ComAp InteliVision 5 CAN User manual




















This manual suits for next models
1
Other ComAp Controllers manuals
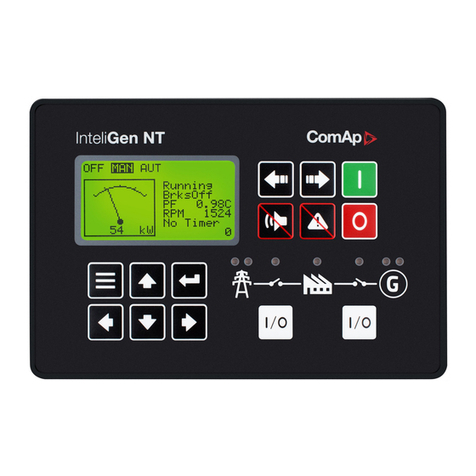
ComAp
ComAp IG-NT User manual
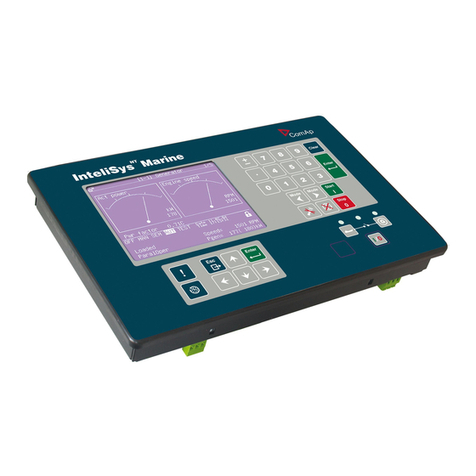
ComAp
ComAp IG-NT GC User manual
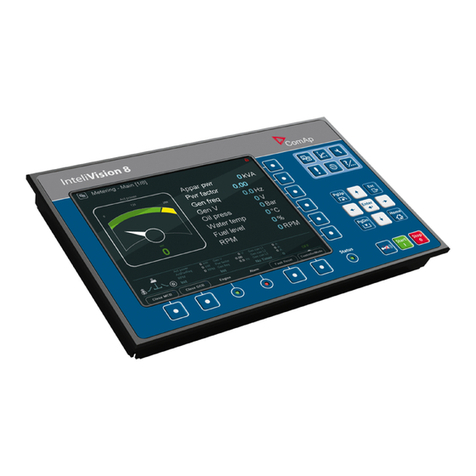
ComAp
ComAp InteliSys NT Programming manual
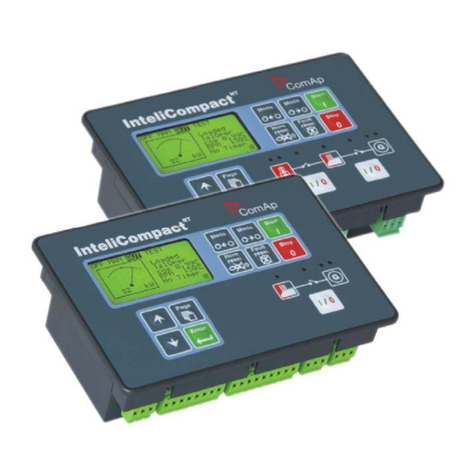
ComAp
ComAp InteliCompact NT Manual
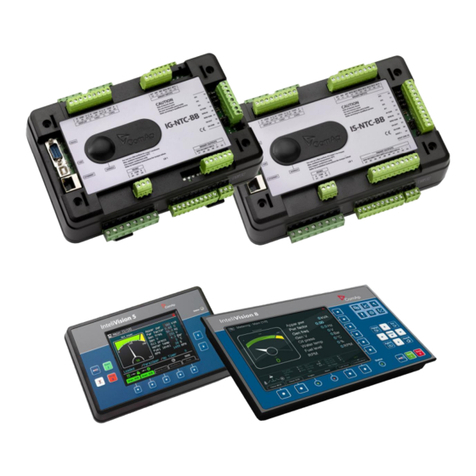
ComAp
ComAp IG-NT GC User manual
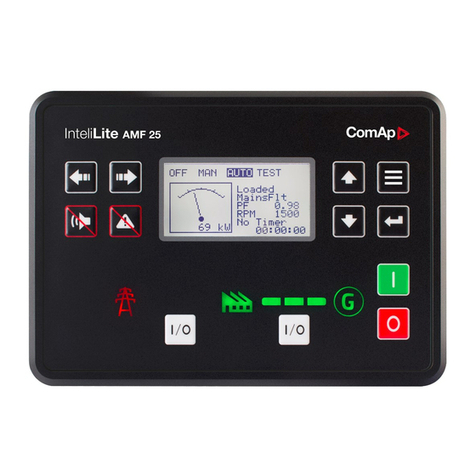
ComAp
ComAp InteliLite MRS16 User manual
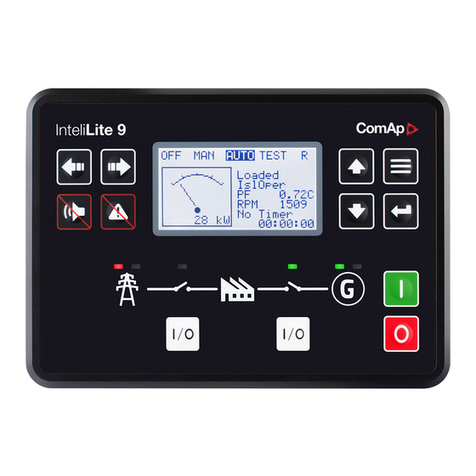
ComAp
ComAp InteliLite 9 User manual
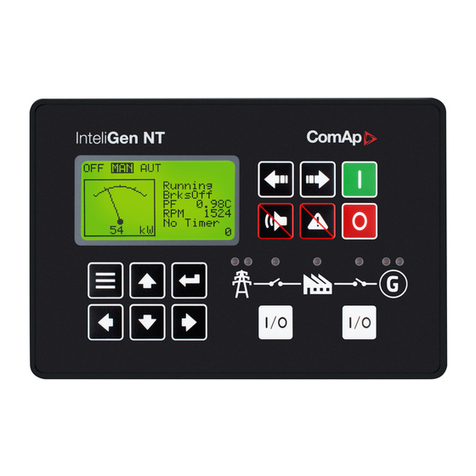
ComAp
ComAp IG-NT User manual
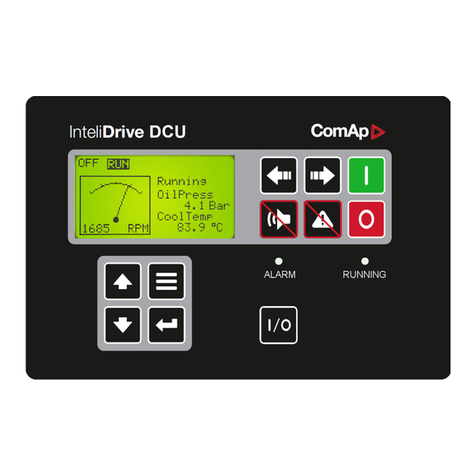
ComAp
ComAp InteliDrive DCU Industrial User manual

ComAp
ComAp IM-NT-BB User manual
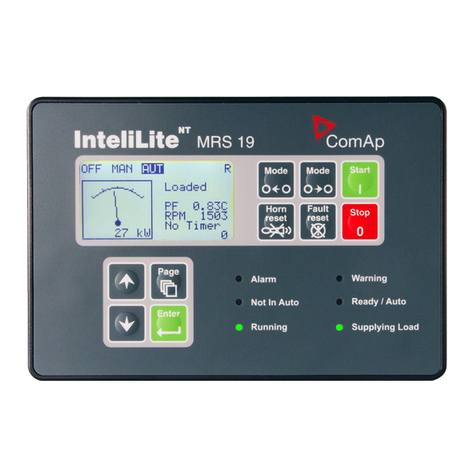
ComAp
ComAp InteliLite NT MRS19 User manual
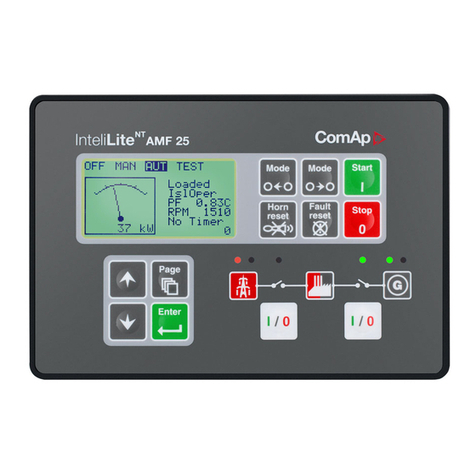
ComAp
ComAp InteliLite NT AMF 25 Manual
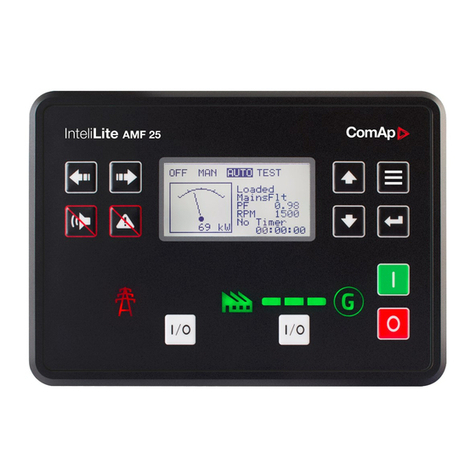
ComAp
ComAp InteliLite MRS16 User manual
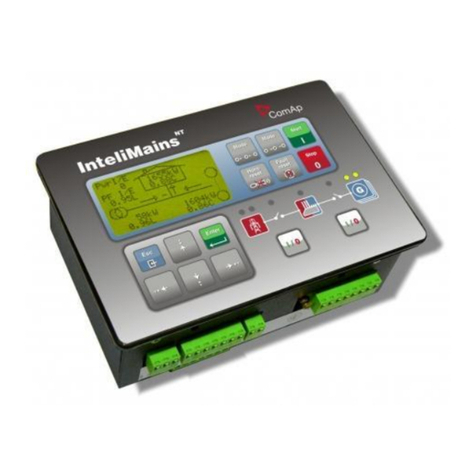
ComAp
ComAp IM-NT-BTB Manual
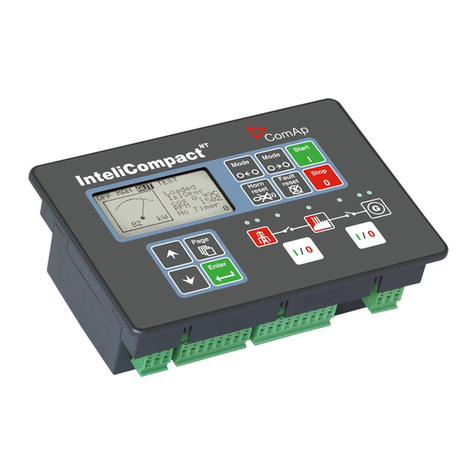
ComAp
ComAp InteliCompact NT User manual
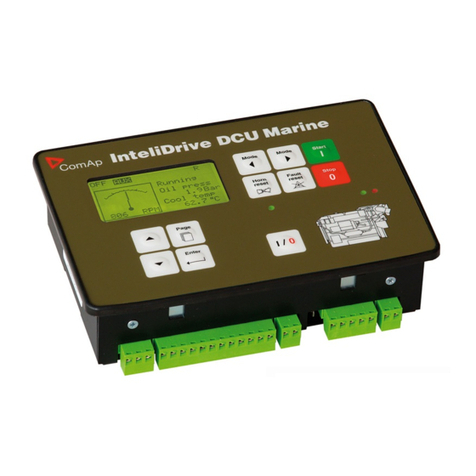
ComAp
ComAp InteliDrive DCU Marine User manual
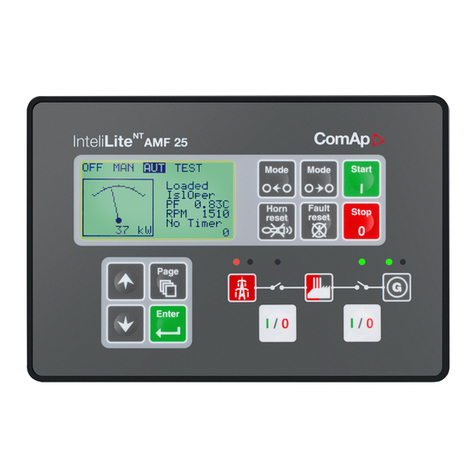
ComAp
ComAp intelilite nt amf20 User manual

ComAp
ComAp L151006001 User manual
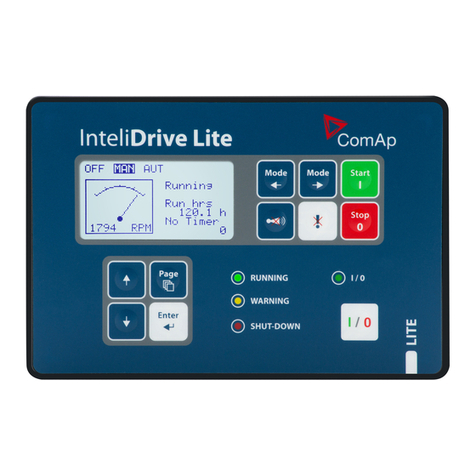
ComAp
ComAp InteliDrive FLX LITE User manual
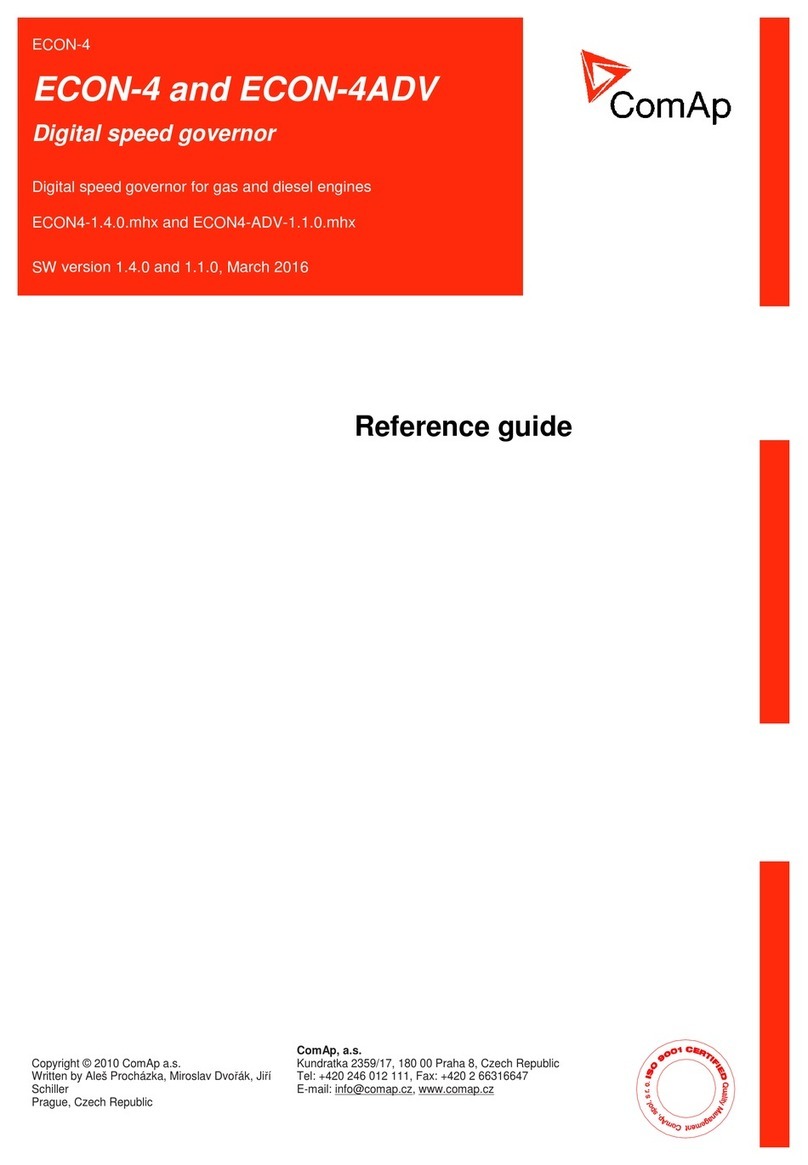
ComAp
ComAp ECON-4 User manual
Popular Controllers manuals by other brands
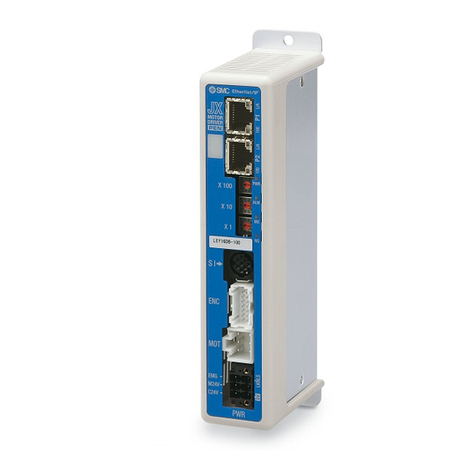
SMC Networks
SMC Networks EtherNet/IP JXC91 Series Information
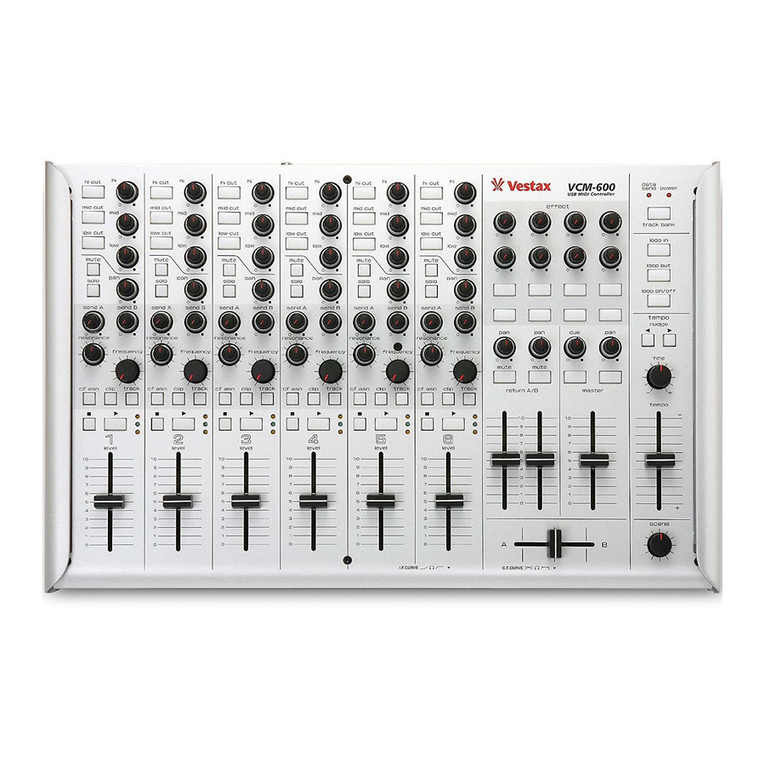
Vestax
Vestax VCM-600 owner's manual
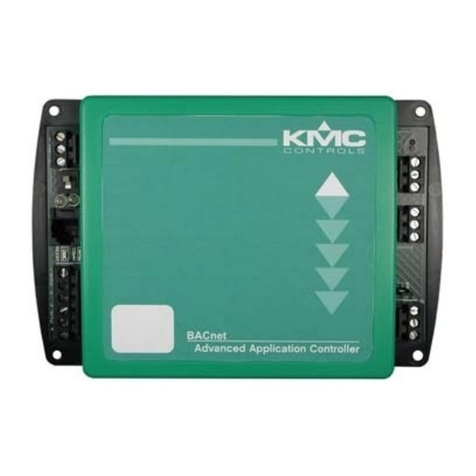
KMC Controls
KMC Controls BAC-7401 Installation and operation guide
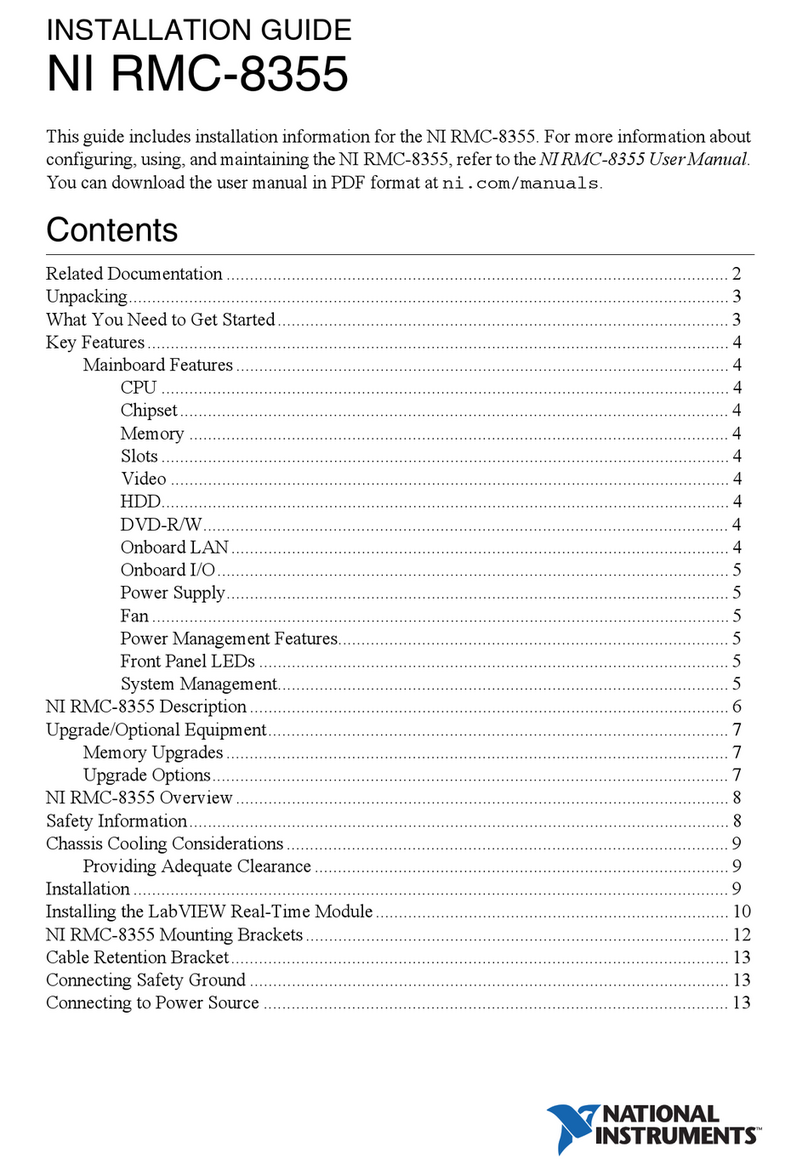
National Instruments
National Instruments NI RMC-8355 installation guide
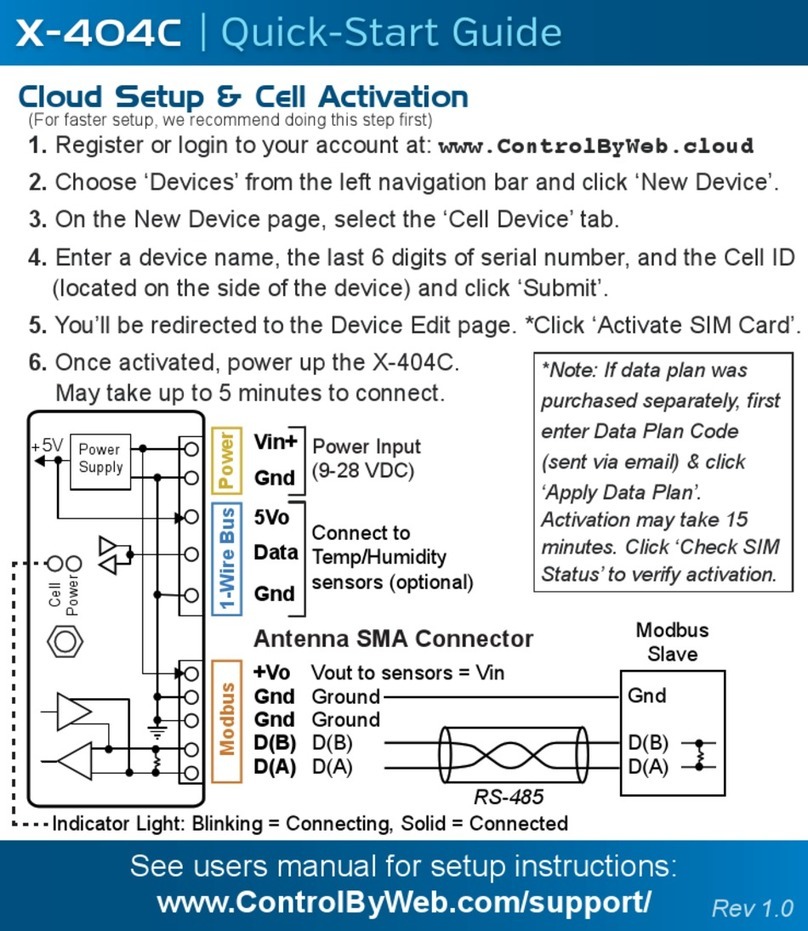
ControlByWeb
ControlByWeb X-404C quick start guide
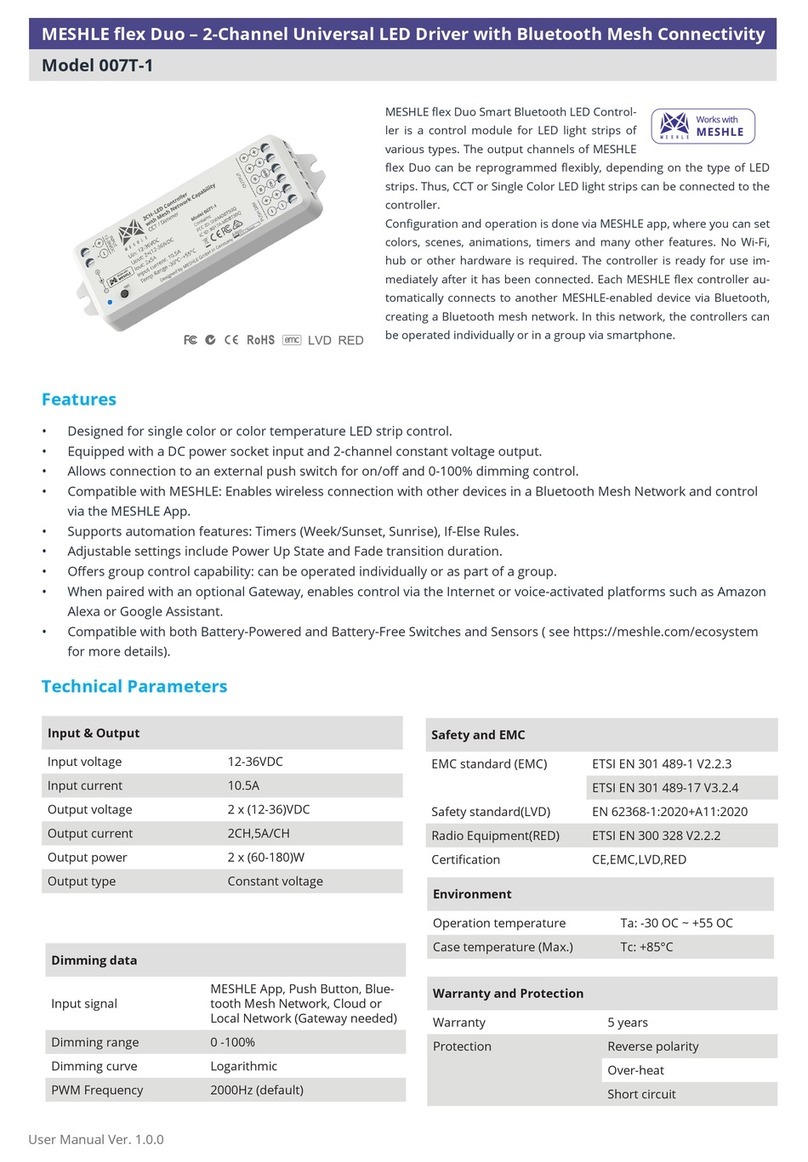
MESHLE
MESHLE 007T-1 quick start guide