Bennett Site Master SP User manual

126305 Rev B 05/22/15
For new books, FAX to:
BENNETT MARKETING SERVICES
(231)799-6202
Or visit our web page at:
http://www.b nn ttpump.com
Site Master SP
Product Manual
B nn tt 1218 E. Pontaluna Road Spring Lak , MI 49456
USA 800-235-7618 Outsid USA 231-798-1310 sal s@b nn ttpump.com
www bennettpump com
READ THIS BOOK
This book has important information for safe installation
and operation of this equipment Read and understand
this book before applying power Keep this book and
tell all service personnel to read this book If these
instructions are not followed, bodily injury, death, or
damage to the equipment may occur

2126305 Rev B 05/22/15
Tabl of Cont nts
Saf ty Instructions ................................................................................................................................. 3
Introduction............................................................................................................................................. 4
Powering up the Module .................................................................................................................... 4
Idle Screen ......................................................................................................................................... 4
Installation............................................................................................................................................... 5
Power Requirements ......................................................................................................................... 5
Connector Descriptions...................................................................................................................... 5
Communication .................................................................................................................................. 6
Field Wiring ........................................................................................................................................ 6
Footprint ............................................................................................................................................. 6
Diagram.............................................................................................................................................. 7
Programming .......................................................................................................................................... 8
Using the Pin pad............................................................................................................................... 8
Gaining Access to Programming ....................................................................................................... 8
Programming Modes.......................................................................................................................... 9
Manager’s Mode 01 (Address)........................................................................................................... 9
Manager’s Mode 12 (Receipt Length) ............................................................................................... 10
Manager’s Mode 13 (Keypad Type) .................................................................................................. 10
Manager’s Mode 14 (Receipt Delay) ................................................................................................. 11
Manager’s Mode 94 (Line Shift)......................................................................................................... 12
Manager’s Mode 99 (Logos) .............................................................................................................. 12
S rvic ..................................................................................................................................................... 14
Connector Functions.......................................................................................................................... 14
LED’s.................................................................................................................................................. 17
SW 1 and SW 2 ................................................................................................................................. 18
Battery................................................................................................................................................ 18
Diagnostics......................................................................................................................................... 18
Manager’s Mode 02 (Real Time Clock)....................................................................................... 18
Manager’s Mode 03 (Audit Trail Report) ..................................................................................... 19
Manager’s Mode 04 (Card Reader Diagnostics)......................................................................... 21
Manager’s Mode 05 (Printer Diagnostics)................................................................................... 22
Manager’s Mode 06 (Pin pad Diagnostics) ................................................................................. 22
Manager’s Mode 07 (Peripheral Counter)................................................................................... 23
Manager’s Mode 08 (Software Version)...................................................................................... 23
Manager’s Mode 09 (Software Restart) ...................................................................................... 23
Manager’s Mode 10 (Maximum Queues) .................................................................................... 24
Manager’s Mode 96 (Communication Performance) .................................................................. 24
Parts......................................................................................................................................................... 25
5x8 Credit Parts Breakdown .............................................................................................................. 25
Wire Harnesses ................................................................................................................................. 27
B nn tt Limit d Warranty Stat m nt ................................................................................................... 29
IMPORTANT
Examine the shipment immediately upon arrival to make certain there has been no damage or loss in
transit Bennett Pump Company, as shipper, is not liable for the hazards of transportation Please make
damage claims directly to the truck line

3126305 Rev B 05/22/15
DANGER: Fire, explosion, injury or death
will occur if fuel filters are changed by untrained
personnel Make sure only trained personnel
change filters
CAUTION: Do not drill holes in fuel
dispensers Holes can cause failure of the
electronic equipment The warranty will become
void Use only adhesive backed sign mounting
brackets
WARNING: Do not operate the equipment
as a dispenser unless it is completely
WARNING: Make sure this equipment is
correctly grounded Failure to do will cause
injury or damage equipment or improper
operation Improper grounding voids the
warranty
WARNING: You must have training in the
operation and programming of this module
before using it READ THE OPERATORS
MANUAL
WARNING: The emergency shut-off valve
(also called the fire valve, shear valve or impact
valve) must be closed when service or
maintenance is performed on this equipment
WARNING: Electronic components are
static sensitive Use proper static precautions
(static straps) before working on the equipment
WARNING: To prevent electric shock, keep
the electrical parts of the terminal dry
WARNING: You must have training in the
installation, service or maintenance of this
equipment (dispenser, pump, console, control
box or submerged pump) before working on it
Maintenance repairs must be done by
authorized personnel only Warranty work may
only be performed by Bennett certified
technicians
DANGER: Disconnect all power to this
equipment and associated submerged pump(s)
during installation, service or any maintenance,
i e , changing filters
DANGER: Gasoline is flammable
NO SMOKING OR OPEN FLAME
DANGER: To prevent injury to you from
vehicles and onlookers, always place a barrier
around this equipment before performing service
or maintenance
WARNING ADVERTISSEMENT ADVERTENCIA
For the safe installation of this equipment, read and understand all warning and cautions Look for these
warnings:
“DANGER” means: If you do not follow the instructions, severe injury or death will occur
“WARNING” means: If you do not follow the instructions, severe injury or death can occur
“CAUTION” means: If you do not follow the instructions, damage can occur to the equipment
Saf ty Instructions

4126305 Rev B 05/22/15
Powering up the Module:
The module receives its power through the Power Supply
There are no power switches on the module The only way
to power on or off the module is by using the Circuit Breaker
The Bennett Logo will appear for approximately 5 seconds
when power is applied to the unit (see figure 1 1)
After the Bennett Logo is displayed the screen will display
the “Please Pay Inside” message
NOTE: “Pl as Pay Insid ” will b display d only if th
modul and/or POS (Point of Sal ) has not b n
configur d or install d at this tim (s figur
1.2). Th m ssag will r turn if th POS do s not
s nd a m ssag to th modul for 60 s conds.
Idle Screen:
Once everything is installed, programmed and configured
properly (see installation section) the module should be
ready to use The idle screen of the module will prompt the
user to either “Pay Here Credit” or “Pay Inside” (see figure
1 3)
FIGURE 1 1 - Bennett Logo
FIGURE 1 2 - “Please Pay Inside”
Introduction
FIGURE 1 3 - Idle Screen

5126305 Rev B 05/22/15
Power Requirements:
120vac must be installed in the head of the unit and
terminated on the terminal strip (see figure 2 1) Neutral
and Hot will be labeled on the terminal strip The Power
Supply will be factory wired to the terminal strip
The Power Supply converts the 120vac into the 12vdc
and 24vdc needed for the module to operate
The module receives its power from the Power Supply
through the J5 connector, on the CPU Board (see figure
2 2)
The module uses a 12vdc voltage source and 24vdc
voltage source Both sources are received through the
J5 connector
The following components use the 12vdc voltage source:
• Card Reader
• Display Backlight
• Receipt Printer Data
The following components use the 24vdc voltage
source:
• Receipt Printer Power
• Display
Connector Descriptions:
All peripherals are plugged into the CPU Board Following is a description of each connector
• J1 - Programming Header
• J4 - Audio Transducer
• J5 - Power Input/Data Link
• J6 - Card Swipe Reader
• J7 - Receipt Printer Power
• J8 - Receipt Printer Data
• J9 - Auxiliary / Natural Gas Comm Hub Board
• J12 - Alpha Numeric Pin pad or Credit only Keypad
• J13 - Left Side Soft Keys
• J14 - Right Side Soft Keys
• J17 - Fan Assembly
• J19 - Display Data
• J20 - Display Backlight
• J22 - Amulet Chip Programming Interface
See the Service Section for more details on the connector pin-outs
Installation
FIGURE 2 2 - J5 Incoming Power
J5 Connector
Terminal Strip
FIGURE 2 1 - Power
Power Supply

6126305 Rev B 05/22/15
DANGER: Circuit Br ak r must b off prior to plugging anything into or unplugging anything
from th modul .
DANGER: Wh n ins rting th plugs into th conn ctors, mak sur that th locking tab points
to th right sid of th conn ctor. G ntly tug th wir s to v rify that th locking tab is
ngag d. Failur to plug th s in corr ctly will damag th modul !
Communication:
The data for the module is also received through the J5 connector
The module communicates directly to the POS via the strip in the
head of the unit and Interconnect Box (see figure 2 2 - on previous
page)
NOTE:
• Th P d stal must b mount d at l ast 18” from any disp ns r or any ar a that’s classifi d
as Class 1 Division 1.
• Installation must b in accordanc with National El ctric Cod (NFPA 70), th Automotiv
and Marin S rvic Cod (NFPA 30A) and all Stat and Local Cod s.
• Us only Und rwrit rs List d Thr ad d Rigid Conduit and List d S aling Fitting with
conductor s als.
• Fi ld conn ctions ar don in th Upp r El ctrical Enclosur . Wir must xt nd 60 inch s
abov bas of th unit to mak El ctrical Conn ctions.
• All conductors ar to b strand d copp r with THHN and gas and oil r sistant insulation p r
National El ctrical Cod .
• Do not us wir small r than 18 gaug .
• Th s data wir s should b twist d tog th r at l ast 3 tim s p r foot to r duc th ff cts of
l ctrical nois on th communication circuit. Du to th risk of nois causing possibl
probl ms with communication, B nn tt highly r comm nds th us of th twist d wir s, but
do s not r quir it.
• Do not us wir nuts on Data Lin s. Do not splic Data wir s. Th y must b dir ct runs.
• It is acc ptabl to pull th Data Lin s in th sam conduit as th t rminal’s pow r.
• Shims should only b us d und r Bolts to nsur th unit is l v l. Improp r shimming that
r sults in misalign d fram is NOT cov r d und r th B nn tt Limit d Warranty.
Field Wiring Diagram on Next Page
Footprint:
Installation (continued...)
Field Wiring:
Data wires required for installation:
(1) 18 gauge for Data +
(1) 18 gauge for Common
(1) 18 gauge for Data -

7126305 Rev B 05/22/15
Installation (continued...)
FIGURE 2 3 - Field Wiring Diagram (Power)
FIGURE 2 4 - Field Wiring Diagram
(Communication)

8126305 Rev B 05/22/15
Programming
Gaining Access to Manager’s Mode:
The right Soft Keys are the only keys required to enter into Manager’s
Mode
Assuming that the top Soft Key is “1” and the bottom Soft Key is “4”
the code for entering into Manager’s Mode is “122114” (see figure 3 2)
Programming
The module has a Manager’s Mode used to access programming and diagnostics The following
instructions explain how to gain access to the Manager’s Mode and how to configure it for operation
Using the Keypad:
There are different keys on the
module that are used for different
functions (see figure 3 1)
• Soft Keys - Normally used for
customer interface
• Numeric Keys - Normally used
for entering alpha-numeric
data
Figure 3 2 - Right Soft Keys
“1”
“2”
“3”
“4”
Figure 3 1 - Keys
Left
Soft
Right
Soft
Numeric
Keys

9126305 Rev B 05/22/15
Once the proper “code” is pressed “Manager Mode: 00” will
be displayed at the top of the screen (see figure 3 3)
NOTE: If th modul is l ft in Manag r’s Mod for 60
s conds without any k ys pr ss d, th unit will
automatically r turn to normal op ration.
Programming Modes:
There are four modes that will need to be programmed prior
to the module operating per the location’s specifications
• Mode 01 - Address
• Mode 12 - Receipt Length
• Mode 13 - Keypad Type
• Mode 14 - Receipt Delay
• Mode 94 - Line Shift
• Mode 99 - Logo
The other modes are for diagnostics and will be discussed in
the Service Section
Manager’s Mode 01:
There is only one mode that must be programmed for the
module to communicate with the P O S Address the module
through Manager’s Mode 01
As soon as the module is in Manager’s Mode press the
numeric [1] key and press the function [Enter] key The
function [Enter] key will be used to enter each mode for
programming or diagnostics
Once the function [Enter] key is pressed the display will show
which address it is currently configured for (see figure 3 4)
At this time press the proper address for that module
NOTE: Us th sam addr ss in th modul as th
Fu ling Point for that disp ns r.
As soon as the numeric number for the address is pressed
the display will show what the new address is (see figure
3 5)
Now that the proper address is being displayed press the
function [Enter] key Once pressed the previous display will return with the new address After this is
complete press the right Soft Key where “EXIT” is present on the display to exit Manager’s Mode 01
If programming is complete press the right Soft Key next to “EXIT” on the display again and the module
will return to normal operation
Programming (continued...)
Figure 3 3 - Mode 00
Figure 3 4 - Mode 01
Figure 3 5 - New Address Set

10 126305 Rev B 05/22/15
Manager’s Mode 12:
To help eliminate paper jams Manager’s Mode 12 will adjust
the length of the receipts It is highly suggested that the
length of the receipt is configured so that the end of the paper
will exit the chute with the least amount of paper There is a
“notch” at the end of the paper chute (see figure 3 6) This
“notch” is made to encourage the customer to place their
thumb inside the notch while removing the receipt from the
paper chute
NOTE: It is sugg st d that this mod b configur d
aft r th first r c ipt is ran. Th l ngth of th
r c ipt will vary, d p nding on th information
s nt from th POS.
Once the module is in Manager’s Mode press the numeric [1]
and [2] key and then press the function [Enter] key
Once the function [Enter] key is pressed the display will show
the current length of the receipt (see figure 3 7) To lengthen
the receipt enter a number larger than the current count
number To shorten the receipt enter a number that is lower
than the current number
As the new count is entered the display will show the new
value (see figure 3 8)
Now that the new setting is being displayed press the function
[Enter] key Once pressed the previous display will return
with the new current count
After this is complete press the right Soft Key where “EXIT” is
present on the display to exit Manager’s Mode 12
If programming is complete press the right Soft Key next to
“EXIT” on the display again and the module will return to
normal operation
Manager’s Mode 13:
Mode 13 is used to program the payment keypad type
Once the module is in Manager’s Mode press the numeric [1]
and [3] keys and then press the function [Enter] key
Once the function [Enter] key is pressed the display will show
the current setting for the keypad (see figure 3 9)
NOTE: For this unit Option 2 must b programm d.
Programming (continued...)
Figure 3 6 - Paper Chute
Paper Chute “notch”
Figure 3 7 - Manager’s Mode 12
Figure 3 8 - Resizing the Receipt
Figure 3 9 - Manager’s Mode 13

11 126305 Rev B 05/22/15
Programming (continued...)
Setting choices are:
Option 1 = EPP (not used)
Option 2 = 5x8 Used when utilizing alpha numeric characters
for credit / fleet operations
Option 3 = 4x4 (not used)
NOTE: If th k ypad is programm d wrong th n it may
not r cogniz th num ric buttons whil b ing
pr ss d.
To change programming, once in Manager’s Mode, press the
top left Soft Key until the displays shows “Manager’s Mode
13” Then press the key below the top left key until “5x8” is
displayed (see figure 3 10) Then press the top left key to
save the change
If programming is complete press the right Soft Key next to
“EXIT” on the display again and the module will return to
normal operation
Manager’s Mode 14:
As the POS sends data to the module for the receipts the data
is broken up in small “increments” At times this can cause
the printer to have slight pauses while printing the receipts If
a location is extremely busy then these pauses could be long
enough for a customer to believe that the receipt is complete
and they will begin to remove the paper from the printer chute
before it is complete
To prevent this from happening Mode 14 is used to send the
receipt data to the printer in a single burst of data The result
will be a single, continual motion where the paper will be
dispensed at one time Essentially, the module will hold the
receipt data until all data has been sent before sending it to
the printer
Once the module is in Manager’s Mode press the numeric [1]
and [4] keys and then press the function [Enter] key
Once the function [Enter] key is pressed the display will show the current setting for the receipt delay
(see figure 3 11)
To change the setting press the numeric keys to enter the desired time for the delay 99 seconds is the
maximum amount of time allowed Once the key is pressed then the display will show what the new
value will be set for (see figure 3 12) Press the [Enter] key to save the new value
If programming is complete press the right Soft Key next to “EXIT” on the display again and the module
will return to normal operation
Figure 3 11 - Manager’s Mode 14
Figure 3 12 - New Receipt Delay
Figure 3 10 - New Keypad Selection

12 126305 Rev B 05/22/15
Programming (continued...)
Manager’s Mode 94:
Manager’s Mode 94 is used to shift the screen text down a
line space on SP display for better viewing
Once the module is in Manager’s Mode press the numeric [9]
and [4] keys and then press the function [Enter] key
Once the function [Enter] key is pressed the display will show
the current setting for line shift (see figure 3 17)
To change the setting, press the numeric [1] key to turn ON
the line shift function To turn this setting OFF, press the nu-
meric [0] key Press the [Enter] key to save the value (see
figure 3 17 and 3 18)
If programming is complete press the right Soft Key next to
“EXIT” on the display again and the module will return to nor-
mal operation
Manager’s Mode 99:
There are thirty six different logos that can be displayed on
the Idle Prompt Screen
This mode is used to set the logo on the bottom right corner
of the display (see figure 3 19) This logo can not be moved
nor can it be displayed while operating the module This logo
can only be displayed on the Idle Prompt Screen
Once the module is in Manager’s Mode press the numeric [9]
key twice and press the function [Enter] key
Once the function [Enter] key is pressed the display will show
which logo is programmed, if any (see figure 3 20)
FIGURE 3 17
FIGURE 3 18
Figure 3 19 - Bennett Logo
Figure 3 20 - Mode 99
Logo 00 shows NO Logo

13 126305 Rev B 05/22/15
Programming (continued...)
There are currently thirty six options that are available for this mode:
NOTE: This list will incr as through tim so if th d sir d logo do sn’t s m availabl pl as
contact B nn tt Pump Company for a compl t list of logos.
As soon as the number for the desired logo is pressed the current logo will disappear The new logo will
not appear until the function [Enter] key is pressed (see figure 3 21)
After this is complete press the right Soft Key where “EXIT” is present on the display to exit Manager’s
Mode 99
If programming is complete press the right Soft Key next to “EXIT” on the display again and the module
will return to normal operation
00 - No Logo
01 - 76 Logo
02 - Air Products Logo
03 - Arco Logo
04 - Beacon Logo
05 - Bennett Logo
06 - BP Logo
07 - Chevron Logo
08 - Citgo Logo
09 - Clark Logo
10 - Conoco Logo
11 - Conoco Phillips Logo
12 - Exxon Logo
13 - Flying J Logo
14 - Fuel Depot Logo
15 - Getty Logo
16 - GoGas Logo
17 - Gulf Logo
18 - Hess Logo
19 - Irving Logo
20 - Lukoil Logo
21 - Mapco Logo
22 - Marathon Logo
23 - Mobil Logo
24 - Phillips 66 Logo
25 - Pure Oil Eagle Logo
26 - Pure Oil Logo
27 - Sapp Brothers Logo
28 - Shamrock Logo
29 - Shell Logo
30 - Sinclair Logo
31 - Sunoco Logo
32 - Tesoro Logo
33 - Texaco Logo
34 - Valero Logo
35 - VP Racing Fuels Logo
Figure 3 21 - Selecting Logo

14 126305 Rev B 05/22/15
Figure 4 1 - CPU Board
S rvic
Connector Functions:
All DC Voltages referenced in this document have a tolerance of +/- 5%
• J1 - Programming Header
For Bennett use only
• J4 - Audio Transducer
Used to connect the speaker that is used to beep and prompt the user to respond to the module
NOTE: Th +12v on Pins 1 and 2 is th sam +12v that nt rs th CPU Board on Pins 1 and 2 of
J5.
NOTE: Th +5v on Pins 3 and 4 is r gulat d on th CPU Board using th +12v suppli d on Pins
1 and 2 of J5.

15 126305 Rev B 05/22/15
S rvic (continued...)
• J5 - Module Power, Module RS-485
Used to connect the debit system to an external power supply and connect the debit system’s RS-485
interface to the 3rd part controller
• J6 (COM 0) - Card Swipe
This is dedicated to RS-232 used to interface the card swipe reader
NOTE: Th +12v on Pin 4 is th sam +12v that nt rs th CPU Board on Pins 1 and 2 of J5.
• J7 - Receipt Printer Power
NOTE: Th sam +24v on Pins 1 and 2 is th sam +24v from Pins 3 and 4 of J5.
NOTE: Th sam +12v on Pin 3 is th sam +12v from Pins 1 and 2 of J5.
NOTE: Th +5v is r gulat d on th CPU Board using th +12v suppli d on Pins 1 and 2 of J5.
• J8 (COM 1) - Receipt Printer
This is dedicated to RS-232 used to interface the receipt printer
J9 (COM 2) - Auxiliary Connector / Natural Gas Com Hub Board
J10 - Not Used
NOTE: Th sam +24v on Pins 1 and 2 is th sam +24v from Pins 3 and 4 of J5.
NOTE: Th sam +12v on Pin 3 is th sam +12v from Pins 1 and 2 of J5.
NOTE: Th +5v is r gulat d on th CPU Board using th +12v suppli d on Pins 1 and 2 of J5.
J11 (COM 3) - Not Used
NOTE: Th +5v on Pins 4 and 6 is r gulat d on th CPU Board from th +12v suppli d on Pins 1
and 2 of J5.
• J12 - Alpha Numeric Keyboard or Credit Only Keypad
This is used to connect the Alpha Numeric Keypad to the keypad matrix
Pins: Pins:
1 +12v 6 RS-485 Return
2 +12v 7 RS-485 -
3 +24v 8 N/C
4 +24v 9 Ground
5 RS-485 + 10 Ground

16 126305 Rev B 05/22/15
S rvic (continued...)
• J13 - Right Side Soft Keys
This is used to connect the left side soft key push buttons to the keypad matrix
• J14 - Left Side Soft Keys
This is used to connect the right side soft key push buttons to the keypad matrix
• J17 - Auxiliary Power
Used for peripheral power requirements
NOTE: Th sam +24v on Pins 1 and 2 is th sam +24v from Pins 3 and 4 of J5.
NOTE: Th sam +12v on Pin 3 is th sam +12v from Pins 1 and 2 of J5.
NOTE: Th +5v is r gulat d on th CPU Board using th +12v suppli d on Pins 1 and 2 of J5.
• J19 - Display Data
Connects to the flex ribbon coming from the graphics display This ribbon contains the display data and
display power
• J20 - Display Backlight
Provides +24v to the display for backlighting
• J22 - Amulet Chip Programming
This connector is used for programming the Amulet Chip Used for updating the SP software

17 126305 Rev B 05/22/15
LEDs:
S rvic (continued...)
Figure 4 2 - CPU Board LEDs
D25D21 D19 D13 D11
D1
D7
D8
D15
D17
D23
• D1 (Red) “Heart Beat” - Blinks at the rate of 1x per second when in normal run mode
• D7 (Red) - RS-485 - RXD
• D8 (Green) - RS-485 - TXD
• D11 (Red) - COM 1 (Magnetic Card Reader) - TXD
• D13 (Green) - COM 1 (Magnetic Card Reader) - RXD
• D15 (Red) - COM 3 (Printer) - TXD
• D17 (Green) COM 3 (Printer) - RXD
• D19 (Red) - COM 2 (Auxiliary) - TXD
• D21 (Green) - COM 2 (Auxiliary) - RXD
• D23 (Red) COM 0 (Not Used)
• D25 (Green) - COM 0 (Not Used)

18 126305 Rev B 05/22/15
SW 1 and SW 2:
These switches are used in conjunction with J1 (Programming Header) With the switches moved away
from the dot the unit is ready for receiving a new code If the switches are moved towards the dot the
unit is in normal run mode There is a white dot on the board to indicate normal run mode
NOTE: Us “SPM/SPP Programming Instructions” (Part Numb r 126036) for instructions on how
to program th unit.
CAUTION: This is only to b us d with th instruction of B nn tt Pump Company.
Battery:
Refer to figure 4 1 for the location of the battery BT2 - Lithium Button Cell Supports both real time clock
(RTC)
NOTE: Wh n this batt ry is fully discharg d th RTC stops working and th d bit syst m will
show a p rman nt door op n condition.
Diagnostics:
There are ten diagnostic modes available with the module These modes are used to help troubleshoot
the software, keypad, printer, card reader or encryption Here is a list of diagnostic modes:
• Mode 02 - Real Time Clock (RTC) Change
• Mode 03 - Audit Trail Print
• Mode 04 - Card Reader Test
• Mode 05 - Printer Test
• Mode 06 - Keypad Test
• Mode 07 - Power Control Counters
• Mode 08 - Software Version
• Mode 09 - Software Restart
• Mode 10 - Maximum Queue
• Mode 96 - Communication Performance
To gain access to these modes follow the same instructions used to enter the programming modes (see
page 9)
Manager’s Mode 02:
There is a Real Time Clock (RTC) that the system uses to track two different Audit Events
1 Software Restarts
2 RTC Changes
Use these events to help show how many times the software in the module has restarted and how many
times the Real Time Clock has been changed Each event will be stamped with a date and time
NOTE: Th r is no way to r s t th s v nts.
S rvic (continued...)

19 126305 Rev B 05/22/15
Once in Manager’s Mode press the numeric [2] key and
press the function [Enter] key
Once the function [Enter] key is pressed the display will show
what the current date and time is set for (see figure 4 3)
The date in figure 4 3 is showing July 1st, 2009
The time in figure 4 3 is showing 2:17 P M
To change the date and time start with entering the last two
digits of the year, the two digits for the month, the two digits
for the day, next enter the two digits for the hour (military
time) and the two digits for the minutes When this is
complete press the function [Enter] key to save the new
setting
After this is complete press the right Soft Key where “EXIT” is present on the display to exit Manager’s
Mode 02
If programming is complete press the right Soft Key next to “EXIT” on the display again and the module
will return to normal operation
Manager’s Mode 03:
After the RTC has been set the Audit Trail Report will print
the date and time that each event happens These reports
will tell when each of the Audit Events have taken place
Once the module is in Manager’s Mode press the numeric
[3] key and press the function [Enter] key
The display will show four different reports that can be
printed out (see figure 4 4)
1 The last 25 times any of the Audit Events have occurred
2 The last 25 times that the Software has Restarted
3 The last 25 times that the Door has been Opened
4 The last 25 times that the RTC (Real Time Clock) has been reset
Press the numeric key that correlates with the desired report and the printer will print out the report
The unit will store a maximum of 4,032 Audit Events If more than the last 25 events is desired continue
to press the same numeric key until it prints that event The report will print the newest events first
After this is complete press the right Soft Key where “EXIT” is present on the display to exit Manager’s
Mode 03
If programming is complete press the right Soft Key next to “EXIT” on the display again and the module
will return to normal operation
S rvic (continued...)
Figure 4 3 - Mode 02
Figure 4 4 - Mode 03

20 126305 Rev B 05/22/15
If programming is complete press the right Soft Key next to “EXIT” on the display again and the module
will return to normal operation
Figure 4 5 is an example of the Audit Events Report This report shows the last 25 events that took
place Notice that the event column (left side of report) reflects the three different types of events
Figure 4 6 is an example of the Software Starts Report This report only reflects the last 25 times that
the software reset Notice that the event column (left side of report) reflects only the software starts
event
Figure 4 7 is an example of the Clock Change Report This report only reflects the last 5 times that the
RTC was reset It has not reached the maximum 25 number of events Notice that the event column
(left side of report) reflects only the clock changes event
S rvic (continued...)
FIGURE 4 5 - All Audit Events
Report
Event
Date
Time
Sequence
Number
FIGURE 4 6 - Software Starts
Report
Event
Date
Time
Sequence
Number
FIGURE 4 7 - Clock Change Report
Event
Date
Time
Sequence
Number
Other manuals for Site Master SP
1
Table of contents
Other Bennett Payment Terminal manuals
Popular Payment Terminal manuals by other brands
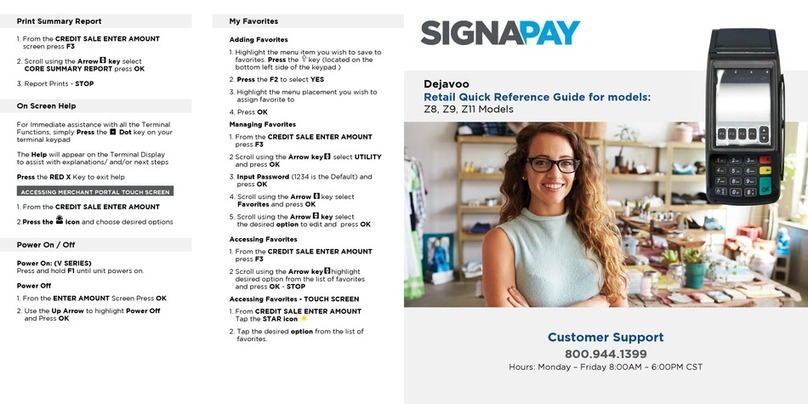
SignaPay
SignaPay Dejavoo Z8 Quick reference guide

oti
oti 6500 TRIO specification
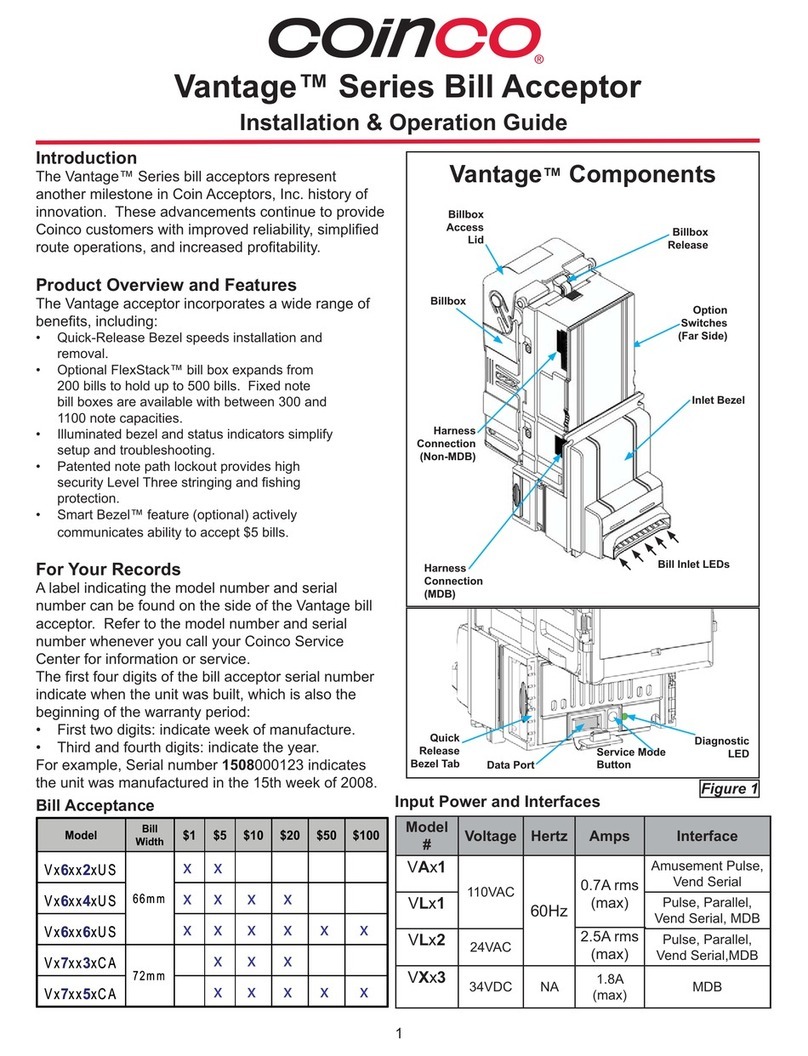
Coinco
Coinco Vantage Series Installation & operation guide
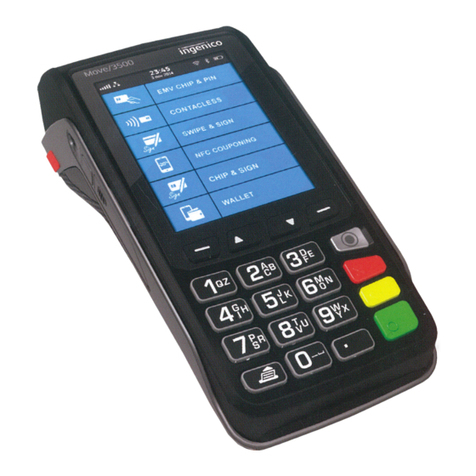
Ingenico group
Ingenico group Move 3500 WiFi quick start guide
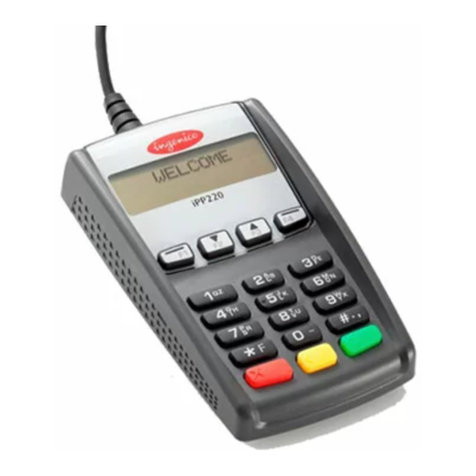
Ingenico
Ingenico IPP200 Series installation guide
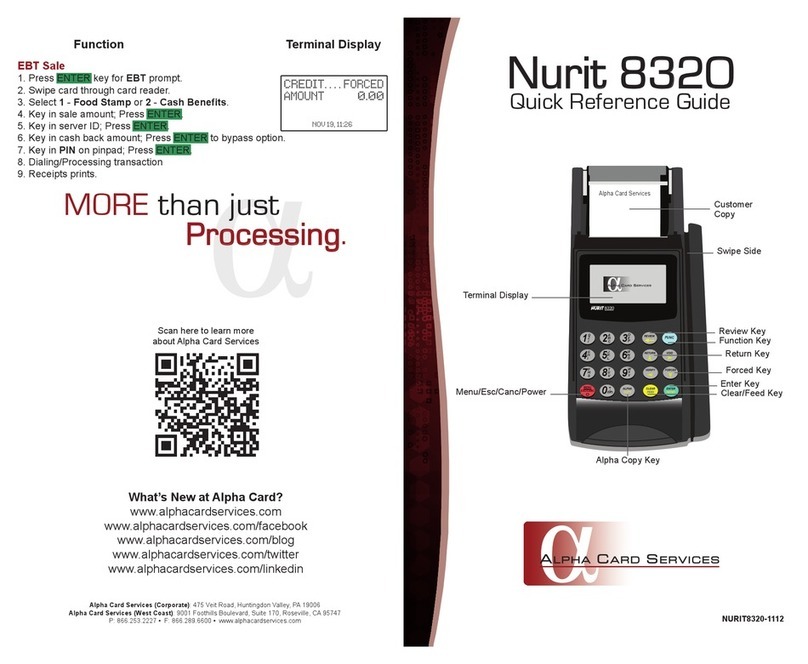
Alpha Card Services
Alpha Card Services Nurit 8320 Quick reference guide