Hauber Elektronik HE100 Series User manual

Betriebsanleitung
englisch
Doc ID: M001-HE100 Stand: 2023-01-27
Vibration Monitoring Unit
Series HE100
•Vibration speed (mm/s, rms)
•ATEX / IECEx / UKEx / EACEx Zone 1 / 2 / 21 / 22
•Analogue current output: 4–20 mA
•Frequency range: 10 Hz –1000 Hz
1 Hz –1000 Hz
Date of manufacture:
Type description:
Serial no.:

HAUBER-Elektronik GmbH
Operating instructions
Vibration Monitoring Unit
Type HE100
Standard and ATEX / IECEx / UKEx / EACEx
HE100
Version: 2023-01-27
Attention!
Prior to commissioning the product, the instruction manual must be read and un-
derstood.
All rights reserved, including rights to translation.
Subject to modifications.
Please contact the company with any questions:
HAUBER-Elektronik GmbH
Fabrikstraße 6
D-72622 Nürtingen
Germany
Tel.: +49 (0) 7022 / 21750-0
Fax: +49 (0) 7022 / 21750-50
info@hauber-elektronik.de
www.hauber-elektronik.de

HAUBER-Elektronik GmbH
3
1 Contents
1Contents...................................................................................................................................................3
2Safety information....................................................................................................................................4
3Scope of this instruction manual..............................................................................................................4
4Vibration Monitoring Unit Type HE100 ....................................................................................................5
5Intended Use............................................................................................................................................5
6Scope of supply .......................................................................................................................................5
7Documents and Certificates.....................................................................................................................5
8Transfer of liability when operating in potentially explosive atmospheres...............................................6
9Fields of application and example labels.................................................................................................7
10 Conditions for safe operation in potentially explosive atmospheres........................................................8
10.1 HE100.01 (ignition protection class "pressure-resistant casing").........................................................8
10.2 HE100.02 (ignition protection class "intrinsically safe")........................................................................8
10.3 HE100.03 cULus Hazloc DIV2..............................................................................................................9
11 Technical data........................................................................................................................................11
11.1 General data.......................................................................................................................................11
11.2 Electrical data .....................................................................................................................................11
11.3 Operating range of the vibration monitoring unit ................................................................................12
11.4 Typical frequency response................................................................................................................13
11.5 Mechanical data..................................................................................................................................14
11.6 Housing dimensions............................................................................................................................14
11.7 Properties of the integrated cable.......................................................................................................15
12 Connection.............................................................................................................................................16
13 Assembly and disassembly....................................................................................................................17
13.1 General notes .....................................................................................................................................17
13.2 Fixing the vibration monitoring unit to the mounting surface..............................................................17
14 Installation and commissioning..............................................................................................................18
14.1 General notes .....................................................................................................................................18
14.2 Wiring diagram....................................................................................................................................18
15 Maintenance and repair.........................................................................................................................21
15.1 General notes .....................................................................................................................................21
15.2 Troubleshooting Table........................................................................................................................21
16 Transport, storage and disposal ............................................................................................................22
17 Accessories............................................................................................................................................22
18 Coding Type HE100...............................................................................................................................23
19 EU and UK Declaration of Conformity ...................................................................................................24

HAUBER-Elektronik GmbH
4
2 Safety information
2.1 General
The safety instructions are intended to protect people and property from damage and hazards
that could arise as the result of improper use, incorrect operation or other misuse or devices,
especially in explosive areas. Therefore, please read the operating instructions carefully before
working on the product or operating it. The operating instructions must be accessible to operat-
ing personnel at all times.
Please make sure that all documents are present and complete before commissioning or per-
forming other work on the product. If the documents have not all been delivered in full or if fur-
ther copies are necessary, they can also be obtained in other languages.
The product is built according to the latest state of the art. However, hazards to people, machin-
ery and systems can still arise as the result of improper handling, unintended use or operation
and maintenance by persons inadequately trained on the product.
All those who are involved in the installation, operation and maintenance of the product in the
operator’s plant must read and understand the operating instructions.
The product may only be assembled, disassembled, installed and repaired by instructed, suffi-
ciently trained and authorised personnel.
2.2 Symbols used
This symbol indicates an explosion hazard.
This symbol indicates a hazard from electrical current.
This symbol indicates information unrelated to safety.
3 Scope of this instruction manual
This instruction manual for the HE100-type vibration monitoring unit applies to the following vari-
ants:
Standard / ATEX / IECEx / UKEx / EACEx
The variants are functionally identical. The ATEX / IECEx / UKEx / EACEx variants also pos-
sess certifications and labels which permit use in potentially explosive atmospheres. For further
information, see chapter "Fields of application” on page 7.

HAUBER-Elektronik GmbH
5
4 Vibration Monitoring Unit Type HE100
The HE100-type vibration monitoring unit is used to measure and monitor absolute bearing vib-
rations in machines in line with DIN ISO 10816.
It offers the following features:
•Operating principle: The two-wire system.
•Measurement parameter: The effective value (rms) of the vibration speed in mm/s, in ac-
cordance with DIN ISO 2954.
•Analogue current output: Interference-free DC signal from 4-20 mA, proportional to the
measuring range of the monitoring unit.
•A break on the monitoring cable can be detected by the subsequent evaluation device:
DC signal value < 3.5 mA.
Fehler! Keine Do kumentvariable v erfügbar.
5 Intended Use
The HE100 type is used exclusively for measuring mechanical vibrations in machines and me-
chanical systems. It may only be used in accordance with the specifications listed in the data
sheet. Main fields of application: Fans, ventilators, blowers, electric motors, pumps, centri-
fuges, separators, generators, turbines and similar oscillating mechanical equipment.
6 Scope of supply
All versions include:
•Vibration monitoring
•Operating instructions
7 Documents and Certificates
You can find the following documents and certificates for HE100 type at www.hauber-elektro-
nik.de where they can be viewed and downloaded:
•EU type examination certificate ATEX, no.: PTZ 16 ATEX 0029 X Rev 3
•UKEx certificate number: UL22UKEX2481X
•IECEx certificate of conformity, no.: PTZ 18.0009 X Rev 2
•UL certificate of conformity, no.: E507077-20191126
•UL Haz Loc Certificate of Conformity & Control Drawing M003-HE100
•CCC certificate for mandatory product certification for China
•Kosha certificate
•EACEx certificate RU C-DE.HA65.B.00053/19
•EAC Declaration

HAUBER-Elektronik GmbH
6
8 Transfer of liability when operating in potentially explosive atmospheres
The owner of the system is exclusively liable for the appropriate configuration of the electrical
connections with respect to explosion protection regulations and correct commissioning.
If the system is installed by a sub-contractor on behalf of the owner, the system may only be
commissioned after the sub-contractor has issued written confirmation in the form of a certificate
of installation that the system has been installed correctly and professionally in accordance with
the applicable legal regulations.
The operator is obliged to notify the responsible authorities of the initial commissioning of explo-
sion-protected systems or system components and their re-commissioning following extensive
changes or maintenance.

HAUBER-Elektronik GmbH
7
9 Fields of application and example labels
HE100.00
HE100.01
HE100.02
HE100.03
Version
Standard CE / IEC / EAC
UL Proc. Cont. Eq. Ord.
Loc.
ATEX / IECEx / UKEx /
EACEx
Pressure-resistant casing
Ex db
Protection through housing
Ex tb
ATEX / IECEx / UKEx /
EACEx
Intrinsic safety Ex ib
UL Proc. Cont. Eq. Haz. Loc.
Division 2
Fields of appli-
cation
Atmospheres not at risk of ex-
plosion
Potentially explosive atmos-
pheres of zones
1 and 21
2 and 22
Potentially explosive atmos-
pheres of zones
1 and 21
2 and 22
Potentially explosive atmos-
pheres according to UL Divi-
sion 2
Marking
E507077
Process Control Equipment
for Ordinary Location
II 2G Ex db IIC T4 Gb
II 2D Ex tb IIIC T120 °C Db
-40 °C ≤ TAmb ≤+60°C
PTZ 16 ATEX 0029 X Rev 3
IECEx
Ex db IIC T4 Gb
Ex tb IIIC T120 °C Db
-40 °C ≤ TAmb ≤+60°C
IECEx PTZ 18.0009 X Rev 2
II 2G Ex db IIC T4 Gb
II 2D Ex tb IIIC T120 °C Db
-40 °C ≤ TAmb ≤+60°C
UL22UKEX2481X
1Ex db IIC T4 X
Ex tb IIIC T120 °C X
-40 °C ≤ TAmb ≤+60°C
№ TP ТС 012/2011
II 2G Ex ib IIC T4 Gb
II 2D Ex ib IIIC T125 °C Db
-40 °C ≤ TAmb ≤+60°C
PTZ 16 ATEX 0029 X Rev 3
IECEx
Ex ib IIC T4 Gb
Ex ib IIIC T125 °C Db
-40 °C ≤ TAmb ≤+60°C
IECEx PTZ 18.0009 X Rev 2
II 2G Ex ib IIC T4 Gb
II 2D Ex ib IIIC T125 °C Db
-40 °C ≤ TAmb ≤+60°C
UL22UKEX2481X
1Ex ib IIC T4 X
Ex ib IIIC T125 °C X
-40 °C ≤ TAmb ≤+60°C
№ TP ТС 012/2011
Class I, Division 2,
Groups A, B, C and D, T4
Class II, Division 2,
Groups F and G, T4
E516625
Process Control Equipment
for Hazardous Location
Type plate
Standards applied
You can find a list of standards, including the related issue dates, in the EU type examination
certificate for the vibration monitoring unit.

HAUBER-Elektronik GmbH
8
10 Conditions for safe operation in potentially explosive atmospheres
The following conditions must be met for safe operation in a potentially explosive atmosphere.
10.1 HE100.01 (ignition protection class "pressure-resistant casing")
Electrical data
min.
typ.
max.
Supply voltage
Un
10 V DC
24 V DC
30 V DC
Current consumption
In
4 mA
4 –20 mA
25 mA
Tab. 1: Electrical data HE100.01
10.2 HE100.02 (ignition protection class "intrinsically safe")
With the ignition protection class intrinsically safe Ex ib IIC or IIC, the sensor
must only be operated in a certified intrinsically safe electrical circuit. The ma-
ximum values must not be exceeded.
The following values relate to the vibration monitoring unit and the supply and
signal circuit.
Electrical data
Max. input voltage of the vibration monitoring unit
Ui
30 V DC
Max. input current of the vibration monitoring unit
Ii
100 mA
Max. input power of the vibration monitoring unit
Pi
600 mW
Capacitance of the vibration monitoring unit
Ci
44 nF
Inductance of the vibration monitoring unit
Li
0 µH
Tab. 2: HE100.02 electrical data

HAUBER-Elektronik GmbH
9
Other conditions
1. Extended ambient temperature range of -40 °C to +60 °C
2. Equipotential bonding takes place during installation.
3. The instruction manual must be heeded.
4. The following feed/inlet isolating amplifiers are tested and approved by Hauber-Elektronik
GmbH for intrinsically safe operation:
•Endress und Hauser
active barrier RN221N with HART® diagnosis
•PHOENIX CONTACT Deutschland GmbH
feed and isolating amplifier MACX MCR-EX-SL-RPSSII 2865340
•Pepperl+Fuchs
SMART transmitter supply unit KFD2-STC3-Ex1
•R. STAHL Schaltgeräte GmbH
transducer supply unit 9260/13-11-10s art. no. 261384
5. The Ex i version must only be operated with the Ex i cable approved by Hauber-Elektro-
nik. On this cable, pin 5 of the M12 connector is assigned to the cable shield. (HE article
number: 11141 (2 m), 11142 (5 m), 11143 (10 m), additional lengths available in stock)
HAUBER-Elektronik is not responsible for changes to the specification of the
feed/inlet isolating amplifier mentioned.
10.3 HE100.03 cULus Hazloc DIV2
The version for DIV2 may not be operated without the safety clip to guard against acci-
dental disconnection of the plug connection! If operated in a potentially explosive at-
mosphere, there is otherwise an explosion hazard, due to spark formation!
For use in DIV2, the supply voltage may not exceed 28.1 V DC. This must be ensured
through the use of an appropriate power supply unit.
Attaching the safety clip
1. Insert the connecting cable socket into the M12 connector as far as it will go (mind the
position of the code cam).
2. Tighten the knurled rotating ring of the socket by hand.
3. Attach the safety clip to guard against accidental disconnection of the plug connection.
- Place both shell halves of the clip around the plug connection.
- Press both shell halves firmly together with your hands until the lock snaps into place.
- Place the arrow connected to the two shell halves around the cable and pull it through
the eyelet at the other end so that the notice "DO NOT DISCONNECT UNDER
VOLTAGE" can be read alongside the cable.

HAUBER-Elektronik GmbH
10
Fig. 1: Safety clip
Fig. 2: Attached safety clip
1 Notice tag
Attaching the protection cap
After disconnecting the plug, the protection cap must be attached to the M12 plug!
Detach the safety clip and attach the protection cap.
1. Disconnect voltage.
2. Pry apart both shell halves of the sleeve with a screwdriver.
3. Close off the M12 plug well with the protection cap.
Fig. 3: Protection cap
Fig. 4: Attached protection cap
Control drawing
Please also note the control drawing HE100-M003.
Electrical data
Max. input voltage of the vibration monitoring unit
Vi-max
28.1 V DC
Max. input current of the vibration monitoring unit
Ii-max
25 mA /
50 mA (only HE101)
Tab. 3: Electrical data HE100.03

HAUBER-Elektronik GmbH
11
11 Technical data
11.1 General data
Each sensor has one of the listed measuring and frequency ranges. Further
ranges on request.
Please indicate the measuring and frequency range in your request.
Measuring range:
0 –8 mm/s (for frequency range > 10 Hz only)
0 –16 mm/s
0 –32 mm/s
0 –64 mm/s
Other measuring ranges See also Coding Type HE100, page
23.
0 … 64 mm/s
Measuring accuracy:
±10 % (according to DIN ISO 2954)
Transverse sensitivity:
< 5%
Frequency range:
10 Hz–1,000 Hz (standard)
1 Hz–1000 Hz
Calibration point
159.2 Hz and 90% amplitude of measuring range
Maximum acceleration
±16.5 g
Lifetime
10 years
MTTF value
399 years
Permissible temperature
ranges
-40 °C –+60 °C (ambient temperature)
-40 °C –+125 °C (measuring head temperature)
Tab. 4: General data
11.2 Electrical data
Output signal:
4 –20 mA (proportional to the measuring range)
Power supply:
10 –30 V DC
Power input (max.):
25 mA
Load/output load (max.):
500 Ω
Fuse *
30VDC, 3A, medium blow
* Ensure that the supply line is protected by a UL-approved fuse for UL-compliant sensor ope-
ration.
Tab. 5: Electrical data

HAUBER-Elektronik GmbH
12
11.3 Operating range of the vibration monitoring unit
The operating range is independent from the measuring range. It can be derived from the maxi-
mum acceleration, which is 16.5 g across all frequencies. The maximum measurable vibration
velocity is based on the formula
For sinusoidal vibration,
applies
Fig. 5: shows the operating range of the vibration monitoring unit, which is limited by the maxi-
mum measurable vibration velocity in mm/s depending on the frequency in Hz.
Fig. 5: Operating range diagram
1 Frequency in Hz
2 Vibration velocity in mm/s
3 Operating range of the vibration monitoring unit
Reading example:
Frequency
(Hz)
Maximum measurable vibra-
tion speed
(mm/s)
250
103
400
64
1000
25
Tab. 6: Reading example of operating range

HAUBER-Elektronik GmbH
13
11.4 Typical frequency response
10 Hz–1,000 Hz (standard)
The frequency response is recorded using a reference sensor.
• 4 Hz. . . 1200 Hz acceleration sensor
Fig. 6: Typical frequency response 10 Hz–1000 Hz
1 Frequency in Hz
2 Amplification in dB
1 Hz–1000 Hz
The frequency response is recorded using two reference sensors.
• 1 Hz. . . 10 Hz laser sensor
• 10 Hz. . . 1200 Hz acceleration sensor
Fig. 7: Typical frequency response 1 Hz–1000 Hz
1 Frequency in Hz
2 Amplification in dB

HAUBER-Elektronik GmbH
14
11.5 Mechanical data
Additional materials and fixings can be found in section "Coding Type HE100"
on page 23.
Housing material:
Stainless steel V2A, material no.: 1.4305 (standard)
Fastening:
Width across flats 24 (hexagonal)
M8 x 8 mm
Pitch: 1.25 mm (standard)
Installation type:
standing/vertical or lying/horizontal
Measuring direction:
Along the fastening axis
Tightening torque sensor
8 Nm
Max. torque of the M12
union nut on the connector
0.4 Nm
Weight:
approx. 200 g
Protection class:
IP 66/67 (when connected)
Tab. 7: Mechanical data
11.6 Housing dimensions
Variante: Standard und ATE X/ IECEx / EAC Ex
11.6.1 Version: Standard and ATEX / IECEx / UKEx / EACEx intrinsic safety Ex i
Fig. 8: Housing with M12 connector
All measurements in
mm
1 M12 connector
2 Width A/F 24
3 Fixing
4 Measuring direction along the fixing axis

HAUBER-Elektronik GmbH
15
11.6.2 Version: ATEX / IECEx / UKEx / EACEx Ex d
Fig. 9: Housing with integrated cable
All measurements in
mm
1 Cable gland for integrated cable
2 Width A/F 24
3 Fixing
4 Measuring direction along the fixing axis
11.7 Properties of the integrated cable
Cable type
12YC11Y 4x03.4 mm²
Conductor material
El-Cu stranded wire
Conductor insulation
TPEE E (12Y)
Coating
PUR
Coating diameter
6.0 ± 0.2 mm
Temperature range
-40 °C –+80 °C fixed
-30 °C –+80 °C moving
Minimum bending radius
30 mm fixed
60 mm moving
Flame resistant
Yes, according to UL 1582 Sec. 1061
Halogen-free
Yes
Tab. 8: Technical data of the integrated cable

HAUBER-Elektronik GmbH
16
12 Connection
Version:
Standard
Connector, M12, 4-pin
Pin 1:
10 –30 V DC
Pin 2:
NC
Pin 3:
4–20 mA
Pin 4:
NC
NC:
Not connected
Version:
ATEX / IECEx / UKEx / EACEx pressure-resistant casing Ex d
ATEX / IECEx / UKEx / EACEx protection through housing Ex tb
Integrated cable
brown
Pin 1:
10 –30 V DC
white
Pin 2:
NC
blue
Pin 3:
4–20 mA
black
Pin 4:
NC
PUR sheathed cable, Ø: approx. 6.5 mm,
4-pin, 0.34 mm2
NC:
Not connected
Version:
ATEX / IECEx / UKEx / EACEx intrinsic safety Ex i
Connector, M12, 5-pin
Pin 1:
10 –30 V DC
Pin 2:
NC
Pin 3:
4–20 mA
Pin 4:
NC
Pin 5:
Sensor housing
NC:
Not connected
The system operates according to the two-wire principle,
i.e. the entire function (voltage supply and current signal) is achieved using 2
wires (Pin 1 and Pin 3).
To avoid capacitive interference, pins 2 and 4 must remain open/unoccupied.

HAUBER-Elektronik GmbH
17
13 Assembly and disassembly
13.1 General notes
Assembly and disassembly work on and with the vibration monitoring unit may only be perfor-
med by an authorised specialist familiar with the safety regulations governing handling electrical
components!
The housing of the vibration monitoring unit must be earthed via the fixing –
through the machine earth of the mounting surface or through a separate pro-
tective conductor (PE)!
13.2 Fixing the vibration monitoring unit to the mounting surface
13.2.1 Prerequisites
• Mounting surface is clean and flat, i.e. free of paint, rust, etc.
• Measuring head area of the vibration monitoring unit must lie flat on the mounting surface.
13.2.2 Tool
•Hex key, width A/F 24
13.2.3 Work steps and instructions
•Screw vibration monitoring unit into the threaded hole of the mounting surface in a fric-
tion-locked manner using a hex key. The tightening torque should be 8 Nm.
•The tightening torque of the M12 union nut of the plug connection must not exceed 0.4
Nm.
To obtain precise measurement values, the vibration monitoring unit must be
fixed to the mounting surface in a friction-locked manner!
Auxiliary structures for fixing are to be avoided! If unavoidable, make them as
firm as possible!
Earth/ground loops are amongst the most common problems in measurement
set-ups with sensitive sensor technology. These issues arise due to unintentio-
nal differences in potential in the electrical circuit between the sensor and eva-
luation unit. As a countermeasure, we recommend our standard earthing con-
cept or, depending on the application, our Alternative earthing concept
Ensure that the earth connection is electrically secure.

HAUBER-Elektronik GmbH
18
14 Installation and commissioning
14.1 General notes
Installation and commissioning of the vibration monitoring unit must be performed by an
authorised specialist who is familiar with the safety regulations when handling
electrical components.
Protect the connection cable and any extension cable from electrical interfer-
ence and mechanical damage! Local regulations and instructions must be ob-
served in doing so!
14.2 Wiring diagram
Earth/ground loops are amongst the most common problems in measurement set-ups with
sensitive sensor technology. These issues arise due to unintentional differences in potential in
the electrical circuit between the sensor and evaluation unit.
Ensure that the earth connection is electrically secure.
14.2.1 Standard earthing concept
With the standard earthing concept, the sensor cable shield has no connection to the sensor
housing. The sensor housing has the same potential as the machine earth.
Fig. 10: Standard earthing concept
1 Machine earth
2 Evaluation unit (measuring instrument, SPS, …)
3 Blue –4 –20 mA current signal
4 Brown –10 –30 V DC
5 Cable shield
6 Evaluation unit for earth potential
7 Optional flexible metal tubing (available for version with integrated cable only)

HAUBER-Elektronik GmbH
19
14.2.2 Alternative earthing concept
With the alternative earthing concept, the sensor cable shield has a connection to the sensor
housing. The sensor housing uncoupled from the machine earth by means of an EMC adapter
(red). With the alternative earthing concept an electrically secure earth connection is only en-
sured for versions with an M12 connector. For variants with an integrated cable, the alternative
earthing concept cannot be used.
Fig. 11: Alternative earthing concept
1 Machine earth
2 Evaluation unit (measuring instrument, SPS, …)
3 Blue –4 –20 mA current signal
4 Brown –10 –30 V DC
5 Cable shield
6 Evaluation unit for earth potential
7 EMC adapter (Hauber item no. 10473)
In your request, please notify us if you would like to use the alternative earthing
concept. We will then provide you with the appropriate sensor cable and the
EMC adapter.

HAUBER-Elektronik GmbH
20
14.2.3 Explosive atmosphere Ex i earthing concept
For the Ex i sensor, the shield is routed via Pin 5 of the plug connection to the potential of the
sensor housing that typically provides the machine earth.
Fig. 12: Ex i earthing concept
1 Machine earth
2 The shield of the Ex i cable is at the
potential of the housing via Pin 5 of the
M12 connector
3 Do not earth the shield
4 Evaluation unit (measuring device,
PLC, etc.)
5 Power supply
6 Hauber Ex i sensor
7 Isolating amplifier
8 Potentially explosive atmospheres of
zones 1 and 21/2 and 22
9 Area not at risk
This manual suits for next models
4
Table of contents
Other Hauber Elektronik Measuring Instrument manuals
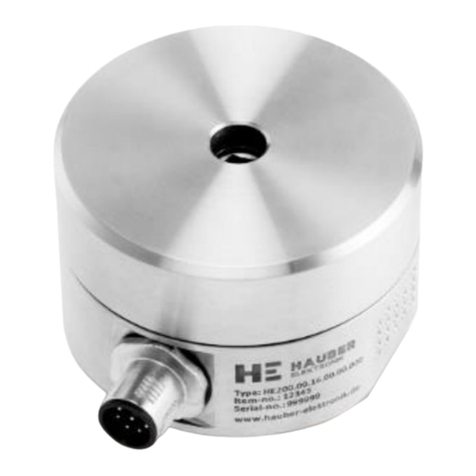
Hauber Elektronik
Hauber Elektronik HE250 Series User manual
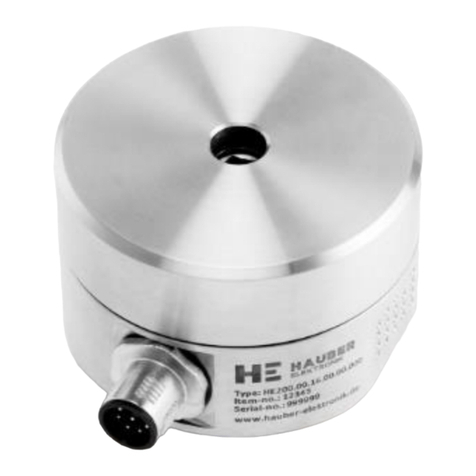
Hauber Elektronik
Hauber Elektronik HE255 Series User manual
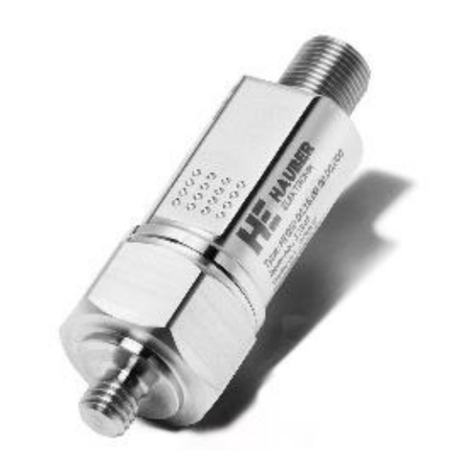
Hauber Elektronik
Hauber Elektronik HE050 Series User manual

Hauber Elektronik
Hauber Elektronik HE103 Series User manual
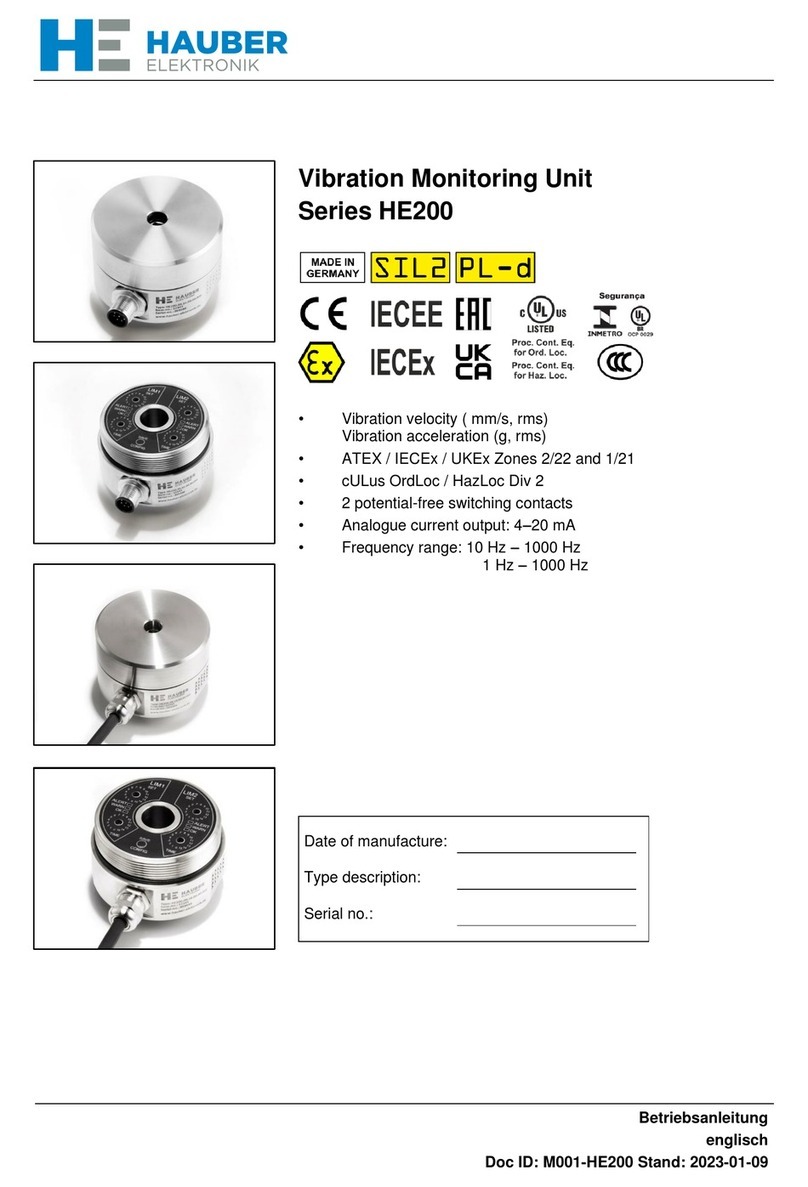
Hauber Elektronik
Hauber Elektronik HE200 Series User manual
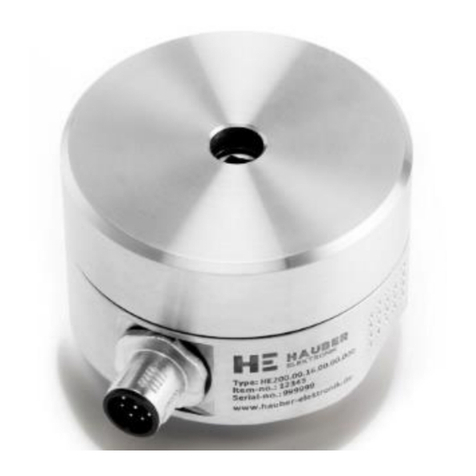
Hauber Elektronik
Hauber Elektronik HE205 Series User manual
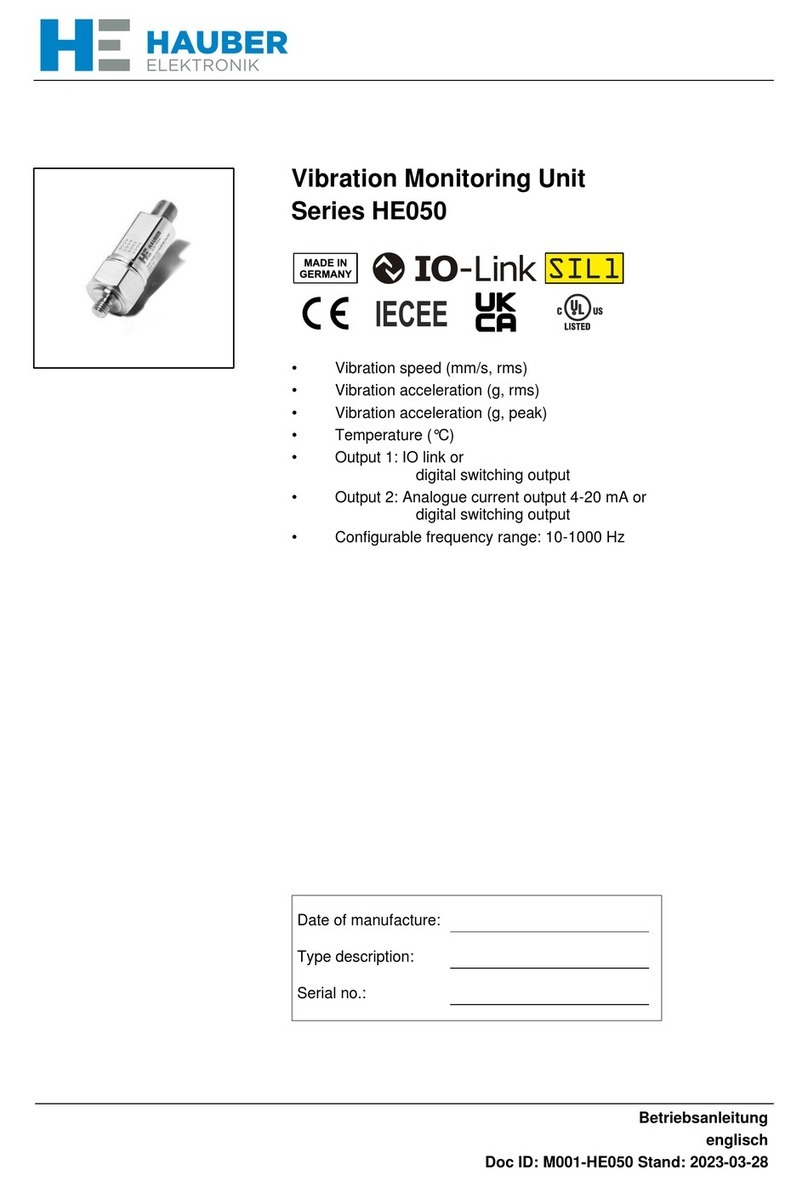
Hauber Elektronik
Hauber Elektronik HE050 Series User manual