Geco G-202-P06 Operating instructions

P.P.U.H. „Geco” Spółka z o. o.
32-060 Liszki, Poland
Cholerzyn 376
tel. 012 6369811, 6361290
fax. 012 6362002
http://www geco.pl
G-202-P06
SELF-CONTAINED CONTROL BLOCK
MAINTENANCE AND REPAIR MANUAL
REFRIGERATION UNITS ORIENTED VERSION
For Program Version 01, 02, 03
We kindly request that you study this manual carefully PRIOR to connecting and starting up
any of our equipment. Should you have any queries or doubts, please contact us between 8
a.m. and 4 p.m. Any comments e-mailed will be appreciated.
Note !!! The date of the last update is given at the bottom of the consecutive pages,
while information regarding the consecutive changes in the programme version and
operation method are given at the end of page XII.
Please, use only the most recent version of our manual. You will receive this version free, by
post, after prior order.

Page 2 Maintenance and Repair Manual for Manufacturers, SBR TYPE G-202-P06
PPUH „GECO” - G-202-P06 01, 02, 03 Program Version PRINTOUT DATED 2011-05-06
I. GENERAL CHARACTERISTICS
The self-contained control block, hereafter called G-202, constitutes a modern, convenient and
easy-to-use equipment and has been made using microprocessor techniques with the application of
automatic surface assembly process.
Owing to the twin part case and revolutionary technical design, the G-202-P06 can be applied to
any refrigerated counters, where may be required to maintain a constant humidity setpoint . The safe
voltage operated control panel (5 V) may be installed in any place, without the necessity of cutting any
additional openings or running a number of power supply cables far away from the equipment being
controlled.
The G-202 has been equipped with two temperature sensors, one humidity sensor, which
provides for the capability of connecting to the actuating module, which are safe voltage operated (5 V),
as well as four outputs allowing direct connecting of the 230 V operated equipment, with loading ability
as summarized in table 1.
If the G-202 is used in refrigeration chambers, it stabilizes the temperature, humidity (in special
mode), as well as controls automatic defrosting, the period of which may be adjusted to specific
surrounding parameters; it is also equipped with a pushbutton for activating manual defrosting. G-202-
P06 has also been equipped with humidity control system switch.
No special maintenance measures are required for these thermostats; the keyboard has been made
from the special kind of foil, high temperatures resistant as well as resistant to most chemicals.
However, cleaning this foil with sharp objects is not allowed. Instead, use the damp cloth and clean the
front panel with it from time to time.
II. DENOTATION METHOD AND TECHNICAL DATA
Denotation: G- 2 0X –P 06K 0 X –M XXXX H
Position: 1 2 3 4 5 6 7 8 9 10 11
1-
2- Cooling reason.
3- Case type: 2- mini panel
4- P
5- Software version.
6-
7- (not available in this version).
8- Sound with sound, 0 without sound.
9- M
10-Relays, details below
11-Humidity sensor.
Additional outputs denotation method:
Number means that relay is mounted, 0- without relay:
1 compressor relay- have to be
2 humidity control relay
3 fan relay
4 - heater/valve relay

Page3
Operating Voltage - 230V +10% -15%
Ambient Temperature - +5C to +40C
Humidity - 20% to 80%
Ip Protection - IP65 on the front panel of the control panel
Table 1 –Relays Denotation and Outputs Loads
Output
Load
P1 –compressor
8A
2HP
1500W
P2 –humidity control
/ drying heater / humidifier
4A
-
750W
P3 –fan
4A
1HP
750W
P4 –defrost heater / valve
8A
-
1500W
Note !!!
Currents as specified in the Table are currents consumed by
particular equipment during normal operation and include starting
currents of this equipment !!!
The aggregate current consumed simultaneously may not exceed 10A !!!
Heater power must be chosen so that in case of failure of G-202 or contactor and switching
then on permanently, there was no possibility of fire or damage to equipment.
If heaters are used in high power should be strictly applied safety
thermostat on evaporator, the thermostat should operate in a different
way, eg mechanical thermostat !!!
III. ORDERING METHOD
The following parameters need to be given in the order, namely:
1. Controller type, e.g. G-202-P06K0B-M1234H
2. The length of tape linking the actuating module and keyboard panel
3. Temperature sensors lengths
4. Humidity sensor length

Page 4 Maintenance and Repair Manual for Manufacturers, SBR TYPE G-202-P06
PPUH „GECO” - G-202-P06 01, 02, 03 Program Version PRINTOUT DATED 2011-05-06
IV. OPERATION METHOD
A - General Information
1. Having turned the equipment on, the three-second starting procedure is activated, during which the
display will show two dashes, for the period of two seconds, and then for the period of one second,
the version of the controller program will be displayed, as well as two to dashes. No activation of the
equipment under control takes place then.
2. Following the completion of the starting procedure, two horizontal dashes signalling the energizing
status will light up on the central segments of the display -
before!!!. The unit will be activated after pressing the pushbutton . The display will show the
temperature value of the chamber sensor.
3. Having pressed and held down the pushbutton for the period of a half second, the display will
start blinking and showing the evaporator temperature, while after the consecutive five seconds, the
G-202 will automatically re-enter the chamber temperature readout mode. Note!!! This function is
dF
4. The compressor activation is signalled by the small red diode
in the right, bottom corner of the display showing the temperature. This allows easier check of
possible damage and malfunction to the system.
5. If the compressor should have turned on, but the compressor has not been turned on due to the
activation of any of the protection systems (see points 6, 7, and 8), the dot signalling the
compressor's operation will be blinking. When the protection system preset time preset elapses, the
daughter will stop blinking and will be lit permanently, while the compressor will be activated .
6. The delay in turning the compressor on after its activation temperature is reached (user set
temperature minus bottom value of the hysteresis) is equal to 30 seconds. If the temperature drops
again during this time. The condition of exceeding 30 seconds will be verified again. This is
designed to protect the compressor against unnecessary activation due to e.g. articles placement,
droughts, etc.
7. After every reaching of the preset temperature (user set temperature minus bottom value of the
hysteresis), as well as following any power failure or voltage drops below 175 volts, the G-202 will
ilure.
8. Having turned the equipment on using the pushbutton, the 5-second delay will appear in the
compressor activation. This is to cancel the power failure protection from point 7 this will also
pertain to the time specified by t
This allows faster compressor operation check.
9.
he controller performance will be different.
The malfunction of the chamber temperature sensor will make the display show the A1
symbol. The controller will activate the compressor in the time cycle (clock-based control) in
accordance with times specified
function as usual.
If the evaporator sensor is damaged, the display will show the A2 symbol. The manual and
automatic defrosting is blocked then!!! The only possibility of defrosting the unit is to
press the pushbutton in order to turn off the unit, and then wait for the ice to thaw.
The malfunction of the humidity sensor will make the display show the A3 symbol.

Page5
If more than one sensor has been damaged, only the A1 symbol will be displayed.
Having repaired the chamber sensor, the A2 symbol will start to be displayed.Having
repaired the evaporator sensor, the A3 symbol will start to be displayed.
10. If the buzzer has been installed in the controller see p. II, the buzzer will signal any pressing of
any button. If the controller is turned off (two horizontal dashes on the display are seen then), the
buzzer will signal only if the following pushbutton is pressed, namely: .
11. The humidity control system activation and deactivation will take place after pressing the
pushbutton. This will be signalled by the green LED.
12. Having pressed and held down the pushbutton for the period of 0,5s , the display will start
showing the measured humidity (without blinking), while after the consecutive five seconds, the
G-202 will automatically re-enter the chamber temperature readout mode.
13. When controller is in on-mode also fans are activated.
14. When controller is in off-mode (two horizontal dashes on display) compressor, fan and heaters are
deactivated.
B - Defrosting
1. If the necessity for the additional defrosting occurs, due to difficult operating conditions, press the
pushbutton. This will make the green LED light constantly on the pushbutton dF
symbol will appear on the display, rather than temperature measurement symbol, and this is where the
unit will enter the defrosting cycle.
2. If the defrosting occurs, and the temperature on the eva
parameter, the unit, after some 10 seconds, will enter the defrosting exiting mode, to resume the
operation when the said mode terminates.
3. If the defrosting occurs, and the temperature on the evaporator is lower t
parameter, the G-202 will activate the defrosting process.
I. Normal work mode:
- defrosting with heater
Defrost heater - on, compressor off, drying heater off, fans on.
After reaching the temperature as specified in the the unit will enter the
defrosting exiting mode.
- defrosting with hot couples
Valve - on, compressor on, drying heater off, fans on.
the unit will enter the
defrosting exiting mode.
II. Drying work mode:
- defrosting with heater
Defrost heater - off, compressor off, fans on.
the unit will exit
defrosting mode.

Page 6 Maintenance and Repair Manual for Manufacturers, SBR TYPE G-202-P06
PPUH „GECO” - G-202-P06 01, 02, 03 Program Version PRINTOUT DATED 2011-05-06
1 - defrosting with hot couples
Valve - on, compressor on, fans on.
the unit will enter the
defrosting exiting mode.
4.Exiting the defrosting mode is followed with deactivated compressor and heater for the period of time
)., The procedure of exiting the
defrosting mode is terminated with dF
green LED blinking on the pushbutton .
5. The defrosting process will be terminated following the achieving of the evaporator temperature as
6. Having turned dF
temperature as stored right before the defrosting commencement, for the period of time as specified
this is intended for preventing claims with res
7. The unit performance is the same as in the case of manual and automatic defrosting.
8. Turning on or turning off The Humidity Control System when in defrosting mode does not change
defrosting procedure.
C –User Parameters Programming
To enter programming mode the controller should be turned on.
Press the pushbutton. This status is signaled by the green LED on pushbutton, while the
one second. Then, the most recently programmed temperature for
Normal Work Mode will be shown.
Enter the required settings, using the pushbuttons, any longer pushbutton holding time
Press , in order to approve the data entered.
the most recently programmed temperature for Humidity Control Mode will be shown.
Press , in order to approve the data entered.
the most recently programmed humidity for Humidity Control Mode will be shown.
Press , in order to approve the data entered.
After that the green LED on pushbutton will go off, and G-202 will end programming mode and
start working with new program.
If in programming mode none of pushbuttons will be pressed for 5 seconds, G-202 will
automatically go out of this mode. In that case the value of changed parameter will not be saved.
The temperature T1 for Normal Work
and the temperature T2 for Humidity Control

Page7
D –Humidity Control
After turning on Humidity Control Mode the temperature T2 (set by user) is stabilized in the chamber.
Humidity control is realised by turning on/off drying heater (2=0) or humidifier (2=1), based on the
measurement of the humidity sensor. Sensor measures humidity in range from 10% to 99%. Measured
humidity is
PROGRAM VERSION 01: Humidity is stabilised with 2% hysteresis.
In drying work mode humidity can be set in range from 10% to 99%.
PROGRAM VERSION 02: Humidity is stabilised with
The malfunction of the humidity sensor will make the display show the A3 symbol and G-202 starts to
operate heater/humidifier relay in the time cycle (clock-based control) in accordance with times
ters.
E –Hysteresis
temperature to higher or lower values with relation to the user preset temperature level.
This is particularly significant with regard to the so-
operated at the temperatures above 0oC.
even values
Symmetric hysteodd values
Example No. 1.
For this hysteresis value, the parameters should
d0d1
Example No. 3.
For this hysteresis value, the parameters should
d0d1
Example No. 2.
For this hysteresis value, the parameters should
d0d1
Example No. 4.
For this hysteresis value, the parameters should
d0d1
Activation Temp.
User Preset Temp.
Deact. Temp.
-

Page 8 Maintenance and Repair Manual for Manufacturers, SBR TYPE G-202-P06
PPUH „GECO” - G-202-P06 01, 02, 03 Program Version PRINTOUT DATED 2011-05-06
V. UNIT PARTICULAR COMPONENTS ACTIVATION GRAPHS
A thick line denotes activation, while the dashed one means deactivation of the particular equipment.
Stop deactivation Operation
activation
IF ERRONEOUS PARAMETERS ARE SET, THE UNIT WILL FAIL TO OPERATE PROPERLY
!!!
1. Normal work mode, heater defrosting (‘r1’=0)
t=c3
COMPRESSOR
HEATER 1
HEATER 2
FAN
Stop Operation DEFROSTING DEFROSTING EXITING Operation Stop
2. Humidity control mode, heater defrosting (‘r1’=0)
t=0
COMPRESSOR
HEATER 1
HEATER 2
FAN
Stop Operation DEFROSTING DEFROSTING EXITING Operation Stop
3. Humidity control mode, hot couples defrosting (‘r1’=1)
t=c3
COMPRESSOR
VALVE
HEATER 2
FAN
Stop Operation DEFROSTING DEFROSTING EXITING Operation Stop
Heater 1 –defrost heater
Heater 2 –drying heater

Page9
VI. SYSTEM PARAMETERS PROGRAMMING
Having activated and checked the unit operation (standard settings are factory set), start entering system
parameters to the G-202 unit.
For this purpose, turn off the unit by pressing the pushbutton. Then press the buttons and
, depress and hold, at the same time press the pushbutton. All the three pushbuttons need to
be depressed and held for at least the period of 3 seconds. If any of these buttons has been released
during the said time, the unit will abandon the programming mode. When the unit has assumed the
programming mode, the LEDs on the and pushbuttons will start to blink, while the display will
shown. Enter the required settings, using the pushbuttons, any longer pushbutton holding time
, in order to approve the data entered and
start entering the next parameter.
Partial entering of the settings is also possible. If any alteration of the particular setting is not
required, simply press the pushbutton and the G-202 unit will assume the next parameter setting
mode.
Note !!!
The refrigeration unit Manufacturer may block access to a portion of or even to all
parameters available from the keyboard, by means of the computer programming unit. If
this is the case, and the alteration of any of the blocked parameters is attempted, the
display will show the ‘bL’ symbol for the period of 1 second.

Page 10 Maintenance and Repair Manual for Manufacturers, SBR TYPE G-202-P06
PPUH „GECO” - G-202-P06 01, 02, 03 Program Version PRINTOUT DATED 2011-05-06
Table 2: Parameters Denotation
Para-
Mete
r
Description
Min
Max
Step
Factory
setting
c0
The defrosting frequency. Note!!! If this parameter is set to
any automatic
defrosti -
neither manual nor automatic defrosting will be available!!!
00
-01
24
1h
6h
c1
Maximal defrosting time if the evaporator has not reached the
preset temperature (d2 parameter) Note!!! If this parameter is set to
00- no time limit will be available
00
-01
99
1min
30min
c2
Minimal compressor stopping time
00
15
1min
3min
c3
Evaporator thawing time
00
15
1min
2min
c4
Drying heater/humidifier stopping time if humidity sensor has been
damaged.
01
99
1min
20min
c5
Maximal compressor operation time
0 denotes the absence of test
00
99
1min
40min
c6
Drying heater/humidifier operation time if humidity sensor has
been damaged.
01
99
1min
10min
c7
Time for which the temperature measured directly prior to the
defrosting commencement will be shown after the defrosting
00
60
1min
5min
c8
Compressor operation time if controlling sensor has been damaged
01
99
1min
25min
c9
Compressor stopping time if controlling sensor has been damaged
01
60
1min
5min
d0
User set minimal temperature
-40
20
d1
User set maximal temperature
d0+1
40
d2
Evaporator temperature at which the defrosting terminates
0
40
d3
Temperature sensor hysteresis value
1
10
d4
Chamber sensor rescaling with relation to actually measured
temperature
-10
10
d5
User set maximal temperature in Humidity Control Mode
d1+1
40
20
d6
Humidity sensor rescaling with relation to actually measured
humidity
-99
99
1%
0%
d7
User set minimal humidity (only in program version: 02, 03)
10
80
1%
10%
d8
User set maximal humidity (only in program version: 02, 03)
d7+1
90
1%
90%
d9
Humidity sensor hysteresis value (only in program version: 02, 03)
1
50
1%
1%
r1
Evaporator defrosting method, the parameter set as follows:
00 defrosting through the heater
01 warm vapour defrosting
00
01
1
00
r2
Humidity control method, the parameter set as follows:
00 drying
01 humidifying
00
01
1
00

Page11
VII. PROBLEMS AND THEIR REMOVAL
defect symptoms
check
1. Display is not lit
although G-202 is
connected to mains
Check:
- if there is voltage 230V on feeding clamps L and N
2. Compressor
does not switch on
although it is
signalled that it is
on: red diode
Check:
- if there is voltage 230V on clamps P2 and N
–If there is, check the compressor
3. Defrosting heater
does not switch on
Check:
- if there is voltage 230V on clamps as described on the casing of the
controller
- if there is, check the heater
4. Drying heater
does not switch on
Check:
- if there is voltage 230V on clamps as described on the casing of the
controller
- if there is, check the heater
5. Error of
temperature
indication
Check:
- connection of sensors to connectors
- the value of parameter ‘d4’
- if the sensor is fixed correctly
- the condition of the cable of the sensor: the cable cannot have any
defects
- in detail the lookout of external surface of sensor shell to see
whether it has not been damaged mechanically.
6. impossible to set
the required
temperature
Check:
the value of parameters ‘d0’ , ‘d1’ (d0<d1), and ‘d5’ (d1<d5)
7. dots on the
display flash, no
possibility to switch
it on
Check :
- the value of feeding voltage
- condition of feeding connectors
- whether feeding connectors are tightened up
8. ‘’abnormal’,
‘strange’ operation
of the unit
Check:
- if there is voltage 230V on feeding clamps L and N
- condition of feeding connectors
- ‘zeroing’ of cooling unit
- condition of electric system and the number of units connected to
one phase
- if the type of thermostat is right (label with description of outlets) for
the unit
- whether the thermostat was not wetted by water or other liquid
- if thermostat is not exposed to humidity or sudden changes of
temperature

Page 12 Maintenance and Repair Manual for Manufacturers, SBR TYPE G-202-P06
PPUH „GECO” - G-202-P06 01, 02, 03 Program Version PRINTOUT DATED 2011-05-06
VIII. RETURNS FOR REPAIR
PPUH ‘GECO’ reserves the right to refuse a free repair of the unit, if
the seals are broken !!!
P.P.U.H. ‘Geco’ Sp. z o. o. is not responsible for loses and damages resulting
from provision of information on the method of making changes in the system
data of G-202 by the producer or its service to the final client, incorrect or
non-professional assembly and for loses caused by defective operation of the
appliance.
IX. CHANGES IN THE CONTROL
1. 17.03.2003: Program version 02. Added 3 service parameters: D7, D8, D9.
2. 12.11.2003: Program version 03. Added 2 service parameters: R1, R2.
10. The appliance
does not reach the
set temperature
and does not cool
Check:
- what temperature was programmed by the user
- set values of particular parameters, in particular ‘c2’, ‘c5’, ‘d0’, ‘d1’,
‘d5’
- item 9 –Problems with defrosting of the unit. If the unit does not
defrost itself fully, it won’t reach the programmed temperature!!!
- the method and place of fixing of the chamber sensor
- whether side panels were not uninstalled from the rack or whether
moving panes were not uninstalled from the display
- WHETHER THE UNIT STANDS IN A DRAFT OR IN SUNLIGHT!!!
- whether ventilators or air conditioning are installed on the ceiling or
nearby - cleanliness of the condenser
- temperature in the shop (each producer defines maximal operating
temperature of an appliance)
- the quantity of gas, ventilators, evaporator heater, hose that carries
away water from the evaporator
11. malfunction of
humidity sensor
Check:
- the value of parameter ‘d6’
- connection of sensor to connector

Page13
X. SCHEME OF CONNECTIONS. ACTUATOR (EXECUTIVE MODULE)
VIEW. THE METHOD OF CONNECTION OF THE EXECUTIVE MODULE
WITH A CONTROL PANEL USING THE TAPE.
T H E D I A G R A M S H O W S TA P E
CONNECTIONS FROM THE INPUT
HOLES VIEW. DIAGRAM SHOWS ALSO
THEIRS PLACEMENT BETWEEN EACH
OTHER, AND ALSO AFTER CORRECT
REALIZATION OF THE CONNECTION.
G 203 CONTROL PANEL FRONT VIEW
G 202 CONTROL PANEL FRONT VIEW
Table of contents
Other Geco Measuring Instrument manuals
Popular Measuring Instrument manuals by other brands
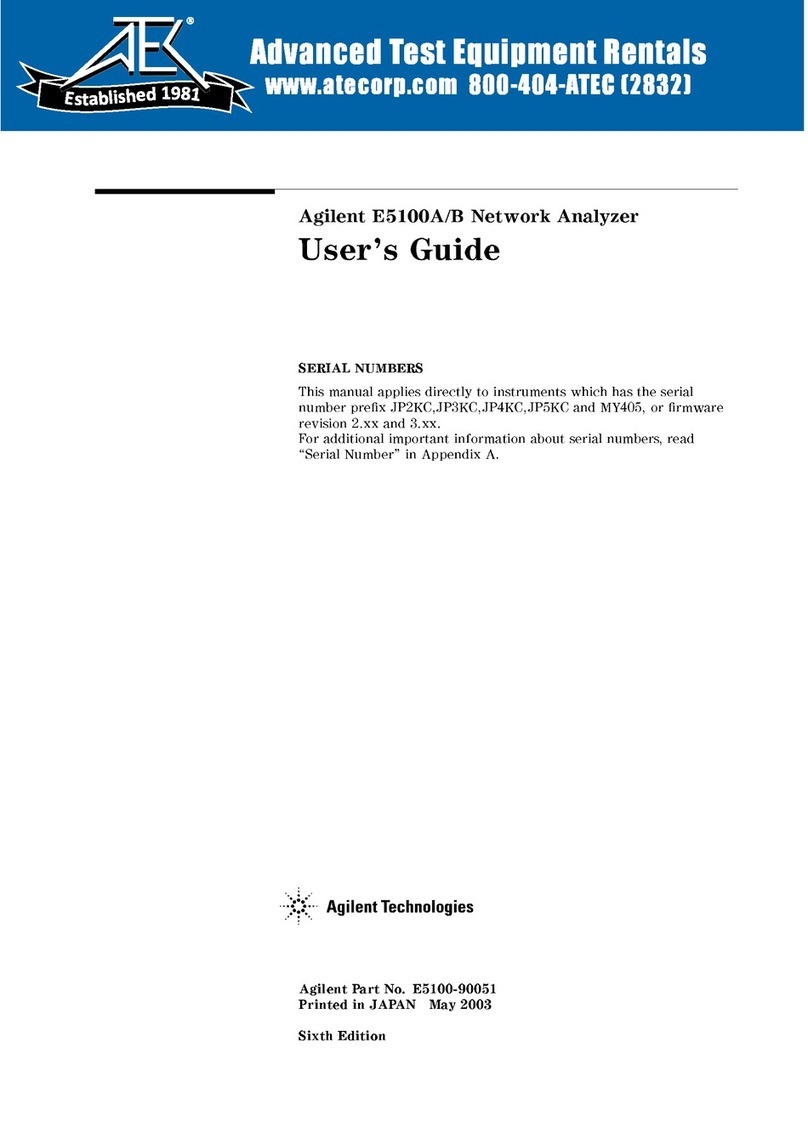
Agilent Technologies
Agilent Technologies E5100A user guide
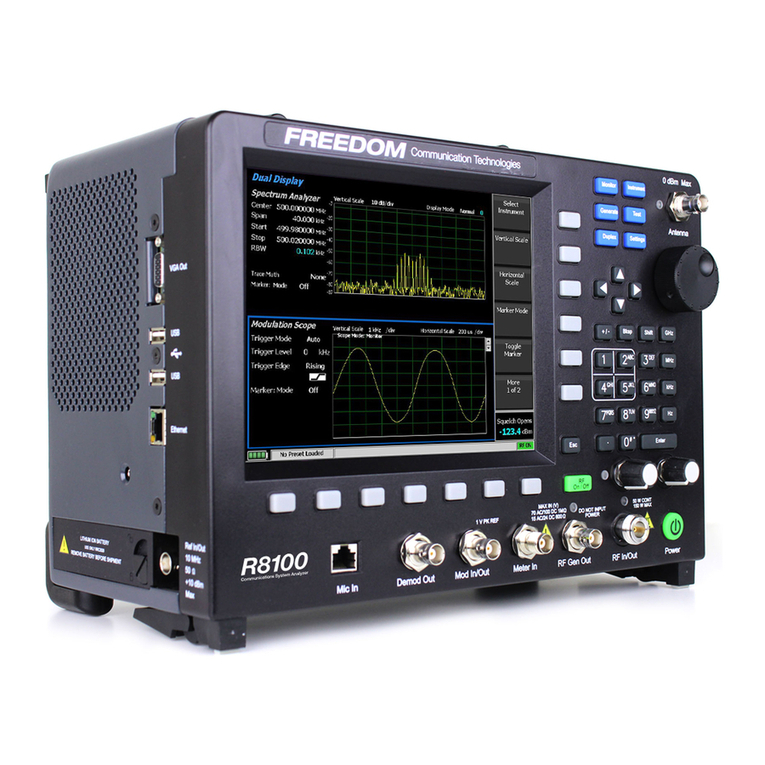
Freedom
Freedom R8000 Series user guide
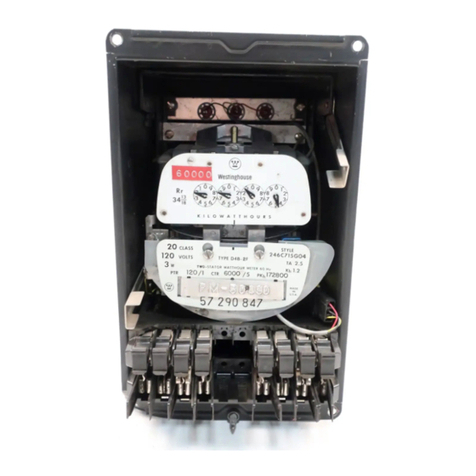
Westinghouse
Westinghouse D48-F, D4B-2F, D4B-3F, D4B-7F, D48-SF instructions
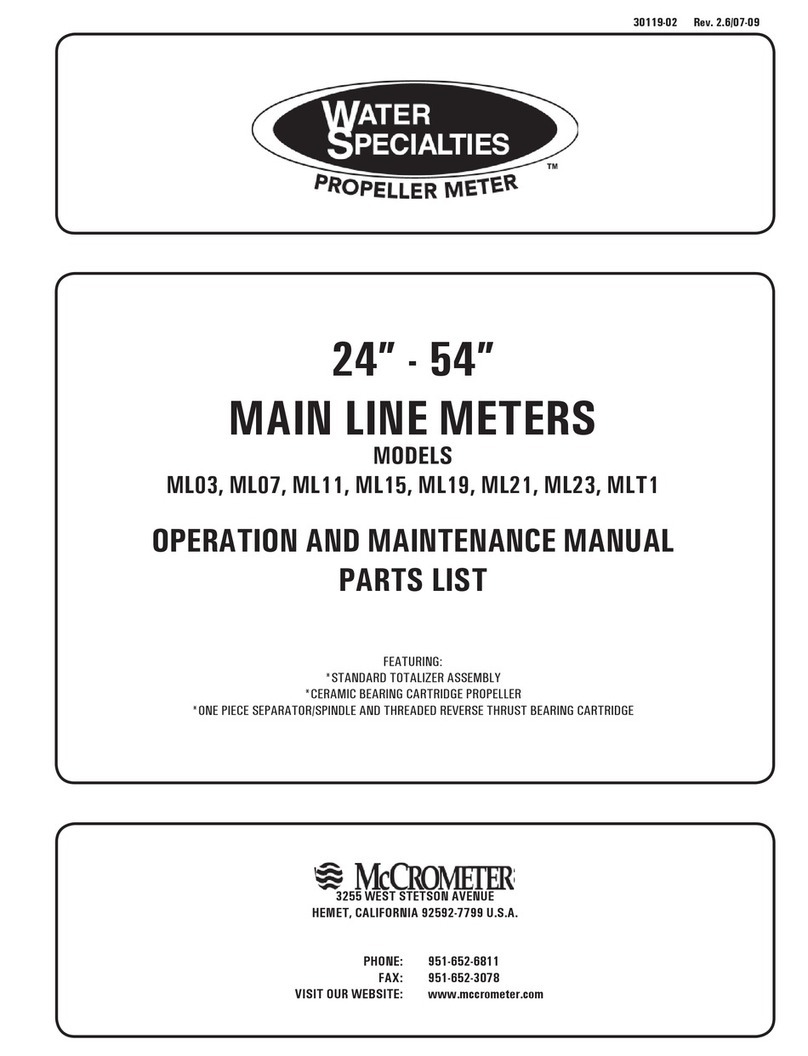
Water Specialties
Water Specialties Propeller meter ML03 Operation and maintenance manual
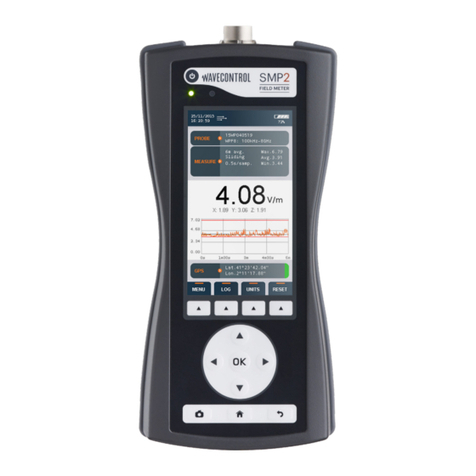
WAVECONTROL
WAVECONTROL SMP2 user manual
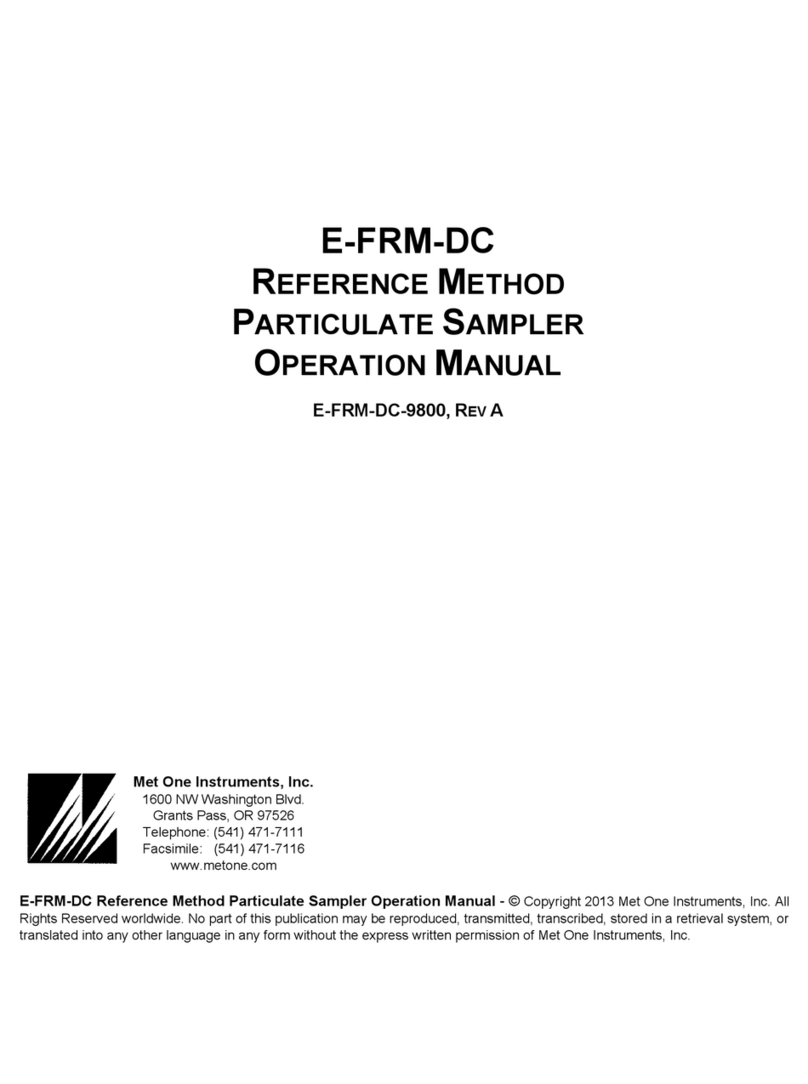
Met One Instruments
Met One Instruments E-FRM-DC Operation manual
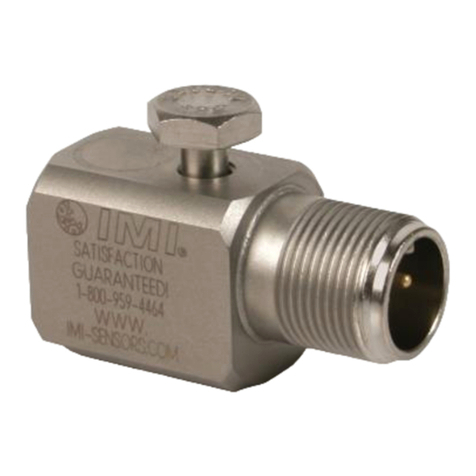
PCB Piezotronics
PCB Piezotronics IMI SENSORS TO602D01 Installation and operating manual
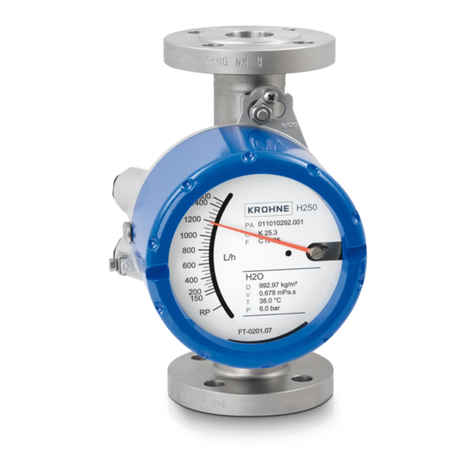
KROHNE
KROHNE H250 M40 Series Supplementary instructions
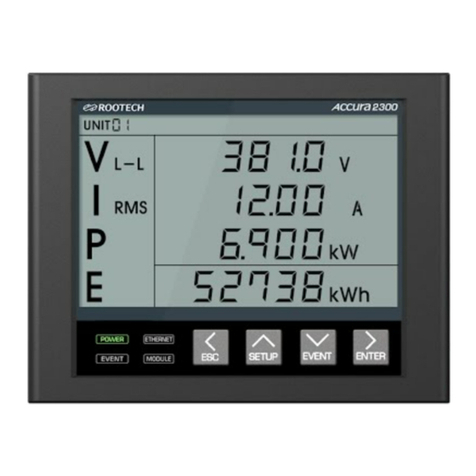
ROOTECH
ROOTECH Accura 2300 Quick setup guide
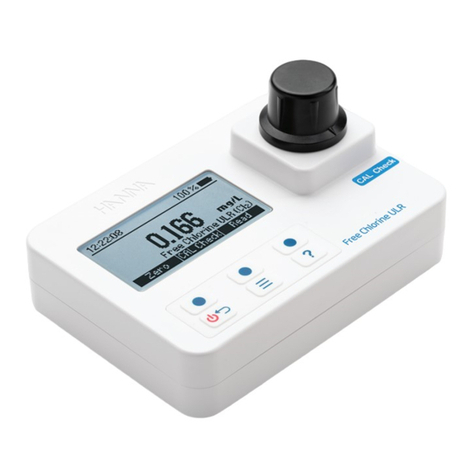
Hanna Instruments
Hanna Instruments HI97762 instruction manual
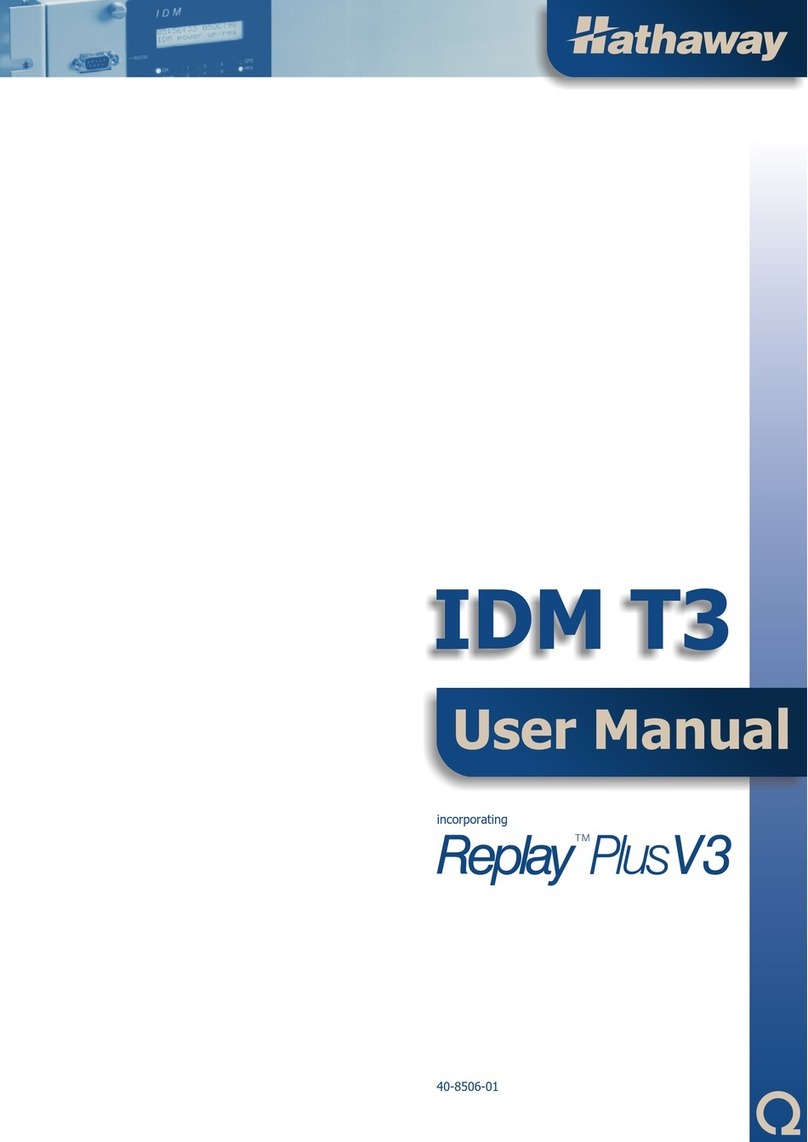
Hathaway
Hathaway Replay PlusV3 user manual
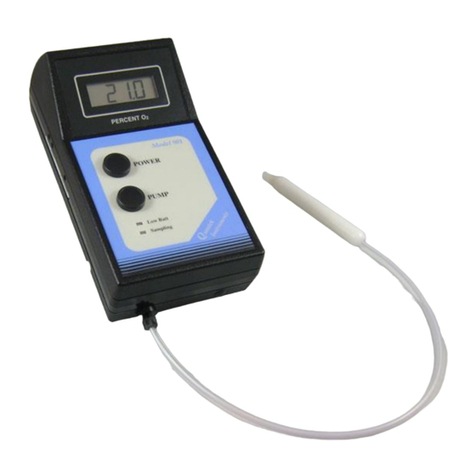
Quantek
Quantek 901 operating instructions