GMV 3010 Quick start guide

GMV SPA
FLUID DYNAMICS EQUIPMENTS AND
COMPONENTS FOR LIFTS
UNI EN ISO 9001
Certified Company
1.01
ENG
English
3010 ¾” VALVE
SELL
TECH
WORK
CUST
USER
3010 ¾” VALVE MANUAL
INSTALLATION,USE AND MAINTENANCE
1 0991 497 EN
AVAILABLE WITH TANK TYPE
HL, HL DRY, HL 50 DRY, HLV, HLV 40 e GL

1 0991 497 EN - 24.03.2017
1.01
ENG
3010 ¾” VALVE MANUAL
INSTALLATION,USE AND MAINTENANCE
2 / 16
GMV Spa declines all responsibility in case you do not follow the instructions in this document.
In particular, disregarding these instructions,may cause safety problems in the installation and for the users.
INDEX
0 GENERAL SECTION 3
0.1 INTRODUCTION 3
0.1.1 DEFINITIONS 3
0.1.2 RULES REFERENCE 4
0.2 INSTALLATION RELATED DOCUMENTS 4
0.3 SAFETY PRECAUTION DURING INSTALLATION 4
0.4 TOOLING 4
0.5 GENERAL ORDERS 4
0.6 LIABILITY AND WARRANTY 5
0.7WARNINGS BEFORE THE INSTALLATION 5
0.8 CLEANING AND POLLUTION PROTECTION 5
1 FEATURES AND REQUIREMENTS 6
1.1 THE 3010 ¾” VALVE 6
1.2 THE FLUID 6
2 INSTALLATION OPERATIONS 6
2.1 HYDRAULIC CONNECTIONS 6
2.2 3010 ¾” VALVE DIMENSIONS 7
2.3 HYDRAULIC CIRCUIT 7
2.4 DECELERATION DISTANCES AND SIGNALS 8
2.5 ELECTRICAL CONNECTIONS 8
2.6 CONNECTION BOX 8
2.6.1 POWER UNITS WITH IMMERSED MOTOR 8
2.6.2 POWER UNITS WITH DRY MOTOR 8
2.7 HYDRAULIC CONNECTIONS 9
2.7.1 CONNECTION WITH HOSE 9
2.7.2 RIGID TUBECONNECTION 9
3 ADJUSTMENTS AND TESTS 9
3.1 ADJUSTMENT OF THE MINIMUM PRESSURE UPWARD –N°11 9
3.2 ADJUSTMENT OF THE OVERPRESSURE –N°1 9
3.3 ADJUSTMENT OF THE UPWARD ACCELERATION –N°4 10
3.4 ADJUSTMENT OF SLOW LEVELLING SPEED –N°2 10
3.5 ADJUSTMENT OF THE UPWARD HIGH SPEED –N°8 10
3.6 ADJUSTMENT OF THE DOWNWARD ACCELERATION –N°7 10
3.7 ADJUSTMENT OF THE DOWNWARD HIGH SPEED –N°9 10
3.8 ADJUSTMENT OF THE UPWARD AND DOWNWARD DECELERATION –N°3 10
3.9 PIPE RUPTURE VALVE (VC)TEST (IN THE VALVE BLOCK)–N°5 11
3.10 ADJUSTMENT OF THE MINIMUM RAM PRESSURE,VSMA –N°6 11
3.11 MANUAL LOWERING OPERATION (EMERGENCY ONLY)–BUTTON (MM) 11
3.12 ADJUSTMENT OF THE MAXIMUM PRESSURE -HAND PUMP 11
4 MAINTENANCE AND FAULT ANALYSIS 12
4.1 PROGRAMMED MAINTENANCE 12
4.2 PERIODICAL MAINTENANCE AND CHECKS TABLE 12
4.3 MAINTENANCE OPERATIONS 12
4.4 FAULT ANALYSIS 14
ENG
All rights reserved.
Any kind of exploitation in any form and by any means is forbidden without a written permission of GMV Spa.
GMV Spa, within technical or manufacturing progress, reserves the right to modify parts or this manual without notice.
Drawings, descriptions and data included in this manual are indicatives.
For all the data not included in this manual refer to the documents of any single part.
To guarantee the products security, do not use spare parts not genuine or not approved by GMV Spa.
GMV Spa will not assume any responsibility if the instructions included in this manual are not observed.
DT 24/03/2017
PR 24/03/2017
GF 24/03/2017
WARNING –IMPORTANT

ENG
1.01
1 0991 497EN -24.03.2017
3 / 16
3010 ¾” VALVE MANUAL
INSTALLATION,USE AND MAINTENANCE
Support and informations:
FLUID DYNAMICS EQUIPMENTS AND
COMPONENTS FOR LIFTS
UNI EN ISO 9001
Certified Company
GMV SPA
Via Don Gnocchi, 10 - 20016 PERO –Milano (Italy)
TEL. +39 02 33930.1 - FAX +39 02 3390379
http://www.gmv.it - e-mail: info@gmv.it
Visit www.gmv.it to check for updates of this document and other product information from
GMV.
Main acronyms and abbreviations
1
Pressure safety valve adjustment (p.max)
2
Levelling / slow speed adjustment (up/down)
3
Deceleration adjustment (up/down)
4
Upward start adjustment
5
Screw for rupture valve test ( EN 81.20)
6
Minimum ram pressure adjustment
7
Downward start adjustment
8
High speed adjustment
9
Down speed compensator (empty/full load)
10
Hand pump max. pressure adjustment
11
Minimum upward pressure adjustment
RUB
Shut-off valve for pressure gauge exclusion
MAN
Pressure gauge
MM
Manual lowering button
PAM
Hand pump
V
Hand pump air purge screw
VP
Pilot valve
CHK
Check valve
VMD
Downward solenoid valve
VML
Jump speed solenoid valve (upward/downward)
PRS
Gauge fitting
S4
Fixed filer (don’t remove)
ISP
Inspection gauge fitting (EN 81.20)
S
Ball valve
PRF
Blocking screw (don’t remove)
0GENERAL SECTION
0.1 INTRODUCTION
0.1.1 DEFINITIONS
NOTES
Indicates information which contents must be seriously taken in consideration.
WARNING
Indicates that the described operation may cause, damages to the system or physical damages if
performed without complying with the safety standards.

1 0991 497 EN - 24.03.2017
1.01
ENG
3010 ¾” VALVE MANUAL
INSTALLATION,USE AND MAINTENANCE
4 / 16
0.1.2 RULES REFERENCE
For all definitions not included in this manual please refer to rules and local laws in force, following, particularly:
- EN 81-2: Safety rules for the construction and installation of lifts,
- UNI–EN-ISO-14121: Safety of machinery - Principles for risk assessment,
- ISO 3864: Safety colours and safety signs
- MD 2006/42: Machine directive.
0.2 INSTALLATION RELATED DOCUMENTS
The documents to use for the installation are those required by the EN81-20:2014 and by the rules in force,
particularly the following:
- THIS INSTALLATION MANUAL
- WIRING AND HYDRAULIC DIAGRAMS (EN81-20 7.3.2.A.6 AND 7).
All the documentation for a correct and safe installation must be stored by the installation responsible.
Please remember that this documentation is considered part of the plant and must be complete, well stored and
unabridged in every part.
In order to maintain the readability, the documentation shouldn’t be damaged and shouldn’t have missing parts.
Moreover, do not tear or deteriorate sheets during consulting.
0.3 SAFETY PRECAUTION DURING INSTALLATION
WARNING
Before starting all kind of installation operation:
ALWAYS verify that all the safety devices, mechanical or electrical, are active and working properly.
0.4 TOOLING
Use standard building-yard tooling for the installation.
0.5 GENERAL ORDERS
The valves shall be maintained in good working order in accordance with the Standards.
To this effect, regular maintenance of the installation shall be carried out, to ensure, in particular, the safety of
the installation.
The safety of an installation shall take into account the ability to be maintained without causing injury or damage
to health.
Regular maintenance of the installation shall be carried out to ensure the reliability of the installation.
The access and the associated environment shall be maintained in good working order.
The competence of the maintenance person within the maintenance organization shall be continuously updated.
NOTE
We inform the owner of the installation that the qualification of the maintenance organization

ENG
1.01
1 0991 497EN -24.03.2017
5 / 16
3010 ¾” VALVE MANUAL
INSTALLATION,USE AND MAINTENANCE
needs to be in conformity with the rules applicable in the country in which the installation operates;
if no rules exist, the qualification can be ensured by a certified EN ISO 9001 quality system
supplemented if necessary to take into account the specific features of the installation.secondo le
EN ISO 9001.
0.6 LIABILITY AND WARRANTY
These instructions are intended for people with experience in installation, adjustment and maintenance of
hydraulic lifts.
GMV disclaims any liability for damage caused by improper or different use from what described in these
instructions or inexperience or carelessness of those responsible to assemble, adjust or repair hydraulic
components.
GMV's warranty is voided if you install any components or parts not original, if you make unauthorized changes
or modifications or made by unauthorized or unqualified personnel.
Unless otherwise indicated, the following situations are forbidden for safety reasons:
- Any product modification;
The installation of the product for purposes other than those described;
Damage to the joints;
Carrying out maintenance or inspections improper or inadequate;
The use of improper accessories and not original spare parts or materials from GMV.
0.7 WARNINGS BEFORE THE INSTALLATION
In these instructions the major points concerning the safety and prevention will be marked with the following
symbols:
General warning.
Warning high risk of danger. Risk of injury (e.g., crushing, sharp edges, protrusions, etc..).
Warning risk of electrical damage (exposed parts).
Beyond the instruction manual, it should take into account national standards, laws, regulations and other rules
on accident prevention and environmental protection, and special operating conditions, such as the use of the
lift, tools and equipment working.
The installation and repair technicians are primarily responsible for their own safety.
This "Manual" applies to the entire life of the facility, during normal operation, testing and maintenance to be an
integral part of the system, so it should be kept in a safe place by the installer.
The installation, commissioning and maintenance of the system may only be performed by trained personnel.
Before starting the installation work:
Use safety devices to protect personnel and prevent falls;
Cover (safely) openings in walls and floor;
Use the tools and means preventing accidental falls;
The gaps should be closed, use appropriate warning signs.
Work on electrical equipment must be performed by an electrician or other qualified personnel.
0.8 CLEANING AND POLLUTION PROTECTION
Impurities and dirty inside the equipment may cause malfunction of the hydraulic system and premature wear.
All disassembled items for inspection or repair, as well as pipes and accessories should be thoroughly cleaned
before re-assembled.

1 0991 497 EN - 24.03.2017
1.01
ENG
3010 ¾” VALVE MANUAL
INSTALLATION,USE AND MAINTENANCE
6 / 16
The oil that came out of the circuit during the repair must be properly collected (rags, ....) and treated
appropriately. Do not throw freely in the environment.
1FEATURES AND REQUIREMENTS
1.1 THE 3010 ¾” VALVE
,
The 3010 ¾” valve is a two speed mechanical valve with the following features:
pump flow : 12-23 l/min
pressure range 12-50 bar
oil temperature range : 10 –70°c
1.2 THE FLUID
GMV use and recommend an hydraulic fluid that :
- Thanks to classification as ISO-L-HFDU category according to ISO 6743-4 and
its biodegradability index > 70%, according to standard OECD 301 B, is
acceptable from an environmental point of view.
- Thanks to the synthetic base and its viscosity index (>180), higher than the
traditional mineral oil, allowing greater stability, ensuring better performance
against wear and aging on systems as lifts for persons and goods, in
accordance with the environmental directive 2006/118/EC.
- Thanks to a flash point above 300°C compared to the 140°C of the traditional
mineral oil it is safer and reduces the risk of fire.
2INSTALLATION OPERATIONS
WARNING
During installation operations never disable safety devices or directly power the pump motor.
2.1 HYDRAULIC CONNECTIONS
- Before starting the installation, you should verify the structural and spatial limits within which you will
work. Consider the mounting methods you are going to use. It is therefore advisable to consider in
advance all conditions affecting the different working procedures and therefore do not take any action
without first considering the consequences. Make sure that the products received are complete with
everything you need and that all products and parts are not damaged during transport.
- Data written on the label should be compared with the order form.
- During the storage period, keep the material in the original container, protected from weather and direct
sun exposure, in order to prevent accumulation of water / condensation which may occur inside the
package. (See Technical data for the range of temperature and humidity). After removing the product,
the packaging material must be properly disposed of, as required by local law. Before recycling should
verify the nature of the various materials and recycle as prescribed.
- GMV is not responsible for any damages caused by manual modifications (or changes) of the
packaging material done by others.
- Any use of the facility, which is different from the original proposal situation should be discussed with
GMV. An application or use not permitted by GMV (patent legal reasons, technical or otherwise) is
under the installer responsibility and may affect the warranty.
- For the installation or replacement of the hydraulic system components, observe the following points
- Always place the elevator on the puffers;
- Make sure the elevator cannot operate accidentally, blocking the main electrical switch;
- Before opening any part of the hydraulic circuit, remove or unscrew the caps is always necessary to
bring the oil pressure to zero.
- In case of welding operations,be care to prevent any contact between the oil and the piston rod, its
seals and other resilient parts that could be damaged;

ENG
1.01
1 0991 497EN -24.03.2017
7 / 16
3010 ¾” VALVE MANUAL
INSTALLATION,USE AND MAINTENANCE
- Remove the spilled oil, remove the oil leaks, keeping equipment clean so leaks can be detected and
easily removed.
2.2 3010 ¾” VALVE DIMENSIONS
250
175
250
2.3 HYDRAULIC CIRCUIT
1
Pressure safety valve adjustment (p/max)
2
Levelling / slow speed adjustment (up/down)
3
Deceleration adjustment (up/down)
4
Upward start adjustment
5
Screw for rupture valve test ( EN 81.20)
6
Minimum ram pressure adjustment
7
Downward start adjustment
8
High speed adjustment
9
Down speed compensator (empty/full load)
10
Hand pump max. pressure adjustment
11
Minimum upward pressure adjustment
RUB
Shut-off valve for pressure gauge exclusion
MAN
Pressure gauge
MM
Manual lowering button
PAM
Hand pump
V
Hand pump air purge screw
VP
Pilot valve
CHK
Check valve
VMD
Downward solenoid valve
VML
Jump speed solenoid valve (upward/downward)
PRS
Gauge fitting
S4
Fixed filer (don’t remove)
ISP
Inspection gauge fitting (EN 81.20)
S
Ball valve
PRF
Blocking screw (don’t remove)

1 0991 497 EN - 24.03.2017
1.01
ENG
3010 ¾” VALVE MANUAL
INSTALLATION,USE AND MAINTENANCE
8 / 16
2.4 DECELERATION DISTANCES AND SIGNALS
CAR SPEED
VN[m/s]
DISTANCE C-E
UP [m]
DISTANCE G-I
DOWN [m]
0 < 0.15
0.10
0.15
0.10 < 0.15
0.15
0.20
0.16 < 0.30
0.20
0.30
2.5 ELECTRICAL CONNECTIONS
Electrical connections must be performed by qualified and experienced personnel.
Before doing any work is necessary to disconnect all electrical power by opening the main switch.
Power wires must be of sufficient section to support the required current and appropriate insulation for the
voltage of the mains.
Wires must not come in contact with hot parts.
The ground wire should always be connected to the screw marked with the appropriate symbol.
2.6 CONNECTION BOX
Power units with immersed motor have the motor connection box located next to valve block.
Power units with dry motor have the motor connection box located in the motor itself.
2.6.1 POWER UNITS WITH IMMERSED MOTOR
W2 U2 V2
U1 V1 W1
2.6.2 POWER UNITS WITH DRY MOTOR

ENG
1.01
1 0991 497EN -24.03.2017
9 / 16
3010 ¾” VALVE MANUAL
INSTALLATION,USE AND MAINTENANCE
2.7 HYDRAULIC CONNECTIONS
12 ÷ 23
3010 ¾”
1/2”
½ X ¾
¾”
/
¾” X ¾
3/4”
½ X M30
NON GMV
22
¾” X M30
WARNING
Be care to keep clean the hose.Dirty inside may damage the piston and valve seal to affect the proper
system operating.
2.7.1 CONNECTION WITH HOSE
- Remove the end fitting of the ball valve, the nut and the locking ring.
- Make sure the terminal fitting is well secured to the shut-off valve.
- Clean and lubricate with oil the thread and the housing of the connector.
- Fix and tight the hose to the fitting.
2.7.2 RIGID PIPE CONNECTION
- Cut the end of the tube at 90° (use a hack saw, DO NOT USE
A TUBE CUTTER).
- Lightly file (make smooth) the inside and outside edges of the
pipe.Pay attention to avoid any chips into the pipe.
- make sure that there is no dirty inside the pipe,as this may
cause a damage to the gaskets (seals) of the piston and the
valves jeopardising the correct functionality of the system.
- Remove the nut and the compression-fitting ring from the
silencer joint.
- Insert the compression fitting ring as shown in the figure.
- Make sure that the silencer joint is tight.
- Clean and apply a thin layer of oil to the thread and the joint
area.
- Insert the tube to the 24°cone.
- Turn the nut to completely tighten the compression-fitting ring.
- Use two wrenches and tighten the nut until the ring comes in
contact with the pipe and no more rotation is possible.
3ADJUSTMENTS AND TESTS
See references on page 3
3.1 ADJUSTMENT OF THE MINIMUM PRESSURE UPWARD –N° 11
- Close the ball valve (S)
- Start the motor-pump (refer to the controller manual).
- Tighten screw (11) to get 5-6 bar pressure.
- Tighten the lock nut (11).
- Re-open the ball valve (S).
- The adjustment is finished.
3.2 ADJUSTMENT OF THE OVERPRESSURE –N° 1
- Open the shut-off valve of the manometer (RUB).
- Close the ball valve (S).
- Loosen the lock nut (1).

1 0991 497 EN - 24.03.2017
1.01
ENG
3010 ¾” VALVE MANUAL
INSTALLATION,USE AND MAINTENANCE
10 / 16
- Loosen the screw (1) two or three turns.
- Start the motor-pump (refer to the controller manual).
- Tighten screw (1) till get the desired maximum pressure (see technical report of the lift).
- Tighten the lock nut (1).
- Re-open the ball valve (S).
- The adjustment is finished.
3.3 ADJUSTMENT OF THE UPWARD ACCELERATION –N° 4
- Loosen the lock nut (4).
- Tighten screw (4) completely.
- Send the car upward, the car will not move.
- Loosen the screw (4) till you get the desired acceleration.
- Tighten the lock nut (4).
- The adjustment is finished.
3.4 ADJUSTMENT OF SLOW LEVELLING SPEED –N° 2
SLOW LEVELLING SPEED MUST BE 1/4-1/6 VS HIGH UPWARD
SPEED AND THE CAR SHOULD RUN THE SLOW SPEED RANGE
CONTINUOUSLY WITHOUT RIPPING.
- Loosen the lock nut (2).
- Tightening the screw (2) reduces the speed (D-E upward, H-I
downward). Loosening the screw (2) increases the speed.
- Tighten the lock nut (2).
- The adjustment is finished.
3.5 ADJUSTMENT OF THE UPWARD HIGH SPEED –N° 8
- Start to send the car upward.
- Loosen the lock nut (8).
- Tighten the screw (8) till you hear the oil returning to the tank, then loosen one turn to close.
- Tighten the lock nut (8).
- The adjustment is finished.
- If needed, in those lifts where the speed must be limited (for example Home Lift con V=0,15 m/s, other
lifts), just gradually tighten the screw 8 to mach the requested speed value.
3.6 ADJUSTMENT OF THE DOWNWARD ACCELERATION –N° 7
- Loosen the lock nut (7).
- Tighten screw (7) completely.
- Send the car downward, the car will not move.
- Loosen slowly the screw (7) till you get the desired acceleration.
- Tighten the lock nut (7).
- The adjustment is finished.
3.7 ADJUSTMENT OF THE DOWNWARD HIGH SPEED –N° 9
- Take out the protection nut of the screw (9)
- Loosen the lock nut (9).
- Tighten the screw (9) to increase the speed, loosen the screw (9) to reduce the speed.
- Tighten the lock nut (9).
- The adjustment is finished.
3.8 ADJUSTMENT OF THE UPWARD AND DOWNWARD DECELERATION –N° 3
You get the maximum deceleration with the screw (3) completely open.
- Loosen the lock nut (3).
- Tighten the screw (3) to reduce the deceleration, loosen the screw (3) to increase the deceleration.

ENG
1.01
1 0991 497EN -24.03.2017
11 / 16
3010 ¾” VALVE MANUAL
INSTALLATION,USE AND MAINTENANCE
- Tighten the lock nut (3).
- The adjustment is finished.
3.9 PIPE RUPTURE VALVE (VC) TEST (IN THE VALVE BLOCK) –N° 5
WARNING
Before doing this test, the pipe rupture valve mounted on the piston should be adjusted (refer to VC
manual)
- Send the car with full load to the highest floor.
- Once the car has stopped.
- Loosen the lock nut (5) to test the rupture valve
- Completely tighten the screw n.5 .
- Call the car to the lowest floor.
- The test is finished.
NOTE:WHEN THE CAR DOWNWARD SPEED MATCHES THE INTERVENTION FLOW,THE
RUPTURE VALVE CLOSES TO STOP THE CAR (IN CASE OF BY-PASS RUPTURE VALVE,THE
CAR LOWERING CONTINUES SLOWLY).IN CASE THE RUPTURE VALVE DOES NOT
CLOSE,FOLLOW THE FACTORY INSTRUCTIONS TO REDUCE ITS INTERVENTION SPEED TO
BE ABLE TO RESTART THE TEST.
- Completely loosen the n.5 .
- During the standard car downward we do not have any intervention of the rupture valve
- Completely tighten the lock nut (5).
- The test is finished.
3.10 ADJUSTMENT OF THE MINIMUM RAM PRESSURE, VSMA (2:1 SYSTEMS) N° 6
Only in installations with traction 2:1.
- Close the ball valve (S).
- Press the manual lowering button (MM) to release pressure.
- Check the pressure on the manometer (MAN) is around 6 bar.
- If the pressure it not correct, adjust screw (6).
- The adjustment is finished.
3.11 MANUAL LOWERING OPERATION (EMERGENCY ONLY) –BUTTON (MM)
- Press the manual lowering button (MM) to send downward the car to the unlock door area
-
3.12 ADJUSTMENT OF THE MAXIMUM PRESSURE - HAND PUMP
- Close the ball valve (S).
- Verify that the suction tube is immersed in the oil.
- Loosen the screw (V) two or three turns to bleed the air.
- Push the lever several times till the oil starts flowing through the
screw (V).
- Tighten the screw (V) completely.
- Loosen the lock nut (10)
- Loosen the screw (10) two or three turns.
- Open the shut-off valve for pressure gauge exclusion (RUB).
- Push the hand pump lever to reach the maximum pressure,
adjust the screw (10) till the value is 2,3 times the full load
pressure (refer to the lift technical report).
-
Example:
If full load pressure is 35 bar, screw (10) should be adjusted to:
35 x 2,3 = 80,5
- When the pressure is correct.
- Tighten lock nut (10).
- Open the ball valve (S).
- The adjustment is finished.

1 0991 497 EN - 24.03.2017
1.01
ENG
3010 ¾” VALVE MANUAL
INSTALLATION,USE AND MAINTENANCE
12 / 16
4MAINTENANCE AND FAULT ANALYSIS
4.1 PROGRAMMED MAINTENANCE
For a correct and safe lift use, it is necessary to make a preventive programmed maintenance, following a fixed
plan.
To define the periodical maintenance frequency, you should consider more events, particularly :
- Number of travel per year
- Travelling and stopping periods
- Age and condition of the lift
- Site and type of the building in which the lift travel
- Passengers and goods demand
- Inside and outside working condition (climate, vandalism, etc.)
In the next table, parts are shared in groups and for each group is shown the type of check and its frequency
recommended. You can find the detailed instructions to perform the operational checks, inside the maintenance
schedules, in the following pages
Please, note that all checks are applicable only if the part is really installed.
4.2 PERIODICAL MAINTENANCE AND CHECKS TABLE
Operation checks
Recommended maximal Frequency
INSTALLATION
MONTH
YEARS
Valve gaskets seal
6
Oil level check up
6
Characteristics of the oil
6
Motor protection operation
6
Filters
1
Pressure check
6
Pressure gauge shut off (6)
6
Pressure test (static pressure x2)
6
Ball valve seal
6
Labels, signs and schemes
6
Overall check-up
5
4.3 MAINTENANCE OPERATIONS
What to do:
Valve gaskets seals
- At the end of installation, and during check-ups, verify the gasket seals, in the following way: with the oil at
room temperature close the ball valve (S) and open the pressure gauge shut off (RUB). Check that the
pressure gauge reading on pressure gauge should not drop more than 4 bar in 5 minutes.
Oil level check-up.
- With the elevator at the highest floor, check, using dipstick or level indicator, that the oil level is above the
minimum level and (if the motor is immersed the motor should be fully covered in oil).
Oil properties.
- Visually check the appearance of the oil, it should not have changed. This operation should be performed
after leaving the elevator stopped a few hours.
Motor protection functionality
- Disconnect one terminal of the thermistors, and check that the motor protection working properly.
Filter
- Check the main filter mounted inside the VRP spool and clean it if is necessary.
Pressures check
- Check static and dynamic (working) pressure at the end of installation. Check regularly that all values of
these parameters remain unchanged.

ENG
1.01
1 0991 497EN -24.03.2017
13 / 16
3010 ¾” VALVE MANUAL
INSTALLATION,USE AND MAINTENANCE
.
Check for the exclusion shut-off pressure gauge
Pressure gauge shut off (RUB)
Close the ball valve (S), open the pressure gauge shut off (RUB) and fully discharge the pressure using electro-
valve (VMD). Close the pressure gauge shut off (RUB) open the ball valve (S) and check that the level shown
on pressure gauge is zero
Pressure test (static pressure x2)
This test assures you about the integrity of parts under pressure, including those which cannot be visually
checked.
To correctly carry out this test follow these instructions:
- Close the pressure gauge exclusion valve.
- Close the ball valve (S). Unscrew the pressure gauge (MAN).
- Connect the flow of the testing hand pump (M) instead of the pressure gauge (G1/4”)
- Open the pressure gauge exclusion valve.
- Open the ball valve (S)
- Open the ball valve of the hand-pump for about a minute.
- Close it again
- Close the ball valve (S) again.
- Continuing with the hand pump, reach the desired pressure value, controlling with the pressure gauge
- After the test,completely unload the pressure pushing with a screwdriver on the VMD valve.
- Close the pressure gauge exclusion valve.
- Disconnect the hand pump
- Screw the pressure gauge (MAN).
Ball valve seal
- Close the ball valve (S) and open the pressure gauge shut off (RUB). Fully discharge the pressure-using
valve (VMD). Check that the pressure shown on pressure gauge (MAN) is zero.
Labels, signs and schemes
- Check that all the tags and diagrams are in place and legible (oil data label, emergency operation manual,
electrical diagram and hydraulic power unit schemes).
Overall check-up
- Perform an overall check up of the power unit. When the overall check-up ends, check all the settings for
the power unit start-up.
- Replace or restore all the components not correctly working.
NOTE
In case of oil replacement, do not throw the oil away in the environment, but give it to oil recycling
company.
NOTE
When the power unit in no longer required, don’t throw it away, but give it to a recycling company or to
the manufacturer.

1 0991 497 EN - 24.03.2017
1.01
ENG
3010 ¾” VALVE MANUAL
INSTALLATION,USE AND MAINTENANCE
14 / 16
4.4 FAULT ANALYSIS
Fault
Possible cause
Possible solution
The car doesn’t
keep the floor
level, pressure
loss.
DEVICES : VRP,
VMD, VSMA, PAM
VRP
Remove the spool and check the cleanliness of the closure.
If the seal is damaged and/or worn, replace it. Reassemble the
spool checking that moves well into its housing.
VMD
Remove the solenoid and control the movement of the plunger
(approx 2 mm). Check the cleanliness of the closure and the
good condition of the sphere. Eventually once cleaned, remark
the closing, with the sphere itself.
Hand pump PAM
Check the closing of the check valve of the hand pump.
Car with full load
doesn't start
upward.
DEVICES : VS
Verify maximum pressure control safety.
Tighten the screw (1) to increase the discharge pressure of the
VS.
Delay too big on
start upward.
DEVICES : VP
Check the adjustment of the screw (4). Clean filters and
restrictors. Check the perfect sliding and closure cleanliness of
the spool (VP). If no improvement is obtained, replace the valve
VP.
The downward
speed is less
than the upward
speed.
DEVICES :
VRF, VMD,
COMPENSATOR
VRF
Check the adjustment of the screw (8).
VMD
Check the cleanliness of filters and restrictors.
SPEED COMPENSATOR
Check the perfect sliding of the spool.
If it’s necessary, tighten the screw (9) to increase downwards
speed.
The lift only runs at
high speed, both
upward and
downward.
DEVICES :
VML, VRF
VML
Check that the screw (3) is open. Clean filters and restrictors.
VRF
Check the perfect sliding of the spool (could be locked in the
open position). Clean the housing and the spool.
The lift only runs at
slow speed, both
upward and
downward.
DEVICES :
VML, VRF
VML
Check that the solenoid valve works in manual mode (with a
screwdriver pushing the nucleus).
Check the electrical connections to the solenoid. Clean filters
and restrictors. Check the travel of the plunger (about 2 mm).
VRF
Check the perfect sliding of the spool (could be locked in the
closed position). Clean the housing and the spool.
The car doesn't
stop correctly at
the floor level, it
goes below and it
has to relevel.
The slow speed
is too high or it
hasn't changed.
DEVICES : VMD,
VRFP
VMD
Check the perfect sliding of the solenoid nucleus. Clean the
housing and the spool.
VRFP
Check that the screw (5) is fully open.
Unmount and check the perfect sliding of the spool.

ENG
1.01
1 0991 497EN -24.03.2017
15 / 16
3010 ¾” VALVE MANUAL
INSTALLATION,USE AND MAINTENANCE

1 0991 497 EN - 24.03.2017
1.01
ENG
3010 ¾” VALVE MANUAL
INSTALLATION,USE AND MAINTENANCE
16 / 16
Doc. n° 1 0991 497 Rev. 1.00 - 24.03.2017 File: 3010 3_4_10991497EN.doc
FLUID DYNAMICS EQUIPMENTS AND COMPONENTS FOR LIFTS
UNI EN ISO 9001
Certified Company
GMV SPA
Via Don Gnocchi, 10 - 20016 PERO –Milano (Italy)
TEL. +39 02 33930.1 - FAX +39 02 3390379
Table of contents
Other GMV Control Unit manuals
Popular Control Unit manuals by other brands
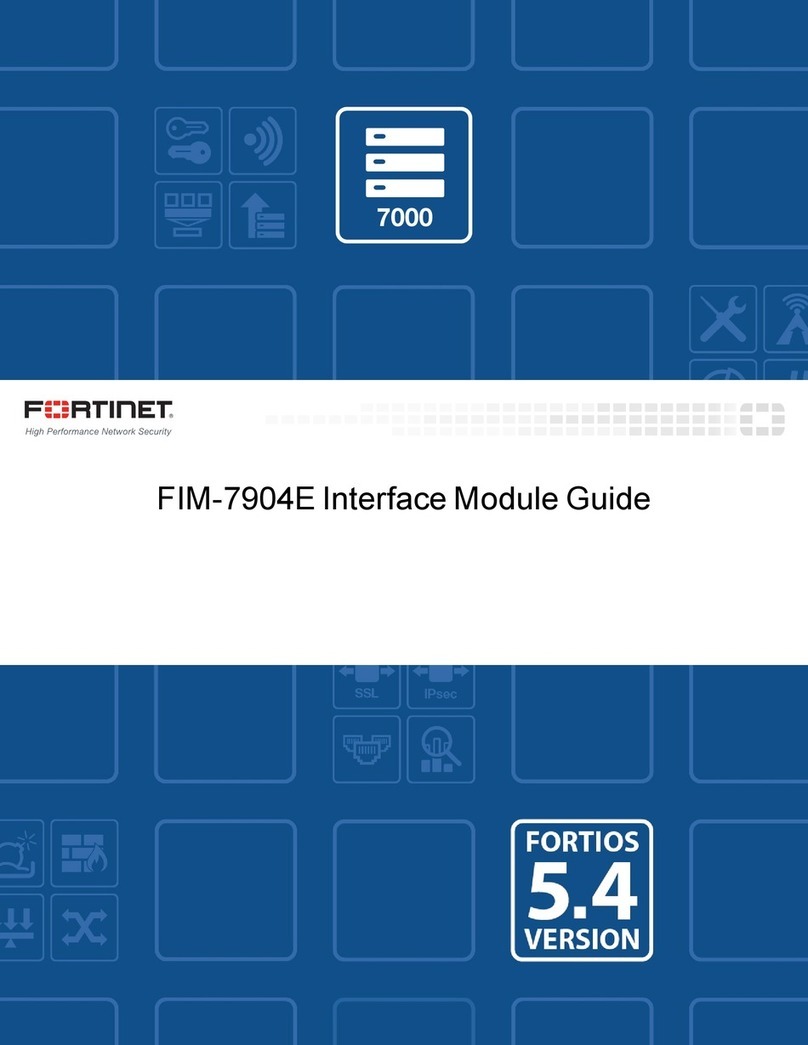
Fortinet
Fortinet FIM-7904E Guide

Panasonic
Panasonic CARICAM AU-VSHL2G operating instructions
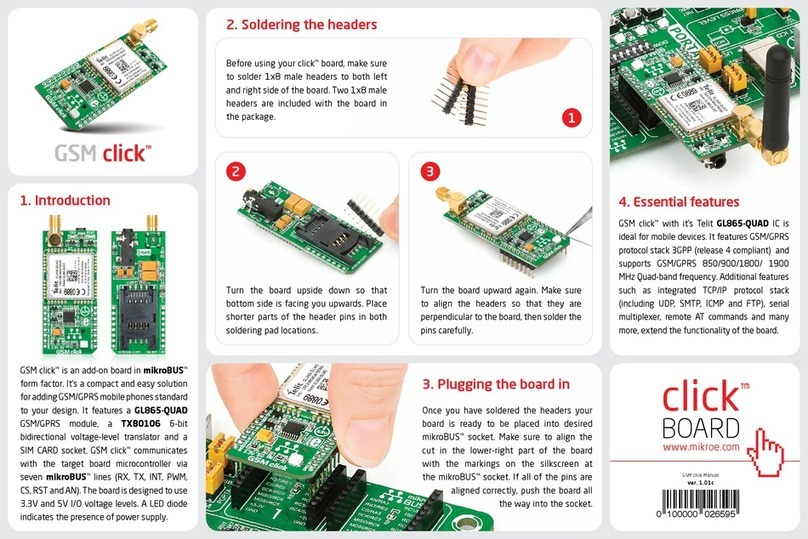
MicroElektronika
MicroElektronika GSM click manual
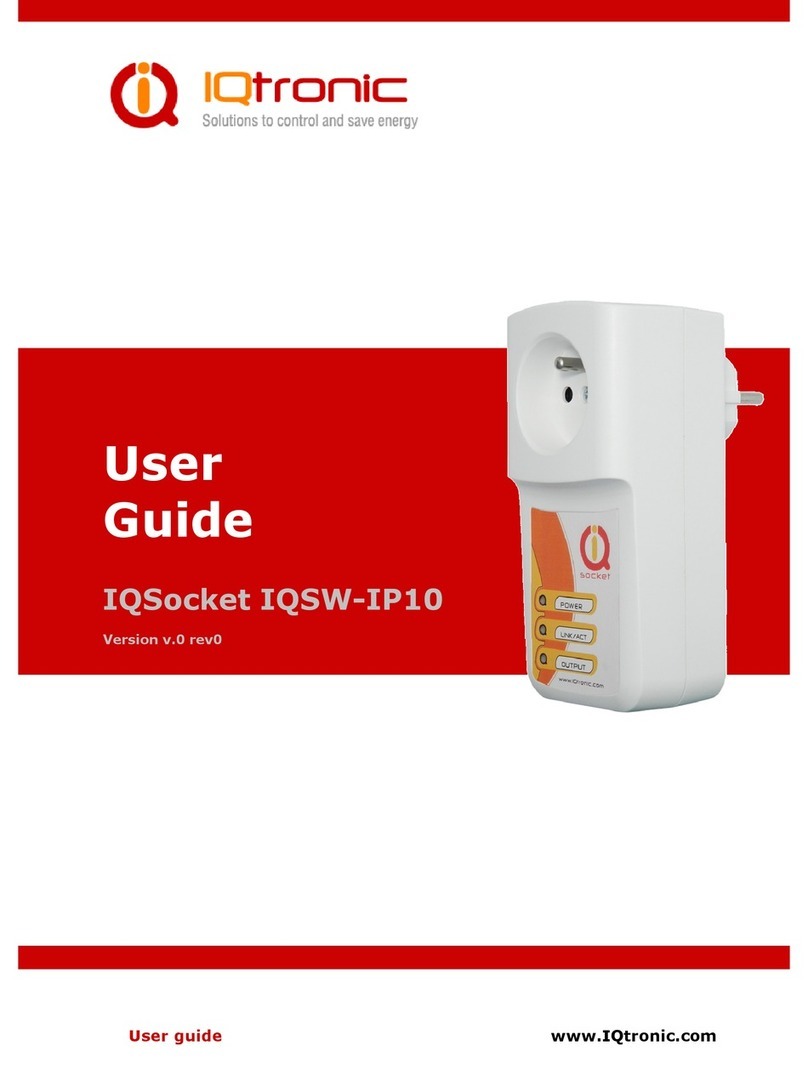
iQtronic
iQtronic IQsocket IQSW-IP10 user guide
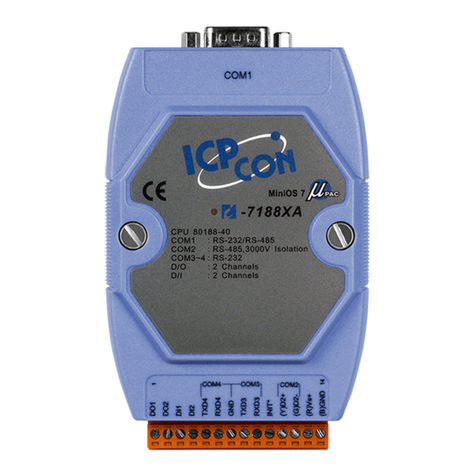
ICP DAS USA
ICP DAS USA I-7188XA quick start guide
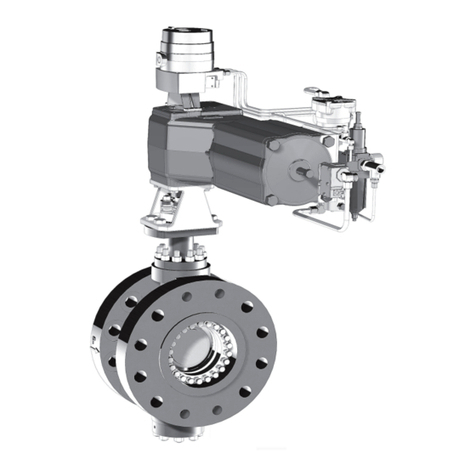
Metso
Metso Neles BW Series Installation maintenance and operating instructions