Emerson Fisher 846 User manual

www.Fisher.com
Fisher™846 Current-to-Pressure Transducer
Contents
Introduction
Scope of Manual 2.............................
Description 2.................................
Specifications 2...............................
Educational Services 5.........................
Installation 6..................................
Hazardous Area Classifications and Special
Instructions for Safe‐Use and Installation
in Hazardous Locations 7.....................
Mounting 8..................................
Pressure Connections 8........................
Supply Pressure 10.........................
Output Pressure 14........................
Electrical Connections 14.......................
Venting Ports 15..............................
Signal Interruption 15..........................
Calibration 16..................................
Standard Performance:
Full Range Input, Direct Action 18.............
Multirange Performance:
Full Range Input, Direct Action 18.............
Standard Performance:
Split Range Input, Direct Action 19.............
4 to 12 mA Input Signal 19..................
12 to 20 mA Input Signal 19.................
Standard Performance:
Full Range Input, Reverse Action 20............
Multirange Performance:
Full Range Input, Reverse Action 20............
Standard Performance:
Split Range Input, Reverse Action 21...........
4 to 12 mA Input Signal 21..................
12 to 20 mA Input Signal 21.................
Transporting the Module Final Assembly 22.......
Principle of Operation 22........................
Electronic Circuit 22...........................
Magnetic Actuator 23..........................
Pilot Stage 23.................................
Booster Stage 24..............................
Troubleshooting 25.............................
Diagnostic Features 25.........................
Stroke Port 25.............................
Figure 1. Fisher 846 Current‐to‐Pressure Transducer
X0234
Remote Pressure Reading (RPR) 25...........
Using a Frequency Counter to read the
RPR Signal 25.........................
In‐service Troubleshooting 26...................
Troubleshooting in the Shop 29.................
Maintenance 31................................
Module Final Assembly 32......................
Removing the Module Final Assembly 34......
Replacing the Module Final Assembly 35.......
Electronic Circuit Board 36......................
Remote Pressure Reading (RPR) Jumper 36.....
Range Jumper 37..........................
Action 37.................................
Removing the Electronic Circuit Board 37......
Replacing the Electronic Circuit Board 38......
Pilot/Actuator Assembly 38.....................
Action 38.................................
Removing the Pilot/Actuator Assembly 39.....
Replacing the Pilot/Actuator Assembly 39.....
Module Subassembly 40........................
Terminal Compartment 40.....................
Exhaust and Stroke Port Screens 41..............
Parts 42......................................
Instruction Manual
D102005X012
846 Transducer
February 2021

Instruction Manual
D102005X012
846 Transducer
February 2021
2
Introduction
Scope of Manual
This instruction manual provides installation, operating, calibration, maintenance, and parts ordering information for
Fisher 846 current‐to‐pressure transducers. Refer to separate manuals for instructions covering equipment used with
the transducers.
Do not install, operate or maintain an 846 current‐to‐pressure transducer without being fully trained
and qualified in valve, actuator, and accessory installation, operation, and maintenance. To avoid
personal injury or property damage, it is important to carefully read, understand, and follow all of the
contents of this manual, including all safety cautions and warnings. If you have any questions about
these instructions, contact your Emerson sales office before proceeding.
Description
The 846 current‐to‐pressure transducer, shown in figure 1, accepts an electrical input signal and produces a
proportional pneumatic output. Typically, 4 to 20 mA is converted to 0.2 to 1.0 bar (3 to 15 psi). Models are available
in direct or reverse action and field‐selectable for full or split range inputs. Refer to the Calibration section for more
information on input/output combinations.
The most common application of the transducer is to receive an electrical signal from a controller and produce a
pneumatic output for operating a control valve actuator or positioner. The 846 may also be used to produce a signal
for a pneumatic receiving instrument.
The 846 is an electronic I/P transducer. It has a single electronic circuit board, as shown in figure 2. The circuit contains
a solid‐state pressure sensor that monitors output pressure and is part of an electronic feedback network. The
self‐correcting ability provided by the sensor/circuit combination allows the transducer to produce a very stable and
responsive output signal.
All active mechanical and electrical components of the 846 are incorporated into a single, field‐replaceable module
called the module final assembly, shown in figure 2. The module final assembly contains the electronic circuit board,
pilot/actuator assembly, and booster stage. The module final assembly is easily removed by unscrewing the module
cover. Its design minimizes parts and reduces the time required for repair and troubleshooting.
The terminal compartment and module compartment are separated by a sealed compartment wall. This
multi‐compartment housing also protects the electronics from contaminants and moisture in the supply air.
Specifications
WARNING
This product is intended for a specific range of pressures, temperatures, and other application specifications. Applying
different pressure, temperature and other service conditions could result in a malfunction of the product, property damage
or personal injury.
Specifications for the 846 transducer are listed in table 1.

Instruction Manual
D102005X012
846 Transducer
February 2021
3
Table 1. Specifications
Input Signal
Standard Performance:
4 to 20 mA DC, 4 to 12 mA DC, or 12 to 20 mA DC.
Field adjustable split ranging.
Multirange Performance:
4 to 20 mA DC. Consult factory for split range input
Equivalent Circuit
See figure 3
Output Signal(1)
Standard Performance:
(Consult factory for split range output)
Direct Action (Minimum span of 6 psi)
Typical outputs: 0.2 to 1.0 bar (3 to 15 psi).
Rangeability between 0.1 and 1.2 bar (1 and 18 psi)
Reverse Action (Minimum span of 11 psi)
Typical outputs: 1.0 to 0.2 bar (15 to 3 psi)
Rangeability between 1.2 and 0.1 bar (18 and 1 psi)
Multirange Performance:
Direct Action (Minimum span of 6 psi)
Typical outputs: 0.2 to 1.9 bar (3 to 27 psi), 0.4 to
2 bar (6 to 30 psi), and 0.3 to 1.7 bar (5 to 25 psi)
Rangeability between 0.03 and 2.3 bar (0.5 and
33 psi)
Reverse Action (Minimum span of 11 psi)
Typical outputs: 1.9 to 0.2 bar (27 to 3 psi), 2 to
0.4 bar (30 to 6 psi), and 1.7 to 0.3 bar (25 to 5 psi)
Rangeability between 2.3 and 0.03 bar (33 and
0.5 psi)
Supply Pressure(2)
Standard Performance: 1.2 to 1.6 bar (18 to 24 psi)
Multirange Performance:
0.2 bar (3 psi)(3) greater than the maximum
calibrated output pressure
Maximum: 2.4 bar (35 psi)
Supply Pressure Medium
Clean, dry air
Per ISA Standard 7.0.01
A maximum 40 micrometer particle size in the air
system is acceptable. Further filtration down to 5
micrometer particle size is recommended. Lubricant
content is not to exceed 1 ppm weight (w/w) or
volume (v/v) basis. Condensation in the air supply
should be minimized
Per ISO 8573-1
Maximum particle density size: Class 7
Oil content: Class 3
Pressure Dew Point: Class 3 or at least 10°C less than
the lowest ambient temperature expected
Output Air Capacity(4)
Standard: 6.4 m3/hr (240 scfh) at 1.4 bar
(20 psi) supply pressure
Multirange: 9.7 m3/hr (360 scfh) at 2.5 bar
(35 psig) supply pressure
Maximum Steady‐State Air Consumption(4)
0.3 m3/hr (12 scfh) at 1.4 bar (20 psi) supply pressure
Temperature Limits(2)
Operating: -40 to 85_C (-40 to 185_F)
Storage :-40 to 93_C (-40 to 200_F)
Humidity Limits
0 to 100% condensing relative humidity
Performance(5)
Note: The performance of all 846 I/Ps is verified
using computer automated manufacturing systems
to ensure that every unit shipped meets its
performance specifications
Accuracy: $0.30% of output span
Linearity, Hysteresis, and Repeatability: $0.3% of
span.
Temperature Effect (total effect including zero and
span): $0.07%/_C (0.045%/_F) of span
Vibration Effect: $0.3% of span per g during the
following conditions:
5 to 15 Hz at 4 mm constant displacement
15 to 150 Hz at 2 g. 150 to 2000 Hz at 1 g.
per SAMA Standard PMC 31.1, Sec. 5.3, Condition 3,
Steady State
Shock Effect: $0.5% of span, when tested per SAMA
Standard PMC 31.1, Sec. 5.4.
Supply Pressure Effect: Negligible
-Continued-

Instruction Manual
D102005X012
846 Transducer
February 2021
4
Table 1. Specifications (continued)
Performance (continued)(5)
Electromagnetic Interference (EMI): Tested per IEC
61326‐1:2013. Meets emission levels for Class A
equipment (industrial locations) and Class B
equipment (domestic locations). Meets immunity
requirements for industrial locations (Table A.1 in the
IEC specification document). Immunity performance
is shown in table 2.
Leak Sensitivity(4):Less than 1.0% of span for up to
4.8 m3/hr (180 scfh) downstream leakage.
Overpressure Effect: Less than 0.25% of span for
misapplication of up to 7.0 bar (100 psi) supply
pressure for less than 5 minutes to the input port.
Reverse Polarity Protection:
No damage occurs from reversal of normal supply
current (4 to 20 mA) or from misapplication of up to
100 mA.
Connections
Supply Air, Output Signal, and Output Gauge:
1/4‐18 NPT internal connection
Electrical: 1/2‐14 NPT internal conduit connection
Adjustments
Zero and Span: screwdriver adjustments located in
terminal compartment.
Remote Pressure Reading (RPR)
Jumper selectable, ON or OFF, if unit includes
option
Frequency Range: 0 to 10,000 Hz
Amplitude: 0.4 to 1.0 Vp‐p
Required Operating Voltage with Remote pressure
Reading Off
Min. 6.0 V (at 4 mA)
Max. 7.2 V (at 20 mA)
Required Operating Voltage with Remote Pressure
Reading On
Min 6.4 V (at 4 mA)
Max. 8.2 V (at 20 mA)
Electrical Classification
Hazardous area:
CSA C/US—Intrinsically Safe, Explosion-proof,
Non-Incendive
FM—Intrinsically Safe, Explosion-proof, Non-Incendive
ATEX—Intrinsically Safe, Flameproof, Type n
IECEx—Intrinsically Safe, Flameproof
Electrical Housing:
Tropicalization (Fungus test per MIL-STD-810)
CSA C/US—Type 4X
FM—Type 4X
ATEX—IP66(6)
IECEx—IP66(6)
Other Classifications/Certifications
CUTR— Customs Union Technical Regulations
(Russian, Kazakhstan, Belarus, and Armenia)
ESMA— Emirates Authority for Standardization and
Metrology - ECAS-Ex (UAE)
INMETRO—National Institute of Metrology, Quality,
and Technology (Brazil)
KGS—Korea Gas Safety Corporation (South Korea)
NEPSI— National Supervision and Inspection Centre
for Explosion Protection and Safety of
Instrumentation (China)
PESO CCOE— Petroleum and Explosives Safety
Organization - Chief Controller of Explosives (India)
Contact your Emerson sales office for
classification/certification specific information
Construction Materials
Housing: Low‐copper aluminum with polyurethane
paint, or 316 stainless steel
O‐Rings: Nitrile, except silicone for sensor O‐rings.
Options
Fisher 67CFR filter regulator, supply and output
gauges or tire valve remote pressure reading, module
cover with multiple stroke ports, stainless steel
housing, or stainless steel mounting bracket.
Weight
Aluminum: 2.9 kg (6.5 lb) excluding options
Stainless Steel: 6.7 kg (14.8 lb) excluding options
-continued-
Other manuals for Fisher 846
2
Other Emerson Transducer manuals
Popular Transducer manuals by other brands
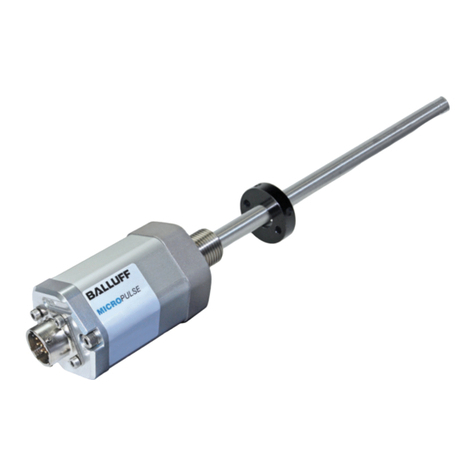
Balluff
Balluff BTL7-S5 B-M Series Condensed guide
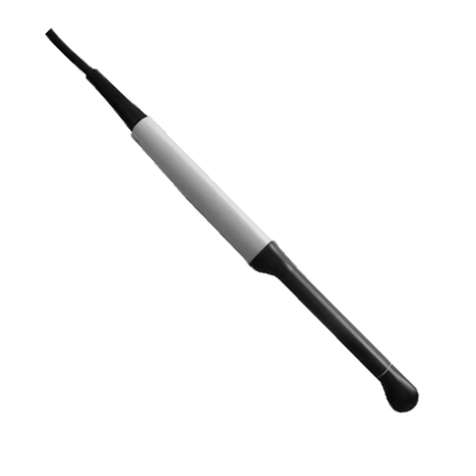
B-K Medical
B-K Medical Type 8506-S user guide

HYDACELECTRONIC
HYDACELECTRONIC HDA 4800 user manual
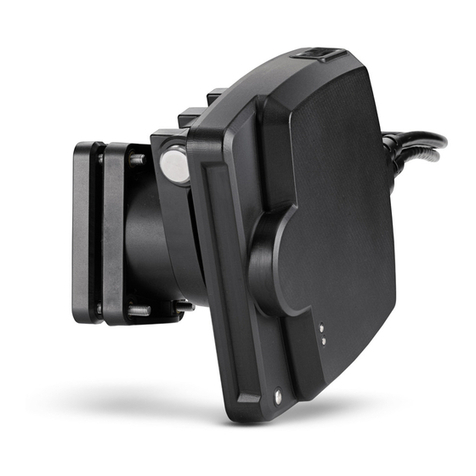
Humminbird
Humminbird MEGA Live instructions
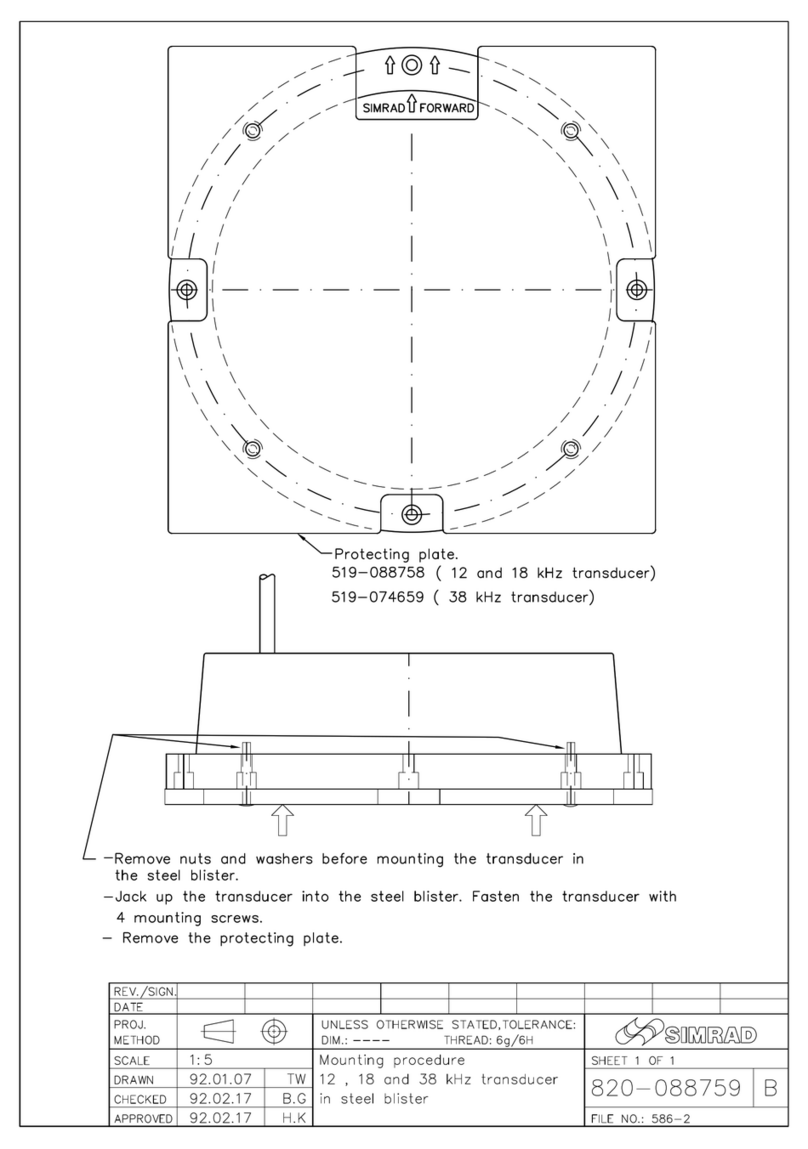
Simrad
Simrad TRANSDUCER MOUNTING PROCEDURE - SCHEMA REV B manual
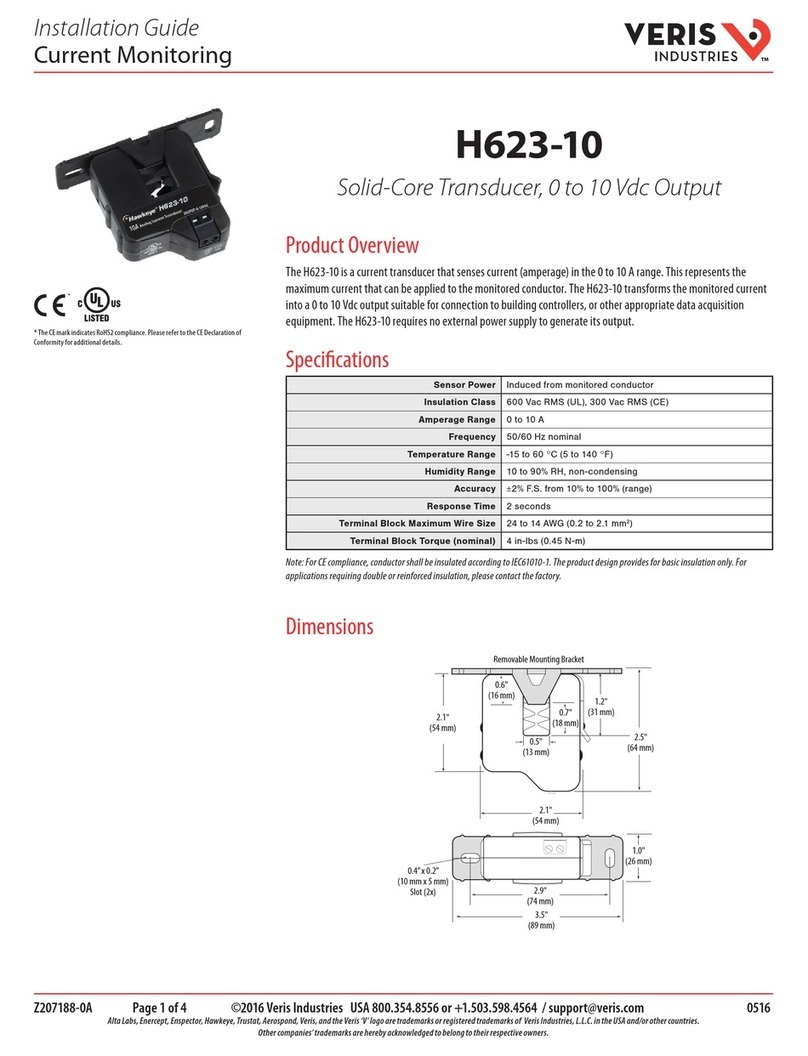
Veris Industries
Veris Industries H623-10 installation guide