BRONKHORST E-7000 Series User manual

Instruction manual
Temperature
control system
for CEM
Doc. no.: 9.17.017F Date: 25-07-2011
ATTENTION
Please read this instruction manual carefully before installing and operating the instrument.
Not following the guidelines could result in personal injury and/or damage to the equipment.

BRONKHORST HIGH-TECH B.V.

BRONKHORST HIGH-TECH B.V.
Even though care has been taken in the preparation and
publication of the contents of this manual, we do not
assume legal or other liability for any inaccuracy,
mistake, mis-statement or any other error of whatsoever
nature contained herein. The material in this manual is
for information purposes only, and is subject to change
without notice.
Bronkhorst High-Tech B.V.
July 2011
Warranty
The products of Bronkhorst High-Tech B.V. are
warranteed against defects in material and workmanship
for a period of three years from the date of shipment,
provided they are used in accordance with the ordering
specifications and the instructions in this manual and
that they are not subjected to abuse, physical damage or
contamination. Products that do not operated properly
during this period may be repaired or replaced at no charge.
Repairs are normally warranteed for one year or the balance
of the original warranty, whichever is the longer.
See also paragraph 9 of the Conditions of Sales.
The warranty includes all initial and latent defects, random
failures, and indeterminable internal causes.
It excludes failures and damage caused by the customer,
such as contamination, improper electrical hook-up, dropping
etc.
Re-conditioning of products primarily returned for warranty
service that is partly or wholly judged non-warranty may be
charged for.
Bronkhorst High-Tech B.V. prepays outgoing freight charges
when any part of the service is performed under warranty,
unless otherwise agreed upon beforehand. However, if the
product has been returned collect to Bronkhorst High-Tech
B.V., these costs are added to the repair invoice. Import
and/or export charges, foreign shipping methods/carriers are
paid for by the customer.

BRONKHORST HIGH-TECH B.V.

BRONKHORST HIGH-TECH B.V.
TABLE OF CONTENTS
1 INTRODUCTION.....................................................................................................7
1.1 General description.............................................................................................................................7
1.2 System configuration..........................................................................................................................7
1.3 Modul configuration ............................................................................................................................9
1.4 In/Output signals.................................................................................................................................9
1.4.1 Rear panel connector .......................................................................................................................10
1.4.2 Connection to remote equipment, I/O...............................................................................................10
1.4.2.1 Analog input/output signals...............................................................................................................10
1.4.2.2 Relay contacts ..................................................................................................................................10
1.4.2.3 Reset input........................................................................................................................................11
1.4.3 CEM connector.................................................................................................................................11
1.5 Connector panel 1000 Watt power supply........................................................................................12
1.5.1 EMC and cables ...............................................................................................................................12
1.6 Readout and control unit CEM 120 Vac / 230 Vac power supply.....................................................12
2 OPERATION.........................................................................................................15
2.1 Foreword...........................................................................................................................................15
2.2 General information..........................................................................................................................15
2.3 Startup and menu selection..............................................................................................................16
2.4 Measure menu..................................................................................................................................18
2.5 Operation menu................................................................................................................................20
2.6 Reset menu ......................................................................................................................................22
2.7 Alarm menu ......................................................................................................................................24
2.8 Instrument menu...............................................................................................................................26
2.9 Local menu.......................................................................................................................................28
2.10 FLOW-BUS menu.............................................................................................................................30
2.11 Calibration with polynomial functions................................................................................................32
2.11.1 General information..........................................................................................................................32
2.11.2 General form.....................................................................................................................................32
2.11.3 Polynomial functions of sensor signal and setpoint..........................................................................32
2.11.4 Presentation of parameters ..............................................................................................................32
2.11.5 Using polynomial functions at readout/control unit ...........................................................................33
3 MAINTENANCE....................................................................................................33
4 TROUBLESHOOTING..........................................................................................33

BRONKHORST HIGH-TECH B.V.

BRONKHORST HIGH-TECH B.V.
9.17.017 page 7
1 INTRODUCTION
1.1 General description
The Bronkhorst High-Tech B.V. serie E-7000 is a modular built digital readout and control system for mass
flow/pressure sensors and controllers. Basically a system consists of one or more (14TE) single channel
readout/control units.
The CEM temperature controllers are capable to control and to power the heater section of CEM systems
(Controlled Evaporator Mixer).
1.2 System configuration
Housing Supply Module A Module B Module C
E-7 # # 0 - ## - ## - ## - … etc.
Housing Code
½ 19" table top (42 TE) 1
½ 19" table top (84 TE) 2
½ 19" rack (42 TE) 3
½ 19" rack (84 TE) 4
Table top cassette (14 TE) 5
Panel mount cassette (14 TE) 6
Other/Specifiy 9
Supply voltage Code
100 ... 240 Vac 0
220 ... 240 Vac 1
110 ... 120 Vac 2
24 Vac 3
24 Vdc 4
Other/Specify 9

BRONKHORST HIGH-TECH B.V.
page 8 9.17.017
Modules with blind front (14 TE) Code
Blind front only 01
Blind front + power supply (linked to module with mains entr.) 03
Blind front + power supply + mains entrance (incl. cable) + FLOW-BUS connection 04
Blind front + power supply + RJ45 conn. for +15Vdc supply voltage + mains entrance
(incl. cable) 05
Blind front + power supply + RJ45 conn. for +15Vdc supply voltage (linked to module
with mains entrance) 06
Modules with single channel Readout/Control-panel (14 TE) Code
R/C-panel + power supply + mains entrance (incl. cable) analog model 10
R/C-panel + power supply (linked to module with mains entry) analog model 11
R/C-panel (linked to module with power supply) analog model 12
R/C-panel + power supply + mains entrance (incl. cable) digital model 13
R/C-panel + power supply (linked to module with mains entry) digital model 14
R/C-panel (linked to module with power supply) digital model 15
Modules with R/C-panel and Ex-proof functions (14 TE) ** Code
R/C-panel + transmitter supply unit for MFM/EPT (Ex-proof) 20
R/C-panel + supply for MFM/EPT (Ex-proof) + valve with XB-coil 21
R/C-panel + supply for MFM/EPT (Ex-proof) + valve with XC-coil 22
Modules for temperature control for CEM-systems (14TE) Code
Temp. R/C-panel + 10 W supply for low capacity CEM-system for W-101 / W-102 33
Temp. R/C-panel + 10 W supply for low capacity CEM-system for W-202 34
Temp. R/C-panel excl. supply for high capacity CEM-system * for W-303 35
R/C-panel (E7000)+ 1000W supply / 230Vac operation for W-303 36
R/C-panel (E7000)+ 1000W supply / 120Vac operation for W-303 37
Blind front + Flow-Bus/RS232 Interface 40
Blind front + Flow-Bus/Profibus-DP Interface 41
None 00
Other/Specify 99
* 1000W power supply will be supplied and charged separately
** Always in combination with powermodule

BRONKHORST HIGH-TECH B.V.
9.17.017 page 9
1.3 Modul configuration
Module X Sensor
Out IO
Output IO
Input
## - # # #
Module
See table Modules, System configuration
*Sensor output signal Code
0 - 5 Vdc A
0 - 10 Vdc B
0 - 20 mA dc (Sinking) C
4 - 20 mA dc (Sinking) D
15 - 20 mA dc E
0 - 20 mA (Sourcing) F
4 - 20 mA (Sourcing) G
FLOW-BUS R
Other/Specify Z
*Not applicable for CEM modules.
I/O output signal Code
0 - 5 Vdc A
0 - 10 Vdc B
0 - 20 mA (Sourcing) C
4 - 20 mA (Sourcing) D
Other/Specify Z
I/O input signal Code
0 - 5 Vdc A
0 - 10 Vdc B
0 - 20 mA (Sourcing) C
4 - 20 mA (Sourcing) D
Other/Specify Z
The temperature control unit offers the ability to set the desired temperature for the heater system of the
CEM. The temperature inside the CEM is monitored with a PT-100 temperature sensor, the signal of which is
being used by the temperature controller to control the adjusted temperature.
Power for the CEM heater is provided for by the R/C module.
For safety reasons the CEM heater W-300 42 Vac is powered with 42 Vac. Because of the high currents
involved, the high power CEM (1000 Watt) has a separate power supply, which is being controlled by the
temperature R/C module, intended for use with this system.
The power for the CEM heater W-300 direct 120 Vac / 230 Vac power supply operation is provided by the
R/C module and does not require a separate power supply.
For detailed information consult manual 9.17.042.
1.4 In/Output signals
If applicable, connection of cables, carrying in- or/and output signals is further explained in the customer
system description.

BRONKHORST HIGH-TECH B.V.
page 10 9.17.017
1.4.1 Rear panel connector
1.4.2 Connection to remote equipment, I/O.
The female I/O (sub-miniature 9-pin) D-connector has the following pin configuration:
Pinnumber description
1
2
3
4
5
6
7
8
9
output signal
input signal
0 V (common)
not connected
relay contact MC
relay contact NO
relay contact NC
reset input
ground (shield)
1.4.2.1 Analog input/output signals
Analog input signals should be connected to pin 2 (+) and 0 V/common.
Analog output signals are available at pin 1 (+) and 0 V/common.
Signals are according to one of the Bronkhorst HIGH-TECH B.V. standards. The model configuration
contains a code, describing the input/output signals.
Notes:
a. Max. load current output (sourcing) : 375 Ohm
b. Min. load voltage output : 10 kOhm
c. Input load resistance (voltage) : 22K4
d. Input load resistance (current) (sinking) : 200 Ohm
1.4.2.2 Relay contacts
The (isolated) relay contacts are available at the following pins:
pin 5: common
pin 6: normally open
pin 7: normally closed
Note: contact arrangement during "power on"/"no alarm".
The specifications of the relay contacts are:
Contact arrangement : SPCO (Single Pole Changeover)
Contact rating : Switch voltage : 24 Vac/dc max.
Switch current : 0,2 A ac/dc max.
Switch power : 3 W/3 VA max.

BRONKHORST HIGH-TECH B.V.
9.17.017 page 11
1.4.2.3 Reset input
The reset input signal should be connected to pin 8 (+ V) and pin 3 (0 V/common).
Reset can be achieved by either pulling the + V input (pin 8) to 0 V (pin 3) by means of a contact or a
transistor, or by applying an active low logic signal to pin 8 (+ V) and pin 3 (0 V). The logic signal level should
be 5 V (high) or 0 V (low).
1.4.3 CEM connector for modules 33,34 and 35.
Pinnumber description
A
B
C
D
E
F
heater
heater
PT100 (T-sensor)
PT100 (T-sensor)
safety switch
safety switch

BRONKHORST HIGH-TECH B.V.
page 12 9.17.017
1.5 Connector panel 1000 Watt power supply 42Vac power supply
mains
input
(1)
from T-control
module
(2)
to CEM (3)
to CEM
(male) (female)
Connector panel separate power supply
connector (1)
Pinnumber description
A
B
C
D
E
F
NC
NC
PT100 (T-sensor)
PT100 (T-sensor)
Heater control signal
Heater control signal
connector (2)
pinnumber Description
A
B
C
D
E
F
NC
NC
PT100 (T-sensor)
PT100 (T-sensor)
safety switch
safety switch
connector (3)
Pinnumber description
A
B
C
D
E
F
Heater 1
NC
Heater 2
Heater 1
NC
Heater 2
1.5.1 EMC and cables
All system setups described in this manual carry the CE-mark. Therefore they have to comply with the EMC
requirements as are valid for this kind of equipment.
However compliance with the EMC requirements is not possible without the use of proper cables and
connector assemblies.
For good results Bronkhorst HIGH-TECH B.V. can provide standard cables. Otherwise follow the guidelines
as stated below. For cables with 9-pin sub D-connectors:

BRONKHORST HIGH-TECH B.V.
9.17.017 page 13
Fold the shield of the cable back over the cable (the shield must be around the cable).
Wind a copper tape around the shield
Solder a black wire on the tape and
connect to pin 9 of connector
copper tape
shielded cable
e.g. LAPP LiYCY
other wires D-connector housing
metalized
connector
8 mm
20 mm
black wire
(shield)
NOTE:
For FLOW-BUS SFTP data (patch)cable connection to RJ45 connectors follow the instructions of the
supplier. It is important to use shielded twisted pair cables and shielded RJ45 modular jack connectors.
1.6 Readout and control unit CEM 120Vac / 230Vac power supply
For information of the direct 120Vac / 230Vac operation CEM unit consult manual 9.17.042.

BRONKHORST HIGH-TECH B.V.
page 14 9.17.017

BRONKHORST HIGH-TECH B.V.
9.17.017 page 15
2 OPERATION
2.1 Foreword
This part describes the operation manual for an E7000 based R/C panel (module code 33,34,35,36 and 37).
2.2 General information
Use 'cursor' keys to scroll through the menu-structure and to select the required menu level.
The 'enter' key is used to acknowledge a selected setting and to enter a edited value and/or text.
Editing can be performed by using the 'cursor' keys to select the character to be edited ( ←/ →) and to scroll
through the available character set or units ( ↑/ ↓).
After power-up the display will show the usual start-up sequence for some seconds.

BRONKHORST HIGH-TECH B.V.
page 16 9.17.017
2.3 Startup and menu selection

BRONKHORST HIGH-TECH B.V.
9.17.017 page 17
Menu descriptions
0001 0000 Startup screen showing company name
0002 0000 Startup screen showing communication check with FLOW-BUS in progress. Takes a short time
(few seconds), depending on system size. If the FLOW-BUS address of the module is occupied,
you can reinstall the module on a new address.
0003 0000 Startup screen showing software revision level
1000 0000 Measure menu or ‘Readout Display’ for reading the temperature and/or setpoint. When there is
an alarmlimit reached it will be shown here. For editing the setpoint/slave factor go down one
level.
2000 0000 Operation menu for selecting setpoint source (and master/slave), fluidset and setpoint slope for
the device to be operated. Also for editing setpoint offset.
3000 0000 Reset menu for quick reset of the alarm by keyboard. Also password input location to enable
advanced use of this module.
5000 0000 Alarm menu for configuration of all alarm options. This menu is secured by means of a
password.
6000 0000 Instrument menu for configuration of the instrument to be operated, such as instrument type,
capacity, sensor type, identification and fluid sets with calibration values. This menu is secured
by means of a password.
7000 0000 Readout menu for configuration of the measure menu. You can select the wanted information for
your display.
8000 0000 FLOW-BUS menu to install module on the FLOW-BUS or start/stop communication with the bus.
This menu is secured by means of a password.

BRONKHORST HIGH-TECH B.V.
page 18 9.17.017
2.4 Measure menu

BRONKHORST HIGH-TECH B.V.
9.17.017 page 19
Menu descriptions
1100 0000 Stepsize editor for editing setpoint/slave-factor by a 0.1% step up or down. By holding down
UP/DOWN key continuously, the step size will increase. Changes are used by the controller
immediately. What is displayed here in this menu depends on the selection of the setpoint
source. Analog setpoints can not be edited.
1200 0000 Cursor editor for editing setpoint/slave-factor by entering the exact (new) value. After pressing
'enter', the changes will be used by the controller. Could be used for large setpoint steps. What is
displayed here in this menu depends on the selection of the setpoint source. Analog setpoints
can not be edited.
1300 0000 Setpoint full. After pressing 'enter', setpoint for controller will be 100% unconditionally (controller
valve will be opened in almost all situations).
1400 0000 Setpoint zero. After pressing 'enter', setpoint for controller will be zero unconditionally (controller
valve will be closed in almost all situations). You will return to the readout display now.
Setpoint will not respond to selected source again until 'enter' has been pressed in the edit
setpoint menu.
NOTE:
Measured values could be readout up to 110.0%, sensor signals > 110.0% will be cut-off.
Setpoint can be entered up to 100.0%. Also you can use setpoint offset correction to eleminate cable offsets
in your system (see operation menu).

BRONKHORST HIGH-TECH B.V.
page 20 9.17.017
2.5 Operation menu
Table of contents
Other BRONKHORST Control System manuals
Popular Control System manuals by other brands
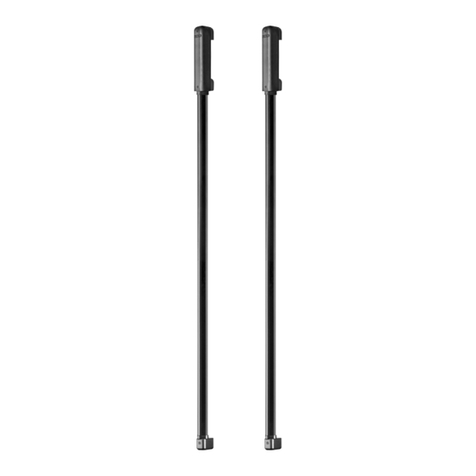
Elkron
Elkron ELR600RT/10 manual
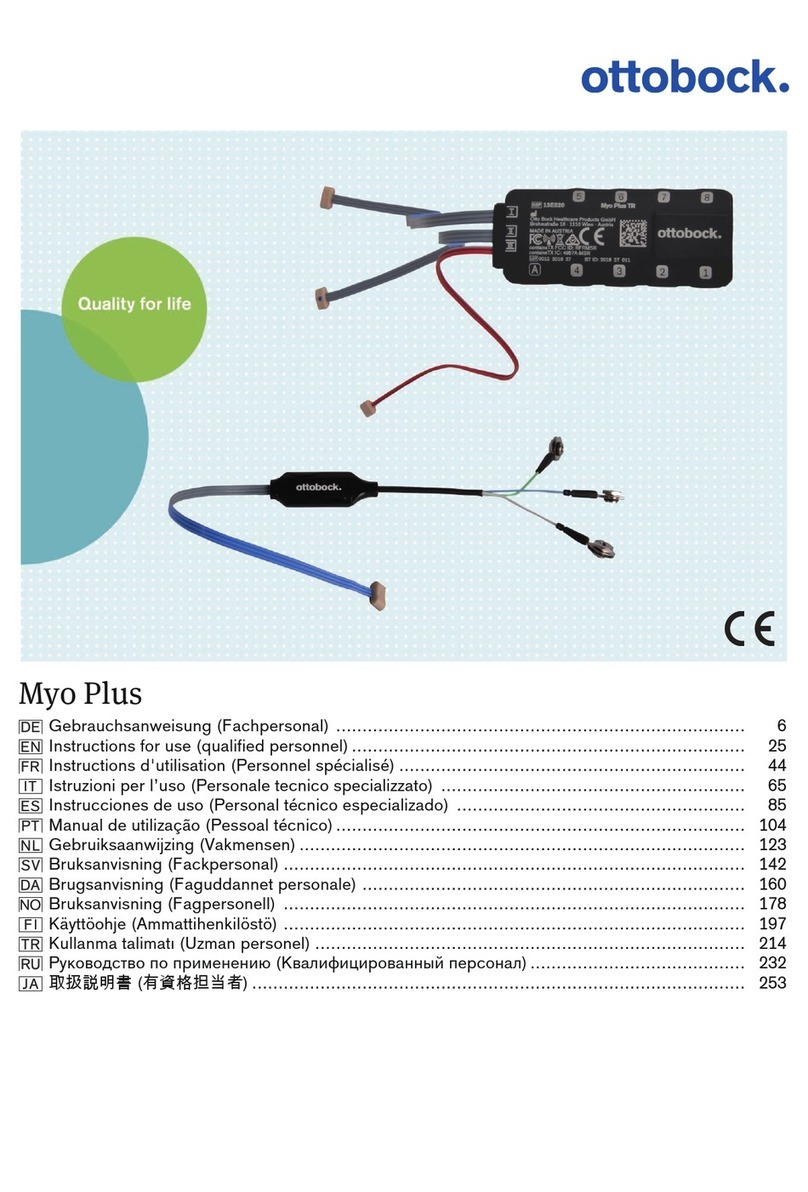
Otto Bock
Otto Bock Myo Plus TR Instructions for use
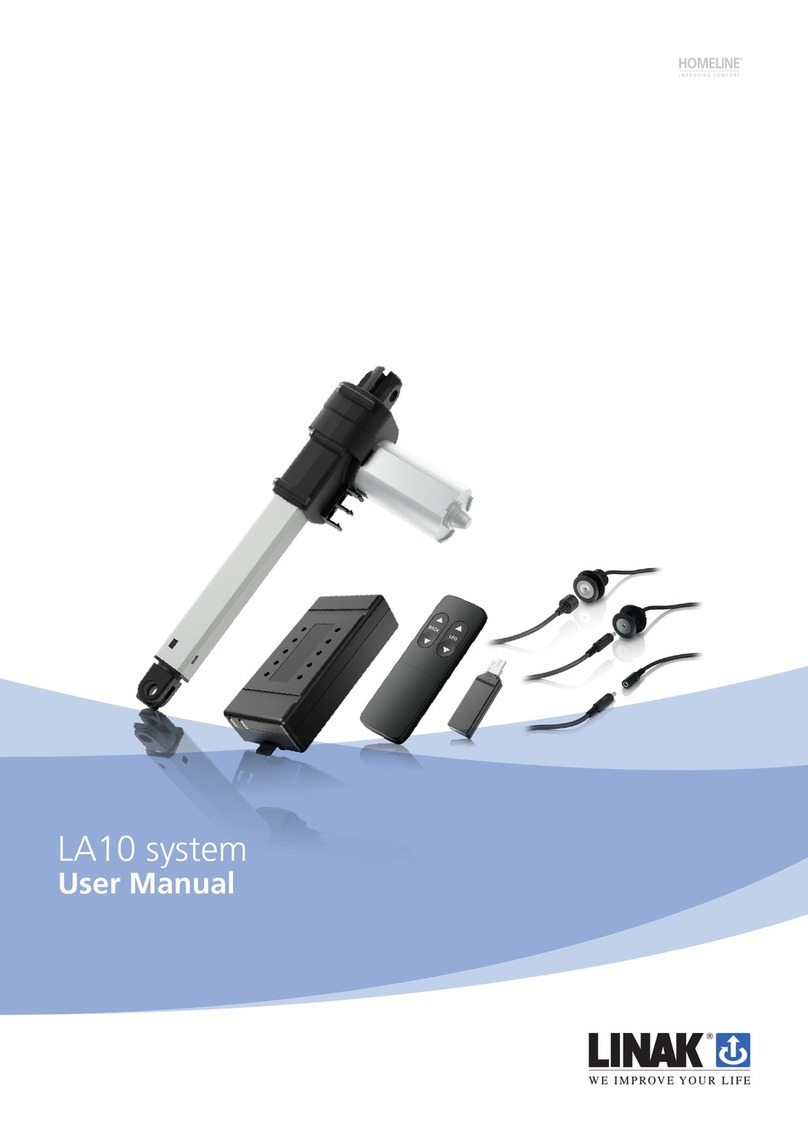
Linak
Linak Homeline LA10 user manual
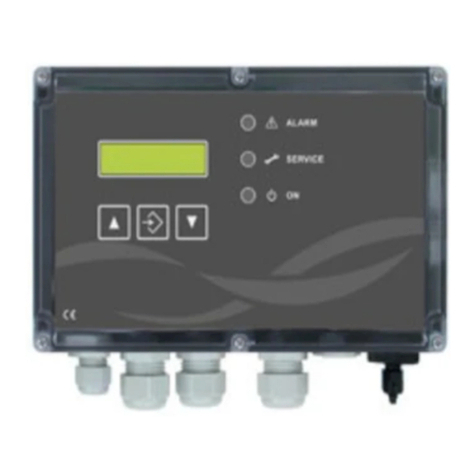
RECO
RECO EasyLine RM-216 CB.11 Operating and installation instructions

LEGRAND
LEGRAND Pass & Seymour Harmony De-Hummer installation instructions
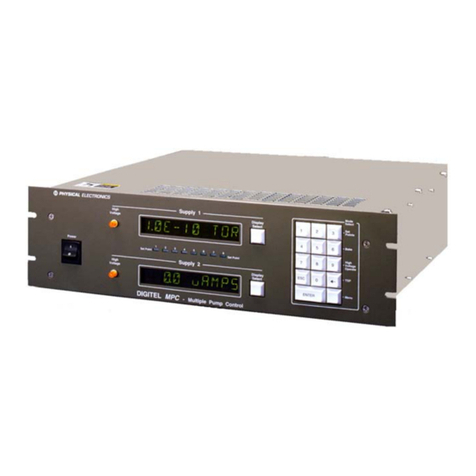
Gamma Vacuum
Gamma Vacuum Digitel MPC 635941 Technician manual

OBSIDIAN CONTROL SYSTEMS
OBSIDIAN CONTROL SYSTEMS NETRON EN12 installation guide
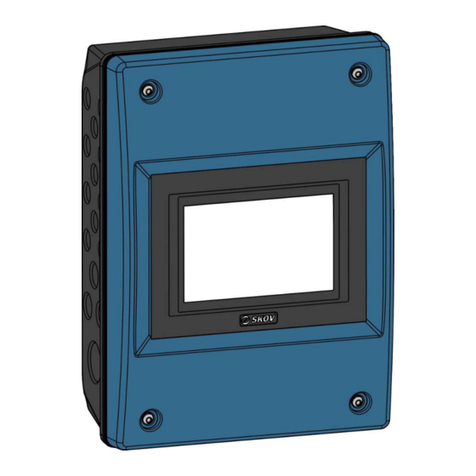
Skov
Skov FarmOnline+ DataLink 131545 Technical user guide

Tekmar
Tekmar 364 Data brochure
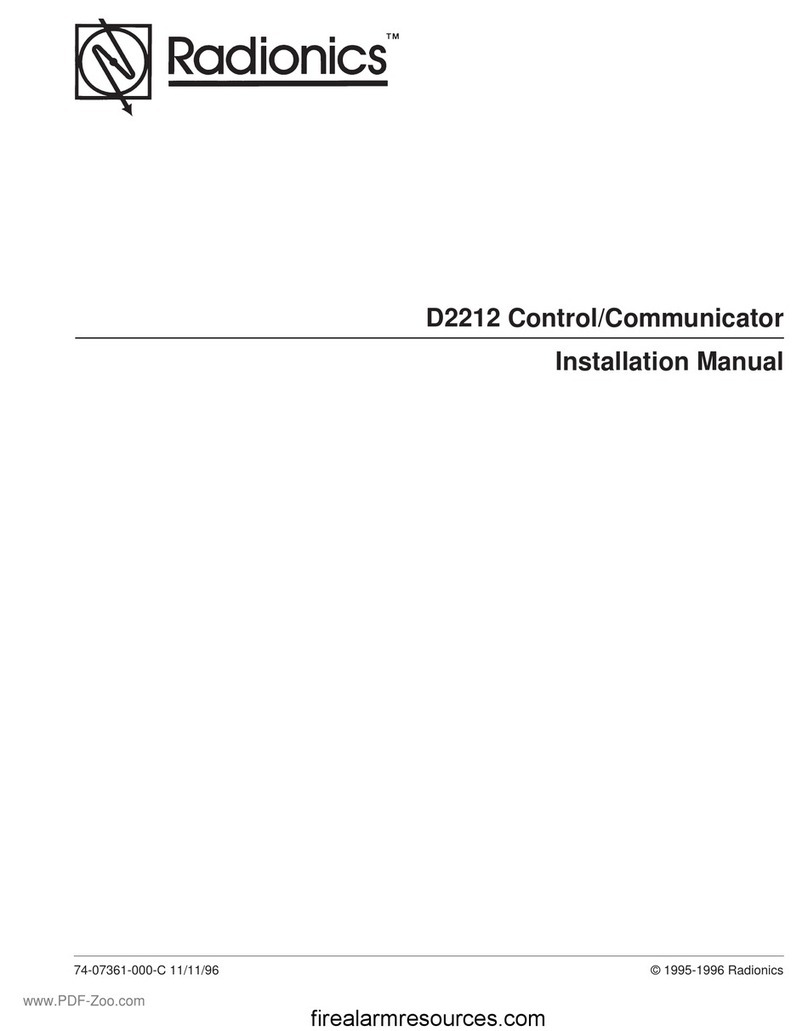
Radionics
Radionics D2212 installation manual
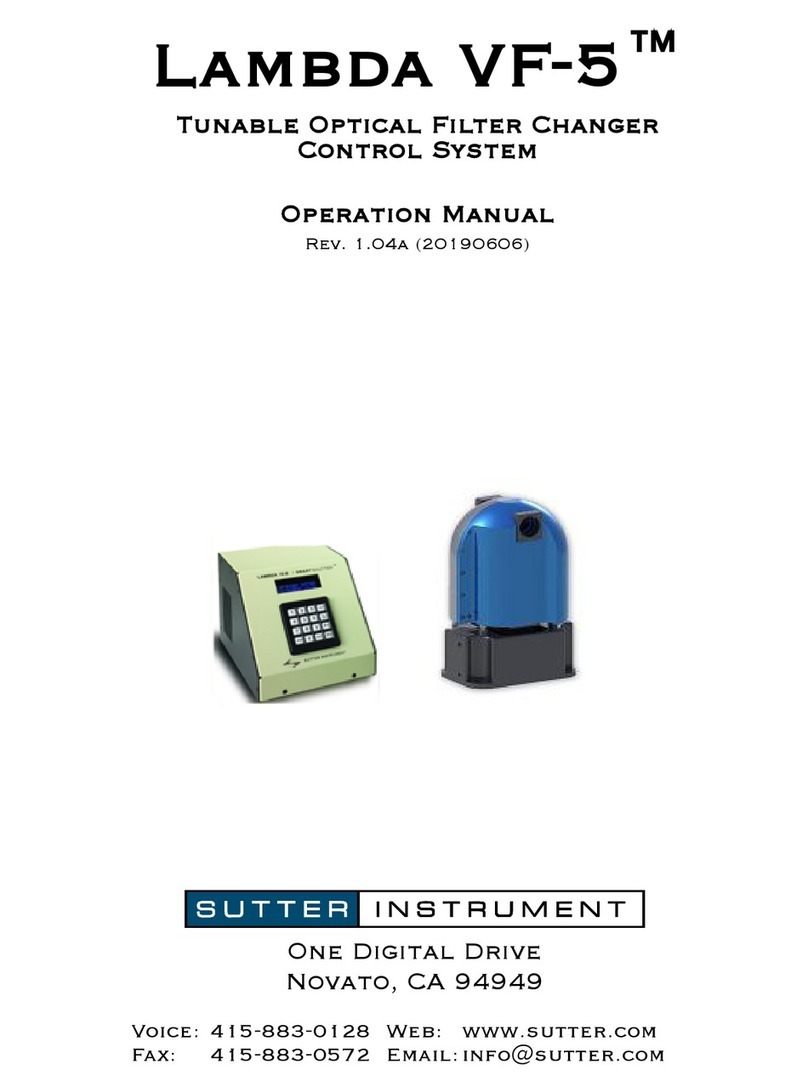
Sutter
Sutter Lambda VF-5 Operation manual
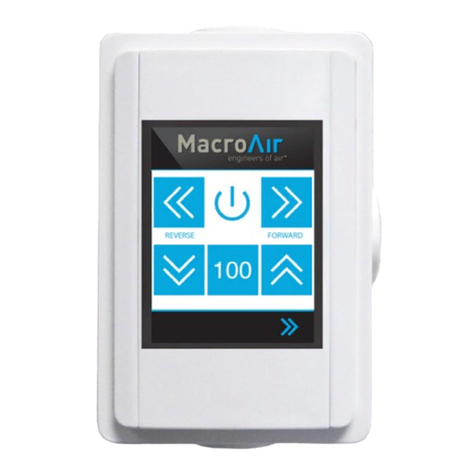
MacroAir Technologies
MacroAir Technologies Controller 4 Operation manual