Hansa C21 User guide

MANUFACTURER: HANSA NEW ZEALAND
+64 7 849 4749 info@hansaproducts.co.nz
www.hansaproducts.com
REST OF WORLD:
Please refer to www.hansaproducts.com for
a current list of our authorised dealers and
contact details relevant to your territory
Original Instructions
Operation, maintenance and safety manual
All operators must fully read and understand
this operator’s manual before using the chipper.
Keep this manual for future reference.

Hansa C21 O&M Manual - OM-022 Revision B 21/08/2018
© Hansa Chippers 2018
TABLE OF CONTENTS
WHAT CAN MY HANSA CHIPPER PROCESS?..................................................................................................................................1
INTENDED USES OF THE CHIPPER ...............................................................................................................................................................1
RECEIVING YOUR HANSA CHIPPER ...............................................................................................................................................1
CHIPPER COMPONENTS........................................................................................................................................................................... 1
ASSEMBLING THE CHIPPER........................................................................................................................................................... 2
ATTACH THE DRAWBAR ...........................................................................................................................................................................2
ATTACH THE MUD GUARDS ...................................................................................................................................................................... 2
ATTACH THE TAIL LIGHTS .........................................................................................................................................................................3
SECURE THE WIRE LOOM .........................................................................................................................................................................3
REWIRE THE TRAILER PLUG.......................................................................................................................................................................3
ATTACH THE WHEELS ..............................................................................................................................................................................4
FIT THE OUTLET CHUTE............................................................................................................................................................................4
FIT THE INLET CHUTE............................................................................................................................................................................... 5
SAFETY .........................................................................................................................................................................................5
OPERATOR COMPETENCY.........................................................................................................................................................................5
TOWING SAFETY ....................................................................................................................................................................................6
IDENTIFYING HAZARDS AND RISKS .............................................................................................................................................................. 6
OPERATION..................................................................................................................................................................................7
SAFE SETUP PROCEDURE..........................................................................................................................................................................7
SAFE OPERATING PROCEDURE...................................................................................................................................................................7
STARTING PROCEDURE ............................................................................................................................................................................9
SHUTDOWN PROCEDURE .......................................................................................................................................................................10
PETROL.............................................................................................................................................................................................. 10
EMERGENCY STOP................................................................................................................................................................................10
STORAGE.................................................................................................................................................................................... 11
TROUBLESHOOTING................................................................................................................................................................... 11
WHAT TO DO IF:.................................................................................................................................................................................. 11
MAINTENANCE........................................................................................................................................................................... 12
KNIFE RE-SHARPENING AND KNIFE REPLACEMENT .......................................................................................................................................12
ANVIL ADJUSTMENT/REPLACEMENT......................................................................................................................................................... 15
ENGINE SERVICING ...............................................................................................................................................................................15
ENGINE OIL......................................................................................................................................................................................... 15
BELT TENSION .....................................................................................................................................................................................16
BELT REPLACEMENT..............................................................................................................................................................................17
TYRE PRESSURE ...................................................................................................................................................................................18
MAINTENANCE &SERVICE INTERVALS ......................................................................................................................................................19
BOLT TORQUE .....................................................................................................................................................................................19
SPECIFICATIONS ......................................................................................................................................................................... 20
DECALS....................................................................................................................................................................................... 21
HANSA GLOBAL INDUSTRIAL LIMITED WARRANTY..................................................................................................................... 23
COMMISSIONING CHECKLIST AND REGISTRATION ..................................................................................................................... 25
SOUND OUTPUT INFORMATION ................................................................................................................................................ 25
EC DECLARATION OF CONFORMITY............................................................................................................................................ 26

Hansa C21 O&M Manual - OM-022 revision A 21/08/2018
© Hansa Chippers 2018
1
What can my Hansa chipper process?
Intended uses of the chipper
The C21 Hansa chipper is built to process organic material including wooden branches not exceeding 130 mm in diameter. It is
designed to be used on by commercial garden maintenance contactors, arborists, tree contractors and hire / rental companies. Do
NOT use the chipper for any other purpose.
Organic wastes include:
Prunings, stalks, roots, vegetable matter, hay, grass, bark
Dry manure
Branches
Palm fronds
Dead and hard timbers (Note: these will dull the knives faster)
Paper or cardboard
Do NOT process:
Flax, root balls
Soil, bones, sand, grit, stones, metal
If you have any questions, contact your authorised dealer.
Do NOT exceed 130 mm branch diameter
Receiving your Hansa chipper
You may receive your chipper assembled from your dealer or it may be packaged in two boxes. Assembly takes approximately 30
minutes, two people working together will make the assembly easier.
Chipper components

Hansa C21 O&M Manual - OM-022 revision A 21/08/2018
© Hansa Chippers 2018
2
Assembling the chipper
When you receive your Hansa brush chipper, the inlet and outlet chute may not be assembled on the chipper. All the fasteners
(bolts, nuts and washers) will be attached to their respective components
Tools required for assembly (not supplied):
•16 mm spanner - to fit the inlet and outlet chute
•17 mm spanner - to fit the inlet and outlet chute
Attach the drawbar
Slide the wire loom through the drawbar so that it
comes out the tow hitch end. Insert three bolts,
spring washers, and heavy washers through the
chassis and the side of the drawbar. Ensure that the
spring washer is touching the bolt head and the
heavy washer is touching the chassis.
Insert two bolts and light washers through the two
center holes in the drawbar bracket, followed by a
heavy washer and nyloc nut. Ensure that the light
washer is touching the bolt head and the heavy
washer is touching the nyloc nut.
Insert two bolts, spring washers, and heavy washers
through the outer holes of the drawbar bracket.
Ensure that the spring washer is touching the bolt
head and the heavy washer is touching the drawbar
bracket. Tighten the nuts and bolts to secure the
drawbar.
Attach the mud guards
Attach the left mud guard - secure the mud guard to
the chipper chassis by inserting three bolts and light
washers through the holes at the base of the
mudguard (indicated by the arrows in the image).
Screw the nyloc nuts on underneath and tighten
them.
Note: Feed the wire loom through the slot in the
mud guard.
Attach the ‘L’ bracket to the top of the mud guard
by screwing in the bolt, spring washer and heavy
washer which has been circled. Ensure that the
spring washer is touching the bolt head and the
heavy washer is touching the ‘L’ bracket.
1
Drawbar
bracket
2

Hansa C21 O&M Manual - OM-022 revision A 21/08/2018
© Hansa Chippers 2018
3
Attach the right mud guard - secure the mud guard
to the chipper chassis by inserting two bolts and
light washers through the holes where the arrows
point to. Screw the nyloc nuts on underneath and
tighten them.
Note: Feed the wire loom through the slot in the
mud guard.
Attach the ‘L’ bracket to the top of the mud guard
by screwing in the bolt, spring washer and heavy
washer which has been circled. Ensure that the
spring washer is touching the bolt head and the
heavy washer is touching the ‘L’ bracket.
Attach the tail lights
Slide the tail light through the hole in the back of the
mud guard. Ensure that the tail light is orientated so
that the indicator is closest to the outside edge of
the mud guard. Insert the bolts through the holes in
the tail light and mud guard, then secure the tail
light by tightening the nuts and bolts.
Note: Do NOT overtighten the nuts.
Lightly press the plastic caps into the inserts above
the bolt head using a nylon hammer or suitable
alternative.
Secure the wire loom
Each mud guard requires seven cable ties to secure
the wire loom to it. (Two more behind the wheel
which cannot be seen in this image).
Rewire the trailer plug
Unscrew the plastic nut from the trailer plug and
slide it onto the wire loom, followed by the rubber
bung. Ensure that the nut and bung are in the
correct orientation (refer to image).
Unscrew all 7 relevant screws and insert the wires
in the correct order (as shown in the image).
Signal Left –Yellow
Brake –Red
Service –N/A
Earth –White
Reverse –N/A
Tail –Brown
Signal Right –Green
3
4
5
6
Plastic
nut
Rubber
bung
Wire
clamp

Hansa C21 O&M Manual - OM-022 revision A 21/08/2018
© Hansa Chippers 2018
4
Tighten the smaller screws to hold the wires
connections in place, then tighten the two bigger
screws to clamp the wire loom into place. Finally,
clip the other half of the trailer plug into place and
screw the plastic nut on.
Attach the wheels
Bolt the wheels on, then screw the wheel nuts on,
ensuring the rounded side of the nuts taper into the
steel rim.
Tighten the nuts using a 19 mm socket, then torque
them to 80 N.m.
Fit the outlet chute
Lightly grease the flange on the chipper body.
Slide the outlet chute onto the greased flange of the
chipper body, ensuring that the locking hinge is
open.
7
8
9
Locking
hinge

Hansa C21 O&M Manual - OM-022 revision A 21/08/2018
© Hansa Chippers 2018
5
Close the locking hinge and tighten the outlet chute
locking handle to secure the outlet chute to the
chipper body.
Note: The outlet chute locking handle will be in the
documentation package.
Fit the inlet chute
Fix the inlet chute - place the inlet chute onto the
chipper body with the black rubber flap sandwiched
in between and ensure all three holes line up.
Tighten the nuts, washers, and bolts using a 16 mm
and 17 mm spanner. Ensure that the washer is
touching the bolt head.
Line up the holes and insert the bolts, washers and
nuts; ensuring that the heavy washer is touching the
bolt head.
Safety
Preventing accidents is the responsibility of every equipment operator. The operator is responsible for any accidents or hazards
occurring to people or their property. Ensure every operator is familiar with the safe operation procedures and controls of the
machine, how to identify hazards, and the steps required to avoid injury while handling and operating the chipper. Relevant
information is contained in this manual.
Do NOT modify the design of the chipper.
Operator competency
Ensure that every person operating the chipper understands and follows the safe operating and maintenance procedures
as detailed in this manual.
Do NOT allow persons below the age of 16 to operate the chipper. Additionally, local regulations may restrict the age of
the operator.
Do NOT allow persons with reduced physical, sensory or mental capabilities, or lack of experience and knowledge to
operate the machine.
10
Outlet
chute
locking
handle
11
12

Hansa C21 O&M Manual - OM-022 revision A 21/08/2018
© Hansa Chippers 2018
6
Towing safety
Rotate the discharge chute to face the opposite direction of the towing vehicle before towing and lock into position
Connect tow coupling to the towing vehicle (check the ball dimensions are the same as the coupling)
Connect safety chain with shackle
Plug in lights and check they are operational
Check wheel nuts periodically to make sure they are secure
Ensure the jockey wheel is in the up position and locked away during travel
Ensure that the machine is towed in accordance with local trailer transport regulations
Identifying hazards and risks
Identify hazards and risks, and take preventative steps to avoid accidents and minimise risk. Possible hazards include, but are not
limited to, moving parts, thrown objects, weight of chipper and components, and the operating environment.
Below is a list of hazards and actions required to prevent injury.
Hazard
Risk
Corrective action
Dust
Injury or irritation of the
eyes
Respiratory irritation
Wear safety glasses
Process freshly cut materials and/or wear a dust mask
Exhaust Fumes
Respiratory irritation
Place the chipper in a manner that the operator is not
exposed to direct exhaust fumes
Hot Exhaust
Heat burns
Keep bare hands and other body parts a safe distance away
from hot exhaust
Fire
Heat burns
Clear any build-up of chipping debris around the engine and
exhaust regularly
Belt Drive
Skin pinching and/or
abrasions
Ensure that the belt guard is in place, and keep away from
the belt and its guarding
Cutting rotor and knives
Pinching, crushing, cutting,
severing
Keep hands and other body parts out of the inlet chute
Use a stick to push materials into the inlet chute
Do NOT push the stick beyond the guard flap
Sound
Damage to hearing
Always wear ear protection when operating the machinery
Discharge material
Eye injury, minor cuts
Always wear safety glasses when operating the machinery
Do NOT stand in front of the outlet chute
Do NOT put the machinery in a place where the
outlet chute is directed on a hard surface
Feeding material
Cuts and scrapes
Wear safety gloves
Wear tight fitting long sleeves and pants to cover bare skin
when operating the machinery
Weight of the chipper
Straining, crushing
Place the machinery on level ground
Do NOT attempt to move the machinery up/down
slopes unless is attached to a towing vehicle
Petrol, oil, grease
Poisoning, skin irritation,
harmful vapours
Take care when handling petrol, oil and grease
Wash skin if contaminated with petrol, oil or grease
Do NOT refuel the chipper in enclosed areas

Hansa C21 O&M Manual - OM-022 revision A 21/08/2018
© Hansa Chippers 2018
7
Operation
The chipper is self-feeding and has a large inlet opening. It can process:
•Prunings, stalks, vines, leaves, roots and vegetable matter, paper and cardboard
•Freshly cut material is better to process than dry material
•Maximum capacity is 130 mm diameter branches
It is helpful (but not required) to keep a wooden stick handy, approx. 60 mm diameter x 600 mm long for:
•Pushing in short, brushy and very leafy materials
•Keeping the inlet chute clear
Safe setup procedure
Before you start:
Ensure the chipper is positioned in an open area and on firm level ground.
Ensure that the outlet chute is discharged onto soft ground (e.g. grass)
Do NOT allow the outlet chute to discharge chip onto hard surfaces (such as a paved or gravel surface)
Ejected material can rebound and cause injury
Keep children, pets, and spectators clear of the work area at all times
Do NOT operate the chipper where there is a hazard to onlookers
Do NOT allow any person under the age of 18 to operate the chipper
Check:
That all screws, nuts, bolts, and other fasteners are properly secured
That all chipper components are in place and in good condition
If any parts are worn or damaged, contact Hansa for replacements
That fuel and engine oil levels are above the minimum levels
That the inlet chute and housing are clear of any leftover material
That all labels are in good condition and easily legible
Replace damaged or unreadable warning and operating
View photos of labels in the ‘Decals’ section
Refuelling:
Take extra care in handling fuels
They are flammable and vapors are explosive
Use only an approved fuel container
Always replace and securely tighten fuel cap after refuelling
Allow engine to cool down before refuelling
Do NOT smoke when using or refuelling the chipper
Never remove fuel cap or add fuel with the engine running
Never refuel the chipper indoors
Never store the chipper or fuel container inside where there is an open flame, such as a water heater
If fuel is spilled, do not attempt to start the engine, but move the chipper away from the area of spillage before
starting
Safe operating procedure
Wear safety equipment: Safety glasses and earmuffs must be worn
at all times
Wear work gloves: Wearing work gloves is optional but highly
recommended - ensure that the gloves fit tightly
Tie long hair up
Long hair could be pulled into the chipper
Wear clothes that sit tightly
Avoid scarves and any items that can get caught in the chipper
Keep your face and body away from the inlet chute
DO:

Hansa C21 O&M Manual - OM-022 revision A 21/08/2018
© Hansa Chippers 2018
8
Stand clear of the discharge zone, even when no material is being fed into the machine
Place the chipper on even ground and direct the outlet chute onto soft ground
Ensure the exhaust is pointing away from the working area and downwind from the operator and onlookers
Keep proper balance and footing at all times and stand at the same level as the chipper
Do NOT overreach
Do NOT run near the machine
Feed only freshly cut material into the chipper
Do NOT feed in materials covered in gravel, stones and dirt as this can rebound, injure the operator and damage
the machinery
Prune to a size that suits the chipper’s capabilities
Pre-cut side branches
Branches will ‘self-feed’ more efficiently
Keep the engine clean of debris and other accumulations
This prevents damage to the engine or possible fire
Feed limbs and branches through butt end first, leaving the foliage on
This helps guide the limb down the inlet chute
It reduces spinning and the occurrence of ejection of small pieces back up the inlet chute
Hold larger branches back and feed the chipper with care until you are familiar with its capacity
The engine will slow down or stall if the branch is too large
Feed longer pieces together with short stubby pieces
Feed soft materials intermittently with branches
The wood chips tend to clean out any soft residue left in the chipper
The chipper can clog up with soft, wet or fibrous materials
Keep the outlet free of blockage
If a blockage occurs, turn the engine off, disconnect the spark plug wire and wait for rotor to stop spinning. Open
the outlet chute and remove material until the outlet chute is clear
As the discharge material piles up
Move the chipper to direct the outlet chute away from the pile, or move the processed material
to avoid blocking
Turn off the engine whenever you leave the work area
Run the chipper in an enclosed area
Exhaust fumes contain carbon monoxide which is poisonous, colourless, odourless, and tasteless
Operate the chipper wearing loose clothing and untied long hair
Stand at a higher level than the base of the chipper when feeding material into it
Process old materials such as dried wooden branches
They get very hard and springy when dried out
They are more awkward to handle
The knives dull much quicker
Feed short, stubby pieces of wood into the chipper
They bounce and spin in the inlet chute
Feed short stubby pieces together with longer pieces
Feed branches that are too large
The chipper can easily stall
Put soil, sand, grit, stones, glass, pieces of metal or other foreign objects into the chipper
This will damage the sharp edge of the cutting knives and can rebound and injure the operator
Put root balls and dead wood into the chipper
This dulls the knives quickly
Overload the chipper (max branch diameter 130 mm)
If the cutting rotor is slowing down, feed the material in slower
Allow processed material to build up in the discharge area as this can:
Prevent proper discharge
Result in kickback of material through the feed opening
Transport the chipper while the engine is running
Tamper with the engine governor settings on the chipper
The governor controls the maximum safe operating speed and protects the engine and all moving parts from
damage caused by overspeed
DO NOT:

Hansa C21 O&M Manual - OM-022 revision A 21/08/2018
© Hansa Chippers 2018
9
Operate the chipper with blunt knives
This causes excessive vibration which may result in damage to the chipper
Touch any guards or stick hands between guards while the chipper is running
Put hands or any other part of the body or clothing:
Inside the feed chute past the rubber flap
Inside or near the opening of the discharge chute
Near any moving part
Remove any guards on the chipper unless the engine is turned off and the cutting rotor has come to a complete standstill
Leave the chipper on while it is unattended
Starting procedure
Turn the ignition key to the “on” position (first click).
Pull the choke lever to turn the choke on.
Turn the throttle lever away from the “min” position,
about 1/3 of the way toward the “max” position.
Disengage the belt drive by winding the engagement
handle counter clock-wise until it comes to a stop.
Turn the ignition key clockwise to start the engine.
Once the engine is started and has warmed up (approx. 10 seconds), turn the choke lever to the “off” position by
pushing the lever in towards the engine.
To engage the belt drive, slowly rotate the engagement
handle clockwise until it comes to a stop. This must be
done slowly to allow the cutting rotor to pick up speed;
otherwise the engine may stall.
Move the throttle lever to the “max” position.
1
1
2
3
4
5
Throttle lever
(1/3 position)
Choke lever
(“on” position)
Ignition key
(“on” position)

Hansa C21 O&M Manual - OM-022 revision A 21/08/2018
© Hansa Chippers 2018
10
WARNING! Do NOT disengage the belt drive with the chipper running at full revs, as this will cause friction and vibration
on the belt drive.
Petrol
The chipper requires 91 unleaded petrol to run; check the petrol level before starting.
Emergency stop
The emergency stop acts as an immediate kill switch to the engine. It does not immediately stop the rotor from spinning. The rotor
will continue to spin for some time due to its rotational inertia. To engage the emergency stop, push the red button. To disengage
the emergency stop, twist the red button clockwise until it releases outwards.
Use it when foreign matter such as sand, stones or metal enter the inlet chute
Use it in response to an immediate hazard/danger to an operator or onlooker
After the rotor comes to a halt, follow the normal shutdown procedure in addition to using
the emergency stop
Inspect the machine before resetting the emergency stop
Under normal conditions, Do NOT use the emergency stop in place of the regular shutdown
procedure
Shutdown procedure
Turn the throttle lever to the “min” position and wait for
the rotor to slow down.
Disengage the belt drive by rotating the engagement
handle anti clock-wise until it comes to a stop.
Turn the ignition key to the “off” position.
1
2
3
Throttle lever
(min position)
Ignition key
(off position)

Hansa C21 O&M Manual - OM-022 revision A 21/08/2018
© Hansa Chippers 2018
11
Storage
Always allow the chipper to cool before storing
Store the chipper out of the reach of children
Store the chipper where fuel vapor will not reach an open flame or spark
Switch the fuel lever to the off position
For extended storage periods, run the engine dry of fuel
Store the chipper out of the rain
Water can rust the steel body of the chipper
Troubleshooting
What to do if:
The chipper won’t start
•The engine oil level might be too low
The chipper is fitted with oil alert and will not start if the oil level is too low
Check the oil level and top up if required
•The chipper is placed on a slope
The chipper is fitted with oil alert and will not start if the oil is not level
Move the chipper to level ground
•The emergency stop is still engaged
Ensure emergency stop is disengaged by twisting the red button clockwise before starting the chipper
Belt drive engagement will not work
•The inlet chute or housing might be blocked
Turn engine off, disconnect the spark plug wire, ensure rotor has completely stopped, remove debris,
restart engine, then attempt to re-engage the belt drive
The chipper slows down and stalls
•The chipper is clogged up
Turn the engine off, disconnect the spark plug wire, ensure rotor has completely stopped, remove debris,
then close and lock the outlet chute
Discharge slows down
•The chipper is clogged up
Turn the engine off, disconnect the spark plug wire, ensure rotor has completely stopped, remove debris,
then close and lock the outlet chute
The chipper is slowing down
•The chipper can’t process the amount of material fed into it
Feed the material in slower
Reduce material volume
The chipper will not self-feed
The knives and/or anvil might be blunt
Inspect and sharpen or replace knives and/or anvil as required. Ensure correct clearances between
knives and anvil
The material is ejected in long strips
•The knives and/or anvil might be blunt
Inspect and sharpen or replace knives and/or anvil as required. Ensure correct clearances between
knives and anvil
The chipper is clogged
Turn the engine off, disconnect the spark plug wire, ensure rotor has completely stopped, remove
debris, then close and lock the outlet chute
The chipper starts making unusual noise, the cutting rotor strikes a foreign object or the chipper starts to vibrate
Turn the engine off, disconnect the spark plug wire, ensure rotor has completely stopped, then inspect
for damage
Replace or repair any damaged parts
Check for and tighten any loose parts
Do NOT attempt to repair the chipper unless you are competent to do so

Hansa C21 O&M Manual - OM-022 revision A 21/08/2018
© Hansa Chippers 2018
12
Maintenance
Maintain the chipper with care and keep it clean at all times.
To service or inspect the equipment, or to change an accessory, you must:
✓Switch the engine off
✓Allow the chipper to cool before any inspections or adjustments
✓Wait until the cutting rotor and engine are at a complete standstill before opening the cutting rotor housing
✓Disconnect the spark plug wire from the spark plug
Initially after 2 working hours:
✓Check for any loose nuts and bolts
✓Check belt tension (refer to belt tension section)
The belts will stretch when they are new
✓Grease the two rotor bearings
One or two pumps are sufficient
Be careful not to over grease
The bearings are greased when the equipment is new
Grease with bearing grease or all-purpose grease
Every 20 working hours:
✓Check for any loose nuts and bolts
✓Check belt tension (refer to belt tension section)
✓Grease two bearings as above, be careful not to over grease
✓Check sharpness of knives
✓Check condition of guarding
A damaged guard must be replaced by an identical or equivalent guard immediately
It is recommended to contact Hansa for a replacement guard.
Knife re-sharpening and knife replacement
How do I know that the knives need re-sharpening?
Chipper loses its self-feeding action with blunt knives
Material has to be pushed in
Material comes out in long strips
Blunt knives will cause excessive vibration
Blunt knives result in damage to the chipper
How to re-sharpen the knives:
If you don’t have a surface grinder or are unsure how to re-sharpen the knives, contact a professional saw doctor or Hansa to
arrange re-sharpening.
Tools and materials required for re-sharpening (approx. 40 mins):
•18 mm spanner
•5 mm hexagonal Allen key
•A stick magnet (optional)
•Surface grinder
•Coolant
WARNING! Do NOT operate your chipper with blunt knives.
WARNING! Be careful when working around the sharp knives. Be aware that even though the power source is
unplugged, the cutting means can still move.

Hansa C21 O&M Manual - OM-022 revision A 21/08/2018
© Hansa Chippers 2018
13
Remove the knives for sharpening
Open the rotor housing cover by removing the
two housing cover locking bolts with an 18 mm
spanner, then lift the rotor housing cover to
access the cutting rotor.
Rotate the cutting rotor to gain access to the
knives, then engage the belt drive to stop the
cutting rotor from rotating.
Use an 18 mm spanner to remove the knives from the cutting rotor. There
are four bolts that you must remove to do so.
Be careful not to drop the bolts or knives into the chipper
A stick magnet can be used to retrieve them if this does occur
Measure the width of the knife and check that it will be at least 46 mm
after sharpening.
If the knives will be shorter than 65 mm, then the knives should be
replaced. Please contact your nearest Hansa dealer.
Sharpen the knives
Sharpen the knives on a surface grinder. A cutting angle of 36 ° is critical
for the performance of the chipper. Make sure plenty of coolant is used
when grinding to avoid softening of the steel knives.
1
2
3
MIN 65 mm
4
36 °

Hansa C21 O&M Manual - OM-022 revision A 21/08/2018
© Hansa Chippers 2018
14
Edge of
cutting
rotor
Reinstall the knives
Clean all mounting surfaces and remount
the knives in the reverse procedure.
Note: Be sure to replace the knives the
correct way around (as shown in the
diagram). Only tighten the clamping bolts
enough to hold the knives in place during
adjustment. Do not tighten them fully until
step 7.
Adjust the knives initially using the
adjustment bolts to protrude the edge of
the knife just past the edge of the knife
holding block.
After sharpening, the width of the knives
will have been reduced, therefore the gap
between the knives and anvil may require
adjustment. This gap is tapered out slightly
to allow for a small amount of movement in
the cutting rotor as it bites into the wood.
If there is not enough clearance, the knife
edge may touch the anvil through
deflection when cutting heavy branches
and damage the sharp edge. Too much
clearance will allow small twigs and fibrous
materials to be dragged through without
being cut.
Adjust the knife in or out using the two
adjustment bolts to achieve the correct
clearance between the knife and anvil. The
clearance between the knife and anvil
should be approximately 1 mm on the
inside closest to the bearing and 3 mm on
the outside closest to the edge of the
cutting rotor (refer to diagram for more
detail).
After the correct clearance is set, fully
tighten the clamping bolts using a torque
wrench to 35 N.m. and tighten the locking
nuts on the adjustment bolts.
5
Adjustment bolts
6
Anvil
Cutting
rotor
Knife
1 mm
clearance
3 mm
clearance
Bearing
Top view: Knife and anvil set-up
Knife holding
block
Knife
Side view: Cutting rotor
7
Clamping bolts
Clamping plate
Knife
Locking nuts
Rotor disk
Knife holding block

Hansa C21 O&M Manual - OM-022 revision A 21/08/2018
© Hansa Chippers 2018
15
Note: Before adjusting the knives, ensure
the gap between the holding block and the
anvil is 4 - 5 mm. If not, then the anvil can
be adjusted through the mounting slots.
Once the position has been set, tighten the
three M10 countersunk anvil bolts and
torque to 50 Nm, then make further
adjustments with the knives as described
above.
Turn the cutting rotor slowly by hand to
check that it turns freely.
Close and secure the outlet chute.
Anvil adjustment/replacement
When cutting edge of the anvil is dull, the anvil may be reversed can be reversed. Each edge of the anvil will typically last for several
hundred hours of operation. When both edges are worn, the anvil will need to be replaced.
To access the anvil the inlet chute needs to be removed (use the reverse procedure to fit the inlet on page 3). A 5 mm Allen key, a
17 mm socket and an extension are required to remove the anvil.
With the knives removed or set right back, the gap between the knife holding block and anvil should be 4 - 5 mm. The position of
the anvil can be adjusted through the mounting slots. When this has been set, tighten the three M10 countersunk anvil bolts using
a torque wrench to 50 Nm and then make further adjustments with the knives as described above.
Turn the cutting rotor slowly by hand to check that it turns freely.
Engine servicing
For servicing of the engine, please refer to the Honda engine manual.
Engine oil
It is recommended you check the oil level every time you use your
chipper. To check the oil level, remove the dipstick, clean the
dipstick, then fully insert the dipstick back into its housing.
Remove it and fill as necessary, using the diagram as a reference.
For optimal performance of your chipper, the engine oil should be
completely changed every 100 operating hours, or roughly once
every 12 months on average.
If the engine oil needs to be changed, follow these steps:
Run the engine for 1-2 minutes in order to warm up the
oil. Place a container underneath the engine. Remove
oil filler cap/dipstick and oil drain plug (using a 19 mm
spanner), then let the oil drain into the container
through the opening in the chassis.
WARNING! Every time the knife clamping bolts are torqued up to 77 Nm and loosened off again, the life of the
bolts is reduced. The knife clamping bolts must be replaced at most after every six sharpens. Contact Hansa for
replacement bolts (m12x50 bolts of grade 10.9 or higher). Use only genuine Hansa bolts.
8
1
Oil drain plug

Hansa C21 O&M Manual - OM-022 revision A 21/08/2018
© Hansa Chippers 2018
16
Screw the oil outlet drain plug back in and fill the engine with 2 Litres of SAE 10W30 or SAE 10W40 through the
oil filler cap (located on the top of the engine).
Using the dipstick, check the oil to make sure it is at the right level (close to the supper limit indicator, but not
over). Screw the oil filler cap/dipstick back into the hole. Dispose of the used engine oil in an environmentally
sensitive way.
Belt tension
Correct belt tension is crucial for minimising belt wear and maximising machine efficiency. To check the belt tension, first ensure
the belt drive is disengaged by turning the engagement handle anticlockwise. Then, from the fully disengaged position, gently turn
the engagement handle clockwise until you feel it start to resist. From this position, turn the engagement handle clockwise. If the
tension is set correctly, the handle should turn one full revolution clockwise before coming to a stop. If there is a difference greater
than 1/6 of a revolution either clockwise or anticlockwise from one full revolution, then the belt tension should be corrected
following the ‘adjusting belt tension’ procedure.
Adjusting belt tension
Using two 24 mm spanners, unlock the two locking nuts from
above the adjustment block on the engagement handle by
turning the top nut anti clockwise and the bottom nut
clockwise. Then move both locking nuts upward along the
thread. It may help to remove the upper exhaust guard (a 13
mm spanner and a 6 mm Allen key are required to do so).
From the fully disengaged position, gently turn the
engagement handle clockwise until you feel it start to resist.
From this position, turn the engagement handle one full
revolution clockwise. This is the recommended tension for the
belt drive when in the fully engaged position.
Using two 24 mm spanners, screw the two M16 adjustment
nuts downwards until they touch the adjustment block. Then
turn the top nut clockwise and the bottom nut anti clockwise
simultaneously to lock the nuts in place.
2
3
1
2
3
Adjustment
nuts
Adjustment
block
Adjustment
nuts
Adjustment
block

Hansa C21 O&M Manual - OM-022 revision A 21/08/2018
© Hansa Chippers 2018
17
Belt replacement
If the belts in your chipper look similar to any of the following images or are clearly broken, then they need to be replaced.
If a belt change is necessary, follow these steps
Using a 6 mm Allen key, unbolt and remove the guards
(9xM8 cap screws).
Using two 17 mm spanners, unbolt and remove the engine
(4xM10 Nuts).
Note: loosen the belt tensioner to allow room for removal.
Remove the old belts and replace (2 x B46 vee belts).
Note: The belts pass in between the idler wheel and belt
guide on the tensioner arm.
1
2
3
Cracked underside of belt
Sidewall belt wear
Soft, swollen belt
Worn cover on back of belt
Split belt cover
Idler Wheel
Tensioner arm
Belt guide

Hansa C21 O&M Manual - OM-022 revision A 21/08/2018
© Hansa Chippers 2018
18
Place engine back in place and ensure the pulleys are in
line.
Fully tighten the four bolts holding the engine to the
chassis. Check the pulleys are still in line by placing a
straight-edge across the top and bottom front pulley. If
they are not in line, loosen the four bolts holding the
engine in to the chassis and then repeat this step.
Ensure belts are properly tensioned (follow the ‘Adjusting
belt tension’ process on page 16). Fasten the guards back
into place.
Note that after replacing a belt, the tension of the new belt will quickly change as the belt initially wears into the pulley system.
Recheck the belt tension after two hours of operation after belt replacement.
Tyre pressure
For the road-towable model, the maximum recommended tyre pressure is 65 Psi.
Do NOT over inflate the tyres. Over inflation may cause tyres to rupture.
4
5
6
Other manuals for C21
1
Table of contents
Other Hansa Chipper manuals
Popular Chipper manuals by other brands

Wallenstein
Wallenstein BX52RI Operator's manual
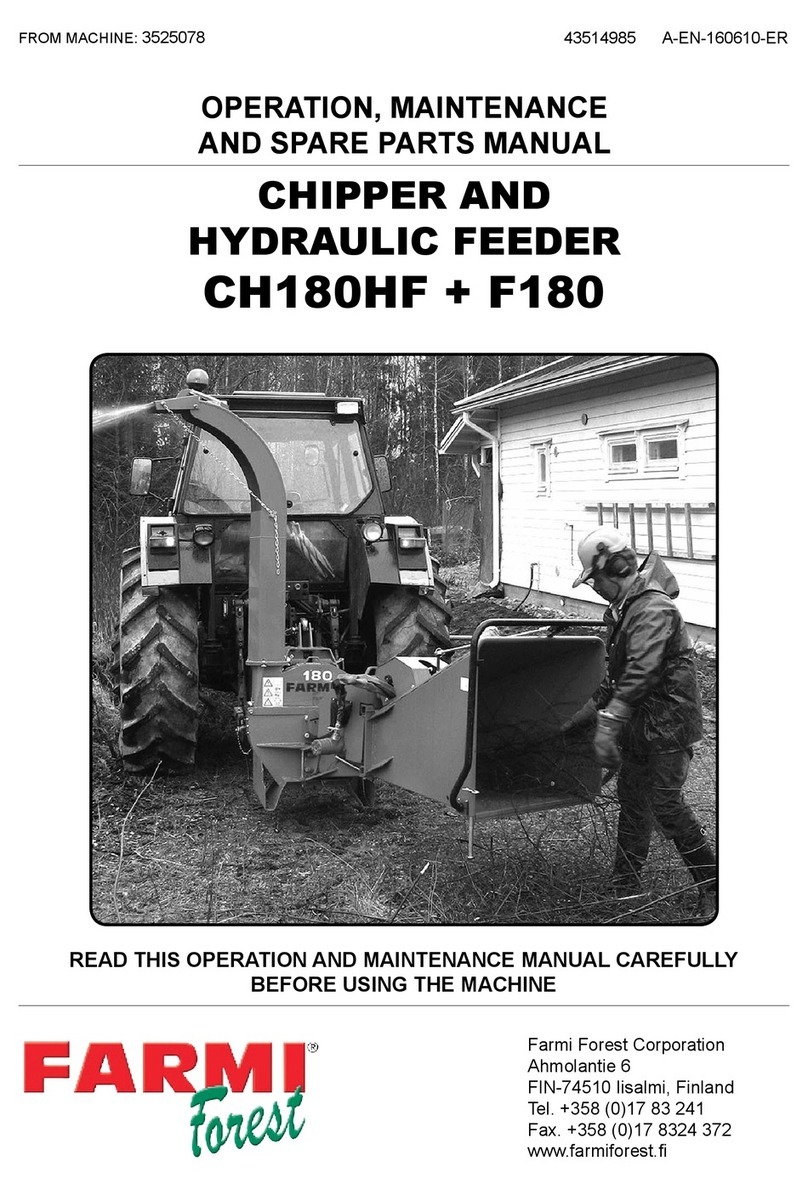
Farmi Forest Corporation
Farmi Forest Corporation CH180HF OPERATION, MAINTENANCE AND SPARE PARTS MANUAL

Stiga
Stiga BioQuiet Instructions for use
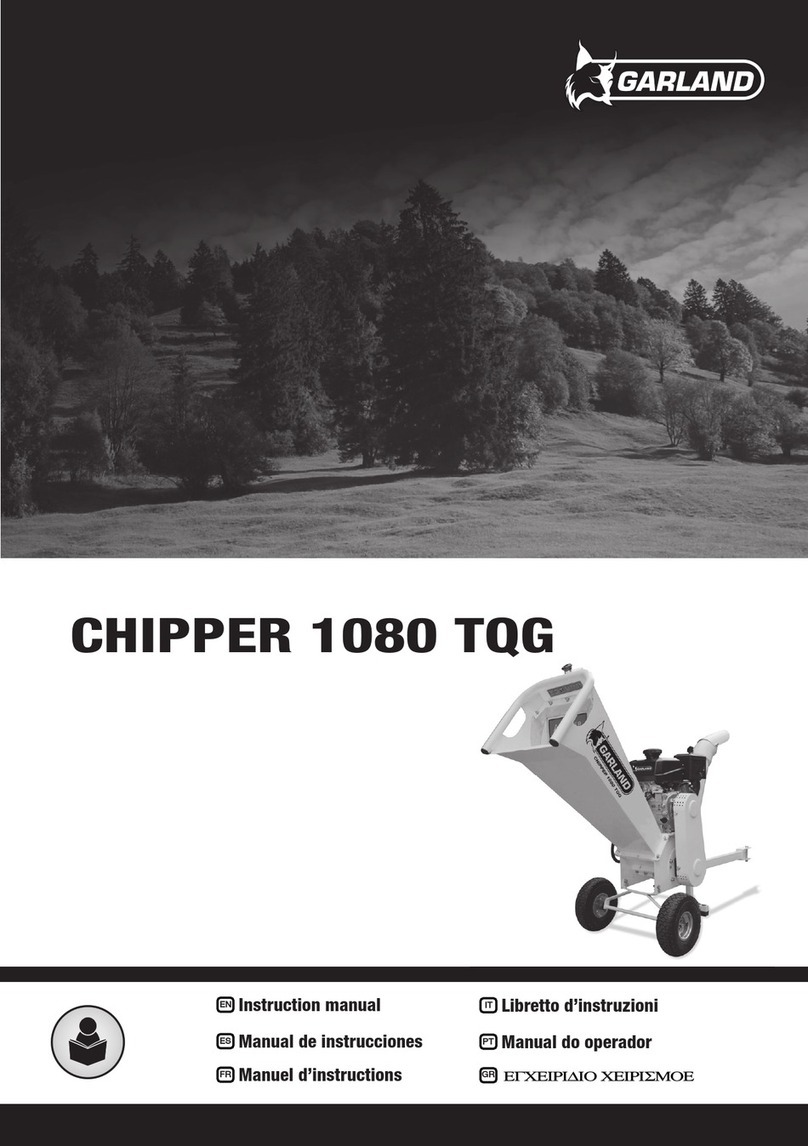
Garland
Garland 1080 TQG instruction manual

Timberwolf
Timberwolf tw pto 150h manual
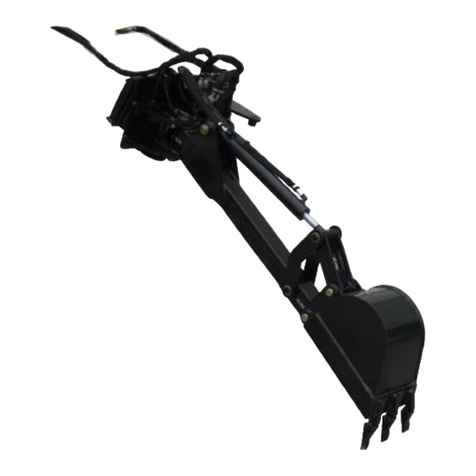
Spartan Equipment
Spartan Equipment 75594 Operator and parts manual