Dynamatic CES User manual

DANGER HIGH VOLTAGE
Motor control equipment and controllers are connected
to hazardous line voltage. When servicing drives and
electronic controllers, there may be exposed
components with their cases and protrusions at or above
line potential. Extreme care should be taken to protect
against shock. Stand on an insulating pad and make it a
habit to use only one hand when checking Components.
Always work with another person in case an emergency
occurs. Disconnect power whenever possible to check
controllers or to perform maintenance. Be sure
equipment is properly grounded. Wear safety glasses
whenever working on an electronic controller or electrical
rotating equipment.
CAUTION
Rotating shafts and above ground electrical potentials
can be hazardous. Therefore, it is strongly
recommended that all electrical work conform to National
Electrical Codes and local regulations. Installation,
alignment and maintenance should be performed only by
qualified personnel.
Factory recommended test procedures, included in the
instruction manual, should be followed. Always
disconnect electrical power before working on the unit
REFER TO OSHA RULES AND REGULATIONS.
PARAGRAPH 1910.219 FOR GUARDS ON
MECHANICAL POWER TRANSMISSION APPARATUS.
NOTE:
Since improvements are continually being made to
available equipment, the enclosed data is subject to
change without notice. Any drawings are for reference
only, unless certified. For additional information contact
your nearest Eddy Current Representative listed in the
Yellow pages under “Power Transmission Equipment”.
Or you can call DSI/Dynamatic® at 1-800/548-2169.
IMPORTANT NOTICE
The printed contents in this manual are to be used for
reference only. Due to periodic engineering design
changes and the addition of modifications, this material
is provided as a guide only.
Refer to engineering drawings for your specific unit. If
you do not have your units engineered drawings, please
contact the publications department at the factory.
For additional information regarding contents, direct your
request to one of the following areas:
Instruction Material Sales/Marketing
Technical/Operational Questions Engineering
Parts/Order Inquiry Customer Service
This notice is provided to clarify the Intent of the
instruction book contents and to inform our customers
how to obtain appropriate technical assistance from the
proper source.
©Copyright DSI/Dynamatic®, 2002

TABLE OF CONTENTS
SECTION 1 - GENERAL INFORMATION Page No.
Introduction 4
Safety 4
Training 4
Receiving and Damage Claims 4
Warranty 4
Handling 4
Storage 5
Long Term Storage 5
Removing from Storage 5
Electrical Part Numbering System 5
Category Number and Description 5
Symbols Used in Illustrations 7
SECTION 2 - GENERAL DESCRIPTION
Construction 8
CES Controller 8
Specifications 8
Power Circuitry 8
Keypad Programming 9
Field Adjustments 9
Light Emitting Diode (LED) Indicators 9
Press Speed Control 9
Angle Measurement 9
CES Digital Master Regulator (DMR) 10
Press Control Interface - Commands Accepted 11
Press Control Interface - Output Signals 12
Press Control Interface – Serial 13
Signals for Customer's Recorder 13
Analog Meters 13
Brake Contactor 13
Press Operating Modes 13
Press Control Parameters 18
SECTION 3 - OPERATION
Purpose 21
Constant Energy System 21
Stamping Press Operation 21
Eddy-Current Clutch and Brake 21
Variable Speed Press Drives 21
Power Amplifier 22
CES Logic Board 23
Logic Power Supply Inputs 23
Logic Control Lines 23
LEM Current Feedback Amplifiers 23
Fault Priority Encoder 23
Fault Codes 23
CES Controller Parameters 24
Keypad Programming 25
Optional Features 27
SECTION 4 - START-UP AND ADJUSTMENT
Power Conversion 30
Press Speed Control 30
Angle Measuring and Control Circuitry 30
Start-Up Procedure 30
Approximate Parameter Settings 33
SECTION 5 - MAINTENANCE AND TROUBLESHOOTING
Maintenance 35
Troubleshooting 35
Renewal Parts, and Service 36
List of Spare Parts Common to All CES/DR Controls 36

4
GENERAL INFORMATION
INTRODUCTION
This instruction manual relates specifically to the CES
Stamping Press Controller. Instructions are in sequence
beginning with General Information and proceeding
through Receiving, Operation, Start-up and Maintenance
and renewal parts information.
Please be sure that you have your units board
schematics and connection diagrams, if you do not have
these drawings, contact the Publications Department at
the factory and request the drawing numbers by
providing the model number and serial number on the
nameplate of your unit. Items on your drawings
supersede any items listed or referred to in this manual.
Please note that there may be charges incurred for
replacement manuals and/or drawings.
If you have any questions regarding this controller
contact the DSI/Dynamatic. DSI/Dynamatic has
distributors located throughout the United States and in
various other countries. If you do not know who your
distributor is, please call the factory at 1-800/548-2169,
fax 262-554-7041, E-mail: sales@drivesourceusa.com,
Web site: www.drivesourceusa.com
SAFETY
With any electronic equipment or rotating electric
machinery, potential safety hazards are present and
require safeguards and proper use. This equipment
must be installed properly, using safe procedures, and
meet the requirements of all applicable safety codes.
The wiring must be in-accordance with the National
Electrical Code and all other local codes and regulations.
Shaft guards as well as protection for operating and
maintenance personnel against high voltage and moving
machine parts is essential. Refer to OSHA rules and
regulations, paragraph 1910.219, for guards on
mechanical power transmission apparatus. Please heed
these safety instructions.
DANGER, WARNING, CAUTION and special
INSTRUCTION labels are applied to the equipment to
remind you of the hazards that exist. Know your
equipment before handling or working on it.
DANGER - is used were an immediate hazard exists.
Failure to follow instructions could be fatal.
WARNING - means a possibility of injury to personnel,
but not as severe as a Danger Warning.
CAUTION - is used to warn of potential hazards and
unsafe practices.
INSTRUCTION labels and notes are used when there is
a need for special instructions related to safety, proper
operation or maintenance.
TRAINING
Training programs are an essential part of safe and
correct operation. Training provides the knowledge
necessary to obtain top performance from your
equipment. DSI/Dynamatic recognizes this fact and
conducts training schools to educate your plant
personnel in safe maintenance and operating
procedures.
Training schools are held at company headquarters, in
Sturtevant, Wisconsin. There is a nominal charge for
this service. If you are interested in scheduling a training
school, please contact the Marketing Department for
further information.
Special training schools structured around your specific
equipment may also be arranged.
RECEIVING AND DAMAGE CLAIMS
Your CES Stamping Press Controller has been operated
and tested at the factory prior to shipment. Specific test
procedures are followed to assure the quality of your
controller. Carrier approved packing methods assure
safe shipment to your plant. Shipment is made F.O.B.
our factory, with the carrier assuming responsibility for
your unit. Therefore, it is essential that you carefully
inspect the shipment upon delivery to ensure that no
damage or lost items have occurred in transit. Loss or
damage is covered by the carrier, not by the product
warranty. File a claim immediately with the carrier if any
damage or loss is found. Should you require assistance
in settling your claim with the carrier, contact our nearest
sales office. You will need the unit model number, serial
number and your purchase order number for
identification.
WARRANTY
Your new CES Stamping Press Controller is covered by
a one-year warranty against any manufacturing defect in
either material or workmanship. This warranty starts on
the date of shipment to your plant. Should the controller
fail within the one-year warranty period, contact the
factory for a Repair Instruction (RI) form. Fill in all
required information on the form and return the form with
the controller to our Repair Service Department in
Sturtevant, WI for warranty repair. Freight charges both
ways are your responsibility.
HANDLING
The CES Stamping Press Controller weighs about 600
pounds. Do not drop or subject the controller to
repeated shock or vibration. Do not stack heavy
material on the controller. The printed circuit boards,
components and electrical wiring may be easily
damaged.
STORAGE
Store electrical control equipment in a clean, dry location
with a non-corrosive atmosphere, protected from sudden
temperature changes, high levels of moisture, shock and

5
vibration. Electrical components are delicate and easily
damaged - provide adequate protection for them.
Ambient temperature should not exceed 25ºC. (77ºF.) on
a continuous basis or 40ºC. (104ºF.) on an intermittent
basis. The minimum temperature must remain above
freezing and above the dew point of ambient air. High
temperature, corrosive atmosphere and moisture are
detrimental to electrical control equipment.
LONG TERM STORAGE
The manufacturer's warranty covers repair or
replacement of defective materials and rectification of
faulty workmanship. It does not cover damage and
deterioration transpired during storage period.
Some examples of deterioration due to storage are:
1. Corrosion of terminals and contacts.
2. Loss of capacitance of electrolytic capacitors.
3. Moisture absorption within insulation and
composition resistors.
These are not manufacturer's defects and will not be
covered by the warranty policy.
Refer questions to the Electrical Engineering
Department in Sturtevant, Wisconsin.
REMOVING FROM STORAGE
Before returning the controller to service after long-term
storage, it will be necessary to carefully inspect it for any
signs of damage or deterioration. Correct any
deficiency. Carefully inspect the controller for signs of
moisture, especially with respect to transformers and
composition resistors. If moist, the autotransformer will
require thorough drying.
Corrosion is an important factor. Inspect terminals,
plugs, sockets and contacts for signs of corrosion. If
detected, cleaning will be necessary.
Before applying power, make sure all connections are
tight.
The suggested procedures given are only
recommendations offered to aid-our customers in
preserving stored equipment. We cannot guarantee
stored equipment, even if all procedures are followed;
damage or deterioration may still occur. Equipment
storage is not covered by warranty.
ELECTRICAL PART NUMBERING SYSTEM
The numbering system for electrical component and
assembly part numbers contains some useful data that
could be of value to the technician working with or
troubleshooting the controller. The number is twelve
digits, arranged in a two-six-four-digit sequence with the
groups separated by dashes. As an example, one
printed circuit board part number may be 15-000825-
0001. This twelve-digit number is the complete number,
as recognized by the computer. Frequently the number
is abbreviated by dropping zeros, i.e., 15-825-1. The
number printed on the board and in the technical
instruction material is the abbreviated form. However,
the actual bill of material and order paper work for that
board would use, the complete number 15-000825-0001.
CATEGORY NUMBER AND DESCRIPTION
(Reference first two digits and chart below)
14 Alarms
15 Assemblies
16 Bearings
17 Blocks
18 Blowers
19 Brackets
20 Cable
21 Cams & gears, cam switch assemblies
22 Cans
23 Capacitors
24 Chassis
25 Circuit breakers
26 Coils A coil assemblies
27 Connectors, plugs sockets
28 Control unit & parts
29 Counters
30 Dial plates & knobs
31 Enclosures
32 Fuses & fuse holders
33 Filters (radio interference)
34 Gaskets & gasket material
35 Generators
36 Hardware
37 Instruments
38 Insulators & Insulation
39 Lights & Fixtures
40 Motors
41 Motor starters & controls
44 Operator's panels
45 Panels
46 Phase Shifters
47 Photoelectric devices
48 Plates
49 Potentiometers
50 Power converters
51 Reactors
52 Regulators
53 Relays & contactors
54 Resistors
55 Semiconductors
56 Shock Mounting
57 Solenoids
58 Switches
59 Servo mechanisms
60 Terminals
61 Thermal devices-excluding motor starter heaters
62 Timers
63 Transducers
64 Transformers, chokes
65 Tube sockets
66 Valves
67 Wires
68 Wiring duct
69 Tubes

6
70 Insulated mounting boards
71 -
72 Master bill of material
73 Engineering data sheets
74 -
75 Reworked or exchanged assemblies
The middle six digits describe a basic type of part, such
as physical or electrical characteristics of a group or
family of parts. As an example, a resistor family of 1/2
watt carbon resistors have the number 000045. The part
number of one specific resistor in this family is a 54-
000045-0102.
The last four digits describe a specific part within the
family and may be assigned in numerical sequence or
may describe the specific part value. The following table
lists those part categories where the last four digits have
a significant meaning to the technician.
Category Part Name Parameter Described
23 Capacitor Capacitance
32 Fuses Ampere rating
49 Potentiometer Resistance
54 Resistors Resistance
55 Power diodes Peak reverse voltage
and SCR’s
Last 4 digits Numeric Value
2593 .025
2592 .25
2591 2.5
0250 25.
0251 250.
0252 2500.
0253 25000.

7

8
CES STAMPING PRESS CONTROLLER DESCRIPTION
CONSTRUCTION
The CES Stamping Press Controller is a solid state,
closed loop velocity controller designed specifically for
use with Dynamatic® eddy-current press drives. The
controller is built with analog, digital and microprocessor
circuitry. All components of the CES Controller are
contained on a sub-panel, except for an autotransformer
that is mounted separately. The panel measures 74" by
31.25". Special sizes are made to order upon request.
CES CONTROLLER
The basic CES press drive controller has proven to be
readily adaptable to synchronization (position) control.
This system utilizes a position transducer (digital shaft
encoder) to measure press position (crank angle) and
compares this feedback information against a digital
position reference. All information is handled in parallel
digital form and has a minimum sample rate compatible
with the system.
The difference between the reference and the feedback
signal (position error) is translated to an analog signal in
a D-A converter. The analog signal is sent to the press
velocity control for final processing and power
amplification for press drive control.
The CES controller is easily applied to single or multiple
action presses where speed control is desirable. The
system offers many unique features not available with
other press drive designs for use on draw presses,
banking presses, transfer presses and on synchronized
presses with automated handling equipment. The
combination of the eddy-current package press drive
and the CES controller offers a simple, safe, low
maintenance and reliable drive system to do a wide
variety of the jobs required of modern production press
equipment.
Specifications
Mechanical
49
-
37 -
Unit
63
42
42
32
21
Input Current
Aac Max
137
91
72
54
35
Input Current
Aac Average
98
65
53
40
26
Clutch Current
ADC
180
120
96
72
48
Brake Current
ADC
90
60
48
48
24
Retrofit control for existing presses have different
specifications from those listed here. Check your
specific unit or contact the factory.
Input Voltage: 480 VAC, +10%, -15%, 60Hz
Output Voltage: 850 VDC Field Forcing
Clutch Duty Cycle: 70%
Brake Duty Cycle: 30%
POWER CIRCUITRY
The incoming three phase 480 VAC connects directly to
the circuit breaker or terminal block at the top of the
panel. 120 VAC power for control circuitry, I/O modules
and the power supply board is provided by transformer
T1. Fuses FU5 and FU6 protect T1 against short circuits
and internal grounds. Capacitors C3, C4 and C5, along
with the impedance of the autotransformer, serve to filter
the incoming power to prevent line noise from affecting
the controller and to reduce line disturbances by the
controller. The autotransformer steps up the line voltage
from 480 VAC to 600 VAC. FU1, FU2 and FU3 are fast
acting semiconductor fuses sized to prevent damage to
the SCR’s in the event of an output short circuit. All
three incoming lines are sensed at the clutch gate driver
board and fed back to the logic board for proper gate
signal synchronization, and ultimately to the DMR
(Digital Master Regulator) for the purpose of ensuring
safe limits. The line voltage may be read on the DMR
display to be discussed later.
Separate contactors for the brake and clutch sections
provide positive mechanical disconnects from the input
power. Each section consists of a full converter
composed of six SCR’s capable of forcing the 300 VDC
rated coils to a peak value of 850 VDC, as well as
causing current flow to cease by inverting or by applying
a negative 850 VDC to the coils. Separate brake and
clutch gate driver boards supply the gate signals to the
appropriate SCR’s; they are located on the left side
bracket. Each SCR has di/dt protection from a series
choke and dv/dt protection from snubber networks
located on the circuit boards, which consist of series
resistors, capacitors and diodes connected in parallel
with the SCR. Also, across each SCR is a Metal Oxide
Varistor (MOV) for transient voltage protection.
A minimum resistive, or latching, load is provided with a
power resistor across each dc bus, identified as C1-C2
and B1-B2. Each bus also has an MOV suppressor to
clamp any high voltages arising due to the inductance of
the coil loads and to provide a current path for the short
period of time between interruption of current (such as a
contactor opening), and the establishment of current flow
in the C phase SCR's by the free wheel gates. Clutch
and brake voltages are fed back to the logic board
through the brake gate driver board. The output leads
are routed through L1 and L2, which are isolated current
feedback sensors with the current signals going directly
to the logic board. The output leads terminate inside
and near the bottom of the logic door.
The CES stamping press controller provides control for
the full range of Dynamatic® eddy-current press drives.
The power conversion circuitry operates from 480 VAC
input and provides a maximum of 850 VDC coil
excitation voltage.

9
Clutch excitation provides up to 180 Amps peak at 70%
duty cycle. Brake excitation provides up to 90 Amps
peak at 30% duty cycle.
KEYPAD PROGRAMMING
The keypad is mounted integrally with the DMR. It is
connected to the main DMR through a ribbon cable and
is used for viewing and modifying various parameters
within the system. The module consists of the following:
a sealed 20-button, dome-contact type keypad; two
independent sets of 8-digit, 7-segment LED displays;
and a row of 8 individual status LED’s. The keypad can
accept the following entries: numbers 0 through 9. Top,
Bot, up arrow, down arrow, *, #, Ent, F1 & F2. Dat is a
non-functional key. All of the operating modes that are
included on the keypad programmer are shown in Figure
2-1. Each mode includes an LED to indicate when it is
in operation. For information on how to use the keypad,
refer to Operation, Section 3.
FIELD ADJUSTMENTS
Some operator control adjustments can be made in the
field. Potentiometer R116 on the power supply can be
adjusted for +5 volts. Six adjustments can be made on
the main logic PCB (15-822-*) as follows: Clutch Velocity
Damping, Clutch Current Damping, Clutch Current Limit,
Brake Velocity Damping, Brake Current Damping and
Brake Current Limit. These adjustments are explained
in Section 4.
LIGHT EMITTING DIODE (LED) INDICATORS
In addition to the LED noted for the keypad programmer,
LED indicator lights are also located on the printed
circuit boards where operating circuit conditions need to
be known. The printed circuit boards that have LED’s
are described below.
LOGIC INTERFACE INDICATOR PCB (15-242-57):
Refer to Figure 2-2 for the identification of the LEDs
found on this printed circuit board.
CLUTCH GATE DRIVER (15-565-27) AND BRAKE
GATE DRIVER (15-565-28) PCBs: Each LED represents
a phase that is firing when it is on. Refer to Figure 2-3,
for the identification of the LEDs found on these printed
circuit boards.
I/O PCB (15-6502-3001): Refer to Figure 2-4 for the
identification of the LEDs found on this printed circuit
board.
PRESS SPEED CONTROL
The press control provides a closed loop speed control
operation with inner current loops on both the clutch and
brake. It provides adjustable acceleration and
deceleration. The reference data is modified by a press
angle measuring and control circuit that changes the
reference profile at adjustable angles, as shown in
Figure 2-5.
ANGLE MEASUREMENT
The press control provides a means of measuring press
angles by utilizing a position resolver mounted on the
output gearing of the press drive. The position
information is then used to set a reference profile based
on stored data of up to 6 angles and 6 predetermined
speeds. Details are further described under "CES
Digital Master Regulator (DMR)" and "Press Operating
Modes."

10
CES DIGITAL MASTER REGULATOR (DMR)
The DMR Controller is a microprocessor based solid
state electronic control system operating in conjunction
with a CES press drive controller. It provides the
interface with the press manufacturer's control. It also
provides the safety circuits necessary to ensure proper
operation of the CES controller. Parameters are scaled
in user units when applicable.
Upon power-up in the field, the values will be set by the
factory. Some of these values will undoubtedly require
modification before the press will function properly. The
keypad must first be unlocked using the proper
password before these parameters may be changed.
See the instruction sheet for your particular EPROM to
learn how to unlock the keypad. The operator must next
present all of the operator alterable parameters from the
keypad programmer and/or they must be downloaded
from the serial interface. Once these values are set,
they are retained and need not be reentered unless the
values are to be changed or a new factory-programmed
NVRAM is installed. The NVRAM memory chip has a
battery internal to the chip that saves the information
stored in the memory during the powering down
situations of the control. This battery has a ten-year life.
However, the battery is only called upon to function
during periods where there is no power applied to the
control. Therefore, the life of the battery may greatly
exceed the ten-year period if there are no extensive
periods where the control is actually turned off. Once
the parameter values have been set, the system may be
run by activating the appropriate signals in the control
circuitry.
High voltage input and output signals for the
microprocessor are handled through optically isolated
solid-state relay modules, which are mounted on an
auxiliary relay mounting rack. All 120 VAC control
signals are converted to 5-volt TTL-logic levels, which
interface with the DMR. There are status LED’s located
next to each relay on the mounting rack. These LEDs
light up to indicate active (closed contact) inputs and
outputs. Refer to the electrical diagrams for the various
control functions passing through this relay mounting
rack.
DMR Assemblies
Part Number
Function
15-779-11
Keypad Display
15-779-113, or -112
Resolver Interface
15-575-20
Main Controller PCB
15-814-3
Serial Interface
15-814-108
Dual D/A
15-775-2
First Fault Indicator
DMR Scaling PCBs
Part Number
Function
15-869-1
Ac Line Voltage (in)
15-869-1
Brake Current Feedback (in)
15-869-1
Clutch Current Feedback (in)
15-869-2
Manual Run Speed (in)
15-869-100
Speed Feedback (output)
The typical DMR, part number 15-820-33 to 37, consists
of the assemblies listed in Table 2-1 and the analog
scaling printed circuit boards listed in Table 2-2. The

11
numbers for a specific control may vary, see your
Control Data Master.
PRESS CONTROL INTERFACE - COMMANDS
ACCEPTED
The CES controller will accept nine different input
command signals from the press controller that are
available for the operator to make, they are as follows:
two Enables, Clutch Contactor ON, Inch, Micro Inch,
Reverse, Control Power ON, Stop-On-Top and Fault
Reset. Some controls also have a Stop-on-bottom
command.
ENABLE:
The enable signals are required to start the drive. These
contacts are the last contact closures in the start
sequence. The clutch contactor ON signal and the two
enable signals must all be given within 170 ms of one
another or a fault will be created. The enable contacts
must be closed in order to run. Upon opening either of
these contacts, the press control signals the CES
controller to stop the drive immediately with a command
to zero speed and to open the clutch contactor 450
milliseconds later. The CES controller responds to this
removal of enable with a normal stop signal. The enable
contact closures must be given only after all safety
features of press operation have been determined to be
in a "GO" status by the press control. The release of the
friction brake through the air pressure switch and/or the
limit switch showing friction brake travel is sometimes
used as the last event in the chain of events that
provides for the integrity of the enable signal given by
the press control to the CES controller. Redundant CES
inputs are provided to ensure that the enable signal is
present and that the receiver is not shorted.
The enable signals consist of two press control contact
closures that put the 115 VAC of the press control into
the I/O board.
CLUTCH CONTACTOR ON (INPUT):
In addition to the enable, the press control provides 115
volts to energize the clutch contactor. This ensures that
the press control has absolute control over the ability of
the CES controller to energize the clutch. This input
signal monitors the 115-volt signal. The clutch contactor
ON signal is one of the signals that activate the CR1
relay.
INCH:
The inch signal indicates that the CES controller is
directed to operate at inch
speed. The inch command is needed, along with
enable, to activate the controller in the inch mode. The
inch command can only be changed when the enable
command is not present; otherwise, a fault will be
generated.
The inch signal consists of a press control contact
closure that puts the 115 VAC of the press control into
the I/O board.
MICRO INCH:
The micro inch signal indicates that the CES controller is
directed to operate at the micro inch speed. The micro
inch command is needed, along with enable, to activate
the controller in the micro inch mode. The micro inch
command can only be changed when enable is not
present; otherwise, a fault condition will be generated.
The micro inch signal consists of a press control contact

12
closure that puts the 115 VAC of the press control into
the I/O board.
REVERSE:
The reverse command is sent to the press control to
indicate that the press is to operate in the inch or micro
inch mode in the reverse direction. The CES controller
uses this information with other signals to establish
either the inch-reverse or micro inch-reverse mode. If
the reverse command is issued with any command other
than the inch or micro inch, a fault will be generated.
The reverse command cannot be changed when enable
is present; otherwise, a fault will be generated.
The reverse signal consists of a press control contact
closure that puts the 115 VAC of the press control into
the I/O board.
CONTROL POWER ON:
The control power on signal is provided by the press
control to activate the 115 VAC control power to the CES
controller. This will close a contact in the secondary of
the CES controller transformer.
STOP-ON-TOP:
The stop-on-top signal is issued by the press control to
indicate that the CES controller should execute a normal
stop-on-top, as described in detail in the section on
"Press Operating Modes." If the stop-on-top command is
present when the enable is received by the CES
controller, a single stroke of the press will take place.
The stop-on-top signal consists of a press control
contact opening that removes the 115 VAC of the press
control to the I/O board.
FAULT RESET:
The fault reset command is a signal from the press
control to reset any fault condition in the CES controller,
allowing for continuation of operation. If the condition is
a result of a clutch current fault or a brake current fault, it
will be necessary to wait five to ten minutes (depending
on the setting of parameters No. 64 for the clutch and
No. 65 for the brake) before resetting; otherwise another
fault will be generated. This delay is necessary to allow
time for the coil to cool down. The time left to wait
before restarting can be displayed in parameter No. 18.
This time is in seconds.
The fault reset signal consists of a press control contact
closure that puts the 115 VAC of the CES controller into
the 1/0 board.
PRESS CONTROL INTERFACE - OUTPUT SIGNALS
The CES controller provides seven different solid-state
output signals that function as contact closures and
contact openings, according to the conditions called for.
The output signals that occur during different phases of
operation are as follows: Normal Stop, Stop Main Motor
Fault, Stop Now Fault, Stop-on-Top Fault, Control
Failure Fault, Clutch ON and TD Relay
NORMAL STOP (OUTPUT):
The normal stop signal from, the CES controller
indicates that the press control is to execute a normal
stop. Receipt of this signal from the CES controller
indicates that the CES controller has commanded the
press drive to be at zero speed. Upon receipt of this
normal stop signal, the press control is directed to
remove the enable signal and set the friction brake. The
normal stop output will be cleared by the press control
giving the enable signal the next time it is desired to run.
The I/O board of the CES controller opens a solid-state
relay contact for the normal stop signal to the press
control.
STOP MAIN MOTOR FAULT (OUTPUT):
The stop main motor fault signal from the CES controller
to the press control requests an emergency stop
condition. The press control then stops the main motor,
sets the flywheel brake, sets the friction brake and
removes the enable signal. The CES controller is placed
in the fault mode.
The 1/0 board of the CES controller opens a solid-state
relay contact for the stop motor fault signal to the press
control.
STOP NOW FAULT (OUTPUT):
The stop now fault signal is an output from the CES
controller. It indicates a second level of emergency stop
in which the press control is to immediately remove the
enable and set the friction brake the software programs
the reference to zero which applies the Eddy Current
Brake to help stop the press.
The I/O board of the CES controller opens a solid-state
relay contact for the stop now fault signal to the press
control.
STOP-ON-TOP FAULT:
The stop-on-top fault signal directs the press control to
complete the present cycle, and then execute a normal
stop-on-top, after which the CES controller is in the fault
mode.
The I/O board of the CES controller opens a solid-state
relay contact for the stop-on-top fault signal to the press
control.
CONTROL FAILURE FAULT (OUTPUT):
The control failure fault is generated by either of two
conditions. One is when the microprocessor watchdog
timer senses a microprocessor failure. The other is
when the power supply monitors sense a failure.

13
The I/O board of the CES controller opens a solid-state
relay contact for the control failure fault signal to the
press control.
CLUTCH ON (SIGNAL):
The clutch ON is a 115-volt output that drives the CR1
relay. A NO CR1 relay contact is in series with the 115
VAC power provided by the press control and a TD
contact. Activating the CR1 relay and the TD relay will
allow the clutch contactor to pull in after the press control
has given the clutch ON command.
The CR1 contactor is activated by the following
conditions:
1. Brake contactor is ON
2. Enable is present
3. No fault is present
4. Clutch contactor ON signal is present
Note: if the brake contactor drops out or clutch ON is
removed, CR1 drops out immediately. If the enable is
lost or either of the two emergency stop faults occurs, a
450-millisecond timer will be started, after which CR1 will
be dropped out. CR1 is also dropped out 450
milliseconds after a normal stop.
TD RELAY:
A TD relay contact is in series with the CR1 contact
closure to provide a redundant path for dropping out the
ac contactor with the loss of the enable signal. The TD
contact is closed when the enable input is present, and it
drops out 600 milliseconds after the loss of enable.
PRESS CONTROL INTERFACE - SERIAL PORT
The serial interface assembly makes it possible for the
DMR to communicate with another microprocessor or a
main computer. This communication link is an RS-422
assembly that is mounted directly to the main DMR
printed circuit board and is connected to the main board
by a ribbon cable. It can be utilized to set references
(i.e., speeds and angles) and to communicate diagnostic
information, faults, etc.
SIGNALS FOR CUSTOMER’S RECORDER
The CES controller provides four different buffered
signals at the terminals. They are as follows:
1. Clutch current
2. Brake current
3. Speed reference
4. Speed feedback
ANALOG METERS
The CES controller contains four analog meters to
provide the service engineer with necessary operating
parameters. They are as follows:
1. Clutch ammeter
2. Brake ammeter
3. Speed indication (SPM)
4. Elapsed time for clutch ON time
BRAKE CONTACTOR
A brake contactor is provided which will be closed under
simultaneous conditions of control power ON being
available and brake current fault not being present. The
brake contactor is opened 10 seconds after stopping on
top when a brake current fault is present.
PRESS OPERATING MODES
The CES controller includes 9 operating modes, as
described in detail below. Among these are the four
basic modes, employed in various combinations, as
follows: Run, Fault, Test and Ready.
I. RUN MODE (NORMAL)
The CES controller is in the run mode if the following
conditions exist:
1. Enable signal is present
2. NO fault is present
3. Reverse is not present
4. Inch is not present
5. Micro inch is not present
6. Clutch contactor ON is present
7. Brake contactor is closed
When in the run mode, the CES controller functions in
the following manner.
A clutch ON command closes the clutch contactor.
Upon initiation of the run mode, the drive reference
signal ramps up from an initial value that is adjustable
from 0 to 3 strokes per minute, at the initial acceleration
rate, until the drive reference equals or exceeds the
programmed reference. After this, the controller uses
the operating acceleration/deceleration rates. The initial
value of 0 to 3 strokes per minutes is adjustable at the
keypad. It is parameter No. 48.
The operating accel and decel rates consist of three
separately adjustable rates to minimize overshoot and
undershoot of the slide speed. The first accel/decel
rates are programmed to start by selecting the proper
press angle. The second and third accel/decel rates are
programmed based on a delta stroke per minute from
the set point. The second rate is adjustable to start up to
25% of rated speed before the set point. The third rate
is adjustable to start up to 15% of rated speed before the
set point.
When in the run mode, the speed reference follows the
profile set by the angles and speeds stored in the
parameter locations as listed in Table 2-3 (also see
Figure 2-5). Every angle and every speed must have an
assigned value.

14
A setting of 360 degrees on any angle will cause the
control to skip the speed setting that immediately
follows.
Parameter Locations Table 2-3
Parameter Number
Data
30
Angle No. 1
31
Speed No. 1 (manual)*
32
Angle No. 2
33
Speed No. 2
34
Angle No. 3
35
Speed No. 3
36
Angle No. 4
37
Speed No. 4
38
Angle No. 5
39
Speed No. 5
40
Angle No. 6
41
Speed No. 6
42
Creep Angle (α7)
43
Stop Angle (α8)
N0TE: *Parameter No. 31 will be the value of the
Manual Speed pot, if one is used.
While in the run mode, when the press control receives a
stop-on-top command, the CES controller will wait for
the creep angle. Upon reaching the creep angle, the
drive reference will decelerate to the creep speed and
remain at creep speed until the stopping angle is
reached. Upon reaching the stopping angle, the CES
controller will set the reference at 0 and issue a normal
stop signal to the press control. At the same time, the
CES controller will initiate a 450-millisecond timer at the
end, of which the clutch ON signal will be dropped,
dropping out the clutch contactor. Upon receipt of the
normal stop signal, the press control will enable the
friction brake and remove the enable signal. The press
control will remove the enable within 450 milliseconds;
otherwise a stop now fault will be generated.
The 450-millisecond timer is included to ensure that
clutch control excitation is removed regardless of other
sequential operations in the event of some type of fault
or failure.
Certain parameters can only be programmed from the
keypad of the DMR. They are listed on Table 2-4.
The run mode will be indicated by the "Run" LED on the
keypad and display board. Some controls have a full
range manual Run Speed pot, others have a +/-5%
manual Run Speed trim pot, while still others function
without any speed pot. Both pots are effective when the
press starts up and after the press passes Angles No. 1.
II. INCH FORWARD MODE (RUN AT)
The CES controller will be in the inch forward mode if the
following conditions exist:
1. Enable signal is present
2. No fault is present
3. Reverse is not present
4. Inch is present
5. Micro inch is not present
6. Clutch contactor ON signal is present
7. Brake contactor is closed
Keypad Programming Table 2-4
Parameter
Number
Data
44
Creep Speed
45
Micro Inch Speed
46
Inch Speed
47
Inch Accel Rate
48
Initial Value of Linear Accel Ramp
49
Initial Accel Rate (A1)
50
Operating Accel Rate No. 1
51
Operating Accel Rate No. 2
52
Operating Accel Rate No. 3
53
Accel Rate Delta SPM No. 1
54
Accel Rate Delta SPM No. 2
55
Operating Decel Rate No. 1
56
Operating Decel Rate No. 2
57
Operating Decel Rate No. 3
58
Decel Rate Delta SPM No. 1
59
Decel Rate Delta SPM No. 2
73
Baud Rate
75
Die Contact Angle
78
Gear Ratio
79
Pulses per Revolution
80
Pot Selector
81-Optional
Stop-on-Bottom – Creep Speed
Angle
82-Optional
Stop-on-Bottom – Apply Brake
Angle
83-Optional
Creep Speed Bottom
When in the inch forward mode, the CES controller
functions in the following manner.
The clutch ON command closes the clutch contactor.
The reference ramps from 0 to the inch reference at the
inch acceleration rate. Upon removal of the enable, the
drive reference goes immediately to 0 and the drive
decelerates to zero speed. At the time the enable is
removed, the 450-millisecond clutch safety timer is
initiated. After 450 Milliseconds the clutch contactor is
dropped out by removing clutch ON. The enable signal
should be the last signal received to eliminate faults.
The drive may be jogged in the inch mode by toggling
the enable signal.
The inch forward mode will be indicated by the "Inch"
LED on the keypad and display board.

15
III. INCH REVERSE MODE (RUN AT)
The CES controller will be in the inch reverse mode if the
following conditions exist:
1. Enable signal is present
2. No fault is present
3. Reverse is present
4. Inch is present
5. Micro inch is not present
6. Clutch contactor ON signal is present
7. Brake contactor is closed
8. The main motor is programmed to run in the reverse
direction
When in the inch reverse mode, the CES controller
functions in the following manner.
The clutch ON command closes the clutch contactor.
The reference ramps from 0 to the inch reference at the
inch acceleration rate. Upon removal of the enable, the
drive reference goes immediately to 0 and the drive
decelerates to Zero speed. At the time the enable is
removed, the 450-millisecond clutch safety timer is
initiated. After 450 milliseconds, the clutch contactor is
dropped out by removing clutch ON. The enable signal
should be the last signal received to eliminate faults.
The drive may be jogged in the inch mode by toggling
the enable signal.
The inch reverse mode will be indicated by simultaneous
illumination of the "Inch" and “Reverse" LEDs on the
keypad and display board.
IV. MICRO INCH FORWARD MODE (RUN AT)
The CES controller will be in the micro inch forward
mode if the following conditions exist:
1. Enable signal is present
2. No fault is present
3. Reverse is not present
4. Inch is not present
5. Micro inch is present
6. Clutch contactor ON signal is present
7. Brake contactor is closed
When in the micro inch forward mode, the CES
controller functions in the following manner,
The clutch ON command closes the clutch contactor.
The reference ramps from 0 to the micro inch reference.
There is no acceleration rate in micro inch. Upon
removal of the enable, the drive reference goes
immediately to 0 and the drive decelerates to zero
speed. At the time the enable is removed, the 450-
millisecond clutch safety timer is initiated. After 450
milliseconds, the clutch contactor is dropped out by
removing clutch ON. The enable signal should be the
last signal received to eliminate faults. The drive should
be jogged in the micro inch mode by toggling the enable
signal.
The micro inch forward mode will be indicated by the
"Micro Inch" LED on the keypad and display board.
V. MICRO INCH REVERSE MODE (RUN AT)
The CES controller will be in the micro inch reverse
mode if the following conditions exist:
1. Enable signal is present
2. No fault is present
3. Reverse is present
4. Inch is not present
5. Micro inch is present
6. Clutch contactor ON signal is present
7. Brake contactor is closed
8. The main motor is programmed to run in the reverse
direction
When in the micro inch reverse mode, the CES
controller functions in the following manner.
The clutch ON command closes the clutch contactor.
The reference ramps from 0 to the micro inch reference.
Upon removal of the enable, the drive reference goes
immediately to 0 and the drive decelerates to zero
speed. At the time the enable is removed, the 450-
millisecond clutch safety timer is initiated. After 450
milliseconds, the clutch contactor is dropped out by
removing clutch ON. The enable signal should be the
last signal received to eliminate faults. The drive may be
jogged in the micro inch mode by toggling the enable
signal.
The micro inch reverse mode will be indicated by
simultaneous illumination of the "Micro Inch" and
"Reverse" LEDs on the keypad and display board.
VI. FAULT MODE
Two fault indicators designed into the controller are the
DMR Fault and First Fault (15-775-2).
The fault mode is entered if any fault is generated. Once
the fault mode has been entered by the initiation of a
fault, the CES controller remains in the fault mode until
the fault mode is remotely reset by the press control
issuing a fault reset command. The fault mode can be
reset locally from the CES controller keypad. Call up
Parameter 63, Clear Faults, and using the Down Arrow
(↓) reduce the faults to zero.
In the fault mode, various faults are stored, indicated and
transmitted to the press control by the CES controller. In
the case of all faults, the press is stopped. There are
various levels of faults; and the urgency with which the
press is stopped differs with the different levels of faults.
The four faults that the CES controller will diagnose are
as follows: Stop Main Motor Fault, Stop Now Fault, Stop-
On-Top-Fault and Control Fault. These are fully
described below. For quick reference during operation,
refer to Table 3-3 and/or 3-4.

16
When a level 0100, 0200 or 0300 fault exists it will be
indicated by an LED on the keypad and display board. A
control fault will be indicated by the absence of the
"control fault" LED on the I/O PCB.
Stop Main Motor Fault - There is only one fault that will
signal the stopping of the main motor in addition to
stopping the press. It is Fault No. 0101, Over-speed
Fault.
0101 Over-speed Fault - An over-speed condition is
defined as follows: If the tach feedback signal
exceeds the speed reference by a set percentage,
an over-speed condition exists. The time allowed
to be over-speed, before a fault is recognized, is
adjustable from 0 to 5 seconds. The over-speed
percentage is adjustable from 0 to 20%. The
reason the main motor is stopped in this case is
that it is considered to be in a runaway condition.
Set for minimum time and minimum over-speed
percent without causing nuisance tripping of fault.
When the over-speed fault is generated, the CES
controller functions in the following manner.
Upon sensing the over-speed fault, a stop motor fault
signal is sent to the press control to remove enable and
initiate the stopping sequence; this includes setting the
friction brake and removing enable from the CES
controller. Speed reference is set to zero. The clutch
converter is inhibited. The clutch contactor drop out
timer is initiated immediately upon detection of an over-
speed fault. The timer will cause the clutch contactor to
drop out in 450 milliseconds by removing the clutch ON
command to the contactor. The brake will be energized
by the negative speed error, while the speed is above
zero, to provide decelerating torque.
Stop Now Faults - There are 18 stop now faults. They
require the press to be stopped immediately, but not the
main motor. Each of these faults is described as follows:
0202 Loss of Tach Fault - Loss of encoder pulses with
10% of clutch current for 200 milliseconds.
0203 Clutch Current Delay Fault - If 10% current is
present in the clutch coil when CR1 is de-
energized, a clutch current delay fault will be
issued.
0206 Press Movement in Wrong Direction Fault -
Press movement detected to be in a direction
opposite of that commanded, based upon
degrees of opposite rotation after enabled. The
number of degrees of rotation before causing
this fault is adjustable from 0 to 10 degrees at
the keypad. Set for minimum degrees without
causing nuisance tripping.
0207 Loss of Line Fault - Loss of an input phase or
greater than 20% drop in ac line for a period of
100 milliseconds.
0208 Enable Without Clutch Contactor ON Fault -
Clutch contactor ON is not present within 170
milliseconds of receiving enable (see Fault No.
0226).
0209 Clutch Contactor ON After Clutch ON is De-
energized Fault - Clutch contactor ON input
signal is present 100 milliseconds after clutch
ON output is de-energized.
0210 Missing Enable Fault - The two enable signals
are not coincident for more than 170
milliseconds.
0211 Inch + Micro Inch + Enable Fault - The presence
of an inch and micro inch command with enable.
0212 Reverse Command Fault - The presence of a
reverse command without an inch or a micro
inch command.
0220 Enable Present After Normal Stop Fault - Enable
present 450 milliseconds after a normal stop is
issued.
0221 Clutch Contactor Not ON In Test Mode Fault -
Clutch contactor ON signal, not present while in
clutch test mode.
0222 Press Movement in Test Mode Fault - Press
movement of 2 degrees detected while in test
mode.
0223 Enable Present In Test Mode Fault - Enable
signal present while in test node.
0224 Stop-On-Top Not Performed Fault - The stop-
on-top function failed to stop the press in 1.5
times the cycle period.
0225 Clutch Contactor ON Removed without
removing enable fault or clutch contactor
removed during the 450 milliseconds required
before de-energizing the clutch contactor.
0226 Clutch Contactor ON Without Enable Fault -
Enable not present within 170 milliseconds of
receiving clutch contactor ON (see Fault No.
0208).
0227 Enable Before Cool Down Expired Fault -
Enabling the CES controller before the cool
down time period has expired following a clutch
current or a brake current fault.

17
0228 Creep Speed Not Reached Before Stop Angle
Fault - During a stop-on-top sequence, the creep
speed is not reached before the press reaches
the stop angle.
When any stop now fault is generated, the CES
controller functions in the following manner.
A stop now fault will be issued to the press control
immediately upon sensing any of the above faults. The
press control should initiate an emergency stopping
sequence that includes setting the holding brake and
removing the enable from the CES controller (among
other items). Speed reference will be set to zero. The
clutch converter is inhibited. The clutch contactor drop
out timer is initiated immediately upon detection of a stop
now fault. The timer will cause the clutch contactor to
drop out in 450 milliseconds by removing the clutch ON
command to the contactor. The brake will be energized
by the negative speed error, while the speed is above
zero, to provide decelerating torque.
Stop-On-Top Faults - There are 8 stop-on-top faults.
They will cause the CES controller to execute a normal
stop upon reaching the top of the press stroke. These
faults do not require an emergency stop but should stop
the press at the top during the next cycle in order for the
problem to be investigated. Each of these faults is
described as follows:
0313 Under-speed Fault - If the tach signal is 3% less
than the speed reference, an under-speed fault
will exist. The time allowed to be under speed is
adjustable from 0 to 5 seconds. Reset at speed
error within 3%.
0314 Clutch and Brake Current Overlap - If clutch and
brake current are present at the same time, a
clutch and brake current overlap fault will exist.
The overlap time allowed is 0.5 second and the
amount of overlap allowable is 5%.
0315 Clutch Current Fault - If clutch current is present
for too long, a clutch current fault will exist. The
time allowed is adjustable from 3 to 20 seconds
and the current allowable is 20%. The CES
controller cannot be enabled until cool down
time has expired.
0316 Brake Current Fault - If brake current is present
for too long, a brake current fault will exist. The
time allowed is adjustable from 3 to 20 seconds
and the current allowable is 20%. The CES
controller cannot be enabled until cool down tine
has expired.
0317 Inch Change Fault - If the inch command signal
is changed while enable is present, an inch
change fault will exist.
0318 Micro Inch Change Fault - If the micro inch
command is changed while enable is present, a
micro inch change fault will exist.
0319 Reverse Change Fault - If the reverse command
is changed while enable is present, a reverse
change fault will exist.
0329 Parameter Out of Limits Fault - If a downloaded
parameter is outside of established limits a
parameter out of limits fault will exist. When
commanded to use the new parameters that
contain a parameter that is outside of the
established limits, the controller will operate at
the established limit of the incorrect parameter
and create a stop-on-top fault.
When any stop-on-top fault is generated, the CES
controller functions in the following manner:
A stop-on-top fault output is issued to the press control.
A normal stop sequence will be initiated (normal stop-on-
top operation). At the completion of this sequence, the
drive will be in a fault mode condition and cannot be
restarted without resetting the fault. If the press does
not reach the stopping angle in 1.5 times the press cycle
period, the CES controller will issue a stop now fault.
Control Faults - A microprocessor watchdog timer
monitors the microprocessor and the power supply for
proper operation. The CES controller issues a control
failure fault any time either one fails or goes out of
tolerance. This type of fault will produce a Stop Now
stop.
FAULT PRIORITY ENCODER
Various conditions have been selected to be monitored
as faults. The faults, in order of priority, are as follows:
- Run Signal is Present
0 Push Reset
1 External
2 Brake Free Wheel
3 Low Line
4 Brake Over-current
5 Clutch Free Wheel
6 Line/Microprocessor
7 Clutch Over-current
In order to read these faults accurately, a PWM Fault
Indicator board, No. 15-775-2, must be plugged into the
corresponding header on the DMR. For a quick
reference during operation, refer to Table 3-3.
VII. SET-UP/TEST MODE
The test mode can only be accessed when the main
motor is OFF and press power is padlocked OFF. In
order to enter, use, and exit the test mode, the following
steps must be followed in the order given:

18
1. CES controller power is applied
2. Enable is not present
3. No fault is present
4. Test mode parameter No. 60 is set to the ON
condition from the keypad and display board
5. CES circuit breaker opened to remove power
6. Main motor and press control power is OFF
7. Jumper across CR2 contacts 15 and 16 on TB14
8. Jumper across TD contacts 26 and 27 on TB14
9. Jumper control power across contacts 300 and 302
10. Incoming leads 320, 321 and 334 removed from
TB10. Tape ends
11. Jumper 115 volts from 302 to 320 and 301 to 334 on
TB10
12. CES circuit breaker closed to reapply power
13. Clutch test and/or brake test performed as required
14. CES circuit breaker opened to remove power
15. Remove jumpers and replace leads that were
changed in steps 7, 8, 9, 10 and 11 above
16. CES circuit breaker closed to reapply power
17. Exit test mode by setting parameter No. 60 to the
OFF condition from the keypad and display board
An LED located on the keypad and display board
indicates the test mode. The test mode is only de-
energized by setting parameter No. 60 to OFF. The test
mode is stored in non-volatile memory.
Clutch Test Mode - In the test mode, the clutch test
mode can be entered by setting the clutch test mode
parameter to ON (parameter No. 61, up arrow (↑)).
The clutch will be engaged full ON with the DMR
automatically doing the following:
1. Issuing a clutch ON command
2. Setting reference to 100%
3. Setting feedback to 0%
4. Releasing the DMR inhibit
In the clutch test mode, the clutch is de-energized by
doing the following:
1. Setting parameter No. 61 to OFF (down arrow (↓))
2. Exiting the test mode or
3. Entering the brake test mode
De-energizing the clutch test mode initiates the following
sequence:
1. Reference and feedback are set to 0%
2. DMR inhibit is activated
3. The clutch ON command is dropped after 450
milliseconds
Brake Test Mode - In the test mode, the brake test mode
can be entered by setting the brake test mode parameter
to ON (parameter No. 62, up arrow (↑)).
The brake will be engaged full ON with the DMR
automatically doing the following:
1. Issuing a brake ON command
2. Setting reference to 0%
3. Setting feedback to 100%
In the brake test mode, the brake is de-energized by
doing the following:
1. Setting parameter No. 62 to OFF (down arrow (↓)).
2. Exiting the test mode or
3. Entering the clutch test mode
De-energizing the brake test mode initiates the following:
1. Reference and feedback are set to 0%
Test Mode Faults - Receiving an enable in the test mode
will result in an enable in the test mode fault. Sensing
press movement in the test mode will initiate a press
movement in the test mode fault.
VIII. READY MODE
The CES controller will be in the ready mode if the
following conditions exist:
1. CES control power is applied
2. It is not in the run, test or fault modes
The ready mode will be indicated by the "Ready" LED on
the keypad and display board.
IX. SPEED CONTROL REFERENCE CLAMP
The CES controller has a maximum speed setting. If the
press control sends a speed reference value that is
greater than this maximum speed to the CES controller,
the CES controller will clamp the reference at the
maximum speed. The “Referenced Clamped" LED will
light on the keypad and display board, indicating that the
reference is clamped.
PRESS CONTROL PARAMETERS
The press control may have constraints on changing of
speeds and press drive parameters while the press is
running. The CES controller will change parameters as
directed by the press control.
Press control parameters are sent by the press control in
a packet of bits representing ASCII characters. The first
two ASCII characters will be AA. The packet length is
68 characters. Space characters are used to complete
the 68-character packet. Upon receiving an EE
command, the AA packet will be transmitted back to the
press control by the DMR for comparison to ensure its
accuracy. The AA will be changed to EE when sent
back.
Fault data is sent by the CES controller upon request of
the press control. The two ASCII characters of the
"Request to Send Fault Data" will be BB. The packet
length of the request will be two characters. The DMR
will send the fault data in a packet of bits representing
ASCII characters. The first two ASCII characters will be
BB. The remaining characters will be four-digit numbers,

19
which will represent faults corresponding to these
numbers. Zeros are used to complete the 68-character
packet.
Monitor data will be sent by the DMR on request of the
press control. The two ASCII characters of the "Request
to Send Monitor Data" will be CC. The packet length of
the request will be two characters. The DMR will then
send the monitor data in a packet of bits representing
ASCII characters. The first two ASCII characters will be
CC. The remaining characters will contain the monitor
data. Zeros are used to complete the 68-character
packet. Numbers in the monitor data will be four digits
with an implied decimal point.
When ready, the press control will send a two-character
packet to the CES controller instructing the DMR to
execute the new parameters. The two ASCII, characters
in this packet of bits will be DD. All characters in the
packet will be 8-bit ASCII (the most significant bit being
zero) with one start, one stop and no parity.
In the run mode the new parameters will take effect at
the first angle after the press reaches the top of the
stroke after having received the DD command to
execute the new parameters. If the press is stopped or
is operating in the inch or micro inch mode then the DD
command to execute the new parameters is given, the
new parameters will take effect immediately. There are
no termination characters for the packets.
The press run data packet should contain the following
information, and in the order given:
1. ASCII characters AA.
2. Six independent angles and speeds defined in pairs.
The angles are in degrees and are defined in a
clockwise (CW) rotation with zero degrees at top
dead center. The speeds are in strokes per minute.
If it is desired to skip an angle, it may be
programmed to be 360.0 degrees and, since the
press will only accept angles from 0 to 359.9
degrees, it will skip the angle programmed for 360.0
degrees.
3. The seventh angle will be the angle that starts
slowing the press down to the creep speed after the
CES controller has received the stop-on-top contact
closure.
4. The eighth angle will be the angle to initiate the
contact that will allow the press control to set the
friction brake after the press has been at creep
speed and reaches this stop angle.
5. The angles will be four digits with an implied decimal
point, in tenths of a degree ranging from 0 to 359.9
degrees.
6. The speeds will be four digits, with an implied
decimal point, in hundredths of a stroke per minute.
7. The press run data should have the format indicated
in Table 2-5.
Press Run Data Format Table 2-5
Packet Number
Data
Par No.
1 through 2
AA
3 through 6
Angle No. 1
30
7 through 10
Speed No. 1
31
11 through 14
Angle No. 2
32
15 through 18
Speed No. 2
33
19 through 22
Angle No. 3
34
23 through 26
Speed No. 3
35
27 through 30
Angle No. 4
36
31 through 34
Speed No. 4
37
35 through 38
Angle No. 5
38
39 through 42
Speed No. 5
39
43 through 46
Angle No. 6
40
47 through 50
Speed No. 6
41
51 through 54
Creep Angle
42
55 through 58
Stop Angle
43
59 through 68
Zeros
CES Monitor Data Format Table 2-6
Packet Number
Data
1 through 2
CC
3 through 6
Inch Speed
7 through 10
Micro Inch Speed
11 through 14
Creep Speed
15 through 18
Operating acceleration rate No. 1
19 through 22
Operating acceleration rate No. 2
23 through 26
Operating acceleration rate No. 3
27 through 30
Acceleration rate delta SPM No. 1
31 through 34
Acceleration rate delta SPM No. 2
35 through 38
Operating deceleration rate No. 1
39 through 42
Operating deceleration rate No. 2
43 through 46
Operating deceleration rate No. 3
47 through 50
Deceleration rate delta SPM No. 1
51 through 54
Deceleration rate delta SPM No. 2
55 through 58
Initial acceleration rate
59 through 62
Average parts per minute
63 through 66
Speed Reference
67 through 68
Zeros
The CES monitor data packet will contain the following
information:
1. ASCII characters CC.
2. Acceleration and deceleration rates will be four
digits, with an implied decimal point, in tenths of a
stroke.
3. The speeds will be four digits, with an implied
decimal point, in hundredths of a stroke per minute.
4. The CES monitor data will have the format indicated
in Table 2-6 per minute per second.

20
A typical program to run a press with a Manual Speed
pot and use the slowdown function to get good parts
would be set up as follows:
1. Angle No. 1 = 180 degrees
2. Manual Speed pot = 16 SPM
3. Angle No. 2 = 115 degrees
4. Speed No. 2 = 10 SPM
5. Angle No. 3 = 360 degrees
6. Speed No. 3 = 10
7. Angle No. 4 = 360 degrees
8. Speed No. 4 = 10
9. Angle No. 5 = 360 degrees
10. Speed No. 5 = 10
11. Angle No. 6 = 360 degrees
12. Speed No. 6 = 10
13. Creep Angle = 305 degrees
14. Stop Angle = 356.5 degrees
15. On the keypad, enter:
Creep Speed = 3 SPM
Table of contents
Other Dynamatic Controllers manuals
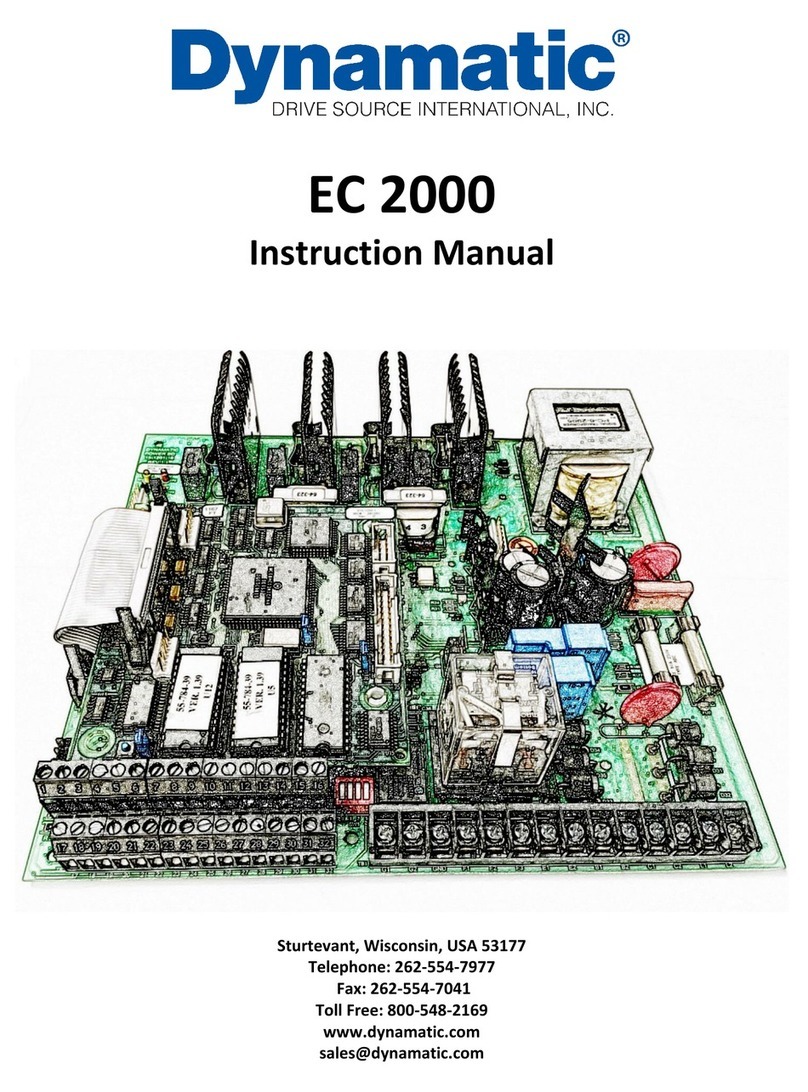
Dynamatic
Dynamatic EC 2000 User manual
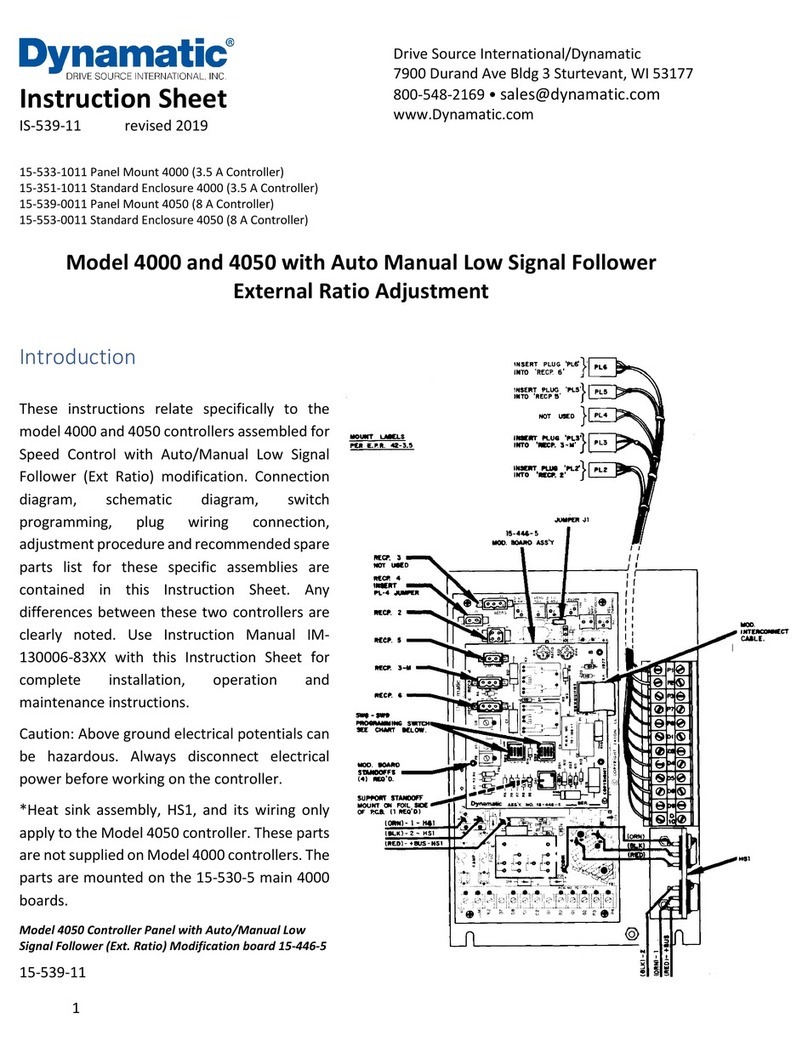
Dynamatic
Dynamatic 4050 User manual
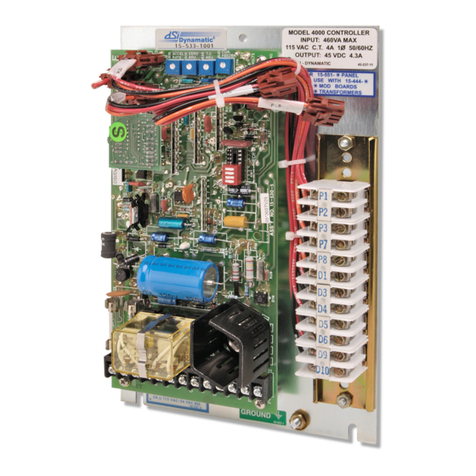
Dynamatic
Dynamatic 4050 User manual
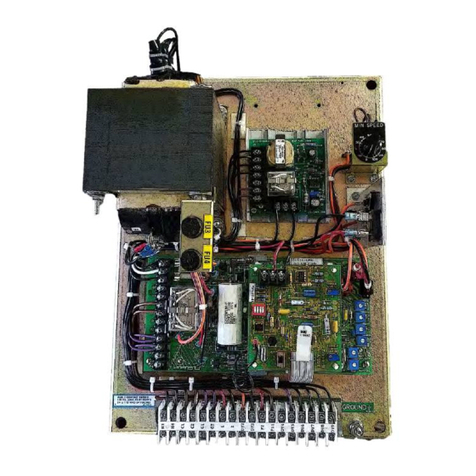
Dynamatic
Dynamatic 4000 User manual
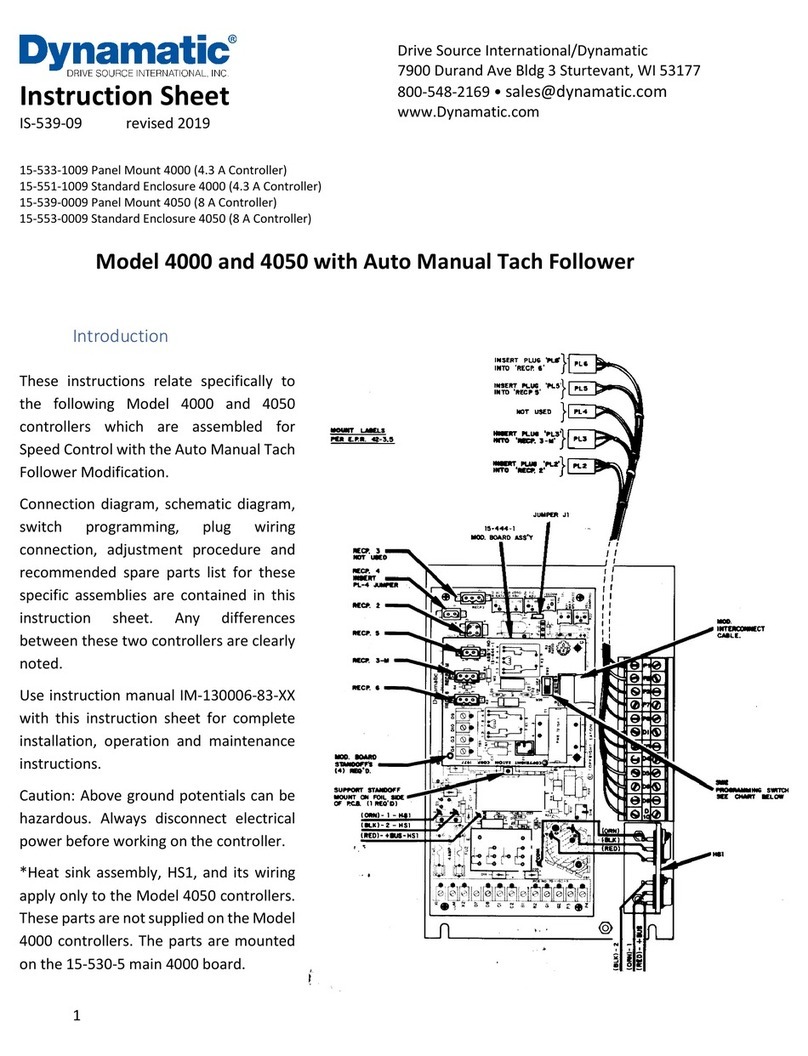
Dynamatic
Dynamatic 4050 User manual
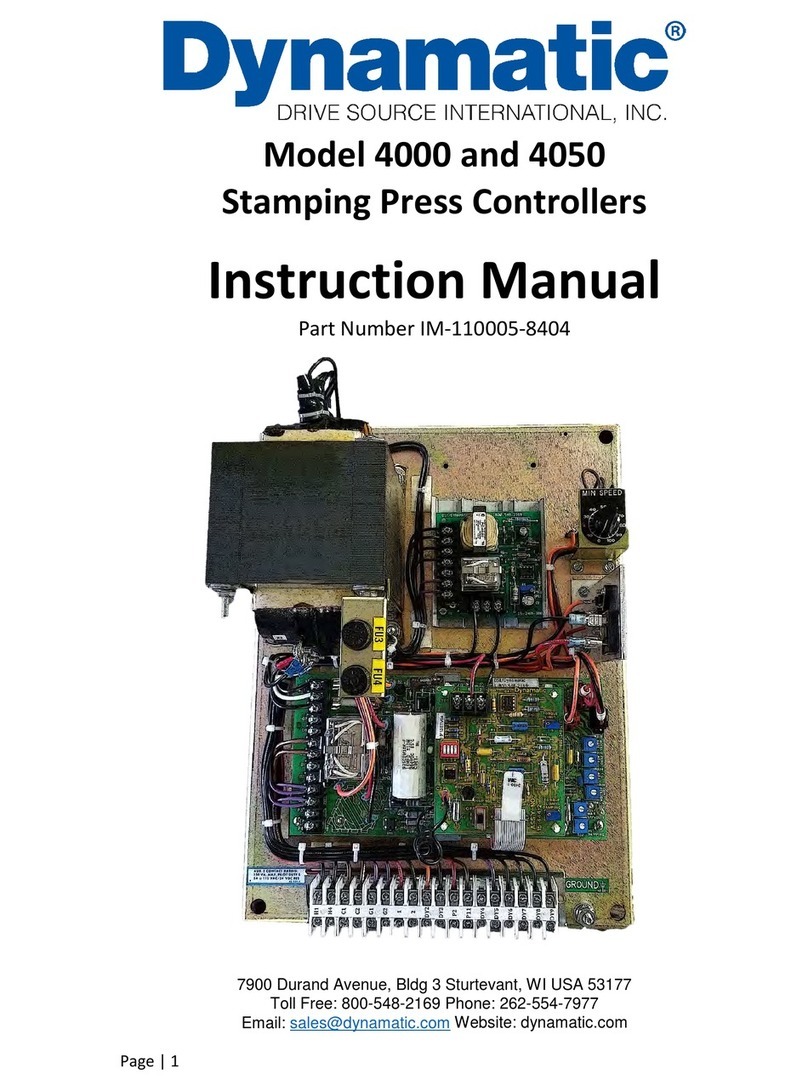
Dynamatic
Dynamatic 4000 User manual
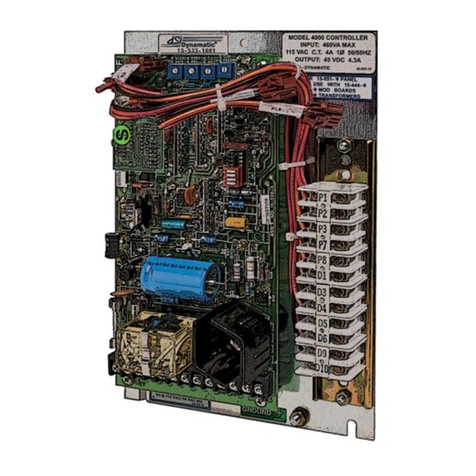
Dynamatic
Dynamatic 4000 User manual
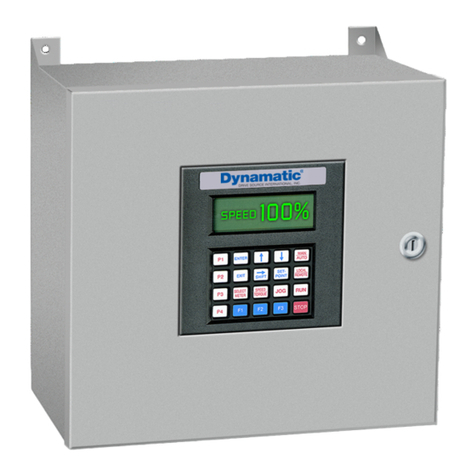
Dynamatic
Dynamatic EC 2000-CES User manual
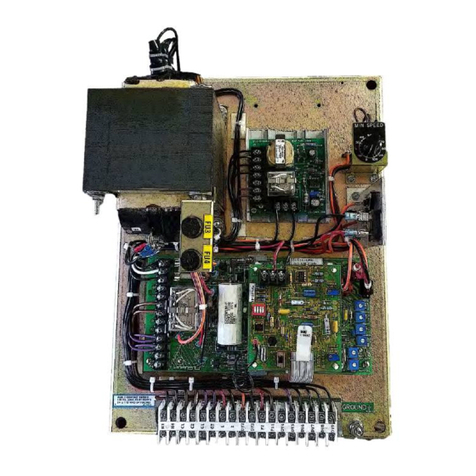
Dynamatic
Dynamatic 4000 User manual