Fluke Datapaq Reflow Tracker User manual

Datapaq
®
Reflow
Tracker
®
USER MANUAL
for use with
Insight™software
Issue 4
MA5120A


Datapaq
®
Reflow Tracker
®
User Manual
for use with Insight™software
Issue 4
DATAPAQ PART NO. MA5120A
Datapaq is the world’s leading brand of
process temperature-monitoring
instrumentation, and maintains
this leadership by continual development
of its advanced, easy-to-use Tracker systems.
Europe & Asia
Fluke Process Instruments
Lothbury House, Cambridge Technopark
Newmarket Road
Cambridge CB5 8PB
United Kingdom
Tel. +44-(0)1223-652400
sales@flukeprocessinstruments.co.uk
www.flukeprocessinstruments.com
North & South America
Fluke Process Instruments
87 Stiles Road, Suite 206
Salem
NH 03079
USA
Tel. +1-425-446-6780
sales@flukeprocessinstruments.com
www.flukeprocessinstruments.com

SAFETY
WARNINGS
For safe use of Datapaq equipment, always:
•Take care to follow its supplied instructions.
•Observe any warning signs shown on the equipment.
Indicates potential hazard.
On Datapaq equipment this normally warns of high temperature, but,
where you see the symbol, consult the manual for further explanation.
Warns of high temperatures.
Where this symbol appears on Datapaq equipment, its surface may be
excessively hot (or excessively cold) and may thus cause skin burns.
© Fluke Process Instruments, Cambridge, UK 2018
All rights reserved
Fluke Process Instruments makes no representations or warranties of any kind whatsoever with respect
to the contents hereof and specifically disclaims any implied warranties of merchantability or fitness for
any particular purpose. Fluke Process Instruments shall not be liable for errors contained herein or for
incidental or consequential damages in connection with the furnishing, performance or use of
the Datapaq software, associated hardware or this material.
Fluke Process Instruments reserves the right to revise this publication from time to time and to make
changes to the content hereof without obligation to notify any person of such revisions or changes.
Datapaq, Reflow Tracker and the Fluke Process Instruments logo are registered trademarks of
Fluke Process Instruments. Microsoft and Windows are registered trademarks of Microsoft Corporation.
Manual set in 10 pt Gill Sans.
User manuals are available in other languages; contact Fluke Process Instruments for details.

CONTENTS
7 Introduction
8 System Components
11 Basic Hardware
11 Thermal Barriers
12 Barriers for DP5 Logger Standard, 6-channel, DP5x60
13 Barriers for DP5 Logger Super-slim, 6-channel, DP5x61
14 Barriers for DP5 Logger Narrow, 6-channel, DP5x62
14 Barriers for DP5 Logger, 12-channel, DP5x12
15 Barriers for Q18 Micro Logger, DQ1804
15 Thermocouple Probes
16 Thermocouple Specification
16 Thermocouple Cables
19 Reflow Temperature Profiles: Creation and Use
20 Probe Location
20 Main Considerations
20 Typical Probe Locations
21 Probe Attachment
21 Good Practice
22 Methods of Attachment
23 Restraining the Cable
23 Preparing the Logger
24 Installing the Logger in the Thermal Barrier
25 Placing the System in the Oven
25 Removing from the Oven and Downloading Data
26 Analysis of Reflow Temperature Profiles
26 Profile Types
27 Checking Profiles
27 Statistical Process Control

31 Wave Solder
32 Running a Wave-solder Temperature Profile
33 Preparing the System for the Oven
34 Removing from the Oven and Downloading Data
35 Analysis of Wave-solder Temperature Profiles
35 Checking Profiles
37 Easy Oven Setup
37 Profile Prediction
38 Recipe Prediction
38 Setting Process Limits
40 Generating Recipe Predictions
40 Refining the Predictions
42 Troubleshooting the Predictions
43 Surveyor
44 Surveyor Hardware: Specifications and Use
44 Carrier Frame
46 Sensors
46 Preparing for a Baseline Survey or Profile Run
48 Running a Baseline Survey and Setting Tolerances
48 Performing a Profile Run
49 Surveyor Index
49 Trends and Predictions with SPC
51 Troubleshooting
51 Checking the Data
52 Testing the Logger and Thermocouples
52 Datapaq Service Department
53 INDEX

REFLOW TRACKER Introduction 7
Introduction
Datapaq
®Reflow Tracker
®, incorporating Insight™software, is a complete
system for monitoring and analyzing the temperature profiles of products within
all types of soldering processes. Power and flexibility make it a perfect tool for
process temperature monitoring, from commissioning and troubleshooting to
process optimization, ensuring consistent quality of product, consistent oven
performance and maximum efficiency. Innovative analysis techniques help in
identifying problems, fine-tuning the process and reducing running costs.
Insight is available for the reflow industry in different levels of sophistication to
meet the requirements of all applications.
•Reflow Tracker Professional – A high-end system, including the
functionality of Surveyor (see below).
•Reflow Tracker – The standard system for wide application, including
ability to perform hardwired telemetry and (with additional hardware and
software) radio telemetry, Easy Oven Setup, and analysis of oven trends
using Statistical Process Control (see below).
•Reflow Tracker Basic – A reduced feature set, but with full analysis
options and wizard-driven procedures.
•Reflow Lite – Essential features for profile-gathering and simple analysis.
Reflow Tracker is equally useful for other soldering applications such as wave solder,
vapor phase, curing ovens and rework stations.
Telemetry options allow full monitoring of temperatures in real time while a
job is actually in the oven: hardwired telemetry is part of the standard system
(see the dedicated User Manual supplied with your data logger), and Reflow
Tracker can be specified to include the TM21 radio-telemetry system.
Statistical Process Control (SPC) allows easy analysis of the results of
profile runs over time, highlighting trends in the performance of your process,
and allowing potential problems to be identified and dealt with before they
occur.
Easy Oven Setup (not available in Insight Reflow Tracker Basic and Reflow Lite)
enables users rapidly and accurately to set up their ovens for new products and/
or new solder formulations by predicting the recipes that should be used to
achieve given temperature profiles – and with the Surveyor option (Insight
Reflow Tracker Professional only) you can compare a reference profile (baseline
survey) of your oven’s ideal performance against a profile which has been
obtained subsequently – by a relatively unskilled operator – in order to check
whether the oven performance has deteriorated.

8 Introduction REFLOW TRACKER
Powerful reporting facilities allow the user to generate customized printouts,
including any or all of the analysis results or raw temperature data.
This manual contains the following sections:
•Basic Hardware (p. 11) – The standard system’s thermal barriers and
thermocouple probes, their specifications and their care and maintenance.
•Reflow Temperature Profiles (p. 19) – All the stages of obtaining a
temperature profile from a typical reflow process, including the positioning
of probes and using the profiles to correct faults in the soldering process.
•Wave Solder (p. 31) – Use of a Reflow Tracker system in a wave-solder
process.
•Easy Oven Setup (p. 37) – Set up an oven for a new product by
predicting an oven recipe. (Not available in Insight Reflow Tracker Basic and
Reflow Lite.)
•Surveyor (p. 43) – Monitor an oven’s performance in order to assess
trends and check whether it has deteriorated. (Insight Reflow Tracker
Professional only.)
•Troubleshooting (p. 51) .
The dedicated User Manual supplied with your data logger should be read in
conjunction with this manual. It provides information on operating the logger,
including:
•Installing Insight and establishing communication between logger and PC.
•Resetting the logger with new data-collection parameters.
•Downloading the collected data to the PC.
•Use of hardwired telemetry.
•Troubleshooting logger problems.
For full details on use of the Insight software, refer to the online Help system
available when the software is installed.
System Components
A typical Reflow Tracker system comprises:
•Data logger, with communications lead and charger; logger with radio-
telemetry option includes internal transmitter.
•Receiver (radio-telemetry option only).
•Thermal barrier – to protect the logger during its time in the oven.
•Thermocouple probes.
•Insight Reflow Tracker software.
•User documentation:

REFLOW TRACKER Introduction 9
○Reflow Tracker User Manual.
○Data logger User Manual (specific to the logger model).
○TM21 Radio-telemetry System User Manual (radio-telemetry option only).
Additional hardware is supplied with Wave Solder (p. 31) and Surveyor
systems (p. 43).
This manual, and other Datapaq user documentation, in various languages, is
available on the Insight installation DVD included with Datapaq systems. During the
software installation, you may select documents to be copied to your PC for rapid
on-demand viewing through Insight.

10 Introduction REFLOW TRACKER

REFLOW TRACKER Basic Hardware 11
Basic Hardware
The standard Reflow Tracker system includes one or more thermal barriers and
appropriate thermocouples.
For use of the data logger, and for other special-purpose hardware,
see the documentation supplied with it.
Thermal Barriers
The thermal barrier provides the thermal and mechanical protection necessary
for the data logger to survive in the hostile environment of reflow, wave-solder,
vapor-phase and curing ovens.
A range of barriers is available to suit different loggers and different purposes.
Specifications of barriers to fit the Datapaq DP5 logger are given below; these
use Microtherm insulation for primary thermal protection.
WARNING
It is essential to use the correct Datapaq thermal barrier for your individual process,
as supplied and approved by Fluke Process Instruments. Failure to use the
appropriate approved barrier, or the use of a barrier in an unapproved manner (e.g.
using above the specified temperature, or for longer than the specified time, or with
insufficient opportunity for adequate cooling between profile runs), can cause
catastrophic damage to the data logger or to other equipment, can endanger
health, or (if lithium batteries are being used)may lead to severe injury or death.
For the same reasons, never use a damaged thermal barrier.
Ensure that all dimensions of your logger/barrier/accessory assembly are such that it
will fit comfortably within the oven through all stages of the process. Pay particular
attention to handles, catches, etc., and to trailing thermocouples. Failure to do this
can cause the assembly to jam in the oven with consequent overheating and
potentially-severe damage to the equipment. Resultant battery-leakage, and the act
of recovering the equipment, may cause skin burns and respiratory irritation.

12 Basic Hardware REFLOW TRACKER
Barriers for DP5 Logger Standard, 6-channel, DP5x60
These barriers also fit Q18 standard 6-channel logger, DQ1860.
TB2015 – Most reflow soldering processes including lead-free
Temp °C 100 150 200 250 280
Duration (mins) 32 16 13 10 9
Dimensions Height
Width
Length
Weight
25 mm
133 mm
210 mm
0.7 kg
1.0 in.
5.2 in.
8.3 in.
1.5 lb
TB2064 – Low-height thermal barrier
Temp °C 100 150 200 250 280
Duration (mins) 25 12 986
Dimensions Height
Width
Length
Weight
20 mm
133 mm
210 mm
0.6 kg
0.8 in.
5.2 in.
8.3 in.
1.3 lb
Part of the range of Datapaq thermal barriers for the Datapaq DP5 logger.

REFLOW TRACKER Basic Hardware 13
TB2065 – Increased protection for frequent use or for long-duration
processes
Temp °C 100 150 200 250 280
Duration (mins) 35 18 13 11 10
Dimensions Height
Width
Length
Weight
29 mm
133 mm
210 mm
0.7 kg
1.1 in.
5.2 in.
8.3 in.
1.5 lb
Barriers for DP5 Logger Super-slim, 6-channel, DP5x61
These barriers also fit Q18 super-slim 6-channel logger, DQ1861.
TB2066 – Low-height thermal barrier
Temp °C 100 150 200 250 280
Duration (mins) 21 11 8 6 6
Dimensions Height
Width
Length
Weight
20 mm
88 mm
334 mm
0.65 kg
0.8 in.
3.5 in.
13.1 in.
1.4 lb
TB2067 – Most reflow soldering processes including lead-free
Temp °C 100 150 200 250 280
Duration (mins) 28 15 11 10 8
Dimensions Height
Width
Length
Weight
25 mm
88 mm
334 mm
0.75 kg
1.0 in.
3.5 in.
13.1 in.
1.7 lb
TB2068 – Increased protection for frequent use or for long-duration
processes
Temp °C 100 150 200 250 280
Duration (mins) 32 18 13 11 10
Dimensions Height
Width
Length
Weight
29 mm
88 mm
334 mm
0.8 kg
1.1 in.
3.5 in.
13.1 in.
1.8 lb

14 Basic Hardware REFLOW TRACKER
Barriers for DP5 Logger Narrow, 6-channel, DP5x62
These barriers also fit Q18 narrow 6-channel logger, DQ1862.
TB2020 – Low-height thermal barrier
Temp °C 100 150 200 250 280
Duration (mins) 25 13 10 8 7
Dimensions Height
Width
Length
Weight
28 mm
84 mm
241 mm
0.5 kg
1.1 in.
3.3 in.
9.5 in.
1.1 lb
TB2021 – Most reflow soldering processes including lead-free
Temp °C 100 150 200 250 280
Duration (mins) 36 18 13 11 10
Dimensions Height
Width
Length
Weight
35 mm
84 mm
241 mm
0.65 kg
1.4 in.
3.3 in.
9.5 in.
1.4 lb
Barriers for DP5 Logger, 12-channel, DP5x12
TB2100 – Low-height thermal barrier
Temp °C 100 150 200 250 280
Duration (mins) 25 13 10 8 7
Dimensions Height
Width
Length
Weight
28 mm
133 mm
243 mm
0.69 kg
1.1 in.
5.2 in.
9.6
in.
1.5 lb
TB2101 – Most reflow soldering processes including lead-free
Temp °C 100 150 200 250 280
Duration (mins) 36 18 13 11 10
Dimensions Height
Width
Length
Weight
35 mm
133 mm
239 mm
0.77 kg
1.4 in.
5.2 in.
9.4 in.
1.7 lb

REFLOW TRACKER Basic Hardware 15
Barriers for Q18 Micro Logger, DQ1804
TB2098 – Reflow soldering processes
Duration 10 mins at 200°C.
Dimensions Height
Width
Length
Weight
27 mm
57 mm
190 mm
0.4 kg
1.1 in.
2.2 in.
7.5 in.
0.9 lb
TB3006 – Long-duration reflow soldering processes
Duration 14 mins at 200°C.
Dimensions Height
Width
Length
Weight
32 mm
71 mm
194 mm
0.6 kg
1.3 in.
2.8 in.
7.6 in.
1.3 lb
Thermocouple Probes
Thermocouple probes utilize an effect by which an e.m.f. is produced in any
electrically conducting material that is not at uniform temperature. The actual
voltage measured is proportional to the temperature difference between the
thermocouple’s ‘hot’ and ‘cold’ junctions (the hot junction being the
measurement junction, and the cold junction being the junction of thermocouple
and measurement instrumentation).
The practical implementation of thermocouples requires sophisticated
electronics to eliminate potential measurement errors which include poor
linearity over the measurement range, and inaccuracy due to temperature
variations at the cold junction.To accommodate these the electronics in the
measuring system must simulate a temperature of 0°C at the cold junction, as
well as compensating for any non-linearity over the range of thermocouple
operation.
Over the years, ‘standard’ thermocouples have been developed using materials
chosen for sensitivity, linearity (consistency of sensitivity over the useful
temperature range), price and availability. Current standards include types K, N,
R, S and T, each type being identified by its connector color. The standard
thermocouple probe for reflow industry use is type K.
All Reflow Tracker systems are supplied with one set of PTFE-insulated
thermocouple probes (part no. PA0210). Other probes available are:
•High-temperature glass-fiber-insulated (PA0215).
•Fine-wire, for use on ball grid arrays (BGAs) (PA1683).
•Special probes for wave-solder pallet (p. 31).
•Surveyor sensors. See p. 46.

16 Basic Hardware REFLOW TRACKER
All have green type-K connectors (conforming to IEC 60584-3).
WARNING
Never connect thermocouples to mains electricity, nor allow thermocouples to
touch an oven’s heating elements. This could cause major injury or death.
Take care when handling thermocouple cables to avoid accidental damage to the
eyes by sharp thermocouple-tips.
Thermocouple Specification
Probe
Type
Temperature
Range
Cable Insulation Accuracy of Probes Supplied
by Datapaq (ANSI MC96.1)
K−150°C to 1,370°C Glass fiber or PTFE ±1.1°C or ±0.4% at 0–1,250°C
The presence of a probe on the product adds to the product’s thermal mass,
changing – however slightly – its rate of heating and cooling. To minimize the
probe’s thermal mass, and therefore its affect on the product, the type K
probes supplied with the Reflow Tracker system are constructed from 0.2-mm
wire.
Thermocouple Cables
The practical operating temperature of the thermocouple probes is limited by
the cable insulation material’s temperature characteristics.
Probes insulated with thin glass fiber, impregnated with a silicone resin binder,
are suitable for use at temperatures up to 500°C continuously and 700°C short
term and should be used if the probe cables could come into close
proximity with infra-red heating elements.
PTFE (polytetrafluoroethylene)-insulated probes are suitable for general-
purpose use at temperatures up to 260°C. PTFE is a robust, flexible, non-stick
material, with a low thermal mass and therefore a quick response time. This is
the standard insulation for reflow use, though it cannot be used when probe
cables may be close to infra-red heating elements.
WARNING
PTFE does not support combustion, but decomposes above 265°C producing small
amounts of toxic fumes.

REFLOW TRACKER Basic Hardware 17
The important products from PTFE thermal decomposition are:
At Temperatures Greater Than: Product
400°C See note*
430°C Tetrafluoroethylene
440°C Hexafluoropropylene
475°C Perfluoroisobutylene
500°C Carbonyl fluoride*, which, in moist air,
converts to the acid gas hydrogen fluoride
*
May also be produced if PTFE tape is kept at 400°C for an extended time.
Health Hazard Data
•Inhalation of decomposition products from PTFE can produce ‘polymer fume
fever’, which has symptoms similar to influenza.
•There is no risk from ingestion or skin contact.
•There are no medical conditions generally aggravated by exposure to PTFE.
Emergency and First-aid Procedures
•If there is accidental contact with PTFE fumes, remove the person
concerned to clean air.
•Self-contained breathing apparatus and protective clothing should be worn
when fire-fighting.

18 Basic Hardware REFLOW TRACKER

REFLOW TRACKER Reflow Temperature Profiles 19
Reflow Temperature
Profiles: Creation and Use
A temperature profile can be acquired by two means:
•Without telemetry – After the logger and product have been in the oven,
data is downloaded from the logger into the PC to be displayed and analyzed
by the Datapaq Insight software.
•Using telemetry – As the logger gathers data from the product inside the
oven, this is transmitted directly to the PC by a hard-wired connection
(serial telemetry) or by radio transmitter/receiver (radio telemetry). The
temperature profile can be watched developing as it happens, i.e. in real
time. For the use of hardwired telemetry, see your dedicated logger User
Manual. For radio telemetry, see the TM21 Radio-telemetry System User
Manual.
This chapter describes all the stages of obtaining a reflow temperature profile
for a PCB while it is in the oven, without telemetry – from how and where to
place the probes, to downloading the data into the software, ready to be
analyzed.
To run a temperature profile in a wave-solder oven, see p. 31.
Before running your PCB and the data logger through the oven you will use the
Insight software to reset the logger, i.e. to prepare it for receiving fresh data.
After the logger has been retrieved from the oven, you will use Insight again to
download the profile data and save it to disk.
In summary, the stages are as follows.
1. Choose positions for, and attach, the thermocouple probes.
2. Setup communication between the data logger and your PC (if this has
not already been done for a previous profile run).
3. Reset the data logger so that it is ready to receive fresh data; in the
process of doing this you will also be able to set the sample collection
interval and the method used to trigger the start of data collection, and to
check the logger’s battery status.
4. Install the logger in its thermal barrier.
5. Run the PCB and logger/barrier through the oven.
6. Download the data from the logger into the Insight software.
7. If necessary, set the oven start position within the data.

20 Reflow Temperature Profiles REFLOW TRACKER
8. Add any additional information that you wish to have recorded with the
profile data.
After this, Insight can be used to analyze the profile data as required.
Probe Location
Whatever the method of heating, the thermal mass of the PCB, its tracks and
the components attached to them significantly influence the time taken for each
physical element to attain a given temperature. Positioning of probes is thus
crucial in ensuring that all key parts of the PCB follow a specified temperature
profile, usually based on data from the solder-paste manufacturer.
Main Considerations
•Large ground planes absorb
more heat and take longer to
achieve reflow temperatures
than narrow tracks.
•Large quad flat packs and ball-
grid arrays absorb a lot of heat;
they are also more susceptible
to damage by thermal shock
than most other components.
•Large surface-mount devices
can shade the tracks to which
they are to be soldered.
•The edges of the PCB heat
more rapidly than the center.
•Is the track density even? If so, the heating may be more uniform; if not,
there may be localized hot and cold spots.
•Is the board double-sided? If so, it may have to go through the oven twice:
the bottom of the board must be kept below reflow temperatures or solder-
ability could be lost, de-wetting experienced, and components could fall off.
•Is it a multi-layer board? If so, it is likely to have more copper and so require
more heat, but it may heat more evenly.
Typical Probe Locations
•Locations likely to achieve the fastest rate of temperature increase, e.g.
board edges and/or locations of components with low thermal mass.
•Locations having a high thermal mass which may require extra time to
achieve reflow temperature.
Probes attached to the PCB and components.
This manual suits for next models
12
Table of contents
Other Fluke Measuring Instrument manuals
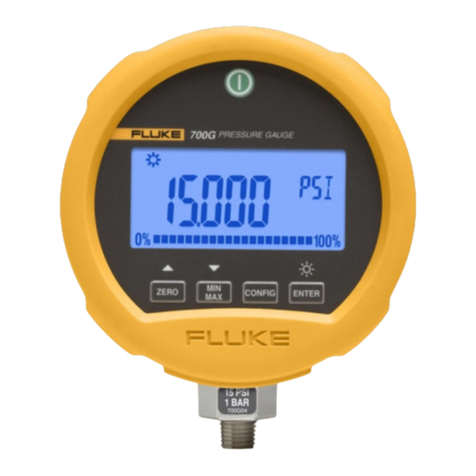
Fluke
Fluke FL700G01 User manual

Fluke
Fluke ESA615 User manual
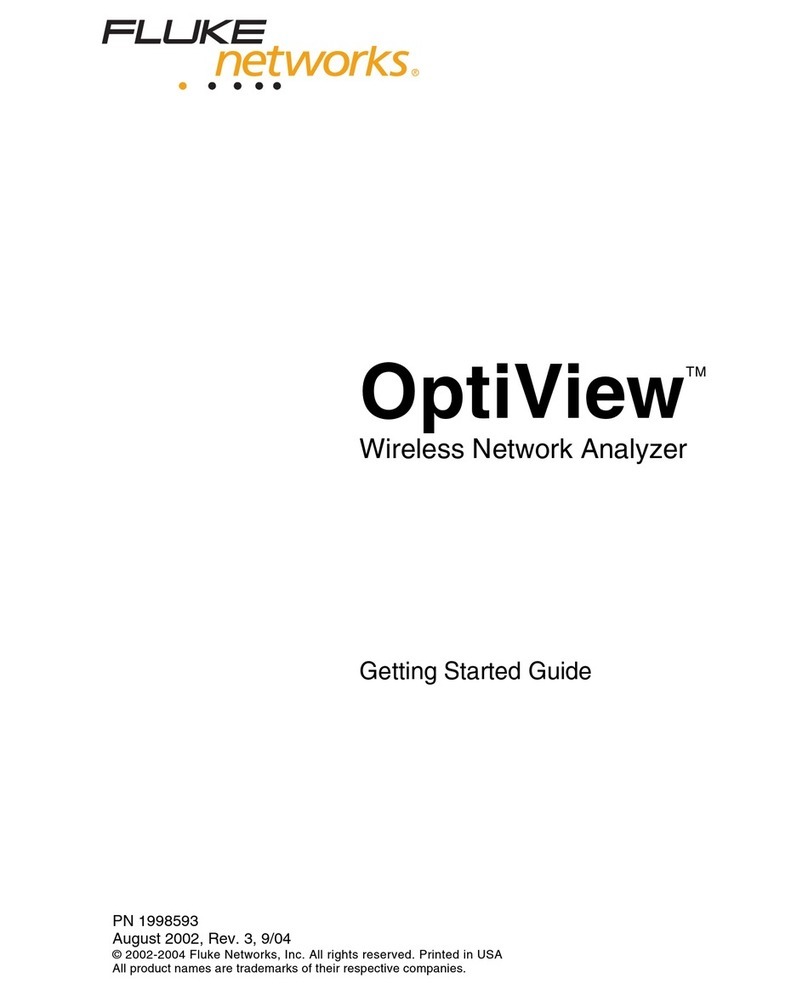
Fluke
Fluke OptiView User manual

Fluke
Fluke a3001 FC Use and care manual

Fluke
Fluke OptiFiber Pro User manual
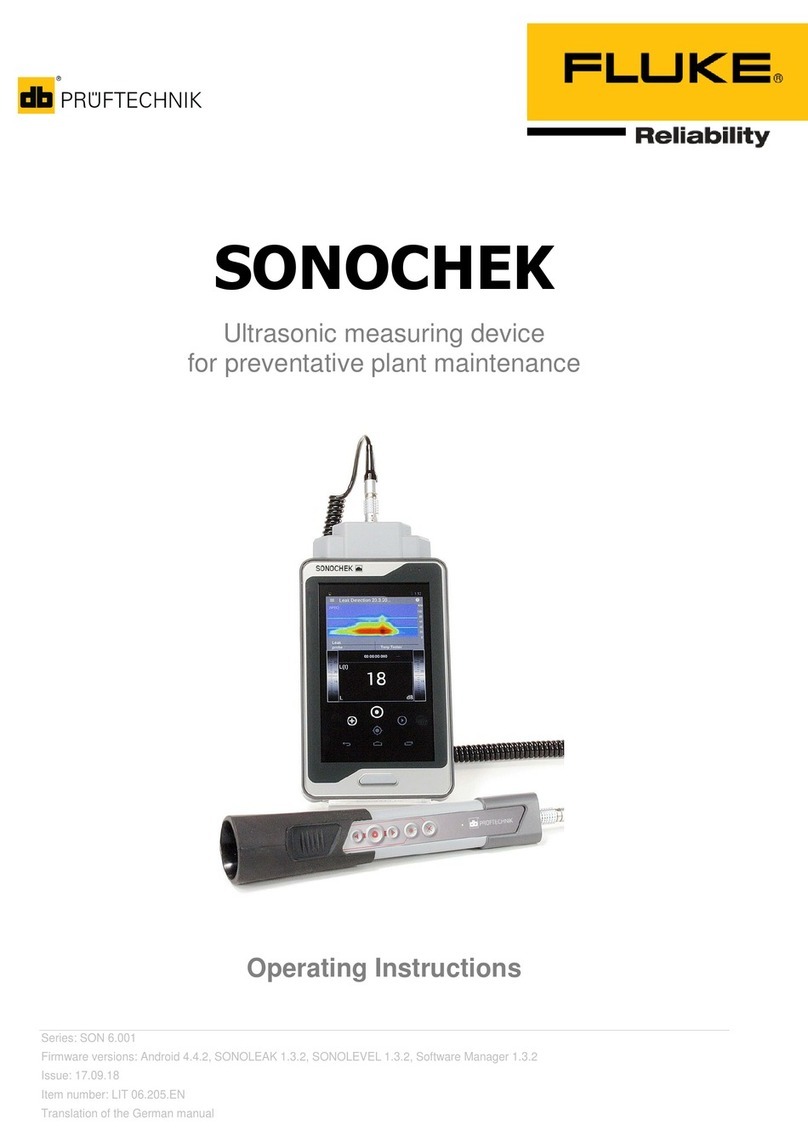
Fluke
Fluke SONOCHEK User manual
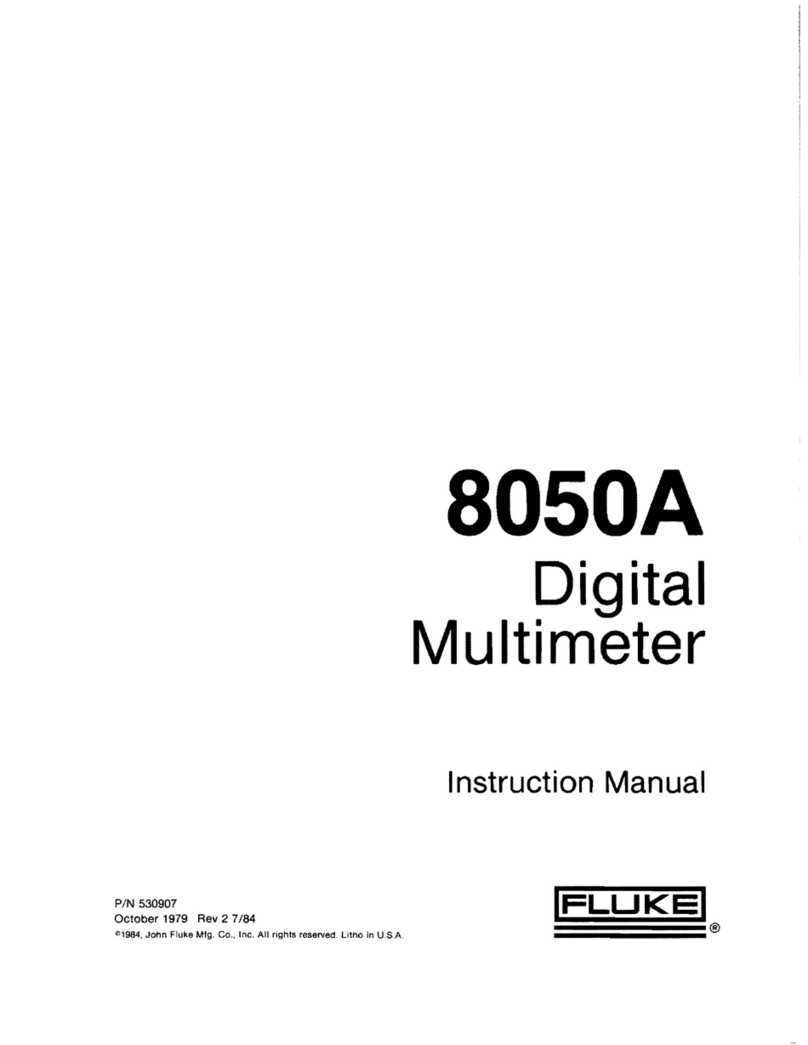
Fluke
Fluke 8050A User manual

Fluke
Fluke SMFT1000/PRO User manual
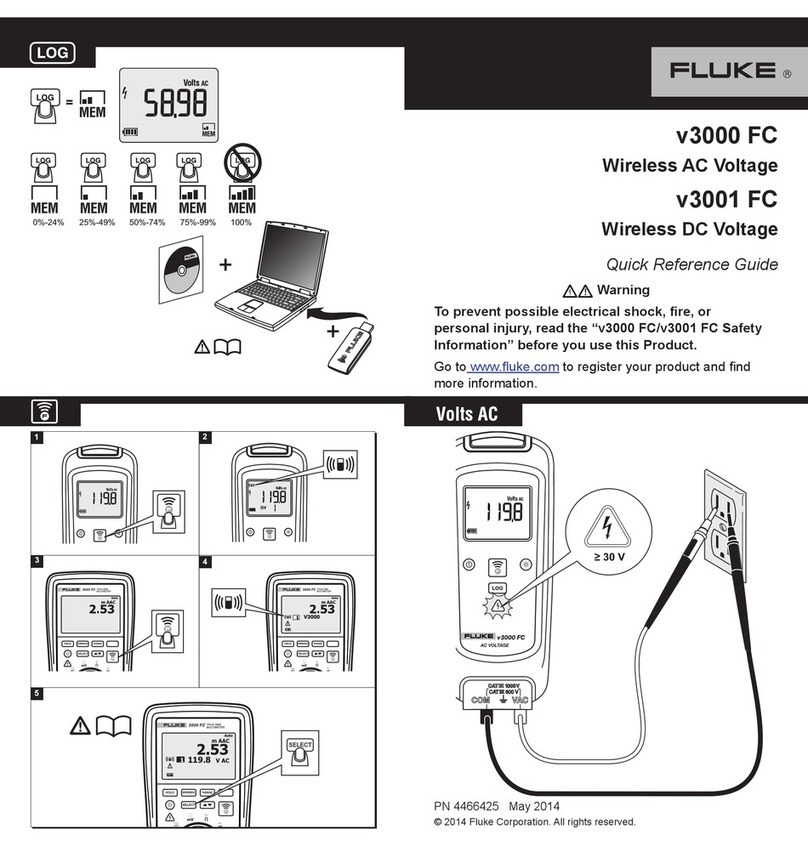
Fluke
Fluke v3000 FC User manual
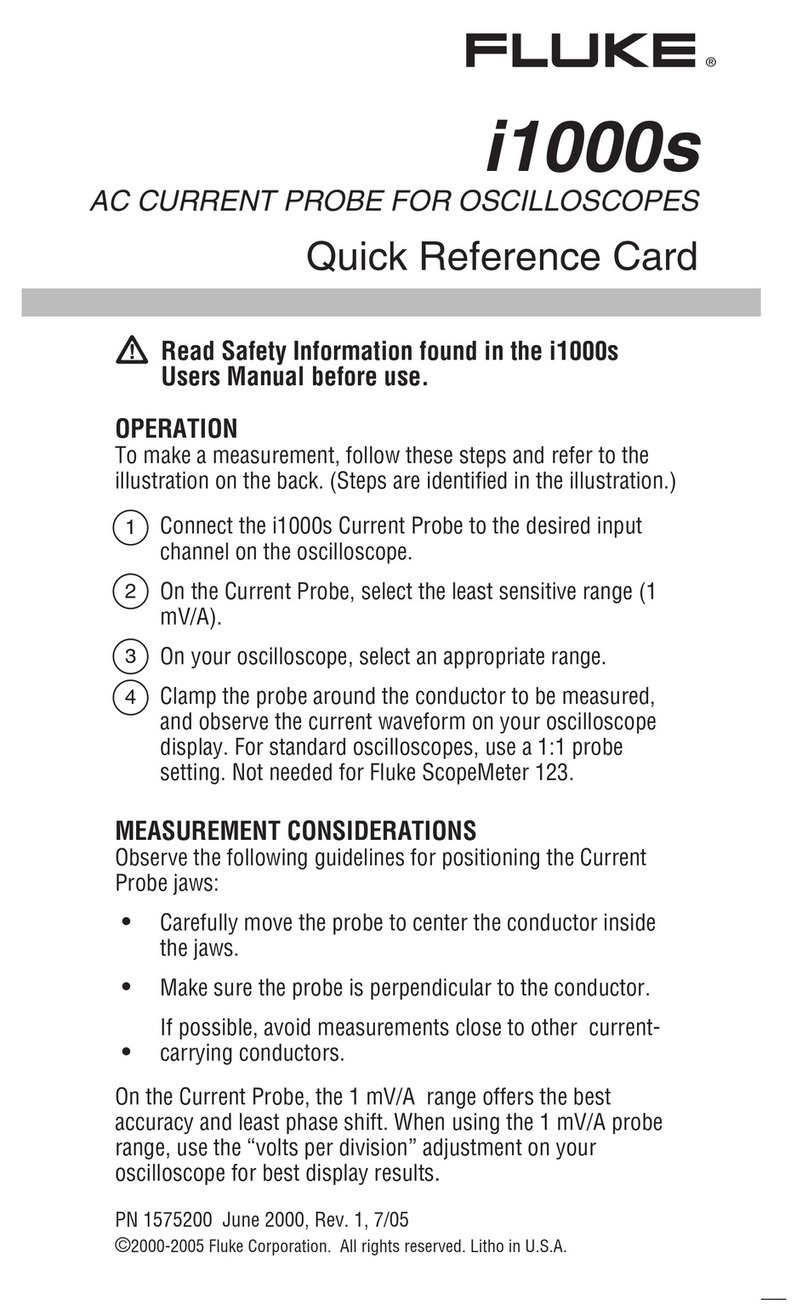
Fluke
Fluke i1000s Reference guide
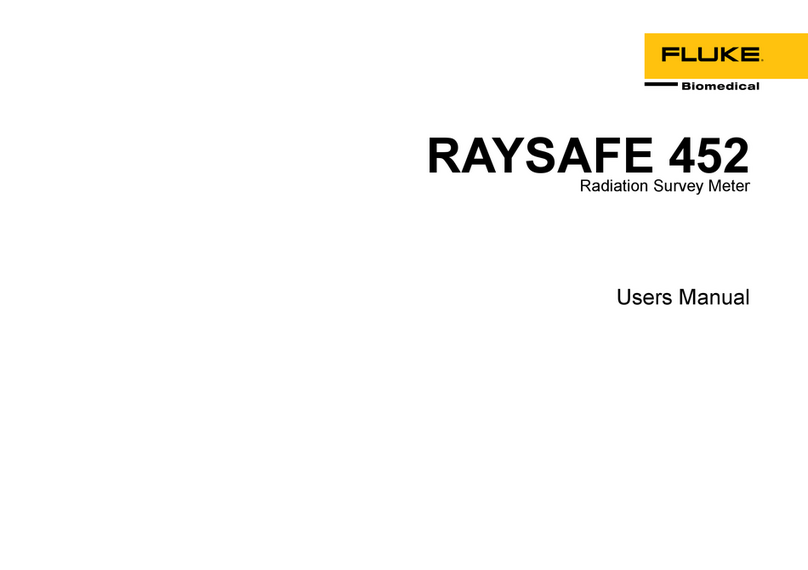
Fluke
Fluke RaySafe 452 User manual

Fluke
Fluke 1760 Parts list manual

Fluke
Fluke 914 Series User manual
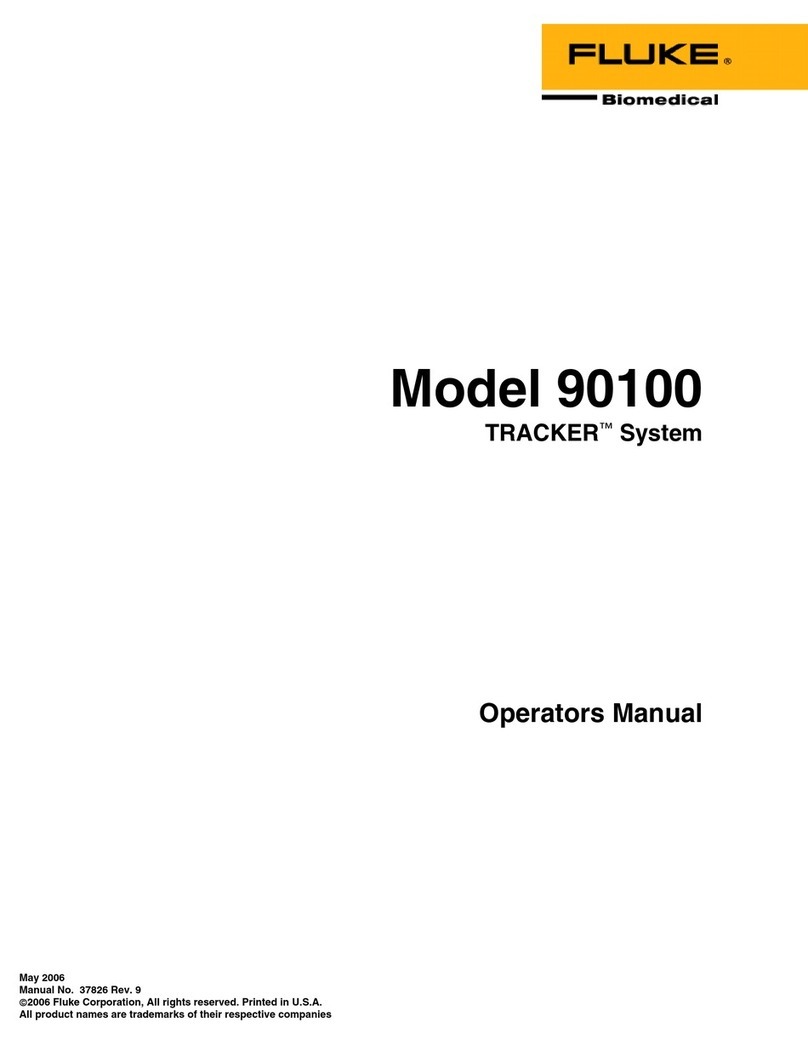
Fluke
Fluke TRACKER 90100 Operators User manual
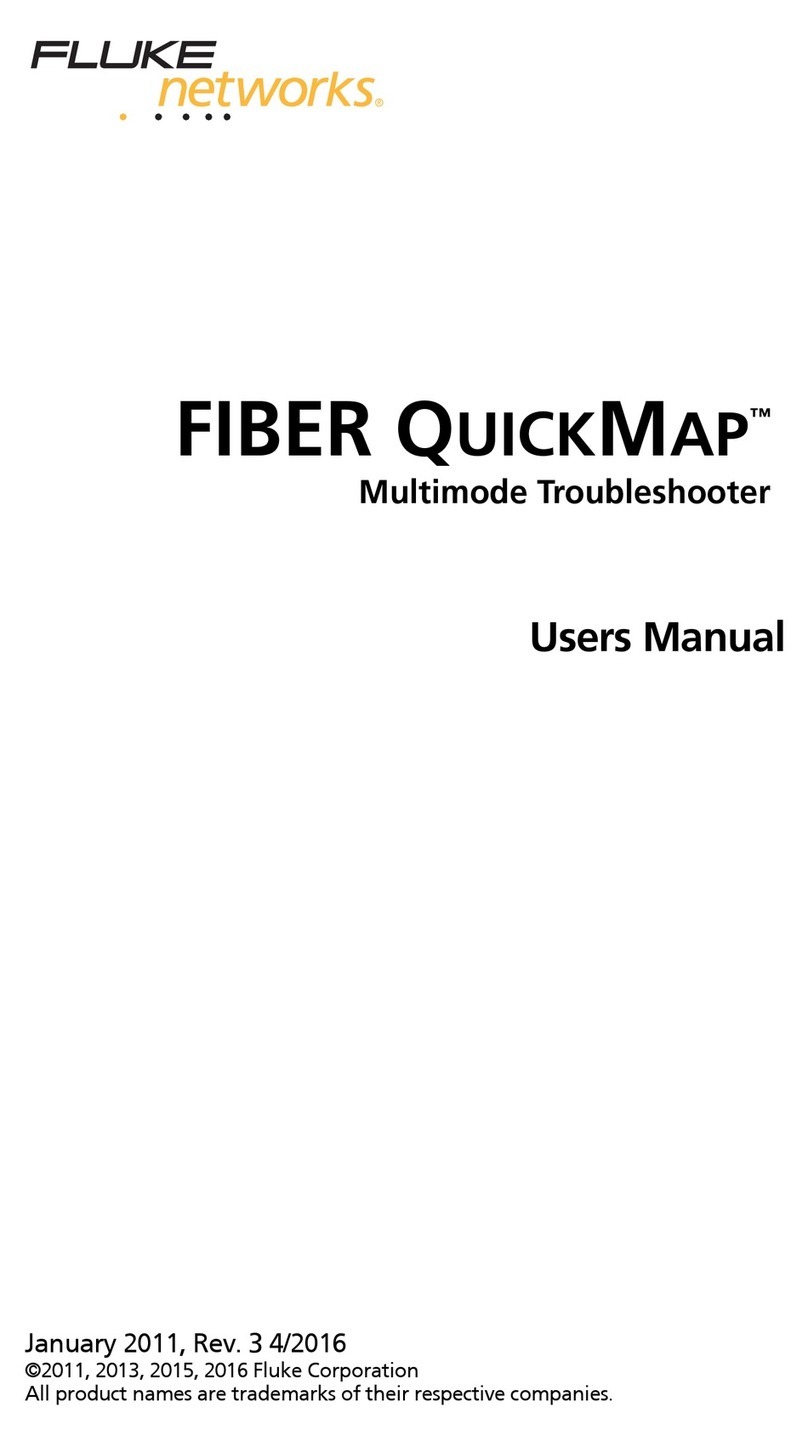
Fluke
Fluke FIBER QUICKMAP User manual
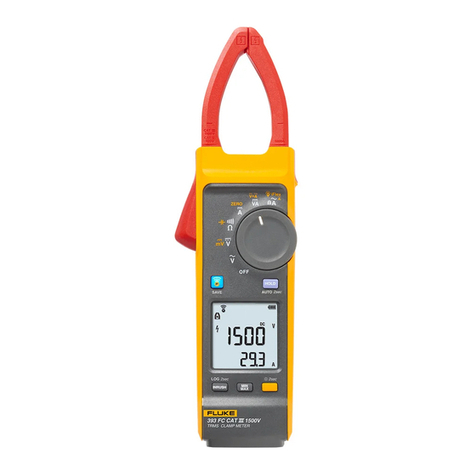
Fluke
Fluke 393 FC User manual

Fluke
Fluke 805 FC User manual
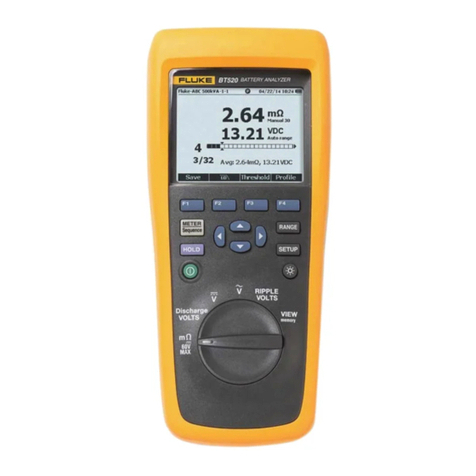
Fluke
Fluke BT520 User manual

Fluke
Fluke 1742 Configuration guide

Fluke
Fluke 931 User manual