Hansa C60RX User guide

HANSA NEW ZEALAND
+64 7 849 4749 info@hansaproducts.co.nz
www.hansachippers.com
HANSA AUSTRALIA
1800 426 722 info@hansaproducts.com.au
www.hansaproducts.com.au
Operation, maintenance and safety manual
All operators must fully read and understand
this operator’s manual before using the chipper.
Keep this manual for future reference.

Hansa C60 RX O&M Manual –OM-015 Revision E 23/10/2019
© Hansa Chippers 2019
TABLE OF CONTENTS
WHAT CAN MY HANSA CHIPPER PROCESS?..................................................................................................................................1
INTENDED USES OF THE CHIPPER ...............................................................................................................................................................1
RECEIVING YOUR HANSA BRUSH CHIPPER....................................................................................................................................1
CHIPPER COMPONENTS........................................................................................................................................................................... 1
SAFETY .........................................................................................................................................................................................2
OPERATOR COMPETENCY.........................................................................................................................................................................2
IDENTIFYING HAZARDS AND RISKS ..............................................................................................................................................................2
TOWING SAFETY ....................................................................................................................................................................................3
TRACK OPERATION SAFETY .......................................................................................................................................................................3
WINCH OPERATION SAFETY......................................................................................................................................................................4
CHIPPING SAFETY................................................................................................................................................................................... 5
CHECKLIST BEFORE OPERATION .............................................................................................................................................................5
SAFE SETUP PROCEDURE......................................................................................................................................................................5
SAFE OPERATING PROCEDURE...............................................................................................................................................................6
OPERATION..................................................................................................................................................................................7
OUTLET CHUTE ADJUSTMENT....................................................................................................................................................................8
FEED ROLLER CONTROL ...........................................................................................................................................................................8
AUTOMATIC FEED CONTROLLER (AFC) ......................................................................................................................................................8
ENGINE LED PANEL................................................................................................................................................................................9
HOUR METER /TACHOMETER...................................................................................................................................................................9
HYDRAULIC WINCH................................................................................................................................................................................9
EMERGENCY STOP................................................................................................................................................................................10
STARTING PROCEDURE ..........................................................................................................................................................................10
SHUTDOWN PROCEDURE .......................................................................................................................................................................11
RUBBER TRACK DRIVE ...........................................................................................................................................................................12
TRACK CONTROL REMOTE PAIRING/UNPAIRING PROCEDURE .........................................................................................................................12
TROUBLESHOOTING................................................................................................................................................................... 13
MAINTENANCE & SERVICE ......................................................................................................................................................... 14
KNIFE RE-SHARPENING AND KNIFE REPLACEMENT .......................................................................................................................................14
ANVIL ADJUSTMENT ............................................................................................................................................................................. 17
BELT TENSION .....................................................................................................................................................................................17
BELT TENSION ADJUSTMENT............................................................................................................................................................... 18
BELT REPLACEMENT.............................................................................................................................................................................. 18
HYDRAULIC PUMP BELT ADJUSTMENT....................................................................................................................................................... 18
GREASING BEARINGS &PIVOT POINTS......................................................................................................................................................19
HYDRAULIC SYSTEM.............................................................................................................................................................................. 20
ENGINE SERVICING ...............................................................................................................................................................................20
C60RX TRACK MAINTENANCE AND RUBBER TRACK TENSION......................................................................................................................... 20
OTHER SERVICING ................................................................................................................................................................................20
ROTOR BEARING REPLACEMENT ..............................................................................................................................................................20
MAINTENANCE &SERVICE INTERVALS ...................................................................................................................................................... 22
BOLT TORQUE .....................................................................................................................................................................................23
SPECIFICATIONS ......................................................................................................................................................................... 23
DECALS....................................................................................................................................................................................... 24
HANSA GLOBAL INDUSTRIAL LIMITED WARRANTY..................................................................................................................... 28
COMMISSIONING CHECKLIST AND REGISTRATION ..................................................................................................................... 30

Hansa C60 RX O&M Manual –OM-015 Revision E 23/10/2019
© Hansa Chippers 2019
1
What can my Hansa chipper process?
Intended uses of the chipper
The C60RX Hansa chipper is built to process organic material including wooden branches not exceeding 254 mm in diameter. It is
designed to be used on by commercial arborists, tree contractors and hire / rental companies. Do NOT use the chipper for any
other purpose.
Organic wastes include:
Prunings, stalks, roots, vegetable matter, hay, grass, bark
Branches
Palm fronds
Dead and hard timbers (Note: these will dull the knives faster)
Paper or cardboard
Do NOT process:
Flax, root balls
Soil, bones, sand, grit, stones, metal
If you have any questions, contact your authorised dealer.
Do NOT exceed 254 mm branch diameter
Receiving your Hansa Brush Chipper
Congratulations on the purchase of a Hansa Model C60RX Brush Chipper.
Chipper components

Hansa C60 RX O&M Manual –OM-015 Revision E 23/10/2019
© Hansa Chippers 2019
2
Safety
Preventing accidents is the responsibility of every equipment operator. The operator is responsible for any accidents or hazards
occurring to people or their property. Ensure every operator is familiar with the safe operation procedures and controls of the
machine, how to identify hazards, and the steps required to avoid injury while handling and operating the chipper. Relevant
information is contained in this manual.
Do NOT modify the design of the chipper.
Operator competency
Ensure that every person operating the chipper understands and follows the safe operating and maintenance procedures
as detailed in this manual.
Do NOT allow persons below the age of 18 to operate the chipper. Additionally, local regulations may restrict the age of
the operator.
Do NOT allow persons with reduced physical, sensory or mental capabilities, or lack of experience and knowledge to
operate the machine.
Identifying hazards and risks
Identify hazards and risks, and take preventative steps to avoid accidents and minimise risk. Possible hazards include, but are not
limited to, moving parts, thrown objects, weight of chipper and components, and the operating environment.
Below is a list of hazards and actions required to prevent injury.
Hazard
Risk
Corrective action
Dust
Injury or irritation of the
eyes
Respiratory irritation
Wear safety glasses
Process freshly cut materials and / or wear a dust mask
Exhaust Fumes
Respiratory irritation
Place the chipper in a manner that the operator or onlookers
are not exposed to direct exhaust fumes
Hot Exhaust
Heat burns
Keep bare hands and other body parts a safe distance away
from hot exhaust
Fire
Heat burns
Clear any build-up of chipping debris around the engine and
exhaust regularly
Belt Drive
Skin pinching and/or
abrasions
Ensure that the belt guard is in place, and keep away from
the belt
Cutting rotor and knives
Pinching, crushing, cutting,
severing
Keep hands and other body parts out of the inlet chute
Use a stick to push materials into the inlet chute
feed roller
Do NOT push material into the feed roller with your
hands
Feed swing arm
Crushing, severing
Do not touch or approach the feed roller motor and swing
arm while the machine is operating
Feed roller and feeding
material
Being pulled into chipper
resulting in possible
crushing, cutting, severing
Do not stand directly in front of the inlet table while feeding
material into the chipper; stand to either side.
Do not climb onto the inlet table or enter the infeed chute
unless the machine is off, and the cutting rotor is stationary
Sound
Damage to hearing
Always wear hearing protection when operating the
machinery
Discharge material
Eye injury, minor cuts
Always wear safety glasses when operating the machinery
Do NOT stand in front of the outlet chute

Hansa C60 RX O&M Manual –OM-015 Revision E 23/10/2019
© Hansa Chippers 2019
3
Do NOT face the machinery in a place where the
outlet chute is directed on a hard surface
Feeding material
Cuts and scrapes
Wear tight fitting safety gloves
Wear tight fitting long sleeves and pants to cover bare skin
when operating the machinery
Weight of the chipper
Straining, crushing
Place the machinery on level ground
Pinch points
Pinching, crushing
When opening/closing the inlet table, bonnet, or other
guard, it is recommended to use the handles provided
Petrol, oil, grease
Poisoning, skin irritation,
harmful vapours
Take care when handling petrol, oil and grease
Wash skin if contaminated with petrol, oil or grease
Do NOT refuel the chipper in enclosed areas
Tracks
Crushing
Ensure area is clear of bystanders while moving the machine
Ensure the operator is controlling the machine from a point
where he/she has complete and unobscured vision of the
machine and its surroundings in the direction of travel
Towing safety
Rotate the discharge chute to face the opposite direction of the towing vehicle before towing and lock into position
Lock the feed table in the up position
Connect the tow coupling to the towing vehicle (check the ball dimensions are the same as the coupling).
Connect safety chain with shackle
If the trailer is fitted with brakes, check handbrake is off and road brakes are on by removing the reversing lever
Check rear brake and indicator lights are operational
Check wheel nuts and axle U-bolts periodically to make sure they are secure
Ensure the jockey wheel is in the up position and locked away during transport
Ensure the machine is sufficiently secured to the trailer
Ensure the machine is towed in accordance with local trailer transport regulations
Track operation safety
Pre-driving checks
✓Ensure the rotor is disengaged
✓Ensure the inlet table is locked in the upright position
✓Ensure the outlet chute is locked in the forward-facing position
✓All drivers must read all driving instructions before driving for the first time
✓First time operators should familiarise themselves with the controls in an open, flat, controlled area free of people and
traffic
✓Ensure the engine throttle is set to at least half way before operating the tracks
Driving considerations
Make sure that the work site terrain is stable enough to firmly support your chipper.
Driving in water and mud should be avoided where possible to reduce track wear and corrosion of the chassis and electrical
wiring/components. If it is not possible to avoid, the chipper should only be driven through water if: the bottom of the
travel path is firm and level; the water is calm and flows slowly; and the water level does not rise above the top surface of
the tracks. Be very careful about the type of bottom of the water path since if it is very soft, the machine may slowly sink
down
It is recommended to wash the undercarriage if it has been driven in salt water or if dirt and mud has made its way into
the track rollers and driving sprockets. Excessive dirt, mud, and sand in the tracks causes unnecessary wear
All operators must comply with local laws for operating and driving a tracked vehicle
Hold the remote with both hands and use the neck strap provided
Ensure the speed setting on the track remote is set to “reduced speed” when making precise manoeuvres and when
mounting and dismounting transport trailers.
The tracks have a built-in braking system that is automatically applied when the joysticks are returned to their resting
positions. Be careful not to release the joysticks too quickly as the brakes could destabilise the machine, especially on
steep terrain

Hansa C60 RX O&M Manual –OM-015 Revision E 23/10/2019
© Hansa Chippers 2019
4
Avoid the following situations if possible:
Drive the chipper on hard, stony and uneven surfaces such as streambed rock, gravel, etc
Leave the rubber tracks lying in the direct sun light for more than three months’time
Make sharp steering manoeuvres on asphalt and cement since this causes excess track pad wear.
Working on asphalt surfaces when their temperature exceeds 60°C since this causes both excess pad wear and damage to
the asphalt surface
Drive the chipper on hard or abrasive surfaces, such as concrete, sand or gravel. If driving on a hard surface is necessary,
do not attempt sharp steering manoeuvres and keep time driving over these surfaces to a minimum. Rubber tracks are
designed predominantly for use on soft terrain, not for hard and abrasive surfaces
Drive the tracks over sharp concrete edges etc
Expose the tracks to fuels or synthetic oils. If this does happen then they must immediately be cleaned
Drive the chipper on steep routes. It is recommended that the C60RX should not be driven on slopes steeper than 15
degrees. The engine is not designed to operate at angles greater than 20 degrees for extended periods of time. Operators
should take their time to become comfortable driving on steep terrain and learn what the machine is capable of. Care
should be taken on steep slopes that are soft or uneven as this could cause the machine to slide or tip into a steeper
position
Do NOT:
Drive the chipper within five metres of people, including the operator. It should be the responsibility of the driver to ensure
that onlookers do not come within five metres of the machine while it is being driven
Allow anyone within the immediate downhill area of the machine when it is being driven on steep terrain
There is a danger of destabilising/rolling the machine when driving up/down steep terrain
Winch operation safety
Winch operation safety:
Be careful when retracting the winch. Do NOT retract the winch past the rollers at the end of the winch boom
The winch does not automatically stop once it reaches the rollers. Retracting the winch too far may damage the
hook or rollers
Do NOT attempt to lift/pull objects that weigh more than 1400 kg.
Ensure you are familiar with the capabilities and weight of the machine before winching particularly heavy objects
Ensure the winch rope is fully retracted and attached to the keeper hook before feeding material into the chipper
This is to ensure the feed roller/cutting rotor does not pull in the winch rope. The rotor is rotating at high speed
and if it does pull the winch rope in, it will do so rapidly and has the potential to cause serious injury to operators
and/or result in damage to the machine
Ensure both stabiliser feet are lowered while operating the winch
Ensure the pull angle of the winch is within the safe operating envelope. This is outlined below:
Maximum slope
15 degrees
Safe operating envelope (vertical)
Safe operating envelope (horizontal)

Hansa C60 RX O&M Manual –OM-015 Revision E 23/10/2019
© Hansa Chippers 2019
5
Ensure the rope wraps around the drum at least five times
Do NOT extend the rope past this point
Winches operate on the friction principle; with less than five wraps, the rope will separate from the
drum
If a replacement winch rope is required, the rope must be of equal or greater strength than what is specified (see the
‘Operation – Hydraulic Winch’ section of this manual). Contact Hansa for more information
Chipping safety
Checklist before operation
Engine:
✓Check oil level in engine
✓Check condition of air cleaner
✓Refer to engine manual for more details
Check Hydraulics:
✓Check level of hydraulic fluid
✓Check all hydraulic components for leaks
General:
✓Check drive belt and pump belt for proper tension
✓Check machine for proper lubrication
✓Check nuts and bolts to ensure they are tight
✓Check diesel level
✓Check that the fuel cap is secured and there is no fuel leaking from the tank
✓Check the tracks are tight and in good condition
✓Check direction of the discharge chute
✓Check guards are all in place and in good condition
✓Check all labels are legible. Replace if necessary (contact Hansa for replacements)
✓Refer to maintenance section for more details
Safe setup procedure
Ensure all pre-operation checks have been done
Setup the work site so there is no danger to traffic or public and provide adequate warnings
Ensure the chipper is positioned on firm level ground
Ensure the feed control bar is in the neutral position when starting the chipper
Ensure the inlet table is clear of material when starting the chipper
Ensure the throttle control lever is the initially in the idle position when starting the chipper
Ensure the outlet chute is discharged onto soft ground (e.g. grass)
Do NOT allow the outlet chute to discharge chip onto hard surfaces (such as a paved or gravel surface)
Ejected material can rebound and cause injury
Keep children and spectators clear of the work area at all times
Do NOT operate the chipper where there is a hazard to onlookers
Do NOT allow any person under the age of 18 to operate the chipper
Refuelling:
Take extra care in handling fuels
They are flammable and vapors are explosive
Use only an approved fuel container
Always replace and securely tighten fuel cap after refuelling
Allow engine to cool down before refuelling
Do NOT smoke when using or refuelling the chipper
Never remove fuel cap or add fuel with the engine running
Never refuel the chipper indoors
Never store the chipper or fuel container inside where there is an open flame, such as a water heater
If fuel is spilled, do not attempt to start the engine. Wipe up the spilled fuel and move the chipper away from the
area of spillage before starting

Hansa C60 RX O&M Manual –OM-015 Revision E 23/10/2019
© Hansa Chippers 2019
6
Safe operating procedure
Wear safety equipment: Safety glasses and hearing protection
must be worn at all times
Wear work gloves: The wearing of work gloves is optional but
highly recommended - ensure that the gloves fit tightly
Do NOT wear loose fitting gloves or gloves with long cuffs
Loose gloves may get snagged by branches, which could result in the operator being pulled into the chipper
Tie long hair up
Long hair could be snagged by a branch and may be pulled into chipper
Wear clothes that sit tightly
Avoid scarves and any items that can get caught in the chipper or snagged on branches
Place the chipper on even ground and direct outlet chute onto soft ground
Ensure exhaust is pointing away from the working area and downwind from the operator and onlookers
Keep proper balance and footing at all times and stand at the same level as the chipper
Do NOT climb onto the feed table to push material into the feed roller
Ensure the chipper is positioned so that there is a minimum inlet table height of 600 mm off the ground
Keep your face and body away from the inlet chute. Stand to the side of the inlet table while feeding material into the
chipper
Standing to the side gives better access to the control bar and helps in keeping clear from flying debris
Feed only freshly cut material into the chipper
Do NOT feed in materials covered in gravel, stones and dirt as this can rebound, injure the operator and damage
the machinery
Prune to a size that suits the chipper’s capabilities
Pre-cut side branches
The branch will ‘self-feed’ more efficiently
Keep the engine clean of debris and other accumulations
This prevents damage to the engine or possible fire
Feed limbs and branches through butt end first, leaving the bushy head on
This helps guide the limb down the inlet chute
It reduces spinning and the occurrence of ejection of small pieces back up the inlet chute
Feed soft materials intermittently with branches
The wood chips tend to clean out any soft residue left in the chipper
The chipper can clog up with soft, wet or fibrous materials
Keep well clear of the outlet chute discharge area, even when the chipper is not currently processing material
High velocity, sharp discharge can cause serious injury
Keep the outlet free of blockage
If blockage occurs, turn the engine off and wait for rotor to stop spinning. Open the outlet chute and remove
material until the outlet chute is clear
Keep the feed roller free of blockage
If blockage occurs, turn the engine off and wait for rotor to stop spinning. Remove the feed roller guard by
unhooking the four rubber latches. Unhook the springs from the base of the chassis. Lift the swing arm up and
insert the rotor pin (located underneath the control panel) into the tab on the housing to lock the swing arm in
place (as per the diagram below). You may now safely clear the blockage. Remove the rotor pin, lower the feed
roller, reposition the springs, then replace the guard
Turn off the engine whenever you leave the work area
DO:
Rotor pin
Swing arm

Hansa C60 RX O&M Manual –OM-015 Revision E 23/10/2019
© Hansa Chippers 2019
7
Run the chipper in an enclosed area
Exhaust fumes contain carbon monoxide which is poisonous, colourless, odourless, and tasteless
Operate the chipper wearing loose clothing and untied long hair
Stand at a higher level than the base of the chipper when feeding material into it
Feed flax and cabbage tree leaves into the machine
These stringy materials can wrap around the rotor shaft and work their way into the bearing.
If any stringy material becomes wrapped around the rotor shaft, remove it before it works itself into the bearing
Process old materials such as dried wooden branches
They get very hard and springy when dried out
They are more awkward to handle
The knives dull much quicker
Feed short, stubby pieces of wood into the chipper
They bounce and spin in the inlet chute
Feed short stubby pieces together with longer pieces
Feed branches that are too large (max 254 mm branch diameter)
The chipper engine will stall, which could result in damage to the engine or drive belts
Put soil, sand, grit, stones or pieces of metal into the chipper
This will damage the sharp edge of the cutting knives and can rebound and injure the operator
Put root balls and dead wood into the chipper
This dulls the knives quickly
Overload the chipper
If the cutting rotor is slowing down, feed the material in slower
Transport the chipper while the engine is running
Tamper with the engine governor settings on the chipper
The governor controls the maximum safe operating speed and protects the engine and all moving parts from
damage caused by overspeed
Operate the chipper with blunt knives
This causes excessive vibration which may result in damage to the chipper
Remove any guards on the chipper unless the engine is turned off and the cutting rotor has come to a complete standstill
Enter the inlet chute
Get on, or lean over the feed table
Put hands or any other part of the body or clothing:
Inside the inlet chute
Inside or near the opening of the discharge chute
Near any moving part
Use the feed control bar as a handle to manoeuvre the machine
Operation
The chipper is self-feeding and has a large inlet opening. It can process:
•Prunings, stalks, vines, leaves, roots and vegetable matter, paper and cardboard
•Freshly cut material is better to process than dry material
•Maximum capacity is 254 mm diameter branches
It is recommended to keep a wooden stick handy, approx. 60 mm diameter x 1000 mm long for:
•Pushing in short, brushy and very leafy materials
•Keeping the inlet table clear
DO NOT:

Hansa C60 RX O&M Manual –OM-015 Revision E 23/10/2019
© Hansa Chippers 2019
8
Outlet chute adjustment
The C60 is fitted with a freely rotating outlet chute, allowing the operator to precisely
control the direction of material discharge from the machine. The chute can easily be
adjusted by undoing the clamping bolt, adjusting the outlet chute direction as needed, then
doing the clamping bolt back up. The outlet chute height can also be adjusted by cranking
the swivel handle on the back of the outlet chute.
Additionally, the top of the outlet chute is fitted with two deflector plates that can be
adjusted to control the angle and distance of discharged material. A wingnut is located on
the side of the upper deflector to lock it in place.
Feed roller control
The C60 is equipped with a feed roller which facilitates the process of feeding material
into the machine. The feed roller is controlled via the yellow control bar which surrounds
the inlet table. The control bar has three settings:
1) Reverse
2) Neutral
3) Feed
When the bar is fully pushed in, the feed roller will be set to reverse. When the bar is fully
pulled out, the feed roller will feed material. The neutral position lies between the reverse
and feed positions.
Automatic Feed Controller (AFC)
The feed roller is fitted with an electronic automatic feed control system which is designed to limit the feed rate of material into
the machine in order to prevent the engine from stalling.
This system eliminates the need to control the speed at which the branches are fed into the chipper manually. A sensor detects the
RPM of the rotor; once this speed drops to a pre-set level the feed roller stops and the branch stops feeding into the machine. The
engine then picks up in RPM and once it reaches a pre-set speed the feed-roller will start feeding again. The feed wheel will also
reverse back slightly after stopping (reducing the friction between the wood and knives), resulting in a quicker engine recovery.
The feed roller will only work once the engine is turned on and the engine has reached full throttle after engaging the rotor. If the
green LED light on the AFC controller is flashing this indicates the feed roller isn’t turning. When this changes to a solid green light
(when the engine reaches maximum throttle of 1620RPM) the feed roller will be operational.
The AFC has 19 different pre-set positions at which the feed will stop.
Adjusting the AutoTrip setting:
1. Turn the ignition key into the ‘ON’ position. Alternatively, this can be adjusted when the machine is in operation.
2. The version number will initially be displayed on the LCD display, wait until this clears.
3. Push the ‘Menu’ button once.
4. Adjust the AutoTrip setting down using the ‘Menu’ button or up using the ‘Set’ button. There are 19 different positions at
which the feed will stop. At setting 1 the engine is dropping further in RPM, whereas at setting 19 the engine is only
dropping marginally in RPM before the feed roller stops. Adjust to a setting which is most suitable to you. Once adjusted
the screen will return to the Hour meter / Tachometer display after 5 seconds, saving the desired setting.
If there are any problems with the electronic automatic feed system, the chipper can be used with the auto-feed disabled. To
disable auto-feed, adjust the AutoTrip setting down to 0 or up to 20.
WARNING! Be careful using the machine with auto-feed disabled as the machine can be stalled easily.
Feed –Neutral –Reverse

Hansa C60 RX O&M Manual –OM-015 Revision E 23/10/2019
© Hansa Chippers 2019
9
Engine LED panel
The engine LED panel has a self-contained engine safety shutdown system as well as a number of warning indicators.
Hour meter / tachometer
The AFC LCD display will toggle between the current engine RPM and machine hours every 5 seconds. Alternatively, the operator
can toggle between the two by pushing the ‘Set’ button.
Hydraulic Winch
Specifications
Model: Comeup HV-3
Rope type: Rope type: 50m DynIce 75 or equivalent (minimum break load 4.2 ton)
Line pull: 1400 kg max
Line speed –20m/min
Winch operation:
The winch is operated via a control panel near the base of the winch unit. The switch on the right controls whether the winch is
being extended or retracted. The switch on the left toggles between remote control and manual control (via the chipper body).
Note: You may only operate the winch while the feed roller is in the neutral position.
2
1
3
4
5
6
8
9
1 –Low fuel indicator
2 –Engine shutdown system activated
3 –Low oil pressure
4 –High coolant temperature
5 –Low alternator output
6 –Auxiliary shutdown
7 –Glow plug active
8 –Air filter restriction
9 –Auxiliary warning lamp
7
Winch
remote
Retract
winch
Remote
operation
mode
Manual
operation
mode
Extend
winch

Hansa C60 RX O&M Manual –OM-015 Revision E 23/10/2019
© Hansa Chippers 2019
10
To disengage the winch, pull the T-handle up and twist to a horizontal position. When the winch is disengaged, the rope may be
freely pulled from the drum (free spool).
Emergency stop
The C60RX has two emergency stops on the top of the inlet chute. The emergency stop acts as an immediate kill switch to the
engine. It does not immediately stop the rotor from spinning. The rotor will continue to spin for some time due to its rotational
inertia. The feed roller, however, will stop almost immediately. To engage the emergency stop, push the red button. To disengage
the emergency stop, twist the red button clockwise until it releases outwards.
Use it when foreign matter such as sand, stones or metal enter the inlet chute
Use it in response to an immediate hazard/danger to an operator or onlooker
After the rotor comes to a halt, follow the normal shutdown procedure in addition
to using the emergency stop
Inspect the machine before resetting the emergency stop
Under normal conditions, do NOT use the emergency stop in place of the regular
shutdown procedure
Starting procedure
Before proceeding, ensure the ‘safe setup procedure’ has been followed on page 5 of this manual.
Ensure the rotor is disengaged by winding the
engagement handle in the clock-wise direction until the
handle comes to a stop (located next to the control
panel).
Additionally, ensure the throttle control is set to idle.
On the control panel, insert the key into the ignition and
turn clockwise to the “on” position (first click). The
orange glow plug light will illuminate. When this light
goes out, turn the key fully clockwise and briefly hold
to start the engine. Allow the engine to warm up for 1-
2 minutes.
At this point you can use the track control remote to
move the machine (follow the procedure outlined in the
“rubber track drive” section of this manual).
1
2
Throttle
control
(idle)
Pull up and twist
Winch handle in
engaged position
Winch handle in
disengaged (free
spool) position

Hansa C60 RX O&M Manual –OM-015 Revision E 23/10/2019
© Hansa Chippers 2019
11
Shutdown procedure
Once the machine is in position for chipping, ensure the
track control remote is disconnected (the feed roller will
not operate unless the remote is disconnected).
Increase the throttle to 1/3 (up to the first notch on the
throttle control gate). Gradually and slowly engage the
rotor by winding the engagement handle in the counter
clock-wise direction until it comes to a stop. This should
be done slowly to allow enough time for the cutting
rotor to pick up speed without stalling the engine.
Increase throttle to full for chipping (move the throttle
lever to the left-most position).
Note: Engine must run at full throttle for the automatic
feed and feed roller to operate. Refer to the
‘Automatic Feed Controller’ section on page 8 to set
the automatic feed control to the desired setting.
To shut the machine down, move the throttle control
lever to the idle position (far-right position).
Once the engine has been given enough time to slow
down to idle speed (about 10-15 seconds), disengage the
rotor by winding the engagement handle in the clock-
wise direction until the handle comes to a stop.
WARNING! Only engage and disengage the rotor at
idle speed otherwise excessive vibration and belt friction
may cause damage.
Allow the engine to cool down by running at idle for at
least 1 –2 minutes before shutting down. Turn the
ignition key anti-clockwise into the off position to shut
the chipper down.
WARNING! The heavy rotor will continue to turn for
some time after the engine has been shut down. Do not
open the rotor housing cover until the engine and cutting
disk have completely stopped and the rotor is
disengaged.
3
4
1
2
3
Throttle
control
(max)
Throttle
control
(idle)
Throttle
control
1/3

Hansa C60 RX O&M Manual –OM-015 Revision E 23/10/2019
© Hansa Chippers 2019
12
Rubber track drive
The C60RX rubber track drive is operated by a fully proportional control remote. The remote has two joysticks, one on the left and
one on the right that control the left and right tracks respectively. With the engine throttle set to half-way, familiarise yourself with
the sensitivity of the tracks by moving the joysticks slowly to begin with. Once you are confident at slower speeds, the engine
throttle can be increased to increase the track speed.
The track control remote has a speed toggle switch with two settings: “full speed” (hare symbol) and “reduced speed” (tortoise
symbol). It is recommended to keep the speed setting at reduced speed until the operator becomes familiar with the controls. The
speed setting should always be set to reduced speed when making precise manoeuvres and when mounting a trailer.
In the case that the remote-control system cannot be operated, such as a flat remote battery, the machine can be switched to
‘manual mode’ by flicking the switch inside the receiver cabinet to “on”. While the machine is in manual mode, the tracks can be
operated via the levers inside the valve cabinet (on the opposite side of the machine to the receiver cabinet).
Track control remote pairing/unpairing procedure
Turn the key of the track control remote anticlockwise to turn the remote off. The remote battery will drain if the
remote is left on.
Start the chipper as per the usual start-up procedure.
Ensure that the cutting rotor is disengaged. The throttle
should be set to at least half-way
4
1
Right track
control
Left track
control
Track mode
control
Emergency
stop

Hansa C60 RX O&M Manual –OM-015 Revision E 23/10/2019
© Hansa Chippers 2019
13
Troubleshooting
The chipper won’t start
•The engine oil level might be too low
The chipper is fitted with oil alert and will not start if the oil level is too low
Check the oil level and top up if required
•The chipper is placed on a slope
The chipper is fitted with oil alert and will not start if the oil is not level
Move the chipper to level ground
Belt drive engagement will not work
•The housing might be blocked
Turn engine off, disconnect the spark plug wire, ensure rotor has completely stopped, remove debris,
restart engine, then attempt to re-engage the belt drive
Drive belts squealing/smoking
•Drive belts are loose/damaged
Turn the engine off, disconnect the spark plug wire, ensure rotor has completely stopped. Follow the
belt tensioning procedure on page 17
Turn the remote on by turning the remote’s key
clockwise to position “1”.
To pair the remote to the receiver, press and hold the
green start button on the remote for a few seconds until
the green LED light on the remote flashes slowly. The
blue status LED light on the receiver (located inside the
electrical cabinet) will flash quickly indicating that it is
paired to the remote.
Drive the C60RX to the desired position using the left and right track controls on the remote.
For safety reasons, the feed roller is disabled while the
tracks are active. To reactivate the feed roller, the
remote must be disconnected from the machine.
To disconnect the remote without causing the safety
system to shut the engine down, the operator can
"acknowledge and allow" the remote to be safely
disconnected by holding down the silver button on the
receiver cabinet while switching off the remote
(by turning the remote key to its “0” position).
2
3
4
Start button
(connects the
remote to the
chipper’s
receiver)
Remote key
(on/off switch for the remote)
Electrical
cabinet
Power LED
(green)
Status LED
(blue)

Hansa C60 RX O&M Manual –OM-015 Revision E 23/10/2019
© Hansa Chippers 2019
14
Discharge slows down
•The chipper is clogged up
Turn the engine off, disconnect the spark plug wire, ensure rotor has completely stopped, remove debris,
then close and lock the outlet chute
Outlet chute is blocked
Outlet is pasted with wet/leafy material
Feed hard, dry material in with softer material
Turn the engine off, disconnect the spark plug wire and ensure rotor has completely stopped. Open up
the outlet chute and clear blockage
The material is ejected in long strips
•The knives and/or anvil might be blunt
Turn the engine off, disconnect the spark plug wire and ensure rotor has completely stopped. Inspect
and sharpen or replace knives and/or anvil as required. Ensure correct clearances between knives and
anvil
The chipper starts making unusual noise, the cutting rotor strikes a foreign object or the chipper starts to vibrate
Turn the engine off, disconnect the spark plug wire, ensure rotor has completely stopped, then inspect
for damage
Replace or repair any damaged parts
Check for and tighten any loose parts
Do NOT attempt to repair the chipper unless you are competent to do so
The chipper stalls when material is being fed
Auto Feed Control is not working
Check that AFC is on
Check the Autotrip setting is not at setting 0 or 20 (manual mode)
If AFC is not working, contact Hansa
The feed roller is not turning
Engine is not running at full throttle
Increase the engine throttle to max RPM
The feed roller is running too fast/slow
Hydraulic pump belt loose/broken
Tension/replace belt
Maintenance & service
Knife re-sharpening and knife replacement
How do I know that the knives need re-sharpening?
Chipper is vibrating excessively when processing material
Chipper is making more noise than usual when processing material
Rotor RPM is dropping more quickly than usual
Material comes out in long strips
Blunt knives will cause excessive vibration
Blunt knives result in damage to the chipper
How to re-sharpen the knives:
If you don’t have a surface grinder or are unsure how to re-sharpen the knives, contact a professional saw doctor or Hansa to
arrange re-sharpening.
WARNING! Do NOT open the housing unless the engine and cutting rotor have completely stopped.
WARNING! Do NOT operate your chipper with blunt knives.
WARNING! Be careful when working around the sharp knives.

Hansa C60 RX O&M Manual –OM-015 Revision E 23/10/2019
© Hansa Chippers 2019
15
Tools and materials required for re-sharpening (approx. 40 mins):
•24 mm ring spanner
•19 mm ring spanner
•16 mm ring spanner
•14 mm Allen key
•Torque wrench with a 24 mm socket and 16mm crows-foot wrench
•A stick magnet (optional)
•Surface grinder
•Coolant
Remove the knives for sharpening:
Open the rotor housing cover by removing the
two housing cover locking bolts with a 19 mm
spanner, then lift the rotor housing cover to
access the cutting rotor. Rotate the cutting rotor
to gain access to the knives, then insert the rotor
pin (normally located under the control panel)
into the housing and through the cut-out in the
rotor to lock it in place.
Using a 24 mm spanner and a 14 mm Allen key,
remove the knives from the rotor. There are three
bolts that you must remove on each knife to do
so.
Be careful not to drop the bolts or knives
into the chipper.
A stick magnet can be used to retrieve
them if this does occur.
Measure the width of the knife and check that it
will be at least 96 mm after sharpening.
If the knives will be shorter than 105 mm, then
the knives should be replaced. Please contact
your nearest Hansa dealer.
Sharpen the knives:
Sharpen the knives on a surface grinder. A cutting
angle of 36 ° is critical for the performance of the
chipper. Make sure there is plenty of coolant used
when grinding to avoid softening of the steel knives.
Note: You do not need to sharpen your knives unless
both sides of the reversible knives have been used.
1
Rotor
locking pin
2
3
MIN 96 mm
4
36 °

Hansa C60 RX O&M Manual –OM-015 Revision E 23/10/2019
© Hansa Chippers 2019
16
Reinstall the knives:
Clean all mounting surfaces and remount the
knives in the reverse procedure. Torque the knife
clamping nuts up to 190 Nm.
After sharpening, the width of the knives will have
been reduced, therefore the gap between the knives
and anvil may require adjustment. There should be
3 mm of clearance between the knife and the anvil.
If there is not enough clearance, the knife edge may
touch the anvil through deflection when cutting
heavy branches and damage the sharp edge. Too
much clearance will allow small twigs and fibrous
materials to be dragged through without being cut.
To adjust the gap between the knives and the anvil,
first loosen the locking nuts from the adjustment
bolts on the anvil mounting plate using a 16 mm
spanner. Now tighten or loosen the two adjustment
bolts. Tightening these bolts will cause the anvil
mounting plate to slide further along the slotted
holes. Ensure you tighten the two bolts evenly to
avoid setting the anvil on an angle.
Once the correct anvil position has been set, ensure
the locking nuts on the adjustment bolts are
tightened. Additionally, ensure the clamping nuts
are torqued to 44 Nm.
Remove the rotor pin and turn the rotor slowly by
hand to check that it turns freely.
Close and secure the outlet chute.
WARNING! Every time the knife clamping bolts are torqued up to 190 Nm and loosened off again, the life of the bolts is
reduced. The knife clamping bolts must be replaced at most after every six sharpens. Contact Hansa for replacement
bolts (m16x50 countersunk bolts of grade 12.9 or higher). Use only genuine Hansa bolts.
5
6
7
Countersink
clamping bolts
Adjustment bolts
Anvil
Rotor
disc
Knife
3 mm
clearance
Bearing
Top view: Knife and anvil set-up
Locking nuts
Rotor disk
Clamping bolts
Knife
Spring washers

Hansa C60 RX O&M Manual –OM-015 Revision E 23/10/2019
© Hansa Chippers 2019
17
Anvil adjustment
Whenever the chipper knives are inspected/sharpened, the condition of the anvil should also be checked. If the edge of the anvil
is significantly rounded and/or uneven, then it should be reversed or replaced. Typically the anvil will maintain its flat edge for
about 500 hours of operation.
Avnil replacement
Remove the feed roller guard by unhooking the
four rubber latches. Unhook the springs from the
base of the chassis. Lift the swing arm up and
insert the rotor pin (located underneath the
control panel) into the tab on the housing to lock
the swing arm in place.
To remove the anvil, you must remove the four
countersink clamping bolts using an 18 mm
socket and extension. If the bolt head turns, hold
it with a 6 mm Allen key.
Note: Do NOT use the Allen key to turn the bolt;
turn only the nut.
Note: Ensure the gap between the knives the
edge of the anvil is 3 mm. If not, then the anvil can
be adjusted via the two adjustment bolts
between the clamping bolts.
If the other side of the anvil hasn’t been used yet: rotate the anvil 180 degrees and place it back on the feed
roller housing wall. If both sides of the anvil are blunt: remove the anvil and replace it with a new one. Contact
Hansa if a replacement anvil is required.
Tighten the clamping bolts back up using an 18 mm socket, ensuring there is a spring washer between the
clamping plate and each nut. Torque the nuts to 44 Nm.
Belt tension
Correct belt tension is crucial for minimising belt wear and maximising machine efficiency. To check the belt tension, fully engage
the belt then open the bonnet. There should be approximately 5 mm deflection in the belt when pressing firmly on the belt (as per
the image below). Alternatively, the tension can also be checked by looking at the tensioning device from underneath the machine;
the notch on the idler arm should line up with ‘15°’ on the tensioner. If required, adjust belt tension.
Note: After using the machine for the first time, or after replacing the belts, it is recommended to check the tension again after the
first 5 hours of operation, as the belt will stretch as it wears into the system.
1
2
3
4
Check for
deflection
here
Countersink
clamping bolts
Rotor Pin
Swing arm

Hansa C60 RX O&M Manual –OM-015 Revision E 23/10/2019
© Hansa Chippers 2019
18
Belt tension adjustment
The belt tension can be adjusted by moving the M16 nyloc adjustment nut (below the machined engagement block) up or down
the engagement thread. You will need to use a 24 mm spanner to do so. The belt tension will increase as the nut is moved down
the thread.
Belt replacement
If the belts in your chipper look similar to any of the following images or are clearly broken, then they need to be replaced.
To remove the belts, open the bonnet and fully disengage the belts. The C60RX requires three SPB1410 belts.
Hydraulic pump belt adjustment
The hydraulic pump is driven by a synchronous belt. The belt does not require any tension, however the belt should not have any
slack either. The belt can be adjusted by loosening the four mounting bolts (using a 13 mm spanner) and moving the pump/pulley
up or down the slotted holes (as per the image below). The bolts are best accessed from beneath the machine. If a replacement
synchronous belt is required, contact Hansa.
Cracked underside of belt
Sidewall belt wear
Soft, swollen belt
Worn cover on back of belt
Split belt cover
Adjustment
nut
Table of contents
Other Hansa Chipper manuals
Popular Chipper manuals by other brands
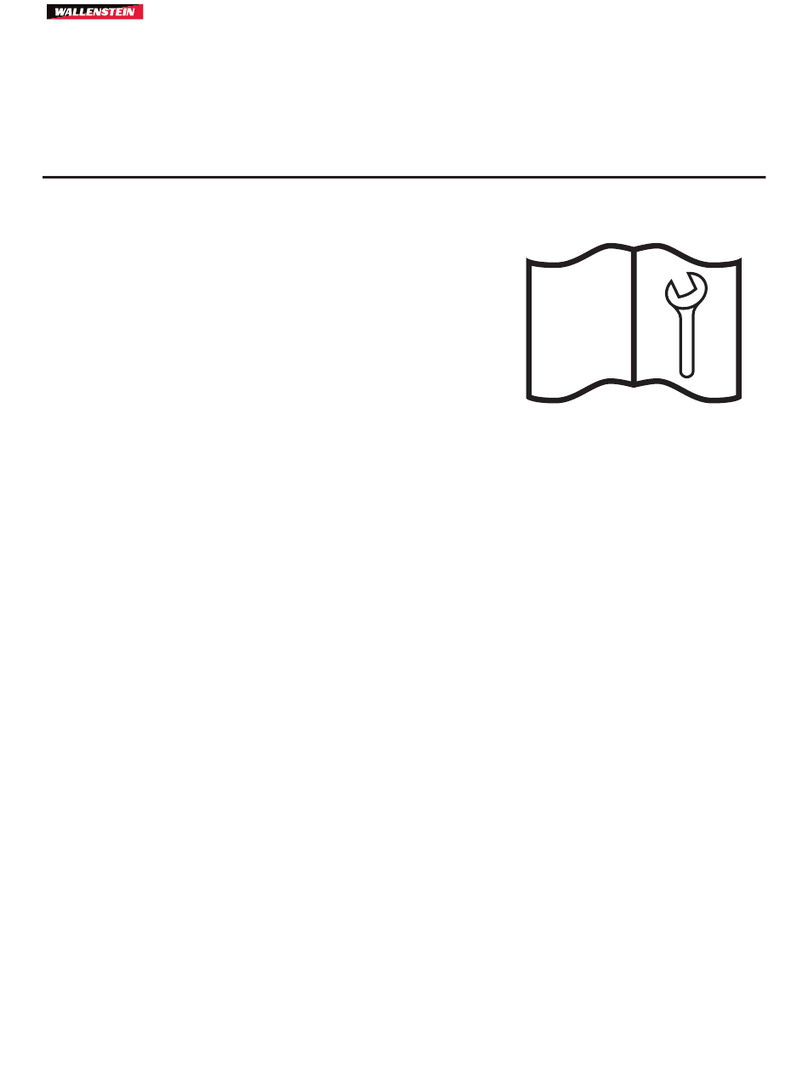
Wallenstein
Wallenstein BXT52S Setup instructions
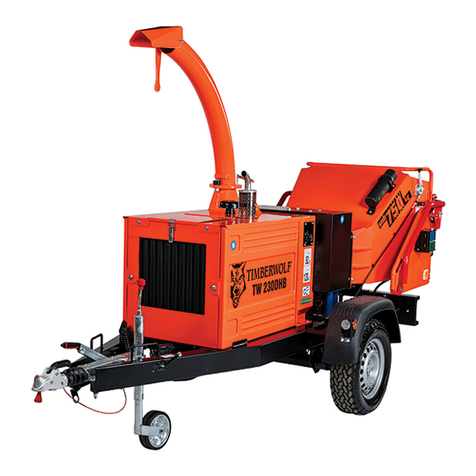
Timberwolf
Timberwolf TW 230DHB instruction manual
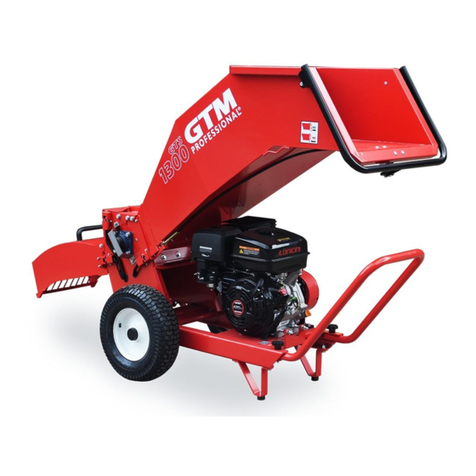
GTM Professional
GTM Professional GTS1300C user manual

Viking
Viking GE 150 instruction manual

Vermeer
Vermeer BC160XL Operating and safety instructions
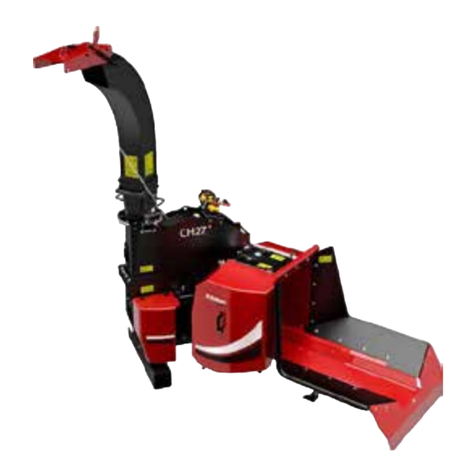
Farmi Forest
Farmi Forest CH27 ACR OPERATION, MAINTENANCE AND SPARE PARTS MANUAL