Danfysik 81083852 User manual

MANUAL FOR
CONTROL MODULE
SMT Version
Part No.: 81083852
Prepared By Approved by
Name P.A.Elkiær
Date 09 FebruarY 2009
Signature
M A N U A L
SMT CONTROL MODULE
SYSTEM 8500
DANFYSIK A/S !DK - 4040 Jyllinge !Denmark !Tel.: +45 46 79 00 00 !Fax.: +45 46 79 00 01 !www.danfysik.com

Revision History log.
REV. By Approved Date Description Page’s
1.0 P.A.E. 27 Apr. 2000 Initial version 92
1.1 PAE 14 Jun 2000 SW Commands updated 78
1.2 PAE 22 Jun 2000 SW version SCS104 81
1.3
1.4
PAE 21Jun 2001 SW version SCS107
Updated print layout
44
Without SW
1.5 PAE 08 Feb 2002 SW version SCS108
Updated print layout
45
Without SW
1.6 PAE 07 Oct 2002 SW version SCS109 47
Without SW
1.7 PAE 08 Dec 2003 SW version SCS110
(RS485 & Always answer)
48
Without SW
1.8 PAE 14 Aug 2008 SW version SCS113
(ON/OFF control & Auto Slew Rate
option)
50
2.0 PAE 09 Feb 2009 SW version SCS114
(Auto slew rate, Two level set, limit)
52
2.1 PAE 17 May 2011 Some spelling mistake corrected 52
2.2 PAE 28 Apr 2011 Plug signal description removed
New Logo and address
52
IMPORTANT!
This documentation contains information which
is the property of DANFYSIK A/S, Denmark.
It is submitted to you in confidence that it will not
be disclosed or transmitted to others without
DANFYSIK’s authorization.

SERVICE
1
MAGNET POWER SUPPLY SYSTEM 8500
Table of contents.
Please note: Manuals for all the system 8000 power supplies are automati-
cally generated. This means that chapters may be omitted if not applicable.
Page.
1 Warranty and warranty repair.. . . . . . . . . . . . . . . . . . . . . . . . . . . . . . . . . . . . . . . . . . . 2
2. Unpacking and installation.. . . . . . . . . . . . . . . . . . . . . . . . . . . . . . . . . . . . . . . . . . . . . 3
2.1. Receivingthegoods.. ................................................. 3
2.2. Instructions for unpacking... . . . . . . . . . . . . . . . . . . . . . . . . . . . . . . . . . . . . . . . . . . . . 3
3.3. Operating by RS 232-C, RS422 or RS 485 I/O.. . . . . . . . . . . . . . . . . . . . . . . . . . . . . . 4
3.3.1. SettinguptheMPS.................................................... 4
3.3.2. Datacommunication.................................................. 19
3.3.3. Programming........................................................ 20
3.3.4. Software Profile Programming.. . . . . . . . . . . . . . . . . . . . . . . . . . . . . . . . . . . . . . . . . 22
3.3.5. Twolevelvalueset................................................... 27
3.3.5.1 Using the two level function.. . . . . . . . . . . . . . . . . . . . . . . . . . . . . . . . . . . . . . . . . . . 28
3.3.6. SWCommands.. .................................................... 29
4. Theoryofoperation................................................... 32
4.2. ControlBoard....................................................... 32
4.2.1. ì-Processor:........................................................ 32
4.2.2. Realtimeclock:..................................................... 33
4.2.3. SerialCommunication:................................................ 33
4.2.4. Parallel Communication:. . . . . . . . . . . . . . . . . . . . . . . . . . . . . . . . . . . . . . . . . . . . . . 34
4.2.5. Interlock, status and OF/OFF control:. . . . . . . . . . . . . . . . . . . . . . . . . . . . . . . . . . . . 34
4.2.6. DACcontrol:. ...................................................... 35
4.2.7. Analogmeasurements:................................................ 36
4.2.8. Motherboard:....................................................... 38
4.2.9. Water Flow measurement:. . . . . . . . . . . . . . . . . . . . . . . . . . . . . . . . . . . . . . . . . . . . . 38
4.2.10. LED indications on the board:. . . . . . . . . . . . . . . . . . . . . . . . . . . . . . . . . . . . . . . . . . 38
4.2.11.Polarityreversal..................................................... 39
4.2.12. Setting up the board parameters:. . . . . . . . . . . . . . . . . . . . . . . . . . . . . . . . . . . . . . . . 39
4.2.13. Interface specification:. . . . . . . . . . . . . . . . . . . . . . . . . . . . . . . . . . . . . . . . . . . . . . . . 41
8 Drawings........................................................... 42
10. PartsLists.. ........................................................ 42
DANFYSIK A/S - DK 2630 TAASTRUP - DENMARK. DOC NO P800000B

SERVICE
2
MAGNET POWER SUPPLY SYSTEM 8500
1 Warranty and warranty repair.
DANFYSIK A/S warrants that the products manufactured by us will be free from defects in material
and workmanship, that adversely would effect the normal functioning of the unit, for a period of 18
months from the date of shipment or 12 months from the date of installation whichever occurs first.
The exeptions to this are:
a) Parts not manufactured by DANFYSIK A/S which are covered by the original
equipment manufacturer's warranty.
b) Repair work which is warranted for six (6) months from the date of shipment from the
DANFYSIK works.
DANFYSIK A/S will repair or replace either on site or at the factory, at option and without charge,
any equipment which proves to be defective within it's warranty period.
In the case of warranty, DANFYSIK A/S will pay or reimburse lowest freight rate (two-way) of any
item returned to DANFYSIK or our designated agent/representative, provided that prior written
authorization for such return has been given by DANFYSIK A/S.
This warranty shall not apply to any equipment which have become defective or unworkable due to
mishandling, improper maintenance, incorrect use, radiation damage or any other circumstance not
generally acceptable for equipment of a similar type.
On standard products, DANFYSIK A/S reserves the right to make changes in design without
incurring any obligation to modify previously manufactured units.
The foregoing is the full extent of this warranty, and no other warranty is expressed or implied. In
no event shall Danfysik be liable for special damages arising from the delivery, late delivery or use
of the equipment.
If any fault develops, the following steps should be taken.
Notify DANFYSIK A/S, giving full details of the problems, and include Model-Type and Serial
number.
On receipt of these information, DANFYSIK A/S will give you either service information or
instructions for shipping.
All shipments of DANFYSIK equipment should be made according to our instructions and shipped
in the original or a similar container.
For smaller parts a carton will be sufficient, if the parts are wrapped in plastic or paper and
surrounded with at least 10 centimetres of shock-absorbing material.
DANFYSIK A/S - DK 2630 TAASTRUP - DENMARK. DOC NO P801030C

SERVICE
3
MAGNET POWER SUPPLY SYSTEM 8500
2. Unpacking and installation.
2.1. Receiving the goods.
The Shipping package should be thoroughly inspected for signs of obvious physical damage
immediately upon receipt.
All materials in the container should be checked against the enclosed packing list.
DANFYSIK A/S will not be responsible for shortages against the packing list unless notified
immediately.
2.2. Instructions for unpacking.
The electronic modules contains sensitive components that may be damage by electrostatic discharge
or wrong handling. Please handle with care and leave the modules inside the anti static bags as long
as possible.
If the modules are damaged in any way, a claim should be filed with the shipping agent, and a full
report of the damage should be forwarded to DANFYSIK A/S or our local agent/representative
immediately.
Upon receipt of this report, you will be issued instructions for the repair, replacement or return
shipment.
Please include the Model no, Type no, Serial no, and Order no for the Power Supply on any
communication with DANFYSIK A/S or our representative.
DANFYSIK A/S - DK 2630 TAASTRUP - DENMARK. DOC NO P802010B

SERVICE
4
MAGNET POWER SUPPLY SYSTEM 8500
SW2
position
Number
Parameter
0 {0000} Parking position
1 {0001} REM_UART_SETUP
2 {0010} REM_LINE_SETUP
3 {0011} REM_ADR_SETUP
4 {0100} LOC_UART_SETUP
5 {0101} LOC_LINE_SETUP
6 {0110} LOC_ADR_SETUP
7 {0111} COLD_BOOT_SETUP
8 {1000} AUX_SETUP_1
9 {1001} POWER_ON_PULSE
10 {1010} AUXILIARY_1_ON_PULSE
11 {1011} AUXILIARY_2_ON_PULSE
12 {1100} POLARITY_DELAY_PULSE
13 {1101} AUX_SETUP 2
14 {1110} AD_AUTO_SCALE
15 {1111} DA_AUTO_SCALE
3.3. Operating by RS 232-C, RS422 or RS 485 I/O.
The Control-Module uses standard serial interfaces compatible with many computers, PC and
terminals.
Two data communication lines are available:
- A REMOTE LINE, with either RS 232C, RS422 or RS 485 communication.
- A LOCAL LINE, with either RS 232C, RS422 or RS 485 communication.
The two channels are galvanically isolated from all other internal voltages through opto couplers but
are supplied from the same voltage source.
3.3.1. Setting up the MPS.
The set up of the MPS is done by two dip switches SW1 and SW2 together with the push button S2
(SETUP), or through SW commands. Please refer to the “ESC” commands in the SW appendix
chapter for further information.
The two dip switches are configured as a multi func-
tion port, that will be validated by the CPU upon
pressing the button S2.
The four levers on SW2 instruct which parameter to set
up, and the eight levers on SW1 deliver the value for
the selected parameter.
A parameter is saved and acknowledged when pressing
the SETUP switch S2.
The SW2 switch position can also be seen as a binary
number. The following table to the right shows the
SW2 number position and which parameters it con-
trols.
Leaving all levers in the OFF position (parking posi-
tion) will disable the SETUP switch, and thereby
prevent any accidental setup modification. All switches
should therefor be left in the OFF position.
If one of the setup modes are selected, the yellow LED
to the left of the switch “LD18" will light up indicat-
ing, that setup port is activated. The eight green LEDs
to the left of SW1 will show the present setup of the
selected parameter. Changing SW1 has no immediate
effect. Pressing S2 will save the settings, and the green
LEDs will then take the same indication as SW1.
DANFYSIK A/S - DK 2630 TAASTRUP - DENMARK. DOC NO P80303Sk

SERVICE
5
MAGNET POWER SUPPLY SYSTEM 8500
Be aware when changing the Baud rates. Wrong setting may cause communication loss. Modifying
a baud rate with the HW switches will alter the baud rate right away, whereas modifying the baud
rate through the appropriate SW command, will first take place after a reset.
Reverting all set ups to the factory default can be accomplished as follows.
Short circuit ST60 (just below SW2). Press at the same time S2 continuously. All green
parameter LEDs will start flashing. After the fifth flash, the default parameters will be
restored. Please note that all parameters will be restored, also any selected addresses and the
ON pulse width. The last one may cause the power supply to be unable to be turned ON.
For switch settings, the following terminology will be used:
DANFYSIK A/S - DK 2630 TAASTRUP - DENMARK. DOC NO P80303Sk

SERVICE
6
MAGNET POWER SUPPLY SYSTEM 8500
UART HW SET UP.
In the “UART HW SETUP” mode the baud rate and associated parameters for the serial lines can
be set.
SW2 selects which line to set up.
Hint: Selecting SW2 will immediately display the present setting on the green LEDs left to SW1.
Parameters
Default setting after “COLD BOOT”
Local Line: 9600Baud, No party, 8 Bits, 2 Stop bits
Remote Line: 9600Baud, No party, 8 Bits, 1 Stop bits
DANFYSIK A/S - DK 2630 TAASTRUP - DENMARK. DOC NO P80303Sk

SERVICE
7
MAGNET POWER SUPPLY SYSTEM 8500
ADDRESS LINE SET UP.
When using the RS422 or RS485 standard for the serial communication Remote or Local, it is
possible to attach a specific address to the line for multi drop connection.
The LOCAL line addressing can be used for controlling more power supplies through one M-Panel.
(SW nr. 4 in the M-PANEL must be ON). Earthing problems has to be taken into consideration to
avoid communication problems due to noise and high differential voltages that may jam the input
signals.
The REMOTE line addressing can be used for controlling more power supplies through one serial
line (one PC). Earthing problems has to be taken into consideration to avoid communication
problems due to noise and high differential voltages that may jam the input signals.
Parameters.
Default setting after “COLD BOOT”
Local Line: Address 0
Remote Line: Address 0
DANFYSIK A/S - DK 2630 TAASTRUP - DENMARK. DOC NO P80303Sk

SERVICE
8
MAGNET POWER SUPPLY SYSTEM 8500
LINE FUNCTION PROTOCOL SETUP.
The “LINE FUNCTION PROTOCOL SETUP” is for setting up serial line protocols.
Following settings are only available from SW version SCS110
Parameters:
Dedefault setting after “COLD BOOT”
v
Remote Line: RS485 Communication: Disabled
(=0) RS485 Line turn around time: 0 Line turn around set bit 0
RS485 Line turn around time: 1 Line turn around set bit 1
OK Answer mode: Disabled
BOOT character: "FF" / "R"
NU Disabled
XON/XOFF Protocol: Disabled
NU Disabled
Local Line: RS485 Communication: Disabled
(=1) RS485 Line turn around time: 0 Line turn around set bit 0
RS485 Line turn around time: 1 Line turn around set bit 1
OK Answer mode: Disabled
BOOT character: "FF" / "R"
NU Disabled
XON/XOFF Protocol: Disabled
NU Disabled
Line turn around set bit: 2, 3: 0, 0 Delay = 0
2, 3: 0, 1 Delay = time to transmit 2 dummy characters
2, 3: 1, 0 Delay = time to transmit 4 dummy characters
2, 3: 1, 1 Delay = time to transmit 8 dummy characters
DANFYSIK A/S - DK 2630 TAASTRUP - DENMARK. DOC NO P80303Sk

SERVICE
9
MAGNET POWER SUPPLY SYSTEM 8500
COLD BOOT SETUP.
After power up or reset, the power supply can wake up in different control conditions. The below
shown switch settings describe the possible Wake up conditions.
Parameters:
Default setting after “COLD BOOT”
Remote addressing: Disabled
Local addressing: Disabled
Default line in: Local
Remote Auto answer: Disabled
Error response: “?”-BELL only
Wake up output current: 0% [From SW version SCS109]
DANFYSIK A/S - DK 2630 TAASTRUP - DENMARK. DOC NO P80303Sk

SERVICE
10
MAGNET POWER SUPPLY SYSTEM 8500
AUXILIARY SETUP 1.
Special options can be initiated with the auxiliary switch set up 1.
Setting of bit 16 and 17 is intended for Offset DAC use. That is a 16 bit setting between 88 and 96%
(Bit16=0 & BIT 17=1) or between 92% and 100% output current (Bit16=1 & BIT 17=1).
For linear DAC settings, please set bit 16 & 17 to transparent mode.
Using the “WA” command a leading zeroes or trailing zeroes input format can be chosen.
- For leading zeroes: “WA 123" equals “WA 000123"
- For trailing zeroes: “WA 123" equals “WA 123000"
Parameters:
Default setting after “COLD BOOT”
DAC 16 & 17: Transparent
Interlock clear: OFF & CLEAR resets interlocks
“WA” Zeroes: WA command uses trailing zeroes.
UNI/BI-Polar DAC: UNIPOLAR (From SW version SCS108)
If a CAMAC Control Module is not inserted at slot P3 (Pin P3.A32 pulled low), the DAC port may
be configured as an output by setting lever 6 to ON. This enables either the DAC bits to be analysed
or to be connected to another power supply in a parallel tracking mode (the second supply must be
configured for CAMAC control). Default setting is disabled, that is High impedance.
DANFYSIK A/S - DK 2630 TAASTRUP - DENMARK. DOC NO P80303Sk

SERVICE
11
MAGNET POWER SUPPLY SYSTEM 8500
ON PULSE TIME SETUP.
Some power supplies requires a longer ON pulse for latching ON. This due to the extended charging
time when containing large capacitor banks. (Typical for switch mode supplies)
Parameters
Default setting after “COLD BOOT”
ON time: 0.5 seconds
DANFYSIK A/S - DK 2630 TAASTRUP - DENMARK. DOC NO P80303Sk

SERVICE
12
MAGNET POWER SUPPLY SYSTEM 8500
AUXILIARY OUTPUT-1 ON PULSE TIME SETUP.
The Auxiliary output line 1 can be programmed to produce a pulse or a static level output, software
command N1, F1. Below are the settings for this Auxiliary line
Parameters
Default setting after “COLD BOOT”
Static level operation
DANFYSIK A/S - DK 2630 TAASTRUP - DENMARK. DOC NO P80303Sk

SERVICE
13
MAGNET POWER SUPPLY SYSTEM 8500
AUXILIARY OUTPUT-2 ON PULSE TIME SETUP.
From SW version SCS108
As an option, can the polarity switch control line can be used as an auxiliary output line 2 exact in
the same way as for the auxiliary -1 line(see previous page).
To disable the polarity sequence and to use the output port as an auxiliary output line, a new software
configuration must be given. This can only be done by authorised Danfysik service personnel.
If enabled the Auxiliary-2 output line can be programmed to produce a pulse or a static level output,
software commend N2, F2. Below are the settings for this Auxiliary line
Parameters
Default setting after “COLD BOOT”
Disabled auxiliary-2 option (enabled polarity change over sequence).
DANFYSIK A/S - DK 2630 TAASTRUP - DENMARK. DOC NO P80303Sk

SERVICE
14
MAGNET POWER SUPPLY SYSTEM 8500
POLARITY DELAY TIME SETUP.
From SW version SCS108
A time delay can be inserted between the OFF state and the activation of the polarity change over
switch. The range of the time delay can be set from 0 to 25.5 seconds, this for letting the rest energy
in the magnet to decay.
The time delay is only inserted, if the power supply was ON before invoking the POL +/- command.
That is, when just changing the polarity in the power OFF mode, no time delay will be inserted.
Parameters
Default setting after “COLD BOOT”
No polarity delay.
DANFYSIK A/S - DK 2630 TAASTRUP - DENMARK. DOC NO P80303Sk

SERVICE
15
MAGNET POWER SUPPLY SYSTEM 8500
AUXILIARY SETUP 2.
From SW version SCS109
Special options can be initiated with the auxiliary switch set up 2.
(Enhancement of AUXILIARY SETUP 1)
Parameters:
Default setting after “COLD BOOT”
ADC multiplication: +1
Polarity status signals Normal.
CAMAC ON/OFF Control CAMAC. - From SW version SCC112
Auto slew rate shape Cosine. - From SW version SCC113
Lever 1 will negate all current read back readings. This is useful when connected to a regulation loop
that requires a positive signal feed back (negative signal feed back is normal for System 8500).
Lever 2 will inverse the status bits coming from the output polarity switch. If you encounter that the
polarity sign is shown inversed on older systems, then this switch corrects the problem.
Lever 3 determines who controls the ON/OFF/RESET line when the CAMAC bit is active (custom
interface plugged into P3 and pulling pin C32 low).
Lever 4 determines the shape of Auto Slew Rate function.
DANFYSIK A/S - DK 2630 TAASTRUP - DENMARK. DOC NO P80303Sk

SERVICE
16
MAGNET POWER SUPPLY SYSTEM 8500
AD AUTO ADJUSTMENT (Gain & Offset).
From SW version SCS104
The scaling factors for the AD channels can automatically be adjusted with this setting.
Parameters
OFFSET adjustment.
The OFFSET adjustment can automatically be executed if the value lies between 0 and 255 of the
AD channel resolution.
To activate the automatic OFFSET adjustment following steps must be performed:
- Select SW2 as above. “setting number14"
- Select the desired channel number “lever 1 to 5" on SW1
- Set lever 8 on SW1 to OFF (The SW1 LEDs will display the present Offset value)
- Ensure that the AD input signal is set to zero. Grounded or turned OFF in any way.
- Press the Setup Button
- To restore the Offset value to default factory setting (Zero), please set lever 7 to one before
pressing the Setup Button.
DANFYSIK A/S - DK 2630 TAASTRUP - DENMARK. DOC NO P80303Sk

SERVICE
17
MAGNET POWER SUPPLY SYSTEM 8500
GAIN adjustment.
From SW version SCS104
The GAIN adjustment can automatically adjust the scaling factor of the selected channel to only
nines. That is eg. 99999 for the 16 bit output current reading. This adjustment is only useful for the
output current and voltage read back (CH0, CH2, CH8, CH11 and CH12) Please do not use this
feature if the output reading is in Volts and Amps and for not applicable channels.
To auto adjust to a specific value, please use the “Esc”ADSET command.
To activate the automatic GAIN adjustment following steps must be performed:
- Select SW2 as above. “setting number14"
- Select the desired channel number “lever 1 to 5" on SW1
- Set lever 8 on SW1 to ON
- Ensure that the AD input signal is set to 100%
- Press the Setup Button
- To restore the Gain value to default factory setting , please set lever 7 to one before pressing
the Setup Button.
DA AUTO ADJUSTMENT (Gain & Offset).
The scaling factors for the DA channels can automatically be adjusted with this setting. This feature
is specially designed for “non calibrated” DACs as for the 855 DAC.
Parameters
DANFYSIK A/S - DK 2630 TAASTRUP - DENMARK. DOC NO P80303Sk

SERVICE
18
MAGNET POWER SUPPLY SYSTEM 8500
OFFSET adjustment.
The OFFSET adjustment can automatically be executed if the value lies between 0 and 255.
To activate the automatic OFFSET adjustment following steps must be performed:
- Select SW2 as above. “setting number15"
- Select the desired channel number “lever 1 to 5" on SW1
- Set lever 8 on SW1 to OFF and lever 7 to OFF (The SW1 LEDs will display the present Offset
value)
- Set the AD channel value (WA for “DA 0") to a value that gives a zero output.
- Press the Setup Button. A given “DA 0 0" or “WA 0” will now produce a zero output at the
DA channel. Due to the unipolar operation of the DACs only positive offset values can be
added.
- To restore the Offset value to default factory setting (Zero), please set lever 7 to one before
pressing the Setup Button.
GAIN adjustment.
The GAIN adjustment can automatically adjust the scaling factor of the selected channel to only
nines. That is eg. 999999 for the WA command.
To auto adjust to a specific value, please use the “Esc”DASET command. (DAC setting in Amps)
To activate the automatic GAIN adjustment following steps must be performed:
- Select SW2 as above. “setting number15"
- Select the desired channel number “lever 1 to 5" on SW1
- Set on SW1 lever 8 to ON and lever 7 to OFF.
- Set the output signal to 100% with the DA or the WA command
- Press the Setup Button.
- To restore the Gain value to default factory setting , please set lever 7 to one before pressing
the Setup Button.
Ps. For Bipolar DAC operations, the Gain adjustment can only be performed at +100%
DANFYSIK A/S - DK 2630 TAASTRUP - DENMARK. DOC NO P80303Sk
Table of contents
Other Danfysik Control System manuals
Popular Control System manuals by other brands
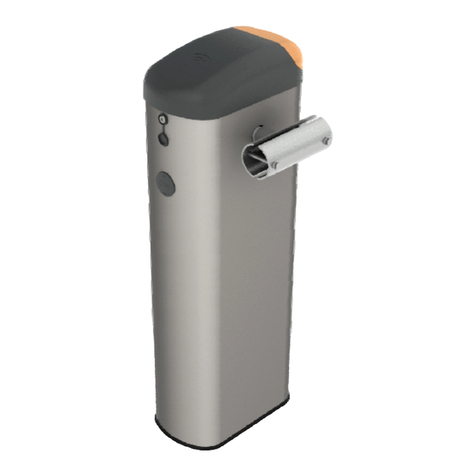
Leb Electronics
Leb Electronics SHUT Instructions for installation, use and maintenance

Phason
Phason AutoFlex Connect II installation guide
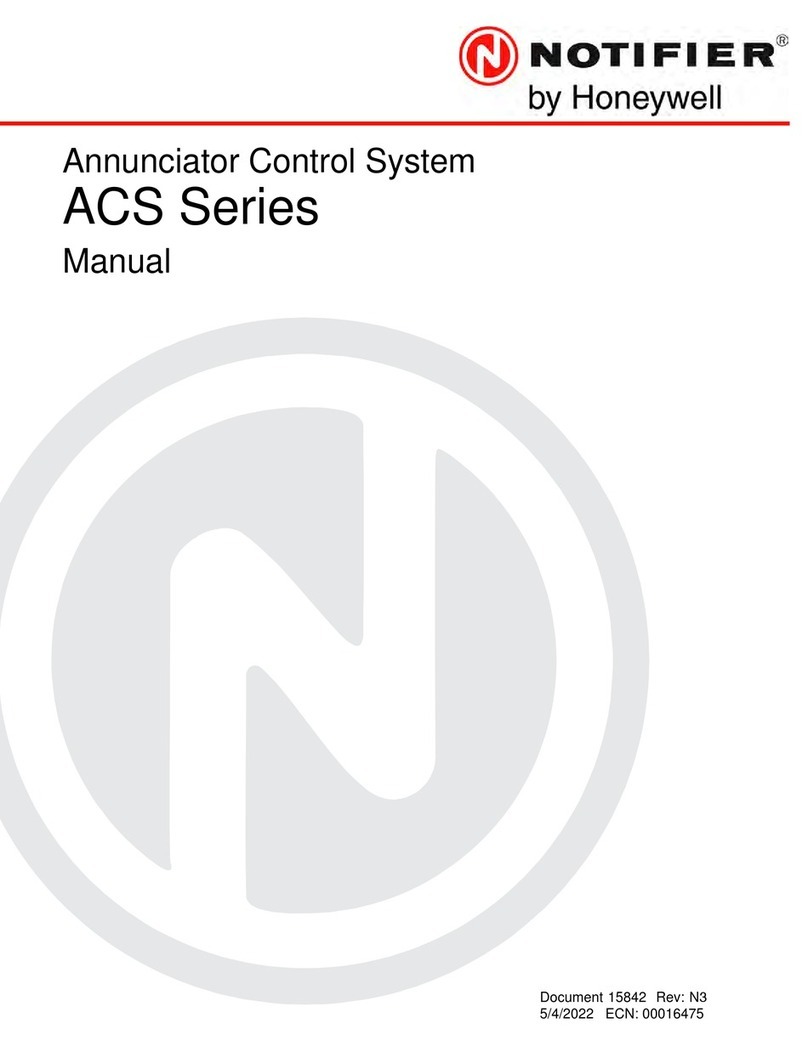
Honeywell
Honeywell NOTIFIER ACS Series manual
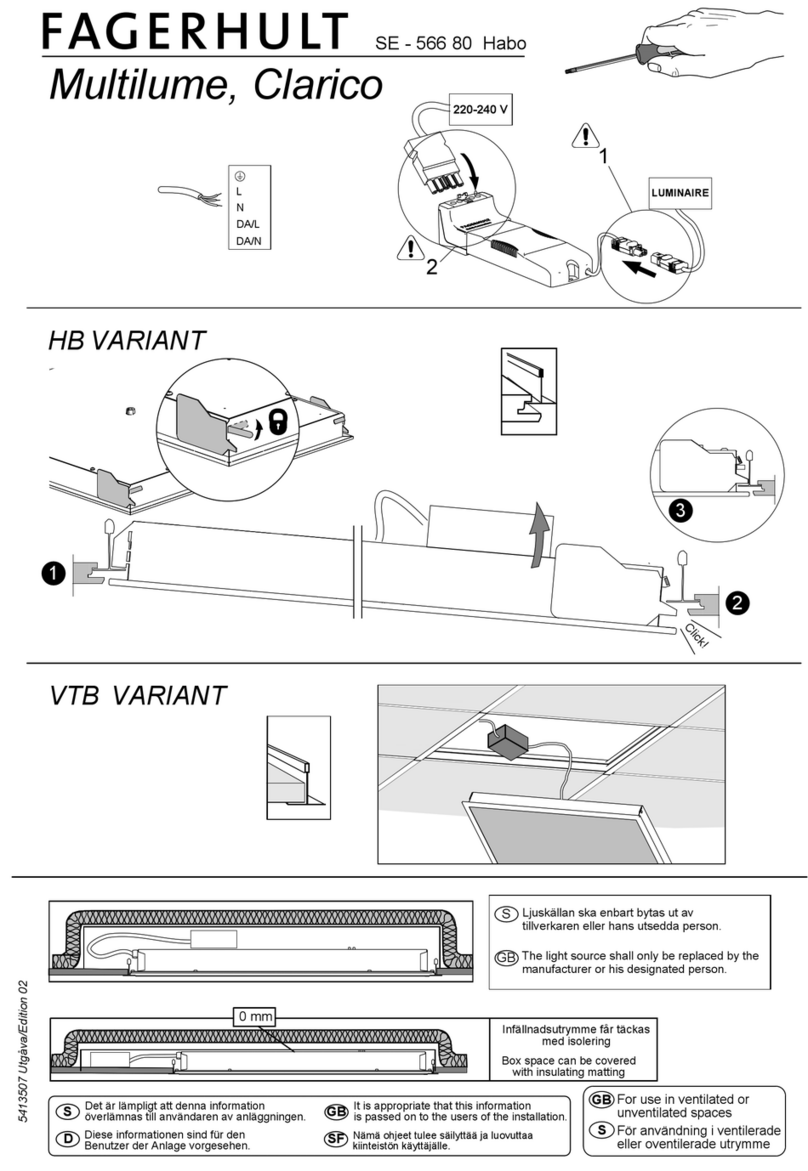
Fagerhult
Fagerhult SE - 566 80 Habo quick start guide
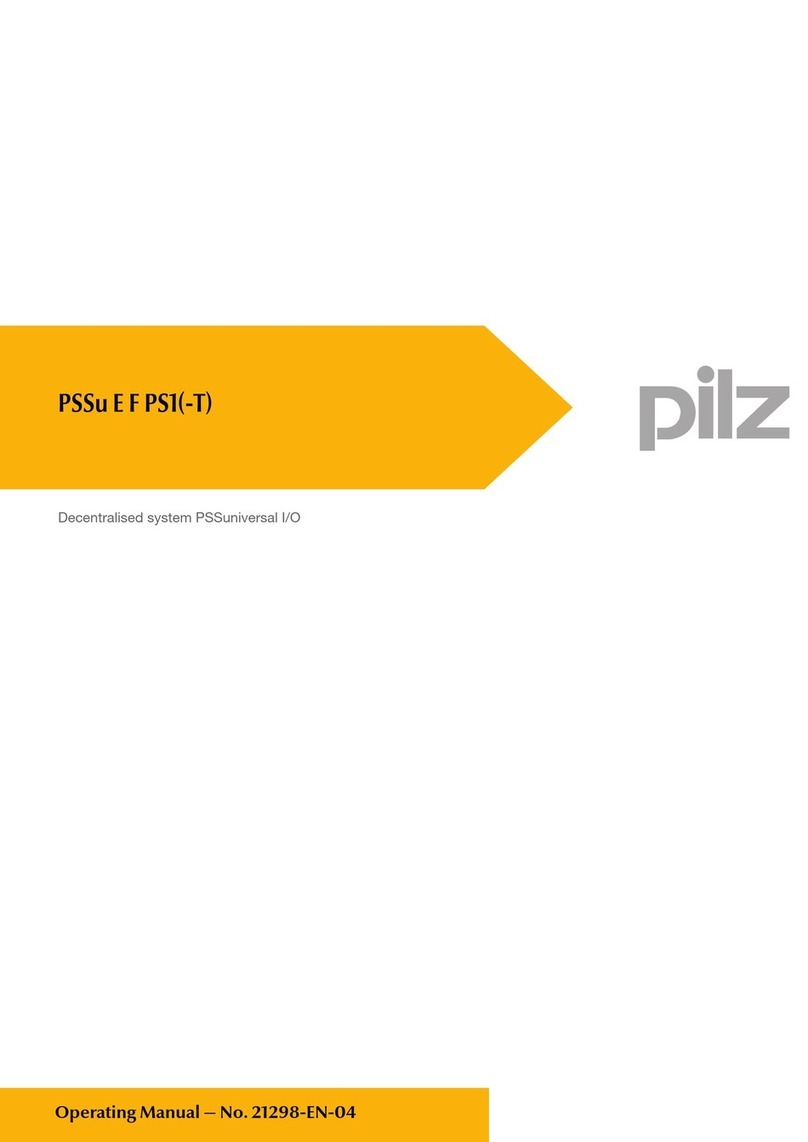
Pilz
Pilz PSSu E F PS1 operating manual
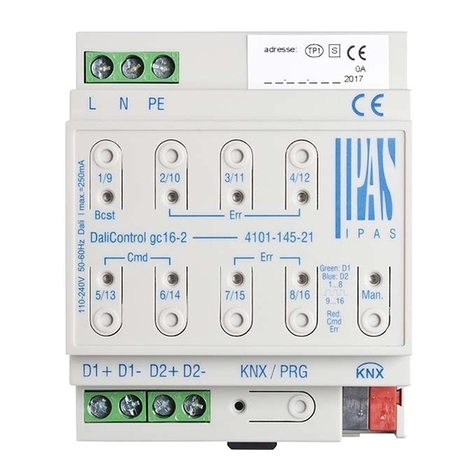
IPAS
IPAS DALI Series Operating and mounting instructions