Galletti LCX Series User manual

LCX
Installation, use and maintenance manual
COOLING-ONLY, HEAT PUMP AND FREE-COOLING
VERSIONS
USER MANUAL

LCX
RG66010687_rev.00 2
For further information or communication, please contact the company at: [email protected]
To find out the weight of each unit, please refer to the table in the paragraph “Rated
specifications”

LCX
RG66010687_rev.00 3
CONTENTS
PAGE
1THE SERIES 6
2FIELD OF APPLICATION 8
3GENERAL INFORMATION 8
4INSPECTION, CONVEYANCE, SITING 10
4.1 INSPECTION 10
4.2 LIFTING AND CONVEYANCE 10
4.3 UNPACKING 11
4.4 SITING 11
5INSTALLATION 12
5.1 INSTALLATION CLEARANCE REQUIREMENTS 12
5.2 GENERAL GUIDELINES FOR PLUMBING CONNECTIONS 13
5.3 WATER CONNECTION TO THE EVAPORATOR 15
5.4 PROCEDURE FOR FILLING THE TANK 16
5.5 SAFETY DEVICES ON THE HIGH-PRESSURE SIDE 17
6ELECTRICAL CONNECTIONS 17
6.1 GENERAL INFORMATION 17
6.2 FLOW SWITCH ON THE WATER SIDE 18
6.3 ELECTRIC CONNECTIONS OF THE CIRCULATION PUMP 18
6.4 REMOTE CONTROLS 19
6.5 REMOTE SUMMER-WINTER SWITCHING 19
7START-UP 21
7.1 PRELIMINARY CHECKS 21
7.2 STARTING OPERATIONS 22
7.3 CHECKS DURING OPERATION 23
7.4 CHECKING THE REFRIGERANT LEVEL 23
7.5 EXPANSION VALVE 24
7.6 STOPPING THE UNIT 25
8OPERATING LIMITS 25
8.1 WATER FLOW TO EVAPORATOR 29
8.2 CHILLED WATER TEMPERATURE 29
8.3 EXTERNAL AIR TEMPERATURE 29
8.4 OPERATION WITH WATER AT LOW TEMPERATURES 29
9SETTING OPERATING PARAMETERS 29
9.1 GENERAL INFORMATION 29
9.2 MAXIMUM PRESSURE SWITCH 32
9.3 MINIMUM PRESSURE SWITCH 32

LCX
RG66010687_rev.00 4
9.4 SERVICE THERMOSTAT 32
9.5 ANTIFREEZE THERMOSTAT 32
9.6 ANTI-RECYCLE TIMER 32
9.7 OIL DIFFERENTIAL PRESSURE SWITCH 32
10 ROUTINE MAINTENANCE AND CHECKS 33
10.1 WARNINGS 33
10.2 GENERAL INFORMATION 34
10.3 REPAIRING THE COOLING CIRCUIT 34
10.4 TIGHTNESS TEST 34
10.5 HARD VACUUM AND DRYING OF THE COOLING CIRCUIT 35
10.6 CHARGING WITH R410A REFRIGERANT 35
10.7 ENVIRONMENTAL PROTECTION 36
11 DECOMMISSIONING THE UNIT 36
12 TROUBLESHOOTING 37
13 WATER PRESSURE DROPS 41
13.1 PRESSURE DROPS IN EVAPORATOR 41
13.2 PRESSURE DROPS IN HEAT RECUPERATOR 41
13.3 PRESSURE DROPS IN FREE-COOLING FINNED PACK HEAT EXCHANGERS 41
14 TECHNICAL DATA SUMMARY 42
15 DIMENSIONAL DRAWINGS 54
16 SUMMARY TABLE OF WEIGHTS 61
16.1 TOTAL STD WEIGHTS 66
16.2 WEIGHT OF HYDRONIC MODULES C-H-F 68
16.3 PUMPING AND STORAGE SYSTEMS 72

LCX
RG66010687_rev.00 5
Declaration of conformity
The declaration of conformity is enclosed as a separate document with the papers supplied with the
machine, usually placed inside the electric control board.

LCX
RG66010687_rev.00 6
1 THE SERIES
COOLING-ONLY and HEAT PUMP
Fluid chillers and heat pumps designed to cool water or mixtures of water and an antifreeze agent,
intended for civil air-conditioning and industrial cooling systems. LCX chillers, available in versions with
different acoustic designs (“S”, “L”, “Q”) and cooling circuit architectures (Efficiency pack 1, 2 , 4), they
cover a range of cooling capacities from 44.4 to 355 kW, calculated with reference to standard test
conditions of water 12°/7° - air entering the finned block heat exchangers 35°C.
Example of product code composition:
Configurations: Chiller - cooling only “C”
Heat pump “H”
Versions: Standard version “S”
Low-noise version – for a low-noise impact “L”
Quiet version - for an extremely low-noise impact “Q”
Efficiency Packs: Efficiency pack 11 compressor per circuit
Efficiency pack 22 tandem compressors on 1 circuit
Efficiency pack 42tandem compressors on 2 circuits
Configurations
Efficiency Pack
Versions
Heat
Pump
H
E.P.
4
E.P.
2 E.P.
1
Quiet
Q
Low
Noise
L
Std.
S
Chiller
C
LCX
R-
410A
configuration
Size + eff.
p
ac
k
version
Full name of the machine L C
X
HQ
Commercial name L C X
Model
Operation H
chiller C
heat pump H
Version Q
standard S
low noise L
Quit Q
104
104

LCX
RG66010687_rev.00 7
Below is a list of all possible models, broken down by efficiency pack :
efficiency pack 1 efficiency pack 2 efficiency pack 4 Indicative cooling
capacity of the
“cooling-only”
version [kW]
- LCX042CL/CQ - 48
- LCX042HL/HQ - 48
- LCX052CL/CQ - 53
- LCX052HL/HQ - 53
- LCX062CS/CL/CQ - 63
- LCX062HS/HL/HQ - 63
- LCX072CS/CL/CQ - 70
- LCX072HS/HL/HQ - 70
- LCX082CS/CL/CQ - 77
- LCX082HS/HL/HQ - 77
LCX091CS/CL/CQ LCX092CS/CL/CQ LCX094CL/CQ 92
LCX091HS/HL/HQ LCX092HS/HL/HQ LCX094HL/HQ 92
LCX101CS/CL/CQ LCX102CS/CL/CQ LCX104CL/CQ 103
LCX101HS/HL/HQ LCX102HS/HL/HQ LCX104HL/HQ 103
LCX121CS/CL/CQ LCX122CS/CL/CQ LCX124CS/CL/CQ 125
LCX121HS/HL/HQ LCX122HS/HL/HQ LCX124HS/HL/HQ 125
LCX141CS/CL/CQ LCX142CS/CL/CQ LCX144CS/CL/CQ 138
LCX141HS/HL/HQ LCX142HS/HL/HQ LCX144HS/HL/HQ 138
LCX161CS/CL/CQ LCX162CS/CL/CQ LCX164CS/CL/CQ 155
LCX161HS/HL/HQ LCX162HS/HL/HQ LCX164HS/HL/HQ 155
- - LCX174CS 162
- - LCX174HS 162
- - LCX194CS/CL/CQ 187
- - LCX194HS/HL/HQ 187
- - LCX214CS/CL/CQ 209
- - LCX214HS/HL/HQ 209
- - LCX244CS/CL/CQ 237
- - LCX244HS/HL/HQ 237
- - LCX274CS/CL/CQ 271
- - LCX274HS/HL/HQ 271
- - LCX294CS/CL/CQ 296
- - LCX294HS/HL/HQ 296
- - LCX324CS/CL/CQ 314
- - LCX324HS/HL/HQ 314
- - LCX364CS/CL 355
- - LCX364HS 355
FREE-COOLING
Fluid chillers with Free-Cooling exchange designed to cool water or mixtures of water and an antifreeze
agent, intended for civil air-conditioning and industrial cooling systems. LCX chillers, available in versions
with different acoustic designs (“S”, “L”) and cooling circuit architectures (Efficiency pack 1, 4), they cover
a range of cooling capacities from 44 to 355 kW, calculated with reference to standard test conditions of
water 12°/7° - air entering the finned block heat exchangers 35°C and Free-Cooling operating conditions
with an air temperature of +5°C and a temperature differential of the finned block heat exchangers of
15°/12°C.
Configurations: Chiller Free-Cooling “F”
Versions: Standard version “S”
Low-noise version – for a low-noise impact “L”
Efficiency Packs: Efficiency pack 11 compressor per circuit
Efficiency pack 42tandem compressors on 2 circuits

LCX
RG66010687_rev.00 8
Below is a list of all possible models, broken down by efficiency pack:
efficiency pack 1 efficiency pack 4 Indicative cooling
capacity of the
“cooling-only”
version [kW]
LCX041FS/FL - 49
LCX051FS/FL - 56
LCX061FS/FL - 64
LCX071FS/FL - 72
LCX081FS/FL - 81
LCX091FS/FL - 93
LCX101FS/FL - 105
- LCX124FS/FL 125
- LCX144FS/FL 139
- LCX164FS/FL 160
- LCX194FS/FL 191
- LCX214FS/FL 213
- LCX244FS/FL 240
- LCX274FS/FL 270
- LCX294FS/FL 295
- LCX324FS/FL 314
- LCX364FS 355
2 FIELD OF APPLICATION
These machines are intended for cooling-heating water and glycol solutions up to a maximum of 35% the
weight, in civil, industrial and technological air-conditioning environments.
Their use is recommended within the functioning limits carried in this manual, or else the warranty
attached to the sales contract would cease.
3 GENERAL INFORMATION
- When installing or servicing the chiller, you must strictly follow the rules provided in this manual, comply
with the directions on the units and take all such precautions as are necessary.
- The fluids under pressure in the cooling circuit and the presence of electrical components may cause
hazardous situations during installation and maintenance work.
Configurations
Efficiency Pack Versions
E.P.
4
E.P.
1
Low
Noise
L
Std.
S
Chiller
F
LCX
F

LCX
RG66010687_rev.00 9
Therefore only qualified personnel may perform any kind of work on the unit.
-THE UNIT MUST BE STARTED UP FOR THE FIRST TIME EXCLUSIVELY BY QUALIFIED
PERSONNEL AUTHORISED BY GALLETTI S.P.A. (SEE ANNEX).
-FAILURE TO COMPLY WITH THE RULES PROVIDED IN THIS MANUAL OR ANY MODIFICATION MADE
TO THE UNIT WITHOUT PRIOR AUTHORISATION WILL RESULT IN THE IMMEDIATE INVALIDATION OF
THE WARRANTY.
Attention: Before performing any kind of work on the unit, make sure it has been
disconnected from the power supply.

LCX
RG66010687_rev.00 10
4 INSPECTION, CONVEYANCE, SITING
4.1 INSPECTION
Upon receiving the unit, check that it is perfectly intact: the chiller left the factory in perfect conditions;
immediately report any signs of damage to the carrier and note them on the Delivery Slip before signing
it. Check, in particular, that the fins of the finned block heat exchangers are not bent and have not
undergone impacts that may have impaired the system's tightness under pressure.
The manufacturer or its agent must be promptly notified of the entity of the damage.
The Customer must submit a written report describing every significant sign of damage.
-commissioning report,
-wiring diagram,
-warranty certificate and list of authorised service centres,
-check the integrity of the documents accompanying the unit and of this manual.
4.2 LIFTING AND CONVEYANCE
While the unit is being unloaded and positioned, utmost care must be taken to avoid abrupt or violent
movements. The unit must be handled carefully and gently: avoid using machine components as
anchorages when lifting or moving it.
The unit should be lifted using Ø1½” GAS steel
pipes at least 3mm thick, to be inserted in the round
holes provided on the base side members (see fig.
below) and identified by means of stickers. The
pipes, which should protrude by at least 250-
300mm on every side, must be slung with ropes of
equal length secured to the lifting hook (provide
stops at the ends of the pipes to prevent the ropes
from slipping off due to the weight).
Use ropes or belts long enough to extend beyond the height of the unit and place spacer bars and
boards on the top of the unit to avoid damaging the sides and top of the unit itself. The rectangular holes
are provided for the attachment of vibration damping supports (optional).
Attention: In all lifting operations make sure that the unit is securely anchored in
order to prevent accidental falls or overturning.

LCX
RG66010687_rev.00 11
4.3 UNPACKING
The packaging must be carefully removed to avoid the risk of damaging the unit. The packaging includes
various materials: wood, cardboard, nylon, etc.
It is recommended to keep them separately and deliver them to suitable waste disposal or recycling
facilities in order to minimise their environmental impact.
Attention: if the unit is supplied with a pump or pumps and/or tank, you will find the expansion tank
packaged in the fan compartment; it must be fixed to the pump intake pipe, where a “TEE” is fixed so as
to form a tight seal, or on the tank itself. Remove the cap and screw in the expansion tank (this should be
done by qualified personnel), check the pre-fill pressure (0.5 - 1.0 bars-r) before filling the water circuit
and starting up the chiller.
Attention: the size of the expansion tank will depend both on the volume of water contained in the
system and the water temperature range; always check the tank capacity in relation to the water content
of the system.
4.4 SITING
You should bear in mind the following aspects when choosing the best site for installing the unit and the
relative connections:
- size and origin of water pipes;
- location of power supply;
- accessibility for maintenance or repairs;
- solidity of the supporting surface;
- ventilation of the air-cooled condenser and necessary clearance;
- direction of prevalent winds: avoid positioning the unit in such a way that the prevalent winds favour the
backflow of air to the condenser coils; a speed of 8 m/s (28.8 km/h) already generates a sufficient
stagnation pressure to guarantee approx. 60% of the nominal air flow rate.[In situations where the
action of air currents is inevitable and there is a simultaneous presence of temperatures below – 5°C,
the control of condensation for low outdoor temperatures must be of the flooding type or with a device
for choking the condensing exchanger -contact the technical department for further details]
- possible reverberation of sound waves.
All models belonging to the LCX series are designed and built for outdoor installation: avoid covering
them with roof structures or positioning them near plants (even if they only partly cover the unit) which
may interfere with the regular ventilation of the unit condenser.
It is a good idea to create a base of adequate dimensions to support the unit. This precaution becomes
essential when the unit is to be sited on unstable ground (various types of soil, gardens, etc.).
We recommend placing a rigid rubber strip between the base frame and the supporting surface.
Whenever more effective insulation is required, it is recommended to use vibration-damping rubber or
spring supports (ref. par. 16).
In the case of installation on roofs or intermediate storeys, the unit and pipes must be insulated from
walls and ceilings by placing rigid rubber joints in between and using supports that are not rigidly
anchored to the walls.
If the unit is to be installed in proximity to private offices, bedrooms or areas where noise levels must be
kept down, it is advisable to conduct a thorough analysis of the sound field generated and verify its
compatibility with the local laws in force.

LCX
RG66010687_rev.00 12
5 INSTALLATION
5.1 INSTALLATION CLEARANCE REQUIREMENTS
It is of fundamental importance to ensure an adequate volume of air both on the intake and outlet sides
of the finned condenser coils; it is highly important to prevent the air delivered from being re-aspirated as
this may impair the performance of the unit or even cause an interruption of normal operation. For this
reason it is necessary to guarantee the following clearances (see figure on this page):
- rear side/plumbing connections: min. 1.0 metre to guarantee access to plumbing connections and/or for
any necessary maintenance on the pumps, tank, expansion tank, flow switch and 3-way free-cooling
valve.
- electric control board side: min. 1.0 metre to guarantee access for inspection and/or maintenance of
cooling components.
- finned pack heat exchanger side: min. 1.5 metres to ensure proper air circulation and access to the
compressor compartment, also from the side.
- top side: there must be no obstacle to expulsion.
Top view of the unit
1.0 m
rear
1.0 m
front
1.5 m
1.5 m

LCX
RG66010687_rev.00 13
5.2 GENERAL GUIDELINES FOR PLUMBING CONNECTIONS
When you are getting ready to set up the water circuit for the evaporator you should follow the directions
below and in any case make sure you comply with national or local regulations (use the diagrams
included in this manual as your reference).
- Connect the pipes to the chiller using flexible couplings to prevent the transmission of vibrations and to
compensate for thermal expansions. These units are all configured for installation of the water inlet-
outlet pipes outside the unit (on the rear) and these pipes are supplied as a standard accessory at no
extra cost for the customer.
- Install the following components on the piping:
pair of quick-connection couplings with pipe section to be welded (optional item that may be
selected from the price list). They facilitate the connecting operations to the plumbing system,
greatly speeding up installation.
temperature and pressure indicators for routine maintenance and monitoring of the unit. Pressure
control on the water side allows to assess the correct functioning of the expansion tank and to detect
water leakage in advance.
sumps on inlet and outlet piping for temperature detection, for a direct view of operating
temperatures. They can also be consulted on the microprocessor on board the unit.
cut-off valves (gate valves) to isolate the unit from the hydraulic circuit.
metal net filter compulsory (inlet piping) with mesh no large than 1 mm, to protect the heat
exchanger from slag or impurities inside the piping.
If the machine is combined with process cycles, it is recommended to install a readily serviceable uncoupling
exchanger to prevent possible operation blockages and/or breakage of the plate evaporator.
air vent valve placed on the higher parts of the hydraulic circuit to bleed the air. [The internal pipes
of the unit are fitted with small air vent valves for bleeding the unit itself: this operation should be
conducted when the unit is disconnected from the power supply - make sure that the circuit is
completely full of water and (FS-FL versions) bleed out the air from the water coils to prevent pump
cavitation (see fig.) and check again to make sure there is no air before starting the pump for the
first time].

LCX
RG66010687_rev.00 14
discharge cock and, where needed, drain tank in order to empty the system for maintenance or
seasonal stops. [A 1” drainage valve is provided on the optional water buffer tank: this operation
may only be carried out when the unit is disconnected from the power supply].
On the FS-FL versions, it is compulsory to use glycol solutions (max. 35% weight) in order to
prevent damage to the finned coil caused by freezing which is very difficult to repair. Carefully
assess the minimum air T to which the unit may be exposed and then determine the % of
antifreeze to be added.
Failure to use anti-freezing solutions may cause serious damage of the free-cooling coils
and to the hydraulic/cooling circuit in general.

LCX
RG66010687_rev.00 15
5.3 WATER CONNECTION TO THE EVAPORATOR
It is extremely important that the water inlet corresponds with the connection marked
with the writing “Water Inlet”.
Otherwise the evaporator would be exposed to the risk of freezing since the antifreeze thermostat would
not be able to perform its function; moreover the reverse cycle would not be activated in the cooling
mode, resulting in additional risks of malfunctioning.
The size and positions of the hydraulic connections are carried on the dimensional tables at the end of
the manual.
The water circuit must be set up in such a way as to guarantee that the nominal flow rate
of the water supplied to the evaporator remains constant (+/- 15%) in all operating
conditions.
The compressors often work intermittently, since the chilling requirements of the user generally do not
coincide with the output of LCX unit. In systems containing little water, where the thermal inertia of the
water is lower, it is a good idea to check that the water content in the section delivering to users satisfies
the condition below:
NsSh
Cc
V
V = water content in user section [m3]
Sh = specific heat of the fluid [J/(kg/°C)]
= fluid density kg/m3]
∆= minimum time lapse between 2 compressor restarts [s]
∆T = allowed water T differential [°C]
Cc = Chilling power [W]
Ns = No. of partialization steps
Inertial Buffer
Ts °C
Inlet water T Outlet water T

LCX
RG66010687_rev.00 16
A standard feature of the LCX units is a device for controlling the flow rate (differential
pressure switch) in the water circuit in the immediate vicinity of the evaporator.
Any tampering with said device will immediately invalidate the warranty.
It is advisable to install a metal mesh filter with mesh no large than 1mm on the inlet
water pipe.
It is strongly recommended to install a safety valve in the water circuit. In the event of
serious equipment faults (e.g. fire) it will enable water to be drained from the system,
thereby preventing possible bursts. Always connect the drain outlet to a pipe with a
diameter at least as large as that of the valve opening and direct it toward an area where
the discharge of water cannot harm people. This is a standard feature of units equipped
with the optional buffer tank (optional) or pump/s kit.
Attention: During hydraulic connection operations, never work with open flames near or
inside the unit.
5.4 PROCEDURE FOR FILLING THE TANK
The tank has not been designed to withstand a depression greater than -0.15 Bar. For
this reason, attention should be paid to ensure that the pressure on the pump intake side,
where the expansion tank is positioned, will always be greater than 0.5 bars while the
pump is running: this helps to reduce the risk of cavitation.
It is extremely important that the installer follows and verifies the following procedure point by point in
order to prevent the risk of the tank exploding or pump cavitation:
a) Discharge the expansion tank until it reaches the pressure of 0.5 bar.
b) Fill the system and pressurise it until approximately + 1 Bar at pump intake (pump stopped).
c) Bleed the system.
d) Check the pump intake pressure (approximately 1 Bar) and start-up the system.
e) Stop the pump after 15-30 minutes and repeat the procedure from step c) until you can no longer
hear any noises caused by the presence of air in the system.

LCX
RG66010687_rev.00 17
5.5 SAFETY DEVICES ON THE HIGH-PRESSURE SIDE
Cooling circuit safety devices are provided on each refrigerant circuit according to the volumetric capacity
of the compressors installed, as prescribed by Directive 97/23 (PED); in particular, with respect to
equipment design, this Directive requires manufacturers to abide by the technical standard nearest to the
type of object produced; in the case of chillers designed for air-conditioning or liquid cooling systems,
standard UNI EN 378-2 is taken into consideration.
According to this standard, for refrigerant mass flow rates of up to 25dm3 per circuit only one pressure
limiting device is required; beyond this limit 2 must be applied. Practically speaking, these are safety
pressure switches designed to protect the cooling circuit in a cascade fashion.
What is meant by cascade protection is illustrated in the figure:
…where pressure switch 1 is set at the “PS” (maximum admissible pressure) of the system, while
pressure switch 2 will have the setting = PS x 0.9 in accordance with the reference technical standard.
6 ELECTRICAL CONNECTIONS
6.1 GENERAL INFORMATION
Before carrying out any work on electrical parts, make sure the power supply is
disconnected.
Check that the mains electricity supply is compatible with the specifications (voltage, number of phases,
frequency) shown on the unit rating plate.
The power connection is made by means of a three-core cable plus neutral and earth cable or single-
core cables (one per phase) + earth according to the minimum section sizes specified in the wiring
diagram, which is an integral part of the documentation accompanying the chiller; the diagram code also
appears on the rating plate inside the compressor compartment.
The size of the cable and line protections must conform to the specifications provided in
the wiring diagram.
The supply voltage may not undergo fluctuations exceeding ±5% and the unbalance between phases
must always be below 2%.
Pressure switch 1 Cut out
Pressure switch 2 Cut out
Cut in
Cut in

LCX
RG66010687_rev.00 18
The above operating conditions must always be complied with: failure to ensure said
conditions will result in the immediate invalidation of the warranty.
The electrical connections must be made in accordance with the information shown in the wiring diagram
provided with the unit and current regulations.
Electrical connections and preliminary checks:
Put on the main switch, turn the ½-turn locking screws of the electric enclosure and open it.
Introduce the power cable 400/3/50+N through the hole provided on the left side of the unit (after first
removing and making a hole in the aluminium square based on the diameter of the electric cable) and
secure it with a cable gland.
Connect the power supply and earthing wire to the terminals of the main switch.
Open the fuse carriers F1 and F2 (or Q1 and Q2 for the motor overload cutouts) of the compressors (F1-
F2-F3-F4 for the fuses or Q1-Q2-Q3-Q4 for the overload cutouts in the case of LCX 4 compressor models)
to prevent them from starting up in the wrong direction in the event of an incorrect phase sequence.
Switch on the power supply by turning the main switch (QS) to ON.
Verify whether the phase sequence R-S-T is correct by checking, on the phase sequence relay situated in
the middle of the electric control board, that the green power on LED and yellow LED indicating the correct
sequence both light up; if this does not occur, disconnect the chiller power supply from the external
distribution panel and swap over two phases; then repeat the operation. IN NO CASE SHOULD YOU
TAMPER WITH THE WIRING DOWNSTREAM FROM THE MAIN SWITCH since this may alter the correct
sequence of other devices, e.g. pump(s).
Close the fuse carriers F1 and F2 of the compressors (F1-F2-F3-F4 in the case of LCX 4 compressor
models).
Close the electrical control board and lock it by means of the ½ - turn locks.
An earth connection is required by law. The installer must connect the earthing wire using the earthing
terminal situated on the electric control board (yellow and green wire).
The power supply to the control circuit is shunted from the power line through an insulating transformer
situated on the electric control board.
The control circuit is protected by suitable fuses.
A standard feature of all units is a phase sequence relay that verifies the correct phase sequence; this is
necessary to ensure that the chiller is completely functional before enabling a compressor start-up.
6.2 FLOW SWITCH ON THE WATER SIDE
All the LCX units are fitted with a blade-type flow switch to protect the evaporator as a standard. This is
installed in series with the water and electrical circuits and wired.
6.3 ELECTRIC CONNECTIONS OF THE CIRCULATION PUMP
If selected when placing the order, the pump kits are supplied pre-wired with all LCX units. For dual
pump kits, whether set up according to an “AND” or “OR” logic, rotation is controlled on a time basis and
triggered in the event of a fault.
The pump must be started before the chiller and stopped after the latter (minimum
recommended delay: 60 seconds). If included as an option, this function is already
performed by the microprocessor on the unit.

LCX
RG66010687_rev.00 19
6.4 REMOTE CONTROLS
If you wish to include a remote control for switching the unit on and off, you must remove the jumper
between the contacts indicated in the wiring diagram and connect the remote ON/OFF control to the
terminals themselves [see annexed wiring diagram].
All remote controls work with a very low voltage (24 Vac) supplied by the insulating
transformer on the electrical control board.
6.5 REMOTE SUMMER-WINTER SWITCHING
If you wish to include a remote control for switching the unit between the summer and winter operating
modes, you must remove the jumper between the contacts indicated in the wiring diagram and connect
the remote switching control to the terminals themselves [see annexed wiring diagram]. The switching
modes vary according to whether the microprocessor control is of the basic or advanced type: detailed
instructions are provided below (see extract of corresponding wiring diagram) and in the microprocessor
user manual, an integral part of the documentation provided.
Chiller (available on C and H versions only)

LCX
RG66010687_rev.00 20
pCO (available on all versions)
This manual suits for next models
153
Table of contents
Other Galletti Chiller manuals
Popular Chiller manuals by other brands
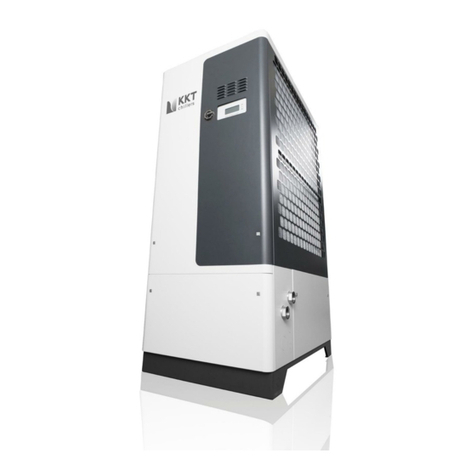
KKT chillers
KKT chillers cBoxX 60 Installation guidelines
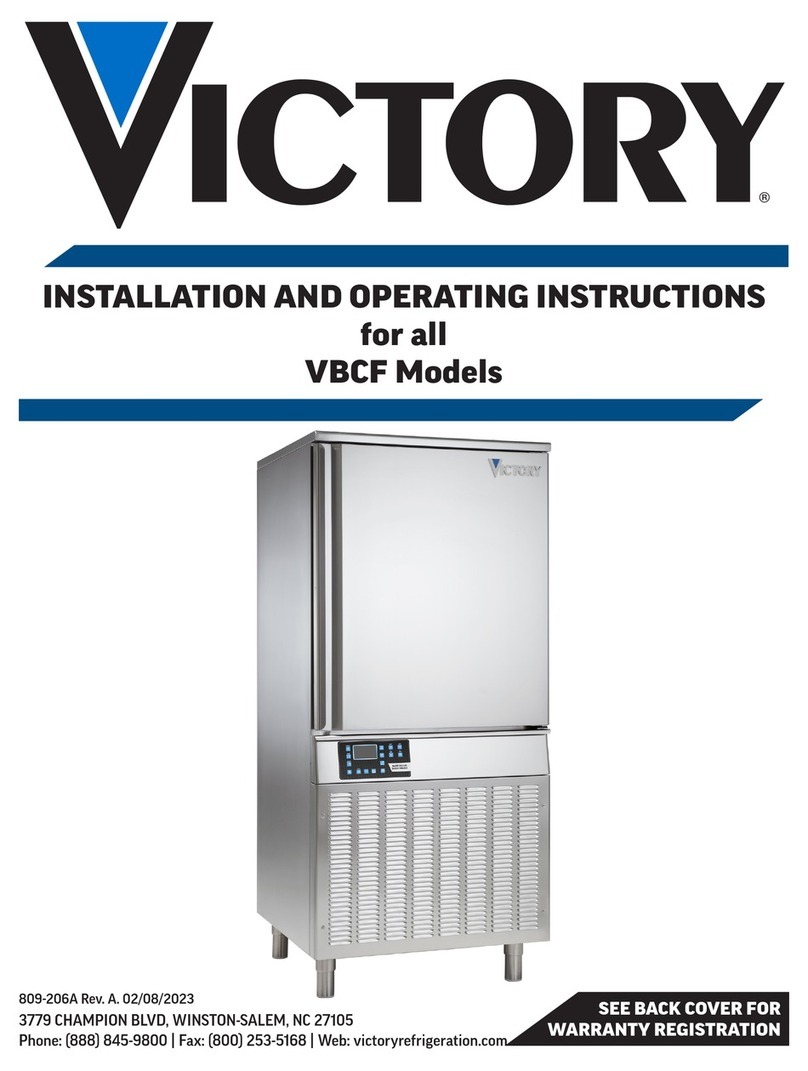
Victory
Victory VBCF5-45P Installation and operating instructions
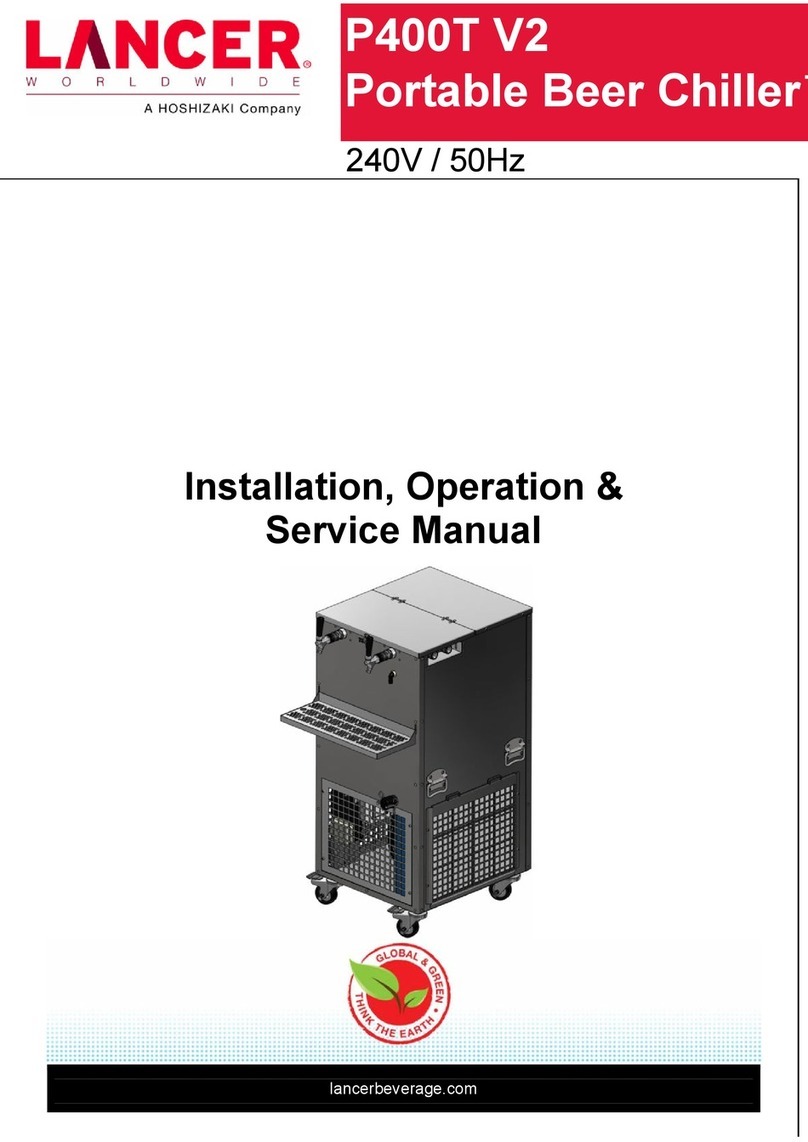
Hoshizaki
Hoshizaki Lancer P400T V2 Installation, operation & service manual
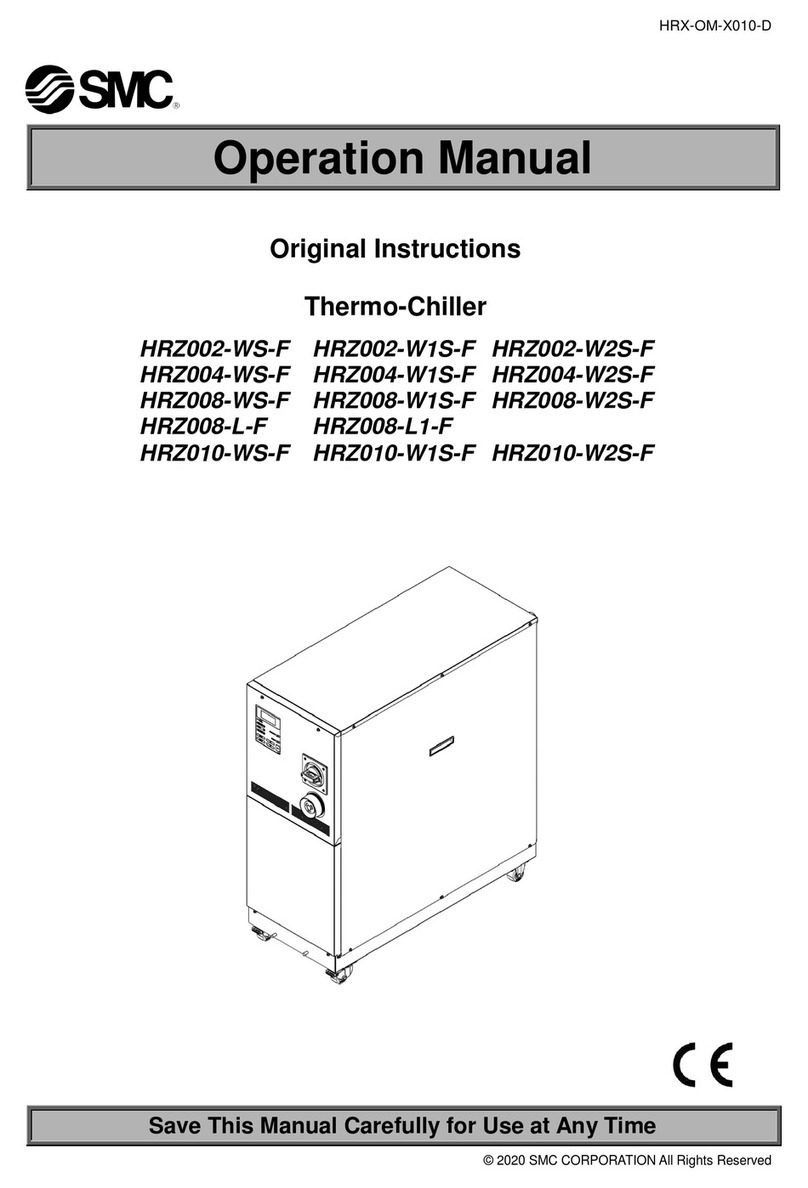
SMC Networks
SMC Networks HRZ002-WS-F Operation manual
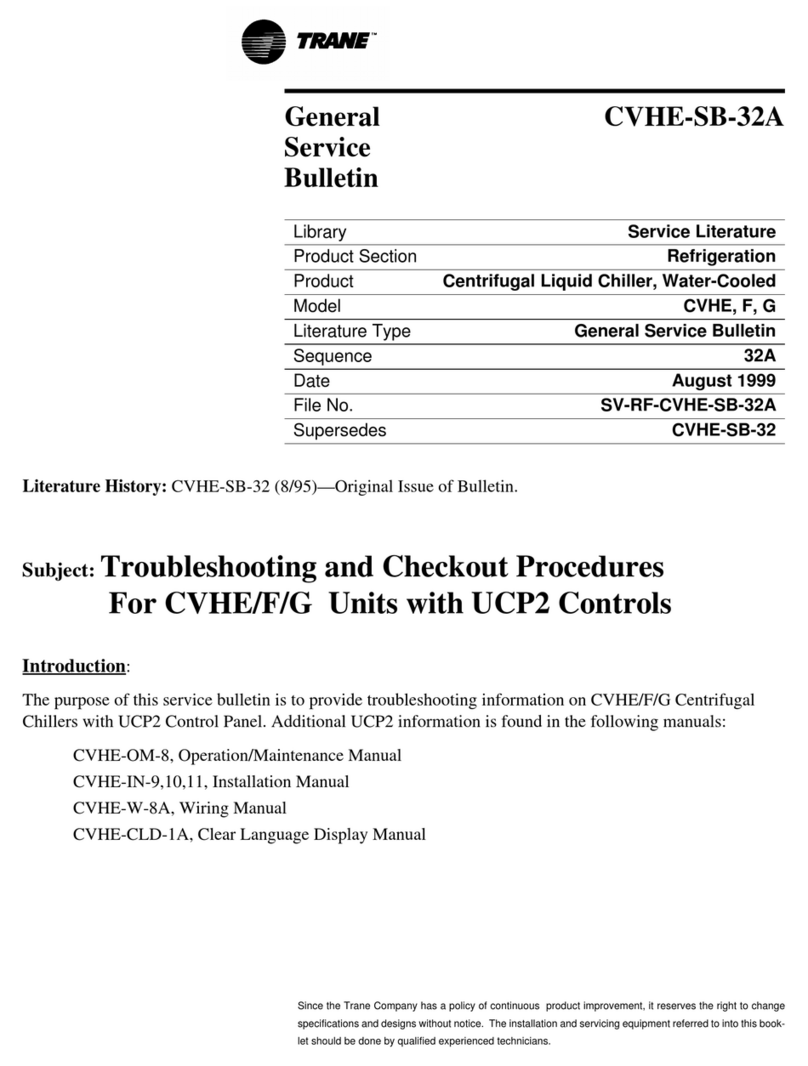
Trane
Trane CVHE Troubleshooting
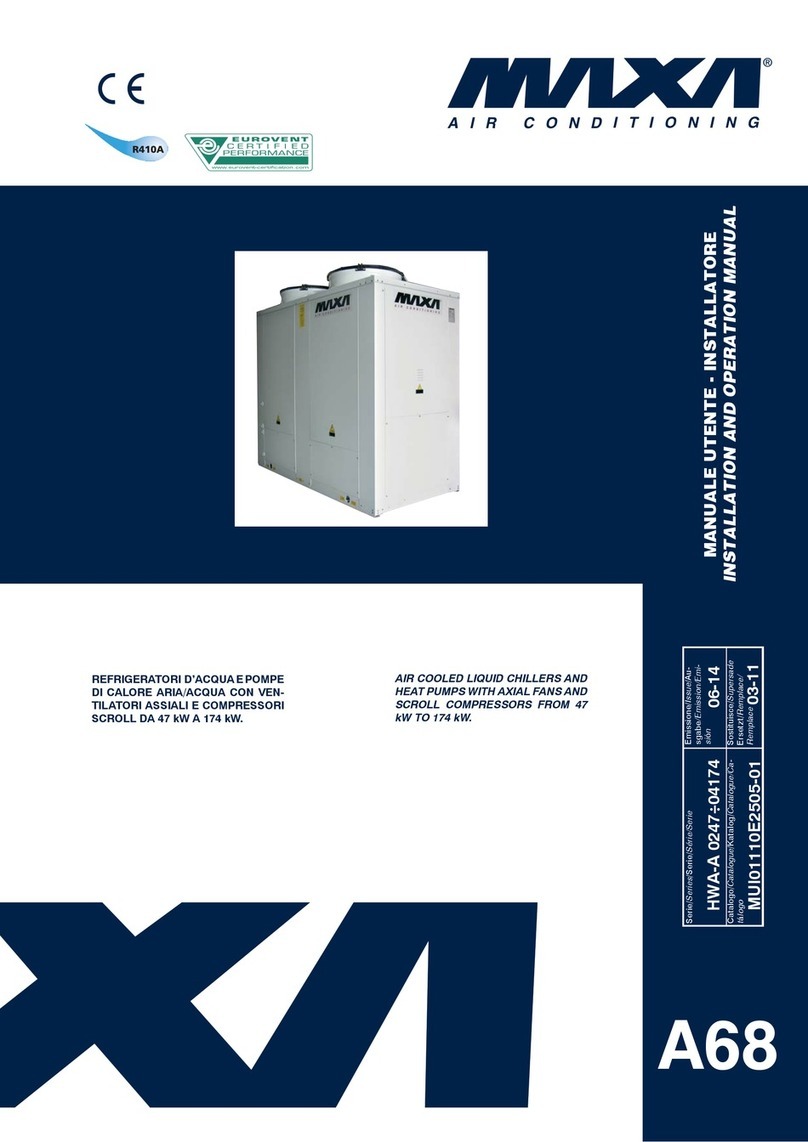
MAXA
MAXA A68 Installation and operation manual
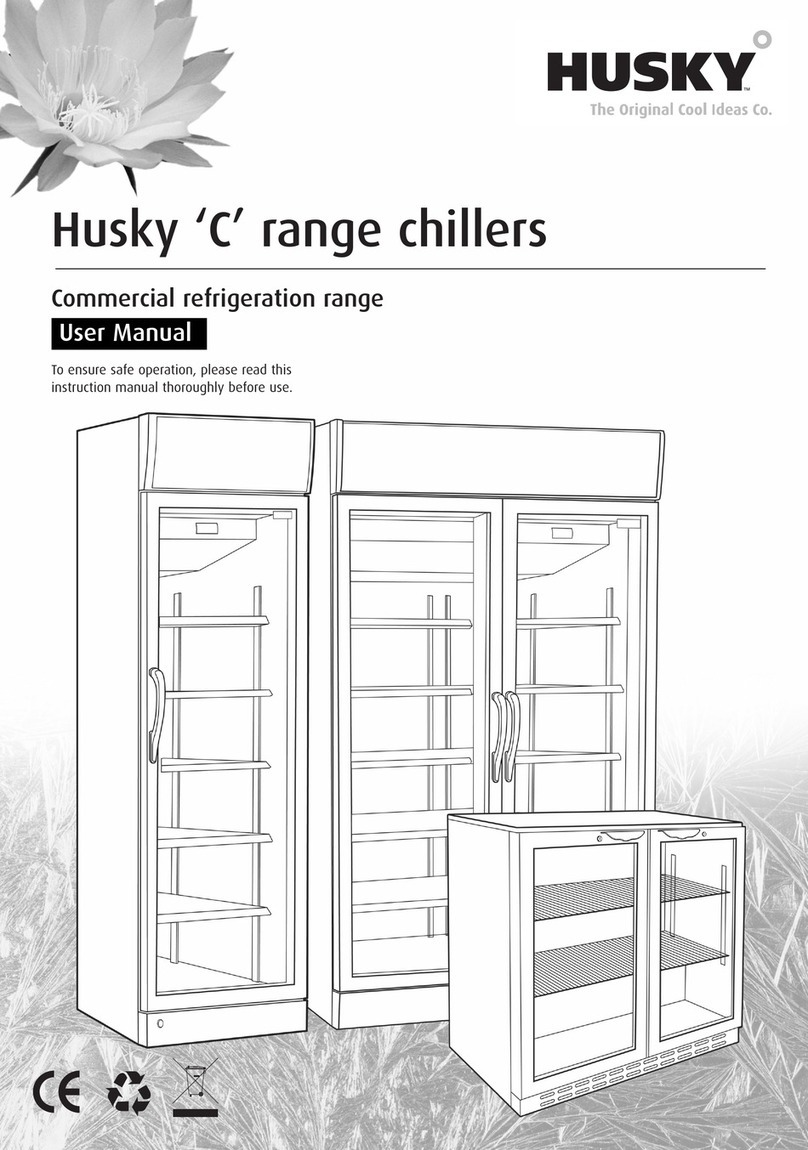
Husky
Husky C Series user manual

York
York Millennium YCAS 310 Installation operation & maintenance

Daikin
Daikin EWAA004D2V3P-H Operation manual
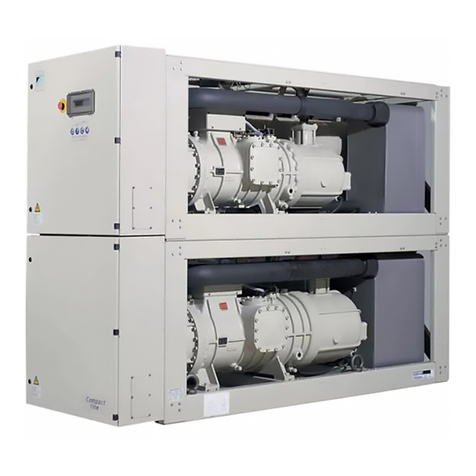
Daikin
Daikin EWLD120MBYNN Operation manual

Lauda
Lauda MC 250 operating instructions

Daikin
Daikin Pathfinder AWV Series Installation, operation and maintenance manual