Danfoss IPS 8 User manual

ir.danfoss.com
User Guide
Intelligent Purging System (IPS 8)
Ammonia, UL approved
230 V AC, 60 Hz. Field coils: 115 V AC 60 Hz
ir.danfoss.com148R9654
Other IPS 8 User Guide languages
Info for UK customers only
Danfoss Ltd. Oxford Road, UB9
4LH Denham, UK

User Guide |Intelligent Purging System (IPS 8) for Ammonia - Technical data, installation and use
2 | BC344024774466en-000201 © Danfoss | DCS (ms) | 2021.03
Legal notice...................................................................................................................................................................................................................3
Technical data..............................................................................................................................................................................................................4
Ordering..........................................................................................................................................................................................................................4
Introduction..................................................................................................................................................................................................................5
Features ...........................................................................................................................................................................................................................5
Working principle .....................................................................................................................................................................................................6
Working cycle ..............................................................................................................................................................................................................7
Air traps............................................................................................................................................................................................................................8
Connection locations..............................................................................................................................................................................................9
Connection points.................................................................................................................................................................................................11
Installation ..................................................................................................................................................................................................................12
Electrical wiring ......................................................................................................................................................................................................14
Light Indicators........................................................................................................................................................................................................19
Quick Startup ............................................................................................................................................................................................................20
Navigation - built in MCX controller..........................................................................................................................................................20
Configuring using the LCD...............................................................................................................................................................................21
Modbus RTU..............................................................................................................................................................................................................24
Maintenance/Service/Disposal......................................................................................................................................................................25
Contents

User Guide |Intelligent Purging System (IPS 8) for Ammonia - Technical data, installation and use
© Danfoss | DCS (ms) | 2021.03 BC344024774466en-000201 | 3
Legal notice This product information is a part of the documentation for the Danfoss scope of delivery and serves
as product presentation and customer advisory service. It contains important information and
technical data regarding the product.
This product information should be supplemented with the information about the industrial safety
and health related regulations at the site of installation of the product. The regulations vary from
place to place as a result of the statutory regulations applicable at the site of installation and are
therefore not considered in this product information.
In addition to this product information and the accident prevention regulations applicable for the
respective country and area where the product is used, the technical regulations for safe and
professional work must also be observed.
This product information has been written in good faith. However, Danfoss cannot be held responsible
for any errors that this document may contain or for their consequences.
Danfoss reserves the right to make technical changes during the course of further development of the
equipment covered by this product information.
Illustrations and drawings in this product information are simplified representations. As a result of
the improvements and changes, it is possible that the illustrations do not exactly match the current
development status. The technical data and dimensions are subject to change. No claims will be
accepted on the basis of them.

User Guide |Intelligent Purging System (IPS 8) for Ammonia - Technical data, installation and use
4 | BC344024774466en-000201 © Danfoss | DCS (ms) | 2021.03
Ordering Unit Code number
Danfoss Intelligent Purging System IPS 8 60Hz unit 084H5003
Accessories/Spare parts Accessory Spare part Code
Flange blind blank incl Bolts, nuts and Gaskets* x 084H5053
SV3 Float Valve x027B2023
ICF 15-4 solenoid, DIN Butt weld 15mm ½ inch x 027L4543
ICF 15-4 solenoid, ANSI Socket weld 15mm ½ inch x 027L4538
ICF 15-4 solenoid, ANSI Butt weld 15mm ½ inch x 027L4602
Welding Flange incl Bolts, nuts and Gaskets x 084H5061
Purger solenoid kit (Armature, tube, Sealing, Orifice, Filter insert) x 084H5051
Solenoid coil, 24V DC x x 018F6968
Coil 93 – 121 V AC, 60 Hz, 16 W/29 VA - for field purge solenoid valves x 018F6813
Coil 110 – 120 V AC, 60 Hz, 16 W - for field purge solenoid valves x 018F4112
Coil 110 – 120 V AC, 60 Hz, 16 W - for field purge solenoid valves x 018F4113
PSU, 24V DC - optional for powering purge points x x 080Z0055
Restrictor, purge line x084H5054
UL compressor Cranck case heater x084H5065
UL condenser coil assy incl screws x084H5066
UL fan motor for condenser Incl fan grid and screws x084H5060
UL extraction Fan x084H5062
UL Air grid with filter (1 piece) x084H5063
Pre-programmed MCX 15 x084H5052
Pressure transmitter evaporator, soldered (AKS 32R) x060G3552
Compressor including Start relay box and Start and Run Capacitor x104L2897
Compressor Hi-temp sensor x084N2003
Expansion valve, R452A x068U3881
Sight glass x014-0191
Pressure transmitter - R717, Threaded, AKS2050 x060G5750
Thermostat for crankcase heater control x060L111166
Temperature sensor - R717, AKS 21M x084N2003
Pressure switch for Fan x Contact Danfoss
Pressure safety switch x Contact Danfoss
* For closing system flange during system pressure testing
Technical data Supply voltage 230 V +/-10% AC, 1ph, 60Hz
Voltage range for field 1)connected solenoid coils: 115 V +/- 10% AC 60Hz
Maximum Current Rating of Overcurrent Protection (MOP) 15A
Minimum Circuit Ampacity (MCA) 6,85A
Power consumption max. 1.25 kW
Short-circuit current rating SCCR 18kA
Temperature range ambient -10 °C – 43 °C (14 °F – 109 °F)
Temperature range transport/storage -30 °C to +60 °C (-22 °F to 140 °F)
Enclosure - Electrical panel Type 12
Weight max. 125 kg (276 lbs)
Dimensions (LxWxH) 1051 x 441 x 703 mm (41.4 x 17.4 x 27.7 inches)
Purger refrigerant R452A 900 gram (31.7 oz)
Max. operating pressure (PS) R452A 28 bar (406 psi)
System refrigerant R717
Max. operating pressure R717 40 bar (580 psi)
Operating temperature R717 -40 °C to +60 °C (-40 °F to 140 °F)
Note:
All Spare part items are parts already built-in to
the IPS 8.
(084H5061, Welding Flange incl Bolts, nuts and
Gaskets are included with IPS 8, not built-in).
1)Field connected coils on Digital Output:
Accessory parts may possible be used at
installation along with the IPS 8.
Description Field connected valves
Q6, COM6, OUT6 YV ICFD Valve
Q7, COM7, OUT7 Y1 Valve
Q8, COM8, OUT8 Y2 Valve
Q9, COM9, OUT9 Y3 Valve
Q10, COM10, OUT10 Y4 Valve
Description Field connected valves
Q11, COM11, OUT11 Y5 Valve
Q12, COM12, OUT12 Y6 Valve
Q13, COM13, OUT13 Y7 Valve
Q14, COM14, OUT14 Y8 Valve

User Guide |Intelligent Purging System (IPS 8) for Ammonia - Technical data, installation and use
© Danfoss | DCS (ms) | 2021.03 BC344024774466en-000201 | 5
The Danfoss Intelligent Purging System (IPS 8)
is a stand-alone, self-contained purging unit
designed to remove non-condensable gases
(NC gases = air and other unwanted foreign
gases) from industrial ammonia refrigeration
systems.
The IPS control can handle up to 8 purge points
automatically.
The ingress of NC gases into a refrigeration
system is inevitable, regardless of the refrigerant,
pressures, or temperatures. NC gases in the
system will result in a decrease in system
efficiency, both in terms of an increase in power
consumption and reduced cooling capacity.
Due to having a different density than ammonia,
the ingressed air will accumulate in specific areas
of the system, where it can be removed using the
Danfoss IPS 8.
The accumulation areas are identified in the
Connection locations section, along with
recommended connection principles.
The purger unit is an electronically controlled,
self-contained R452A refrigerant system that runs
independent of the main ammonia system and
with only one flange connection to the ammonia
plant.
The flanged opening allows the ammonia gas/
NC gas mix access to the purger’s heat exchanger,
where it is split into ammonia condensate and NC
gases. The ammonia condensate is returned by
gravity to the main plant, while the NC gases are
purged to the atmosphere through e.g. a water
bath.
Through the flanged opening, the purger unit
has access to the parameters from the ammonia
plant required for full electronic control.
The unit runs automatically in 24-hour cycles,
checking for the presence of NC gases and, if
present, removes the NC gases.
To regain and retain the design capacity of the
main ammonia system and prevent future air
accumulation, it is highly recommended to install
the Danfoss IPS 8.
Introduction
Features • State-of-the-art electronically controlled unit
based on the Danfoss MCX controller platform
• Reduced power consumption of the ammonia
plant
• Automatic purging response to NC gases in the
refrigeration system
• Continuous and smart monitoring of
differential pressure between the system
refrigerant and the purger’s refrigerant
• Smart purging that minimizes refrigerant
(ammonia) release to the environment
• Self-contained unit operation, which functions
independently from the main plant
• An operation log for easy purging cycle data
monitoring
• Industry standard Modbus RTU
communication for remote monitoring and
system integration
• Reduced purging unit power consumption
compared to other units due to on-demand
operation only
• Self-diagnostics for both unit and system
operation to shut down in the event of
malfunctions
• Cost-effective installation with few mechanical
and electrical connections
• A fully brazed and leak-tested R452A cooling
system, minimizing leakage risks
• A plug-and-play stand-alone design, which
simplifies installation and commissioning while
reducing potential errors
• No need for advanced settings
• A compact and easy-to-handle design
• Danfoss patented design

User Guide |Intelligent Purging System (IPS 8) for Ammonia - Technical data, installation and use
6 | BC344024774466en-000201 © Danfoss | DCS (ms) | 2021.03
Working principle The Danfoss IPS 8 is factory-tested and ready to
use in ammonia plants with a condenser pressure
of more than 6,5 bar (94 psi). The purger is
charged with 900 gram (31.7 oz) of R452A.
Only 2 mechanical connections are needed for
the purger (see fig. 1). The flow of ammonia/NC
gases from the main plant is done through the
flange for ammonia (see 13 in Fig. 1 below), while
the NC gas purge is done through the blow-off
pipe after the purge restrictor (18).
Through the flange for ammonia (13), a mixture
of ammonia gas and NC gases enters the heat
exchanger (12) part of the purger.
The ammonia gas/NC gas mix is cooled down
below the condensing temperature of the
ammonia by the R452A circuit. At this point,
ammonia gas condenses and returns by gravity
to the ammonia plant whereas the NC gases
accumulate in the heat exchanger (12) for
subsequent purging.
By condensing the ammonia gas, a new
ammonia/NC gases mix is naturally pulled
through. This new mix is separated through a
continuous process.
As the NC gas concentration in the heat
exchanger (12) increases, the R452A heat
exchanger pressure and temperature will
simultaneously decrease.
The controller continuously monitors the R452A
heat exchanger pressure as well as ammonia
pressure and temperature. When the R452A
pressure reaches a predefined pressure difference
when compared with the ammonia pressure
(temperature) it prepares to purge the NC gases
through the solenoid valve (16). The blow-off
is activated by the solenoid (16) and through
appropriate piping/hosing, should be led into
a water bath. This process is recommended
to retain small amounts of ammonia (see
Installation section).
1 Compressor R452A 11 Expansion valve, R452A
1a Compressor Cranck case heater 12 Heat exchanger Ammonia/R452A
2 Thermostat for crankcase heater control 13 Welding Flange
3 Discharge temp sensor R452A 14 Pressure transmitter R452A
3a Suction temperature sensor R452A 15 Pressure transmitter R717
4 Pressure safety switch 16 Solenoid valve AKVA and coil
5 Condenser 17 NC temperature sensor
6 Extraction fan 18 Restrictor, purge line
7 Pressure switch for Fan 19 MCX 15 (Pre-programmed)
8 Receiver 20 PSU, 24V
9 Filter
10 Sight glass 21 Fusible plug (138 °C (280 °F))
Fig. 1 - Purger R452A lay-out
1
1a
2
3
4
5
7
8
9
21
10
11
15
16
17
18
13
12
14
6
19 20
3a

User Guide |Intelligent Purging System (IPS 8) for Ammonia - Technical data, installation and use
© Danfoss | DCS (ms) | 2021.03 BC344024774466en-000201 | 7
Working cycle The Danfoss IPS 8 operates in 24-hour cycles, of
which 45 minutes are dedicated to an R452A pull
down. At power on, the pull down is initiated
immediately. If no NC gases are detected during
the 45 minute pull down, the system will close
the solenoid valve at purge point 1 and open the
solenoid valve at point 2. After a cycle time of 24
hours/N (Number of purge points), the
compressor will pull down again condensing the
ammonia. After 24 hours, all purge points have
been vented one time.
To identify NC gases, the controller utilizes upper
and lower thresholds for R452A evaporating
temperature. If, during pull down, the
temperature continues decreasing and the lower
threshold is passed, the controller considers
this to be a high concentration of NC gases
and opens the purge solenoid valve. The purge
valve will stay open until sufficient condensing
ammonia is present to lift the R452A evaporating
temperature above the upper threshold.
The compressor will continue running and if the
temperature again decreases below the lower
threshold, a new purge will be performed. This
process will be repeated until the R452A heat
exchanger temperature stays above the lower
threshold for >45 minutes following the previous
closure of the purge valve.
Fig. 2 - Power on & Cycle at no NC gases present: CST (compressor start time) and PDT (pull down time) are configurable
* Cycle (CST) = 24 hours/N (number of purge points)
Cycle (CST) *
Purger Pull down
(PDT): 45 min
Cycle (CST) *
Purger Pull down
(PDT): 45 min
Time
Power on
Purger Pull down
(PDT): 45 min
On
Off
On
Off
Compressor
Purge valve
Fig. 3 - Purging procedure - Low R452A evap. temperature detected during PDT: Thresholds are configurable
* If low evaporator temperature is detected (passing lower threshold), the purging procedure will be repeated immediately
Time
On
Off
On
Off
Compressor
Purge valve
Evaporator Temp. (Tsat452)
Upper Threshold (VClseT)
Lower Threshold (VClseT)
Non condensables has been purged
- new cycle starts *

User Guide |Intelligent Purging System (IPS 8) for Ammonia - Technical data, installation and use
8 | BC344024774466en-000201 © Danfoss | DCS (ms) | 2021.03
Air traps
Fig. 4 Liquid level. Bottom connected receiver Fig. 5 Liquid level. Top connected receiver
For systems with low pressure liquid level control,
the correct condenser/ receiver installation is as
shown in Fig. 4 and Fig. 5.
The discharge gas from the compressor (1) is
led to the condenser (2) where it is condensed.
The receiver (3) holds the liquid until there is a
demand for liquid from the LP side, e.g., until the
expansion valve (4) opens. If the expansion valve
is closed, the liquid condensed in the condenser
will need to be stored in the receiver and the
level will increase. To ensure a free flow to the
receiver, the gas must be allowed to leave the
receiver; this process is accomplished through
the pressure equalizing line (a). The pressure
equalizing line makes the pressure in the receiver
the same as in the compressor discharge line.
The pressure in the condenser outlet is lower due
to the pressure loss in the condenser. Since the
condenser outlet pressure is lower than in the
receiver, it is therefore necessary to mount the
condenser higher than the receiver and allow for
a higher liquid level in the piping between the
condenser and the receiver (b).
The liquid column in the line (b) compensates for
the pressure difference between the condenser
outlet and the receiver.
Fig. 4 shows the liquid connection at the bottom
of the receiver.
If the liquid from the condenser is connected to
the top of the receiver (Fig. 5), a slightly different
arrangement must be made.
The liquid line (b) from the condenser to the
receiver will need to have a goose neck/liquid
trap to ensure that the liquid column is actually
established.
As air is heavier than ammonia gas, the air will
collect in two locations in this type of installation:
On top of the liquid in the receiver (x) and/or
on top of the liquid in the drop leg from the
condenser (y).

User Guide |Intelligent Purging System (IPS 8) for Ammonia - Technical data, installation and use
© Danfoss | DCS (ms) | 2021.03 BC344024774466en-000201 | 9
Connection locations
The correct locations for the air purger to be
connected to the ammonia plant are:
(See Fig. 6 and Fig. 7)
- on top of the receiver or
- on top of the liquid in the drop leg from the
condenser.
The air purger (5) is connected to the two purge
points through solenoid valves (px and py).
Note that only one solenoid should be open at
any given time, otherwise the liquid column in
the condenser will be short-circuited.
The air purger must have its own liquid return
drop leg (c) connected in parallel with the
condenser’s drop legs (b).
When the purger is connected to the receiver
i.e. solenoid (px) open, the liquid level in the air
purgers drop leg (c) will be equal to the receiver
liquid level (3); when the purger is connected to
the condenser outlet i.e. solenoid (py) open, the
liquid level will
be equal to the liquid level in the
condenser drop leg (b).
Fig. 6 Purger connections (px) & (py). Drain piping (c) must be vertical/downward slope
Air purger installation in a low-pressure liquid level controlled installation
Alternatively, the air purger draining of liquid can
be achieved effectively through an HP float valve
(6) to the low pressure side (see Fig. 7).
Fig. 7 Purger connections (px) & (py). Drain piping (c) must be vertical/downward slope

User Guide |Intelligent Purging System (IPS 8) for Ammonia - Technical data, installation and use
10 | BC344024774466en-000201 © Danfoss | DCS (ms) | 2021.03
Connection locations
(continued) For systems with a high-pressure liquid level
control, the air will collect in the float valve (3).
(See Fig. 8).
The compressor (1) supplies high-pressure gas to
the condenser (2), where it is condensed.
The float valve (3) will flash any liquid back to
the LP side. The air purger (5) must be connected
to the float valve through a solenoid valve (pv).
The ammonia liquid condensed in the air purger
must be drained through drain pipe (c) to the LP
side via a float valve (6).
Air purger installation in a high-pressure liquid level controlled installation
The air purger must always be mounted
above the highest liquid level to be able
to drain the ammonia condensed in it.
Otherwise, the air purger can flood and
potentially purge ammonia liquid.
The purger liquid return leg (c) must
always be mounted vertically or at
minimum, with a downward slope.
The solenoid valves at the connection
points must never be activated at the
same time. Finalize purging at one
location before switching to the next.
General
Fig. 8 Purger connections (pv). Drain Piping (c) must be vertical/downward slope
Follow the installation guide strictly during Purger installation.
Install the Purger unit in a location where the bottom flange level
and any gas inlet connection level is above any possible ammonia
liquid level.
Liquid drain piping from the purger must always have a
downward slope.
Install a shut off valve close to the bottom flange entrance
to enable removal of the unit and closing for high pressure
ammonia gas.
Connect proper resistant piping to the purging outlet pipe and
ensure the purged non-condensables are discharged into a water
bath of max. 200 liter.
Merci de suivre scrupuleusement le guide d’installation lors du
montage du Purger.
Installez le Purger à une hauteur où le niveau de la bride inférieure et
le niveau de tous raccords d’entrée de gaz sont supérieurs à tous les
niveaux d’ammoniac liquide.
La tuyauterie d’évacuation du liquide du purgeur doit toujours avoir
une pente descendante.
Installez une vanne d’arrêt près de l’entrée de la bride inférieure pour
permettre le démontage de l’unité et assure l’étanchéité du réseau
ammoniac haute pression.
Raccordez une tuyauterie de pression appropriée au tuyau de sortie
du purgeur et assurez-vous que les incondensables purgés sont
évacués dans récipient d’au moins 200 litres d’eau.
Cod. 99000572 Cod. 99000572
WARNING ! AVERTISSEMENT !

User Guide |Intelligent Purging System (IPS 8) for Ammonia - Technical data, installation and use
© Danfoss | DCS (ms) | 2021.03 BC344024774466en-000201 | 11
Connection points
Single point purging setup is possible (Fig. 9) i.e.
no solenoid valves with the Danfoss IPS 8 unit.
This kind of installation should be installed as
shown in Fig. 9 i.e. above the receiver or using a
float valve. (See section on connection locations).
For single point purging as in Fig. 9, the setting in
the MCX for the number of valves to‘0’or switch
off the multi-purging functionality in the general
setup (Parameter Name: Activate Multipurger).
As factory default, the Danfoss IPS 8 is configured
to handle 8 purge points (Fig. 10). The correct
amount of purge points connected needs to
be setup in the MCX controller after power-up.
Both power and control wiring of the installed
solenoid valves coils should take place prior to
first power up.
Multi-point purging
NEVER HAVE MORE THAN 1 PURGE POINT
OPEN AT A TIME.
Always close one purge valve before opening
the next.
This is done by turning the purger unit power
on (Parameter Name: Activate Multipurger) and
entering the number of actual purge points
in the program. See section“Programming/
configuration”.
Fig. 9 Single point purging from receiver Fig. 10 Multi-point purging from up to 8 purging points
Purge Points
- up to 8 points
ICF 15-4
Be aware of liquid traps
Where slope is
shown above, ensure
downward sloping
pipe flowing towards
purger drop leg.
NH₃ gas + NC gases
SVA
SNV
Liquid drain to Low
pressure side
Receiver
Ammonia Liquid
Ammonia Liquid
Ammonia gas + NC gases
NH₃ bypass for
draining purger
SVA
SNV
SNV
SV3
SVA

User Guide |Intelligent Purging System (IPS 8) for Ammonia - Technical data, installation and use
12 | BC344024774466en-000201 © Danfoss | DCS (ms) | 2021.03
.
21HL1 21HL2 21HL3
PURGING
Progeco srl
MODEL
WIRINGDIAGRAM
ELECTRICSUPPLY
FULLLOAD CURRENT
Industrialcontrol panel for general use
LARGESTMOTOR
FLA
LARGESTRESISTANCE
RLA
SCCRCURRENT
CONSTRUCTIONYEAR
ENCLOSURE
RATING
DANFOSSINTELLIGENT
PURGINGSYSTEM (IPS 8) – NAM
RIV19E01
1PH+ N/GRD
230V60Hz
6,2A
4,19A
0,24A
18kA
03/ 2020
TYPE12
ViaLaghi,Calcinelli (PU)
www.progecoautomazione.it
Installation
Lifting Procedure
The Danfoss IPS 8 must be installed in
accordance with locations recommended in the
Connection locations and Connection points
sections of this document.
The unit has a enclosure, Type 12 and must be
installed indoor only with ambient temperature
ranging from -10 °C to 43 °C / 14 °F to 109 °F).
Avoid installation in direct sunlight as this may
lead to excessive sunlight exposure and ambient
temperatures above allowed limits. For ambient
temperatures below -10 °C (14 °F) the air purger
must be installed in a heated and ventilated area.
The unit must be installed in a non-ATEX/Ex-zone
atmosphere as the purger unit is not explosion proof.
The purger unit should be kept in an upright
position at all times - from receipt to final
installation.
Use all 4 lifting eyes (Fig. 11) and suitable lifting
gear during installation. Weight of IPS: 125kg
(276 lbs).
Install the unit on an even horizontal base 0.05
to 1.1 meter (2 to 43 in) above a service platform
with sufficient support and allowing the purger
subframe to be bolted to the support (see
example in Fig. 12). Maintain recommended
distances in all directions (Fig. 12) to allow fan
cooling and servicing.
Always leave the unit off for at least 12 hours
from finished installation to first time power up.
Electrical work must comply to national
and local electrical codes.
It is important that the support
construction is level to ensure the
internal liquid trap is properly filled.
Angle to horizontal < 2 degrees
Fig. 11
Fig. 12 Installation dimensions
All 4 lifting eyes must be positioned correctly, to match the actual used lifting gear
All 4 lifting eyes must be used
* For easy access to the main switch
and servicing, the Purger unit shall be
installed between 0,05 to 1,1 m (2 to 43 in)
above service platform level.
Min. 300 mm Min. 900 mm
Observe:
IPS 8 must not be placed inside a closed
in-closure. At least two sides should
have no walls in front of IPS 8
A
A
1051 mm
703
Min. 900 mm Min. 500 mm
Purging pipe OD 17.2 mm
for rubber hose to water ba
th.
Do not unscrew restrictor
inside pipe. Risk of purging
high NH3 concentration.
32 mm
Min. 4 00 mm
1051 mm Min. 500 mmMin. 900 mm
Min. 400 mm
32 mm
Min. 300 mm
446 mm

User Guide |Intelligent Purging System (IPS 8) for Ammonia - Technical data, installation and use
© Danfoss | DCS (ms) | 2021.03 BC344024774466en-000201 | 13
Installation (continued)
Fig. 13 Ammonia connection
Fig. 14 Enclosed weld flange - See Danfoss Data sheet, -Spare
parts and accessories, - AI249786497379en-000601, page 10
1. Prepare the ammonia pipework with the weld
flange according to Fig. 13 and Fig. 14. The
main/drain piping should never be smaller
than inner diameter Ø37 mm (1.5 in).
2. Complete the supporting structure able to
carry 125 kg (276 lbs).
3. Lift the purger into position using the lifting
eyes on each side of the purger’s cabinet.
Remove the rubber plug from the flange
opening.
4. Connect the weld flange with the purger flange
using the enclosed flat gasket and tighten the
supplied 4 bolts diagonally to a torque of 60 Nm
(44.3 ft-lb).
5. Insert 4 bolts (not supplied) through the purger
frame and the support construction and tighten.
6. Perform a leak test to ensure an airtight
connection.
7. In the event the purger unit needs to be
dismantled please contact Danfoss for
instructions.
8. Correctly install a suitable pipe/hose from the
purge solenoid valve for blow-off of NC gases
in accordance with local or national
regulations.
Note: Prior to replacing the water in the
water tank ensure that the purger is
switched off and the shut off valve at the
flanged purger inlet is closed. Leave the
unit in this condition for a period to allow
the remaining gas in the piping to be
dissolved/released.
Watch out for bubbles.
Establish a procedure for regular
checking the pH level and bubble
pattern.
If continuous bubbles are observed
in the
water tank during‘‘stand by” (Green light
indicator) in normal operation, one or
more of the purge solenoid valves needs
repair or replacement.
9. Prepare an outside water tank with a maximum
of 200 liters (53 gal.) and ensure the piping
allows the purged gas to be immersed in the
water.
10.Regularly check the pH level of the tank’s
contents.
11.The pH level should never exceed 12.6.
Otherwise the water content must be renewed.
12.Dispose of concentrated waste water in
accordance
with to local/national regulations.
Enclosed gasket
Flange for NH₃ connection. Remove rubber plug
Enclosed bolts, Torque: 60 Nm
(44.3 ft lb) diagonal tension
Purging pipe OD 17.2 for rubber hose to water bath
Do not unscrew restrictor inside pipe.
Risk of purging high NH₃ concentration
Enclosed weld flange (fig. 14)
547
8 x 11 mm (hole) 274
416,4
198
310
155

User Guide |Intelligent Purging System (IPS 8) for Ammonia - Technical data, installation and use
14 | BC344024774466en-000201 © Danfoss | DCS (ms) | 2021.03
Electrical wiring
The internal wiring of the purger is done at the
factory. Only the electrical wiring for the main
power supply, the purge point solenoids and
optional bus communication needs wiring on site.
Electrical panel can only be opened at key unlock and with the main switch off.
Note: Authorized personel only
Fig. 15 Controller box external
Fig. 16 Controller box internal
Rigid metal conduits SHALL be used, according
to NEC.
Key Lock
ON/OFF Switch
21HL1 21HL2 21HL3
PURGING
Progeco srl
MODEL
WIRING DIAGRAM
ELECTRIC SUPPLY
FULL LOAD CURRENT
Industrial control panel for general use
LARGEST MOTOR
FLA
LARGEST RESISTANCE
RLA
SCCR CURRENT
CONSTRUCTION YEAR
ENCLOSURE
RATING
DANFOSSINTELLIGENT
PURGINGSYSTEM (IPS 8) – NAM
RIV19E01
1PH + N/GRD
230V 60Hz
6,2A
4,19A
0,24A
18kA
03 / 2020
TYPE 12
ViaLaghi, Calcinelli (PU)
www.progecoautomazione.it
14GD1
Danfoss
080Z0055
16D0
Danfoss
MCX15B
Piastra - Plate
Retroportella - Rear of the door
25 x 100
FISSAGGIO SU PIASTRA RETROPORTELLA
FIXING ON THE REAR DOOR PLATE
ST1
M12
ST2
M12
ST3
M12
BPL
M16
BPH
M16
YV1
M16
TR
M16
M2
M16
LLS
M16
PPH
M16
PSH
M16
VR1
M16
RC
M16
M1
M16
INGRESSO CAVI DA IMPIANTO VERSO QUADRO ELETTRICO
CABLE INPUT FROM PLANT TO ELECTRIC PANEL
25 x 60
25 x 60
12QF4
14QF5
11FR1 11FR2 11FR3
15KM4
21KM1 21KM2 21KM3
GUAINA LOGICA
LOGIC SHRINK
SUPPLY LINE
230V 60Hz 1PH +N
ATTENTION, VOLTAGE PRESENCE
230V 60Hz 1PH +N
L1 / N1 / GRD
GR1
M12
GR2
M12
40 x 100
GUAINA SONDE
PROBE SHRINK
10QF0
11QF1 11QF2 11QF3
XM3
14QF6
14QF8
14T1
GUAINA POTENZA
POWER SHRINK
0-230
0-110
XM0
XM1
XM2
XM4
Observe:
- All wiring must comply with local and national regulations.
- Power connection wire recommendation: Minimum 75 °C (167 °F) rate copper wire.

User Guide |Intelligent Purging System (IPS 8) for Ammonia - Technical data, installation and use
© Danfoss | DCS (ms) | 2021.03 BC344024774466en-000201 | 15
Electrical wiring
(continued)
M1
COMPRESSOR
M2
CONDENSER FAN
VR1
AIR EXTRACTION FAN
21KM1 21KM2 21KM3
Field Installed
Use Copper Conductors Only 75°
11FR1 11FR311FR2
Terminal block
torque 0,5-0,6 Nm
11QF311QF211QF1
Terminal Block For Field Installed
Calibrate aux.cont.
OF-OF
Calibrate aux.cont.
OF-OF
Calibrate aux.cont.
OF-OF
Fig. 17
Fig. 18
10GRD
Main protection shall be provided in
the field, use Fuse 16A CC Fast or
Circuit Breaker C16A
Use Copper Conductors Only 75°
Terminal Block For Field Installed
Torque 0,5-0,6 Nm
Field Installed
Insulate conductors in heat shrink tubing with signaling
10QF0
Electric Panel
TERRE IMPIANTO
SYSTEM SIDE
LATO IMPIANTO
SYSTEM SIDE
PIASTRA FRONTALE
FRONTAL PLATE
PORTA QUADRO
PANEL DOOR
CARPENTERIA QUADRO
PANEL CARPENTRY
PIASTRA QUADRO
PANEL PLATE

User Guide |Intelligent Purging System (IPS 8) for Ammonia - Technical data, installation and use
16 | BC344024774466en-000201 © Danfoss | DCS (ms) | 2021.03
Electrical wiring
(continued)
Fig. 19
Fig. 20
RC
CRANKCASE HEATER
Field Installed
Use Copper Conductors Only 75°
Terminal block
torque 0,5-0,6 Nm
15KM4
12QF4
Terminal Block For Field Installed
14QF7
14QF5 14QF6
14GD1
14T1
14QF8

User Guide |Intelligent Purging System (IPS 8) for Ammonia - Technical data, installation and use
© Danfoss | DCS (ms) | 2021.03 BC344024774466en-000201 | 17
Electrical wiring
(continued)
PPH
FAN PRESSURE SWITCH
Field Installed
16D0 16D0
Q1
START MOTORS
16D0
Q2
SOLENOID VALVE
16D0
Q3
STANDBY SYSTEM
16D0
Q4
RUN SYSTEM
16D0
Q5
ERROR SYSTEM
16D0
Q6
SOLENOID VALVE
16D0
Q7
SOLENOID VALVE
16D0
Q8
SOLENOID VALVE
16D0
Q9
SOLENOID VALVE
PSH
HIGH PRESSURE
Field Installed
YV1
Field Installed
YVICFED
Field Installed
Y1 Y2 Y3
Use Copper Conductors Onl
y
75°
Terminal block
torque 0,5-0,6 Nm
Terminal Block For Field
Installed
SOLENOID VALVE
Q14
16D0
ALARM
Q15
16D0
Y4
Field Installed
Y5 Y6 Y7 Y8
Use Copper
Conductors Only
75°
Terminal block
torque 0,5-0,6 Nm
Terminal Block For
Field Installed
SOLENOID VALVE
Q13
16D0
SOLENOID VALVE
Q12
16D0
SOLENOID VALVE
Q11
16D0
SOLENOID VALVE
Q10
16D0
Fig. 21
Fig. 22

User Guide |Intelligent Purging System (IPS 8) for Ammonia - Technical data, installation and use
18 | BC344024774466en-000201 © Danfoss | DCS (ms) | 2021.03
Electrical wiring
(continued)
16D0
I1
AIR COMPRESSOR
ON RUN
16D0 16D0
I3
MOTORS FAULT
16D0 16D0
I2
SYSTEM OFF
16D0 16D0
I4
AVAILABLE
16D016D0 16D0 16D016D0
11FR1 11FR2 11FR3
11QF1 11QF2 11QF3
OF OF OF
Field Installed
Use Copper Conductors Only 75°
Terminal block
torque 0,5-0,6 Nm
Terminal Block For Field Installed
16D0
I5
AVAILABLE
16D0
I6
AVAILABLE
16D0
I7
AVAILABLE
16D0
I8
AVAILABLE
16D0
I9
AVAILABLE
16D0
I10
AVAILABLE
16D0
I11
AVAILABLE
16D0
I12
AVAILABLE
16D0 16D0
16D0
I13
AVAILABLE
16D0
I14
AVAILABLE
16D0
I15
AVAILABLE
16D0
I16
AVAILABLE
16D016D0 16D0
I18
AVAILABLE
16D0
I17
AVAILABLE
16D0
Fig. 23
Fig. 24

User Guide |Intelligent Purging System (IPS 8) for Ammonia - Technical data, installation and use
© Danfoss | DCS (ms) | 2021.03 BC344024774466en-000201 | 19
Fig. 25
Lights ON Status Compressor
ON
Compressor
OFF
Purge Valve
ON
Purge Valve
OFF Alarm
Green Stand by x x
Yellow Run x x
Green & Yellow Purging x x
Green & Yellow
& Red
Uninterupted Long time
purging (> 150 h) x x*
Red Occurs when: Check list
of alarms description (x**) x** x
* The purger continuous purging until max running period (default 160 h) is reached and the purger compressor will stop
** The purger compressor stops when alarm occurs
Light Indicators
21HL1 21HL2 21HL3
PURGING
Progeco srl
MODEL
WIRING DIAGRAM
ELECTRIC SUPPLY
FULL LOAD CURRENT
Industrial control panel for general use
LARGEST MOTOR
FLA
LARGEST RESISTANCE
RLA
SCCR CURRENT
CONSTRUCTION YEAR
ENCLOSURE
RATING
DANFOSS INTELLIGENT
PURGING SYSTEM (IPS 8) – NAM
RIV19E01
1PH + N/GRD
230V 60Hz
6,2A
4,19A
0,24A
18kA
03 / 2020
TYPE 12
Via Laghi, Calcinelli (PU)
www.progecoautomazione.it
21HL1 21HL2 21HL3
PURGING

User Guide |Intelligent Purging System (IPS 8) for Ammonia - Technical data, installation and use
20 | BC344024774466en-000201 © Danfoss | DCS (ms) | 2021.03
Navigation - built in MCX
controller
(Placed at the rear of the front
panel door)
Quick Startup
After switching on the controller, a display
window will momentarily show the actual
software version, followed by the default main
operating window shown in Fig. 26.
While in operation mode, the Up/Down arrow
buttons lead the user to the status windows
described in Table 01 below.
Fig. 26 - Default main window. Operating (start) mode. (Examples only)
Table 01 - Status windows
Purge Point percentage Distribution of the actual purging on the various purge points
Dis. temp. Actual R452A discharge temperature (°C)
Main Window default See above
Cycle info Acc. time Purge valve open (h)
Past events Last 7 purging events (min)
For the fastest possible system configuration after connecting all purge points to the IPS and following
first power up of the IPS, follow these simple instructions:
1. Navigate from the Main Menu to Login
2. Enter password '200'.
3. Choose 'Parameters'.
4. Choose 'Unit Config'
5. Choose 'Valve Settings'
6. Enter the amount of purge solenoid valves connected to the IPS.
R717 low Pres limit
Actual R717 Pres
Actual R452A Pres
Upper Threshold for Purge Valv
e
Lower Threshold for Purge Valv
e
Actual R452A Temp
Compressor on Error/Alarm Purge valve open Purge point (1-8)
Main screen, current informaon on IPS status
Status of purging process and purging counters
Log of purging events
Informaon on Purge points acvity
Temperature and superheat status
Esc
.
Up
Down Enter
Not
Used
Other manuals for IPS 8
5
This manual suits for next models
1
Table of contents
Other Danfoss Water Filtration System manuals
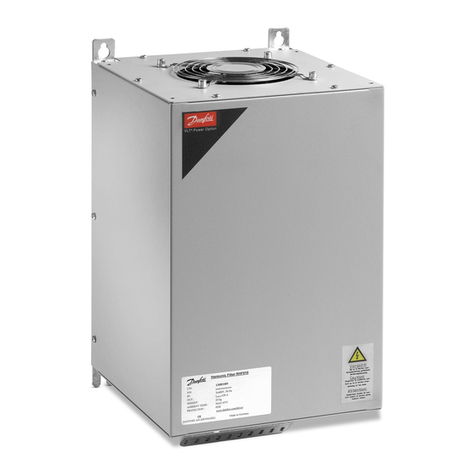
Danfoss
Danfoss AHF 010 Guide
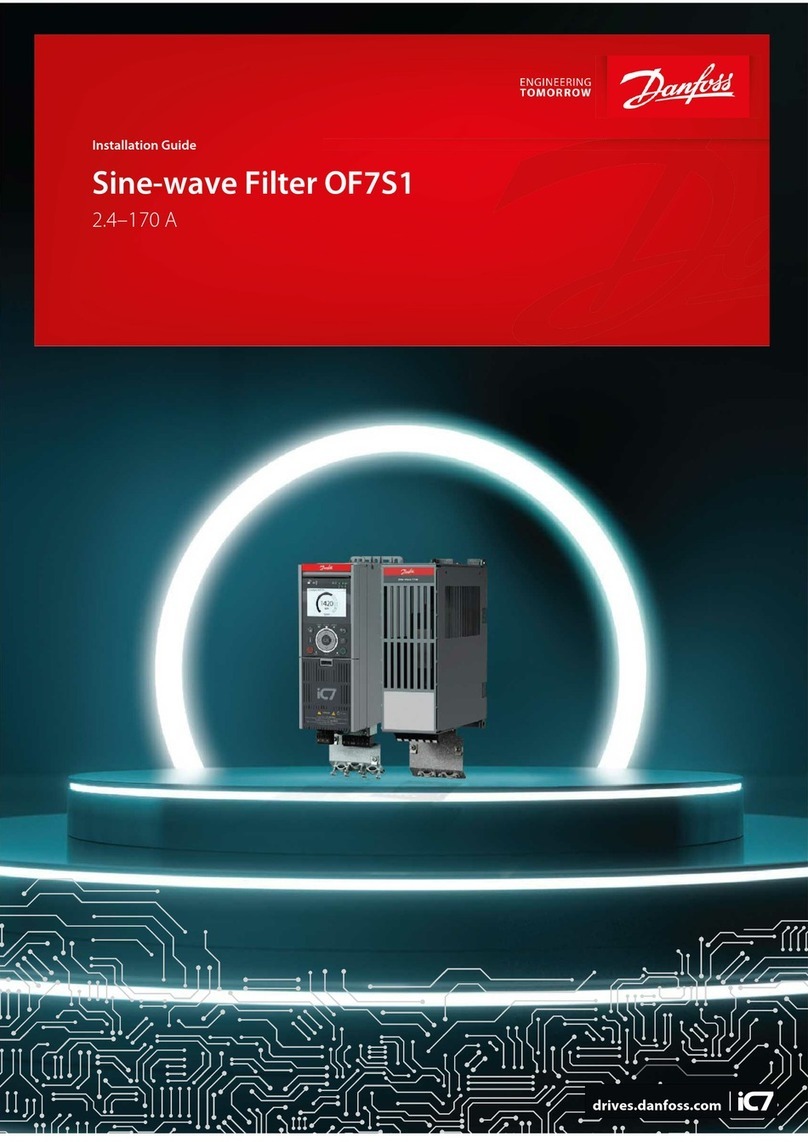
Danfoss
Danfoss OF7S1 User manual
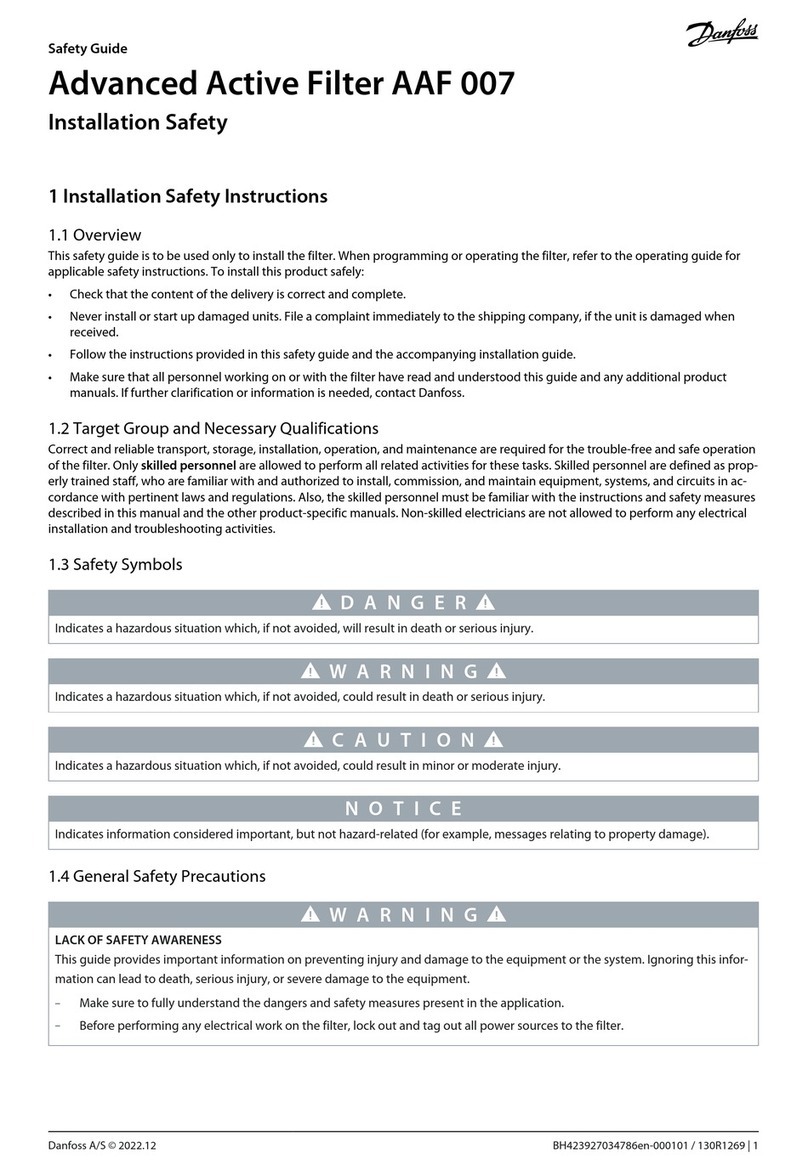
Danfoss
Danfoss AAF 007 Installation and operating manual
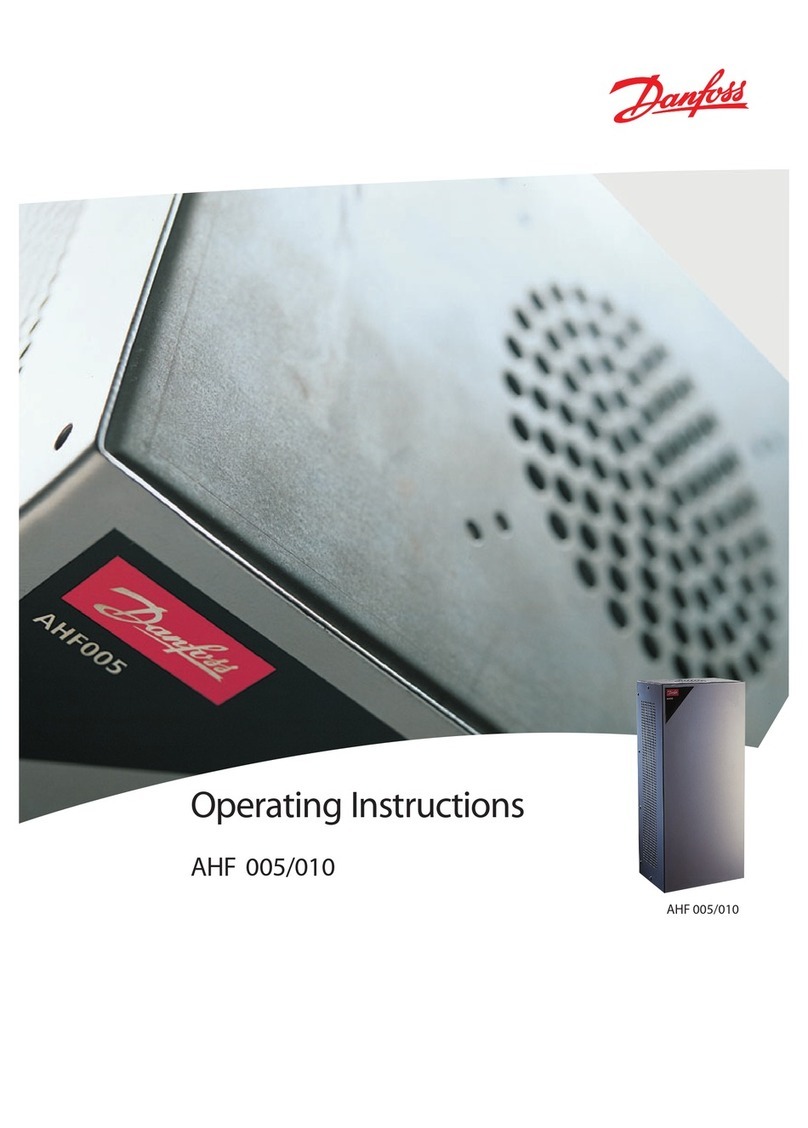
Danfoss
Danfoss VLT AHF 005 User manual
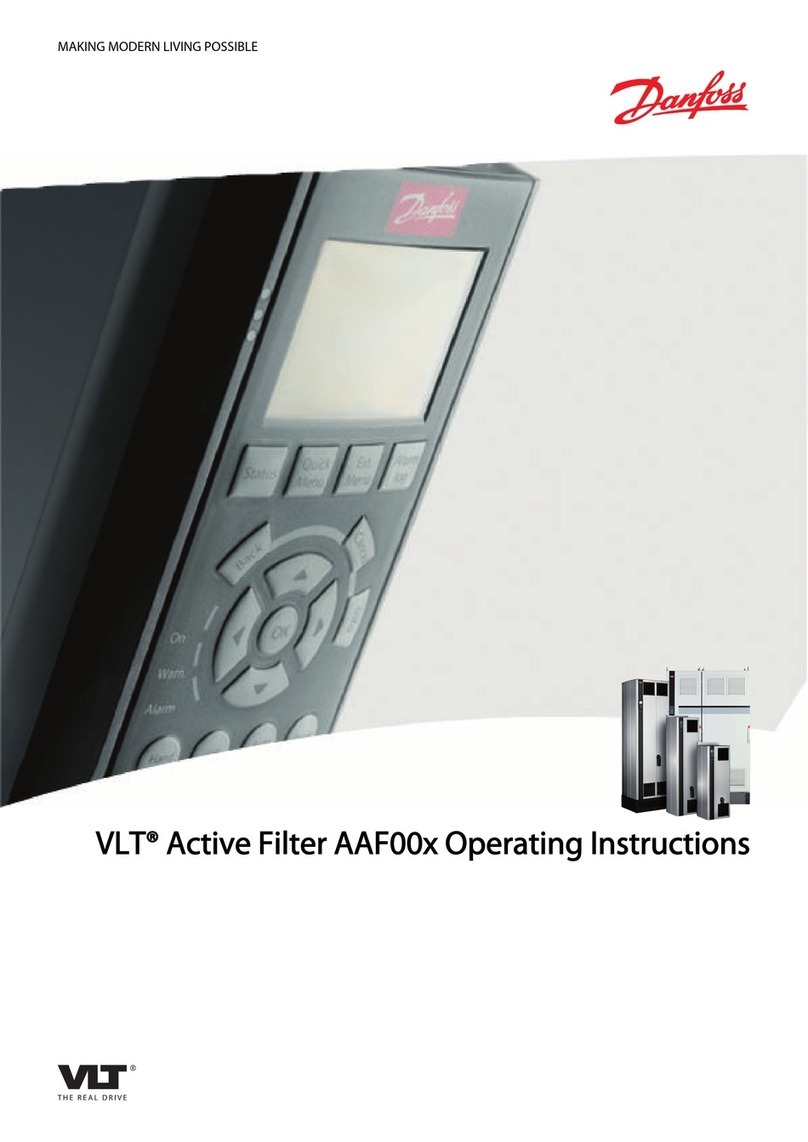
Danfoss
Danfoss VLT AAF00x User manual
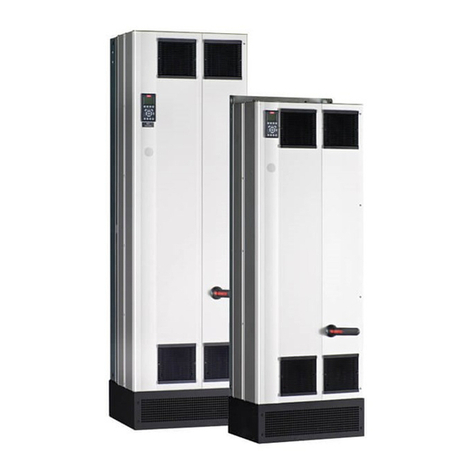
Danfoss
Danfoss VLT AAF006 User manual
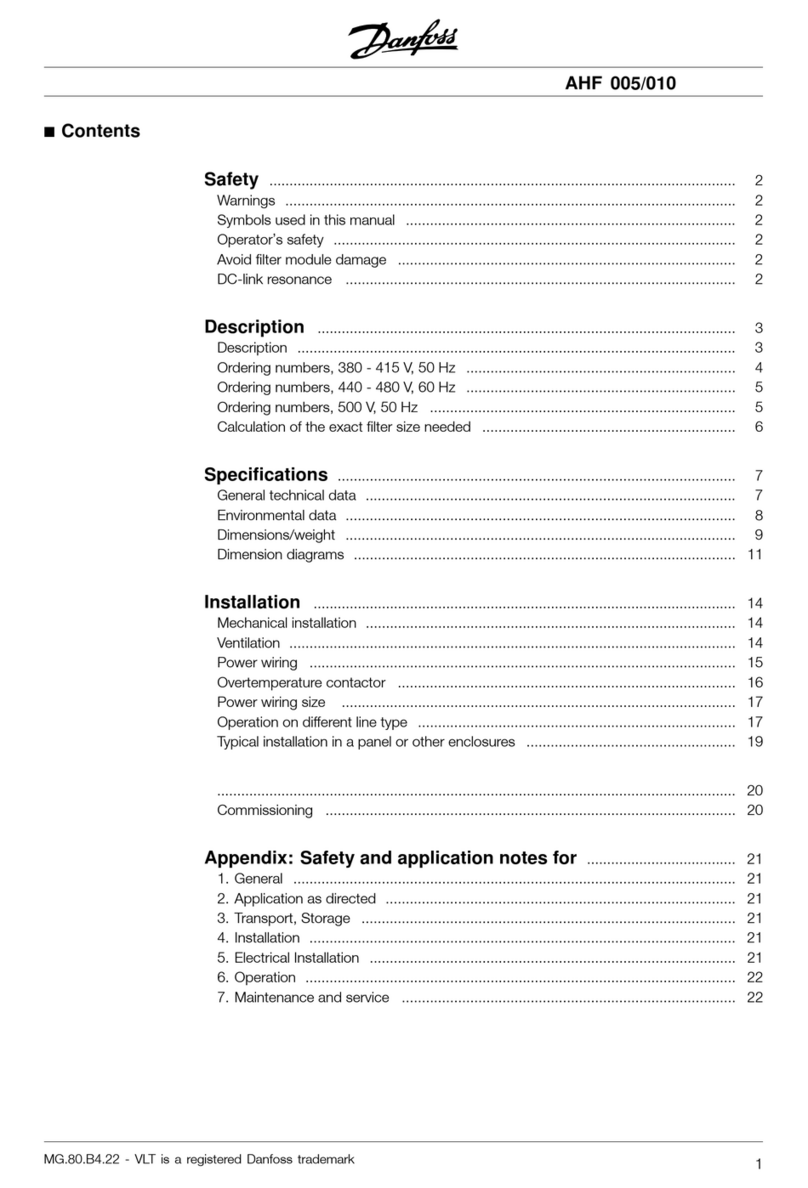
Danfoss
Danfoss AHF 005 User manual
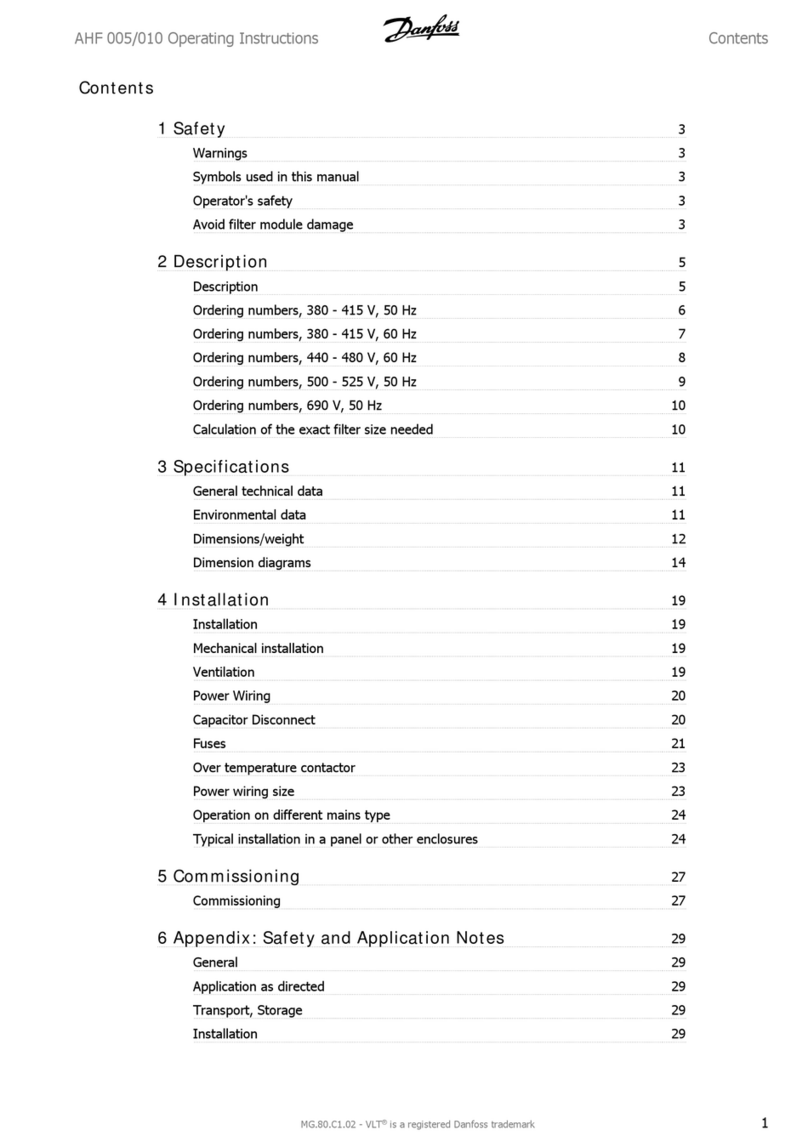
Danfoss
Danfoss AHF 005 User manual
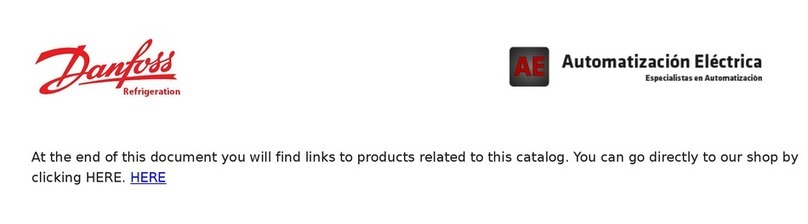
Danfoss
Danfoss VLT AAF006 User manual
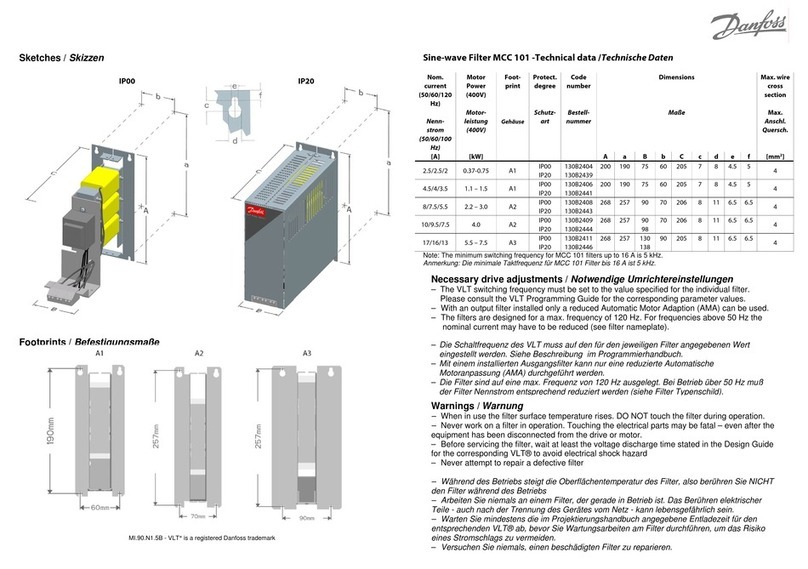
Danfoss
Danfoss 130B2404 Instruction sheet