Hastings 6600 Operating instructions

HASTINGS
Load Pick Up Tool Manual
Model 6600 Model 6605
Operating and
Maintenance Manual
Manual part number P31086
Revision
7

1
HASTINGS L OAD PICKUP TOOL
Operating and Maintenance
Manual
Hastings Fiber Glass Products, Inc.
1301 W. Green St., P.O. Box 218
Hastings, MI 49058
Phone 269-945-9541 • Fax 269-945-4623
Email –hastings@hfgp.com

3
Specifications
The following specifications apply to the Hastings Model 6600 and Model
6605:
Voltage Rating 27kV Nominal, 29.2 kV Maximum*
Current Rating 300 Amps*
Minimum Conductor Size #6 AWG
Maximum Conductor Size 1 ¼”diameter
*While the maximum rating for the Model 6600 and Model 6605
is stated above, the actual rating will be based on the lowest rating
of any component used with the Load Pickup tool. If you use
15kV jumper cable, the entire assembly will be rated at 15kV. If
you use less than a 2/0 cable, the current rating will be reduced
accordingly.

4
Chapter 1
Basic Operations
Catalog Number 6600 and 6605
WARNING This unit is designed for
use on high voltage systems. It must be properly
assembled and maintained to provide adequate worker
safety. Only trained individuals, willing to take the
responsibility for the quality of this tool should assemble
or use this tool! Any misuse or improper maintenance of
this tool could result in serious injury or death!
This manual covers the assembly and operation of both the Model 6600 and Model 6605 load
pickup tool. The Model 6600 has the ability to accept a jumper cable ferrule, while the Model
6605 has a stud to accept a jumper clamp. The upper portions of these two tools are identical.
Cable Installation (for Model 6600 only)
To install a jumper cable in Model 6600, use the following procedure. First, the unit should be
cocked, or at least have the contact rod withdrawn far enough to clear the lower contact. (For
information on cocking the tool, see the paragraph on cockingon page 6.) Remove the two
screws holding the red hand guard in place, using a ¼ inch slotted screwdriver. (See Fig. 1)
After the screws are removed, the two halves of the red hand guard can be pulled away from
the clear housing. Be careful not to damage or trip the operating mechanism by moving the
hand guard a long distance. It only has to move away from the housing far enough for the
locking pins to be free of the lower contact assembly. (See Fig. 2) If the lower contact
assembly doesn’t slide freelyout of the housing, a light shaking should be sufficient to cause it
to slide free of the housing.

5
Fig. 1 Fig. 2
Fig. 3
The jumper cable should have a tin plated copper threaded ferrule termination on the end to be
connected to theload pickup tool. Place the lock washer between the nut and the lower contact
assembly and thread the ferrule into the lower contact assemblyits full length. The flat side of
the ferrule must align with the setscrew in the lower contact assembly. (See Fig. 3) Turn the
ferrule as necessary to align the flat with the setscrew. Tighten the setscrew with a 5/32” hex
wrench. Lock the ferrule in place with the ferrules lock nut and washer, using a 13/16” and a 1
¼” wrench.
Insert the lower contact assembly with cable into the clear tube using the jumper cable to push
the contact back in place. The groove in the lower contact assembly must align with the pin
holes under the hand guards. Once aligned, install the hand guards back in place locking the
lower contact assemblyin place with the pins. Visually check to make sure the pins in the hand
guard are in the groove of the contact assembly. It is possible to incorrectly assemble the tool
with the pins in the area of the wrench flats. This incorrect assemblywill prevent the tool from
working properly. Insert the screws in the hand guard and tighten.

6
Prior to use
Inspect the tool for anydamage and for anyloose or missingparts. There should be no cracks
in the clear tube or any other part of the tool. There should be no visible metal flash or
contamination on the inside or outside of the tool. The cable attached to the tool and the
clamp on the opposite end should be secure and in good working order. The tool should be
capable of being cocked and tripped without undue force or roughness of operation.
Cocking
The safety latch should be in the upper, or locked position prior to cocking. (See Fig. 6) This
can be accomplished by pushing the safety upwards, or bypulling on the lanyard. To cock the
load pickup tool, it must be removed from the conductor. Remove the cocking tool from its
holder. (See Fig. 4)
Fig. 4 Fig. 5
Push the cocking tool all the wayinto the load pickup tool until it makes contact with the
internal assembly. While turningthe cocking tool clockwise continue to keep light pressure
on the cocking tool. (See Fig. 5) This will engage the cocking tool with the internal assembly.
If you see the contact rod rotating in the housing, you have already engaged the assembly.
Continuing to turn slightly while pulling will aid in breaking the contacts internally. Continue
to pull the cocking tool until the contact has latched in the fully open position and the tool can
be pulled no further. Release the pulling pressure on the cocking tool and rotate it slightly
counter clockwise to release it from the internal assembly. Remove the cocking tool
completely and replace it back in its storage positionin the aluminum clamp casting. Damage
to the internal assemblywill occur if the cocking tool is not removed prior to tripping. The
load pickup tool is now cocked. The contacts can be seen to be visuallyopen, through the
clear tube.
Installation
Wheninstallingtheload pickuptool,itisrecommendedtoattachtheoppositeendofthe jumper
to the de-energized line first. Unless the de-energized line is grounded, the jumper must now
be considered and handled as energized. The load pickup tool should then be attached to the
energized conductor using either rubber gloves or a shotgun stick. The energized conductor
must be secure enough to support both the weight of the load pickup tool as well as withstand

7
the pull that will be applied to the lanyard during the operation of the tool. Both ends must be
securely attached and the de-energized line must have all grounds removed prior to operating
the load pickup tool.
Tripping
Once all of your company’s operating procedures for energizing a line have been completed,
the tool can be operated. Using an insulated stick or rubber gloves, the safety latch must be
pulled to its lower position, which will place the unit in the firing position. (See Fig. 6 & 7)
Locked Position Firing Position
Fig. 6 Fig. 7
Any downward motion of the operating rod from this point onmayoperate the load pickup
tool. It is recommended that either a hot stick be used to pull on the operating lanyard, or that
a rope be attached to the end of the lanyard so that the operator be can positioned away from
the load pickup tool prior to operating it. Once the operator is in a safe position, the lanyard
should be pulled firmly to operate the load pickup tool.
If the lanyard is not pulled far enough to trip the Load Pickup tool, the safety latch may re-
engage, preventingit from tripping with another pullon the lanyard. Should this happen, it will
benecessaryto repeat the step of moving the safetylatch to its lower position before attempting
to operate the Load Pickup tool again.
There should be no attempt to remove the load pickup tool unless the tool has been bypassed
with other equipment or the line has been de-energized. There are no provisions on the load
pickup tool to break the load. Regardless of which clamp is removed first, both clamps and
cable will still be energized and must be handled according to standard operating procedures.
Chapter 2
Care & Maintenance
ItmaybecomenecessarytodisassembletheLoadPickuptooltocompleteathoroughinspection
of the tool or to make necessaryrepairs.

8
Inspect the contact rod to make sure there is no pitting in the contact area.
Inspect the clear tube to make sure there is no contamination on the inside or outside.
Inspect the contacts to make sure there is no pitting on the contact itself, or on the housing that
would interfere with the contact rod.
Inspect the safety mechanism (including the spring plungers) for smooth, positive operation.
Inspect the unit for smooth operation of the lanyard and correct operation of the safety
mechanism.
Inspect the internal contact rod for smooth operation.
Inspect the lanyard for any cuts or nicks.
Inspect the eye-screw of the clamp for smooth operation.
Donotuseacetoneorchlorinatedsolventsfor cleaningplasticparts. IsopropylAlcohol,VM&P
naphtha, turpentine, or soap and water can be used.
The tool should always be stored in the “tripped” condition to remove long term stress from the
spring.
Chapter 3
Testing
Testing the Load Pickup Tool
To insure that your Hastings Load Pickup tool is in proper working order, theunit can betested
using the Hastings Ground/Jumper Assembly Tester, Catalog number 6714.
Attach the jumper assembly to the Load Pickup tool by securing a jumper clamp to the stud
(model 6605) or a cable to the threaded cable ferrule termination (model 6600). The jumper
clamp on theopposite end of the cable and the Load Pickup tool can now be securely tightened
onto opposite ends of the copper test bar of the tester.
Forproperinstructionsofthetester,refertoinstructionsP15094thatareincludedwiththetester.
When measuringthecablelength,measuretothebottom ofthe redhandguard. Select theinput
voltage from the correct cable chart supplied with the tester. The voltage input is determined
by the cable size and length. To include the Load Pickup tool, an additional voltage must be
added to the input voltage. An additional voltage of 3.5 is added for model 6600, and 5.0 volts
for model 6605. Note that the Load Pickup tool must be in the fired position to complete the
circuit.

9
Chapter 4
Lower Contact
Disassembly of lower contact
The load pickup tool should not be cocked prior to disassembly. Remove screws from red
hand guard; pull the hand guard halves apart until holding pins exit the clear tube. (See Fig. 1
& 2) On model with the cable attached, pull cable and bottom assembly will come out of the
clear tube. (See Fig. 8)
Fig. 8
On the model with the stud, use the cocking tool to pull the contact rod from the lower contact
assembly. It is not necessaryto completely cock the tool, just pull back on thecocking tool far
enough to allow the contact rod to clear the lower contact assembly. Loosen setscrew in the
lower contact housing with a 5/32” hex wrench and then remove the threaded stud by turning
counter clockwise with a wrench on the nut. Hold the unit upright and shake, the contact
assemblyshould come out of the tube, if not, use a screwdriver to pry with through the hole in
the tube where the threaded stud was removed.
The lower bushing holder that contains the contacts can be removed by using a 1” and a 1 ¼”
wrench. Turn counter clockwise to loosen and remove the lower bushing. For field
replacement of the contact, the contact bushingmust be replaced with one from the factory
with the contact already installed.
On the model with the cable installed, the cable does not have to be removed. If the cable is to
be removed, loosen the setscrew that secures the threads of the ferrule. Use a 13/16” and a 1
¼” wrench to loosen the locknut. Unscrew the ferrule from the bushing holder.
Assembly of lower contact
Install lower bushing into the lower bushing holder and tighten with a 1” and 1 ¼” wrench.
On the model with requiring a ferrule with cable, install the lock washer between the nut and
the lower contact assembly, then thread the ferrule into the bushingholder fully and align the

10
flat on the ferrule with the setscrew in the bushing holder. Tighten the setscrew and tighten
the lock nut on the ferrule.
Ferrule model - slide the bushing assembly into the clear tube until the groove in the bushing
holder aligns with the mountingholes for the hand guard. Visually check to make sure the
pins in the hand guard are in the groove of the contact assembly. It is possible to incorrectly
assemble the tool with the pins in the area of the wrench flats. This incorrect assemblywill
prevent the tool from working properly. Install hand guard and tighten the two screws.
Stud model - slide the bushing assembly into the clear tube until the holes of the bushing align
with the holes for the hand guard and the stud. Install the hand guard and tighten the two
screws. Install the stud until it bottoms out and then tighten the setscrew in the bushing
holder.
Chapter 5
Trigger Mechanism
Disassembly of trigger mechanism
The load pickup tool should not be cocked prior to disassembly. Remove the two screws and
nuts that hold the black plastic cap on, using a 1/8” hex wrench and a 3/8” socket wrench, and
remove the cap. (See Fig. 9) Remove the extension spring from the aluminum casting. (See
Fig. 10)
Fig. 9 Fig. 10
Remove the square bellcrank from the aluminum casting bydriving out the drive pin using a
hammer and a 3/16” diameter punch. (“B” in Fig. 10) Move the operating rod assembly
slightlyoff to the side. The plunger can be removed from the main bodycasting. If the
plunger needs to be removed from the bellcrank, remove the drive pin that secures the plunger
(trigger) to the square bellcrank using a hammer and a 3/32” diameter punch. (“A” in Fig.
10).

11
Assembly of trigger mechanism
Install the 3/32” diameter drive pin through the square bellcrank and the plunger.(“A” in Fig.
10)
Grease the small diameter portion of the plunger with lithium grease and insert it into the main
body casting.
Place the square bellcrank over the two hole lug of the casting and secure it through the top
hole of the lug with a 3/16” drive pin. (“B” in Fig. 10) The square bellcrank should freely
pivot after the pin is installed.
If the operating rod was removed, attach it to the square bellcrank using the 1/8” diameter pin.
Note that the pin goes through the square bellcrank and the slot of the fitting on the end of the
operating rod. The spring plunger on the lower end of the operating rod must be facing away
from the clear tube when it is installed.
Attach the extension spring to the aluminum casting. (See Fig. 10) Reinstall the black plastic
cap with the two screws and nuts. (See Fig. 9)
Chapter 6
Upper Contact
Disassembly of upper contact
The Load Pickup tool should not be cocked during disassemblyof the upper contact to prevent
the spring from creating a hazard to the operator. Make sure the unit is “tripped” or in the
closed position before continuing.
Remove the two screws from the red hand guard using a ¼” slotted screwdriver. Disengage
the hand guards from the clear tube. (See Fig. 1 & 2) Remove the four screws that hold the
clear tube to the aluminum clamp body with a 1/8” hex wrench. Remove the clear tube.
Loosen the set screw in the main body casting with a 3/32” hex wrench. Secure the aluminum
clamp body and turn the upper bushing counter clockwise using a 1” wrench.
When the upper bushing is removed from the aluminum clamp body, the entire contact rod
assemblywill come with it. (See Fig. 11)

12
Fig. 11
The compression springinside of the aluminum clamp bodycan also be removed at this time.
To remove the upper bushing, disengage the larger diameter plastic disc bydrivingout the
drive pin with a hammer and a 3/16” punch. If there are anyraised deformations around the
pinhole, theywill have to be removed prior to sliding the upper bushing off that end. A slight
amount of lithium grease in that area will also aid removal of the bushing.
For field replacement, a new upper bushing must be used with the new contacts already
installed. (See Fig. 12)
Fig. 12
Assembly of upper contact
Lightly grease the contacts inside the upper bushing and both raised contact areas of the
contact rod with lithium grease. (See Fig. 11 & 12) Do not get grease in the chamfer area, on
the back side of the contact assembly. (See Fig. 13)

13
Fig. 13
Slide the bushing onto the rod until it is beyond the area for the large diameter disc. Make
sure that the large internal chamfer is facing the mating chamfer of the small diameter disc.
Slide the large diameter disc over the rod and secure in place with the 3/16” diameter drive
pin. Both ends of the drive pin must be below flush of the O.D. of the disc.
The inside of the main body casting needs to be cleaned with a solvent to remove anymetal
particles or dirt that mayhave accumulated from prior use.
Lightly grease the compression spring O.D. with lithium grease, and install inside the
aluminum clamp body. Place the contact rod assembly, starting with the end with the small
diameter disc, into the aluminum clamp body. Captivate byscrewing the bushing into the
aluminum clamp body and tighten with a 1” wrench. Tighten the set screw with a 3/32” hex
wrench.
Slide the clear tube onto the aluminum clamp body and align the four screw holes. Note that
the tube must be rotated until themounting holes for the red hand guard are in the location to
allow the operating rod run parallel to the clear tube. Install and tighten the four screws
holding the tube to the clamp body. Install hand guard and tighten the two screws.
Chapter 7
Parts List
The following two pages show replacement part numbers that may be used for repairs.

14

15
This manual suits for next models
1
Table of contents
Other Hastings Measuring Instrument manuals
Popular Measuring Instrument manuals by other brands
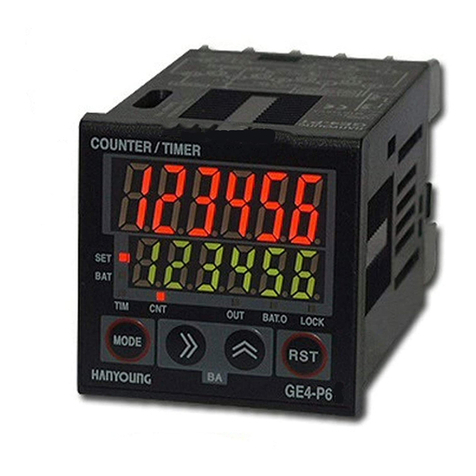
HANYOUNG NUX
HANYOUNG NUX GE Series instruction manual

Dilog
Dilog DL7030 user manual
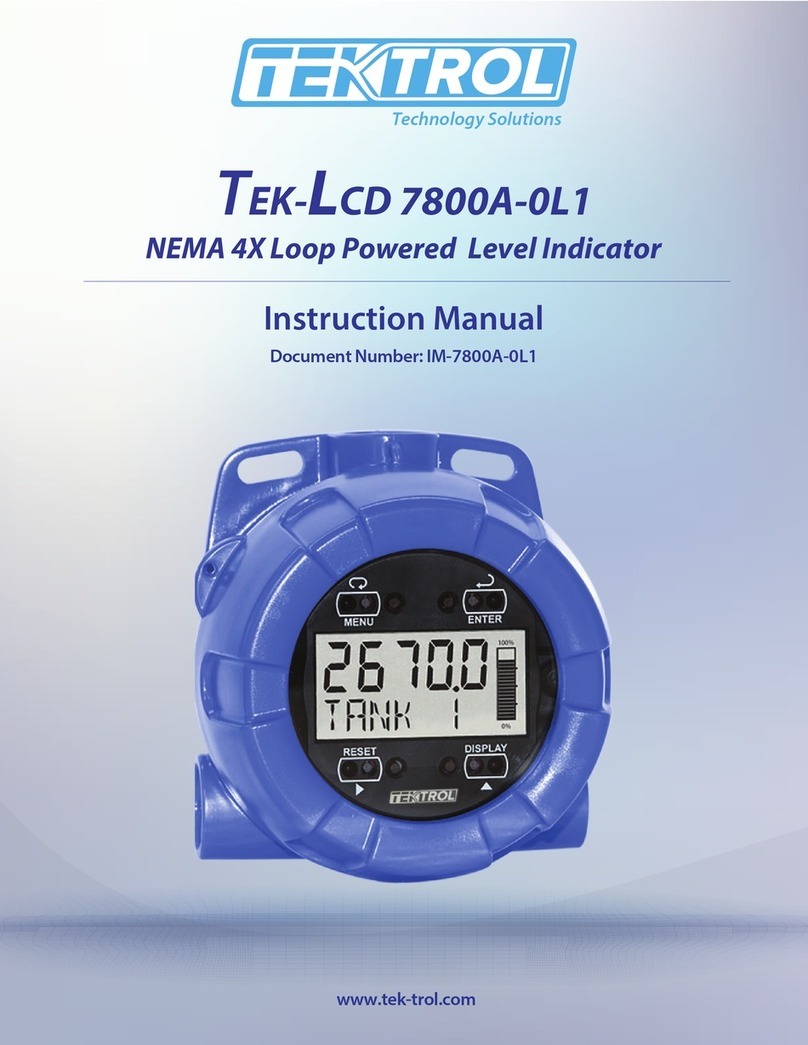
Tek-Trol
Tek-Trol TEK-LCD 7800A-0L1 instruction manual

Aqualytic
Aqualytic AL 110 instruction manual
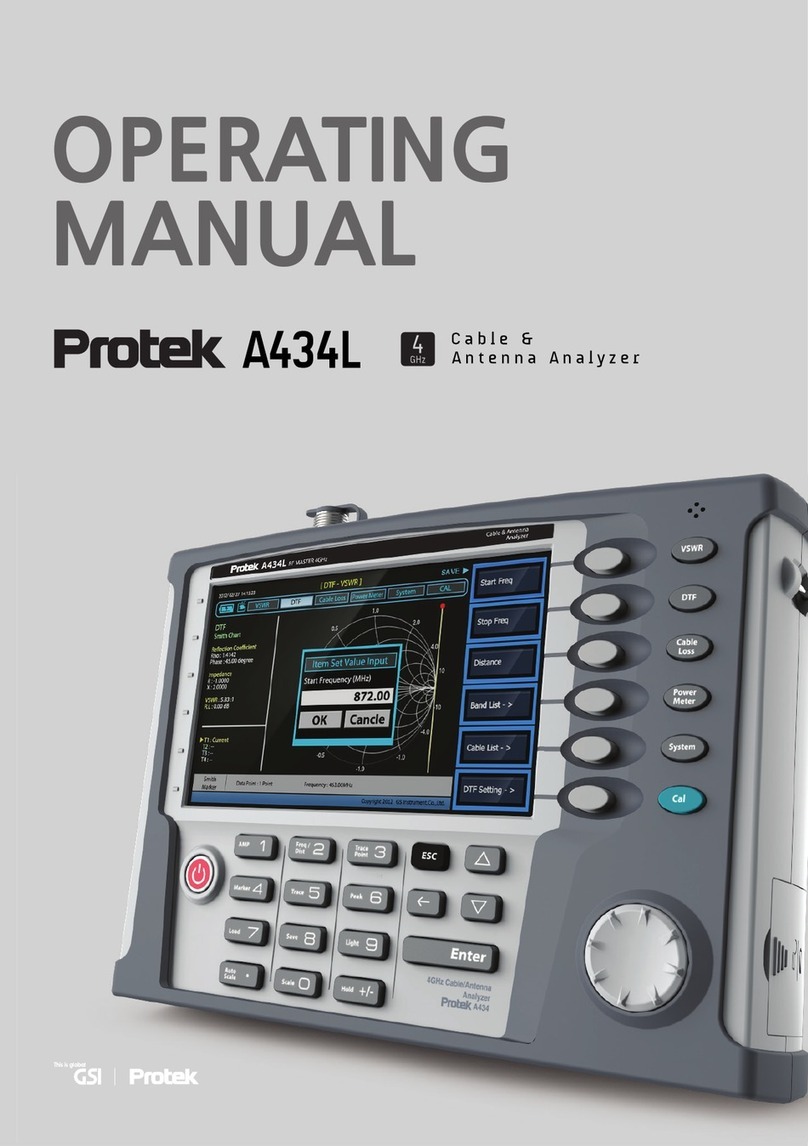
PRO-TEK
PRO-TEK A434L operating manual

Kyoritsu Electrical Instruments Works, Ltd.
Kyoritsu Electrical Instruments Works, Ltd. KEW 8343 instruction manual