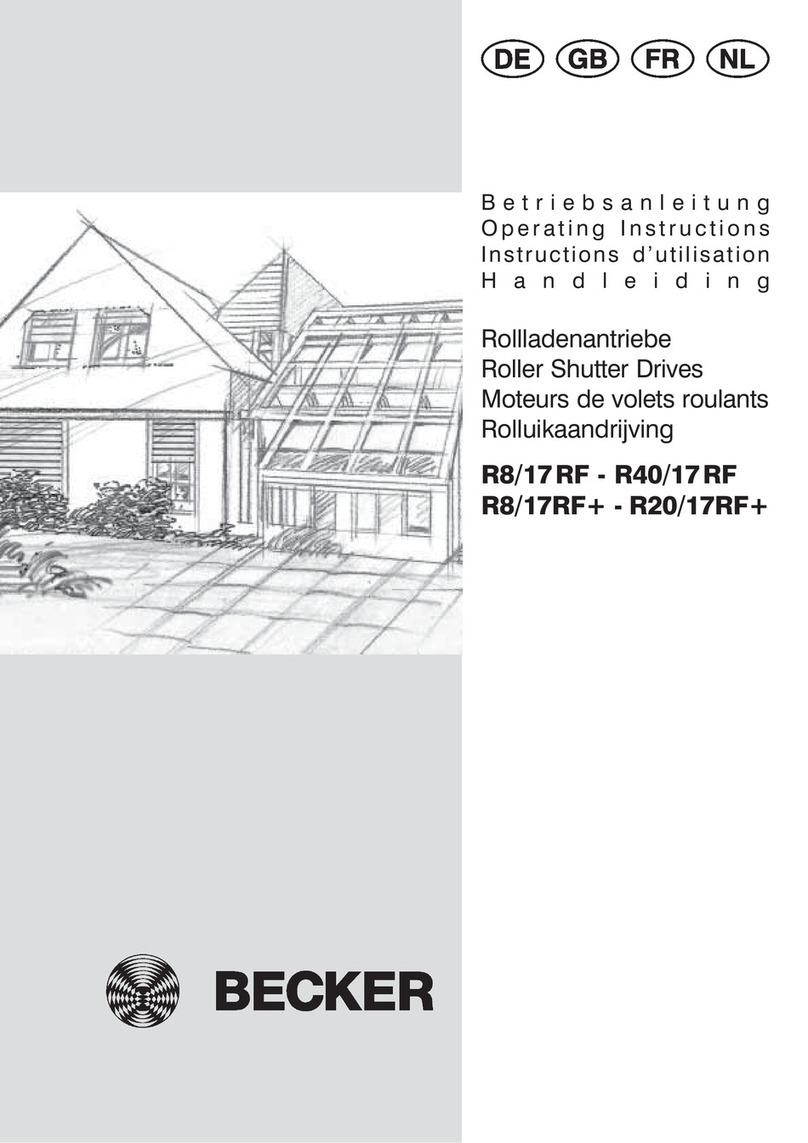
Becker
Becker R8/17RF User manual
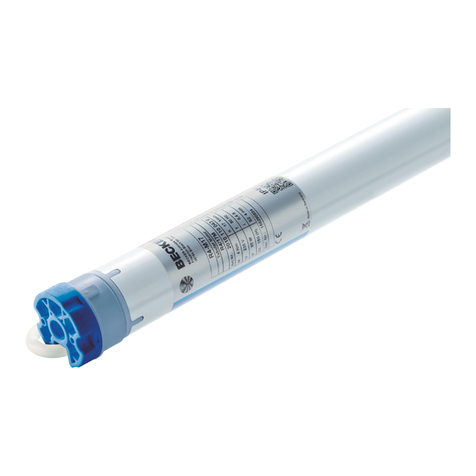
Becker
Becker R4-17 User manual

Becker
Becker P5-B01 User manual

Becker
Becker enocean R30-17 User manual
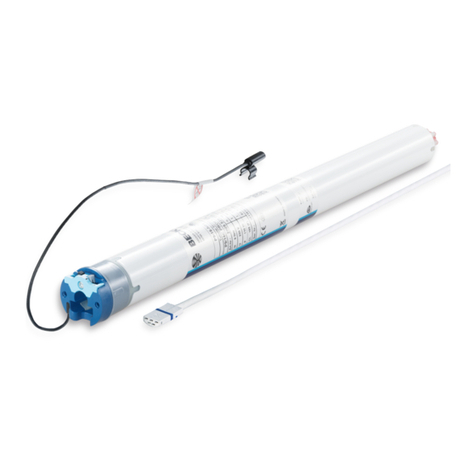
Becker
Becker enocean P5-16 User manual
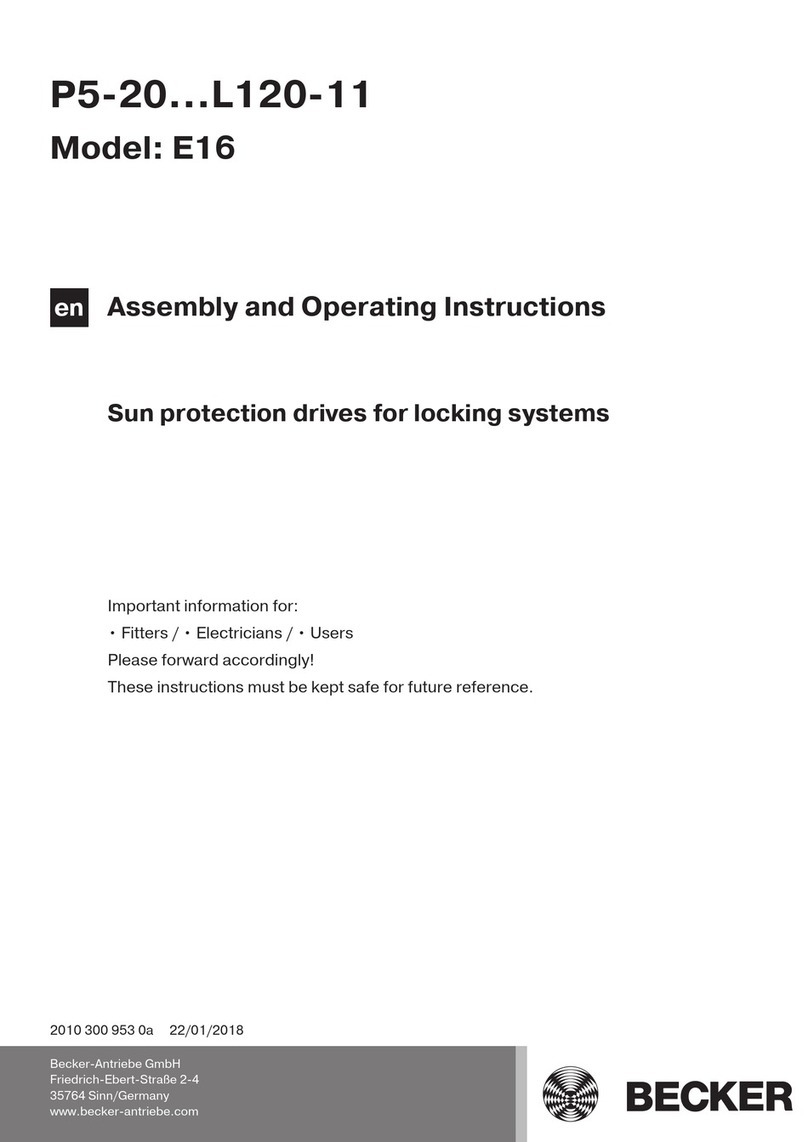
Becker
Becker P5-20...L120-11 Series User manual
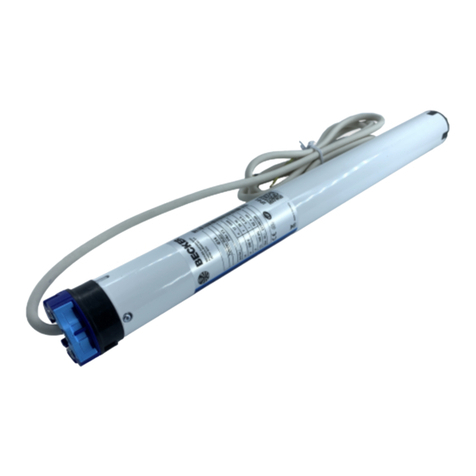
Becker
Becker R12/17RO+ User manual

Becker
Becker R8 17C PR+ User manual
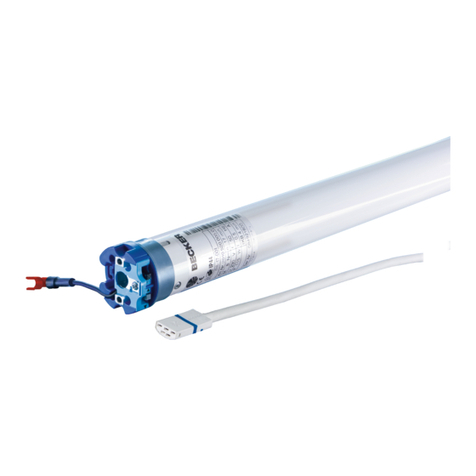
Becker
Becker C01a User manual
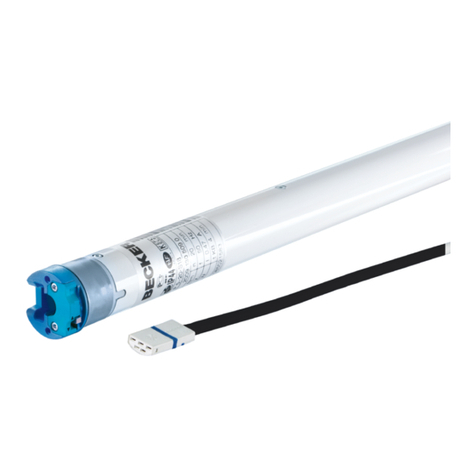
Becker
Becker P5-20-C18 PLUS User manual
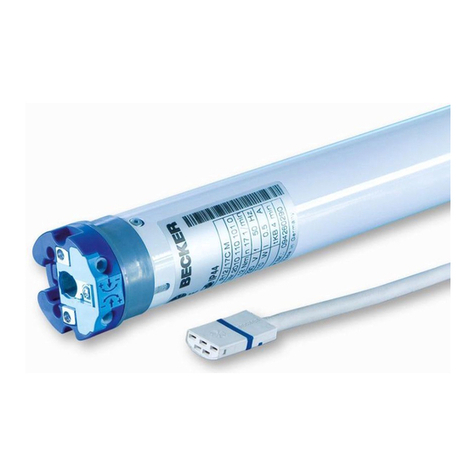
Becker
Becker R8/17PS User manual

Becker
Becker P5/16PRF+A1 User manual
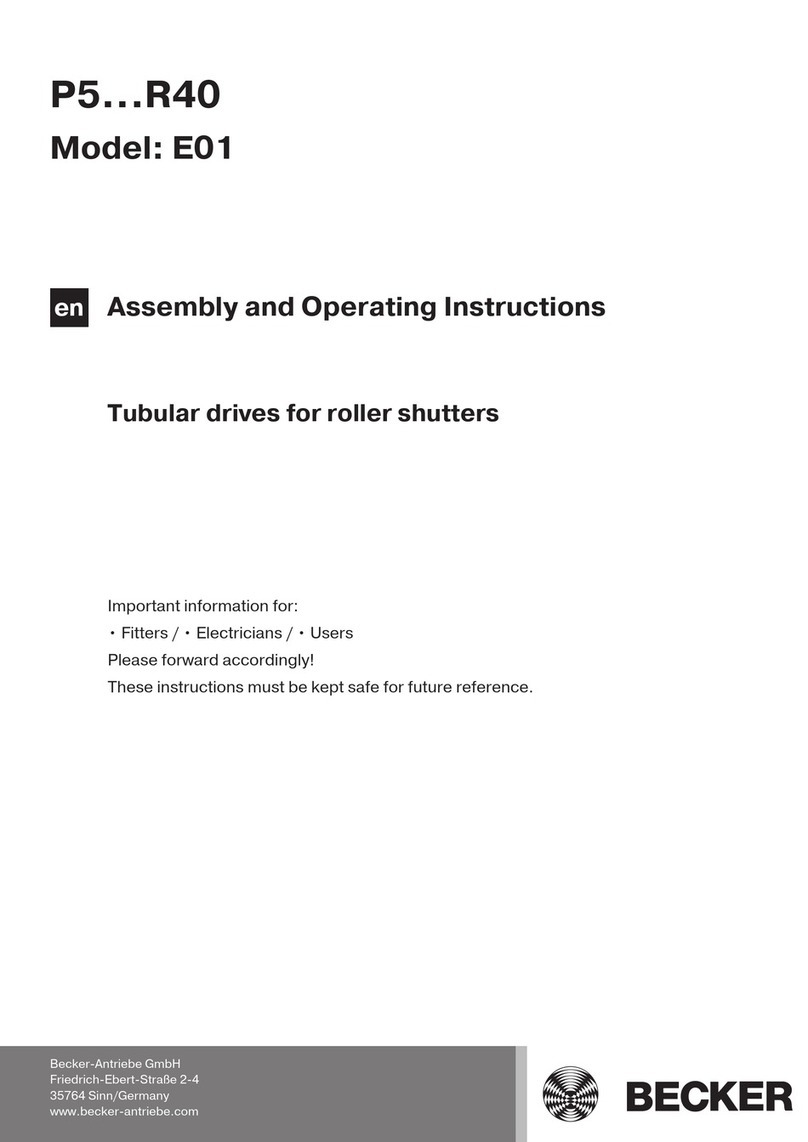
Becker
Becker E01 Series User manual

Becker
Becker E12a User manual
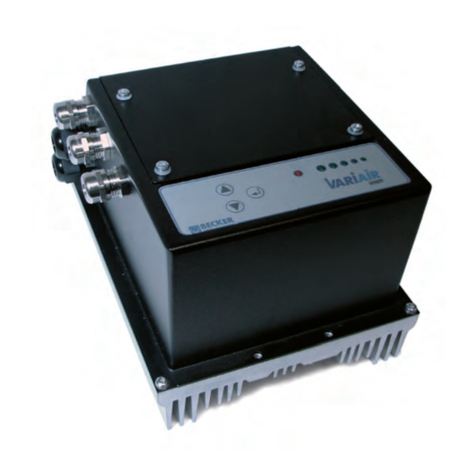
Becker
Becker VariAir VAU4/3 User manual

Becker
Becker M User manual
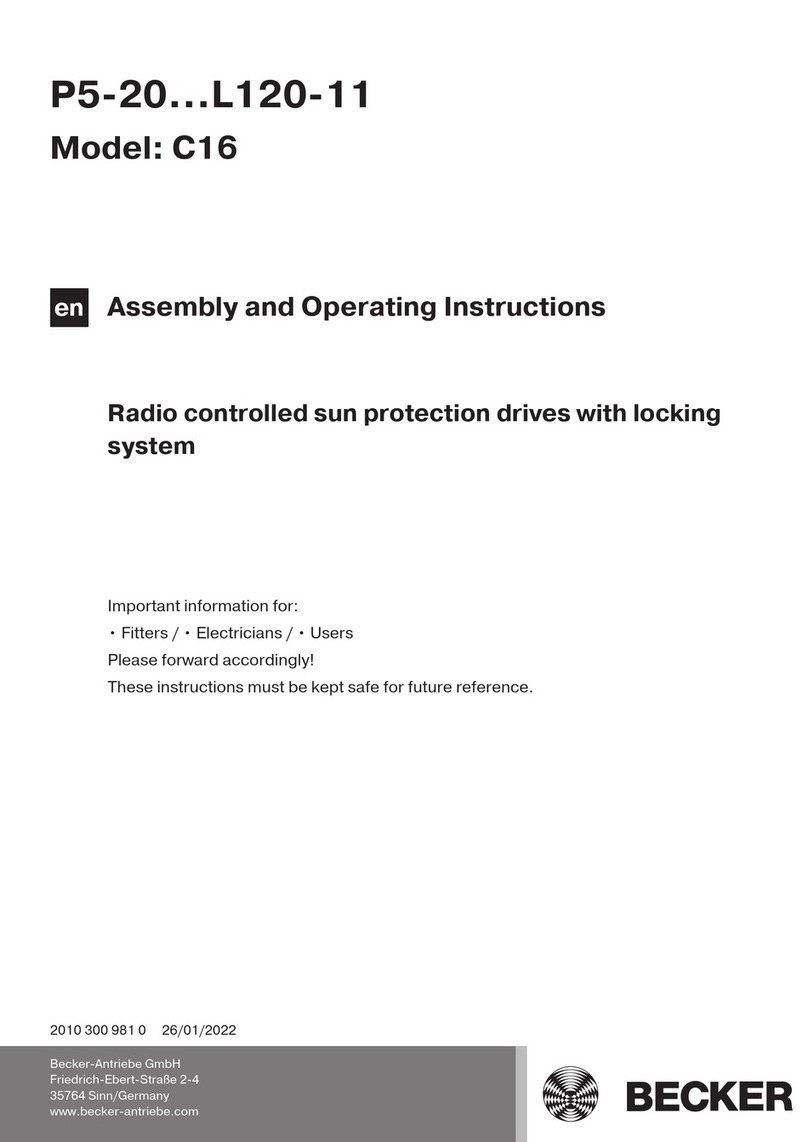
Becker
Becker C16 User manual

Becker
Becker U30 User manual
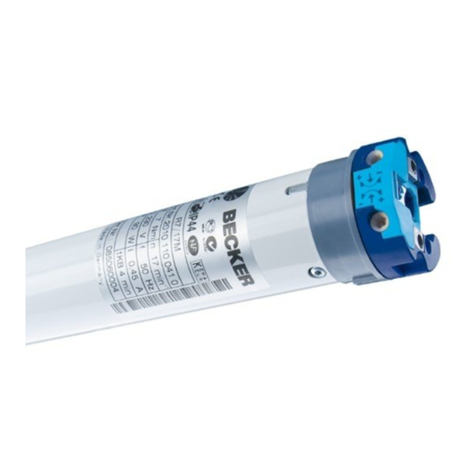
Becker
Becker P5/20M User manual