Ebimicro MFCTH User manual

https://ebimicro.com Hoogkamerstraat 188, 9140 Temse Oos-Vlaanderen Belgium +32 470 80 80 83
ii
CONTENTS
Introduction................................................................................................................................................................................3
Installation ..................................................................................................................................................................................4
Wall mounting installation:......................................................................................................................................................4
Wiring:................................................................................................................................................................................................4
MFCTH Typical wiring diagram..................................................................................................................................................5
Power Supply: .......................................................................................................................................................................................6
Modbus RTU connection: ...............................................................................................................................................................7
Sensor connection:..........................................................................................................................................................................10
Analog Output:...................................................................................................................................................................................14
Relay Output:......................................................................................................................................................................................15
DEVICE HARDWARE SETTING ........................................................................................................................................16
DEVICES MENU SETTING...................................................................................................................................................16
Menu structure and guidance:.............................................................................................................................................. 16
➢Temperature set point...........................................................................................................................................................17
➢Relative Humidity set point.................................................................................................................................................17
➢Heat/Cool Mode........................................................................................................................................................................18
➢Humidifying/Dehumidifying mode..................................................................................................................................18
➢Use Multiple sensors...............................................................................................................................................................18
➢Number of sensors...................................................................................................................................................................19
➢Network Settings......................................................................................................................................................................19
➢Output Type................................................................................................................................................................................20
➢PID Enable...................................................................................................................................................................................20
➢Open Collector Output ...........................................................................................................................................................20
➢Reset ..............................................................................................................................................................................................20
➢Standby.........................................................................................................................................................................................20
MODBUS REMOTE CONTROLLING/MONITORING APPLICTION (Ebicon)...................................................20

https://ebimicro.com Hoogkamerstraat 188, 9140 Temse Oos-Vlaanderen Belgium +32 470 80 80 83
3
INTRODUCTION
MFCTH is a temperature and humidity controller made for industrial use under specific condition
but as well can be widely used as the environmental condition is covered by the device
specification. The controller will be delivered with a high quality temperature and relative
humidity sensor from Senserion AG (Switzerland) with high precision and very stable in long term.
And it can be powered with typical industrial voltage (+24VDC) but as well with a voltage range of
12-36VDC.
Its communication protocol (MODBUS RTU) makes it capable of logging data to a PC and as well
being controlled and monitored remotely from distance(1200m).
A free of charge application (Ebicon) can be downloaded to control and monitor the controller
and also logging the data locally.
A mixed output can help you have different possibilities from analog to relay controlling according
to your needs.
The device has PID control function which helps to have smarter control of your environmental
temperature and relative humidity and more energy efficiency .
Its high rank protection makes its life time much longer and make it capable to operate in different
conditions like humid, dusty and greasy environments.
On top of all the good quality and reliability of our device (which make us proud of) , a default
guarantee of 3 years (on all our products) makes you more sure of having a good support and
insured investment.

https://ebimicro.com Hoogkamerstraat 188, 9140 Temse Oos-Vlaanderen Belgium +32 470 80 80 83
4
INSTALLATION
⚠Please read the installation instruction step by step and make sure all steps are followed
before powering up your device or connecting to your PC.
Note: MFTCH is designed to be mounted on wall but if installing it on din rail required you can use
our din rail kit(adaptor). Because MFCTH is IP64 protected it’s possible to install it at industrial
environment but under its specification (please refer to the device datasheet for more info
available on https://ebimicro.com/mfcth/ )
Wall mounting installation:
You can follow the enclosure dimension on MFCTH datasheet to install the device but
Before mounting MFCTH on the wall please note the following:
•To give your device a longer life time try to install it in an environment covered from direct
son light(the enclosure is NOT UV protected) and it the temperature range of -10 to 50°C.
•The sensor can be connected with maximum 2meter length cable without repeater. This
can go up to 7 meters by using SM8 multiplexer and I2CR repeater and up to 35 meters
by using I2CRL repeater/ line extender.
Wiring:

https://ebimicro.com Hoogkamerstraat 188, 9140 Temse Oos-Vlaanderen Belgium +32 470 80 80 83
5
MFCTH Typical wiring diagram
24VDC
+ -
USB/
RS485
120R 120R
Slave n Slave
n+1
OR
Heat/Cool system
Humidity system
Heat/Cool system
Humidity system
Relay
output 1
Relay
output 2
Analog
Output 1
(A1/GND)
Analog
Output 2
(A2/GND)
DO NOT MIX ANALOG AND RELAY
OUTPUT IN CASE OF USING AC MOTOR
CONTACTOR.
GND_Sensor
SDA_Sensor
SCL_Sensor
V+_Sensor
GND
24V DC
RS485A
RS485 /B
GND_Analog Output1(Temp)
Analog Output1(Temp)
GND_Analog Output2(Rh)
Analog Output1(Rh)
Relay Output2(Rh)
Relay Output1(Tmp)
SHT2x/SHT3x
(*Follow the wiring
diagram printed on PCB)
MFCTH

https://ebimicro.com Hoogkamerstraat 188, 9140 Temse Oos-Vlaanderen Belgium +32 470 80 80 83
6
Follow the wiring label printed on the PCB and match the connection to the following instruction
step by step:
Power Supply:
Prepare a stable DC power source between 12 to 36 VDC (24V recommended) and follow the
terminal labeling to connect it to MFCTH.
⚠Make sure the power is off before and until the installation is completely done.

https://ebimicro.com Hoogkamerstraat 188, 9140 Temse Oos-Vlaanderen Belgium +32 470 80 80 83
7
Modbus RTU connection:
Connection Port
Each device [MASTER or SLAVE] has a connection port with 2 terminals that are used to
communicate with that particular device over MODBUS RTU –RS485. These terminals are mostly
marked as A [or DATA +] and B [or DATA -]. The cabling is done such that all these devices are
connected in parallel. This means that all the A terminals should be connected together and all the B
terminals should be connected together
QUICK TIP- Reversing the ‘A’ and ‘B’ connections of a device can lead to NOT being able to
communicate with that device. In many cases, the whole communication systems can stop working
owing to the reverse polarity [voltage] found on the terminals of incorrectly connected device
In order to avoid this problem, it is recommended that the cable of same color should be used to
connect all A terminals together and similarly cable of same color [but different that the color used
for A] to be used to connect all B terminals together.
Connection between the devices
The easiest and the best way to connect the devices in a MODBUS RTU –RS485 communication is
using DAISY CHAIN method. It is shown below. Any other way of connecting the devices together is
not recommended as it might cause communication issues or damage to the overall system.

https://ebimicro.com Hoogkamerstraat 188, 9140 Temse Oos-Vlaanderen Belgium +32 470 80 80 83
8
Maximum distances and number of slaves
The maximum length of the communication cable should be no longer than 800m [recommended].The
maximum number of devices that can be connected over this network can be 32[for Modbus RTU],
including the master device [The PC in our case]
*apart from the network, No. of slaves also depend on the data logger specification.
Terminal Resistances
In order to avoid signal reflections, it is required to turn on the 120 ohm terminal resistance at ends
of the communication cable. In our case, we are required to turn ON the terminal resister of the last
device. In some cases, it is also required to turn ON the terminal resister of the first device.
Note: The terminal resistor is assembled on the PCB and you can turn it on/off (Enable/ Disable) if
the condition of your network falls in above situation. To activate the terminal resistor please
follow the related instruction for modifying menu on the device or use Ebicon application.
Grounding
For MODBUS communications, properly grounding your instrument is important, especially when
working close to high voltage sources such as PV arrays. An instrument that is not appropriately
grounded can give false readings, fail completely or turn into a safety hazard
QUICK TIP-If you are encountering noise or irregular or abnormal problems with a Modbus serial
link, the problem is likely related to grounding, incorrect shielding, or wiring power wires next to
Modbus wiring.
Type of cables to use
For MODBUS communications, a shielded and twisted pair cable is used. One example of such cable
is Belden 3105A. But any cable with similar characteristics can be used to connect all the devices
together. The shielding can be of 2 types: braided [like a mesh of thin conducting wires] or like a foil
[consiting of a thin sheet of metal covering the twisted wires]. Both types of shielding are OK.

https://ebimicro.com Hoogkamerstraat 188, 9140 Temse Oos-Vlaanderen Belgium +32 470 80 80 83
9
QUICK TIP- This arrangement improves immunity to electromagnetic disturbances because the cable
forms a series of successive coils, each of which faces in the opposite direction to the next one: in
this manner any magnetic field in the environment traverses each pair of coils in opposite directions
and its effect is thus very reduced (theoretically, the effect on each coil is exactly the opposite of the
effect on the next one and thus the effect is cancelled).
Wiring characteristics:
•0.22–0.5 mm2 for runs up to 300 meters
•0.5–0.75 mm2 for runs up to 1200 meters
•Characteristic impedance: 120 Ohm +/- 10%;
•Use Shielded twisted-pair cable if the bus cable exceeds 3m.
•Each shield must be grounded at one side only
•Overvoltage/overcurrent transient protection should be provided

https://ebimicro.com Hoogkamerstraat 188, 9140 Temse Oos-Vlaanderen Belgium +32 470 80 80 83
10
Sensor connection:
The controller detects and reads both SHT2x and SHT3x sensors automatically. Of course it’s
possible to connect one sensor directly to the controller at the time but it’s also possible to read
multiple sensors (up to 8 sensors) in case if required.
Single sensor connection:
For a simple single sensor connection, you need to follow wiring label printed on PCB board. The
maximum cable length is recommended to be maximum 2 meters. If a longer connection is
required it’s possible to use one of our I2C bus repeater(I2CR) or I2C bus repeater/line
extender(I2CRL).
Multiple sensors connection:
It’s possible to connect a sensor multiplexer (SM8) to MFCTH which allows you to read multiple
sensor(up to 8 sensors) with a milliseconds time delay. In case of using sensor multiplexer, MFCTH
will make an average of both temperature and humidity measured by the sensors. To active this
function you need to go to the related menu using the MFCTH keypad on the device or by using
our Modbus master software (Ebicon) as following:
1. Connect a SM8 multiplexer to your MFCTH controller by following the wiring label printed
on PCB.
2. Connect your sensors to SM8 (follow wiring instruction of SM8 Datasheet).

https://ebimicro.com Hoogkamerstraat 188, 9140 Temse Oos-Vlaanderen Belgium +32 470 80 80 83
11
⚠Always start from connection number 1 and don’t skip connection
enumeration to avoid error in reading sensors. It’s also highly advised to use the
same type of sensors (choose all the sensors from SHT2x or SHT3x) to reduce
reading time and errors.
3. Enable using Multiple sensors (see Menu Instruction).
4. Edit the number of sensors you will connect and would like to read.
I2C repeater/ Line extender:
In case of longer bus length required to install your sensor far from the controller unit, we have
two solutions for a short range (5meters) and also long range (35meters). The installation and
wiring needs to be done following the type of the chosen option for your needs accordingly:
1. I2CR (I2C bus repeater for maximum 5 meters length connection):

https://ebimicro.com Hoogkamerstraat 188, 9140 Temse Oos-Vlaanderen Belgium +32 470 80 80 83
14
Analog Output:
MFCTH Controller comes with two separate analog output for temperature and relative humidity.
Both output can be use individually to control your environmental controlling equipment(cooling
or heating/humidifying or dehumidifying) like motor drivers or any kind of controlling equipment
that would be used to control the temperature or relative humidity of your installation. The
outputs are providing 4 analog output type as follow:
1. 0-10VDC
2. 0-20mA
3. 4-20mA
4. PWM
Analog output connection:
A1 : Temperature Control Output
A2 : Relative Humidity Control Output

https://ebimicro.com Hoogkamerstraat 188, 9140 Temse Oos-Vlaanderen Belgium +32 470 80 80 83
15
Each output can be affected by PID control calculation is case if activated. This will give a huge
effect for a smarter and more efficient control of your environment.
Relay Output:
As like analog output, MFCTH will provide you also to individual relay output for both temperature
and relative humidity. It can be used to activate a switch, alarming system or any kind of warning
or activator system that would work with the relay specification (see Figure 1).
Relay Output Specification:

https://ebimicro.com Hoogkamerstraat 188, 9140 Temse Oos-Vlaanderen Belgium +32 470 80 80 83
16
Figure 1
Relay Output Connection:
Relay Output 1(NO1|COM1|NC1) : Temperature Control Output
Relay Output 2(NO2|COM2|NC2) : Relative Humidity Control Output
DEVICE HARDWARE SETTING
The MFCTH doesn’t requires any hardware setting in order to operate.
DEVICES MENU SETTING
Most of settings of MFCTH are possible to be set(modified) using keypad of the device. By default
the screen shows measured temperature and relative humidity after each other for about 5 secs
each with a prefix character to recognize one from the another. The temperature will be shown
with char as prefix and relative humidity with char as prefix.
Menu structure and guidance:

https://ebimicro.com Hoogkamerstraat 188, 9140 Temse Oos-Vlaanderen Belgium +32 470 80 80 83
17
Measured Value
+Press both(ENTER/EXIT
MAIN MENU)
NET SETTING
TEMP SETPOINT
RH SET POINT
ID(1-247)
NBT RESISTOR(0-1)
PARITY(0-2)
BAUD RATE(0-6)
:Up :Down :SHORT PRESS=RETURN
| LONG PRESS=SAVE
:0=DIS | 1=EN
:0=NONE | 1=EVEN/2=ODD
:0=4800 | 1=9600 | 2=19200 |
3=38400 | 4=57600 | 5=115200 |
6=230400
OUTPUT TYPE
PID EN/DIS
:0=0-10V | 1=0-20mA | 2=4-
20mA | 3=PWM
HEAT/ COOL MODE
HUMID/ DEHUMID
MODE
OPEN COLLECTOR
RESET
STAND BY
:0=DIN PID | 1=EN PID
:0=Cooling | 1=Heating
:0=Deumidifying | 1=Humidifying
:0=EN OPEN COLLECTOR |
1=DIS OPEN COLLECTOR
USE MULTI SENSORS :0=DISABLED | 1=ENABLED
NUMBER OF
SENSORS(1-8)
Menu Structure
As explained the default value to show on display are measured temperature and relative
humidity but you can enter the menu settings by pressing both up/down buttons at the same
time. The menu will start with set value for temperature set point and you can scroll Up/ Down
using Up/ Down buttons as shown in menu structure.
Menu Instruction:
➢Temperature set point
You can set the setpoint of desired temperature for your environment. It’s the set point
which your controller reacting on to activate the relay (Output 1) or changing the analog
output value(A1) accordingly and depending on the setting for cooling or heating mode.
➢Relative Humidity set point
You can set the setpoint of desired humidity level for your environment. It’s the set point
which your controller reacting on to activate the relay (Output 2) or changing the analog

https://ebimicro.com Hoogkamerstraat 188, 9140 Temse Oos-Vlaanderen Belgium +32 470 80 80 83
18
output value(A2) accordingly and depending on the setting for humidifying or
dehumidifying mode.
➢Heat/Cool Mode
The controller can be set to two different mode to controll the temperature:
1. Heat Mode: means your enviremet soppused to get heated and by default it
gets cold. So, the controller needs to try to heat it up to the desired
temperature set point as it goes below the set point.
2. Cool Mode: means your enviremet soppused to get coled down and by default
it gets warm. So, the controller needs to try to cool it down to the desired
temperature set point as it goes above the set point.
➢Humidifying/Dehumidifying mode
The controller can be set to two different mode to controll the relative humidity:
1. Humidifying Mode: means your enviremet soppused to get humid and by
default it gets dry. So, the controller needs to try to humidify it up to the
desired humidity set point as it goes below the set point.
2. Dehumidifying Mode: means your enviremet soppused to dehumidified and by
default it gets humid. So, the controller needs to try to dehumidfy to the
desired hemid set point as it goes above the set point.
➢Use Multiple sensors
It’s possible to connect and read multiple sensors (up to 8) to the controller to get average
of measured temperature and relative humidity in case if needed.
⚠Attention:
•To use this function you need an extra device called SM8 which you
can find in the list of our products|accessories.(see
https://ebimicro.com )
•In case if using this feuture please make sure your multiple
sensors(at least 2) are connected to the SM8 and the SM8 is
connected to the MFCTH controller according to the wiring
diagram of the devices(please refer to the datasheet of SM8 for
connecting the sensors and wiring).
•Enabling this function without connecting multi sensors will causing
errors in communication with the sensor and misbehave of the
controller.

https://ebimicro.com Hoogkamerstraat 188, 9140 Temse Oos-Vlaanderen Belgium +32 470 80 80 83
19
➢Number of sensors
After connecting the desired number of sensors to SM8(and then connecting it to MFCTH)
you need to set the number of connected sensors here.
➢(Modbus)Network Settings
It’s possible to configure the MFCTH network parameters including the device ID in this
menu. By entering this menu you will be in the NETWORK SETTING branch of the menu
structure as following:
•Device ID
The device ID needs to be unique within your Modbus network, in case if you
have more than one Modbus device connected to the network you can set it
between 1 to 247.
Note: If you use only one device, you can skip this step as leave it as its default
value 1.
•NBT Resistor
Depending on your network connection length and the amount of devices
connected to your network you need to enable (activate) the terminal resistors
of 1 or maximum 2 devices.
⚠Attention: Please never active the terminal resistors of two device within
your network to avoid dropping the bus resistance below the acceptable level and
getting communication issues.
•Parity
As a part of Modbus over serial line specification, it’s possible to set the parity to
“None”, “Even” or “Odd”.
⚠Attention: It’s highly recommended to leave this setting to its default if it’s
not really need to edit else it will cause losing communication to the master (in
our case Ebicon application).
•Baud Rate
Baud rate like Parity is also a part of Modbus over serial line specification and
changing this parameter will effect the communication speed. For a long bus line
it’s recommended to set it as low as could be sufficent enough but if your
communaction had no issue leave that as default.
⚠Attention: Changing Baud Rate only on MFCTH controller which is the
slave in your network will lose your connection to the master which the PC in that
case. So, please make sure the Master and Slave are running at the same Baud
Rate.

https://ebimicro.com Hoogkamerstraat 188, 9140 Temse Oos-Vlaanderen Belgium +32 470 80 80 83
20
➢Output Type
MFCTH has 4 types of analog output which you can choose according to your needs. This
change will be applied to both analog outputs the same for temperature and relative
humidity.
0 : 0-10VDC
1 : 0-20mA
2 : 4-20mA
3 : PWM
➢PID Enable
As a nice feuture of MFCTH it has a PID controller which will make your enviremental
control much smarter and energy efficient. It will also reasult to a smooth changing of
temprature and relative humidity in case if you use analog output to drive your system.
Note: The PID parameters have been set by deffault to the most efficient values for
temperature and Relative humidity control and the parameters will effect the PID result
of both temperature and humidity. To modify the PID values according to your needs and
your envirement you can use Ebicon application.
➢Open Collector Output
The analog output of MFCTH can be set to Open Collector as well in case if needed.
⚠Attention: Enable this function if you familiar with the topic or ask your expert if it
needed to be enabled for your installation.
➢Reset
It’s always possible to reset all your configurations. By resetting your controller all
Modbus Holding registers will be back to their default value (including device ID).
⚠Attention: Resetting the device will set the device ID to the default value
which is 1 and that may cause communication issues in case you have a device
with same ID (1) on your network.
➢Standby
Setting your controller to stand by mode will disable all outputs. It will be useful in case
of holding the control on your environmental condition like maintaining your installation
etc.
MODBUS REMOTE CONTROLLING/MONITORING APPLICTION (EBICON)
As a very important part of our solutions to control your environmental condition we provide you
a free of charge software (Ebicon) developed to monitor and control(configure) your controller’s
Table of contents
Popular Controllers manuals by other brands
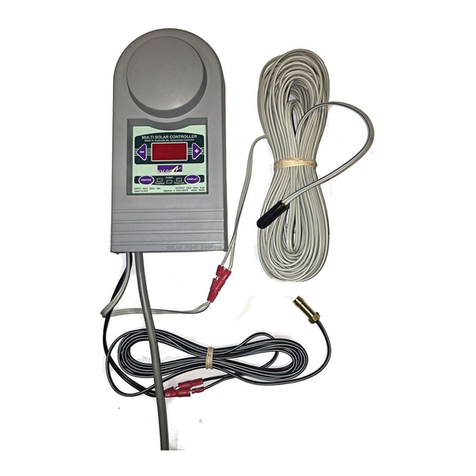
Ascon Pool
Ascon Pool MS3D user manual
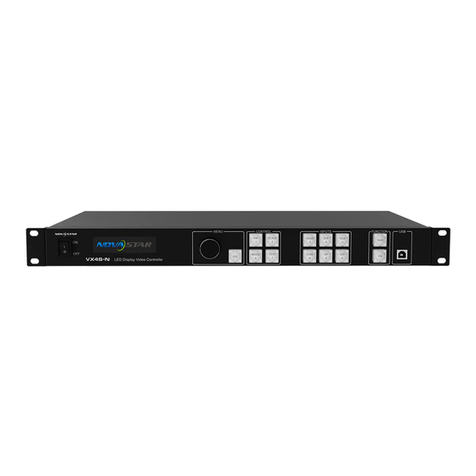
NovaStar
NovaStar VX4S-N user manual
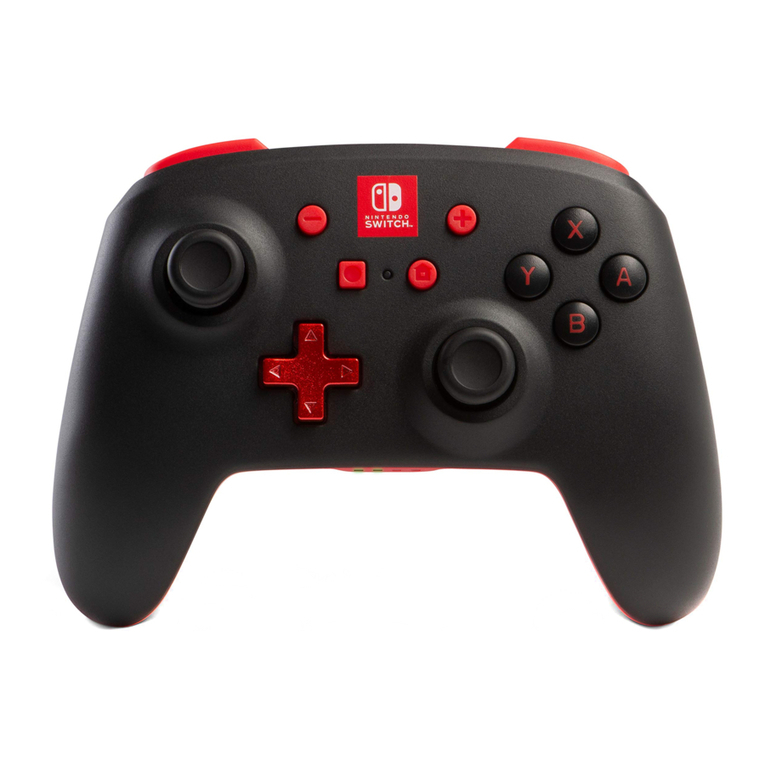
Power A
Power A ENHANCED WIRELESS CONTROLLER user manual
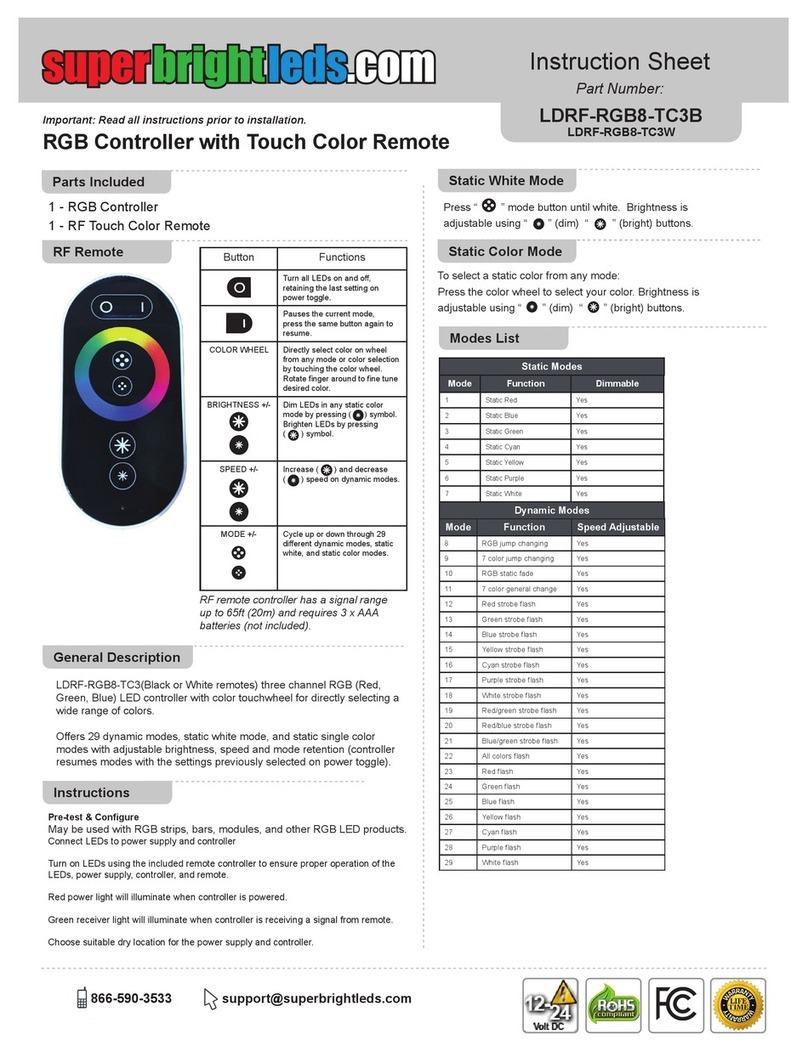
superbrightleds
superbrightleds LDRF-RGB8-TC3B instruction sheet
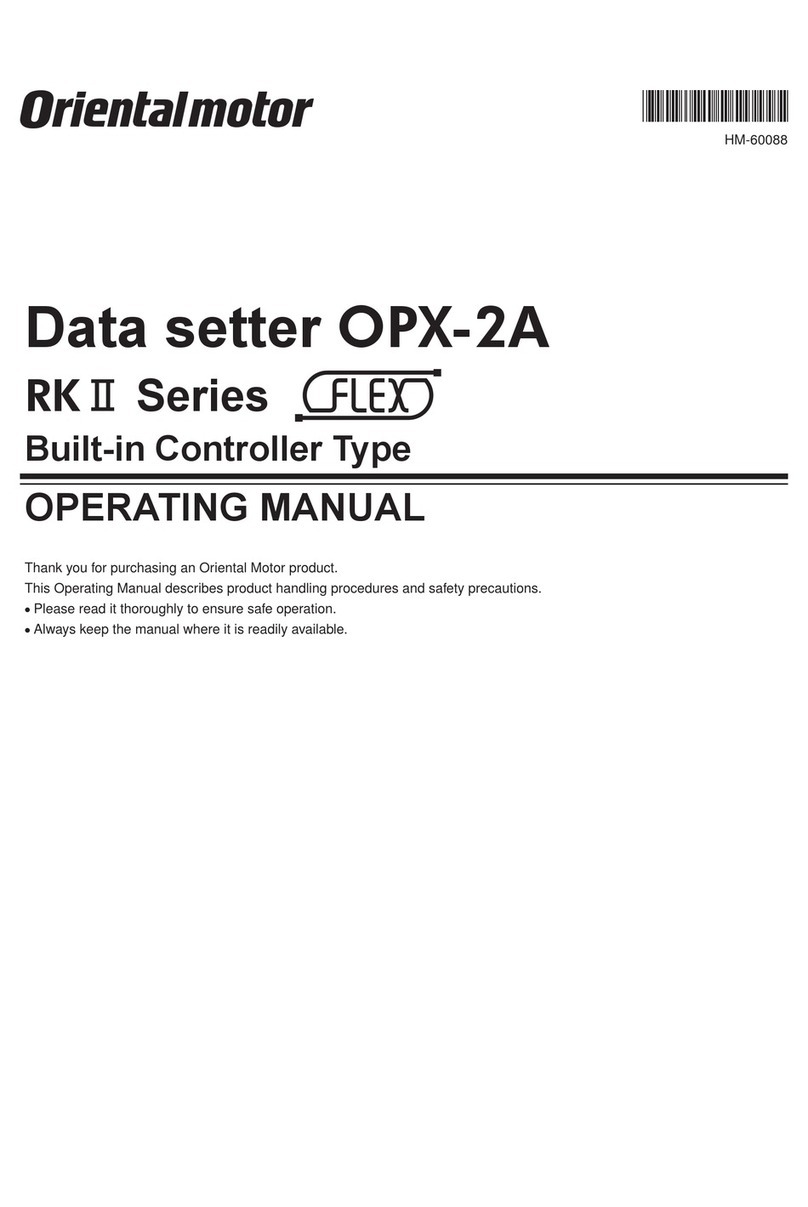
Oriental motor
Oriental motor FLEX RK II Series operating manual
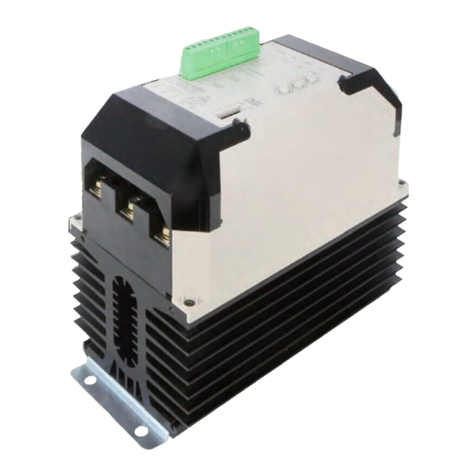
HANYOUNG NUX
HANYOUNG NUX TPR-3SL instruction manual