HADEF 16/12-EX Assembly instructions

5.52.190A.01.01.04
Rev.04
HADEF Spur Gear Hoist
Type 16/12-EX
Explosion proof design
II 2G Ex h IIB T3 Gb or II 2D Ex h IIIA T200°C Db
DANGER!
Not to be used with IIC gases and IIB gases hydrogen sulphide and ethylene oxide and
light metal and shock sensitive dusts.
It is not allowed to use the equipment in area at risk from explosion where gas AND
dust does both exist at the same time!
Installation, Operating and
Maintenance Instructions

2
5.52.190A.01.01.04
NOTICE!
The installation or mounting instructions for incomplete machines you’ll find in chapter “Installation”
o
by Heinrich de Fries GmbH
Heinrich de Fries GmbH, Gauss Str. 20, D-40235 Düsseldorf
Heinrich De Fries GmbH will be named HADEF in the following text.
Original operating- and maintenance instructions in German language.
Translation in other languages is made of the German original.
A copy may be requested in writing or is available for download on www.hadef.com
Subject to changes.
Table of Contents
1Information..........................................................................................3
2Safety...................................................................................................4
2.1 Warning notice and symbols............................................................................................4
2.2 Duty of care of the owner..................................................................................................4
2.3 Requirements for the operating personnel.....................................................................5
2.4 Appropriate use.................................................................................................................5
2.5 Basic safety measures......................................................................................................6
2.6 Explosion protection.........................................................................................................8
3Transport and Storage .....................................................................11
3.1 Transport..........................................................................................................................11
3.2 Safety device for transport .............................................................................................11
3.3 Storage .............................................................................................................................11
4Description........................................................................................11
4.1 Areas of application ........................................................................................................11
4.2 Design...............................................................................................................................11
4.3 Functions..........................................................................................................................12
4.4 Important components....................................................................................................12
5Technical data...................................................................................12
6Installation.........................................................................................12
6.1 Trolley...............................................................................................................................12
6.2 Tools.................................................................................................................................13
7Control...............................................................................................13
7.1 Brake and pawl ................................................................................................................13
8Commissioning.................................................................................14
8.1 General .............................................................................................................................14
8.2 Load chain........................................................................................................................14
9Safety check......................................................................................14
10 Functional test..................................................................................14
10.1 Checks before the initial start-up...................................................................................14
10.2 Functional test.................................................................................................................15
11 Maintenance......................................................................................15

5.52.190A.01.01.04
3
11.1 General............................................................................................................................. 15
11.2 Monitoring........................................................................................................................15
11.3 Replacing the load chain................................................................................................ 15
12 Inspection ......................................................................................... 15
12.1 Periodic checks...............................................................................................................15
12.2 Checking the load chain................................................................................................. 16
12.3 Checking the load hook.................................................................................................. 17
12.4 Check of the pawl............................................................................................................17
12.5 Check of the brake system.............................................................................................17
12.6 Check of the suspension bolt ........................................................................................ 18
13 Service............................................................................................... 18
13.1 Load chain ....................................................................................................................... 18
13.2 Pulleys..............................................................................................................................18
13.3 Load hook ........................................................................................................................18
13.4 Gear ..................................................................................................................................19
13.5 Gear spring pressure brake ........................................................................................... 19
13.6 Overload protection ........................................................................................................ 19
13.7 Lubricant - Selection....................................................................................................... 19
13.8 Lubricant for food industry –Selection (as option*)....................................................19
14 Trouble .............................................................................................. 19
15 Remedy ............................................................................................. 20
16 Decommissioning ............................................................................ 20
16.1 Temporary decommissioning ........................................................................................ 20
16.2 Final decommissioning/disposal...................................................................................20
1 Information
The products meet European Union requirements, in particular the valided EU Machine Directive.
The entire company works acc. to a certified quality assurance system as per EN ISO 9001.
The production of components at our work is subject to strict, intermediate checks.
After assembly, the products are subject to a final test with overload.
For the operation of hoists, the national accident prevention apply in Germany, amongst others.
Lifting equipment for use in areas prone to explosion complies with current legislation, standards and
regulations and is classified in the applicable Ex-protection class.
The stated performance of the devices and meeting any warranty claims require adherence to all instructions
in this manual.
Before delivery, all products are packed properly. Check the goods after receipt for any damage caused
during transport. Report any damage immediately to the forwarding agent.
This manual serves for safe and efficient use of this hoist. Illustrations serve to explain something and may
differ from the illustration of the existing unit as they only serve as an example.
Documentation of component manufacturers that may be supplied additionally, must be observed, in case of
differences between these documentation and our manuals, the specification of the our manual must be
observed.
NOTICE!
We refer to the prescribed equipment tests before initial start-up, before putting back into operation and the
regular periodic inspections.
In other countries any additional national regulations must be observed.

4
5.52.190A.01.01.04
2 Safety
DANGER!
To assess the intended use of the devices correctly, the user must carry out an Ex-zone
classification.
The classification must be carried out in accordance with all current legislation, standards and
regulations for areas prone to explosion!
2.1 Warning notice and symbols
Warnings and notice are shown as follows in these instructions:
DANGER!
This means that there is a high risk that leads, if it is not avoided, to death or severe injury.
WARNING!
This means that there is a risk that could lead, if it is not avoided, to death or severe injury.
CAUTION!
This means that there is little risk that could lead, if it is not avoided, to slight injury or damage to the device or its
surrounding.
NOTICE!
Gives advice for use and other useful information.
Danger from electricity.
Danger from explosive area.
2.2 Duty of care of the owner
DANGER!
Failure to follow the instructions of this manual can lead to unpredictable hazards.
For any resulting damage or personal injury, HADEF assumes no liability.
The unit was designed and built following a risk analysis and careful selection of the harmonized standards
that are to be complied with, as well as other technical specifications. It therefore represents state-of-the-art
technology and provides the highest degree of safety.
Our delivery includes the hoist supplied beginning at its suspension and ending at the load hook and if
supplied with control, the control line/hose that leads to the hoist. Further operating material, tools, load
attaching devices as well as main energy supply lines must be assembled according to the valid rules and
regulations. For explosion-proof equipment, all these parts must be approved for use in area prone to
explosion, or they must be suitable for use in area prone to explosion. The owner is responsible for this.
However, in everyday operation this degree of safety can only be achieved if all measures required are
taken. It falls within the duty of care of the owner/user of the devices to plan these measures and to check
that they are being complied with.
Complete the operating and installation instructions by any instructions (regarding supervision or
notifications)that are important for the special kind of use of the equipment, i.e. regarding organization of
work, work flow and human resources.
In particular, the owner/user must ensure that:
The unit is only used appropriately.
The device is only operated in a fault-free, fully functional condition, and the safety components, in
particular, are checked regularly to ensure that it is functioning properly.
The required personal protective equipment for the operators, service and repair personnel is available
and is used.
The operating instructions are always available at the location where the equipment is used and that they
are legible and complete.
The unit is only operated, serviced and repaired by qualified and authorized personnel.
This personnel is regularly trained in all applicable matters regarding safety at work and environmental
protection, and that they are familiar with the operating manual and, in particular, the safety instructions it
contains.
Any safety and warning signs on the devices are not removed and remain legible.

5.52.190A.01.01.04
5
customers equipment at site must comply with currently applicable ATEX-regulations
WARNING!
It is not allowed to make constructive changes of the equipment!
2.3 Requirements for the operating personnel
The units may only be operated by qualified persons that are appropriately trained and that are familiar with
it. They must have their employer’s authorization for operation of the units.
Before starting work, the operating personnel must have read the operating and installation instructions,
especially the chapter "Safety Instructions".
This is especially important for operating personnel that rarely uses the equipment, i.e. for installation or
maintenance work.
DANGER!
In order to avoid severe injury, please pay attention to the following when using the equipment:
Use protective clothes/equipment.
Do not wear long hair hanging down open.
Do not wear rings or other jewelry.
Do not wear clothes that are too big/wide.
Do not reach into ropes, chains, drive parts or other moving parts with your hands
2.4 Appropriate use
The permitted safe working load of the devices must not be exceeded! An exception can be made during the
load test before initial operation, carried out by a licensed qualified person.
Defective devices and load suspension devices must not be used until they have been repaired! Only
original spare parts must be used. Non-compliance will result in any warranty claims becoming void.
Liability and warranty will become void if unauthorized modifications of the units are made by the user!
The permissible ambient temperature when operating the devices:
Type of drive
Device classification for
Not explosive atmosphere
Explosive atmosphere
according to ATEX )* )**
Manually driven
-20°C/+50°C
-20°C/+40°C
Motor driven
-20°C/+40°C
-20°C/+40°C
) * At an atmospheric pressure range from 0.8bar to 1.1bar and an oxygen content of approx. 21%
) ** Devices of this category have been specially modified and labeled by the manufacturer
DANGER!
The permissible ambient temperature must not be exceeded!
The appropriate use of the hoists is vertical lifting and lowering of unguided loads. In combination with
trolleys, loads can also be moved horizontally.
DANGER!
The use is not allowed:
for pulling loose of stuck loads, dragging of loads and inclined pulling.
in explosive atmosphere, except the unit is especially modified for it and marked by an indication label.
in reactor containment vessels.
to transport people.
The device is not suitable for use on stages and in studios.
Persons must not stand under a suspended load.

6
5.52.190A.01.01.04
NOTICE!
If the units are not used appropriately, it is not possible to ensure safe operation.
The owner and operator have sole liability for all personal injury and damage to property arising from
inappropriate use.
DANGER!
It’s only allowed to use the unit in the EX-classification which is named on the type plate; or in lower
classes
2.5 Basic safety measures
Observe installation-, operation and maintenance instruction.
Take notice of caution notes at units and in the manual
Observe safety distances.
Take care for a free view on the load.
Only use the hoists appropriately.
The equipment is to be used exclusively for movement of goods. Under no circumstances my persons be
moved.
Never load the devices beyond their working load limit.
Pay attention to the accident prevention regulations (UVV).
Should the hoist be used outside of Germany, please pay attention to the national regulations that apply.
Supporting structures and load-attached devices used in conjunction with this equipment must provide an
adequate safety factor to handle the rated load plus the weight of the equipment. In case of doubt, consult
a structural engineer.
If the equipment has not been used for a period of time, carry out visual checks of all main components
such as chains, load hooks etc. and replace any damaged parts with new, original spare parts before
putting the equipment back into operation!
Do not use a hoist that is defective, pay attention to any abnormal noise it makes during operation.
Stop working immediately in case of disturbances and remedy failures.
Any damage and faults must be reported to a responsible supervisor immediately.
If the unit is put into motion, any persons in the immediate vicinity must be informed by calling to them!
Please pay attention to the regulations for load carrying devices UVV for both positive and non-positive
methods of attaching loads.
The lifting tackle or the load must be securely attached to the hook and be seated at the bottom of the
hook.
The safety catch of hooks must be closed.
When charged, the housing may not be in contact somewhere.
Stop lowering the load when the bottom block or the load is being set down or is prevented from being
lowered further.
The load chain must not be twisted.
Twisted chains must be aligned before attaching the load.
The correct alignment of the chain links can be seen from the weld seams.
The chain links must always be aligned in one direction.
Don't bump against something with load or hook
Illustration 1
Motor drive is prohibited.
The devices are not suitable for continuous operation. In order to avoid too high temperatures of the
brake discs that are not permitted, the following maximum continuous operating times must not be
exceeded:
Light use (highest load is seldom lifted)
Medium use (roughly equal frequency of light, medium and heavy loads)
Heavy use (nearly always largest permissible load)
=
=
=
60 min
30 min
15 min
Let the hoist stand still at least 15 minutes afterwards to cool down the brake.

5.52.190A.01.01.04
7
WARNING!
The following is not allowed:
to lift another load than the nominal safe working load
to manipulate the sliding clutch if units are equipped with
The use of elongated or damaged chains or wire ropes. Replace them immediately by new, original
parts.
Never loop the load chain around a load nor place or pull the chain over edges.
Never repair damaged load hooks (e.g. by hammering), but replace them by original hooks.
DANGER!
Special safety measures for use in areas prone to explosion.
Not to be used with IIC gases and IIB gases hydrogen sulphide, ethylene oxide and light metal and shock
sensitive dusts!
No use in temperature class T5 or T6.
It is not allowed to use the equipment in area at risk from explosion where gas AND dust does both exist
at the same time!
During assembly and operation of explosion-proof equipment, the relevant regulations of i.e. BG-Chemie
about the use of equipment in area at risk from explosion, must be adhered to by the user/owner.
Please make sure that external ventilation is sufficient.
Please wear conductive shoes. Gloves should have a shunt resistance of < 108.
It is not allowed to take off clothes.
The surface temperature of the devices could increase by a variety of external circumstances. For this
reason, the surface temperature is to be monitored.
Avoid ignitable dust deposits.
Remove dust deposits daily before commencing work and ensure that dust cannot settle between moving
parts.
Never remove dust with compressed air - remove it with a wet bolt of cloth.
Defective units or units that show abrasion of its surface rust on chains, hooks, or suspension devices,
must be taken out of service.
Please observe the prescribed intervals.
Assembly and maintenance work must only be carried out in an atmosphere not prone to explosion.
Check the grease level of the bearings regularly
Exchange friction surfaces in time and (an exception to this are electric units - maintenance of the brakes
must only be effected by HADEF).
Protect the device from impact, friction, rough handling and moisture.
Special scope
Use of different EX-zones is depended from the EX-classification of the unit. Find the EX-classification on its
type plate.
Unit classified
in EX-classification
No use
in EX-zone
3G
0,20,1,21,22
3D
0,20,1,21,2
2G
0,20,21,22
2D
0,20,1,2

8
5.52.190A.01.01.04
2.6 Explosion protection
The EX classification of the unit is indicated on a
separate plate, situated on the unit.
Illustration 2
Example of ATEX classification:
II
2
G
Ex h
IIB
T4
Gb
CE-marking
European Union
explosion-proof operating
material
II
device group / application
I
II
danger of mine damp
other areas prone to explosion
2
device category
1
2
3
for use in zone 0
for use in zone 1
for use in zone 2
G
EX atmosphere
G
D
...caused by gas, steam, fog
...caused by dust
Ex h
type of protection
for mechanical devices, including e. g.
“c” construction safety
“k” encapsulation of liquids
IIB
explosion group II (gases)
IIA
IIB
IIC
limit gap widths (MESG) > 0,9 mm
limit gap widths (MESG) ≤0,9 to ≥0,5 mm
limit gap widths (MESG) < 0,5 mm
T4
Temperature class - gases
(for dust only the tempera-
ture in °C is stated)
T1
T2
T3
T4
T5
T6
limit temperature 450 °C
limit temperature 300 °C
limit temperature 200 °C
limit temperature 135 °C
limit temperature 100 °C
limit temperature 85 °C
Gb
EPL (equipment protection level)
Ga
Gb
Gc
e.g. Group II (for gases, vapours, mist):
level of protection: very high (complies with zone 0)
level of protection: high (complies with zone 1)
level of protection: enhanced (complies with zone 2)
2.6.1 EX-Category
EX - Zone
1+21
2+22
1+21
2+22
Device category
2
2
Expl.-group of gases
Expl.-group of dust
IIB
IIIA
IIB
IIIA
Temperature class - gases
Temperature class - dust
T4
T135°C
T3
T200°C

5.52.190A.01.01.04
9
DANGER!
The classification for the device can be found on the EX-type plate on the unit.
The device must only be used in the classification stated or in a lower classification.
2.6.2 Surface temperature of the devices
DANGER!
The temperature class mentioned on the EX-type plate on the unit must be observed, - make sure
that the max. surface temperature is even fallen short of.
DANGER!
The maximum surface temperature of the equipment must always be lower than the ignition
temperature of the gas/vapour/dust/air mixture. Equipment which has been classified in higher
temperature classes is, of course, also approved for use in applications with lower temperature
classes. As gas/air mixtures for T5 do not occur with normal use, and only very rarely occur for T6,
for specific gas/air mixtures such as carbon disulphide (IIC), our hoists are not rated for these
temperature classes and must not be used for these classes.
Temperature
class
Ignition tem-
perature of gas
°C
max. surface
temperature of the
operating material in
°C
T1
>450
450
T2
>300 <450
300
T3
>200 <300
200
T4
>135 <200
135
T5
>100 <135
100
T6
>85 <100
85
2.6.3 EX zone classification
Areas that are prone to explosion are classified into zones. The owner must determine the zone that exists.
Information on the zone classification can be found in IEC 60079-10 and in national standards. The following
table contains an overview of the zone classification in combination with the device category.
Gases
Vapours
Mist
device category
(Gases)
Dust
device category
(dust)
explosive
atmosphere
is present
Zone 0
1G
Zone 20
1D
continuously, long-term or
frequently
Zone 1
2G
Zone 21
2D
occasionally
Zone 2
3G
Zone 22
3D
rarely or short-term

10
5.52.190A.01.01.04
2.6.4 Explosion hazards … recognizing and preventing!

5.52.190A.01.01.04
11
3 Transport and Storage
CAUTION!
Transport may only be done by qualified personnel. No liability for any damage resulting from improper
transport or improper storage.
3.1 Transport
The devices are checked and if so adequately packed before delivery.
Do not throw or drop the equipment.
Use adequate means of transport.
Transport and means of transport must be suitable for the local conditions.
3.2 Safety device for transport
NOTICE!
Should a safety device for transport exist, please remove it before commissioning.
3.3 Storage
Store the equipment at a clean and dry place.
Protect the equipment against dirt, humidity and damage by an appropriate cover.
Protect hooks, wire ropes, chains and brakes against corrosion.
DANGER!
Units that show corrosion must be taken out of service!
4 Description
4.1 Areas of application
The devices must be as far as possible installed in a covered room.
If they are used in the open, protect the units against the effects of weather such as rain, hail, snow, direct
sunshine, dust, etc. - we recommend to use a cover in parking position. If the device is set up in a
continuously humid environment with strong temperature fluctuations, the correct functionings are
endangered by the forming of condensation.
NOTICE!
Use only in the intended atmosphere with a humidity of up to 100%, but not under water!
Depending on the type of device, it is suitable for use in area at risk from explosion in the EX-classification
stated.
The EX-classification is mentioned on the EX-type plate on the hoist. The use of the unit is only allowed for
the EX-classification mentioned on the EX-type plate or lower EX classification.
4.2 Design
Ratchet lever hoists are manual hoists with
suspension hook for stationary use.
They can also be combined with monorail trolleys.
Operation by hand through hand chain.
Illustration 3

12
5.52.190A.01.01.04
4.3 Functions
The load is lifted or lowered by pulling one of the chain falls of the endless hand chain of the hoist. A load
pressure brake prevents automatic lowering of the load after releasing the hand chain.
In combination with hand geared trolleys, the trolley is moved to the left or to the right side by pulling the
hand chain.
In combination with push travel trolleys the trolley is moved by pushing or pulling the load or, without load, by
pulling the load chain.
NOTICE!
The best protection against functional failures in case of extreme environmental impact is the regular use of
the equipment.
4.4 Important components
Gear
Gear components are made of high-quality material.
Load pressure brake
Holds the load in any position. Hardened safety pawls.
Housing
Depending on the model made from steel plate or aluminium die-casting (Not for explosion proof equipment).
In case of ex proof hoists, the housing is only made of steel plates.
Load chain
According to EN 818-7-T high quality chain. All components match precisely to each other. Therefore please
only use original chains.
Load hook
Forged steel. Rotating, this facilitates attaching the load and avoids twisting of the chain. With safety catch.
Overload protection
Hoists with overload protection protects the hoist by a slipping clutch from damage by overload. When the
slipping clutch operates, lifting of the load is stopped. Lifting is only possible again after the load has been
lowered and reduced to nominal load.
Special Parts
For use in explosion dangerous areas, are be installed some special units, special treated surfaces or made
in special material.
5 Technical data
Capacity
kg
5000
10000
15000
20000
25000
30000
40000
50000
Number of chain falls
1
2
3
4
5
2 x 3
2 x 4
2 x 5
Load chain
mm
13 x 36
13 x 36
13 x 36
13 x 36
13 x 36
13 x 36
13 x 36
13 x 36
Lifting path when reeling off
30 m hand chain
mm
1130
66
43
33
26
43
33
26
Hand chain pull for lifting
N
290
310
330
350
370
2 x 330
2 x 350
2 x 370
weight at 3 m lift approx.
kg
kg
78
100
135
170
198
270
340
396
weight per add. m lift
kg
3,8
8,6
12,4
16,2
20
24,8
32,4
40
DANGER!
These Hoists are only suitable for use only in the following EX-classification:
CE EX II 2G Ex h IIB T3 Gb or CE EX II 2D Ex h IIIA T200°C Db or lower classification.
6 Installation
The assembly and installation depends on the local environment. The hoist must be suspended in a way that
it can position itself freely.
6.1 Trolley
For assembly on a beam a travel limit must be placed at either end of the track.
This must be attached so that any elastic limitation buffer or the trolley wheels are driven against them in
their end position when moving.

5.52.190A.01.01.04
13
Generally, additional lifting gear (e.g. fork lift, lifting platforms) will be required for the assembly. These must
take the weight of the devices securely.
6.2 Tools
7 Control
Only people that are familiar with the operation of the lifting devices and cranes may be entrusted with their
operation. They must be authorized by the employer for the operation of the equipment. The employer must
ensure that the operating instructions are available near the equipment and that they are accessible for the
operating personnel.
Lifting and Lowering by pulling the endless hand
chain.
Lifting - pull the chain fall at the right side –
the hand chain wheel turns clockwise
Lowering - pull the chain fall at the lift side –
the hand chain wheel turns anti-clockwise
Illustration4
NOTICE!
For double lifting mechanism
Operate both lifting mechanism, synchronous resp.evenly.
CAUTION!
Run in of chain into the chain container for hoist with double lifting mechanism
For a correct run in of chain into both chain containers, the lowering operation must be carried out, without
load, at certain intervals, until both chain container are empty.
For motorized devices with operating limit switches "lowering"
Lower until the operating limit switch is released.
Non-observance can lead to device damages!
WARNING!
The hoist must always hang centrally under the beam or under its suspension point.
7.1 Brake and pawl
The brake system needs a minimum load of 3% of the capacity.
Only this minimum load makes sure that the load-pressure-brake closes correctly. When the brake closes
correctly, the load is safely held
GEFAHR!
Working situations with no guarantee that the minimum load is charged, are forbidden!

14
5.52.190A.01.01.04
8 Commissioning
8.1 General
Should the unit be used in Germany:
Please observe the validated, national accident prevention regulations.
For other countries:
Inspections as above. Please observe the national rules and regulations and the instructions in this manual!
NOTICE!
Hoists up to 1000 kg capacity and without motor-driven trolleys of hoisting unit must be tested by a “qualified
person” before putting into operation for the first time.
Hoists of 1000 kg capacity and up or with more than one motor-driven hoist movement; i.e. lifting and trolley
movement, must be tested by a “licensed qualified person” before putting in operation.
An exception is “hoists ready for operation” acc. validated national regulations with EU-declaration of
conformity.
Definition “qualified person” (former expert)
A “qualified person” has learned, due to occupational training and experience and the job that the person has
done, the skills needed to tests the material for one’s work.
Definition “licensed qualified person” (former approved expert)
A “licensed qualified person” has, due through special occupational training, knowledge about testing of the
material for one’s work and knows the national accident prevention regulations and other prescriptions and
technical regulations. This person must test the material for one’s work regularly with regard to design and
kind of use. The license will be given to qualified person be the approved supervision authorities (ZÜS).
8.2 Load chain
Before commissioning the load chain must be aligned and oiled.
For the first commissioning of motorized hoists, chain oil is supplied with the delivery.
Move safety note and fixing wire away from the chain.
CAUTION!
Do not use grease for lubrication of load chain.
Without lubrication, manufacturer's warranty and/or liability will be void.
NOTICE!
Continuous, thorough lubrication will increase the life of the chain considerably.
9 Safety check
Before putting into service initially or when putting back into service, it must be checked whether:
All fastening screws (if existent), socket pins, flap socket and safety devices are tightened and secured.
The chains are correctly placed, oiled and in good condition.
10 Functional test
10.1 Checks before the initial start-up
Lifting gear
Load chains must not be twisted.
Lubricate the load chain with gear oil or suitable chain lubricant before first loading.
Trolley drive
The open-lying teeth of the trolley drive must be lubricated.
Hand gear for hand geared trolley
Ensure correct fit of the hand chain, it must not be twisted and must hang freely.

5.52.190A.01.01.04
15
10.2 Functional test
Lifting gear
Check lifting and lowering functions, initially without a load.
Then check the brake function under load. The load must be securely held.
Trolleys
Carefully move the trolley to the end positions and check the positions of the end stops.
11 Maintenance
11.1 General
All monitoring, servicing and maintenance operations are to ensure correct functioning of the equipment;
they must be effected with utmost care.
Only “qualified persons” may do this work.
Servicing and maintenance work must only be done when the hoist is not loaded.
Records must be kept of all test results and measures taken.
11.2 Monitoring
The monitoring and servicing intervals stated are valid for operation under normal conditions and single-shift
operation. In case of severe operating conditions (e.g. frequent operation with full load) or special
environmental conditions (e.g., heat, dust, etc.), the intervals must be shortened correspondingly
11.3 Replacing the load chain
CAUTION!
If there is any visible damage and when the conditions for replacement are reached (i.e. one or several
dimensions in the table have been reached, there is corrosion or elongation), the chain must be replaced.
When replacing the chain, also check the chain wheels.
Procedure:
Only insert new chains in an unloaded state and as the chains that are currently in the device –i.e. not
twisted.
Remove chain from its fastening at the end and attach a chain link which is open at the side.
A chain link which is open at the side, can
easily be produced by grinding out a small
piece. The opening must have the same
thickness as the chain link.
Illustration 5
Hang a new original chain (same size and oiled) in the side opened chain link and insert it.
Make sure the chain is not installed twisted.
Make sure the chain links are aligned in one direction.
Assemble the chain to the end fastening.
12 Inspection
12.1 Periodic checks
Independently from the regulations of the individual countries, lifting devices must be checked at least yearly
by a qualified person or licensed qualified person regarding its functional safety.
12.1.1 Components to be checked
The following must be checked:
Dimensions of load chain, load hooks, pawls, bolts, ratchet wheels, brake linings.
The dimensions must be compared to the dimensions in the tables.
A visual inspection for deformations, cracks and corrosion must be carried out.

16
5.52.190A.01.01.04
CAUTION!
When the wear limit is reached, the part must be exchanged by a new, original part.
at
commissioning
daily
checks
1st maintenance
after
3 months
Inspection
Maintenance
every
3 months
Inspection Mainte-
nance
every
12 months
Check screw connections
X
X
Check lifting, lowering functions.
X
X
Check brake function
X
X
for ratchet lever hoists: Check free-wheeling mechanism of the
chain
X
X
Brake - check wear of brake lining
X
Check chain wheels, ratchet wheels and pawls.
X
Clean and lubricate the load chain.
X
X
X
Check the load chain for elongation and wear
X
Check the load hook for cracks and deformation
X
Load hook - check the safety catch
X
X
Check and lubricate the bearing of the chain pulleys.
X
X
Check the chain pulleys
X
X
Have the equipment checked by a qualified person
(periodic inspection)
X
Clean off of dust (don’t use compressed air)
X
Check of corrosion
X
X
Surface coated –wear control for
Load chain, hand chain, hook, housing
X
X
Check grease - bearings
X
X
Check grease –pinion of trolleys *
X
X
Name plates –exist, check readability
X
Protection earthing –check (pneumatich equipment) *
X
X
*if applicable
WARNING!
If one or several of the dimensions fall below or exceed the dimensions in the table, or if cracks or
corrosion are found, the parts must be replaced with original spare parts.
12.2 Checking the load chain
CAUTION!
The load chain must be tested over its entire length!
The measure of the load chain must be carried out especially in the areas which are subject to the highest
wear. Through the lifting movement, these are the contact points of the chain with sprocket wheel and
deflection pulleys.
acc. DIN 685-part 5
L11 = pitch increase over 11 chain links
L1 = pitch increase over 1 chain link
Illustration 6
dm= detected link diameter (d1+d2)/2
Illustration 7
Chain dimensions
Table 1
Dimensions
mm
Chain size
3x9
4x12
4,2x12,2
5x15
5,6x15,8
5,6x17
6x18
6,3x19,1
7,1x20,1
L11
105,6
136,6
138,2
170,6
179,1
194,2
203,9
216,4
227,9
L1
9,9
12,7
12,8
15,7
16,6
18
18,9
20
21,2
dm
2,7
3,6
3,8
21,2
5,0
5,0
5,4
5,7
6,4
Table 2
Dimensions
mm
Chain size
7,1x21
7,9x23
8x24
9x24,8
9x27
10x28,1
10x30
13x36
16x45
L11
238,5
260,6
272,1
281,2
300,8
318,6
340,7
408,3
505,6
L1
22,3
24,1
25,3
26,1
28,1
29,6
31,8
37,9
47,4
dm
6,4
7,1
7,2
8,1
8,2
9,0
9,0
11,9
14,4

5.52.190A.01.01.04
17
WARNING!
When the dimensions listed in the table are reached due to wear or deformation, the chain must be
replaced!
DANGER!
In case of corrosion and/or wear of the surface coating, the chains must be exchanged by original
chains.
12.3 Checking the load hook
Load hook
X = measuring distance hook mouth width
Y = measured length from hook no. 6
H = thickness of hook saddle
Illustration 8
Dimension
mm
Capacity/chain falls
5000 kg
10000 kg
15000 kg
20000 kg
25000 kg
30000 kg
40000 kg
50000 kg
X or Y
45/-
56/-
-/130
-/145
-/160
-/180
-/200
-/225
H
48
67
85
95
106
118
132
150
Dimensions in the tables are theoretical values without tolerances.
Please fill in the measured
values before putting into
operation:
Capacity
kg
X or Y
mm
H
mm
CAUTION!
When the dimension of hook opening width is deformed more than 10% or when the dimension of the hook
bottom thickness is fallen short of by 5% due to wear, the hook must be replaced.
DANGER!
In case of corrosion and/or wear of the surface coating, the hooks must be exchanged by original
hooks or the coating must be renewed.
12.4 Check of the pawl
A
Vmin
kg
mm
mm
5000-50000
35
33,25
12.5 Check of the brake system
Ratchet wheel (A) and brake linings (B)
D
Vmin
tn
tv min
A 2xB
kg
mm
mm
mm
mm
5000/1 - 50000/10
131
129
3
2,5

18
5.52.190A.01.01.04
12.6 Check of the suspension bolt
Suspension bolt
dn
dv min
kg
mm
mm
5000-50000
25
23,8
13 Service
13.1 Load chain
Wear at the links is mainly due to insufficient maintenance of the chain.
To ensure optimal lubrication of the links, the chain must be lubricated at regular intervals, depending on
usage.
Lubricate the chain with oil that creeps.
Always lubricate the chain when it is not under load so that the oil can wet the links affected by wear. It is
not sufficient to lubricate the chain from the outside, as this will not ensure the formation of a lubricating
film within the links. The adjacent link points must always be lubricated to prevent excessive wear.
If the same lifting operations are carried out constantly, the switching area from a lifting to a lowering
movement must be given special attention.
Thoroughly effected lubrication of the chain will prolong the life of the chain by approx. 20 times,
compared to dry run with unlubricated chain.
Wash dirty chain with petroleum or a similar cleaner, under no circumstances heat the chain.
If there are environmental influences that foster wear, such as sand, a dry lubricant should be used, e.g.
graphite powder.
When lubricating the chain’s condition of wear should be checked.
CAUTION!
Do not use grease for lubrication of load chain.
Without lubrication, manufacturer's warranty and/or liability will be void.
13.2 Pulleys
13.3 Load hook
Check bearings and pulleys yearly
Clean and lubricate the bearings of hooks and pulleys with grease
Slight bearings are maintenance free
When bearings resp. slight bearings are worn of, change the complete pulley
Use
Recommendation
Interval
Load chain
oil for example: FUCHS RENOLIN PG 220
or special chain lubricant
Use NO grease!
0,2 l
3 month
Use
Recommendation
Interval
Pulleys
FUCHS
RENOLIN PG220
Acc. to demand
12 month
Use
Recommendation
Interval
Load hook
bearing
FUCHS
RENOLIN PG220
Acc. to demand
12 month

5.52.190A.01.01.04
19
13.4 Gear
Regular checks of lubrication are necessary. The teeth must be cleaned and re-lubricated after approx. 3
years. We recommend to use a lubricant of class EP2 or similar products. In case of severe conditions of
use (e.g. dust, regular lifting of the nominal load,etc.), please shorten maintenance intervals.
13.5 Gear spring pressure brake
During the check, brake lining wear is verified. The brake linings must be replaced when the wear limit is
already reached at one position of the lining, - as this can be the case when wear of the linings is irregular.
CAUTION!
The brake linings must be free from fracture. Avoid oil, grease, dirt and humidity on the brake linings as this
increases wear.
13.6 Overload protection
DANGER!
The factory setting of the overload protection/slipping clutch is secured by sealing. In case of any changes
will void the warranty. Should maintenance be necessary, please contact a service company authorized by
the manufacturer.
13.7 Lubricant - Selection
FUCHS
SHELL
ESSO
MOBIL
TOTAL
CASTROL
KLÜBER
Renolit FEP 2
Alvania EP 2
Unirex EP 2
Mobilux EP 2
MULTIS EP2
--
--
Stabylan 5006
--
--
--
--
Optimol Viscoleb 1500
Klüberoil 4UH 1-1500
--
--
--
--
--
--
Wolfracoat 99113
Chain lubricant OKS 451
13.8 Lubricant for food industry –Selection (as option*)
SHELL
MOBIL
CASTROL
KLÜBER
Gearing
FM Grease HD2
Mobilgrease FM 222
--
Klüberoil 4UH 1-1500 N
Load chain
--
Lubricant FM 100
Optimol Viscoleb 1500
--
Load hook;
Pulleys
Gear rim;
Drive pinion
FM Grease HD2
Mobilgrease FM 222
--
--
* must be mentioned by order
14 Trouble
DANGER!
Assembly, disassembly and maintenance operations must only be carried out in an atmosphere not
prone to explosion!
Please pay attention to the following in case of problems:
Troubles with the equipment must only be repaired by qualified personnel.
Secure the unit against unintended operation start.
Put up a warning note indicating that the unit is not to be used.
Secure the working area of moving parts of the unit.
Please read the chapter "Safety instructions".
Notes on the repair of faults are found in the following table.
For the repair of failures please contact our service department.
CAUTION!
Trouble caused by wear or damage to parts such as wire ropes, chains, chain wheels, axes, bearings,
brake parts, etc., must be remedied by replacing the parts with original spare parts.

20
5.52.190A.01.01.04
15 Remedy
Problem
Cause
Remedy
Load is not lifted
Overload
reduce the load to nominal load
load got stuck
set the load free again
brake linings are worn
Do maintenance and
exchange the brake linings
Load chain is twisted
Align the load chain
Defect of chain, gear or chain wheels
Do maintenance and replace defective parts by original
spare parts
Pawl does not engage properly
Check the pawl and replace it if necessary
Pawl spring is missing
Do maintenance and replace defective parts by original
spare parts
It is difficult to lift the load
Overload
reduce the load to nominal load
Dirty chains, gear or chain wheels
Do maintenance, lubricate chains, gear and chain wheels
Defect of chain, gear or chain wheels
Do maintenance and replace defective parts by original
spare parts
Load is lifted with interruptions
Pawl spring is missing or defective
Do maintenance and replace defective parts by original
spare parts
Hoist does not lift without load
Brake spring is missing
Do maintenance and replace defective parts by original
spare parts
Hoist does not lift the whole distance long
Hook stucks, chain is twisted
Place hooks and chains in correct position
Brake remains closed
(stuck)
The load hook was pulled against the housing and got
stuck there.
Release the hook, suspend the load again, lower the load,
unload the hoist.
Hoist does not lower the load
Brake too tight
Lift the brake.
Brake too tight due to rust
Replace rusty parts and effect periodic inspection
Load slips down partially during lowering
Foreign-object between the brake discs
Remove the foreign-object, clean the surface
Should the surface show lines, replace the brake disc
Load slips down during lowering
Brake discs are missing, are installed incorrectly or are
worn
Replace the brake discs resp. install them correctly
16 Decommissioning
WARNING!
It is essential that the following points are observed in order to prevent damage to the equipment or critical
injury when the device is being decommissioned:
It is mandatory that all steps for decommissioning the machine are carried out in the indicated sequence:
First secure the working area for decommissioning, leaving plenty of space.
Read the chapter "Safety instructions".
Disassembly is carried out in reverse order to the assembly.
Please make sure that all operating material is disposed of in accordance with environmental regulations.
16.1 Temporary decommissioning
Measures are as above.
Also read the chapter “Transport and storage”.
16.2 Final decommissioning/disposal
Measures are as above.
After disassembly, ensure that the disposal of the equipment and any materials it contains is carried out
in accordance with environmental regulations.
Table of contents
Other HADEF Lifting System manuals
Popular Lifting System manuals by other brands
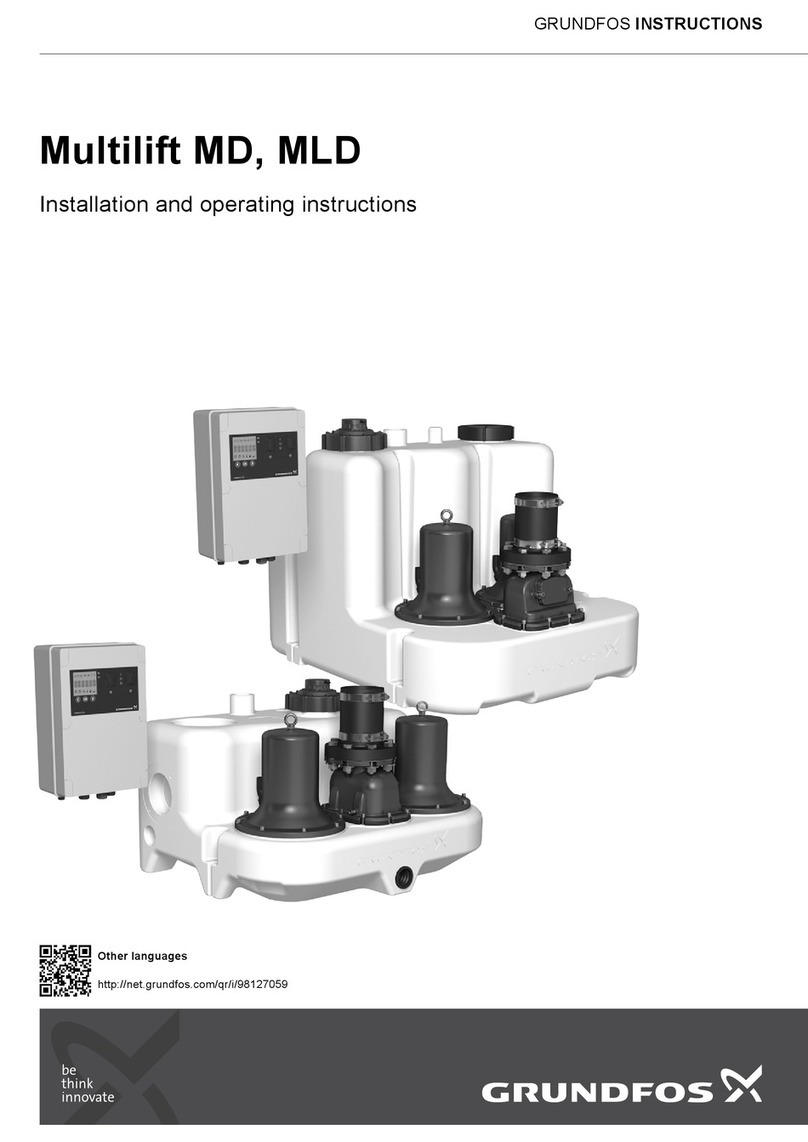
Grundfos
Grundfos Multifit MD Series Installation and operating instructions

morse
morse MORSPEED 288-1 Operator's manual
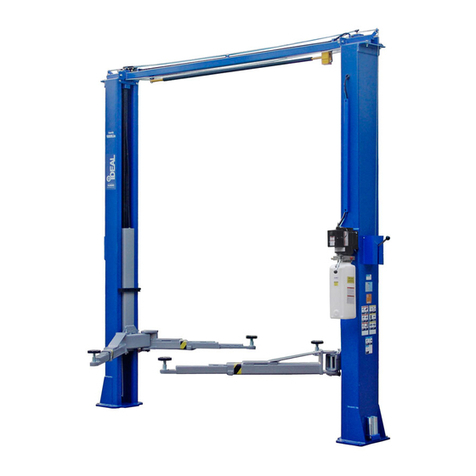
IDEAL
IDEAL TP10KAC-DX Installation & operation manual
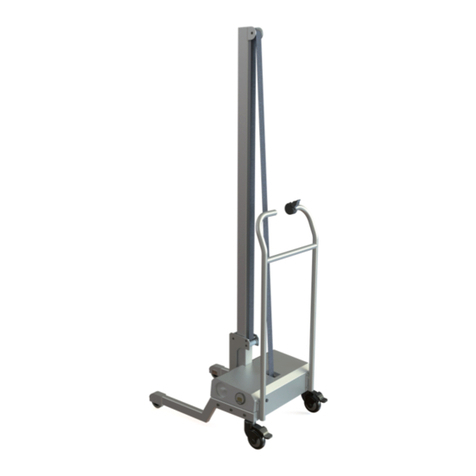
TAWI
TAWI CR80 User manual and spare parts list

Magliner
Magliner CooLift CPA43HTC owner's manual
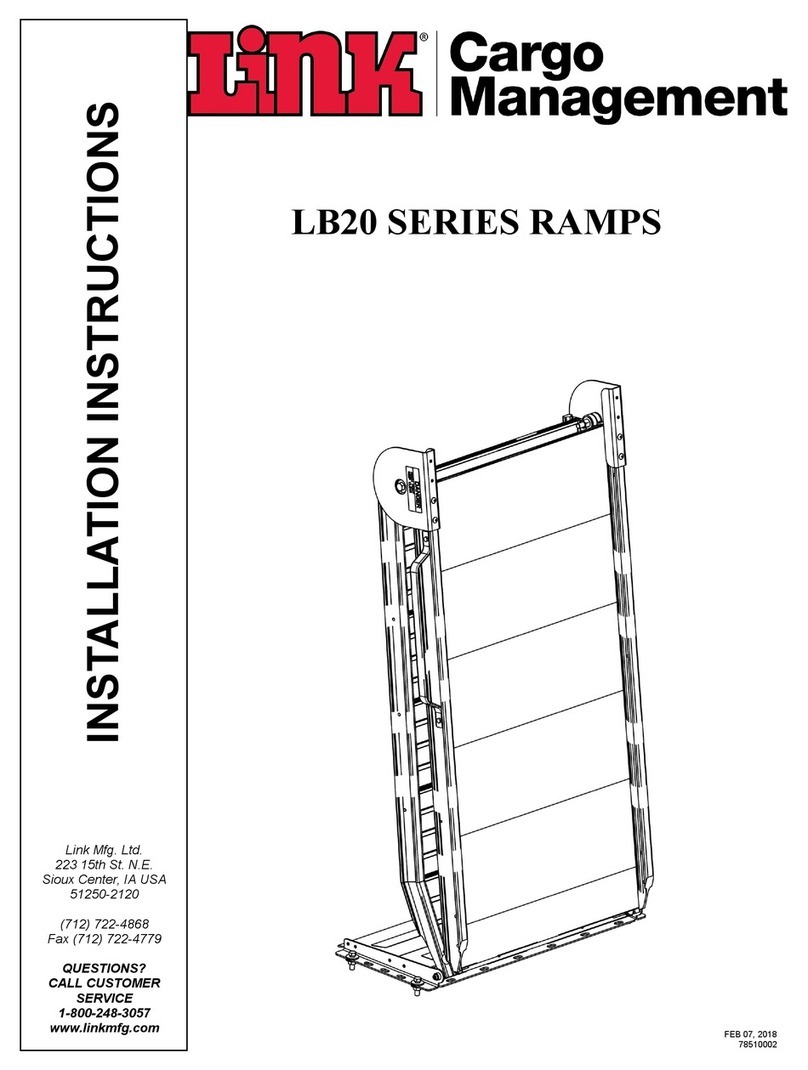
Link
Link LB20 Series Installation instructions manual