Cincinnati Fan DDF Guide

OMM-14-0509-page 1
Installation, Safety, Operation & Maintenance Instructions And Parts List
For Model DDF, Direct Drive Tube Axial Fans
Arrangement 4
All Cincinnati Fan products are packaged to minimize any damage during shipment. The freight carrier is responsible
for delivering all items in their original condition as received from Cincinnati Fan. The individual receiving this equipment
is responsible for inspecting this unit for any obvious or concealed damage. If any damage is found, it should be noted
on the bill of lading before the freight is accepted and the receiver must file a claim with the freight carrier.
ATTENTION: RECEIVING DEPARTMENT
LONG TERM STORAGE NOTICE
If this fan will NOT be installed and put into operation within 30 days, refer to the “Long Term Storage
Instructions” on page 11. Failure to follow all applicable long term storage instructions, will void your warranty.
This fan should be stored indoors in a clean, dry location.
FAN SERIAL NUMBER: ________________________ MFG. DATE: ____________________
NOTE: The serial number above is a required reference for any assistance. It is stamped on the fan nameplate.
FAN SPECIFICATIONS:
Model: ________ Wheel Size and Type: ___________________
FAN PERFORMANCE DATA: (If entered on order)
CFM: ________ SP: ________ (Inches of Water Gauge) Motor BHP: ________
Density: ________ Altitude: ________ (Ft. above S. .) Airstream Temperature: ________°F.
Fan RPM: ________ Maximum Safe Fan RPM: ____________ DO NOT EXCEED THIS RPM
MOTOR DATA: (This section is completed only if the motor was supplied by Cincinnati Fan)
HP: __________ RPM: ____________ Voltage: ______________________________ Phase:________
Hz: ___________ Frame Size: ___________ Enclosure: ____________ Efficiency: ____________
IF Motor is EXP, Class(es) & Group(s) are:_________________________
Manufacturers Model Number: ___________________________ CFV Part Number: ___________
FAN SPECIFICATIONS
Form: OMM-14-0509
Effective: 5/4/09
Supersedes: OMM-14-0507
Part No.: 01230
READ ENTIRE MANUAL INCLUDING “SECTION IV. INITIAL UNIT STARTUP” BEFORE
ATTEMPTING TO INSTALL AND OPERATE THIS EQUIPMENT.
NOTE

DANGER
OMM-14-0509-page 2
TABLE OF CONTENTS
Hazardous voltage High speed rotating ock out/Tag out to Avoid injury. NEVER Avoid injury. You MUST
can cause electrical equipment can cause prevent personal injury operate without A read and understand all
shock and death. severe personal injury. BEFORE starting ANY required safety instructions in this manual
service or inspection. guards in place. BEFORE installing.
I. GENERAL
A. Unpacking and Handling .............................2
B. Safety Accessories & Instructions............2-3
II. INSTALLATION
A. Vibration.......................................................3
B. Mounting Methods....................................3-4
C. Safety Guards..............................................4
D. Dampers and Shutters.................................4
E. Set Screw & Taper-lock Bushing
Torque Values ..............................................4
III. ELECTRICAL
A. Disconnect Switches ...................................5
B. Motors.......................................................5-6
C. Maximum Fan Speed ..................................6
IV. INITIAL UNIT STARTUP
A. Pre-Startup & Post-Startup Checks.............7
B. Vibration.......................................................7
V. ROUTINE INSPECTION & MAINTENANCE.....8
A. Hardware .....................................................8
B. Motor Bearing ubrication ...........................8
C. Propeller Balance ........................................8
D. Vibration.......................................................8
E. Dampers and Shutters ................................8
F. Safety Equipment or Accessories ................9
VI. ORDERING PARTS ...........................................9
VII. TROUBLESHOOTING .....................................10
VIII. LONG TERM STORAGE .................................11
IX. WARRANTY, LIABILITY & RETURNS............12
X. PARTS DRAWING ...........................................13
I. GENERAL
A. Unpacking:
Be careful not to damage or deform any parts of the fan when removing it from the packaging container. All the
packaging material should be kept in the event the fan needs to be returned.
Handling:
Handling of the fan should be performed by trained personnel and be consistent with all safe handling practices.
Verify that all lifting equipment is in good operating condition and has the proper lifting capacity. The fan should be
lifted using well-padded chains, cables or lifting straps with spreader bars. Some fan models have lifting eye
locations provided in the fan base. NEVER lift the fan by the motor shaft, motor eye bolt, or any other part of
the fan assembly that could cause distortion of the fan assembly.
B. Safety Instructions & Accessories:
1. Safety Instructions:
All installers, operators and maintenance personnel should read AMCA Publication 410-96, “Recommended Safety
Practices for Users and Installers of Industrial and Commercial Fans”. This manual is included with the fan.
Additional copies can be requested by writing us at Cincinnati Fan, 7697 Snider Rd., Mason, OH 45040-9135
2. Sound:
Some fans can generate sound that could be hazardous to personnel. It is the responsibility of the user to measure the
sound levels of the fan and/or system, determine the degree of personnel exposure, and comply with all applicable
safety laws and requirements to protect personnel from excessive noise.
3. Air Pressure and Suction:
In addition to the normal dangers of rotating machinery, the fan can present additional hazards from the suction or pres-
sure created at the fan inlet or discharge. Suction at the fan inlet can draw materials into the fan where they become high
velocity projectiles at the discharge and cause severe personal injury or death. It can also be extremely dangerous to per-
sons in close proximity to the inlet or discharge as the forces involved can overcome the strength of most individuals.

OMM-14-0509-page 3
NEVER OPERATE A FAN WITH A NON-DUCTED INLET AND/OR DISCHARGE. IF THE FAN INLET
AND/OR DISCHARGE IS NON-DUCTED, IT IS THE USERS RESPONSIBILITY TO INSTALL AN
INLET AND/OR DISCHARGE GUARD.
NO GUARANTEE OF ANY LEVEL OF SPAR RESISTANCE IS IMPLIED BY SPAR RESISTANT
CONSTRUCTION. IT HAS BEEN DEMONSTRATED THAT ALUMINUM IMPELLERS RUBBING ON RUSTY
STEEL CAN CAUSE HIGH INTENSITY SPAR S. AIR STREAM MATERIAL AND DEBRIS OR OTHER SYSTEM
FACTORS CAN ALSO CAUSE SPAR S.
4. Temperature:
Some fans, fan components and all motors operate at temperatures that could burn someone if they come in contact
with them. If this potential hazard could exist in your installation, steps must be taken by the user to protect anyone
from coming in contact with this equipment.
5. Spark Resistance; (Per AMCA Standard 99-0401-86 and ISO 13499)
6. Safety Accessories:
Guards:
All moving parts must be guarded to protect personnel. Safety requirements can vary, so the number and types of
guards required to meet company, local, state and OSHA regulations must be determined and specified by the actual
user or operator of the equipment.
NEVER start any fan without having all required safety guards properly installed. All fans should be checked on
a regular schedule, for missing or damaged guards. If any required guards are found to be missing or defec-
tive, the power to the fan should be immediately turned off and locked out in accordance with OSHA regula-
tions. Power to the fan should NOT be tuned back on until the required guards have been repaired or replaced.
This fan can become dangerous due to a potential “windmill” effect, even though all electrical power has been turned off
or disconnected. The propeller should be carefully secured to prevent any rotational turning BEFORE working on any
parts of the fan/motor assembly that could move.
7. Access or Inspection Doors:
II. INSTALLATION
A. Vibration:
Before any mounting method is selected, the user should be aware of the effects vibration will have on the fan, motor
and other parts. Improper fan installation can cause excessive vibration causing premature prop and/or motor bearing
failure, that is not covered under warranty. Vibration eliminator pads, springs or flexible connectors should be properly
installed to prevent any fan vibration from transmitting to the foundation, support structure or ducting.
B. Mounting Methods:
1. In Duct Work
Any component of a building structure that will be supporting the fan and any duct work must have the weight load
capacity and be rigid enough to support the weight of the fan without bending, bowing or flexing during operation. If not,
severe vibration can occur that could lead to fan and/or structural failure. Consult an architectural or structural engineer
for assistance.
Model DDF fans are designed to be mounted in duct work of the same diameter as the fan. The flange rings are pre-
punched and should be bolted to duct flanges having the same dimensions. We do offer companion rings, as an option,
to make the connection process easier. These fans can be mounted with the motor shaft in a horizontal or vertical up-
blast (motor shaft up) configuration.
WARNING
DANGER
I
SHUT THE FAN DOWN IMMEDIATELY IF THERE IS ANY SUDDEN INCREASE IN VIBRATION.
WARNING
NEVER OPEN ANY ACCESS OR INSPECTION DOORS WHILE THE FAN IS OPERATING. SERIOUS INJURY OR
DEATH COULD RESULT FROM THE AFFECTS OF AIR PRESSURE OR AIR SUCTION. DISCONNECT OR LOC
OUT POWER TO THE FAN AND LET THE PROP COME TO A COMPLETE STOP BEFORE OPENING ANY TYPE OF
ACCESS OR INSPECTION DOOR.
DANGER

The use of flexible connectors on the inlet and outlet of the fan will make it possible to mount this fan in a duct system
and isolate any fan/motor vibration from the duct work. If flexible connectors will be used, the fan should be equipped
with horizontal or vertical support clips. Threaded rod should be used to connect the support clips to the building struc-
ture. Each rod should be strong enough to support two (2) times the weight of the entire fan/motor assembly. Spring
hangers would be needed on the rods to isolate any fan vibration from the building.
The connectors should be selected to handle the operating conditions for air volume and pressure that the fan will pro-
duce. All ducting or accessories, added by the user, should be independently supported. DO NOT use the
fan/motor assembly to support any additional weight. Inlet and/or discharge duct elbows should be located a mini-
mum of 3 fan diameters from the fan. Any duct elbows located closer than 3 wheel diameters to the fan inlet or discharge
WILL reduce the air performance and fan efficiency.
Non-Ducted Fan Inlet:
Any fan with no ducting on the inlet must have an inlet guard. The fan should be located so the inlet is, at least, 3 fan
diameters away from any wall or bulkhead to eliminate a reduction in air flow.
Non-Ducted Fan Discharge:
Any fan with no ducting on the discharge must have a discharge guard.
2. On Machinery
If this fan will be mounted on machinery, the surface it will be mounted to must be strong and rigid enough to support the
weight of the entire fan without flexing, bowing, bending or oil-canning and thus causing vibration. Companion rings are
available that will match the flanges on the DDF fan. To minimize any leakage, it is recommended that some type of
caulking be used between the fan flange and the machine.
C. Safety Guards:
Cincinnati Fan offers guards, as optional, to keep your fan in compliance with OSHA safety regulations. These include
inlet or discharge guards. It is the responsibility of the user to make sure this fan meets all local, state and OSHA safety
regulations. If you have a specific guard requirement not covered by OSHA, please contact the local Cincinnati Fan sales
office for assistance.
D. Dampers and Shutters: (Airflow control devices)
If the fan is supplied with any type of air flow control device, it should be closed before initial start-up of the fan to mini-
mize overloading of the motor. Any airflow control device, with bearings, should be maintained in accordance with the
manufacturers instructions. Any air flow control device, with an automatic control mechanism, should be adjusted per the
manufacturers recommendations. Automatic shutters are opened and closed by the airflow from the fan.
E. Set Screw and Taper-lock Bushing Torque Values:
All propeller set screws are tightened to the proper torque prior to shipment. Some props may have taper-lock hubs and
split, taper-lock bushings to secure the prop to the motor shaft.
NOTE: Check all set screw or taper-lock bushing torques. Forces encountered during shipment, handling, rigging and
temperature can affect factory settings. For correct torque values, see Tables 1 and 2below.
OMM-14-0509-page 4
DANGER
SET SCREW TORQUE VALUES TORQUE VALUES FOR
TAPER-LOCK BUSHINGS
Diameter & Number
of Treads/Inch
Hex Wrence Size
(Across Flats)
Required Torque
(Inch Pounds)
1/4-20
5/16-18
3/8-16
7/16-14
1/2-13
5/8-11
1/8”
5/32”
3/16”
7/32”
1/4”
5/16”
65
165
228
348
504
1104
Taper-lock
Bushing Size
Required Torque
(Inch Pounds)
H
B
P
Q
R
95
192
192
350
350
Table 2Table 1

OMM-14-0509-page 5
Set screws should NEVER be used more than once. If the set screws are loosened, they MUST be replaced.
Use only knurled, cup-point, set screws with a nylon locking patch.
CAUTION
ALL WIRING CONNECTIONS, INSPECTION AND MAINTENANCE OF ANY MOTOR MUST BE PERFORMED BY A
LICENSED ELECTRICIAN IN ACCORDANCE WITH THE MOTOR MANUFACTURERS RECOMMENDATIONS, ALL
ELECTRICAL CODES AND OSHA REGULATIONS. FAILURE TO PROPERLY INSTALL, MA E WIRING
CONNECTIONS, INSPECT OR PERFORM ANY MAINTENANCE TO A MOTOR CAN RESULT IN
MOTOR FAILURE, PROPERTY DAMAGE, EXPLOSION, ELECTRICAL SHOC AND DEATH.
DANGER
III. ELECTRICAL
A. Disconnect Switches:
All fan motors should have an independent disconnect switch located in close visual proximity to turn off the electri-
cal service to the fan motor. Disconnects must be locked out in accordance with OSHA “lock out-tag out” pro-
cedures any time inspection or maintenance is being performed on the fan and/or motor assembly. The
“lock out-tag out” procedure should be performed by a licensed electrician or authorized personnel.
All disconnects should be sized in accordance with the latest NEC codes (National Electric Codes) and any local
codes and should be installed only by a licensed electrician. “Slow blow” or “time delay” fuses or breakers should be
used since the initial start-up time for the fan motor, although rare, can be up to 10 seconds.
B. Motors:
1. DO NOT connect or operate a motor without reading the motor manufacturers instructions supplied with the
fan. The basic principle of motor maintenance is: EEP THE MOTOR CLEAN AND DRY. This requires periodic
inspections of the motor. The frequency of the inspections depends on the type of motor, the service and environ-
ment it will be subjected to and the motor manufacturers instructions.
2. Cleaning: Cleaning should be limited to exterior surfaces only. Follow motor manufacturers cleaning instruc-
tions.
3. Lubrication: Most small motors have sealed bearings that are permanently lubricated for the life of the motor. Some
larger motors have grease plugs that should be replaced with grease fittings to perform re-lubrication. These motors,
or any motor with grease fittings, should be lubricated in accordance with the motor manufacturers recommenda-
tions. ubrication frequency depends on the motor horsepower, speed and service. BE SURE you use compatible
grease and DO NOT over grease.
4. Location: On Model DDF fans, the motor is in the airstream. The standard motor is a Totally Enclosed type motor
which is suitable in a clean, dry airstream below 104°F. (40°C). If the airstream will be wet, dirty or reach tempera-
tures above 104°F (40°C), a completely different type of fan should be used. Consult our local sales office for your
area for proper fan selection assistance. On 12” and 15” fan sizes, if the motor is an Explosion Proof type, the motor
conduit box will not fit on the motor inside the fan drum. It is removed from the motor, shipped loose with the fan,
and will require the Purchaser of User to install it outside the drum. All wiring and connections between the conduit
box and the motor must meet NEC (National Electric Codes) standards. This assembly process should only be com-
pleted by a licensed electrician.
In order to properly perform the pre-start and the post-start checks on page 7, it is strongly recommended that an
additional conduit box be purchased and mounted on the outside of the fan drum. This will allow you to make
electrical connections from the conduit box on the motor to the outside of the fan and take motor amperage
checks outside of the fan. It will also allow you to make any fan rotation changes, if necessary. Additional motor
conduit boxes can be purchased from your local electrical supply house, motor distributor or repair shop.
NOTICE
5. Wiring Connections: All wiring connections should be made for the proper voltage and phase as shown on the
motor nameplate. Connections should follow the motor manufacturers recommendations as shown on the wiring
schematic. This wiring diagram will be located on the outside of the motor, inside of the motor conduit box or on
the motor nameplate. Reversing some wires might be necessary to get the correct fan rotation.
6. Motors with Thermal Overload Protection: If a motor is equipped with thermal overloads, the thermal overload
must be wired per the wiring schematic to be operable. There are 3 types of thermal overloa s:
a. Automatic: These will automatically shut the motor down if the internal temperature exceeds the
design limits.

OMM-14-0509-page 6
b. Manual: These motors will have a button on them. If the motor overheats, it will shut down. After you have
inspected the motor and eliminated the over heating problem, you will need to “reset” it by pushing the button.
You should still lock out the power BEFORE inspecting the motor.
c. Thermostats: This type of thermal is a temperature sensing device ONLY. If the motor overheats, the thermo-
stats will open or close (depending on the type) and send a “signal” to the electrical box. THEY WILL NOT
TURN THE MOTOR OFF. These are pilot circuit devices that must be connected to the magnetic starter
circuit.
7. EXPLOSION PROOF Motors: No motor is explosion proof. Explosion proof (EXP) motors are designed so if there is
an explosion WITHIN the motor, the explosion will be CONTAINED INSIDE the motor and not allowed to get out to
the atmosphere. All explosion proof motors must be selected based on the atmosphere and/or the environment the
motor will be operating in. Explosion proof motors are designed, rated, and labeled for their operating conditions
based on Classes, Groups and “T” Codes. The Class, Group and “T” Code of an EXP motor MUST be selected
based on the atmosphere and/or environmental conditions the motor will be operating in. Consult the NEC
(National Electric Code) and the NFPA (National Fire Protection Association) for the proper EXP motor
Class, Group and “T” Code required for your specific application and location.
NOTICE:
a. All EXP motors have some type of thermal overload as required by UL (Underwriters Laboratories).
Refer to all of Section 6 on page 5 and above.
b. All EXP motors are required to have the UL (Underwriters Laboratories) and CSA (Canadian Standards
Association) listing numbers on the motor name plate or on a separate plate attached to the motor. The
Class, Group and “T” Code the motor is designed for must also be listed.
8. Normal Motor Operating Temperatures:
Using your hand to test the normal running temperature of a motor can be a very painful experience;
The normal operating temperature of a fully loaded, open type, electric motor operating in a 70°F. (21° C.)
ambient temperature is 174°F. (79° C.)
C. Maximum Fan Speed and Motor Speed Controllers:
If you will be using any type of motor speed controller with this fan, DO NOT exceed the maximum safe fan speed.
Installing and using a speed control device requires special training and certification as required by the speed con-
trol manufacturer. See the manufacturers instructions for proper use, installation and wiring connections for the maxi-
mum speed settings. It may also be necessary to “block out” some speeds to eliminate a resonant vibration problem.
The maximum safe fan speed is shown on the data sheet shipped with the fan. If you have lost the data sheet, con-
tact Cincinnati Fan or our sales office for your area. You must have the serial number from the fan name plate for us
to determine the maximum safe fan speed. Cincinnati Fan will only extend the motor manufacturers warranty, when
used with a speed controlling device, if the motor has the words “Inverter Duty” marked on the motor name plate. If
the motor does not have “Inverter Duty” marked on the motor name plate, and you have a motor failure, you will be
required to contact the motor manufacturer for any service or warranty claims.
IF AN EXPLOSION PROOF MOTOR IS USED IN AN AREA CONTAINING VOLATILE LIQUIDS, GASES,
FUMES OR DUST FOR WHICH THE MOTOR WAS NOT DESIGNED TO OPERATE IN, AN
EXPLOSION AND/OR FIRE CAN OCCUR.
DANGER
MAKE SURE YOU LOCK OUT THE POWER TO THE MOTOR BEFORE INSPECTING ANY MOTOR WITH
AUTOMATIC THERMALS. WHEN THE THERMALS COOL DOWN, THEY WILL ALLOW THE MOTOR TO
AUTOMATICALLY START UP AGAIN, UNLESS YOU HAVE LOCKED OUT THE POWER TO THE MOTOR.
DANGER

OMM-14-0509-page 7
NOTICE: Failure to complete and document all the following pre-startup and both post-startup
checks, listed in Sections A and B (below), could void all warranties.
IV. INITIAL UNIT STARTUP
A. Pre-Startup & Post-Startup Checks: (Check blocks as each step is completed. Retain this for your records.)
A1. Pre-Startup Checks Completed By: ___________________________________ DATE: ___________________
A2. 8 Hour, Post-Startup Checks Completed By: _______________________ DATE: ___________________
A3. 3 Day, Post-Startup Checks Completed By: _____________________ DATE: ___________________
MAKE SURE POWER TO THE MOTOR IS LOCKED OUT BEFORE STARTING PRE-STARTUP OR POST-STARTUP CHECKS.
BEFORE MOUNTING FAN IN DUCT WORK OR ON A MACHINE:
If you will be mounting this fan into a duct system, and there is no access door in the fan drum, it is strongly recom-
mended that an access door be installed in the duct work section next to the fan. That will allow you access to perform
the post-startup checks more easily.
1. ■
■■
■■
■Check the propeller by spinning it by hand to ensure it rotates freely.
2. ■
■■
■■
■Check the propeller set screws to make sure they are tight per the Table 1 on page 4.
3. ■
■■
■■
■If the propeller has a taper-lock bushing, make sure the bolts are tightened per Table 2 on page 4.
4. ■
■■
■■
■Make certain there is no foreign material in the fan or duct work that can become a projectile.
5. ■
■■
■■
■Ensure all electrical power components are properly sized and matched for your electrical system.
Also refer back to the NOTICE in Section B-4 on page 5 regarding an additional motor conduit box.
6. ■
■■
■■
■Record the Full oad Amps listed on the motor nameplate. You will need to refer to this later.
Low Voltage: _________________________
High Voltage: ________________________
AFTER MOUNTING FAN IN DUCT WORK OR ON A MACHINE:
7. ■
■■
■■
■Check all duct work hardware to make sure it is tight.
8. ■
■■
■■
■Check that any required guards are properly secured.
9. ■
■■
■■
■Any dampers or shutters should be fully opened and closed to make sure there is no binding or interference.
10. ■
■■
■■
■If your fan is mounted on an elevated support structure, make sure the structure is welded at all the joint connections
and the structure is properly braced to prevent any “side sway”.
11. ■
■■
■■
■Make sure the propeller is stationary prior to startup. Starting a fan with a prop that is rotating backwards can
cause propeller damage.
12. ■
■■
■■
■Apply power to the fan motor momentarily (i.e. “bump start”) to check the propeller rotation. If the fan is rotating in the
wrong direction, reconnect the motor leads per the motor manufacturers wiring schematic. The fan rotation must
match the rotation indicated by the rotation arrow decals on the outside of the fan drum. After reconnecting the
leads, repeat this step.
13. ■
■■
■■
■Apply power to the blower motor and let it come up to full speed. Turn off the power. ook and listen for any unusual
noise or mechanical abnormality while the propeller is still spinning. If any are noticed, lock out the power, wait for the
propeller to come to a complete stop, locate the cause and correct it.
14. ■
■■
■■
■Unlock power and start the fan.
15. ■
■■
■■
■Measure, record and keep the following motor data for future reference and comparison.
(Single phase motors will only have L1 and L2 leads.)
Amperage draw on each motor lead: L1 _______ L2 _______ L3 _______
(Running amps SHOULD NOT exceed the motor nameplate amps for the voltage being operated on). Compare
these amp readings to the Full Load Amps you recorded in Step 6 above.
Voltage coming to motor leads: L1_______ L2_______ L3_______
(Should be about the same input voltage on all leads)
16. ■
■■
■■
■Make sure any inspection doors in the duct work are securely bolted or locked.
B. Vibration:
All props are balanced to comply with ANSI S2.19, G6.3. However, rough handling in shipment and/or erection, weak
and/or non-rigid foundations, and misalignment may cause a vibration problem after installation. After installation, the
vibration levels should be checked by personnel experienced with vibration analysis and vibration analysis equipment.

A. Hardware:
All fan and hardware should be checked to make sure it is tight. Propeller set screws or taper-lock bushings should be
tightened to the torque values shown in Tables 1 and 2 on page 4.
NOTE: If any set screws have come loose, they must be thrown away and replaced. NEVER use set screws more
than once. Replace with knurled, cup-point set screws with a nylon locking patch.
B. Motor Bearing Lubrication:
1. Motor Bearings:
Most smaller motors have sealed bearings that never require re-lubrication for the life of the motor. For any motors with
grease fittings, consult the motor manufacturers recommendations with reference to the lubrication frequency and the
type of grease that should be used.
DO NOT over grease the motor bearings. Generally, 1-2 shots should be enough. Use a hand operated grease gun at
no more than 40 PSI. DO NOT attempt to lubricate the motor bearings while the motor is running.
C. Prop Balance:
All propellers are balanced at the factory. It is not uncommon that additional “trim balancing” is required after the fan is
assembled. Trim balancing of the fan assembly, in the field, is typically always necessary for all replacement props.
Air stream material or chemicals can cause abrasion or corrosion of the fan parts. This wear is generally uneven and,
over time, will lead to the prop becoming unbalanced, causing excessive vibration. When that happens, the prop must
be rebalanced or replaced. The other air stream components should also be inspected for wear or structural damage
and cleaned or replaced if necessary. After cleaning any fan propeller, it should be balanced.
There are two ways to balance a fan propeller:
1. Add balancing weights for fabricated aluminum, steel or stainless steel props:
Balance weights should be rigidly attached to the prop at a location that will not interfere with the fan hous-
ing nor disrupt air flow. They should (if at all possible) be welded to the prop. When trim balancing the prop,
on the fan, be sure to ground the welder directly to the propeller. Otherwise, the welding current will likely
pass through the motor and damage the motor bearings.
2. Grinding off material for cast aluminum propellers:
If you are grinding on the prop to remove material, be very careful not to grind too much in one area. That
could affect the structural integrity of the prop.
D. Vibration:
As mentioned previously in this manual, excessive vibration can cause premature motor bearing failure that could lead
to catastrophic failure of the fan. After performing any routine maintenance, the vibration readings should be taken
again. New readings should be taken (maximum every 12 months) and compared to the previous readings. If any
major differences are present, the cause should be determined and corrected before the fan is put back into
operation.
The most common causes of vibration problems are:
1. Propeller unbalance. 3. Poor fan inlet and/or discharge conditions.
2. Mechanical looseness. 4. Foundation stiffness.
E. Dampers and Shutters: (Airflow control devices)
Turn off and lock out power to the fan motor. Any dampers or shutters should be periodically inspected to make sure
all parts are still operable within their full range and there is no interference with any other fan components. Any bear-
ings or seals should be checked for their proper function. The manufacturers maintenance instructions should be fol-
lowed.
OMM-14-0509-page 8
BEFORE STARTING ANY INSPECTION OR MAINTENANCE, BE SURE FAN IS TURNED OFF, POWER IS LOC ED OUT
AND THE PROPELLER HAS BEEN CAREFULLY SECURED TO PREVENT WIND MILLING. IF THE OPERATING
CONDITIONS OF THE FAN ARE TO BE CHANGED (SPEED, PRESSURE, TEMPERATURE, ETC.) CONSULT
CINCINNATI FAN, OR OUR SALES OFFICE FOR YOUR TERRITORY, TO DETERMINE IF THE UNIT WILL
OPERATE SAFELY AT THE NEW CONDITIONS.
WARNING
V. ROUTINE INSPECTION & MAINTENANCE
Periodic inspection of all the fan parts is the key to good maintenance and trouble-free operation. The frequency of
inspections must be determined by the user and is dependent upon the severity of the application. BUT,it should
NEVER exceed a 12 month period. The user should prepare an inspection and maintenance schedule and make sure
it is adhered to.

OMM-14-0509-page 9
F. Safety Equipment & Accessories:
It is the users responsibility to make sure that all safety guards required by the company, local, state and OSHA regula-
tions are properly attached and fully functional at all times. If any guards become defective or non-functional at any time,
the power to the fan MUST be turned off and locked out until complete repairs and/or replacements have been
made, installed and inspected by authorized personnel.
Any accessories used in conjunction with the fan should also be inspected to make sure they are functioning within their
intended limits and design specifications. The manufacturers maintenance manuals should be referred to for correct
maintenance procedures. These accessories include, but are not limited to, the following:
Seals, inspection doors, vibration isolators, air flow or pressure measuring equipment, hoods, controls, special coat-
ings, silencers, expansion joints, flexible connectors and filters.
VI. ORDERING REPLACEMENT PARTS:
Under normal conditions, you should not need any spare or replacement parts for at least 24 months after shipment
from Cincinnati Fan. That does not include any wear due to abrasion, corrosion, excessive temperatures, abuse, mis-
use, accident or any severe conditions the fan was not designed for.
NOTICE:
1. If this fan is vital to any process that could cost you lost revenue, we strongly recommend that you keep a
replacement propeller and motor at your location.
2. If this fan is vital for the safety of any people and/or animals, we strongly recommend that you keep a com-
plete fan/motor assembly, as originally ordered, at your location.
To order any parts or complete units, contact us for the name of our sales office for your area. Or you can find
them on our website at: www.cincinnatifan.com
WE MUST HAVE THE FAN SERIAL NUMBER FROM THE FAN NAME PLATE TO IDENTIFY PARTS CORRECTLY.

OMM-14-0509-page 10
Troubleshooting should only be performed by trained personnel. Any potential electrical problems should only
be checked by a licensed electrician. All safety rules, regulations and procedures MUST be followed. Failure to
follow proper procedures can cause property damage, severe bodily injury and death.
DANGER
VII. TROUBLESHOOTING:
Potential problems and causes listed below are in no order of importance or priority. The causes are only a list
of the most common items to check to correct a problem. If you find the cause of a problem, DO NOT assume it is
the ONLY cause of that problem. Different problems can have the same causes.

OMM-14-0509-page 11
5. General Motor Procedure:
If the motor is not put into service immediately, the motor must be stored in a clean, dry, warm location. Minimum
temperature of 50°F. (10°C,). Several precautionary steps must be performed to avoid motor damage during storage.
a. Use a “Megger” each month to ensure that integrity of the winding insulation has been maintained. Record the
Megger readings. Immediately investigate any significant drop in insulation resistance.
b. DO NOT lubricate the motor bearings during storage. Motor bearings are packed with grease at the factory.
c. If the storage location is damp or humid, the motor windings must be protected from moisture. This can be done
by applying power to the motor’s space heaters, (IF AVAI AB E) while the motor is in storage. If the motor does
not have space heaters, storing it in a damp or humid location will, very quickly, cause internal corrosion and
motor failure which is not warranted.
NOTE:
For specific storage instructions, for the actual motor and any accessory parts that were supplied, refer to
the manufacturer’s instructions.
VIII. LONG TERM STORAGE INSTRUCTIONS: (Storage exceeding 30 days after receipt of equipment)
NOTE: Failure to a here to these instructions voi s all warranties in their entirety.
1. Storage site selection:
a. evel, well-drained, firm surface, in clean, dry and warm location. Minimum temperature of 50°F (10°C).
b. Isolated from possibility of physical damage from construction vehicles, erection equipment, etc.
c. Accessible for periodical inspection and maintenance.
2. The fan should be supported under each corner of its base to allow it to “breath”. Supports (2 x 4’s, timbers, or rail-
road ties) should be placed diagonally under each corner.
3. If the equipment is to be stored for more than three (3) months, the entire fan assembly must be loosely covered
with plastic, but not tightly wrapped.
4. Storage Maintenance:
A perio ic inspection an maintenance log, by ate an action taken, must be evelope an main-
taine for each fan. See example below. Each item must be checke monthly.
EXAMPLE:
Storage / Maintenance Schedule Log

IX. LIMITED WARRANTY:
Cincinnati Fan & Ventilator Company (Seller) warrants products of its own manufacture, against defects of material and workmanship
under normal use and service for a period of eighteen (18) months from date of shipment or twelve (12) months from date of installa-
tion, whichever occurs first. This warranty does not apply to any of Seller’s products or any part thereof which has been subject to
extraordinary wear and tear, improper installation, accident, abuse, misuse, overloading, negligence or alteration. This warranty does
not cover systems or materials not of Seller’s manufacture. On products furnished by Seller, but manufactured by others, such as
motors, Seller extends the same warranty as Seller received from the manufacturer thereof. Expenses incurred by Purchaser’s in
repairing or replacing any defective product will not be allowed except where authorized in writing and signed by an officer of the
Seller.
The obligation of the Seller under this warranty shall be limited to repairing or replacing F.O.B. the Seller’s plant, or allowing credit at
Seller’s option. THIS WARRANTY IS EXPRESSLY IN LIEU OF ALL OTHER WARRANTIES EITHER EXPRESSED OR IMPLIED
INCLUDING THE WARRANTIES OF MERCHANTABILITY AND FITNESS FOR A PARTICULAR PURPOSE AND OF ALL OTHER
OBLIGATIONS AND LIABILITIES OF THE SELLER. THE PURCHASER AC NOWLEDGES THAT NO OTHER REPRESENTA-
TIONS WERE MADE TO PURCHASER OR RELIED UPON BY PURCHASER WITH RESPECT TO THE QUALITY OR FUNCTION
OF THE PRODUCTS HEREIN SOLD.
Removal of the Sellers nameplate or any generic fan nameplate containing the fan serial number voids all warranties, either written or
implied. Failure to complete and document all the pre-startup and post startup checks and perform the suggested routine mainte-
nance checks voids all warranties, either written or implied.
LIMITATION OF LIABILITY:
Notice of any claim, including a claim for defect in material or workmanship, must be given to Seller in writing within 30 days after
receipt of the equipment or other products. Seller reserves the right to inspect any alleged defect at Purchaser’s facility before any
claim can be allowed and before adjustment, credit, allowance replacement or return will be authorized. See RETURNS below.
Seller’s liability with respect to such defects will be limited to the replacement, free of charge, of parts returned at Purchaser’s
expense F.O.B. Seller’s plant and found to be defective by the Seller.
IN NO EVENT WILL SELLER BE LIABLE FOR SPECIAL, INDIRECT, INCIDENTAL OR CONSEQUENTIAL DAMAGES, WHETHER
IN CONTACT, TORT, NEGLIGENCE, STRICT LIABILITY OR OTHERWISE, INCLUDING WITHOUT LIMITATION DAMAGES FOR
INJURY TO PERSONS OR PROPERTY, LOST PROFITS OR REVENUE, LOST SALES OR LOSS OF USE OF ANY PRODUCT
SOLD HEREUNDER. PURCHASER’S SOLE AND EXCLUSIVE REMEDY AGAINST SELLER WILL BE THE REPLACEMENT OF
DEFECTIVE PARTS AS PROVIDED HEREIN OR REFUND OF THE PURCHASE PRICE FOR DEFECTIVE PRODUCTS, AT SELL-
ER’S SOLE OPTION. SELLER’S LIABILITY ON ANY CLAIM, WHETHER IN CONTRACT, TORT, NEGLIGENCE, STRICT LIABILI-
TY OR OTHERWISE, FOR ANY LOSS OR DAMAGE ARISING OUT OF OR IN CONNECTION WITH PURCHASER’S ORDER OR
THE PRODUCTS OR EQUIPMENT PURCHASED HEREUNDER, SHALL IN NO CASE EXCEED THE PURCHASE PRICE OF THE
EQUIPMENT GIVING RISE TO THE CLAIM.
RESPONSIBILITY:
It is the understanding of the Seller that Purchaser and/or User will use this equipment in conjunction with additional equipment or
accessories to comply with all Federal, State and local regulations. The Seller assumes no responsibility for the Purchaser’s or Users
compliance with any Federal, State and local regulations.
RETURNS:
Cincinnati Fan & Ventilator Company assumes no responsibility for any material returned to our plant without our permission. An RMA
(Return Material Authorization) number must be obtained and clearly shown on the outside of the carton or crate and on a packing
slip. Any items returned must be shipped freight prepaid. Failure to comply will result in refusal of the shipment at our receiving
department.
OMM-14-0509-page 12
DISCLAIMER
This manual, and all its content herein, is based on all applicable known material at the time this manual was created. Any parts of
this manual are subject to change at any time and without notice.
If any statements, diagrams and/or instructions contained herein, for components not manufactured by the Seller, conflict with
instructions in the manufacturer’s manual (i.e.: motors, dampers, etc.), the instructions in the manufacturer’s manual, for that compo-
nent take precedent.
Should you want the latest version of this manual, please contact us or our sales office for your area. Or, you can print a current ver-
sion by going to our website at: www.cincinnatifan.com
7697 Snider Road, Mason, OH 45040-9135
Phone: (513) 573-0600 Fax: (513) 573-0640
E-Mail: [email protected]
Table of contents
Popular Fan manuals by other brands

dreo
dreo DR-HTF008S user manual
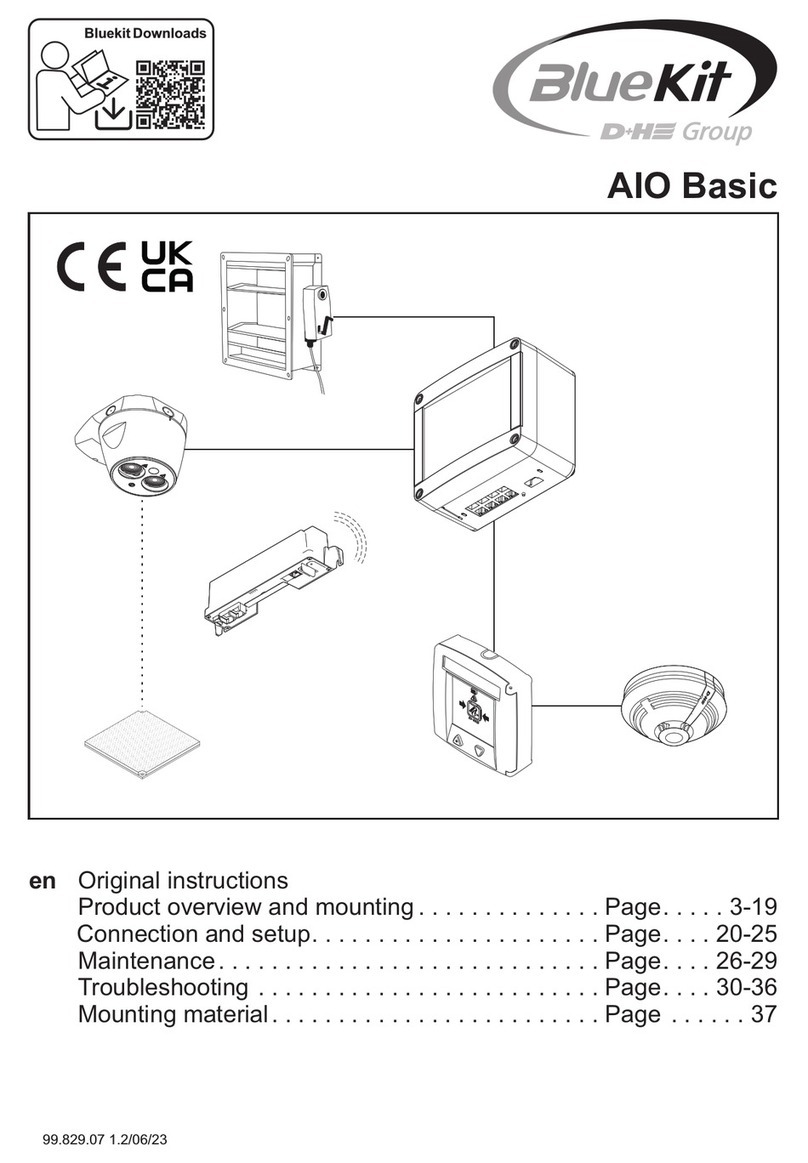
D+H
D+H BlueKit AIO Basic Original instructions
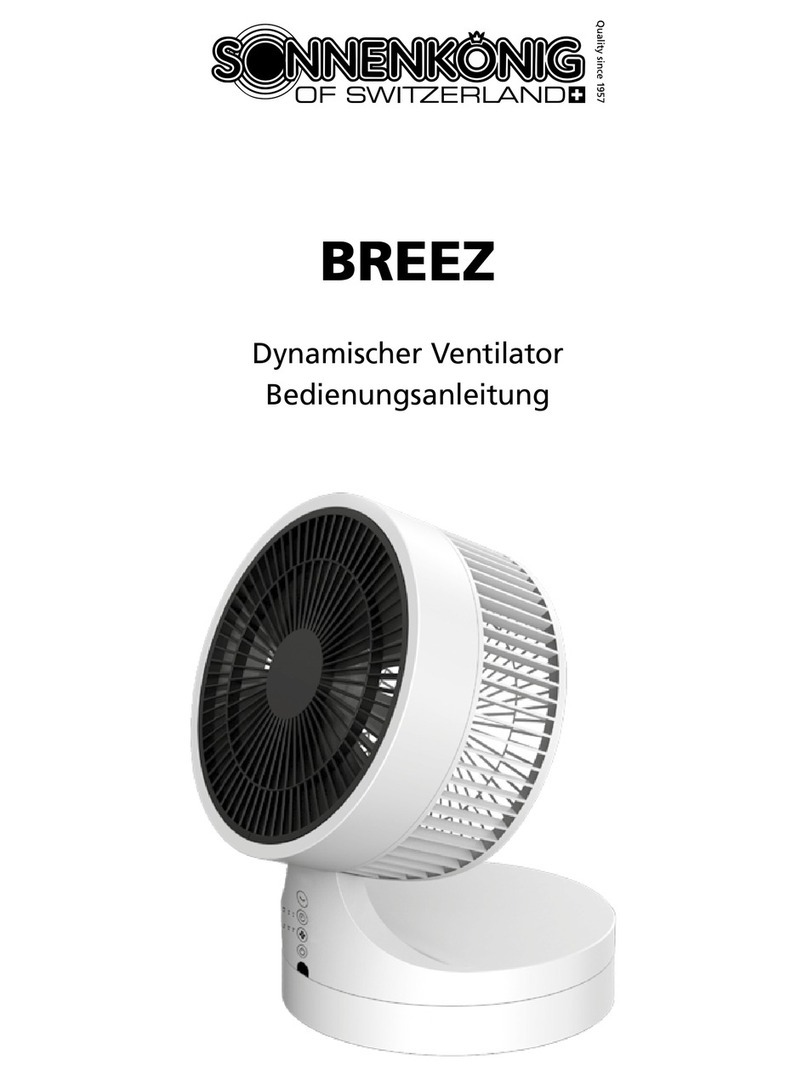
Sonnenkonig
Sonnenkonig BREEZ instruction manual
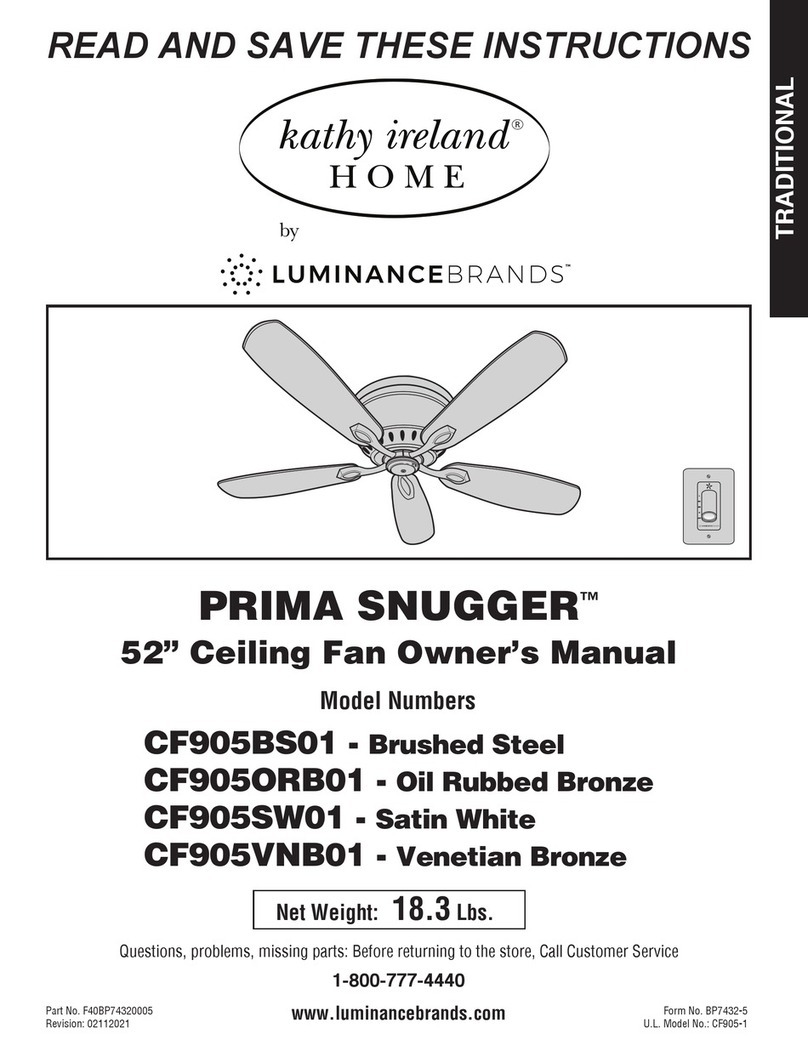
Luminance Brands
Luminance Brands Kathy Ireland Home Prima Snugger CF905BS01 owner's manual
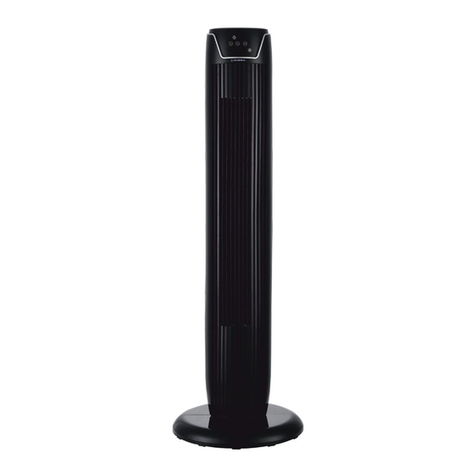
Morris
Morris MTF-16235 instruction manual
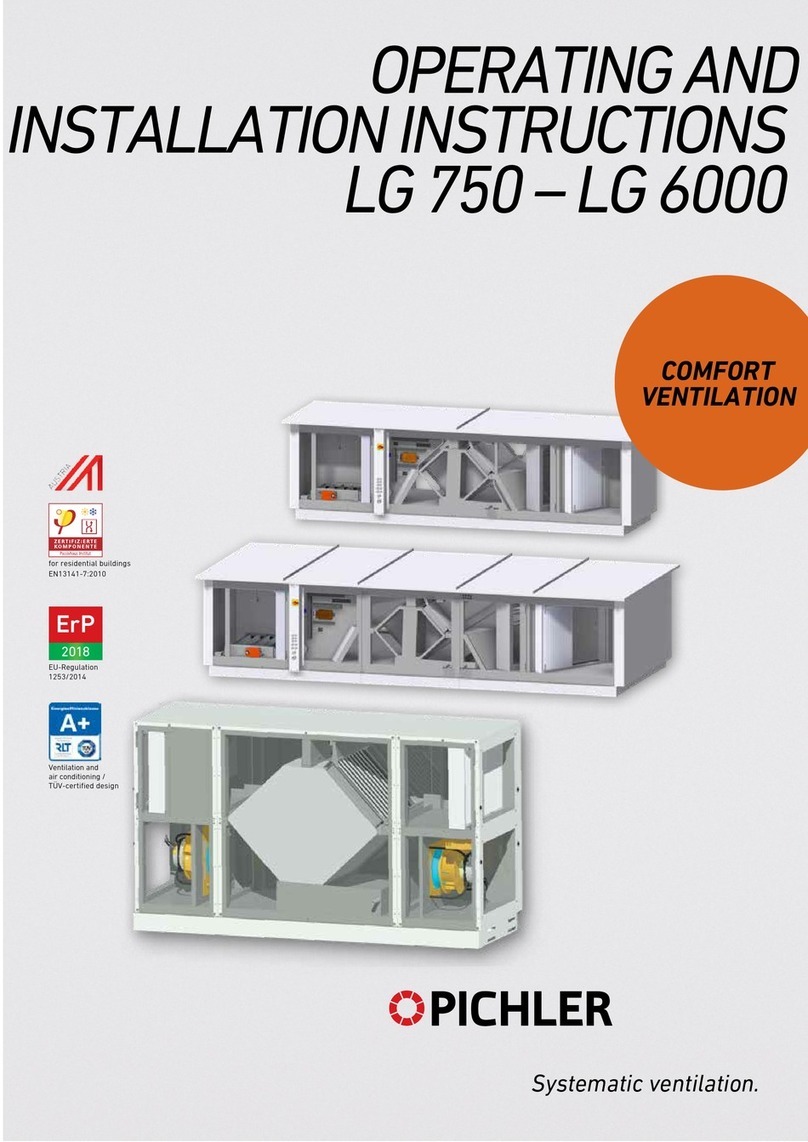
Pichler
Pichler LG Series Operating and installation instructions