FMT Swiss AG 23 190 Instruction Manual

00 430 932 A804 GB
Manual Flow Meter
OPERATING INSTRUCTIONS
AND SAFETY NOTES

2
Operating Instructions – Manual Flow Meter
FMT Swiss AG
This documentation is exclusively intended for the operating company and their sta.
Without our written consent, the content of this documentation (textes, gures, drawings, charts,
diagrams etc. ), must not be duplicated or distributed, neither in full or in part, utilized for the purpose
of competition or passed on/made availabe to third parties.
FMT Swiss AG
Fluid Management Technologies Swiss AG
Gewerbestraße 6
6330 Cham / Switzerland
Tel. +41 41 712 05 37
Fax +41 41 720 26 21
Email: info@fmtag.com
Internet: www.fmtag.com
Operating instructions translation
Date of issue: 09/2021
We reserve the right to make design and product modications, which serve to improve the product.

3
Operating Instructions – Manual Flow Meter
Table of Contents
1. Introduction ________________________________________________________________________4
1.1. Preface ____________________________________________________________________________4
1.2. Obligations of the personnel ___________________________________________________________4
1.3. Symbols in this manual _______________________________________________________________4
1.3.1. Structure of the warning notes _________________________________________________________4
1.3.2. Hazard symbols _____________________________________________________________________5
1.3.3. General symbols _____________________________________________________________________5
2. Safety notes ________________________________________________________________________5
2.1. Authorized personnel_________________________________________________________________5
2.2. Intended conditions of use ____________________________________________________________6
2.3. Reasonably foreseeable misuse ________________________________________________________6
3. Risks involved in handling the manual ow meter and the uids to be used________________________6
4. Design and functional description ______________________________________________________7
4.1. LCD display _________________________________________________________________________8
4.2. User controls________________________________________________________________________8
4.3. Measuring chamber __________________________________________________________________9
4.4. Battery compartment_________________________________________________________________9
5. Technical data_______________________________________________________________________9
6. Assembly__________________________________________________________________________10
7. Installation ________________________________________________________________________10
8. Routine operation __________________________________________________________________10
8.1. Output of uid during standard operation (Normal Mode) __________________________________11
8.1.1. Resetting partial volumes ____________________________________________________________13
8.1.2. Resetting the resettable total volume (RESET TOTAL)_______________________________________12
8.2. Fluid delivery with display of current ow rate (Flow Rate Mode)_____________________________12
8.2.1. Resetting partial volumes ____________________________________________________________13
9. Calibration ________________________________________________________________________14
9.1. Denition _________________________________________________________________________14
9.2. Why calibrate? _____________________________________________________________________13
9.3. Calibration mode ___________________________________________________________________14
9.3.1. Displaying the valid calibration factor– resetting the factory calibration factor (if necessary) ______14
9.3.2. Calibration during simulated operation _________________________________________________16
9.3.3. Meter calibration during simulated operation ____________________________________________16
9.3.4. Changing the K FACTOR directly _______________________________________________________19
10. Conguration of the meter ___________________________________________________________21
11. Maintenance_______________________________________________________________________22
11.1. Replacing the batteries ______________________________________________________________22
11.2. Cleaning the measuring chamber ______________________________________________________23
12. Troubleshooting ___________________________________________________________________23
13. Repair/Service _____________________________________________________________________24
14. Disposal___________________________________________________________________________24
15. EC Declaration of Conformity _________________________________________________________25
16. Exploded view, manual ow meter _____________________________________________________26

4
Operating Instructions – Manual Flow Meter
1. Introduction
1.1. Preface
Please carefully read these operating instructions and observe in particular all safety notes!
Our sta will be pleased to provide support if you have any questions about the product.
Yours sincerely, FMT Swiss AG
1.2. Obligations of the personnel
Before they start to work, all persons who are entrusted with work with manual ow meter, are obliged:
– to follow all applicable regulations on occupational safety and accident prevention.
– to read and to comply with all safety instructions and warning notes contained in
these operating instructions.
Please observe the following instructions in the interest of all concerned:
■ Refrain from any unsafe working methods!
■ Adhere to all hazard and warning notes contained in this manual!
■ In addition to this documentation, keep to all generally accepted safety rules,
legal provisions as well as all other binding rules regarding occupational safety,
accident prevention and environmental protection!
■ Wear appropriate protective clothing in accordance with the work to be done!
■ Perform only work for which you have been suciently trained and instructed!
■ Only genuine spare parts as well as original tools and auxiliaries of the manufacturer are
allowed to be used in order to ensure the functional safety and maintain the warranty coverage.
1.3. Symbols in this manual
1.3.1. Structure of the warning notes
The warning notes have the following structure:
SIGNAL WORD
Type and source of the hazard
■ Consquences of non-compliance with the notes.
■ Measures to avoid that risk.
Depending on the danger level, dierent signal words are used:
Signal word Danger level
Consequences
of non-compliance
DANGER Imminent threat
of danger
Death or serious
bodily injury
WARNING Possible threat
of danger
Death or serious
bodily injury
CAUTION Possibly dangerous
situation
Minor bodily
injury
ATTENTION Possibly dangerous
situation
Damage to
material property
NOTE
Indicates further information or tips which facilitate work.

5
Operating Instructions – Manual Flow Meter
1.3.2. Hazard symbols
Symbol Meaning
General hazard symbol. The warning note marked in this way contains
supplementary information on the type of hazard.
This symbol warns of dangerous electrical voltages.
This symbol warns of a hazardous explosive atmosphere.
1.3.3. General symbols
Symbol Meaning
■A small black square indicates the work you have to perform.
–The dash denotes lists.
aThe arrow identies cross-references.
If cross-references to other chapters are required within the text, the expression is
shortened for reasons of clarity.
Example: aChapter 2 Safety notes.
This means: please refer to chapter 2 for the safety notes.
2. Safety notes
Various dangers may occur if the manual ow meter is improperly handled during installation, commis-
sioning and daily operation.
WARNING
Risk of injury and damage to material property because of improper
handling!
■ Hold the manual at the disposal of the operating sta at the usage site
of the unit.
■ Country-specic safety measures and accident prevention regulations
must be observed.
2.1. Authorized personnel
Only qualied and authorized persons are allowed to operate and to work on the oval gear meter.
Persons are qualied if they are, due to their training, experience, instruction and knowledge of the
relevant standards, able to assess assigned tasks and to identify potentially hazardous situations.
These persons must have been authorized by the person responsible for the safety of the unit and
must be able to identify and to avoid potential dangers.
All persons charged with installation, operation, maintenance and repair work, must have read and
understood this operation manual.
A copy of this operating manual must be stored permanently and ready at hand at the place of usage
of the unit.

6
Operating Instructions – Manual Flow Meter
2.2. Intended conditions of use
The manual ow meter was designed and constructed for the precise measurement and registration
of volumes of various media such as engine oils SAE 5 to 50 / gear oils SAE 80 to 240 (Item No. 19 698;
19698 950; 19698 95), antifreeze agents and radiator uids (Item No. 19 700).
The manual ow meter is intended for integration at the end of a discharge hose, e. g. a hose reel.
The user is liable for any damage resulting from non-intended use. The manual ow meter is only suita-
ble for use with ame retardant uids.
2.3. Reasonably foreseeable misuse
Any departure from the usage stipulations (other media, use of force) or user modications (changes,
use of non-original parts) can be dangerous and are considered as non-intended usage.
The use in the food industry is forbidden.
The manual ow meter must not be used in explosion risk areas.
Use only genuine replacement parts for repairs, because otherwise the warranty will be invalidated.
DANGER
Risk of injury and material damage from explosive vapours.
■ Never pump explosive uids such as gasoline or other uids
with similar ashpoints.
3. Risks involved in handling the manual ow meter
and the uids to be used
Improper use of engine and gear oils, antifreeze agents and radiator uids may constitute a risk to
humans and to the environment. Provide adequate ventilation and avoid splashing in the working area.
Do not allow leaking uids to enter drains or ground water. Local and country regulations relating to
domestic water supply must be obeyed.
DANGER
Use of engine and gear oils.
■ Engine and gear oils may cause lung damage if swallowed.
WARNING
Risk of slips and falls because of leaks.
■ In case of an excessive leakage, the manual ow meter must be immediately
stopped and the source of the leakage must be repaired.
CAUTION
■ Avoid skin and eye contact.
■ In case of contact with the eyes, rinse the eyes with plenty of drinking water
and consult a physician.
■ Use appropriate equipment such as protective gloves and goggles.
■ Keep the material data safety sheet at hand and adhere to it.

7
Operating Instructions – Manual Flow Meter
NOTE
■ Particular mention must be given to all local water protection regulations,
especially with regard to lling installations, which must be constructed, built,
maintained and operated in such a way, that any risk of water pollution and/or
any other environmental damage is excluded.
■ The operator of such an installation is responsible for continuously monitoring
the compliance with the above stated requirements at the place of installation.
4. Design and functional description
The manual ow meter is a liquid counter with an electronic register and a digital display.
The medium owing through the meter sets two oval gear wheels in rotation, whereby a Hall sensor
transmits pulses to the electronic register. By means of a calculation factor, these pulses are converted
into the actual ow volume which appears on the display.
The factor has been pre-set at the factory using an average that has turned out to be useful in normal
operation. However, this factor can be easily adapted to specic requirements by the user.
The volume ow can be started and stopped by means of the manually actuated valve built in
upstream of the meter. The anti-drop coupler behind the meter immediately stops the owing uid
and prevents any dripping.
The user needs only two membrane key switches for operation: RESET and TOTAL (total volume).
The electronic component is shockproof and sealed against the entry of oil. It meets the RFI and
EMI shock test conditions.
The electronic components and LCD display sit at the top of the oval gear meter, well insulated against
the wet measuring chamber. There is a cover to protect them against the working environment.
MEASURING
CHAMBER
RESET BUTTON
LCD DISPLAY
TOTAL BUTTON

8
Operating Instructions – Manual Flow Meter
4.1. LCD display
The meter‘s LCD display is equipped with two numeric registers and dierent types of display modes
showing information to the user only when it is actually needed with the operation / function going on
at the moment.
Key:
1. Register of partial volume (5 digits with oating decimal: 0.000+99999) showing the amount
of liquid that has been delivered since the RESET button was last pressed.
2. Battery charge.
3. Display of the calibration mode.
4. Register of total volume (6 digits with oating decimal 0.0-999999x10/x100) showing
two dierent kinds of total volumes:
4.1 Non-resettable total volume (TOTAL).
4.2 Resettable total volume (RESET TOTAL).
5. Total volume multiplication factor (x10/x100).
6. Type of total volume display (TOTAL/RESET TOTAL).
7. Units for total volume; L = litres; GAL= gallons.
8. Flow rate display.
9. Display of measuring unit for partial volumes:
QTS = quarters; PTS = pints; L = litres; GAL = gallons.
4.2. User controls
There are two push buttons on the meter (RESET and TOTAL), each controlling two main functions
(pressed individually) and various auxiliary sub-functions (pressed simultaneously).
Main functions:
■ RESET button: Resetting the partial volume register and the (resettable) total volume register
RESET TOTAL.
■ TOTAL button: Calling up the calibration mode. When pressed together, the two buttons call
up the conguration mode where you select the unit of measurement.

9
Operating Instructions – Manual Flow Meter
4.3. Measuring chamber
The measuring chamber is located in the centre of the meter.
There is a oval gear in the measuring chamber, set in rotation by the ow of liquid. Each revolution
will generate an electrical pulse that is processed by the microprocessor on the control circuit board.
The microprocessor uses a calibration factor (i.e. a‚weighting‘ assigned to each pulse) to convert the
pulses generated by the gears‘ revolutions into an intelligible value representing the volume of liquid
that has passed through. It is then displayed in the unit pre-set before in the corresponding registers
of the LCD display for partial and total volumes, respectively.
All of our oval gear meters leave the factory with a default calibration factor = 1000 called
„FACTORY K FACTOR“. There is a possibility to calibrate the meter in order to adapt that factor to the
physical properties of dierent liquids.
There is always a possibility to return to the manufacturer‘s default setting.
4.4. Battery compartment
The meter is powered by two 1.5 V standard batteries (N1).
The battery compartment is inside the body. Remove the screw plug
( achapter 15.1, pos. 4) to replace the batteries.
5. Technical data
Manual ow meter 19 698
19698 950
19698 951
19 700
Version non calibratable
Mechanical measuring components oval gears
Flow volume (l/min) 0 – 30 1 – 35
Typical uids engine oils SAE 5 to 50
gear oils SAE 80 to 240
radiator uids
antifreeze agents
Nominal pressure (bar) 70
Operating pressure min. (bar) 0,30 0,35
Temperature range (°C) -10 / +50
Viscosity (mPa s) 8 – 5000
Measuring tolerance (%) ± 0,5 %
Repeat accuracy ± 0,3 %
Display digital, three digits before and two digits
behind the decimal point
Digit height (mm) 8
Resolution (l) 0,002
Impulses (pulses/l) 46
Measuring unit quarters (QTS), pints (PTS), litres (L), gallons (GAL)
Batteries LR 1_1,5 V
Battery lifetime approx. 2 years in case of an operating time
of 0.5 hours a day (20 °C)
Connection thread G ½“ f
Material housing die-cast aluminium
Weight (kg) 1,92 / 1,68 / 1,65 1,92
Tab. 5-1 Technical data, manual ow meter

10
Operating Instructions – Manual Flow Meter
6. Assembly
The manual ow meter is supplied with assembly included.
According to the version, accessories may be or must be mounted.
NOTE
■ Ensure cleanliness during installation and an exact connection and accurate
sealing.
7. Installation
The inlet and outlet of the manual ow meter are aligned in a straight axis and are equipped with
a G 1/2“ thread. The meter may be installed in any given position, as a xed unit in a pipeline and/or
as a mobile unit on a spigot.
The manual ow meter does not have a pre-dened ow direction. Both ends may alternatively serve
as inlet or outlet, as needed. However, it is absolutely important that the side that is used as inlet
(where the pipeline arrives) is equipped with a lter with suitable performance characteristics. Solid
particles getting into the measuring chamber might clog up the ovar gear.
8. Routine operation
The manual ow meter is supplied ready for use.
Even after periods of prolonged storage, it will be ready for operation without any lengthy preparations.
The only action that may be necessary from time to time during normal operation is to reset the registers
of partial and/or resettable total volumes.
To accomplish that, call up the two displays for normal operation. The rst normal operation display
contains the partial volume and resettable total volume (RESET TOTAL). The other display shows the
partial volume and the non-resettable (absolute) TOTAL volume. The LCD automatically switches between
resettable and absolute total in a given period of time. This has been set at the factory and cannot be
inuenced by the user.
RESETTABLE
TOTAL VOLUME
register
ABSOLUTE
VOLUME
register
PARTIAL VOLUME register
The register of the absolute total (TOTAL) cannot be reset by the user. It will continue counting during the
entire lifetime of the meter. The resettable and non-resettable registers of total volumes (RESET TOTAL and
TOTAL) share the same‚window‘ and the same digits of the LCD display. For that reason, the two numbers
cannot be viewed at the same time but are always shown alternately in the display.
The oval gear meter has been programmed so that the one or the other total is visible at certain
moments / in certain modes during operation:
■ The absolute total volume (TOTAL) is visible in standby mode.
■ The resettable total (RESET TOTAL) is visible at the following times / in the following modes:
- For a short moment (several seconds) after resetting the (resettable) partial volume.
- During uid delivery.
A few seconds after uid delivery, this short time span expires and the meter switches to standby mode.
The display of the bottom register shows the absolute total volume.

11
Operating Instructions – Manual Flow Meter
NOTE
For the display of total volumes, there are 6 digits available, plus two icons x10/x100. The
increments are activated in the following sequence:
0,0 ---> 99999,9 ---> 999999 ---> 100000 x10 ---> 999999 x10 ---> 100000 x100 --->
999999 x100
8.1. Output of uid during standard operation (Normal Mode)
During standard output of liquid, the meter will count and at the same time display the volume having
gone through the device so far, and the resettable total (RESET TOTAL).
Accidental pressing of the RESET or TOTAL button does not have any eect
in this state.
A few seconds after uid delivery, the display of the lower register will change from resettable total to
absolute total: The word RESET above the word TOTAL will disappear, and the value of the resettable total
will be replaced by the absolute total.
We call this state (or mode)„standby“. It will persist as long as the user does not carry out any more
actions on the meter.
8.1.1 Resetting partial volumes
For resetting the partial volume register: Press the RESET button
while the meter is in standby, i.e. when you see the word TOTAL in
the display.
When you press RESET, the display will rst switch on all the
segments, one after the other, and then switch them all o again.
When the reset is complete, the display will rst show the partial
volume having been reset and then RESET TOTAL.
After a couple of seconds, RESET TOTAL will be replaced by the
NON-resettable total amount TOTAL.

12
Operating Instructions – Manual Flow Meter
8.1.2. Resetting the resettable total volume (RESET TOTAL)
You can reset the resettable total only if you have reset the
register of the partial volumes before. To reset the resettable total:
press RESET for several seconds. The display will show the words
RESET TOTAL (see g.):
You must carry out the following steps (in this order):
1. Wait until the display is back to default standby mode
(i.e. showing only TOTAL).
2. Press RESET shortly.
3. The meter will now start resetting the partial volume register.
4. While the display shows RESET TOTAL, shortly press RESET.
5. The display will show all the segments again. Only then follows
the phase where all segments are switched o. Finally, there
will be a display showing the total that has been reset
(RESET TOTAL).
8.2. Fluid delivery with display of current ow rate (Flow Rate Mode)
It is possible to output a liquid and have the following displays available at the same time:
■ Partial volumes having been output.
■ Current ow rate (Flow Rate) in [unit of partial volume per min.], as shown below.
This is how you get into this mode:
■ Wait until the meter is in default standby mode (i.e. the display shows only the total volume).
■ Press TOTAL shortly.
■ Start output operation.
The display of the current ow rate will be updated every 0.7 secs. For that reason the display
may‚utter‘ somewhat with low ow rates. However, the higher the ow rate, the more stable the
display will be.
NOTE
The current ow rate will be shown in the unit set for the partial volume register.
That means if partial and total volume have been set to dierent units (as shown in
the example below) you must bear in mind that the ow rate shown is in the unit
set for partial volumes. In the example shown, the ow rate is in L./min.
The word L next to the ow rate refers to the register of the (resettable and NON-resettable) total volumes
which will be displayed again as soon as you leave the‚current ow rate‘ display mode. In order to go back
to the default standby mode, press the TOTAL button again. Accidental pressing of the RESET or TOTAL
button does not have any eect in this state.

13
Operating Instructions – Manual Flow Meter
NOTE
RESET TOTAL and absolute total (TOTAL) are not shown in this mode. However,
the values nevertheless go up. You can check after uid discharge. Wait for the
default standby mode and press TOTAL shortly.
8.2.1. Resetting partial volumes
In order to reset the partial volume register, you must rst complete the output of liquid. Wait until the
display shows a ow rate of 0.0 (see g.) and then press RESET shortly.
The eect is dierent from what you would have if you press Reset in default standby mode. There is no
phase where all the segments are rst switched on and then o again. Instead, the register will display the
reset partial volume immediately.
9. Calibration
9.1. Denition
Calibration factor or„K FACTOR“:
This is the multiplication factor the system ascribes to the electronic pulses it receives in order to convert
them into a plain unit of measurement.
■ FACTORY K FACTOR: Calibration (default) factor pre-set at the factory.
Factory K Factor = 1000.
This calibration factor ensures maximum precision under the following operating conditions:
Fluid Oils Antifreeze agents /
radiator uids
Flow rate 0-30 l/min 1-35 l/min
You can always return to the original Factory K Factor even after you have changed the value.
The procedure is simple.
■ USER K FACTOR: This is the calibration factor the user has set to adapt the meter to specic
requirements (i.e. the user has carried out a calibration procedure).
9.2. Why calibrate?
The manual ow meter is delivered with a setting made by the manufacturer. In most operating
conditions, this setting will ensure a precise measurement.
If a calibration is necessary, it should be conducted under the operating conditions in
which the meter is used, such as in the following extreme conditions:
■ Fluids having a viscosity close to the admissible limits (e.g. antifreeze with low viscosity,
high-viscosity oils for gearboxes).
■ Extreme ow rates (i.e. close to upper or lower limits).

14
Operating Instructions – Manual Flow Meter
9.3. Calibration mode
The manual ow meter oers the possibility to carry out a quick and precise electronic calibration by
changing the calibration factor ( K FACTOR).
There are two calibration procedures you may choose from:
■ Calibration during simulated operation (requiring actual output of liquid to be carried out).
■ Direct calibration (simply changing the calibration factor).
By briey pressing the TOTAL button > FLOW RATE screen, and subsequently pressing the RESET and
TOTAL buttons for a longer time, the calibration process can be called up for the following reasons:
■ To display the valid calibration factor.
■ To reset the calibration factor pre-set at the factory (FACTORY K FACTOR) after calibration by the user.
■ To change the calibration factor using one of the two available calibration procedures.
During calibration, the registers on the LCD display - that normally show partial and total volumes
of liquid output – will take on new meanings.
During calibration, the meter cannot carry out normal output operation.
During calibration, the count of the absolute total volume of liquid having been output
(non-resettable total) will not increase.
NOTE
The manual ow meter is equipped with a non-volatile memory which ensures
that the saved calibration and total discharge amount data are retained over an
extended period, even without power supply. After battery replacement, a new
calibration is not necessary.
9.3.1. Displaying the valid calibration factor– resetting the factory calibration factor
(if necessary)
By briey pressing the TOTAL button > FLOW RATE screen, and subsequently pressing the
RESET and TOTAL buttons for a longer time, the calibration process can be called up for the
following reasons:
Two situations are possible:
a) User never changed the calibration factor and/or user restored the factory calibration factor
after changing it: the display will show the following:
The word FACT (short for FACTORY) indicates that the valid calibration factor is the factor pre-set
at the factory.
b) If calibrations have been made by the user, the calibration value currently used is indicated
(in our example 0,998).
The word USER indicates that the calibration factor currently used was entered by the user.
The ow chart below shows the schematics of the display modes the LCD display may go through.
In this mode, the user may press RESET and thus change from the USER to the FACTORY FACTOR.

15
Operating Instructions – Manual Flow Meter
In order to conrm your choice, shortly press TOTAL while the display shows either
USER or FACT.
After re-start, the meter will use the new calibration factor you just conrmed.
NOTE
When you conrm restoration of the Factory K Factor, the old user factor will be
deleted from memory.
Standby
Standby
RESET long
KEY
RESET short
TOTAL long
TOTAL short
Time OL 1

16
Operating Instructions – Manual Flow Meter
9.3.2. Calibration during simulated operation
This procedure is basically a simulated output of liquid into a calibration vessel under actual operating
conditions (ow rate, viscosity etc.). The procedure must be carried out with utmost care.
NOTE
Absolutely bear in mind the following points in order to guarantee proper
calibration:
■ Have your equipment properly vented before calibration.
■ Use a calibrated vessel holding at least 5 litres with a precise full mark.
■ For calibration, tap a certain amount of test liquid with a constant ow rate,
exactly as you would do in normal operation. Continue until the vessel is full.
■ Do not decrease the ow rate when you approach the full mark. Instead, turn
the spigot on and o and ll the vessel in small batches, but make sure the ow
rate remains unchanged.
■ When you are nished be sure to wait a few minutes and let air bubbles escape
that may still be in the calibration vessel. Otherwise there is a danger you get a
wrong value because the level in the vessel may still go down.
■ Be sure to carry out the following procedure correctly.
9.3.3. Meter calibration during simulated operation
Operation Display conguration
1
2
NONE
Meter is in default standby mode, not counting.
SHORT PRESS OF THE TOTAL BUTTON
The meter changes to the FLOW RATE screen.
3LONG PRESS OF THE RESET AND TOTAL BUTTONS
Meter switches to calibration mode, displaying TOTAL.
Display no longer shows total volume, but instead the valid
calibration factor. FACT and USER indicate whether valid
calibration factor is FACTORY K FACTOR or USER K FACTOR.
4 PRESS RESET SEVERAL SECS
Meter shows TOTAL display and the resettable total register
displays zeroes. Meter is now ready for simulated operation
calibration.

17
Operating Instructions – Manual Flow Meter
5 FILL LIQUID INTO CAL VESSEL
Start simulated operation, but do not press any
buttons yet.
Simulated operation may be interrupted and continued
as necessary. Continue lling the vessel until full mark
is reached. It is not necessary to top out at any specic
value.
Set value Actual value
6 PRESS RESET SHORTLY
This is how the meter‚knows‘ that sim op for calibration
is complete. Make sure cal vessel has really been lled
up to full mark before you do this.
For calibration you must correct the count indicated
by the partial volume register (ex.: 9,800), entering the
actual value, i.e. the volume of the cal vessel. An arrow
at the bottom left of the display (pointing up or down)
indicates the direction in which USER K FACTOR is
changed. Increase or decrease when actions 6 or 7 are
carried out.
7 PRESS RESET SHORTLY
Direction of arrow ips. This may be repeated as
often as necessary.

18
Operating Instructions – Manual Flow Meter
8 PRESS TOTAL SHORTLY / SEVERAL SECS
Value indicated will change as indicated by arrow:
■ One increment per each time TOTAL is pressed.
■ Continuous if the TOTAL button is held down,
the rst 5 increments slow, then fast.
■ If you overshoot, go back to point 6 and
repeat (6).
9 LONG PRESS OF THE RESET BUTTON
This is how the meter‚knows‘ that calibration is now
complete.
Before you press the button, be absolutely sure the
display shows the correct value (volume of vessel).
Actual valueSet value
The meter will now calculate the new USER K FACTOR:
This may take a couple of seconds depending on the
complexity of the correction. The arrow will disappear
during this phase, but the word TOTAL will remain
unchanged.
If you carry out this action right after point 5 the new
USER K FACTOR will be equal to the FACTORY K FACTOR.
It will be ignored, therefore.
10 NO OPERATION
After completion of the calculation the new USER K
FACTOR will be displayed a few seconds. Next, the meter
will re-start. Finally, the meter will be back in default
standby mode.
PLEASE NOTE: From now on, the new value set will be
used as the new valid K Factor and will remain even after
replacement of batteries!
11 NO OPERATION
The meter stores the new K Factor for operation
and is now ready for operation using the newly set
USER K FACTOR.

19
Operating Instructions – Manual Flow Meter
9.3.4. Changing the K FACTOR directly
This procedure is helpful for the correction of a mean error that may occur as a result of many output
operations. In the event you observe a mean percentage error during normal meter operation you may
carry out a correction by changing the valid User K Factor by that percentage. In order to calculate the
correction of the USER K FACTOR, proceed as follows:
New calibration factor = old calibration factor x
Example:
Observed mean percentage error E % -0,9 %
Current K Factor 1.000
New USER K FACTOR 1.000 x 100-(-0,9)÷100=
1.000 x (100+0,9)÷100=
1.009
If the meter displays less than the actual amount of liquid output (negative error), the new K Factor must
be greater than the old one (see example). The opposite is true if the value indicated is greater than the
actual amount (positive error).
Operation Display conguration
1 NO
Meter is in default standby mode, not counting.
2SHORT PRESS OF THE TOTAL BUTTON
The meter changes to the FLOW RATE screen.
3LONG PRESS OF THE RESET AND TOTAL BUTTONS
The meter changes to the calibration mode, the word
TOTAL is displayed, and the calibration factor used is
displayed instead of the total volume. The messages
FACT and USER indicate which one of the two factors
(manufacturer or user) is currently being used.
4 LONG PRESS OF THE RESET BUTTON
The meter shows TOTAL display and the resettable
total register displays zeroes.
The meter is now ready for simulated operation
calibration.

20
Operating Instructions – Manual Flow Meter
5 LONG PRESS OF THE RESET BUTTON
Changing valid K Factor directly: The word DIRECT is
displayed, together with the calibration factor currently
in use. An arrow at the bottom left of the display
(pointing up or down) indicates the direction in which
the displayed value is changed. Increase or decrease
when actions 5 or 6 are carried out.
6 PRESS RESET SHORTLY
Direction of arrow ips. This may be repeated as often
as necessary in order to set the correct direction.
7 SHORT / LONG PRESS OF THE TOTAL BUTTON
Value indicated will change as indicated by arrow:
■ One increment per each time TOTAL is pressed.
■ Continuously if TOTAL is held down. Display will‚roll‘
more quickly if button is held permanently.
If you overshoot, go back to point 5 and repeat.
8 LONG PRESS OF THE RESET BUTTON
This is how the meter‚knows‘ that calibration is now
complete.
Before you press this button, be absolutely sure the
value indicated is the value you wanted to set.
9 NO OPERATION
After the following calculation the new USER K FACTOR will
be displayed a few secs. Next, the meter will re-start. Finally,
the meter will be back in default standby mode.
PLEASE NOTE: From now on, the new value set will be
used as the new valid K Factor and will remain even after
replacement of batteries!
10 NO OPERATION
The meter stores the new K Factor for operation and
is now ready for actual operation using the newly set
USER K FACTOR.
This manual suits for next models
5
Table of contents
Other FMT Swiss AG Measuring Instrument manuals
Popular Measuring Instrument manuals by other brands
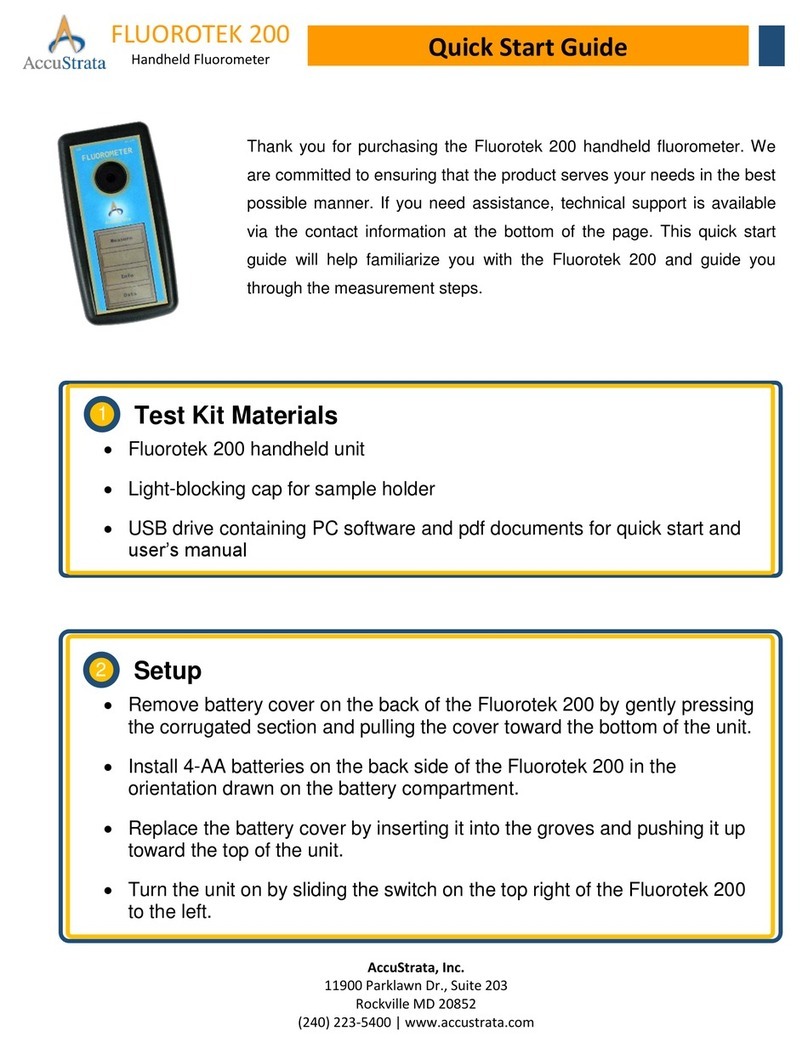
AccuStrata
AccuStrata FLUOROTEK 200 quick start guide
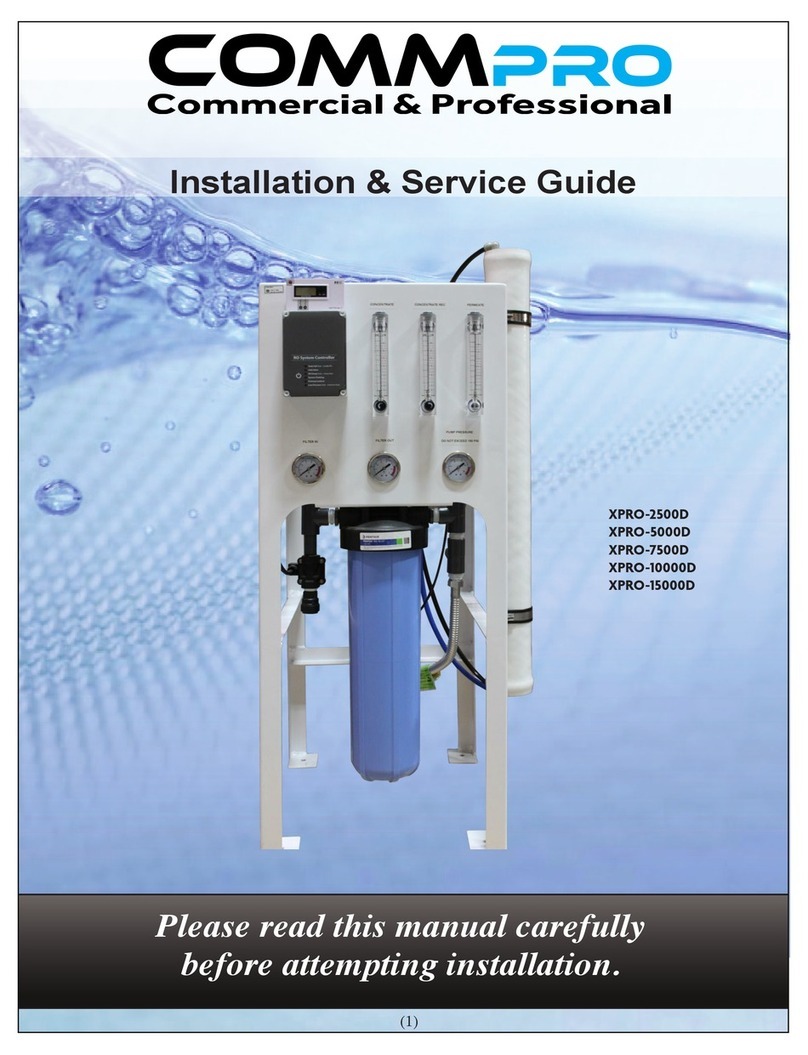
HM Digital
HM Digital CommPro Series Installation & service guide
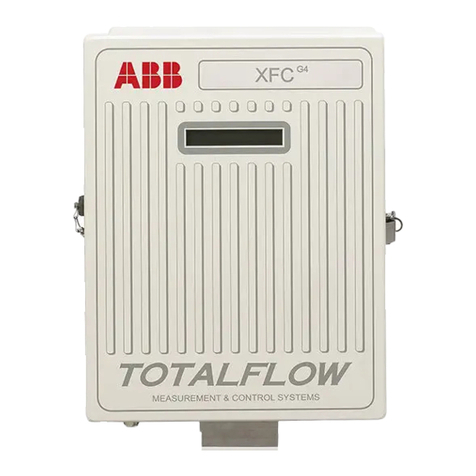
ABB
ABB TOTALFLOW X G4 Series Startup guide
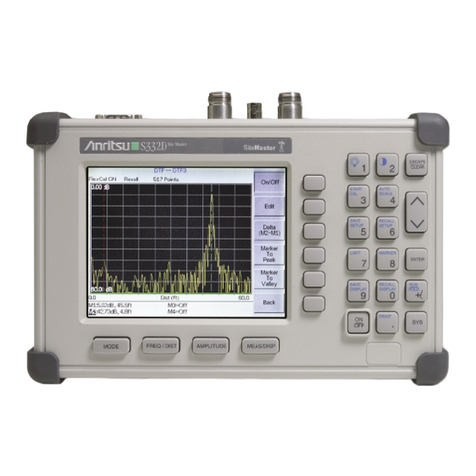
Anritsu
Anritsu Site Master S331D Programming manual
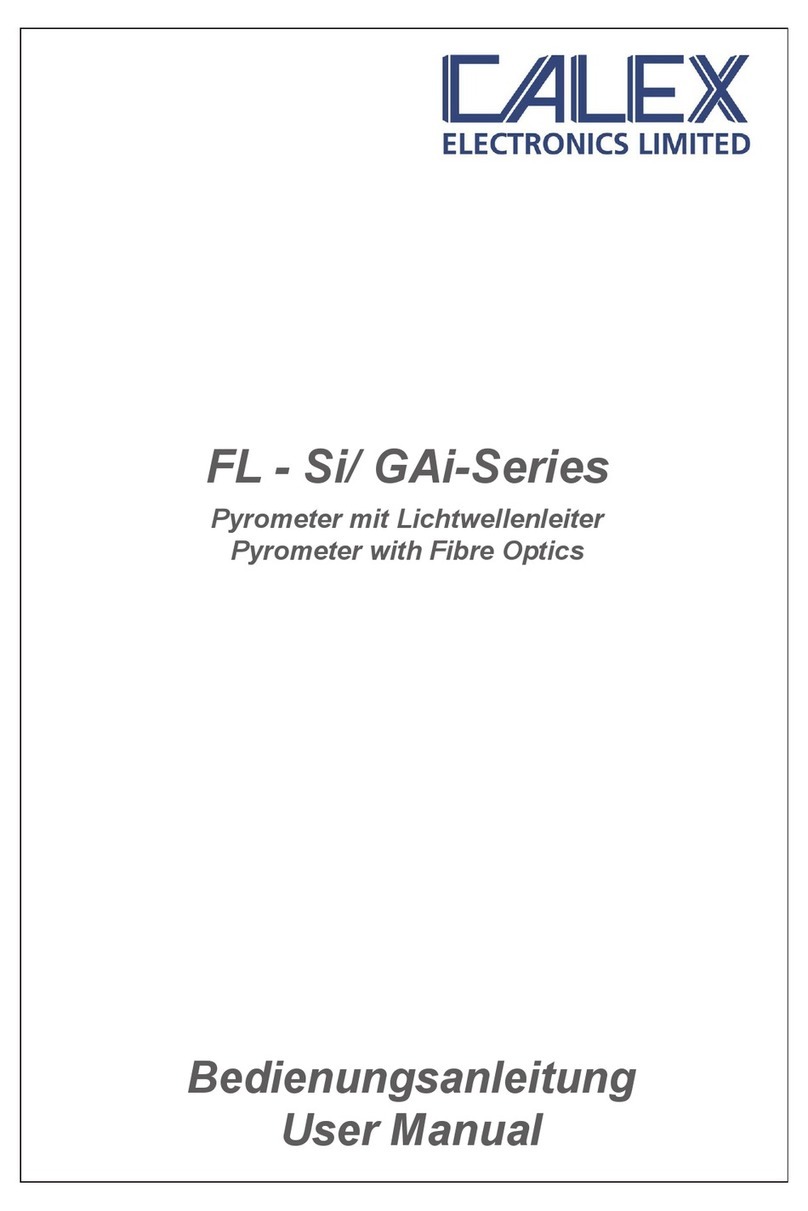
Calex
Calex FL - Si Series user manual
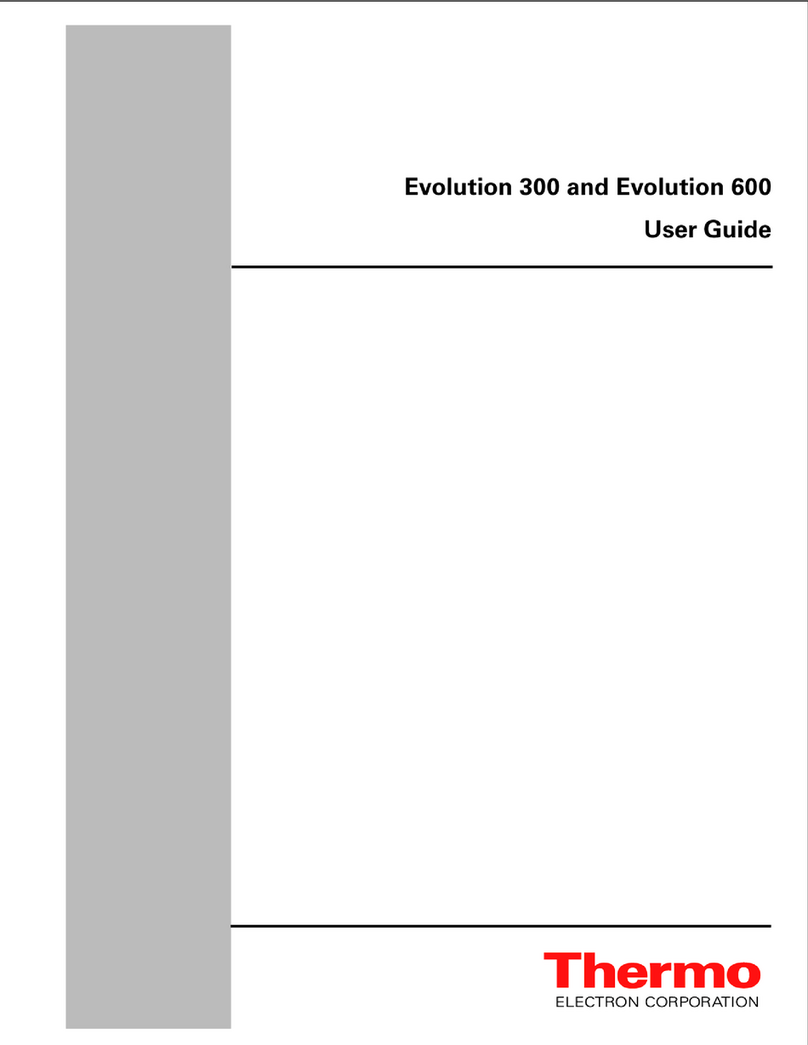
Thermo Electron
Thermo Electron Evolution 300 user guide