Cissell MAN77 User manual

Page 1
MAN 77 06/00
OWNER’S MANUAL
THIS MANUAL MUST BE GIVEN TO THE EQUIPMENT OWNER.
CISSELL MANUFACTURING COMPANY
HEADQUARTERS PHONE:(502)587-1292
831 SOUTH FIRST ST. SALESFAX:(502)585-3625
P.O.BOX32270 SERVICE/PARTSFAX: (502)681-1275
LOUISVILLE,KY 40232-2270
Call Office
Conveyor

Page 2
NOTICE
THECUSTOMER/OWNERMUSTPOSTOPERATINGINSTRUCTIONSANDSAFETYPRE-
CAUTIONSINCLOSEPROXIMITYTOTHECONVEYOROPERATOR.
SAFETYPRECAUTIONS
READTHISOWNER’SMANUALTHROUGHLY BEFOREINSTALLING,OPERATING, AND
PERFORMINGANYMAINTENANCE. KEEPTHISMANUALFORFUTURE
REFERENCE.
POWERTOTHECONVEYORMUSTALWAYS BE DISCONNECTED ORSHUTOFFPRIOR
TOATTEMPTINGANYSERVICE OR ADJUSTMENT TOTHECONVEYOR.
BECAUTIOUSANDALERTFORANYLOOSEARTICLEOFCLOTHINGOR
JEWELRYTHAT MIGHT BECOME ENTANGLED IN THE CONVEYOR LINKS,
TROLLEYS,DRIVEMECHANISMSORANYMOVINGCOMPONENTOFTHE
CONVEYOR.
DONOT ATTEMPTTOREMOVE OR RELEASE ANY ITEM CAUGHT OR
ENTANGLED IN ANY PART OF THE CONVEYOR UNTIL AFTER POWER TO THE
CONVEYORHASBEENCOMPLETELYDISCONNECTED.
BE ALERT FOR ANY BODY PART (FINGER, HAND, HAIR, ETC.) THAT COULD BE
CAUGHTINANYMOVINGCOMPONENTOFTHECONVEYOR.
POSTOPERATOR INSTRUCTIONS AND SAFETY WARNINGSINAPROMINENT
LOCATION.

Page 3
TABLE OF CONTENTS
Page
Safety Precautions .................................................................................................................... 2
GeneralInformation, DamagedGoods .................................................................................... 4
AssemblyInstructions ............................................................................................................... 5-6
ConveyorOrderIdentification System.................................................................................... 7-8
OperatingInstructions .............................................................................................................. 9
DimensionsandClearance - Garment Bag.............................................................................. 10
Lubricants -Worm Gear Reducers .......................................................................................... 11
ConveyorTrackLubrication .................................................................................................... 12
IdlerWheelAssembly Parts ..................................................................................................... 13
LinkDriveSprocket Assembly Parts....................................................................................... 14
ReturnEnd,DriveEndParts.................................................................................................... 15
ControlBoxAssemblyParts..................................................................................................... 16
CissellEquipmentWarranty ..................................................................................................... 17

Page 4
CISSELL CALL OFFICE CONVEYOR
GENERAL INFORMATION
The Cissell Conveyor is designed for simplicity in assembly and erection. The following instructions
provide a basic guide for the satisfactory reassembly and erection of the Conveyor. If followed, in the
sequence outlined, the assembly and erection can be performed with a minimum of effort. Since the
Conveyor is completely modular in construction and assembly, the size of the Conveyor can be in-
creased or decreased at any time, by adding or removing straight track sections and links.
UNCRATING
Uncrate and unpack all Conveyor units carefully. Compare the units received with the bill of material
and be certain that all parts are at hand before starting erection.
DAMAGED GOODS
Goods damaged by the customer in handling, erection, or operation shall be the entire responsibility
of the customer.
All Cissell Conveyor equipment is thoroughly inspected and carefully packed before leaving the
factory. Responsibility for its safe delivery is assumed by the carrier at the time of shipment.
Claims for loss or damage to the contents must be made by the cosignee upon the carrier.
Do not return damaged merchandise to Cissell. File your claim with the carrier as follows: (Claim for
loss or damage is shipment cannot be filed be Cissell).
CONCEALED LOSS OR DAMAGE involves damage that does not become apparent until the
equipment is unpacked. Contents may be damaged in transit due to rough handling even through the
carton (or crate) may not show external damage.
When such damage is discovered, immediately make a written request for inspection by the Carrier’s
agent within fifteen (15) days of the delivery date.
Keep all crating, cartons and fillers. The carrier will require inspection of these and will furnish you
with an inspection report and the necessary forms for filing a concealed damage or loss claim. Your
protection against loss from concealed damages can be safeguarded only by following these instruc-
tions carefully.
VISIBLE LOSS OR DAMAGE involves any external evidence of loss or damage, and such damage
must be noted on the carrier’s freight bill or express receipt, and must be signed by the carrier’s
agent.
Failure to describe adequately such external evidence of loss or damage may result in the carrier
refusing to honor a damage claim. The form required to file such a claim will be suppied by the
carrier, and such a claim cannot be filed by Cissell.
MISSING ITEMS. When receiving a shipment, be sure that the number of items, packages, crates,
etc. correspond to those listed on the Bill of Lading. Any loss must be noted on the carrier’s freight
bill or express receipt as outlined above (VISIBLE LOSS OR DAMAGE). However, when an omission
is discovered that is not a “loss in transit”, immediately notify your distributor or, when the shipment
was “drop-shipped” (directly to the customer from the factory) you may notify Cissell immediately as
to the omission, giving the invoice number, date of delivery, serial number of the conveyor, and
description of the parts omitted.

Page 5
ASSEMBLY INSTRUCTIONS
STRAIGHT FLOOR MODEL CONVEYORS
Motor or drive end is preferably located toward rear of plant away from Call Counter.
When removing drive end from crate (and during erection), do not lift or exert force on the link drive sprocket.
Avoid shock to either the motor, or the motor control box mounted (on the drive end section) adjacent to the
electricmotor.
ERECTION
1. Position all Conveyor sections on floor in general location for erection, with motor or drive end toward
rear of plant.
2. Position base assemblies on floor in final locations. Allow at least 14” from the curved end of the track
for clothes clearance, and 14” from the side track to the wall, whenever the Conveyor is placed close to a
wall.
3. Place vertical columns in base assemblies.
4. Place coupler sections on the top of each intermediate column; no coupler being required on either of the
two end columns.
5. Place drive end section on top of the rear colomn, and the 180 degree return end on top of the front
column.
6. Insert the ends of two straight track sections (or equal length) into the ends of the 180 degree track
section of the drive end; the opposite ends of the straight track sections into the first coupler. Line up the
holes in the straight track sections with the mounting holes in the 180 degree track section and in the
first coupler. Insert bolts in the mounting holes but do not tighten. Place the head of the bolts on the
inside of the tubular track; a round washer and crown nut on the outer end of each bolt.
7. Continue to install the remaining pairs of straight track sections between adjacent couplers. Line up the
holes in the straight track sections with the mounting holes in the couplers. Insert bolts (with washer
and nut) in the mounting holes of the couplers but do not tighten.
8. Do not insert the ends of the last of the straight track sections into the ends of the 180 degree return end
section.
9. Loosen the motor mounting plate on the drive end; slide motor mounting plate forward, so that the chain
can be lifted free of the small chain sprocket on the drive motor. This will permit free rotation of the
large link drive sprocket.
10. Feed each preassembled link assembly into the tubular track; joining each successive link assembly by
connecting a short swivel link to the end of an adjacent link by means of the cross pin in the swivel link.
Feed the links around the link drive sprocket so that the roller sleeve of each J bolt enters a tooth of the
link drive sprocket. Be sure the name CISSELL on each link faces to the outside.
11. Feed the links of the last link assembly into the 180 degree track section of the return end assembly;
insert the ends of the track section into the ends of the 180 degree track section of the return end; insert
bolts in the mounting holes, but do not tighten. Join the final adjacent end links of the link assemblies
by connecting the short swivel link to the adjacent end link by means of the cross pin in the swivel link.
12. Align track; butt the ends of each adjacent track section tightly and then tighten the track bolts. Do not
leave a space between the ends of the adjacent track sections as this will materially reduce the life
expectancy of the (nylon) plastic roller wheels.

Page 6
13. Level entire Conveyor by raising (or lowering) the respective vertical column in its base; or by raising (or
lowering) the respective coupler (or end section) on the top of the columns. Tighten the set screws in the
socket of each base. Tighten the set screws in the socket of each end section and central coupler. After
alignment, pull the Conveyor links by hand, to make sure that everything is free, and that the J bolts
are not hitting anything.
14. Replace the motor drive chain onto the large chain sprocket of the link drive sprocket and onto the small
chain sprocket of the drive motor; slide the motor mounting plate into its original position, being certain
the chain is tight, and then tighten the bolts attaching the motor plate to the drive end assembly.
15. Install the manual switch on the curved track portion of the motor drive end; attach the flexible cable
thereof to the motor control box and to the side face of the central channel of the drive assembly with the
small cable clamp provided. Connect wiring as per the wiring and electrical installation drawings.
16. Start the Conveyor and check to see that all moving parts operate freely. Adjust is required.
17. Follow the instructions enclosed in this manual to obtain the required coordination between the dial and
link identifications.
18. If alphabetical disc targets are employed for link identification, these are to be placed on the lower bar of
the links.
If the links are to be numerically identified, attach the self-adhesive numerical identification tabs to the
upper bar of each link.
19. Put vaseline (or light grease) in the bottom of the track so that the rollers can pick this up. Repeat this
about every six months or when the track surface becomes dry.
This light grease cannot fall on garments, as the rollers are contained with the tubular track. It will reduce
wear on the rollers and make the Conveyor run more quietly.
20. Check and tighten drive chain in three to four weeks and every six months thereafter.
21. The gear reduction drive of the drive motor is filled with oil at the factory. Before placing Conveyor into
operation, remove the tag and screw from the vent tube on the top of the motor; remove the oil level plug
on the side of the motor to make sure that the oil is to the level of this plug. If not, add Mobil Gear 636
Extreme Presure Oil (or equivalent) into the oil level opening by employing a long spout oil can. When
oil drips from the opening, the oil level is correct. See separate page “LUBRICANTS - WORM GEAR
REDUCERS” for detailed information regarding oil.

Page 7
CONVEYOR ORDER IDENTIFICATION SYSTEM
NOTE: Digital Control Available Only for Fixed Link Numbering Systems.
1. OPEN BAR NUMBERING (Notches up-Smooth bar down)
Each link carries a single number (1, 2, 3, 4,--etc.) and the links are numbered consecutively up to the capacity
of the Conveyor.
The operator, at the loading station, hangs an order on an available open bar and writes the number of this
bar on a copy of the invoice.
This marked copy of the invoice is filled at the Call Counter, either alphabetically (by customer name) or
numerically (by invoice number).
Before removing the order from the Conveyor, the attendant at the Call Counter is required to “match”
customer name as well as bar number, providing a “double check” before delivering the order to the customer.
The open bar provides the most flexible and efficient use of each link bar; allowing adequate space for orders
regardless of size. Orders may be pushed side to side, on any open bar, without disturbing order identifica-
tions.
2. OPEN BAR-ALPHABETICAL (Notches up-Smooth bar down)
The links of the Conveyor are divided into 26 alphabetical groups; the number of links assigned to each
alphabetical division are proportioned to accomodate the number of customer names to be served by each
alphabetical group.
Alphabetical identification discs are hung on the lower bar of the links.
A tally of customers names taken from weekly receipts will indicate a reasonable space allocation for each
alphabetical division. In day to day operation, the operator at the loading station may shift the alphabetical
discs in increase or decrease the space allocation for each division.
No marking of the invoice copies of the operator at the loading station is required; as the attendant removes
the orders from the Conveyor, alphabetically by customer name.
Due to the continuous variation in space allocation for the alphabetical system, it is not possible to have a
digital control for such a system. However, if a fixed number of links are permanently assigned to each alpha-
betical letter, a digital control can be furnished for this arrangement.
3. MULTIPLE BAR NUMBERING (Notches down-Smooth bar up)
The hanging bar of each link is divided into ten spaces; each space to receive a single order. The spaces of each
link are numbered consecutively (1, 2, 3, 4,--etc.) up to the capacity of the Conveyor.
The operator at the loading station hangs an order in an available space, and writes the number of this space
on a copy of the invoice.
This marked copy of the invoice is filed at the Call Counter, either alphabetically (by customer name), or
numerically (by invoice number).
The attendant is required to match only the space number before removing the order from the Conveyor.
However, to provide a “double check”, the attendant should “match” the customer’s name before delivering the
order to the customer.

Page 8
4. PRESELECTED NUMBERING (Notches down-Smooth bar up)
This system is especially suited for self-service, and for applications having relatively uniform order sizes that
will allow predetermined use of all consecutively numbered spaces of a link.
The hanging bar of each link is divided into equal spaces (standare, 10 spaces per link); each space receiving a
singleorder.
The spaces of each link are numbered consecutively (1, 2, 3, 4,--etc.) up to the capacity of the Conveyor.
A set of numbers, in tag form, is kept at the Call Counter.
When a customer brings an order in, the attendant removes a numbered tag (preferably at random), and
staples this tag to the office copy of the invoice. The attendant also writes this number on the customer’s copy
of the invoice.
When the customer calls for the order, the attendant is required to match only the tag or space number before
removing the order from the Conveyor. However, to provide a “double check”, the attendant should “match”
the customer’s name before delivering the order to the customer.
Under this system, the numbered tags may be re-used, and when re-used, the attendant should remove the tag
from the office copy of the invoice and return same to the tag file for re-use.
If the tag is not re-used, the attendant must secure a correspondingly numbered “new tag” from “stock”, and
place in the tag file for subsequent use.
5. LAST TWO DIGITS OF INVOICE NUMBER (Notches down-Smooth bar up)
This system requires link space numbers to be arranged in multiples of 100.
Example: A 500 garment capacity Conveyor has 50 links, each divided into 10 spaces.
The last two digits of consecutively numbered invoices will run from 01, 02, 03 --up to 98, 99, 00. Thus, for a
500 garment capacity Conveyor, 5 garment spaces will be assigned to each digit; 5 spaces for 01, then 5 spaces
for 02, 5 spaces for 03--, 5 spaces for 98, 5 spaces for 99 and finally 5 spaces for 00.
As order identified by invoice 14309 would be hung on one of the spaces marked - 09. Similarly, an order
identified by 14389 would be hung on one of the spaces maked 89.
Operator at loading station hangs an order in an available space identified by the last two digits of the invoice
number.
Since the attendant at the Call Counter will remove orders from the Conveyor as indicated by the last two
digits of the invoice number appearing on the customer’s copy of the invoice, no filing or marking of invoices is
required.
Before removing an order from the Conveyor, the attendant at the Call Counter is required to “match”
customer’s name as well as the space number corresponding to the last two digits of the invoice number
number, thus providing a “double check” before delivering order to the customer.
This system can also be used with the open-bar link arrangement by utilizing a full link (or multiples thereof)
for each digit designation 01, 02, 03, -- etc.

Page 9
OPERATING INSTRUCTIONS
The standard Cissell Garment Storage and Retrieval Conveyor is factory fitted with hand and/or foot
switches. An electronic automatic control is available as an option.
The conveyor hand switch is of a 3-position detent design. The hand switch may be moved from the
center, “OFF” position to either the right of left position and will remain in that position until
changed. The conveyor will continue to move in either clockwise or counterclockwise direction until
the hand switch is returned to the center, “OFF” position.
The conveyor foot switch is a two position momentary contact, self centering design. When either the
left side or right side of the switch is depressed, the conveyor will operate in the chosen direction
only as long as the switch is physically held in position with the foot. Upon release of foot pressure,
the conveyor will stop, and the switch will automatically return to the center “OFF” position.
The hand and foot switches are mechanically and electrically interlocked such that when one of the
switches is operating the conveyor, the other switch is locked out and cannot operate the conveyor.
When the switch controlling conveyor operation is returned to the center “OFF” position, either
switch will then be available to operate the conveyor.
WARNING:
When one of the switches has control of the conveyor, the other switch should remain in the center
“OFF” position at all times. Do not attempt to place or hold the non-operative switch in either
operating direction. This could be a hazard to the operators because when the operating switch is
returned to the “OFF” position, control immediately shifts to the other switch and the conveyor
(especially floor model conveyors), it is important that the switches not be activated until verifying
that persons at the opposite end are alerted to your desire to use the conveyor.
Operation of the conveyor via the automatic electronic control is covered by instructions in the
operating manual furnished with the automatic control.

Page 10
DIMENSIONS AND CLEARANCE - GARMENT BAG

Page 11
LUBRICANTS - WORM GEAR REDUCERS
For special applications that involve severe ambient temperature extremes or a
seasonal oil requirement, use Mobil SHC 629.
AmbientTemperature -30 to 15 deg.F 16 to 50 deg.F 51 to 100 deg.F 111 to165 deg.F
Max.Operating Temp. 150 deg.F 185 deg.F 200 deg.F 200 deg.F
Viscosity@100deg.F.SUS 1919 to 2346 2837 to 3467 4171 to 5098
ISOViscosity Grade 320 460 680 1000
Compounded with: 3% to 10% fatty or synthetic fatty oils or mild EP additives
AGMA LubricantNo. #7 Comp. #8 Comp. #8A Comp.
CitiesService Co. CITGO EP Comp.68 CITGO Cyl. Oil 400-S CITGO Cyl. Oil 680-7 CITGO Cyl. Oil 680-7
FiskeBros. Refining SPO-233 SPO-277 SPO-288 SPO-288
Gulf Oil Corp. SL-460 EP Transgear EP 460 Transgear EP680 Transgear EP800
KeystoneDiv. KSL-365 KSL-366 K-600 K-620
MobilOil Corp. SHC 629 Mobil 600W Mobil 600W Super MobilExtra Hecia
Shell OilCorp. Omala 68 Omala 460 Omala 680 Omala 800
Sun Oil Corp. Sunep 1050 Sunep 1110 Sunep 1150 Sunoco Gear Oil & AC
Texaco, Inc. Meropa 68 Vanguard Cyl. Oil 460 Honor Cyl. Oil 680 650T Cyl. Oil 1000
American Lub, Inc. SHC 9065 Ind. Gear Oil 140 AGMA #8 Gear Oil AGMA #8 Gear Oil
Chevron NL Gear Comp. 100 NL Gear Comp. 460 NL Gear Comp. 680 NL Gear Comp. 1500
Initial Oil Change
The oil in a new speed reducer should be changed at the end of 250 hours of operation. (30 days for 8
hour per day service. 15 days for 16 hour service, 10 days for 24 hour service).
Subsequent Oil Changes
Under normal conditions, after the initial oil change, the oil should be changed after every 2,500
hours of operation, or every six months, whichever occurs first. Under severe conditions (rapid
temperature changes, moist, dirty, or corrosive environment) it may be necessary to change oil at
intervals of one to three months. Periodic examination of oil samples taken from the unit will help
establish the appropriate interval.
Overfilling Or Underfilling
If a speed reducer is overfilled with oil, the energy used in churning the excessive oil can result in
overheating. If this occurs, shut down the drive, remove the oil level plug and allow oil to drain until
oil ceases to drain from the level hole, reinstall the oil level plug, and restart the drive. If the speed
reducer is underfilled, the resultant friction can cause overheating and possible damage. If this
occurs, fill the speed reducer to the oil level plug hole and check the gearing for excessive wear.

Page 12
CONVEYOR TRACK LUBRICATION
Apply Vaseline or light grease in the bottom of the roller track to lubricate the path of
the rollers.
A narrow strip of lubrication, about 1/8” in diameter and placed along the center of the
roller path for about one foot at five foot spacings will be picked up and spread by the
rollers.
Do not apply lubricant beyond the path of the rollers as this will serve no useful pur-
pose.
Repeat every six months or when the track surface becomes dry.
A properly lubricated track will provide quiet roller operation and greatly extend the
operating life.

Page 13
IDLER WHEEL ASSEMBLY - C301
Ref. No. Part No. Description
1 C310 3/8”-24 Castle Nut
2 C227 13/16” Washer
3 C217 Ball Bearing
4 C143 Retaining Ring
5 C228 Sleeve Spacer
6 C129 Bearing Housing
7 FB124 5/16”-18 x 1 Hex Head
Cap Screw
8 C189 Idler Wheel
9 C249 5/16”-18 Hex Nut
10 TU2814 5/16” Split Lockwasher
11 C125 Link Sprocket Support
12 OP265 3/8-16 x 1/2 Set Screw
13 TU3604 Cotter Pin
14 C139 Retaining Ring
15 C2118 Sprocket Shaft

Page 14
LINK DRIVE SPROCKET ASSEMBLY-C300
Ref. No. Part No. Description
1 C310 3/8”-24 Castle Nut
2 C227 13/16” Washer
3 C217 Ball Bearing
4 C143 Retaining Ring
5 C228 Sleeve Spacer
6 C129 Bearing Housing
7 C363 5/16”-18 x 1 1/4” Hex
Head Cap Screw
8 C1056 #40 Chain 1/2 Pitch, 56”
SC400 #40 Chain 1/2 Pitch, 57”
9 C130 Drive Sprocket-60 Tooth
10 C119 Link Drive Sprocket
11 C125 Link Sprocket Support
12 OP265 3/8-16 x 1/2 Set Screw
13 TU2814 5/16” Split Lockwasher
14 TU3604 Cotter Pin
15 C249 5/16”-18 Hex Nut
16 C2118 Sprocket Shaft
17 C139 Retaining Ring
18 TU4684 Key, 3/16” Sq. x
1-1/2” Long

Page 15
RETURN END PARTS - C649 (Consists of Ref. No. 1-11
DRIVE END PARTS - C648 (Consists of Ref. No. 4-11)
Ref. No. Part No. Description
1 TU2334 Octogon Box
2 TU2335 Box Cover
3 TU2878 #10 x 5/8” Sheet Metal Screw
4 C374 #10 Wire Nut
5 C375 3 Wire Cable (11’ 3” Long)
6 C152 Column Strap - 2-1/8
7 C377 #10 - 32 x 3/4” Bolt
8 TU4942 #10 - 32 Nut
9 C151 Column Strap - 1-7/8
10 C154 Foot Switch less Cord
11 C2110 Heyco Bushing

Page 16
CONTROL BOX
Ref. No. Part No. Description
1 C1844 Control Box
3 C2085 Contractor Rail
4 C183 Rating Nameplate
5 TU15138 Transformer
7 TU3266 #8 - 32 Hex Nut
8 FB87 #8 Lockwasher
9 C2086 Bottom Panel
10 SV332 #8 - 32 x 3/8” Screw
11 EA-00685-0 Reversing Contractor
Ref. No. Part No. Description
13 TU3479 #10 - 32 x 7/16”
Truss Screw
14 SB180 Switch Box Cover
15 TU7733 #8 Self-Drill Screw
16 C1843 Control Box Cover
17 FB187 #10 Lockwasher
18 TU2842 #10 - 32 Hex Nut
19 TU2372 Bushing

Page 17
WARRANTY
The Cissell Manufacturing Company (Cissell) warrants all new equipment (and the original parts thereof)
to be free from defects in material or workmanship for a period of one (1) year from the date of sale thereof
to an original purchaser for use, except as hereinafter provided. With respect to non-durable parts
normally requiring replacement in less than one (1) year due to normal wear and tear, including, but not
limited to, cloth goods, valve discs, hoses, and iron cords, and with respect to all new repair or replacement
parts for Cissell equipment for which the one (1) year warranty period has expired, or for all new repair
or replacement parts for equipment other than Cissell equipment, the warranty period is limited to ninety
(90) days from date of sale. The warranty period on each new replacement part furnished by Cissell in
fulfillment of the warranty on new equipment or parts shall be for the unexpired portion of the original
warranty period on the part replaced.
With respect to electric motors, coin meters and other accessories furnished with the new equipment, but
not manufactured by Cissell, the warranty is limited to that provided by the respective manufacturer.
Cissell's total liability arising out of the manufacture and sale of new equipment and parts, whether under
the warranty or caused by Cissell's negligence or otherwise, shall be limited to Cissell repairing or
replacing, at its option, any defective equipment or part returned f.o.b. Cissell's factory, transportation
prepaid, within the applicable warranty period and found by Cissell to have been defective, and in no event
shall Cissell be liable for damages of any kind, whether for any injury to persons or property or for any
special or consequential damages. The liability of Cissell does not include furnishing (or paying for) any
labor such as that required to service, remove or install; to diagnose troubles; to adjust, remove or replace
defective equipment or a part; nor does it include any responsibility for transportation expense which is
involved therein.
The warranty of Cissell is contingent upon installation and use of its equipment under normal operating
conditions. The warranty is void on equipment or parts; that have been subjected to misuse, accident, or
negligent damage; operated under loads, pressures, speeds, electrical connections, plumbing, or
conditions other than those specified by Cissell; operated or repaired with other than genuine Cissell
replacement parts; damaged by fire, flood, vandalism, or such other causes beyond the control of Cissell;
altered or repaired in any way that effects the reliability or detracts from its performance, or; which have
had the identification plate, or serial number, altered, defaced, or removed.
No defective equipment or part may be returned to Cissell for repair or replacement without prior written
authorization from Cissell. Charges for unauthorized repairs will not be accepted or paid by Cissell.
CISSELL MAKES NO OTHER EXPRESS OR IMPLIED WARRANTY, STATUTORY OR OTHERWISE,
CONCERNING THE EQUIPMENT OR PARTS INCLUDING, WITHOUT LIMITATION, A WARRANTY
OF FITNESS FOR A PARTICULAR PURPOSE, OR A WARRANTY OF MERCHANTABILITY. THE
WARRANTIES GIVEN ABOVE ARE EXPRESSLY IN LIEU OF ALL OTHER WARRANTIES, EXPRESS
OR IMPLIED. CISSELL NEITHER ASSUMES, NOR AUTHORIZES ANY PERSON TO ASSUME FOR
IT, ANY OTHER WARRANTY OR LIABILITY IN CONNECTION WITH THE MANUFACTURE, USE OR
SALE OF ITS EQUIPMENT OR PARTS.
For warranty service, contact the Distributor from whom the Cissell equipment or part was purchased.
If the Distributor cannot be reached, contact Cissell.
Table of contents
Other Cissell Sander manuals
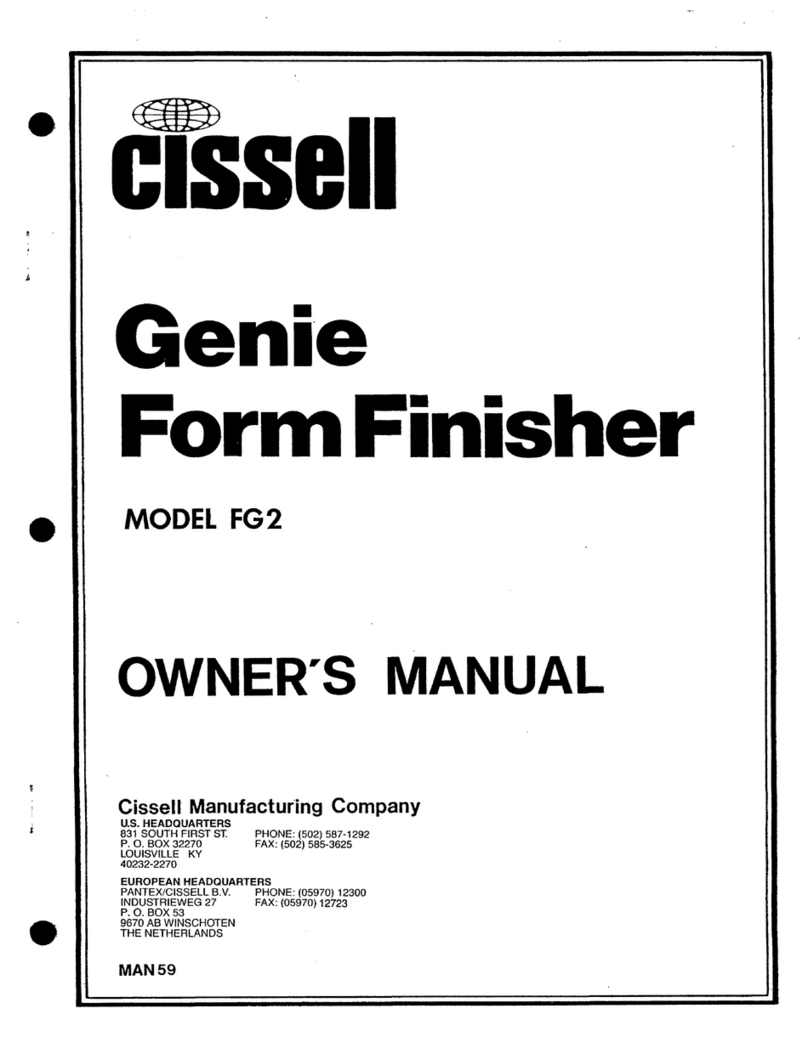
Cissell
Cissell GENIEMAN59 User manual
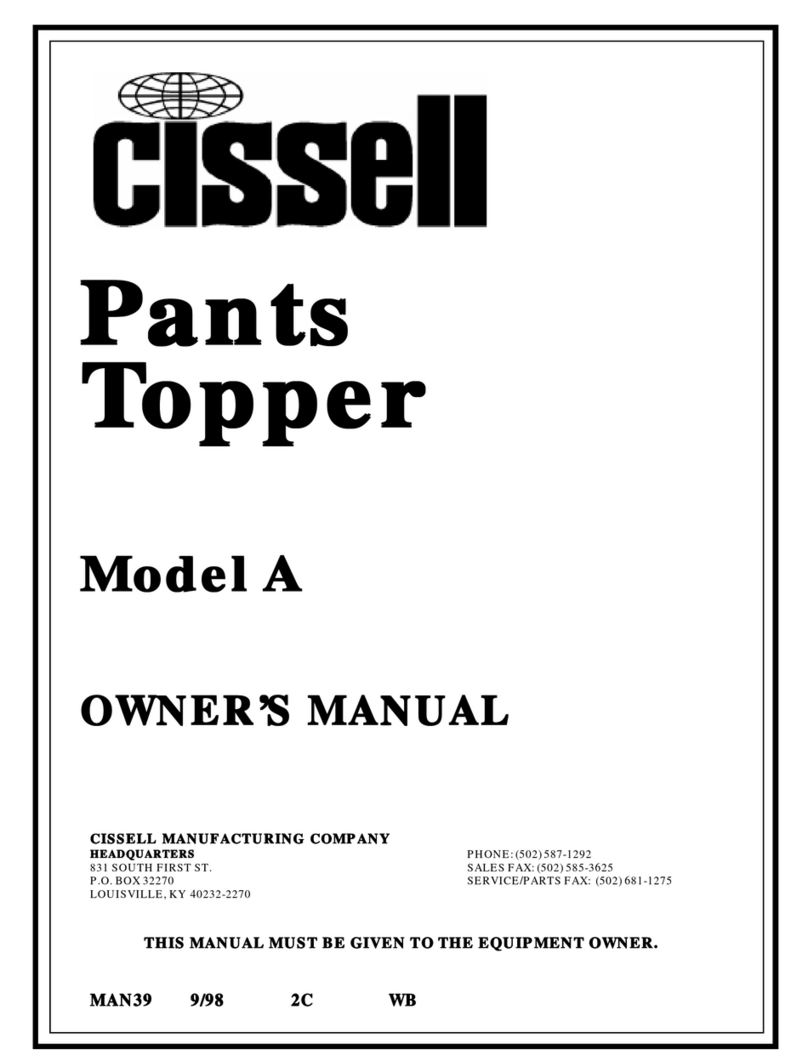
Cissell
Cissell PANTOPAMAN39 User manual

Cissell
Cissell MUMAN196 User manual
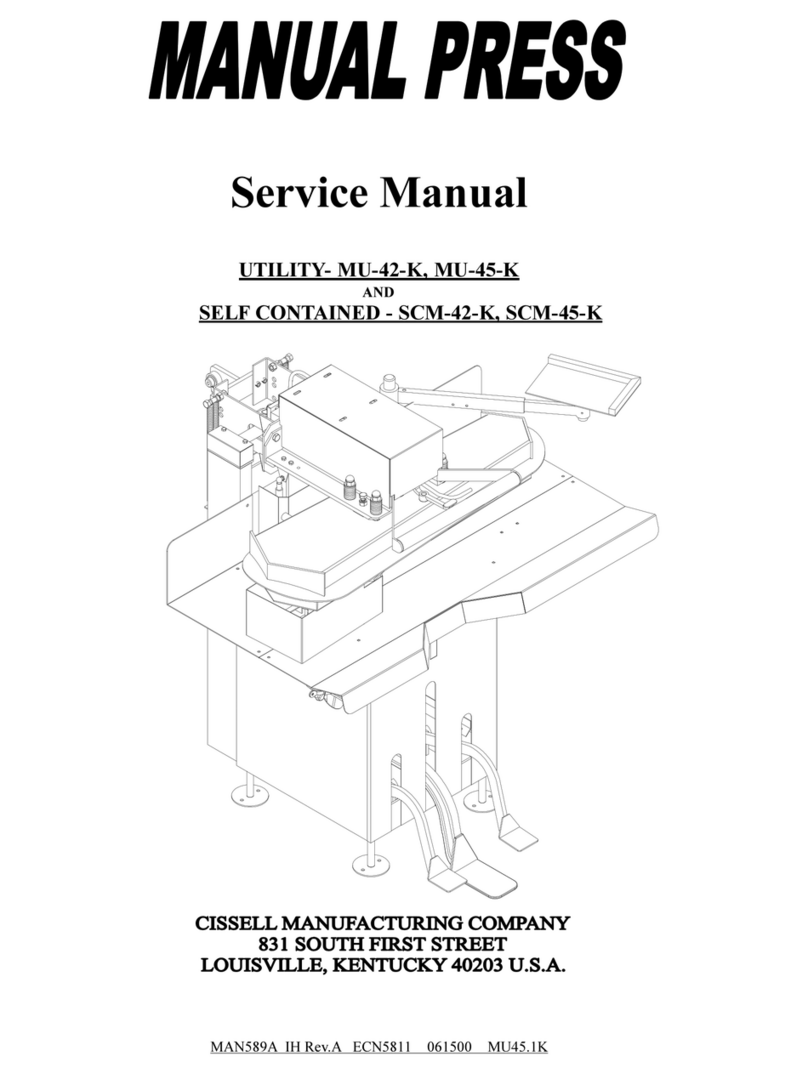
Cissell
Cissell KMAN589A User manual
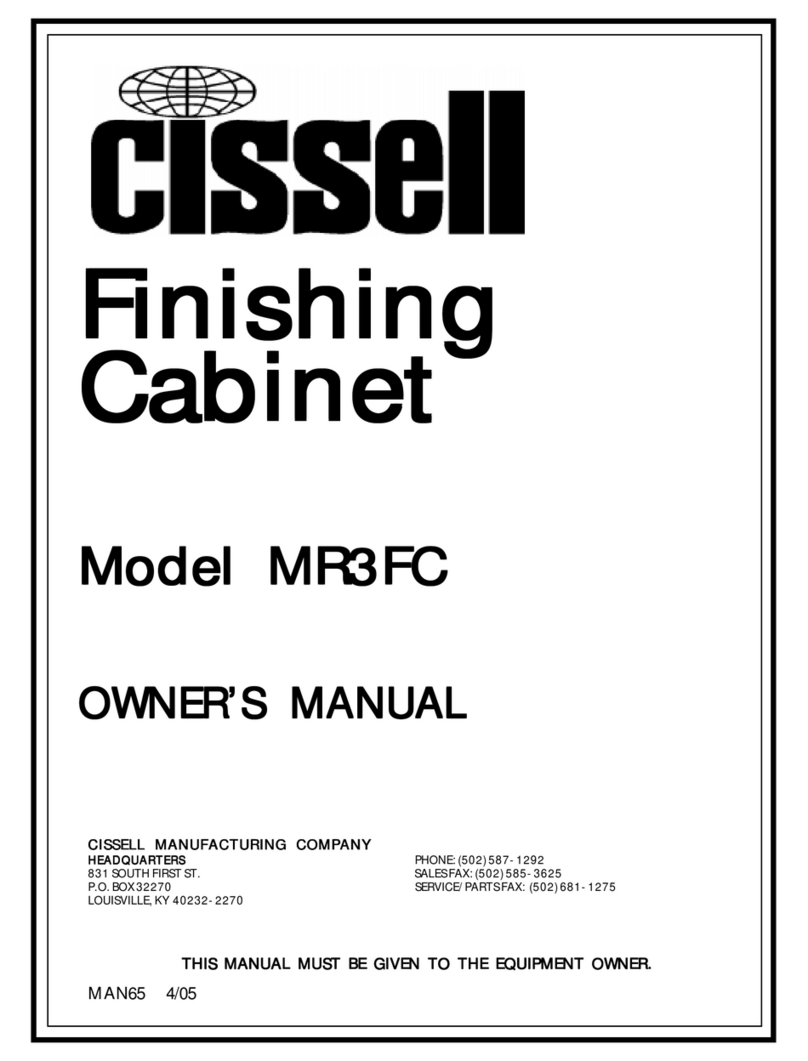
Cissell
Cissell MAN65 User manual
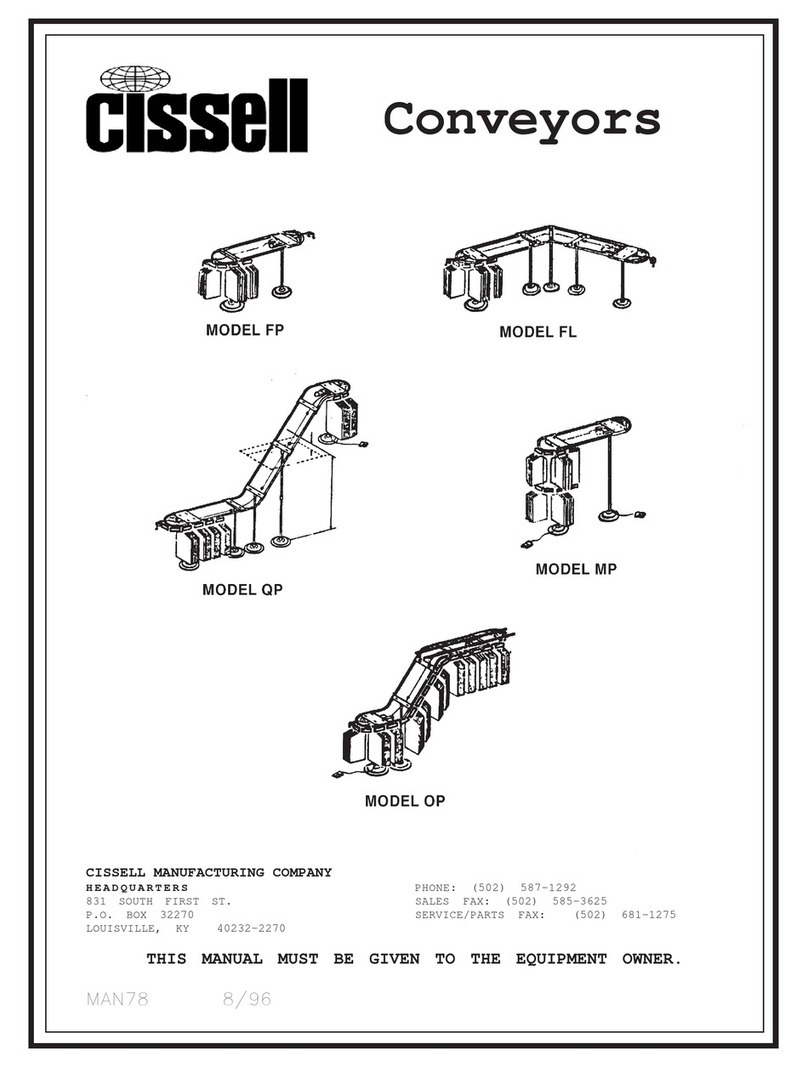
Cissell
Cissell MAN78 User manual
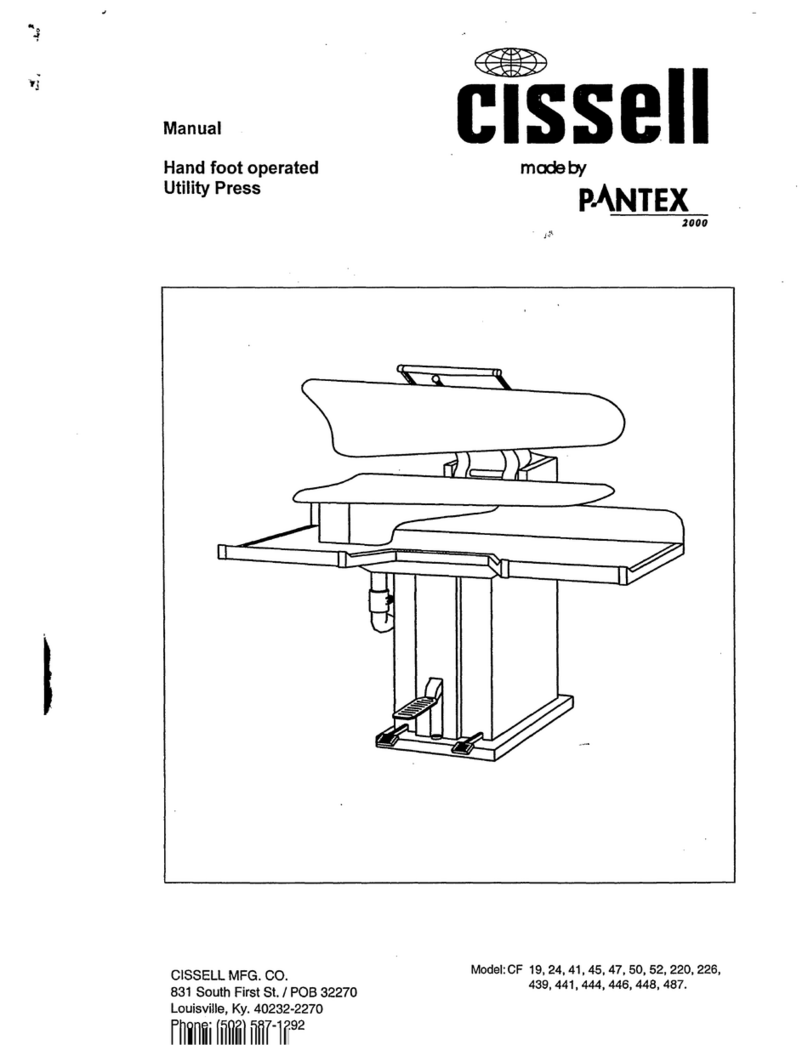
Cissell
Cissell CF 487 User manual
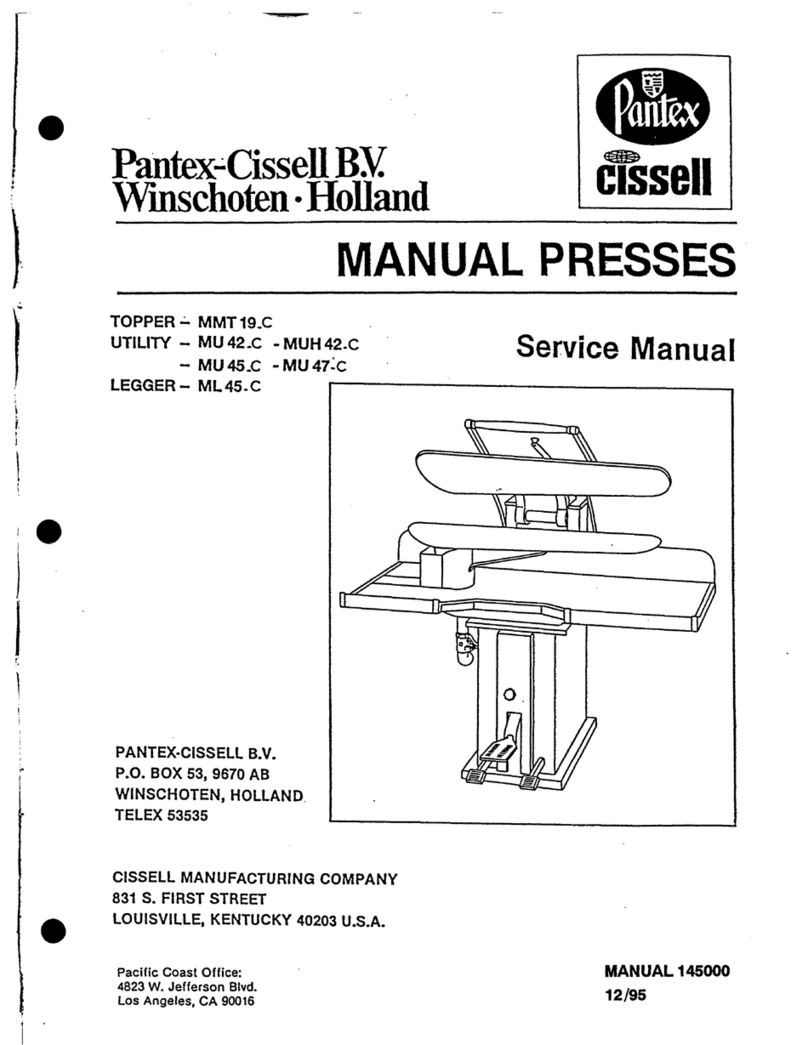
Cissell
Cissell MUCMAN145000 User manual
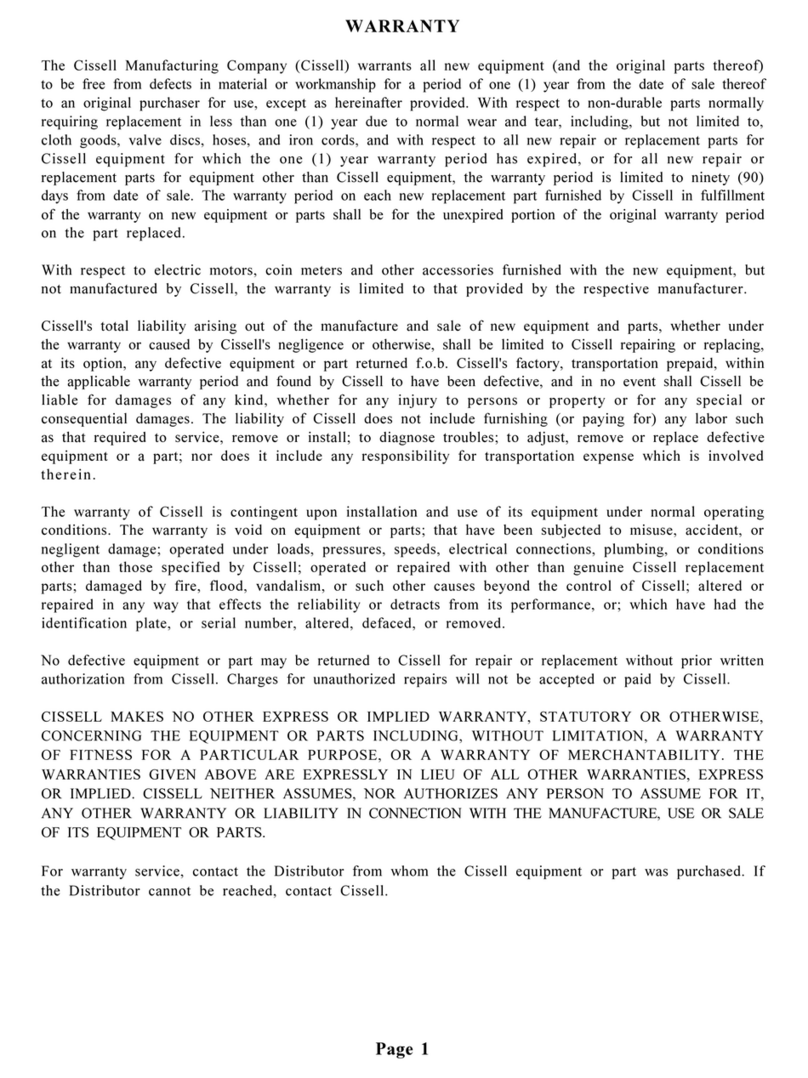
Cissell
Cissell FINTUNMAN67 User manual
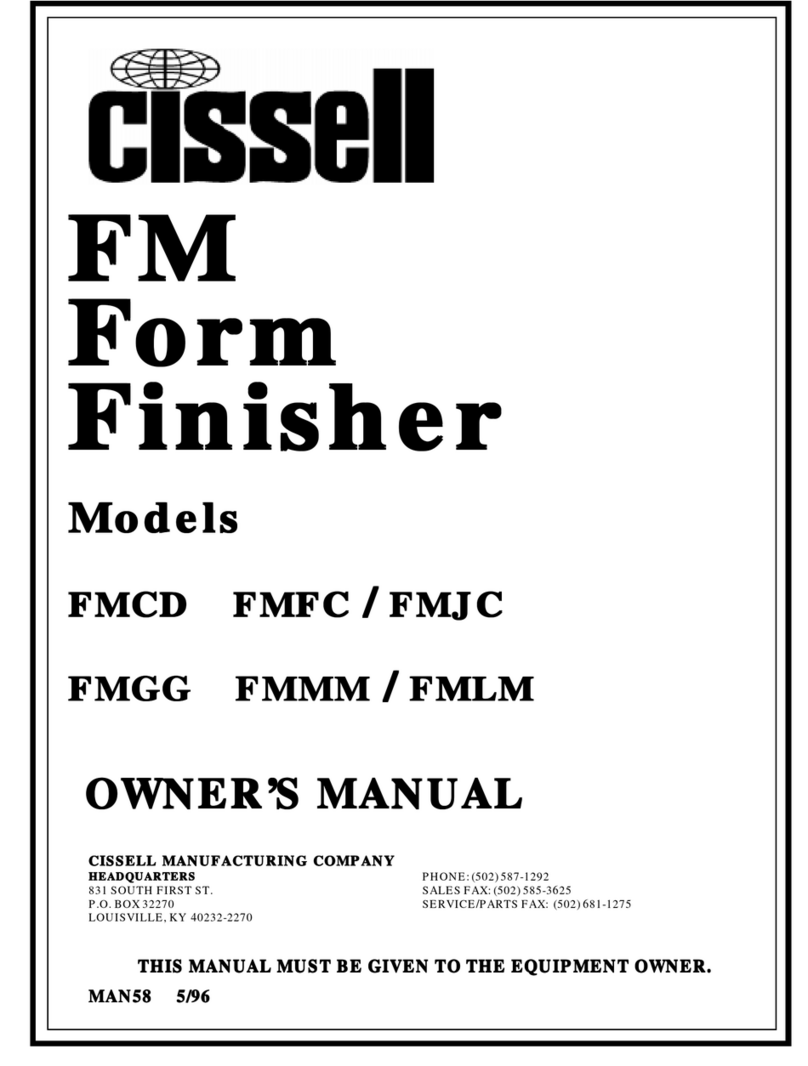
Cissell
Cissell FMMAN58 User manual