BECS BECSys5 User manual

Operation and Maintenance Manual


9487 Dielman Rock Island Ind Dr, St. Louis, MO 63132 www.becs.com
Operation and Maintenance Manual
Rev:
L13
TABLE OF CONTENTS
Warnings......................................................................... 1
General Guidelines ......................................................... 2
Firmware Version ........................................................... 2
Environmental Conditions .............................................. 2
Electrical Specifications ................................................. 2
NSF Suggested Operation Ranges .................................. 3
Applicable Sensor Operation Ranges ............................. 3
Section A: Programming the Controller ........................ 4
A – 1: Adjusting the Display Contrast ....................... 4
A – 2: Security Settings ............................................. 4
A – 2.1: Access Codes and levels .......................... 4
A – 2.2: Setting Access Codes ............................... 4
A – 3: Navigating the menus ..................................... 4
A – 3.1: Common status messages ........................ 4
A – 3.2: The Menu Screens ................................... 5
A – 3.3: The Lock Screen Key .............................. 6
A – 4: Inputs .............................................................. 6
A – 4.1: pH Setup .................................................. 6
A – 4.2: ORP Setup ............................................... 6
A – 4.3: Cl Inputs Setup ........................................ 7
A – 4.3.1: Free Cl Setup ..................................... 7
A – 4.3.2: Total Cl Setup .................................... 7
A – 4.3.3: Combined Cl ...................................... 7
A – 4.4: Temperature Setup ................................... 7
A – 4.5: Conductivity/TDS Setup .......................... 8
A – 4.6: Flow Rate Setup ....................................... 8
A – 4.7: pH & Chlorine Inventory Setups ............. 8
A – 4.8: Turbidity .................................................. 8
A – 4.9: Surge Pit Level ........................................ 8
A – 4.10: Pressure & Vacuum Setup ..................... 8
A – 4.10.1: Filter Influent Pressure .................... 8
A – 4.10.2: Filter Effluent Pressure ................... 8
A – 4.10.3: Filter Differential Pressure .............. 9
A – 4.10.4: Pump Effluent Pressure................... 9
A – 4.10.5: Strainer Vacuum ............................. 9
A – 4.10.6: Total Dynamic Head ....................... 9
A – 5: Control Outputs ............................................ 10
A – 5.1: pH Control ............................................. 10
A – 5.2: Chlorine Control .................................... 11
A – 5.3: Chlorine Booster Control ....................... 13
A – 5.4: Super Chlorination ................................. 13
A – 5.5: Dechlorination ....................................... 14
A – 5.6: Ozone Control ........................................ 14
A – 5.7: Heater ..................................................... 14
A – 5.8: Autofill ................................................... 15
A – 5.9: TDS Control ........................................... 15
A – 5.10: Sensor Wash ........................................ 15
A – 5.11: Enzyme ................................................ 15
A – 5.12: UV Turndown ...................................... 15
A – 5.13: Polymer ................................................ 16
A – 5.14: Recirculation Pump.............................. 16
A – 5.9.1: VFD Control: ................................... 16
A – 5.15: Alarm Relay ......................................... 16
A – 6: Control Options ............................................. 17
A – 6.1: Flow Restored Feed Delay ..................... 17
A – 6.2: Power Saver ............................................ 17
A – 6.3: pH Lockout ............................................. 17
A – 7: Calculations ................................................... 18
A – 7.1: Enter Parameters ..................................... 18
A – 7.2: LSI Setup ................................................ 18
A – 8: System Configuration .................................... 18
A – 8.1: System Info ............................................. 18
A – 8.2: Communication ...................................... 18
A – 8.2.1: Direct Baud Rate ............................. 18
A – 8.2.2: Ethernet Setup ................................. 18
C – 8.2.3: Call Out Setup.................................. 18
A – 8.2.4: Installed Options .............................. 19
A – 8.3: Datalog Frequency .................................. 19
A – 8.4: Date, Time & Units ................................ 20
A – 8.5: User Setup .............................................. 20
A – 8.6: Display Options ...................................... 20
A – 9: VFD Turndowns ............................................ 20
A – 10: 4-20mA Outs ............................................... 20
A – 11: Access Menu ............................................... 21
Section B: The Normal Display ................................... 22
B – 1: Inputs and Feeds ............................................ 22
B – 2: Alarms & Status messages ............................. 22
Section C: Using the Face Panel Quick Keys ............... 23
C – 1: The Set Points Key ........................................ 23
C – 2: The Relay Mode Key ..................................... 23
C – 3: The Cal Key (calibration) .............................. 24
C – 4: The Reset Fail / Safe Key .............................. 24
C – 5: The Emergency Off Key ................................ 24
Section D: Maintenance ............................................... 25
D – 1: Potentiometric Sensors (pH and ORP) .......... 25
D – 2: Free Chlorine Sensor ..................................... 25
D – 3: Total Chlorine Sensor .................................... 26
D – 4: Conductivity Sensor ...................................... 27
Section E: Feed Charts ................................................. 28
E – 1: Spa Feed Charts ............................................. 28
E – 2: Pool Feed Charts ............................................ 29
Section F: Replacement Parts ....................................... 30
Section G: Warranty ..................................................... 32


Page 1
9487 Dielman Rock Island Ind Dr, St. Louis, MO 63132 www.becs.com
Operation and Maintenance Manual
Rev:
L13
Warnings
Pay particular attention to the following warnings encountered while utilizing your
BECSys5 Water Chemistry Controller:
Caution: Various caution boxes may be found throughout the manual text.
Warning: Various other warning boxes may be
found throughout the manual text.

Page 2
www.becs.com 9487 Dielman Rock Island Ind Dr, St. Louis, MO 63132
Operation and Maintenance Manual
Rev:
L13
General Guidelines
Proper installation and use of the BECSys controller depends on the specific needs of the application. Read the manual
completely before starting the installation and ensure all guidelines and recommendations are followed. All components
should be mounted and the flow cell plumbing installed and pressure tested before wiring the controller. Ensure
compliance with all applicable plumbing and electrical codes during the installation as well.
Firmware Version
This manual was written for firmware v1.54. If you received newer firmware but did not receive a copy of the manual
covering that version of firmware, please contact your distributor.
Environmental Conditions
The BECSys5 is housed in a NEMA 4X (IP65) enclosure. It should not be used in explosive environments. The
BECSys5 should be mounted so that adequate ventilation is provided around the enclosure, preventing general
environmental specifications from being exceeded (see table below).
Environmental Specifications
Specification Ratin
g
Storage Temperature -40 to 85 Deg C
A
mbient Operating Temperature -18 to 50 Deg C
A
mbient Humidit
y
95% non condensing maximum humidit
y
Electrical Specifications
The BECSys5 may be ordered in either an 115VAC model or a 230VAC model. Following are the electrical
specifications for each model:
Controller Ratings
115VAC Mode
l
230VAC Mode
l
V
oltage: 115VAC 60Hz 230VAC 50Hz
Phase: Single Single
Current: 12.25 Amps Full Load 12.125 Amps Full Load
(¼
A
mp
–
Controller)
(
⅛Amp
–
Controller)
(12 Amps
–
Relay Outputs: 3A X 4)
(
12
A
mps
–
Relay Outputs: 3
A
X 4)
Relay Output Ratings
115VAC Mode
l
230VAC Mode
l
Relay 1 (K1) 250
V
AC (max)
–
3 Amps 250VAC (max)
–
3
A
mps
Relay 2 (K2) 250
V
AC (max)
–
3 Amps 250VAC (max)
–
3
A
mps
Relay 3 (K3) 250
V
AC (max)
–
3 Amps 250VAC (max)
–
3
A
mps
Relay 4 (K4) 250
V
AC (max)
–
3 Amps 250VAC (max)
–
3
A
mps
Caution: The BECSys controller should not be installed where it is accessible to the public.
Caution: The BECSys controller should be sealed while under operation. All IO, power cables, and unused
ports must be sealed using hardware rated NEMA4 or better. Damage to the controller caused by improper
sealing of the enclosure is not covered under warranty.

Page 3
9487 Dielman Rock Island Ind Dr, St. Louis, MO 63132 www.becs.com
Operation and Maintenance Manual
Rev:
L13
NSF Suggested Operation Ranges
ORP 650mV to 850m
V
pH 6.8 to 8.2
Free
A
vailable 0 to 10 ppm
Chlorine
Applicable Sensor Operation Ranges
Standard Sensors
pH 0.0 to 14.0 pH
ORP -1500mV to 1500m
V
T
emperature 32°F to 212°F (0°C to 100°C)
Reed Flow Switch Switch Point (On): 2.0 gpm
Rotary Flow Switch Switch Point (On): 1.5 gpm
Optional Sensors
A
mperometric ppm 0 ppm to 20 ppm
T
otal Chlorine 0 ppm to 20 ppm
Pressure Transducer 0 to 100 PSI
V
acuum Transducer -14.7 to 85 PSI
V
acuum Swichgage 0
–
30 in. HG
Pressure Swichgage 0
–
50 PSI
Differential Swichgage 0
–
50 PSI
Conductivity Sensor 0
–
20,000 micromho
T
urbidimeter 0
–
20.0 NTU
Flowmeter 0
–
655.35 Kgpm

Page 4
www.becs.com 9487 Dielman Rock Island Ind Dr, St. Louis, MO 63132
Operation and
Maintenance Manual
Rev:
L13
Section A: Programming the Controller
A – 1: Adjusting the Display Contrast
You can adjust the display contrast by holding down
either the up or down arrow keys for two seconds,
then after the controller beeps three times, use the
up and down keys to adjust the contrast.
A – 2: Security Settings
A – 2.1: Access Codes and levels
To view what access level you were given, press
the lock screen button while in any menu.
The Main Menu will also display who is logged on
along with the version of firmware.
You do not need to set all the access codes for
each level if you do not wish to. Also, a disabled
access code is not equivalent to 000, so entering
000 when it prompts for an access code will only
work if you have specifically assigned an access
code to be 000.
A – 2.2: Setting Access Codes
To set an access code, press the menu button,
then:
Select System Config
Choose User Setup
Then select the access level you want to set an
access code for.
To set Operator 1's access code, you would select
Oper. Access Codes, then select Operator 1.
Pressing and holding the +/- button disables the
access code, while pressing enter will enable and
set the access code to the value on the screen.
Operators may only change their own access code.
Managers may change their access code and any of
the Operators.
A – 2.3: Controller Options
Depending on how a particular controller is
configured, not all of the options listed in this
manual may be available.
A – 3: Navigating the menus
The controller's menus incorporate built in help text
to aid in understanding the function of each
parameter, item, and option.
A – 3.1: Common status messages
The very bottom line of the display contains the
time and date on the left while the right is reserved
for a number of status messages; the most
common are as follows:
"Busy..." - Indicates the controller is busy doing
something critical and it cannot stop until it
finishes. Until this message disappears, the
controller will not respond to your key presses
(although it does record them any will process
them when done). Normally this message is only
seen briefly after changing a setting, but it is also
used for lengthier operations such as factory
defaults and in the extremely rare case where the
internal diagnostics detect a memory problem and
attempts to correct it.
"(1 of 2) (More )" - and the like indicate there
are more options for you to choose from than the
controller could show at one time. Press the right
arrow key (Next) to view them. The left number
indicates the current page, while the right number
indicates the total number of pages.
"Bad Value, Retry..." - Accompanied by an error
beep, this indicates the value you just entered was
not within the allowable range of values and was
not stored.
Warning: Interrupting the controller by
turning the power off while it displays the busy
message could result in the complete loss of all
of its settings.

Page 5
9487 Dielman Rock Island Ind Dr, St. Louis, MO 63132 www.becs.com
Operation and Maintenance Manual
Rev:
L13
A – 3.2: The Menu Screens
Most of the features of the controller are
configured via the Menu button's menus. The
menu screens can be broken up into two types:
entry screens and lists.
A – 3.2.1: Entry Screens
An entry screen is used to enter a value using
the keypad.
The current value is usually displayed at the top
while the cursor will be positioned under the
current digit or character of the value you are
entering in. The up and down arrows allow you
to move the cursor right or left so you do not
have to retype the existing digits if you only wish
to change one.
Most numerical values will display the minimum
and maximum values you can enter in at the
bottom of the display in the format "< ### to
###>". These ranges many times will be
dependant on other values you have set, such as
alarm points or set points, while others are
simply fixed to stay within a reasonable range.
Entering a value that is not within the acceptable
range will result in an error beep and the
message "Bad Value, Retry..." being displayed in
the status area.
For some values, certain keys may take on
special functions that are explained in the lower
lines of the screen. The Down/up message in
the example above is one of them.
A – 3.2.2: List Screens
The list screens are mainly composed of lists of
menu items that you can choose from by either
pressing an item's number or by using the up
and down arrow keys to select it (indicated by
the arrow) and then pressing enter to choose it.
Using the up and down arrow keys also allows
you to view each item's help text. And if the
item leads to an entry screen or a list screen that
sets a setting (see below), the current value is
displayed in the lower right side.
Lists can also be used to change a setting:
When a list is used this way, it will display the
current setting followed by the words "Change
to:". Because it is a list, you can select an item
with the up/down buttons to see help
information about that particular selection.
There are a few list screens that use the entire
width of the display for displaying values
associated with each item and therefore do
not have help. See Section C: Using the
Quick Set Face Panel Keys for examples of
these types of screens.

Page 6
www.becs.com 9487 Dielman Rock Island Ind Dr, St. Louis, MO 63132
Operation and
Maintenance Manual
Rev:
L13
A – 3.3: The Lock Screen Key
When not in a menu (i.e. viewing the normal
display), pressing the lock screen key will prevent
the controller from paging the screen to show
more inputs, alarms, and other status information.
See Section B: The Normal Display for more info
about using the lock screen key in the normal
display.
While within any menu, if the user does not press
a key within sixty seconds of the last key press, the
current user is logged out and the screen is
returned to the normal display. To prevent the
controller from timing out, you may lock the
screen.
While within a menu, pressing the Lock Screen key
will bring up a popup menu:
The first option on the popup will be either to
lock or unlock the screen depending on the
current lock state. While the screen is locked, key
presses normally are ignored. However, in some
instances certain keys are given special functions
while the screen is locked, such as using the up
and down arrows to scroll the help text if all of the
help text cannot be displayed at once.
You can also lock/unlock the screen without
bringing up the popup menu by holding down
the lock button for one second. The
controller will acknowledge this action with a
triple beep and the yellow Lock Screen light
will turn on.
The Lock button popup menu also identifies who
is currently logged on, and provides an option for
the user to log off. You can also select cancel if
you pressed the lock button in error.
A – 4: Inputs
To enter the program menu, press the Menu button
on the front face panel of your controller. This will
allow the viewing of the Main Menu where the
programming options are displayed.
The Cl inputs, Cl Inventory Input, Chlorine
Control, and Chlorine booster control are all
displayed as either Chlorine and Cl or Bromine
and Br depending on the chemical selected in the
Cl feed menu. This manual is written using the
Chlorine setting. If you select Bromine as the
sanitizing chemical, the controller will display
Bromine and Br instead of Chlorine and Cl, but
the menus and functions are otherwise exactly the
same as shown.
A – 4.1: pH Setup
If your controller is configured to monitor pH,
you will have the following options:
High Alarm (Op): The high alarm will activate
when the pH reaches or rises above this setting.
You may disable this alarm by holding down the
+/- key for 1 second.
Low Alarm (Op): The low alarm will activate
when the pH reaches or falls below this setting.
You may disable this alarm by holding down the
+/- key for 1 second.
Alarm Hysteresis (Mgr): This value sets the
amount that the pH reading has to rise above the
high alarm or fall below the low alarm before the
alarm will shut off.
A – 4.2: ORP Setup
If your controller is configured to monitor ORP,
you will have the following options:
High Alarm (Op): The high alarm will activate
when the ORP reaches or rises above this setting.
You may disable this alarm by holding down the
+/- key for 1 second.
Low Alarm (Op): The low alarm will activate
when the ORP reaches or falls below this setting.
You may disable this alarm by holding down the
+/- key for 1 second.
Alarm Hysteresis (Mgr): This value sets the
amount that the ORP reading has to rise above the
high alarm or fall below the low alarm before the
alarm will shut off.

Page 7
9487 Dielman Rock Island Ind Dr, St. Louis, MO 63132 www.becs.com
Operation and Maintenance Manual
Rev:
L13
A – 4.3: Cl Inputs Setup
A – 4.3.1: Free Cl Setup
If your controller is configured to monitor Free
Cl, it may be either calculated or a probe may be
attached.
A – 4.3.1.1: Input Source: Calculated
High Alarm (Op): The high alarm will
activate when the free Cl reaches or rises
above this setting. You may disable this
alarm by holding down the +/- key for 1
second.
Low Alarm (Op): The low alarm will
activate when the free Cl reaches or falls
below this setting. You may disable this
alarm by holding down the +/- key for 1
second.
Alarm Hysteresis (Mgr): This value sets
the amount that the Cl input readings have
to rise above their high alarm or fall below
their low alarm before the alarm will shut
off.
A – 4.3.1.2: Input Source: Probe
High Alarm (Op): The high alarm will
activate when the free Cl reaches or rises
above this setting. You may disable this
alarm by holding down the +/- key for 1
second.
Low Alarm (Op): The low alarm will
activate when the free Cl reaches or falls
below this setting. You may disable this
alarm by holding down the +/- key for 1
second.
Alarm Hysteresis (Mgr): This value sets
the amount that the Cl input readings have
to rise above their high alarm or fall below
their low alarm before the alarm will shut
off. Note this value is used for free, total,
and combined Cl alarms.
Calibrate (Op): This selection allows you
to do a single point calibration of free Cl,
enter the reading from you test kit, and press
enter. The value entered must be 0.5 ppm
or greater.
Reset Calibration (Op): Resets the
calibration to the original factory setting.
A – 4.3.2: Total Cl Setup
If your controller is configured to monitor Total
Cl, you will have the following options:
High Alarm (Op): The high alarm will activate
when the total Cl reaches or rises above this
setting. You may disable this alarm by holding
down the +/- key for 1 second.
Low Alarm (Op): The low alarm will activate
when the total Cl reaches or falls below this
setting. You may disable this alarm by holding
down the +/- key for 1 second.
Alarm Hysteresis (Mgr): This value sets the
amount that the Cl input readings have to rise
above their high alarm or fall below their low
alarm before the alarm will shut off. Note this
value is used for free, total, and combined Cl
alarms.
A – 4.3.3: Combined Cl
If your controller is configured to monitor
Combined Cl, you will have the following
options:
High Alarm (Op): The high alarm will
activate when the combined Cl reaches or rises
above this setting. You may disable this alarm
by holding down the +/- key for 1 second.
Alarm Hysteresis (Mgr): This value sets the
amount that the Cl input readings have to rise
above their high alarm or fall below their low
alarm before the alarm will shut off. Note this
value is used for free, total, and combined Cl
alarms.
A – 4.4: Temperature Setup
If your controller is configured to monitor
temperature, you will have the following options:
High Alarm (Op): The high alarm will activate
when the temperature reaches or rises above this
setting. You may disable this alarm by holding
down the +/- key for 1 second.
Low Alarm (Op): The low alarm will activate
when the temperature reaches or falls below this
setting. You may disable this alarm by holding
down the +/- key for 1 second.
Alarm Hysteresis (Mgr): This value sets the
amount that the temperature reading has to rise
above the high alarm or fall below the low alarm
before the alarm will shut off.
Caution: Amperometric chlorine sensors
require the use of a temperature sensor and
a properly calibrated pH sensor. Refer to
the instruction pamphlet included with the
sensor at the time of installation.

Page 8
www.becs.com 9487 Dielman Rock Island Ind Dr, St. Louis, MO 63132
Operation and
Maintenance Manual
Rev:
L13
A – 4.5: Conductivity/TDS Setup
If your controller is configured to monitor
Conductivity/TDS, you will have the following
options:
High Alarm (Op): The high alarm will activate
when the input reaches or rises above this setting.
You may disable this alarm by holding down the
+/- key for 1 second.
Low Alarm (Op): The low alarm will activate
when the input reaches or falls below this setting.
You may disable this alarm by holding down the
+/- key for 1 second.
Alarm Hysteresis (Mgr): This value sets the
amount that the Conductivity/TDS reading has to
rise above the high alarm or fall below the low
alarm before the alarm will shut off.
A – 4.6: Flow Rate Setup
If your controller is configured to monitor Flow
Rate, you will have the following options:
Low Alarm (Op): The low alarm will activate
when the flow rate reaches or falls below this
setting. You may disable this alarm by holding
down the +/- key for 1 second.
Alarm Hysteresis (Mgr): This value sets the
reading that the flow rate must rise above the low
alarm before the alarm will shut off.
A – 4.7: pH & Chlorine Inventory Setups
If your controller is configured to monitor
chemical inventories, a sensor may be used or a
contact switch. If a sensor is used, you will have
the following options:
Low Alarm (Op): This value sets at what level or
weight the inventory low alarm will be activated.
You may disable this alarm by holding down the
+/- key for 1 second.
Alarm Hysteresis (Mgr): This value sets at what
level the inventory level or weight has to rise
above the low level or weight alarm setting before
the alarm will shut off.
A – 4.8: Turbidity
If your controller is configured to monitor
Turbidity, you will have the following options:
High Alarm (Op): The high alarm will activate
when the input reaches or rises above this setting.
You may disable this alarm by holding down the
+/- key for 1 second.
Alarm Hysteresis (Mgr): This value sets the
level that the turbidity reading has to rise above
the high alarm setting before the alarm will shut
off.
A – 4.9: Surge Pit Level
If your controller is configured to monitor the
Surge Pit Level, a sensor may be used or a contact
switch. If a sensor is used, you will have the
following options:
High Alarm (Op): The high alarm will
activate when the input reaches or rises above
this setting. You may disable this alarm by
holding down the +/- key for 1 second.
Low Alarm (Op): The low alarm will activate
when the input reaches or falls below this
setting. You may disable this alarm by holding
down the +/- key for 1 second.
Alarm Hysteresis (Mgr): This value sets the
amount that the surge pit level has to rise above
the high alarm or fall below the low alarm
before the alarm will shut off.
A – 4.10: Pressure & Vacuum Setup
A – 4.10.1: Filter Influent Pressure
If your controller is configured to monitor the
Filter Influent Pressure, either a PSI transducer,
Vacuum transducer, or a gauge may be used. If
a transducer is used, you will have the following
options:
High Alarm (Op): The high alarm will activate
when the pressure reaches or rises above this
setting. You may disable this alarm by holding
down the +/- key for 1 second.
Low Alarm (Op): The low alarm will activate
when the pressure falls below this setting. You
may disable this alarm by holding down the +/-
key for 1 second.
Alarm Hysteresis: (Mgr) This value sets the
amount that the pressure reading has to rise
above the high alarm or fall below the low
alarm before the alarm will shut off.
Display Input (Op): This option
enables/disables displaying the influent pressure
on the normal display.
A – 4.10.2: Filter Effluent Pressure
If your controller is configured to monitor the
Filter Effluent Pressure, either a PSI transducer,
or a pressure gauge may be used. If a transducer
is used, you will have the following options:
High Alarm (Op): The high alarm will
activate when the pressure reaches or rises
above this setting. You may disable this alarm
by holding down the +/- key for 1 second.
Low Alarm (Op): The low alarm will activate
when the pressure reaches or falls below this
setting. You may disable this alarm by holding
down the +/- key for 1 second.

Page 9
9487 Dielman Rock Island Ind Dr, St. Louis, MO 63132 www.becs.com
Operation and Maintenance Manual
Rev:
L13
Alarm Hysteresis (Mgr): This value sets the
amount that the pressure reading has to rise
above the high alarm or fall below the low
alarm before the alarm will shut off.
Display Input (Op): This option
enables/disables displaying the Filter Effluent
pressure on the normal display.
A – 4.10.3: Filter Differential Pressure
If your controller is configured to monitor the
Filter Differential Pressure, you will have the
following options:
High Alarm (Op): The high alarm will
activate when the pressure reaches or rises
above this setting. You may disable this alarm
by holding down the +/- key for 1 second.
Alarm Hysteresis (Mgr): This value sets the
amount that the pressure reading has to rise
above the high alarm before the alarm will shut
off.
A – 4.10.4: Pump Effluent Pressure
If your controller is configured to monitor the
Pump Effluent Pressure, you will have the
following options:
High Alarm (Op): The high alarm will
activate when the pressure reaches or rises
above this setting. You may disable this alarm
by holding down the +/- key for 1 second.
Low Alarm (Op): The low alarm will activate
when the pressure reaches or falls below this
setting. You may disable this alarm by holding
down the +/- key for 1 second.
Alarm Hysteresis (Mgr): This value sets the
amount that the pressure reading has to rise
above the high alarm or fall below the low
alarm before the alarm will shut off.
Display Input (Op): This option
enables/disables displaying the Pump Effluent
pressure on the normal display.
A – 4.10.5: Strainer Vacuum
If your controller is configured to monitor the
Strainer Vacuum, either a transducer or a gauge
may be used. If a transducer is used, you will
have the following options:
High Vac Alarm (Op): The high vacuum
alarm will activate when the pressure reaches or
falls below this setting. This is actually a low
pressure alarm that operates in the negative
pressure range, which is a vacuum. You may
disable this alarm by holding down the +/- key
for 1 second.
If the recirc pump is assigned a relay, the
high strainer vacuum alarm will trigger an
emergency off of the system.
High Vac Warning (Op): The high vacuum
warning will activate when the pressure reaches
or falls below this setting. This is actually a low
pressure alarm that operates in the negative
pressure range, which is a vacuum. You may
disable this alarm by holding down the +/- key
for 1 second.
The high strainer vacuum warning is
generally used to indicate to the operators
that the strainer needs cleaned. While this
warning does flash the alarm LED, it does
not shut down any pumps or feeds.
Alarm Hysteresis (Mgr): This value sets the
level that the pressure reading must rise above
the alarm settings before the alarm will shut off.
A – 4.10.6: Total Dynamic Head
If your controller is configured to monitor the
Total Dynamic Head, you will have the
following options:
Display TDH (Op): Enables displaying total
dynamic head on the normal display.
High Alarm (Op): The high alarm will
activate when the total dynamic head across the
pump reaches or rises above this setting. You
may disable this alarm by holding down the +/-
key for 1 second.
Low Alarm (Op): The low alarm will activate
when the total dynamic head across the pump
reaches or falls below this setting. You may
disable this alarm by holding down the +/- key
for 1 second.
Alarm Hysteresis (Mgr): This value sets the
amount that the total dynamic head has to rise
above the high alarm or fall below the low
alarm before the alarm will shut off.

Page 10
www.becs.com 9487 Dielman Rock Island Ind Dr, St. Louis, MO 63132
Operation and
Maintenance Manual
Rev:
L13
A – 5: Control Outputs
Press the Menu button on the front of the Controller
and select Control Outputs. Depending on the
controller configuration, some control outputs may
or may not be installed.
A – 5.1: pH Control
If your controller is configured to control pH, you
will have the following options:
Control Type (Op): Choose from On/Off or
Time Base Proportional control.
In general, if you are using a motor driven
chemical feeder then you should choose the
On/Off option. If you are using a solenoid
driven or pulsed diaphragm chemical feeder
(such as Pulsatron, most LMI models or most
Prominent Models), you should choose the
TBP option. This feature helps to hold a set
point and to minimize over-shoot by making a
standard feeder mimic the action of more
sophisticated modulating feeders.
If you choose the On/Off option and are
feeding up, then the controller will activate
the chemical feeder whenever the pH falls
below the set point and continue to feed until
the pH rises above the set point plus
hysteresis at which point it will stop.
If you choose the TBP option and are feeding
up then the controller will activate the
chemical feeder whenever the pH falls below
the set point and will feed for a percentage of
the Time Base (default one minute)
proportional to the offset from set point. For
the remainder of the Time Base the feeder will
be paused. The feeder will continue this feed
and pause cycle until the controller achieves
the set point plus hysteresis. The closer to set
point, the less time the feeder is ON.
Set Point (Op): This value sets the desired level
to maintain the pH at. Input the desired pH set
point.
Span/Prop. Bnd (Op): This option is only shown if
the Control Type is Time Base Proportional. This value
sets the distance (or span) from the set point that
the output will be proportionally controlled.
Time Base (Op): This option is only shown if the
Control Type is Time Base Proportional. This sets the
total time that control is based on. During this
time, the feeder will turn on for a percentage of
the Time Base and turn off for the remainder.
Failsafe Timer (Op): This value sets the time
that the relay is allowed to stay continuously on.
The most common failures of automated
chemical feed systems are depletion of the
chemical supply and/or chemical feeder
failure. Both problems result in the controller
being unable to reach set point in a reasonable
period of time. The failsafe timer sets the
maximum length of time the feeder can run.
If the feeder has been trying to achieve set
point without success for the selected time,
the controller will cut power to the feeder,
flash the Reset Fail/Safe LED on the face
panel and display a message to alert the
operator. If in TBP Pause mode, the
controller will reset the timer.
An operator must reset the failsafe through
the Reset Fail/Safe button to re-enable
normal control.
Dead Band (Mgr): This option is only shown under
dual pH control. This value sets the amount the
input must exceed the set point by before the feed
of the opposite direction will trigger. (The range is
from twice the feeds' hysteresis to 2.8 pH)
Warning: Disabling the failsafe timers is
highly discouraged. They are an important
safety feature to protect against dangerous
chemical overfeeds and will protect the
equipment from running continuously if it runs
out of chemical.
Warning: Increasing or decreasing the
Span/Prop. band or Time Base may cause the feed
to severely overshoot or never achieve set point.
Adjust this option only when recommended to do
so by a factory representative.
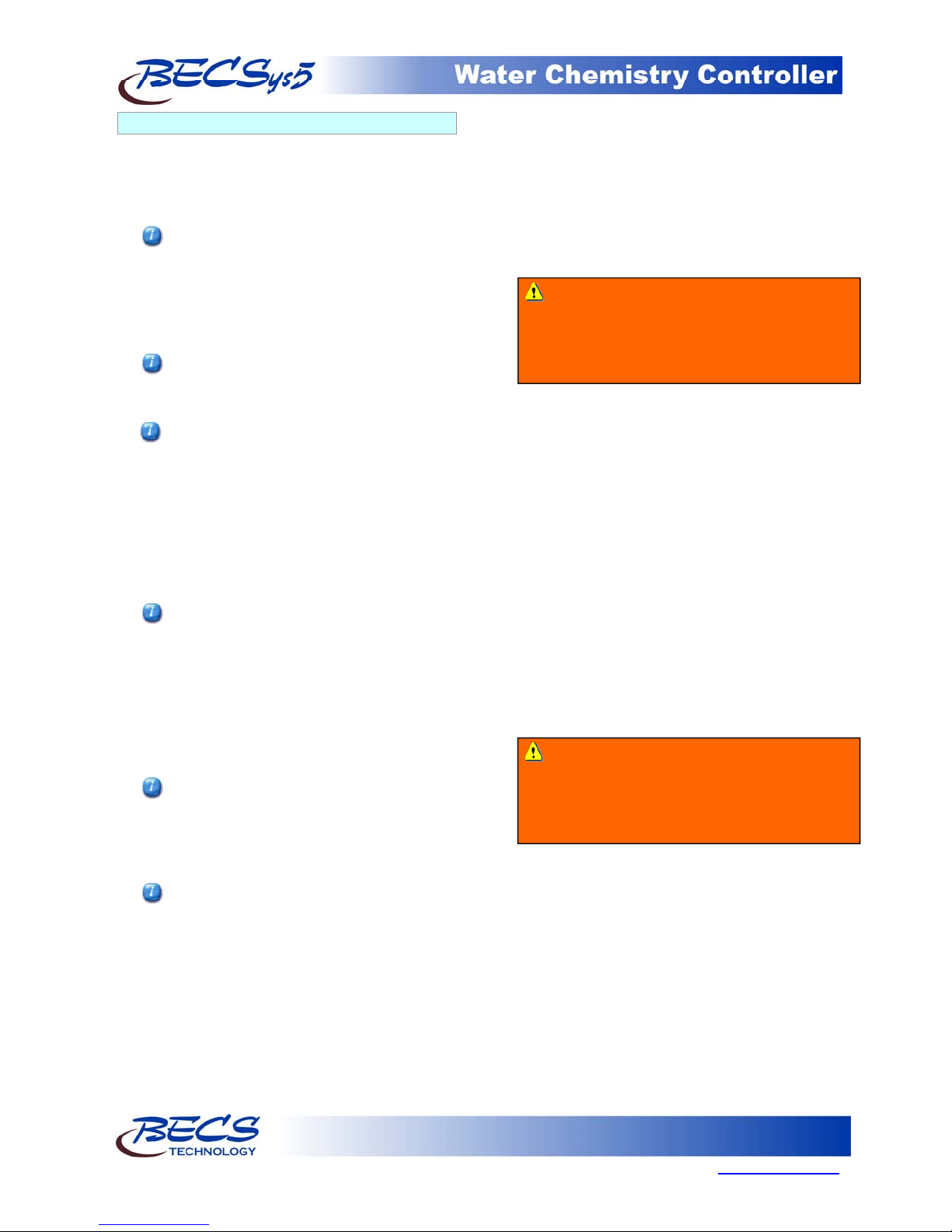
Page 11
9487 Dielman Rock Island Ind Dr, St. Louis, MO 63132 www.becs.com
Operation and Maintenance Manual
Rev:
L13
A – 5.2: Chlorine Control
After entering the Control Outputs option, select
the Cl Control from the menu. This will allow the
programming of the following:
Sanitizer Chemical (Op): Sets the sanitizer
chemical name (Chlorine or Bromine).
This option controls what chemical name the
controller displays for the Cl inputs and the
primary sanitization/oxidizing chemical.
Control Input Src (Op): This option is only available
if the free Cl Input source is set to Calculated or Probe.
Choose between ORP and free Cl to use as the
primary control input for the sanitizer feed.
If the free Cl Input is selected and the free Cl
Input source is set to probe, ORP is still used
for control while the free Cl interlock timer is
running.
If the free Cl Input is selected and the free Cl
Input source is set to calculated, the controller
still controls off of ORP, but the ORP set
point is calculated by the controller based on
the free Cl set point, the pH set point, and the
free Cl calibration. Modification of any one
of those three values will result in a new ORP
set point.
Control Type (Op): Choose from On/Off or
Time Base Proportional control.
In general, if you are using a motor driven
chemical feeder then you should choose the
On/Off option. If you are using a solenoid
driven or pulsed diaphragm chemical feeder
(such as Pulsatron, most LMI models or most
Prominent Models), you should choose the
TBP option. This feature helps to hold a set
point and to minimize over-shoot by making a
standard feeder mimic the action of more
sophisticated modulating feeders.
If you choose the On/Off option, then the
controller will activate the chemical feeder
whenever the ORP falls below the set point
and continue to feed until the ORP rises
above the set point plus hysteresis at which
point it will stop.
If you choose the TBP option, then the
controller will activate the chemical feeder
whenever the ORP falls below the set point
and will feed for a percentage of the Time
Base (default one minute) proportional to the
offset from set point. For the remainder of
the Time Base the feeder will be paused. The
feeder will continue this feed and pause cycle
until the controller achieves the set point plus
hysteresis. The closer to set point, the less
time the feeder is ON.
ORP Set Point (Op): This option is NOT shown if
the Control Source is set to free Cl and the free Cl Input
source is set to Calculated. This value sets the desired
level to maintain the ORP at.
ORP Span/Prop. Bnd (Op): This option is only
shown if the Control Type is Time Base Proportional and
the ORP Set Point is shown above. This value sets the
distance (or span) from the set point that the
output will be proportionally controlled.
Free Cl Span/Prop Bnd (Op): This option is only
shown if the Control Type is Time Base Proportional, the
Control Source is set to free Cl, and the free Cl Input source
is set to probe. This value sets the distance (or span)
from the set point that the output will be
proportionally controlled.
Free Cl Set Point (Op): This option is only shown if
the Control Source is set to free Cl. This value sets the
desired level to maintain the free Cl at.
Free Cl Ctrl Hyst (Rep): This option is only shown if
the Control Source is set to free Cl and the free Cl Input
source is set to probe. This value sets the amount the
input must rise above set point before the feed will
shut off.
Time Base (Op): This option is only shown if the
Control Type is Time Base Proportional. This sets the
total time that control is based on. During this
time, the feeder will turn on for a percentage of
the Time Base and turn off for the remainder.
Warning: Increasing or decreasing the time
base may cause the feed to severely overshoot
or never achieve set point. Adjust this option
only when recommended to do so by a factory
representative.
Warning: Increasing or decreasing the
proportional band may cause the feed to
severely overshoot or never achieve set point.
Adjust this option only when recommended to
do so by a factory representative.

Page 12
www.becs.com 9487 Dielman Rock Island Ind Dr, St. Louis, MO 63132
Operation and
Maintenance Manual
Rev:
L13
A – 5.2: Chlorine Control (continued)
Failsafe Timer (Op): This value sets the time
that the relay is allowed to stay continuously on.
The most common failures of automated
chemical feed systems are depletion of the
chemical supply and/or chemical feeder
failure. Both problems result in the controller
being unable to reach set point in a reasonable
period of time. The failsafe timer sets the
maximum length of time the feeder can run.
If the feeder has been trying to achieve set
point without success for the selected time,
the controller will cut power to the feeder,
flash the Reset Fail/Safe LED on the face
panel and display a message to alert the
operator. If in TBP Pause mode, the
controller will reset the timer.
An operator must reset the failsafe through
the Reset Fail/safe button to re-enable normal
control.
Alt Set Point (Op): The 4 Event 28 Day Timer
allows you to program a schedule to define when
to use alternate set point.
Alt Set Point 4 Event 28 Day Timer: To
program the 4 Event 28 Day Timer, perform
the following:
Select the Alt. Set point from the Cl (Br)
Control menu.
Now select the 4Event 28Day Timer from the
Alt. Set Point menu.
Selecting Event1 will allow you to select the
weekly interval to use the alternate set point.
If the 1st, 2nd, 3rd, or 4th week is selected,
the timer will only trigger on that week in the
four-week cycle. The Odd Weeks selection
will trigger on the 1st and 3rd weeks, the
Even Weeks selection will trigger on the 2nd
and 4th weeks, and the Every Week selection
triggers every week.
The week number and day of week for the
current date is displayed on the bottom
right side of these screens.
The first week is fixed to be the week of
Sunday, January 2
nd
, 2000 and every four
weeks afterwards.
The next set of screens will allow you to
choose the actual day(s).
Select what day of the week, or every day, the
alternate set point should be used.
Once you make your selection you will be
returned to the 4Event 28Day Timer menu
where you will have a new menu item: Event
1 Times.
Select the Event1 Times from the 4Event
28Day Timer menu.
This screen allows you to set both the start
time and the end time for the event's
programmed weeks/days. To toggle
AM/PM, press the +/- key while the cursor is
on the time you wish to change.
If your start time is before midnight (12:00
AM) and the end time is after midnight, the
alternate set point will continue to be used
the following day up to the end time even if
that day did not fall within the week/day
selection for that event.
Example:
Event1 Week/Day: Odd weeks/ Tuesday
Event1 Times: 11:00 PM to 3:00 AM
Event2 Week/Day: Even weeks/ Monday
Event2 Times: 11:00 PM to 6:00 AM
Current Week/Day: 2nd/Tuesday
Current Time: 4:00 PM
The alternate set point last ran from 11:00 PM
last night to 6:00AM this morning.
The next time the alternate set point will run will
be from 11:00 PM next Tuesday to
3:00AM next Wednesday.
ORP Set Point (Op): This value sets the
desired level to maintain the ORP at during any
of the programmed alternate set point events.
Free Cl Set Point (Op): This option is only
available if the free Cl probe is installed and the
Control Source is set to free Cl. This value sets the
desired level to maintain the free Cl at during
any of the programmed alternate set point
events.
Bracketed Free Cl (Op): This option is only
available if the free Cl probe is installed and the Control
Source is set to ORP. If enabled, the controller will
override the ORP control so that the free Cl will
not drop out of a programmed range.
Bracketed ORP (Op): This option is only available if
the free Cl probe is installed and the Control Source is set to
free Cl. If enabled, the controller will override the
free Cl control so that the ORP will not drop out
of a programmed range.
Warning: Disabling the failsafe timers is
highly discouraged. They are an important
safety feature to protect against dangerous
chemical overfeeds and will protect the
equipment from running continuously if it runs
out of chemical.

Page 13
9487 Dielman Rock Island Ind Dr, St. Louis, MO 63132 www.becs.com
Operation and Maintenance Manual
Rev:
L13
A – 5.3: Chlorine Booster Control
If your controller is configured to control a
Chlorine Booster pump, you will have the
following options:
Control Input (Op): This option is only available if
the free Cl Input is enabled. Choose between ORP,
free Cl or, if the free Cl probe is used, both to
control the chlorine booster.
ORP Trigger Point (Op): This option is only shown
if the Control Input is ORP or Both. This value sets
the ORP level that the input must drop below to
activate the chlorine booster control. (the range is
–1000 mV to the Cl Booster's ORP Set Point)
Free Cl Trigger Point (Op): This option is only
shown if the Control Input is free Cl or Both. This value
sets the free Cl level that the input must drop
below to activate the chlorine booster control. (the
range is from 0.0 free Cl to the Cl Booster's free Cl
Set Point)
ORP Set Point (Op): This option is only shown if the
Control Input is ORP or Both. This value sets the
ORP level that once it is reached the chlorine
booster control will shut off. (the range is from Cl
Booster's ORP Trigger Point to the ORP high
alarm point)
Free Cl Set Point (Op): This option is only shown if
the Control Input is free Cl or Both. This value sets the
free Cl level that once it is reached the chlorine
booster control will shut off. (the range is from the
Cl Booster's free Cl Trigger Point to the free Cl
high alarm point)
Failsafe Timer (Op): This value sets the time
that the relay is allowed to stay continuously on.
The most common failures of automated
chemical feed systems are depletion of the
chemical supply and/or chemical feeder
failure. Both problems result in the controller
being unable to reach set point in a reasonable
period of time. The failsafe timer sets the
maximum length of time the feeder can run.
If the feeder has been trying to achieve set
point without success for the selected time,
the controller will cut power to the feeder,
flash the Reset Fail/Safe LED on the face
panel and display a message to alert the
operator. If in TBP Pause mode, the
controller will reset the timer.
An operator must reset the failsafe through
the Reset Fail/Safe button to re-enable
normal control.
A – 5.4: Super Chlorination
If your controller is configured for Super
Chlorination, you will have the following options:
Control Input (Op): This option is only available if
the free Cl probe is installed. Choose between free Cl
and ORP to use to control the Super Chlorination
feed.
4 Event 28 Day Timer (Op): To program when
the super chlorination should trigger, select 4Event
28Day Timer from the Super Chlorination menu:
Selecting Event1 will allow you to select the
weekly interval to trigger the Super
Chlorination. If the 1st, 2nd, 3rd, or 4th week
is selected, the timer will only trigger on that
week in the four-week cycle. The Odd Weeks
selection will trigger on the 1st and 3rd weeks,
the Even Weeks selection will trigger on the
2nd and 4th weeks, and the Every Week
selection triggers every week.
The week number and day of week for the
current date is displayed on the bottom
right side of these screens.
The first week is fixed to be the week of
Sunday, January 2
nd
, 2000 and every four
weeks afterwards.
Next you can select the day of the week (or
every day) the event should be triggered on.
Once you make your selection, you will be
returned to the 4Event 28Day Timer menu where
you will have a new menu item: Event 1 Start
Time.
Select the Event1 Start Time from the 4Event
28Day Timer menu.
This screen allows you to set the time to trigger
the event on the programmed weeks/days. The
event will trigger at the start time if the
controller is running at that time. To toggle
AM/PM, press the +/- key. Enter the desired
time and press enter.
After setting the time, press the left arrow to
return to Super Chlorination's main menu. Here
you will notice the next scheduled super
chlorination is displayed for you. The controller
will also list the last super chlorination here once
one has been completed.
Warning: Disabling the failsafe timers is
highly discouraged. They are an important
safety feature to protect against dangerous
chemical overfeeds and will protect the
equipment from running continuously if it
runs out of chemical.

Page 14
www.becs.com 9487 Dielman Rock Island Ind Dr, St. Louis, MO 63132
Operation and
Maintenance Manual
Rev:
L13
A – 5.4: Super Chlorination (continued)
Maximum Time On (Op): This value sets the
maximum time you want the Super Chlorination
on to reach the set point. If the time expires
before set point is reached, the controller will
trigger the SuperChlor failsafe alarm and end the
SuperChlor feeds. (the range is from 0:00 to
18:00 hours)
An operator can reset the failsafe through the
Reset Fail/Safe button; however the failsafe
alarm will automatically clear itself when the
regular Cl feed begins feeding.
ORP Set Point (Op): This option is only shown if the
Control Input is set to ORP. This value sets the
desired ORP level to shock the pool.
Free Cl Set Point (Op): This option is only shown if
the Control Input is set to free Cl. This value sets the
desired free Cl level to shock the pool.
A – 5.5: Dechlorination
If your controller is configured for Dechlorination,
you will have the following options:
Control Input (Op): This option is only available if
the free Cl probe is installed. Choose between free Cl
and ORP to use to control the dechlor feed.
Follow Super Chlorination (Op): Choose
whether or not you want your dechlorination to
automatically follow your super chlorination.
4 Event 28 Day Timer (Op): The 4 Event 28
Day Timer allows you to program the
dechlorination on a schedule. See the section on
Super Chlorination's 4 Event 28 Day Timer for
details on how to set this.
Maximum Time On (Op): This value sets the
maximum time you want the dechlorination on to
reach the set point. (the range is from 0:00 to
18:00 hours)
ORP Set Point (Op): This option is only shown if the
Control Input is set to ORP. This value sets the
desired final ORP level.
Free Cl Set Point (Op): This option is only shown if
the Control Input is set to free Cl. This value sets the
desired final free Cl level.
A – 5.6: Ozone Control
If your controller is configured for Ozone Control,
you will have the following options:
Control Input (Op): This option is only available if
the free Cl probe is installed. Choose between free Cl,
ORP, or both to use to control the Ozone feed.
ORP Set Point (Op): This option is only shown if the
Control Input is ORP or Both. This value sets the
ORP level that the input must drop below to
activate the Ozone.
Free Cl Set Point (Op): This option is only shown if
the Control Input is free Cl or Both. This value sets the
free Cl level that the input must drop below to
activate the Ozone.
Fireman Switch (Op): This option is only shown if a
relay is assigned to the recirculation pump or backwash.
This value sets the minimum amount of time to
leave the recirculation pump on or delay the start
of backwash after the Ozone relay shuts off.
Failsafe Timer (Op): This value sets the time
that the relay is allowed to stay continuously on.
A – 5.7: Heater
If your controller is configured for Heater Control,
you will have the following options:
Temp. Ctrl Enable (Op): Enables or disables
controlling the Heater using the Temperature
Input.
Set Point (Op): Only shown if Temp. Ctrl is enabled.
This value sets the desired temperature. (the
range is from the temperature low alarm to the
temperature high alarm)
Failsafe Timer (Op): Only shown if Temp. Ctrl is
enabled. This value sets the time that the relay is
allowed to stay on without reaching set point
before the relay is locked out. If the heater has
been trying to achieve set point without success
for the selected time, the controller will cut power
to the heater, flash the Reset Fail/Safe LED on
the face panel and display a message to alert the
operator.
An operator must reset the failsafe through
the Reset Fail/safe button to re-enable normal
control.
Fireman Switch (Op): This option is only shown if a
relay is assigned to the recirculation pump or backwash.
This value sets the minimum amount of time to
leave the recirculation pump on or delay the start
of backwash after the heater relay shuts off.
Alternate Temperature (Op): Only shown if Temp.
Ctrl is enabled. The 4 Event 28 Day Timer allows
you to program an alternate set point on a
schedule. See the Chlorine (Bromine) Control's
Alt Set Point for details on how to set this.
After the schedule is set, you may choose the
alternate temperature set point option and enter
the desired setting.

Page 15
9487 Dielman Rock Island Ind Dr, St. Louis, MO 63132 www.becs.com
Operation and Maintenance Manual
Rev:
L13
A – 5.8: Autofill
If your controller is set up to control an Autofill
valve, it can be triggered by the Surge Pit Level (if
monitored) or a proximity switch.
Set Point (Op): Only shown if Autofill sensor type is
set to Surge Pit Level. This value sets the surge pit
level that the controller will fill to.
Alternate Set Point (Op): Only shown if Autofill
sensor type is set to Surge Pit Level. To program when
to use the alternate set point, see the section on
Chlorine (Bromine) Control’s Alternate Set point
Timer Settings. After the schedule is set, you may
choose the alternate set point option and enter the
desired setting.
Start Delay (Op): Sets the time required for the
water level to stay below the trigger point before
fill begins.
End Delay (Op): Sets the time required for the
water level to remain above shutoff point before
ending the fill.
Failsafe Timer (Op): This value sets the time
that the relay is allowed to stay on without
reaching set point before the relay is locked out. If
Autofill has been trying to achieve set point
without success for the selected time, the
controller will cut power to the relay, flash the
Reset Fail/Safe LED on the face panel and display
a message to alert the operator.
An operator must reset the failsafe through
the Reset Fail/safe button to re-enable normal
control.
A – 5.9: TDS Control
If your controller is set up to monitor the TDS of
the water, you will have the following options:
Makeup water TDS (Op): Enter the test kit
TDS reading for the water controlled by your
Autofill. This is used to determine the appropriate
TDS set point.
Pool TDS cycle (Op): Enter the pools' cycle
multiplier of the incoming makeup water. The
resulting TDS set point is the incoming makeup
water's TDS times this value.
Failsafe Timer (Op): This value sets the time
that the relay is allowed to stay on without
reaching set point before the relay is locked out. If
the TDS control has been trying to achieve set
point without success for the selected time, the
controller will cut power to the relay, flash the
Reset Fail/Safe LED on the face panel and display
a message to alert the operator.
An operator must reset the failsafe through
the Reset Fail/safe button to re-enable normal
control.
A – 5.10: Sensor Wash
If your controller is set up to do a Sensor Wash
you will have the following options:
4 Event 28 Day Timer (Op): Once you have
entered Sensor Wash, select 4Event 28Day Timer
from the menu. The 4 Event 28 Day Timer allows
you to program the sensor wash on a schedule. See
the section on Super Chlorination's 4 Event 28
Day Timer for details on how to set this.
Start/End Time (Op): Allows you to set
what times the feed may be triggered during a
day.
# Of Cycles (Op): Only shown if Duration is not
zero. Sets how many times the relay will trigger
between the Start and End times.
Duration (Op): Sets how long the feed will run
for each cycle. If set to zero, there are no cycles
and the relay will simply be on when current time
is between the active event's start and end times.
A – 5.11: Enzyme
If your controller is configured to control an
Enzyme feed, you will have the following options:
Start/End Time (Op): Allows you to set what
times the feed may be triggered during a day.
# Of Cycles (Op): Only shown if Duration is not
zero. Sets how many times the relay will trigger
between the Start and End times.
Duration (Op): Sets how long the feed will run
for each cycle. If set to zero, there are no cycles
and the relay will simply be on when current time
is between the start and end times.
A – 5.12: UV Turndown
If your controller is configured to control a UV
unit, you will have the following options:
Combined Cl Set Point (Op): This option is only
shown if both the free Cl and total Cl probes are installed.
This value sets the Combined Cl level that the
input must be equal to or drop below to activate
the turndown.
Start Delay (Op): This option is only shown if both the
free Cl and total Cl probes are installed. Time the
combined free Cl must remain at or below set
point before activating turndown.
Fireman Switch (Op): This option is only shown if a
relay is assigned to the recirculation pump or backwash.
This value sets the minimum amount of time to
leave the recirculation pump on or delay the start
of backwash after the UV turndown relay turns on.

Page 16
www.becs.com 9487 Dielman Rock Island Ind Dr, St. Louis, MO 63132
Operation and
Maintenance Manual
Rev:
L13
A – 5.13: Polymer
If your controller is configured to control a
Polymer feed, you will have the following options:
High Set Point (Op): Only shown if control type is
set to Turbidity Control. When the turbidity reading
rises above this value for the Trigger Delay Time,
the controller will trigger the polymer control
cycle.
Low Set Point (Op): Only shown if control type is set
to Turbidity Control. At the end of each control
cycle, the controller checks to see if the turbidity
reading is below this value. If it is, the control
cycle ends, otherwise the controller starts a new
control cycle.
Cycle Time (Op): Only shown if control type is set to
Turbidity Control. This value sets the control cycle
duration. At the beginning of each cycle, the relay
turns on, stays on for the programmed On Time,
then shuts off for the remainder of the cycle time.
On Time (Op): Only shown if control type is set to
Turbidity Control. This value sets how long the
controller will feed polymer during each control
cycle.
Trigger Delay Time (Op): Only shown if control
type is set to Turbidity Control. This value sets how
long the turbidity reading must remain above the
high set point before triggering the polymer
control cycle.
Start/End Time (Op): Only shown if control type is
set to Cycle Timer. Allows you to set what times the
feed may be triggered during a day.
# Of Cycles (Op): Only shown if control type is set to
Cycle Timer. Sets how many times the feed will be
triggered between the Start and End times.
Duration (Op): Only shown if control type is set to
Cycle Timer. Sets how long the feed will run for
each cycle.
A – 5.14: Recirculation Pump
If your controller is configured to control the
Recirculation Pump, you will have the following
options:
Pres. Alarm Delay (Op): Delay pressure and
vacuum alarms from triggering for this amount of
time whenever the recirc pump starts up.
Heater Fireman Switch (Op): This option is only
shown if a relay is assigned to the Heater control. This
value sets the minimum amount of time to leave
the recirculation pump on or delay the start of
backwash after the heater shuts off.
Ozone Fireman Switch (Op): This option is only
shown if a relay is assigned to the Ozone control. This
value sets the minimum amount of time to leave
the recirculation pump on or delay the start of
backwash after the Ozone relay shuts off.
UV Turndown Fireman Switch (Op): This
option is only shown if a relay is assigned to the UV
Turndown. This value sets the minimum amount of
time to leave the recirculation pump on or delay
the start of backwash after the UV turndown relay
turns on.
A – 5.9.1: VFD Control:
Allows you to configure the VFD control settings
for the Recirculation Pump. Once you have
selected VFD Control you will have the following
items to choose from:
OOR alarm delay (Op): This option is only
shown if the Control Input is set to Flow Meter. If the
output required to meet the set point exceeds
100%, the triggering of the Out Of Range
(OOR) alarm will be delayed by this amount of
time. Set to 0 to disable the alarm.
Set Point (Op): Allows you to set the value to
control to. (in % or flow rate depending on
what the control input is set to).
Dead Band (View Only): This option is only
shown if the Control Input is set to Flow Rate. The
VFD output will not change until the input is
this far away from the set point.
Backwash Output (View Only): This option is
only shown if the backwash control is configured. Sets
the VFD percent output to use when
backwashing.
Minimum Output (View Only): The
controller will always keep the VFD output
above this % except when the relay is off.
A – 5.15: Alarm Relay
There are no programmable options for the Alarm
Relay. Whenever there is an alarm or Emergency
Off is active, this relay will turn on.
Table of contents
Other BECS Controllers manuals