Dynamatic 4050 User manual

1
Instruction Sheet
IS-539-11 revised 2019
15-533-1011 Panel Mount 4000 (3.5 A Controller)
15-351-1011 Standard Enclosure 4000 (3.5 A Controller)
15-539-0011 Panel Mount 4050 (8 A Controller)
15-553-0011 Standard Enclosure 4050 (8 A Controller)
Model 4000 and 4050 with Auto Manual Low Signal Follower
External Ratio Adjustment
Introduction
These instructions relate specifically to the
model 4000 and 4050 controllers assembled for
Speed Control with Auto/Manual Low Signal
Follower (Ext Ratio) modification. Connection
diagram, schematic diagram, switch
programming, plug wiring connection,
adjustment procedure and recommended spare
parts list for these specific assemblies are
contained in this Instruction Sheet. Any
differences between these two controllers are
clearly noted. Use Instruction Manual IM-
130006-83XX with this Instruction Sheet for
complete installation, operation and
maintenance instructions.
Caution: Above ground electrical potentials can
be hazardous. Always disconnect electrical
power before working on the controller.
*Heat sink assembly, HS1, and its wiring only
apply to the Model 4050 controller. These parts
are not supplied on Model 4000 controllers. The
parts are mounted on the 15-530-5 main 4000
boards.
Model 4050 Controller Panel with Auto/Manual Low
Signal Follower (Ext. Ratio) Modification board 15-446-5
15-539-11
Drive Source International/Dynamatic
7900 Durand Ave Bldg 3 Sturtevant, WI 53177
www.Dynamatic.com

2
INTRODUCTION.................................................................................................................... 1
Connection diagram for Standard Enclosure 4000 Controller................................................................3
Schematic Diagram for 4000 Controller .................................................................................................4
Connection Diagram for 4000 Panel Mount and 4050 Controllers ........................................................5
Schematic Diagram for 4050 Controller .................................................................................................6
Low Signal Follower Modification PCB 15-446-5/0102 ..........................................................................6
Modification PCB Mounting ..................................................................................................................... 7
GENERAL DESCRIPTION........................................................................................................ 7
Visual Inspection...................................................................................................................................... 7
Preliminary Adjustments.......................................................................................................................... 7
Operator Controls .......................................................................................................................................7
Main PCB 15-530-5 or 15-530-6..................................................................................................................8
Trimpot Illustration:................................................................................................................................8
Low Signal Follower Mod PCB.....................................................................................................................9
Adjustment Procedure ............................................................................................................................. 9
Zero Adjust R19 with LED monitor..............................................................................................................9
Zero Adjust R19, Alternate Method............................................................................................................9
Max Speed/Volts R21- ................................................................................................................................9
Max Speed/Volts R21 with LED monitor.....................................................................................................9
Max Speed/Volts R21, Alternate Methods ...............................................................................................10
Time Constant (TC) Adjust ........................................................................................................................10
Current Feedback R20*- ...........................................................................................................................10
Accel Rate R18 ..........................................................................................................................................11
Velocity Damping R22*-............................................................................................................................11
Automatic Operation ............................................................................................................................. 11
Circuit Diagram for Input Signals ..........................................................................................................12
Greater than 7.5 Vdc ............................................................................................................................12
Renewal Parts List.................................................................................................................................. 14

3
Connection diagram for Standard Enclosure 4000 Controller
ED-58211

4
Schematic Diagram for 4000 Controller
Note 1: This equipment must be installed in compliance with National Electrical Code and all applicable
state and local codes.
Note 2: Transformer may be supplied as a winding in the ac motor or as a separate item. Standard
connections to winding in mechanical unit and to separate transformer are both shown above.
Note 3: To eliminate linear acceleration on manual speed, open contact 4 on SW9.
Note 4: To add linear acceleration to Auto, close contact 1 on SW9
Note 5: For alternate input signals, program contacts SW*-1, 2, 3, & 4 as shown above

5
Connection Diagram for 4000 Panel Mount and 4050 Controllers
ED-56811

6
Schematic Diagram for 4050 Controller
Low Signal Follower Modification PCB 15-446-5/0102

7
Modification PCB Mounting
If you have purchased a complete controller this section may be passed over and you may proceed to
General Description.
1. Place the Main PCB in front of you with the long dimension in a horizontal position and the
terminal strip to the left.
2. Remove the DIP switch by pulling it straight out of the receptacle, RECP 1. Then, peel the adhesive-
backed label off the other half of RECP 1.
3. Insert the arrow-type locking head of the four nylon stand-offs supplied into the four 0.188”
diameter holes in the main PCB and press in. The tabs will snap out to lock the stand-offs
permanently in position.
4. Hold the modification PCB assembly over the stand-offs with the ribbon connector toward you
and insert the ribbon connector plug into RECP 1. Be careful to see that all 16 pins are started
properly into the receptacle before pressing the plug in.
5. Align the holes in the modification PCB assembly over the stand-offs and press over the tapered
posts until the locking flanges snap out to lock the board in position.
General Description
This modification circuit accepts a transducer output signal (current or voltage) and conditions it to
produce a dc reference voltage for the controller. The circuit is adjusted for a specific linear drive speed
range to be obtained for a given transducer output range.
The modification can also be placed in the Manual Mode whereby the drive speed is controlled by an
external Manual Speed potentiometer.
Linear acceleration may be selected for Auto, Manual or both modes of operation.
Visual Inspection
1. Before proceeding to the preliminary adjustments, check the controller for any damage that may
have occurred during shipment, such as loose connections and damaged wire or components.
2. Check all interconnecting wires for conformance to connection diagram and schematic as supplied
in the instruction sheet.
3. Check the Operator’s controls (which are supplied by customer) to see if they are connected
properly per the connection diagram. This includes the Manual Speed pot R5, the Manual/Auto
selector switch and the start and Stop pushbutton controls.
Preliminary Adjustments
Perform the following preliminary adjustments (with no power applied to the controller)
1. Operator Controls (Supplied by customer unless specified)
a. Set the Manual Speed potentiometer to 0% (Full CCW)
b. Set the Auto/Manual selector switch to the Manual position.

8
c. Note location of Start and Stop pushbuttons.
2. Main PCB 15-530-5 or 15-530-6
The pots used are screwdriver adjust single turn pots. Do not use a screwdriver with a blade width
exceeding 1/8 inch.
a. Set the Accel Rate potentiometer R18 to 100% (Full CW)
b. Set the Zero Adjust potentiometer R19 to 0% (Full CCW)
c. Set the Max Speed/Volts potentiometer R21 to 0% (Full CCW)
d. Set the Velocity Damping potentiometer R22 as follows (see trimpot illustration):
e. Set the Time Constant (TC) Adjust potentiometer R26 as follows (see trimpot illustration):
Mechanical Unit Model Numbers
Velocity
Damping
Setting
Models AC/Fractional
Models EC/AS
Fractional
14
0%
181/182/184/186
18/21
50%
214/216/254/256
25
75%
280/320/360/440
27
75%
Mechanical Unit Model Numbers
TC Adjust
Setting
Models AC/Fractional
Models EC/AS
FHP/181/182
0%
184/186/214
14/18
50%
216/254/256/280
21
30%
320/360/440
25/27
100%
*Typical product number stamped on mechanical unit nameplate:
1. A1-100214-0053, specific mechanical model is AC-214
2. B2-100210-0008, specific mechanical model is AS-21
Trimpot Illustration:

9
f. Set the Current Feedback potentiometer R20 to 0% (Full CCW).
g. Put jumper J1 in Norm position.
3. Low Signal Follower Mod PCB 15-446-5
a. Set the Bias potentiometer R20 to 0% (Full CCW)
b. Set the programming switches SW8 and SW9 as indicated in the programming chart on the
connection diagram. The linear acceleration may be selected for Auto, Manual or both modes
of operation.
Adjustment Procedure
Caution: To avoid personal injury or damage to the test equipment remove power before connecting or
disconnecting test equipment.
The Model 4000 and 4050 controllers contain an LED status monitor which provides a visual means of
setting the maximum speed and minimum bias. This LED set up along with an alternate method is given
below.
1. Turn ON the power to the drive and start the ac motor.
2. Start the controller with the Start pushbutton. Note the location of the Stop pushbutton.
3. Zero Adjust R19 with LED monitor- Slowly increase the Zero Adjust Potentiometer R19 CW
while monitoring the LED, D22. When controller output is turned ON or clutch voltage is turned
ON (or the drive shaft begins to rotate), the LED should start flashing. Now just back off slowly
until flashing stops.
Zero Adjust R19, Alternate Method- This adjustment can be set to provide zero rpm or some
minimum speed greater than zero, as required by the machine operating requirements.
a. For zero rpm, turn the Zero Adjust potentiometer R19 CW until the output shaft just begins
to turn. Then, back off the control until the output shaft just stops turning. Stop and start the
controller a few times to be sure the drive shaft does not rotate.
b. For a minimum speed greater than zero, the LED cannot be used. Turn the Zero Adjust
potentiometer CW until the desired speed is attained. For a accurate setting use a tachometer
or stroboscope.
4. Max Speed/Volts R21-This adjustment can be set to limit drive speed to its rated maximum or
to a slower speed as required by the machine process. An LED status monitor has been provided
on the main board to allow you to set the maximum speed without the use of a tachometer,
stroboscope or voltmeter. However, an alternate method of setup using this equipment is given
to set the maximum speed point. The tachometer or stroboscope will give an accurate rpm setting
while the use of a voltmeter will give only an approximate speed setting. This is because the
voltmeter is measuring generator voltage instead of actual output rpm.
Max Speed/Volts R21 with LED monitor Set the Manual Speed potentiometer R5 at 100% (Full
CW). The drive should be loaded for best results. Set the Max Speed/Volts potentiometer R21 at
100% (Full CW). Caution: drive will go to top speed. The LED should be out when the drive is at
top speed. With the LED out, slowly turn the Max/Speed/Volts potentiometer R21 CCW until the
LED lights. This indicates that the speed of the drive is in the regulating range of the controller.

10
The clutch voltage should drop below 45V. This will be approximately the maximum rated speed
of the drive. The maximum speed point setting will vary with different mechanical units.
There are two other conditions for which the LED will be out besides the drive being set for zero
speed or running wide open above the regulating range. These are whenever the “E” relay is
deenergized (the drive is stopped), or due to a wiring error, ground or some malfunction of the
controller itself.
Max Speed/Volts R21, Alternate Methods-
a. To set maximum rated speed with a tach or stroboscope: turn the Manual Speed
potentiometer R5 to 100% (Full CW). Allow the drive to accelerate to full speed, Turn the Max
Speed/Volts pot CW until the rated speed indicated is the same as the speed listed on the
nameplate of the mechanical unit.
b. To set approximate maximum speed with a voltmeter, connect a voltmeter (60 Vac scale)
across terminals G1 and G2. Turn the Manual Speed pot R5 to 100% (Full CW). Allow the drive
to accelerate to full speed. With the drive at full speed, turn the Max Speed/Volts pot CW
until the meter reading ceases to rise. Back off the adjustment (CCW) until the meter reading
just begins to drop. This is the point of maximum speed.
c. To set a maximum speed that is less than rated maximum speed requires the use of a
tachometer or stroboscope indicator. This cannot be accomplished with the LED status
monitor. Turn the Manual Speed potentiometer to 100% (Full CW). Allow the drive to
accelerate to full speed, slowly increase Max Speed/Volts potentiometer setting CW until the
desired speed is indicated.
5. Since there may be some interaction between the Zero Adjust and the Max Speed/Volts,
particularly if the minimum speed is other than zero, repeat steps 3 and 4 until the desired speeds
are obtained for both the zero and max positions of the Manual Speed pot.
6. Time Constant (TC) Adjust R26-The TC Adjust is used to set current feedback by using coil
voltage and a variable RC combination to simulate the different coil time constants of various size
drives. A trimpot illustration is provided to facilitate the setting of this control. Sufficient range
has been provided for drive sizes from fractional through 20 hp for the 4000 controller and up to
125 hp for the 4050 controller. Set you TC control appropriately for your individual drive size as
shown in Preliminary Adjustments.
Settings are not critical and so may be “tuned” for each drive. High inertia applications can benefit
from a higher than normal setting.
7. Current Feedback R20*-Normal operation will not require use of this potentiometer. Certain
applications are best met with a negative current feedback responses which is slower in settling
and less likely to overshoot at low rpms. There are some low inertia, light load, linear acceleration
applications that may also benefit from improved low-end linearity with current feedback
damping. If you have one of these applications, remove Jumper J1 from the Normal position and

11
place it in the Increased position. Adjust current Feedback R20 as required to obtain desired drive
response.
*See Basic 4000/4050 manual for a more detailed description of this adjustment.
8. Accel Rate R18- The purpose of Linear Acceleration is to slow down drive response to an increase
in command. Without Linear Accel control, the drive will respond to operator speed adjustments
very quickly, limited only by the torque capacity of the drive. With the Linear Accel circuit, the
output of the controller is linear with respect to time. This circuit is adjustable from 3 to 90
seconds. Linear acceleration may be selected for Auto, Manual or both modes of operation. When
set at the slowest acceleration rate, the drive will take 90 seconds to accelerate from zero to rated
speed, following a linear ramp. When less than rated speed is set, the time required to reach top
speed is proportionally less.
To set the Accel Rate: stop the controller with the Stop pushbutton. Turn the Manual Speed
potentiometer to 100% (Full CW). With the drive at a complete stop, push the start pushbutton
and time the interval required for the drive to accelerate from zero to full speed. Adjust the Accel
Rate potentiometer R18 CCW for a slower accel rate, or CW for a faster accel rate. This
potentiometer sets the acceleration rate for both the Manual and Automatic modes.
Note: Only the Acceleration Rate is adjustable. The response of the controller to a reduced command is
instantaneous. The response of the drive to a decrease in command is a function of drive system load and
inertia.
9. Velocity Damping R22*-This potentiometer is used to match the controller response to the drive
response (drive response is a function of the clutch coil time constant and system inertia). The
proper setting for this adjustment depends on the drive size and total load inertia.
See Preliminary Adjustments. If instability (speed control becomes erratic) occurs at any setting
increase (turn CW) slightly until the speed becomes stable. This completes the adjustment
procedure.
*See Basic 4000/4050 manual for a more detailed description of this adjustment.
Automatic Operation
1. For standard dc current input signals to the 4000/4050 controller, program switch SW*-1
through -4 on 15-446-5 mod board per chart on page 2 or 4.
2. For other dc voltage input signals, open contacts SW8-1 through -4 on 15-446-5 mod board per
chart on page 2 or 4 and connect an external series dropping resistance as follows:
a. 0-7.5 Vdc input signal – no external series dropping resistor is required.
7.5 Vdc is the maximum signal voltage that should be applied to the controller. Lower
voltages, down to 0-5.5 Vdc will also work satisfactorily.
b. Input signals greater than 7.5 Vdc- require the addition of a dropping resistor to reduce
the voltage applies to P9 & P10 to a maximum of 7.5V. This resistor, RS, should be

12
connected in series with terminal P10 on the 15-446-5 mod. Board. The input signal should
then be applied to one side of resistor RS and terminal P9 as shown below. This will result in
a nominal voltage of 7.5V applied to P9 & P10.
Circuit Diagram for Input Signals
Greater than 7.5 Vdc
The value of RS should be determined as follows:
VIN = Voltage input signal
RS= Value of customer supplied series resistor in ohms.
RS= 680 Vin – 5100
The value of RS is not critical; therefore, it is not necessary to use the exact value calculated for it. The
nearest standard resistor value to the calculated value may normally be used, as long as the maximum
voltage applied to P9 & P10 is between the limits of 5.5-7.5 Vdc.
The minimum wattage of resistor, RS, should be determined as follows:
PRS = minimum wattage rating of RS
PRS = 2(−7.5)2
1. Set the Auto/Manual switch to Auto.
2. Set the Ratio pot R55, located on the operator’s station or on the cover (supplied by the customer
unless requested), to 50% CW. The Ratio pot R19, located on the modification board, is not used.
Turn the process control ON and set it for minimum signal output.
3. With minimum signal output, start the controller and adjust the Bias pot R20 CW until the drive
just begins to run. Then adjust the potentiometer CCW until the drive just stops (R20 on the
modification board)
4. Set the process control for maximum signal output. Adjust the Ratio pot R55 for the maximum
speed.

13
5. Repeat Steps 3 and 4 until desired tracking is obtained.
6. For speed control signals independent of process control signals, place the switch in Manual and
adjust the Manual Speed pot for desired speed.
7. Check motor current to make sure the motor is operating within its rating. If motor current
exceeds the nameplate rating, shut it down and correct the problem. This completes the
adjustment procedure.
Note: Some transducer installations may cause the Low Signal Follower circuit to operate incorrectly.
Typically, in these applications there will be no control of the output at C1 and C2 on the controller,
resulting in either no drive output or full output speed. Another possible problem is erratic drive
speed. These problems are caused by signal noise into the follower circuit.
These problems can normally be corrected by jumpering the P9 terminal on the follower mod board
to the COM terminal on the main 15-530-* controller board 15-530-5 or 15-530-6.
Caution: a ¼ amp, 115 volt fuse must be installed in series with the P9 line from the transducer
into the follower board when P9 and COM are jumpered as described above. This will prevent a possible
run away if a ground fault occurs in the drive.

14
Renewal Parts List for Standard 4000 & 4050 Controllers with Auto/Manual Low Signal Follower (ext.
Ratio)
Qty
Part Number
Description
Legend
Model 4000 Controllers
15-530-0005 Main PCB Assembly **
1
27-123-0001
Mini-Jumper
J1
*2
32-018-4091
Fuse, 4 Amp, 250 V
FU1, 2
*1
53-398-0001
Relay, 4pdt, plug-in
E
15-533-1011 Panel Mount
1
15-530-0005
Main PCB (Refer to PCB parts list above)
*1
15-446-0005
Low Signal Follower PCB assembly
4
36-298-0010
Circuit board support
15-535-1011 Standard Enclosure
1
15-530-5
Main PCB (Refer to PCB parts list above)
*1
15-446-0005
Low Signal Follower PCB assembly
1
15-531-1001
Base Assembly
1
15-532-0006
Cover assembly (Basic)
1
15-529-0008
Selector Switch
SW
1
15-358-253
Alternate speed pot
R55
*1
15-529-0001
Pushbutton assembly
PB1, 2
*1
15-358-252
Speed Pot
R5
4
36-298-0010
Circuit board support
Model 4050 Controllers
15-530-0006 Main PCB Assembly **
1
27-123-0001
Mini Jumper
J1
*2
32-028-0100
Fuse, 10 Amp, 250 V
FU1, 2
*1
53-398-0001
Relay, 4pdt, plug-in
E
15-539-0011 Panel Mount
1
15-530-0006
Main PCB (Refer to PCB parts list above)
*1
15-444-0005
Low Signal Follower PCB assembly
1
15-529-0019
Heat sink assembly, incl. Q1 & D3
4
36-298-0010
Circuit board support
15-553-0011 Standard Enclosure
1
15-539-0011
Basic Panel assembly (Refer to Panel Mount parts list
above)
*Denotes minimum spare parts **Denotes suggested spares when downtime is critical

15
Drive Source International/Dynamatic
7900 Durand Ave Bldg 3 Sturtevant, WI 53177
www.Dynamatic.com
Other manuals for 4050
2
This manual suits for next models
1
Table of contents
Other Dynamatic Controllers manuals
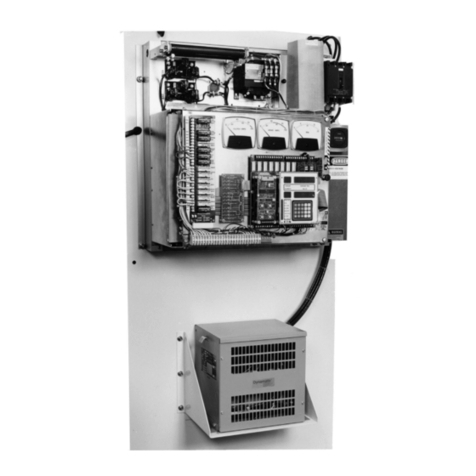
Dynamatic
Dynamatic CES User manual
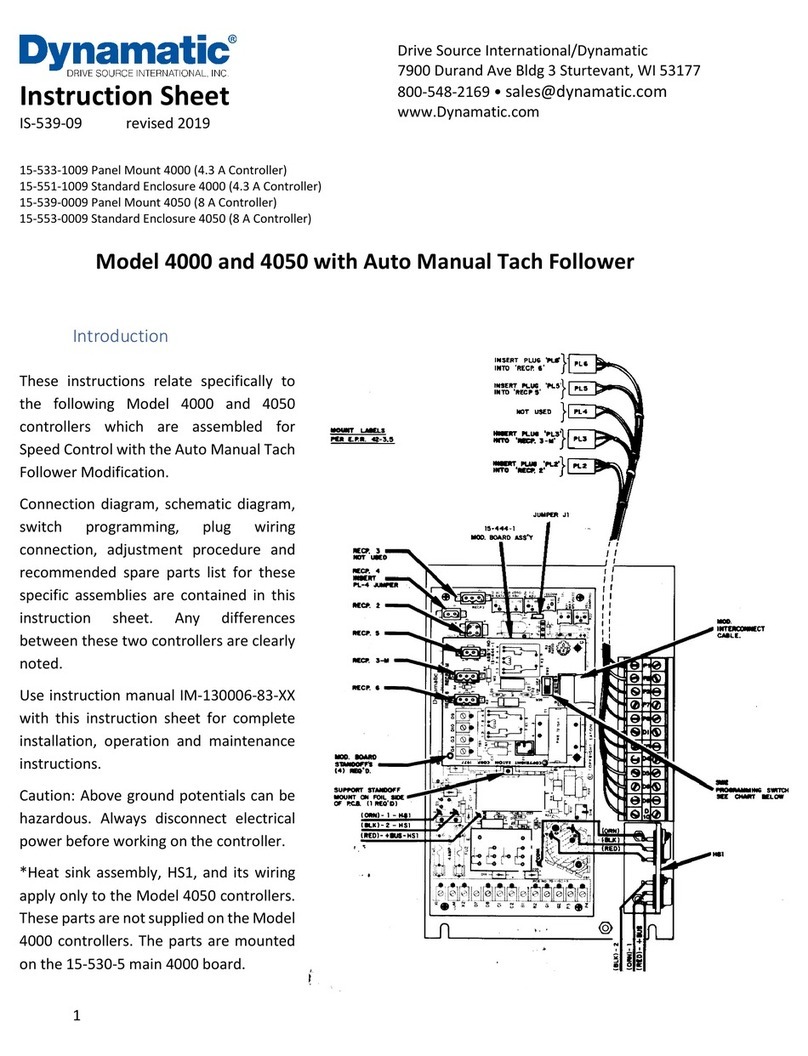
Dynamatic
Dynamatic 4050 User manual
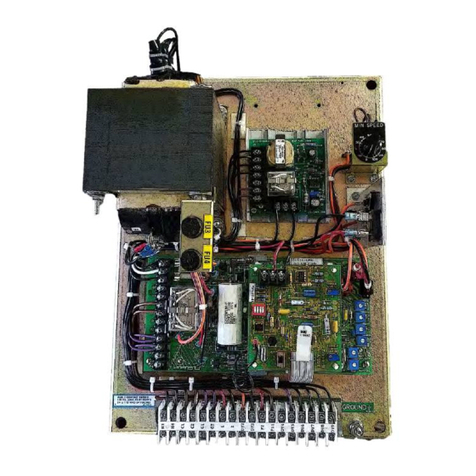
Dynamatic
Dynamatic 4000 User manual
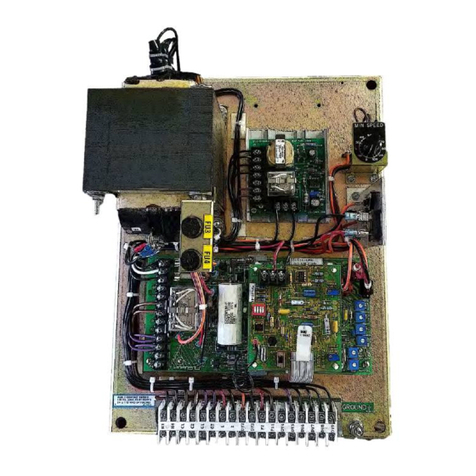
Dynamatic
Dynamatic 4000 User manual
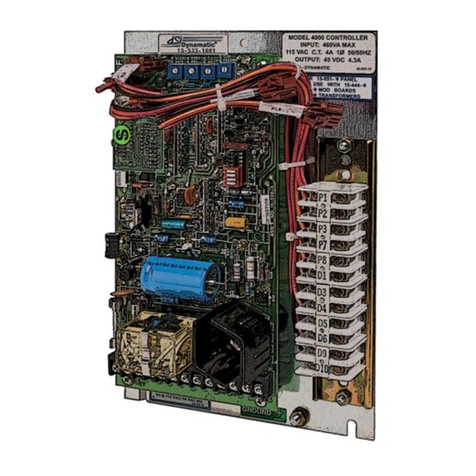
Dynamatic
Dynamatic 4000 User manual
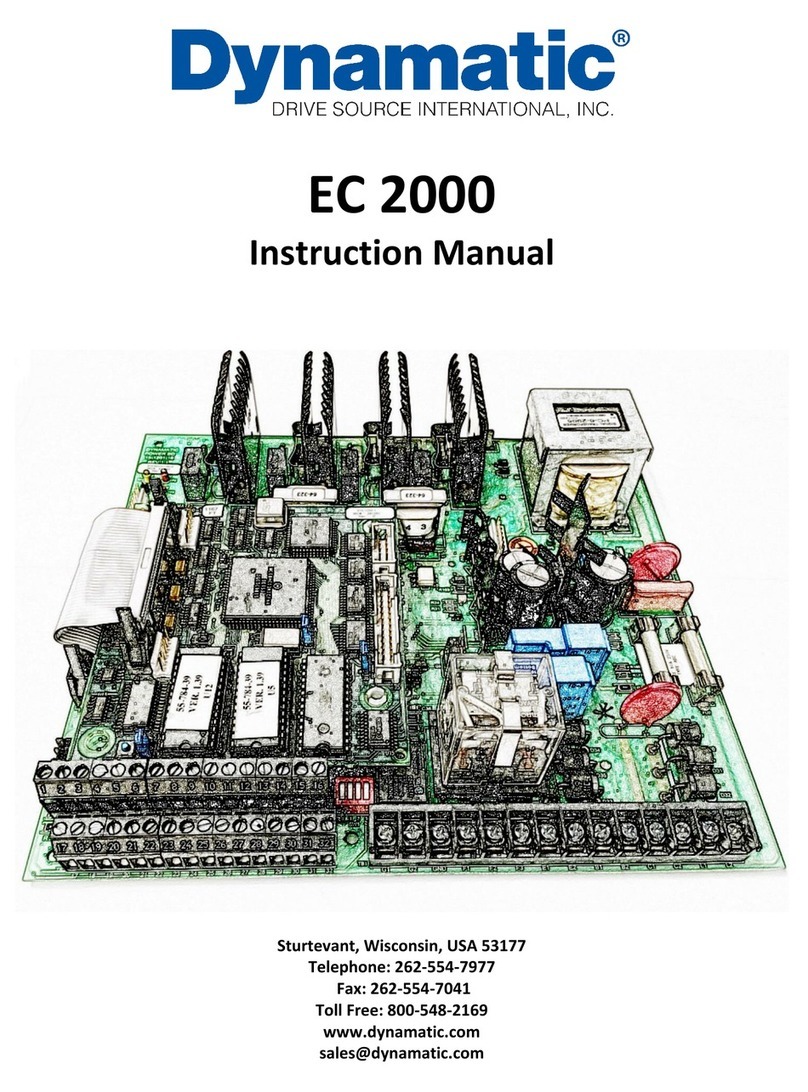
Dynamatic
Dynamatic EC 2000 User manual
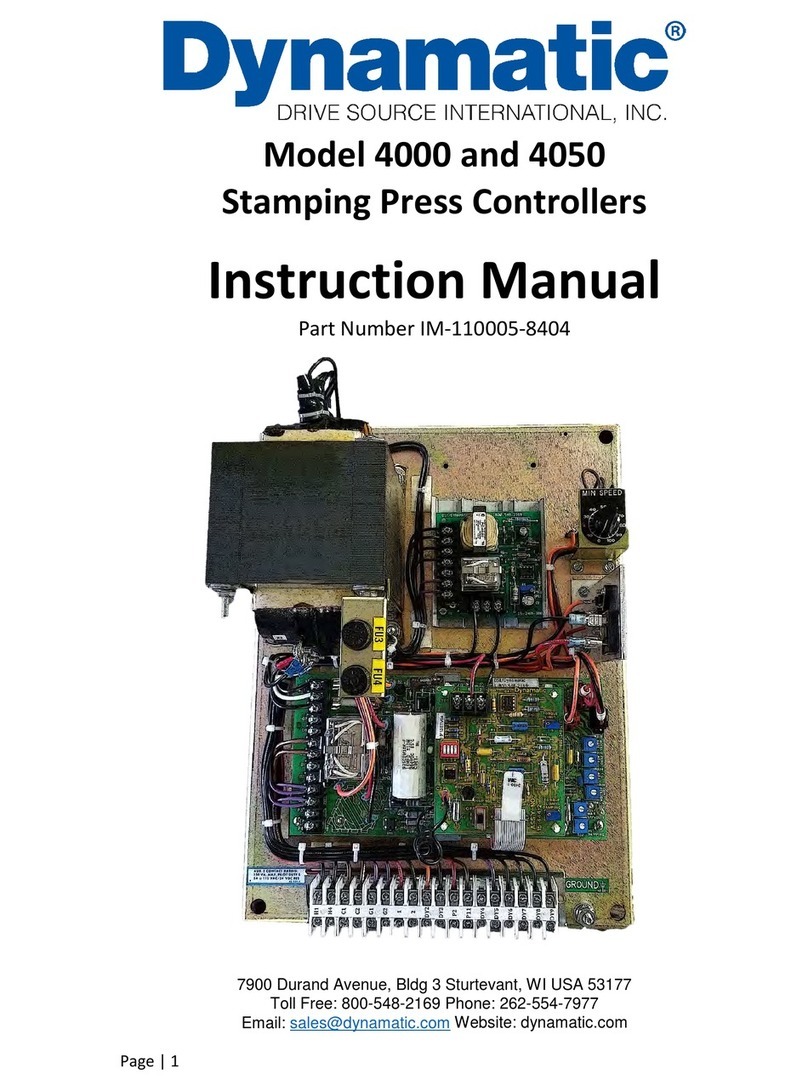
Dynamatic
Dynamatic 4000 User manual
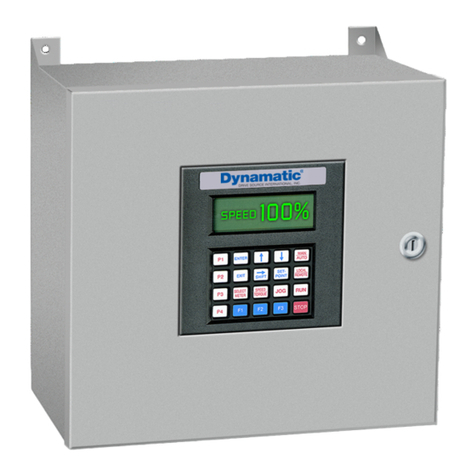
Dynamatic
Dynamatic EC 2000-CES User manual
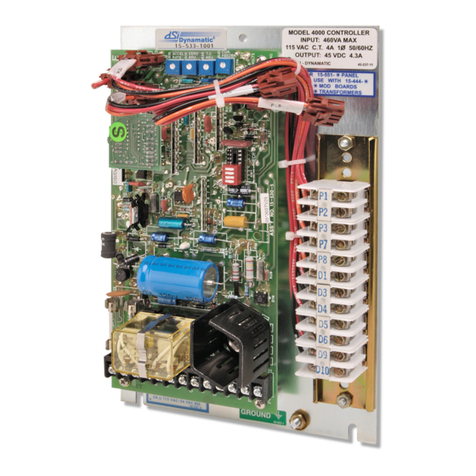
Dynamatic
Dynamatic 4050 User manual
Popular Controllers manuals by other brands

Taconova
Taconova NOVASTAT EL BASIC manual

Superior Electric
Superior Electric 9T92PVC2 Series instructions

Armacost Lighting
Armacost Lighting RGB14REM quick start guide
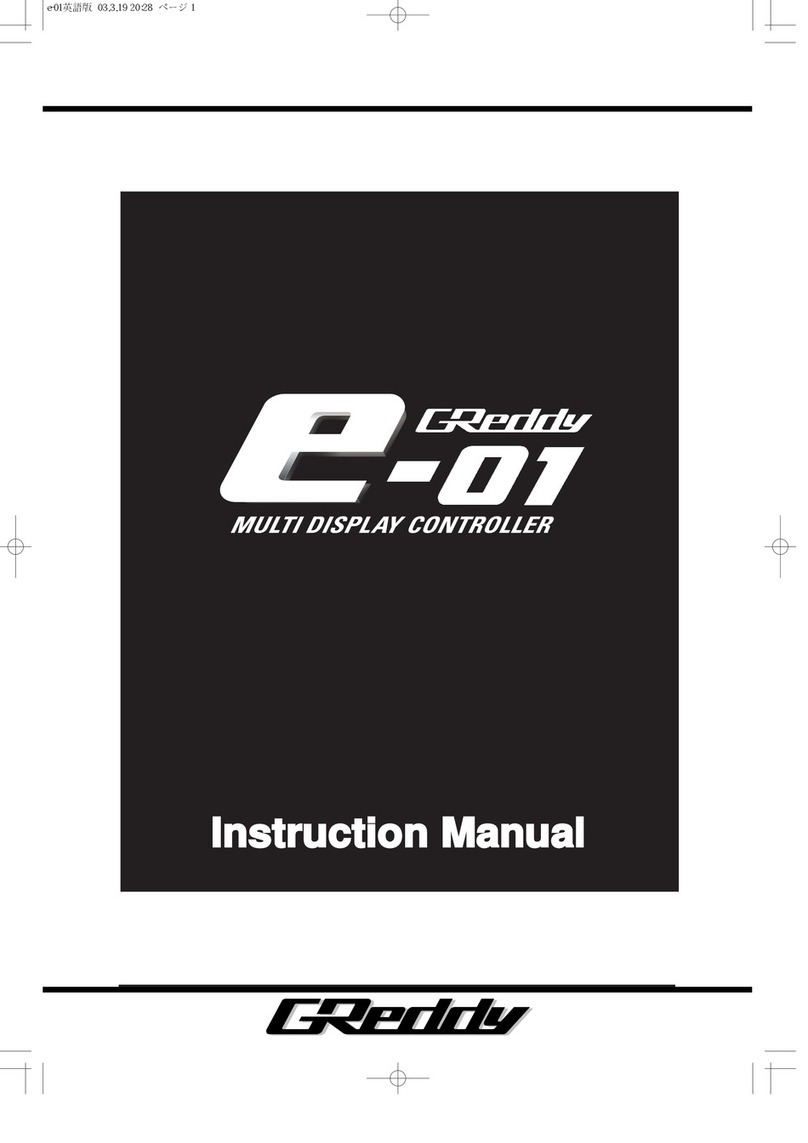
GReddy
GReddy e-01 instruction manual
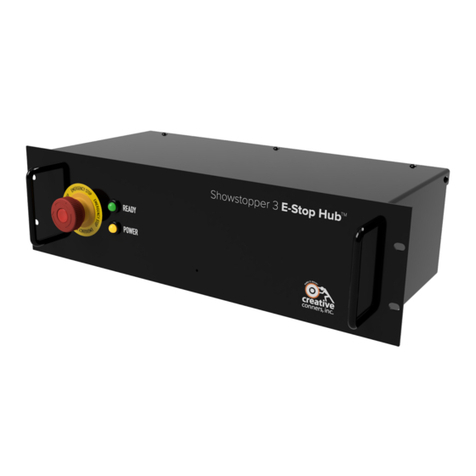
Creative Conners
Creative Conners SHOWSTOPPER 3 E-STOP HUB Reference manual

Asparion
Asparion D700 manual