Presys DCY-2050 User manual

DCY-2050 and DCY-2051 Universal Process Controller
LD1
LD2
DCY-2051
PRESYS
PRESYS
LD1 LD2
DCY-2050
TECHNICAL MANUAL
A
M
/
AM
/
Presys Instruments
presys

PRESYS | Instruments DCY-2050 and DCY-2051
EM0013-01
Table of Contents
Page
1.0 - Introduction........................................................................................... 1
1.1 - Description........................................................................................... 1
1.2 - Order Code Number............................................................................. 3
1.3 - Technical Specifications....................................................................... 4
2.0 - Installation............................................................................................. 7
2.1 - Mechanical Installation......................................................................... 7
2.2 - Electrical Installation............................................................................. 8
2.3 - Process Input Signal Connection.......................................................... 8
2.3.1 - Thermocouple Connection.............................................................. 9
2.3.2 - RTD Connection............................................................................. 10
2.3.3 - Milliampere Input............................................................................ 11
2.3.4 - V or mV Input................................................................................. 12
2.4 - Control and Alarm Output Signal Connection....................................... 12
2.5 - Connection Diagrams........................................................................... 15
2.6 - Communication..................................................................................... 16
2.7 - Engineering Units................................................................................. 16
3.0 - Operation............................................................................................... 17
3.1 - Normal Operation................................................................................. 17
3.2 - Configuration........................................................................................ 20
3.2.1 - Level 1 - General........................................................................... 23
3.2.2 - Level 2 - Inputs.............................................................................. 26
3.2.3 - Level 3 - Outputs........................................................................... 29
3.2.4 - Level 4 - Alarms............................................................................. 31
3.2.5 - Level 5 - Control............................................................................ 33
3.2.6 - Level 6 - Tune................................................................................ 42
3.2.7 - Level 7 - Setp (Programmable Set-Point)...................................... 47
3.2.8 - Level 8 - Calibration....................................................................... 50
3.2.9 - Level 9 - RS................................................................................... 50
4.0 - Maintenance........................................................................................... 51
4.1 - Controller Hardware.............................................................................. 51
4.2 - Hardware Configuration........................................................................ 52
4.3 - Snubber Use for Relay.......................................................................... 53
4.4 - Calibration............................................................................................. 54
4.5 - Hardware Maintenance Guidelines...................................................... 61
4.6 - Parts Listing.......................................................................................... 63
4.7 - Recommended Spare Parts Listing...................................................... 67
presys

PRESYS | Instruments DCY-2050 and DCY-2051
Introduction
Page 1
1.0 - Introduction
1.1 - Description
The PRESYS DCY-2050 and 2051 Controllers are microprocessor-based
instruments which control and show any process variable found in industrial plants, such
as: temperature, pressure, flow, level etc. The difference between models DCY-2050
and 2051 lies just in the form which process variables are shown. In model DCY-2051
the process variable is shown on a display by four larger size digits. They are provided
with two types of non-volatile internal memories (E2PROM and NVRAM) to store
configuration and calibration values. Its high accuracy is warranted by auto-calibration
techniques based on high thermal stability voltage reference.
They can communicate with computers by optional communication module RS-
232 or RS-422/485.
The DCY-2050 and 2051 Controllers have been designed according to modularity
and flexibility concepts. Therefore, five plug-in points are provided inside the controllers
for the installation of optional modules. By acquiring just these optional modules, the
user is capable of transforming a Single-Loop controller, into a Dual-Loop controller, of
obtaining a wide variety of control output types, such as: by relay, by open collector
voltage, by solid-state relay, voltage (1 - 5V, 0 - 10V), current (4 - 20mA). It can even be
provided with three alarm module types, such as: by relay, by open collector voltage and
by solid-state relay.
They are provided with several control modes: ON-OFF, PID (with all its
combinations), time proportioning, heating-cooling, programmable set-point, cascade
and remote set-point input.
The DCY-2050 and 2051 Controllers are provided with auto-tune algorithm to
compute the PID parameters for optimizing control capabilities.
They incorporate all standard control characteristics, such as: auto manual
bumpless transfer, output saturation, remote set-point and programmable set-point up to
ten segments, protection against integral saturation, etc.
They are capable of monitoring two universal standard inputs, accepting a direct
thermocouple connection, RTDs, current (mAdc) and voltage (mVdc, Vdc). The
thermocouple and RTD inputs are automatically linearized by means of tables stored in
the EPROM memory. A 24Vdc voltage source, isolated and with short circuit protection,
is provided for transmitter power supply.
The type of input selected by the user is enabled by jumpers and by the software
configuration. All configuration data can be protected by a password system, and are
stored in the non-volatile memory in the event of a power failure.
They allow a power supply from 90 to 240Vac.
presys

PRESYS | Instruments DCY-2050 and DCY-2051
Introduction
Page 2
The instruments are housed in an extruded aluminum case which makes them
highly immune to electrical
noise, electromagnetic
interference and resistant to
the most severe and rough
industrial use conditions.
On the instrument front
panels there are two red
displays jointly configurable
with the decimal point for up
to four high visibility digits.
The upper display can either
show the controlled variable
or the mnemonics: SP 1,
SP 2, OUT 1, OUT 2
corresponding to the values
shown on the lower display.
The lower display can show
the following values: channel 1
set-point, channel 2 set-point,
channel 1 output and channel 2
output. The control outputs 1
and 2 are represented in
percentage of full scale
output. The function of the
UP, DOWN and ENTER keys
to change the set-point/output
values is described in section
3.1. The A/M key on the
controller front panels allows
toggling between automatic
and manual modes. The
green led in the A/M key
indicates, when illuminated,
the controllers in the manual
mode and, when extinguished, the controllers in the automatic mode. In the controllers
configuration modes both displays show the mnemonics and the parameter values. The
pair of red leds can be used as a visual alarm indication associated to the outputs of
alarms 2, 3 and 4, or can indicate that the measured variable and the set-point/output
shown on the displays refer to 1 or 2 control loops. We may be provided with up to three
alarm outputs. Each of those alarm outputs may be: by relay, by open collector or by
triac.
PRESYS
LD1 LD2
DCY-2050
A
UTOMATIC / MANUAL
UP KEY
DOWN KEY
SCREW FOR CONTROLLER
INSERTION/REMOVAL IN/FROM CASE
ENTER
(1) PLACE FOR STICKING THE
ENGINEERING UNITS
(2) PROCESS
VARIABLE DISPLAY
(3) SET- POINT OR OUTPUT
INDICATION DISPLAY
(4) CONFIGURABLE
SIGNALING LEDS
ENTER
A
UTOMATIC/ MANUAL
UP KEY
DOWN KEY
Fi
g
. 1 - Controllers Front Panel DCY-2050/2051
(3)
(2)
(4)
(1)
(4)
presys

PRESYS | Instruments DCY-2050 and DCY-2051
Introduction
Page 3
1.2 - Order Code Number
Note - The spans and input types, control algorithms, the indication, the use of relays as
alarms and the alarm points are, among others, items which the user may program
through the front keys (if desired, specify such information so the whole programming
may be previously prepared by Presys).
Note: Any other desired software or hardware characteristics, may be available upon
request.
Code Example:
1) DCY - 2051 - 1 - 4 - 1 - 1 - 1 - 0 - 0
This code defines a DCY - 2051 Controller with output 1 to 4 at 20mA, output 2
with SPST relay , outputs 3 and 4 with SPDT relay . Power supply in the range of 90 to
240 Vac, does not use communication and is intended for use in a sheltered place. The
placing of such optional modules may offer a practical application for channel 1 heating-
cooling control (output 1-heating and output 3-cooling) and ON-OFF control for channel
2 (output 2). Output 4 can be a high, low or a deviation alarm output to channel 1 or
channel 2.
Order Code
Output 1 (For Control only)
Output 2 (Control or alarm)
Output 4 (Alarm or control 2 auxiliary "cooling")
Power Supply
Communication
Output 3 (Alarm or control 1 auxiliary " cooling")
Same code as for output 1
Same coding as for output 3
0-Notused
0-Notused
1-SPDTRelay
1-90to240Vac
0-Notused
1-4-20mA
2 - 1-5 Vdc
3 - 0-10 Vdc
4 - SPST Relay
2 - Open collector voltage
2-24Vdc
1-RS232
5 - Open collector voltage
3 - Solid-state relay
6 - Solid-state relay
2-RS485
DCY - 2050/ 2051 ---
---
Degree of Protection of Enclosure
0 - General purpose, sheltered place
1 - Front, drip proof
2-Weather
p
roof
3-RS422
presys

PRESYS | Instruments DCY-2050 and DCY-2051
Introduction
Page 4
1.3 - Technical Specifications
Inputs:
Two thermocouple configurable inputs (J, K, T, E, R, S, under ITS - 90), RTD Pt
- 100 under DIN 43760, 4 to 20mA, 0 to 55mVdc, 1 to 5Vdc, 0 to 10Vdc. Input
impedance of 250Ωfor mA, 10MΩfor 5Vdc and 2MΩabove 5Vdc. Table 1 shows
the temperature range limits for thermocouple and RTD and the resolution for the
linear input sensors.
Input sensor Span
Thermocouple lower
limit
°F
higher
limit
°F
lower
limit
°C
higher
limit
°C
Type J -184.0 1886.0 -120.0 1030.0
Type K -346 2498 -210 1370
Type T -418 752 -250 400
Type E -148.0 1436.0 -100.0 780.0
Type R -58 3200 -50 1760
Type S -58 3200 -50 1760
RTD
Pt-100 2- or 3-wire
-346.0
1256.0
-210.0
680.0*
Linear
Span
Resolution
Voltage 0 to 55mV
6μV
0 to 5V
500μV
0 to 10V
1mV
Current 0 to 20mA
2μA
(*) including wire resistance
Table 1 - Input Sensor Measuring Span
Control functions:
* ON-OFF Control. * Reason Control.
* PID Control. * Cascade Control.
* PID Control with AUTO-TUNE. * Remote set-point input
* Heating-cooling Control. * Programmable set-point
presys

PRESYS | Instruments DCY-2050 and DCY-2051
Introduction
Page 5
Control outputs:
. Analog output 4 to 20mAdc, 1 to 5Vdc, 0 to 10Vdc, use of optional cards with
plug-in fitting foreseen for up to two 300 Vac modules galvanically isolated from
inputs and power supply. Maximum load of 750Ω.
. SPST relay output with 3A capacity at 220Vac.
. Open collector voltage output (24Vdc, 20mA maximum with isolation).
. Solid-state relay output (2A 250Vac with isolation).
Alarm outputs:
. SPST relay output with 3A capacity at 220Vac.
. SPDT output relay with 3A capacity at 220Vac.
. Open collector voltage output (24Vdc, 20mA maximum with isolation).
. Solid-state relay output (2A 250Vac with isolation).
Serial communication:
RS-232 or RS-422/485 with isolation at 50Vdc, as an optional module with plug-in
fitting independent from outputs.
Indication:
Two red display sets with four digits which can be jointly configured with the
decimal point.
Configuration:
By front panel pushbuttons and internal jumpers.
Scanning time:
Standard 130 ms, for input indications within the -999 to 9999 span. Display
updating at each 0.5 second.
Accuracy:
±0.1% of full scale for TC, RTD inputs, mA, mV, Vdc.
±0.5% of full scale for analog control output.
Linearization:
±0.1% for RTD and ±0.2% for TC.
Square root extraction:
±0.5% of readings, for input above 10% of span. 0 to 5% of programmable Cut-off.
Cold junction compensation:
±2.0°C in the range from 0 to 50°C of ambient temperature.
presys

PRESYS | Instruments DCY-2050 and DCY-2051
Introduction
Page 6
2-Wire Transmitter Power Supply:
24Vdc voltage and 50mA maximum, isolated from outputs, with short-circuit
protection.
Stability at ambient temperature:
±0,005% per °C of span referred to an ambient temperature of 25°C.
Power Supply:
90 to 240Vac Universal, (10W nominal), 24Vdc. Other values are optional.
Operating ambient:
0 to 50°C temperature and 90% maximum relative humidity.
Dimensions:
1/8DIN (48 x 96mm) and 162mm depth.
45 x 92mm panel cutout.
Weight:
0.5kg nominal.
Warranty:
One year.
presys

PRESYS | Instruments DCY-2050 and DCY-2051
Installation
Page 7
2.0 - Installation
2.1 - Mechanical Installation
The DCY - 2050 and 2051 controller front panels are 1/8DIN size (48 x 96mm).
They are attached from the rear by two rails which push the instrument against
the panel.
After preparing a 45 x 92mm panel cutout, remove the two rails and slide the
instrument from the front until it touches the panel and from the rear engage the rails in
the controllers tightening the screws, as illustrated in figure 2.
Fig. 2 - Dimensional drawing, panel mounting cutout and side view
presys

PRESYS | Instruments DCY-2050 and DCY-2051
Installation
Page 8
2.2 - Electrical Installation
The DCY-2050 and 2051 controllers may be powered by any voltage between 90
and 240Vac or Vdc. Note that power is always applied to the internal circuit when the
instruments are connected to the AC supply.
Make the connections of the process input and output signals to the instrument
with the power off.
Refer to figure 3 on instrument I/O terminal designations for power supply,
grounding, communication and process input and output signals.
Signal cables should be kept as far away as possible from the power supply
cables..
Since the instrument housing is a metallic case it will be necessary to connect the
instrument ground terminal (gnd earth) to the local earth ground; this terminal should
never be connected to the neutral loop terminal.
Fig. 3 - DCY-2050 and 2051 Controller Terminals
2.3 - Process Input Signal Connections
The DCY-2050 and 2051 controllers in their two standard universal inputs can be
connected to thermocouples, 2 or 3-wire RTDs, mA, mV or V. In order to know the input
sensor types and spans refer to table 1, section 1.3 on Technical Specifications.
The enabling of a certain type of input sensor is obtained by internal jumpers
(refer to section 4.2 on hardware Configuration) and by a proper sensor selection in
configuration time (refer to section 3.2 on Configuration). Therefore, the connections
explained below shall only become effective if the instrument hardware and software are
correctly configured.
COLD JUNCTION
SENSOR
INPUT 1
INPUT 2
OUTPUT 1
OUTPUT 2
OUTPUT 3
OUTPUT 4
NC
NC
NO
NO
COMMUNICATION
PHASE POWER SUPPLY
90 to 240Vac
23 (+)
NEUTRAL
COLD JUNCTION
SENSOR
COMMUNICATION INPUT 2 INPUT 1
POWER SUPPLY
NEUTRAL PHASE NO NC NO NC
OUTPUT 4 OUTPUT 3 OUTPUT 2OUTPUT 2 OUTPUT 1
presys

PRESYS | Instruments DCY-2050 and DCY-2051
Installation
Page 9
The wiring of a type of sensor in input 1, will not restrict the simultaneous use of
any other sensor, whether or not of the same type, in input 2.
To prevent noise induction from occurring in the sensor when connecting wire to
the I/O terminal use twisted pair cable and run the sensor connection wire through a
metallic tube or use a shielded cable. Be sure to connect only one shielded wire end to
the negative I/O board terminal, or to the sensor ground, as outlined in the following
items.
WARNING: THE GROUNDING OF THE TWO SHIELDED WIRE ENDS MAY CAUSE
DISTURBANCE TO THE CONTROLLERS.
2.3.1 - Thermocouple Connection
Whenever using just one thermocouple, the user should preferably connect it to
input 1 of the controllers, in order to obtain a greater accuracy in temperature
measurements, since the cold junction sensor is solidly attached to the I/O terminal and
closer to input 1.
Apply thermal paste from the thermocouple I/O terminals to the cold junction
sensor in order to reduce the cold junction compensation error.
Connect the thermocouple to terminals 2(+) and 3(-) to use input 1 or to terminals
5(+) and 6(-) to use input 2 as shown in figure 4.
Use appropriate compensation cables of the same construction material as the
thermocouple to connect the thermocouple to the controller I/O terminals. Check that the
correct thermocouple polarity is the same as that of the corresponding terminals.
Fig. 4 - Thermocouple Connection
654321
654321
-+ -+
-+ -+
Grounded Ungrounded
Thermocouple
Note 1
Note 1
Twisted pair or
shielded wire
Channel 2 Channel 1 Channel 2 Channel 1
Note1: Keep shielded wire disconnected at this end.
presys

PRESYS | Instruments DCY-2050 and DCY-2051
Installation
Page 10
2.3.2 - RTD Connection
A RTD accepts a 2-, 3-, or 4-wire connection. All connection types are shown in
figure 5.
In the event of a 2-wire RTD, connect the RTD between I/O terminals 1 and 3 to
use input 1 or to terminals 4 and 6 to use input 2 as illustrated in figure 5.
For a 3-wire RTD, connect the RTD in the same way as for the previously
described 2-wire connection, except that a third wire for RTD compensation should be
connected to terminal 2 in the case of input 1 and to terminal 5 in the case of input 2, see
figure 5.
A 4-wire RTD should be connected to the controllers in the same manner as for a
3-wire connection, except that the fourth RTD wire is disregarded and left disconnected,
see figure 5.
The use of a 3-wire RTD provides a higher accuracy than a 2-wire connection.
The RTD wiring should be of the same material, length and gauge to ensure
proper resistance compensation on all terminal connections. The maximum connecting
wire resistance is 10Ωper wire. The minimum wire gauge should be 18AWG for
distances of up to 50 meters and 16 AWG for distances in excess of 50m.
Fig. 5 - RTD Connection
654321
65 4 3 2 1
654321
654321
654321
654321
GROUNDED
UNGROUNDED
2-WIRE 3-WIRE 4-WIRE
2-WIRE 3-WIRE 4-WIRE
Channel 2 Channel 1 Channel 2 Channel 1 Channel 2 Channel 1
Channel 2 Channel 1
Channel 2 Channel 1 Channel 2 Channel 1
Note 1: Let the shield wire disconnected at this end.
Note 1 Note 1 Note 1 Note 1
Note
1
Note 1
Note 1
Note 1
RTD
RTD RTD RTD
RTD RTD
NC NC
NC NC
presys

PRESYS | Instruments DCY-2050 and DCY-2051
Installation
Page 11
2.3.3 - Milliampere Input
A standard 4 to 20mA current source can be applied between terminals 1(+) and
3(-) in the case of input 1, and between terminals 4(+) and 6(-) in the case of input 2;
such current can originate from an externally powered Transmitter. In the event that the
internal controller 24V voltage source is used to power a 2-wire Transmitter the current is
received only on terminal 1(+) in the case of input 1 and received only on terminal 4(+) in
the case of input 2. Figure 6 illustrates those two connection possibilities.
Two-wire Transmitter
Note 1: Keep shielded wire disconnected at this end.
Note 2: Connect shielded wire to transmitter ground terminal. If ground terminal non-e
x
istent keep shielded wire disconnected at this end.
(Transmitter should not
be grounded)
4-wire Transmitter
Ungrounded Transmitter
Fig. 6 - Current source Connection
presys

PRESYS | Instruments DCY-2050 and DCY-2051
Installation
Page 12
2.3.4 - Voltage Source Connection in mV or V
Either a 0 to 55mVdc or a 0 to 5Vdc voltage must be applied between terminals
2(+) and 3(-) in the case of input 1 and between terminals 5(+) and 6(-) in the case of
input 2. A 0 to 10Vdc voltage must be applied between terminals 1(+) and 3(-) in the
case of input 1 and between terminals 4(+) and 6(-) in the case of input 2. Those
connections are illustrated in figure 7.
Note 1: Keep shielded wire disconnected at this end.
Note 2: Connect shielded wire to power supply ground terminal. If ground terminal non-e
x
istent keep shielded wire disconnected at this end.
_
_
_
_
_
_
_
_
+G
+G
+G
+G
+G
+G
+G
+G
0to55mV 0a55mV
0 to 55mV 0to55mV
0to5V
0to10V 0to10V 0to10V0to10V
0to5V
0to5V 0to5V
or or
or or
_
_
_
_
+
+
+
+
_
_
_
_
+
+
+
+
Note 1
Note 1
Note 2
Note 2
Power supply not to
be grounded
Power supply not t
o
be grounded
Fig. 7 - Voltage Source Connection
2.4 - Control and Alarm Output Signal Connection
In their most complete versions the controllers can be provided with up to four
output signals: output 1, output 2, output 3 and output 4. Output 1 can only be used as a
control output. Outputs 2, 3 and 4 can be used as control or alarm outputs, depending on
controllers software configuration established by the user. A maximum of three alarm
outputs can be provided.
presys

PRESYS | Instruments DCY-2050 and DCY-2051
Installation
Page 13
In the case of outputs 1 and 2 we can have six types of different outputs between
the current I/O terminals: current (4 to 20mA), voltage (0 to 5Vdc), voltage (0 to 10Vdc),
SPST relay, open collector voltage and solid state relay.
For outputs 3 and 4 there are three types of different outputs: SPDT relay, open
collector voltage and solid-state relay. Figure 8 illustrates the control outputs and figure 9
the alarm outputs of the controllers.
Note that the I/O terminals will only show output signals if the corresponding
optional module is installed and the output is correctly configured. Refer to sections 3.2
on Configuration and 4.3 on Adding optional modules for more details on installation and
configuration of optional modules.
13
13
15
15
17
20
14
14
16
16
18
21
19
22
OUTPUT 1
OUTPUT 1
OUTPUT 2
OUTPUT 2
OUTPUT 3
OUTPUT 4
CONTROL MODE INTERNAL DEVICE TERMINALS
Current Output (1)
Voltage Output (1)
CurrentOutput(2)
Voltage Output (2)
Cooling (1)
Cooling (2)
Time proportioning (1)
Heating (1)
ON - OFF (1)
Time proportioning (2)
Heating (2)
ON - OFF (2)
4to20mA 0to5V 0to10V
4to20mA 0to5V 0to10V
SCR
SCR
SPST
SPST
NC
NC
C
C
SCR
SCR
SPDT
SPDT
NC
NC
C
C
NO
NO
+24V
+24V
+24V
+24V
Logic
Logic
Logic
Logic
+
+
-
-
-
(1) Designates first control loop
(2) Designates second control loop
Fig. 8 - Control Output Connections
presys

PRESYS | Instruments DCY-2050 and DCY-2051
Installation
Page 14
(*) Relay contacts assume that SAFE condition (see section 3.2 on Configuration) was selected for
relays and that the controllers are powered and in no-alarm condition. With no power Supply or in
alarm condition with SAFE option selected, contact state is changed.
Fig 9 - Alarm Output Connections
15
17
20
16
18
21
19
22
OUTPUT 2
OUTPUT 3
OUTPUT 4
FUNCTION INTERNAL DEVICE TERMINALS
Alarm
Alarm
Alarm
SCR
SCR
SCR
SPDT
SPST
SPDT
NC
NC
C
C
C
NO
NO*
+24V
+24V
+24V
Logic
Logic
Logic
*
NC
*
*
*
-
presys

PRESYS | Instruments DCY-2050 and DCY-2051
Installation
Page 15
2.5 - Connection Diagram
12
3
4
5
678
910
1112
13
14
1516
17
18
1920
21
22
23
24
GND
EARTH
COMMOM Tx- Tx+ Rx- Rx+
COMMUNICATION
INPUT2 INPUT1
POWER SUPPLY
OUTPUT 4 OUTPUT 3 OUTPUT 2 OUTPUT 1
NEUTRAl LINE
SCR SCR SCRSCR
+24V +24V +24V +24V
Logic Logic Logic Logic
+
+
+
+
C
NC
(1)
C
NC
(1)
NC
C
NO
(1)
(1)
NC
C
NO
(1)
(1)
+
+
RTD
Current 4-20mA
Voltage 0 to 10V
COMMOM Tx Rx
GND
RS-232
Relay 1Relay 3
Relay 4 Relay 2
Transmitter Power Supply +24V
RS-422/485
+
+
+
+
4to20mA
0to5V
0to10V
Notes:
(1) Referring to first control loop
(2) Referring to second control loop
Outputs 1, 2, 3 , 4 and communication are optional
(2)
Control (2)
or alarm
Only for
con
t
rol
(
1
)
Alarm or cooling
control (2)
Alarm or cooling
control (1)
24Vdc 23 (+)
24 ( )
presys

PRESYS | Instruments DCY-2050 and DCY-2051
Installation
Page 16
2.6 - Communication
The DCY-2050 / 2051 controllers can communicate with computers by RS-232 or
RS-422/485 since optional module is installed and the communication parameters are
configured.
2.7 - Engineering Units
A label containing a selection of Engineering Units is supplied with each
controller. Select the one corresponding to the variable shown on the display and stick it
to the front panel of the controllers.
presys

PRESYS | Instruments DCY-2050 and DCY-2051
Operation
Page 17
3.0 - Operation
3.1 - Normal operation
The DCY-2050 and 2051 controllers are provided with two operational modes:
normal mode and configuration mode.
In normal operation mode we can further have the automatic operation mode and
the manual operation mode.
In the automatic operation mode (closed loop system) the controllers receive the
input signals, compare them with the set-points and automatically generate through
control algorithms the output signals which adjust the input signals to the set-points.
In the manual operation mode (open loop system) the user himself establishes
the values in output percentage to control the measured variables.
The selection between the automatic and manual modes is made through the
automatic/manual (A/M) key on the controllers front panel. When in the manual mode the
green LED indicating the manual state is illuminated.
The controllers normal mode, in which they operate most of the time, will be
named zero level. In this level the upper display can show: denomination of set-point 1
(SP 1), denomination of output 1 (OUT1), denomination of set-point 2 (SP 2),
denomination of output 2 (OUT2), value of input 1 (IN 1) and value of input 2 (IN 2). The
lower display can show: the value of set-point 1 (V_SP 1), the value of output 1 (V_OUT
1), the value of set-point 2 (V_SP2) and the value of output 2 (V_OUT 2). Whenever the
controllers are connected, they start a display indication of the last selection shown,
before being disconnected. In order to switch to other options, the UP, DOWN and
ENTER keys should be used, as illustrated in figure 10.
Figure 10, below, illustrates all those display possibilities at the operation level.
presys

PRESYS | Instruments DCY-2050 and DCY-2051
Operation
Page 18
Operation Level
Fig. 10 - Options for Operation Level
GENERAL
OUT 1 INPUT 1
OUT 2 INPUT 2
GENERAL
SP 1 INPUT 1
SP 2 INPUT 2
CONF
CONF
V_OUT 1 V_OUT 1
V_OUT 2 V_OUT 2
V_SP 1 V_SP 1
V_SP 2 V_SP 2
PASSWORD
V
alues for checking
purposes only
Set-point values can
be altered, both in
automatic mode
and manual mode.
Output values can only
be altered in manual
mode.
presys
This manual suits for next models
1
Table of contents
Other Presys Controllers manuals
Popular Controllers manuals by other brands
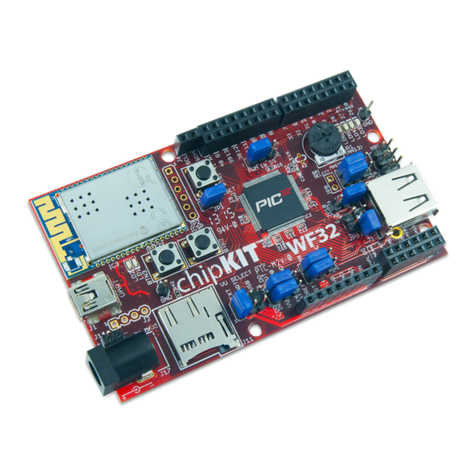
Digilent
Digilent chipKIT wf32 Reference manual
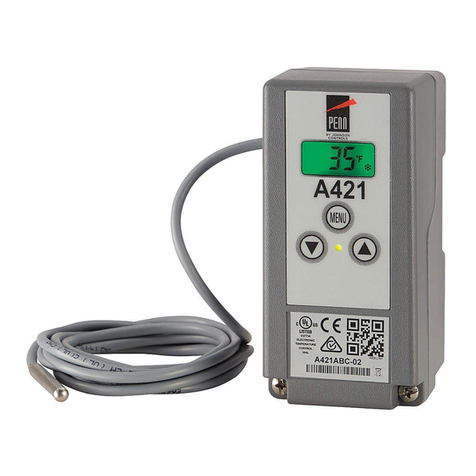
Johnson Controls
Johnson Controls Penn A421 Series quick start guide
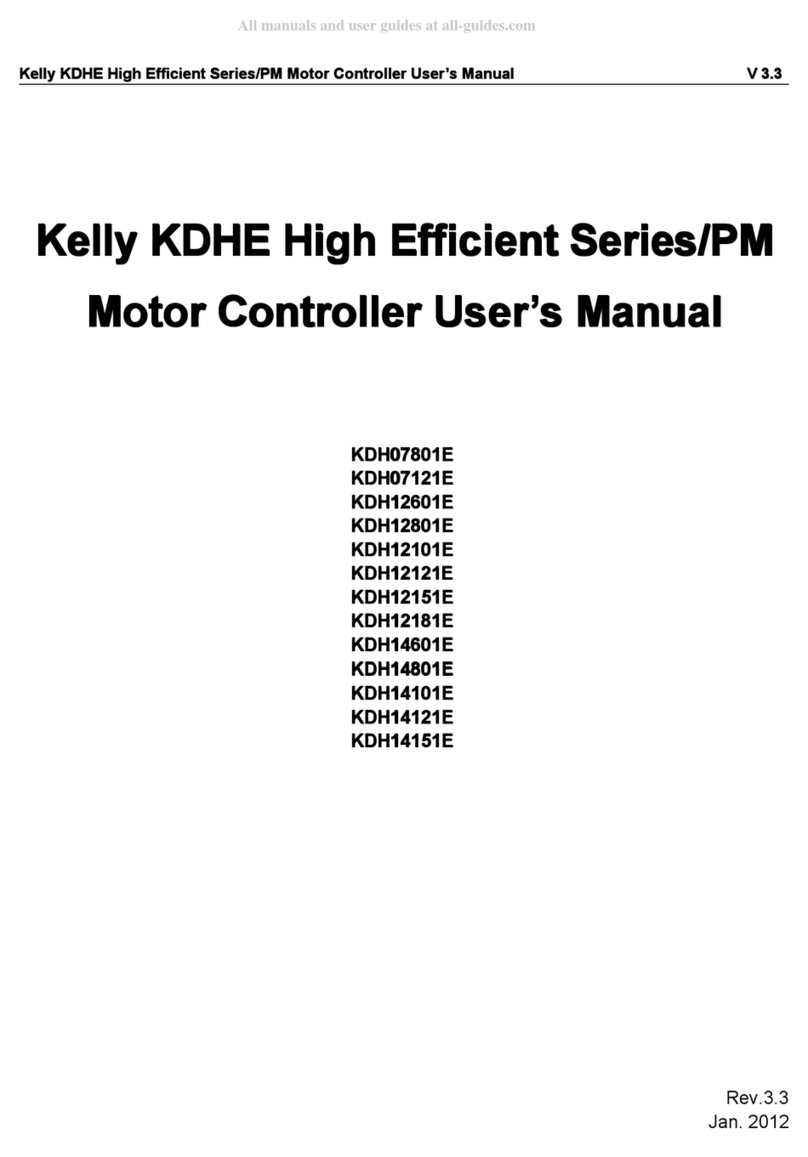
Kelly
Kelly KDHE Series user manual
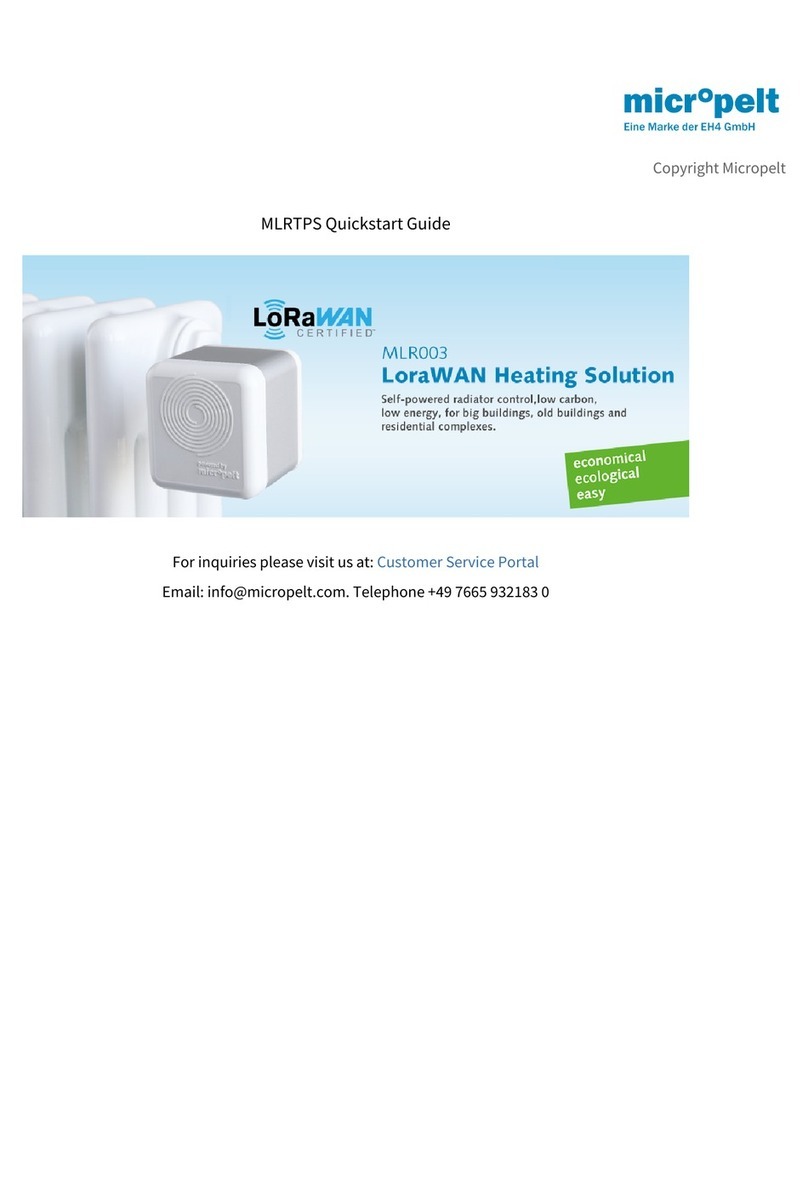
Micropelt
Micropelt MLR003 quick start guide
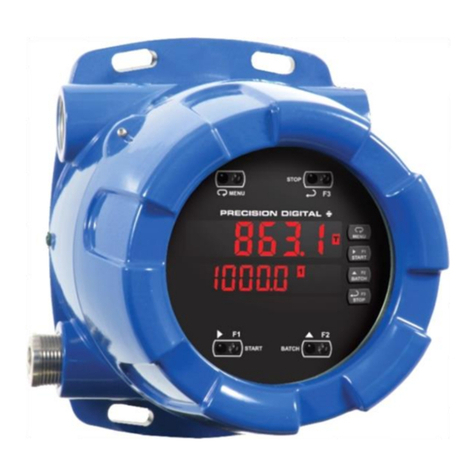
Precision Digital Corporation
Precision Digital Corporation ProtEX-MAX PD8-6310 instruction manual
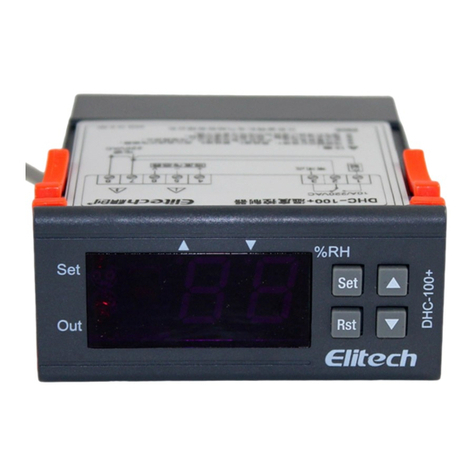
Elitech
Elitech DHC-100+ instructions