CG Emotron VS Series User manual

Smart solutions.
Strong relationships.
Emotron
VS Series Drive

Emotron VS Series Quick Start Guide
- 1 -
Thank you for choosing Emotron VS Series General Purpose AC Motor Drives
from CG Drives & Automation. This user manual presents a detailed description of
Emotron VS series with respect to product features, structural characteristics,
functions, installation, parameter setting, troubleshooting, commissioning and daily
maintenance, etc. Be sure to carefully read through the safety precautions before use,
and use this product on the premise that personnel and equipment safety is ensured.
IMPORTANT NOTES
◆To illustrate the details of the products,pictures in this manual based on products with outer
casing or safety cover being removed. When using this product, please be sure to well install
outer casing or covering by the rules, and operating in accordance with the manual contents.
◆The illustrations this manual for illustration only and may vary with different products you have
ordered.
◆The company is committed to continuous improvement of products, product features will
continue to upgrade, the information provided is subject to change without notice.
◆If you are using have questions, please contact our regional agents or our customer service
center.
◆The company's other products please visit our website. http://www.cgglobal.com
Emotron VS
AC drive
Quick Start Guide
Document number: 01-5480-02
Edition: r0.2
Date of release: 2019-08-08
© Copyright CG Power and Industrial Solutions Limited 2019 - 2020.
CGPISL retain the right to change specifications and illustrations in the text,
without prior notification. The contents of this document may not be copied
without the explicit permission of CGPISL.

Emotron VS Series Quick Start Guide
- 2 -
Contents
CONTENTS.................................................................................................................................. - 2 -
CHAPTER 1 SAFETY PRECAUTIONS ........................................................................................ - 4 -
1.1 SAFETY CONSIDERATIONS ..................................................................................................... - 4-
1.2 PRECAUTIONS...................................................................................................................... - 6-
CHAPTER 2 PRODUCT INFORMATION...................................................................................... - 8 -
2.1 NAMEPLATE INFORMATION ..................................................................................................... - 8-
2.2 INFORMATION OF CG PRODUCT MODEL .................................................................................. - 9-
2.3 TECHNICAL FEATURES ........................................................................................................ - 10 -
2.4 CONFIGURATION,MOUNTING DIMENSIONS AND WEIGHT ......................................................... - 14 -
2.5 EXTERNAL DIMENSIONS OF KEYPAD ..................................................................................... - 17 -
CHAPTER 3 INSTALLATION AND WIRING .............................................................................. - 19 -
3.1 INSTALLATION ENVIRONMENT ............................................................................................... - 19 -
3.2 INSTALLATION DIRECTION,SPACE AND COOLING .................................................................... - 19 -
3.3 FIXED MANNER ................................................................................................................... - 21 -
3.4 CONFIGURATION OF PERIPHERAL DEVICES ............................................................................ - 22 -
3.5 WIRING WAY OF VS SERIES ................................................................................................. - 25 -
3.6 TERMINAL CONFIGURATION.................................................................................................. - 28 -
3.7 EMI SOLUTIONS................................................................................................................. - 37 -
CHAPTER 4 OPERATION AND DISPLAY.................................................................................. - 39 -
4.1 INTRODUCTION OF LCD KEYPAD .......................................................................................... - 39 -
4.2 INTRODUCTION OF LED KEYPAD .......................................................................................... - 43 -
4.3 MOTOR AUTO-TUNING......................................................................................................... - 46 -
4.4 PASSWORD SETTING........................................................................................................... - 46 -
4.5 KEYPAD LOCK .................................................................................................................... - 46 -
CHAPTER 5 LIST OF PARAMETER.......................................................................................... - 47 -
5.1 FIVE LED (DIGITAL)DISPLAY INDICATORS............................................................................... - 48 -
5.2 STANDARD FUNCTION PARAMETERS ..................................................................................... - 48 -
CHAPTER 6 SPECIFICATION OF PARAMETERS .................................................................... - 83 -
GROUP A0 SYSTEM PARAMETERS.............................................................................................. - 83 -
GROUP B0FREQUENCY COMMAND............................................................................................. - 86 -
GROUP B1START/STOP CONTROL START/STOP CONTROL ........................................................... - 89 -
GROUP B2ACCEL/DECEL PARAMETERS...................................................................................... - 93 -
GROUP C0 DIGITAL INPUT ......................................................................................................... - 95 -
GROUP C1 DIGITAL OUTPUT.....................................................................................................-102 -
GROUP C2 ANALOG AND PULSE INPUT ......................................................................................-107 -
GROUP C3 ANALOG AND PULSE OUTPUT................................................................................... - 111 -
GROUP C4 VIRTUAL IO............................................................................................................- 112 -
GROUP D0PARAMETERS OF MOTOR 1 ......................................................................................- 113 -
GROUP D1V/F CONTROL PARAMETERS OF MOTOR 1..................................................................- 115 -
GROUP D2VECTOR CONTROL PARAMETERS OF MOTOR 1...........................................................- 119 -
GROUP D3PARAMETERS OF MOTOR 2 ......................................................................................-122 -
GROUP D4V/F CONTROL PARAMETERS OF MOTOR 2..................................................................-122 -
GROUP D5VECTOR CONTROL PARAMETERS OF MOTOR 2...........................................................-122 -
GROUP E0 PROTECTION PARAMETERS .....................................................................................-122 -
GROUP F0 PROCESS PID ........................................................................................................-127 -
GROUP F1 MULTI-REFERENCE AND SIMPLE PLC FUNCTION ........................................................-131 -

Emotron VS Series Quick Start Guide
- 3 -
GROUP F2 SWING FREQUENCY,FIXED LENGTH,COUNT AND WAKEUP..........................................-135 -
GROUP H0 COMMUNICATION PARAMETERS................................................................................-138 -
GROUP L0 KEYS AND DISPLAY OF KEYPAD PARAMETERS.............................................................-139 -
GROUP L1 USER-DEFINED DISPLAY PARAMETERS ......................................................................-140 -
GROUP U0 STATUS MONITORING ..............................................................................................-142 -
GROUP U1 FAULT RECORD ......................................................................................................-143 -
GROUP Y0INCENSE MAKING MACHINE PARAMETERS ...................................................................-144 -
CHAPTER 7 SOLAR COMMISSIONING.................................................................................. - 146 -
7.1 PARAMETERS DESCRIPTION................................................................................................-146 -
7.2 SOLAR COMMISSIONING GUIDE ...........................................................................................-151 -
CHAPTER 8 ELEVATOR COMMISSIONING ........................................................................... - 157 -
8.1 PARAMETERS DESCRIPTION................................................................................................-157 -
8.2.MULTI-STEP SPEED SETTING METHOD ..................................................................................-162 -
8.3 ELEVATOR COMMISIONING GUIDE........................................................................................-163 -
CHAPTER 9 MAINTENANCE AND TROUBLESHOOTING...................................................... - 164 -
CHAPTER 10 MAINTENANCE AND INSPECTION.................................................................. - 169 -
10.1 INSPECTION ....................................................................................................................-169 -
10.2 MAINTENANCE.................................................................................................................-170 -
APPENDIX A: MODBUS COMMUNICATION PROTOCOL ...................................................... - 172 -
APPENDIX B: BRAKING RESISTOR....................................................................................... - 178 -

Emotron VS Series Quick Start Guide
- 4 -
!
Chapter 1 Safety Precautions
Safety Precautions
Safety signs in this manual and in the main Instruction manual:
NOTE ! Additional information as an aid to avoid problems.
CAUTION!
Indicates the situation in which the failure to follow operating
requirements may cause moderate or slight injury and damage
to equipment
Warning!
Failure to follow these instructions can result in serious injury to
the user in addition to serious damage to the AC drive.
Users are requested to read this chapter carefully when installing, commissioning and repairing
this product and perform the operation according to safety precautions as set forth in this chapter
without fail. CG will bear no responsibility for any injury and loss as a result of any violation operation.
1.1 Safety Considerations
The use phase
Safety
class
Considerations
Before
Installation
Danger
◆Do not install the product if the package is with water, or
component is missing or broken.
◆Do not install the product if the label on the package is not
identical to that on the inverter.
Caution
◆Be careful of carrying or transportation. Risk of devices
damage.
◆Do not use damaged product or the inverters missing
component .Risk of injury.
◆Do not touch the parts of control system with bare hands. Risk
of ESD hazard.
Installation
Danger
◆Installation base shall be metal or other non-flammable
material. Risk of fire.
◆Do not install inverter in an environment containing explosive
gases, otherwise there is danger of explosion.
◆Do not unscrew the fixing bolts, especially the bolts with red
mark.
Caution
◆Do not leave cable strips or screws in the inverter. Risk of
inverter damage.
◆Install the product at the place with less vibration and no direct
sunlight.
◆Consider the installation space for cooling purpose when two
or more inverters are placed in the same cabinet.

Emotron VS Series Quick Start Guide
- 5 -
Wiring
Danger
◆Wiring must be performed by authorized and qualified
personnel. Risk of danger.
◆Circuit-breaker should be installed between inverter and the
mains. Risk of fire.
◆Make sure the input power supply has been completely
disconnected before wiring. Failure to comply may result in
personnel injury and/or equipment damage.
◆Since overall leakage current of this equipment may be bigger
than 3.5mA, for safety's sake, this equipment and its associated
motor must be well grounded so as to avoid risk of electric
shock.
◆Never connect the power cables to the output terminals (U/T1,
V/T2, W/T3) of the AC drive. Pay attention to the marks of the
wiring terminals and ensure correct wiring. Failure to comply will
result in damage to the AC drive.
◆Install braking resistors at terminals (+)and PB only. Failure to
comply may result in equipment damage.
◆AC 220V signal is prohibited from connecting to other
terminals than control terminals R1A, R1B, R1C andR2A, R2B,
R2C. Failure to comply may result in equipment damage.
Caution
◆Since all adjustable frequency AC drives from CG have been
subjected to hi-pot test before delivery, users are prohibited from
implementing such a test on this equipment. Failure to comply
may result in equipment damage.
◆Signal wires should to the best of the possibility be away from
main power lines. If this cannot be ensured, vertical
cross-arrangement shall be implemented, otherwise interference
noise to control signal may occur.
◆If motor cables are longer than 100m, it is recommended
output AC reactor be used. Failure to comply may result in faults.
Before
Power-on
Danger
◆Inverter shall be power-on only after the front cover is
assembled. Risk of electrical hazard.
Caution
◆Verify that the input voltage is identical to the rated voltage of
product, correct wiring of input terminals R/L1, S/L2, and T/L3
and output terminals U/T1, V/T2, and W/T3, wiring of inverter
and its peripheral circuits, and all wires should be in good
connection. Risk of inverter damage.
After Power-on
Danger
◆Do not open the cover after power. Risk of electrical hazard.
◆Do not touches any input/output terminals of inverter with bare
hands. Risk of electrical hazard.
Caution
◆If auto tuning is required, be careful of personal injury when
motor is running. Risk of accident.
◆Do not change the defaults of parameters. Risk of devices
damage.
During
Operation
Danger
◆Non-professionals shall not detect signals during operation.
Risk of personal injury or device damage.
◆Do not touch the fan or the discharging resistor to check the
temperature. Failure to comply will result in personal burnt.
Caution
◆Prevent any foreign items from being left in the devices during
operation. Risk of device damage.
◆Do not control start/stop of inverter by ON/OFF of contactor.
Risk of device damage.

Emotron VS Series Quick Start Guide
- 6 -
Maintenance
Danger
◆Maintenance and inspection can only be performed by
professionals . Risk of personal injury.
◆Maintain and inspect devices after power is off. Risk of
electric hazard.
◆Repair or maintain the AC drive only ten minutes after
the AC drive is powered off. This allows for the residual
voltage in the capacitor to discharge to a safe value.
Failure to comply will result in personal injury.
◆All pluggable components can be inserted or pulled out
only when power has been turned off.
◆Set and check the parameters again after the AC drive
is replaced.
1.2 Precautions
1.2.1 Motor Insulation Inspection
When the motor is used for the first time or when the motor is reused after being kept, or when
periodical inspection is performed, insulation inspection shall be conducted with motor so as to avoid
damaging the inverter because of the insulation failure of the motor windings. The motor wires must be
disconnected from the inverter during the insulation inspection. It is recommended to use the 500V
mega meter, and the insulating resistance measured shall be 5MΩ at least.
1.2.2 Motor Thermal Protection
If the motor rating does not match that of the inverter, especially when the rated power of the
inverter is higher than that of the motor, adjust motor protection parameters in the inverter or install
thermal relay to protect motor.
1.2.3 Operating with the Frequency Higher than Grid Power Frequency
Output frequency of VS is 0.00Hz~600.00Hz. If VS is required to operate above 50.00Hz, please
take the endurance of mechanical devices into consideration.
1.2.4 Mechanical Vibrations
Inverter may encounter mechanical resonance point of the load device at certain output
frequencies which can be avoided by setting the skip frequency parameters of the inverter.
1.2.5 Motor Heat and Noise
Since output voltage of inverter is PWM wave and contains a certain amount of harmonics, so
that the temperature, noise and vibration of the motor will be higher than those when the inverter runs
at grid power frequency.
1.2.6 Voltage-sensitive device or capacitor on output side of the AC drive
Do not install the capacitor for improving power factor or lightning protection voltage-sensitive
resistor on the output side of the AC drive because the output of the AC drive is PWM wave.
Otherwise, the AC drive may suffer transient overcurrent or even be damaged.
1.2.7 Contactor at the I/O terminal of the AC drive
When a contactor is installed between the input side of the AC drive and the power supply, the AC
drive must not be started or stopped by switching the contactor on or off. If the AC drive has to be
operated by the contactor, ensure that the time interval between switching is at least one hour since
frequent charge and discharge will shorten the service life of the capacitor inside the AC drive.
When a contactor is installed between the output side of the AC drive and the motor, do not turn
off the contactor when the AC drive is active. Otherwise, modules inside the AC drive may be
damaged.
1.2.8 Applied with the Rated Voltage
Apply VS with the rated voltage. Failure to comply will damage inverter. If required, take a
transformer to boost or step-down voltage.

Emotron VS Series Quick Start Guide
- 7 -
1.2.9 Do Not Apply a 3-Phase Input Inverter to 2-Phase Input Applications
Do not apply a 3-phase input inverter to 2-phase input applications. Otherwise, it will result in faults
or damage inverter.
1.2.10 Lightning Protection
VS has integrated lightning over-current protection device which has certain self-protection
capacity against the lightning. Additional protection devices have to be installed between inverter
and power supply in the area where lightning occurs frequently.
1.2.11 Altitude De-rating
In places where the altitude is above 1000 m and the cooling effect reduces due to thin air, it is
necessary to de-rate the AC drive. Contact CG for technical support.
1.2.12 Some special usages
If wiring that is not described in this manual such as common DC bus is applied, contact the agent
or CG for technical support.
1.2.13 Cautions for Inverter Disposal
The electrolytic capacitors on the main circuit and PCBA may explode when they are burnt.
Emission of toxic gas may be generated when the plastic parts are burnt. Please dispose inverter as
industrial wastes.
1.2.14 Adaptable Motor
The standard adaptable motor is adaptable industrial asynchronous induction motor or PMSM.
For other types of motor, select a proper AC drive according to the rated motor current.
The cooling fan and rotor shaft of non-variable-frequency motor are coaxial, which results in
reduced cooling effect when the rotational speed declines. If variable speed is required, add a more
powerful fan or replace it with variable-frequency motor in applications where the motor overheats
easily.
The standard parameters of the adaptable motor have been configured inside the AC drive. It is
still necessary to perform motor auto-tuning or modify the default values based on actual conditions.
Otherwise, the running result and protection performance will be affected.
The AC drive may alarm or even be damaged when short-circuit exists on cables or inside the
motor. Therefore, perform insulation short-circuit test when the motor and cables are newly installed or
during routine maintenance. During the test, make sure that the AC drive is disconnected from the
tested parts.

Emotron VS Series Quick Start Guide
- 8 -
Chapter 2 Product Information
2.1 Nameplate information
Fig 2-1 Nameplate information
Model Explanation
Model show on product nameplate contains information below.
VSX 48 - 009 - 20 CEB
Product Series
VSX - General Purpose Drive
VSM - Compact Machine Drive
VSS - Single Phase Drive
VSR - Solar Drive
Input ac voltage level
11:110-130Vac/160Vdc
23:220-240Vac/310Vdc
48:380-480Vac/540Vdc
Rated current(A)
003 –2.5A
- - -
009 –9.5A
2p5 –2.5A
- - -
9p5 –9.5A
Brake chopper
B = Brake chopper
EMC filter
N = No filter
E = C3 filter
Control panel
C = Standard panel
Protection class
20 = IP20
Fig 2-2 Model Explanation

Emotron VS Series Quick Start Guide
- 9 -
2.2 Information of CG Product Model
2.2.1 Information of CG General Drive
Table 2-1 VS Series General Product model and technical data
Model No.
Power capacity KVA
Rated
Input
current
A
Rated output
current
A
Applicable motor
kW
HP
VSX Series 3-Phase:415V,50/60Hz Range:-20%~+20%
VSX48-003-20CEB
1.5
3.4
2.5
0.75
1
VSX48-004-20CEB
3
5.0
4.2
1.5
2
VSX48-006-20CEB
4
5.8
5.5
2.2
3
VSX48-009-20CEB
6
11
9.5
3.7, 4
5
VSX48-013-20CEB
8.9
14.6
13
5.5
7.5
VSX48-017-20CEB
11
20.5
17
7.5
10
VSX48-024-20CEB
17
26
25
11
15
VSX48-032-20CEB
21
35
32
15
20
VSX48-038-20CEB
24
38.5
37
18.5
25
VSX48-045-20CEB
30
46.5
45
22
30
VSM Series 3-Phase:415V,50/60Hz Range:-20%~+20%
VSM48-003-20CEB
1.5
3.4
2.5
0.75
1
VSM48-004-20CEB
3.0
5.0
4.2
1.5
2
VSM48-006-20CEB
4.0
5.8
5.5
2.2
3
VSM48-009-20CEB
6.0
11
9.5
3.7, 4
5
VSS Series 1-Phase:220V,50/60Hz Range:-20%~+20%
VSS23 2p5 CEB
1.0
6.5
2.5
0.37,0.4
0.5
VSS23 4p2 CEB
1.5
9.3
4.2
0.75
1.0
VSS23 5p5 CEB
2.0
11
5.5
1.1
1.5
VSS23 7p5 CEB
3.0
15.7
7.5
1.5
2
VSS23 9p5 CEB
4.0
24
9.5
2.2
3
2.2.2 Information of CG Solar Drive
Table 2-2 VSR Series Product model and technical data
Model No.
Recommende
d Solar Array
Power kWP
Maximum
Input DC
Current A
Output
Current A
Motor kW
Frame
Size
VSR11 Series: 110VAC/160VDC input
VSR119p5
1.1
18
9.5
0.75
VSR2
VSR23 Series: 220VAC/310VDC input
VSR232p5
0.6
4.5
2.5
0.37, 0.4
VSR1
VSR234p2
1.1
7.5
4.2
0.75
VSR237p5
2.25
10
7.5
1.5
VSR2
VSR239p5
3.3
18
9.5
2.2
VSR48 Series:415VAC/540VDC input
VSR48003
1.1
4.5
2.5
0.75
VSR2
VSR48004
2.25
7.5
4.2
1.5
VSR48006
3.3
10
5.5
2.2
VSR48009
6
18
9.5
3.7, 4
VSR3
VSR48013
8.25
20
13
5.5
VSR48017
11
30
17
7.5

Emotron VS Series Quick Start Guide
- 10 -
2.3 Technical Features
2.3.1 Features of General Drive
Table 2-3 Technical features of general drive
Project
Specifications
Power input
Rated input
voltage (V)
3-phase 415 V (-20%~+20%)
1-phase 220V (-20%~+20%)
Rated input
current (A)
See table 2-1
Rated input
frequency(Hz)
50Hz/60Hz,tolerance±5%
Power output
Applicable motor
(kW)
See table 2-1
Rated output
current(A)
See table 2-1
The maximum
output voltage
(V)
0~rated input voltage, error<±3%
The maximum
output frequency
(Hz)
0.00~600.00 Hz,unit0.01Hz
Control
characteristics
V/f patterns
V/f control
Sensor-less vector control 1
Sensor-less vector control 2
Speed range
1:50 (V/f control)
1:100 (sensor-less vector control 1)
1:200(sensor-less vector control 2)
Speed accuracy
±0.5% (V/f control)
±0.2% (sensor-less vector control 1 & 2)
Speed
fluctuation
±0.3% (sensor-less vector control 1 & 2)
Torque response
< 10ms (sensor-less vector control 1 & 2)
Starting torque
0.5Hz: 180% (V/f control, sensor-less vector control 1)
0.25Hz: 180% (sensor-less vector control 2)
Basic functions
Carrier
frequency
0.7kHz~16kHz
Overload
capability
G Model:150% Rated Current 60s,180% Rated Current
10s,200% Rated Current 1s.
P Model:120% Rated Current 60s,145% Rated Current
10s,160% Rated Current 1s.
Torque boost
Automatic torque boost;Manual torque boost 0.1%~30.0%
V/F Curve
Three ways: Three ways: straight; multi-point type; N
Th-type V / F curve(1.2 Th -type, 1.4 Th -type, 1.6 Th -type,
1.8 Th -type, 2 Th -type)
Acceleration and
deceleration
Curve
Line or curve acceleration and deceleration mode.
Four kinds of acceleration and deceleration time,Ramp
Time Range :0.0~6000.0s
DC brake
DC brake start frequency: 0.00~600.00Hz
DC brake time:0.0s~10.0s
DC brake current:0.0%~150.0%
Basic functions
Jog brake
Jog frequency range:0.00Hz~50.00Hz.
Jog deceleration time: 0.0s~6000.0s.
Simple PLC,
Multi-speed
Through the built-in PLC or control terminal to achieve up to
16 speed running
Built-in PID
Facilitate the realization of process control loop control
system

Emotron VS Series Quick Start Guide
- 11 -
Automatic
voltage
adjustment
(AVR)
When the grid voltage changes, can automatically maintain
a constant output voltage
Fast current limit
function
Minimize over current fault protection inverter running
Over voltage
Over current
System automatically limits of current and voltage during
operation to prevent frequent
Run
Command
source
Given the control panel, control terminal, serial
communication port given.
Frequency given
Sources: digital setting, keyboard potentiometer setting,
analog Voltage, given analog current reference pulse is
given, the serial port is given, multi-speed given, PLC is
given, the process PI D reference. There are several ways
to switch
Input terminal
7 Switch input terminals, one way to make high-speed pulse
input.
3-channel analog inputs, including 2-way 0~10V / 0~
20mA voltage and current options,
a way to support -10~+10 V input
output
terminal
2-way switch output terminal, which supports a maximum
road speed 100kHz pulse output.
2 relay output terminals.
2 analog output terminal, and optional voltage and current.
Featured
functions
Parameter copy, parameter backup, flexible parameter displayed & hidden.
Common DC bus(Contains below 30 KW).
Various master & auxiliary command and switchover.
Reliable speed search started.
A variety of Accel / Decel curves programmable.
Timing control, fixed length control, count function.
Three faults recorded.
Over excitation brake, overvoltage stall protection programmable, under voltage
stall protection programmable, restart upon power loss.
Four kinds of Accel/Decel time.
Motor thermal protection.
Flexible fan control.
Process PID control, simple PLC, 16-step speed control programmable.
Wobble frequency control.
Multi-functional key programmable, field-weakening control.
High-precision torque control, V/f separated control, torque control at sensor-less
vector control.
Protection
function
Provide fault protection dozen: Overcurrent, Overvoltage, Undervoltage,
Overtemperature, Overload Etc Protection.
Display and
keyboard
LED Display
LCD Display
Display Parameters
Key lock and
function
selection
Realize some or all of the keys locked, scope definition
section keys to prevent misuse
Run and stop
monitoring
information
In the run or stop can be set to monitor U0 group four
objects were.
Environment
Place of
operation
Indoors, no direct sunlight, free from dust, corrosive gases,
flammable gases, oil mist, water vapor, water drop and salt,
etc.
Altitude
0~2000m
De-rate 1% for every 100m when the altitude is above 1000
meters

Emotron VS Series Quick Start Guide
- 12 -
Ambient
temperature
-10℃~40℃(VSS/VSR)
-10℃~50℃(VSM/VSX)
Relative
humidity
5~95%, no condensation
Vibration
Less than 5.9m/s2 (0.6g)
Storage
temperature
-20℃~+70℃
Others
Efficiency
Rated power≥93%
Installation
Wall-mounted or Flange mounting
IP grade
IP20
Cooling
method
Fan cooled
2.3.2 Features of Solar Drive
Table 2-4 VSR11 Series Technical features
Input specification
PV Input
Maximum Input DC Voltage
400VDC
Recommended Voc Range
170~400VDC
Recommended MPPT
Voltage Range
140~240VDC
Starting Voltage Range
80~400VDC
Grid or backup generator input
Input voltage
Single phase110V (-15%~30%)
Output specification
Rated output voltage
3PH 110V
Output frequency
0~600.00Hz(default: 0~50.00Hz)
Protection
Built-in Protection
Lightening protection, over-current, overvoltage, output phase-lose,
under-load, under-voltage, short circuit, overheating, water pump dry
run etc.
Table 2-5 VSR23 Series Technical features
Input specification
PV Input
Maximum Input DC Voltage
450VDC
Recommended Voc Range
320~370VDC
Recommended MPPT
Voltage Range
250~350VDC
Starting Voltage Range
80~450VDC
Grid or backup generator input
Input voltage
Single phase 220V (-20%~20%)
Output specification
Rated output voltage
3PH 220V
Output frequency
0~600.00Hz(default: 0~50.00Hz)
Protection
Built-in Protection
Lightening protection, over-current, overvoltage, output phase-lose,
under-load, under-voltage, short circuit, overheating, water pump dry
run etc.
Table 2-6 VSR48 Series Technical features
Input specification
PV Input
Maximum Input DC Voltage
800VDC

Emotron VS Series Quick Start Guide
- 13 -
Recommended Voc Range
500~700VDC
Recommended MPPT
Voltage Range
450~600VDC
Starting Voltage Range
230~800VDC
Grid or backup generator input
Input Voltage
Three phase 415V(-20%~20%)
Output specification
Rated output voltage
3PH 415V
Output frequency
0~600.00Hz(Default 0~50.00Hz)
Protection
Built-in Protection
Lightening protection, over-current, overvoltage, output phase-lose,
under-load, under-voltage, short circuit, overheating, water pump dry
run etc.
General Parameters
Application Site
No direct sunshine, no dust, corrosive gas, combustible gas, oil mist,
steam, dripping or salinity etc.
Altitude
0~2000 m
.Above 1000m, derate the rated current capacity by 1% for every
100m
Environment Temperature
-10℃~50℃(Above 40℃~ with deration)
Above 40℃, derate the rated current capacity by 1% for every 1℃.
Humidity
5~95%,non-condensation
Vibration
less than 5.9 m/s2(0.6g)
Storage Temperature
-20℃~+70℃
Efficiency
Rated Power Run≥93%
Installation
Wall or rail mounting
Protection Grade
IP20
Cooling
Forced Air Cooling

Emotron VS Series Quick Start Guide
- 14 -
2.4 Configuration, Mounting Dimensions and Weight
2.4.1 VSX Series
◆0.7~2.2KW Dimensions and wall mounting dimensions:
H
H1
W
W1
2-φd
D
2-φ6.0
2-φ3.0
Fig 2-3 0.7~2.2kW Wall installation diagram
◆4~22KW Dimensions and wall mounting dimensions:
Fig 2-4 4~22kW Wall installation diagram

Emotron VS Series Quick Start Guide
- 15 -
Table 2-7 Configuration, mounting dimensions and weight
Model NO.
External and installation dimensions(mm)
Weight
(Kg)
W
H
D
W1
H1
Mounting
Hole
Diameter
3-Phase:415V,50/60Hz Range:-20%~+20%
VSX48-003-20CEB
80
200
170
60
185
4.5
1.45
VSX48-004-20CEB
VSX48-006-20CEB
VSX48-009-20CEB
116.6
186.6
175
106.6
176.6
4.5
2.45
VSX48-013-20CEB
2.5
VSX48-017-20CEB
146
249
181.7
131
236
5.5
3.4
VSX48-024-20CEB
3.5
VSX48-032-20CEB
198
300
189.7
183
287
5.5
6.35
VSX48-038-20CEB
6.45
VSX48-045-20CEB
6.45
2.4.2 VSM Series
W
H
D
H1
W1
d1
H2
d2
H3
Fig 2-5 Product size
Table 2-8 Configuration, mounting dimensions and weight
Model.
External and Install dimensions (mm)
N.W
(kg)
W
H
D
W1
H1
H2
H3
Install
hole
d1
Install
hole
d2
VSM48-003-20CEB
75
150
117
65
140
35
38.5
4.5
4.5
0.85
VSM48-004-20CEB
VSM48-006-20CEB
93
171
130
82
160
35
39
4.5
4.5
1.45
VSM48-009-20CEB

Emotron VS Series Quick Start Guide
- 16 -
2.4.3 VSS Series
Fig 2-6 Product size
Table 2-9 Configuration, mounting dimensions and weight
Model
External and installation dimensions(mm)
Wei
ght
(kg)
W
H
D
W1
W2
H1
H2
H3
H4
Install
Hole
d1
Install
Hole
d2
Single-Phase: 220V,50/60Hz
VSS23 2p5 CEB
95
162
120
85
11
151.5
152
110.8
130
4.5
4.5
1.1
VSS23 4p2 CEB
VSS23 5p5 CEB
110
173
135
100
11
163
163
121.8
140.5
4.5
5
1.5
VSS23 7p5 CEB
VSS23 9p5 CEB
2.4.4 VSR Series
◆VSR frame 1 and 2
(Same with VSS)

Emotron VS Series Quick Start Guide
- 17 -
◆VSR frame 3
Table 2-10 Product size chart
Model No.
Dimensions and installation size(mm)
Weight
(kg)
W
W1
H
H1
D
Installation
Aperture
VSR3
146
131
249
236
177
5.5
3.2
2.5 External Dimensions of Keypad
2.5.1 VSX Series
74.6
116.6
R4.3
15.5
2
0.15
3.8
28
8
71.6
113.6
15.9
15.6
Fig 2-7 LCD Keyboard size diagram
External keyboard installation instruction:
1. first install the panel according to inverter’s power range corresponding to the size of hole as shown
on scheme 2-11, After that insert keyboard pad into the mounting panel and then insert the
keyboard module into the keyboard pad.(Before removing the keyboard pad, first remove the
keyboard, then remove as shown in the scheme).

Emotron VS Series Quick Start Guide
- 18 -
80+0.2
-0
135+0.2
-0
1
2
Keypad assembly Keypad tray Mounting plate
(The thickness of the
plate can`t be more
than 1.5 mm)
Press 4 hooks on both sides of the
mounting ,the keypad tray will be get out
LCD:Hole
size of mounting plate
Fig 2-8 LCD keyboard installation hole size diagram
2.5.2 VSS/VSR Series
Fig 2-9 Keyboard size diagram
External keyboard installation instruction:
1.first install the panel according to inverter’s power range corresponding to the size of hole as shown
on scheme 2-5, After that insert keyboard pad into the mounting panel and then insert the keyboard
module into the keyboard pad. (Before removing the keyboard pad, first remove the keyboard, then
remove the pad as shown in the scheme)
1
2
64+0.2
-0
99+0.2
-0
Keypad assembly Keypad tray Mounting plate
(The thickness of the
plate can`t be more
than 1.5 mm)
Press 4 hooks on both sides of the
mounting ,the keypad tray will be get out
Hole size of mounting plate
Mounting plate
Fig 2-10 External keyboard installation whole size diagram

Emotron VS Series Quick Start Guide
- 19 -
Chapter 3 Installation and Wiring
3.1 Installation Environment
1) Ambient temperature in the range of -10℃~50℃.
2) Drive should be installed on surface of flame retardant object, with adequate surrounding space for
heat dissipation.
3) Installation should be performed where vibration is less than 5.9m/s2 (0.6g).
4) Avoid from moisture and direct sunlight.
5) Protect the cooling fan by avoiding oil, dust and metal particles;
6) Do not expose to an atmosphere with flammable gases, corrosive gases, explosive gases or other
harmful gases.
7) Prevent drilling residues, wire ends and screws falling into drive.
8) Ventilation part of the drive should be installed outside from harsh environment (e.g. Textile facilities
with fiber particles and chemical facilities filled with corrosive gases or Loaded dust cover).
3.2 Installation Direction, Space and Cooling
Below is an example of VSX inverter.(VSM & VSS & VSR are same as VSX)
A fan is integrated in VSX for forced air cooling. VSX has to be installed vertically for the purpose
of good cooling circulation. Sufficient spaces have to be left between VSX and its peripheral objects.
Multi- VSX can be installed in parallel horizontally and vertically. See followings for specific space
requirement, heat dissipating capacity and mass airflow.
VS series inverter installation : Wall installation.
The wall mount
Fig 3-1 Installation methods
This manual suits for next models
30
Table of contents
Other CG DC Drive manuals
Popular DC Drive manuals by other brands
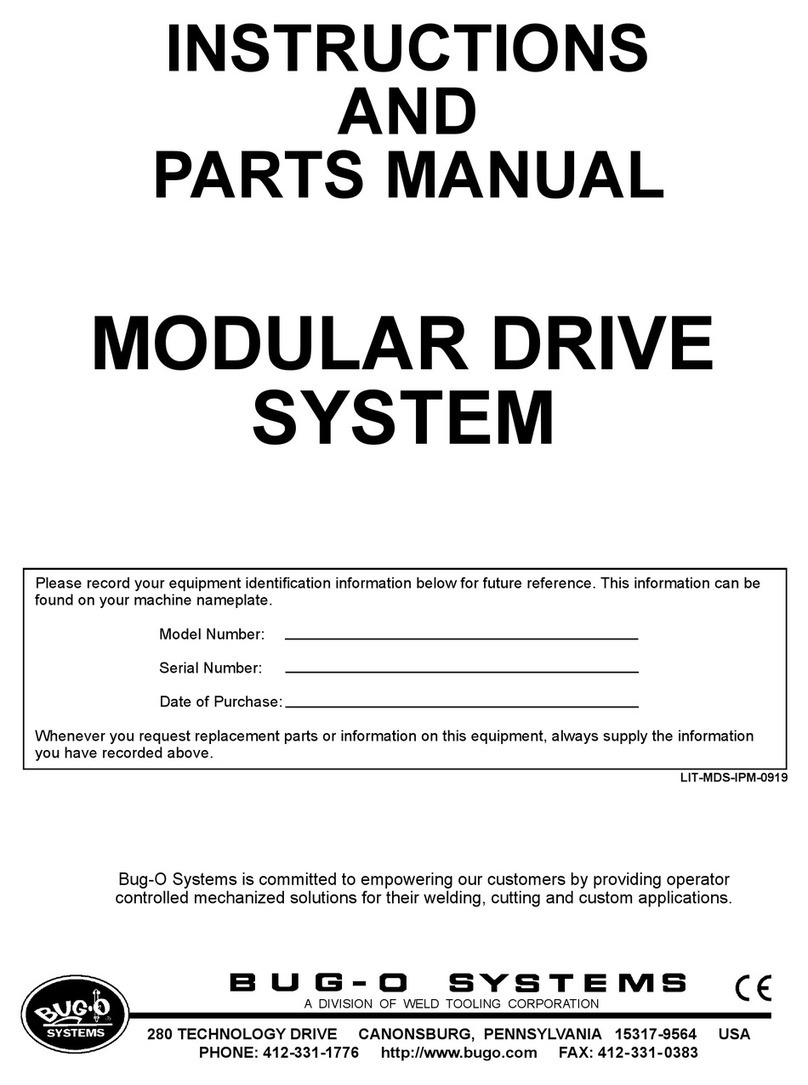
WELD TOOLING CORPORATION
WELD TOOLING CORPORATION BUG-O SYSTEMS MPD-1000 Instructions and parts manual
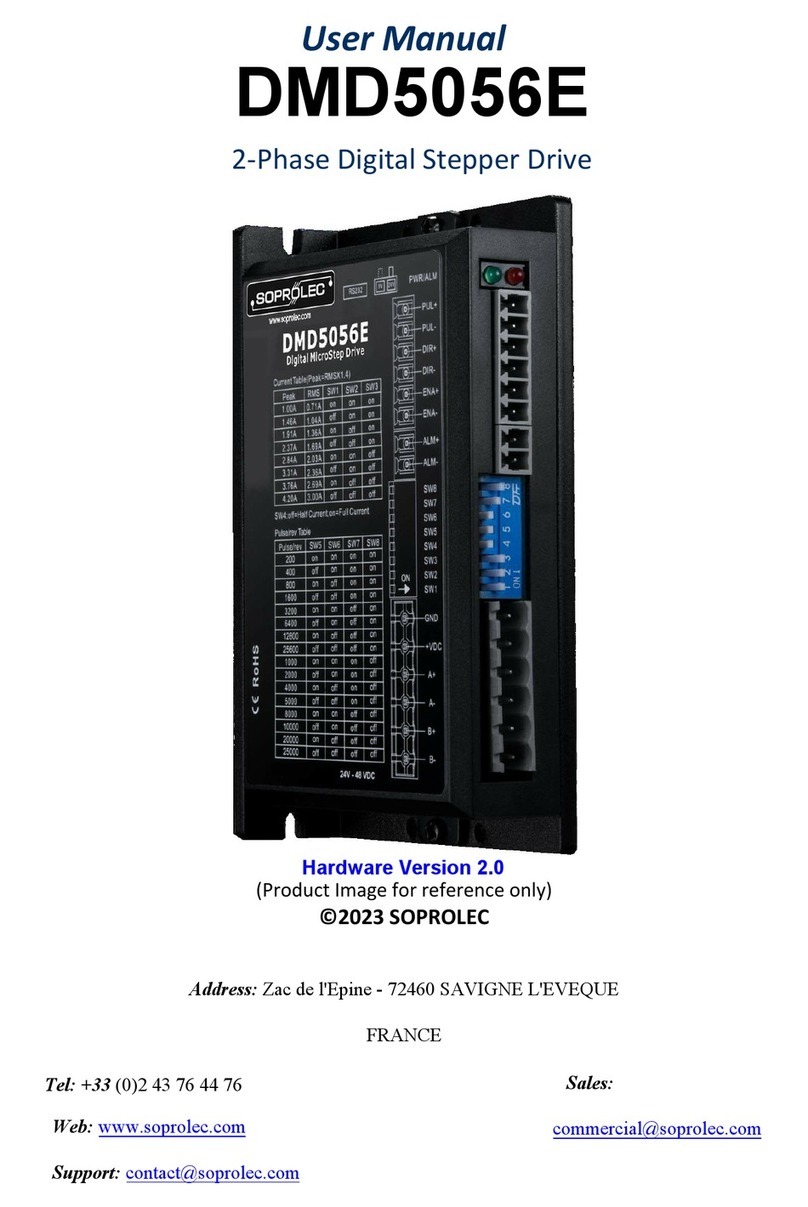
SOPROLEC
SOPROLEC DMD5056E user manual
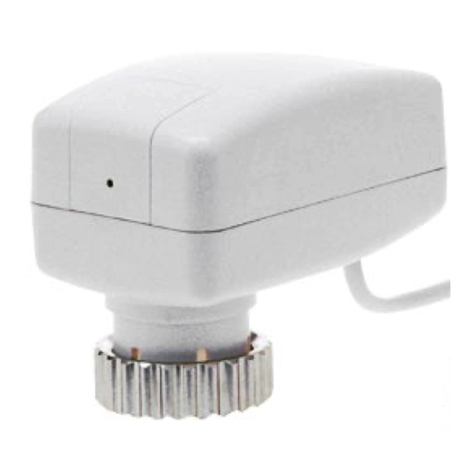
sauter
sauter AXM 117SSeries manual
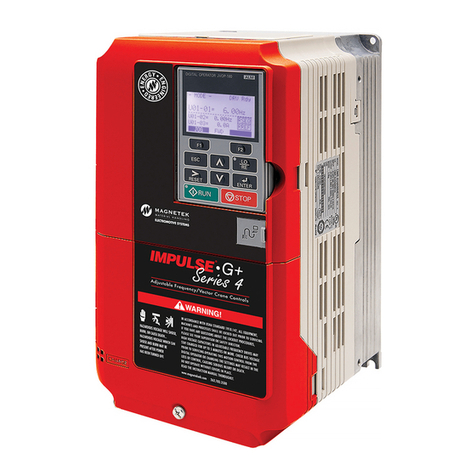
Magnetek
Magnetek Impulse G+ series 4 Technical manual
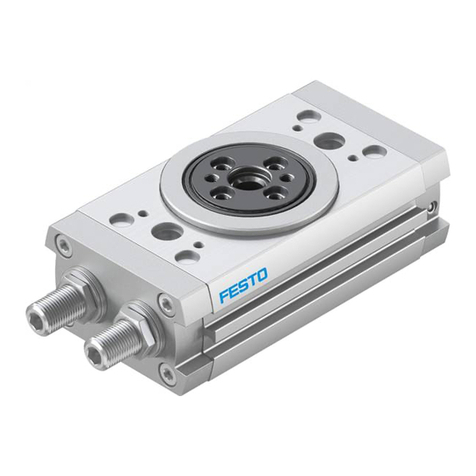
Festo
Festo DRRD-12 operating instructions

Esco
Esco FA121 EKS Series Mounting and operating instruction