Cembre Rolly 1000 User manual

THERMAL TRANSFER PRINTER
ROLLY 1000
OPERATION AND MAINTENANCE
MANUAL
ENGLISH
07 M
037
E

CONTENTS
1. PRODUCT INTRODUCTION..................................................................................1
1.1 Directives 2002/95/EC and 2002/96/EC........................................................... 1
1.2 Specification …................................................................................................. 1
1.2.1 Printer ....................................................................................................... 1
1.2.2 Environment............................................................................................... 2
1.2.3 Hardware.................................................................................................... 2
1.2.4 Bar Code.................................................................................................... 2
1.3 Optional Items.................................................................................................. 3
1.4 Supplies............................................................................................................ 3
1.4.1 Label Specification ................................................................................... 3
1.4.2 Ribbon Specification ................................................................................. 3
2. GETTING STARTED............................................................................................. 4
2.1 Unpacking and Inspection................................................................................. 4
2.2 Equipment Checklist......................................................................................... 4
2.3 Printer Parts ..................................................................................................... 5
2.4 Buttons, Indicators and Adjustment Knobs ....................................................... 6
3. SET UP.................................................................................................................. 9
3.1 Setting Up the Printer....................................................................................... 9
3.2 Ribbon Installation............................................................................................ 9
3.3 Label Roll Installation .................................................................................... 10
3.3.1 Distance/Black Line Detector Positioning ................................................... 11
3.4 Self-test ......................................................................................................... 12
3.5 Dump Mode.................................................................................................... 13
4. USING THE PRINTER ........................................................................................ 14
4.1 Power-on Utilities............................................................................................ 14
4.1.1 Gap/Black Mark Sensor Calibration Utility .............................................. 14
4.1.2 Printer Initialisation................................................................................... 15
4.2 Troubleshooting Guide.................................................................................... 16
5. PRINTER CLEANING.......................................................................................... 17
5.1 Print Head Cleaning ........................................................................................ 17
5.2 Printer Cover Cleaning ................................................................................... 17
5.3 Internal Parts Cleaning.................................................................................... 17
APPENDIX LCD Control Panel Operation Map..................................................... . 18

1. PRODUCT INTRODUCTION
ROLLY 1000 has rugged steel construction and durable metal mechanism ensuring the
ability to work in industrial environments. Rolly 1000 is equipped with a 32-bit RISC
processor, which offers up to 4”/sec print speed. The back-lit LCD display, simplifies printer
status management and operation and the moveable sensor design can meet a wide range
of media.
Frequently used bar code formats are available while fonts and bar codes can be
printed in any one of four directions. ROLLY 1000 provides a choice of five different sizes of
alphanumeric font, OCR-A, OCR-B and one true type font.
1.1 Directives 2002/95/CE and 2002/96/CE
Following information applies in member states of the European Union:
USER INFORMATION in accordance with “Directives 2002/95/EC
and 2002/96/EC regarding the reduction of hazardous substances
in electrical and electronic equipment, including the disposal of
waste”.
The 'Not in the bin' symbol above when shown on equipment or packaging means that the
equipment must, at the end of its life, be disposed of separately from other waste.
The separate waste collection of such equipment is organised and managed by the
manufacturer.
Users wishing to dispose of such equipment must contact the manufacturer and follow the
prescribed guidelines for its separate collection. Appropriate waste separation, collection,
environmentally compatible treatment and disposal is intended to reduce harmful
environmental effects and promote the reuse and recycling of materials contained in the
equipment. Unlawful disposal of such equipment will be subject to the application of
administrative sanctions provided by current legislation.
1.2 Specification
1.2.1 Printer
Item Specification
Printing Mode Thermal transfer and direct thermal
Resolution 300 DPI
Max. Print Length
450 mm
Max. Print Width 104 mm
Print Speed 2,3,4 ips
1

1.2.2 Environment
Operating Environment
Temperature
5 ~ 40° C
Humidity 30 % ~ 85 %
Storage Environment
Temperature
-10 ~ 60° C
Humidity 20 ~ 95 %
Ventilation Free air environment
1.2.3 Hardware
Sensors Label gap sensor, ribbon end sensor, black mark sensor, head printer
open sensor, label taken sensor.
Memory Flash ROM (2MB), DRAM (2MB) and 8M optional flash ROM (memory
module)
Interface RS-232C (RS422/485 option), Centronics (SPP), USBV1 .1 and Internal
LAN adapter (option).
Cutter 4 inch width (Media thickness up to 0.25 mm)
Power 100-240 V universal switching power supply.
1.2.4 Bar code
Code 39, Code 39C, Code 93, Code128 subsets A.B.C, Codabar, Interleave 2 of 5,
EAN-8, EAN-1 3, EAN-1 28, UPC-A, UPC-E, EAN and UPC 2(5) digits add-on, CPOST,
MSI, PLESSEY, POSTNET, EAN-14, ITF-14, PDF-417, Maxicode, DataMatrix, QR code.
2

1.3 Optional items
Cutter module
1.4 Supplies
1.4.1 Media specification
Item Specification
Type Reel media: precut wraparound cable markers,
precut cable tags, labels
Media Width Max. 116 mm ( Max. 4,4” )
Media Thickness 0,06 ~0,25 mm (0,4 mm per TPM-ROLL)
Media Roll Diameter 203 mm (Max.)
Roll Core Diameter 25 or 77 mm
Black Mark Width 3 mm (Min.)
1.4.2 Ribbon specification
Item Specification
Ribbon Width 25,4 ~114,3 mm
Ribbon Length 300 m (Max.)
3

2. GETTING STARTED
2.1 Unpacking and inspection
ROLLY 1000 is specially packaged to withstand damage in shipping. In case of evident
damage on receipt, contact the supplier directly to specify the nature and extent of
damage. Please retain the packaging materials in case you need to reship the printer.
2.2 Equipment checklist
ROLLY 1000 printer
Ribbon take up spool
Power supply cable
Centronics interface cable
USB interface cable
3’’ paper core adapter
Operating software on GENIUS SUITE CD
Black printer ribbon
Protective cover
4

2.3 Printer components
Figure 1. Printer front view
Figure 2. Printer rear view
5
External Label Feed Opening
Centronics Port
RS-
232C Port
USB-Port
Power Switch
Power Supply Connector
Aux. LED
LCD Display
Control
Buttons
Printer Right
Side Cover
Lower
Front
Panel

Figure 3. Printer interior view
2.4 Buttons, Indicators and Adjustment Knobs
Power Indicator
When the printer is in the power-on condition, the Power indicator is lit.
On-line Indicator
This green On-Line indicator is lit when the printer is ready; the On-Line indicator blinks
when pressing PAUSE button.
Error Indicator
The red Error indicator lights in the event of a printer error such as memory full,
carriage open, cutter error, etc.
MENU/SELECT button
Provided with a built-in menu, the printer allows the user to directly set printing
parameters or view printer status on the LCD display.Press the MENU button to enter
printer setup mode. Press the MENU button again to proceed to the next item.
Setup is comprised of: Printer Setup, Sensor Setup, System Setup, File Setup and
Printer Test. For more information, please refer to Appendix for the structure and
operation at logic of the menu.
6
Ribbon R
ewind
Spindle
Ribbon Tension
Adjustment Knob
Ribbon Supply
Spindle
Print Head
Pressure
Adjustment Knob
Print
H
ead
L
ift
L
ever
Media G
uide
B
ar
Media
G
uide
Clamp
Media
S
pindle

PAUSE/EXE/INC button
This buttons conbines three functions:
A. PAUSE button if the printer is in the Ready status. By pressing the PAUSE button:
(1) the printer stops at the completion of printing of the current media, (2)
the On-Line LED flashes, and (3) the printer holds all data in memory. This
allows for trouble-free replacement of media stock and thermal transfer ribbon. A
second depression of the PAUSE button will restart the printer.
B. EXE/INC button if in Setup mode. Press EXE/INC button to increase the value of
parameters or execute the selected item.
FEED/DEC button
This button also has dual functions: Feed one medium row and decrease the value of
parameters.
Press the FEED button, the printer will advance one medium row.
Press the DEC button to change parameter settings or exit the submenu.
Print head lift lever
When opening the Print Head Lift Lever, On-Line LED is off, the LCD display shows
“Carriage Open”. After engage the print head lift lever, press the FEED button, printer
will re-register the media then show READY on the LCD display and the screen will
return to ready condition.
Ribbon tension adjustment knob
The
ribbon tension adjustment knob
offers six settings to suit different widths of
ribbon. Turning the knob clockwise from
0 to 5 tightens the ribbon. A light click is
audible between settings. A louder click indicates setting 1. Factory setting is 5.
Print head pressure adjustment knob
Each print head pressure adjustment knob has 5 settings to allow for different media
reel widths. For a 50 mm or narrower reel, the left hand setting may need to be
increased and the right hand decreased, while for a 100 mm wide reel, both knobs
should have the same setting. Factory setting is 5 on each knob.
7

Print head burn line adjustment screw
The
print head adjustment screws
are used
to fine tune print quality for different
thicknesses of media. Turning the knobs adjusts the print head burn line forward
or backward relative to the platen roller.
Usually no
adjustment is required, so proceed with caution as incorrect setting
may move the
print head burn line from its optimum position, reducing print
quality and possibly
damaging the printer.
To re-optimise the print
head burn line by moving it forward, increase
print head
pressure as in section above and
turn these screws counter-clockwise. Test print.
Continue to adjust and test until the highest print quality is achieved.
Attention: The print head moves 0.7 mm for each 360 degree turn. Proceed with
caution, turning the screws only ¼ of a turn each time and in the same direction
of rotation.
Figure 4. Print Head Adjustment Screws
8
Print Head Adjustment Screws

3. SET UP
3.1 Setting up the printer
1. Place the printer on a flat, secure surface.
2. Make sure the POWER switch is off.
3. Connect the printer to the computer with the provided USB or Centronics cables.
4. Plug the power supply cable into the power supply connector at the rear of the
printer, and then plug the power cable into a properly earthed power outlet.
3.2 Ribbon installation
1. Open printer right side cover and lower front panel.
2. Disengage print head lift lever.
3. Install a new ribbon onto the ribbon supply spindle (fig. 5).
Notice : Ribbon should be placed to the left end of spindle.
Figure 5a.
Ribbon sensor
Figure 5. Ribbon installation
4. Locate the take up spool on the ribbon rewind spindle.
5.
Locate the ribbon on the supply spindle with the leading edge hanging down at the
front. Pull the ribbon leading edge through the printer
ensuring it passes through
the ribbon sensor
(fig. 5a) and follows the correct path (fig. 8) and then attach with
tape to the
take up spool.
6. Manually turn the ribbon rewind spindle (R) to tension the ribbon.
9
Take up spool on
ribbon rewind spindle
Printer Ribbon
on supply
spindle
Ribbon sensor
Printer Ribbon

Figure 6. Ribbon & Media installation path
3.3 Loading Media reels
1. Locate the 3” hub on the media spindle
and mount a reel of media (fig. 8).
2. Pull the media leading edge under the media
guide bar,
ensuring it passes
through the
green Gap / Black mark sensor and is against
the black stop on left
side (figs. 9a & 9b)
, then
under the Print head, until it protrudes from the machine.
3. Adjust the clamp to restrict
sideways movement of the media and close
it to the
bar, ensuring the media can advance freely by pulling it from the front.
Figure 7a.
Gap/Black mark sensor
Figure 7. Media reel installation
10
3”
adaptor
Gap/Black mark sensor
Label roll
Media guide bar

3.3.1 Distance/black line sensor positioning
Media will advance correctly only if the sensor
is correctly aligned. Manually
position the sensor, depending on the media being printed, as follows:
- For
TTL…media
,
align the long line
marked on the sensor with the centre
of the left hand label, see fig. 9a.
Figure 9a
- For TPM-ROLL media, align the long line
with the centre of the lateral
holes
to the
left of the reel, see fig. 9b.
Figure 9b
- For
KM-ROLL
media
,
align the
short line
marked on the sensor with
the centre of any label, see fig. 9c.
Figure 9c
- Using the Print head lever, lower the print head and lock the lever.
- Close front and side covers.
- Power up the printer.
11
Long line of the detector in the
centre of the left hand label
Long line of the detector in
the centre of the lateral holes
Holes
TTL
…
media
Sensor
Sensor
Stop
Stop
Stop
Short line of the detector
in
the centre of any
label
Sensor
KM
-
ROLL media
TPM
-
ROLL
media

3.4 Self-test
To initiate the self-test mode, depress the MENU button.
Press MENU button to scroll to Printer test.
Press EXE button to enter the submenu and press MENU button to Printer Config. Press
EXE button to print printer internal setting. In self-test, a check pattern is printed to verify
the performance of the print head followed by the printer internal settings as shown
below:
1. Printer model and firmware version
2. Check sum
3. Serial port setting
4. Code page setting
5. Country code setting
6 Print speed setting
7. Print density setting
8. Label size setting
9. Gap (Bline) width and offset setting
10. Backing paper transparence
11. File list
12. Memory available
PRINTER INFO
Figure 10. Printout of self-test
12
Print head check pattern
Firmware version
Firmware check sum
Printed mileage (meter)
Serial port configuration
Country code
Print speed (inch/sec)
Print density
Label size (inch)
Gap distance (inch)
Gap/Black mark sensor sensitivity
Backing paper transparency
Numbers of download files
Total & available memory space

3.5 Dump mode
To enter dump mode, press MENU button to scroll the cursor to “Printer Test” then press
EXE button to enter the submenu. Press MENU button to scroll dump mode. Press EXE
button to select line dump mode or page dump mode. Press MENU button to select
EXIT to enter dump mode. In this mode, any character sent from the host computer will
be printed in two columns, as shown in Figure 11.
In the left hand column are the characters received and in the right hand columns are the
corresponding hexadecimal values. This is very helpful to users for the verification of
programming commands or debugging of printer programs. Reset the printer by pressing
the FEED button.
Abbildung 11. Ausdruck im Übergabe-Modus
Figure 11. Printout of dump mode
13
ASCII data Hexadecimal da
ta related to
left column of ASCII data

4. USING THE PRINTER
4.1 Power-on utilities
There are two power-on utilities to calibrate sensors and initialise the printer hardware.
These utilities are activated by pressing the PAUSE button, PAUSE and FEED buttons
and turning on the printer power simultaneously. The utilities are:
1. Gap/black mark sensor calibration
2. Printer initialisation
4.1.1 Gap/Black mark sensor calibration utility
This utility is used to calibrate the sensitivity of the gap/black mark sensor. The
gap/black mark sensor must be calibrated whenever changing the label media,
executing printer initialization, or the message “NO PAPER” appears in the
display, even when material is present.
Calibrate the sensor by following one of the procedures:
- Verify that the sensor is correctly positioned (refer to section 3.3.1)
Procedure A, using the power on off switch.
1. Install the ribbon and media (refer to sections 3.2 and 3.3) and engage the print
head lift lever.
2. Turn off printer power.
3. Press PAUSE then power up the printer. Release the PAUSE key when
“GAP/BLINE sensor calibrating....” message is shown on the LCD display.
The printer will calibrate the Gap / Black mark sensor automatically.
Procedure B, using the Control buttons.
1. Install the ribbon and media (refer to sections 3.2 and 3.3) and engage the print
head lift lever.
2. Turn on the printer.
3. The ‘MENU’ button twince; message ‘Sensor calib‘ displayed.
4. The ‘PAUSE’ button once; message ‘Auto gap’ displayed.
5. The ‘PAUSE’ button once; printer will operate and the sensor will calibrate.
6. The ‘MENU’ button six times; message ‘Exit’ displayed.
7. The ‘PAUSE’ button once; message ‘Sensor calib’ displayed.
8. The ‘MENU’ button four times; message ‘Exit’ displayed.
9. The ‘PAUSE’ button once; message ‘Ready’ displayed.
14

4.1.2 Printer initialisation
Printer initialisation will restore default printer settings slown below.
Item Default value
Cleared by
initialisation
Parameter saved
when power off
Mileage N/A No Yes
Check sum N/A No Yes
Serial port 9600,n,8,1 Yes Yes
Code page 437 Yes Yes
Country code 001 Yes Yes
Tear mode On Yes Yes
Peel mode Off Yes Yes
Cutter mode Off Yes Yes
Offset 0 Yes Yes
Reference point 0,0 Yes Yes
Print direction 1 Yes Yes
Speed 4 inch/sec Yes Yes
Density 07 Yes Yes
Label size 4 x 2.5” Yes Yes
Gap/Bline sensor Gap Sensor Yes Yes
Gap(Bline) 0.12” (3 mm) Yes Yes
Transparency 142 Yes Yes
Ribbon sensor
sensitivity 1 Yes Yes
LCD language English Yes Yes
Aux. LED Off Yes Yes
Aux. Buzzer Off Yes Yes
Download files N/A No Yes
RTC N/A No No
Please follow the steps below to initialise the printer:
1. Turn off the printer power.
2. Hold down the PAUSE and FEED buttons and turn on the printer power.
3. Do not release the buttons until the red LED flash in turn.
Notes:
Printing method (thermal transfer or thermal direct printing ) will be set
automatically at the activation of printer power.
When printer initialisation is complete, please calibrate the gap/blackmark sensor
again.
15

4.2 Troubleshooting guide
The following guide lists the most common problems that may be encountered when
operating this printer. If it still does not function please contact your local Cembre office or
Agent.
Problem Reasons Solutions
“NO RIBBON”
1. Running out of ribbon.
2. The ribbon is
installed incorrectly.
3. The ribbon doesn’t pass
through the sensor.
1. Supply a new ribbon.
2. Refer to the steps in
section 3.2 to reinstall the ribbon.
3. Reintroduce the ribbon through
the ribbon detector.
“NO PAPER”
1. Running out of media.
2. The label roll is
installed incorrectly.
3. The moveable
gap/black mark sensor is
not placed in the proper
location.
1. Supply a new media reel.
2. Refer to the steps in section 3.3
to reinstall the media reel.
3. Move the sensor to the
proper location.
Poor printing
quality
1. Dirt has accumulated
on the print head.
2. The density setting is
incorrect.
3. Ribbon and media
are incompatible.
4. The pressure of the print
head is incorrect.
1. Refer to section 5.1 to clear the
print head.
2. Adjust the print density and
speed.
3. Use compatible proper
ribbon and media.
4. Refer to the section 2.4 to adjust
the print head pressure.
Power indicator
does not illuminate
1. The power cable is not
properly connected.
2. The voltage is not correct.
1. Check the power lead is property
between printer and mains.
2. Check the supply voltage at the
rear of printer.
“PAPER JAM”
1. The media size is not
set correctly.
2. Media may be stuck in
print mechanism.
1. a. Reset the media size.
b. Re-calibrate the gap/black
mark sensor.
2. Remove the stuck label.
“CARRIAGE OPEN”
The printer carriage is open. Close the print carriage.
16

5. PRINTER CLEANING
The printer should be cleaned regularly to retain high quality and optimum performance.
5.1 Print head cleaning
1. Switch off and unplug the printer.
2. Open the printer cover.
3. Open the print head using the lift lever.
4. Remove the media and ribbon (If loaded).
5. Using a swab soaked in dilute alcohol, wipe along the print head carefully.
6. Do not close the print head until the alcohol has evaporated.
7. Close the printer cover.
Do not use harsh or abrasive cleaning materials or solvent.
5.2 Printer cover cleaning
1. Switch off and unplug the printer.
2. Using a lint-free cloth soaked in water or mild detergent, lightly wipe the printer cover.
5.3 Internal parts cleaning
1. Switch off and unplug the printer.
2. Open the printer right side cover.
3. Remove the media and ribbon (If loaded).
4. Open the print head using the lift lever.
5. Using a soft cloth soaked in alcohol or mild detergent, carefully wipe the internal parts.
6. The rubber roller should be cleaned with a wet cloth.
7. Install the ribbon and media, close the print head lift lever.
8. Close the printer right side cover.
17

APPENDIX LCD Control Panel Function Map
18
Other manuals for Rolly 1000
1
Table of contents
Other Cembre Printer manuals
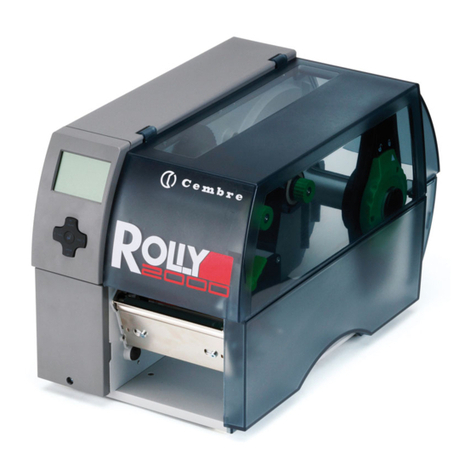
Cembre
Cembre ROLLY 2000 User manual
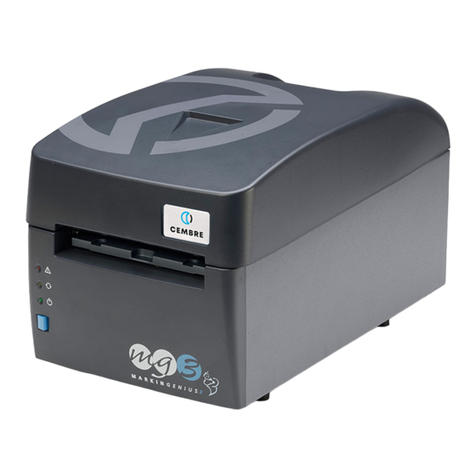
Cembre
Cembre Markingenius MG3 User manual
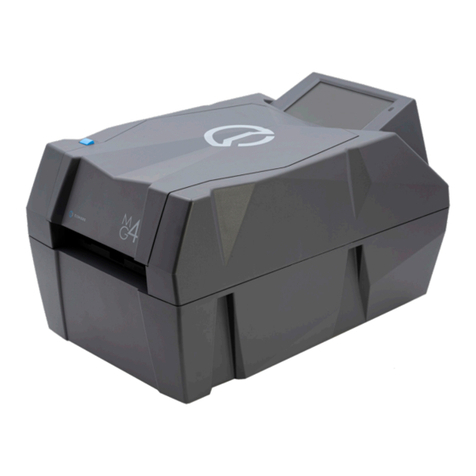
Cembre
Cembre MG4 User manual
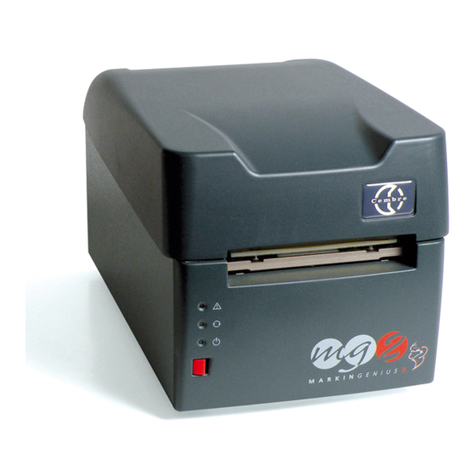
Cembre
Cembre MarkinGenius 2 User manual
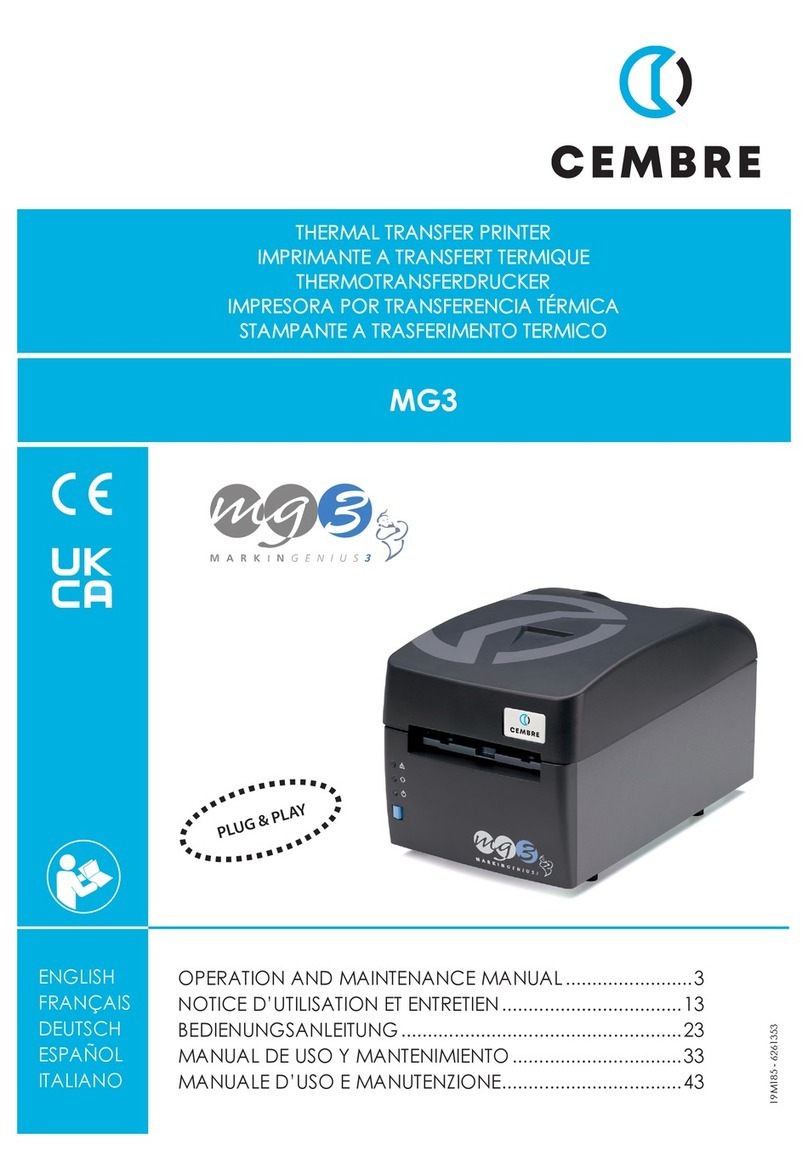
Cembre
Cembre MG3A User manual

Cembre
Cembre Rolly 1000 User manual
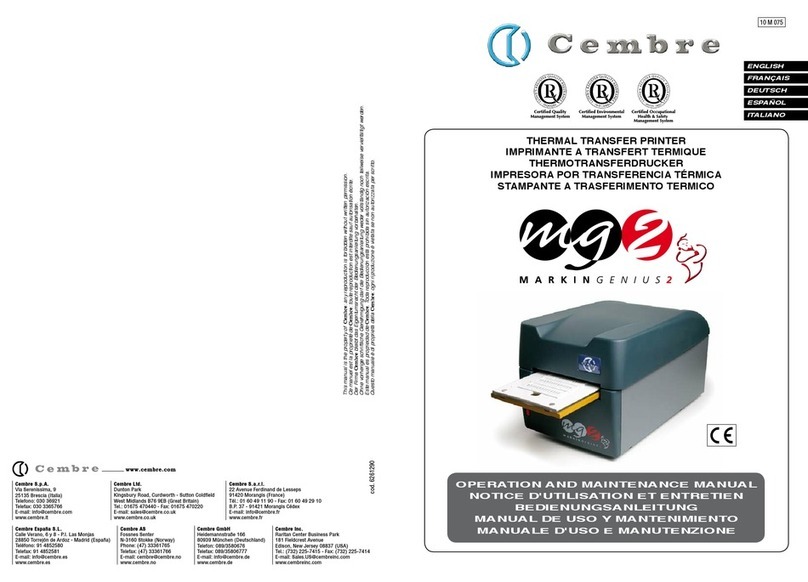
Cembre
Cembre Markin Genius2 User manual
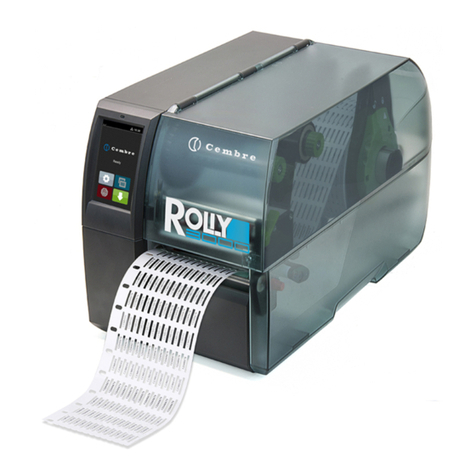
Cembre
Cembre ROLLY 3000 User manual
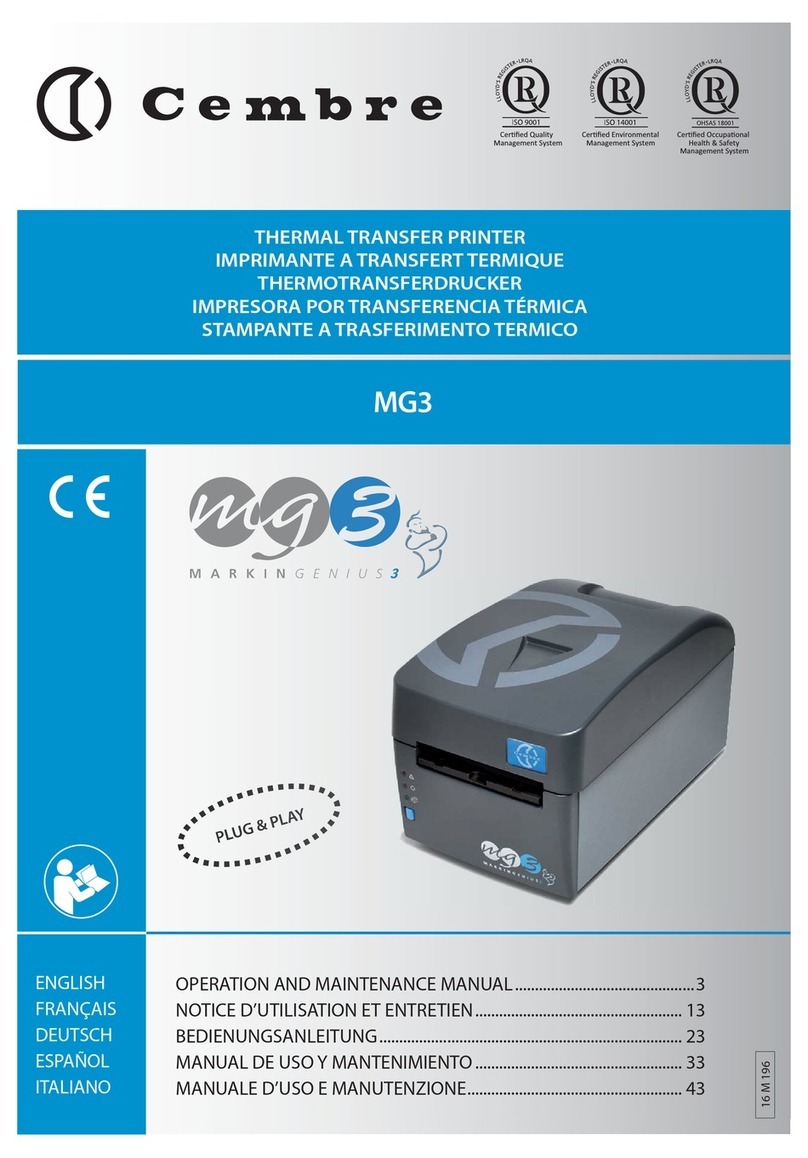
Cembre
Cembre Markingenius MG3 User manual
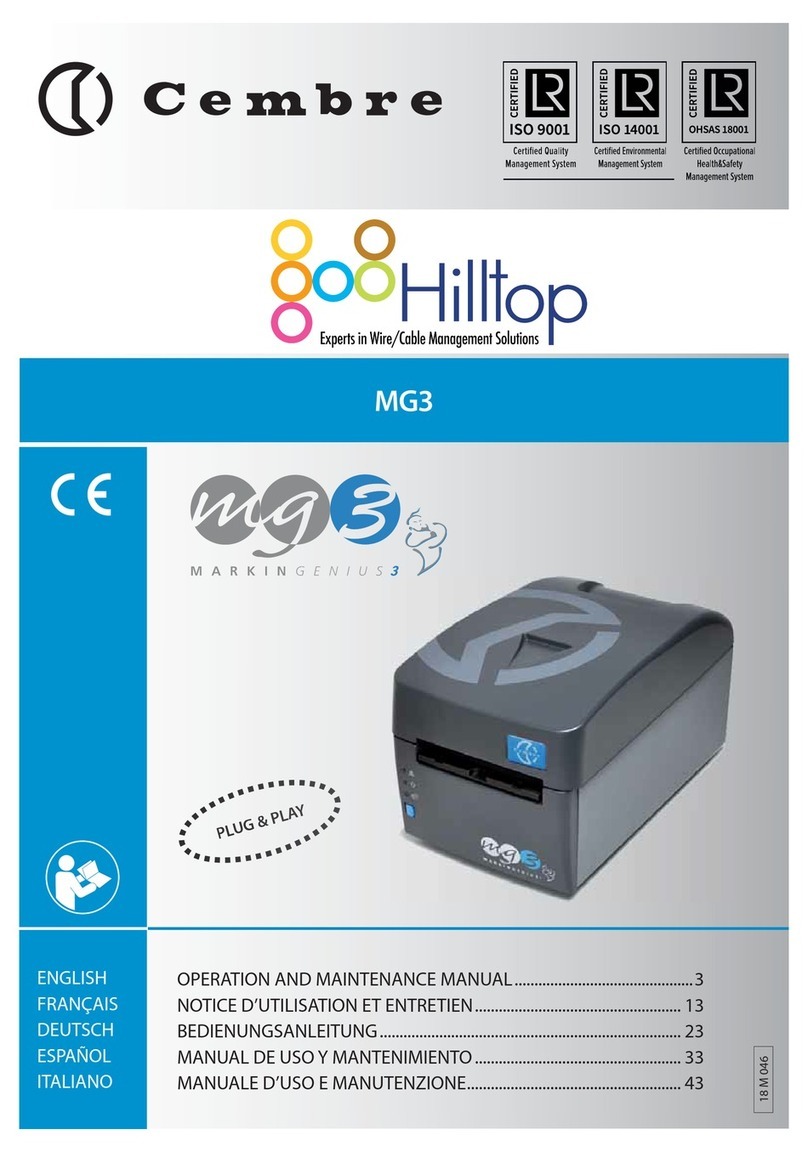
Cembre
Cembre Markingenius MG3 User manual