Dyna-Flo DFC Parts list manual

Dyna-Flo Control Valve Services Ltd.
Edmonton, Alberta, CANADA
Website: www.dynaflo.com
Phone: 780 •469 •4000
Toll Free: 1 •866 •396 • 2356
Fax: 780 •469 •4035
Model
DFC Valve Actuator
Operation, Parts and Instruction Manuals
Instruction Manual May 2007
1
Dyna-Flo DFC
Operation, Parts and Instruction Manual
Table of Contents
Actuator Specifictions 3
Unpacking Actuator 4
Rigging Set Up Diagram 4
Bench Setting 4
Bench Setting Diagram 5
Mounting 5
Yoke Nut Tightening Diagram 6
Maintenance 7
Actuator Disassembly 7
Actuator Assembly 8
Actuator Mounting Diagram 9
Torque Chart 11
DFC Diaphragm Plate Diagram 11
Actuator Cross Section 12
Parts List 14
Model Builder 20
Figure 1 Model DFC
Actuator and DF2000 Valve

Model
DFC Valve Actuator
Operation, Parts and Instruction Manuals
Dyna-Flo Control Valve Services Ltd.
Edmonton, Alberta, CANADA
Website: www.dynaflo.com
Phone: 780 •469 •4000
Toll Free: 1 •866 •396 • 2356
Fax: 780 •469 •4035
Instruction Manual May 2007
2
!NOTICE! These instructions are meant to be used in conjunction with the Dyna-Flo DFC/
DFO Series Technical (Sales) Bulletin. If you do not have the Technical Bulletin,
contact Dyna-Flo immediately, or visit www.dynaflo.com
It is the intention of this document to provide users with an accurate guide for
safe installation and maintenance of Model DFC valve actuators. Revisions and
updates are available at above mentioned website.
Introduction
The Model DFC series linear output spring and diaphragm actuators are used in all kinds of demanding
applications. The large area of the diaphragm allows low-pressure operation, and the spring provides fail
safe positioning of a control valve on loss of the pneumatic supply. Model DFC actuators are used to
automate control valves in both throttling and on/off control of liquids or gases.
When combined with a Dyna-Flo Model DF2000 or 360 control valve, the DFC is part of a rugged control
valve assembly, to which a wide variety of controllers and instruments can be attached.
Dyna-Flo’s high level of quality specifications used in manufacturing the Model DFC and DFO series linear
pneumatic actuators ensures superior performance and customer satisfaction.
! CAUTION !
To avoid personal injury or installation damage as a result of the sudden release of process
pressure or the breaking of parts, do not install the actuator assembly where service
conditions could exceed the limits stated in this manual or on the equipment nameplates. Only
well trained experienced technicians should perform these procedures. Be sure to use
safe work practices and lockout procedures. Always be aware of the hazards of spring-loaded
actuators. Be sure that they are in the failed (de-energized) position before performing any
maintenance procedure. These actuators have dangerous pinch points. Never put your hands
inside the valve unless you are certain that the actuator cannot move.
General
The following instructions are to be thoroughly reviewed and understood prior to installing,
operating or performing maintenance on this equipment. Work on this equipment should be
done by experienced personnel. Throughout the manual, safety and caution notes appear and
must be strictly followed to prevent serious injury or equipment malfunction.
Scope
This manual will provide detailed information on the complete disassembly and reassembly of the Model
DFC pneumatic actuator. Refer to seperate instruction manuals for the installation of positioners and all
other accessories used with these actuators. Do not apply any other conditions to the actuator without
first contacting your Dyna-Flo sales office.
This manual is written to be a practical and useful guide to successfully using the Dyna-Flo Model DFC for
many years.

Dyna-Flo Control Valve Services Ltd.
Edmonton, Alberta, CANADA
Website: www.dynaflo.com
Phone: 780 •469 •4000
Toll Free: 1 •866 •396 • 2356
Fax: 780 •469 •4035
Model
DFC Valve Actuator
Operation, Parts and Instruction Manuals
Instruction Manual May 2007
3
Table 1
Model DFC Actuator Specifications
SPECIFICATION
ACTUATOR SIZE
1069 2069 2105 2156 3105 3156 3220(1)
Nominal Effective
Area
inch2 69 69 105 156 105 156 220
cm2 445 445 667 1006 677 1006 1419
Yoke Boss
Diameter
inch 2-1/8 2-13/16 2-13/16 2-13/16 3-9-16 3-9/16 3-9/16
mm 54 71 71 71 90 90 90
Acceptable Valve
Stem Diameter
inch 3/8 1/2 1/2 1/2 3/4 3/4 3/4
mm 9.5 12.7 12.7 12.7 19.1 19.1 19.1
Maximum Allowable
Output Thrust
lb 2300 2700 5650 7550 5650 6800 8800
N 10,230 12,010 25,131 33,582 25,131 30,246 39,142
Maximum
Travel(2)
Standard
inch 1-1/8 1-1/2 22223
(3)
mm 29 38 51 51 51 51 76
Top-Loaded
inch 3/4 --- 3/4 --- --- 1-1/8 ---
mm 19 --- 19 --- --- 29 ---
Maximum Casing
Pressure for Actuator
Sizing(4,5)
Psig70706555655550
kPag 483 483 448 379 448 379 345
Maximum Excess
Diaphragm Pressure(4)
Psig20201010101010
kPag 138 138 69 69 69 69 69
Maximum Diaphragm
Casing Pressure(4,5)
Psig90907565756560
kPag 621 621 517 448 517 448 414
Approximate Weight
lbs 48 50 90 121 94 122 254
Kg 22 23 41 55 43 55 115
Material
Temperature
Capabilities
Nitrile Elastomers -40 to 180oF (-40 to 82oC)
Silicone Elastomers -65 to 300oF (-54 to 149oC)
NOTES:
1These values also apply to the DFC Size 3220-4 actuator.
2Actuator travel may be less than the value listed after connected to the valve.
3Maximum actuator travel for the 3220-4 is 4 inches (102 mm).
4See Specification section for definitions.
5This Maximum Casing Pressure is not to be used for normal operating pressure. Its purpose is to allow for
typical regulator supply settings and/or relief valve tolerances.

Model
DFC Valve Actuator
Operation, Parts and Instruction Manuals
Dyna-Flo Control Valve Services Ltd.
Edmonton, Alberta, CANADA
Website: www.dynaflo.com
Phone: 780 •469 •4000
Toll Free: 1 •866 •396 • 2356
Fax: 780 •469 •4035
Instruction Manual May 2007
4
how to install the actuator on the valve. The actua-
tor must be installed on the valve before being
installed into the pipeline. Ensure that the travel
has been checked; refer to the “Bench Settin Actua-
tor” section (below) for detailed instructions on this
procedure.
Bench Setting Actuator
(Refer to Figure 3)
! CAUTION !
To prevent valve stem damage perform
the bench setting with actuator removed
from valve!
! CAUTION !
The following procedures must be com-
pleted before installing the stem connec-
tor (Key 22) between the actuator stem
(Key 3) and the valve stem (Key 31).
Except for the DFC Size 3220, the stem
connector assembly (Key 22) will need to
be installed to prevent the stem from
rotating while adjusting the bench set.
1 To properly verify bench setting 3 pieces of
information are required:
1Upper Bench Set Loading Pressure
2Lower Bench Set Loading Pressure
(example: on a 10-30 Psig bench set, 10
is the lower and 30 Psig is the upper)
3Travel
This information is available on the actuator
name plate (Key 33). If information is missing
or incomplete contact your Dyna-Flo Sales
Office.
2Before applying pressure to the actuator make
sure that the spring (Key 2) is properly seated
onto the spring seat (Key 20) (not required on
a new factory assembled actuator).
3Connect a supply line with a gauge that can
accurately measure both 0 Psi and the upper
bench set pressure.
4Apply maximum casing pressure to the
actuator to verify seal integrity is good. Use a
soapy and solution to check for any air leaks
from the lower casing gasket (Key 13) and the
diaphragm (Key 7). On a new actuator this will
have been done a tthe factory and won’t be
required.
Unpacking
Check the Packing List against materials recieved,
while unpacking the actuator. The Packing List
describes actuator and accessories in each shipping
container.
When lifting the actuator from the shipping contain-
er, it is advisable to remove 2 actuator casing bolts,
180oapart, and temporarily replace them with eye
bolts and nuts. Position the lifting straps through
the eye bolts to avoid damage to the tubing and
mounted accessories. See Figure 3.
Installation
! CAUTION !
Do not use an operating pressure that
exceeds the Maximum Diaphragm Casing
Pressure (See Table 1). Also make sure
that the operating pressure does not
create a force on the actuator stem that is
greater than the Maximum Allowable Out-
put Thrust (See Table 1)!
If the actuator has been installed on the valve in
the factory, the assembly is ready to be placed
inline. Refer to the proper Dyna-Flo valve manual
for installation. Refer to the “Mounting: Actuator to
Valve” section (Page) for detailed instructions on
Figure 2 Rigging Setup

Dyna-Flo Control Valve Services Ltd.
Edmonton, Alberta, CANADA
Website: www.dynaflo.com
Phone: 780 •469 •4000
Toll Free: 1 •866 •396 • 2356
Fax: 780 •469 •4035
Model
DFC Valve Actuator
Operation, Parts and Instruction Manuals
Instruction Manual May 2007
5
Rated Valve
Travel Scale
(Key 24)
Mark Upper
Bench Set
Loading
Pressure
Mark Lower
Bench Set
Loading
Pressure
Magnet/Ruler
Combination Setup Trave l
Indicator
Disk
(Key 27)
Travel Scale Adjusted
To Coincide With The
Travel Of The Travel
Indicator Disk After
Actuator Has Been
Mounted To Valve
Lower Bench
Set Loading
Pressure Mark
Upper Bench
Set Loading
Pressure Mark
*Note: Distance
of Travel Should
Match Specification
Given on Name Plate
(Key 33)
Figure 3 Bench Set Spring Adjustment Diagram
For Push Down to Close Valves
1Apply the upper bench set loading pressure
plus 5 Psi (34 kPa) to the actuator and note
where stem travel stops, this should occur
when the travel stop (Key 10) encounters the
upper casing (Key 5). The intent is for the travel
stop to contact the upper casing at the exact
time the upper bench set loading value is
reached. Apply 5 Psi (34 kPa) above and below
the upper bench set value to verify this.
(Example: for a 10-30 bench set the travel stop
should contact the upper casing at exactly 30
Psig) If stem (Key 3) travel stops before or
after the upper bench set value, the spring
adjuster (Key 21) will need to be adjusted to
obtain the proper bench set. You may need to
relieve pressure to the actuator in order to
adjust the spring adjuster. Turning the spring
adjuster up (towards the top of the actuator)
will increase the bench set pressure.
2Once the upper bench set pressure has been
set, use a magnet or piece of tape to attach
a piece of metal or ruler to the bottom of the
actuator stem (Key 3) to use as an indicator
arm. Make a mark to indicate the stem position
at the upper bench set pressure (See Figure 3).
Make sure the travel is fully extended.
3Adjust the gauge to the lower bench set
pressure and mark the actuator stem position.
The measurement between the upper and
lower bench set marks should equal the travel
indicated on the name-plate within 1/16” (1.6 mm).
!Note !
If these steps do not allow you to reach
the proper bench set pressure then an
incorrect or damaged spring may be the
problem. Contact your Dyna-Flo Sales
Office for more information.
Mounting: Actuator to Valve
! CAUTION !
During mounting the actuator stem and
valve stem could come into contact with
each other. Ensure that the valve stem is
pushed down before trying to install the
actuator, doing this will help to protect
the stem threads from getting damaged.
! CAUTION !
It may be necessary to apply loading
pressure to the actuator temporarily to
move the actuator stem and allow for
more clearance between it and the valve
stem. Use extreme caution when moving
the pressurized actuator; ensure that no
clothing, hair, hands or tools come in
between the two stems or moving parts.
If loading pressure fails personal injury or
property damage may occur.
1 Make sure the valve is securely supported
using a vice or similar method before proceed-
ing. It is advised to place valve on a surface
that will be able to support the combined
weight of valve and actuator.

Model
DFC Valve Actuator
Operation, Parts and Instruction Manuals
Dyna-Flo Control Valve Services Ltd.
Edmonton, Alberta, CANADA
Website: www.dynaflo.com
Phone: 780 •469 •4000
Toll Free: 1 •866 •396 • 2356
Fax: 780 •469 •4035
Instruction Manual May 2007
6
Mounting: Actuator to Valve
(cont’d)
2Make sure the stem is pushed down away from
the actuator. Thread the two nuts (Keys 28 &
29) all the way onto the valve stem. Install the
travel disk (Key 27) onto the valve stem
(concave side down) so that it rests on the jam
nuts. Note: with the travel disk on the stem it
may not be possible to mount the actuator
because the travel disk will not slide through
the yoke boss mounting area. Before attempt-
ing to mount the actuator check to see that the
disk will go through the yoke boss mounting
area. If not, the travel disk will need to be
inserted on the stem after the yoke nut (Key
27). Place the travel disk overtop of the yoke
nut during the yoke nut installation process.
3Be sure to have the yoke nut (Key 32) sitting
inside the actuator yoke or have the yoke nut
ready to be placed in between the actuator
stem and valve stem when lowering the
actuator onto the valve. Carefully lift and lower
the actuator onto the valve, this may require
more than one person or a heavy lifting device.
Once on the valve, orientate the actuator to be
properly aligned parallel with the valve body
(see Figure 5).
4Thread the yoke nut onto the valve bonnet and
tighten using a heavy blunted chisel and
hammer until the yoke is secured tightly to the
valve (Refer to Figure 4). DO NOT OVER
TIGHTEN.
Stem Connector Installation
1Apply upper loading pressure plus 5 Psi (34
kPa) to the actuator if loading pressure was not
applied prior to mounting. This should put the
the actuator in the fully up position.
2Install the travel scale (Key 24) to the actuator
using the speed nuts (Key 26) and machine
screws (Key 25). Position the travel disk (Key 27)
on top of the jam nuts at the bottom of the
travel scale (Key 24) by adjusting the jam nuts
(Keys 28 & 29). Carefully move the plug / stem
up until the travel disk indicates full travel as
indicated on the travel scale. The movement of
the plug / stem must be done with caution not
to damage the stem.
3As shown in Figure 3, the valve stem should fit
inside the actuator stem. Install the stem
connector (Key 22). It is important to position
the stem connector so that the threads
properly engage with those of the stems.
Connect the other half of the stem connector
and orientate the stem connector as show in
Figure 3. It is at this time that any accessories
(such as positioner arms) that need to be
connected to the stem connector should be
put in place. Install the stem connector bolts
and tighten.
4Re-position the travel disk (Key 27) under the
stem connector (Key 22), thread up the jam
nuts (Keys 28 & 29) to hold the travel disk in place
and tighten the jam nuts together (Refer to
Figure 3). Do not over tighten the jam nuts.
5Apply pressure and stroke the valve several
times. Loosen the travel scale (Key 24) and
reposition it to align with the closed position of
the valve and verify that the travel is still
accurate to the value indicated on the name
plate (Key 33). If travel is inaccurate it may be
necessary to repeat the stem connector
procedures or to refer back to Bench Setting
Actuator.
Figure 4 Yoke Nut Tightening

Dyna-Flo Control Valve Services Ltd.
Edmonton, Alberta, CANADA
Website: www.dynaflo.com
Phone: 780 •469 •4000
Toll Free: 1 •866 •396 • 2356
Fax: 780 •469 •4035
Model
DFC Valve Actuator
Operation, Parts and Instruction Manuals
Instruction Manual May 2007
7
Maintenance
! WARNING !
Disconnect all power lines and pneumatic
lines making sure the actuator is depres
surized prior to commencing disassembly.
Remove any power source that may cause
the actuator to spontaneously move. Also,
relieve any spring pressure or compres-
sion before you start the disassembly
process, this can be done by lowering the
spring adjuster (Key 21).
! CAUTION !
Use bypass valves or completely shut off
process media to isolate the valve from
the process pressure and fluids. Relieve
process pressure and drain process media
from both side of the valve.
Actuator Disassembly
1 Make sure that the valve and actuator are
securely supported and that valve body is
clamped in place and unable to move during
disassembly.
2Completely remove spring compression by
turning the spring adjuster (Key 21) until
loose. Once spring compression is removed
disassemble the stem connector (Key 22) and
remove both halves. Inspect all the threads on
both halves of the stem connector and make
sure there is no damage.
3If removal of the actuator from the valve is
necessary, the yoke nut (Key 32) will need to be
completely loosened. Using a heavy blunted
chisel and hammer, completely loosen the yoke
nut (Key 32) (Refer to Figure 4). Note: the yoke
nut will not be able to be removed until the
actuator is lifted from the valve (Refer to Un-
packing and Mounting sections for actuator
hoisting instructions).
4Before work begins make sure that the
actuator is secured in place and properly
supported.
Spring removal
1Unscrew the spring adjuster (Key 21) and
remove it from the actuator stem. With the
spring adjuster removed it is possible to re
move the spring seat (Key 20) from the yoke
(Key 1). Inspect the threads of the spring
adjuster and for damage and corrosion. Also,
inspect the spring.
Upper Diaphragm Casing Disassembly
1Remove all the diaphragm casing cap screws
(Key 18) and nuts (Key 19). Lift the upper
diaphragm casing (Key 5) from the actuator.
2From the top of the open actuator remove the
hex head bolt (Key 11) and travel stop (Key 10).
The actuator stem (Key 3) may rotate
during hex head bolt removal, it may be
necessary to hold the stem or tap the wrench
with a hammer to loosen the bolt. Use extreme
caution and avoid damaging the actuator stem
during this process. Remove the stem from the
yoke mounting end.
3Being careful not to damage the actuator stem
(Key 3) remove it from the actuator. Inspect
the actuator stem for thread damage, deep
scratches and corrosion. Minor scratches and
corrosion can be polished out (scratches that
will not stop your fingernail are considered
minor), if there are deep scratches, corro-
sion or damage the actuator stem will need to
be replaced.
4Remove the upper diaphragm plate (Key 8)
from the actuator and diaphragm (Key 7),
inspect the plate for cracks and wear. Note: on
older actuators the upper diaphragm plate
maybe composed of two separate pieces.
Inspect the diaphragm for tears, abnormal
stretching, cracks and pliability. If the dia-
phragm is brittle, torn or cracked it will need to
be replaced.
5Remove the lower diaphragm plate and inspect
it for any cracks, wear or corrosion.
6Using a pair of pliers or other tool, remove the
snap ring (Key 14) from the yoke (it sits overtop
of the bushing (Key 15). Replace if necessary.

Model
DFC Valve Actuator
Operation, Parts and Instruction Manuals
Dyna-Flo Control Valve Services Ltd.
Edmonton, Alberta, CANADA
Website: www.dynaflo.com
Phone: 780 •469 •4000
Toll Free: 1 •866 •396 • 2356
Fax: 780 •469 •4035
Instruction Manual May 2007
8
Maintenance
(cont’d)
Upper Diaphragm Casing Disassembly
(cont’d)
7Remove the bushing (Key 15) from the actua-
tor being careful not to damage the bushing,
seals or actuator yoke. The actuator stem
(Key 3) and spring adjuster (Key 21) may be
used with extreme caution to remove the
bushing. By threading the spring adjuster part
way onto the actuator stem the assembly may
be inserted up into the yoke and used as a
plunger to push out the bushing.
8Using a pick set or small screwdriver, remove
the o-rings (Keys 16 & 17) from the bushing
being careful not to damage bushing surfaces.
Inspect the sealing surfaces of the bushing for
deep scratches and corrosion, replace if nec-
essary. O-rings and gaskets should normally be
replaced during maintenance.
Lower Diaphragm Casing Removal
1 Remove the lower diaphragm casing cap
screws (Key 18) and lift lower diaphragm casing
(Key 4) off of the yoke (Key 1). Remove the
lower casing gasket (Key 13) clean and inspect
the yoke / lower casing sealing surfaces for
damage. O-rings and gaskets should be re
placed during maintenance.
! NOTICE !
For the DFC Size 3220 inspect the o-ring
groove on the top surface of the yoke
(Key 1) for any deep scratching or corro-
sion. Also check the lower diaphragm
casing (Key 4) for any deformation exces-
sive tightening may have caused. O-rings
and gaskets should be replaced during
maintenance.
Actuator Assembly
! CAUTION !
Before assembling the actuator, make
sure that the yoke and actuator are
securely supported with a clamping device
and on a surface that will support the
assembled actuator weight.
! NOTICE !
Use an anti-seize compound that is
approved for the service conditions that
the actuator is being installed into.
Lower Diaphragm Casing
Bushing Installation
1 Coat the lower diaphragm gasket (Key 13) with
anti-seize compound and place on to the yoke
(Key 1) (on a DFC size 3220 actuator there is
an o-ring in place of the gasket). The holes of
the gasket should align with the holes on the
yoke.
2Install the lower diaphragm casing (Key 4),
tighten cap screws (Key 12) using a criss-cross
pattern. DO NOT over tighten the cap screws
as excessive tightening could warp the casing
or deflect and cause the gasket to leak.
3Lubricate the bushing seals (Keys 16 & 17) with
silicone-based lubricant and place them into
the bushing (Key 15) as shown in Figure 6. Pack
the inside of the bushing with lubricant
(Lubriplate®Mag-1 or equivalent) and insert the
bushing into the yoke (Key 1). The bushing is
held in place with the snap ring (Key 14) that
fits into the groove in the yoke above the
bushing (Refer to Figure 6).
Spring Installation
! NOTICE !
It may be desirable to have an appro-
priately sized block of wood nearby to be
placed in the bottom of the yoke to be
used as support for the stem/spring
assembly while working on the actuator.
1 Coat the stem (Key 3) threads with anti-seize
compound and thread the spring adjuster (Key
21) onto the stem. Place the spring seat (Key
20) onto the stem so that it rests on the spring
adjuster as show in Figure 7.
2Insert the spring (Key 2) into the barrel on the
yoke (Key 1) and slide stem assembly from
Step 1 into the yoke. It may be necessary to
support the spring/stem assembly using a
block of wood or similar item while assembling
the upper portion of the actuator.

Dyna-Flo Control Valve Services Ltd.
Edmonton, Alberta, CANADA
Website: www.dynaflo.com
Phone: 780 •469 •4000
Toll Free: 1 •866 •396 • 2356
Fax: 780 •469 •4035
Model
DFC Valve Actuator
Operation, Parts and Instruction Manuals
Instruction Manual May 2007
9
Maintenance
(cont’d)
Upper Diaphragm Casing Assembly
1Place the lower diaphragm plate (Key 6) into
the lower diaphragm casing (Key 4) and onto
the actuator stem (Key 3) as shown in
Figure 7. Insert the diaphragm (Key 7) into the
lower casing over the lower diaphragm plate
and align the holes on the diaphragm with
those of the lower casing.
2Install the upper diaphragm plate (Key 8) onto
the actuator stem so that it rests in the dia-
phragm (for a two piece diaphragm plate
design both parts of the plate will need to be
installed Figure 6 Key 9).
3Place the travel stop (Key 10) over the actuator
stem so that it rests on the upper diaphragm
plate. Coat the threads of the hex head bolt
with anti-seize and thread it into the top of
the actuator stem (Key 3), tighten the hex
head bolt completely making sure that the
holes on the diaphragm still align with those of
the lower casing (Refer to Torque Chart on
Page 11).
4Lift and place the upper diaphragm casing (Key
5) onto the top of the actuator, make sure that
the holes of the upper casing align with those
of the lower casing (Key 4) and diaphragm
(Key 7). Install the casing cap screws (Key 18)
into the casings, Do Not coat the cap screws
with anti-seize. Thread the nuts (Key 19) onto
the casing cap screws, Do Not over tighten the
cap screws refer to Torque Chart on Page 11.
Tighten the casing cap screws in a crisscross
pattern to half required torque and in the
same pattern completely tighten cap screws to
full torque. In a circular pattern re-tighten the
casing cap screws (Key 18) to full torque.
5Refer to Bench Setting Actuator portion of
manual to complete the actuator assembly.
32
33
Figure 5 Actuator & Valve Mounting Diagram

Model
DFC Valve Actuator
Operation, Parts and Instruction Manuals
Dyna-Flo Control Valve Services Ltd.
Edmonton, Alberta, CANADA
Website: www.dynaflo.com
Phone: 780 •469 •4000
Toll Free: 1 •866 •396 • 2356
Fax: 780 •469 •4035
Instruction Manual May 2007
10
Casing-Mounted Travel Stops
! NOTICE !
For casing-mounted travel stop options
refer to Figure 8. These options are avail-
able to limit travel in both down and up
directions.
Adjusting Casing-Mounted Travel Stops
1 Remove the travel stop caps (Key 34, Types 3
& 4) and loosen jam nuts (Key 40) if they
impede adjustments in Step 2.
2Use the jam nuts (Key 40, Type 3), the exten-
sion stem (Key 39, Type 4) and travel stop
screw (Key 37, Type 5) to adjust the travel
limit.
3After adjustments have been made, it will be
necessary to re-tighten the jam nuts (Key 40)
and replace the travel stop caps (Key 34, Types
3 & 4).
Casing-Mounted Travel Stop Disassembly
! NOTICE !
For maintenance purposes it is only neces-
sary to disassemble the travel stops as far
as need be to accomplish the required
maintenance.
1 Remove the travel stop cap (Key 34). For down
travel stops (Type 3) the jam nuts (Key 40)
must be loosened so that the travel stop is not
causing any spring compression.
! WARNING !
Disconnect all power lines and pneumatic
lines making sure the actuator is depres-
surized prior to commencing disassembly.
Remove any power source that may cause
the actuator to spontaneously move. For
down travel stops relieve any spring
pressure or compression before you start
the disassembly process, this can be done
by lowering the spring adjuster (Key 21).
! CAUTION !
Use bypass valves or completely shut off
process media to isolate the valve from
the process pressure and fluids. Remove
any tubing or piping from the connection
on top of the yoke (Key 32).
2 Using a wrench on the jam nuts (Key 40) un-
screw the extension stem (Key 39) and remove
it. Inspect the extension stem for damage or
corrosion, replace if necessary.
3 Remove all the diaphragm casing cap screws
(Key 18) and nuts (Key 19). Lift the upper dia-
phragm casing (Key 5) from the actuator. For
Types 3 and 4 the travel stop assembly will be
removed with the upper diaphragm casing.
4 Record the position of the travel stop (Key 36)
compared to the cap screws (Key 42) for reas-
sembly purposes. Remove the travel stop and
cap screws.
5 Inspect all travel stop parts for damage or
corrosion and replace if necessary.
Casing-Mounted Travel Stop Assembly
1 Reassembly the actuator parts in reverse order
starting at Step 4 of the Casing-Mounted Travel
Stop Disassembly, be sure to apply anti-seize
compound to the threads of the extension
stem (Key 39). Return the cap screws (Key 42)
and travel stop (Key 36) to their original posi-
tion as recorded in Step 4. Refer to the Upper
Diaphragm Casing Assembly procedures on
Page for instruction on casing reassembly.
2 Retighten the spring adjuster (Key 21) to its
original position and adjust the travel stops to
their desired limits as per Adjusting Casing-
Mounted Travel Stop procedures.

Dyna-Flo Control Valve Services Ltd.
Edmonton, Alberta, CANADA
Website: www.dynaflo.com
Phone: 780 •469 •4000
Toll Free: 1 •866 •396 • 2356
Fax: 780 •469 •4035
Model
DFC Valve Actuator
Operation, Parts and Instruction Manuals
Instruction Manual May 2007
11
Our Commitment of Quality
Dyna-Flo is committed to continuous improvement. All efforts have been taken to maximize the accuracy of this
information. Without notification, product specifications and designs may be modified at any time. The issue of this
document is for information only, and does not imply suitability, a warranty, or guarantee for a specific service.
9
14
16
16
17
13
Lubriplate® Mag-1
or equivalent
Figure 6 Model DFC Actuator Cross Section (2 Piece Diaphragm Plate Design)
Table 2
Model DFC Actuator Torque Chart
Actuator Stem Hex Head Bolt Torque (Key 11)
Actuator Size Ft-lbs. N•m
1069 30 41
2069 50 68
2105, 2156, 3105, 3156, 3220 135 183
Casing Cap Screws Torque (Keys 19 & 20)
All Sizes Ft-lbs. N•m
Full Torque 20 27

Model
DFC Valve Actuator
Operation, Parts and Instruction Manuals
Dyna-Flo Control Valve Services Ltd.
Edmonton, Alberta, CANADA
Website: www.dynaflo.com
Phone: 780 •469 •4000
Toll Free: 1 •866 •396 • 2356
Fax: 780 •469 •4035
Instruction Manual May 2007
12
30
5
18
19
4
12
17
16
3
1
21
22
23
29
31
28
26
24
20
2
15
16
14
6
8
7
10
11
13
25
27 *
*
* Note: part of valve
body assembly.
*
Figure 7 Model DFC Actuator Cross Section

Dyna-Flo Control Valve Services Ltd.
Edmonton, Alberta, CANADA
Website: www.dynaflo.com
Phone: 780 •469 •4000
Toll Free: 1 •866 •396 • 2356
Fax: 780 •469 •4035
Model
DFC Valve Actuator
Operation, Parts and Instruction Manuals
Instruction Manual May 2007
13
TYPE 4
UP STOP DFC
TYPE 5
UP STOP DFC
TYPE 3
DOWN STOP DFC
34
35
39
40
44
36
42
43
41
34
39
44
38
42
35
5
37
40
Figure 8 Model DFC Actuator Cross Section

Model
DFC Valve Actuator
Operation, Parts and Instruction Manuals
Dyna-Flo Control Valve Services Ltd.
Edmonton, Alberta, CANADA
Website: www.dynaflo.com
Phone: 780 •469 •4000
Toll Free: 1 •866 •396 • 2356
Fax: 780 •469 •4035
Instruction Manual May 2007
9 Upper Diaphragm Plate (2 Piece Design)
Zinc Plated Steel
10 Travel Stop
Steel
(See Table 3, Page 17)
11 Actuator Stem Hex Head Bolt
Zinc Plated Steel
(See Table 3, Page 17)
12 Hex Head Cap Screw
Zinc Plated Steel
Size 1069 & 2069 (Qty. 6) H5CZ38.034
Size 2105, 2156, H5CZ38.034
3105, 3156
(Qty. 8)
Size 3220 (Qty. 12) H5CZ12.100
13 Gasket
Composition
Size 1069 & 2069 1E80120402D
Sizes 2105, 2156, 1E84540402D
3105,3156
Size 3220 (O-Ring Nitrile) 1D26910699D
14 Snap Ring
SST
Size 1069 & 2069 1E80133702D
Size 2105, 2156, 1E84563899D
3105, 3156, 3220
15 Bushing
Brass
Size 1069 & 2069 1E68281401D
Size 2105, 2156, 1E84571401D
3105, 3156
Size 3220 1N1316X005D
16 O-Ring
Buna (Qty. 2)
Size 1069 & 2069 1D23750699D
Size 2105, 2156, 1C56220699D
3105, 3156
Size 3220 1E73690699D
17 O-Ring
Buna
Size 1069 & 2069 1C41570699D
Size 2105, 2156, 1E84580699D
3105, 3156, 3220
18 Hex Head Cap Screw (casing)
Zinc Plated Steel
Size 1069 & 2069 (Qty. 16) H5FZ38.100
Size 2105 & 3105 (Qty. 20) H5FZ38.100
Size 2156 & 3156 (Qty. 24) H5FZ38.100
Size 3220 (Qty. 28) H5FZ38.114
Parts
Key Description Part Number
1 Yoke
Cast Iron
Size 1069 3E88461904D
Size 2069 3E82081904D
Size 2105 & 2156 3E90081904D
Size 3105 & 3156 3E84591904D
Size 3220 3N13031904D
2 Spring
Steel
(See Table 4, Page 18)
3 Stem
17-4
Size 1069 3E8847X174D
Size 2069 2E8209X174D
Size 2105 & 2156 2J3328X174D
Size 3105 & 3156 2E8461X174D
Size 3220 2N13172174D
Size 3220-4 21A3812X01D
4 Lower Diaphragm Casing
Steel
Size 1069 & 2069 2E68262506D
Size 2105 & 3105 3E84532506D
Size 2156 & 3156 3E84772506D
Size 3220 & 3220-4 2N13102506D
5 Upper Diaphragm Casing
Steel
Size 1069 & 2069 2E68142899D
Size 2105 & 3105 3E84462899D
Size 2156 & 3156 3E84672899D
Size 3220 2N12782899D
6 Lower Diaphragm Plate
Steel
Size 1069 & 2069 1F88582409D
Size 2105, 2156, 1F89094402D
3105, 3156
Size 3220 1N13152409D
7 Diaphragm
Nitrile / Nylon
Size 1069 & 2069 2E66990220D
Size 2105 & 3105 2E85960220D
Size 2156 & 3156 2E85980220D
Size 3220 2N13090220D
8 Upper Diaphragm Plate
Cast Iron
Size 1069 & 2069 31B2029904D
Size 2105 & 3105 41B2030904D
Size 2156 & 3156 2E84751904D
Size 3220 2N12701904D
14

Dyna-Flo Control Valve Services Ltd.
Edmonton, Alberta, CANADA
Website: www.dynaflo.com
Phone: 780 •469 •4000
Toll Free: 1 •866 •396 • 2356
Fax: 780 •469 •4035
Model
DFC Valve Actuator
Operation, Parts and Instruction Manuals
Instruction Manual May 2007
Size 2069, 2105, 2156 1A41322412D
Size 3105, 3156, 3220 1A37542412D
29 Jam Nut
Steel Pl.
Size 1069 1P13122414D
Size 2069, 2105, 2156 1A35372412D
Size 3105, 3156, 3220 1A35112412D
30 Vent Cap
Plastic Y602-1BD
31 Valve Stem
32 Yoke Nut
33 Actuator Name Plate
34 Travel Stop Cap
Brass
Type3
Size 1069 & 2069 1F59781401D
Size 2105, 2156, 1H11111401D
3105, 3156
Size 3220 1R38761401D
Type 4
Size 1069 & 2069 1F59781401D
Size 2105, 2156, 1F83961401D
3105, 3156
Size 3220 1R38761401D
Steel
Type 4
Size 1069 & 2069 1F59782409D
35 Travel Stop Body
Cast Iron
Type 3
Size 1069 & 2069 1K72351901D
Size 2105, 2156, 2K72301901D
3105, 3156
Size 3220 2U14181902D
Type 4
Size 1069 & 2069 37A9437X01D
Size 2105, 2156, 37A9432X01D
3105, 3156
Size 3220 37A9661X01D
36 Casing-Mounted Travel Stop
Steel
(See Table 5, Page 19)
15
Parts
Key Description Part Number
19 Hex Nut (casing)
Zinc Plated Steel
Size 1069 & 2069 (Qty. 16) NHFZ38
Size 2105 & 3105 (Qty. 20) NHFZ38
Size 2156 & 3156 (Qty. 24) NHFZ38
Size 3220 (Qty. 28) NHFZ38
20 Spring Seat
Steel Pl.
Size 1069 & 2069 1R17992312D
Size 2105, 2156, 1R18002312D
3105, 3156
3220 1N12961905D
21 Spring Adjuster
Steel Pl.
Size 1069 & 2069 1E82102410D
Size 2105, 2156, 1E84622410D
3105, 3156
Size 3220 1N13181X01D
22 Stem Connector Assembly
Steel Pl.
Size 1069 18A1243X01D
Size 2069 18A1668X01D
Size 2105 & 2156 18A1671X01D
Size 3105 & 3156 18A1672X01D
Size 3220 18A1675X01D
23 Stem Connector bolt
Part of Stem Connector Assembly (Qty. 2)
24 Travel Scale
SST
(See Table 3, Page 17)
25 Machine Screw
SST (Qty. 2)
Size 1069, 2069, 2105, 2156 1E79323899D
Size 3105, 3156, 3220 1E83133899D
26 Speed Nut
SST (Qty. 2) 242-206
27 Travel Disk
SST
Size 1069 1E79313899D
Size 2069, 2105, 2156 1E80753899D
Size 3105 & 3156 1E83283899D
Size 3220 1B97183899D
28 Stem Nut
Steel Pl.
Size 1069 1P13122414D

Model
DFC Valve Actuator
Operation, Parts and Instruction Manuals
Dyna-Flo Control Valve Services Ltd.
Edmonton, Alberta, CANADA
Website: www.dynaflo.com
Phone: 780 •469 •4000
Toll Free: 1 •866 •396 • 2356
Fax: 780 •469 •4035
Instruction Manual May 2007
43 Lock Washer
Steel
Size 1069 & 2069 1A48782899D
Size 2105, 2156, 1A87322899D
3105, 3156
Size 3220 1A54932898D
44 Elbow Vent
Plastic
Size 1069, 2069, 2105, 27A5516X01D
2156, 3105, 3156
Size 3220 17A6572X02D
Parts
Key Description Part Number
37 Travel Stop Screw
Steel
Type 5
Size 1069 & 2069 1F75373513D
Size 2105, 2156, 1K13113513D
3105, 3156
Size 3220 13A2133X01D
38 Travel Stop Nut
Brass
Type 4
Size 1069 & 2069 18A2303X01D
Size 2105, 2156, 18A1272X01D
3105, 3156
39 Extension Rod (Stem)
Steel
Type 3
Size 1069 & 2069 1F75363503D
Size 2105, 2156, 1J23273503D
3105, 3156
Size 3220 1V7764X00AD
Bronze
Type 4
Size 1069 & 2069 27A9655X01D
Size 2105, 2156, 27A9656X01D
3105, 3156
Size 3220 27A9763X01D
40 Hex Head Jam Nut
Zinc Plated Steel
Size 1069 & 2069 1A35372412D
Size 2105, 2156, 1A35112412D
3105, 3156, 3220
41 Hex Nut
Zinc Plated Steel
Type 3
Size 1069 & 2069 1A41322412D
Size 2105, 2156, 1A37542412D
3105, 3156, 3220
42 Hex Head Cap Screw
Zinc Plated Steel
Type 3
Size 1069, 2069, 2105, 1A36842405D
2156, 3105, 3156
Size 3220 1N12932899D
Type 4
Size 1069, 2069, 2105 1A36842405D
2105, 2156, 3105, 3156
16

Dyna-Flo Control Valve Services Ltd.
Edmonton, Alberta, CANADA
Website: www.dynaflo.com
Phone: 780 •469 •4000
Toll Free: 1 •866 •396 • 2356
Fax: 780 •469 •4035
Model
DFC Valve Actuator
Operation, Parts and Instruction Manuals
Instruction Manual May 2007
17
Table 3
Keys 10, 11 & 24 Actuator Stem Hex Head Bolt, Travel Stop and Travel Scale
Actuator Size Travel inch (mm) Hex Head Bolt Travel Stop Travel Scale
1069
3/4 (19) 1R4089X004D 1R40952409D 1E79363999D
1-1/8 (29) 1R4091X003D 1R40962409D 17A9814X01D
2069
3/4 (19) 1R4089X004D 1R40952409D 1E80813899D
1-1/8 (29) 1R4091X003D 1R40962409D 1E80823899D
1-1/2 (38) 1R4092X002D 1R40972409D 1E80833899D
2105
3/4 (19) 1R4098X002D 1R41052409D 1E80813899D
1-1/8 (29) 1R4099X002D 1R41082409D 1E80823899D
1-1/2 (38) 1R4101X002D 1R41062409D 1E80833899D
2 (51) 1R4102X001D 1R41072409D 1R44453898D
2156
3/4 (19) 1R4098X002D 1R41052409D 1E80813899D
1-1/8 (29) 1R4099X002D 1R41082409D 1E80823899D
1-1/2 (38) 1R4101X002D 1R41062409D 1E80833899D
2 (51) 1R4102X001D 1R41072409D 1R44453898D
3105
3/4 (19) 1R4098X002D 1R41052409D 1E83313899D
1-1/8 (29) 1R4099X002D 1R41082409D 1E83323899D
1-1/2 (38) 1R4101X002D 1R41062409D 1E83333899D
2 (51) 1R4102X001D 1R41072409D 1E83343899D
3156
3/4 (19) 1R4098X002D 1R41052409D 1E83313899D
1-1/8 (29) 1R4099X002D 1R41082409D 1E83323899D
1-1/2 (38) 1R4101X002D 1R41062409D 1E83333899D
2 (51) 1R4102X001D 1R41072409D 1E83343899D
3220
3/4 (19) 1R4110X001D 1R41162409D 1H74573899D
1-1/8 (29) 1R4110X001D 1R41152409D 1H74583899D
1-1/2 (38) 1R4098X002D 1R41142409D 1H74593899D
2 (51) 1R4099X002D 1R41132409D 1H74603899D
3 (76) 1R4102X001D 1R41072409D 1H74613899D

Model
DFC Valve Actuator
Operation, Parts and Instruction Manuals
Dyna-Flo Control Valve Services Ltd.
Edmonton, Alberta, CANADA
Website: www.dynaflo.com
Phone: 780 •469 •4000
Toll Free: 1 •866 •396 • 2356
Fax: 780 •469 •4035
Instruction Manual May 2007
18
Table 4
Key 2 Actuator Spring Chart
Actuator Size Travel inch (mm)
Diaphragm Pressure Range Psig (kPag)
3-15 (21-103) 6-30 (41-207)
1069
3/4 (19) 1E80582708D (light grey) 1E80522708D (orange & red)
1-1/8 (29) 1E80532709D (dark grey) 1E80552708D (dark blue)
2069
3/4 (19) 1E80582708D (light grey) 1E80522708D (orange & red)
1-1/8 (29) 1E80532709D (dark grey) 1E80552708D (dark blue)
1-1/2 (38) 1E80562709D (dark green) 1E80582708D (light grey)
2105
3/4 (19) 1E82622708D (light green) 1E82552708D (aluminum & red)
1-1/8 (29) 1E82612708D (dark grey) 1E82642708D (light grey)
1-1/2 (38) 1E82662708D (orange) 1E82622708D (light green)
2 (51) 1E82692708D (dark green) 1E82652708D (red)
2156
3/4 (19) 1E82572708D (brown) 1E82602708D (bronze)
1-1/8 (29) 1E82622708D (light green) 1E82552708D (aluminum & red)
1-1/2 (38) 1E82652708D (red) 1E82572708D (brown)
2 (51) 1E82702708D
(aluminum & dark blue)
1E82632708D
(aluminum & dark green)
3105
3/4 (19) 1E82622708D (light green) 1E82552708D (aluminum & red)
1-1/8 (29) 1E82612708D (dark grey) 1E82642708D (light grey)
1-1/2 (38) 1E82662708D (orange) 1E82622708D (light green)
2 (51) 1E82692708D (dark green) 1E82652708D (red)
3156
3/4 (19) 1E82572708D (brown) 1E82602708D (bronze)
1-1/8 (29) 1E82622708D (light green) 1E82552708D (aluminum & red)
1-1/2 (38) 1E82652708D (red) 1E82572708D (brown)
2 (51) 1E82702708D
(aluminum & dark blue)
1E82632708D
(aluminum & dark green)
3220
3/4 (19) 1N12792708D (red) ---
1-1/8 (29) 1N71932708D (white) 1N12812708D (brown)
1-1/2 (38) 1N12872708D (yellow) 1N12792708D (red)
2 (51) 1N12842708D (light green) 1N12852708D (light blue)
3 (76) 1N12862708D (dark grey) 1N12872708D (yellow)

Dyna-Flo Control Valve Services Ltd.
Edmonton, Alberta, CANADA
Website: www.dynaflo.com
Phone: 780 •469 •4000
Toll Free: 1 •866 •396 • 2356
Fax: 780 •469 •4035
Model
DFC Valve Actuator
Operation, Parts and Instruction Manuals
Instruction Manual May 2007
19
Table 5
Key 36 Casing-Mounted Travel Stop (Type 3)
Actuator Size Travel inch (mm) Travel Stop
1069
3/4 (19) 1E80662409D (Qty: 4)
1-1/8 (29) 1E80672409D (Qty: 4)
2069
3/4 (19) 1E80662409D (Qty: 4)
1-1/8 (29) 1E80672409D (Qty: 4)
1-1/2 (38) 1E80682409D (Qty: 4)
2105
3/4 (19) 1E83192409D (Qty: 4)
1-1/8 (29) 1E83192409D (Qty: 4)
1-1/2 (38) 1E80642409D (Qty: 4)
2 (51) 1E83212409D (Qty: 4)
2156
3/4 (19) 1E83192409D (Qty: 4)
1-1/8 (29) 1E83192409D (Qty: 4)
1-1/2 (38) 1E80642409D (Qty: 4)
2 (51) 1E83212409D (Qty: 4)
3105
3/4 (19) 1E83192409D (Qty: 4)
1-1/8 (29) 1E83192409D (Qty: 4)
1-1/2 (38) 1E80642409D (Qty: 4)
2 (51) 1E83212409D (Qty: 4)
3156
3/4 (19) 1E83192409D (Qty: 4)
1-1/8 (29) 1E83192409D (Qty: 4)
1-1/2 (38) 1E80642409D (Qty: 4)
2 (51) 1E83212409D (Qty: 4)
3220
3/4 (19) 1N12882409D (Qty: 3)
1-1/8 (29) 1N12892409D (Qty: 3)
1-1/2 (38) 1N12902409D (Qty: 3)
2 (51) 1N12914092D (Qty: 3)
3 (76) 1N12922409D (Qty: 3)
3220-4 4 (102) 11A8131X01D (Qty: 3)

Model
DFC Valve Actuator
Operation, Parts and Instruction Manuals
Dyna-Flo Control Valve Services Ltd.
Edmonton, Alberta, CANADA
Website: www.dynaflo.com
Phone: 780 •469 •4000
Toll Free: 1 •866 •396 • 2356
Fax: 780 •469 •4035
Instruction Manual May 2007
20
Ordering Guide
Dyna-Flo DFC / DFO Series Actuators | Model Numbering System
Sample Part Number
DFC - 2 069 - B H N - X
Denotes Special Construction
XSpecial (Consult Dyna-Flo Sales Office)
Options
NNone (Standard)
Bench Range, psig
FAIL CLOSED FAIL OPEN
A3 - 15 H6 - 30 A3 - 15 H6 - 30
B4 - 15 Y8 - 30 B3 - 14 I 6 - 28
C5 - 15 I 9 - 30 C3 - 13 J 6 - 27
D6 - 15 J 10 - 30 D3 - 12 K6 - 26
E7 - 15 K12 - 30 E3 - 11 L6 - 24
F8 - 15 L14 - 30 F3 - 10 M6 - 22
U9 - 15 M15 - 30 G3 - 8 N6 - 21
G10 - 15 N16 - 30 O6 - 20
V11 - 15 O17 - 30 XSpecial P6 - 19
P18 - 30 Q6 - 18
XSpecial Q19 - 30 R6 - 17
R20 - 30 S6 - 16
S21 - 30 T 6 - 15
T 22 - 30
Travel, Inch
A3/4 D2G3-1/2
B1-1/8 E2-1/2
C1-1/2 F3
XSpecial Travel
Actuator Size, in2
156 156
069 69
220 220
105 105
Valve Mounting Connection, Inch
12-1/8
22-13/16
33-9/16
Action
CFail Closed OFail Open
X
N
H
B
069
2
C
W14 - 26
SSide Mounted Handwheel
TTop Mounted Handwheel
1Type 1 Up Stop - DFO
2Type 2 Down Stop - DFO
3Type 3 Down Stop - DFC
4Type 4 Up Stop - DFC
5Type 5 Up Stop - DFC
This manual suits for next models
1
Other Dyna-Flo Controllers manuals
Popular Controllers manuals by other brands

ESI
ESI MoCo user guide
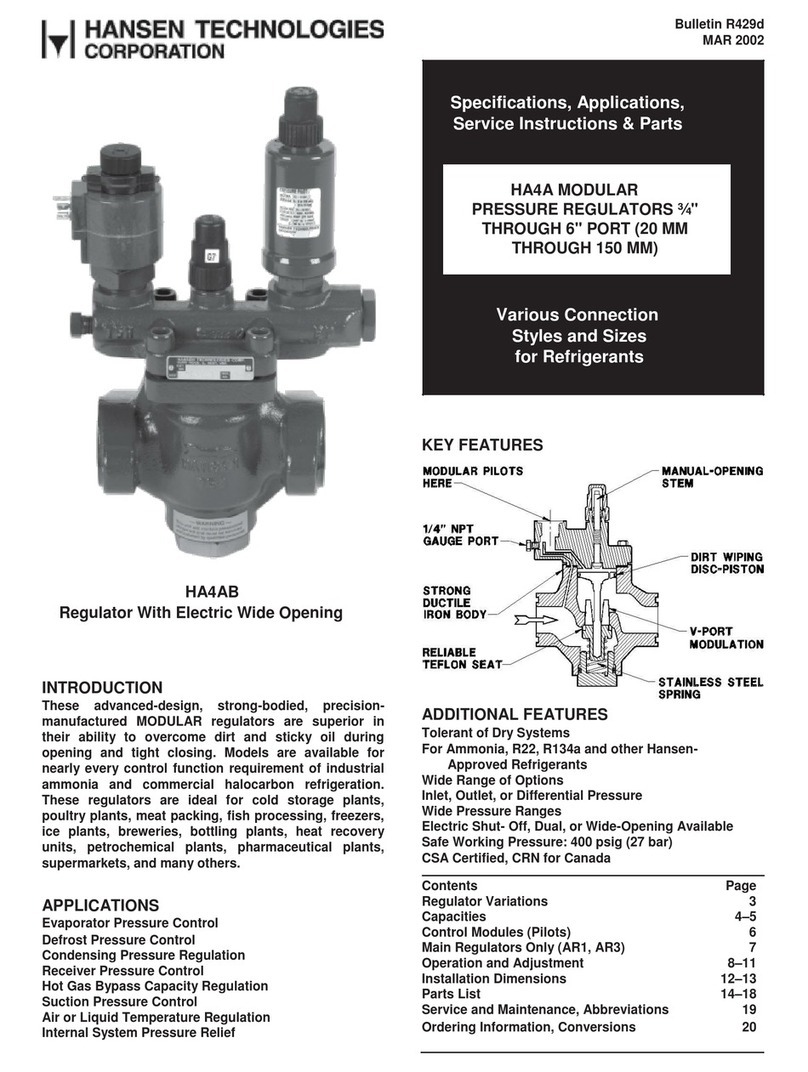
Hansen
Hansen HA4A series Specifications, Applications, Service Instructions & Parts

Morningstar
Morningstar SunSaver SS-6 Operator's manual
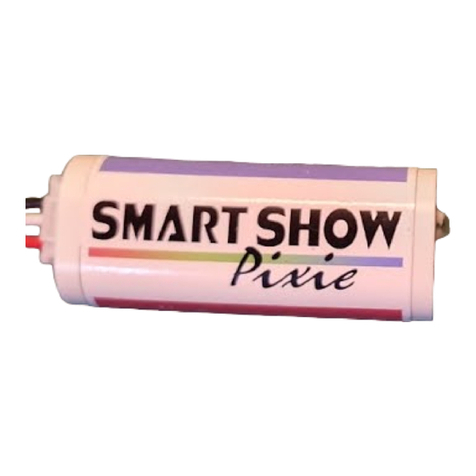
SMART SHOW
SMART SHOW Pixie Installation & use
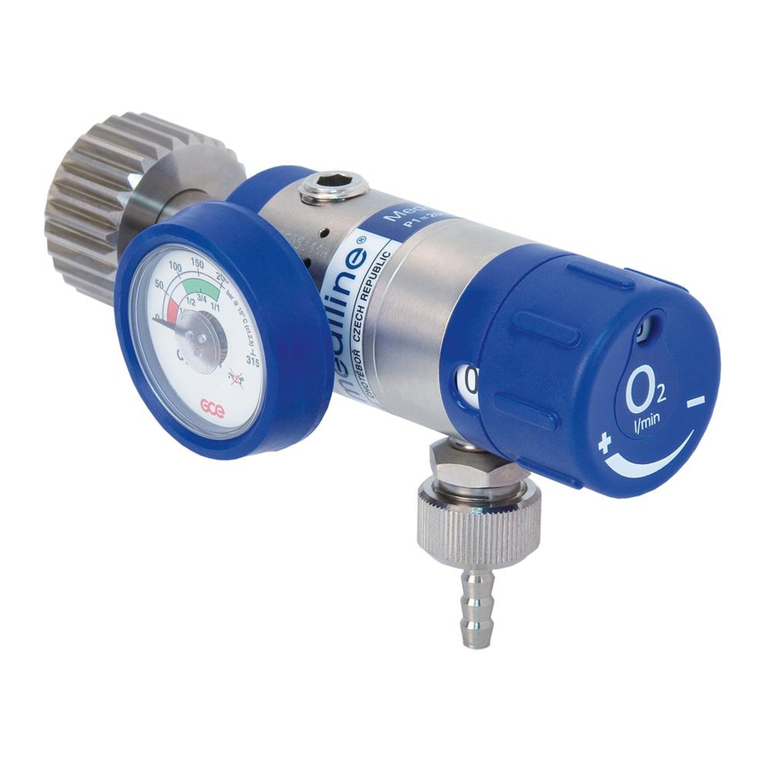
gce mediline
gce mediline MEDIREG II Instructions for use

Samson
Samson 4765 Mounting and operating instructions