DIMA HC-100 User manual

TB-1026
HybridC
HC-100/200
Service Manual Ver1.1
This document contains proprietary information which is protected by copyright. All rights are
reserved. No parts of this document may be photocopied, reproduced, or translated into
another language without the prior written consent of DIMA Group B.V. .
The information contained in this document is subject to change without prior notice.
© Copyright 2008 DIMA Group B.V.


HYBRID Coater Service Manual ver?1.1 Table of Contents
1
Table of Contents
1. Introduction 4
1.1 About this Manual 4
1.2 Model Overview 5
2. Safety 6
2.1 Warnings 6
2.2 Emergency Switches 6
3. Machine Overview 7
3.1 Introduction 7
3.2 Electrical Block Diagram 7
3.3 Block Diagram of Air 8
3.3.1 Routing of the Air Lines 9
3.3.2 Air Lines Routing of the Options 10
3.3.2.1 With Options HC-1050 or HC-1051 10
3.3.2.2 With Options HC-1000, HC-1010, or HC-1030 12
3.4 With Options HC-1160/1170 14
3.5 Electrical Compartment in Front 15
3.6 Electrical Compartment in Rear 17
3.7 Detection of Exhausted Air 19
3.8 X and Y Movement 19
3.9 Head with Connection PCB 20
3.10 Dispense Head PCB 21
3.11 Z Movement at HC-100 21
3.12 ZØ Movement at HC-200 22
3.13 Embedded Software 23
3.14 Additional Revision Information 23
3.14.1 General 23
3.14.2 HC-100 Specific 24
3.14.3 HC-200 Specific 24
3.14.4 HC-1160/ HC-1170 General 24
3.14.5 HC-1170 Specific 24
4. Machine Installation 25
4.1 Pre-installation Checks 25
4.2 Unpacking the Machine and Removing Transport Locks 25
4.3 Placing and Leveling the Machine 27
4.4 Connections and Pressure Setting 27
4.5 Completion of the Installation 28
4.6 Installing Special Options 28
4.6.1 Installing Options DD-52XX 28
4.6.2 Installing Option HC-1050/ HC-1051 28
4.6.3 Installing Option HC-1210/ HC-1215 31
4.6.4 Installing Option HC-1230/ HC-1231 31
4.6.5 Installing Options HC-1235 and HC-1236 32
4.6.6 Installing Option HC-1320 32
4.7 Installing Options HC-1380 and HC-1390 34
4.8 Installing Options HC-1160 and HC-1170 35

Table of Contents HYBRID Coater Service Manual ver1.1
2
4.8.1 Placing/Adjusting Stopper Pin/Product Detect Sensor of Conveyor 35
4.8.2 Adjusting the Conveyor Level and Height 37
4.9 Setting-up the weight scales 38
4.9.1 Settings 38
4.9.2 Setting-up the Com Parameters 38
5. Maintenance 41
5.1 Introduction 41
5.2 Service Diagnostics 41
5.3 Regular Maintenance 42
5.4 Checklist for the Maintenance of the HYBRID 46
6. Electrical Wiring 50
6.1 Electrical Wiring Diagrams 50
6.2 Overview of the Wiring Diagrams 50
7. Pneumatics 52
7.1 Overview 52
7.2 Pneumatics Diagram 52
8. Diagnostics for PCB’s 55
8.1 Introduction 55
8.2 Controller EL-04873 55
8.2.1 LED’s on Upper Left Side of the EL-04873 56
8.2.2 LED’s near Connectors P1 and P2 on the EL-04873 57
8.2.3 LED’s near Connector P3 and P4 on the EL-04873 58
8.2.4 LED’s on Upper Right Side of the EL-04873 59
8.2.5 LED’s on Bottom Left Side of the EL-04873 61
8.2.6 LED’s near Connectors P21 till P26 on the EL-04873 62
8.2.7 LED’s near Connectors P27 till P29 on the EL-04873 63
8.2.8 Explanation of DIP-switches on EL-04873 64
8.3 Advanced Power LED Controller EL-04872 66
8.4 Stepper Drivers EL-04874 67
8.5 Interconnection PCB EL-04875 68
9. Small Repairs and Adjustments 70
9.1 Pressure Settings 70
9.2 Focusing the Fiducial Camera 70
9.3 Replacing the Fiducial Camera at a HC-100 71
9.4 Replacing the Fiducial Camera at a HC-200 72
9.5 Replacing Stepper Motors 73
9.5.1 Replacing the Stepper Motors of the X and Y axis 73
9.5.2 Replacing the Stepper Motor of the Z axis on the HC-200 74
9.5.3 Replacing the Stepper Motor of the Ø axis 76
9.6 Replacing PCB’s of Stepper Motors 77
9.7 Replacing and Adjusting the Encoder 77
9.8 Exchanging the Flexible Cable Duct on the HC-200 80
9.9 Adjusting the X, Y, Z and Ø Limits 82
9.9.1 Adjusting the Limits for the X Axis 82
9.9.2 Adjusting the Limits for the Y Axis 82
9.9.3 Adjusting the Limits for the Z Axis with the HC-100 82
9.9.4 Adjusting the Limits for the Z Axis with the HC-200 83
9.9.5 Adjusting the Limits for the Ø Axis with the HC-200 84

HYBRID Coater Service Manual ver?1.1 Table of Contents
3
9.10 Replacing the Differential Pressure Switch 84
9.11 Fitting a new stop pin in a conveyor 86
10. Spare Parts 87
A. Electrical Wiring Diagrams Revision 1.0 103
B. Electrical Wiring Diagrams Revision 1.1 110
C. Electrical Wiring Diagrams of Options 128
D. EL-04806 Dispense Head PCB Overview 139
E. EL-04873 Control PCB Overview 143
F. EL-04875 Connection PCB Overview 155
G. EL-04876 Dispense Head PCB Overview 161
H. EL-04879 Dispense Head PCB Overview 165
I. I/O Assignment 168

Chapter 1 HYBRID Coater Service Manual ver1.1
4
1. Introduction
1.1 About this Manual
This manual provides information to be used by the DIMA authorized service engineer to
maintain and repair the HYBRID Coating machine. It describes the HYBRID C, it’s cabling
and pneumatics, regular maintenance work, and the spare parts. The manual further
describes how to perform some small repairs, and modifications. The options for the HYBRID
C are also described in this Service Manual.
For general information about the HYBRID C, refer to the user documentation (User Manual
+ Machine Reference Manual).
Due to technical innovations and improvements, data in this manual may differ from the
machine at hand. DIMA however tries to keep this manual as up to date as possible.
Next table shows an overview of the previous and current versions of this manual.
Version Release date Changes
1.0 October 2007 Initial Release
1.1 July 2008 Set-up of Chapter 5 changed, also added
checklist. In Chapter 9 the Section about
stepper motors SS53 was extended . Also the
revision of the stop pin was added. Additional
SS-numbers were given in Chapter 10. Valve
heating added in several Chapters.
When you have any questions or remarks about the HYBRID Conformal Coating machine or
this Service Manual, please contact DIMA.
DIMA Group B.V.
Beukelsdijk 2
5753 PA Deurne
Tel : +31 493 352 752
Fax: +31 493 352 750
e-mail: [email protected]

HYBRID Coater Service Manual ver1.1 Chapter 1
5
1.2 Model Overview
The HYBRID C is available in two versions:
HC-100: The HC-100 robot is equipped with X, Y, and Z axis. The 3-axis robot can handle
up to 4 different tools. Tools can be dispense valves, spray valves, grippers, etc.
They are mounted onto a Z slide, or on a Z slide combined with a fixed tilt
mechanism as a fourth axis. This combination is mounted onto an adapter for 1, 2,
3, or 4 valves. Tools and valves can be configured outside of the machine and can
be mounted onto the robot as one single unit. The 3-axis robot comes with a
camera on the Z axis, computer with DIMASOFT User Software, a base for
adapter plates, one electronic pressure transducer for the main air supply, one
electronic pressure transducer for detection of exhausted air and illumination
inside the machine.
HC-200: The HC-200 robot is equipped with X, Y and Z and Φaxis. The 4-axis robot can
handle up to 4 different tools. Tools can be dispense valves, spray valves,
grippers, etc. They are mounted onto a valve mount. Tools and valves can be
configured outside of the machine and can be mounted onto the robot as one
single unit. The 4-axis robot comes with a camera on the Z axis, computer with
DIMASOFT User Software, a base for up to 4 valve mounts, one electronic
pressure transducer for the main air supply, one electronic pressure transducer for
detection of exhausted air and illumination inside the machine.
Both robots can be configured as a batch or inline machine and can be reconfigured in the
field at any time.

Chapter 2 HYBRID Coater Servicce Manual ver1.1
6
2. Safety
Refer to the User Manual for general Safety Information.
2.1 Warnings
Never enter the machine when the motors of the Coating
Head or of the Conveyor are running.
Do not overrule the hood locks and do not run the HYBRID
C in any way with the hoods open.
Do not overrule the push buttons place don the Safety
Panel.
When working with test fluids be aware of the following:
Consult the Material Safety Data Sheet (MSDS) for all fluids
used with the HYBRID C. The MSDS provides material
usage instructions, safety precautions, information about
personal protective equipment, and disposal instructions.
Fluids can be extremely dangerous when working with high
pressure. They should be safely contained. Be sure the
pressure is removed before performing any adjustments or
maintenance. A beam of high pressure fluid can cut like a
sharp knife and can even result in death.
2.2 Emergency Switches
Emergency switches are installed on two places on the machine. Immediately push one of
these switches when an emergency occurs. The machine will immediately switch off. The pC
and the motor stay on.
When the situation is normal again, the Emergency Switch can be pulled out and the
machine can be restarted as described in the User Manual.

HYBRID Coater Service Manual ver1.1 Chapter 3
7
3. Machine Overview
3.1 Introduction
This Chapter gives an overview of the machine. Drawings of electrical wiring can be found in
Appendix A and B.
3.2 Electrical Block Diagram
Below figure shows the block diagram of the electrical parts of the machine.
Z-Limit
EL-04875
Connection
PCB
-Limit (HC-200 only)
-Encoder
(HC-200 only)
X-Limits
Y-Limits
M
Cable
Chain
Cable
Chain
EL-04874
Stepper Driver
EL-04874
Stepper Driver
EL-04874
Stepper Driver
EL-04874
Stepper Driver
EL-04874
Stepper Driver
EL-04874
Stepper Driver
EL-04548
Processor
Module
XYZ C1C2
X
Y
Fuses Fuses
Power
Supply
24Vdc
Power
Supply
48Vdc
Control Circuit & Fuses
Fuses
Main Switch
On/Off Switch
Emergency Switch
Interiour Light
EL-04873
Control
PCB
PCMonitor
RS232/USB
Keyboard
Trackball
24Vdc
Differential
Pressure
Switch
Mounting
Bracket for up
to 8 Pressure
Sensors
EL-04872
Power
LED
Control
M
M
MZ
Cable
Chain
EL-04876
or
EL-04806
or
EL-04879
Valve Mount
Assembly
Valve Mount
Assembly
Valve Mount
Assembly
Valve Mount
Assembly
1234
Rotary Valve 1
Rotary Valve 2
EL-00578
Camera
EL-04870 or
EL-04807
Advanced Fid.
Camera
Illumination
Doorlock Front
Doorlock Back
Pushbutton
Control Panel
Exhauster
Detection

Chapter 3 HYBRID Coater Service Manual ver1.1
8
3.3 Block Diagram of Air
Below figure shows the block diagram of the air parts of the machine.
EL-04875
Connection
PCB
Cable
Duct
Cable
Duct
EL-04548
Processor
Module
EL-04873
Control
PCB
Mounting Bracket for up to
8 Pressure Sensors
(Pressure Sensors part of
Kit HC-1050 or HC-1051)
Cable Duct
Valve Mount
Assembly
Valve Mount
Assembly
Valve Mount
Assembly
Valve Mount
Assembly
1234
Air Filter
&
Pressure Regulation
Air Supply
Air
Distribution
Block
optional Pressure
Reducing Valves(Part of
Kit HC-1050 or HC-1051)
Output for
Medium
Pressure or
other optional
Functions
Valves for
Up/Down/Tilt/Normal
Valves for Atomising Air or
other functions
12
34
EL-04872
Power
LED
Control
Air Distributor Cross
(HC-200 only)
Main Air IN
optional
Solenoid
Valves
(Part of Kit
HC-1050 or
HC-1051)
1
2
3
4
A1
A2
B1
B2
C1
C2

HYBRID Coater Service Manual ver1.1 Chapter 3
9
3.3.1 Routing of the Air Lines
NOTE: This section shows the route from the incoming air till the air switch on the Coating
Head. The following sections show the routing of the air lines needed with the
several options.
A The pressurized air enters the machine at the left of the front bottom and from there one
air line runs to the distribution block (#1) at the left in the bottom compartment. The
distribution block consists of two blocks connected together. The connection hose (#2)
makes the air connection.
B From there (#1) the air is distributed via one line straight to the pressure sensor on the
large PCB in the bottom rear of the machine. This is always the first pressure sensor (#3)
at the bottom right hand side bracket of the large PCB.
In
Out to
coating
head 2
1
3

Chapter 3 HYBRID Coater Service Manual ver1.1
10
C From there (#1) the main air pressure is distributed directly to an air switch #4 on the
coating head (with HC-100 = figure 3a). Or to the air switch #5 on the fixed part of the
coating head (with HC-200 = figure 3b).
3a 3b
3.3.2 Air Lines Routing of the Options
3.3.2.1 With Options HC-1050 or HC-1051
Kit HC-1051 is intended for pressure up to 2.5 bar for atomizing air. Kit HC-1050 is intended
for pressure up to 7 bar for a tank or cartridge. These kits contain one pressure reducing
valve, one solenoid valve with bracket, one pressure sensor, one Y connection and four air
lines and some fasteners.
A For this purpose an air line runs directly from the distribution block (#1) to the Pressure
Reducing Valve (#6) either No. 1050 or No. 1051. The outlet line from the Pressure
Reducing Valve goes into the cable duct above the bottom in the rear compartment of the
machine.
B Here it splits in an Y connection (#7). The long end runs to the pressure sensor (#8) on
the large PCB (the next free position).
4
5
6
7

HYBRID Coater Service Manual ver1.1 Chapter 3
11
C The short end runs to the inlet (#9) on the back of the solenoid valve (#11).
rear of coating head on HC-100 rear of coating had on HC-200
D The outlet (#10) of this solenoid valve (#11) is connected via one of the air lines in the
fixed duct and the flexible duct all the way to the first interconnection (#12) on the coating
head. Keep the order of these air lines leading from the solenoid valves the same all the
way to the coating head and further to the intended tool! For convenience they are
numbered on the interconnection plate and on the coating head. Till here all is similar
with the HC-100 and the HC-200.
NOTE: The HC-1051 is normally used for
atomizing air and runs through the
smaller air lines to the coating
head. When no atomizing air is
needed it can be used for other
purposes. The HC-1050 is normally
used to pressure a tank or cartridge
and runs from the outlet of the
solenoid valve directly to the tank or
cartridge inside working area.
9
10
12
11
8
12

Chapter 3 HYBRID Coater Service Manual ver1.1
12
E The previous figure shows an example of a HC-100 equipped with various tools. Here the
air lines are taken from the front of the coating head. They are controlled by the pressure
reducing valves from the front panel and the controlled pressure is put on the fluid in the
cartridge or syringe.
F At a HC-200 these air lines run in a flexible duct several times around the coating head
into the interconnections A1, B1, and C1 as seen in Block Diagram of Air at the beginning
of this chapter. The Y connection is the main air IN.
G However it is possible that the three connections on the coating head aren’t sufficient,
then it is possible to run the air line directly to one of the tanks (inside or outside the
working area). From there a fluid line can run to a tool on the coating head.
3.3.2.2 With Options HC-1000, HC-1010, or HC-1030
A At the HC-100 the air line is continued at the underside of the switch (#4) into the flexible
air duct. And from there to the inlet connection (#13) of the air block (#14). The air block
is used to distribute the pressure of the main air to the various solenoid valves #15 which
are mounted on it. From here two air lines #16 run down to each tool on the front of the
Coating Head. This way you can perform an OUT and IN function on a tool. Like a slide
function down and up (see example), or tilt function out and in! The speed regulation is
done on the tool with the small knobs (#17).
A1, B1, C1
#Y
13
15 14
16
16
17

HYBRID Coater Service Manual ver1.1 Chapter 3
13
B At the HC-200 the pressure of the main air is from the air switch #5 through a line into the
flexible duct #18 around the Coating Head to the distributing cross #19 under the clear
plastic disc. Here the main pressure (#21) enters the cross (#19) of the rotating head and
is distributed inside this cross to sides behind the cover #20 where it can exit into the
corresponding tool. This cover (#20) must be removed and the tool can be mounted here.
C From behind the cover (#20) the air is distributed directly into the back plate (#22) of the
tool. There it runs inside to up to three solenoid valves. The upper one (#23) is used for
the slide In and Out, the middle one (#24) can be used to actuate the needle. The lower
one (#25) can be used for the tilt action. Again on the tools you can find the knobs (#26)
for fine adjustment of the movement.
19
18
23
24
22
12
21 20
25
26

Chapter 3 HYBRID Coater Service Manual ver1.1
14
3.4 With Options HC-1160/1170
The HC-1160 consists of a chain conveyor with two stepper motors, two stopper pin
cylinders and one product sensor. The HC-1170 has additionally two clamping rails which
are actuated by two air cylinders. The next block diagram shows the lay-out of the
connections.
Air
Distribution
Block
PCB of Stepper
Motor Front Rail
PCB Of Stepper
Motor Rear Rail
EL-04548
Processor
Module
EL-04873 Control PCB
EL-04872
Power LED
Control
See Section 1.2 for relation to complete Electrical Block Diagram and Section 1.3 for relation to Block Diagram of Air
Front Conveyor Rail
Rear Conveyor Rail
3
P10
SMEMA Connectors
P19
P9
2
2
1
14
4
5
5
IN OUT
1. Stepper Motors for Chain Drive
2. Clamping Cylinders (HC-1170 only)
3. Product Sensor
4. Stopper Pin Cylinders
5. 3/2 Way Valves
= Air Lines

HYBRID Coater Service Manual ver1.1 Chapter 3
15
= Electrical Wires
3.5 Electrical Compartment in Front
This compartment contains:
Opening through which the hose for external air supply enters the machine. This hose is
connected to a pressure controller and air filter/ water separator unit.
Personal Computer with frame grabber, USB and/or RS232 interface to EL-04873
controller, display, keyboard and trackball.
Electro panel with 230VAC circuit and power supplies for 24Volt and 48Volt. Also a
24VAC transformer is present feeding the control circuit with On-Off switches and
Emergency Stops (See wiring diagrams HC-0200-0115 and HC-0200-0215).
Flow detection switch on the air exhaust channel.
For spare parts of this part see wiring diagrams.
1 2 3 4 5 6 7 8 9 10

Chapter 3 HYBRID Coater Service Manual ver1.1
16
Pos. Cable Purpose Remark
1 KHP-0100-0501 mains of PC
2 EL-04763 keyboard
3 EL-04763 track ball
4 EL-04766 (RS232) software interface P11 on main board
5 EL-04772 display
6 EL-04780 (USB) software interface P13 on main board
7 USB for option control via connector bracket
8 USB for option control via connector bracket
9 EL-04781 ethernet interface via SMEMA-board
10 KHC-0100-0105 Frame grabber/ camera PC/ CAM
Connect wiring to PC as above.
Push PC into electrical compartment.

HYBRID Coater Service Manual ver1.1 Chapter 3
17
3.6 Electrical Compartment in Rear
This compartment contains:
Electro panel with EL-04873 Control PCB and EL-04872 Advanced Power LED Control
(See wiring diagrams HC-0200-0315 and HC-0200-0415).
Mounting bracket for external connections (Ethernet, USB etc.).
The EL-04873 Control PCB contains the complete control of the machine. It get its
commands from the Personal Computer. On this PCB two different types of PCB’s are
present:
One EL-04548 Processor Module. This module contains a very powerful processor and
fast memory. The embedded software can be flashed in this module. Updating the
program can be done by the machine.
Up to six EL-04874 Stepper Driver Modules. These modules are used to drive the stepper
motors of the machine. The position of a module determines for which function a stepper
is used. From left to right: X, Y, Z, Ø, Conveyor 1(front), Conveyor 2 (rear). If a function is
not used the corresponding position stays empty. Each module gets its own 48Volt power
supply. A LED is present on the bottom side of each module indicating the presence of
this 48Volt. On the module only the power part of the stepper control is located.
NOTE: The modules are identical, so interchangeable for testing purposes.
On the right side of the EL-04873 Control PCB up to 8 Pressure Sensors may be present.
Numbers are present on the PCB indicating the sensor number of the position. On
position 1 (bottom, right) is always a pressure sensor present. This one is used to
measure the pressure of the incoming air supply. The other ones are optional (for use in
combination with HC-1050 and HC1051 option). See appendix E for more information.

Chapter 3 HYBRID Coater Service Manual ver1.1
18
Appendix I shows more detailed information about the I/O of this PCB.
For spare parts of this part see wiring diagrams.
Mounting bracket for external connections (Ethernet, optional SMEMA, weighing scale, etc.).
This manual suits for next models
1
Table of contents
Other DIMA Dispenser manuals
Popular Dispenser manuals by other brands
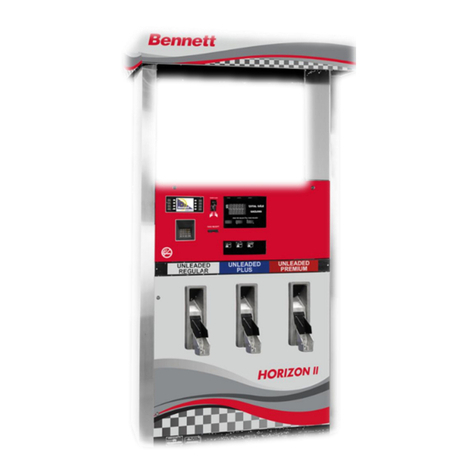
Bennett
Bennett Horizon 2422FS-1 Series installation manual
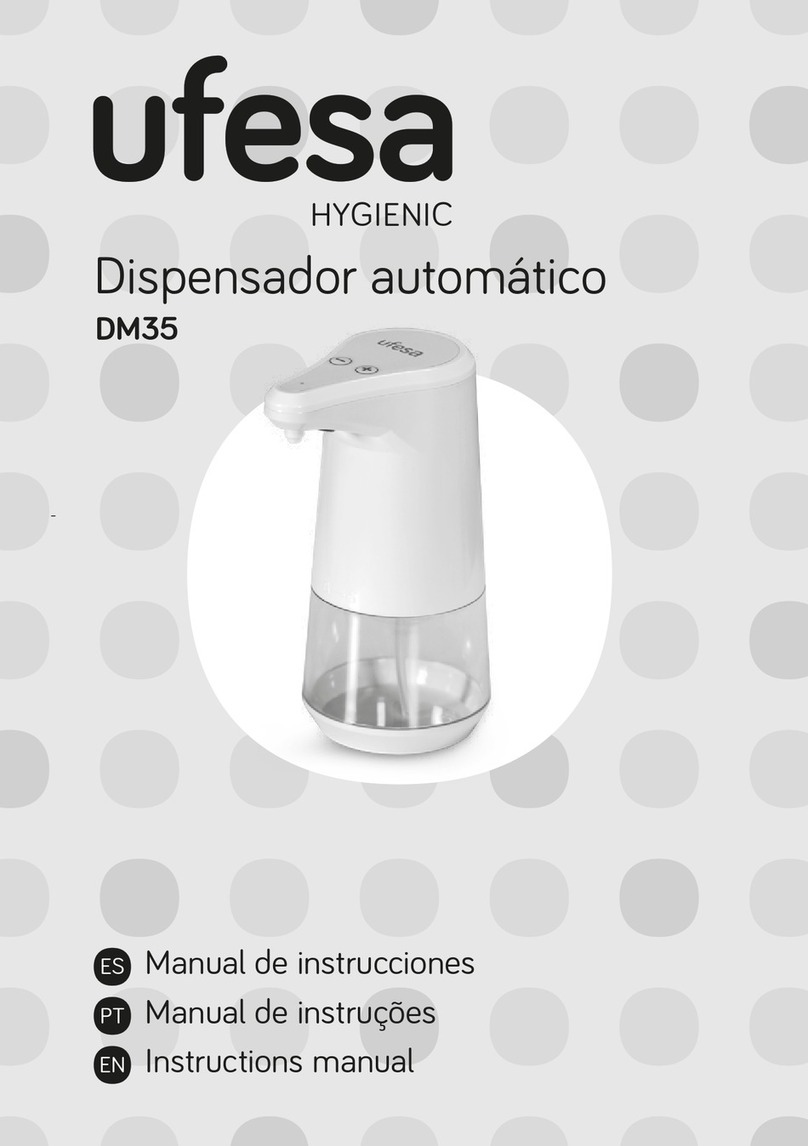
UFESA
UFESA Hygienic DM35 instruction manual

Bennett
Bennett CNG Series installation manual

HoMedics
HoMedics mybaby MYB-W10-CA Instruction manual and warranty information

Billi
Billi Quadra 420 installation guide

Cornelius
Cornelius IDC Pro255 Setup guide
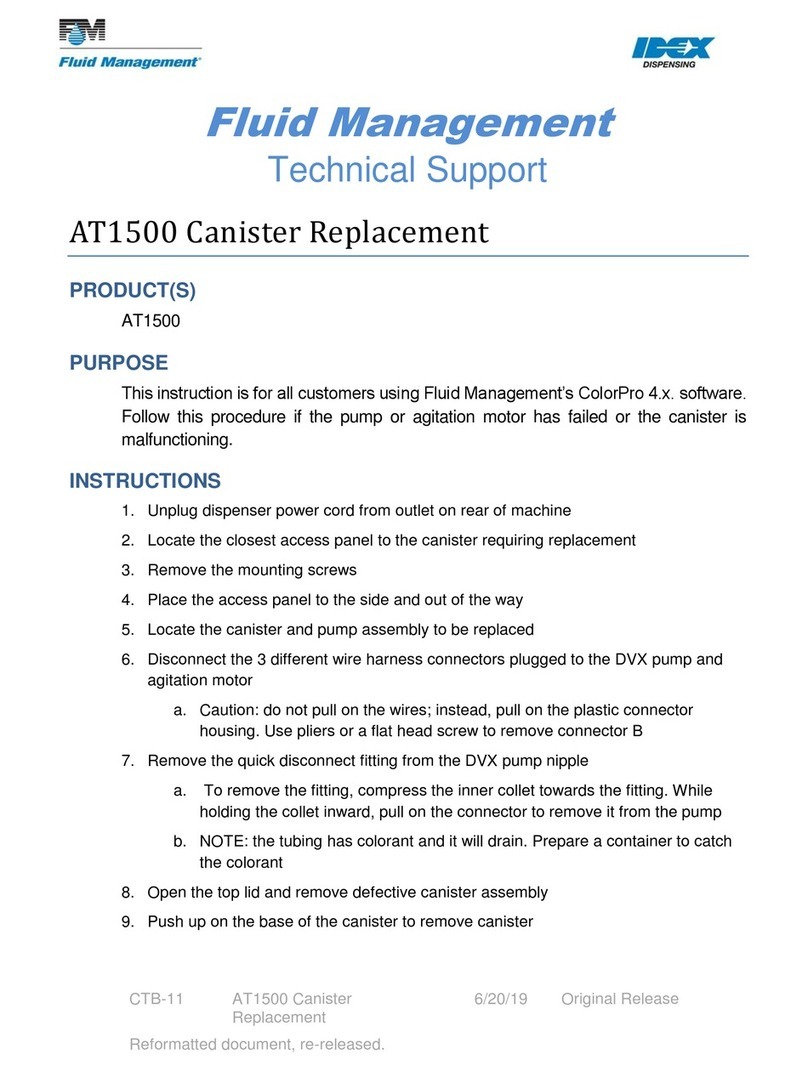
Idex
Idex Fluid Management AT1500 Technical support
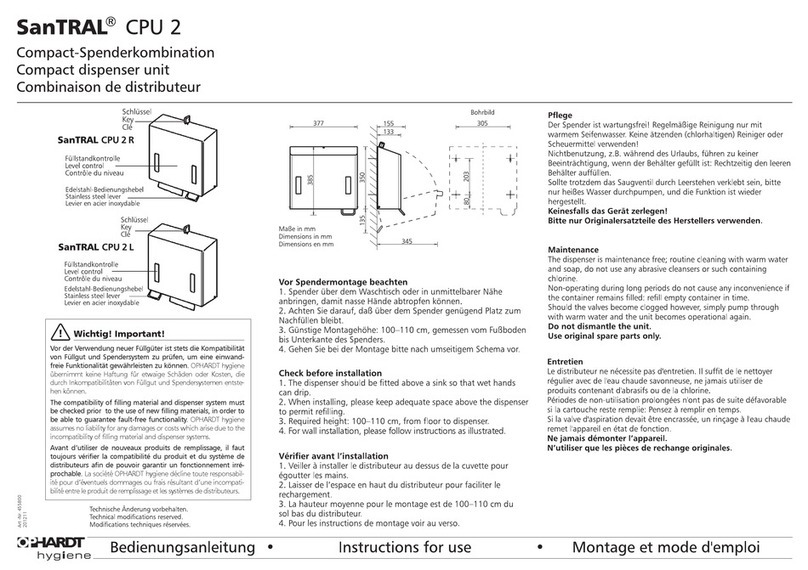
OPHARDT HYGIENE
OPHARDT HYGIENE SanTRAL CPU 2 Instructions for use
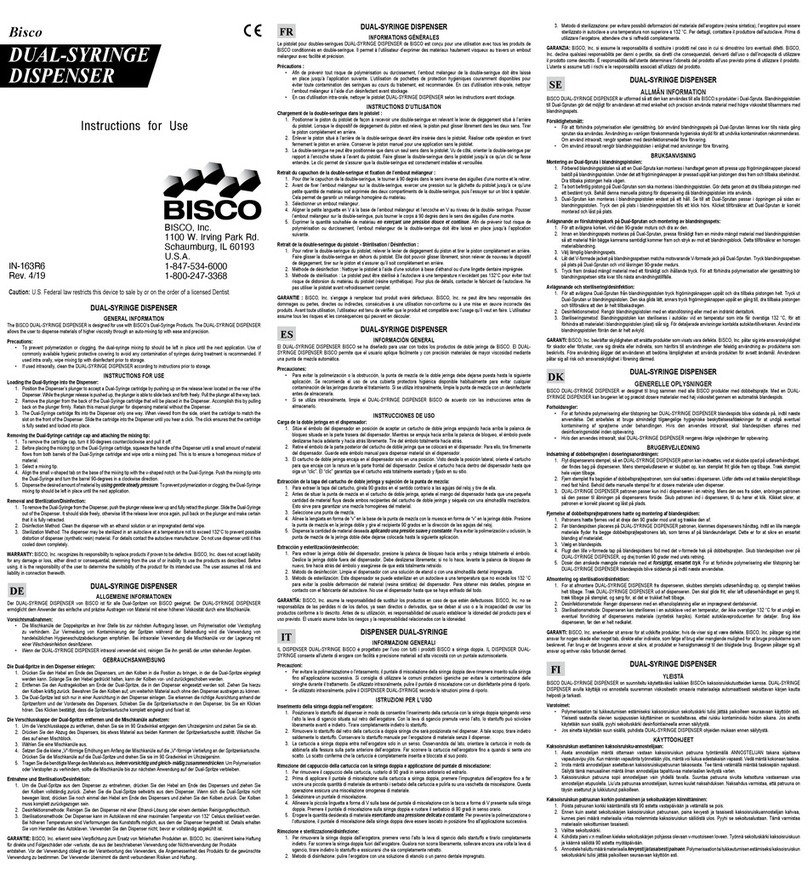
Bisco
Bisco IN-163R6 Instructions for use

amspa
amspa Mobile Fuel Dispenser owner's manual
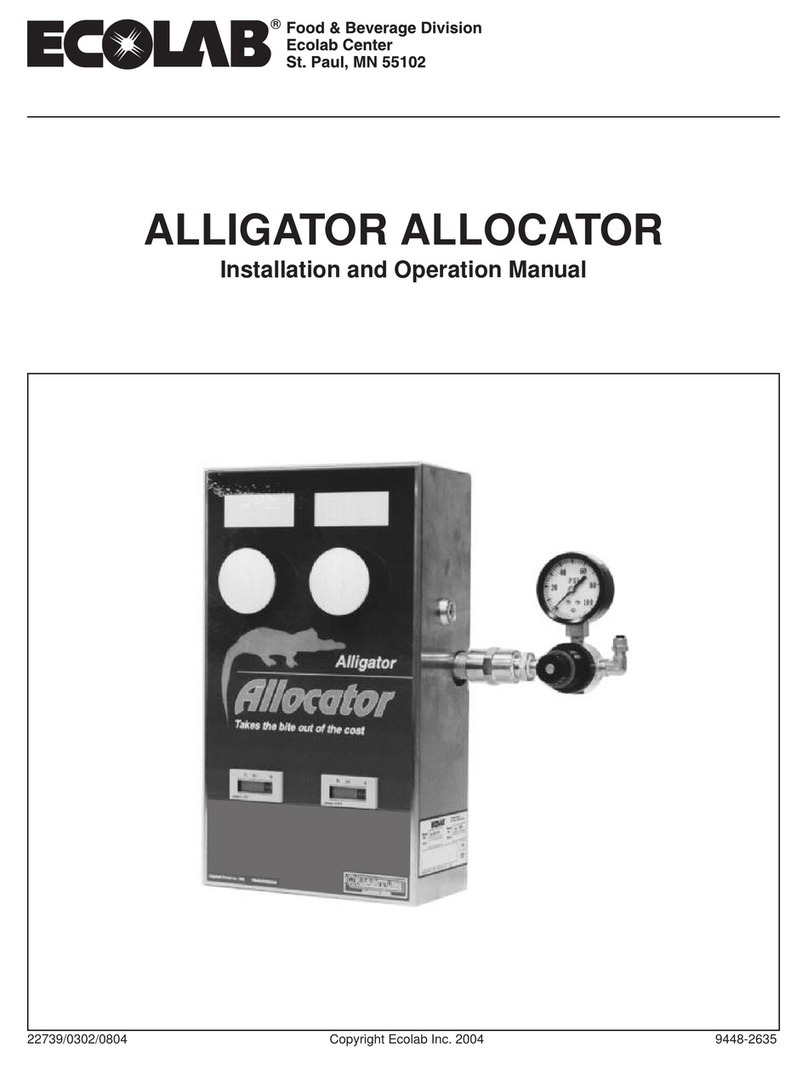
Ecolab
Ecolab ALLIGATOR ALLOCATOR 100 Installation and operation manual

Kolin
Kolin KWD-BL59BSS owner's manual