Igema SMLC2 User manual

Edition 12/2020
D-08-B-51037-EN-00
INSTALLATION AND OPERATING INSTRUCTIONS
SMLC2
for use with the level probe: EL030 or EL19-2
or the multirodprobes EL963 and MS015A/B
SIL 3
Low water level limiter

2
Product philosophy
Thank you for placing your trust in IGEMA and deciding in favour of one of our
high-quality products.
For more than 100 years, measuring and control systems have been developed,
produced and sold worldwide under the IGEMA brand name.
“Steam is our passion” and we offer you the entire programme for the safe and
economic operation of your plants, especially in the steam and condensate sector.
We take care of the modernisation of steam boilers equipped with sophisticated
mechanical technology as well as new plants operated with innovative and future-
oriented electronic solutions.
Please read the installation and operating instructions carefully to ensure a safe and
reliable operation.
In addition to the information on installation and operation, you will also find important
information on maintenance, care, safety and value retention of your measuring and
control system.

3
Table of contents
1. Important safety instructions.............................................................................5
1.1 Symbols used in these instructions...................................................................5
1.2 Intended use of the device................................................................................6
1.3 Safety at work ...................................................................................................7
1.4 Safety instructions for this device......................................................................8
1.5 Exclusion of liability...........................................................................................8
2. Contents of packing............................................................................................9
3. Use in compliance with regulations ..................................................................9
4. System description...........................................................................................10
4.1 Function..........................................................................................................10
4.2 LED-Display....................................................................................................11
5. Assembly and Installation................................................................................12
5.1 Installation dimensions and descriptions.........................................................12
5.2 Installation.......................................................................................................13
5.3 Electrical connection.......................................................................................13
5.3.1 Schematic diagram.....................................................................................13
5.3.2 Assignment plan.........................................................................................14
5.3.3 Procedure...................................................................................................15
5.4 Fitting the electrode.........................................................................................16
5.5 Fixing elements for mounting probes..............................................................17
5.6 Mounting in the add-on housing......................................................................18
5.7 Shortening the electrode extension.................................................................21

4
6. Configuration.....................................................................................................22
7. Technical data ...................................................................................................22
7.1 Device data - controller...................................................................................22
7.2 Device data - probe.........................................................................................23
7.3 SIL- characteristics..........................................................................................24
7.4 Maximum ratings of potential free contacts.....................................................24
7.5 Data plate........................................................................................................24
8. Fault analysis and rectification........................................................................25
9. Warranty.............................................................................................................25
10. Conformity declaration.....................................................................................26
11. Certificates.........................................................................................................27
12.Annex.................................................................................................................29

5
1. Important safety instructions
KEEP THESE INSTALLATION AND OPERATING INSTRUCTIONS IN A SAFE PLACE!
Commissioning as well as maintenance and repair work may only be carried out by qualified
persons in compliance with the installation instructions given in this operating manual. The
correct installation, commissioning, maintenance and operation of the device presupposes that
the person in charge is familiar with measurement and control systems and complies with the
general installation and safety instructions. In addition, the correct and intended use of tools
and the handling of safety devices must be ensured. Unqualified personsmust not be assigned
the above tasks!
IGEMA GmbH accepts no liability for damage to property or personal injury caused by
unqualified persons or by failure to observe these installation and operating instructions. If no
sufficiently qualified person can be found, IGEMA GmbH can be commissioned with the
installation/maintenance.
1.1 Symbols used in these instructions
In the following installation and operating instructions, safety instructions are marked with the
following symbols:
Danger
This symbol and signal word refer to a potentially
hazardous situation which could result in death or
injuries if ignored.
Caution electrical voltage
This symbol and signal word indicate live parts
with an immediate danger of death from electric
shock.
Caution hot
This symbol with a signal word indicates a
potentially hazardous situation that can result in
severe burns and scalds all over the body.

6
Caution
This symbol and signal word refer to a potentially
hazardous situation which could result in
personal injury, property and environmental
damage if ignored.
Caution
This symbol and signal word refer to a potentially
hazardous situation which couldresult in damage
to the equipment if ignored.
Info
This symbol indicates useful information and
recommendations as well as measures that will
prolong the value of your measuring and control
system.
1.2 Intended use of the device
Use these installation and operating instructions, the identification on the rating
plate (see 7.5) and the technical data sheet to check whether the device is
suitable for the intended use/application. The device complies with the
requirements of the European Pressure Equipment Directive 2014/68/EU.
The device may only be used to indicate fill levels on containers.
The maximum values of the pressure and temperature range of the device must be checked
before installation. If the maximum allowable operating values of the device are lower than
those of the system on which it is to be installed, protective instruments for the device, such
as pressure reducers or similar, must be provided to avoid limit situations. The device may
only be used in accordance with the information in these installation and operating instructions
or for the parameters and applications agreed in the supply contract. (see rating plate, 7.5)
The operator of the direct water level indicator is obliged to familiarise himself on the
compatibility of the medium and the device. In case of doubt, contact the relevant installation
manager or site manager.
The correct installation position, alignment and flow direction of the device must be observed!
Before installing the IGEMA product on boilers or containers, it is essential to remove all
protective covers and, if necessary, the protective film from rating plates and sight glasses.
Caution

7
1.3 Safety at work
Before installation or carrying out maintenance work on the device, safe access
must be ensured and a secure working area with sufficient lighting must be
defined and marked out. Always use lifting equipment for heavy loads!
Before starting any work, carefully check which liquids or gases are or have been in the
pipeline. (flammable substances, irritating substances,substances hazardous to health) When
opening or dismantling the device, residues of the medium can escape. Subsequent fumes
are also possible in unpressurized and cold systems. Use designated PPE such as safety
goggles and respiratory protection!
Special attention must be paid to the condition of the environment around the installation or
maintenance site. Be aware of e.g.: potentially explosive atmospheres, lack of oxygen in tanks
and pits, dangerous gases/liquids, extremetemperatures, hot surfaces,fire hazard (e.g. during
welding) and moving machine and system components. Protect yourself from excessive noise
by taking the required protective measures.
For all maintenance work or new installations, on new or existing boilers or vessels, it is
imperative to check thatthe boiler or vessel has been depressurised and that the pressure has
been safely reduced to atmospheric pressure. In principle, no system should be regarded as
unpressurized even if indicated by pressure measuring devices such as pressure gauges or
sensors. When releasing the pressure, make sure that no persons are in the release area.
Carefully check whether you and/or other persons in the vicinity need PPE to protect yourself
from external influences such as high and low temperatures, radiation, noise, danger to eyes,
loose objects that can fall down or chemicals.
There is always a risk of injury when handling large and/or heavy equipment. Observe the load
handling regulation as a minimum requirement for working with loads. Avoid handling the
device with your own physical force, e.g. by lifting, pulling, carrying, pushing or supporting it,
especially to prevent back injuries. Use lifting equipment to move heavy and bulky equipment
in accordance with Article 1, Section 2 of the German Load Handling Regulation
(LasthandhabV).
Under normal operating conditions the surface of the device can become very
hot! Under the maximum operating conditions, the surface temperature can
exceed 350°C. After shutting off or, if necessary, shutting down the boiler, wait
until the temperature has normalized to room level. To avoid the risk of burns
and scalds, always use PPE including safety goggles!
Danger
Caution
hot!

8
1.4 Safety instructions for this device
These installation and operating instructions are an integral part of the device
and must be forwarded to the responsible departments "Goods inward,
Transport, Installation, Commissioning and Maintenance". They must be kept in
such a way that the technical staff have access to these documents at all times.
If the device is passed on to a third party, these installation and operating
instructions must also be included in the national language of the third party.
Avoid shocks and hard contact during transport, as this can lead to damage. During
intermediate storage, the device must be kept dry and secured against damage.
When servicing the unit, make sure to use sharp-edged internal parts and avoid shards of
broken glass. There is a risk of cutting hands and arms! Always wear work gloves when
changing packing, valve seat and valve plug.
For units with a dead weight of 30 kg or more, the customer must provide adequate support
(e.g. via a spring suspension device, etc.). This can be attached to the holding strap/eyelet on
the device.
When returning goods to IGEMA GmbH, the applicable safety and environmental laws
according to GGVSEB [German ordinance on the national and international carriage of
dangerous goods by road, rail, and inland waterways] must always be observed. If there are
any risks to health or the environment due to residues or the device has a mechanical defect
this must be indicated when returning the device and the necessary precautionary measures
must be taken. If the returned goods are devices that have come into contact with or contain
hazardous substances, a safety data sheet must be enclosed, and the goods must be clearly
marked. In addition, the hazardous substance must be reported to the logistics service
provider.
1.5 Exclusion of liability
IGEMA GmbH Mess- und Regelsysteme will assume no liability if the above regulations,
instructions and safety precautions are not observed and followed. If they are not expressly
listed in the installation and operating instructions, changes to an IGEMA device are carried
out at the risk of the user.
Caution

9
2. Contents of packing
1 SMLC2 controll unit
1 probe EL030, EL19-2, EL963 oder MS015A/B* resp.
1 set of installation and operating instructions
* depending on order
3. Use in compliance with regulations
The self-monitoring low level limiter SMHL2 in conjunction with the level probe EL03 or EL19-
2 is a level limiter, an "equipment part with safety function" according to:
EU-Richtlinie 2014/68/EU
DIN EN 12952-11 DIN EN 12953- 9
DIN EN 61508 -1/ -2/ -3 DIN EN 61326-1/-3-2
DIN EN 60730-1
The limiter meets the requirements for own fault detection under SIL3.
Type aproval certificates:
Type aproval due to PED / Certificatnumber: 01 202 931-B-16-0021
Type aproval due to SIL / Registrationnumber: 44 799 13775201
Other applied technical rules: Waterlevel 100
The limiter is used for monitoring a water minimum fill level in steam boilers. If the water level falls below
the minimum (water fill level) the limiter must reliably switch off the boiler’s burner control so that no
overheating of the boiler can occur and thus injury to people or damage to installations is prevented.
The prescribed minimum water fill level in the boiler is dependent on the system and is given by the
boiler manufacturer. Measuring of the water level is carried out via the probes EL030, EL19-2, EL963
or MS015A/B (see corresponding assembly and operating instructions) which are fitted in the boiler or
mounting flange.
When operating a steam boiler system with limited supervision and also when operating without constant
supervision the required maintenance procedures must be carried out self-monitored via control
equipment on the limiter.
The permanet self-monitoring ensures the safety function. Thus a test button is not neccessary.
Probes for use with SMHL2:
Name
PS
TS
Anschluss
Electrode length
EL030
32 bar
239°C
G ½"
125mm –1700mm
EL19-2
200 bar
367°C
G ½"
130mm –1700mm
EL963
8 bar
175°C
Flange
130mm
MS 015A
32 bar
239°C
G 1"
60mm –1500mm
MS 015B
32 bar
239°C
G 1½"
60mm –1500mm

10
4. System description
4.1 Function
The SMLC2 low water level limiter works in conjunction with the IGEMA EL030, EL19-2,
EL963, or MS015A/B level probes on the basis of the conductive fill level method of
measurement whereby the electric conductivity of the water medium is used. The conductivity
of the medium is measured in µS/cm. For this method of measurement to function reliably a
minimum conductivity of the substance to be measured is required.
The conductive method of measurement makes two statements: electrode submerged or
electrode emerged or switch point reached or not reached. Before installation the length
(observe thermal elongation) of the electrodemust be adjusted to the desired switching points,
e.g. for switching off burner and interrupting the safety circuit.
The limiter determines the current water level (electrode submerged / electrode emerged) in
the boiler. If all conditions for correct operation are met, the safety chain for the steam
generator is enabled (burner can switch on). On detection (level has fallen below minimum
level) the output “pre-alarm” is switched on immediately and the red LED starts to flash (1Hz).
Should this state be present for longer than the alarm delay time set (4s, 8s, 12s, 16s), the
output of the safety chain will be switched off (safe operation mode) and the LED “ALARM”
(red) remains permanently lit.
The factory setting for the alarm delay time is 4s.
To avoid faulty trips, e.g. due to foam or turbulent surface, the detection state is assumed not
before the electrode is permanently submerged for 1,5s.
In the event of a fault (e.g. broken cable, electronics malfunction, ...) the safety chain is
switched off immediately.
Safe operating mode, during which the output contacts of the device go into rest position,
corresponds at the same time to the de-energised state of the limiter.
So that after a fault the burner control does not start up again of its own
accord, manual locking (latching) of the burner must be carried out on
site. It is not a component of the limiter.
The general function of the limiter SMHL2 is displayed by the lighting of the green LED
"POWER”. The input stage of the SMLC2 compares the values of the insulation and the limiter
electrodes. Thus, besides the normal operationg stage, low water detection and triggering of
the insulation surveillance are implemented. Malfunctions of the measuring cable (e.g. short
circuit or cable break) will be detected, too.
The power flowing via the contacts of the safety chain is limited in the SMLC2 by a 4 amp fuse
protection by which sticking of the contacts is prevented.
Danger

11
The self-monitoring system is capable of identifying any possible first failure the moment it
occurs and switching off the downstream relays. Failure to detect a fault is therefore
impossible.
The self-monitoring is a periodic overall test of the device and takes place every 2sec as a fully
automatic process. This test is a background job and only an error detection will be displayed.
Because of this special first failure safe design manual tests are not necessary so there are no
test switches on the SMLC2..
4.2 LED-Display
Permanent green LED: normal operating mode
sound operation
Flashing green LED (1 Hz): low voltage
Uv < 180V
Permanent red LED:
Level has been below electrode for more than 4 (8, 12, 16)
sec. Returns to normal operating mode, if electrode is
longer than 2 sec in water again.
Low water (LLW)
Flashing red LED for 4..16s (1 Hz):
Resistance of insulation electrode below threshold for >
5 sec.
Subsequently: permanent red LED.
Returns to normal operating mode, if resistance of insulation
electrode above threshold again.
Insulation electrode
stained
Permanent red and yellow LEDs:
RAM/ROM/CPU test faulty; 2nd processor does not answer.
Return to normal operation mode if failure corrected.
System failure
permanent red LED together with flashing (1 Hz) yellow
LED:
Short circuit or cable break.
Fault in measuring cable

12
5. Assembly and Installation
The limiter is supplied in a plastic plug-in housing for fitting into switch cabinets. The housing
is designed for quick fitting with a spring catch for the DIN EN 50022 standard 35 mm carrier
rail and for screw fixing on a mounting plate.
5.1 Installation dimensions and descriptions
Base Front view Side view
with connection terminals
1 Screws for snap fixing
2 Holes, ø 4,3 mm
3 Fixing screws
4 Snap fixing
5 Holder
6 Cable feedthrough
7 Hood

13
5.2 Installation
Ensure protection class in accordance with current regulations.
- With snap fixing for standard DIN EN 50022 35 mm carrier rail
Fix device on standard carrier rail by means of the snap fixing (4).
Release fixing screws (3) and pull hood (7) from holder (5).
- Without snap fixing
Release fixing screws (3) and pull hood (7) from holder (5)
Release screws (1) and remove snap fixing (4). Drill through the marked point (2) in the
holder (5) with ø 4.3 mm drill bit.
Fit holder (5) on base plate with two M4 screws.
5.3 Electrical connection
The device terminal strip is live during operation!!
Before working on the device disconnect it from the mains!!
The device must be protected mains-side by the operator with a max.
T M 2A fuse!
If inductive consumers are connected, voltage peaks occur when
switching off. For this reason, connected inductive consumers (e.g.
contactor) must be provided additionally with an RC circuit: e.g. 0.1µF
/ 100Ω.
5.3.1 Schematic diagram
Steam boiler with probe Limiter
4-wire cable with shield
Danger
Danger
Danger

14
5.3.2 Assignment plan
In the normal operating condition (safety chain closed; burner ON) the output contacts 7 and
8 or 10 and 12 (pre-alarm OFF) are closed.
The configuration of the terminals is printed at the back of the housing.
(EL968 and MS015A/B: check separate Installation and Operating instructions)
SMHL2
Safety chain
Signalling
EL030 oder EL19-2
electrical connection:
shielded cable 4 x 0,75mm2
e.g. Helutherm 145 Multi-C; IGEMA Art.Nr. 40-55214
●
1 23
Mains voltage: see data plate
Lead connection at
probe plug
1 Screw
2 Probe plug
3 Seal
4 Contact carrier
5 Screw ring
6 Measuring cable

15
5.3.3 Procedure
•Pierce or pull out cable feedthrough (6) and feed connection cable through. Check supply
voltage. See name plate for allowable voltage. Use shielded connection cable (4 x 0,75
mm²) to the electrode (z.B. Helutherm 145 Multi-C - IGEMA Art.No. 40-55214).
•Length of connecting line max. 100 m.
•Only connect shielding on the SMHC2 control unit (terminal 6). After electrical connection -
with device disconnected from the mains - put hood (7) on holder (5) and tighten fastening
screws (3).
During installing it must be considered whether the cable used is UV-
resistant and that the UV protection is ensured on the installation side if
necessary.
The cable must not come into contact with heat-conducting parts.
The probe is equipped with a plug connector (4-pole).
For aligning the probe plug to the local circumstances, the upper nut can be released
(∅33.5mm). In doing so care must be taken not to move the plug in the probe!! (AF24).
The inner part can be carefully turned into the correct position.
On refitting caremust be taken that the seal is correctly seated! Retighten the upper nut without
moving the plug in the probe.
For connecting probe and controller pre-fabricated cables in various
lengths are available as accessories. If pre-fabricated cables are not used
the connection plugs must be wired according to the wiring plan.
1 Measuring electrode
2 insulation electrode 2
3 insulation electrode 1
⚫GND
Caution
Caution

16
5.4 Fitting the electrode
It is essential to remove the protective tube for transport before
installation!
If several electrodes are screwed into a flange the probe plugs (2) and the
associated probes should be labelled to prevent confusion!
EL968 and MS015A/B: check separate Installation and Operating instruction
Fixing the electrode extension (9)
Push the electrode extension (9) approx.
30 mm over the electrode shank (8) until
the ø 4.3 mm hole matches the threaded
hole in the electrode shank.
Screw up both parts by means of the
enclosed M4 set screw with AF2 hexagon
socket.
Screwing in the electrode
•Release screw (1) and pull off electrode plug (2)
•Clean and check sealing surfaces
•Insert (new) sealing ring (6)
•Lubricate thread (7) with heat-resistant solid lubricant
(e.g. graphite).
•Screw in electrode and tighten, max. tightening
torque Md=140 Nm.
•Make electrical connection only after installation in
the boiler.
Do not seal thread with PTFE strip or
the like!
When commissioning the boiler, check
the probe screw connection in the
flange for leaks and retighten if
necessary!
Screw
probe plug
Seal
Contact carrier
Threaded ring
Sealing ring
Thread
Electrode shank
Electrode
extension
Danger
Danger
Danger
Caution

17
5.5 Fixing elements for mounting probes
The flanges, seals, screws and nuts listed in the table below are designed in accordance with
DIN EN 12952 und 12953.
Flanges according to DIN
PN
DN
DIN
Form
Threaded hole
Material
40
50
EN1092-1
A
according to drilling
plan 1
1.0460
63
EN1092-1
B2
100 / 160
EN1092-1
40
100
EN1092-1
A
according to drilling
plan 1,3,4,5
1.0460
63
EN1092-1
B2
100 / 160
EN1092-1
Drilling plans 1-6
Seals according to DIN
PN
DN
DIN
Material
40
50
EN 1514-1 IBC
Graphite with plain metal insert
63
2697
RSt 37-2/ 0.5 graphite
100 / 160
40
100
EN 1514-1 IBC
Graphite with plain metal insert
63
2697
RSt 37-2/ 0.5 graphite
100/160

18
Screws according to DIN
PN
DN
DIN
Quantity
Dimension
Material
40
50
976
4
M16 x 75
1.7709
63
M20 x 100
100/160
M24 x 110
40
100
976
8
M20 x 90
1.7709
63
M24 x 110
100/160
2510
LM27 x 145
Ck 35
Nuts according to DIN
PN
DN
DIN
Quantity
Dimension
Material
40
50
EN 24032
8
M16
1.7258
63
M20
100/160
M24
40
100
EN 24032
16
M20
1.7258
63
M24
100/160
2510
NFM27
C 35
5.6 Mounting in the add-on housing
If shut-off valves are mounted between the process connections of the add-
on-housing and the boiler supports, an electric locking system (end switch)
has to be installed. A drain valve should be mounted to the add-on-housing.
Caution

19
Illustration of add-on-housing
Materials
Flange
1.0460
Pipes
St35.8 / 16 Mo 3 (according to pressure range)
Stainless steel and ASME-compliant materials upon request.

20
Construction dimensions
PN
DN
Construction dimensions min. mm
d
C
D
A1
A2
16
50
60,3
115
15
85
100
25
40
63
135
100
100
105
160
115
16
100
114,3
140
15
100
150
25
40
63
160
140
160
100
155
160
165
Process connection M1
PN
DN
DIN
DIN sealing form
16
50
100
DIN EN 1092-1
Type 11
Form B1
25
40
63
Form B2
100
160
Process connection M2
PN
DN
DIN
DIN sealing form
16
20
DIN EN 1092-1
Type 11
Form B1
25
40
63
25
Form B2
100
160
On request ASME-compliant flanges, weld-on ends or DIN or ASME-compliant socket
welding on the process connection M2 are also an option.
Table of contents
Other Igema Control System manuals
Popular Control System manuals by other brands
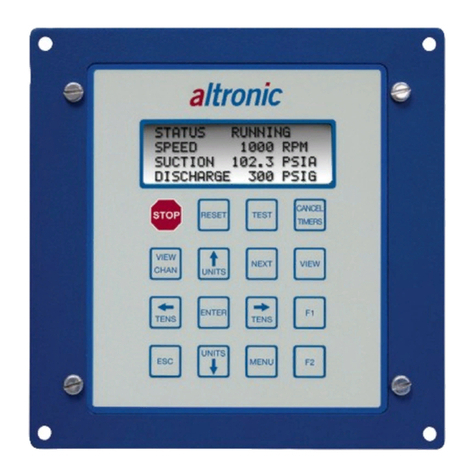
Altronic
Altronic DE-3000 operating instructions
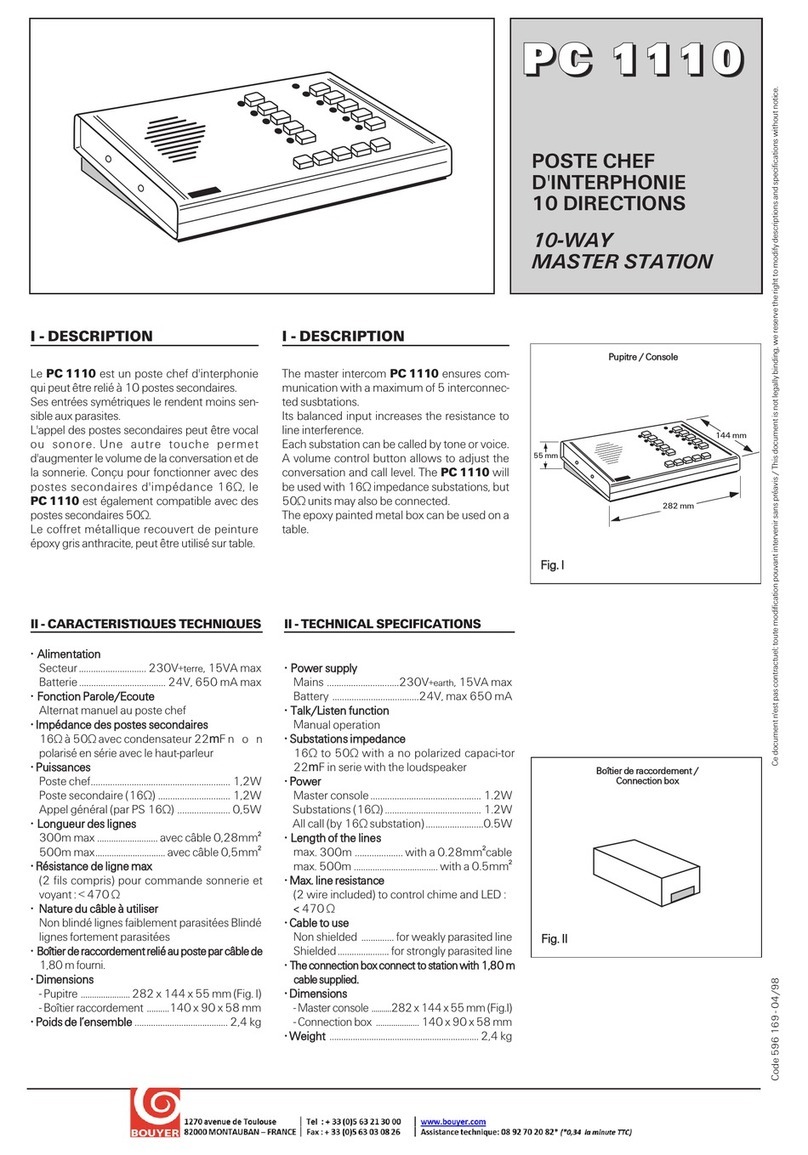
Bouyer
Bouyer PC 1110 manual

Crosswater
Crosswater Elite Operation and care guide
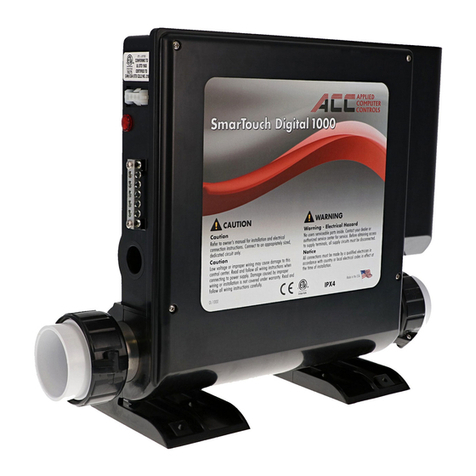
ACC
ACC SmarTouch Digital series User & Programmers Manual
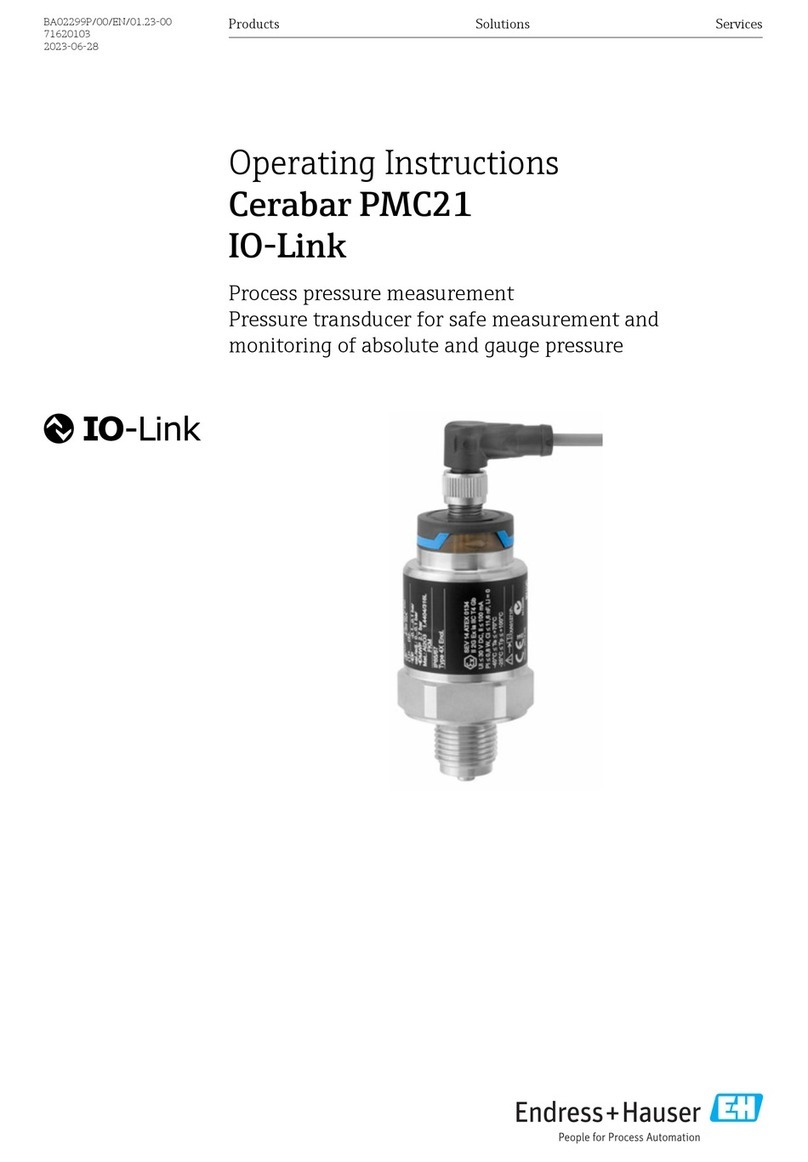
Endress+Hauser
Endress+Hauser Cerabar PMC21 operating instructions
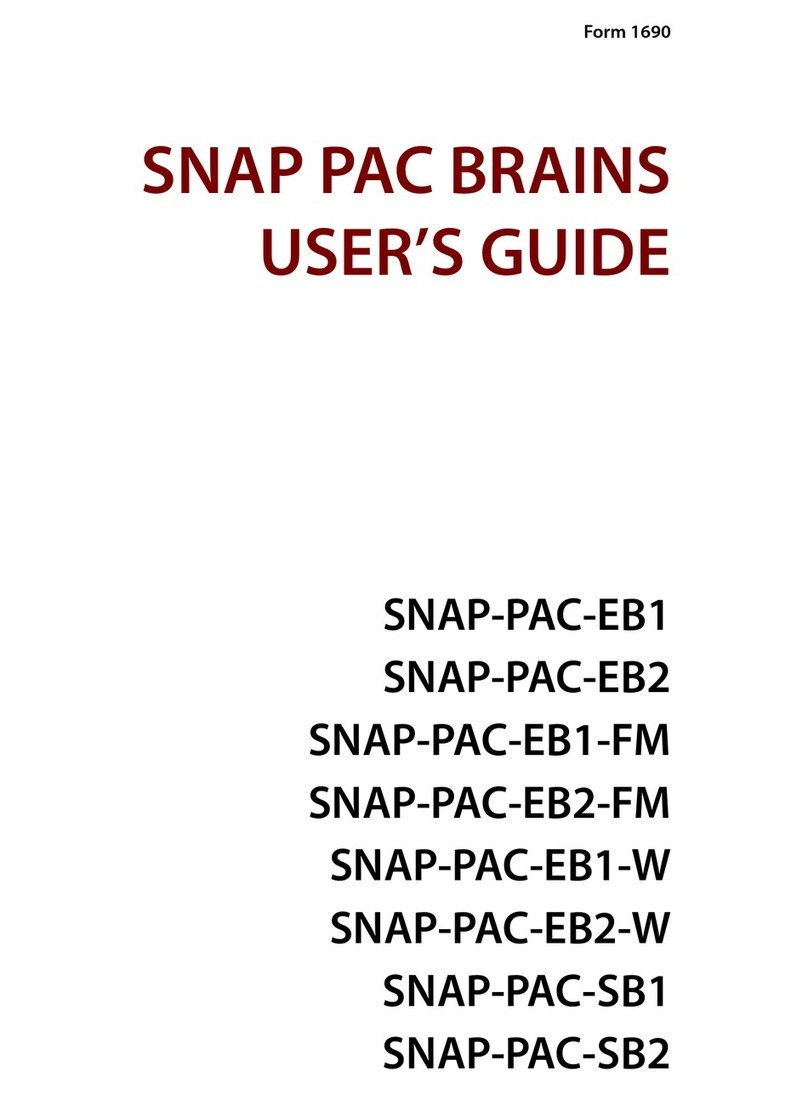
SNAP PAC BRAINS
SNAP PAC BRAINS SNAP-PAC-EB1 user guide