GCAN GCAN-PLC-510 User manual

GCAN-PLC-510
Programmable Logic Controller
User manual
Document version V4.02(2021/03/24)

2
Guangcheng Technology GCAN-PLC user manual
Revision History:
Version
Date
Reason
V1.00
2016/12/20
Create
V2.01
2017/11/22
Add parameters
V3.01
2018/01/22
Add protocol part
V3.20
2018/07/18
Adjust structure
V3.25
2019/3/21
Selection table update
V4.00
2020/02/21
Update product parameters
V4.01
2020/08/07
Update some content
V4.02
2021/3/24
Change the appearance

3
Guangcheng Technology GCAN-PLC user manual
Contents
1. Introduction....................................................................................................... 4
1.1 Overview.................................................................................................. 4
1.2 Performance..............................................................................................5
1.3 Typical application................................................................................... 5
2. Installation......................................................................................................... 6
2.1 Module appearance...................................................................................6
2.2 Fixed module............................................................................................ 6
2.3 Wiring method..........................................................................................8
2.4 Interface definition................................................................................... 9
2.5 System status indicator........................................................................... 11
3. Communication connection.............................................................................13
3.1 Serial connection.................................................................................... 13
3.2 CAN connection..................................................................................... 13
3.3. CAN-Bus terminal resistance................................................................ 14
3.4 PLC program running switch and reset button.......................................15
4. Program operation switch and reset button..................................................... 16
5 OpenPCS Programming software usage...........................................................17
5.1 Installation of OpenPCS......................................................................... 17
5.2 Programming interface........................................................................... 17
5.3 Create project and download program....................................................17
6 Module selection table......................................................................................26
Technicalspecifications....................................................................................... 28
Sales and service..................................................................................................30

4
Guangcheng Technology GCAN-PLC user manual
1. Introduction
1.1 Overview
GCAN-PLC-510 programmable logic controller is a bus module controller
integrated with PLC function. It has the characteristics of compact, cost-
effective, can be used to connect the CAN-Bus system, Modbus system and
distributed bus terminal module, and these terminal modules can be expanded
in a modular way.
A complete control system consists of a bus module controller (GCAN-
PLC-510),1-32 arbitrary number of GC series terminal modules (GC-1008,
GC-3804, etc.) and a terminal module.
The GCAN-PLC-510 supports automatic configuration. You do not need
to set parameters on the computer. The controller will automatically assign the
I/O interface according to the positional relationship of the inserted terminal
module.
The GCAN-PLC-510 is programmed according to the IEC 61131-3
standard using the OpenPCS programming system. OpenPCS programming
system provides a variety of debugging features (such as breakpoints, single-
step, monitoring, etc.) to make debugging easier. The GCAN-PLC-510
configuration/programming interface is a Micro-USB interface that can be used
to load PLC programs.
The GCAN-PLC-510 complies with the ISO 11898 CAN bus protocol.
Support CANopen/ Modbus RTU/ Modbus TCP communication protocol and
can be used as CANopen/ Modbus RTU/ Modbue TCP master or slave.
GC series programmable controller expansion module currently includes:
digital input expansion module, digital output expansion module, analog input
expansion module, analog output expansion module, Pulse input and output
module, communication port expansion module (RS232/485, 4G, Bluetooth,
WiFi, Zigbee,GPRS, etc.) For detailed selection list, please refer to Chapter 6
of this manual.

5
Guangcheng Technology GCAN-PLC user manual
1.2 Performance
●One-channel CAN-Bus interface, one-channel Ethernet interface, one-
channel RS232/485 (multiplexed) serial interface
●Programming Software: OpenPCS ( according to IEC 61131-3standard)
●Support CANopen protocol master/slave function
●Support Modbus RTU/TCP master/slavefunction
●In the case of sufficient power supply (plus expansion power modules), the
number of expandable IO modules is up to 32 (up to 32x8 DI/DO points)
●Transmit 4 PDOs ( CANopen) and receive 4 PDOs (CANopen)
●Configuration mode is automaticconfiguration
●Supply power: 24V DC(18~30V)
●Input current, 400mA+ ( total GC-bus current)
●Starting current: about 2.5 times continuouscurrent
●Power contacts: maximum24VDC
●Electrical isolation: 1500Vrms
●Working temperature: -40.00℃~85.00℃
●Protection level: IP20
1.3 Typical application
Connect with the distributed bus terminal module to form a complete programmable
control node.

6
Guangcheng Technology GCAN-PLC user manual
2. Installation
This chapter introduces the method installation and wiring, the meaning of the
indicator and the interface.
2.1 Module appearance
GCAN-PLC-510 appearance as shown in Figure 2.1
GCAN-PLC-510 includes three communication interfaces, a controller
programming interface, a set of controller power interface, twosetsof I/O power
interfaces, two sets of Shielding line interfaces. Among them, the
communication interface includes one Ethernet interface, one CAN-Bus
interface and one RS232/RS485interface.
Figure 2.1 the appearance of GCAN-PLC-510
2.2 Fixed module
GCAN-PLC-510 and its matching terminal installation method is shown
in Figure 2.2

7
Guangcheng Technology GCAN-PLC user manual
Figure 2.2 GCAN-PLC-510 programmable controller installation
Figure 2.3 GCAN-PLC-510 self-locking mechanism
As shown figure 2.2, install the GCAN-PLC-510 on the guide rail until the
lock is stuck. Then you need to rotate the orange knob on the left end of the
controller counterclockwise to fix the left end of the controller on the guide rail.
The GCAN-PLC-510 has a self-locking mechanism that can effectively prevent
equipment from falling.
As shown figure 2.3, you can release the self-locking mechanism by
pulling out the orange label and take out the controller or matching terminal
module. Before taking out the controller, you need to rotate the orange knob on
the left end of the controller clockwise to unlock it.

8
Guangcheng Technology GCAN-PLC user manual
The GCAN-PLC-510 can connect up to 32 distributed bus terminal
modules. When inserting the GC series terminal module, be sure to insert it
along the groove on the right side of the existing module sequentially until the
lock is stuck. When you assemble the nodes correctly, there is no obvious gap
between the terminal modules. If the modules are not assembled correctly, the
entire node will not operate normally.
Please note: When using the GCAN-PLC-510 controller, you must ensure that
you have installed terminal modul at the right end of the entire node, and the
terminal resistance module has been fixed to the bottom without looseness, as
shown in Figure 2.4. This terminal module will ensure the data transmission
and power supply between GC series IO modules. The lack of this terminal
module or improper installation will cause errors in the entire system.
Figure 2.4 GC-0001 Terminal resistance module installation method
2.3 Wiring method
The power wiring as shown in figure 2.4. First, use a flat-blade
screwdriver to insert into the square hole, hold the top edge of the metal sheet
in the square hole, and press toward the hole. Then, insert the wire into the hole.
After plugging in, pull out the screwdriver and the wire can be firmly locked in
the hole.

9
Guangcheng Technology GCAN-PLC user manual
Figure 2.4 GCAN-PLC-510, the power wiring of programmable controller
2.4 Interface definition
The main control module of GCAN-PLC-510 is composed of bus
communication module and power supply module. The bus communication
module integrates an Ethernet interface, an RS232/485 multiplex interface, and
a CAN bus interface, which are led out using RJ45 interface, RJ45 interface,
and 4P terminal interface respectively. The RS232 and RS485 interface styles
are shown in Figure 2.6, and the interface definitions are shown in Table 2.1;
the CAN bus interface style is shown in Figure 2.7.The interface definition is
shown in Table 2.2.
Figure 2.6 RS-232 interface style of GCAN-PLC-510

10
Guangcheng Technology GCAN-PLC user manual
Terminal
RJ45 number
DB9 number
Meaning
RS232_TX
3
2
RS232 data send
RS232_RX
6
3
RS232 data receive
GND
4
5
Signal ground
RS485_A+
8
7
RS485 signalA+
RS485_B-
1
8
RS48 signal B-
Table 2.1 RS232 and RS485 interface definition of GCAN-PLC-510
Figure 2.7 CAN bus terminal block of GCAN-PLC-510
Terminal
Serial number
Meaning
CAN-H
1
CAN bus-high
SHIELD
2
Shield
CAN-L
3
CAN bus-low
CAN-G
4
CAN bus-GND
Table 2.2 CAN bus terminal definition of GCAN-PLC-510
The power wiring terminal block of GCAN-PLC-510 is shown in Figure
2.8, and its interface definition is shown in Table 2.3. The power supply part of
GCAN-PLC-510 contains 8 terminals.
Note that: connecting between terminal 3 and terminal 4, terminal 5 and
terminal 6, terminal 7 and terminal 8 inside the module.

11
Guangcheng Technology GCAN-PLC user manual
Figure 2.8 GCAN-PLC-510, Power terminal block
Terminal
Number
Definition
24V
1
Input 24V power
0V
2
GND power
+
3
IO positive power
+
4
IO positive power
-
5
IO negative power
-
6
IO negative power
PE
7
shield
PE
8
shield
Table 2.3 GCAN-PLC-510, terminal definition
2.5 System status indicator
GCAN-PLC-510 has two sets of status indicators, contains 6
circular status indicators in the left area and 2 power indicators in the right area.
The specific indicating function of the indicator is shown in table 2.4.

12
Guangcheng Technology GCAN-PLC user manual
Indicator
Color
Status
PWR
green
Power
SYS
green
System
RUN
green
Run
ERR
green
Error
IO RUN
green
GC-Bus run
IO ERR
green
GC-Bus error
NO.1 on the right
green
Power
NO.3 on the right
green
GC-Bus power
Table 2.4 GCAN-PLC-510, indicators
Indicator
Status
Meaning
PWR
bright
Power supply normally
not bright
Power supply abnormally
SYS
Blinking
Working status
not bright
Initialization error
RUN
Blinking
Run normal
not bright
stop
ERR
bright
System error
not bright
System normal
IO RUN
Blinking
GC-Bus run normally
not bright
GC-Bus stop
IO ERR
bright
GC-Bus error
not bright
GC-Bus normal
Terminal module
NO.1 on the right
bright
Power supply normally
not bright
Power supply abnormally
NO.3 on the right
bright
External power supply
normally
not bright
External Power supply
abnormally
Table 2.5 GCAN-PLC-510, indicators status

13
Guangcheng Technology GCAN-PLC user manual
3. Communication connection
3.1 Serial connection
GCAN-PLC-510 uses standard serial port level(RS232: ±3~15V), so the
module can directly connect to the device with RS232 interface.
3.2 CAN connection
GCAN-PLC-510 connect to CAN-Bus as described in figure 3.1, CAN-H
connect CAN-H, CAN-L connect CAN L to make communication.
GCAN-PLC-510, must be installed two 120 ohms terminal resistance at
the farthest end of CAN-Bus network; if the node number is more than 2,
intermediate nodes needn't to install 120 ohms terminal resistance. For branch
connections, the length should not exceed 3 meters.
Figure 3.1 CAN-Bus network structure
Please note: CAN-bus cable can use ordinary twisted pair and shielded twisted
pair. The theoretical maximum communication distance mainly depends on the
bus baud rate. The relationship between the maximum bus length and the baud
rate is shown in Table 3.1. If the communication distance exceeds 1km, the
cross-sectional area of the line should be greater than Φ1.0mm2. The specific
specifications should be determined according to the distance. The general rule
is to increase the distance as the distance increases.

14
Guangcheng Technology GCAN-PLC user manual
Baud rate
Distance
1 Mbit/s
40m
500 kbit/s
110m
250 kbit/s
240m
125 kbit/s
500m
50 kbit/s
1.3km
20 kbit/s
3.3km
10 kbit/s
6.6km
5 kbit/s
13km
Table 3.1 the relationship between CAN-Bus length and baud rate.
3.3. CAN-Bus terminal resistance
In order to enhance the reliability of CAN communication and eliminate
the interference of CAN bus terminal signal reflection, the two farthest
endpoints of the CAN bus network usually need to add terminal matching
resistors, as shown in Figure 3.2. The value of the terminal matching resistance
is determined by the characteristic impedance of the transmission cable. For
example, the characteristic impedance of the twisted pair is 120Ω, and the two
end points on the bus should also be integrated with 120Ω terminal resistance.
If other nodes on the network use different transceivers, the terminal resistance
must be calculated separately.
Figure 3.2 GCAN-PLC-510 connect with other nodes
Please note: GCAN-PLC-510 hasn't integrated 120Ω terminal resistance. If the
number of nodes is more than 2, the middle node does not need to install 120Ω
terminal resistance. When you need to use it, connect the both sides of the
resistance to CAN_H and CAN_L

15
Guangcheng Technology GCAN-PLC user manual
3.4 PLC program running switch and reset button
GCAN-PLC provides a core refresh USB interface, a running switch and a
reset button. The physical drawing after opening the cover is shown in Figure
3.3.
Figure 3.3 Physical Diagram of Kernel Refresh Interface
In Figure 3.3,
①is the USB interface cover. The default is closed. You can gently pry open
the cover plate by using the attached screwdriver to close the gap under the
cover plate.
②Micro-USB interface, which is the refresh interface of the kernel. GCAN-
PLC programmable logic controller uses Micro-USB data line as download line
of PLC core files. You can connect GCAN-PLC to USB-A interface of PC
through Micro- USB cable
③To run/stop the dial switch, and
④to reset the button.
Note: When the dial number of the run/stop switch is above (on the side of the
back reset button), it means that the PLC is in operation;when the dial number
of the run/stop button is below (on the side of the reset button), it means that
the PLC is in stop state. The reset button is used to upgrade the GCAN-PLC
core. Please use the button under the guidance of our technical staff.

16
Guangcheng Technology GCAN-PLC user manual
4. Program operation switch and reset
button
The GCAN-PLC-510 provides a program running switch and a reset button.
Physical picture after opening cover plate as shown in Figure 4.1:
Figure 4.1 Physical picture after opening cover plate
Note:
1. When the dip switch of the running switch is up (facing away from the reset
button), the PLC is in operation state; When the dip switch of the running
button is located down (towards the reset button side), it represents the PLC
In the stopped state.
2. After power-on, hold down the reset button until the ERR indicator blinks to
restore the PLC, factory IP address: 192.168.1.30.

17
Guangcheng Technology GCAN-PLC user manual
5 OpenPCS Programming software usage
5.1 Installation of OpenPCS
OpenPCS programming software download address:
http://gcgd.net/tecinfo1_1086.html
5.2 Programming interface
Figure 5.1 OpenPCS programming interface
Programming interface of OpenPCS mainly contains:
1)Menu
2) Project window
3)Edit window
4)Output window
5)Catalog window
5.3 Create project and download program
Note: GCAN series PLC uses the network port to download the program, and
the factory IP address of the PLC: 192.168.1.30.
5.3.1 Create project

18
Guangcheng Technology GCAN-PLC user manual
Click “File”, than select ”New” to create a new file, as shown in Figure 5.2.
Figure 5.2 Create project
5.3.2 Add program page file
Add files to the project (for example: add a program page ST, Program
written in ST language), as shown in Figure 5.3.
Please note that: the string entered in the name field cannot start with a number.

19
Guangcheng Technology GCAN-PLC user manual
Figure 5.3 Create a new file
5.3.3 Programming
First define the variable in the variable area (VAR to END_VAR) VAR
v1:INT:=0; v2:INT:=0;
oled at%Q0.0:Byte; END_VAR
After the variable is defined, start programming. The following is a simple
routine statement written in ST:
LED Marquee routines:
IF v1<100 then v1:=v1+1;
ELSE
v1:=0; v2:=v2+1;
if v2>=255 then v2:=0;
end_if;
oled:=int_to_byte(v2); end_if;
5.3.4 Set up debug connection
Click “PLC”, then select “Connections..”, as shown in Figure5.4.

20
Guangcheng Technology GCAN-PLC user manual
Figure 5.4 Debug connection
Click “New” to set up parameters, port number is the actual serial port
number of the computer, shown in Figure 5.5.
This manual suits for next models
2
Table of contents
Popular Controllers manuals by other brands
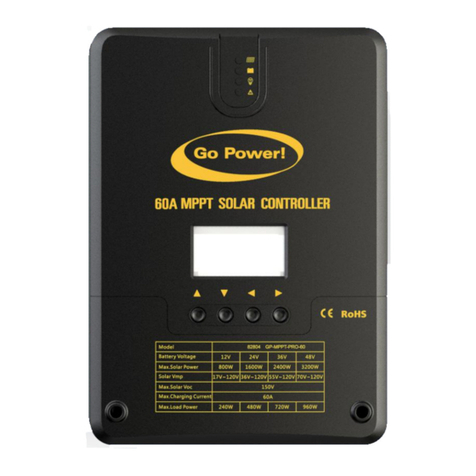
Go Power
Go Power MPPT-PRO Series user manual
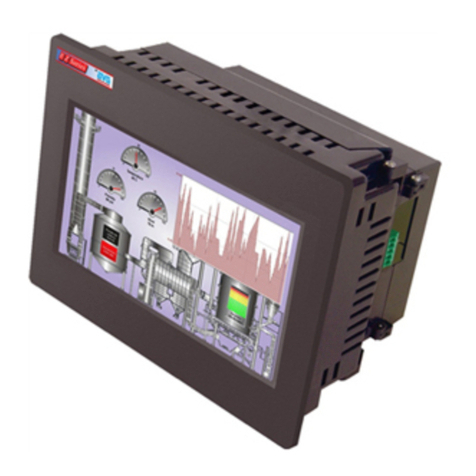
EZAutomation
EZAutomation EZ7-TouchPLC quick start guide
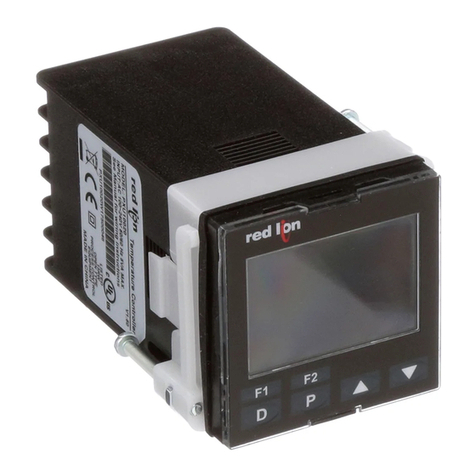
red lion
red lion PXU100B0 instructions

Oriental motor
Oriental motor ASTEP AZ Series user manual
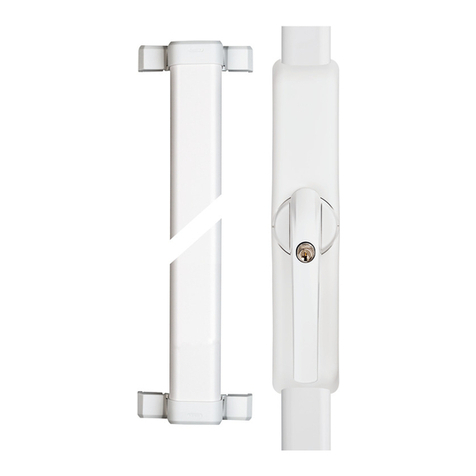
Abus
Abus HomeTec Pro FCA3000W manual
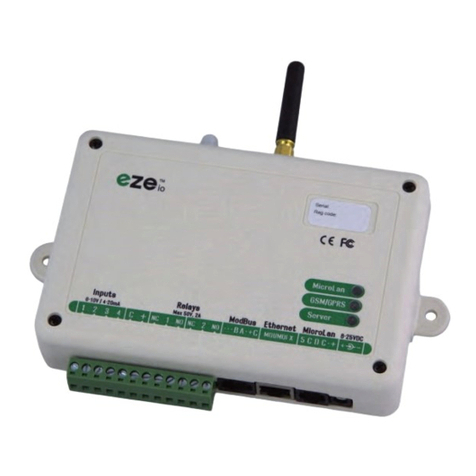
Intech Instruments Ltd
Intech Instruments Ltd ezeio-STD Supplementary manual