BRINKMANN PUMPS BBV1 User manual

Operating instructions (Translation)
BBV1, BBV2 100 bar and higher
Pressure relief valve BBV1-2, BBVH1-2 100 bar and higher
BBV1-2 100 bar and higher
Englisch
2018-11-26

Table of Content
1 General 4
1.1 About the documentation 4
1.2 Manufacturer´s address 4
1.3 Symbolism 5
2 Safety 6
2.1 Intended use 6
2.2 Personnel qualification and training 6
2.3 Basic safety instructions 6
2.4 Basic hazards 7
3 Device description 8
3.1 Functional principle 8
3.2 Basic design 9
4 Technical data 11
4.1 General 11
4.2 Permissible pressure range 12
4.2.1 Operating pressure 12
4.2.2 Layout pressure setting range - flow rate BBV1, 2 12
4.3 Permissible temperature range 12
4.4 Material data 12
4.5 Dimensions 12
5 Transport and storage 13
5.1 General 13
5.2 Storage 13
6 Installation 15
6.1 Safety instructions for installation 15
6.2 Mechanical installation 16
6.2.1 Preparation 16
6.2.2 Screw-in valve 16
6.2.3 Pipeline installation 16
6.3 Connection lines 17
6.3.1 General 17
6.3.2 Mounting Connection lines 17
7 Operation start-up 18
7.1 Safety instructions for start-up 18
7.2 Pressure setting 19
7.3 Further operation start-up 21

8 Removal 22
8.1 Safety instructions for removal 22
8.2 General 23
9 Maintenance 24
9.1 Safety instructions for maintenance 24
9.2 Maintenance work 25
9.3 Maintenance instructions 25
10 Repairs 27
10.1 Safety instructions for repair 27
10.2 General 28
10.3 Detecting and eliminating failures 29

Pressure relief valve BBV1-2, BBVH1-2 100 bar and higher
4
2018_11_26 BBV1-2 100 bar and higher
1 General
1.1 About the documentation
These operating instructions describe the installation, operation and maintenance
of the following device:
Pressure relief valve BBV1-2 100 bar and higher,
The device is manufactured in different versions. Information about the version
concerned in the individual case can be found on the device's type plate.
These operating instructions are a component of the device and must be kept ac-
cessible for the personnel near the device at all times.
If you have any questions about these operating instructions, please contact the
manufacturer.
1.2 Manufacturer´s address
Brinkmann Pumpen
K. H. Brinkmann GmbH & Co. KG
Friedrichstraße 2
DE 58791 Werdohl
Tel: +49 (0) 23 92 / 5006-0
Fax: +49 (0) 23 92 / 5006-180
E-mail: sales@brinkmannpumps.de
Web: www.brinkmannpumps.de

Pressure relief valve BBV1-2, BBVH1-2 100 bar and higher
BBV1-2 100 bar and higher 2018_11_26
5
1.3 Symbolism
DANGER
Identification of an immediate hazard, which would result in death or severe bod-
ily injury if not avoided.
WARNING
Identification of a potential medium risk hazard, which would lead to death or se-
vere bodily injury if not avoided.
CAUTION
Identification of a low risk hazard, which could lead to minor or medium bodily inju-
ry if not avoided.
NOTICE
Flagging of notices to prevent property damage.
Identification of basic safety instructions. Non-compliance can lead to hazards for
people and the device.
Flagging of special user tips and other especially useful or important information.

Pressure relief valve BBV1-2, BBVH1-2 100 bar and higher
6
2018_11_26 BBV1-2 100 bar and higher
2 Safety
2.1 Intended use
1. The device has been designed for operation with fluid.
2. The device may be operated in filled condition only.
The medium must be compatible with the materials used in the device. The
chemical competence is necessary for this. Be careful with ethylene oxide or
other cathalytic or exothermic or self-decomposing materials. Please consult
the manufacturer in cases of doubt.
3. The device may be operated only in usual industrial atmospheres. If there are
any aggressive substances in the air, always ask the manufacturer.
4. Operation of the device is only permissible when complying with the operating
instructions and applicable documents.
Deviating operating conditions require the express approval of the manufac-
turer.
5. In case of any use of the device not according to specification, any warranty is
voided.
2.2 Personnel qualification and training
The staff designated to assemble, operate and service the device must be properly
qualified. This can be through training or specific instruction. Personnel must be
familiar with the contents of this operating instructions.
Read the operating instructions thoroughly before use.
2.3 Basic safety instructions
1. Comply with existing regulations on accident prevention and safety at work
along with any possible internal operator regulations.
2. Pay attention to the greatest possible cleanliness.
3. Wear suitable personal protection equipment.
4. Do not remove, make illegible or obliterate type plates or other references on
the device.
5. Do not make any technical changes on the device.
6. Maintain and clean the device regularly.
7. Use spare parts approved by the manufacturer only.

Pressure relief valve BBV1-2, BBVH1-2 100 bar and higher
BBV1-2 100 bar and higher 2018_11_26
7
2.4 Basic hazards
DANGER
Hazardous fluids!
Danger of death when handling hazardous fluids.
1. Comply with the safety data sheets and regulations on handling hazardous
fluids.
2. Collect and dispose of hazardous fluids so that no hazards arise for people
or the environment.
WARNING
Failure of load-carrying parts due to overload!
Danger of injury from flying parts.
Danger of injury from spurting fluids.
1. Depressurise the device and all connection lines before doing any work.
2. Securely prevent the restoration of pressure while working on the device.
WARNING
Failure of load-carrying parts due to overload!
Danger of injury from flying parts.
Danger of injury from spurting fluids.
1. Use only connections and lines approved for the expected pressure range.
2. Securely prevent exceeding the permissible pressure, e.g. by using pressure
relief valves or rupture discs.
3. Design pipework so that no tensions, e.g. caused by changes in length due to
fluctuations in temperature, are transmitted to the device.
WARNING
Failure of load-carrying parts due to overload!
Danger of injury from flying parts.
Danger of injury from spurting fluids.
1. Consider the permissible pressure setting range of the valve.
2. Check the pressure setting (the valve must not block).

Pressure relief valve BBV1-2, BBVH1-2 100 bar and higher
8
2018_11_26 BBV1-2 100 bar and higher
3 Device description
3.1 Functional principle
Pressure relief valves of the BBV1-2 series are directly operated seat valves and
are used to safeguard low-pressure hydraulic circuits.
Explanation
1
Housing
2
Valve cone
3
Valve seat
4
Threaded bush
5
Compression spring
6
Hexagonal nut
7
Adjustment screw
8
Protective cap
The valve cone is pressed by the compressed spring into the valve seat, which
blocks Pressure connection (P) from Tank connection (T). When the response
pressure is reached by adjusting with the setscrew, the valve cone releases the
fluid flow to the tank connection.
The valve should preferably be mounted vertical, with the adjustment screw facing
down.
The flow direction is marked with an arrow on the unit housing. It is always imple-
mented from the pressure port (P) to the tank connector (T).

Pressure relief valve BBV1-2, BBVH1-2 100 bar and higher
BBV1-2 100 bar and higher 2018_11_26
9
3.2 Basic design
EBV1, 2
BBV1, 2
Explanation
Explanation
1.
Damping plugs
1.
Housing
2.
Valve seat
2.
Damping plugs
3.
O-Ring
3.
Valve seat
4.
Valve cone
4.
O-Ring
5.
O-Ring
5.
Valve cone
6.
Support ring
6.
O-Ring
7.
Compression spring
7.
Support ring
8.
Threaded bush
8.
Compression spring
9.
O-Ring
9.
Threaded bush
10.
Support ring
10.
O-Ring
(only NG 20)
11.
Support ring
11.
Hexagonal nut
(only NG 20)
12.
Adjustment screw
12.
Hexagonal nut
13.
Protective cap
13.
Adjustment screw
14.
Protective cap

Pressure relief valve BBV1-2, BBVH1-2 100 bar and higher
10
2018_11_26 BBV1-2 100 bar and higher
BBVH1, 2
Explanation
1.
Housing
10.
O-Ring
2.
Damping plugs
11.
Support ring
3.
Valve seat
(only NG 20)
4.
O-Ring
12.
Check nut
5.
Valve cone
13.
Adjustment screw
6.
O-Ring
14.
Twist grip
7.
Support ring
15.
Washer
8.
Compression spring
16.
Hexagonal nut
9.
Threaded bush
17.
Washer

Pressure relief valve BBV1-2, BBVH1-2 100 bar and higher
BBV1-2 100 bar and higher 2018_11_26
11
4 Technical data
4.1 General
General information BBV1, 2
Design
Seat valve, directly operated
Fixing type
Screw-in valve / Pipeline installation
Connection KP 1 (BBV1, 2)
BBV1, 2 R 5
Whitworth pipe thread G ¾
BBV1, 2 D 1
Tank connection:
Whitworth pipe thread G ½
Type of damping
Valve cone with damper
Mounting position
preferably vertical, pressure set screw facing down
Max. flow capacity
Qmax.
See section 4.2 “Permissible pressure range”
Operating pressure
p
Nominal pressure
pN
Pressure setting ranges
pv min.
pv max.
Viscosity
νmin
1 mm2/s
νmax
600 mm2/s
Fluid temperature
ϑm
See section 4.3 “Permissible temperature range”
Ambient temperature
ϑu
Material
See section 4.4 “Material data”
Filtering
Filter porosity: max. 20 µm for very hard particles 1.000 –10.000 HV
max. 50 µm for hard particles 50 –70 HRC.
max. 60 µm for middle hard particles < 50 HRC
See the pollution classifications diagram in the screw pumps catalog
Permissible media
Oil and water based coolant according to the operating instruc-
tions in the screw pumps catalog
(1) Pipe thread: ISO 228-1

Pressure relief valve BBV1-2, BBVH1-2 100 bar and higher
12
2018_11_26 BBV1-2 100 bar and higher
4.2 Permissible pressure range
4.2.1 Operating pressure
Nominal size
Nominal pressure
Inlet pressure
Outlet pressure
pN[bar]
pe min. [bar]
pe max [bar]
pR max [bar]
10
400
15
410
210
4.2.2 Layout pressure setting range - flow rate BBV1, 2
Pressure stage
Pressure setting ranges [bar]
Flow [l/min]
pv min.
pv max.
Qmax.
at pv max.
200
10
200
60
150
150
55
4.3 Permissible temperature range
Sealing material
Fluid temperature ϑm (1)
ϑm min [°C]
ϑm max [°C]
80
FKM
-15
(1) Comply with media-specific properties.
Sealing material
Ambient temperature ϑu
ϑu min. [°C]
ϑu max. [°C]
60
FKM
-15
4.4 Material data
Nominal size
Fixing type
Material
Housing
Seal
Compression
spring
Other materials
10
R
EN-GJL-250
FKM
Spring steel
Steel
R = Pipe valve
4.5 Dimensions
Dimensions of the device can be found in the relevant technical data sheets.

Pressure relief valve BBV1-2, BBVH1-2 100 bar and higher
BBV1-2 100 bar and higher 2018_11_26
13
5 Transport and storage
5.1 General
●After receipt, check the device for transport damages.
●If transport damage is noticed, report this immediately to the manufacturer
and the carrier. The device must then be replaced or repaired.
●Dispose of packing material and used parts in accordance with the local stipu-
lations.
5.2 Storage
The device's function is tested in the plant with mineral hydraulic oil. Then all con-
nections are closed. The remaining residual oil preserves the interior parts for up to
6 months.
Metallic exposed exterior parts are protected against corrosion by suitable conser-
vation measures, also up to 6 months.
In case of storage, a dry, dust-free and low-vibration environment is to be ensured.
The device is to be protected against influences from weather, moisture and strong
fluctuations of temperature. The recommended storage conditions are to be ad-
hered to.
Below the permissible ambient temperature ϑuelastomer seals lose their elasticity
and mechanical loading capacity, since the glass transition temperature is fallen
below. This procedure is reversible. A force action on the device is to be avoided in
case of storage below the permissible ambient temperature ϑu.
When storing for a long period of time (> 6 months), treat all surfaces at risk of
corrosion again with suitable preserving agents.
If high air humidity or aggressive atmospheres are expected, take additional corro-
sion-preventing measures.
Storage in corrosion protection bags (VCI) maximum of 6 months.
NOTICE
Corrosion/chemical impact
Improper storage can render the device useless.
1. Protect endangered surfaces by means of suitable conservation measures.
2. Comply with recommended storage conditions.

Pressure relief valve BBV1-2, BBVH1-2 100 bar and higher
14
2018_11_26 BBV1-2 100 bar and higher
Recommended storage conditions
1. Storage temperature: 5 °C - 25 °C
2. Relative air humidity: < 70 %
3. Protect elastomer parts from light, especially direct sunlight.
4. Protect elastomer parts from oxygen and ozone.
5. Comply with maximum storage times of elastomeric parts:
○5 Years: AU (Polyurethane rubber)
○7 Years: NBR, HNBR, CR
○10 Years: EPM, EPDM, FEP/PTFE, FEPM, FKM, FFKM, VMQ,
FVMQ

Pressure relief valve BBV1-2, BBVH1-2 100 bar and higher
BBV1-2 100 bar and higher 2018_11_26
15
6 Installation
6.1 Safety instructions for installation
DANGER
Hazardous fluids!
Danger of death when handling hazardous fluids.
1. Comply with the safety data sheets and regulations on handling hazardous
fluids.
2. Collect and dispose of hazardous fluids so that no hazards arise for people
or the environment.
WARNING
Failure of load-carrying parts due to overload!
Danger of injury from flying parts.
Danger of injury from spurting fluids.
1. Depressurise the device and all connection lines before doing any work.
2. Securely prevent the restoration of pressure while working on the device.
WARNING
Failure of load-carrying parts due to overload!
Danger of injury from flying parts.
Danger of injury from spurting fluids.
1. Use only connections and lines approved for the expected pressure range.
2. Securely prevent exceeding the permissible pressure, e.g. by using pressure
relief valves or rupture discs.
3. Design pipework so that no tensions, e.g. caused by changes in length due to
fluctuations in temperature, are transmitted to the device.

Pressure relief valve BBV1-2, BBVH1-2 100 bar and higher
16
2018_11_26 BBV1-2 100 bar and higher
6.2 Mechanical installation
6.2.1 Preparation
●Check the device for transport damage and dirt.
●Remove existing preservatives.
○Use only those cleaning agents that are compatible with the materials
used in the device.
○Do not use cleaning wool.
●Compare the environmental and ambient conditions at the place of installation
to the permissible conditions.
○Expose the device only to small vibrations, see IEC 60034-14.
○Secure sufficient access for maintenance and repair.
6.2.2 Screw-in valve
●Screw the screw-in valve into the designated housing with the specified
torque.
○Do not damage seals during assembly.
Tightening torques [Nm]
Nominal size
Pressure stage [bar]
≤ 200
10
100 ±5
Select the material and dimensions of the planned housing to ensure sufficient
safety for all conceivable operating conditions.
6.2.3 Pipeline installation
●Install the device preferably vertical with the pressure adjustment screw facing
down.
●Take measures against accidental touching of hot surfaces (> 60 °C).

Pressure relief valve BBV1-2, BBVH1-2 100 bar and higher
BBV1-2 100 bar and higher 2018_11_26
17
6.3 Connection lines
6.3.1 General
WARNING
Failure of load-carrying parts due to overload!
Danger of injury from flying parts.
Danger of injury from spurting fluids.
1. Use only connections and lines approved for the expected pressure range.
2. Securely prevent exceeding the permissible pressure, e.g. by using pressure
relief valves or rupture discs.
3. Design pipework so that no tensions, e.g. caused by changes in length due to
fluctuations in temperature, are transmitted to the device.
Additional connections
1. Provide measurement connections for pressure and temperature as close as
possible to device.
2. If necessary, provide a facility to fill or empty the device and the line system.
3. If necessary, provide a facility to vent the device and the line system.
6.3.2 Mounting Connection lines
Position of the device connections: See chapter 3 “Device description”
●Clean all lines.
○Do not use cleaning wool.
○Pickle and flush welded pipes.
●Remove the protective plugs.
●Mount the lines.
○Comply with the manufacturer's information.
○Do not use any sealing materials such as hemp, Teflon tape or putty.

Pressure relief valve BBV1-2, BBVH1-2 100 bar and higher
18
2018_11_26 BBV1-2 100 bar and higher
7 Operation start-up
7.1 Safety instructions for start-up
DANGER
Hazardous fluids!
Danger of death when handling hazardous fluids.
1. Comply with the safety data sheets and regulations on handling hazardous
fluids.
2. Collect and dispose of hazardous fluids so that no hazards arise for people
or the environment.
WARNING
Failure of load-carrying parts due to overload!
Danger of injury from flying parts.
Danger of injury from spurting fluids.
1. Consider the permissible pressure setting range of the valve.
2. Check the pressure setting (the valve must not block).
CAUTION
Hot surfaces!
Burn injury to skin if touched.
1. Wear protective gloves at temperatures ≥48°C.

Pressure relief valve BBV1-2, BBVH1-2 100 bar and higher
BBV1-2 100 bar and higher 2018_11_26
19
7.2 Pressure setting
The response pressure of the device is factory set to the mean value of each pres-
sure stage. If applicable, the pressure setting must be adapted during commission-
ing.
Pressure setting for actuation type: A for precise adjustment
1
Hexagonal nut
3
Protective cap
2
Adjustment screw
●Remove the protective cap
●Remove hexagon nut
●Set the response pressure using the adjusting screw
○clockwise = Higher response pressure
○counterclockwise = Lower response pressure
●Tighten hexagonal nut
●Put on the protective cap
WARNING
Failure of load-carrying parts due to overload!
Danger of injury from flying parts.
Danger of injury from spurting fluids.
1. Consider the permissible pressure setting range of the valve.
2. Check the pressure setting (the valve must not block).

Pressure relief valve BBV1-2, BBVH1-2 100 bar and higher
20
2018_11_26 BBV1-2 100 bar and higher
Pressure setting for actuation type: B with knob
1
Check nut
2
Twist grip
●Loosen the lock nut
●Set the response pressure with the adjusting screw
○clockwise = Higher response pressure
○counterclockwise = Lower response pressure
●Secure the twist grip with a lock nut
WARNING
Failure of load-carrying parts due to overload!
Danger of injury from flying parts.
Danger of injury from spurting fluids.
1. Consider the permissible pressure setting range of the valve.
2. Check the pressure setting (the valve must not block).
This manual suits for next models
3
Table of contents
Popular Control Unit manuals by other brands
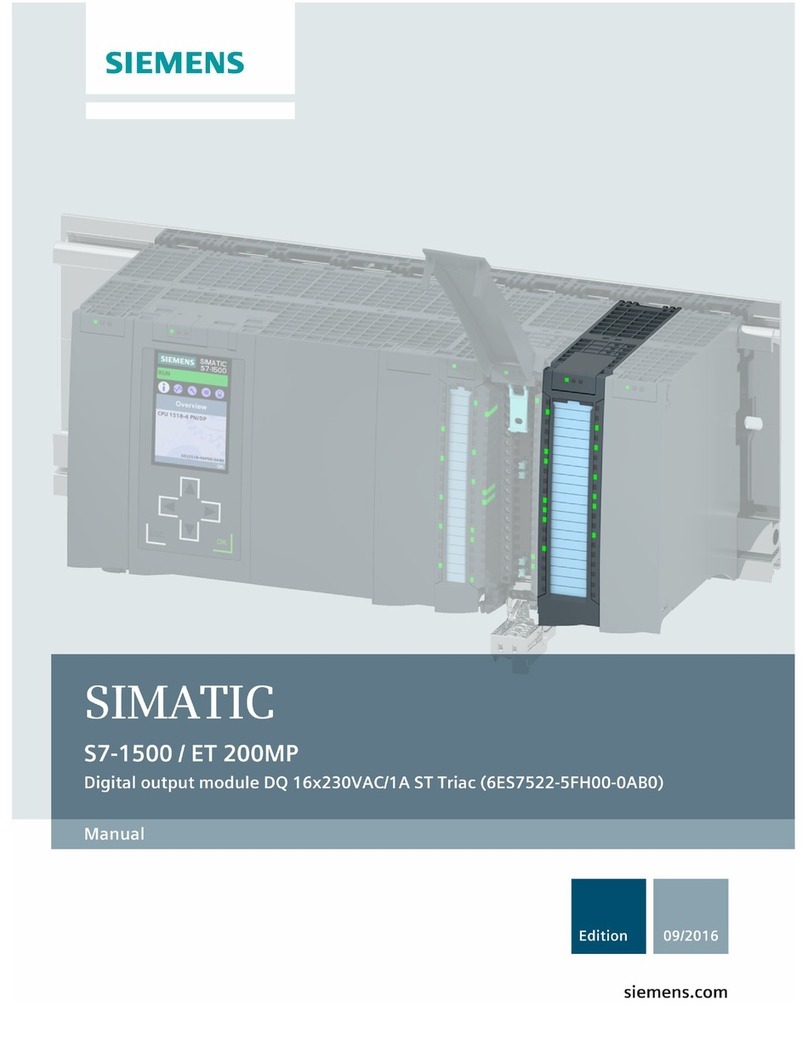
Siemens
Siemens Simatic S7-1500 manual

Wolf
Wolf BM-Solar Installation and operating instructions
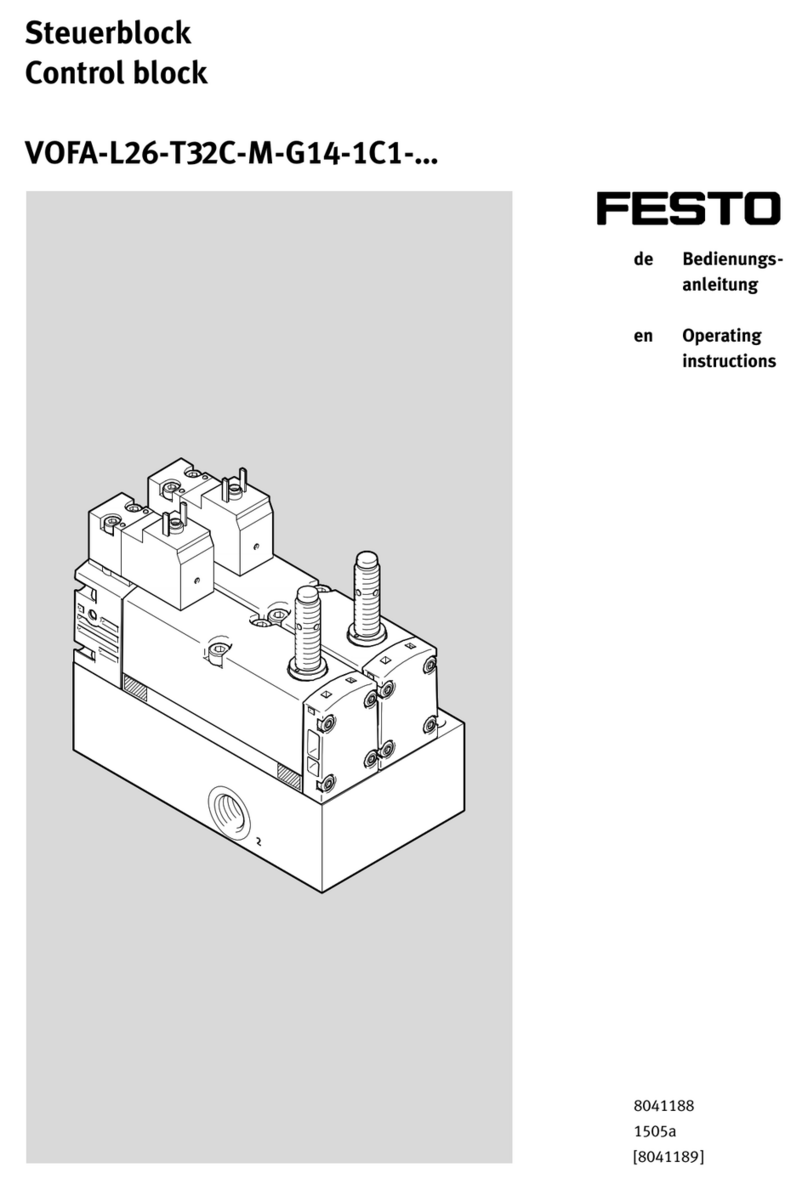
Festo
Festo VOFA-L26-T32C-M-G14-1C1 Series operating instructions
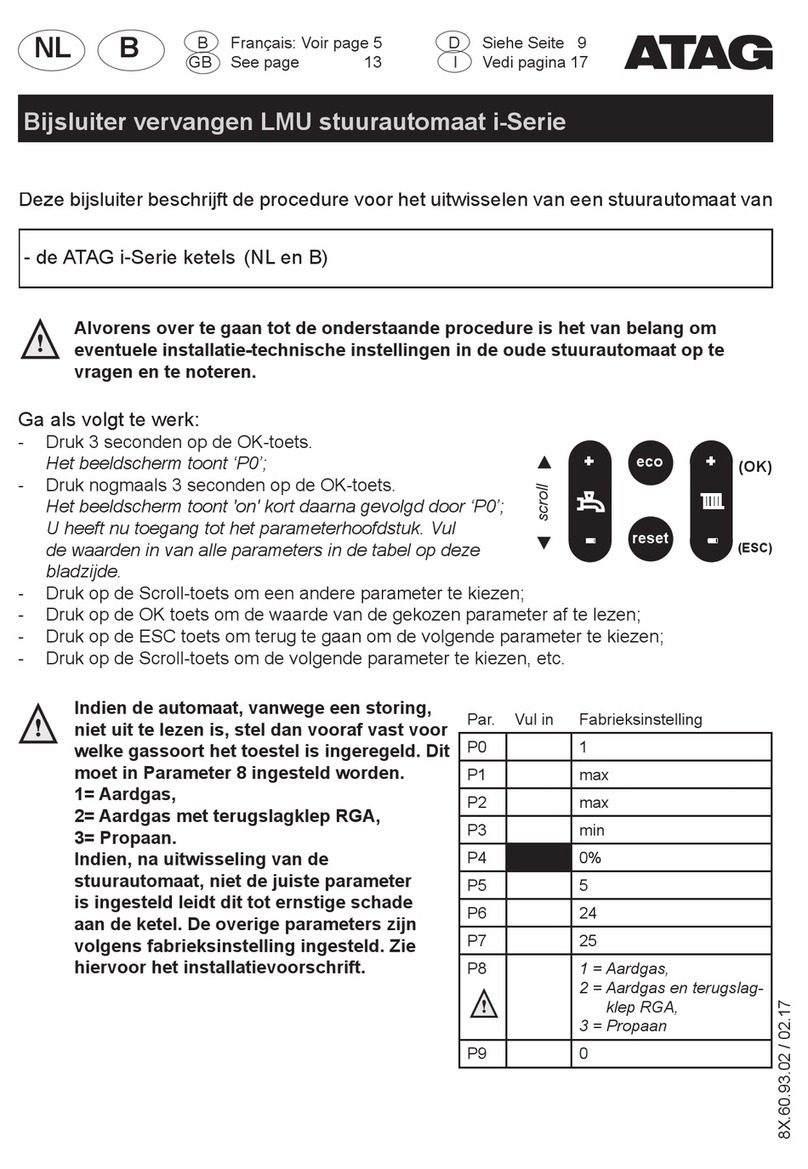
Atag
Atag LMU-C i-Series instructions

Emerson
Emerson ANDERSON GREENWOOD 4020HP Installation, operation and maintenance instructions
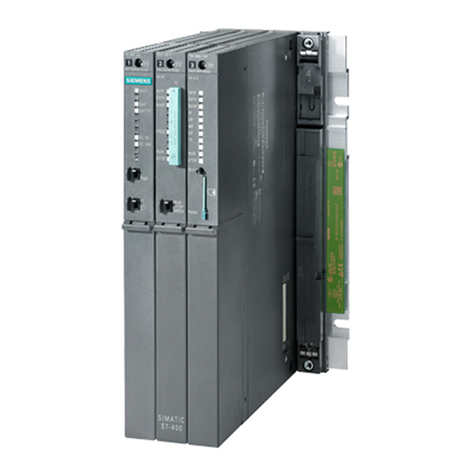
Siemens
Siemens FM 458-1 DP user manual