Eltorque EQS 1374 User manual

Page 1 of 41
User Manual
EQS 1374
MT50 & MT150
Electrical Multi-turn Valve Actuators
Revision Date: 24.02.2022

Page 2 of 41
Table of Contents
Table of contents
1. Introduction........................................................................................................................................3
1.1 System Overview ......................................................................................................................3
1.2 Description ................................................................................................................................4
1.3 Features....................................................................................................................................5
1.4 Area of use................................................................................................................................5
1.5 Technical support information...................................................................................................5
1.6 Reader groups ..........................................................................................................................6
1.7 Notation used in this manual.....................................................................................................6
1.8 Related documentation.............................................................................................................6
1.9 Disclaimer .................................................................................................................................7
1.10 Terms and abbreviations ..........................................................................................................7
1.11 About this manual .....................................................................................................................9
2. HSE Information ............................................................................................................................. 10
2.1 Care and cleaning of actuator................................................................................................ 10
2.2 Disposal and waste handling ................................................................................................. 10
3. Specifications and manual operation .......................................................................................... 12
3.1 Technical data........................................................................................................................ 12
3.2 External construction.............................................................................................................. 14
3.3 About the Rolls-Royce Marine UT valve manifolds ............................................................... 15
3.4 Operating conditions.............................................................................................................. 16
3.5 Actuator duty type.................................................................................................................. 16
3.6 Manual operation ................................................................................................................... 17
4. Installation....................................................................................................................................... 20
4.1 Mounting actuator on valve.................................................................................................... 20
4.2Electrical installation............................................................................................................... 22
4.3 Pinout..................................................................................................................................... 23
4.3.1 Digital Interface..................................................................................... 24
4.3.2 CAN Interface ....................................................................................... 25
4.3.3 Dual CAN Interface............................................................................... 26
4.4 Earthing of product................................................................................................................. 26
4.5 Configuration of actuator........................................................................................................ 27
4.5.1 Selecting correct configuration.............................................................. 27
5. Maintenance, service and troubleshooting ................................................................................. 29
5.1 Maintenance........................................................................................................................... 29
5.2 Spare parts............................................................................................................................. 29
5.3 Troubleshooting ..................................................................................................................... 30
5.4 Control system examples....................................................................................................... 31
Torque and Screw Recommendations.................................................................. 36
A. 1. Eltorque torque recommendations......................................................................................... 36
A. 2. Mounting screws and lubrication............................................................................................ 36
Earthing Methods in Maritime Installations .......................................................... 39
B. 1. Summary:............................................................................................................................... 39
B. 2. Drawing references:............................................................................................................... 39

Page 3 of 41
1. INTRODUCTION
1.1 System Overview
The Eltorque Lifelong Intelligent control concept provides maintenance-free,
configurable eco-friendly and fully electric actuators with real-time feedback.
The Eltorque actuators are divided in two main families:
•QT-series of actuators are ideal for quarter-turn valves such as butterfly and
ball-valves.
•MT-series of actuators are multi-turn actuators optimized for linear valves
such as globe valves, and with a form factor that make the MT-series ideal for
manifold actuation.
The Eltorque actuators are fully electric and can be connected in series. They
offer a plug and play solution with low installation costs and high level of
security. By combining the Eltorque actuators with the Eltorque Hybrid Marine
Cable, the cost of installation is even further reduced.
The Electric serial connected actuator installation eliminates the cable clutter,
transportation loss, air or oil leakage associated with conventional actuator
installations.
The use of permanent magnet-based motor technology and efficient electric,
mechanics and firmware design guarantee an eco-friendly and cost-efficient
ownership.
Eltorque actuators have a proven track record of lifelong maintenance-free
operation with 15 years of proven operation.
Fig. 1: System overview example

Page 4 of 41
Fig. 2: MT150 on 6xND125 X-over manifold
1.2 Description
Table 1: Product overview
Part number
Description
MT50 1.0 with CANopen Interface for DN50
MT50 1.0 with Digital Interface for DN50, AC version
MT50 1.0 with Digital Interface for DN50, DC version
MT50 1.0 with CANopen Interface for DN80
MT50 1.0 with Digital Interface for DN80, AC version
MT50 1.0 with Digital Interface for DN80, DC version
MT50 1.0 with CANopen Interface for DN100
MT50 1.0 with Digital Interface for DN100, AC version
MT50 1.0 with Digital Interface for DN100, DC version
MT150 1.0 with CANopen Interface for DN125
MT150 1.0 with Digital Interface for DN125
MT150 1.0 with CANopen Interface for DN150
MT150 1.0 with Digital Interface for DN150

Page 5 of 41
1.3 Features
The Eltorque actuators provides a wide range of attractive features:
•Optimized single-axis architecture, ensuring a compact and low-weight
actuator.
•Accurate real-time magnetic position control with no mechanical limit
switches, ensuring maintenance-free operation.
•Few spare parts - low lifetime costs.
•Easy setup and commissioning –low installation cost.
•Specific alarms including over-torque and temperature –providing high
operation safety.
•Robust implementation of CANbus ensuring a reliable serial connection.
•Self-lock feature which allows movements from the motor, but locks
movements from the gear side.
•Remote programming via the CAN cable.
•Specific alarms including over-torque and temperature –providing high
operation safety.
•Fast and precise motor reduces the closing time.
1.4 Area of use
Eltorque actuators are an ideal choice in a wide range of Maritime and Onshore
systems including, but not limited to:
•Cargo handling
•Bilge and ballast
•Tank gauging
•SPS system
•Anti-heeling systems
•RSW systems
•Bulk handling
•Fuel systems
•Hydro power and district heating
•Waste water treatment
•HVAC system
•Fire water system
•Oil Production system, oil transfer line
1.5 Technical support information
If you require technical support outside of this manual, we recommend that you
use the support functions available on the web-site or contact us via e-mail.
If you have feedback to this manual, that should also be routed through e-mail.
Eltorque AS
Julianus Holms veg 34
7071 Trondheim
Norway
Web: www.eltorque.com

Page 6 of 41
e-mail: [email protected]
Phone: +47 74 85 55 20
Fax: +47 74 85 55 12
1.6 Reader groups
The following reader groups have been defined for this manual:
•Project and engineering personnel
•Installation personnel
•Operators
•Supervisors
•Technical support personnel
•Technical management personnel
1.7 Notation used in this manual
The following notations have been used in this manual:
Bold is used for commands and menu selection
Italic is used to give emphasis to information. It is also used for names of
documents referred to in the manual.
Note! Note is used to draw attention to important or helpful information.
Caution! A caution is used when there is a danger that the equipment is damaged if
you do not follow the instructions.
Warning is used to draw attention to information of very high importance,
for example to avoid injuries to personnel.
1.8 Related documentation
This manual refers to the following documentation.
Table 2: Related documentation
Document
Document ID
Hybrid Marine Cable data sheet
Eltorque document ID 1946
Eltorque E3C Manual
Eltorque document ID 1687
Guidelines for earthing in maritime
installations
Published by the Norwegian Electrical Safety
Directorate. Available on net or supplied by
Eltorque on request.

Page 7 of 41
1.9 Disclaimer
The information contained in this document is subject to change without prior
notice. Eltorque AS shall not be liable for errors contained herein or for incidental
or consequential damages about the furnishing, performance, or use of this
document. It is the customer’s responsibility to verify that he has the latest
revision available by checking the document area of www.eltorque.com
1.10Terms and abbreviations
Table 3: Terms and abbreviations
Term
Description
ABS
American Bureau of Shipping.
AFD
Asbestos Free Declaration.
Analog Control
Step-less control utilizing analog signals, e.g., 4-20 mA. Allows positioning of
the valve actuator between Open and Closed.
BTO
Break to open.
CAN/CANbus
Controller Area Network.
CANbus is a fieldbus which allows communication between a maximum of 127
actuators connected to the same network. It is not a “master-slave” network (ref.
Modbus), hence all the nodes in the network can actively send messages at their
own initiative. Communication is prioritized meaning that urgent messages are
transmitted and received before information with lower priority. Compared to
Modbus, CANbus has quite a few advantages:
−More reliable communication
−More nodes per network
−More control and configuration features are available
−Higher performance
CANopen
CANopen is a higher-level protocol and is running on top of the CAN protocol for
all Eltorque actuators.
The standard consists of an adressing scheme for the nodes on the CAN bus and
several small protocols for communicating with each node. In terms of the OSI
model, CANopen implements the levels above, including the network layer.
CCS
Central Control System.
Communication
Interface Box
Electronic device controlling the actuator according to signals from an overall
control system such as a PLC or other type of electronic controller.
Configuration
The set-up of parameters, which affects the actuator’s performance and behavior.
Digital Control
Simple control utilizing relays, on/ off switches and indicators. Allows only Open
or Closed functionality for a valve actuator.
DNV GL
Det Norske Veritas Germanischer Lloyd.
E3C
Eltorque Common Configuration Controller.
E-VCI
Eltorque Valve Control Interface
E-VCS
Eltorque Valve Control System offers a dedicated control system
for operation of Eltorque actuators.
Eltorque Valve Control System is suitable for installations where the operator
requires full control of all valves and pumps, and in addition monitor level,
temperature, flow and pressure.

Page 8 of 41
Term
Description
Hazardous area
Area in which the permanent or periodical presence of explosive substances
causes a risk of explosion.
Products described in this manual are not suitable for use in hazardous areas.
Eltorque can deliver actuators for use in such areas if required. Please contact
your local representative for further details.
HMI
Human Machine Interface.
HSE
Health, Safety and Environment.
HVAC
Heath, ventilation and air condition
IACS
International Association of Classification Societies
IAS
Integrated Automation System.
ICS
Integrated Control System.
IMO
International Maritime Organization
LR
Lloyd’s Register.
MAST
Maximum allowable stem torque/thrust.
MD
Material Declaration.
MEPC
The Marine Environment Protection Committee
OSI model
Open Systems Interconnection model. The model is a conceptual model that
standardizes communication systems without regard to the underlying internal
structure. The model partitions a communication system into abstraction layers.
Out of range
Definition of position. The outgoing shaft is outside the defined position area.
PF
Power factor
PCB
Printed circuit board.
PLC
A Programmable Logic Controller is a digital computer used for automation of
industrial processes, such as control of machinery on factory assembly lines,
measurement and control of process plants etc.
RSW
Refrigerated sea water system
SDoC
Supplier Declaration of Conformity.
SOLAS
Safety Of Life At Sea –conversion under IMO concerning safety for personnel and
ships at sea
VA
Voltampere
UPS
Uninterruptable power supply.
Valve
A valve is a device that controls the flow of materials (gases, fluidized solids,
slurries, or liquids) by opening, closing, or partially obstructing various
passageways.
This manual refers to quarter-turn valves with a 90 degrees movement between
Closed and Open position.
Valve actuator
A device for control of valves in various process control systems.
Valve top
flange
The flange on top of the valve which integrates the actuator.
As an example, most butterfly valves comprise four screw holes for the flange
integration and a square stem for valve operation.
Within range
Definition of position. The outgoing shaft is within the defined position area.

Page 9 of 41
1.11About this manual
Chapter 1 introduces the product and this manual.
This chapter is intended for all reader groups.
Chapter 2 informs on health, safety and environment issues.
The reader group for this chapter is for supervisors, technical support and
technical management personnel.
Chapter 3 provides product specifications and manual operations instructions.
This chapter is intended for all reader groups
Chapter 4 covers the mechanical installation on valves and the electrical
installation of power and control signal.
The reader group for this chapter is installation personnel.
Chapter 5 provides maintenance and troubleshooting information. The reader
group for this chapter is installation and maintenance personnel.
Appendix A gives an overview of torque recommendations.
The reader group for this chapter is installation personnel.
Appendix B includes the document “Earthing Methodology in Maritime
Installations” The reader group for this chapter is installation personnel,
technical support and technical management personnel.

Page 10 of 41
2. HSE INFORMATION
This chapter includes safety information that the user needs to know to operate
the equipment without doing harm to personnel or the environment.
The operation of the equipment is safe provided that the recommended
operating procedures are followed. There are specific hazards however
that need to be addressed so that the user knows how to deal with them.
Electrical installations shall be designed and installed by personnel with
certifications according to applicable laws and regulations. Ensure that
all such work is done according to applicable laws and regulations.
Service must always be performed by trained personnel.
2.1 Care and cleaning of actuator
Caution! Do not use ammonia, alkaline cleaners, lye or strong acid for cleaning as
this can damage the protective anodized layer of the product surface.
Caution! Do not use high pressure power washer directly on the actuators as the
product is not IP69K rated.
2.2 Disposal and waste handling
All batteries and electronic equipment may contain substances harmful to the
environment. After removing used equipment, return them for disposal
according to local governmental guidelines.

Page 11 of 41
This page is left intentionally blank

Page 12 of 41
3. SPECIFICATIONS AND MANUAL OPERATION
3.1 Technical data
MT50 1.0
MT150 1.0
Torque1
10-50 Nm
50-150 Nm
Valve stem speed1
7-17 rpm
5-15 rpm
Valve applications2
Rolls-Royce Marine UT multi-turn bilge and X-over valve manifolds, PN10
DN50
DN80
DN100
DN125
DN150
Closing time1
20 sec
25 sec
30 sec
60 sec
65 sec
Physical Properties
Dimensions (H/W/D)
411/ 115/ 224 mm
550/ 146/ 274 mm
Weight
15 kg
28 kg
Encapsulation
IP68 (5m 1 hr)
Corrosion protected aluminium enclosure
Operation temperature
-25 –55 C
Colour
Black and silver
Over/ under temperature
protection
Motor current is switched off in case of over-temperature
Stator coils utilized as heating elements in case of low temperatures
Electrical and Control Properties
Supply voltage AC
110-240 V AC (50/60 Hz) or 125-230 V DC
Power consumption
Max: 120W/ 280 VA, Standby: 11W
Max: 240W/ 560 VA, Standby: 14W
Supply voltage DC at
actuator (min-nom-max)3
20 - 24 - 28 VDC
Not available
Current at DC operation
<3 ADC (20VDC)
Open/Close time (20VDC)
ND50/80/100: 33s/42s/51s
Cable glands
Up to 4 pcs M20 glands allows serial connection of
power supply and fieldbus wiring.
Threaded holes in actuator capsule.
Use IP68 glands for all wires, EMC type for fieldbus wiring.
Control interfaces
Digital: 2 DI (Open & Close) & 3 DO (Open,Closed & Alarm)
CANopen Fieldbus: Max 127 nodes per network, allows positioning and other
extended control of actuator.
Position sensor
Absolute position sensor, provides correct feedback even after a power failure.
Resolution 4,85 °/
Maximum 13 turns
Resolution 5,84 °/
Maximum 16 turns
Configuration
USB connection to PC using E3C, Manual EQS ID 1687
Configurable parameters
Valve type, Open and Closed positions .
Actuator speed, torque and valve position regions.
Inverted IO or fieldbus parameters depending on control interface
Emergency and safety
Manual operation
Standard feature using ergonomic crank shaft.
Mechanical valve position indicator.
Visual status indication by LED when actuator is powered.
Safety function disables motor in case of manual operation while actuator is
powered.
Number of turns
Closed - Open
39
49
59
70
80
1
Configurable using E3C, Manual EQS ID 1687
2
Adapted flange bracket and stem connection is required and must be ordered with the actuator
3
This implies that a VDC power grid should be star topology (e.g. one actuator per 24VDC power
line).

Page 13 of 41
MT50
MT150
Fig. 3: External dimensions
411
550
146
274

Page 14 of 41
3.2 External construction
1. External housing
2. Cable gland holes 4 x M20
3. Valve bracket
4. Valve stem adapter with red valve position
indicator
5. Valve position scale
6. Manual Operation shaft cover
7. Crank handle for manual operation
8. Status indicator LED
Closed = YELLOW
Closing = Blinking YELLOW
Open = GREEN
Opening = Blinking GREEN
Stopped or positioned = Flashing GREEN
Alarm = RED
9. Top Cover
10. Driving pins
Front view
Top view
Bottom view
Fig. 4: External construction
1
2
5
3
4
6
7
8
10
4
9

Page 15 of 41
3.3 About the Rolls-Royce Marine UT valve manifolds
The Rolls-Royce Marine UT valve manifolds consist of two
or more multi-turn globe valves in five different sizes.
The valve size refers to the nominal diameter of the valve,
which in turn affects the flow capabilities:
-DN50
-DN80
-DN100
-DN125
-DN150
The globe valves can be arranged in bilge manifolds where
2 or 3 valves are aligned in one row.
Such valves are always “non-return”, i.e. valve plug is not
fixed to the stem and will lie on the valve seat because of
gravity when the valve is opened. Such valves will only allow
flow in one direction when the liquid from the pipes
underneath the valve manifold lifts the plug upwards.
The valves can also be arranged in X-over manifolds where 4 or 6 valves are aligned in 2x2 or 2x3
rows.
In these manifolds, the plug is fastened to the stem and will be lifted up when the valve is opened.
This allows flow in both directions.
Fig. 5: 1-box 2-cell X-over and Bilge valve manifolds
When globe valves are operated, the maximum torque is required near closed position:
-Forces from the flowing medium will push the plug up or downwards depending on flow direction.
Note: The force will increase with both pressure and valve size.
-Friction in the bonnet and stem threads increases both when the plug is in contact with the body
and with forces applied by the flowing medium.
Note: The valves are equipped with a grease nipple for lubrication of valve stem threads, it is
important that grease is applied regularly to ensure friction in the threads is kept as low as
possible.
The MT actuators are equipped with electronic torque sensor to ensure that the actuator stops in case
the valve’s operation torque becomes too high.
Note: When the actuator is configured during the installation, it is important that its torque/ force limits
are set according to valve size and pressure. This procedure is described in section 4.5.
Fig. 5 Globe valve components
(Source: Wikipedia –Globe Valve)

Page 16 of 41
3.4 Operating conditions
The MT50 & MT150 1.0 is especially suitable for use below deck on ships and other offshore vessels
due to its compact design, low power consumption and robust construction.
It can also be used in other applications as long as the following criteria’s are met:
-Operating temperature is kept within specified limits.
-Actuator is placed indoors and not exposed to direct sunlight.
-Protected from extensive corrosive atmospheres like on open deck of ships or other areas
exposed to salt water spray. Cleaning or pollution with strong alkaline or acidic chemicals can also
cause corrosion problems.
-Actuator must not be placed in hazardous areas where the presence of explosive atmospheres
might cause explosion hazard.
3.5 Actuator duty type
When electric valve actuators operate, they generate internal heat due to thermal loss in motor and –
control electronics. The MT actuators combine low power consumption with high efficiency to ensure
that internal thermal loss is kept low.
Still, duty cycle needs to be considered when designing the valve control system to ensure that the
actuators can operate the valves without over-heating.
In case the actuator’s internal temperature becomes too high, it will send out an alarm signal via the
control interface. Should the temperature continue to rise, the actuator will shut down the motor until
temperature decreases to a safe level.
To avoid problems with over-temperature alarms and actuator shutting down, duty cycle requirements
should be considered before selecting actuator.
Fig. 6: Open-Close and positioning duty
Actuators used for Open-Close duty either open or close the valves, intermediate positions are not
approached. The valves are rarely operated and the interval between operations may be a few
minutes or even several months.
Open-Close duty will be relevant for MT actuators with Digital control interface.
Actuators used for positioning duty will approach defined intermediate positions to set a static flow
through a pipeline, applicable positions also include Open and Closed.
Positioning duty will be relevant for MT actuators with CANopen Interface.
For both these duty types, the same maximum continuous running time (tclose or tpos) is 5 minutes
followed by a rest period (trest) of minimum 5 minutes.
The duty type limitations stated above applies for maximum operation temperature, and torque, see
section 3.1. If operating temperatures and or torque are lower, the actuator can be operated more than
the duty type limitations stated above.
Valve position
Time
tclose trest tpos trest tpos

Page 17 of 41
3.6 Manual operation
In case of power failure, control system error or another fault preventing normal operation of the
actuator, it can be operated manually without the need of additional tools:
1. Unscrew and remove Manual Operation
shaft cover.
Fig. 7: Removing MO shaft cover.
2. Attach crank handle on MO shaft.
3. Turn Clockwise to close or Counter-
clockwise to open valve.
4. Valve position can be seen on the visual
indicator scale.
5. When MO is completed, remove crank
handle and refit it onto its holder.
Fig. 8: Visual valve position indicator
Fig. 9: Manual operation features
Open
Close
5
3
2
4

Page 18 of 41
Note: The actuator has a sensor which is
sensing that the MO shaft cover is removed.
Actuator cannot be operated remotely until the
cover is replaced and tightened against the top
cover. The actuator’s indicator LED will be Red
when cover is removed and motor current will be
switched off.
6. Refit and tighten MO shaft cover until it
stops against top cover.
Fig. 10: Refitting MO shaft cover

Page 19 of 41
This page is intentionally left blank

Page 20 of 41
4. INSTALLATION
4.1 Mounting actuator on valve
The RRM UT valve manifolds and MT actuators must be mounted with the valve stem vertically and
facing upwards. Before mounting actuator, please make sure there is sufficient space for installation,
service and manual operation above and around it:
Fig. 11: Space for installation, service and manual operation
1. Remove hand-wheel for manual
operation.
2. Unscrew and remove the 4 fastening
screws for the valve bonnet.
Note: These screws must be discarded
as longer ones are required to fasten
the actuator.
Fig. 12: Removing hand-wheel and fastening
screws.
2
1
This manual suits for next models
2
Table of contents
Other Eltorque Controllers manuals
Popular Controllers manuals by other brands
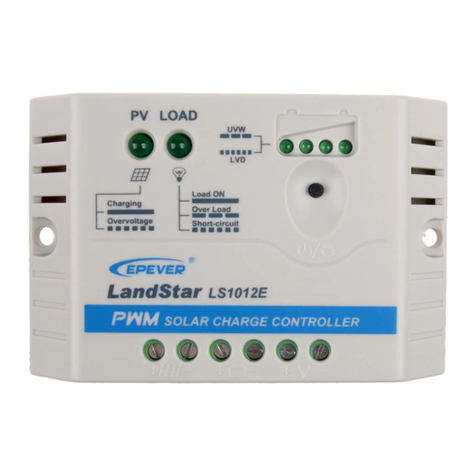
Epever
Epever LS-E Series user manual
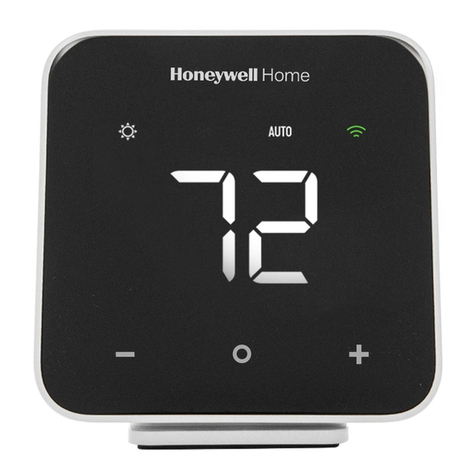
resideo
resideo Honeywell Home PRO D6 quick guide
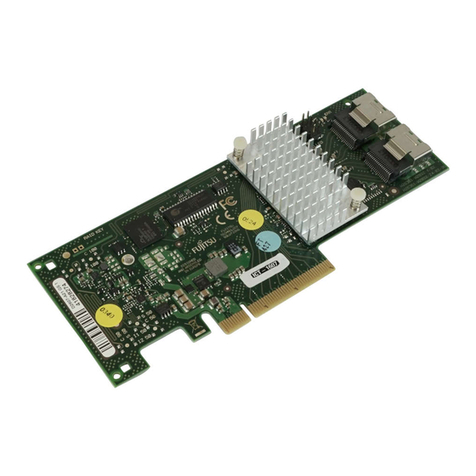
Fujitsu
Fujitsu RAID 0/1 SAS based on LSI MegaRAID user guide
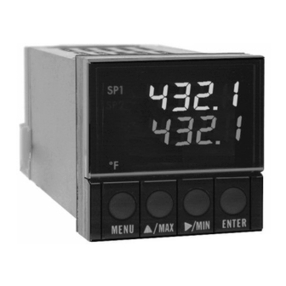
Omega
Omega MICROMEGA CN77000 series user guide
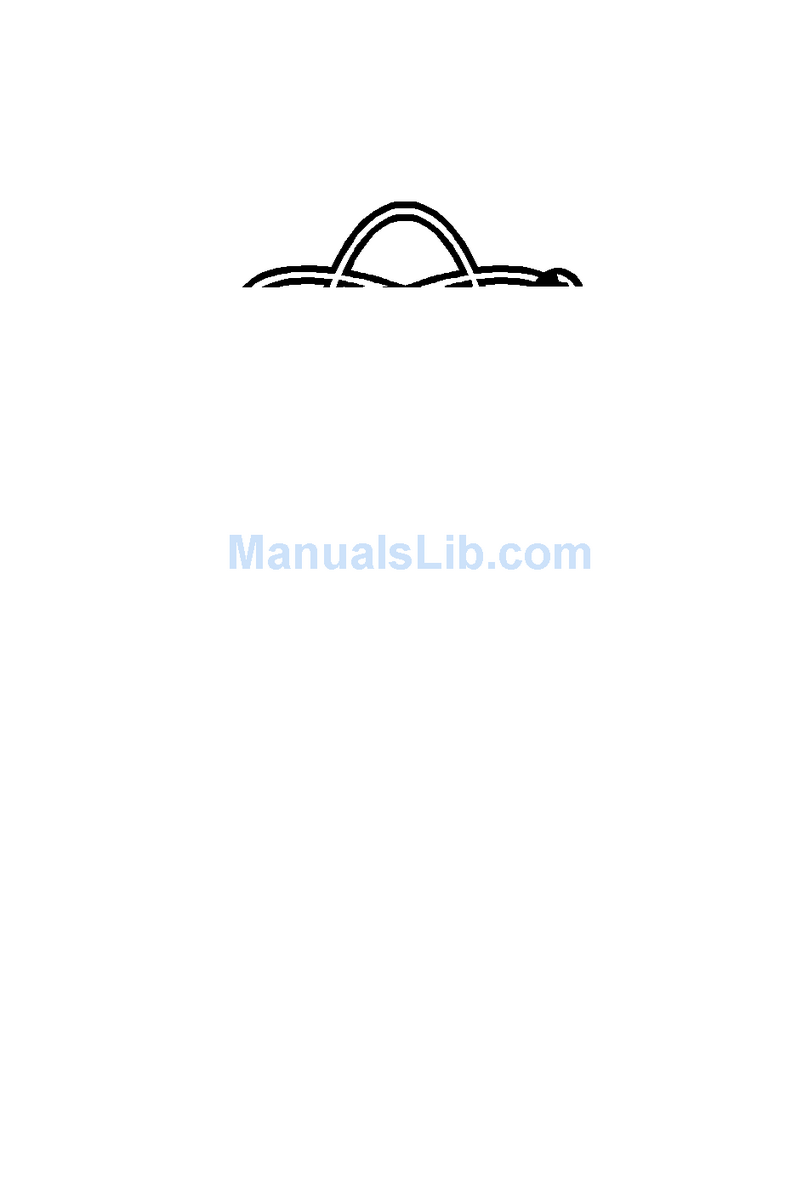
Ryger
Ryger NAVIGATOR DMX Controller instruction manual
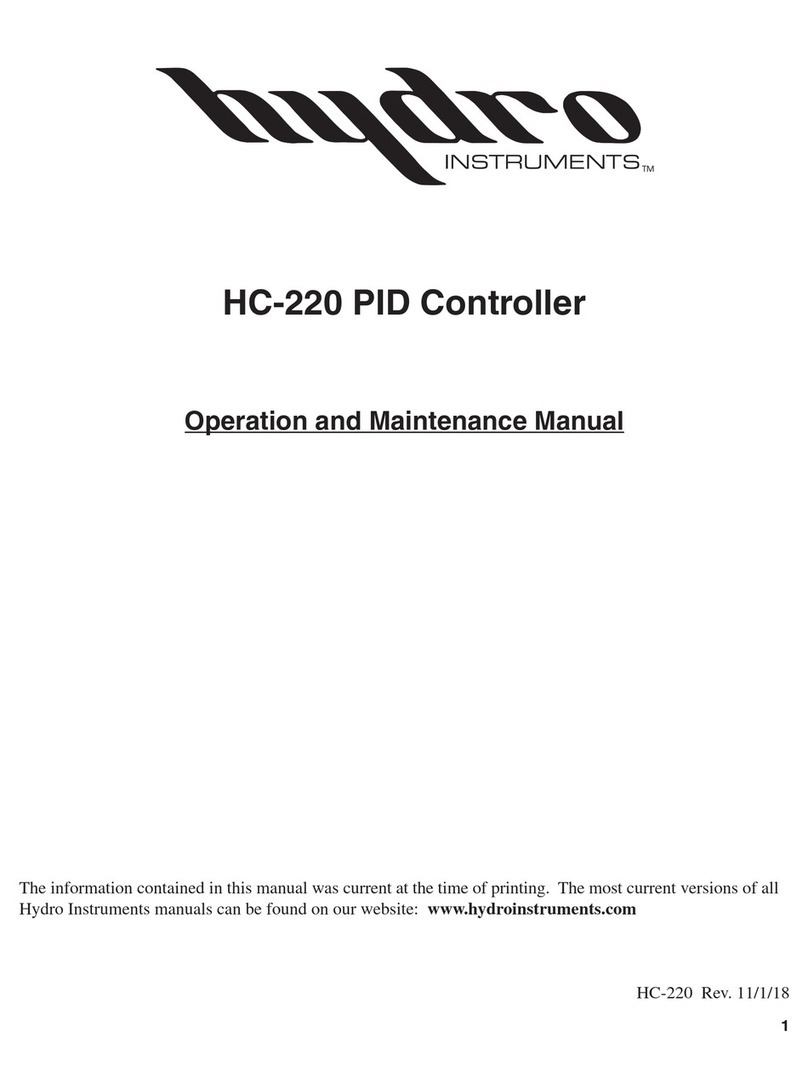
Hydro Instruments
Hydro Instruments HC-220 Operation and maintenance manual