esera automation ECO 10 User manual

Art. No. 11601-24
*if the sensor or actuator supports Auto-E-Connect. For details, please refer to the operating instructions of the sensor or actuator.
All rights reserved. Reproduction as well as electronic duplication of this user guide, complete or in part, requires the written consent of
ESERA GmbH. Errors and technical modification subject to change. ESERA GmbH 2021
www.esera.de 11601-24 V1.0 R1.1 Manual Page 1 of 13
User Guide
ECO 10 1-Wire Controller
Professional 1-Wire Controller
of the 3rd Generation
The ECO 10 1-Wire Controller represents a high-
performance 3rd generation 1-Wire Interface for
sensors and actuators
Fully automatic integration of sensors* and
actuators*
Auto-E-Connect Support Level I and II
1-Wire Controller for autonomous communication
and updating of the 1-Wire Network.
Fast readout of all 1-Wire Components in a
1-2 seconds cycle
Cyclic output of the processed 1-Wire data in plain
text
Data communication via socket server/client, TCP
or UDP
Designed for small to large 1-Wire Networks
Power supply of the 1-Wire Network
Top-hat rail housing for control cabinet installation
Wide supply voltage range
Management of all ESERA and many standard
1-Wire Modules and Chips
Note
Before you start assembling the ECO 10 and put the unit into operation, read this operating manual
thoroughly, especially the section on safety instructions.
All settings and configurations of the ECO 10 are carried out with the Config Tool 3 software.
You can find this software on the ESERA website. Please refer to the operating instructions for Config
Tool 3, which you will find under the "HELP/SUPPORT" tab within the Config Tool 3 software.

*if the sensor or actuator supports Auto-E-Connect. For details, please refer to the operating instructions of the sensor or actuator.
All rights reserved. Reproduction as well as electronic duplication of this user guide, complete or in part, requires the written consent of
ESERA GmbH. Errors and technical modification subject to change. ESERA GmbH 2021
www.esera.de 11601-24 V1.0 R1.1 Manual Page 2 of 13
1 Product description
Sensors and Aktuators
The ECO 10 1-Wire Controller supports up to 30 sensors, actuators, iButton keys or memory devices (hereinafter
referred to collectively as Devices). Up to 5 data values can be output per 1-Wire Device. This means that the
ECO 10 can provide up to 150 data values, which is a very large number and a very good price per data value
ratio.
Data interface
The ECO 10 1-Wire Controller has an ASCII data interface.
You can communicate with your smart home or industrial control, e.g. PLC, supervisory control and data
acquisition systems (SCADA) ASCII TCP protocol with the ECO 10 Controller.
In this way, the ESERA ECO 10 equipments provide an optimal interface between modern digital
1-Wire Devices and your monitoring system.
Autonomous management
The ECO 10 is intended for the autonomous management of a 1-Wire Network. You no longer need to worry
about 1-Wire commands or formulas for evaluating the 1-Wire Devices. The ECO 10 independently scans
the 1-Wire Network for new 1-Wire Devices, reads their Auto-E-Connect data, automatically adapts* the
device libraries and outputs the adapted data in plain text, adapted to the scanned 1-Wire Devices.
Designed for all 1-Wire Networks
The 1-Wire interface of the ECO 10 is specially designed to safely operate small to very large 1-Wire
Networks with long cable distances.
1-Wire Devices can be operated simultaneously in parasitic or normal mode.
The currently strongest 1-Wire interface has been developed for maximum data security even for complex
network structures.
Formatted Data output
The ECO 10 outputs the 1-Wire Device data ready prepared, e.g. for Temperature sensors in C° cyclically.
It is only necessary to divide by 100.
In addition, the article number for ESERA-Modules can be entered, the calculation and output is adapted to
the function of the module.
System time / real-time clock
You do not have a real-time clock with battery buffering in your system? No problem, the ECO 10 will gladly
provide the time with date. The real-time clock (RTC) is supplied by a maintenance-free gold cap (super
capacitor) for approx. 2 days if the supply voltage fails.
What is a goldcap (super capacitor)? You can find an explanation here:
https://de.wikipedia.org/wiki/Superkondensator
Power supply
For power supply, the ECO 10 has a wide range input of 9 - 30VDC and is therefore equally well suited for
industry-typical 12V and 24V system supplies.
Suitable DIN rail or plug-in power supply units can be found in our webshop.
Commissioning
Support Videos for commissioning and configuration can be found on our Website www.esera.de under
„Service and Support“, Support Videos.
Note
Basics and tips on the 1-Wire Bus system can be found in the ESERA Online Shop under
1-Wire Basics or please refer to our eBook in the shop under Training/Documentation.

Art. No. 11601-24
*if the sensor or actuator supports Auto-E-Connect. For details, please refer to the operating instructions of the sensor or actuator.
All rights reserved. Reproduction as well as electronic duplication of this user guide, complete or in part, requires the written consent of
ESERA GmbH. Errors and technical modification subject to change. ESERA GmbH 2021
www.esera.de 11601-24 V1.0 R1.1 Manual Page 3 of 13
2 Auto-E-Connect Support
The ECO 10 1-Wire Controller supports Auto-E-Connect Level I and II.
Auto-E-Connect Level III is supported from the ECO 100 series onwards.
3 Auto-E-Connect System
With the launch of the ECO controllers, the ESERA Auto-E-Connect® 1-Wire Plug and Play system for the
1-Wire Bus is now introduced and supported.
This means that fully automatic configuration of the 1-Wire Devices* (sensors and actuators) on the 1-Wire
Bus is now possible.
It is optimised for commercial and industrial applications and enables significant added value beyond sensor
and chip data.
The Auto-E-Connect function is built up in three levels. Currently there are Level I, Level II and Level III
available.
With Auto-E-Connect Level III, fully automatic configurations of the 1-Wire Devices on the
1-Wire Bus are possible. It is optimised for industrial and IoT applications and enables significant added
value beyond sensor and chip data.
With the Auto-E-Connect function, ESERA Devices are recognised fully automatically, suitable libraries are
started and ready-formatted data is output.
The Auto-E-Connect functionality will be available for the ECO Controller and ESERA-Station 200 Pro from
2021.
Auto-E-Connect Level I
OWD Detect: detection of new sensors* and actuators* and automatic start of adapted libraries
Auto-E-Connect Level II
Visualisation product data: read out and visualise the Auto-E-Connect and manufacturer data of sensors* and
actuators*, e.g. article number, date of manufacture, firmware and hardware version.
Auto-E-Connect Level III, not ECO 10, only supported from ECO 100 PRO onwards.
Extended Plug and Play System for 1-Wire Bus
oPre Configuration: The OWD number for the next installation can be written to the 1-Wire Device*.
oAutomatic Positioning: The Device* logs on to each ECO Controller with Auto-E-Connect III with the new
desired OWD number. This automatic login works up to the maximum possible OWD number of the ECO
Controller.
oSensorfinder Function: The ECO 10 can activate a status LED within the ESERA 1-Wire Pro sensors*. The
status LED flashes or lights up permanently for a certain time. This makes it much easier to detect a device
in a 1-Wire Network. Faster detection saves a lot of time and therefore money when searching for a 1-Wire
Device.
oClasses Assignment: ESERA 1-Wire Devices are assigned to OWD classes with the same properties. This
assignment enables fully automatic visualisation and data evaluation in control systems. A class list is
available from ESERA.
For further information on the ESERA Auto-E-Connect system, please refer to the ESERA website and the
ESERA Config Tool 3.
Auto-E-Connect is registered by ESERA GmbH as a German and European Patent.

*if the sensor or actuator supports Auto-E-Connect. For details, please refer to the operating instructions of the sensor or actuator.
All rights reserved. Reproduction as well as electronic duplication of this user guide, complete or in part, requires the written consent of
ESERA GmbH. Errors and technical modification subject to change. ESERA GmbH 2021
www.esera.de 11601-24 V1.0 R1.1 Manual Page 4 of 13
4 Technical data
Ethernet interface: TCP/IP or UDP, Socket Server or Client
- 10/100 MBit Ethernet Interface (RJ45)
- Auto Negotiation (Full-duplex and Half-duplex)
- Auto MDI/MDIX
- Support für DHCP and fixed IP-Adresse
Auto-E-Connect: Level I and II supported
Auto-E-Connect Level III is only supported from ECO 100 onwards
Data, Firmware Update
and Configuration ESERA Config Tool 3
Software Support: ECO Dashboard 100
Supply voltage: 9-30VDC
Current consumption max. 1000mA
Power supply RTC: Goldcap, Buffering of the internal clock (RTC) in the event of a supply voltage failure for
approx. 2 days. In the event of a longer failure, the RTC must be reset. The gold cap is
charged after approx. 2 hours.
1-Wire interface : 1-Wire Bus (+5V, ground (GND) and Data)
Protective circuits: ESD-, overvoltage and reverse polarity protection
Connection: Screw terminals (up to 2.5qmm cable cross-section)
Output voltage: +5V (+/-10%), max. 300mA, overload, overvoltage and short-circuit protected
Isolation: Galvanic isolation between Ethernet and 1-Wire interface
Supported DS2401, DS1963, DS1990, DS1820, DS18S20, DS18B20, DS2413, DS2438, DS2450
1-Wire Devices: DS2408, DS2405, DS2406 (input only), DS2423, other chips on request. We will be
happy to support further components as an OEM product for you.
5 Ambient conditions
Operating temperature: -5°C to +50°C
Storage temperature: -20°C to +70°C
Relative humitidy: 10% bis 92% (non condensing)
Room classification: Operate only in dry rooms
Protection system: IP20
Protection class: III
Dimensions: 35 x 90 x 70mm (WxHxD)
6 Conformity
EN 50090-2-2
EN 61000-4-2, ESD
EN 61000-4-3, HF
EN 61000-4-4, Burst
EN 61000-4-5, Surge
EN 61000-6-1, Interference immunity
EN 61000-6-3, Interference radiation
RoHS
7 Display LED
The module has various indicator LEDs.The function oft he displays is as follows
Display
Designation
Function
LED Green
PWR
Display for supply voltage
LED Green
DATA
After switching on the unit, the LED flashes 3x
flashes during 1-Wire activity
flashes when sending data via the data interface
flashes very quickly if "KAL Receive" has been
activated and the "KAL Messages" of the control
system are missing.
LED Yellow
data interface
Network Link LED,
Lights up when there is a network connection
LED Green
data interface
Network Data LED
Lights up when there is data traffic via the data interface

Art. No. 11601-24
*if the sensor or actuator supports Auto-E-Connect. For details, please refer to the operating instructions of the sensor or actuator.
All rights reserved. Reproduction as well as electronic duplication of this user guide, complete or in part, requires the written consent of
ESERA GmbH. Errors and technical modification subject to change. ESERA GmbH 2021
www.esera.de 11601-24 V1.0 R1.1 Manual Page 5 of 13
8 Connection diagram
Module top side, 1-Wire Bus
1= ground / GND 1-Wire
2= 1-Wire Data
3= 5V output
Module bottom side, power supply
11 = Minus supply voltage
12 = Plus supply voltage
5 = Reset Button on the inside
9 Reset Button
Operating the reset button with non-conductive
material, e.g. match.
The reset is carried out via the reset button of the
system.
carried out. When the button is pressed, the unit is
restarted. The stored data is retained, but
all connections are interrupted
This keystroke does not correspond to an
interruption of the power supply.
Note
The Minus pole of the supply voltage / power supply unit of the ECO 10 should be connected to earth
potential (PE). This establishes a functional earth
Note
The module may only be operated at the voltages and under the ambient conditions specified for it. The
operating position of the unit is arbitrary.
The modules may only be put into operation by a qualified electrician.
For further information on the operating conditions, see the following instructions under "Operating
conditions".

*if the sensor or actuator supports Auto-E-Connect. For details, please refer to the operating instructions of the sensor or actuator.
All rights reserved. Reproduction as well as electronic duplication of this user guide, complete or in part, requires the written consent of
ESERA GmbH. Errors and technical modification subject to change. ESERA GmbH 2021
www.esera.de 11601-24 V1.0 R1.1 Manual Page 6 of 13
10 Connection example 1-Wire Multisensor
11 Connection example only iButton reading unit

Art. No. 11601-24
*if the sensor or actuator supports Auto-E-Connect. For details, please refer to the operating instructions of the sensor or actuator.
All rights reserved. Reproduction as well as electronic duplication of this user guide, complete or in part, requires the written consent of
ESERA GmbH. Errors and technical modification subject to change. ESERA GmbH 2021
www.esera.de 11601-24 V1.0 R1.1 Manual Page 7 of 13
12 Connection example with iButton and/or RFID reading unit

*if the sensor or actuator supports Auto-E-Connect. For details, please refer to the operating instructions of the sensor or actuator.
All rights reserved. Reproduction as well as electronic duplication of this user guide, complete or in part, requires the written consent of
ESERA GmbH. Errors and technical modification subject to change. ESERA GmbH 2021
www.esera.de 11601-24 V1.0 R1.1 Manual Page 8 of 13
13 Connection example 1-Wire Hub III, sensors and actuators

Art. No. 11601-24
*if the sensor or actuator supports Auto-E-Connect. For details, please refer to the operating instructions of the sensor or actuator.
All rights reserved. Reproduction as well as electronic duplication of this user guide, complete or in part, requires the written consent of
ESERA GmbH. Errors and technical modification subject to change. ESERA GmbH 2021
www.esera.de 11601-24 V1.0 R1.1 Manual Page 9 of 13
14 Software
Data interface ESERA ASCII Text protocol
The Ethernet interface is configured with the aid of the Windows ESERA programme Config Tool 3, which
can be found in the download area of the ESERA online shop.
15 Configuration and Communikation with ECO 10
The ECO 10 has extensive configuration and formatting options that are read out and operated with the
ESERA Config Tool 3.
Since communication between ECO 10 and Config Tool 3 takes place via the open ESERA ASCII text
protocol, you can also exchange data with any terminal program (e.g. z.B. Hercules oder Putty)
via UDP / TCP/IP at any time with ECO 10 and carry out the configuration.
Details on the communication commands can be found in the document "Programming Manual", which can
be found in the download area of the ESERA online shop and within Config Tool 3.
15.1 ESERA ASCII Text protocol
The ECO 10 provides a protocol in ASCII format. The ESERA text protocol in ASCII format can be used very
easily for configuration and analysis. Special emphasis was placed on good readability and traceability. The
ESERA text protocol works with "GET" and "SET" commands, which probably every programmer has already
used in his own projects.
Hinweis
For security reasons, only one socket data connection with the ECO 10 is possible at a time.
The IP address is preset to DHCP.

*if the sensor or actuator supports Auto-E-Connect. For details, please refer to the operating instructions of the sensor or actuator.
All rights reserved. Reproduction as well as electronic duplication of this user guide, complete or in part, requires the written consent of
ESERA GmbH. Errors and technical modification subject to change. ESERA GmbH 2021
www.esera.de 11601-24 V1.0 R1.1 Manual Page 10 of 13
The ESERA text protocol is disclosed and documented. The current version of the ESERA protocol description
can be found in the Programming Manual in the download area of the article and the ESERA Config Tool 3.
16 1-Wire Network, cabling
The special feature of the 1-Wire system is the "BUS technology". All devices (sensors and actuators) are
operated in parallel on a three-wire line, which is used for both power supply and data communication. The
1-Wire Bus system joins the list of other successful bus systems such as CAN or Modbus RTU. All of the
installation principles recommended for these are also applicable and appropriate to 1-Wire.
The maximum size of a 1-Wire Network is determined by various factors. These are mainly:
- Total cable length and cable type
- Number of 1-Wire devices
- Type of cable installation (topology)
- Number and design of cable connectors (unnecessary connection transitions should be avoided)
All factors in total are summarised and designated as 1-Wire Bus load. Each increase of a factor increases the
1-Wire Bus load for the 1-Wire Controller and thus reduces the maximum network size..
According to our many years of experience and a lot of feedback from customers, the following conservative
recommendation can be made:
- Maximum cable length 50 -120m
- Number of 1-Wire devices no more than 20 -22 pieces
- As linear a topology as possible without T-junctions
The topology in particular plays a major role. If possible, it should be installed in a linear topology. The linear
topology can be compared like pearls on a pearl necklace. The data line should be laid from one device to the
next without T-joints.
Furthermore, the type of cable used can also be mentioned here. We recommend for the cabling
CAT5 or CAT6 network cable. It is also possible to use J-Y(St)Y telephone cables and KNX cables. Longer cable
runs are possible with CAT5 versus CAT7 cables.
With twisted pair cables, a longer connection length can be achieved in an undisturbed environment, as the
capacitive bus load is lower. A total length of 50 m and more can be easily achieved without additional measures.
In disturbed, commercial and industrial environments, the cable should always be shielded in order to increase
the "robustness" or interference sensitivity of the system.
17 Firmware-Update
The latest device software (firmware) can
be found in the download area of the Config
Tool 3. Please check for a new firmware
version when commissioning the ECO 10.
Please always use the latest version.
The firmware update is carried out via
Config Tool 3.
Please observe the operating instructions
for Config Tool 3, which you will find under
the "HELP/SUPPORT" tab in Config Tool 3.
You can find a video about the firmware
update on our website under "Service and
Support, Support Videos".
Note
The above statements on 1-Wire are hints and tips and do not describe any product property or represent
any guaranteed product property of the ECO 10.
Information on the basics and tips on the 1-Wire Bus system can also be found in the ESERA Online Shop
under https://www.esera.de/1-wire-grundlagen/

Art. No. 11601-24
*if the sensor or actuator supports Auto-E-Connect. For details, please refer to the operating instructions of the sensor or actuator.
All rights reserved. Reproduction as well as electronic duplication of this user guide, complete or in part, requires the written consent of
ESERA GmbH. Errors and technical modification subject to change. ESERA GmbH 2021
www.esera.de 11601-24 V1.0 R1.1 Manual Page 11 of 13
17.1 Recovery function Firmware-Update
If the update is faulty, e.g. due to a power failure during the update, you can use the
recovery function. To do this, press and hold the reset button (this is located under
hole 11 on the top of the module), start the update in Config Tool 3 and release the
reset button after approx. 1 second after starting in Config Tool 3. The update should
now start.
After performing an update, we recommend that you disconnect the ECO 10 from the
power supply for approx. 30 seconds and restart it.
If you have any problems with the installation, we will be happy to help you. Simply
18 Example for integration in IP-Symcon
We provide ESERA IP-Symcon software modules for easy integration of the ECO 10 into IP-Symcon via our
website. This gives you seamless integration into the software.
Details can be found on the ESERA website under "Compatible controllers / Control units / IP-Symcon
integration".
https://www.esera.de/kompatible-steuerungen-zentralen/ip-symcon-integration/
19 Example for Integration in Loxone
Via the shop we provide a sample project for the simple integration of the ECO 10 into the Loxone Miniserver.
This allows you to expand the Miniserver with many 1-Wire functions.
Details can be found on the ESERA website under "Compatible controllers / Control units / Loxone integration".
https://www.esera.de/kompatible-steuerungen-zentralen/loxone-integration/demo-1-wire-controller-1-loxone-
integration/
20 Example for Integration in FHEM
For integration into the open source automation software FHEM, we provide a software module for easy
integration of the ECO 10. This provides you with a very powerful 1-Wire interface in FHEM.
Details can be found on the ESERA website under "Compatible controllers / Control units / FHEM integration".
https://www.esera.de/kompatible-steuerungen-zentralen/fhem-integration/
21 Example for Integration in KNX Automation
For integration into a KNX automation system, we offer a software module for the Gira Homeserver together with
Grot company. This provides you with a very powerful 1-Wire integration for your KNX system. Details can be
found on the ESERA website under "Compatible controllers / Control units / KNX Gira Homeserver“.
https://www.esera.de/cat/index/sCategory/339
Note
Please also refer to the operating instructions for Config Tool 3, which you will find under the
"HELP/SUPPORT" tab within Config Tool 3.
Furthermore, you will find a video about the firmware update on our website under "Service and Support,
Support Videos".
Note
After carrying out an update, we recommend that you disconnect the ECO 10 from the power supply for
approx. 30 seconds and restart it.
Pressing the reset button does not correspond to an interruption of the power supply.

*if the sensor or actuator supports Auto-E-Connect. For details, please refer to the operating instructions of the sensor or actuator.
All rights reserved. Reproduction as well as electronic duplication of this user guide, complete or in part, requires the written consent of
ESERA GmbH. Errors and technical modification subject to change. ESERA GmbH 2021
www.esera.de 11601-24 V1.0 R1.1 Manual Page 12 of 13
22 Your software not listed?
Due to the text protocol used, the ECO 10 can be integrated extremely universally into many devices and
software solutions.
23 Operating conditions
The module may only be operated at the voltages and under the ambient conditions specified for it. The unit may
be operated in any position. The unit is intended for use in dry and dust-free rooms.
If condensation forms, an acclimatisation period of at least 2 hours must be waited for.
The assemblies may only be put into operation under the supervision of a qualified electrician. Do not operate the
assembly in an environment where flammable gases, vapours or dusts are or could be present.
24 Assembly
The mounting location must be protected from moisture. The unit may only be used in dry indoor spaces. The unit
is intended for mounting inside a control cabinet as a stationary device.
25 Disposal note
Do not dispose of the device within the household waste!
According to the directive concerning old electrical and electronic appliances,
electronic devices must be disposed of via the collecting points for old electronic
appliances!
26 Safety instructions
When using products that come into contact with electrical voltage, the valid VDE regulations must be
observed, especially VDE 0100, VDE 0550/0551, VDE 0700, VDE 0711 and VDE 0860
All final or wiring work must be carried out with the power turned off.
Before opening the device, always unplug or make sure that the unit is disconnected from the mains.
Components, modules or devices may only be put into service if they are mounted in a contact proof housing. During
installation they must not have power applied.
Tools may only be used on devices, components or assemblies when it is certain that the devices are disconnected
from the power supply and electrical charges stored in the components inside the device have been discharged.
Live cables or wires to which the device or an assembly is connected, must always be tested for insulation faults or
breaks.
If an error is detected in the supply line, the device must be immediately taken out of operation until the faulty cable
has been replaced.
When using components or modules it is absolutely necessary to comply with the requirements set out in the
accompanying description specifications for electrical quantities.
If the available description is not clear to the non-commercial end-user what the applicable electrical characteristics for
a part or assembly are, how to connect an external circuit, which external components or additional devices can be
connected or which values these external components may have, a qualified electrician must be consulted.
It must be examined generally before the commissioning of a device, whether this device or module is basically
suitable for the application in which it is to be used.
In case of doubt, consultation with experts or the manufacturer of the components used is absolutely necessary.
For operational and connection errors outside of our control, we assume no liability of any kind for any resulting
damage.
Kits should be returned without their housing when not functional with an exact error description and the
accompanying instructions. Without an error description it is not possible to repair. For time-consuming assembly or
disassembly of cases charges will be invoiced.
During installation and handling of components which later have mains potential on their parts, the relevant VDE
regulations must be observed.
Devices that are to be operated at a voltage greater than 35 VDC / 12mA, may only be connected by a qualified
electrician and put into operation.
Commissioning may only be realized if the circuit is built into a contact proof housing.
If measurements with an open housing are unavoidable, for safety reasons an isolating transformer must be installed
upstream or a suitable power supply can be used.
After installing the required tests according to DGUV / regulation 3 (German statutory accident insurance,
https://en.wikipedia.org/wiki/German_Statutory_Accident_Insurance) must be carried out.

Art. No. 11601-24
*if the sensor or actuator supports Auto-E-Connect. For details, please refer to the operating instructions of the sensor or actuator.
All rights reserved. Reproduction as well as electronic duplication of this user guide, complete or in part, requires the written consent of
ESERA GmbH. Errors and technical modification subject to change. ESERA GmbH 2021
www.esera.de 11601-24 V1.0 R1.1 Manual Page 13 of 13
27 Warranty
ESERA GmbH guarantees that the goods sold at the time of transfer of risk to be free from material and workmanship
defects and have the contractually assured characteristics. The statutory warranty period of two years begins from date of
invoice. The warranty does not extend to the normal operational wear and normal wear and tear. Customer claims for
damages, for example, for non-performance, fault in contracting, breach of secondary contractual obligations,
consequential damages, damages resulting from unauthorized usage and other legal grounds are excluded. Excepting to
this, ESERA GmbH accepts liability for the absence of a guaranteed quality resulting from intent or gross negligence.
Claims made under the Product Liability Act are not affected.
If defects occur for which ESERA GmbH is responsible, and in the case of replacement goods, the replacement is faulty,
the buyer has the right to have the original purchase price refunded or a reduction of the purchase price. ESERA GmbH
accepts liability neither for the constant and uninterrupted availability of the ESERA GmbH or for technical or electronic
errors in the online offer.
We develop our products further and we reserve the right to make changes and improvements to any of the products
described in this documentation without prior notice. If you need documentation or information about older product
28 Trademarks
All mentioned designations, logos, names and trademarks (including those which are not explicitly marked) are
trademarks, registered trademarks or other copyright or trademarks or titles or legally protected designations of their
respective owners and are hereby expressly recognized as such by us. The mention of these designations, logos, names
and trademarks is made for identification purposes only and does not represent a claim of any kind on the part of
ESERA GmbH on these designations, logos, names and trademarks. Moreover, from their appearance on ESERA GmbH
webpages it cannot be concluded that designations, logos, names and trademarks are free of commercial property rights.
ESERA and Auto-E-Connect are registered trademarks of ESERA GmbH.
Auto-E-Connect is registered by ESERA GmbH as a German and European Patent.
29 Contact
ESERA GmbH
Adelindastrasse 20
87600 Kaufbeuren
GERMANY
Tel.: +49 8341 999 80-0
Fax: +49 8341 999 80-10
www.esera.de
WEEE-Number: DE30249510
Table of contents
Other esera automation Controllers manuals
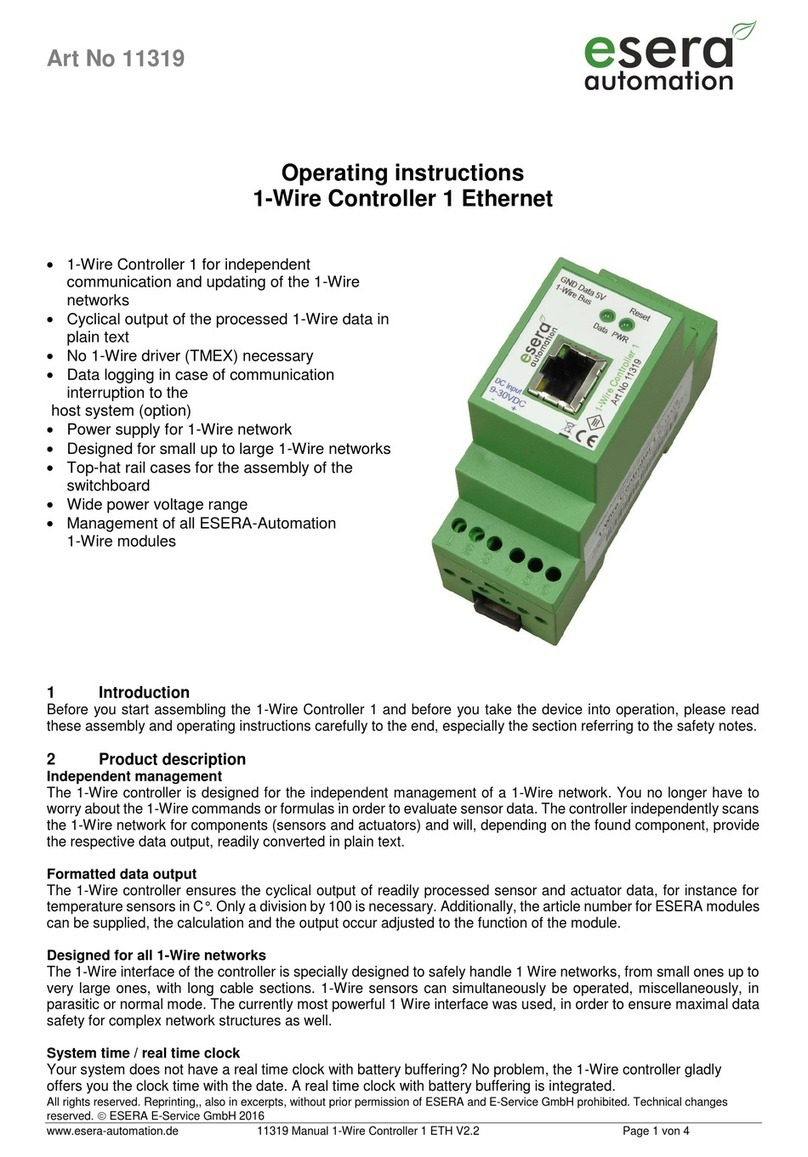
esera automation
esera automation 11319 User manual
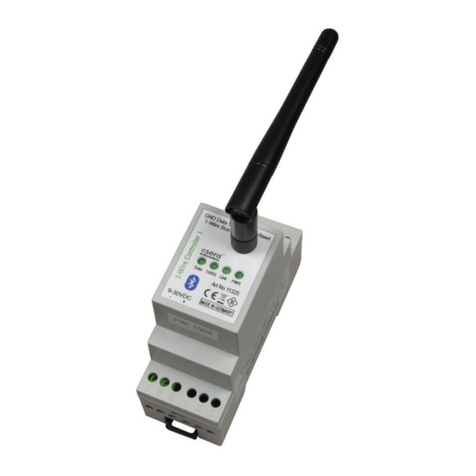
esera automation
esera automation 11325 User manual

esera automation
esera automation 11320 User manual
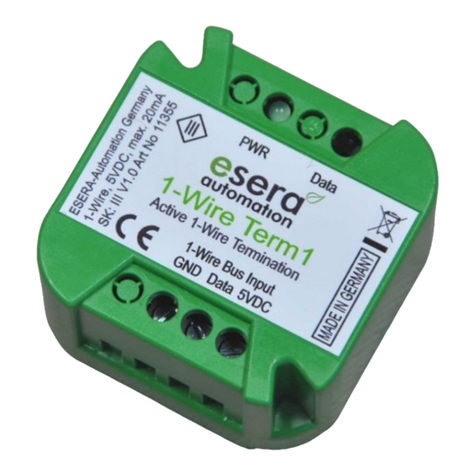
esera automation
esera automation 1-Wire Controller 1 User manual
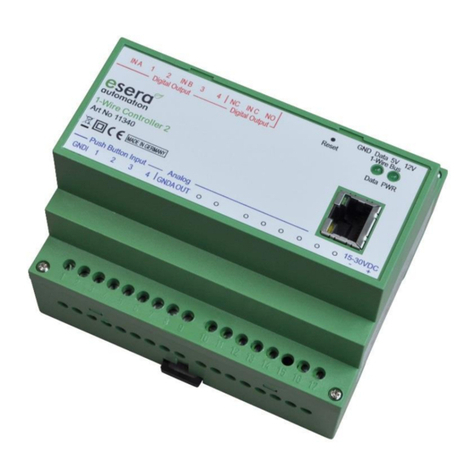
esera automation
esera automation Auto-E-Connect 11340 User manual
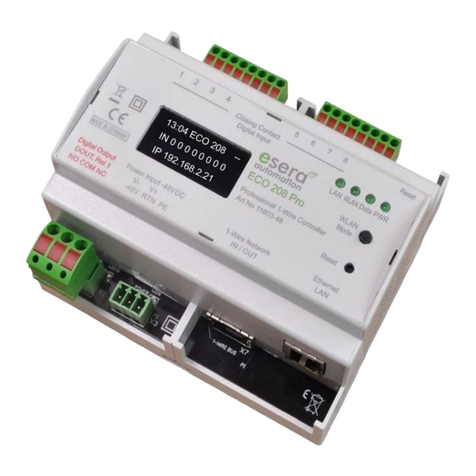
esera automation
esera automation ECO 208 PRO User manual
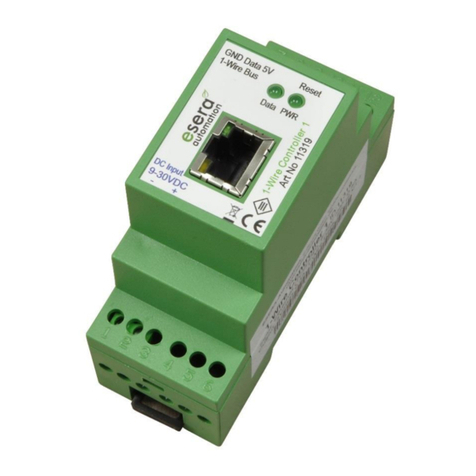
esera automation
esera automation 11319 User manual