EUCHNER ESM-2H2 Series User manual

1
Operating Instructions
2-Hand Safety Relay ESM-2H2..
Correct use
The ESM-2H2.. is an extremely compact, uni-
versal two-hand safety device. It complies with
ENISO13851, typeIIIC, and is intended for use
in safety circuits that are designed according to
EN60204-1, e.g. on presses, punches and bending
tools.
Due to the internal error monitoring, the ESM-2H2..
can, despite its very compact dimensions, be used
for all applications up to the highest category, safety
category4, PLe according to 13849-1, SILCL3
according to EN62061 or typeIII C according to
ENISO13851.
Before the device is used, a risk assessment must
be performed on the machine, e.g. according to the
following standards:
fENISO13849-1
fENISO12100
fIEC62061.
Correct use includes observing the relevant require-
ments for installation and operation, particularly
based on the following standards:
fENISO13849-1
fEN60204-1
fIEC62061.
Important!
fThe user is responsible for the integration of
the device in a safe overall system. For this
purpose, the overall system must be validated,
e.g. according to ENISO13849-2.
fThe device user must assess and document
remaining risks.
fIf a data sheet is included with the product, the
information on the data sheet applies.
Safety precautions
WARNING
fInstallation and setup of the device must be
performed only by authorized personnel.
fObserve the country-specic regulations when
installing the device.
fThe electrical connection of the device is only
allowed to be made with the device isolated.
fThe wiring of the device must comply with the
instructions in these operating instructions,
otherwise there is a risk that the safety function
will be lost.
fIt is not allowed to open the device, tamper with
the device or bypass the safety devices.
fAll relevant safety regulations and standards are
to be observed.
fThe overall concept of the control system in
which the device is incorporated must be vali-
dated by the user.
fFailure to observe the safety regulations can re-
sult in death, severe injuries and serious damage.
fNote down the version of the device (see type la-
bel Vx.x.x) and check it each time prior to setup.
If the version changes, the use of the device in
the overall application must be validated again.
Features
f2 safe, redundant relay outputs
fCyclical monitoring of the output contacts
fFeedback loop for monitoring downstream contac-
tors or expansion modules
fShort circuit and ground fault monitoring
fExtremely compact design
fUse up to PLe, SILCL3, category4 or typeIIIC
according to ENISO13851
Function
The two-hand relay ESM-2H2.. is suitable for setting
up and monitoring two-hand circuits and is used to
protect the operating personnel. Dangerous work
steps can only be triggered when both two-hand
buttons connected are actuated simultaneously,
i.e. within 0.5s.
It is ensured that a single fault or malfunction does
not lead to a loss of the safety function and that
every fault is detected by cyclical self-monitoring
no later than the next actuation.
When the operating voltage is applied to A1 and A2
and the feedback loop X1 and X2 closed, the
ESM-2H2.. is ready for use. To be able to initiate
a switching operation, the output relays must be
de-energized. The output relays only switch to the
energized position when the two-hand buttons T1
and T2 are actuated simultaneously, i.e. within 0.5s.
The output relays are not switched if:
fOnly one two-hand button is actuated or the time
between the actuation of the two two-hand buttons
is >0.5s,
fThe feedback loop is open (error in external con-
tactor or expansion module),
fAnother error (short circuit, cable break, error in
the switching device) has occurred.
When T1 and/or T2 are/is released, the output re-
lays are open (safe) immediately. In order to trigger
a new operation, both two-hand buttons must rst
be released and the feedback loop must be closed.
Fig. 1: Block diagram for ESM-2H2..
Mounting
As per EN60204-1, the device is intended for in-
stallation in control cabinets with a minimum degree
of protection of IP54. It is mounted on a 35 mm
mounting rail according to DINEN60715TH35.
Fig. 2: Mounting/removing
Installation
Prevent unintentional actuation or bypassing
of the safety function
The two-hand buttons must be arranged as per the
standard ENISO 13851 such that unintentional
actuation or simple bypassing of the safety function
is excluded. As such the operation of both buttons
using one hand must be prevented by a sufcient
distance (at least 260mm) or by a separating wall.
Actuation using the forearm, elbow, knee, hip or
other parts of the body can be effectively prevented
by further increasing the distance between the two
buttons, sufcient distance from the oor and/or
covers and/or separating walls.
Distance between the two-hand buttons and
the danger area
It is required that a minimum distance between the
buttons for the two-hand circuit and the danger area
of the machine or installation is maintained so that,
after the release of one or both buttons, the dan-
ger area can only be reached when the dangerous
movement has been interrupted or ended.
According to the standard DIN EN ISO 13855 this
distance is calculated using the following equation:
S = (K x T) + C
S: Minimum distance from the nearest pushbutton
(two-hand button) to the danger area.
K: Parameter in mm/s, derived from data on the
approach speed of the body or parts of the body,
for two-hand circuits 1,600mm/s.
T: The stopping time for the entire system in sec-
onds, that is the time from the release of the
two-hand buttons to the end of the dangerous
movement.
C: Additional distance in mm related to intrusion into
the danger area before the safeguard activates.
For two-hand circuits this distance is 250mm,
if the buttons are covered appropriately it can
also be set to 0mm , however Smust then be
at least 100mm.
Example
The stopping time of the overall system is 90ms.
Then from the above equation the minimum dis-
tance is:
S = (1,600 mm/s x 0.09 s) + 250 mm
S = 144 mm + 250 mm = 394 mm
If a suitable cover is used, Scan be reduced to
144mm.

2
Operating Instructions
2-Hand Safety Relay ESM-2H2..
Electrical connection
fWhen the 24 V version is used, a safety transform-
er according to EN61558-2-6 or a power supply
unit with electrical isolation from the mains must
be connected.
fExternal fusing of the safety contacts must be
provided.
fA maximum length of the control lines of 1,000 m
with a conductor cross-section of 0.75mm² must
not be exceeded.
fThe conductor cross-section must not exceed
2.5mm².
fIf the device does not function after setup, it must
be returned to the manufacturer unopened. Open-
ing the device will void the warranty.
A1 Power supply
A2 Power supply
S11 Control line T1
S12 Control line T1
S13 Control line T1
S21 Control line T2
S22 Control line T2
S23 Control line T2
X1, X2 Feedback loop
13-14 Safety contact 1
23-24 Safety contact 2
Fig. 3: Connections
Setup procedure
Notice
The items listed under Electrical connection must
be observed during commissioning.
1. Wiring ESM-2H2.. to two-hand buttons:
Wire the ESM-2H2.. to the two-hand buttons as
per Fig. 5.
2. Wiring feedback loop:
If your application provides for external contactors
or expansion modules, connect them to the device
according to Fig. 6.
3. Wiring power supply:
Connect the power supply to terminals A1 and A2
(see Fig. 7).
Attention: Wiring only in de-energized state.
4. Starting the device:
Switch the operating voltage on.
5. Switching to the operating status:
Actuate the two buttons T1 and T2 simultaneously,
or within 0.5s.
The positively driven relays switch on.
6. Switching to the idle status:
Release the two buttons T1 and T2.
The positively driven relays switch off.
What to do in case of a fault?
Device does not switch on:
fCheck the wiring by comparing it to the wiring
diagrams.
fCheck the two-hand buttons used for correct
function and adjustment.
fCheck the operating voltage at A1 and A2.
fIs the feedback loop closed or a jumper tted?
Technical data
Parameter Value
Version ESM-2H201 ESM-2H202 ESM-2H203
Operating voltage AC/DC 24 V AC 115V AC 230 V
Rated supply frequency 50 - 60 Hz
Permissible deviation ± 10%
Power consumption DC 24 V AC 230 V
Approx. 1.5 W Approx. 3.7 VA
Control voltage at S12/S13 and S22/S23 DC 24 V
Control current (both buttons) Approx. 2 x 40 mA
Release time of the safety relay after
releasing a button < 20 ms
Response delay after actuation of the
buttons < 20 ms
Synchronization time < 0.5 s
Safety contacts 2 NO contacts
Max. switching voltage AC 250 V
Breaking capacity AC: 250 V, 1,500 VA, 6 A for ohm resistive load (6 operating cycles/minute)
250 V, 3 A for AC-15
DC: 24 V, 144 W, 6 A for ohm resistive load (6 operating cycles/minute)
24 V, 3 A, for DC-13
Minimum contact load 24 V, 20 mA
Contact fuses 10 A gG
Conductor cross-section 0.14 - 2.5 mm²
Max. length of control cable 1,000 m with 0.75 mm²
Contact material AgSnO2
Mech. contact life Approx. 1 x 107
Test voltage 2.5 kV (control voltage/contacts)
Rated impulse withstand voltage, leakage
paths/air gaps 4 kV (DIN VDE 0110-1)
Rated insulation voltage 250 V
Degree of protection IP20
Temperature range DC24V: -15°C to +60°C
AC230V/115V/24V: -15°C to +40°C
Degree of contamination 2 (DIN VDE 0110-1)
Overvoltage category 3 (DIN VDE 0110-1)
Weight Approx. 230g
Mounting Mounting rail according to DIN EN 60715 TH35
Reliability values according to EN ISO 13849-1 for all variants of the series ESM-2H2 1)
Load (DC-13; 24V) ≤0.1 A ≤1 A ≤3A
nop ≤400,000 cycles ≤100,000 cycles ≤22,500 cycles
T10D 20 years
Category 4
PL e
PFHD1.2x10-8 1/h
1) Additional data can be requested from the manufacturer for applications that deviate from these conditions.
Device cannot be switched on again after an
emergency stop:
fCheck the two-hand buttons used for correct
function.
fCheck the wiring (short circuits or similar?)
fIs the feedback loop closed?
If the fault persists, perform the steps listed under
Setup procedure.
If these steps do not remedy the fault either, return
the device to the manufacturer for examination.
Opening the device is impermissible and will
void the warranty.
Maintenance
The device must be checked once per month for
proper function and for signs of tampering and
bypassing of the safety function. The device is
otherwise maintenance-free, provided that it was
installed properly.
Disposal
Pay attention to the applicable national regulations
and laws during disposal.
EU declaration of conformity
The declaration of conformity is part of the operating
instructions, and it is included as a separate sheet
with the device.
The EU declaration of conformity can also be found
at: www.euchner.com
Service
If servicing is required, please contact:
EUCHNER GmbH + Co. KG
Kohlhammerstraße 16
70771 Leinfelden-Echterdingen
Germany
Service telephone:
+49 711 7597-500
E-mail:
support@euchner.de
Internet:
www.euchner.com

Operating Instructions
2-Hand Safety Relay ESM-2H2..
3
Subject to technical modications; no responsibility is accepted for the accuracy of this information. © EUCHNER GmbH + Co. KG 2109071-07-08/22 V1.1.0 (translation of the original operating instructions)
Fixed terminals Plug-in terminals
Fig. 4: Dimension drawing for ESM-2H2..
Application
The buttons in the two-hand circuit must be arranged and be such that accidental operation is prevented and the protective effect cannot be easily bypassed.
Here the regulations in the applicable standards, in particular ENISO13851 and DIN EN ISO 13855, are to be observed.
The ESM-2H2.. is intended for the connection of two-hand buttons each with one NC contact and one NO contact.
Jumper X1-X2:
see description
Fig. 5: Wiring for the ESM-2H2.. with two-hand buttons (NC/NO contact)
Feedback loop Power supply
Fig. 6: If an external contactor or expansion module (e.g. ESM-ES3..) is to be
connected to ESM-2H2.. to increase the rating of the contacts or the
number of contacts, its positively driven monitoring contacts (NC con-
tacts) are to be connected in series and connected to the connections
for the feedback loop X1 and X2.
Fig. 7: Connection of the power supply to terminals A1 and A2 (power supply
according to the technical data).
This manual suits for next models
4
Other EUCHNER Relay manuals
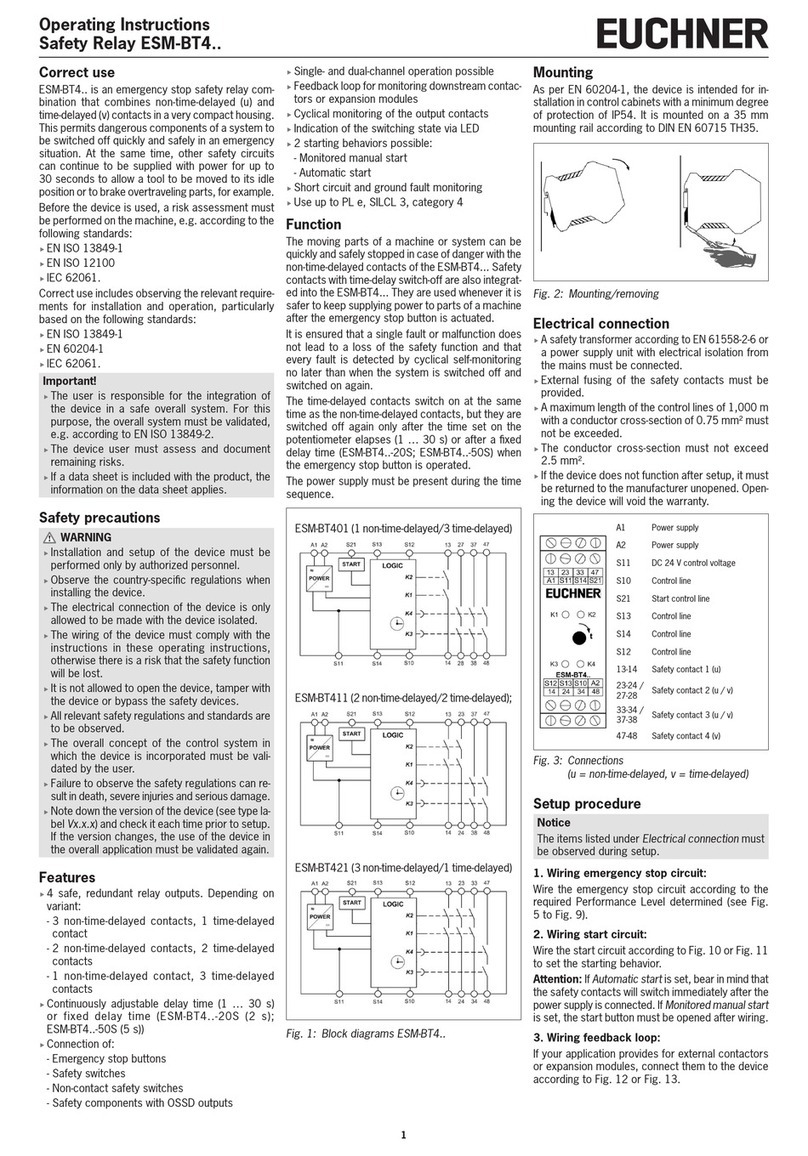
EUCHNER
EUCHNER ESM-BT4 Series User manual
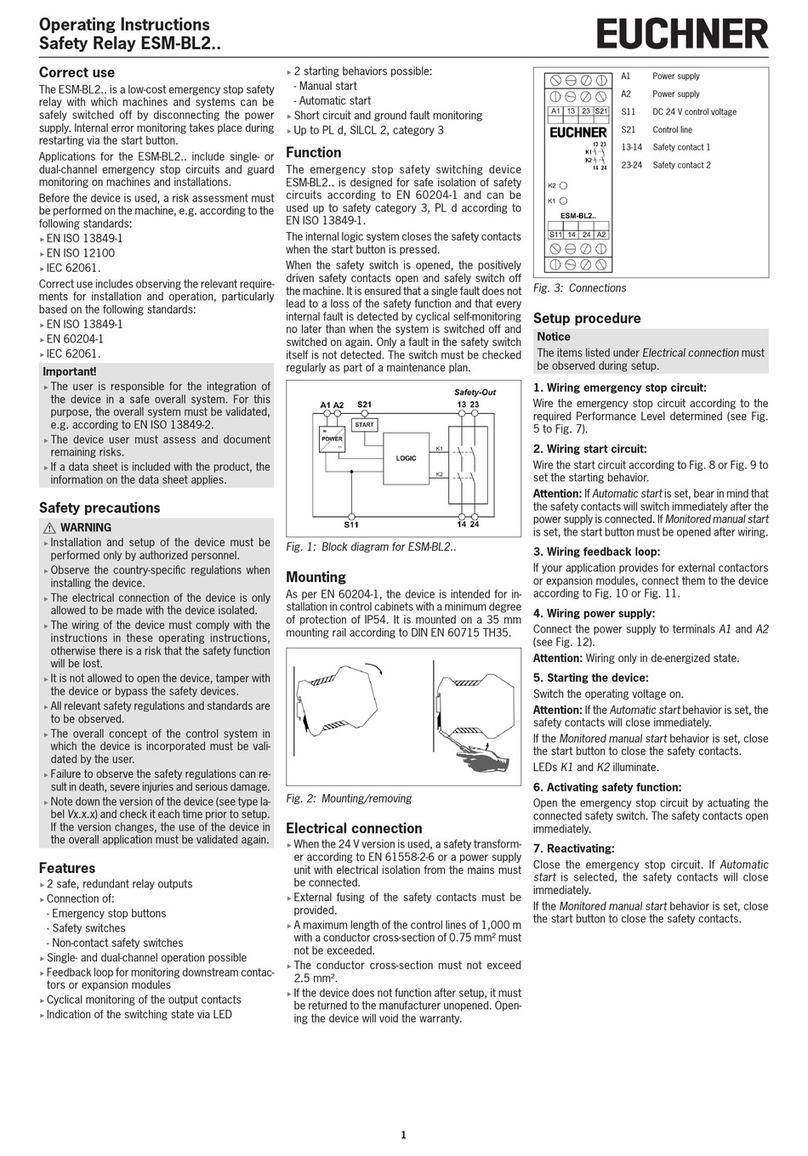
EUCHNER
EUCHNER ESM-BL2 Series User manual

EUCHNER
EUCHNER ESM-BA3 Series User manual
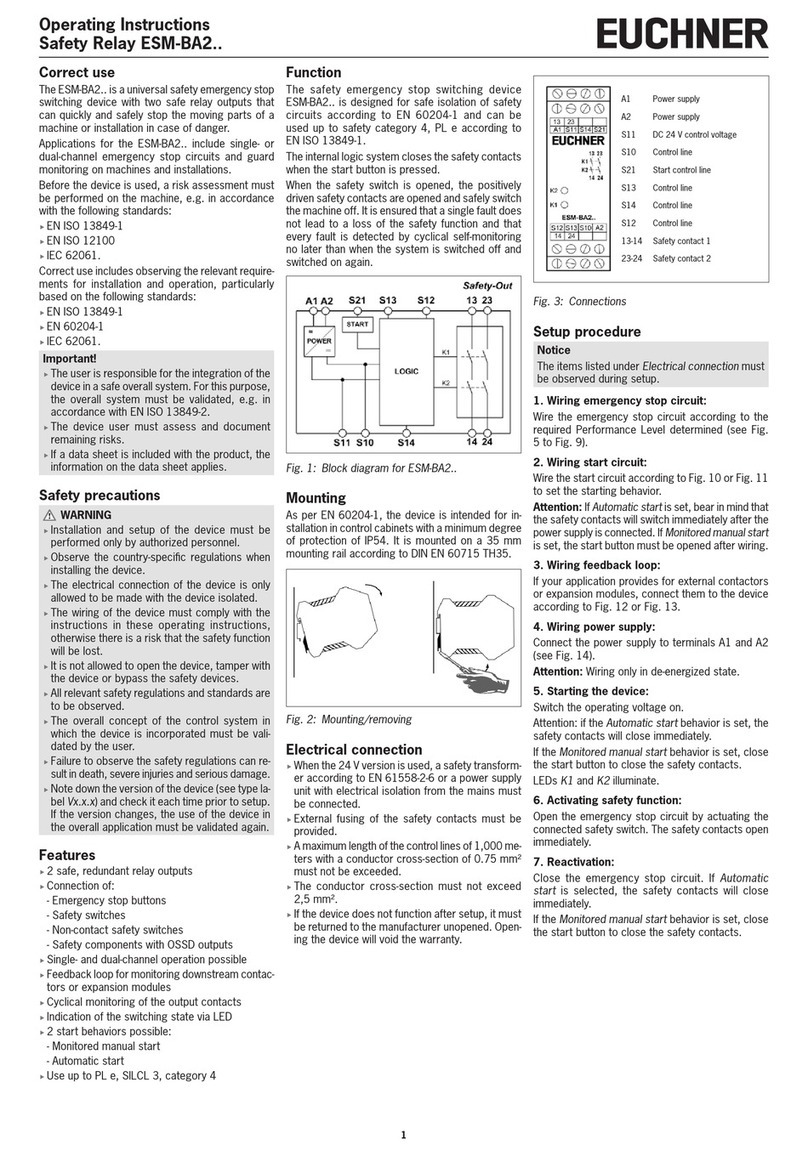
EUCHNER
EUCHNER ESM-BA2 Series User manual
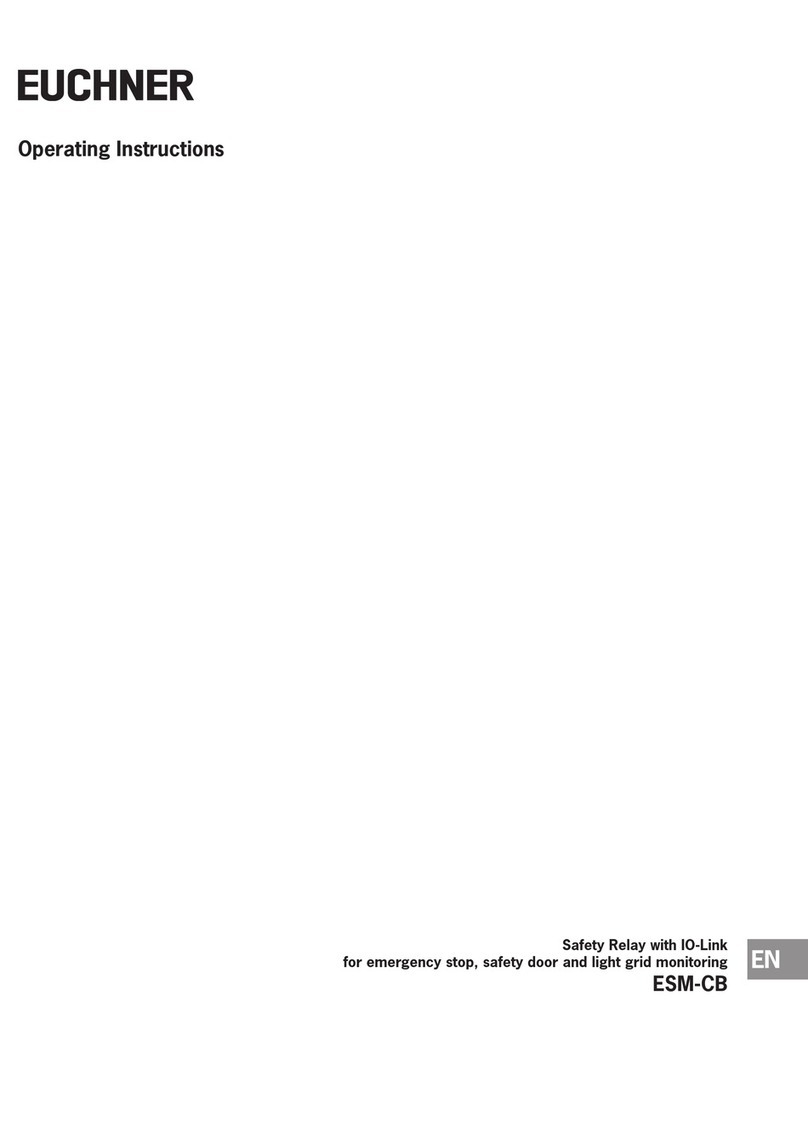
EUCHNER
EUCHNER ESM-CB User manual
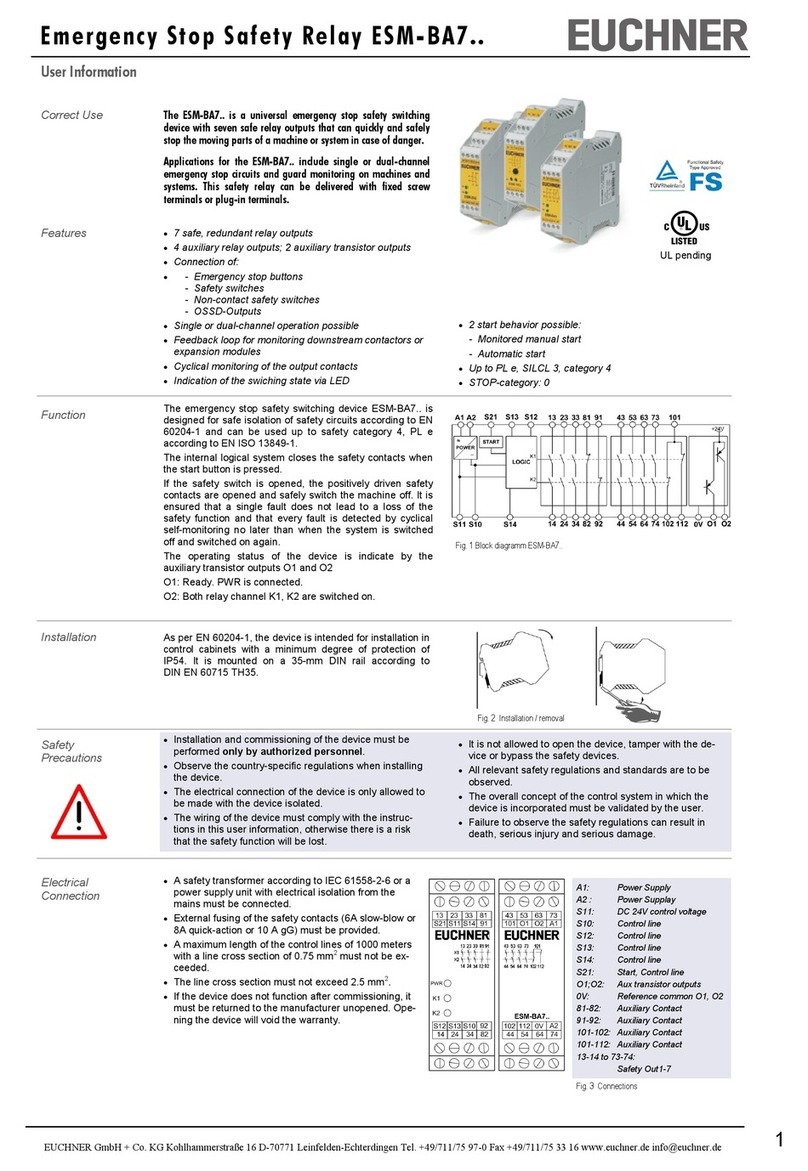
EUCHNER
EUCHNER ESM-BA7 Series Operation manual
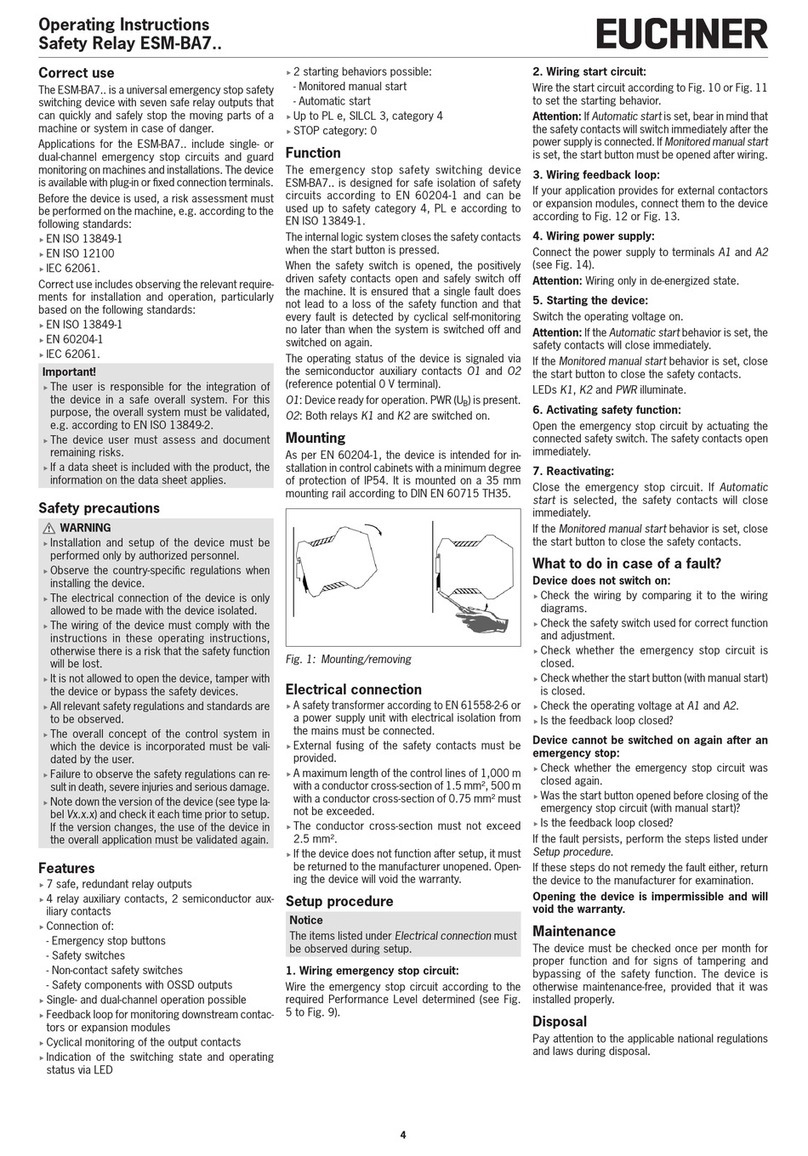
EUCHNER
EUCHNER ESM-BA7 Series User manual
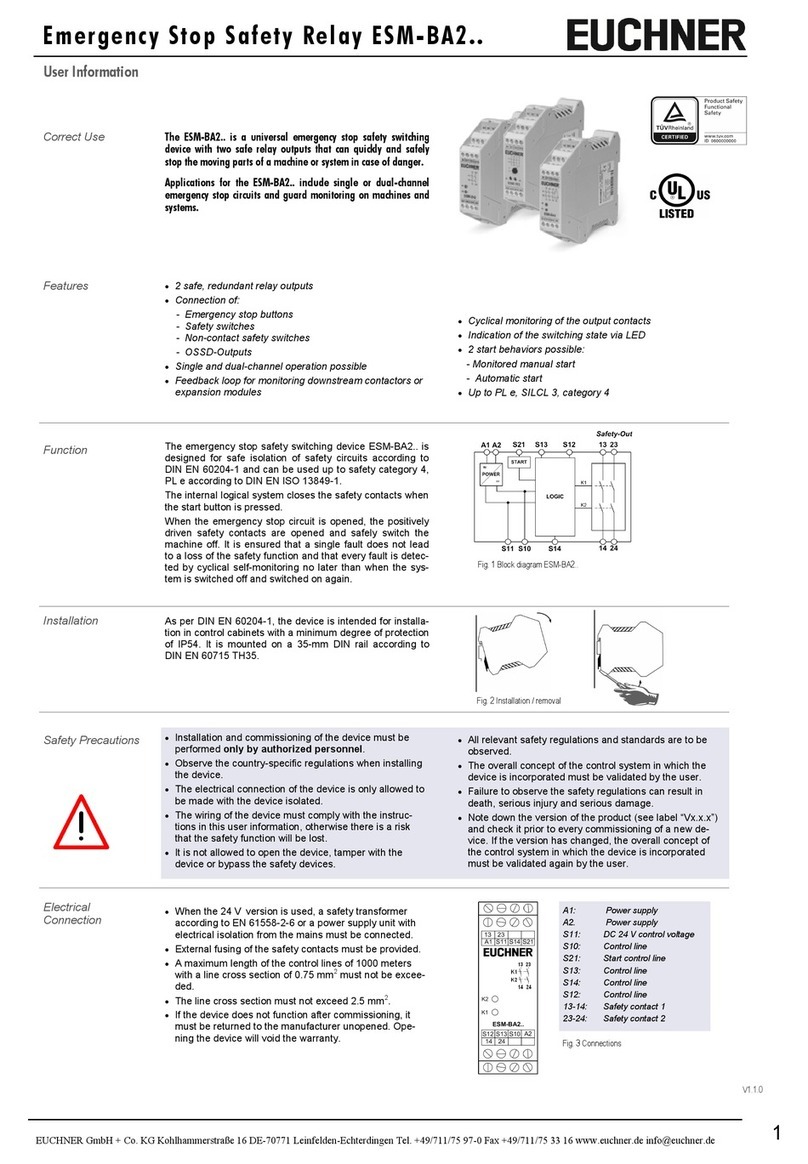
EUCHNER
EUCHNER ESM-BA2 Series Operation manual
Popular Relay manuals by other brands
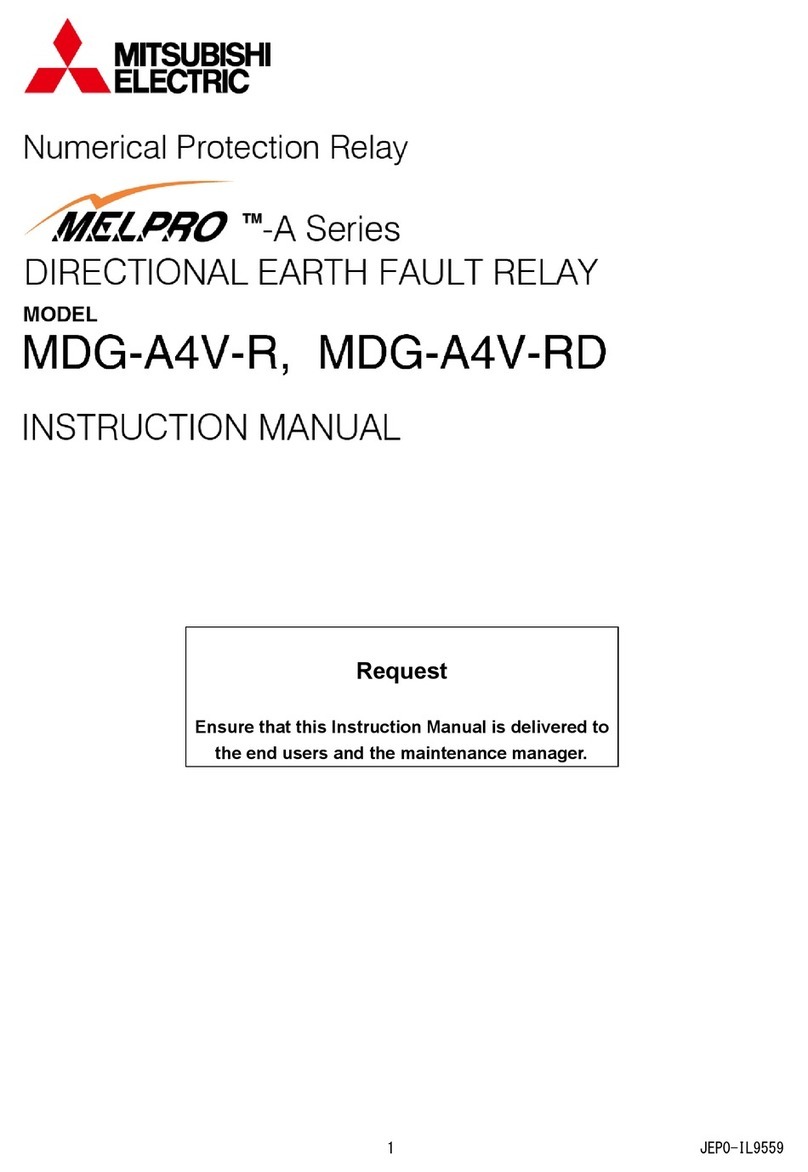
Mitsubishi Electric
Mitsubishi Electric MELPRO-A Series instruction manual

MULTISPAN
MULTISPAN VPR 3P user manual
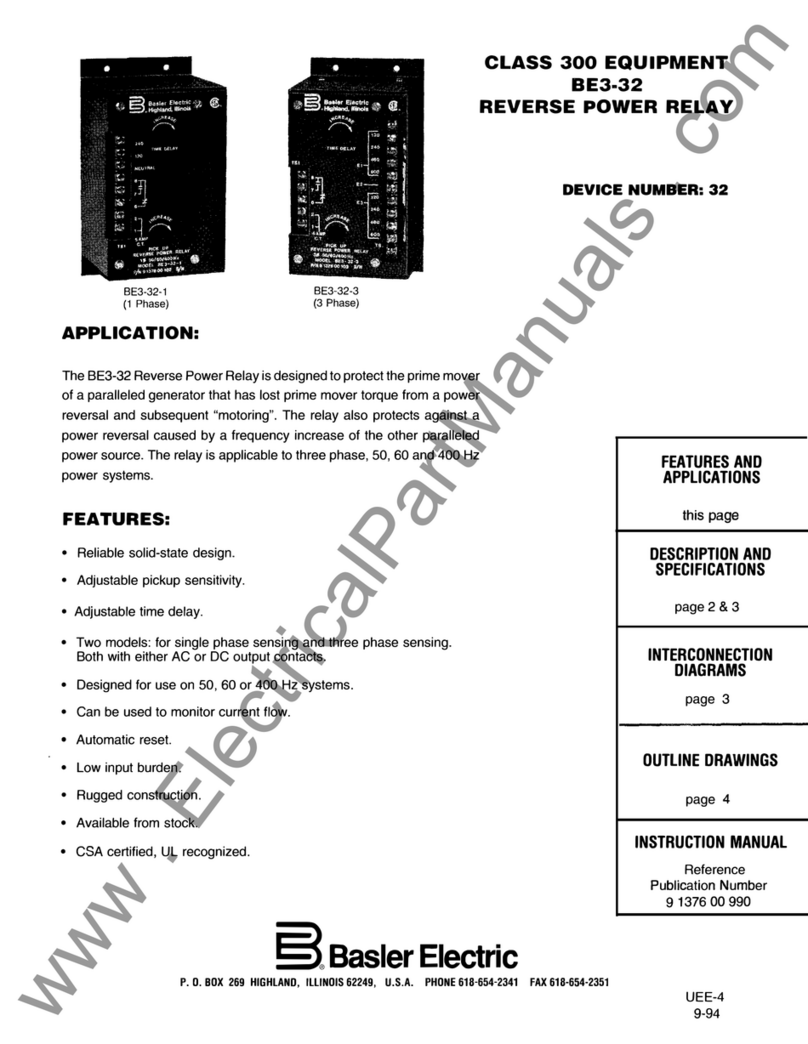
Basler
Basler Class 300 manual
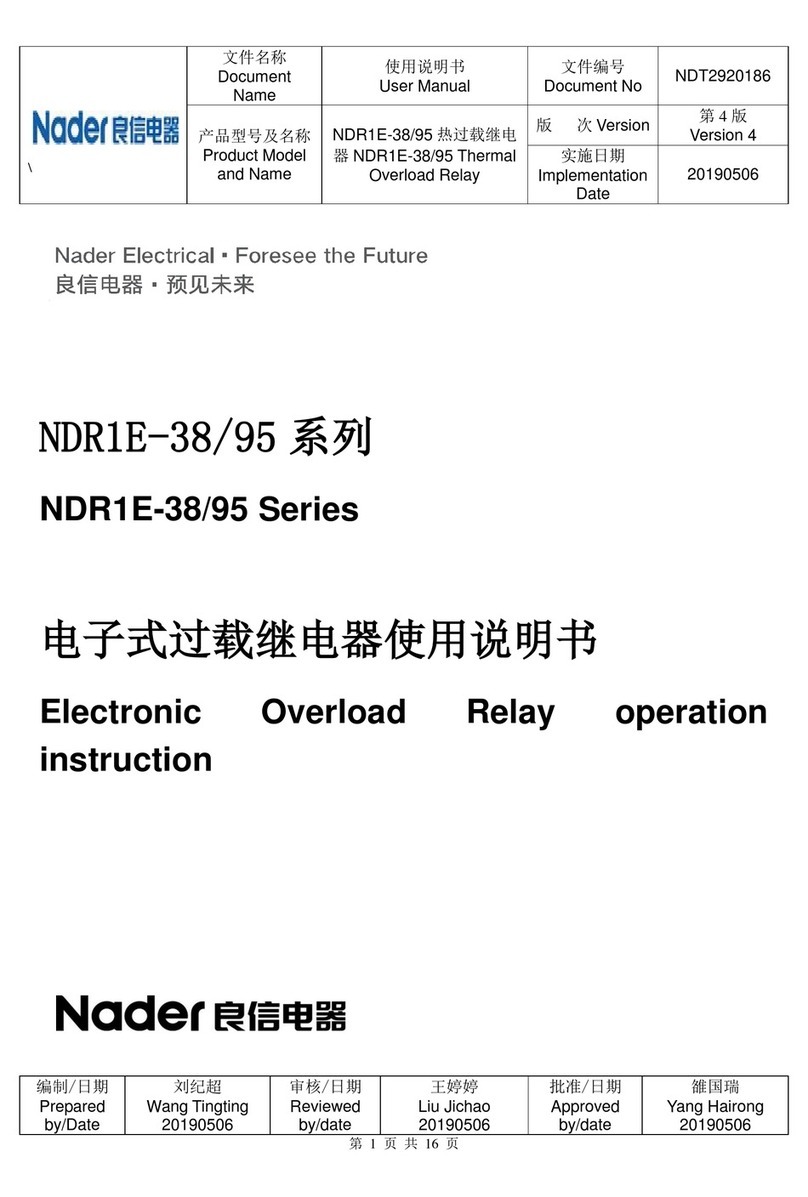
nader
nader NDR1E-38 Series operation instruction
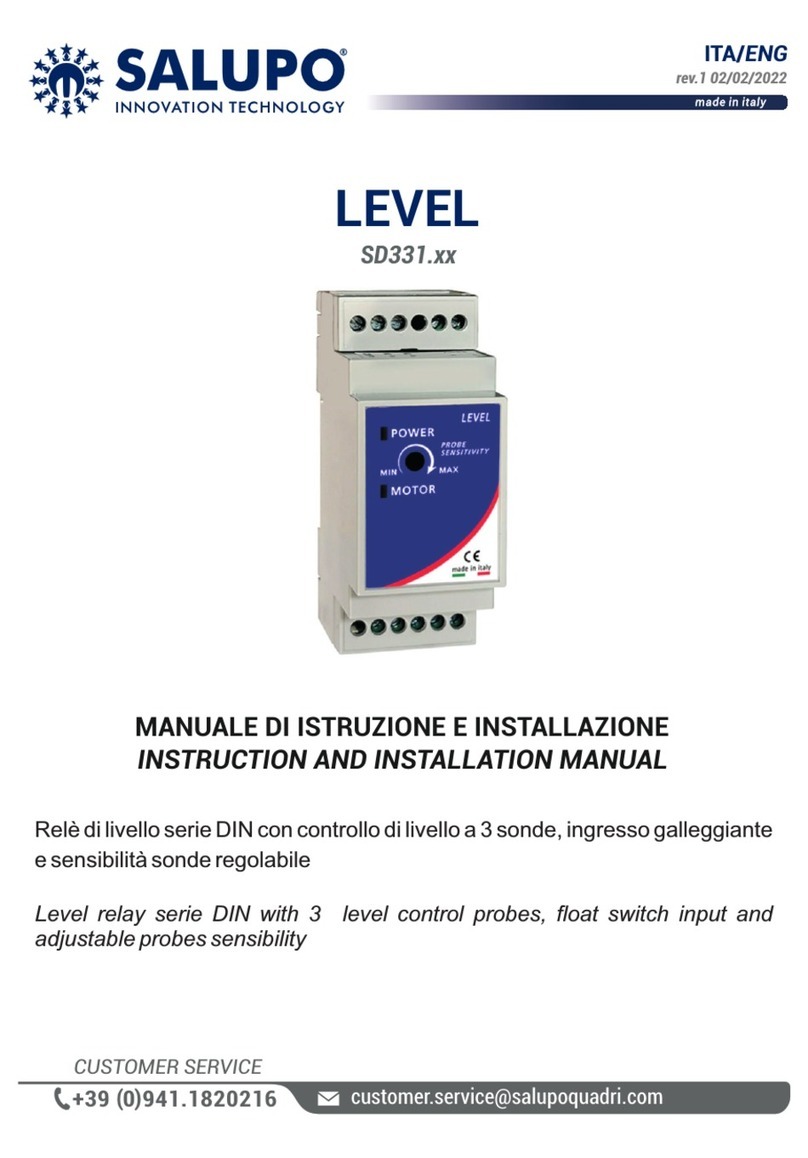
SALUPO
SALUPO LEVEL Series Instruction and installation manual
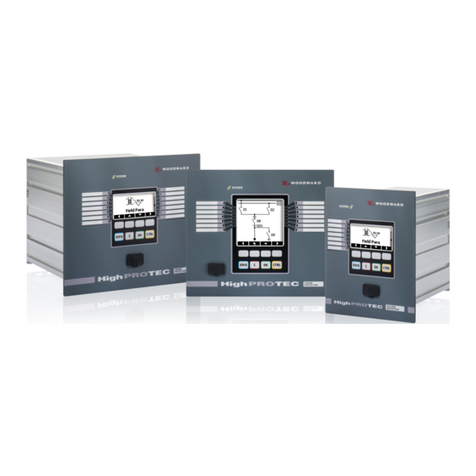
Woodward
Woodward HighProTec Series troubleshooting guide