Concens icon User manual

GB
USER MANUAL
icon
Linear In-line Actuator
USER MANUAL |icon |March 2022 |1
icon
Check for updates at www.concens.com
Contents
Introduction to icon 2
icon overview 3
Introduction to Concens Actuator Studio (CAS) 4
Basic operation 6
icon configurations
SDB – Single actuator/Direction control/Basic IO 8
SDH – Single actuator/Direction control/Hall output 10
SDP – Single actuator/Direction control/Position output 12
SPP – Single actuator/Position control/Position IO 14
SBS – Single actuator/Bus control/Status IO 16
MDO – Multiple actuator/Direction control/Override 18
icon accessories 20
Declarations and warnings 21
Contact information 21

USER MANUAL
2|USER MANUAL |icon |March 2022
icon
Introduction
Features
Integrated controller
Internal stroke limitation
Internal current limitation with adjustable limits
Internal heat protection
Adjustable start/stop ramp
Modbus RTU Interface on RS485
Interconnection of up to 128 units – up to 8 units synchronous
Plug & Play solution with conXion Box/Box+/DIN
Free downloadable software – Concens Actuator Studio (CAS)
icon is the intelligent actuator from Concens. The integrated controller provides advanced features and enables the
use of Modbus RTU on an RS-485 serial communication line.
The icon series of actuators – icon35, icon50 and icon60 – is based on the well-known con product line and has the
same physical dimensions as a con35, con50 and a con60.
icon Datasheet: https://www.concens.com/information/downloads/
icon Quick Guide: https://www.concens.com/information/downloads/#manual
conXion Box/Box+/DIN Installation Guide: https://www.concens.com/information/downloads/#manual
Ensure that the actuator is fixed in both its end brackets before use, as this will result in incorrect positioning.
Related documentation
icon Datasheet icon Quick Guide &
conXion Installation Guide

icon configurations
icon
congurations
SDB
Single Actuator
Direction Control
Basic IO
SDH
Single Actuator
Direction Control
Hall Output
SDP
Single Actuator
Direction Control
Position Output
SPP
Single Actuator
Position Control
Position Output
SBS
Single Actuator
BUS Control
Status/Control IO
MDO
Multiple Actuators
Direction Control
Override
Conguration letter A B C D E F
Voltage 12/24 VDC üüüüüü
Direction in/out üüü - - ü
5/10 VDC ref. output - - - ü- -
Stop input - - - - ü-
Override input - - - - - ü
Error output - - - - ü-
Analog position input - - - ü- -
Analog position output - - ü- -
-
Stop input/Pos. OK output - - - ü-
-
Hall Output - ü---
-
Single actuator setup Multi actuator
setup
icon actuators come in six different factory configurations as shown in the table below.
Configuration SDB SDH SDP SPP SBS MDO
Description Single/
Direction/Basic
Single/
Direction/Hall
Single/Direction/
Position
Single/Direction/
Position
Single/Bus/
Status
Multiple/
Direction/Overide
Configuration
letter A B C D E F
No./Color
Yellow (2) RS485 TX +A RS485 TX +A RS485 TX +A RS485 TX +A RS485 TX +A RS485 TX +A
Green (1) RS485 RX -B RS485 RX -B RS485 RX -B RS485 RX -B RS485 RX -B RS485 RX -B
Orange (3) GND Signal Hall B output GND Signal GND Signal GND Signal GND Signal
Black (4) GND Power GND Power GND Power GND Power GND Power GND Power
White (7) Not used Hall A output Position output 5-10 V reference Not used Override
Brown (6) Dir. IN Dir. IN Dir. IN Pos ok/stop input Error out Dir. IN
Blue (5) Dir. OUT Dir. OUT Dir. OUT Position input Stop input Dir. OUT
Red (8) Power 12/24 V Power 12/24 V Power 12/24 V Power 12/24 V Power 12/24 V Power 12/24 V
For all configurations except SDH, Signal GND (pin 3) and Power GND (pin 4) must be connected at the end
of the actuator cable, i.e. at the Molex Minifit jr. connector. This connection is established inside the conXion units but
can be removed with a jumper. Please refer to the installation manual for further details.
The numbers in the (parentheses) refer to the Molex Minifit layout.
Please find further information on jumper settings for the conXion Box, Box+ and DIN versions in the
conXion - Installation Guide:
https://www.concens.com/information/downloads/#manual
All icon actuators come with an 8-pin Molex Mini fit JR connector unless specified otherwise and the connections for
each configuration are shown in the table below.
USER MANUAL |icon |March 2022 |3
icon
USER MANUAL

USER MANUAL
4|USER MANUAL |icon |March 2022
icon
Concens Actuator Studio
Concens Actuator Studio (CAS) is the software package, which is used to set the parameters and control the actuators
during the development and test phase.
CAS can be downloaded free of charge from the Concens website:
https://www.concens.com/information/downloads/#software
Concens Actuator
Studio (CAS)
To connect the icon actuator to CAS, we recommend using the Concens programming
cable as shown below in conjunction with the conXion box, box+ or DIN.
Programming cable
CC-874-01-0000-00-00
conXion Box
CC-971-07-0000-00-00
conXion DIN
CC-971-06-0000-00-00
conXion Box+
CC-971-05-0000-00-00

When CAS is started, it initially shows a window with information about version etc. This window closes automatically
after 10 seconds or can be closed manually after which the overview screen appears.
The number of icons connected can be adjusted, and the number of lines shown in the overview window will change
accordingly. Only one icon at a time can be active and operated in CAS. However, it is possible to see all actuators in
the overview. If an actuator is recognized the uptime counter will be counting if “Active” is ticked.
When more icons are connected, they must have different addresses. All single setup icons come with default address
8. This can be changed under the “Service/Config” tab. Enter new address in “Modbus address” and click “Save/
Update”.
Address range for single actuators is
1 to 199. Multi setup icons (MDO) are
preset to addresses from 200 to 207
with 200 being “Master” (please refer to
MDO section).
USER MANUAL |icon |March 2022 |5
icon
USER MANUAL

USER MANUAL
6|USER MANUAL |icon |March 2022
icon
Basic operation
icon actuators use pulses generated by motor revolutions to control the position and to synchronize more actuators
running in a multiple actuator setup.
All icon actuators are configured and initialized from factory, but it may be required to perform additional initialization
during installation to ensure proper operation. This is done using the “Home” and “Learn” functions in CAS. Home
returns the piston to the fully retracted position and stores this position as “Home” (Position 0). The Learn function
runs a full cycle and determines both fully retracted and fully extracted positions of the piston. Please note that these
positions may be determined by physical limitations in the mechanical design of the application and not by the end
positions of the actuator.
Before performing a "Home" or "Learn" cycle the actuator(s) need to be pinned or installed in both the rear and front
bracket. Otherwise the piston can spin and give an incorrect result.
Click the “Run Learn” under the “Service/Config” tab to perform a learn cycle. If required by the application, “Home”
position can be changed to fully extracted position and, speed during learn can be adjusted. All actuators in a multi-
actuator setup must be “Homed” individually.
If pin 5 and pin 6 are connected to GND simultaneously for more than 10 seconds, Homing/Learning is started.
During this the actuator will travel at a lower speed and it is important that neither of the brackets can rotate freely.
0-point - (Homing) and maximum stroke length (Learning) are saved during this cycle.
Please note: Learn will reset settings for “Range Scale”.
Performing a Learning without having access to the CAS
software can be done by using either the handset or conXion
Box+ by pressing and holding both in and out buttons for 10
seconds.
Depending on the original setting of the “actuator home
position” the end position will either be Retracted or Extracted
after performing the Learning process.
Safe zones can equally be set without having access to the
CAS software by using the handset or conXion Box+.
Setting the safe zone out is done by pressing both buttons for
5 seconds and then pressing out button.
Setting the safe zone in is done by pressing both buttons for 5
seconds and then pressing in button.

Other basic parameters that can be adjusted under the “Actuator/Parameters” tab.
As a part of a learn cycle, “Safe Zone” values are default set to 50 steps (Backwards) and full stroke-50 steps (Forward).
If the stroke length is entered manually, it is necessary also to enter Safe Zone values.
USER MANUAL |icon |March 2022 |7
icon
USER MANUAL

USER MANUAL
8|USER MANUAL |icon |March 2022
icon
icon SDB (Single Actuator/Direction Control/Basic IO)
The icon SDB is the basic version of the icon family. It is recognized by the capital letter A in the part number (e.g.
350100-713232A020000). The SDB version can be used as a “Plug and Play” solution controlled by a simple
handset, two dry contacts or by a PLC. The conXion Box/Box+/DIN can be used as an interface. Please refer to
conXion Box/Box+/DIN documentation for further details.
Block diagram
A block diagram for the icon SDB configuration is shown below:
M
Motor
controller
H-Bridge
Internal power regulator
generates 3,3 V for
processor and supply 12
and 24 V to
motorcontroller
Microprocessor
runs program
according to
firmware in the
EEprom and
secure
functionality
EEPROM
contains
firmware,
parameters and
memory for
saving data
RS 485 driver
which is
interface for
data
communication
12/24
VDC GND
RS 485 TX +A
RS 485 RX -B
Icon Block Diagram SDB
White and orange wire are
not used. Signal GND
(orange) is connected to
GND (black) inside the icon
Direction IN: Brown wire
Direction OUT: Blue wire
SDB Pin Assignment
Pin no. Wire color Function
1Green RS485 -B
2 Yellow RS485 +A
3Orange GND signal
4Black GND
5Blue Direction OUT
6Brown Direction IN
7 White Not used
8Red Power (12 or 24 VDC)
Pin numbers refer to Molex 8-pin connector. Signal GND and Power GND is connected inside the icon.
Please Note:
White, Brown, Blue and Orange wire have different functionality according to configuration.
See Data sheet for more information.

SDB has inputs for direction (in/out). Pin 5 and pin 6 are used for direction commands. They are active low and must
be pulled to power GND to activate.
Interconnection/Modbus control
The icon SDB can also be controlled via Modbus with the same functions as mentioned above. More SDB icons can
be connected to the same bus if they have individual addresses. If controlled with Modbus it is still possible to override
with input from the handset or contacts. However, the handset or contact-set should be, either common for all icons or
each would need its own.
Application example with an icon connected to PLC with Modbus interface via conXion DIN:
icon conXion DIN PLC with Modbus card
USER MANUAL |icon |March 2022 |9
icon
USER MANUAL

USER MANUAL
10 |USER MANUAL |icon |March 2022
icon
icon SDH (Single Actuator/Direction Control/Hall output)
The SDH configuration of icon provides the same features as SDB and in addition to this, it has outputs for hall
signals. SDH is recognized by the capital letter B in the part number (e.g., 350100-713232B020000). The SDH
version can work as a “Plug and Play” solution controlled by a simple handset with two dry contacts or by a PLC.
The conXion Box/Box+/DIN is used as an interface for these options. Please refer to conXion Box/Box+/DIN
documentation for further details.
Block diagram
A block diagram for the SDH configuration is shown below:
M
Motor
controller
H-Bridge
Internal power regulator
generates 3,3 V for
processor and supply 12
and 24 V to
motorcontroller
Microprocessor
runs program
according to
firmware in the
EEprom and
secure
functionality
EEPROM
contains
firmware,
parameters and
memory for
saving data
RS 485 driver
which is
interface for
data
communication
12/24
VDC GND
RS 485 TX +A
RS 485 RX -B
Icon Block Diagram SDH
Direction IN: Brown wire
Direction OUT: Blue wire
Hall B signal: Orange wire
Hall A signal: White wire
SDH Pin Assignment
Pin no. Wire color Function
1Green RS485 -B
2 Yellow RS485 +A
3Orange Hall B signal
4Black GND
5Blue Direction OUT
6Brown Direction IN
7 White Hall A signal
8Red Power (12 or 24 VDC)
Please Note:
White, Brown, Blue and Orange wire have different functionality according to configuration.
See Data sheet for more information.

SDH has inputs for direction (in/out) and two channel hall outputs. Pin 5 and pin 6 are active low and must by pulled
down to power GND to activate. The hall channels at pin 3 and pin 7 are 3.3 Vpp square wave signal (max 5mA) with
a 50% duty cycle and a 90˚ phase shift. Hall outputs are NPN logic TTL level.
If pin 5 and pin 6 are connected to GND simultaneously for more than 10 seconds, Homing/Learning is started.
During this the actuator will travel at a lower speed and it is important that neither of the brackets can rotate freely.
0-point - (Homing) and maximum stroke length (Learning) are saved during this cycle.
Special function for SDH is hall output at pin 3 (hall A) and pin 7 (hall B)
Interconnection/Modbus control
The icon SDH can also be controlled by Modbus but with the same limitations as already mentioned. You can add
numerous SDH icons to your application if each is provided with an individual address. If controlled with Modbus it is
still possible to override with an analogue input from the handset or contacts. However, the handset or contact-set
should be, either common for all icons or each would need its own.
Application example with an icon connected to PLC with Modbus interface via conXion DIN:
icon conXion DIN PLC with Modbus card
USER MANUAL |icon |March 2022 |11
icon
USER MANUAL

USER MANUAL
12 |USER MANUAL |icon |March 2022
icon
icon SDP (Single Actuator/Direction Control/Position output)
The SDP configuration of icon provides the same features as SDB and in addition to this, it has an analogue position
output. SDP is recognized by the capital letter C in the part number (e.g., 350100-713232C020000). The SDP
version can work as a “Plug and Play” solution controlled by a simple handset with two dry contacts or by a PLC. The
conXion Box/Box+/DIN can be used as an interface. Please refer to conXion Box/Box+/DIN documentation for
further details.
Block diagram
A block diagram for the SDP configuration is shown below:
M
Motor
controller
H-Bridge
Internal power regulator
generates 3,3 V for
processor and supply 12
and 24 V to
motorcontroller
Microprocessor
runs program
according to
firmware in the
EEprom and
secure
functionality
EEPROM
contains
firmware,
parameters and
memory for
saving data
RS 485 driver
which is
interface for
data
communication
12/24
VDC GND
RS 485 TX +A
RS 485 RX -B
Icon Block Diagram SDB
White and orange wire are
not used. Signal GND
(orange) is connected to
GND (black) inside the icon
Direction IN: Brown wire
Direction OUT: Blue wire
SDP Pin Assignment
Pin no. Wire color Function
1Green RS485 -B
2 Yellow RS485 +A
3Orange GND signal
4Black GND
5Blue Direction OUT
6Brown Direction IN
7 White Position voltage output
8Red Power (12 or 24 VDC)
Numbers refer to pin layout of the 8-pin Molex plug of the icon.
Please Note:
White, Brown, Blue and Orange wire have different functionality according to configuration.
See Data sheet for more information.

SDP has inputs for direction (in/out), and analog feedback output for position. The inputs for direction at pin 5 and
pin 6 are active low and must by pulled to power GND to activate. Pin 7 is an analog output that relate to the actual
position of the piston. The output has two ranges, which can be selected in CAS: 0-5 VDC and 0-10 VDC for 24
VDC icons, but only 0-5 V range for 12 VDC icons. Power GND and Signal GND must be connected at the PLC or
at the end of the cable. If pin 5 and pin 6 are connected to GND simultaneously for more than 10 seconds, Homing/
Learning is started. During this the actuator will travel at a lower speed and it is important that neither of the brackets
can rotate freely. 0-point - (Homing) and maximum stroke length (Learning) are saved during this cycle.
The "homing" process can only be performed from the CAS software.
Interconnection/Modbus control
The SDP configuration can also be controlled by Modbus but with the same limitations as already mentioned. You can
add numerous SDP icons to your application if each is provided with an individual address. If controlled with Modbus it
is still possible to override with analog input from handset or contacts. However, the handset or contact-set should be,
either common for all icons or each would need its own.
Application example with an icon connected to PLC with Modbus interface via conXion DIN:
icon conXion DIN PLC with Modbus card
USER MANUAL |icon |March 2022 |13
icon
USER MANUAL

USER MANUAL
14 |USER MANUAL |icon |March 2022
icon
icon SPP (Single Actuator/Position control/Position output)
The SPP configuration of icon has the same feature as SDB and in addition to this it has is an analog position input
and a position OK output. It is recognized by the capital letter D in the part number (e.g., 350100-713232D020000).
With SPP the position of the actuator can be controlled by an analogue voltage, i.e. 5 VDC will move the piston to 50%
of the stroke if 10 VDC input range is used. The conXion Box/Box+/DIN are used as an interface for these options,
but you are free to use other options. Please refer to the conXion Box/Box+/DIN documentation for
further details.
Modbus control is not recommended with the SPP configuration as the analogue input always has higher priority than
Modbus commands.
Block diagram
A block diagram for the SPP configuration is shown below:
M
Motor
controller
H-Bridge
Internal power regulator
generates 3,3 V for
processor and supply 12
and 24 V to
motorcontroller
Microprocessor
runs program
according to
firmware in the
EEprom and
secure
functionality
EEPROM
contains
firmware,
parameters and
memory for
saving data
RS 485 driver
which is
interface for
data
communication
12/24
VDC GND
RS 485 TX +A
RS 485 RX -B
Icon Block Diagram SPP
Position control with
potentiometer. White wire
is reference (0-5(10)V).
Blue wire is position input.
Yellow wire is signal GND.
Brown wire has multiple functions:
Position OK output
Stop input
Initiate Homing/Learning cycle
Please Note:
White, Brown, Blue and Orange wire have different functionality according to configuration.
See Data sheet for more information.

The icon SPP has an analog input for positioning at pin 5 and a reference output at pin 7. Reference voltage is
selectable via CAS, i.e. 5 or 10 VDC (5 VDC only for 12 VDC actuators). Pin 6 has combined purpose for “Position
OK”, “STOP”, and “Home/Learn”. Under normal conditions pin 6 is “high” (3.3 VDC/max 5mA) when the actuator is
moving. When the target position is reached it signals “Position OK” by switching to 0 V (low) and the actuator stops.
In addition to this, pin 6 can also be used as an input by pulling it down to GND. This will stop the actuator. If pin 6 is
connected to pin 5 during power up the Homing/Learning cycle is activated.
SPP Pin Assignment
Pin no. Wire color Function
1Green RS485 -B
2 Yellow RS485 +A
3Orange GND Signal
4Black GND
5Blue Position input
6Brown Position ok output/stop input
7 White 5 – 10 VDC reference
8Red Power (12 or 24 VDC)
USER MANUAL |icon |March 2022 |15
icon
USER MANUAL

USER MANUAL
16 |USER MANUAL |icon |March 2022
icon
icon SBS (Single Actuator/Bus control/Status control IO)
The SBS configuration of icon is designed for Modbus communication and control only. It has, however, one digital
stop input and one digital error output. SBS is recognized by the capital letter E in the part number (e.g. 350100-
713232E020000).
Block diagram
A block diagram for the SBS configuration is shown below:
M
Motor
controller
H-Bridge
Internal power regulator
generates 3,3 V for
processor and supply 12
and 24 V to
motorcontroller
Microprocessor
runs program
according to
firmware in the
EEprom and
secure
functionality
EEPROM
contains
firmware,
parameters and
memory for
saving data
RS 485 driver
which is
interface for
data
communication
12/24
VDC GND
RS 485 TX +A
RS 485 RX -B
Icon Block Diagram SBS
White
wire is
not used
Brown wire is used
for error output. It
changes state from
0Volt to 3,3 Volt in
case an error is
detected
Orange wire is Signal GND. In this
configuration Signal GND and
Power GND can be ordered and
connected inside the icon which
enables the use of a 6-wire cable
instead of 8-wire cable
Blue wire is used for ”STOP” input
and if pulled to ground any
movement is disabled
SBS Pin Assignment
Pin no. Wire color Function
1Green RS485 -B
2 Yellow RS485 +A
3Orange GND Signal
4Black GND
5Blue Stop input
6Brown Error output
7 White Not used
8Red Power (12 or 24 VDC)
Please Note:
White, Brown, Blue and Orange wire have different functionality according to configuration.
See Data sheet for more information.

Pin 5 (active low) is a digital stop input, which disables the motor drivers in the icon completely. Pin 6 (active high) is
a fault output. Any fault detected is indicated by a change from 0 VDC to 3.3 VDC at this pin. Pin 3 is a signal GND
connection.
The conXion Box/Box+/DIN can be used as an interface. Please refer to the conXion Box/Box+/DIN documentation
for further details.
Interconnection/Modbus control
The interconnection of icon SBS is illustrated below. Up to 10 icons can be connected in the same setup without
additional hardware. More than 10 units require a Modbus hub or similar.
icon conXion DIN PLC with Modbus card
USER MANUAL |icon |March 2022 |17
icon
USER MANUAL

USER MANUAL
18 |USER MANUAL |icon |March 2022
icon
icon MDO (Multiple actuator/Direction control/Override)
The icon MDO is designed to work in a multi-actuator setup. It allows up to eight icons to run synchronized sharing a
common load based on the master/slave principle. MDO is recognized by the capital letter F in the part number (e.g.
350100-713232F020000).
The conXion Box/Box+/DIN can be used to cascade the actuators to simplify wiring etc. Please refer to the conXion
Box/Box+/DIN documentation for further details. Each conXion needs it´s own connection to the main power supply.
It is not possible to control an MDO setup via Modbus as this bus is used for synchronization purposes.
Block diagram
A block diagram for the MDO configuration is shown below:
M
Motor
controller
H-Bridge
Internal power regulator
generates 3,3 V for
processor and supply 12
and 24 V to
motorcontroller
Microprocessor
runs program
according to
firmware in the
EEprom and
secure
functionality
EEPROM
contains
firmware,
parameters and
memory for
saving data
RS 485 driver
which is
interface for
data
communication
12/24
VDC GND
RS 485 TX +A
RS 485 RX -B
Icon Block Diagram MDO
Direction IN: Brown wire (active low)
Direction OUT: Blue wire (active low)
Orange: Signal GND
White wire is used for Override. In normal state voltage level is 3.3 V, when
Override is activated it is pulled to ground (0 V = active low)
MDO Pin Assignment
Pin no. Wire color Function
1Green RS485 -B
2 Yellow RS485 +A
3Orange GND Signal
4Black GND
5Blue Direction OUT
6Brown Direction IN
7 White Override (active low)
8Red Power (12 or 24 VDC)
Please Note:
White, Brown, Blue and Orange wire have different functionality according to configuration.
See Data sheet for more information.

All actuators in an MDO setup must have different addresses with the master being number 200 and slaves counting
from 201 to 207. All other parameters in the icons must be identical. This is configured from factory but can be
changed via CAS.
Please refer to the Basic Operation section to perform Homing of the actuators and please note that all actuators in
an MDO setup must be Homed individually.
Pin 5 and pin 6 of the master icon are used to control the actuators out and in respectively. Both pins are active low,
i.e. they need to be pulled down to GND to activate.
Pin 7 is an override input (active low), which enables individual travel (adjustment) of one actuator in the setup. After
activating pin 7, pin 5 and pin 6 on the specific actuator can be used to move the piston.
Interconnection
The figure below shows an MDO setup with conXion DIN units connected to a PLC using the Direction Out and
Direction In pins on the master actuator. Please refer to Installation Guide for conXion Box/Box+/DIN for details
about interconnections etc.
USER MANUAL |icon |March 2022 |19
icon
USER MANUAL

USER MANUAL
20 |USER MANUAL |icon |March 2022
icon
icon Accessories - incl. Part No.
Part No. for our conXion products and the optional accessories
conXion Box
CC-971-07-0000-00-00
conXion DIN
CC-971-06-0000-00-00
Programming cable
CC-874-01-0000-00-00
Handset - Online conFIGURATOR (C3/4)
CC-HST-001920-011000
Power supply 24VDC/2A w/cable (EU/UK/US/AU)
CC-980-02-0000-00-01
Concens Free Downloadable software CAS
(Concens Actuator Studio)
conXion cable, 0,25 m
CC-875-01-0000-00-00
conXion cable, 1 m
CC-875-02-0000-00-00
conXion cable, 5 m
CC-875-03-0000-00-00
conXion cable, 10 m
CC-875-04-0000-00-00
conXion cable, 20 m
CC-875-05-0000-00-00
conXion Box+ with buttons In/Out
CC-971-05-0000-00-00
Other manuals for icon
3
Table of contents
Other Concens Controllers manuals
Popular Controllers manuals by other brands
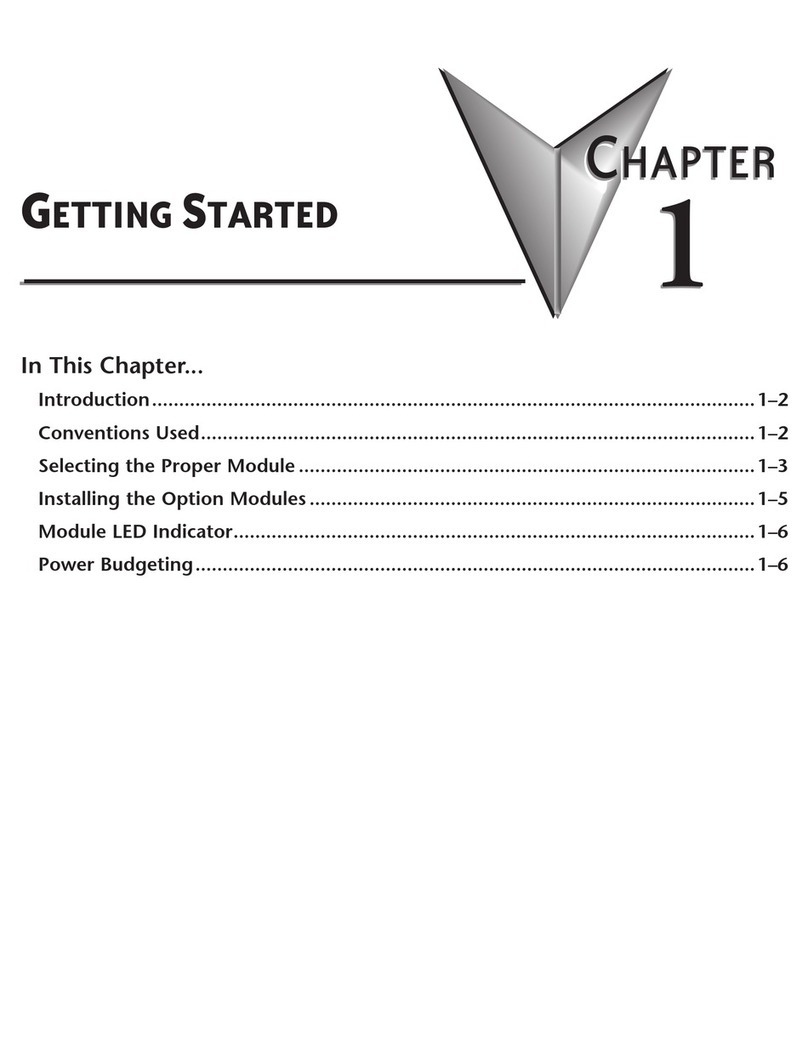
AutomationDirect
AutomationDirect DL05 Getting started

EP Solar
EP Solar eTracer Series instruction manual
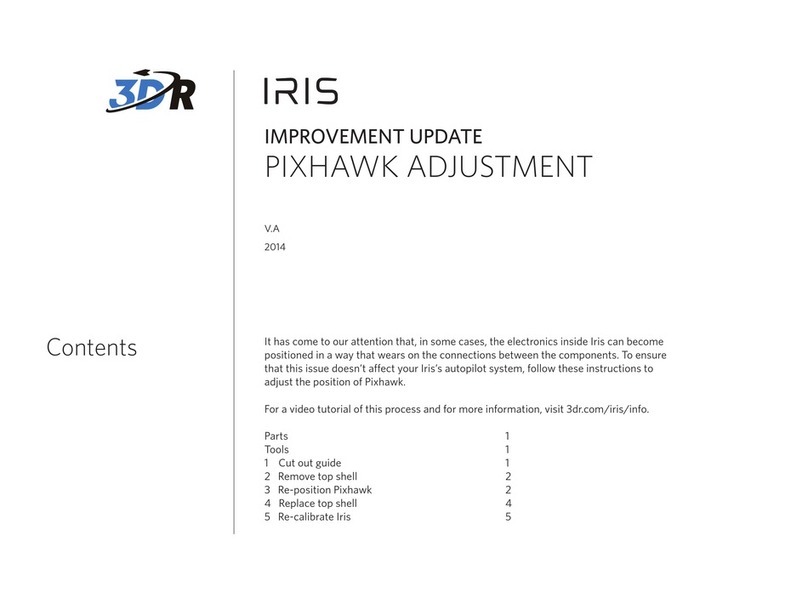
3D R
3D R IRIS PIXHAWK Mounting, Electrical Connection, Adjustment
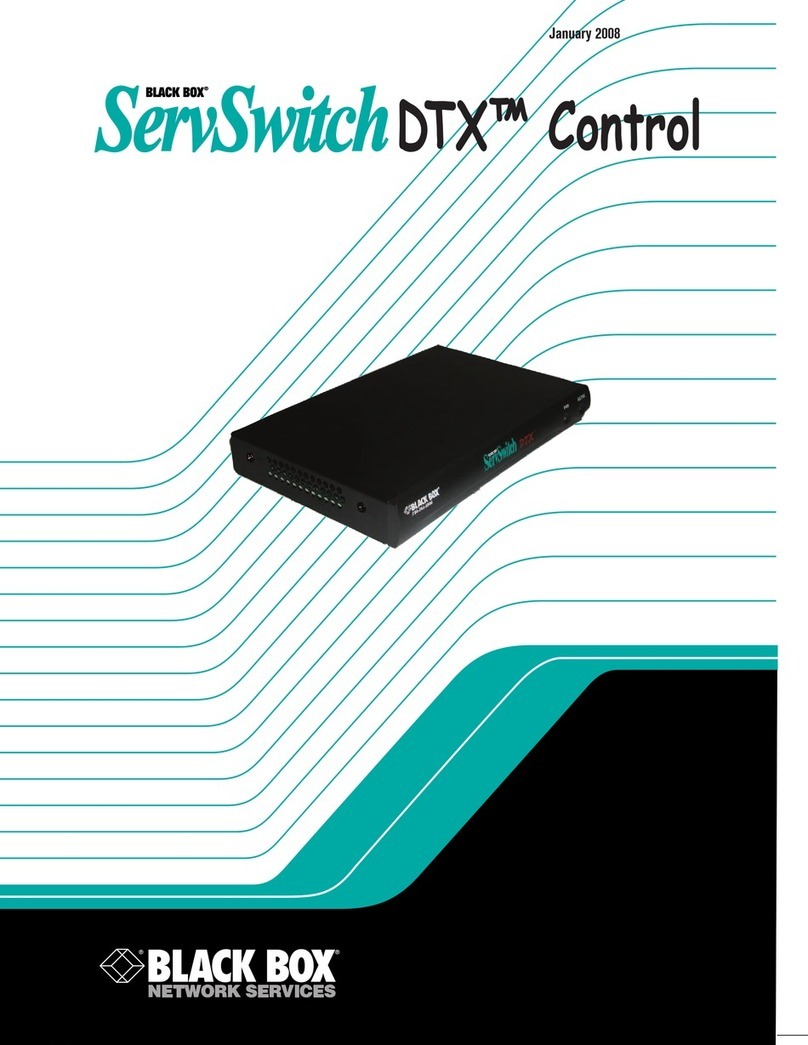
Black Box
Black Box servswitch DTX5000-CTL user guide

Welbilt
Welbilt Frymaster YUM WINGSTREET K3000 Operation manual
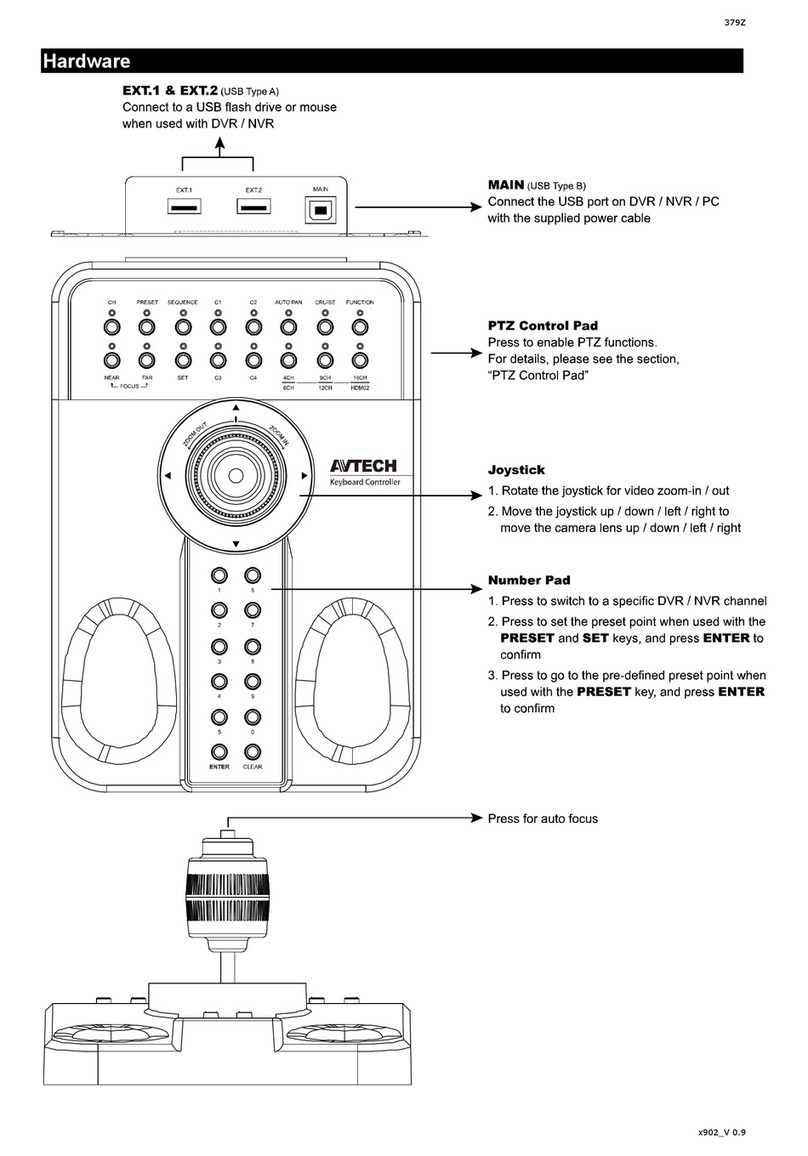
Avtech
Avtech AVX102 Hardware manual