Cedes CabSafe 3D User manual

115 944 en | 200820 | V1.0
CabSafe 3D Sensor & Controller
Installation and Operation Manual
CEDES AG is certified according to ISO 9001: 2015
English Pages 2 - 14

CabSafe 3D Sensor & Controller English
© CEDES | V 1.0 CEDESAG reserves the right to modify or change technical data without prior notice. 2/28
Contents
1 About this manual..................................... 2
1.1 Measurements ..............................................2
1.2 Related documents.......................................2
1.3 CEDES headquarters ...................................2
2 Safety information .................................... 3
2.1 Non-intended use..........................................3
2.2 Intended use .................................................3
3 Symbols, safety messages....................... 3
3.1 Symbols ........................................................3
3.2 Safety message category .............................3
4 Introduction CabSafe System..................4
4.1 CabSafe System Overview...........................4
4.2 General Operation ........................................5
5 CabSafe Controller.................................... 5
5.1 Overview.......................................................5
5.2 Features........................................................6
5.3 Safety Instructions ........................................6
5.4 System integration ........................................6
5.5 Mechanical installation..................................6
5.6 Electrical connection.....................................7
5.7 Door position signal ......................................8
5.8 Functional selection DIP switches ................8
5.8.1 Settings for the 3D sensor mounting position.8
5.8.2 Settings for the door position detection ..........8
5.8.3 Settings for the door opening height:..............9
5.8.4 Settings for the 2D versus 3D Active:.............9
5.8.5 Output logic selector.......................................9
5.8.6 Operation frequency selector..........................9
5.9 Timing diagram .............................................9
5.10 Controller output logic.................................10
5.11 Startup CabSafe Controller.........................10
5.12 LED status description................................10
5.13 Trouble Shooting.........................................12
5.14 Product label...............................................12
5.14.1 Product label Controller PCB........................12
5.14.2 Product label Controller Box.........................12
5.15 Maintenance................................................13
5.16 Type description Controller.........................13
5.17 Delivery package ........................................13
5.18 Accessory magnet switch ...........................13
5.19 Technical data CabSafe Controller .............15
5.19.1 Mechanical...................................................15
5.19.2 Environmental...............................................15
5.19.3 Operation characteristics..............................15
5.19.4 Connectors...................................................16
5.19.5 General.........................................................16
5.20 Dimensions CabSafe Controller..................16
5.20.1 Dimensions PCB solution.............................16
5.20.2 Dimensions Box solution..............................17
6 CabSafe 3D sensor................................. 17
6.1 Overview CabSafe 3D sensor.....................17
6.2 Features of the CabSafe 3D sensor: ..........17
6.3 Type description CabSafe 3D sensor kit.....17
6.4 Safety information.......................................18
6.4.1 Non-intended use.........................................18
6.4.2 Hazards of laser radiation.............................18
6.5 Installation CabSafe 3D sensor ..................18
6.5.1 Field of application .......................................18
6.5.1.1Elevator door widths and heights............18
6.5.1.2Glass door elevators...............................18
6.5.2 Mechanical installation.................................19
6.5.3 Mounting position.........................................19
6.5.3.1Center opening door...............................19
6.5.3.2Side opening door (left or right):.............19
6.5.3.3Mounting distance to the door ................20
6.5.4 Mounting brackets........................................20
6.5.4.1Dimensions flush mounting bracket........21
6.5.4.2Cut out for flush mounting.......................21
6.5.4.3Mounting plate kit....................................21
6.5.4.4Back transom mounting..........................22
6.6 Electrical connection CabSafe 3D ..............22
6.7 Field of view ................................................22
6.8 Timing diagram............................................24
6.9 Start-up CabSafe 3D...................................25
6.10 LED status description................................25
6.11 Troubleshooting ..........................................25
6.12 Maintenance................................................25
6.13 Product label ...............................................26
6.14 Technical Data CabSafe 3D sensor............26
6.14.1 Mechanical...................................................26
6.14.2 Environmental..............................................26
6.14.3 Operation characteristics..............................27
6.14.4 Connection cable and connectors................27
6.14.5 General ........................................................27
6.15 Dimensions CabSafe 3D sensor.................28
7 Disposal...................................................28
1 About this manual
This installation and operation manual in English, with
metric measurements is the original version.
The version number is printed at the bottom of each
page.
To make sure you have the latest version, check the
product page on www.cedes.com..
1.1 Measurements
Measurements are, if not stated otherwise, given in
mm (non-bracketed numbers) and imperial dimen-
sions (numbers in brackets).
1.2 Related documents
116 101 CE confirmation
116 106 Operating manual cegard/Pro CabSafe 2D
Light Curtain
1.3 CEDES headquarters
CEDES AG
Science Park
CH-7302 Landquart
Switzerland

CabSafe 3D Sensor & Controller English
© CEDES | V 1.0 CEDESAG reserves the right to modify or change technical data without prior notice. 3/28
2 Safety information
IMPORTANT READ BEFORE IN-
STALLATION!
The CabSafe system was developed and manufac-
tured using state-of-the-art systems and technolo-
gies. However, injury and damage to the sensor can
still occur.
To ensure safe conditions:
►Read all enclosed instructions and information.
►Follow the instructions given in this manual care-
fully.
►Observe all warnings included in the documenta-
tion and attached to the sensor.
►Do not use the sensor if it is damaged in any way.
►Keep the instruction manual on site.
The CabSafe system should only be installed by au-
thorized and fully trained personnel! The installer or
system integrator is fully responsible for the safe inte-
gration of the sensor. It is the sole responsibility of the
planner and/or installer and/or buyer to ensure that
this product is used according to all applicable stand-
ards, laws and regulations in order to ensure safe op-
eration of the whole application.
Any alterations to the device by the buyer, installer or
user may result in unsafe operating conditions.
CEDES is not responsible for any liability or warranty
claim that results from such manipulation.
Failure to follow instructions given in this manual
and/or other documents related to the CabSafe sys-
tem may cause customer complaints, serious call
backs, damage, injury or death.
2.1 Non-intended use
The CabSafe system must not be used for:
·Protection of dangerous machine such as
presses
·Equipment in explosive atmospheres
·Equipment in radioactive environments
·Outside the specified environments
Figure 1: Non-intended use
Use only specific and approved safety devices for
such applications, otherwise serious injury or death
or damage to property may occur!
2.2 Intended use
The CabSafe 3D Time-of-Flight (TOF) sensor, the ce-
gard/Pro (CabSafe 2D) light curtain, and the CabSafe
Controller are the components that make up a
CabSafe system. The CabSafe system is intended to
safeguard automatic doors in elevator applications
where it detects persons or objects approaching the
elevator door as well as persons or objects standing
between the elevator doors. All other applications
must be approved by CEDES.
3 Symbols, safety messages
3.1 Symbols
Symbol Meaning
►Single instruction or measures in
no particular order
1.
2.
3.
Sequenced instructions
·List, in no order of importance
èReference to a chapter, illustration
or table within this document
Im-
portant Important information for the cor-
rect use of the sensor
3.2 Safety message category
Warning of serious health risks
WARNING
Serious health risks
Highlights critical information for the safe use of the
sensor. Disregarding these warnings can result in
serious injury or death.
►Follow the measures highlighted by the triangle-
shaped arrows
►Consult the safety information in Chapter 2 of
this manual
Caution of possible health risk
CAUTION
Possible health risks
Highlights critical information for the safe use of the
sensor. Disregarding these warnings can result in
injury.

CabSafe 3D Sensor & Controller English
© CEDES | V 1.0 CEDESAG reserves the right to modify or change technical data without prior notice. 4/28
►Follow the measures highlighted by the triangle-
shaped arrows
►Consult the safety information in Chapter 2 of
this manual
Notice of damage risk
CAUTION
Possible health risks
Disregarding these notices can lead to damage to the
sensor, the door controller and/or other devices.
►Follow the measures highlighted by the triangle-
shaped arrows
4 Introduction CabSafe System
The CabSafe System provides a complete elevator
door protection solution that complies with ASME
A17.1-2019 / CSA B44:19 Safety Code for Elevators
and Escalators when installed in compliance with
these operating instructions. The CabSafe System
consists of:
·A CabSafe Controller
·A cegard/Pro Light Curtain (hereafter referred to
as the CabSafe 2D) to detect persons or objects
between the elevator doors; and
·A CabSafe 3D Time-of-Flight Sensor to detect per-
sons or object approaching the elevator entrance.
The CabSafe system is designed for and can be used
in center-opening as well as left- or right-side opening
elevator door applications. It is suitable for both dy-
namic and static light curtain installations.
The CabSafe Controller:
·Performs continuous testing of the CabSafe 2D
and CabSafe 3D sensor
·Logically combines the signals from the CabSafe
sensors into one output to elevator control
·Manages configuration parameters for the
CabSafe system.
This documentcontains the technical specifications of
the CabSafe 3D sensor and the CabSafe Controller
and their installation procedure. The technical speci-
fication of the CabSafe 2D light curtain is provided in
the separate CEDES user manual 116 106.
The CabSafe Controller tests the function as well as
detects the signals from the entrance area sensor and
the light curtain together. Depending on an internal
sequencing, the CabSafe Controller either holds the
door open, allows it to reverse or allows it to close.
The comfort of the CabSafe system improves due to
contactless detection of approaching persons with a
simultaneous increase in the availability of the cabin.
The CabSafe 3D detection field is automatically ad-
justed during movement of the door(s). When in-
stalled correctly, the CabSafe 3D sensor is rendered
inoperative 450 mm (17.72 in.) before full door clo-
sure based on the
·the CabSafe 2D light curtain (only for dynamic in-
stallations);
·a door position signal from the door control; or
·a door position switch (e.g. magnetic or optical
sensor)
The CabSafe system is designed and developed to
fulfill the requirements of the ASME A17.1-2019 /
CSA B44:19 and previous versions of the Elevator
and Escalator Safety Code. For correct function, only
system components described in this document and
the cegard/Pro (CabSafe 2D) Installation and Opera-
tion Manual (see CEDES document 116 106) shall be
used.
WARNING
Door protection systems, such as the CabSafe
System, do not provide absolute safety for elevator
passengers passing through the doorway. They
cannot be used as failsafe devices of the door
mechanism. This safety function must be provided
by a fail-safe force and a kinetic energy limiter by
the door drive.
4.1 CabSafe System Overview
Figure 2 shows the principal of the CabSafe System
architecture. The CabSafe 2D transmitter (Tx),
receiver (Rx) and the CabSafe 3D sensor are all
connected to the CabSafe Controller.

CabSafe 3D Sensor & Controller English
© CEDES | V 1.0 CEDESAG reserves the right to modify or change technical data without prior notice. 5/28
CabSafe-
Controller
CabSafe-3D
Elevator controller
cegard/Pro
CabSafe-2D Rx
cegard/Pro
CabSafe-2D Tx
Figure 2: Principal CabSafe system architecture
The following chapters provide a description for
following components:
CabSafe Controller Chapter 5
CabSafe 3D sensor Chapter 6
For a description of the cegard/Pro (CabSafe 2D) light
curtain, please refer to the cegard/Pro Installation and
Operating Instructions: CEDES part number 116 106.
4.2 General Operation
The operating sequence of the CabSafe System be-
gins with the opening of the elevator door(s). As this
occurs, the CabSafe System is initialized by a signal
from one of the following:
- the CabSafe 2D light curtain (dynamic installa-
tion only);
- the elevator control; or
- a door position sensor (e.g. a magnet switch or
a fork type light barrier).
The CabSafe 3D detection field is calibrated within
one second of the doors reaching their fully open po-
sition, and the opening also causes the CabSafe Con-
troller to start monitoring the CabSafe 2D and
CabSafe 3D sensors for the presence of persons or
objects between the elevator doors or approaching
the elevator doors. When a person or object is de-
tected, the output will change state so that the door
operator will reverse the doors or hold them in their
open state.
A timer (3D-time in Figure 8) has been implemented
in the CabSafe controller to minimize the effects of
cross-traffic in the CabSafe 3D detection field. The
timer starts when a person or object is detected ap-
proaching the elevator cab. If this timer expires before
an infringement of the CabSafe 2D (i.e. person or ob-
ject actually entered the elevator cab), objects in the
CabSafe 3D detection field will be ignored. When an
object is detected by the CabSafe 2D, this timer is re-
set. The duration of the timer is as specified in ASME
A17.1-2019 / CSA B44:19 and is currently 20 sec-
onds.
The CabSafe 3D is rendered inoperative once the
doors are less than 450 mm (17.72 in) apart. This dis-
tance is monitored based on a signal from one of the
following:
- the CabSafe 2D light curtain (dynamic installa-
tion only);
- the elevator control; or
- a door position switch (e.g. a magnet switch or a
fork type light barrier) .
After the doors have reached their fully-closed state,
the sequence starts over.
5 CabSafe Controller
5.1 Overview
The CabSafe Controller is responsible for the
communication with the individual components
(CabSafe 2D light curtain and CabSafe 3D sensor). It
provides a signal to the elevator control that indicates
when the elevator door can be closed. The CabSafe
Controller manages regular testing of the CabSafe
components, including when the door has reached its
fully open position. If a CabSafe component fails, the
CabSafe Controller provides a signal to hold the door
open and indicates a fault has occurred.
The CabSafe Controller is available with either a:
- Push-Pull output; or a
- Relay output.
Additionally, each output type is available as a:
- PCB mounted on a PCB carrier (Figure 3a); or
- PCB mounted in an IP 54 enclosure (Figure
3b).

CabSafe 3D Sensor & Controller English
© CEDES | V 1.0 CEDESAG reserves the right to modify or change technical data without prior notice. 6/28
(A) (B)
Figure 3: (a) CabSafe Controller PCB on a PCB carrier, (b) PCB in
a box [Drawings: chapter 0]
5.2 Features
- PCB for new installations or enclosure solution
(IP54) for modernization
- Push-pull or relay version
- One output logically combines the signals from:
ocegard/Pro CabSafe 2D Light Curtain
oCabSafe 3D Sensor
- Different door geometries selectable
5.3 Safety Instructions
WARNING
- Switch off main power to the elevator control
system and mark clearly that the elevator is
out of service.
- Do not mount the CabSafe Controller on the
moving door panel.
- Follow all applicable safety measures.
- Make sure that your installation complies with
all applicable regulations and safety
measures.
- Avoid any damage to the CabSafe Controller
- Observe the ESD protection protocol when re-
moving the PCB from the packaging and dur-
ing installation.
- Don’t drill additional holes into the PCB
- Don’t touch the PCB during operation.
- To avoid mechanical stress to the PCB,
plug/unplug the connectors only when the
PCB is mounted to the PCB carrier or PCB
box.
- Use only appropriate connections to the
CabSafe Controller
- It is prohibited to make any changes to the
CabSafe Controller itself (only DIP switch set-
tings).
- Only the CEDES CabSafe 2D and CabSafe
3D sensors can be connected to a CabSafe
Controller
- Connection cord with a length exceeding 2
meters shall be protected in a raceway.
5.4 System integration
The CabSafe Controller provides DIP switches
(chapter 5.8) to configure
- elevator door types (center and side opening)
- elevator door entrance height
- method to inactivate the CabSafe 3D sensor
when the door is closing
After the
- setting of the DIP switches according to the ele-
vator door type and height,
- the installation of all CabSafe components
- the connection of all CabSafe components to
the CabSafe Controller and
- verification of the detection capabilities of all
CabSafe components
the CabSafe system is ready for use.
5.5 Mechanical installation
The CabSafe Controller box and the CabSafe
Controller carrier can be mounted in any orientation
on a flat surface.
The mounting holes of the PCB carrier (dimensions in
chapter 5.20.1) or the CabSafe Controller Box
(dimensions in chapter 5.20.2) provide a stable and
robust installation. The PCB carrier can also be
snapped on a 45mm DIN rail.
Up to 6 cables can be guided through grommets (two
grommets on three sides of the CabSafe controller
box, see also Figure 3 b). The shipping kit of the
controller contains two types of grommets with
different hole diameter:
4x grommets with Ø4.5mm
2x grommets with Ø3.0mm
The grommets with the smaller diameter should be
used for thinner cables (e.g. for the connection cable
of the cegard/Pro CabSafe 2D transmitter (Tx), white
M8 plug). Depending on the required sealing rate of
the final installation the cables can be guided through
the rubber grommets in different ways:
a. Press the M8 connection plug through the hole
of the grommet
b. Cut the grommet on one side so that the cable
can be inserted from the side and then position
the grommet in the CabSafe controller.
alternatively
c. remove the WAGO plug, guide the cable through
the grommet, reconnect the WAGO plug

CabSafe 3D Sensor & Controller English
© CEDES | V 1.0 CEDESAG reserves the right to modify or change technical data without prior notice. 7/28
Each standard shipping kit also contains two blind
stoppers which can be used if only four or five cables
are connected to the CabSafe controller.
For increased protection against moisture, use a
silicon sealant around the cable entry points and on
the sealing of the cover.
5.6 Electrical connection
1
2
3
4
5
6
7
8
9
10
11
12
ERROR
OUT
3D
LC
NC
NO
Common
USP
GND
Door operator
(elevator control)
(J4)
Power (J6)
19 … 37 VDC
Power
J5
Door position
(J5)
IN (BN)
IN (BK)
CabSafe-2D Rx
Light Curtain
(J2)
SYN (GN)
GND (BU)
PWR (BN)
PWR (BN)
GND (BU)
SYN (BK)
PWR (BN)
GND (BU)
RS485-A(WH)
RS485-B (GY)
RS485-Y (GN)
CabSafe-2D Tx
Light Curtain
(J1)
J1
J2
RS485-Z (BK)
CabSafe-3D
(J3)
J3
1 2 3
J4 1 2
J6
OUT (WH)
Figure 4: Electrical connections CabSafe Controller with relay output
ERROR
OUT
3D
LC
USP
GND
J5
Door position
(J5)
Power (J6)
24 VDC
Power
IN (BN)
Out (WH)
1
2
3
4
5
6
7
8
9
10
11
12
OUT
IN (BK)
CabSafe-2D Rx
Light Curtain
(J2)
SYN (GN)
GND (BU)
PWR (BN)
PWR (BN)
GND (BU)
SYN (BK)
PWR (BN)
GND (BU)
RS485-A(WH)
RS485-B (GY)
RS485-Y (GN)
CabSafe-2D Tx
Light Curtain
(J1)
1 2 3
J6
3 2 1
J1
4 3 2 1
J2
12
RS485-Z (BK)
CabSafe-3D
(J3)
654321
J3
Figure 5: Electrical connections CabSafe Controller with push pull output
Details for the door position signal/switch are
provided in chapter 5.7.
The connection of the push-pull output is
schematically described in Figure 6:

CabSafe 3D Sensor & Controller English
© CEDES | V 1.0 CEDESAG reserves the right to modify or change technical data without prior notice. 8/28
µC
NPN
Load
iNPN
PNP
Load
iPNP
USP
Output
GND (0V)
Figure 6: Schematic electric connections for the CabSafe
Controller with push pull output
5.7 Door position signal
The connection of the door position signal is only
required for static light curtain installations. For
dynamic installations (when the light curtain is
mounted on the door(s)), the CabSafe 2D light curtain
can provide the door closing signal to the CabSafe
Controller. So for dynamic installations a connection
to the connector J5 is not required.
For static installations, the CabSafe Controller
expects a door position signal which is provided by
either the elevator control or from a door position
sensor.
For the door position signal (Connector J5) either
- a contact (e.g. a magnetic switch) or
- a 24 VDC signal
can be used. In case of a contact: the contact must
be able to switch a current of 2.3 mA. In case of a 24
VDC signal: the ground (GND) of the signal source
must have the same 0 V DC reference (i.e. it must be
connected to the same ground (GND) that the
CabSafe Controller is connected to).
J5
IN (BN)
Out (WH)
12
Door position
switch
J5
IN (BN)
12
24 VDC Door
position signal
Figure 7: Options for the door position signal
In general: the signal at pin 2 of the plug J5 shall be
high (+24 VDC) when the door is closed.
The actuation should occur when the elevator door
opening is between:
·Elevator door opening ≤400 mm (15.75 in.) and
·Elevator door opening ≥300 mm (11.81 in.). [For
elevators with no glass doors ≥0 mm (0 in.) is
possible.]
For a correct function DIP #3 and DIP #4 must be set
according to chapter 5.8.2.
Notice:
The door position signal to the CabSafe Controller
(see Figure 7) can also be generated by an elevator
control or other sensors (e.g. fork type barrier).
5.8 Functional selection DIP switches
The configuration of the CabSafe-System is managed
by settings of twelve (12) DIP switches. The location
of the switches is shown in Figure 4 and Figure 5. The
switches are described further in the tables that
follow.
DIP Function
1Mounting position
2
3Door closing detection
4
5
Door height
6
7
8
9 Bypass
10 Logic
11 Frequency
12 Not used
Table 1: Overview functional settings
CAUTION
Do not change settings of any switch if the
CabSafe-Control unit is powered on. Damage may
occur!
5.8.1 Settings for the 3D sensor mounting
position
Mounting position DIP 1 DIP 2
No function * 0 0
Left 1 0
Right 0 1
Center 1 1
Table 2: Mounting position of sensor in the transom seen from the
hallway into the cabin (*= Factory default.)
At least the position of one DIP has to be changed to
enter operation mode.
5.8.2 Settings for the door position detection
Door closed detection DIP 3 DIP 4
No function * 0 0
Dynamic installation of the
CabSafe 2D:
by light curtain 1 0
Static installation of the
CabSafe 2D:
by door position signal or an
elevator control signal (*)
0 1
Table 3: Definition of how the door closing or door closed is
detected (*= factory default)

CabSafe 3D Sensor & Controller English
© CEDES | V 1.0 CEDESAG reserves the right to modify or change technical data without prior notice. 9/28
(*-> Recommended setting for glass door elevators,
assuming that the light curtain is not installed at the
leading door edge because of the visible cable
guiding.)
At least the position of one DIP has to be changed to
enter operation mode.
5.8.3 Settings for the door opening height:
Door height
range DIP 5 DIP 6 DIP 7 DIP 8
No function * 0 0 0 0
6.66 ft to 7.5 ft 1 0 0 0
>7.5 ft to 8.5 ft 0 1 0 0
>8.5 ft to 9 ft 0 0 1 0
>9 ft to 10 ft 0 0 0 1
Table 4: Door height range (*= factory default)
At least the position of one DIP has to be changed to
enter operation mode.
5.8.4 Settings for the 2D versus 3D Active:
Bypass 3D sensor DIP 9
3D active 0
3D inactive 1
Table 5: DIP settings to bypass 3D sensor
A setting of DIP 9 to “1” causes that the CabSafe
Controller is only operated with the 2D sensor. This
functionality requires that the 3D sensor to be
physically disconnected from the CabSafe Controller,
otherwise an error is displayed.
5.8.5 Output logic selector
Output logic selection
DIP 10
Standard 0
Inverted 1
Table 6: DIP settings to change output logic
With DIP 10 the output logic is inverted (see chapter
5.10).
5.8.6 Operation frequency selector
Operation frequency selection DIP 11
Standard 0
Inverted 1
Table 7: DIP settings to 3D sensor operation frequency.
With DIP 11 the operation frequency of the CabSafe
3D sensor is modified. (see chapter 6.7).
5.9 Timing diagram
Figure 8:Timing diagram (DIP10 = 0)
Time Description Value
t1 Power on time < 5 s
t2 Typ. reaction time of the CabSafe Controller output caused by an object entering the
detection field of the CabSafe 2D sensor <140 ms
t3 Typ. release time of the CabSafe Controller output after clearance of the detection field
of the CabSafe 2D sensor < 20 ms +
Light curtain
t4 Typ reaction time of the CabSafe Controller output caused by an object detection of the
CabSafe 3D sensor < 250 ms
t5 Typ. release time of the CabSafe Controller output after clearance of the detection field
of the CabSafe 3D sensor 1.7 s
t6 3D-time (see chapter 4.2) 20 sec
Table 8: Descriptions of the times provided in Figure 8
ON
OFF
Object
No object
Object detected
No object detected
NO contact closed
NC contact closed t1 t2 t3 t4 t5 t4 t4 t2
t6 t6 t6
Power up
CapSafe-System
Object detection
CabSafe-2D
Output to
elevator control
Object detection
CabSafe-3D

CabSafe 3D Sensor & Controller English
© CEDES | V 1.0 CEDESAG reserves the right to modify or change technical data without prior notice. 10/28
5.10 Controller output logic
Push Pull
0V
USP
Output (PNP/NPN DO)
DIP10 = 1 0V
USP
Output (PNP/NPN LO)
DIP10 = 0
Relay
Object detected by 3D-sensor
No object detected by 3D-sensor
Object detected by light curtain
No object detected by light curtain
Open
Relay State
DIP10 = 1 for Normally Open (NO-COM); DIP10=0 for Normally Closed (NC-COM)
Open
Closed
Relay state
DIP10 = 0 for Normally Open (NO-COM); DIP10=1 for Normally Closed (NC-COM)
Closed
Figure 9: Controller output logic
5.11 Startup CabSafe Controller
1. Make sure that the CabSafe 2D and CabSafe 3D
sensors are connected.
2. Switch on supply. The POWER-LED at the
CabSafe Controller will change from OFF to Green
ON.
3. After 5 seconds power up time and elevator door
open check the LED “3D”. If the LED is OFF
means: there is no objected detected with the
CabSafe 3D sensor.
4. Check the LED “LC”. If the LED is OFF means:
there is no objected detected with the CabSafe 2D
light curtain.
5. Test if the LED “OUT” changes state by interrupt-
ing the protective field of the CabSafe 2D light cur-
tain. Perform the test of the light curtain from inside
of the cabin. The light curtain must signal object
detected at all times if
a. an object with a height of 80 mm (3.15 in.) is
detected at any position of the protective field
and
b. an object with a height of 50 mm (1.97 in.) is
detected at any position at the floor
during this test.
6. Test if the LED “OUT” changes state by interrupt-
ing the detection field of the CabSafe 3D sensor.
Correct function shall be tested by a person walk-
ing from outside towards the cabin (walking speed
between 0.3 m/s and 1.0 m/s). The CabSafe 3D
sensor must signal object detected at all tests.
5.12 LED status description
LED Status Description
POWER OFF Power OFF
Green ON Power ON
Table 9: Description Power LED

CabSafe 3D Sensor & Controller English
© CEDES | V 1.0 CEDESAG reserves the right to modify or change technical data without prior notice. 11/28
LED Status Description
ERROR OFF System running
Pulse See Table 11 for error codes
Out
OFF
Relay output = energized (NO
contact closed)/ PNP output =
ON
DiP10=0: No object detected
by the CabSafe 3D sensor or
by the CabSafe 2D light
curtain
Orange
ON
Relay output = de energized
(NC contact closed)/ PNP
output = OFF
DiP10=0: Object detected by
the CabSafe 3D sensor or by
the CabSafe 2D light curtain
3D
OFF No object detected by the
CabSafe 3D sensor
Pulse
3D rendered inoperative
(Pulse signal: 300 ms On,
900 ms pause)
- by a door position
signal
- by light curtain or
- by 3D-time out (see
chapter 4.2 and
Figure 8)
Orange
ON Object detected by the
CabSafe 3D sensor
LC
OFF No object detected by the
CabSafe 2D light curtain (LC)
Orange
ON Object detected by the
CabSafe 2D light curtain (LC)
Table 10: Description status LEDs
Pulse error definition:
Error
No Pulse
code Description
1
1 flash,
1 pause Internal CabSafe 3D-
sensor error
or manipulation:
Check first
if CabSafe 3D sensor
is manipulated (e.g. covered)
. If
not,then
please replace CabSafe
Controller
22 flash,
1 pause Reserved
33 flash,
1 pause Configuration error
Invalid CabSafe Controller
DIP
switch setting, see 5.8
44 flash,
1 pause Internal error, please replace
CabSafe Controller
55 flash,
1 pause Reserved
66 flash,
1 pause
Communication problem
CabSafe Controller <->
CabSafe
3D Sensor
77 flash,
1 pause Reserved
88 flash,
1 pause Reserved
99 flash,
1 Pause General CabSafe Controller
system error (IC temperature,
voltage, …)
Table 11: Error code description
Blinking code:
Flash = 300 ms On / 300 ms Off
Pause = 1’800 ms

CabSafe 3D Sensor & Controller English
© CEDES | V 1.0 CEDESAG reserves the right to modify or change technical data without prior notice. 12/28
5.13 Trouble Shooting
PWR
(Green)
ERROR
(Red)
Out
(Orange)
3D
(Orange)
LC
(Orange)
OFF OFF OFF OFF OFF ·Check electrical connections from Controller to power supply.
·Check supply voltage of the door controller.
ON OFF OFF OFF OFF No error, normal operation
ON OFF ON OFF ON No error and normal operation if protective field of CabSafe 2D light
curtain is interrupted
If CabSafe 2D Light Curtain is not interrupted, follow trouble shooting
instructions in CabSafe 2D user manual
ON OFF ON ON OFF No error and normal operation if CabSafe 3D sensor detects
approaching object.
If CabSafe 3D sensor does not detect approaching object, follow trouble
shooting instructions in chapter 6.11
ON OFF OFF BLK OFF No error and normal operation.
Two options
·3D time out, 20 s timer active (see chapter 4.2 and Figure 8)
·Door closed
ON BLK ON ON ON
or
OFF
Check error blinking code according to Table 11
Table 12: Trouble shooting
5.14 Product label
5.14.1 Product label Controller PCB
CabSafe Controller 100-R-00, EVR
ON: 116 096 / PN: 115 653
HW 0.04 / SW 0.60
Lot 200417/00654321/01234/000048
CSAB44.1:19 /ASMEA17.5-2019
Power 19.2 … 37 VDC
Curr. 500mARMS@24VDC
Relay output 1 A@ 30VDC
CEDES
SWISS MADE
CEDESAG
Science Park
CH-7302 Landquart
Figure 10:Product Label PCB
The label includes information according to table
below:
ON 1xx xxx Customer order number (ON) existing of 6
numbers with space after the third
PN 1xx xxx Internal CEDES part number (PN) existing
of 6 numbers with space after the third
CabSafe
Controller
100-R-00,
EVR
Description of the CabSafe Controller
(acc. to type description, see chapter
5.16).
Lot number Manufacturing Date (200417),
manufacturing job number (00654321),
employee number responsible for final
test (01234), and incremental count
(000048) build the lot number.
HW / SW
Index Increasing digits with the following
meaning:
1.xx: major changes, e.g. additional
functionality
x.0x: error correction, bug fix, new
compilation, no additional functionality
x.x0: ‘cosmetic’ update, no functional
influence
Table 13: Description of label content
5.14.2 Product label Controller Box
CabSafe Controller 100-PP-00, EVR, BX
ON 116 120 / PN 115 869
HW 0.04 / SW 0.136
Lot 200417/00654321/01234/000048
CSAB44.1:19 /ASMEA17.5-2019
Power 19.2 … 28.8 VDC
Curr. 500mARMS@24VDC
Relay output 1A@ 30VDC
CEDES
SWISS MADE
CEDESAG
Science Park
CH-7302 Landquart
Figure 11:Product Label Controller Box (Push-Pull
output)
For the description of the label content see Table 13

CabSafe 3D Sensor & Controller English
© CEDES | V 1.0 CEDESAG reserves the right to modify or change technical data without prior notice. 13/28
5.15 Maintenance
The CabSafe Controller does not need regular
maintenance.
5.16 Type description Controller
Coding:CabSafe Controller abb-cc-dd, eee, ff, ggggg
Examples:
CabSafe Controller 100-PP-00
CabSafe Controller 100-R-00, EVR
Example Description and options
CabSafe Controller
_ (Blank)
a 1 Series
1 -> HW series 1
2 -> HW series 2
bb 00 01 -> SW series 01
02 -> SW series 02
-
cc PP Output type
PP-> Push pull
R -> Relay
-
dd 00 DIP-Switch settings
00 -> All DIP = 0
01 -> DIP settings according
to PD
,
eee EVR Supply voltage
_ -> 24 VDC +/-20%
EVR -> extended voltage
range [19-37 VDC]
,
ff BX Housing type
_ -> pure PCB
PC -> PCB on carrier
BX -> Box
BI -> Box including IP65
sealing kit
,
ggggg OEM01 Type of connection cables
_ -> None
OEM01 -> according to
customer specification
Table 14
5.17 Delivery package
The CabSafe Controller Box as well as the CabSafe
Controller PCB are shipped without connection plugs
for the CabSafe 2D light curtain and CabSafe 3D
sensor. The connection plugs of the individual
CabSafe components are shipped together with the
CabSafe components itself.
5.18 Accessory magnet switch
For static installations of the CabSafe 2D light curtain
the following magnetic switch can be installed to
provide a door closing signal to the CabSafe
Controller.
3000
Figure 12: Dimensions door position sensor

CabSafe 3D Sensor & Controller English
© CEDES | V 1.0 CEDESAG reserves the right to modify or change technical data without prior notice. 14/28
The sensor and the actuator have to be positioned so that the actuation occurs when the elevator door opening
(“W” in Figure 13 and Figure 14) is between:
·Elevator door opening ≤400 mm and
·Elevator door opening ≥300 mm
Status door Status switch
Close Contact
close
Open Contact
open
Switching
element
Central opening (view from hallway into cabin)
Switch mounted left side Switch mounted right side
d
W
d
W
Figure 13: Magnet switch in case of central opening
Status door Status switch
Close Contact
close
Open Contact
open
Switching
element
Side opening (view from hallway into cabin)
Left side opening Right side opening
d
W
Actuator
W
Figure 14: Magnet switch in case of side opening
The cable outlet of the sensor must always be positioned towards the door opening direction at the installed door
as indicated in Figure 14. It is only one switch required per elevator (for central and for side opening).

CabSafe 3D Sensor & Controller English
© CEDES | V 1.0 CEDESAG reserves the right to modify or change technical data without prior notice. 15/28
Description Min. Max. Comments
Type Switch: BN 80-RZ
Housing Thermoplastic enclosure
Contact type Bistable, 1 reed contact
Enclosure rating IP67
Range actuating magnet BP 11 S 10 mm 30 mm
Cable length 3 m PVC
Operating temperature range -25°C + 75°C
Bounce time 0.5 ms
Switching current 0.5 A 2.3 mA provided by CabSafe
Controller at USP=24VDC
Mechanical life (operations) 109
Weight 26 g
Table 15: Specification magnet switch
Description Min. Max. Comments
Type BP 11 S
Housing Metal
Weight 40 g
Table 16: Specification actuator
5.19 Technical data CabSafe Controller
5.19.1 Mechanical
Attribute
Value
Controller-Box
Dimensions (l x h x
w) 120 x 94.1 x 51 mm
(4.72 x 3.70 x 2.01
in.) (See Figure 16)
Material PC/ABS blend
Color Blue
Weight (incl. PCB) 140 Grams
PCB on adapter
Dimensions 71.4 x 68.3 x 47.5
mm (2.81 x 2.69 x
1.87 in.) (See
Figure 15)
Weight 45 Grams
Table 17
5.19.2 Environmental
Attribute
Value
Enclosure rating PCB IP00
Enclosure rating box IP54
Operating temperature
CabSafe 3D sensor -20°C … +50°C (-4°F
… 122°F)
Operating temperature
Controller -20˚C … +60˚C (-4°F
… 140°F)
Table 18
5.19.3 Operation characteristics
Attribute Value
Supply voltage USP
Push pull version
Relay version 24 VDC +/- 20%
19.2 … 37 VDC
Supply voltage light curtain
(J1 and J2) 24 VDC
Supply voltage 3D sensor
(J3) 24 VDC
Max. power up time < 5 s
Average power
consumption
Door closed
Door open 6 W
12 W
Inrush current at 24 VDC
(including CabSafe 2D
light curtain and CabSafe
3D sensor)
11 A
Current 500 mA RMS at 24
VDC
Output type Push-Pull or Relay
Max Push-Pull current /
capacitance 120 mA /
100 nF
Max. relay current 1 A@ 30VDC
Min. switching current
(relay) 0.01 mA
Max. number of
mechanical relay
operations
> 20 x106
Max. relay switching
voltage 37 VDC
Typical system response
time CabSafe 3D
CabSafe 2D < 250 ms
< 20 ms + response
time CabSafe 2D
light curtain
Table 19

CabSafe 3D Sensor & Controller English
© CEDES | V 1.0 CEDESAG reserves the right to modify or change technical data without prior notice. 16/28
5.19.4 Connectors
Attribute Value Plug type Remark
3D sensor 6-pin
(J3) WAGO
734-106
(*) Plugs already
connected at
connection
cables
CabSafe-2D
Tx 3-pin
(J1) WAGO
734-103
(*)
CabSafe-2D
Rx 4-pin
(J2) WAGO
734-104
(*)
Door
position 2-pin
(J5) WAGO
734-102
(*)
Power/Output 3-pin
(J6)
[Push
Pull
version]
WAGO
231-103
(*)
Power 2-pin
(J6)
[Relay
version]
WAGO
231-102
(*)
Output 3-pin
(J4)
[Relay
version]
WAGO
231-103
(*)
Table 20 CabSafe Controller Connectors [* -> or WAGO equivalent]
5.19.5 General
Attribute Value
EMC emission EN 12015:2014
EMC immunity EN 12016:2013
ISO 22200:2009
Vibration IEC 60068-2-6:2007
Shock IEC 60068-2-27:2008
Eye Safety IEC 60825-1:2014
RoHS, REACH 2011/65/EU, 1907/2006 EU
Certificates
cCSAus
Liftinstituut
CE
CSA B44.1:19 / ASME A17.5-
2019
ASME A17.1-2019 / CSA
B44:19
2014/30/EU, 2014/33/EU
Table 21 CabSafe Controller Certification
5.20 Dimensions CabSafe Controller
5.20.1 Dimensions PCB solution
Side view PCB
Top view
PCB & Adapter plate
PCB on adapter
PCB adapter plate
Side view
66.28 (2.69 in.)
71.38 (2.81 in.)
47.5 (1.87 in.)
44.5 (1.75 in.)
31.51 (1.24 in.)
4 (0.16 in.)
50 (1.97 in.)
50 (1.97 in.)
28
(64.5)
Figure 15: Dimensions CabSafe Controller PCB solutions

CabSafe 3D Sensor & Controller English
© CEDES | V 1.0 CEDESAG reserves the right to modify or change technical data without prior notice. 17/28
5.20.2 Dimensions Box solution
51
110 (4.33 in.)
94.1 (3.70 in.)
120 (4.72 in.)
50 (1.97 in.)
4x Ø5 (Ø0.197 in.)
51 (2.01 in.)
Figure 16: Dimensions CabSafe Controller Box solution
6 CabSafe 3D sensor
6.1 Overview CabSafe 3D sensor
The CabSafe 3D sensor is used to detect the
presence of persons or objects approaching the
elevator cab entrance. To fulfill the requirements of
ASME A17.1-2019 / CSA B44:19, the CabSafe 3D
must be used in conjunction with a CabSafe
Controller and a CabSafe 2D light curtain.
As an extension to existing door-protection devices,
the purpose of the CabSafe 3D sensor is to monitor
the entrance area of the elevator door for people or
objects approaching the elevator cab. By using “Time
of Flight” (TOF) technology, the CabSafe 3D sensor
can detect the difference between a person (or object)
approaching the elevator cab and a stationary person
or object in the elevator cab entrance area. The
sensor's compact housing is optimized for difficult
mounting locations, including narrow elevator cab
transoms.
Figure 17: Principal installation of a CabSafe 3D sensor (example
for side opening)
6.2 Features of the CabSafe 3D sensor:
·Fulfills requirements of ASME A17.1-2019 / CSA
B44:19
·Suitable for both center- and side-opening appli-
cations
·Easy installation
·Reliable object detection using Time-of-Flight
(TOF) technology
·Integrated LED indication
·Reduces accidents caused by being hit by the el-
evator door(s)
·Reduces damage to the elevator doors
·Easy configuration of the monitored area
·Automatic door recognition
6.3 Type description CabSafe 3D sensor kit
CabSafe 3D – a – bb – cc
aVersion
- Series one
2 Series two (future)
bb Mounting brackets
- None
P Partially recessed (future)
F Flush mounting (fully recessed)
S Surface stainless steel mounting
cc Installation
- Universal
L Left (future)
C Center (future)
R Right (future)
Example:CabSafe 3D-F

CabSafe 3D Sensor & Controller English
© CEDES | V 1.0 CEDESAG reserves the right to modify or change technical data without prior notice. 18/28
6.4 Safety information
The CabSafe 3D sensor must be used in conjunction
with a CabSafe Controller and a CabSafe 2D light
curtain. It is the responsibility of the installer to ensure
that, on completion, the installation complies with all
the relevant codes and regulations that pertain to
elevator door protection devices.
6.4.1 Non-intended use
The CabSafe 3D sensor must not be used for:
• Elevator with pure glass doors (see 6.5.1.2)
• Protection of dangerous machines
• Equipment in explosive atmospheres
• Equipment in radioactive environments
Use only specific and approved safety devices for
such applications, otherwise serious injuryor death or
damage to property may occur.
6.4.2 Hazards of laser radiation
CabSafe 3D sensor is in conformance with IEC
60825-1, 2014 Ed.3 and 21 CFR 1040.10*
*According to the document Laser Notice. 56 issued
by FDA on May 8, 2019
WARNING
The sensor should never be opened. If it is opened
intentionally or accidentally the laser radiation can
reach to a hazardous Class 4 level and exposure
to eyes and skin from direct, reflected and
scattered radiation must always be avoided.
Do not operate the device with a defective or
missing cover glass or lens. In case of such an
event switch off the power supply immediately.
Use of additional optics in any form in front of the
sensor or modifying the sensor or its optical
components in anyway is absolutely prohibited.
Noncompliance will lead to unforeseeable
outcome.
6.5 Installation CabSafe 3D sensor
Following precautions must be followed when the
CabSafe 3D sensor is integrated into a CabSafe sys-
tem.
- The CabSafe 3D sensor must be connected to the
CabSafe Controller (see Figure 4).
- The switch settings in the CabSafe Controller must
be set according to the
omounting position of the sensor (chapter 6.5.1
and 5.8) and
oelevator entrance height (chapter 6.5.1 and
5.8)
oopposite elevator installations (chapter 6.7 and
5.8.6)
- Use only the dedicated mounting brackets of the
CabSafe 3D sensor (see 6.5.4)
- Prepare and install sensor at the recommended
mounting positions (see 0)
- For elevators with glass doors consider specific
door design instructions and different mounting in-
structions for the CabSafe 3D sensor (see 6.5.1).
The installation should be done in the following order:
- Switch off power and mark clearly that this
elevator is out of service (LOTO Lock Out Tag
Out).
- Mechanical installation of the CabSafe 3D
sensor (chapter 6.5.1)
- Make sure the DiP Switches of the CabSafe
Controller are set according to the installation
(see chapter 5.8).
- Electrical installation and integration of CabSafe
3D sensor to the CabSafe Controller
- Power-up and test for proper function.
6.5.1 Field of application
6.5.1.1 Elevator door widths and heights
Installation of the CabSafe 3D using the instructions
that follow is suitable for:
·Center opening applications with elevator door
heights from 2.03 m to 3.05 m (6.67 ft to 10 ft)
and opening widths up to 1.37 m (4.5 ft).
·Side opening (left and right) applications with
elevator door heights from 2.03 m to 2.43 m
(6.67 ft to 8 ft) and door opening widths up to
1.37 m (4.5 ft).
·Side opening (left and right) applications with
elevator door heights from 2.43 m to 2.74 m (8 ft
to 9 ft) anddoor opening widths upto 1.10 m (3.6
ft).
For dimensions that fall outside of these ranges,
please contact your local CEDES representative for
assistance.
6.5.1.2 Glass door elevators
For elevators with glass doors the following
requirements must be considered in addition to
chapter 6.5.1.1:

CabSafe 3D Sensor & Controller English
© CEDES | V 1.0 CEDESAG reserves the right to modify or change technical data without prior notice. 19/28
·The leading edge of all doors must be metal
(preferred brushed stainless steel) and shall
have side lengths of equal or more than 40 mm
(1.57 in.).
Light curtain
Cabin 3D Sensor
≥40 mm
≥40 mm
Glass doors Glass doors
Figure 18: Metal side lengths for glass doors
·The mounting distance “S” is reduced according
to chapter 6.5.3.3.
·The signal change for the door position must be
generated for a door opening between 300 mm
(11.81 in.) and 400 mm (15.75 in.), see chapter
5.7.
·Static mounting of the CabSafe 2D light curtain,
assuming that the light curtain is not installed at
the leading door edge because of the visible
cable guiding, see chapter 5.8.2.
6.5.2 Mechanical installation
WARNING
Electrical and mechanical
Hazards
Electrical shock and unexpected movement of the
protected application can cause serious injury or
death.
►Follow all applicable safety measures.
►Use only specific and approved tools.
►If the CabSafe 3D sensor has to be adjusted, the
main power supply must be switched off and
marked as out of service (LOTO Lock Out Tag
Out).
NOTICE
Mechanical damage to the CabSafe
3D sensor
►Do not drill additional holes into the sensor.
►Do not overtighten the mounting screws.
►Mount the brackets on a flat surface
6.5.3 Mounting position
IMPORTANT
for a correct installation
A. Cable must exit right when looking into the el-
evator cabin (Figure 19, Figure 20, Figure 21)
B. The field of view of the sensor must be ori-
ented towards the outside of the elevator
cabin.
C. Elevators with glass doors or extraordinary re-
flective surfaces require
·a reduced installation distance to the door
(see chapter 6.5.3.3) and
·a metal frame at the leading edge of the
doors (see 6.5.1.2).
The mounting position of the CabSafe 3D sensor is
dependent on the type of door opening.
6.5.3.1 Center opening door
The center of the sensor mounting bracket must be
located in the center of the door entrance.
CabSafe-3D
Equal
Figure 19: Mounting location and orientation - center opening door
6.5.3.2 Side opening door (left or right):
The sensor located near the slam post (strike jamb)
and a minimum distance from the slam post (strike
jamb) must be maintained; see Figure 20 and Figure
21 for details.
CabSafe-3D
CabSafe-3D
(observe cable direction -> right side)
D
Figure 20: Mounting location and orientation – right side opening
door

CabSafe 3D Sensor & Controller English
© CEDES | V 1.0 CEDESAG reserves the right to modify or change technical data without prior notice. 20/28
CabSafe-3D
(observe cable direction
D
Figure 21: Mounting location and orientation – left side opening
door
For left- and right-side door opening, the center of the
mounting bracket should be positioned at a distance
D= 240 ±10 mm (9.45 ±0.4 in) from the slam post
(strike jamb).
6.5.3.3 Mounting distance to the door
In flush mounting applications the center of the
CabSafe 3D sensor should be positioned at a
distance between 25 mm and 70 mm (0.98 in. and
2.76 in.) from the cabin door
Position of mounting bracket
Distance “S”
Typical:
≥25 mm
≤70 mm
Figure 22: Typical installation distance CabSafe 3D sensor to the
front of the cabin door (top view)
IMPORTANT
for glass elevators
For glass elevators the installation distance S has
to be in the range of 25 mm to 70 mm (0.98 in. to
2.76 in.).
For backside transom applications (see Figure 29):
for center, left or right door opening the maximum dis-
tance “S” of the center of the CabSafe 3D sensor to
the front of the hoist way door (see Figure 23) shall
be equal or less than 314 mm (12.36 in.) [Figure 23
to Figure 25].
Distance “S”
Figure 23: Installation distance CabSafe 3D sensor to the front of
the hoistway door (top view)
Lobby
Cabine
S
Cabine Lobby
Side view Top view
S
Figure 24: Installation distance CabSafe 3D sensor to the front of a
single speed hoist way door
Lobby
Cabine Cabine Lobby
Side view Top view
S
S
Figure 25: Installation distance CabSafe 3D sensor to the front of a
two speed hoist way door (telescope)
6.5.4 Mounting brackets
The following mounting brackets are available for the
installation of a CabSafe 3D sensor in the transom
Type Remark
Flush mounting Optional mounting plate
for thin transoms (< 2 mm
[0.079 in.]) available
Back transom mount-
ing Mainly for modernization
Table 22: Mounting hardware
This manual suits for next models
2
Table of contents
Popular Control System manuals by other brands
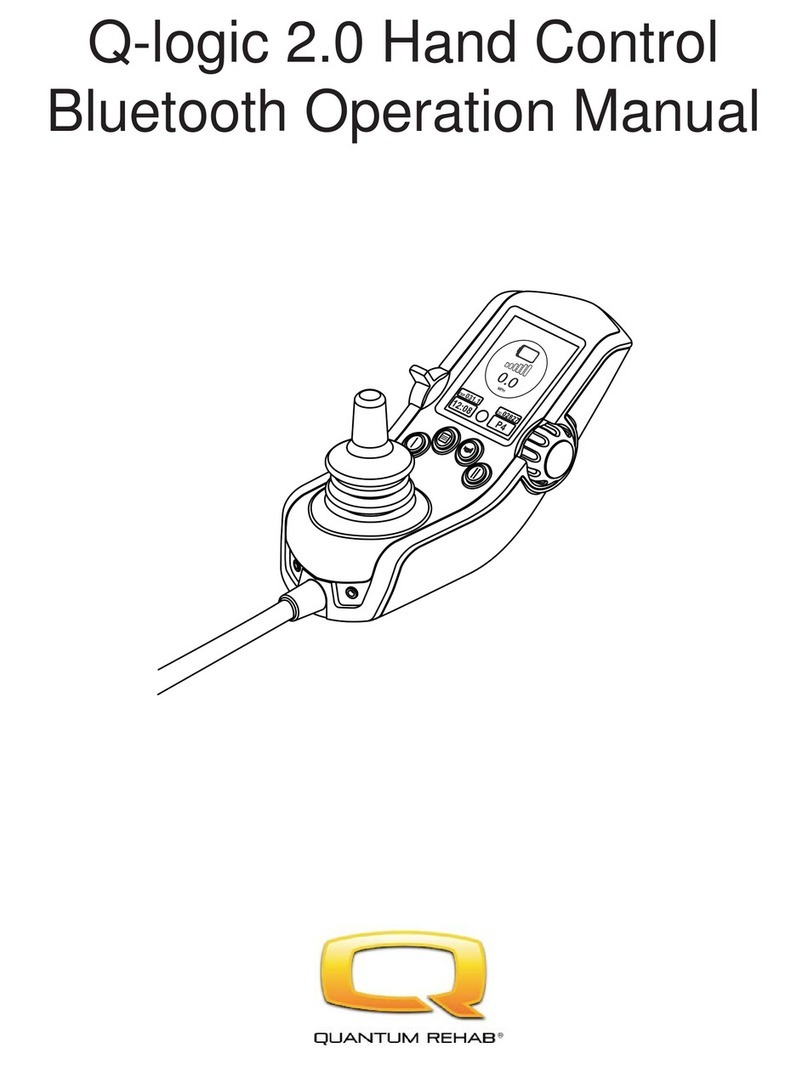
Quantum Rehab
Quantum Rehab Q-logic 2.0 Operation manual

eta
eta KNX operating instructions
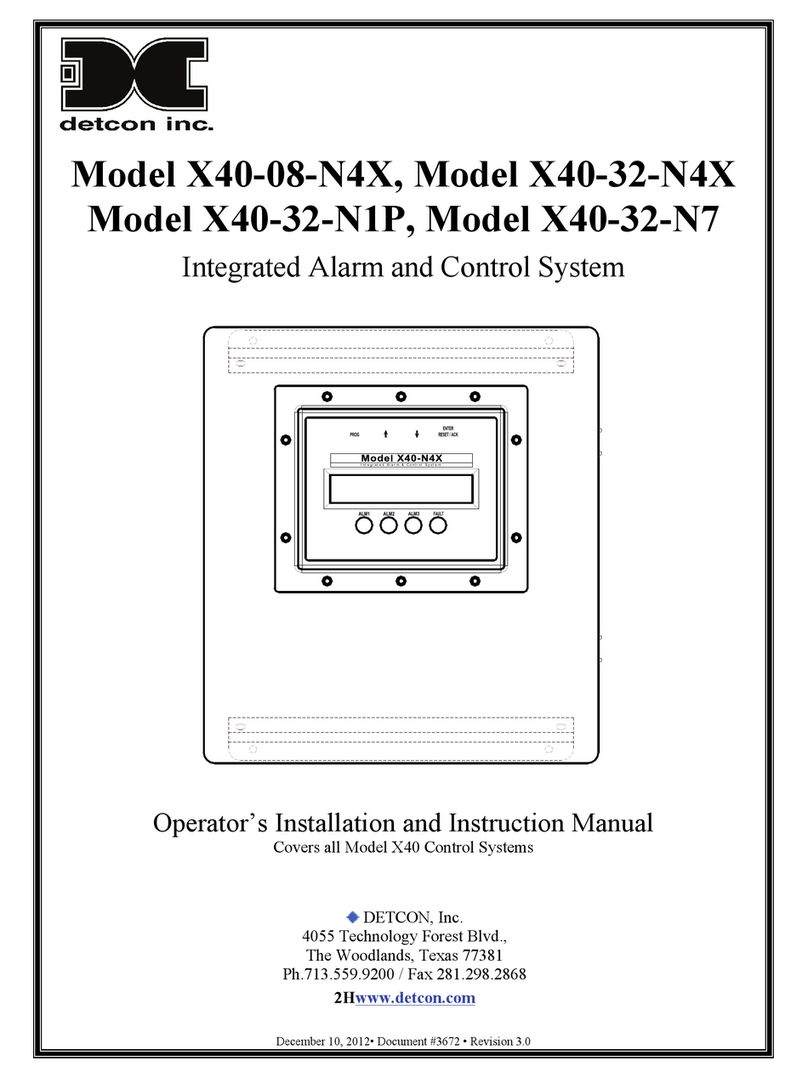
Detcon
Detcon X40-08-N4X Operator's installation and instruction manual
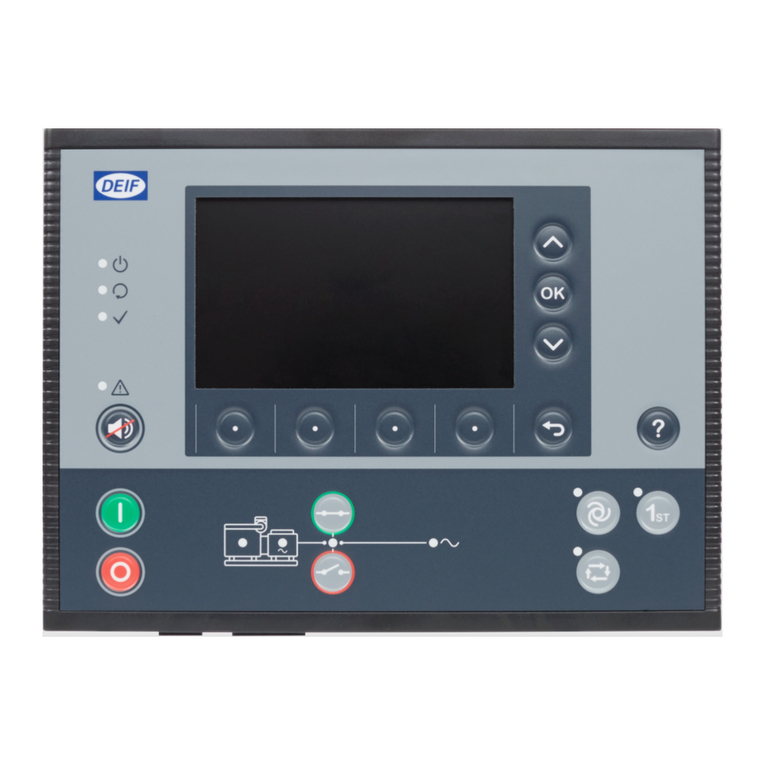
Deif
Deif PPM 300 Operator's manual
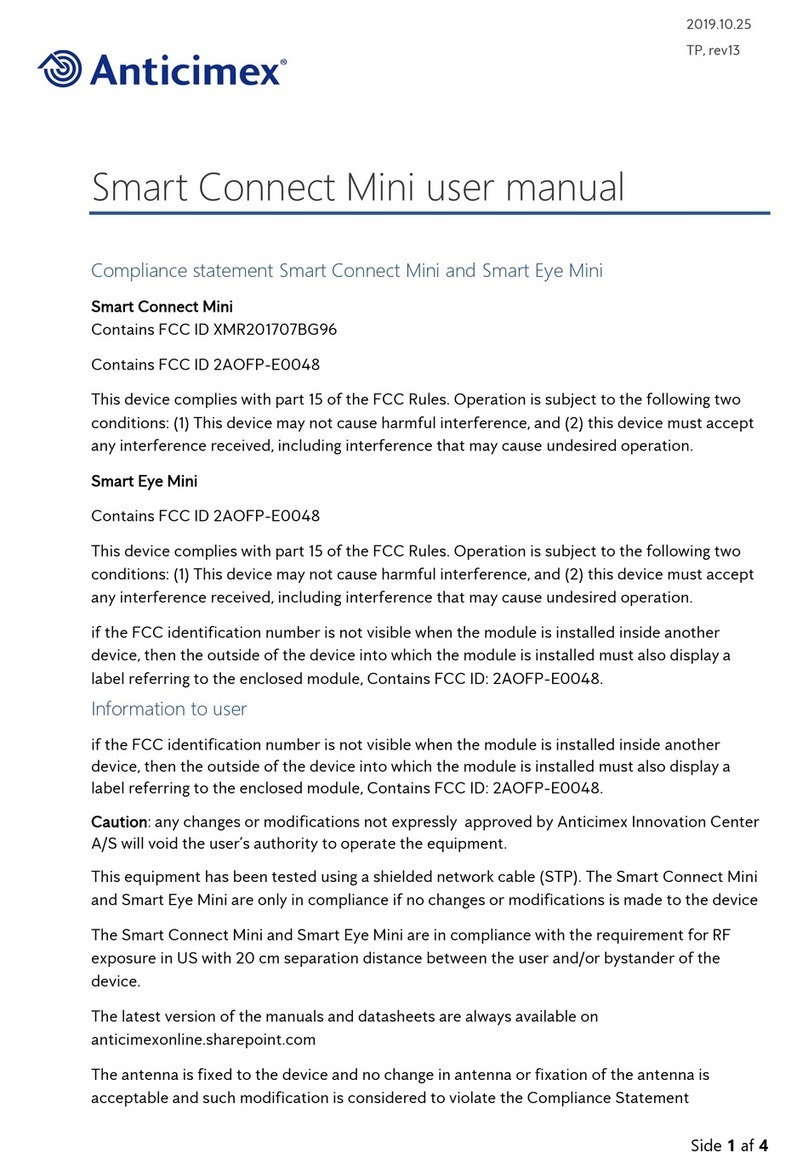
Anticimex
Anticimex Smart Connect Mini user manual

Exhausto
Exhausto EFC 25 Installation & operating instructions
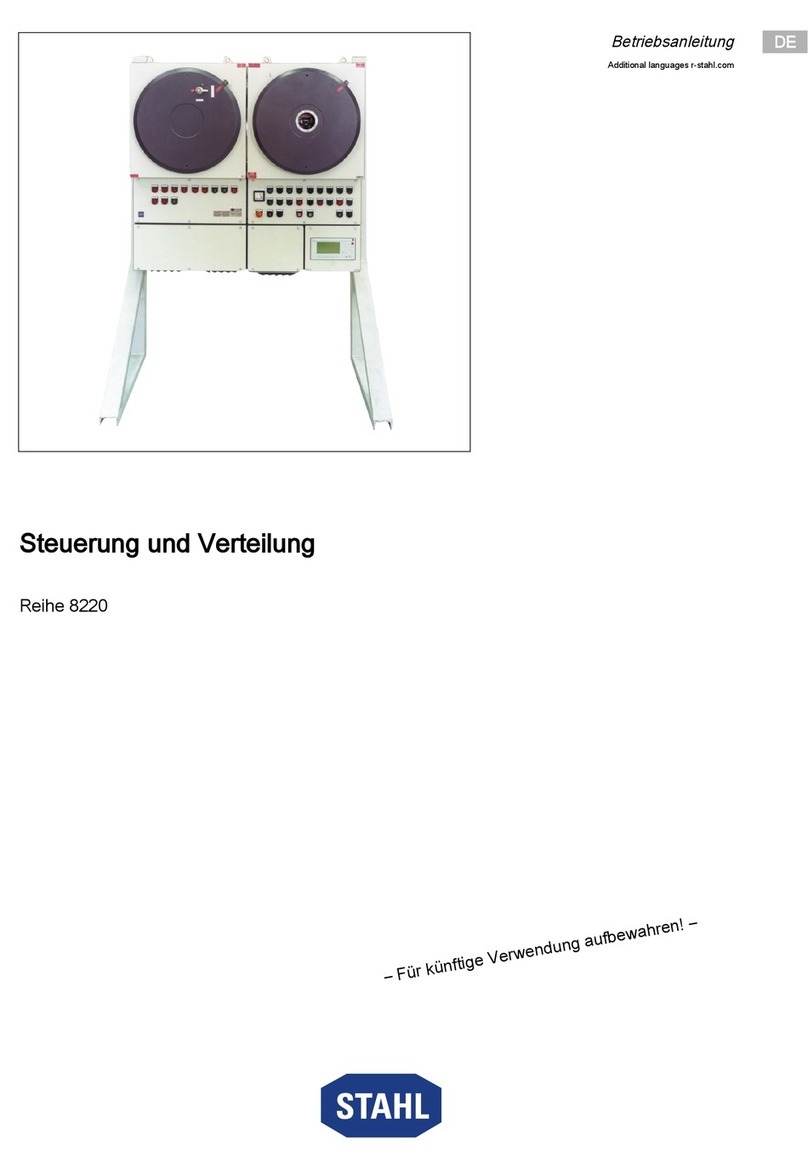
Stahl
Stahl 8220 Series operating instructions

Preston Cinema Systems
Preston Cinema Systems F I + Z manual
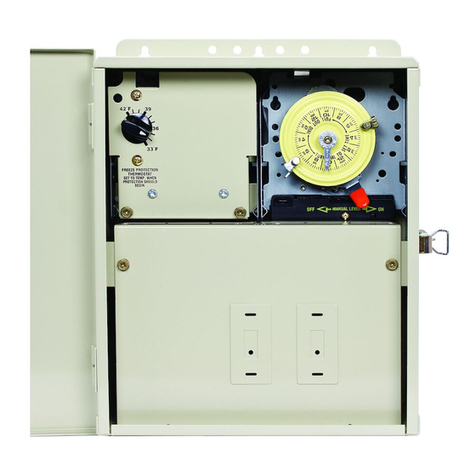
Intermatic
Intermatic FREEZE SENTRY PF1100 Series Installation, operation & service manual

TECSYSTEM
TECSYSTEM FO 935 instruction manual
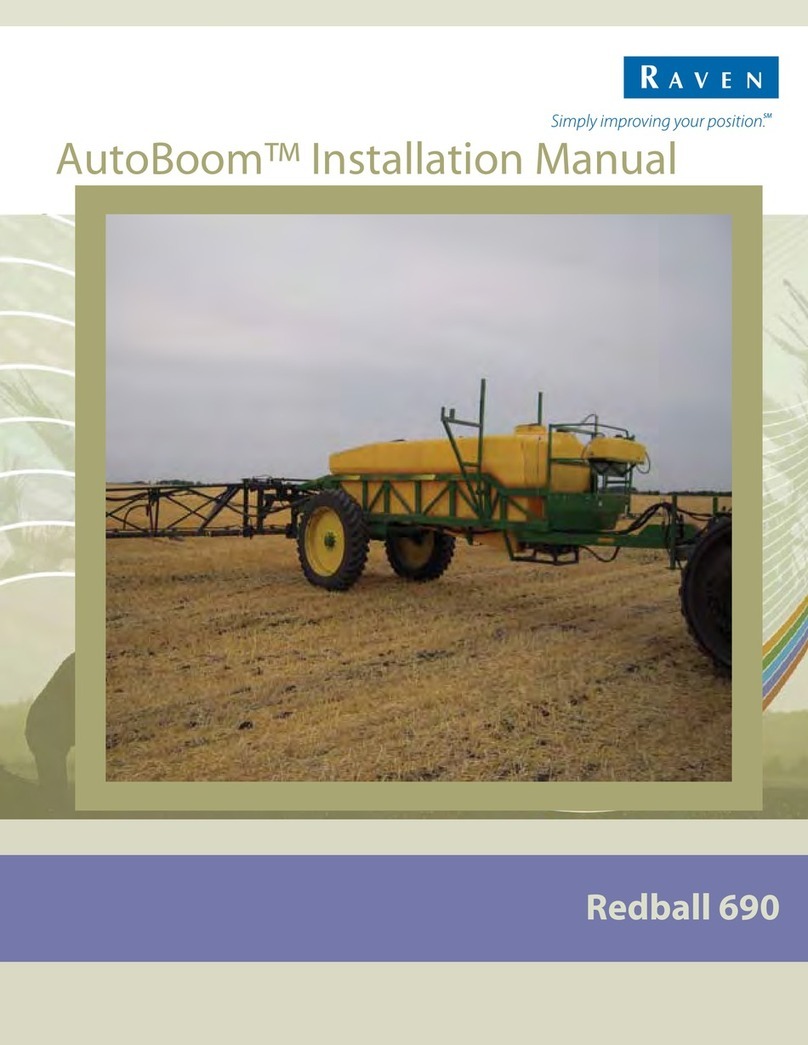
Raven
Raven AutoBoom installation manual
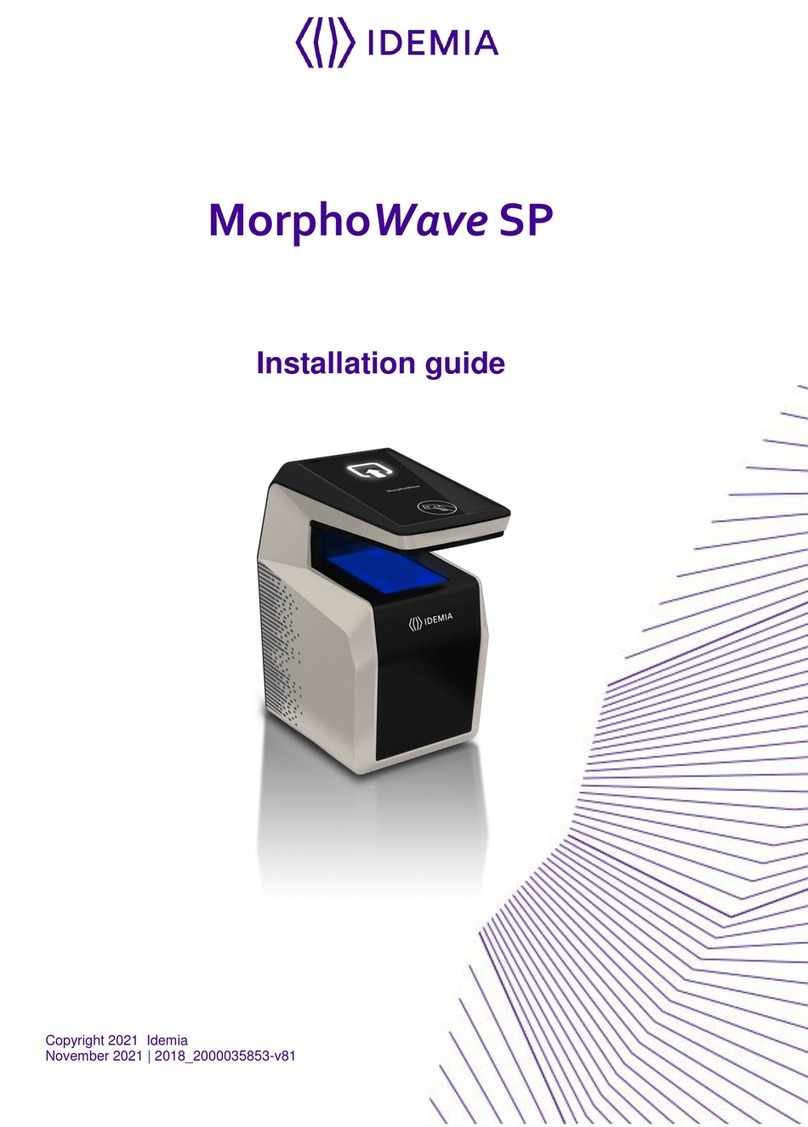
Idemia
Idemia MorphoWave SP installation guide