Hansa C45 User guide

HANSA NEW ZEALAND
+64 7 849 4749 info@hansaproducts.co.nz
www.hansachippers.com
HANSA AUSTRALIA
1800 426 722 info@hansaproducts.com.au
www.hansaproducts.com.au
HANSA C45
Operation, maintenance, and safety manual
All operators must fully read and understand
this operator’s manual before using the chipper.
Keep this manual for future reference.
Register your Hansa chipper to qualify
www.hansaproducts.com/registration

Hansa C45 O&M Manual –OM-027 First Release 4/05/2021
© Hansa Chippers 2021
TABLE OF CONTENTS
WHAT CAN MY HANSA CHIPPER PROCESS?...............................................................................................................................................1
INTENDED USES OF THE CHIPPER .....................................................................................................................................................................................................1
CHIPPER OVERVIEW ..........................................................................................................................................................................................2
SAFETY ....................................................................................................................................................................................................................3
OPERATOR COMPETENCY .............................................................................................................................................................................................................3
IDENTIFYING HAZARDS AND RISKS..............................................................................................................................................................................................3
TOWING SAFETY ............................................................................................................................................................................................................................4
CHIPPING SAFETY .............................................................................................................................................................................................................................5
CHECKLIST BEFORE OPERATION ..................................................................................................................................................................................................5
SAFE SETUP PROCEDURES ...........................................................................................................................................................................................................5
SAFE OPERATING PROCEDURES...................................................................................................................................................................................................5
OPERATION ...........................................................................................................................................................................................................8
OUTLET CHUTE ADJUSTMENT ..........................................................................................................................................................................................................8
FEED ROLLER CONTROL ....................................................................................................................................................................................................................9
AUTOMATIC FEED CONTROL ...........................................................................................................................................................................................................9
ADJUST THE AUTO-TRIP SETTING:............................................................................................................................................................................................10
HOUR METER /TACHOMETER ......................................................................................................................................................................................................11
EMERGENCY STOP.........................................................................................................................................................................................................................11
BOTTOM BUMP BAR (OPTIONAL MACHINE FEATURE).................................................................................................................................................................11
STARTING PROCEDURE..................................................................................................................................................................................................................12
SHUTDOWN PROCEDURE ..............................................................................................................................................................................................................13
TROUBLESHOOTING ....................................................................................................................................................................................... 14
MAINTENANCE & SERVICE ............................................................................................................................................................................ 15
WARNINGS....................................................................................................................................................................................................................................15
LIFTING THE SWING ARM FOR ACCESS..........................................................................................................................................................................................15
OPENING THE ROTOR COVER FOR ACCESS TO CUTTING ROTOR...................................................................................................................................................16
KNIFE RE-SHARPENING AND KNIFE REPLACEMENT..............................................................................................................................................................16
ANVIL ADJUSTMENT ...................................................................................................................................................................................................................19
BELT TENSION................................................................................................................................................................................................................................20
CHECKING AND SETTING BELT TENSION...................................................................................................................................................................................20
BELT REPLACEMENT .................................................................................................................................................................................................................21
GREASE POINTS...........................................................................................................................................................................................................................22
GENERAL GREASE POINTS ........................................................................................................................................................................................................22
ENGINE OUTPUT SHAFT GREASING......................................................................................................................................................................................24
HYDRAULIC SYSTEM ...................................................................................................................................................................................................................24
ENGINE SERVICING .....................................................................................................................................................................................................................24
OTHER SERVICING ......................................................................................................................................................................................................................24
ROTOR BEARING REPLACEMENT ..............................................................................................................................................................................................24
TYRE PRESSURE..........................................................................................................................................................................................................................25
BOLT TORQUE .............................................................................................................................................................................................................................25
MAINTENANCE &SERVICE INTERVALS ...................................................................................................................................................................................26
SPECIFICATIONS ............................................................................................................................................................................................... 27
DECALS................................................................................................................................................................................................................. 28
HANSA GLOBAL INDUSTRIAL LIMITED WARRANTY ........................................................................................................................... 32
COMMISSIONING CHECKLIST AND REGISTRATION ............................................................................................................................. 34

Hansa C45 O&M Manual –OM-027 First Release 4/05/2021
© Hansa Chippers 2021
1
What can my Hansa chipper process?
Intended uses of the chipper
The Hansa C45 chipper is built to process organic material including wooden branches not exceeding 178mm in diameter. It is
designed to be used on by commercial arborists, tree contractors and hire / rental companies. Do NOT use the chipper for any
other purpose.
Organic wastes include:
Prunings, stalks, roots, vegetable matter, hay, grass, bark
Branches
Palm fronds
Dead and hard timbers (Note: these will dull the knives faster)
Paper or cardboard
Do NOT process:
Flax, root balls
Soil, bones, sand, grit, stones, metal
If you have any questions, contact your authorised dealer.
Do NOT exceed 178mm branch diameter

Hansa C45 O&M Manual –OM-027 First Release 4/05/2021
© Hansa Chippers 2021
2
Chipper overview

Hansa C45 O&M Manual –OM-027 First Release 4/05/2021
© Hansa Chippers 2021
3
Safety
Preventing accidents is the responsibility of every equipment operator. The operator is responsible for any accidents or hazards
occurring to people or their property. Ensure every operator is familiar with the safe operation procedures and controls of the
machine, how to identify hazards, and the steps required to avoid injury while handling and operating the chipper. Relevant
information is contained in this manual.
Do NOT modify the design of the chipper.
Operator competency
Ensure that every person operating the chipper understands and follows the safe operating and maintenance procedures
as detailed in this manual.
Do NOT allow persons below the age of 18 to operate the chipper. Additionally, local regulations may restrict the age of
the operator.
Do NOT allow persons with reduced physical, sensory or mental capabilities, or lack of experience and knowledge to
operate the machine.
Identifying hazards and risks
Identify hazards and risks, and take preventative steps to avoid accidents and minimise risk. Possible hazards include, but are not
limited to, moving parts, thrown objects, weight of chipper and components, and the operating environment.
Below is a list of hazards and actions required to prevent injury.
Hazard
Risk
Corrective action
Dust
Injury or irritation of the
eyes
Respiratory irritation
Wear safety glasses
Process freshly cut materials and / or wear a dust mask
Exhaust Fumes
Respiratory irritation
Place the chipper in a manner that the operator or onlookers
are not exposed to direct exhaust fumes
Fire
Heat burns
Clear any build-up of chipping debris around the engine and
exhaust regularly
Hot Exhaust
Heat burns
Keep bare hands and other body parts a safe distance away
from hot exhaust
Belt Drive
Skin pinching and/or
abrasions
Ensure that the belt guard is in place, and keep away from
the belt
Cutting rotor and knives
Pinching, crushing, cutting,
severing
Keep hands and other body parts out of the inlet chute
Use a stick to push materials into the inlet chute
feed roller
Do NOT push material into the feed roller with your
hands
Feed swing arm
Crushing, severing
Do not touch or approach the feed roller motor and swing
arm while the machine is operating
Feeding roller and
feeding material
Being pulled into chipper
resulting in possible
crushing, cutting, severing
Do not stand directly in front of the inlet table while feeding
material into the chipper; stand to either side.
Do not climb onto the inlet table or enter the infeed chute
unless the machine is off, and the cutting rotor is stationary
Sound
Damage to hearing
Always wear hearing protection when operating the
machinery
Discharge material
Eye injury, minor cuts
Always wear safety glasses when operating the machinery
Do NOT stand in front of the outlet chute

Hansa C45 O&M Manual –OM-027 First Release 4/05/2021
© Hansa Chippers 2021
4
Do NOT face the machinery in a place where the
outlet chute is directed on a hard surface
Feeding material
Cuts and scrapes
Wear tight fitting safety gloves
Wear tight fitting long sleeves and pants to cover bare skin
when operating the machinery
Weight of the chipper
Straining, crushing
Place the machinery on firm level ground
Do NOT attempt to move the machinery up/down
slopes unless is attached to a towing vehicle
Pinch points
Pinching, crushing
When opening/closing the inlet table, bonnet, or other
guard, it is recommended to use the handles provided
Petrol, oil, grease
Poisoning, skin irritation,
harmful vapours
Take care when handling petrol, oil and grease
Wash skin if contaminated with petrol, oil or grease
Do NOT refuel the chipper in enclosed areas
Towing safety
Before towing, rotate the discharge chute to face either forwards or backwards, parallel with the direction of towing and
lock into position by; 1. Engaging lock pin and 2. Tightening outlet crank handle:
Lock the inlet table in the up position
Connect the tow coupling to the towing vehicle (check the ball dimensions are the same as the coupling)
Connect safety chain with shackle
If the machine is fitted with brakes, check handbrake is off and road brakes are on by removing the reversing lever
Plug in lights and check they are operational
Check wheel nuts and axle U-bolts periodically to make sure they are secure
Ensure the jockey wheel is in the up position and locked away during transport
Ensure the machine is towed in accordance with local trailer transport regulations
Turn the machine off while towing
2. Tighten outlet crank handle
1. Engage lock pin (up)

Hansa C45 O&M Manual –OM-027 First Release 4/05/2021
© Hansa Chippers 2021
5
Chipping safety
Checklist before operation
Engine:
✓Check oil level in engine
✓Check condition of air cleaner
✓Refer to engine manual for more details
Check Hydraulics:
✓Check level of hydraulic fluid
✓Check all hydraulic components for leaks
General:
✓Check machine for proper lubrication
✓Check nuts and bolts to ensure they are tight
✓Check tires for proper air pressure as stated on the tire
✓Check diesel level
✓Check that the fuel cap is secured and there is no fuel leaking from the tank
✓Check direction of the discharge chute
✓Check guards are all in place and in good condition
✓Check all labels are legible. Replace if necessary (contact Hansa for replacements)
✓Refer to maintenance section for more details
Safe setup procedures
Ensure all pre-operation checks have been done
Setup the work site so there is no danger to traffic or public and provide adequate warnings
Ensure the chipper is positioned on firm level ground
Ensure the feed control bar is in the neutral position when starting the chipper
Ensure the inlet table is clear of material when starting the chipper
Ensure the throttle control lever is the initially in the idle position when starting the chipper
Ensure the outlet chute is discharged onto soft ground (e.g. grass)
Do NOT allow the outlet chute to discharge chip onto hard surfaces (such as a paved or gravel surface)
Ejected material can rebound and cause injury
Keep children and spectators clear of the work area at all times
Do NOT operate the chipper where there is a hazard to onlookers
Do NOT allow any person under the age of 18 to operate the chipper
Refuelling:
Take extra care in handling fuels
They are flammable and vapors are explosive
Use only an approved fuel container
Always replace and securely tighten fuel cap after refuelling
Allow engine to cool down before refuelling
Do NOT smoke when using or refuelling the chipper
Never remove fuel cap or add fuel with the engine running
Never refuel the chipper indoors
Never store the chipper or fuel container inside where there is an open flame, such as a water heater
If fuel is spilled, do not attempt to start the engine. Wipe up the spilled fuel, and move the chipper away from
the area of spillage before starting
Safe operating procedures
Wear safety equipment: Safety glasses and hearing protection
must be worn at all times
Wear work gloves: The wearing of work gloves is optional but
highly recommended - ensure that the gloves fit tightly
Do NOT wear loose fitting gloves or gloves with long cuffs
Loose gloves may get snagged by branches, which could result in the operator being pulled into the chipper
DO:

Hansa C45 O&M Manual –OM-027 First Release 4/05/2021
© Hansa Chippers 2021
6
Tie long hair up
Long hair could be snagged by a branch and may be pulled into chipper
Wear clothes that sit tightly
Avoid scarves and any items that can get caught in the chipper or snagged on branches
Place the chipper on even ground and direct outlet chute onto soft ground
Ensure exhaust is pointing away from the working area and downwind from the operator and onlookers
Keep proper balance and footing at all times and stand at the same level as the chipper
Do NOT climb onto the inlet table to push material into the feed roller
Ensure the chipper is positioned so that there is a minimum inlet table height of 600 mm off the ground
Keep your face and body away from the inlet chute. Stand to the side of the inlet table while feeding material into the
chipper
Standing to the side gives better access to the control bar and helps in keeping clear from flying debris
Feed only freshly cut material into the chipper
Do NOT feed in materials covered in gravel, stones and dirt as this can rebound, injure the operator and damage
the machinery
Prune to a size that suits the chipper’s capabilities
Pre-cut side branches
The branch will ‘self-feed’ more efficiently
Keep the engine clean of debris and other accumulations
This prevents damage to the engine or possible fire
Feed limbs and branches through butt end first, leaving the bushy head on
This helps guide the limb down the inlet chute
It reduces spinning and the occurrence of ejection of small pieces back up the inlet chute
Feed soft materials intermittently with branches
The wood chips tend to clean out any soft residue left in the chipper
The chipper can clog up with soft, wet or fibrous materials
Keep well clear of the outlet chute discharge area, even when the chipper is not currently processing material
High velocity, sharp discharge can cause serious injury
Keep the outlet free of blockage
If blockage occurs, turn the engine off and wait for rotor to stop spinning. Open the outlet chute access panel and
remove material until the outlet chute is clear
Keep the feed roller free of blockage
If a blockage occurs, only attempt to manually remove the blockage when the engine is off, and the cutting rotor
is stopped. To get access to the feed roller area, refer to the instructions in the “Error! Reference source not
found.” section in this manual.
Turn off the engine whenever you leave the work area
Run the chipper in an enclosed area
Exhaust fumes contain carbon monoxide which is poisonous, colourless, odourless, and tasteless
Operate the chipper wearing loose clothing and untied long hair
Stand at a higher level than the base of the chipper when feeding material into it
Feed flax and cabbage tree leaves into the machine
These stringy materials can wrap around the rotor shaft and work their way into the bearing.
If any stringy material becomes wrapped around the rotor shaft, remove it before it works itself into the bearing
Process old materials such as dried wooden branches
They get very hard and springy when dried out
They are more awkward to handle
The knives dull much quicker
Feed short, stubby pieces of wood into the chipper
They bounce and spin in the inlet chute
Feed short stubby pieces together with longer pieces
Feed branches that are too large (max 254 mm branch diameter)
The chipper engine will stall, which could result in damage to the engine or drive belts
Put soil, sand, grit, stones or pieces of metal into the chipper
This will damage the sharp edge of the cutting knives and can rebound and injure the operator
Put root balls and dead wood into the chipper
DO NOT:

Hansa C45 O&M Manual –OM-027 First Release 4/05/2021
© Hansa Chippers 2021
7
This dulls the knives quickly
Overload the chipper
If the cutting rotor is slowing down, feed the material in slower
Transport the chipper while the engine is running
Tamper with the engine governor settings on the chipper
The governor controls the maximum safe operating speed and protects the engine and all moving parts from
damage caused by overspeed
Operate the chipper with blunt knives
This causes excessive vibration which may result in damage to the chipper
Remove any guards on the chipper unless the engine is turned off and the cutting rotor has come to a complete standstill
Enter the inlet chute
Get on, or lean over the feed table
Put hands or any other part of the body or clothing:
Inside the inlet chute
Inside or near the opening of the discharge chute
Near any moving part
Use the feed control bar as a handle to manoeuvre the machine

Hansa C45 O&M Manual –OM-027 First Release 4/05/2021
© Hansa Chippers 2021
8
Operation
The chipper is self-feeding and has a large inlet opening. It can process:
•Prunings, stalks, vines, leaves, roots and vegetable matter, paper and cardboard
•Freshly cut material is better to process than dry material
•Maximum capacity is for the C45 is 178 mm
It is recommended to keep a wooden stick handy, approx. 60 mm diameter x 1000 mm long for:
•Pushing in short, brushy and very leafy materials
•Keeping the inlet table clear
Outlet chute adjustment
The C45 is fitted with a rotating outlet chute and deflector, allowing the operator to control the direction of material discharge
from the machine:
Adjust outlet rotation direction: disengage the lock pin (down), loosen the rotation crank handle, change outlet direction, then
tighten the rotation crank handle to lock into position.
Adjust outlet height: turn outlet height crank handle clockwise (higher) or anticlockwise (lower).
Adjust deflector angle: loosen wingnut, adjust angle, tighten wingnut.
Lock for towing: rotate the discharge chute to face either forwards or backwards, parallel with the direction of towing and lock
into position by:
1. engaging lock pin and
2. tightening rotation crank handle.
Outlet height adjustment
Outlet rotation adjustment
Outlet deflector adjustment
Loosen wingnut to
adjust deflector angle
Lock pin for towing (up = locked) Only works with outlet facing forwards or backwards
Rotation lock crank handle
(clockwise = locked)
Outlet height crank handle
(clockwise = higher)
Handle for rotating outlet

Hansa C45 O&M Manual –OM-027 First Release 4/05/2021
© Hansa Chippers 2021
9
Feed roller control
The feed roller is controlled with the yellow control bar which surrounds the inlet table.
The control bar has three settings:
1) Reverse
2) Neutral
3) Feed
When the bar is fully pushed in, the feed roller will be set to reverse. When the bar is fully
pulled out, the feed roller will feed material. The neutral position lies between the reverse
and feed positions.
Automatic Feed Control
The electronic automatic feed control system controls the feed roller and improves operation by:
✓Keeping the engine RPM at optimal speed and power
✓Preventing the engine from stalling when overloaded
✓Assisting with clearing blockages
This system eliminates the need for the operator to control the speed at which material is manually fed into the chipper. A sensor
detects the speed of the cutting rotor, once this speed drops to a pre-set level, the feed roller stops the material feeding into the
machine. The engine then recovers to higher RPM and once it reaches a pre-set speed the feed-roller will start feeding again. The
feed roller will also reverse back slightly after stopping (reducing the friction between the wood and knives), resulting in quicker
RPM recovery.
The feed control can be set to 6 different AutoTrip levels from 1 to 6 or be disabled (OFF). Setting “1” is the default factory setting
which allows the engine to drop the most in speed before pausing feeding. Setting “6” allows the engine to drop the least in speed
before pausing feeding. Setting “OFF” will disable automatic feed control and the engine may stall if it is overloaded. If there are
any issues with the electronic automatic feed system, the chipper can be used with the auto-feed disabled.
WARNING! Be careful using the machine with auto-feed disabled as the machine can be stalled easily.
Feed –Neutral –Reverse

Hansa C45 O&M Manual –OM-027 First Release 4/05/2021
© Hansa Chippers 2021
10
Adjust the auto-trip setting:
Press “OK” to enter the menu
Press “OK” to enter “Trip Setting” (highlighted in
blue)
Use the arrows to navigate up and down settings.
Push “OK” to change the active trip setting to the
highlighted setting (highlighted in blue).
Once the desired setting has been selected, push
the “ESC” button twice to go back to the main
menu
1
2
3
Arrows to
navigate
“OK” to
select
Active trip
setting
4

Hansa C45 O&M Manual –OM-027 First Release 4/05/2021
© Hansa Chippers 2021
11
Hour meter / tachometer
The display screen shows:
▪Tachometer: Engine speed (RPM, revolutions per minute). The engine speed is measured from the cutting rotor speed
sensor and so only displays accurate speed while the cutting rotor is engaged.
▪Hour meter (also displays minutes)
Emergency stop
The C45 has two emergency stops on the top of the inlet chute. The emergency stops act as an immediate kill switch to the engine.
It does not immediately stop the rotor from spinning. The rotor will continue to spin for some time due to its rotational inertia. The
feed roller, however, will stop almost immediately. To engage the emergency stop, push the red button. To disengage the
emergency stop, twist the red button clockwise until it releases outwards.
Use it when foreign matter such as sand, stones or metal enter the inlet chute
Use it in response to an immediate hazard/danger to an operator or onlooker
After the rotor comes to a halt, follow the normal shutdown procedure in addition to
using the emergency stop
Inspect the machine before resetting the emergency stop
Under normal conditions, do NOT use the emergency stop in place of the regular
shutdown procedure
Bottom bump bar (optional machine feature)
The C45 may be fitted with a bottom bump bar which acts as an extra safety feature in addition
to the emergency stops. Pushing the bump bar in immediately stops the movement of the feed
roller. After activating the bump bar, the movement of the feed roller may be reset by setting
the feed roller control bar to neutral, then back to feeding. The bump bar is designed to be
activated by pushing against it with your hand, knee, foot or other body part in the event in
which an operator is caught by in-feeding branches.
Hour meter (hours
and minutes)
Engine speed
(RPM, revolutions
per minute)

Hansa C45 O&M Manual –OM-027 First Release 4/05/2021
© Hansa Chippers 2021
12
Starting procedure
Before starting the machine, operators must read the section “Chipping Safety” in this manual and follow all instructions.
Ensure the rotor is disengaged by winding the
engagement handle in the anti-clockwise direction
until the handle comes to a stop (located next to the
control panel).
Additionally, ensure the throttle control is set to idle.
Insert the key into the ignition and turn clockwise to
the “on” position (first click). Wait a few seconds for
the electronic controller to start up, then turn the key
clockwise (second click) to crank the engine until it
starts. Allow the engine to warm up for 1-2 minutes.
Note: If the engine fails to start on the first attempt,
the key must be turned back to the off position before
attempting to start again.
Increase the throttle up to the first notch on the throttle
control gate. Gradually and slowly engage the rotor by
winding the engagement handle in the clockwise
direction until it comes to a stop. This should be done
slowly to allow enough time for the cutting rotor to pick
up speed without stalling the engine.
Increase throttle to maximum for chipping (move the
throttle lever to the highest position).
Note: Engine must run at full throttle for the automatic
feed control system to operate correctly.
1
Throttle
control
(idle)
2
3
First notch
for
engagement
4
Throttle
control
(max)

Hansa C45 O&M Manual –OM-027 First Release 4/05/2021
© Hansa Chippers 2021
13
Shutdown procedure
To shut the machine down, move the throttle control
lever to the idle position (lowest position).
Once the engine has been given time to slow down to
idle speed (about 10-15 seconds), disengage the rotor by
winding the engagement handle in the anti-clockwise
direction until the handle comes to a stop.
WARNING! Only engage and disengage the rotor at
idle speed otherwise excessive vibration and belt friction
may cause damage.
Allow the engine to cool down by running at idle for at
least 1 –2 minutes before shutting down. Turn the
ignition key anti-clockwise into the off position to shut
the chipper down.
WARNING! The heavy rotor will continue to turn for
some time after the engine has been shut down. Do not
open the rotor housing cover until the engine and cutting
disk have completely stopped and the rotor is
disengaged.
1
Throttle
control
(idle)
2
3

Hansa C45 O&M Manual –OM-027 First Release 4/05/2021
© Hansa Chippers 2021
14
Troubleshooting
The chipper won’t start
•The engine oil level might be too low
The chipper is fitted with oil alert and will not start if the oil level is too low
Check the oil level and top up if required
•The chipper is placed on a slope
The chipper is fitted with oil alert and will not start if the oil is not level
Move the chipper to level ground
•The emergency stop is engaged
Ensure both emergency stops are disengaged by twisting the red buttons clockwise before starting the
chipper
Belt drive engagement will not work
•The housing might be blocked
Turn engine off, ensure rotor has completely stopped, remove debris, restart engine, then attempt to
re-engage the belt drive
Drive belts squealing/smoking
•Drive belts are loose/damaged
Turn the engine off, ensure rotor has completely stopped. Follow the belt tensioning procedure
Discharge slows down
•The chipper is clogged up
Turn the engine off, ensure rotor has completely stopped, remove debris, then close and lock the outlet
chute
Outlet chute is blocked
Outlet is pasted with wet/leafy material
Feed hard, dry material in with softer material
Turn the engine off and ensure rotor has completely stopped. Open the outlet chute and clear blockage
The material is ejected in long strips
•The knives and/or anvil might be blunt
Turn the engine off and ensure rotor has completely stopped. Inspect and sharpen or replace knives
and/or anvil as required. Ensure correct clearances between knives and anvil
The chipper starts making unusual noise, the cutting rotor strikes a foreign object, or the chipper starts to vibrate
Turn the engine off, ensure rotor has completely stopped, then inspect for damage
Replace or repair any damaged parts
Check for and tighten any loose parts
Do NOT attempt to repair the chipper unless you are competent to do so
The chipper stalls when material is being fed
Auto-feed control is not working
Check the Autotrip setting is not set to “OFF”
If auto-feed system is not working, contact Hansa
The feed roller is not turning
Engine is not running at full throttle
Increase the engine throttle to max RPM
WARNING! Do NOT open the housing unless the engine and cutting rotor have completely stopped.

Hansa C45 O&M Manual –OM-027 First Release 4/05/2021
© Hansa Chippers 2021
15
Maintenance & service
Warnings
Lifting the swing arm for access
Lifting the swing arm to get access to the feed roller area may be required for:
•Inspecting, replacing, and adjusting the anvil
•Clearing a blockage
To lift the swing arm for access:
•Turn the engine off and wait for rotor to stop spinning.
Do NOT open the rotor cover or attempt to access this area unless the engine is off, and rotor has
stopped turning.
•Open the rotor cover
•Carefully release the feed roller springs
The feed roller springs can store a dangerous amount of energy so extreme care needs to be taken
when releasing them. Ideally, try to release them using a stick or long tool. In any case, keep your
hands away from the swinging path of the handle as it releases the tension.
•Lift the swing arm up and insert the rotor lock pin into the locking hole:
•With the machine off and cutting rotor stopped, the feed roller area can be accessed safely.
Do NOT attempt to access this area unless the engine is off, and rotor has stopped turning.
WARNING! Do NOT perform any service & maintenance activities with the engine running unless it is safe to do so. Do
not perform any service & maintenance activities while the cutting rotor is still spinning.
Carefully release both feed roller springs
Rotor lock pin
Swing arm held up

Hansa C45 O&M Manual –OM-027 First Release 4/05/2021
© Hansa Chippers 2021
16
Opening the rotor cover for access to cutting rotor
WARNING! Do NOT open rotor cover
when engine is on and/or rotor is still
spinning.
Ensure rotor has stopped spinning. Remove
the two bolts from rotor cover and
disconnect the rubber bonnet latch.
Ensure outlet chute rotation is locked. Pull on
outlet chute to swing rotor cover open.
Reverse process to close. Do not operate the
machine without the rotor cover bolts
installed.
Knife re-sharpening and knife replacement
How do I know that the knives need re-sharpening?
Chipper is vibrating excessively when processing material
Chipper is making more noise than usual when processing material
Rotor RPM is dropping more quickly than usual
Material comes out in long strips
Blunt knives will cause excessive vibration
Blunt knives result in damage to the chipper
How to re-sharpen the knives:
If you don’t have a surface grinder or are unsure how to re-sharpen the knives, contact a professional saw doctor or Hansa to
arrange re-sharpening.
Tools and materials required for re-sharpening (approx. 40 mins):
•24 mm ring spanner
•19 mm ring spanner
•16 mm ring spanner
•14 mm Allen key
•Torque wrench with a 24 mm socket and 16mm crows-foot wrench
•A stick magnet (optional)
•Surface grinder
•Coolant
WARNING! Do NOT operate your chipper with blunt knives.
WARNING! Be careful when working around the sharp knives.
1
2
Pull outlet chute here to
swing rotor cover open

Hansa C45 O&M Manual –OM-027 First Release 4/05/2021
© Hansa Chippers 2021
17
Remove the knives for sharpening:
Open the rotor cover (refer to “Opening the rotor
cover for access to cutting rotor” in the
“Maintenance & service” section in this manual).
Rotate the cutting rotor to gain access to the
knives, then insert the rotor locking pin (normally
located under the rotor cover pivot pin) into the
housing and through the cut-out in the rotor to
lock it in place.
Using a spanner and Allen key, remove the three
knife mounting bolts from each knife
To preserve the Allen key cut-out in the
bolt heads, loosen them by turning the nut
and holding the bolt head stationary.
Be careful not to drop the bolts or knives
into the chipper.
A stick magnet can be used to retrieve
them if this does occur.
Measure the width of the knife and check that it
will be at least 96 mm after sharpening.
If the knives will be shorter than 96 mm, then the
knives should be replaced. Please contact your
nearest Hansa dealer.
Sharpen the knives:
Sharpen the knives on a surface grinder. A cutting
angle of 36 ° is critical for the performance of the
chipper. Make sure there is plenty of coolant used
when grinding to avoid softening of the steel knives.
Note: You do not need to sharpen your knives unless
both sides of the reversible knives have been used.
1
Rotor
locking pin
2
3
MIN 96 mm
4
36 °

Hansa C45 O&M Manual –OM-027 First Release 4/05/2021
© Hansa Chippers 2021
18
Reinstall the knives:
Clean all mounting surfaces and remount the knives
in the reverse procedure. Torque the knife clamping
nuts up to 190 Nm. Note: Torque the nuts while
holding the bolt head stationary, to ensure correct
torque.
After sharpening, the width of the knives will have
been reduced, therefore the gap between the knives
and anvil may require adjustment. There should be
3 mm of clearance between the knife and the anvil.
If there is not enough clearance, the knife edge may
touch the anvil through deflection when cutting
heavy branches and damage the sharp edge. Too
much clearance will allow small twigs and fibrous
materials to be dragged through without being cut.
To adjust the gap between the knives and the anvil,
first loosen the locking nuts from the adjustment
bolts on the anvil mounting plate using a 16 mm
spanner. Now tighten or loosen the two adjustment
bolts. Tightening these bolts will cause the anvil
mounting plate to slide further along the slotted
holes. Ensure you tighten the two bolts evenly to
avoid setting the anvil on an angle.
Once the correct anvil position has been set, ensure
the locking nuts on the adjustment bolts are
tightened. Additionally, ensure the clamping nuts
are torqued to 44 Nm.
Remove the rotor pin and turn the rotor slowly by
hand to check that it turns freely.
Close and secure the rotor cover.
WARNING! Every time the knife clamping bolts are torqued up to 190 Nm and loosened off again, the life of the bolts is
reduced. The knife clamping bolts must be replaced at most after every six sharpens. Contact Hansa for replacement
bolts (M16x50 countersunk bolts of grade 12.9 and Zinc finish). Use only genuine Hansa bolts.
5
6
Countersink
clamping bolts
Adjustment bolts
7
Locking nuts
Rotor disk
Clamping bolts
Knife
Anvil
Rotor
disc
Knife
3 mm
clearance
Bearing
Top view: Knife and anvil set-up
Spring washers
Table of contents
Other Hansa Chipper manuals
Popular Chipper manuals by other brands
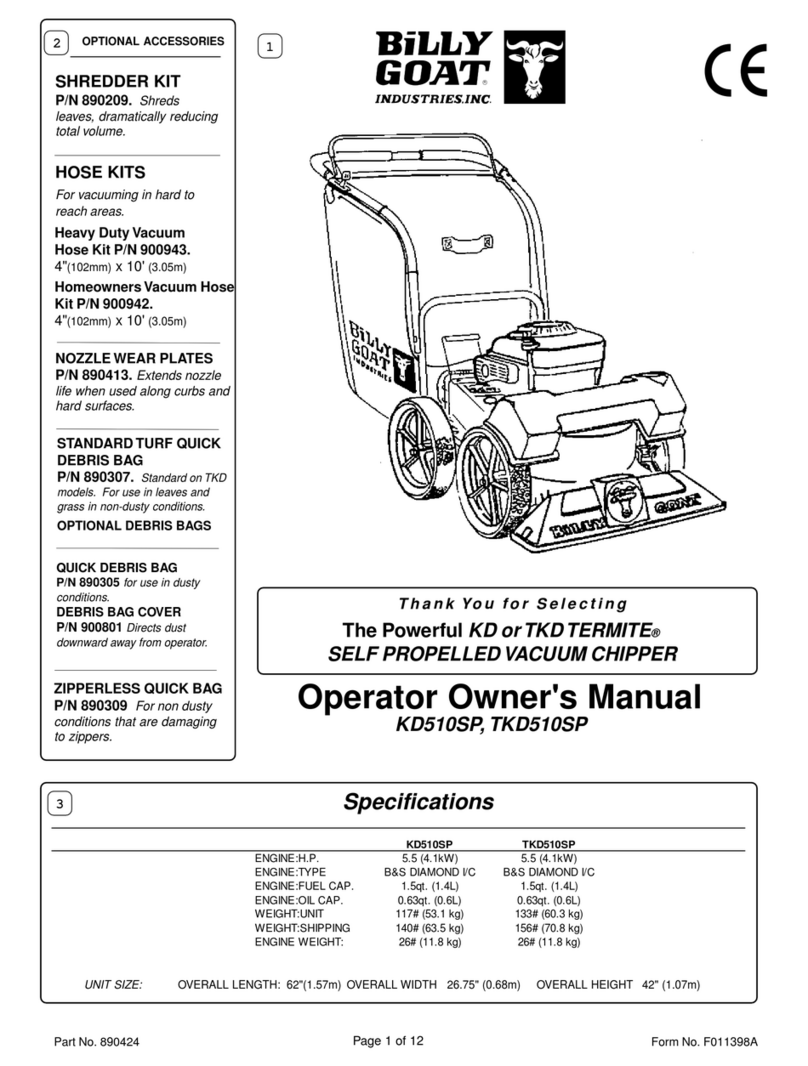
Billy Goat
Billy Goat TERMITE KD510SP Operator owner's manual
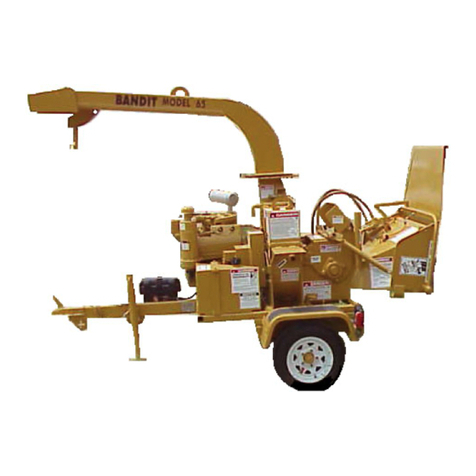
Band-it
Band-it BRUSH BANDIT 65 Operating & parts manual

Sears
Sears Craftsman 247-795890 owner's manual

GardenBeaut
GardenBeaut GB-S3.1 user manual

DR
DR VERSA TRAILER Safety & Operating Instructions
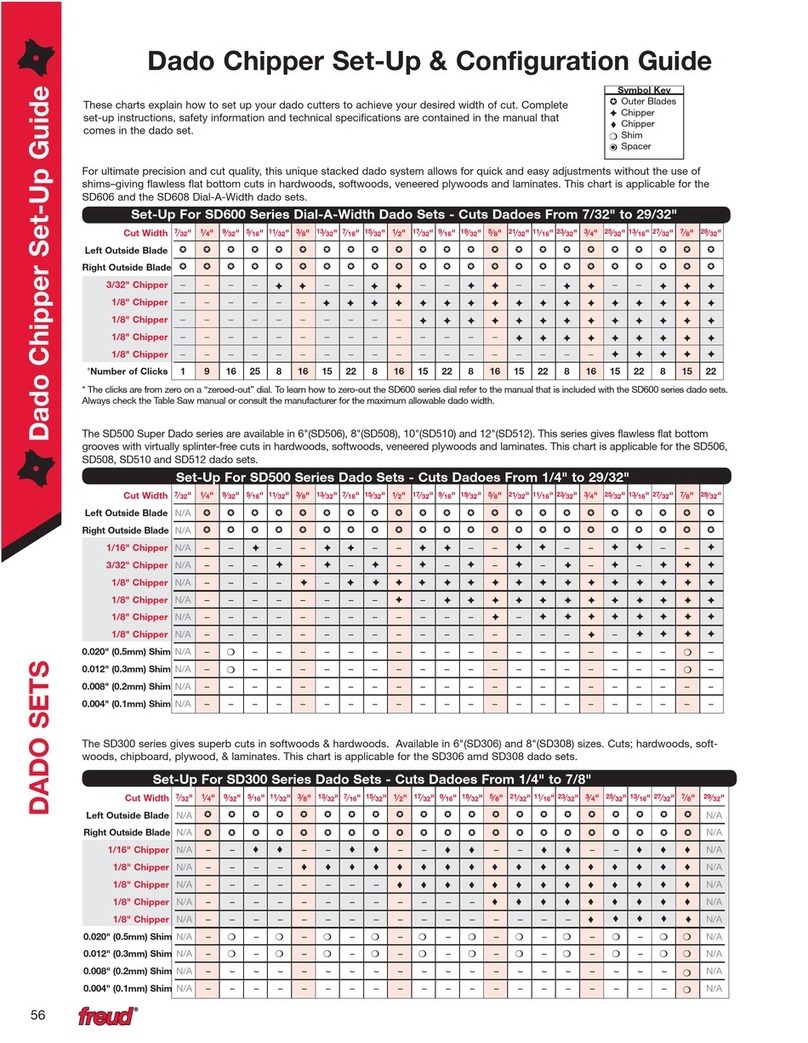
Freud
Freud SD200 Series Setup and configuration guide