HBM PaceLine CLP User manual

Mounting Instructions | Montageanleitung |
Notice de montage | Istruzioni per il montaggio
English Deutsch Français Italiano
CLP

Hottinger Baldwin Messtechnik GmbH
Im Tiefen See 45
D-64293 Darmstadt
Tel. +49 6151 803-0
Fax +49 6151 803-9100
www.hbm.com
Mat.: 7-2001.3616
DVS: A03616_04_YI0_02 HBM: public
01.2020
EHottinger Baldwin Messtechnik GmbH.
Subject to modifications.
All product descriptions are for general information only.
They are not to be understood as a guarantee of quality or
durability.
Änderungen vorbehalten.
Alle Angaben beschreiben unsere Produkte in allgemeiner
Form. Sie stellen keine Beschaffenheits- oder Haltbarkeits
garantie dar.
Sous réserve de modifications.
Les caractéristiques indiquées ne décrivent nos produits
que sous une forme générale. Elles n'impliquent aucune
garantie de qualité ou de durablilité.
Con riserva di modifica.
Tutti i dati descrivono i nostri prodotti in forma generica e non
implicano alcuna garanzia di qualità o di durata dei prodotti
stessi.

Mounting Instructions | Montageanleitung |
Notice de montage | Istruzioni per il montaggio
English Deutsch Français Italiano
CLP

2A03616_04_YI0_02 HBM: public CLP
English
1 Safety instructions 3........................................
2 Scope of supply 7..........................................
3 Application instructions 9...................................
4 Structure and principle of operation 10........................
5 Conditions on site 11........................................
5.1 Ambient temperature 11.......................................
5.2 Moisture 12..................................................
5.3 Deposits 12..................................................
6 Mechanical installation 13....................................
6.1 Important precautions during installation 13......................
6.2 General installation guidelines 14...............................
7 Connection 18...............................................
8 Specifications (VDI/VDE/DKD 2638) 19........................
9 Dimensions 21..............................................

Safety instructions
CLP A03616_04_YI0_02 HBM: public 3
1 Safety instructions
Intended use
Force transducers of the CLP type series are solely designed for measuring
static and dynamic compressive forces within the load limits specified by the
technical data for the respective maximum capacities. Any other use is not ap
propriate.
To ensure safe operation, always comply with the regulations in the mounting
and operating instructions, together with the following safety rules and regula
tions, and the data specified in the technical data sheets. It is also essential to
observe the applicable legal and safety regulations for the relevant application.
The force transducers are not intended for use as safety components. Please
also refer to the "Additional safety precautions" section. Proper and safe opera
tion of force transducers requires proper transportation, correct storage, setup
and mounting, and careful operation.
Operating personnel
Mounting and operation of the force transducer must only be carried out by fully
qualified personnel. Qualified personnel in this respect means persons en
trusted with installing, mounting, starting up and operating the product, who are
familiar with the operation of the force transducer and possess the appropriate
qualifications for their function.
Load-carrying capacity limits
The information in the technical data sheets must be complied with when using
force transducers. The respective specified maximum loads in particular must
never be exceeded. The following limits set out in the specifications must not
be exceeded:
SLimit loads
SLateral load limits
SBreaking loads
SPermissible dynamic loads
STemperature limits

Safety instructions
4A03616_04_YI0_02 HBM: public CLP
When several force transducers are connected, it must be noted that the load/
force distribution is not always uniform.
Use as a machine element
Force transducers can be used as machine elements. When used in this man
ner, it must be noted that, to favor greater sensitivity, the force transducers
were not designed with the safety factors usual in mechanical engineering.
Please refer here to the section "Load-carrying capacity limits", and to the
specifications.
Additional safety precautions
Force transducers cannot (as passive transducers) implement any safety-rele
vant cutoffs. This requires additional components and constructive measures,
for which the installer and operator of the plant is responsible.
In cases where a breakage or malfunction of the force transducer would cause
injury to persons or damage to equipment, the user must take appropriate addi
tional safety measures that meet at least the requirements of applicable safety
and accident prevention regulations (e.g. automatic emergency shutdown,
overload protection, catch straps or chains, or other fall protection).
The electronics conditioning the measurement signal should be designed so
that measurement signal failure does not subsequently cause damage.
General dangers of failing to follow the safety instructions
Force transducers are state-of-the-art and failsafe. There may be dangers in
volved if the transducers are mounted, sited, installed and operated inappropri
ately, or by untrained personnel. Every person involved with siting, starting-up,
operating or repairing a force transducer must have read and understood the
mounting instructions and in particular the technical safety instructions. The
force transducers can be damaged or destroyed by non-designated use of the
force transducer or by non-compliance with the mounting and operating instruc
tions, these safety instructions or any other applicable safety regulations (BG
safety and accident prevention regulations) when using the force transducers.
Force transducers can break, particularly if overloaded. The breakage of a
force transducer can also cause damage to property or injury to persons in the
vicinity of the force transducer.

Safety instructions
CLP A03616_04_YI0_02 HBM: public 5
If force transducers are not used according to their designated use, or if the
safety instructions or specifications in the mounting and operating instructions
are ignored, it is also possible that the force transducer may fail or malfunction,
resulting in injury to persons or damage to property (due to the loads acting on
or being monitored by the force transducer).
The scope of supply and performance of the transducer covers only a small
area of force measurement technology, as measurements with piezoelectric
sensors presuppose the use of electronic signal conditioning. In addition,
equipment planners, installers and operators should plan, implement and re
spond to the safety engineering considerations of force measurement
technology in such a way as to minimize residual dangers. Prevailing regula
tions must be complied with at all times.
Important instructions for your safety are specifically identified. It is essential to
follow these instructions in order to prevent accidents and damage to property.
Symbol Significance
WARNING This marking warns of a potentially dangerous situa
tion in which failure to comply with safety require
ments could result in death or serious physical injury.
CAUTION This marking warns of a potentially dangerous situa
tion in which failure to comply with safety require
ments could result in slight or moderate physical in
jury.
Notice This marking draws your attention to a situation in
which failure to comply with safety requirements
could lead to damage to property
Waste disposal
In accordance with national and local environmental protection, material recov
ery and recycling regulations, old transducers that can no longer be used must
be disposed of separately and not with normal household waste.
If you need more information about disposal, please contact your local authori
ties or the dealer from whom you purchased the product.

Safety instructions
6A03616_04_YI0_02 HBM: public CLP
Conversions and modifications
The design or safety engineering of the transducer must not be modified with
out our express permission. Any modification shall exclude all liability on our
part for any damage resulting therefrom.
Qualified personnel
Qualified personnel are persons entrusted with the setup, mounting, startup
and operation of the product, who have the appropriate qualifications for their
function.
This includes people who meet at least one of the three following requirements:
1. Knowledge of the safety concepts of automation technology is a require
ment and as project personnel, you must be familiar with these concepts.
2. As automation plant operating personnel, you have been instructed how to
handle the machinery. You are familiar with the operation of the equipment
and technologies described in this documentation.
3. As commissioning engineers or service engineers, you have successfully
completed the training to repair the automation systems. You are also au
thorized to operate, ground and label circuits and equipment in accordance
with safety engineering standards.
It is also essential to comply with the legal and safety requirements for the rele
vant application during use. The same applies to the use of accessories.
The force transducer must only be installed by qualified personnel, strictly in
accordance with the specifications and with the safety requirements and regu
lations.
Maintenance
The CLP force transducer is maintenance-free.
Accident prevention
The prevailing accident prevention regulations must be taken into account,
even though the nominal (rated) force values in the destructive range are well
in excess of the full scale value.

Scope of supply
CLP A03616_04_YI0_02 HBM: public 7
2 Scope of supply
Ordering number
1-CLP/3kN Piezoelectric force washer CLP/3kN with test report; cable
length 1 m
1-CLP/7kN Piezoelectric force washer CLP/7kN with test report; cable
length 1 m
1-CLP/14kN Piezoelectric force washer CLP/14kN with test report; cable
length 1 m
1-CLP/26kN Piezoelectric force washer CLP/26kN with test report; cable
length 1 m
1-CLP/36kN Piezoelectric force washer CLP/36kN with test report; cable
length 1 m
1-CLP/62kN Piezoelectric force washer CLP/62kN with test report; cable
length 1 m
1-CLP/80kN Piezoelectric force washer CLP/80kN with test report; cable
length 1 m
1-CLP/3kN-0.5M Piezoelectric force washer CLP/3kN with test report; cable
length 0.5 m
1-CLP/7kN-0.5M Piezoelectric force washer CLP/7kN with test report; cable
length 0.5 m
1-CLP/14kN-0.5M Piezoelectric force washer CLP/14kN with test report; cable
length 0.5 m
1-CLP/26kN-0.5M Piezoelectric force washer CLP/26kN with test report; cable
length 0.5 m
1-CLP/36kN-0.5M Piezoelectric force washer CLP/36kN with test report; cable
length 0.5 m
1-CLP/62kN-0.5M Piezoelectric force washer CLP/62kN with test report; cable
length 0.5 m
1-CLP/80kN-0.5M Piezoelectric force washer CLP/80kN with test report; cable
length 0.5 m

Scope of supply
8A03616_04_YI0_02 HBM: public CLP
To be ordered separately
Ordering number
Cable for extension in combination with coupling CCO
1-KAB143-0.5 Transducer connection cable (material: PFA), 0.5m long;
10-32 UNF connector plug at both ends
1-KAB143-2 Transducer connection cable (material: PFA), 2m long; 10-32
UNF connector plug at both ends
1-KAB143-3 Transducer connection cable (material: PFA), 3 m long; 10-32
UNF connector plug at both ends
1-KAB143-7 Transducer connection cable (material: PFA), 7 m long; 10-32
UNF connector plug at both ends
1-KAB143-10 Transducer connection cable (material: PFA), 10m long;
10-32 UNF connector plug at both ends
1-KAB176-1 Transducer connection cable (material: PFA), 1m long; 10-32
UNF connector plug on transducer end, BNC on amplifier end
(e.g. suitable for digital charge amplifier CMD600)
1-KAB176-2 Transducer connection cable (material: PFA), 2m long; 10-32
UNF connector plug on transducer end, BNC on amplifier end
(e.g. suitable for digital charge amplifier CMD600)
1-KAB176-3 Transducer connection cable (material: PFA), 3m long; 10-32
UNF connector plug on transducer end, BNC on amplifier end
(e.g. suitable for digital charge amplifier CMD600)
Coupling and summing box
1-CCO Coupling for connection cable for piezoelectric sensors,
10-32UNF plug at both ends
1-CSB4/1 Summing box for parallel connection of piezoelectric sensors,
10-32 UNF connectors

Application instructions
CLP A03616_04_YI0_02 HBM: public 9
3 Application instructions
Piezoelectric force washers of the CLP type series are suitable for measuring
compressive forces. Because they provide highly accurate dynamic and quasi-
static force measurements, they must be handled very carefully. Particular care
must be taken when transporting and installing the devices. Dropping or knock
ing the transducer may cause permanent damage.
The transducers are extremely stiff and have a high natural frequency.
Limits for acceptable mechanical, thermal and electrical stress are listed in the
Specifications section on page 19. It is essential that these are taken into ac
count when planning the measuring set-up, during installation and, ultimately,
during operation.
Notice
Like all piezoelectric force sensors, the piezoelectric force washers of the CLP
series are only exposed to great force (greater than 10% of the sensor capac
ity) if they are connected to a charge amplifier, or short-circuited. If the sensors
are loaded without this measure being taken, voltage flashover can result,
which could damage the sensor.

Structure and principle of operation
10 A03616_04_YI0_02 HBM: public CLP
4 Structure and principle of operation
The CLP force washer is based on the piezoelectric principle.
Compressive forces are transmitted to measuring elements that are sensitive to
force via the upper and lower force application surfaces. These separate the
electrical charges in proportion to the applied force. A charge amplifier can then
convert these electrical charges to an analog voltage signal.
Fig. 4.1 Force is applied via the upper/lower force application surface
The piezoelectric principle of measurement only requires minimal displace
ment, so the stiffness of the transducer is therefore exceptionally high. The re
sulting high resonance frequencies make piezoelectric force transducers pre
destined for dynamic applications.
The force washer is hermetically welded and the coaxial cable is permanently
connected to the sensor. Compressive force generates a negative electrical
charge.

Conditions on site
CLP A03616_04_YI0_02 HBM: public 11
5 Conditions on site
Protect the force washer from moisture or weather conditions such as rain,
snow and ice, as well as salt water.
CAUTION
Measurement errors (forces too small or too large) occur if the insulation resis
tance is less than 1011 ohms. This could lead to measurement errors from the
measuring system, and therefore danger for the operating personnel of the sys
tem in which the transducer is installed.
To obtain a sufficiently high value, all the plug connections have to be kept
thoroughly clean. A strong (greater than 10 N/min at room temperature in ther
mal equilibrium) positive or negative signal drift of the output signal without any
force applied indicates insufficient insulation resistance. The plug connection
contacts should therefore be cleaned with a clean, lint-free cloth and a cleaning
agent (pure isopropanol).
Protect the transducer plug against pollution and under no circumstances touch
the charge amplifier connectors (plug face) with your fingers. The supplied
cover should always be in place when the connection is not in use.
5.1 Ambient temperature
The influence of the temperature on the sensitivity is low and can be ignored.
However, thermal stresses will occur in the force washer if it is heated un
evenly, and these will generate an output signal. The following measures im
prove the stability of the measurement:
SMake sure that the temperatures of the sensor and the components used to
pre-stress the sensor are as even as possible before starting to measure.
This applies in particular to long measurements and when adjusting the
force washers

Conditions on site
12 A03616_04_YI0_02 HBM: public CLP
SAvoid temperature fluctuations, e.g. from hand warmth, shortly before mea
surement.
SAfter each measurement cycle, perform a reset (zeroing) or if possible, use
a high-pass filter.
SNote the temperature limits for the transducer (see the Specifications sec
tion, page 19).
5.2 Moisture
Moisture or a tropical climate are to be avoided. When the connection cable is
properly connected to the charge amplifier, the CLP force washer has degree
of protection IP65 per EN 60529.
The enclosure of the transducer is made entirely of stainless steel. The trans
ducer must be protected against chemicals that could attack the transducer
body steel or the cable.
With stainless steel force transducers, note that acids and all materials which
release ions will also attack stainless steels and their seam welds. Any result
ing corrosion could cause the force transducer to fail. In this case, appropriate
protective measures must be implemented.
5.3 Deposits
Dust, dirt and other foreign matter must not be allowed to accumulate suffi
ciently to divert some of the measuring force, thus invalidating the measured
value (force shunt).

Mechanical installation
CLP A03616_04_YI0_02 HBM: public 13
6 Mechanical installation
6.1 Important precautions during installation
SHandle the transducer with care.
SShould high welding currents flow over the sensor, there is a risk - espe
cially if the sensor is not fully in contact, that unintentional welding may oc
cur, and that removal will then no longer be possible. HBM provides highly
flexible EEK ground cables, which can be screwed on above and below the
sensor, to electrically short-circuit it.
SMake sure that the sensor is not loaded with more than the force limit.
The pre-stress force and the force being measured should not usually be
greater than the nominal (rated) force.
WARNING
There is a danger of the transducer breaking if it is overloaded. This can cause
danger for the operating personnel of the system in which the transducer is in
stalled.
Implement appropriate safety measures to avoid overloads or to protect against
the resulting dangers.

Mechanical installation
14 A03616_04_YI0_02 HBM: public CLP
6.2 General installation guidelines
The forces to be measured must act perpendicularly to the force washer. Tor
sional and bending moments, eccentric loading and lateral forces may produce
measurement errors and destroy the transducer, if limit values are exceeded
(see Specifications).
The contact surfaces that transmit the force to the piezoelectric transducer
must be flat, stiff and clean. Paint and coatings must be removed. Components
that come directly into contact with the force application surfaces of the force
washer should have a hardness value of 43 HRC.
In the CLP series force washers, the maximum bending moment is subject to
loading with a force in the measuring grid direction. The following rule applies:
A force washer loaded with nominal (rated) force must not be additionally
loaded with a bending moment. This also applies to a force washer where no
force is acting in the measuring grid direction.
36kN: d=10.1mm; D=24mm; H=3.5mm;
14kN: d=6.1mm; D=16mm; H=3.5mm;
3kN: d=2.7mm; D=8mm; H=3mm;
Fig. 6.1 CLP dimensions

Mechanical installation
CLP A03616_04_YI0_02 HBM: public 15
Force acting on the force washer (pre-stress force + force to be measured) as a % of the nominal
(rated) force
Maximum bending moment as a % (see Specifications for 100%)
Fig. 6.2 Maximum loading of a force washer with bending moment, subject to the
force applied in the measuring grid direction
The maximum bending moments allowed can be found in the Specifications
section, page 19.
The transducer needs to be pre-stressed so that forces can be measured. We
recommend selecting a pre-stress value so that the sum of the pre-stress force
and the force to be measured is equal to approximately half the nominal (rated)
force of the force washer. The force washer can be loaded with the greatest
bending moment in this range.
The pre-stress force is usually generated via the bolts. The minimum quality for
the bolts is 10.9. Fig. 6.3. shows the typical mounting situation.

Mechanical installation
16 A03616_04_YI0_02 HBM: public CLP
ground Ra0.5
Customer side
component
Customer-side component
Force to be measured Force to be measured
Fig. 6.3 Force washer pre-stressed by the bolt
The minimum pre-stress force must be 10% of the nominal (rated) force. The
force washer itself can be used to determine the pre-stress force. The test re
port accompanying the transducer contains the sensitivity that you need to set
on the charge amplifier in this mounting step.
You can also use torque to adjust the pre-stress. Please use the recommended
torque from the table below, which also outlines other details about the bolts to
be used.
Once mounted, the force washer works in a force shunt, as the component
generating the pre-stress is mounted parallel to the force washer (springs con
nected in parallel).
Notice
Pre-stress forces must act precisely in the measuring grid direction, neither
bending moment nor lateral force may occur. Otherwise the transducer can be
destroyed.

Mechanical installation
CLP A03616_04_YI0_02 HBM: public 17
WARNING
If you want to introduce tensile forces, comply with the maximum load-carrying
capacity of the pre-stress elements. There is a danger of breakage if the ac
ceptable loading is exceeded. This can cause danger for the operating person
nel of the system in which the transducer is installed.
When tensile forces are exerted, the tensile force is acting on the pre-stress
elements in addition to the pre-stress force, so these elements must be de
signed accordingly.
Force
washer
Bolts
(regular thread)
Recommended
pre-stress force
in kN
Tightening
torque
in Nm
Minimum
thread reach
in mm
1-CLP/3kN M2.5 0.6 0.3 3
1-CLP/7kN M4 1.4 1.1 5
1-CLP/14kN M6 2.8 3.2 5
1-CLP/26kN M8 5.2 7.8 10
1-CLP/36kN M10 7.2 13.5 12
1-CLP/62kN M12 12.4 27.9 15
1-CLP/80kN M14 16 41.9 20
The sensitivity of the measurement chain is reduced by these installation re
quirements. Calibration (adjustment) in the mounting conditions is therefore
necessary in all cases. Both precise reference force transducers (e.g. C18 se
ries) and the calibrated piezoelectric sensors in the CFT series are available for
this purpose. You can also request calibration from HBM; the HBM calibration
laboratory would be happy to provide you with a proposal for calibrating your
pre-stressed sensors. This is always possible if your design can be installed in
our calibration system.

Connection
18 A03616_04_YI0_02 HBM: public CLP
7 Connection
Sensors of the CLP series are delivered with a permanently integrated connec
tion cable that is 1m or 0.5 m in length. You can use a coupling (for example
coupling 1-CCO available from HBM) to connect an extension cable. It is possi
ble to connect as many as four CLP series sensors in parallel; the CSB sum
ming box from HBM is used for this purpose.
Notice
If the CLP series sensors are mechanically arranged in parallel, the structural
parts touching the sensors must be sufficiently stiff and in plane-parallel align
ment with one another. This always applies when several sensors with joint
load applications are mounted. This is important, to prevent the maximum per
mitted bending moment being exceeded while pre-stressing the sensors.
Handle the transducer connection cable carefully, as it cannot be repaired. If it
is damaged, the complete sensor must be replaced.
Fig. 7.1 CLP piezoelectric force washer
This manual suits for next models
14
Table of contents
Languages:
Other HBM Measuring Instrument manuals
Popular Measuring Instrument manuals by other brands
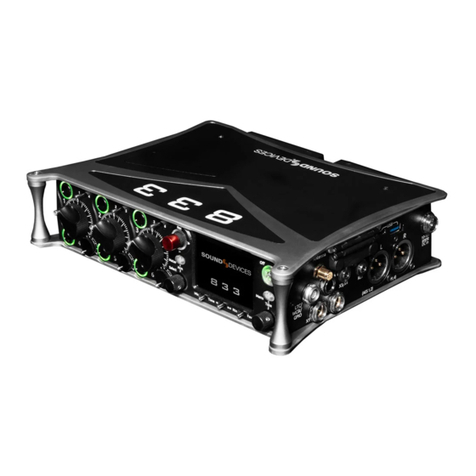
Sound Devices
Sound Devices 833 user manual
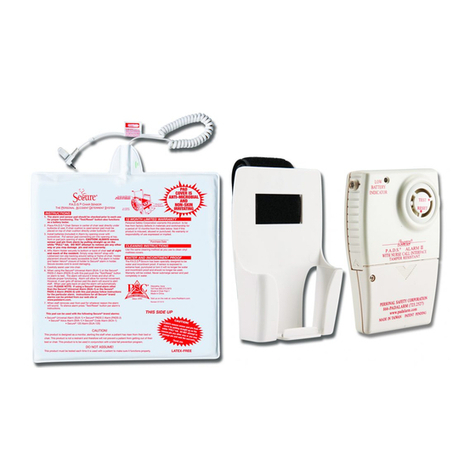
Secure
Secure PADS-2 quick start guide

Servomex
Servomex NanoTrace DF-745SG Operator's manual
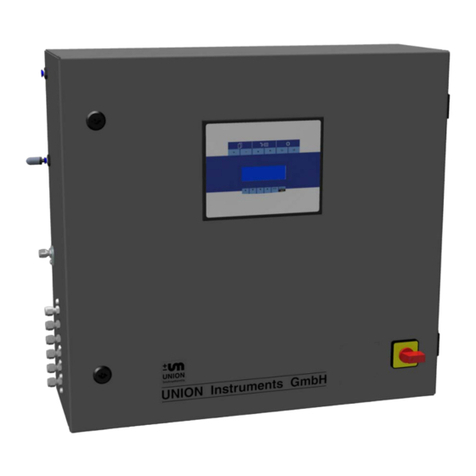
Union
Union INCA3021 Translation of the original operating instructions

Blue-White
Blue-White F-300 quick start guide
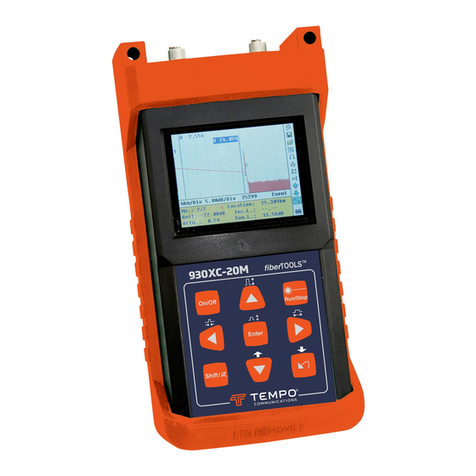
Tempo Communications
Tempo Communications 930XC-20C instruction manual