handtmann INOVA User manual

OPERATING MANUAL
DOUBLE-SEAT VALVE
INOVA
(Type 580)
BA 058000.06 EN

© 2006
Albert Handtmann Armaturenfabrik GmbH
& Co. KG Technical Documentation
All copy rights regarding this technical documentation and all
drawings submitted to the receiver in person remain at all
times with Albert Handtmann Armaturenfabrik GmbH & Co.
KG, Biberach, Germany.
They must not be copied or reproduced without prior written
authorization.

Handtmann Worldwide
Technology for a Prosperous Future
The Handtmann Armaturenfabrik can look
back over a long and successful tradition.
Today it is part of the globally operating
Handtmann Group of Companies.
The Handtmann Armaturenfabrik is one of
the leading suppliers of armatures and
process systems for the beverage industry.
Increasingly positive activities can also be
seen in the fields of biotechnology and the
pharmaceuticals industry.
Our ambitious goals can only be realized
with a highly qualified and motivated team.
We are not looking for short-term
successes but rather the creation of a long-
term partnership with our customers.
Albert Handtmann Armaturenfabrik GmbH & Co. KG · Arthur-Handtmann-Strasse 11 · D-88400 Biberach an der Riss
Telephone +49- (0) 7351-342-0 · Fax +49- (0) 7351-342- 4480 · sales.fittings@handtmann.de · www.handtmann.de

Contents
4 / 36
DOUBLE-SEAT VALVE INOVA (Type 580)
BA 058000.06 EN 15.11.2018
0Contents
0Contents................................................................................................................................................... 4
1Foreword ................................................................................................................................................. 6
2Safety....................................................................................................................................................... 7
2.1 General Information ............................................................................................................................ 7
2.2 Proper Application ............................................................................................................................... 7
2.3 Improper Application........................................................................................................................... 7
2.4 The User's Duty to Exercise Diligence.................................................................................................. 7
2.5 Symbols................................................................................................................................................ 8
2.6 Basic Safety Advice .............................................................................................................................. 9
3Delivery.................................................................................................................................................. 11
3.1 Transport ........................................................................................................................................... 11
3.2 Instructions for Delivery and Performance........................................................................................ 11
3.3 Storage Instructions........................................................................................................................... 11
3.4 Disposal of Packaging......................................................................................................................... 11
4Description of Function .......................................................................................................................... 12
4.1 Valve types......................................................................................................................................... 12
4.1.1 Process Integration, Mechanical.......................................................................................... 14
4.1.2 Process Integration, Electrical ............................................................................................. 14
5Technical Data........................................................................................................................................ 15
6Operation/Use ....................................................................................................................................... 17
6.1 Valve Switching Functions ................................................................................................................. 17
6.1.1 Production – Valve Closed ................................................................................................... 17
6.1.2 CIP or Production Valve Open ............................................................................................. 17
6.1.3 Seat cleaning – valve seat open........................................................................................... 18
6.1.4 Seat cleaning - lower valve seat........................................................................................... 18
6.1.5 Cleaning – Balancer (B) ........................................................................................................ 19
6.1.6 Cleaning – Leakage Chamber (L).......................................................................................... 19
6.2 CIP cleaning........................................................................................................................................ 20
6.3 Leakage detection.............................................................................................................................. 20
6.4 Valve control...................................................................................................................................... 21
7Installation and Commissioning ............................................................................................................. 22
7.1 Installation of the Valve Housing....................................................................................................... 22

Contents
15.11.2018
DOUBLE-SEAT VALVE INOVA (Type 580)
BA 058000.06 EN 5 / 36
7.2 Installation of the Valve inset ............................................................................................................ 23
8Disassembly/Assembly........................................................................................................................... 24
8.1 Preparation for Disassembly of the Valve.......................................................................................... 24
8.2 Complete Disassembly – Valve inset.................................................................................................. 25
8.3 Partial Disassembly – Valve inset ....................................................................................................... 27
8.4 Assembly tools ................................................................................................................................... 28
8.5 Valve assembly................................................................................................................................... 28
9Repair..................................................................................................................................................... 29
10 Maintenance / Cleaning ......................................................................................................................... 31
10.1 Preparation for Maintenance ............................................................................................................ 31
10.2 General Maintenance Intervals.......................................................................................................... 31
10.3 Inspection Intervals............................................................................................................................ 32
10.4 Cleaning Parameters .......................................................................................................................... 32
10.5 Seal change ........................................................................................................................................ 32
10.6 Seals ................................................................................................................................................... 33
10.6.1 Sealing Material ................................................................................................................... 34
10.7 Spare Parts List................................................................................................................................... 34
11 Disposal.................................................................................................................................................. 35
11.1 Disposal of Packaging......................................................................................................................... 35
11.2 Disposal of the Valve Parts................................................................................................................. 35

Foreword
6 / 36
DOUBLE-SEAT VALVE INOVA (Type 580)
BA 058000.06 EN 15.11.2018
1Foreword
This operating manual is for the information of the service personnel, the user and if
necessary specialist personnel. It is part of the valve delivery. No chapter from this manual
may be deleted. A missing operating manual or missing pages are to be replaced
immediately.
An understanding of the double-seat valve's function is a prerequisite for a smooth
operation.
Every person charged with the valve’s installation, commissioning, operation, maintenance
and repair must have read this manual and especially the chapter on safety and have
understood both the content and the terminology.
If necessary, in-house instruction taking into account the specialist qualifications of the
respective persons must take place.
In order to avoid operating errors and to ensure the correct implementation of the required
testing measures, this operating manual must be available at all times to the operating
personnel.
The Handtmann Armaturenfabrik assumes no responsibility for damages or operating faults
resulting from the non-compliance with this operating manual.
This operating manual applies to the INOVA double-seat valve Type 580 in the following
executions:
Types Equipment
INOVA Plus Single-seat lifting, balancer cleaning, leakage chamber cleaning
INOVA Top Single-seat lifting, balancer cleaning
INOVA Basic Leakage chamber cleaning, balancer cleaning
This documentation may be amended by the updating service of Albert Handtmann
Armaturenfabrik GmbH & Co. KG. Amendments to this document may be carried out
without prior notification.

Safety
15.11.2018
DOUBLE-SEAT VALVE INOVA (Type 580)
BA 058000.06 EN 7 / 36
2Safety
2.1 General Information
All persons involved with the installation, commissioning, operation and maintenance of the
double-seat valve must carefully read and observe the following instructions. Your safety is
at stake.
2.2 Proper Application
Double-seat valves are used in the food and beverage industry and the pharmaceutical and
chemical industry. They are used as single valves or in the valve group (valve knot).
Double-seat valves form the point of intersection between two separate piping systems
with different liquid media. Due to their function, they safely separate the liquid media from
each other or transfer the media from one piping system to the other.
2.3 Improper Application
Improper application occurs if:
•Liquid media different to that envisaged in the operating manual are conducted
through the valves.
•Operating conditions different to those envisaged in the operating manual apply.
•The safety instructions are disregarded in the operation, assembly and maintenance.
•Independent modifications or changes to the double-seat valve are carried out that
restrict safety or functionality.
2.4 The User's Duty to Exercise Diligence
Both operator and user must ensure that only authorized and trained personnel work with
the double-seat valve.
The user must especially ensure that:
•The double-seat valve’s installation is carried out in accordance with the instructions.
•The double-seat valves are used in accordance with their purpose and only in a
functional state.
•Only qualified and authorized personnel use and maintain the double-seat valves.
•The legal requirements of the operating safety regulations are adhered to.

Safety
8 / 36
DOUBLE-SEAT VALVE INOVA (Type 580)
BA 058000.06 EN 15.11.2018
2.5 Symbols
Below are the explanations for the symbols used.
Warning - Danger from electrical current!
This symbol indicates that there is a danger to the life and health of persons due to
electric voltage.
Warning – Danger to persons!
This symbol indicates that there is a danger to the life and health of persons.
Caution – Damage to components!
This symbol indicates that special care should be taken.
Note
This symbol indicates an environmentally friendly process or disposal.
Note
This symbol refers to special instructions.

Safety
15.11.2018
DOUBLE-SEAT VALVE INOVA (Type 580)
BA 058000.06 EN 9 / 36
2.6 Basic Safety Advice
Warning – Danger to persons!
Adhere to the following safety instructions in order to avoid dangers to life and health.
Endangerment to service personnel
Explanations Measures
Squeezing danger to fingers, hands and feet
Unintentional opening and closing of the valve must be prevented
during maintenance work.
Do not place your hands in the valve housing or the seat area of
the valve disk.
The valve weighs several kilograms.
Bruising injuries can arise during transport, assembly or in
maintenance work.
Disconnect the electrical connection to the
valve.
Disconnect the pneumatic connection to
the valve.
(Compressed air hose)
Always wear safety shoes and protective
gloves.
Secure the valve against slipping and falling
during assembly, disassembly and in
maintenance work.
Blow and impact danger
Low spring tension
Before taking out the valve inset and loosening the screws, the
valve can be pneumatically lifted.
When carrying out maintenance work the piping system should be
made pressure-free or drained beforehand in the area concerned.
The piping area awaiting maintenance should be sealed off from
the other piping system.
Apply compressed air to the main drive.
Before removing the valve inset, check
which liquid medium was in the piping. If
necessary, rinse the piping again
beforehand with water.
Check the piping pressure before the valve
inset is removed from the housing.
Danger of burning, scalding and causticization
If the piping system is subjected to higher media temperatures the
surface temperature of the valve housing can also reach this
value.
If the liquid medium is drained from the system, this can lead to
burns, scalding or causticization for the operating and
maintenance personnel.
Detergent can leak from the leakage outlet during CIP cleaning.
Attach warning signs.
Rinse the piping system with cold water
before carrying out maintenance work.
Install collecting tubs or a collecting piping
system for controlled pressure-free
drainage of the CIP media.
Make sure, if during the maintenance work
the CIP is activated, that no-one is standing
in the danger area of the leakage outlet.

Safety
10 / 36
DOUBLE-SEAT VALVE INOVA (Type 580)
BA 058000.06 EN 15.11.2018
Malfunction due to incorrect handling
Explanations Measures
The valve should be made inoperative if
malfunctions occur.
Disconnect the electrical connection to the
valve.
Solve faults immediately.
The valve should be installed in such a way that the complete
valve inset can be removed.
Make sure that there is sufficient space
above the drive.
The valve should be installed so that a complete draining by
gravity of the product or leakage chamber is ensured.
Install the valve in a vertical position in
horizontal piping.
The valve’s switching function is defective or takes place jerkily.
The valve has not been properly installed during assembly.
Install the valve housing free from tension
in the piping system.
Residues from welding or assembly can disturb the switching
function.
Before installing the valve remove welding
residues and other contaminants from the
valve housing.
The function can be put out of action or considerably disturbed if
faulty or non-specified parts are assembled or exchanged on the
valve.
This can also lead to injuries to the operating and maintenance
personnel.
Only use accepted parts from the
manufacturer.
If the valve is not checked or maintained at regular intervals, this
can lead to malfunction or major disturbance.
Check the valve within the framework of
the fixed operating maintenance cycles.
When in strong demand, the seals in the
product chamber sealing should be
changed more regularly.
Malfunction through improper use
The valve’s operating area is envisaged for certain operating states
(pressure, temperature, media).
The valve’s function can be disturbed greatly by different
operating conditions.
Make sure of proper utilization.
Transport

Delivery
15.11.2018
DOUBLE-SEAT VALVE INOVA (Type 580)
BA 058000.06 EN 11 / 36
3Delivery
3.1 Transport
The double-seat valves or prefabricated valve units should remain in the delivered packing
systems until assembly.
After unpacking the goods and before assembling them the operating manual must be read.
Warning – Danger to persons!
Possibly supplied foil packings are airtight. Therefore never pull packing material over
the head. Otherwise, there is a danger of suffocation!
Warning – Danger to persons!
Lifting equipment or aids that are too weak can break.
Always make sure of sufficient carrying capacity when selecting lifting equipment or
aids.
Only use tested and approved lifting equipment and aids such as:
Shackles e.g. complying with DIN 82101
Slinging chains e.g. complying with DIN 5687 Quality Class 8
3.2 Instructions for Delivery and Performance
•Check the delivery note data for factual correctness.
•Check the delivery for completeness. Later complaints will not be accepted.
•Carry out a visual inspection of the packing system for external transport damages.
These should be brought to the attention of the forwarder immediately. Complaints
for unrecognizable transport damages should be made within a week.
3.3 Storage Instructions
The goods should be stored in dry, closed rooms if possible in the original packaging. UV
radiation and direct sunlight should be avoided. The maximum air moisture should be no
higher than 60%; the maximum storage temperature should not exceed 40%.
3.4 Disposal of Packaging
Note
The packaging should be disposed of in a proper and environmentally friendly way.
National regulations should be adhered to.

Description of Function
12 / 36
DOUBLE-SEAT VALVE INOVA (Type 580)
BA 058000.06 EN 15.11.2018
4Description of Function
Double-seat valves are installed at critical connection points of two process pipings. The
different liquid media flowing through the pipings are sealed twice (double) against each
other in the valve’s seat area through the upper and lower valve disk.
The leakage chamber is formed between both valve disks. Should a leakage occur at one of
the two valve disks, then the respective medium can flow out through the leakage chamber
to the outside.
The leakage-free switching function is characteristic for the double-seat valve:
1. The lower valve disk moves in the valve seat’s sealing area against the upper
valve disk. At the same time, the leakage chamber is completely closed.
2. The valve disks now lying against each other move from the upper valve seat
area into the open valve position.
3. When the valve is closed, the adjacent valve disks now move into the upper
valve seat area. The leakage chamber is still closed.
4. The lower valve disk moves in the valve seat’s sealing area to its final position
and at the same time slowly opens the leakage chamber.
The upper and lower valve disk are integrated into the respective balancer. During the
switching function, the balancers move between product chamber and the upper or lower
flushing chamber.
The sealing between the product chamber and the flushing chamber is effected through a
gap-free tensioned lip sealing.
The valve’s switching process is carried out via two pneumatically controlled pistons in the
valve actuator. The piston movement is transferred to the valve’s main rod with the lower
valve disk or a superimposed valve rod with the upper valve disk.
4.1 Valve types
INOVA double-seat valve
Order code 580xx
Type Single-seat
lifting
Leakage
chamber
cleaning
Balancer
cleaning
INOVA P lus
INOVA T op
INOVA B asic

Description of Function
15.11.2018
DOUBLE-SEAT VALVE INOVA (Type 580)
BA 058000.06 EN 13 / 36
02
Fig. 1: INOVA double-seat valve Type 580
1Compressed air supply
2Balancer with integrated upper valve disk
3Leakage chamber
4Balancer with integrated lower valve disk (piston insert)
5CIP outflow for upper and lower flushing chamber
6Valve actuator
7CIP connection for upper flushing chamber
8Valve seat area
9CIP connection for lower flushing chamber
10 CIP supply
11 Leakage outlet
1
2
3
4
5
6
7
8
9
10
11

Description of Function
14 / 36
DOUBLE-SEAT VALVE INOVA (Type 580)
BA 058000.06 EN 15.11.2018
4.1.1 Process Integration, Mechanical
Four standard housing executions are offered for the integration of the double-seat valves
in the piping system (standard execution in bold print). The other housing executions are
available on request.
03
Fig. 2: Form of execution
A Form II (e.g. execution 58001-II)
B Form X (e.g. execution 58004-X)
Note
In the housing form Xthe line-evens are moved by 90°; in the housing execution II these run
parallel to each other. The broad line in the symbol display indicates the upper line-even.
Order No. Execution X Order No. Execution II
58001 / 58061 58001 / 58061
58002 / 58062 58002 / 58062
58003 / 58063 58003 / 58063
58004 / 58864 58004 / 58864
4.1.2 Process Integration, Electrical
There are various control units available for the integration of the double-seat valves in the
automated production CIP process:
Types Valve position Control valves BUS system
S 1/2 --
S0 / S0-A 1/2 0/3 ASI
S3 / S3-A 2 3 ASI
•Proximity switch for position (S)
•Control unit for position and function check (SO)
•Control unit for switching, position and function check (S3)
A
B

Technical Data
15.11.2018
DOUBLE-SEAT VALVE INOVA (Type 580)
BA 058000.06 EN 15 / 36
Transport
5Technical Data
Product range
Materials Stainless steel 1.4301 or 1.4404
Seals EPDM, FDA conform
Surface area ≤ 0.8 µm
size (DN) 50, 65, 80, 100, 125, 150, 200
size (OD) 2“, 2 ½“, 3“, 4“
Other parts
Materials Stainless steel 1.4301
Seals EPDM / HNBR
Surface area polished, matte
Production
Operating pressure 0 - 10 bar
Temperature 0 -95 °C
Pressure impact safety 40-50 bar tested
Control air 5 -8 bar
Cleaning
CIP operating pressure 2 -5 bar
Flushing chamber pressure < 0.5 bar
Temperature 0 – 95 °C / 140 °C
Noise emissions
Operator position noise < 70 dB(A)

Operation/Use
16 / 36
DOUBLE-SEAT VALVE INOVA (Type 580)
BA 058000.06 EN 15.11.2018
04
Fig. 3: Valve dimensions [mm]
DN OD a b c d e
50 2“ 100,4 128,0 85,0 347,5 695,5
65 2 ½“ 115,4 145,0 100,0 371,0 751,0
80 3“ 130,4 183,5 116,0 464,0 898,5
100 4“ 140.4 192.0 136.0 521,5 984.5
125 --- 180,4 245,0 165,0 575,5 1120,5
150 --- 180,4 257,5 190,0 588,0 1170,5
Kvs value [m3/h]
DN OD Passage above Valve seat Passage below Weight in kg
50 2“ 82 64 88 17,5
65 2 ½“ 135 100 150 27,5
80 3“ 200 150 230 37,2
100 4“ 310 215 395 49,5
125 --- 390 370 460 79,5
150 --- 505 430 605 84,0
Transpot

Operation/Use
15.11.2018
DOUBLE-SEAT VALVE INOVA (Type 580)
BA 058000.06 EN 17 / 36
6Operation/Use
6.1 Valve Switching Functions
The double-seat valve’s function is characterized through the following described switching
statuses.
6.1.1 Production – Valve Closed
•The various process media flow through the upper and lower piping system or
valve housing.
•Both valve disks are in the final position in the seat area and seal the piping
systems against each other.
•The leakage chamber, which is connected with the free environment, is
formed between both valve disks.
•When there are sealing problems in the seat area, the respective medium can
flow through the leakage chamber and the leakage outlet to the outside.
05 06
Fig. 4: Valve closed Valve open
6.1.2 CIP or Production Valve Open
•Through the compressed air supply at Pos. A (Page 21, Fig. 7/8) the lower
valve disk moves from its final position against the upper valve disk. At the
same time, the seat sealing is maintained. The double-seat valve switches
leak-free.
•The leakage chamber between the now adjacent valve disks is sealed via the
leakage chamber sealing.
The valve disks travel into the opened valve position.
•When the valve is closed, the valve disks now travel against the upper valve
seat.
•The lower disk, maintaining its seat sealing, travels into the final position and
at the same time continually opens the leakage chamber.

Operation/Use
18 / 36
DOUBLE-SEAT VALVE INOVA (Type 580)
BA 058000.06 EN 15.11.2018
6.1.3 Seat cleaning – valve seat open
•Through the compressed air supply at Pos. B (Page 21, Fig. 7+8) the upper
valve disk moves from the valve seat and at the same time makes a defined
gap free.
•The cleaning medium flows from the upper piping area into the leakage
chamber and flows around the valve seat area.
•The cleaning medium is guided outdoors through the leakage outlet.
•The upper valve disk again moves against the valve seat and closes the gap.
07 08
Fig. 5: Upper valve seat Lower valve seat
6.1.4 Seat cleaning - lower valve seat
•The lifting of the valve disk takes place through compressed air supply at Pos.
C (Page 21, Fig. 7/8). In so doing, the lower valve disk moves from the valve
seat and makes a defined gap free.
•The cleaning medium flows from the lower piping area into the leakage
chamber and flows around the valve seat area.
•The cleaning medium is guided outdoors through the leakage outlet.
•The lower valve disk again moves into the valve seat and closes the gap.

Operation/Use
15.11.2018
DOUBLE-SEAT VALVE INOVA (Type 580)
BA 058000.06 EN 19 / 36
6.1.5 Cleaning – Balancer (B)
09
Fig. 6: Cleaning methods
In hygienically sensitive processes we recommend connecting the flushing chambers to the
CIP circuit via controllable valves.
•During the valve switching process the balancers move between the product
chamber and the adjacent upper and lower flushing chambers.
•The cleaning medium flows through the flush chambers via a stationary inflow
and outflow.
•The balancers’ upper and lower product-affected area are thus integrated into
the cleaning process.
6.1.6 Cleaning – Leakage Chamber (L)
This is an option if the double-seat valve is not equipped with any single-seat lifting.
•In the valve’s closed and open position, the leakage chamber between the
two valve disks is sealed all the way to the piping system.
•Through a stationary supply pipe, cleaning medium can be injected from
below into the leakage chamber.
•The cleaning medium is guided outdoors through the leakage outlet.
(B)(L)

Operation/Use
20 / 36
DOUBLE-SEAT VALVE INOVA (Type 580)
BA 058000.06 EN 15.11.2018
6.2 CIP cleaning
Double-seat valves are optimally designed for automated CIP processes.
See also Chapter 10.4, Page 34 (cleaning parameters).
•If the double-seat valve does not have any single-seat lifting, it should then be
cleaned at the same time as the pipe cleaning. At the same time, the valve
should be moved in short intervals into the OPEN and CLOSED position.
•If the double-seat valve is equipped with single-seat lifting, then the
respective valve disk can be lifted if the accompanying pipe is located in the
CIP operation.
•If the double-seat valve has leakage chamber cleaning, this can be activated
during the valve’s CLOSED position when there is a pipe in the CIP operation.
•If cleaning of the balancer is planned, this can be activated during the valve’s
CLOSED position when there is a pipe in the CIP operation.
6.3 Leakage detection
It is essential that the form seals in the separate valve disks are protected from mechanical
damage during operation and maintenance.
A leakage in the area of the product and flushing chamber can be recognized as described
below:
•In the case of defective form seals of a valve disk, liquid flows out from the
respective pipe at the leakage outlet in a closed valve position.
•In the case of defective sealing of the leakage chamber, liquid runs out at the
leakage outlet with an opened valve.
•In the case of defective inner sealing of the flushing chambers (lip seals), liquid
flows into the upper or lower flushing chambers. As this is normally filled with
flushing water from the last CIP cleaning, liquid flows away immediately at the
respective CIP outflow.
•In the case of defective exterior sealing of the flushing chambers (quad ring),
liquid flows out at the guide bush’s upper or lower venting bore hole.
This manual suits for next models
8
Table of contents
Other handtmann Control Unit manuals

handtmann
handtmann 12605 User manual
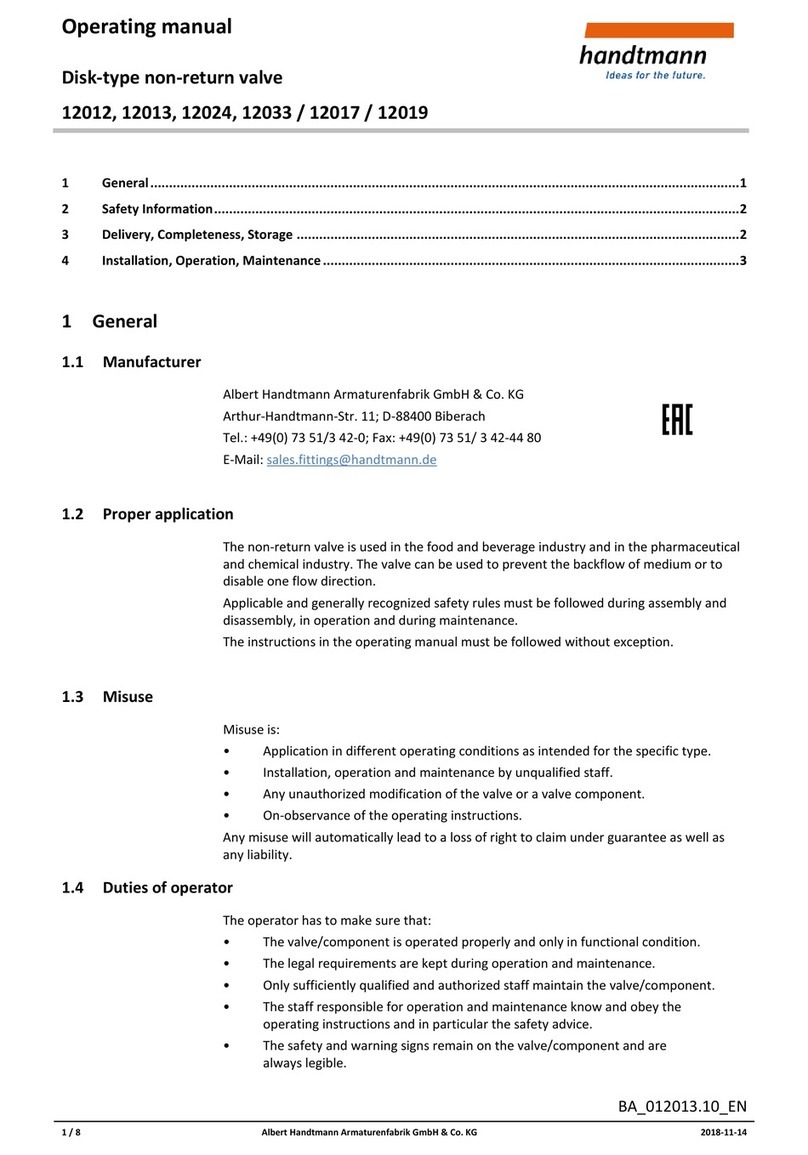
handtmann
handtmann 12012 User manual
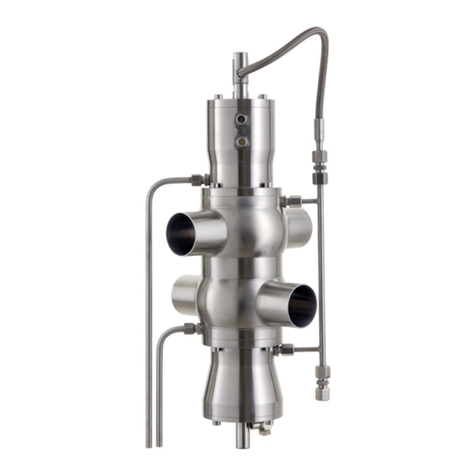
handtmann
handtmann 491 User manual

handtmann
handtmann FLOWmag 12020 User manual

handtmann
handtmann 33501 User manual
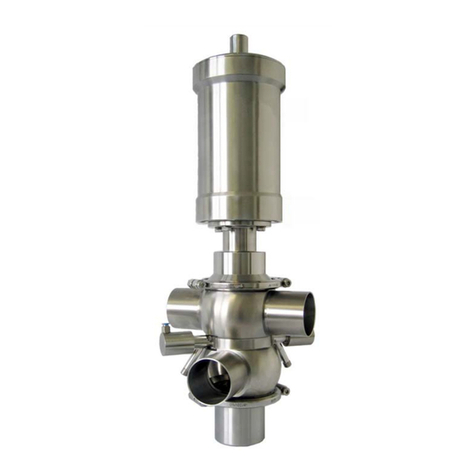
handtmann
handtmann 75100 User manual

handtmann
handtmann 12504 User manual

handtmann
handtmann 12503 User manual

handtmann
handtmann 12501 User manual
Popular Control Unit manuals by other brands

Krom Schroder
Krom Schroder PFU 780 technical information
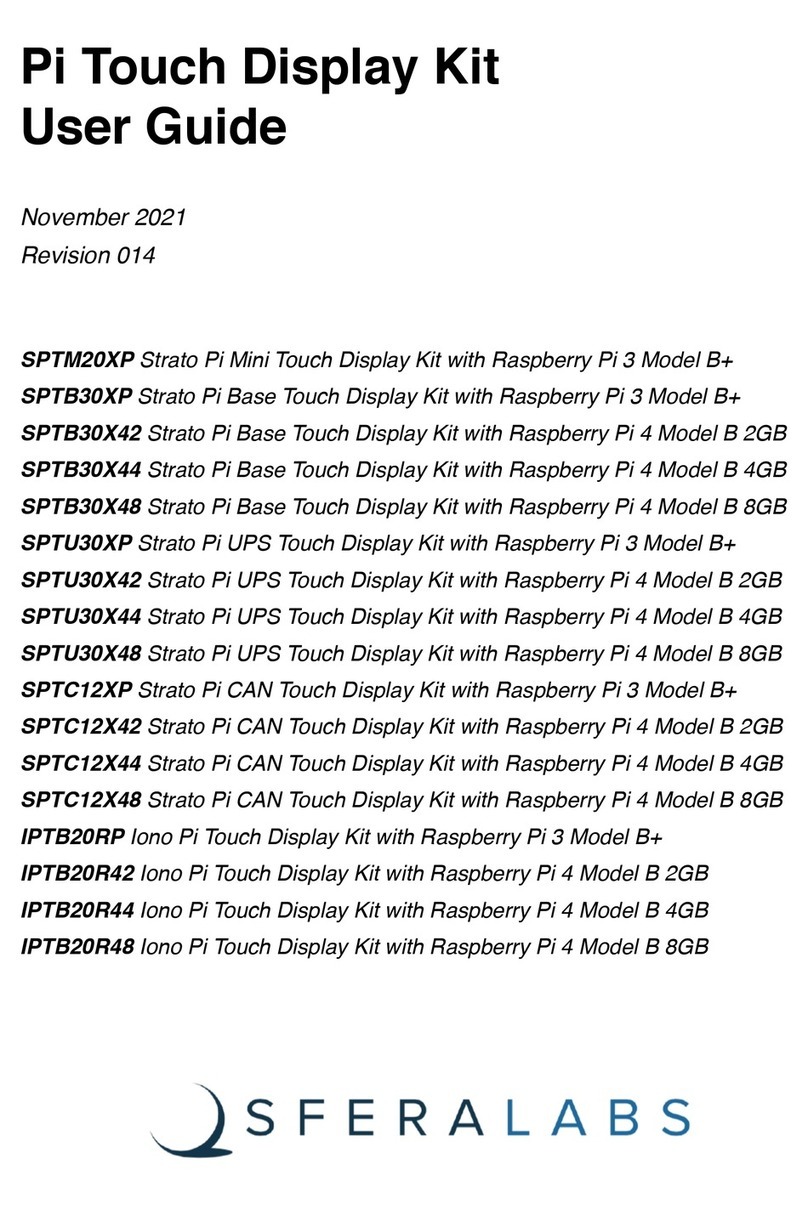
Sferalabs
Sferalabs Strato Pi SPTM20XP user guide
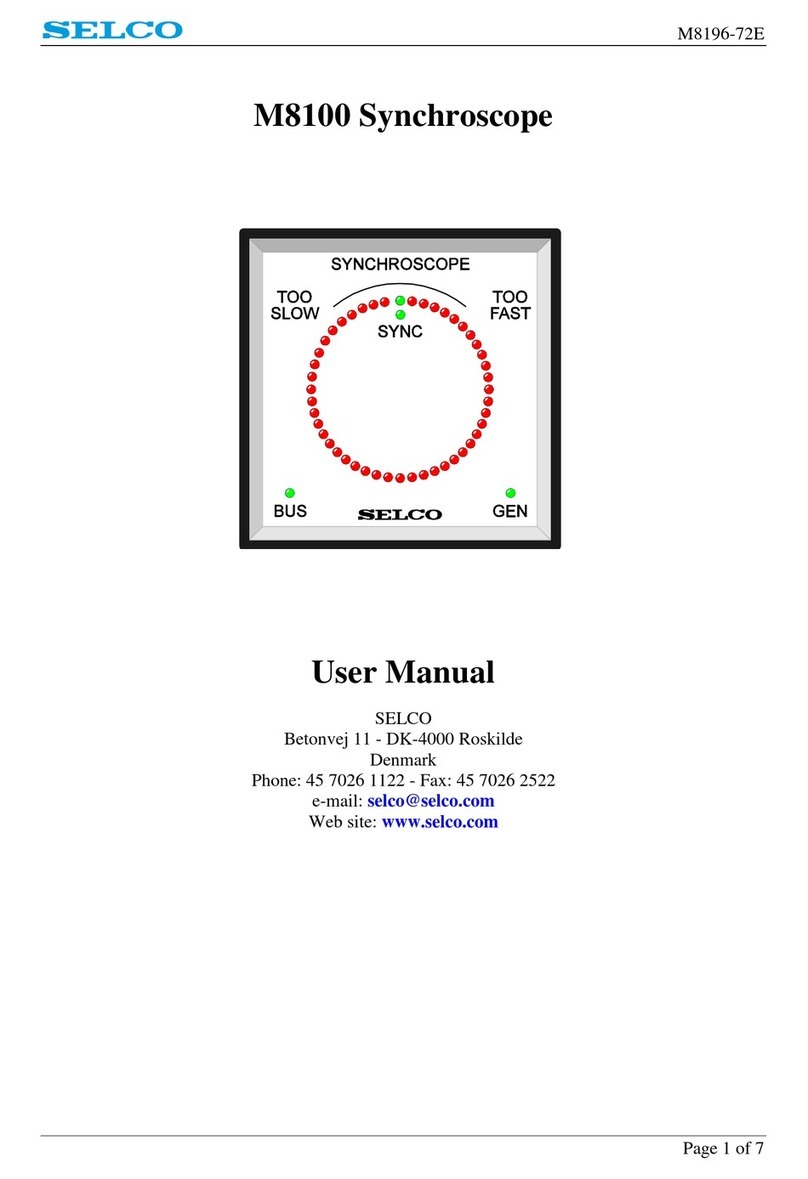
Sel
Sel M8100.0060 user manual
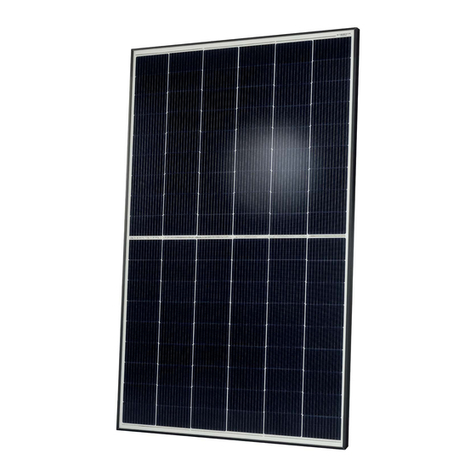
Qcells
Qcells Q.PEAK DUO M-G11 Series Installation and operation manual
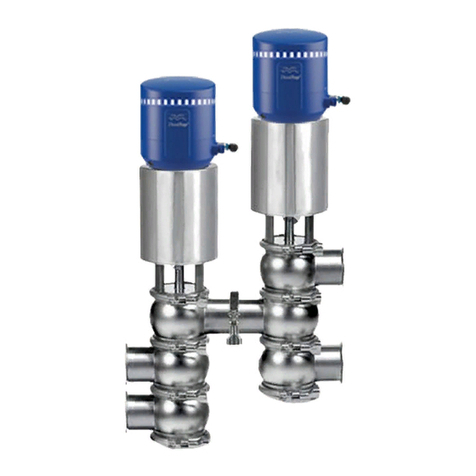
Alfalaval
Alfalaval Unique 7000 Series instruction manual
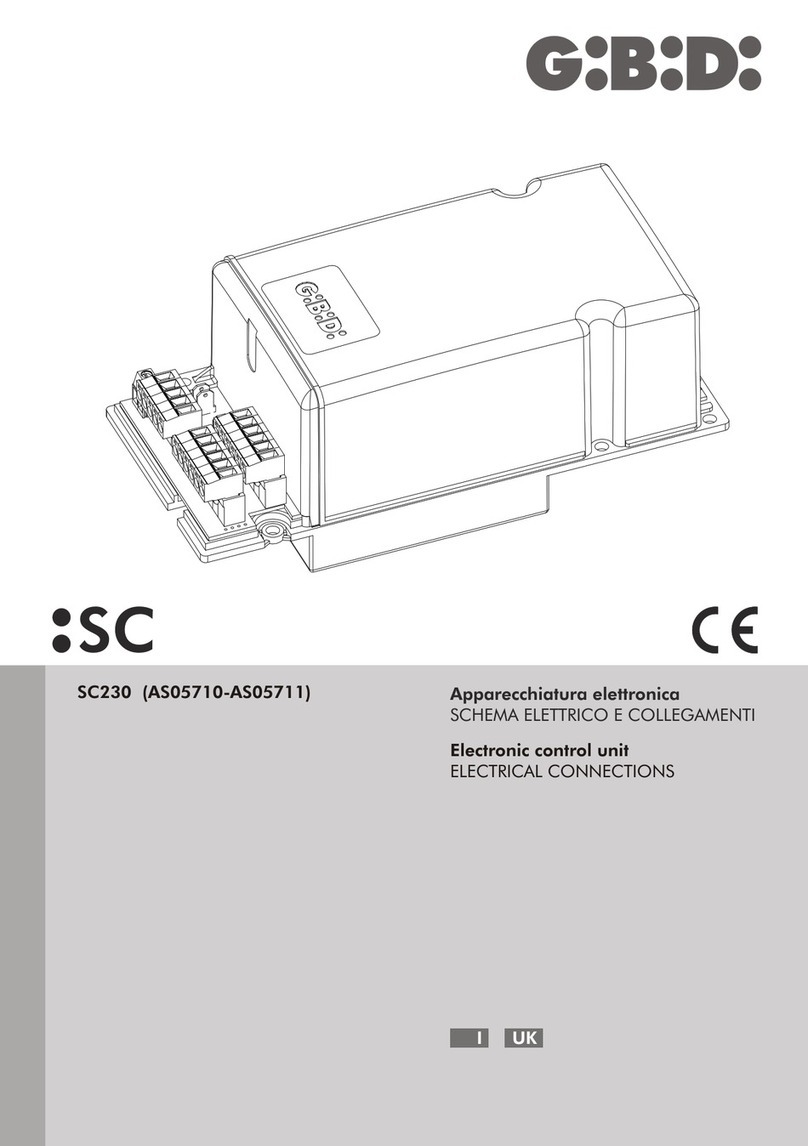
GiBiDi
GiBiDi SC230 electrical connections